MST YE4 User manual

1
YE4 High Pressure Plunger Pump
Operations Manual
Milestone Pump
MILESTONE MANUFACTURING & ENGINEERING

2
Description
The YE4 series plunger is featured of compact structure, light weight and high
efficiency. This pump is designed to handle clear water, emulsion and other liquids
which physical nature is similar to clear water. The temperature of the liquid shoud
be 0-50℃.
There are 2 gear reduction ratio at the driven end. The pump fluid end could
be equipped with different standard packing seals according to different
requirements. The pump head doesn’t need to remove when changing the plunger
or packing seals.
The control valve could adjust pressure automatically, which could protect the
pump from overpressure.
Application
The YE4 series pump could be used as the power device of oilfield water
injection and high pressure water cleaning equipment, widely used in petroleum,
chemical, iron and steel metallurgy, ship transport, water conservancy and other
industries.
Supplied range
The pump could be supplied as
a complete set. It can include
the pump body, the pressure
control valve, safety valve,
coupling, electric motor/diesel
engine, base, spare parts and
accessories.
Technical data
YE4 High Pressure Pump Specification
Max. Motor Speed
r/min 1750 Plunger stroke mm 120
Plunger
Diameter
mm
Pump Speed 320r/min Pump Speed 366r/min
Max.pressure(Mpa) at
fixed power(kw)
Rated Flow
Max.pressure(Mpa) at
fixed power(kw)
Rated Flow
110
132
160
200
L/min
m3/h
110
132
160
200
L/min
m3/h
45 31 38 46 57
173
10.4 28 33 40 45 195
11.7
50 25 31 37 46
213
12.7 22 27 33 36 240
14.4
55 21 25 31 38
258
15.5 19 22 27 30 295
17.7
60 18 21 26 32
307
18.4 16 19 23 25 350
21
65 15 18 22 27
361
21.7 13 16 19 21 415
24.9
70 13 15 19 24
418
25.1 11 13 17 19 480
28.8

3
Pump Structure
a. Pump power end
(a) Structure
Number 1 2 3 4
Parts crankcase cover crankcase Bearing Crank assembly
Number 5 6 7 8
Parts Connecting-rod
Assembly
Cross-head
assembly
Bearing Small Gear Shaft
The crank case is made of high strength cast iron, with good water and dust
proof functions. The vent cap at the top of the case could balance the air pressure.
Please remove the cap when filling the oil.
The driven assemblies are installed in the case. The high speed shaft and the
crankshaft are driven by the character gear, with smooth transmission and low
noise. Three sets of crank and connecting rod mechanism drive the reciprocating
movement of the plunger. The driving end uses forced oil lubrication, supplied by
the external oil pump. The lubricating parts includes connecting rod pin shaft,
connecting rod axle bush, high speed bearing and cross slide road.
(b) Working Principle
With the motor or diesel engine, the high-speed shaft transmits the torque to
the crankshaft via a pair of herringbone gears and simultaneously decelerates. The
connecting-rod assembly will convert the crankshaft’s rotation into crosshead
device’s reciprocating motion, which will drive plungers to work.

4
b. Fluid End
(a) Structure
The liquid end is composed by pump head , intake liquid valve, draining valve,
packing seal, plunger, pressure regulating valve, safety valve etc
No. Part No. Part No. Part No. Part
1 Valve body 15 Nut 29 Cover A 43 Valve seat
2 Nut 16 Bolt 30 Cover B 44 Valve sleeve
3 Bolt stud 17 Inside
Hexagon bolt
31 O-ring 45 Joint
4 O-ring 18 Packing box 32 Reinforcing
mat
46 Pad
5 Valve seat 19 Dustproof
ring
33 Valve seat 47 Seat
6 Valve rod 20 O-ring 34 valve disk 48 Bolt
7 Pivot ring 21 Gland packing 35 Gland 49 Pressure guage
8 Guide bushing 22 Pivot ring 36 screw 50 Pressure Joint
9 O-ring 23 Plunger 37 Adjusting bolt 51 Pressure nut
10 Valve cover 24 O-ring 38 Valve body 52 damper
11 Hexagon bolt 25 Pressing ring 39 Guid rod 53 Pad
12 Out sleeve 26 O-ring 40 Disc spring 54 O-ring
13 Disc spring 27 Reinforcing
mat
41 Cone valve 55 Pump head
casing
14 Spring plate 28 valve spring 42 O-ring

