MST ZW Instruction Manual


Please carefully readthe operation instructionsbefore use ofthe product.
Operation installation
ZW Self-Priming Pump
Z W

CONTENTS
General
Application Range
Model meaning
Structure Specification
Brief diagram of structure
Pump installation
Use of the pump
Maintenance, disassembly and assembly
Failures causes and troubleshooting
01
01
01
02
03
04
05
06
07
08
09
03
标准参数
Standerd Specifications
性能曲线图
Installing Dimensions Drawing
Performance Curve

01
ZW SELF-PRIMING PUMP
ZW ISO
Y
YB
150 ZW 180 - 30
(m)
3
(m /h)
(mm)
MODEL MEANING
3
Means the flow (m /h)
Means a self-suction pump
Means the suction inlet aperture(mm)
self-priming pump is an energy saving pump
designed with ISO international standard and developed thr-
ough absorbing and improving the related technical data both
and abroad and belongs to self-priming centri-
fugal pump and uses the mechanical seal of a ceramic ring
so as to resist any sandy liquid to go into the sealing face,
preventing it from getting scratched. This pump holds the
advantages of a compact structure, easy operation, stable
movement, easy maintenance, high efficiency, long duration
and strong self-suction capacity and, as no foot valve is ne-
eded to be mounted on the pipeline and only a certain am-
ount of leading liquid is required to be filled into the pump
before work, improves the work condition while simplifying
the pipeline system.
This pump can be equipped with either Y series common
motor or YB series explosion-proof one upon the different
surroundings of use.
1
2
3
4
1.Widely used in environmental protection, aquaculture
2.This pump, when mounted with
a
shaking
arm
shower, can
have the water burst into air and then scattered
in a thin
drop for spraying, useful to a farm, nursery, orchard and
tee plantation.
3.Suitable for pure water and liquid include many solid particles
4.This pump can work together with a pressure filter
of
any
model and specification and is the most ideal matching
pump to send pulpy materials
to
the s
aid filter for pressure
filtering.
domestic
Means the head (m)
广泛应用于市政排污工程、河塘养殖、轻工、造纸、
纺织、食品、化工、电业、纤维、浆料和混合悬浮
等化工介质领域
即可适用于清水,又可以吸排含有大量固体颗粒和
长纤维杂志液体。介质重度不超过1240kg/m3
light industry, paper making, textile industry, food,
chemical engineering, electric power, fiber, slurry,
suspension and so on
介质PH值铸铁材质6-9, 不锈钢2-13
or continuous fiber and unit weight of the medium should not
more tham 1240kg/m3. Medium PH if cast iron: 6-9 Stainless
steel: 2-13

02
70
This pump casing consists of a suck-in room, a liquid
storing room, a scroll room, a liquid back hole, an air-liquid
separating room etc. and holds an axially-liquid-back structure.
After the pump is normally started, the impeller sucks in the
all liquid inside of the suck-in room and the air inside of
the pipeline and gets them completely mixed inside of it,
then, under the action of the centrifugal force, the liquid,
carrying the air, flows towards the outer edge of the scroll
room and, on the outer edge of the impeller, a white foam
band of a certain thickness and a quickly rotating liquid ring
are formed. The air-liquid mixture gets into the air-liquid
separating room through the expanding pipe and, as the flow
-rate is abruptly lowered thereafter, the lighter air is separ-
ated from the mixture and rises through the vomit port of
the pump casing and is exhausted therefrom. The liquid with
the air off returns to the liquid storing room and gets into
the impeller again through the liquid back hole, where it is
mixed again with the air sucked in from the suck-in pipe-
line and, under the action of the quickly rotating impeller,
flows towards the outer edge of the impeller again , al-
ong with the repeated process, the air in the suck-in pipeline
is continually reduced till being sucked up, the self-suction
process ends and the pump gets into the normal work. This
unique exhaust capacity makes the pump able to transport
the air-contained liquid without a foot valve mounted and
of a good cabin cleaning function when used on an oil ship.
There is a cooling room on the bottom of the bearing
body with some pumps and, when the bearing body's temp-
erature rise is over 70oC with the bearing heated, the cool-
ing liquid can be injected in through any one of the cooling
liquid unions in the cooling room for cycled cooling. The
sealing mechanism inside of the pump used to prevent the
liquid from leaking from the high pressure area to the low
one is the front and rear seal rings, the front ring is mount-
ed on the pump casing and the r ear one on the bearing body.
When the seal ring gets worn out to a certain extent after a
long time work of the pump and thus affecting both effici-
ency and self-suction property of it, it should be replaced.
ZW SELF-PRIMING PUMP

