National Lab PCGE Series Operating instructions

1
Recirculating chillers for liquids
PCGE 11 - PCGE 3300
OCGE 31 - OCGE 240
PCGEZ 08 - PCGEZ 480
English Operating and maintenance manual
Deutsch Bedienungs- und Wartungsanleitung
National Lab GmbH
Grambeker Weg 157, D-23879 Moelln
Phone: +49 (0)45 42 / 84 91 10
Fax: +49 (0)45 42 / 84 91 11
E-MAIL: SERVICE@NATIONALLAB.COM

2
TABLE OF CONTENTS
1. GENERAL USER AND MAINTENANCE MANUAL ......................................................................3
1.1. HOW TOUSE THIS MANUAL................................................................................................3
1.2. GENERAL DESCRIPTIONS/INTENDED USE ............................................................................3
2. GENERAL SAFETY INSTRUCTIONS........................................................................................3
3. DESCRIPTION OF THE CHILLER, COMPONENTS AND OPTIONS.............................................5
3.1 DESCRIPTION...................................................................................................................5
3.2 REFRIGERANT CIRCUIT......................................................................................................5
3.2.1 STANDARDCOMPONENTS USED IN THE CHILLER..............................................................................5
3.2.2 OPTIONS REFRIGERATION CIRCUIT ..............................................................................................6
3.3 COOLING MEDIUM CIRCUIT (CONSUMERCIRCUIT) ...............................................................6
3.3.1 STANDARDCOMPONENTS USED IN THE CHILLER..............................................................................6
3.3.2 OPTIONS HYDRAULIC CIRCUIT.....................................................................................................7
3.3.3 SINGLE-CIRCUIT SYSTEM WITH TANK (STANDARD)...........................................................................7
3.3.4 SINGLE-CIRCUIT SYSTEM WITHOUT TANK........................................................................................8
3.4 ELECTRIC CIRCUIT............................................................................................................8
3.4.1 STANDARDCOMPONENTS USED IN THE CHILLER..............................................................................8
3.4.2 OPTIONS ELECTRIC CIRCUIT........................................................................................................9
3.5 HOUSING .........................................................................................................................9
4. TRANSPORT/ PACKAGING/ STORAGE................................................................................11
4.1 REMOVING THE PACKAGING AND HANDLINGTHE CHILLER .................................................. 11
4.2 DISPOSALOF PACKAGINGMATERIALS............................................................................... 11
4.3 STORAGE ....................................................................................................................... 11
5. LOCATION AND INSTALLATION .........................................................................................12
5.1 CHOOSING A LOCATION................................................................................................... 12
5.2 ASSEMBLY (CONNECTIONS) .............................................................................................13
5.2.1 CONNECTIONTO THE REFRIGERANTCIRCUIT (CONSUMER CIRCUIT) ................................................13
5.2.2 CONNECTIONTO THE ELECTRICITY MAINS.....................................................................................14
6. OPERATION........................................................................................................................15
6.1 CHECK LIST FORTHE INITIAL START-UP OF WATERRECIRCULATING CHILLERS..................... 15
6.1.1 WATER REQUIREMENTS................................................................................................................15
6.1.2 CHECKLIST FOR PCGE11 TO PCGE 3300........................................................................................15
6.2 CHECKLIST FOR STARTING UP OIL RECIRCULATINGCHILLERS............................................. 17
6.2.1 OIL REQUIREMENTS.....................................................................................................................17
6.2.2 CHECKLISTE FOR OCGE 31 TO OCGE240.......................................................................................17
6.3 CHECK LIST FORCOMMISSIONING GLYCOL RECIRCULATING CHILLERS ................................18
6.3.1 REQUIREMENTS FOR THE WATER-GLYCOLMIXTURE........................................................................18
6.3.2 CHECKLIST FOR PCGEZ 08 TO PCGEZ480......................................................................................18
6.4 OPERATINGSETTINGS FOR THE ELECTRONIC CONTROLLER................................................. 20
6.4.1 CONTROLLER TYPE ”AÜ(PCGE11 TO PCGE 28; PCGEZ 08) ...............................................................21
6.4.2 CONTROLLER TYPE ”BÜ(PCGE31 TO PCGE 520; OCGE 31 TO OCGE240; PCGEZ37 TO PCGEZ 180) ....22
6.4.3 CONTROLLER TYPE ”CÜ(PCGE590 TO PCGE 3300;PCGEZ240 TO PCGEZ480)...................................22
6.5 SHUTTING DOWNTHE CHILLER ........................................................................................ 23
6.5.1 SWITCHINGON/OFF IN DAILYOPERATION.....................................................................................23
6.5.2 TEMPORARY DECOMMISSIONING ..................................................................................................24
6.5.3 DECOMMISSIONINGFOR TRANSPORT PURPOSES............................................................................24
7. MAINTENANCE ...................................................................................................................24
7.1 MAINTENANCE OPERATIONS.............................................................................................24
7.2 DAILY RECORD ............................................................................................................... 25
8. DISPOSAL ..........................................................................................................................26
9. MALFUNCTIONS/TROUBLESHOOTING................................................................................26
9.1 POSSIBLE ALARM SIGNALS AND THEIR RECTIFICATION....................................................... 27
9.1.1 CONTROLLER TYPE ”AÜ(PCGE11 TO PCGE 28; PCGEZ 08) ...............................................................27
9.1.2 CONTROLLER TYPE ”BÜ(PCGE31 TO PCGE 520; OCGE 31 TO OCGE240; PCGEZ 37 TO PCGEZ 180) .....28
9.1.3 CONTROLLER TYPE ”CÜ(PCGE590 TO PCGE 3300;PCGEZ240 TO PCGEZ480)...................................30
10. FEATURES AND TECHNICAL DATA ......................................................................................64
10.1 TECHNICAL FEATURES..................................................................................................... 64
10.2 PUMP AND TANK CHARACTERISTICS.................................................................................. 65
10.3 COMPONENTS WITH A WEIGHT OF MORE THAN20 KG......................................................... 66
11. DIAGRAMS .........................................................................................................................67
11.1 LEGEND ......................................................................................................................... 67
11.2 WIRING DIAGRAM........................................................................................................... 69
11.3 COOLING HYDRAULIC DIAGRAM..................................................................................... 82
12. REGULATION ON PRESSURE EQUIPMENT...........................................................................93
13. DECLARATION OF CONFORMITY.........................................................................................94
14. PROGRAMMED MAINTENANCE REGISTER.........................................................................945
15. INDIVIDUAL SPECIFICATION...........................................................................................956

3
1. GENERAL USER AND MAINTENANCE MANUAL
1.1. HOW TO USETHIS MANUAL
This operating and maintenance manual is intended for specialist personnel who are responsible for the install ation,
commissioning and operation of cooling water recirculating chillers of the type ProfiCool Genius (PCGE), oil recircu-
lating chillers of the type OilCool Genius (OCGE) and glycol recirculating chillers of the type ProfiCool Genius Zero
(PCGEZ). The term ”chiller’is used asa general name for these appliances.
This operating and maintenance manual is an essential constituent of the chiller. Every user, operator and service
technician is required to carefully read the information and instructions contained in thisoperating and mainte-
nance manual particularly those that affect safety beforetransporting, installing, using, performing any
maintenance on or disposing of the chiller.
The owners and operators of the chiller shall ensure that all work to be carried out on the chiller is only undertaken
by personnel with suitable specialist qualifications.
The operating and maintenance manual is divided into two sections that contain adetailed description ofthe three
type series PCGE, OCGE and PCGEZ, with their respective standards and withadditional information onthe cus-
tomer-specific design and the respective model of your chiller, wherever this differs from the standard model. Here
you will find information such as the circuit diagram for the chiller you have chosen.
1.2. GENERAL DESCRIPTIONS/INTENDED USE
The ProfiCool, OilCool and ProfiCool Zerochillers have been designed for the purpose of keeping acertain quantity
of cooling medium, e.g. water, water-glycol moistureor oil constantly within certain temperature limits (operating
range), with the aid of atechnical cooling process. The most commonly used cooling medium, also called the ”con-
sumer refrigerant’ismains water. This operating manual uses the general term cooling medium. However, the
cooling medium and the materials used in the circuit must be compatible with one another. It is therefore neces-
sary to check and ensure before commissioning that the cooling medium is suitable for the intended purpose.
These chillers are recommended for use in the recirculated chilling of liquids (cooling media) in industrial and com-
mercial applications, particularly in cases where specific and constant temperatures are required, such as in me-
chanical engineering, in the plastics industry, in surface technology and in the laser industry.
Explanation of the product designations PCGE, OCGE and PCGEZ:
PCGE ProfiCool Genius recirculating water chiller
OCGE OilCool Genius recirculating oil chiller
PCGEZ ProfiCool Genius Zero recirculating glycol chiller
2. GENERAL SAFETY INSTRUCTIONS
SYMBOLS USED ONTHE CHILLER OR IN THE MANUAL:
Chiller
Cooling medium inlet
WARNING OF DANGER
Read the instructions carefully, dis-
connect the electricity supply and re-
lease the pressure from any pressur-
ized components before carrying out
any maintenance work on the chiller.
Cooling medium outlet
Direction of rotation for fan/pump
Operating and maintenance manual: warning and hazard symbols
GENERAL WARNING GENERAL HAZARD:
General warning general safety hazard for people and property!
DANGER ELECTRICAL CURRENT:
Danger of an electrical accident occurring while carrying out work on parts of the chiller and the
systems/equipment connected to it while they are connected to the electricity supply!