3
c. Pressure regulator Valve
The function of the valve is mainly constant pressure overflow, so that the
pressure in the water system is kept in the adjusting value. The valve is used to protect
the high pressure water system from overload, and the valve is closed and used as the
safety valve at this time. When the high pressure water system is overloaded, open the
valve to let the high pressure water flow out.
Adjustment methoud: Use a wrench to adjust the nut ( Part no. 15) in the valve.
Moving clock wise, the pressure turns larger. Moving counterclockwise, the pressure
turns smaller.
d. Safety valve:
The pump is equipped with a spring-loaded safety valve, that is pre-adjusted to
the maximum rated working pressure of the complete set of plungers. When the
system pressure in the pump exceeds this pressure, the valve trips and bleeds to
protect the systems.
Pump Insallation
1. Please check the pump carefully and make sure everything is in good condition
before installation. The pump should be placed horizontally and correct the levelness
with pad iron, then firmly fastened with bolts. If not in one horizontal level, do not tight
it.
2. The pump requires firm installation when working together with other machinery. In
addition to it, the base should be also need to be kept in the horizontal level, when the
pump unit as the fixed machinery.
3. To reduce the pipe loss, the water inlet pipe of the pump should be as short as
possible, the max length should not exceed 6m. Please use suitable pipe dimensions to
isolate the mechanical vibration.
The suction pipe diameter of the pump should be equal or bigger than the pump
inlet diameter. In order to ensure the reliable operation of the pump, the inlet pressure
should be about 0.06-0.33MPa, the flow rate is 1.5-2 times of output flow.
4. Please leave some spaces around the pump to replace the wearing parts and
lubricants.
5. Pump base mounting dimensions(mm)

4
Pump Lubrication
The pump drive end is splash lubrication and the crankcase oil storage of about 12
liters. When filling oils, remove the vent cap and fill oils through the oil hole. The
Crankcase lubricating oil should be 15W/40CD at an ambient temperature of 15 ℃~
40 ℃, 15W/3CD at an ambient temperature of 5 ℃~ 15 ℃.
Please check the oil level at regular time to keep the oil at the required level. In
winter, please make the pump run more than 20 minutes without loads. After the oil
temperature rising, step up the pressure to the rated value.
Pump operation
a. Before operation:
(1) Before starting the new pump, please make sure every bolt and nut is tight ,
especially the pump head.
(2) For the long-term stopped pump, please check the main components before
starting:
Clean the rust preventing oil in the case, check if the crosshead, connecting rod,
drive shaft, driven shaft and other parts have rusts or scratches. If available, please
polish the parts with sand polishing cloth and clean up with cloth.
If the case is not clean (due to the environment), please clean the case completely
and then filled with new lubricating oil to prevent the power end parts from being
damaged.
Please check if the seal parts are in good condition and replace the damaged ones.
After checking, please replace the serious corrosion parts and make sure all the
threaded connection is tightened.
(3) When operate the new pump or pump with longer stopped time, please rotate
the shaft to check if the rotator parts are flexible.
Please pay special attention to the shaft in the power end, the direction of
rotation must be consistent with the rotation plate. Otherwise the corss head would be