1
8
2
9
4
11
3
10
5
12
6
13
7
14
Clutch
Inlet seat
Pump shaft
Front seal ring
Bearing
Impeller
Mechanical seal
Rear cover
Bearing body
Baffle ring
Pump casing
Liquid filling hole
Outlet seat
Liquid back hole
BRIEF
03
ZX SERIES SELF-PRIMING PUMP

238
476
714
952
1190
1428
GPM
32.8
65.6
98.4
131.2
164
H
m
Feet
ZW SELF-PRIMING PUMP
Performance Curve
性能曲线图
04

suction flange
discharge flange
ZW SELF-PRIMING PUMP
安装尺寸图 INSTALLING DIMENSIONS DRAWING
05

06
PUMP INSTALLATION
1
2
3
4
A 3.5
B
C
2-3
D
5
6
7
8
3-4
70
9
12 M12 1.5
1. With the shafts of both pump and motor linked in actu
tion, pay attention to the concentricity between the pump
shaft and the motor's output; and carefully mount and
calibrate the pump as which will leave a bigger affection
to the running stability and duration of it.
2. Fasten the nut on the pump's clutch, or the impeller may
be made easily movable to cause a mechanical failure.
3. Have the pump inlet higher than the central line of the
pump shaft so as to have a certain volume of liquid kept
inside of the pump to get a better self-suction capacity
and prevent the mechanical seal from drying friction.
4. Cautions for the installation of the suck-in pipeline:
A.The installation height of the suck-in port shall not be
over 3.5m and, if the condition is allowed, lower than
the lowest water storing surface as can as possible and
make the length of the suck-in pipe as short as possible
and the elbow less mounted so as to shorten the self-su-
ction time and enhance the self-suction function.
B. The valve, flange etc. inside of the suck-in pipeline
shall be prevented from air or liquid leaking, that means
no air-leaking is allowed inside of it.
C. To prevent any solid etc. impurities from sucking into
the pump, a filter should be set on the suck-in pipeline,
with the effective filtering area 2-3 times the section of
the pipeline and the filter checked in a periodic time.
D. Get both suck-in and vomiting pipelines a stand of
their own and do not let the pump bearing any pipeline.
5. During installation of the pump, make the static ground-
ing resistance of it and the pipeline up to the set require-
ment.
6. Check if there is stones, iron sand or any other impurity
inside of the pump casing and the pipeline in installation.
7. Take a final check after the unit actually runs for 3-4h
and it
is
deemed for the installation to have been
well
done
if non-bad condition. Check the bearing temperature
during trial, which shall not be over 70 .
8. For the bearing
body
of t
he p
ump s
et w
ith a cooling ro
om ,
use a rubber or plastic pipe of a 12mm diameter inner
hole to fit the cooling
liquid union, the thread size is
M12x1.5.
9. When the pump can not successfully exhaust the air du-
ring the self-suction process due to an one-way valve
which is mounted on the outlet pipeline of it, set a small
exhaust pipe and valve at the outlet.
ZW SELF-PRIMING PUMP