4
DANGER HOT SURFACES/HIGH TEMPERATURE OF COOLING MEDIUM:
Danger of burns due to high temperatures in the hot parts of the chiller
and/or the cooling media it contains!
DANGER MOVING PARTS:
Danger of injuries due to contact with the moving parts of the chiller!
DANGER EYE INJURIES:
Danger of eye injuries resulting from the use of compressed air or from fluid particles during
cleaning work!
All work connected with the installation, operation and maintenance of the chiller must be performed in accordance
with the instructions contained in the operating and maintenance manual and in compliance with the legal provi-
sions that apply in the country where the device is installed. All cleaning/maintenance work that requires access to
the chiller has to be performed by qualified specialistpersonnel who have been informed of the necessary precau-
tions to be taken. Read the operating and maintenance manual carefully before performing any work on the device.
The chiller has been designed and manufactured in such as wayas to comply with the standards that apply in the
respective country. Should the chiller be used for the incorrect purpose or not in accordance with theoperating and
maintenance manual, the manufacturercannot be held responsible.
THE FOLLOWING POINTS MUST BE OBSERVED BEFORE COMMISSIONINGAND WHILE OPERATING THE CHILLER:
§Familiarize yourself with all the operating controls.
§The chiller may be used solely for the intended purpose.
§Make sure that all the working limits indicated in the operating and maintenance manual are observed.
§Use protective devices to check electricalinsulation. Do not carry out any work on any parts of the equipment
that might be live with wet clothing, hands or feet.
§Check at regular intervals whether the safety and control devices of the chiller are functioning properly.
§Never hit the pipes located on the inside of the chiller with objects of any kind.
§Any maintenance operations not mentioned in the operating and maintenance manual must not be carried out
by personnel without the manufacturer½sprior written authorization if any equipment components are under
pressure.
§Never spill orpour any cooling medium into the environment as this may causedamage to health. Beforethe
chiller is resold, the cooling medium must be drained from the chiller using suitable equipment. Please contact
customer service of the nearest dealer in this connection.
§The side panels of the chiller must not be removed unless this is absolutely necessary. Even if the side panels
are only partially removed, isolate the chillerfrom the electricity supply and affix a sign to the control panel
bearing the warning ”Maintenance work on chiller in progress’. Replace the side panels as quickly aspossible.
§The components of the chiller must not be modified in any way.
§Bypassing the electrical protective devices may result in overloading of the chiller.
The chillers are exclusively designed for cooling the types of cooling medium listed in the following table.
PCGE series: Water with ethylene glycol added as anti-freeze, where necessary. If glycol is used, the mini-
mum limit of 20% and maximum limit of 25% should be observed.
OCGE series: Lubricating or hydraulic oil with aviscosity of 10 cST or higherwith atemperature limit vary-
ing according to the oil type.
PCGEZ series: Water with ethylene glycol added as anti-freeze with aminimum of 20% and amaximum of
25% applying to chillers with a standard configuration.
The maximum operating conditions (temperature of the cooling medium and room temperature) and the permissi-
ble features for the cooling medium are contained in Section 5 of this manual.
When handling liquids intended for aspecial purpose, e.g. health or food applications, please check the
contractually defined technical specifications. Cooling medium with ahigh content of solid matter may
not be used with these chillers.
Possible risks:
CAUTION: The chiller is equipped with a main switch.
The authorized installationtechnician must ensure that the chiller has been connected to the electricity
mains in accordance with the standard EN 60204 and must ensure compliance with all other applicable
national standards.
Fire:
According to European Standard EN 378-2, these chillersmay be equipped with asafety valve fordraining cooling
medium.
The electricity supply must be disconnected in the event of fire. Fire extinguishers or fire extinguishing systems
filled with powder, foam orcarbon dioxide should be used by preference. The chiller may also be cooled with nebu-
lized water. The use of water in large quantitiesmust be avoided because if there is leakage of refrigerant, the re-
sulting chemical reaction no matter how slight may have a corrosive effect.
In any case, it is necessary to reduce the ambient temperature and/or that of the chiller and wait for the tempera-
ture to fall before carrying out any work on the unit.
You are advised to include this device in your Fire Prevention Plan and Factory Safety Plan.

5
Make sure that suitable precautions have been implemented to avoid and combat any possible risks.
In the event of refrigerant leakage:
The refrigerant may lead to asphyxiation if it is inhaled in high concentrations. It is necessary to ensure adequate
ventilation for the room in which the chiller is installed.
Be sure to the read the safety data sheet with the relevant values and warnings.
Excessive pressure on the cooling medium side:
The chiller is equipped with safety devices on the cooling medium side.
These have to be mounted by the installation technician. The installation of any such devices must comply with the
applicable national standards and be carried out in accordance with the limits given in this manual.
Depletion of the ozone layer:
The use of HFC refrigerants, in compliance with Regulation CE/842/2006, reduces damage to the ozone layer and
minimizes the greenhouse effect.
3. DESCRIPTION OF THE CHILLER, COMPONENTS AND OPTIONS
3.1 DESCRIPTION
The chiller is supplied ready for connection. It consists of ahousing, afully hermetically sealed cooling medium cir-
cuit, the refrigerant circuit, the cooling medium circuit and the electrical circuit, including all control and monitoring
devices which are required for fully automatic operation. The selected and usedcooling medium must comply with
environmental standards and the legal provisions.
3.2 REFRIGERANT CIRCUIT
3.2.1 STANDARD COMPONENTS USED IN THE CHILLER
The preceding abbreviations indicate the position in the drawings.
Not all components are contained in all models.
CCompressor
Scroll-type compressor of fully hermetic design with integrated bimetal switch and oil sight glass.
Semi-hermetic compressor:
Semi-hermetic compressorwith integrated bimetal switch and oil sight glass.
Reciprocating piston compressor:
Reciprocating piston compressor, fully hermetic with integrated bimetal switchand, in most models, an oil sight
glass.
CND Condenser / Condenser safety grating
Condenser as fin-type heat exchanger consisting of copper pipes with aluminium fins. The safety grating for the
housing protects the condenser on the inside against mechanical damage. The positioning of the condenser avoids
any additional heat load on the components located inside the housing.
EVA Evaporator
Insulated shell tube heat exchanger or stainless steel plate heat exchanger.
HP High-pressure pressostat
The high-pressure pressostat protectsthe refrigeration circuit of the chiller against excessively high operating pres-
sure (high-pressure fault).
In this kind of fault, the high-pressure pressostat switches the compressoroffwhen the preset limit is exceeded.
The compressor cannot be started up again until the preset differentialpressure has been reached and the Reset
button located inside the chiller has been pressed. The fault is displayed on the control unit.
LP Low-pressure pressostat
The low-pressure pressostat protects the refrigeration circuit of the chiller against excessively low operating pres-
sure (low-pressure fault).
When this kind of fault occurs, the low-pressure pressostat switches the compressor off when the preset limit is
undershot. The compressor starts up automatically if when the permitted pressure ratios have been re-established
between the high and lowpressure sides via the internal pressure compensation system. The fault is displayed on
the control unit while it persists.

6
Manometer in the refrigeration circuit
MHP High-pressure manometer:
The manometer shows thepressure on the high-pressure side within the refrigeration circuit. The display is locat-
ed on the connection side, above the cooling mediumconnections.
MLP Low-pressure manometer
The manometer shows the pressure on the low-pressure side within the refrigeration circuit. The display is locat-
ed on the connection side, above the cooling mediumconnections.
PV Pressostatic fan control
The condensation pressure is controlled by pressostatic activation and deactivation of the fans. This type of control
allows adaptation to different operating conditions at constant condensation temperatures.
R Crank case heating
The electrical crank case heating is activated after the main switch has been turned on. Itprotects againstarefrig-
erant accumulating in the compressor. This avoids faults during the compressor start-up phase at lowambient
temperatures.
V Ventilator (fan)
Axial: Low-noise axial ventilator (maintenance-free).
Radial: Low-maintenance radial ventilator for connection to an air duct on the customer½s premises.
Injection process
a. Capillary injection (up to cooling capacities of approx. 2.5 kW).
The refrigerant is injected via a defined capillary.
b. VE Expansion valve (from cooling capacities of approx. 2.5 kW)
Thermostatic valve that limits the evaporation pressure to a maximum.
(MOP; maximum operating pressure).
Piping (cooling system)
Closed pipe system made of copper tubing, including fittings. Supplied as required with additional fittings such as
non-return valves, filter drier, sight glass and service connections.
3.2.2 OPTIONS REFRIGERATION CIRCUIT
Condenser air filter, aluminium (reusable)
The condenser air filter protects the condenser against dirt. It is easy to clean and can be reused over a long period
of time.
IAF Air filter monitoring
Heavy contamination of the air filter is indicated by an acoustic warning signal visible on the controller, which is
triggered by the pressostat.
Variable fan speed control
The condensation pressureis kept at aconstant level by fanswith aspeed control and is particularly suitable for
use at extremely low ambient temperatures.
Hot gas bypass regulating device
The bypass pipe with solenoid valve and throttle device is used when there are exact requirements on the constan-
cy of the cooling medium outlet temperature or when there are high load fluctuations.
Water-cooled condenser (instead of air-cooled condenser)
This consists of aplate heat exchanger or ashell tube heat exchanger that uses existing cooling water to condense
the refrigerant. It replacesthe finned pack heat condenser and the fan.
This coolsand recondenses the refrigerant. The cooling water requirement can be adjusted according to the con-
densation pressure with a pressostatic control valve.
3.3 COOLING MEDIUM CIRCUIT (CONSUMER CIRCUIT)
3.3.1 STANDARD COMPONENTS USED IN THE CHILLER
MF Manometer for the cooling medium
In chillers with an integrated pump, the manometer indicates the pressure at the cooling medium outlet. In chillers
with no integrated pump, the manometer indicates the pressure at the cooling medium inlet.
P Pump
A single-stage or multi-stage centrifugal pump of horizontal or vertical design isused according to the type of mod-
el.