5
damaged badly.
(4) Before starting, turn on all valves on the inlet and outlet pipes for preparation
for no-load start.
(5) Before starting, please make sure the inlet and outlet pipe fittings are
tightened, to prevent the cavitation caused by air.
(6) Before starting, fill the required lubricating oil to the fixed oil level in the case.
b. Starting:
(1) Starting the motor
(2) No-load start, so that the liquid from the pump outlet spout, so that all the air
can be discharged from the hydraulic end to avoid cavitation.
(3) The pump that operates normally without loads could run under pressure. The
pressure process should be carried out slowly. In the process, stop to check the pump if
any abnormal sound and vibration.
(4) Please check if the temperature of stuffing box, case and other parts rise
sharply. The general oil temperature shall not exceed 80 ℃.
(5) Please check the operation condition and plunger seals at all times. It is normal
that the plunger surface with water droplets and a small leak of the stuffing box. While
the large leak will affect the normal establishment of the system pressure and need to
replace new parts.
(6) Caution: Do not stand in the front of the running pump head to avoid personal
injury from an accident.
C. Stop
Before stopping the electric motor, open the pressure regulator to release the
pump pressure to zero. Then remove the pressure connector.
If the pump would be stopped for a long time, empty the oil while the oil is
still hot. Open the case, rinse the tank with a flushing oil and coated with rust
preventing oil, apply grease on the plunger and intermediate rod to form a
lubricating layer.
Loosen all covers in the system and valves to make sure all liquid in the system
flows out.
While because the inlet valve and the drain valve between the chamber is a
sealing space, it could’t be emptied with the above steps. So please make the
pump run a short time after the fluid end empty, to exhaust all liquid. Please
make sure that pressure regulating valve, relief valve, safety valve, etc. are

6
fully open in the system, to prevent the pump from running under pressure
without liquid, which could damage the pump.
Note: Due to the low ambient temperature in winter, please remember to run
with this method to protect the pump head from freezing.
Pump operation
(1) Check the oil level before running. The oil must be replace after 50 hours of the first
operation. After that, oil will be renewed for about 200 hours each time.
(2) All the bolts of the pump must be tightened.
(3) During the operation, the lubricating oil’s temperature should not be more than
70 ℃, and the medium’s temperature should not be higher than 55 ℃.
(4) Replace the oil with the hot crankcase and empty the old oil. If there is iron solids in
the case, use magnets to clean up and plug oil hole. Then fill the new oil through the
oul hole (oil type and quantity are as the regulation). Too much oil will increase the
temperature of oil because of too much resistance in oil.
(5) The oil should be emptied at least once a year, and wash the crankcase with the
cleaning oil, then inject the new oil.
(6) Before changing the oil, check the water leakage and oil spilling, the check all seal
rings and packing seals, especially the seals for the sealing rods.
(7) Ensure the threaded connection between the plunger and the middle rod must be
tightened before running.
(8) The leakage of the intake and draining valve in the fluid end will reduce the flow of
the pump. So when the pump stops for a long time, it should be removed for
inspection. Check the valve plate, the valve seat, the O seal ring on the valve seat, and
enter the drain valve spring to see if they are worn.
(9) The bolts on the packing box and intake/draining valve must be symmetrical when
they are fastened.
(10) Stop the pump to check once any abnormal sound and vibration during the normal
operation.
(11) The safety valve has been adjusted in the factory. Please do not disassemble or
loosen the valve without authorization.

7
Failure & Reasons
Code Failure
A The capacity is not enough
B Discharge pressure could not reach the set value
C Noise
D The power end casing is heated
E The pump could not pump water
F Oil leakage of the middle rod at the power end
G Pressure gauge indicates abnormal
H Pressure regulator is unstable
I Water Leakage in the stuffing box
NO. Reason A B C D E F G H I
1 The valves in the sution
pipe don’t open
√√√
2 Blocking in suction line √√√√
3 Water pressure is too
low
√√√
4 There is a crack in the
head of the liquid end
pump.
√√
5 Inlet pipeline is broken
or lax connection
√√√√
6 O-ring or dustproof ring
broken
√
7 Pressure regulator valve
is not tight
√
8 Pressure regulator is
not stable or pressure
gauge damper is not
open.
√√
9 The crankcase is
flooded.
√√
10
Connecting rod failure
or the bearing is stuck.
√√
11 The oil level is too high √√
12 Unspecified type of
lubricating oil in
crankcase。
√√
13 The pump head or
liquid end leak
√√√√
14 The oil seal of the
middle rod is damaged.
√√