USE OF THE PUMP
Preparations and checks prior to starting
1. According to the running states, this series self-suction
pumps are lubricated with quality calcium-based grease
and 10# engine oil separately. For those lubricated with
grease, fill grease into the bearing box in a periodic time
and, for those with engine oil, fill it fully when the oil
level is insufficient.
2. Check if the stored liquid inside of the pump casing is
above the upper edge of the impeller and, if not, prime li-
quid directly from the filling port on the casing. Do not
start the pump in case of an insufficient stored liquid, or
the pump would not work normally and the mechanical
seal would be easily damaged.
3. Check if the moving parts of the pump are jammed or
collided; if the foot on the pump bottom and the nuts on
the joints are loose; check the concentricity or the para-
llelism between the shafts of both pump and motor; check
if there is air-leaking with the inlet pipeline and settle it if
any; open the valve on the suck-in pipeline and slightly
open (not fully) the outlet control valve.
Start and operation
1. Pay attention to the pump shaft to see if it moves in the
correct direction when to start the self-suction pump; and
if there is abnormal sounds and vibration when it moves.
2. Pay attention to the readings on both pressure gauge and
vacuum meter, when the indications of which get stable
after a periodic time fluctuation after the pump is started,
that means liquid has been primed into the pump and the
pump gets into the normal liquid transportation. Before
the pump gets into the normal liquid transportation, e.g.
During the self-suction process, pay special attention to
the temperature rise of the liquid and stop the pump to
check the cause if this process is too long and the tem-
perature is so caused too high.
3. Temporarily stop the pump in case of a difficult self-su-
ction caused due to too high liquid temperature and make
it lower by means of the back flow into the pump of the
liquid in the vomiting pipeline or supplementing liquid
directly from the filling port on the pump casing, then
start the pump again.
4. It is possible for an air erosion to occur with the pump
that causes a severe vibration and noise during the work
of the pump and the air erosion occurs with two causes:
one is too quick flow rate in the inlet pipe and the other
is too high suction travel. For the former, adjust the out-
let control valve, raise the reading on the pressure gauge
and remove it in case of block-up in the inlet pipeline; for
the latter, properly lower the pump's installation height.
1
10
2
3
()
1
2
3
4
07
ZW SELF-PRIMING PUMP

08
5
()
1
2
3
O
()
O
A
B
C
D
O()
MAINTENANCE, DISASSEMBLY AND ASSEMBLY OF THE PUMP
5. When the pump is stopped because of something during
work and started again, slightly (not fully) open the outlet
control valve. This is benefit for the air to be exhaus-ted
on-time from the vomiting port during the self-suction pr-
ocess and also ensures the pump is started with a lighter
load. Meanwhile, pay attention to checking if there is a
leak from the pipeline system.
Stop
1. First close the valve on the vomiting pipeline.
2. Have the pump stopped running.
3. In cold seasons, drain out the liquid stored inside of the
pump casing and the water inside of the bearing's cooling
chamber completely to prevent any parts from being fro-
zen to crack.
This pump features a simple and reliable structure, dur-
ability and is generally unnecessary to be disassembled often
for maintenance if working normally. Troubleshoot it in case
of a failure.
Cautions at maintenance
When the rolling bearing and both front and rear seal
rings are worn out to a certain degree after a long time run-
ning of the pump, replace them; the mechanical seal does
not need to be removed for a check provided that no liquid
leakwith it while does when there is a serious leak from the
leaking port on the lower side of the bearing. Take care of
the mechanical seal during disassembly and assembly, clean
the fitted face, properly keep the mirrors of both static and
dynamic rings and do not knock on them and get them co-
llided, as the cause for the leaking of it is mainly at the
burrs on the frictional pair mirrors. To repair it, grind the
mirrors to have it recovered. Another cause for the mech-
anical seal to leak is the O -type rubber seal ring (or
buffering gasket) improperly mounted or deformed or aged,
then adjust or replace it.
Pump disassembly and assembly sequences
A. Remove the motor or take out the clutch.
B. Remove the bearing assembly, check the radial space
between the impeller and the front oral ring and check
if the impeller nut is loose.
C. Screw out the impeller nut, pull out the impeller and c heck
the radial space between the impeller and the rear seal ring.
D. Loosen the fixing screw on the mechanical seal, pull
-
out the dynamic ring and check the fitting state bet
end-faces of both static and dynamic rings and
ween the
the sealing state of the O -type seal ring (or the bu-
ffering gasket).
ZW SELF-PRIMING PUMP