7
Differential pressure monitor
The differential pressure monitor protects the plate heat exchange of the chiller against excessively lowflow rates
and hence against damage caused by ice formation.
3.3.2 OPTIONS HYDRAULIC CIRCUIT
BP Automatic bypass / Overflow valve
The overflow valve is intended to guarantee aminimum throughput in the cooling medium circuit. This protects the
evaporator and the pump.
BPM Manual bypass
This type of bypass can be used to manually adjust the minimum throughput in the cooling medium circuit.
CAA Automatic cooling medium feed via a float valve
The cooling medium is filled up automatically by the float valve if the level in the tank falls below a minimum.
EV 1 Solenoid valve 1 (connect without current) in return circuit
These valves should be used in open systems when the consumers are installed on ahigher level. This isgenerally
used as a valve combination with VNR(see below).
FL Flow controller
The flow controller located in the cooling medium inlet monitors the flow in the cooling medium and consumer cir-
cuit. It switches the cooling system off if the throughout falls below a minimum.
LVE Flow switch (systems open to the atmosphere with tank)
The flow switch islocated in the tank and monitors the cooling medium level.
If the water level falls and reaches the minimum value, the cooling system andthe pump(s) are switched off. The
chiller cannot be switched on again until the cooling medium has been filled upto the MAX mark on the level dis-
play.
RA Tank heating
The tank heating warms the cooling medium in the tank. It is used to achieve the optimum operating temperature
within a short time if there is a low ambient temperature and no process heat is being added.
TD Digital thermometer in return circuit (systems with single and dual circuit)
The digital thermometer shows the inlet temperature of the cooling medium.
VNR Non-return valve in the supply line
These valves are used in open systems when the consumers are positioned atahigher level and prevent uncon-
trolled flow of the cooling medium back into the tank when the pump is stationary. They are generally used in
combination with a solenoid valve (EV, see above).
Dirt trap
If there is arisk of the cooling medium becoming contaminated by solids with adiameter > 1 mm during operation,
adirt trap with an appropriate mesh width has to be used. This should preferably be fitted outside of the chiller so
that it can be cleaned easily. It is important to note the flow direction. The dirt trap must be cleaned at regular in-
tervals after commissioning the chiller, or as required.
Pump alternatives
Apump is provided as standard and supplies apressure of 2to 3bar at the defined nominal flow rate. Other
pumps can of course be selected according to the project. Depending on the pressure and volume it may be neces-
sary to carry out adjustments to the system characteristics with the aid of control valves.
3.3.3 SINGLE-CIRCUIT SYSTEM WITH TANK (STANDARD)
The cooling medium circuit has been designed as system open to the atmosphere. The circuit consists of the follow-
ing components:
§pump of horizontal or vertical design,
§tank, open to the atmosphere, thermally insulated with draining facility, optical filling level indicator andcover
to prevent contamination of the cooling medium.
§piping system consisting of copper or plastic pipeswith manometer and probe connection for the operating
thermostats.
The volume of cooling medium in the tanks is acontributory factor to maintaining the constancy of the cooling me-
dium outlet temperature. The pump conveys the cooling medium within the circuit out of the tank to the consumer
and then back into the tank via the evaporator.

8
Legend:
1 Compressor
2 Condenser
3 Expansion valve
4 Evaporator
5 Pump
6 Consumer
7 Tank
3.3.4 SINGLE-CIRCUIT SYSTEM WITHOUT TANK
The cooling medium circuit is designed as a single-circuit system without tank. The pump conveys the cooling me-
dium inside the circuit through the evaporator and through the consumer.
The cooling medium in cooled inside the evaporator. The circuit consists of the following components:
§pump of horizontal or vertical design,
§piping system consisting of copper or plastic pipes with manometer and probe connection for the operating
thermostats and the digital temperature display.
If designed as a system closed to the atmosphere, the external circuit must be provided with venting connec-
tions and with pressure compensation tank if required!
Legend:
1 Compressor
2 Condenser
3 Expansion valve
4 Evaporator
5 Pump
6 Consumer
3.4 ELECTRIC CIRCUIT
3.4.1 STANDARD COMPONENTS USED IN THE CHILLER
ALR Composite Failure Report
The composite failure report summarizes all fault messages from the compressor, the pump(s), fan(s) of the high-
pressure and low-pressure pressostats, the flow monitor as well as the breakage of probes. Voltage-free series
connection of this composite reporttakes place atthe terminals in the switch cabinet (see circuit diagram in the
Annex).
IG Main switch
The chiller carries no current after it has been turned off with the main switch. The switch is located on the door of
the switch cabinet.
MTC Motor protection switch for compressor
If the motorcurrent increases beyond the set value or if there is ashort circuit, the motor protection switch turns
off and interrupts the current supply. The motor protection switch has to be turned on manually after the cause of
the malfunction has been eliminated. The motor protection switch is located in the switch cabinet.
MTP Motor protection switch for pump
If the motorcurrent increases beyond the set value or if there is ashort circuit, the motor protection switch turns
off and interrupts the current supply. The motor protection switch has to be turned on manually after the cause of
the malfunction has been eliminated.

9
The motor protection switch is located in the switch cabinet.
ROO Remote control
The chiller can be switched off by the consumer or from a control room with the aid of an external contact. When
this occurs, the main switch remains permanently switched on.
QE Switch cabinet
The switch cabinet contains all the electrical components and safety devices.
TLT Temperature controller
Temperature control and regulation is carried out by the temperature controllerof the chiller in accordance with the
preset value.
The temperature controller with digital display is integrated in the door of the switch cabinet. Fault messages are
displayed on the temperature controller by means of codes.
3.4.2 OPTIONS ELECTRIC CIRCUIT
Connecting cable with CEE plug
A ready-to-use mains cable is supplied with 6m oilflex cable and CEE plug 4-pole (3P+PEN)or 5-pole (3P+N+PE).
Compressor winding protection
Depending on the compressor type, the protection is provided either by Klixon (bimetal strip) or by atemperature
probe. If the maximumpermissible winding temperature is attained, the motorprotection switch turns off the com-
pressor.
3.5 HOUSING
Legend for all the following housing versions:
1 Level
2 Power supply
3 Temperaturecontroller
04I Cooling medium inlet
04O Cooling medium outlet
05I Cooling water condenser inlet (*)
05O Cooling water condenser outlet (*)
(*) in water-cooled chillers
MODELS: PCGE 11, PCGE 21, PCGE 25, PCGE 28; PCGEZ 08
MODELS
A
B
H
C
D
E
F
G
I
L
M
(“)
PCGE 11, 21, 25 / PCGEZ
08
575
445
540
/
490
/
/
/
80
56
608
$’
PCGE 28
5
75
445
640
/
490
/
/
/
80
56
608
(’

10
MODELS: PCGE 31, PCGE 41, PCGE 61; OCGE 31, OCGE 41, OCGE 61; PCGEZ 37, PCGEZ 50, PCGEZ 70
MODELS
A
B
H
C
D
E
F
G
I
L
M
(“)
PCGE 31, 41, 61 / OCGE 31, 41, 61
580
650
920
845
419
80
583
80
/
82,5
1036
(’
PCGEZ 37, 50, 70
580
650
920
845
419
80
583
80
/
82,5
1041
(’
MODELS: PCGE 81, PCGE 111, PCGE 141; OCGE 81, OCGE 111, OCGE 141; PCGEZ 100, PCGEZ 160
MODELS
A
B
H
C
D
E
F
G
I
L
M
(“)
PCGE 81, 111 / OCGE81, 111
760
760
1330
1250
767
100
972
100
/
84
1445
1’
PCGEZ 100
760
760
1330
1250
767
100
972
100
/
84
1445
1’
PCGE 141 / OCGE141 / PCGEZ 160
760
760
1380
1300
767
100
972
100
/
84
1510
1’
MODELS: PCGE 150 to PCGE 1100; OCGE 150 to OCGE 240; PCGEZ 180 to PCGEZ 480
MODELS
A
B
H
C
D
E
F
G
I
L
M
(“)
PCGE
150,
200,220,290 / OCGE
150,
200, 240 / PCGEZ 180, 240 1325 760 1535 1400 300 300 603 300 / 84 / 1’
PCGE 370 to 590
PCGEZ 300,360, 480 1325
1520 1535
1400 300 300 603 300 / 84 / 1$’
PCGE 730,880
1325
2280
1535
1400
300
300
603
300
/
84
/
1$’
PCGE 1000,1100
1325
3040
1535
1400
300
300
603
300
/
84
/
2’

11
MODELS: PCGE 1300, PCGE 1900, PCGE 2200
MODELS
A
B
H
C
D
E
F
G
I
L
M
(“)
PCGE 1300 to 2200
1525
3990
2140
2060
381
100
/
/
200
310
/
3’
4. TRANSPORT/ PACKAGING/ STORAGE
4.1 REMOVING THE PACKAGING AND HANDLING THE CHILLER
Each chiller is supplied in areinforced carton on awooden pallet. The chiller must be kept in an upright position at
all times. NOTE: Tilting the chiller may cause serious damage!
Procedure:
* Remove the strapping from the carton. Always wear safety gloves when using scissors
or other tools to cut the straps.
* Remove the carton.
* Raise the chiller using suitable lifting gear.
NOTE: If the chiller is fitted with eyebolts, these must be used for lifting it in accordance with the applicable
safety standards.
If the chiller is not fitted with eyebolts, the lifting gearmust be appropriate forthe weight of the chiller, asindi-
cated on the identification plate and in the Annex.
* Remove the pallet (if present).
* Place the chiller in the desired location.
* Remove the operating manual, accessories and key from the chiller.
PCGE 81- PCGE3300
4.2 DISPOSAL OFPACKAGING MATERIALS
We recommend that you keep the original packaging for the chillerin case it has to be transported to another loca-
tion or sent to aservice centre. In any case, the waste packaging materialmust be deposited with the responsible
waste disposal companies.
4.3 STORAGE
The chiller must be stored in rooms protected fromweather-related influences. These roomsmust be dryand have
a temperature range of between +5 and +50±C.