8
15 The pressure regulating
valve is jammed
√
16 Pressure spring stuck √
17 Intake/draining valve is
jammed
√√
18 Pressure regulator valve
fails
√√√
19 The nozzle diameter is
too large
√
20 The nozzle diameter is
too small
√√
21 The packing seal is
damaged
√
Table of contents
Other MST Water Pump manuals
Popular Water Pump manuals by other brands

Draper
Draper 16128 manual
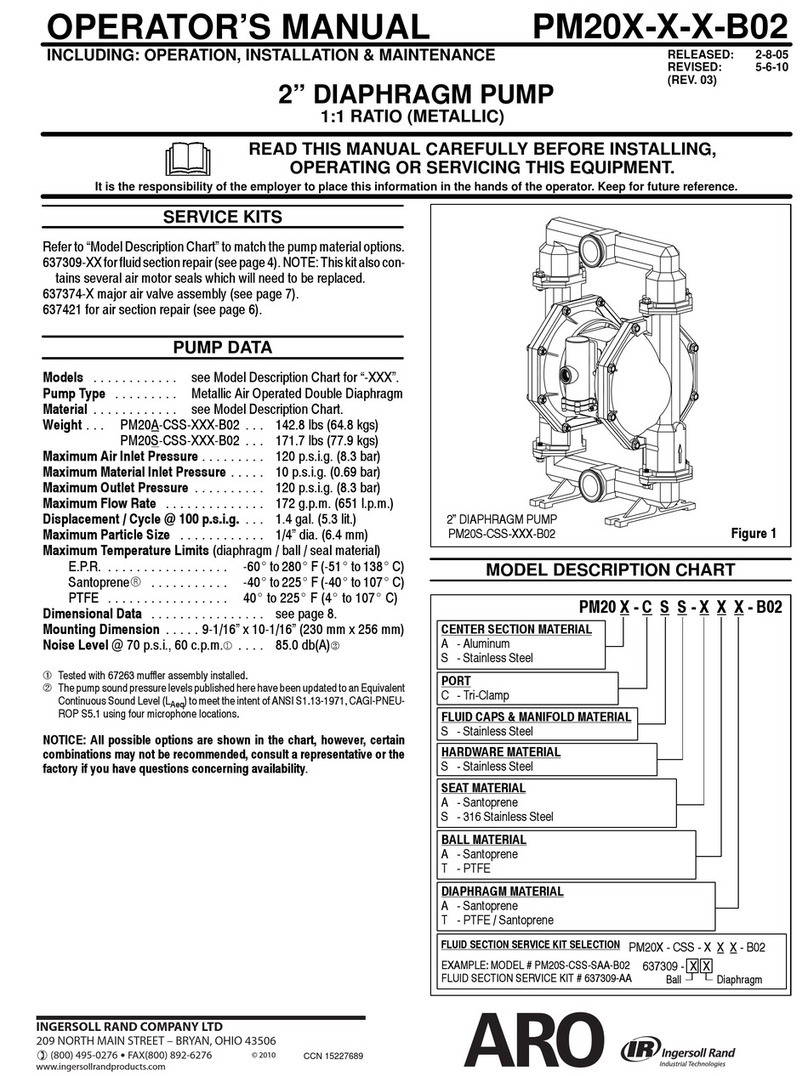
Ingersoll-Rand
Ingersoll-Rand PM20X-X-X-B02 Operator's manual
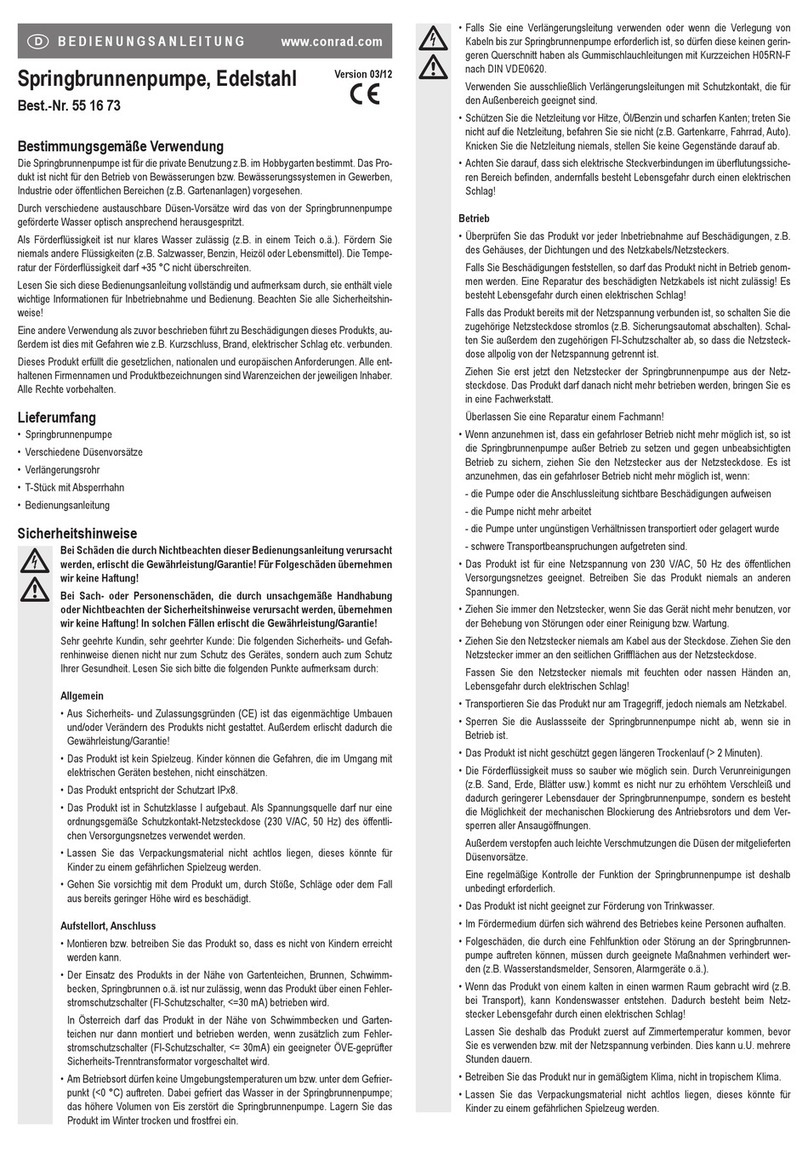
Conrad