E
F
G
E. Screw out the fixing nut on the clutch and pull out
the clutch.
F. Remove the end cover on the bearing to remove both
pump shaft and bearing.
G. Take reversed sequences for assembly.
1. No waterout of pump
2. Bigger noiseand vibration
3. Insufficient water-out
quantity
4. Toobig consumption of shaft
power
a. No orinsufficient liquid storedinside of pump
casing
b. Airleaks from suck-inpipeline
c. Tooslow speed
d. Toohigh suction travel or too long suck-in
pipeline
e. Toosevere leakage from mechanical seal
f. Airinside of suck-inpipeline unable tobe
exhausted from theoutlet
a. Foot unstable
b. Pump shaftbent
c. Steam erosion
d. Bearing seriouslyworn out
e. Impurities existinside of inletpipeline
a. Impurities getinto suck-in pipeor impeller geat
blocked up
b. Tooslow speed
c. Impeller orimpeller seal seriouslyworn out
a. Tooheavy flow
b. Tooquick speed
c. Pump shaftbent or impellerjammed or collided
d. The geatinside of thepump blocked-up orjammed
a. Raise theoutlet pressure
b. Properly lowerit
c. Replace orcorrect
d. Get ridof blocking matters
a. Get ridof impurities
b. Adjustthe speed tothe rated one
c. Replace oralring
a. Solidify it
b. Replace orcorrect it
c. Adjustworking conditions
d. Replace it
e. Get ridof impurities
a. fill sufficientliquid
b. check andsettle the airleak
c. adjust thespeed
d. lower suctiontravel or shortensuck-in pipeline
e. repair orreplace it
f. open theoutlet valve tolet air out
Failure Causes Troubleshooting
09
ZW SELF-PRIMING PUMP

As we are constantly endeavouring to improve the performance of our equipment.
The company reserves the right to make alteration from time to time and equipment differ from that detailed in this brochure.

Table of contents
Other MST Water Pump manuals
Popular Water Pump manuals by other brands
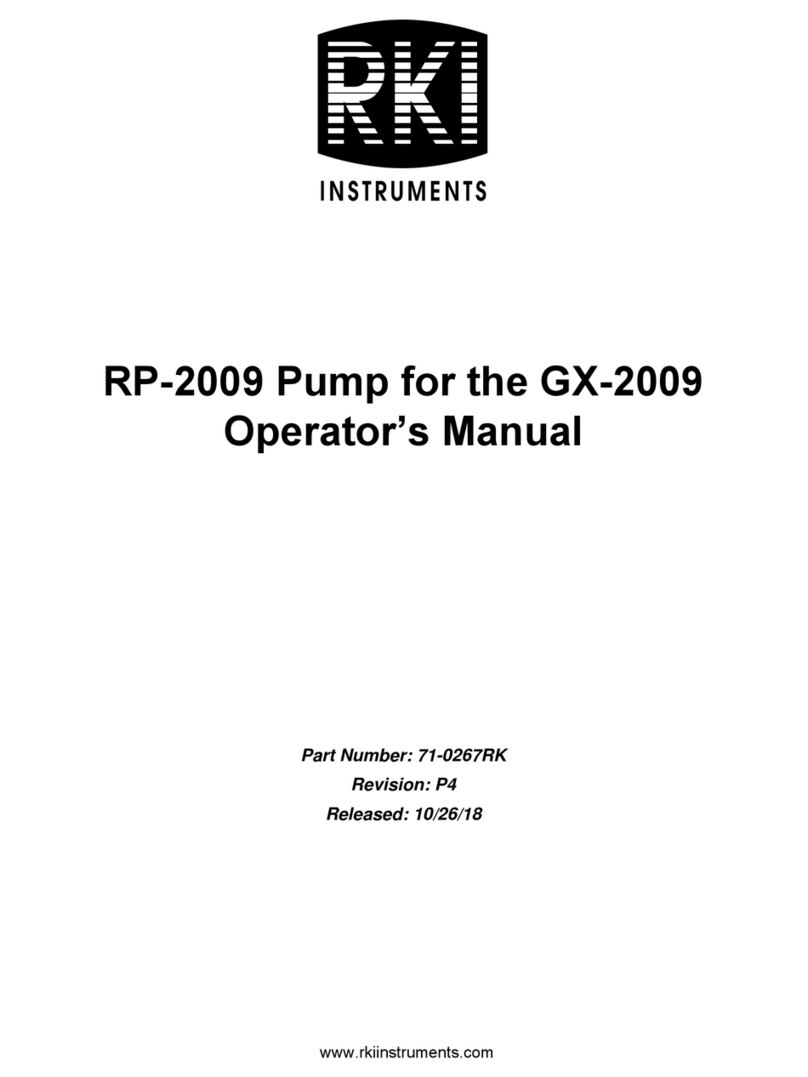
RKI Instruments
RKI Instruments RP-2009 Operator's manual
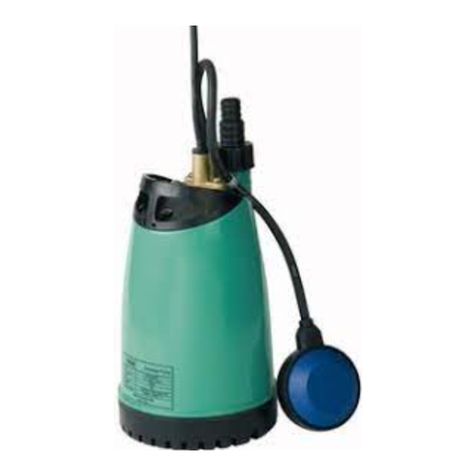
Wilo
Wilo Drain TM 25/6 A Installation and operating instructions