12
If thechiller is stored forlonger than 12 months, please contact the manufacture before
starting up the chiller again to check the condition ofthe machine parts, particularly the elec-
trical components.
See Chapter 6.5.2 (Temporary decommissioning).
5. LOCATION AND INSTALLATION
5.1 CHOOSING A LOCATION
Install the chiller in aprotected dry area, free of fumes, dust or flammable vapours that is not subject
to an explosive hazard. The atmospheremust be free of any constituents that may impair the proper
functioning of the chiller.
Asuitable area must be found in which atemperature of not less than +2±Cand definitely not morethan +40±C
can be guaranteed at any time of the year while the machine is operating. If you wish to operate the chiller at am-
bient temperatures of lessthan +2±Cor morethan +40±C, please contact the manufacturer in connection with the
necessary adaptations.
We recommend that appropriate ventilation should be provided. Operating the chiller heats up the area in which it
is installed. This applies particularly to chillers with a standard air-cooled condenser.
So as not to impair the cooling capacity of the chiller, we recommend protecting it against directsunlight. You
should avoid connecting the axial ventilators to air ducts as they do not havesufficient compression.
Higher ambient temperatures than those given as areference value in the data sheet reduce the cooling capacity.
The chiller should be installed on a horizontal and level surface that is capable of absorbing the compre ssive load of
the chiller. Larger chillers have holes at the ends of the supporting rails so that they can be fastened to the floor.
When the chillerisinstalled outside, it should be protected against any atmospheric influences. Please consult the
manufacturerfor further details.
Position the chiller so that the instrument displays can be read easily and the controls can be easily accessed.
Allow sufficient space for the possible installation of further components.
There must be sufficient free space above the chiller to ensure that air can flow freely to cool the condenser.
(Sample illustration. See thecorresponding letters for theother versions. B isalways thefront side)
Models
A (m) B (m) C (m) D (m) E (m) LOCATION
PCGE 11 to 28, PCGEZ
08
1
1
1
1
1
Indoors
PCGE 31 to 61, OCGE 31 to 61,
PCGEZ 37 to 70
1
1
1
1,5
1
Sheltered outdoor
location
PCGE 81 to 141, OCGE 81 to 141,
PCGEZ 100 to 160
1
1
1
2
1
PCGE
150 to 1100, OCGE15
0 to 240,
PCGEZ 180-480 1 1 1 3 1 Outdoors (shelter
recommended)
PCGE 1300-3300 1 2 1 4 2

13
5.2 ASSEMBLY (CONNECTIONS)
5.2.1 CONNECTION TO THE REFRIGERANT CIRCUIT (CONSUMER CIRCUIT)
All work may only be carried out by specialist personnel!
Procedure: -In closed systems, make sure that the maximum obtainable cooling medium pressure in the supply
line does not cause a higher pressure level than the maximum permitted for the chiller.
-Check the cleanliness of the supply line and the piping system to be connected.
-Connect the chiller with the consumer circuit; the identification of the joints (cooling medium in-
let/outlet) is indicated on the chiller by means of the symbols described in the introduction to the
manual.
-Make all the connections, without rotating the sleeves located on the hose.
The cooling medium circuits of the Series PCGE and PCGEZ with tank are open to the at-
mophere as standard!
Use piping, connections and fastening components with a cross-section to match the capacity of the chiller and the
possible volume flow. This should not be smaller than the diameter of the chillerconnections.
In the case of rigid connections, check during the initial start-up of the chiller that it is not subject to any vibrations
that might endanger the integrity of the components.
We also recommend that you should plan to install the following system components:
Abypass system with suitable valves upstream and downstream of the chiller.This isintended to allow use
of the consumer circuit if you have to remove the chiller fromthe circuit, switch it off or use it in different
ways at the same time.
Apipeline system with integrated filter near the chiller to protectthe pump against solid matter and avoid
deposits on the heat exchangers. The recommended mesh width for the chillers is 25µwith amaximum
pressure lossat the filterof 1bar. The use of afilter with amesh width of 60µis particularly suitable for
chillers of the OGCE seriesif they are fitted with agear pump, so as to avoid unusual wear of the compo-
nent.
In the models without flow monitoring, we suggest that you should install such acomponent if the system
exhibits losses or very high cooling medium consumption due to evaporation or intervention by the opera-
tor. A further reason may be triggering of the solenoid valve to shut down the system. The flow meter may
trigger an alarm and enable immediate operator intervention.
On no account may the total pressure loss of the system exceed avalue above that of the pump perfor-
mance.
Another option for directlyfilling the tank involves attaching aT-fitting to the cooling medium outlet fitting
in order to connect the cooling medium circuit with asupply pipe. This is used to fill the chiller. We also
recommend connecting avalve to the supply pipe in order to stop the flow when the tank is full or to re-
start the flow as soon as atop-up is necessary.
Fig.1
A Male-male fitting
B From thesupply line
C To the consumer cooling circuit
D T-fitting
E Connecting pieceto cooling medium outlet

14
5.2.2 CONNECTION TO THE ELECTRICITY MAINS
The properties of the electricity mains (size, protection system, earth connection) must comply with the legislation
applying to the electrical properties of the chiller in the country in which it is installed.
The general regulations pertaining to installation are listed below.
The electrical installation may only be carried out by qualified personnel!
The mains connection should be established with a rubber-sheathed cable connected to a TN-C system with direct
earthing.
230 V version (1 phase):
Connection with asingle-phase, three-wire system (1/N/PE AC). The phase conductor and the neutral conductor
must be connected directlyto the main switch of the chiller.
The protective earth conductor must be connected to the earthing point of the chiller.
400 V version (3 phase):
Connection with athree-phase, four-wire system (3/PEN AC). The three-phase conductormust be connected di-
rectly to the main switch of the chiller.No neutralconductor is used. The PENmust be connected to theearthing
point of the chiller.
If different mainsvoltages and frequencies are available, the country-specific features must be observed.
Make sure that the mains voltage and the frequency match the data on the identification plate of the chiller and
agree with those in the table in the supplement and that the permitted values are not exceeded. Check the mains
for correct values and test the function of the earthing and protection systems.
Install ageneral isolating switch for the electricity mains close to the chiller.The connecting circuit forthe chiller
must be equipped with a circuit breaker and residual current protective device.
You can find information on the electrical power input values for the chiller in the supplement.
Before you connect the chiller to the mains, make sure that the general isolating switch disconnects the chiller from
the electricity mains.
Pass the wires in the flexible polymer cable gland in the control panel (see photo for position) to connect the power
cable. Feed the connecting lead through the aperture in the rear plate (PCGE 31-PCGE 141) on the base of the
chiller. Lay the cable on the upright up to the gland on the base of the switch cabinet (PCGE 200- PCGE 3300). In-
side the switch cabinet lay the cable in the installation duct upto the main switch, where it is connected directly.
Check that the screws on the terminal clamps are firmly seated!
Holes for feeding through the power cable
Cable inlet

15
6. OPERATION
6.1 CHECK LIST FORTHE INITIAL START-UP OF WATERRECIRCULATING CHILLERS
After extraordinary maintenance work or after turning off the main switch for more than 1hour, eachstart-up
should be treated as an initial start-up.
The initial start-up calls fora number additional checks to ensure safe and reliable performance of the system.
Before start-up:
Make sure that the pump motor is not blocked: simply move the fan of the pump motor one quarterof a turn.
6.1.1 WATER REQUIREMENTS
Quality:
Standard chillers require water of mains water quality. If no water of mains quality is available, please contact the
manufacturerfor advice.
If additives are being used, make sure that these are suitable for use with the materials and components of the
chiller. Note that the quantity of additives may impair the performance of the chiller, e.g. due to unsuitable viscosi-
ty). The pipelines of the water circuit may be made of copper, stainless steel or plastic.
General operating conditions:
In standard recirculating chillers the outlet temperature of the cooling mediummust be between +5±Cand +20±C.
If temperature values of more than +20±Care required for the preset temperature, please contact the manufac-
turer for appropriate adaptations.
Conditions during commissioning:
The inlet temperature of the cooling medium should not be more than +25±C.
If temperature values of less than +5±C apply to the preset temperature, antifreeze must be used.
The glycol must contain anti-corrosion additives. In the standard configuration, the PCGE series, ethylene glycol in
concentrations of 20% up to a maximum of 34% may be used for minus temperatures down to 10±C. Add anti-
freeze for ambient temperatures of approx. Ä0±C.
When antifreeze is used, it is important to make sure that the current consumption remains within the data indicat-
ed on the identification plate on the motor.
6.1.2 CHECKLIST FOR PCGE 11 TO PCGE 3300
Controller Type ”AÜ, see 6.4 (PCGE 11 toPCGE 28)
1) Removethe lid paneland thetwo sidepanels.
2) Fill the collection tank. Openthe tank cap and fill the tank (using a T-fitting if necessary) while watching thelevelindica-
tor (refer to Fig. 1,Point 5.2.1).
3) Openthe filler screw on thepump head.
4) Tighten the screw again whenonly cooling medium flows out.
5) Openthe shut-off valve.
6) Movethe main switch of the chiller to position ”1’. Thedisplay will show ”OFF’and the pump will start up.
7) Top up thetank again if too much cooling medium hasflowed out of theshut-off valve.
8) After afew minutes carefully openthe filler screw again in order to removeany residual air. Tighten the screw again af-
terwards.
9) Replace theupper lid panel and the two sidepanels.
10) Start up the compressor by pressing the button for 3 seconds.
11) Wait until the chiller has attained the operating conditions. This is indicated whenthe actual temperature shownin the
display matchesthe preset targettemperature.
12) When the chiller iswithin the operating conditions set by the manufacturer,check whether the electrical absorption of
the chiller agrees with the data indicated on theidentification plate and with those contained in thetable inthe supple-
ment.
Controller Type ”BÜ, see 6.4 (PCGE 31 toPCGE 520)
1) Removethe front plate and the two side panels.
2) Openthe tank cap and fill the tank (using a T-fitting if necessary)while watching the levelindicator (refer to Fig. 1,
Point 5.2.1).
3) Openthe filler screw on thepump head.
4) Tighten the screw again whenonly cooling medium flows out.
5) Openthe shut-off valve.
6) Openthe switch cabinetwith the key supplied (fastened to the main switch whenthe chiller isdelivered).
7) Ensure that the motor protection switches (”MTC’and ”MTP’) arein position ”0’.
8) Fill the tank to the maximum (upper arrow, level indicator is located on the bottom right of the frame). See Section
6.1.1 (Water requirements).
9) Movethe motor protection switches ”MTC’and ”MTP’to position ”1’.