Conrad 55 16 73 operating instructions
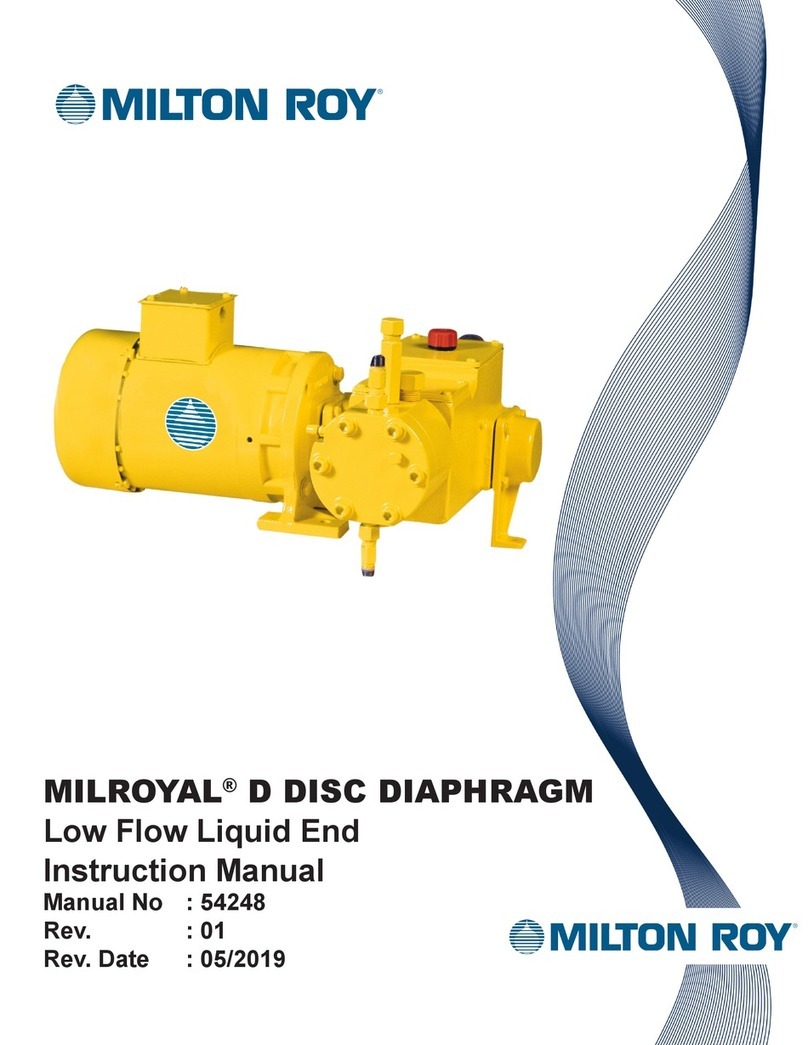
Milton Roy
Milton Roy MILROYAL D instruction manual
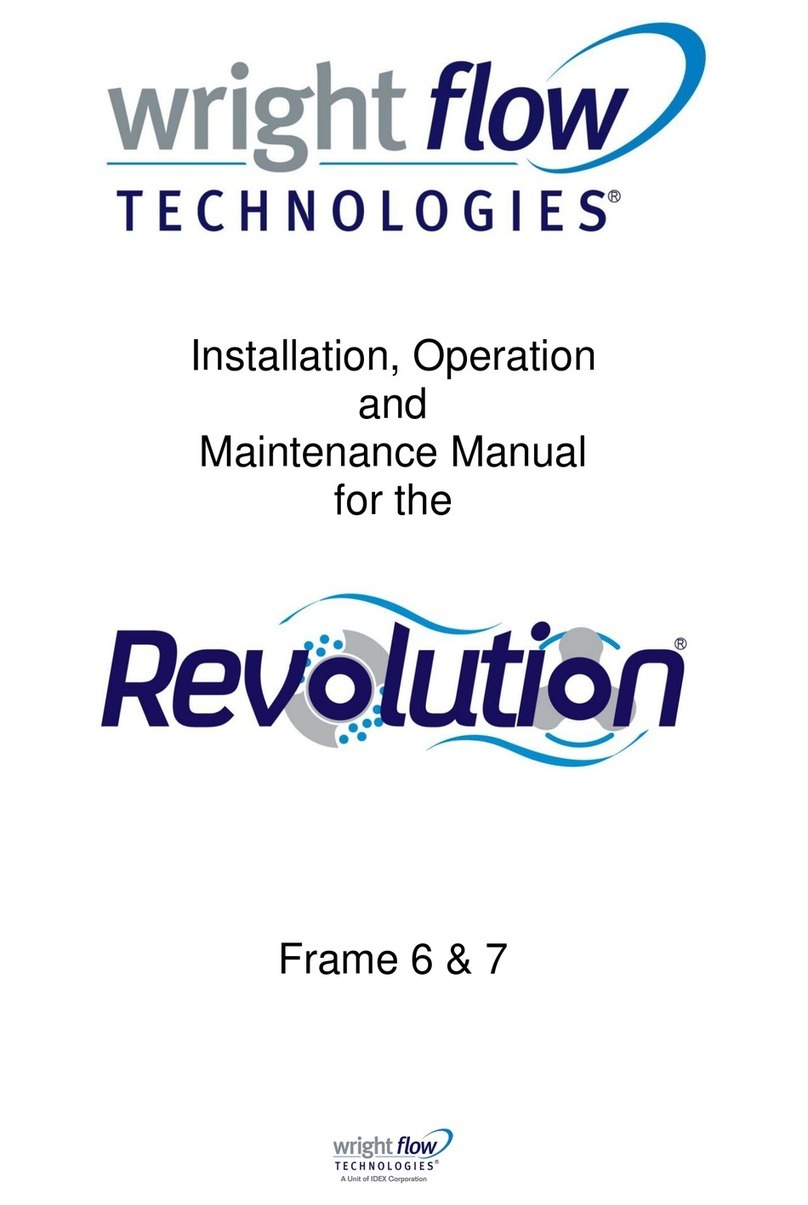
Wright Flow Technologies
Wright Flow Technologies Revolution R0150X Installation, operation and maintenance manual