Ozito
Ozito APR-012 instruction manual

Hilti
Hilti DWP 10 Original instructions for use
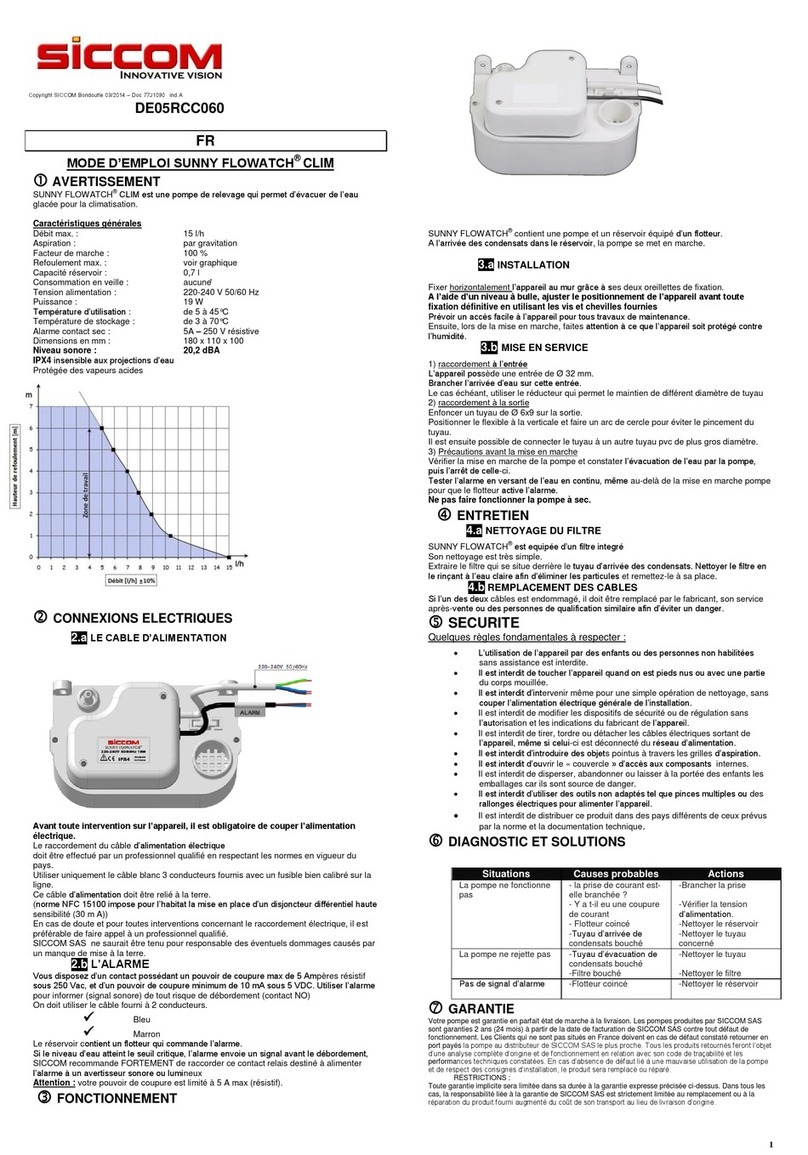
Siccom
Siccom SUNNY FLOWATCH CLIM DE05RCC060 instruction manual