16
10) Make sure that the water is able to circulate adequately. Itthe circuit might be interrupted by something such as a
valve, electrical valve, afilter oranything else, aby-pass circuit (automatic overflow valve) must be installed in or-
der to prevent damageto the pump.
11) Lock the switch cabinet with the key.
12) Movethe main switch of the chiller to position ”1’(thetemperature of the cooling medium appears on the display).
Never touch any part of the refrigerant circuit whenthe chiller isrunning!
13) Start up the compressor by pressing the button for 3 seconds.
14) Becausethe pump startsup immediately, makesure that the direction of rotation for thepump matchesthe direc-
tion of the arrow onthe casing. If it is rotating in theopposite direction, turn off themain switch of the chiller im-
mediately and arrange for thepolarity of the chiller to bereversed.
15) After afew minutes carefully openthe filler screw again in order to removeany residual air. Tighten the screw again
afterwards.
16) Wait until the chiller has attained the operating conditions. This is indicated whenthe actual temperature shownin
the display matchesthe preset targettemperature.
17) Check whether the pressure shown is within the limits specified for the pump. If not, take appropriate action to en-
sure that thepump isrunning within the specified limits.
18) Check the level in thetank and top up with cooling medium if required. Fastenthe tank cap afterwards.
19) Wait for thecompressor to switch on. The compressor symbol will appear on the display (see Section6.4).
20) Check the inside of the chiller and the piping system for leakage or looseconnections.
21) Fit the front paneland thetwo side panels back onto thecasing.
22) Check the preset targetvalue.The chiller is normally factory-set to thetemperature required by the customer.
23) When the chiller is within the operating conditions set by themanufacturer, check whether the current uptake of the
chiller agrees with the data indicated on the identification plate and with those contained in the table in the supple-
ment.
Controller Type ”CÜ, see 6.4 (PCGE 590 to PCGE 1100)
1) Removethe front plate and the two side panels.
2) Open the tank cap and fill the tank (using a T-fitting if necessary) while watching the level indicator (refer to Fig. 1, Point
5.2.1).
3) Openthe filler screw on thepump head.
4) Tighten the screw again whenonly cooling medium flows out.
5) Openthe shut-off valve.
6) Openthe switch cabinet with the key supplied (Fastened to the main switch whenthe chiller isdelivered).
7) Ensure that the motor protection switches (”MTC’and ”MTP’) arein position ”0’.
8) Fill the tank to the maximum (upper arrow, level indicator is located on the bottom right of the frame). See Section 6.1.1
(Water requirements).
9) Movethe motor protection switches ”MTC’and ”MTP’to position ”1’.
10) Make sure that the water is able to circulate adequately. It the circuit might be interrupted by something such asa valve,
electrical valve, afilter or anything else, aby-pass circuit (automatic overflow valve) must be installed in order to pre-
vent damageto the pump.
11) Lock the switch cabinet with the key.
12) Movethe main switch of the chiller to position ”1’(thetemperature of the cooling medium appears on the display).
Never touch any part of the cooling medium circuit when the chiller isrunning!
13) Start up the chiller by pressing the button(LED lights up).
14) Because the pumpstarts upimmediately, make sure that the direction of rotation for thepump matchesthe direction of
the arrow on the casing. If it is rotating in the opposite direction, turn off the main switch of the chiller immediately and
arrange for thepolarity of thechiller to be reversed.
15) Afterafew minutes carefully open the filler screw again in order to remove any residual air. Tighten the screw again af-
terwards.
16) Wait until the chiller has attained the operating conditions;this is indicated when the display shows the preset working
range.
17) Check whether the pressure shown is within the limits specified for the pump. If not, take appropriate action to ensure
that pump isrunning within the specified limits.
18) Check the level in thetank and top up with cooling medium if required. Fastenthe tank cap afterwards.
19) Wait for thecompressor to switch on. The compressor symbol will appear on the display (see Section6.4).
20) Check the inside of the chiller and the piping system for leakage or looseconnections.
21) Fit the front paneland thetwo side panels back onto thecasing.
22) Check the preset targetvalue.The chiller is normally factory-set to thetemperature required by the customer.
23) When the chiller is within the operating conditions set by the manufacturer, check whether the current uptake of the
chiller agreeswith thedata indicated on theidentification plate and with thosecontained in the table inthe supplement.
Controller Type ”CÜ, see 6.4 (PCGE 1300 to PCGE 3300)
1) Removethe sidepanels.
2) Open the tank cap and fill the tank (using a T-fitting if necessary) while watching the level indicator (refer to Fig. 1, Point
5.2.1).
3) Openthe filler screw on thepump head.
4) Tighten the screw again whenonly cooling medium flows out.
5) Openthe shut-off valve.
6) Openthe switch cabinetwith the key supplied (Fastened to the main switch whenthe chiller isdelivered).
7) Ensure that the motor protection switches (”MTC’and ”MTP’) arein position ”0’.

17
8) Make sure that the water is able to circulate adequately. It the circuit might be interrupted by something such asa valve,
electrical valve, a filter or anything else, aby-pass circuit (automatic overflow valve) must be installed in order to pre-
vent damageto the pump.
9) Check the inside of the chiller and the piping system for leakage or looseconnections.
10) Movethe motor protection switches ”MTC’and ”MTP’to position ”1’.
11) Lock the switch cabinet with the key.
12) Movethe main switch of the chiller to position ”1’(thetemperature of the cooling medium appears on the display).
Never touch any part of the cooling medium circuit when the chiller is running!
13) Start up the chiller by pressing the button(LED lights up).
14) Because the pumpstarts upimmediately, make sure that the direction of rotation for thepump matchesthe direction of
the arrow on the casing. If it is rotating in the opposite direction, turn off the main switch of the chiller immediately and
arrange for thepolarity of thechiller to be reversed.
Do not carryout anywork inside the chiller if the main switch is in the ONüposition!
15) Make surethat the water isable to circulate adequately.
16) Check whether the pressure shown is within the limits specified for the pump. If not, take appropriate action to ensure
that pump isrunning within the specified limits.
17) Start up the chiller by pressing the button(LED no longer lights up).
18) Check the inside of the chiller and the piping system for leakage or looseconnections.
19) Fill the tank up to the maximum.
20) Fasten thetank cap afterwards.
21) Fit the two sidepanelsback onto the casing.
22) Start up the chiller by pressing the button(LED lights up).
23) Wait for thecompressor to switch on. The compressor symbol will appear on the display (see Section6.4).
24) Wait until the chiller has attained the operating conditions. This is indicated when the actual temperature shown in the
display matchesthe preset targettemperature.
25) Check the preset targetvalue.The chiller is normally factory-set to thetemperature required by the customer.
26) When the chiller is within the operating conditions set by the manufacturer, check whether the current uptake of the
chiller agreeswith thedata indicated on theidentification plate and with thosecontained in the table inthe supplement.
6.2 CHECKLISTFOR STARTING UP OIL RECIRCULATING CHILLERS
After turning off the main switch for more than 1 hour or after extraordinary maintenance work, each chiller start
should be regarded as an initial start-up.
The initial start-up calls fora number additional checks to ensure safe and reliable performance of the system.
6.2.1 OIL REQUIREMENTS
Quality:
The oil used for filling the chiller should have a viscosity index in accordance with the standards indicated in the fol-
lowing table.
OCGE Series Tank close to the chiller (max. 2m)
Gear pump (option) with remote tank
(>2m)
Oil/
Outlet temperature ≤
ISO32/
min. +20±C ≤
ISO46/
min. +25±C ≤
ISO68/
min. +30±C ISO10÷ISO68
General operating conditions:
The oil recirculating chilleris designed for cooling medium temperatures of +20±Cto +30±C. If the temperature
values deviate from these, please contact the manufacturer.
Conditions during commissioning:
The use of oil with ahigher viscosity and lower cooling temperatures may cause overloading of the circulation
pump. If this is the case, the cooling medium circuit must be adapted accordingly. In suchcases, contact the man-
ufacturer.
6.2.2 CHECKLISTE FOR OCGE 31 TO OCGE 240
Controller Type ”BÜ, see 6.4 (OCGE 31 to OCGE 240)
1) Removethe front plate and the two side panels.
2) Connect the supplydevices or the external tank. Make sure that the level of the contents is higher than the pump to
support the automatic priming system. UseaT-fitting if necessary for filling (referto Fig. 1, Point 5.2.1). One essential
requirement isthe availability of asuitable vent opening for the system, particularly for chillers with gear pumps.
3) Openthe filler screw on thepump head.
4) Tighten the screw again whenonly oil flows out.
5) Openthe shut-off valve.
6) Openthe switch cabinetwith the key supplied (Fastened to the main switch whenthe chiller isdelivered).
7) Ensure that the motor protection switches (”MTC’and ”MTP’) arein position ”0’.
8) Movethe motor protection switches of thechiller to position ”1’.