AeroBed
AeroBed 103H-AU instruction manual

Rocket Medical
Rocket Medical CRAFT Operator's guide
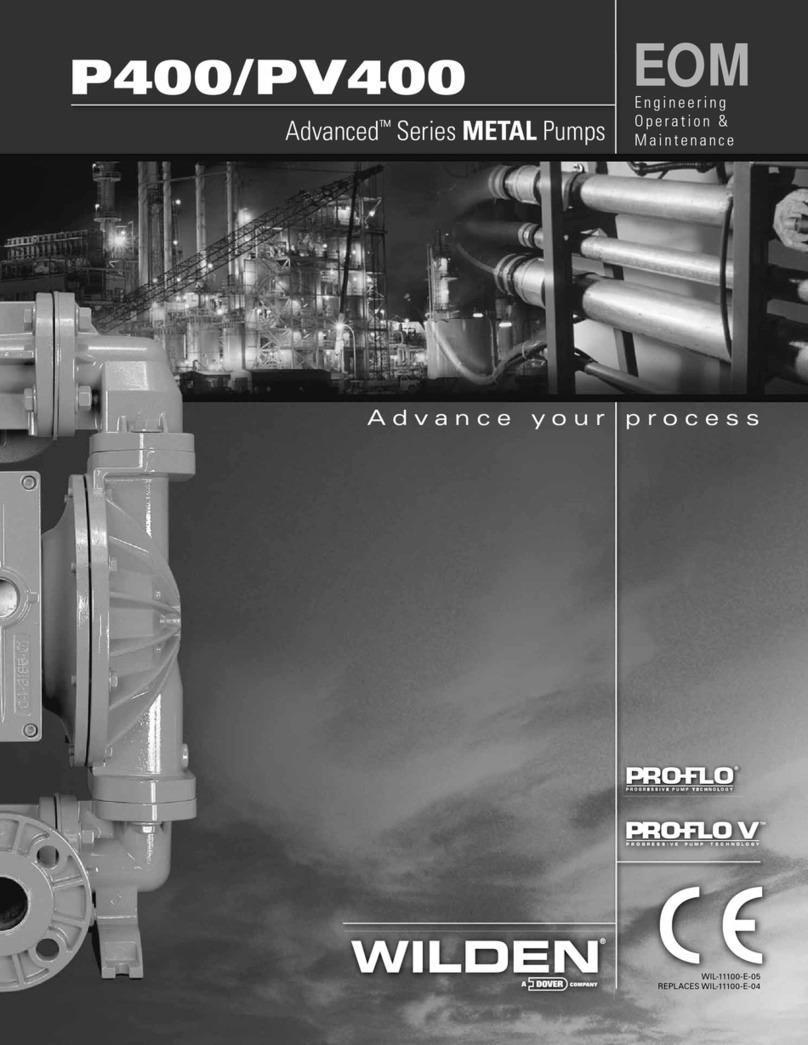
Dover
Dover Wilden Advanced Series Engineering, operation & maintenance
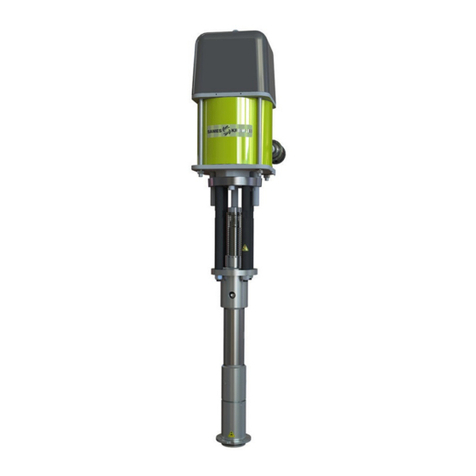
SAMES KREMLIN