Jefferson
Jefferson JEFSUBPDW266-95 user manual

Abbott
Abbott PLUM A + System Operating Manual
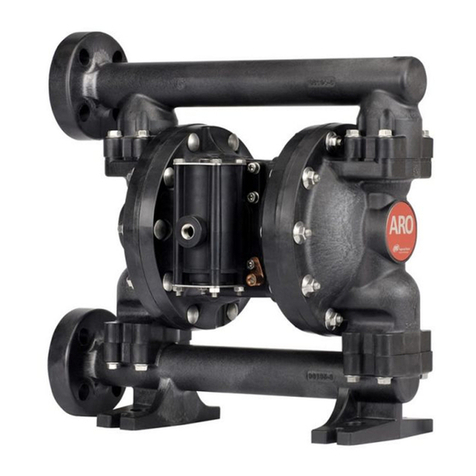
Ingersoll-Rand
Ingersoll-Rand ARO PD10E Series Operator's manual

Pentair Pool Products
Pentair Pool Products HYDROMATIC S4BX Installation and service manual

Oase
Oase Aquarius Universal Classic 600 operating instructions
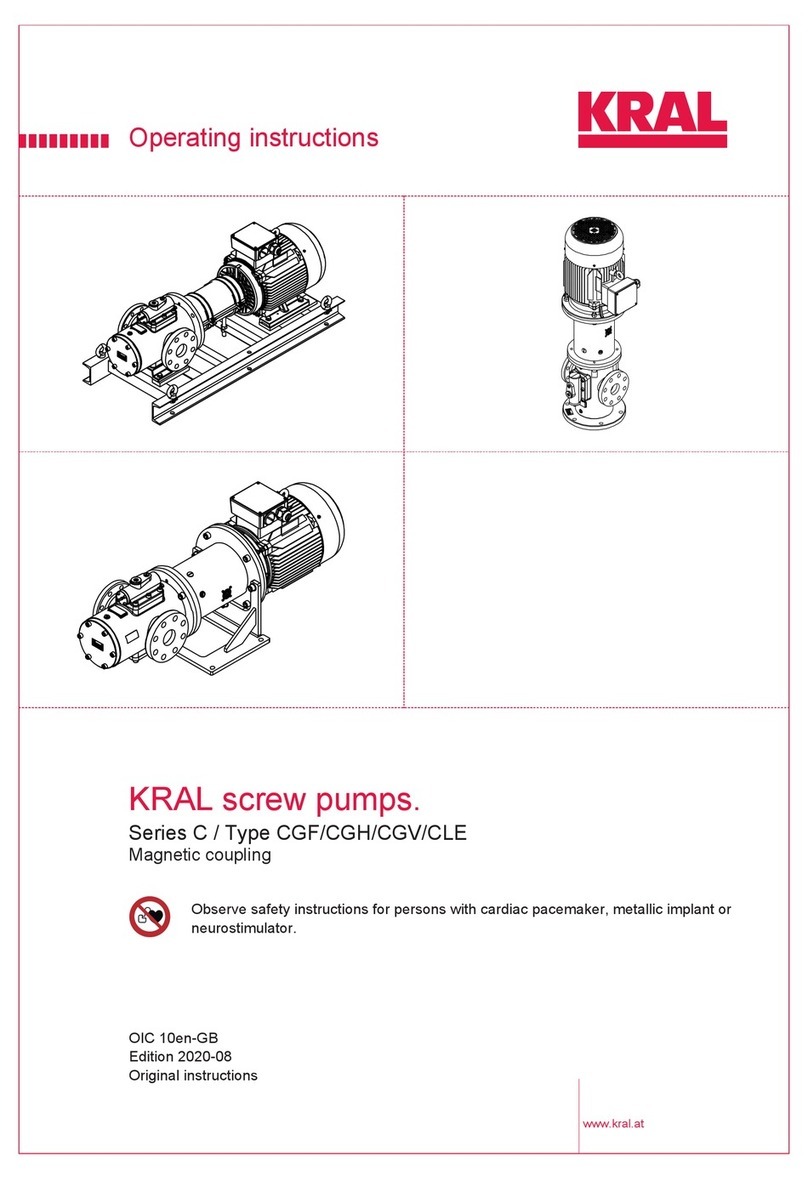
KRAL
KRAL Series C operating instructions

Johnson Pump
Johnson Pump PUMProtector Inlet Strainer instruction manual