18
9) Make sure that the oil is able to circulate adequately. It the circuit might be interruptedby something such as avalve,
electrical valve, afilter or anything else, a by-pass circuit (automatic overflow valve) must be installed in order to pre-
vent damageto the pump.
10) Lock the switch cabinet with the key.
11) Movethe main switch of the chiller to position ”1’(thetemperature of the cooling medium is displayed).
Never touch any part of the refrigeration circuit when the chiller is running!
12) Start up the compressor by pressing the button for 3 seconds.
13) Wait until the chiller has attained the operating conditions. This is indicated whenthe display shows the presetworking
range.
14) Becausethe pump startsup immediately, makesure that the direction of rotation for thepump matchesthe direction of
the arrow on the casing. If it is rotating in the opposite direction, turn off the main switchof thechiller immediately and
arrange for thepolarity of thechiller to be reversed.
15) After afew minutes carefully openthe filler screw again in order to removeany residual air. Tighten the screw again af-
terwards.
16) Check whether the pressure shown is within the limits specified for the pump. If not, take appropriate action to ensure
that pump isableto run within the specified limits.
17) Wait for thecompressor to switch on. The compressor symbol will appear on the display (see Section6.4).
18) Check the inside of the chiller and the piping system for leakage or looseconnections.
19) Fit the front paneland thetwo side panels back onto thecasing.
20) The chiller isnormally factory-set to thetemperature required by the customer.
21) When the chiller is within the operating conditions set by the manufacturer, check whether the current uptake of the
chiller matchesthe dataindicated on the identification plate and thosecontained in the table in the supplement.
6.3 CHECK LIST FORCOMMISSIONING GLYCOLRECIRCULATING CHILLERS
After turning off the main switch for more than 1 hour or after extraordinary maintenance work, each chiller start
should be regarded as an initial start-up.
The initial start-up calls fora number additional checks to ensure safe and reliable performance of the system.
6.3.1 REQUIREMENTS FOR THE WATER-GLYCOL MIXTURE
Quality:
A water-glycol mixture should be used for filling the chiller (glycol = ethylene glycol). Corrosion-inhibiting additives
may also be included provided they are explicitly authorized for this purpose by the manufacturer concerned. The
glycol content must be at least 20% and should not exceed 25%.
Cold water discharge temperature Ethylene glycol in %
Ä0±C
- 5±C
- 10±C
20
20
25
General operating conditions:
The glycol recirculating chiller is designed for cooling medium temperatures of -10±C to Ä0±C.
Conditions during commissioning:
Should liquid temperaturesdifferent to those described in the general operating conditions occur during the initial
start-up, be sure to contact the manufacturer.
6.3.2 CHECKLIST FOR PCGEZ 08 TO PCGEZ 480
Controller Type ”AÜ, see 6.4 (PCGEZ 08)
1) Removethe upper lid paneland the two sidepanels.
2) Openthe tank cap and fill the tank (using a T-fitting if necessary)while watching the levelindicator (refer to Fig. 1, Point
5.2.1).
3) Openthe filler screw on thepump head.
4) Tighten the screw again whenonly cooling medium flows out.
5) Openthe shut-off valve.
6) Movethe main switch of the chiller to position ”1’(thedisplay will show ”OFF’,and the pump will start to run).
7) Top up thetank again if too much cooling medium hasflowed out of theshut-off valve.Fasten the tank cap again after-
wards.
8) After afew minutes carefully openthe filler screw again in order to removeany residual air. Tighten the screw again af-
terwards.
9) Replace theupper lid panel and the two sidepanels.
10) Start up the compressor by pressing the button for 3 seconds.
11) Wait until the chiller has attained the operating conditions. This is indicated whenthe actual temperature shownin the
display matchesthe preset targettemperature.
12) When the chiller iswithin the operating conditions set by the manufacturer,check whether the current uptake of the
chiller matchesthe dataindicated on the identification plate and thosecontained in the table in the supplement.

19
Controller Type ”BÜ, see 6.4 (PCGEZ 37 to PCGEZ 180)
1) Removethe front plate and the two side panels.
2) Open the tank cap and fill the tank (using a T-fitting if necessary) while watching the level indicator (refer to Fig. 1, Point
5.2.1).
3) Openthe filler screw on thepump head.
4) Tighten the screw again whenonly water-glycol mixture flows out.
5) Openthe shut-off valve.
6) Openthe switch cabinetwith the key supplied (Fastened to the main switch whenthe chiller isdelivered).
7) Ensure that the motor protection switches (”MTC’and ”MTP’) arein position ”0’.
8) Fill the tank to the maximum (upper arrow, level indicator is located on the bottom right of the frame). See Section 6.1.1
(Water requirements).
9) Movethe motor protection switches ”MTC’and ”MTP’to position ”1’.
10) Make sure that the water-glycol mixture is able tocirculateadequately. It the circuit might be interrupted by something
such as avalve, electrical valve, a filter or anything else, aby-passcircuit (automatic overflow valve) must beinstalled in
order to prevent damageto the pump.
11) Lock the switch cabinet with the key.
12) Movethe main switch of the chiller to position ”1’(thetemperature of the cooling medium is displayed).
Never touch any part of the cooling circuit whenthe chiller is running!
13) Start up the compressor by pressing the button for 3 seconds.
14) Make sure that the direction of rotation for the pump matches the direction of the arrow on the casing because the pump
starts up immediately. If it is rotating in the opposite direction, turn off the main switch of the chiller immediately and ar-
rangefor the polarity to be reversed.
15) Afterafew minutes carefully open the filler screw again in order to remove any residual air. Tighten the screw again af-
terwards.
16) Wait until the chiller has attained the operating conditions. This is indicated whenthe actual temperature shownin the
display matchesthe preset targettemperature.
17) Check whether the pressure shown is within the limits specified for the pump. If not, take appropriate action to ensure
that pump isable to run within the specified limits.
18) Check the level in thetank and top it up if required. Put thetank cap back in place.
19) Wait for thecompressor to switch on. The compressor symbol will appear on the display.
20) Check the inside of the chiller and the piping system for leakage or looseconnections.
21) Fit the front paneland thetwo side panels back into place.
22) The chiller isnormally factory-set to thetemperature required by the customer.
22) When the chiller is within the operating conditions set by the manufacturer, check whether the current uptake of the
chiller matchesthe dataindicated on the identification plate and thosecontained in the table in the supplement.
Controller Type ”CÜ, see 6.4 (PCGEZ 240 to PCGEZ 480)
1) Removethe front plate and the two side panels.
2) Open the tank cap and fill the tank (using a T-fitting if necessary) while watching the level indicator (refer to Fig. 1, Point
5.2.1).
3) Openthe filler screw on thepump head.
4) Tighten the screw again whenonly cooling medium flows out.
5) Openthe shut-off valve.
6) Openthe switch cabinetwith the key supplied (Fastened to the main switch whenthe chiller isdelivered).
7) Ensure that the motor protection switches (”MTC’and ”MTP’) arein position ”0’.
8) Fill the tank to the maximum (upper arrow, level indicator is located on the bottom right of the frame). See Section 6.1.1
(Water requirements).
9) Movethe motor protection switches ”MTC’and ”MTP’to position ”1’.
10) Make sure that the water is able to circulate adequately. It the circuit might be interrupted by something such asa valve,
electrical valve, afilter or anything else, aby-pass circuit (automatic overflow valve) must be installed in order to pre-
vent damageto the pump.
11) Lock the switch cabinet with the key.
12) Movethe main switch of the chiller to position ”1’(thetemperature of the cooling medium appears on the display).
Never touch any part of the cooling circuit whenthe chiller is running!
13) Start up the chiller by pressing the button(LED lights up).
14) Because the pumpstarts upimmediately, make sure that the direction of rotation for thepump matchesthe direction of
the arrow on the casing. If it is rotating in the opposite direction, turn off the main switch of the chiller immediately and
arrange for thepolarity of thechiller to be reversed.
15) Afterafew minutes carefully open the filler screw again in order to remove any residual air. Tighten the screw again af-
terwards.
16) Wait until the chiller has attained the operating conditions. This is indicated when the actual temperature shown inthe
display matchesthe preset targettemperature.
17) Check whether the pressure shown is within the limits specified for the pump. If not, take appropriate action to ensure
that pump isrunning within the specified limits.
18) Check the level in thetank and top up with cooling medium if required. Fastenthe tank cap afterwards.
19) Wait for thecompressor to switch on. The compressor symbol will appear on the display (see Section6.4).
20) Check the inside of the chiller and the piping system for leakage or looseconnections.
21) Fit the front paneland thetwo side panels back onto thecasing.
22) Check the preset targetvalue.The chiller is normally factory-set to thetemperature required by the customer.
23) When the chiller is within the operating conditions set by the manufacturer, check whether the current uptake of the
chiller agreeswith thedata indicated on theidentification plate and with thosecontained in the table inthe supplement.