SAMES KREMLIN REXSON SH715 user manual
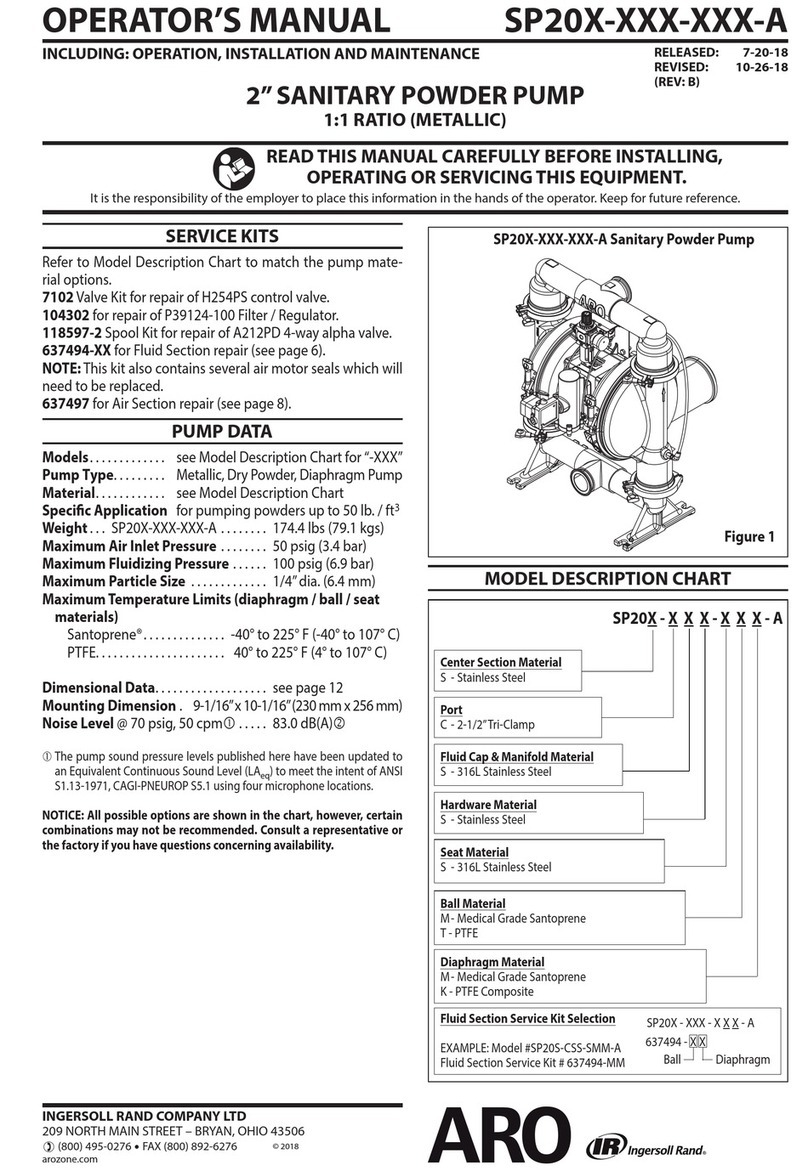
Ingersoll-Rand
Ingersoll-Rand ARO SP20 Series Operator's manual

Wilo
Wilo SiClean Comfort Series Installation and operating instructions

KSB
KSB Sewatec Installation & operating manual