20
6.4 OPERATING SETTINGS FOR THE ELECTRONIC CONTROLLER
All work on the chiller may only be carried out by specialist personnel!
The chiller is supplied pre-adjusted for normal operating conditions and normally does not require any modifica-
tions, except for the setting the temperature of the cooling medium to the desired value. Checking and anypossi-
ble adaptation of the operating parameters is carried out via the controls on the front of the chiller and via the co n-
trol panel. The chillers are equipped with an operating thermostat to maintain the cooling medium temperature at a
constant value. The various models may be equipped with two types of operating thermostats:
Type Display onthe electronic controller Models
Type
A
PCGE 11 to 28
PCGEZ 08
Symbols
Compressor active(ON) programming phase (flashes); anti-short-circuit delay active(flashes)
Defrosting function (ON) programming phase(flashes)
AUX
Second relay active(ON)
A temperature alarm hasbeen triggered (ON)
Type
B
PCGE 31 to 520
OCGE 31 to 240
PCGEZ 37 to 180
Symbols
degrees Celsius
degrees Fahrenheit
bar
PSI
Compressor 1
Compressor 2
Unit in standby*
General alarm
High-pressurealarm
Low-pressurealarm
Antifreeze heating activated Time display
Flow alarm
Function menuactivated
Water pump: symbollights up when
water pump is active
Condenser fan: symbol lights up whenthe dig-
ital output (relay) isconfigured asa fan
ON/OFF or symbollights up when the propor-
tional output to thecondenser fan isactive.
Type
C
PCGE 590 to 1100 (Checklist 1)
PCGE 1300 to 3300 (Checklist 2)
PCGEZ 240 to 480 (Checklist 1)
Symbols
degrees Celsius
degrees Fahrenheit
bar
PSI
Compressor 1
Compressor 2
Compressor 3
Compressor 4
Compressor 5
Compressor 6
Antifreeze heating activated
General alarm
Flow alarm
Time display
Water pump: symbollights up when
water pump is active
Condenser fan: symbol lights up whenthe dig-
ital output (relay) isconfigured asa fan
ON/OFF or symbollights up when the propor-
tional output to thecondenser fan isactive.
This manual suits for next models
49
Table of contents
Languages:
Popular Chiller manuals by other brands
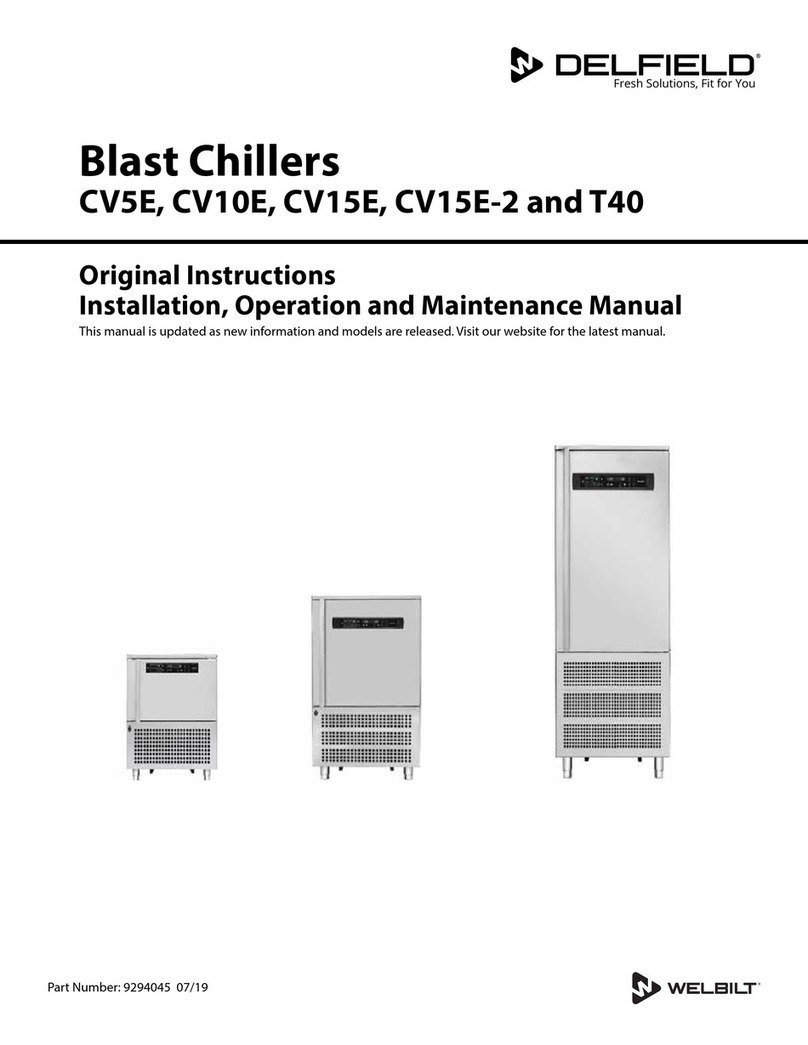
Welbilt
Welbilt Delfield CV5E Original instructions
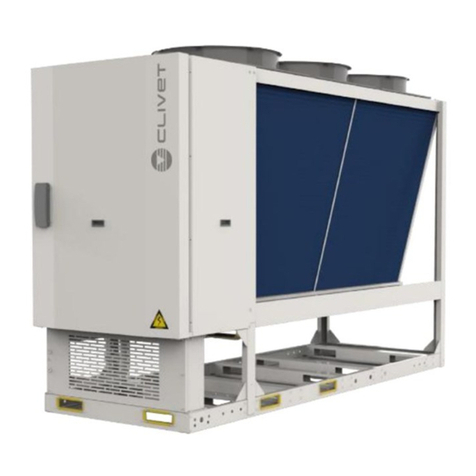
CLIVET
CLIVET WSAN-YES 18.2 Manual for installation, use and maintenance

Daikin
Daikin EWLQ014KBW1N Operation manual
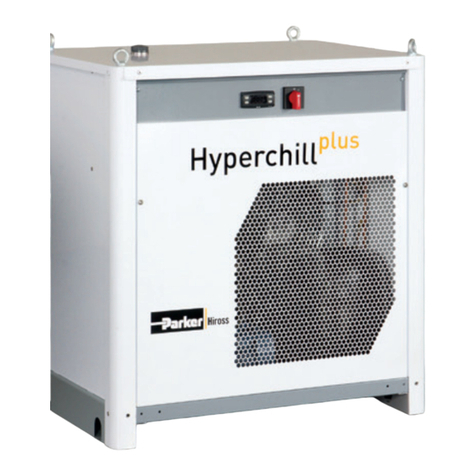
Parker Hiross
Parker Hiross Hyperchill Plus ICEP002 user manual
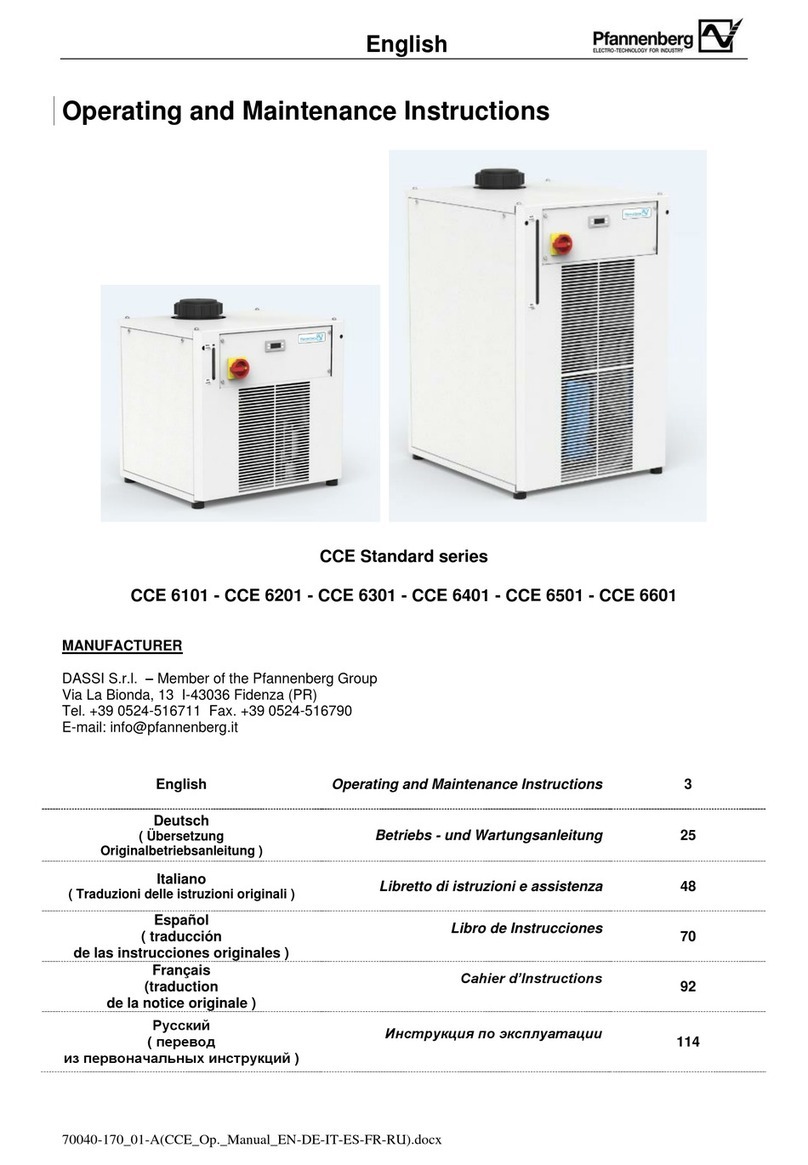
Pfannenberg
Pfannenberg CCE 6101 Operating and maintenance instructions
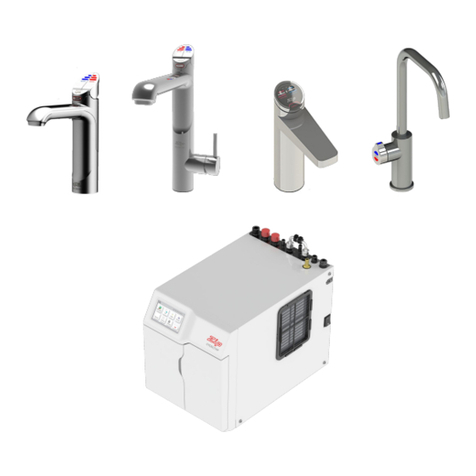
Zip
Zip HydroTap G4 user guide
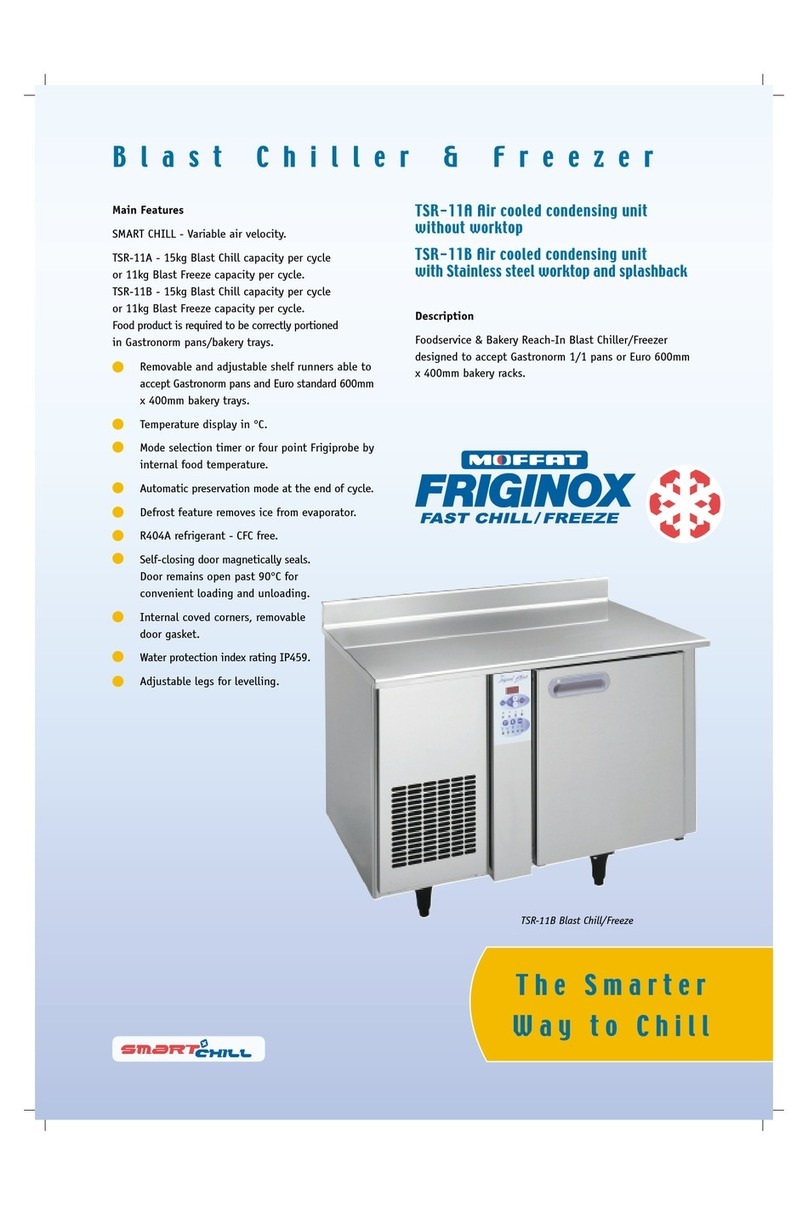
Moffat
Moffat Friginox TSR-11A Specifications
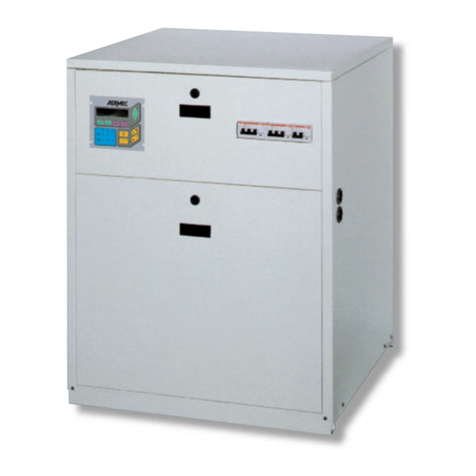
AERMEC
AERMEC NBW Series Technical and Installation Booklet
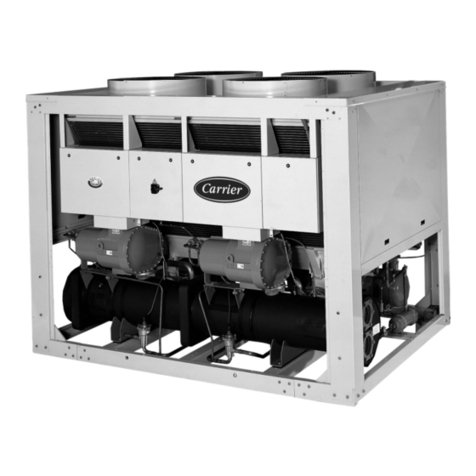
Carrier
Carrier 30GX Series Installation, operation and maintenance instructions
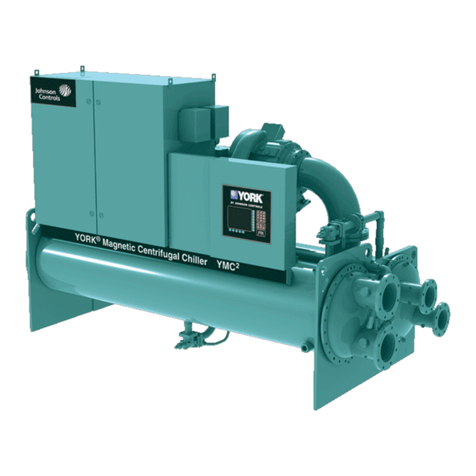
York
York YMC2 Operation and maintenance
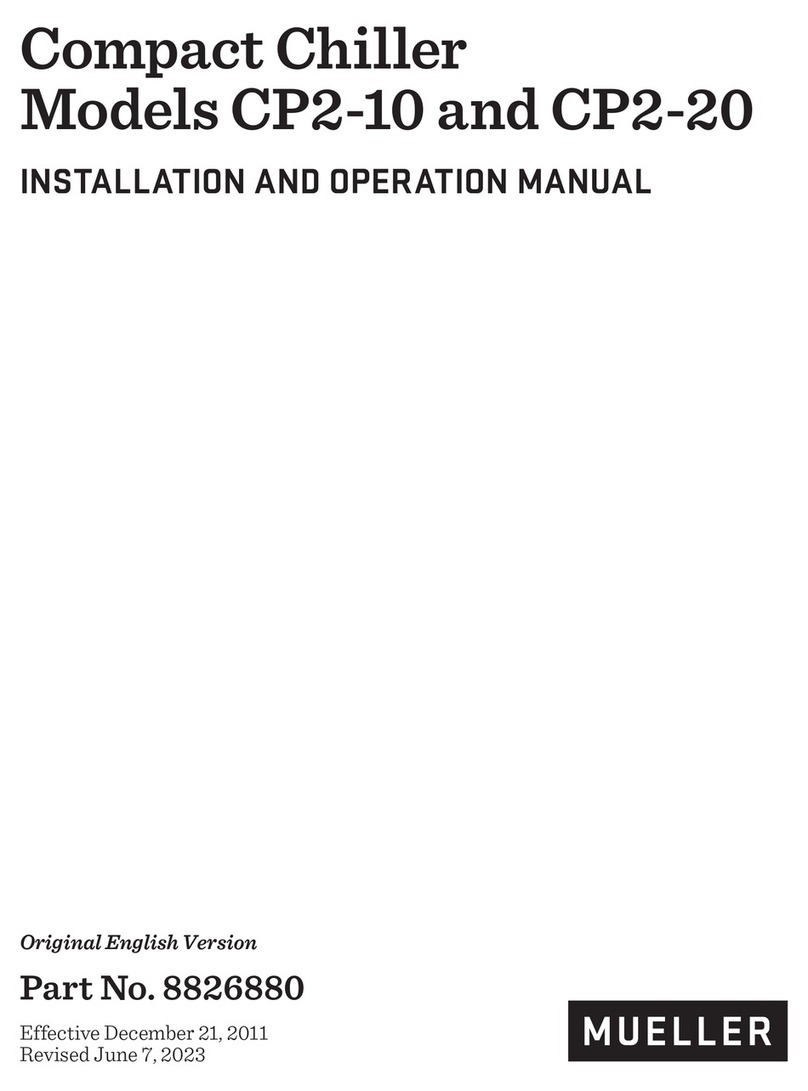
Mueller
Mueller CP2-10 Installation and operation manual
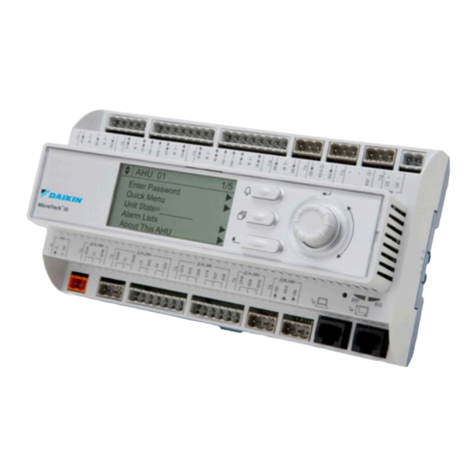
Daikin
Daikin McQuay MicroTech III manual