Navitron NT888G MK2 User manual

NAVITRON SYSTEMS LTD
NT888G MK2 AUTOPILOT
OPERATING MANUAL
17 The Tanneries
Brockhampton Lane
Havant, Hants, U.K. PO9 1JB
Registered in England No. 2607869
Tel: (023) 9249 8740
Fax: (023) 9249 8783
Int. Code: +44 23
Web: www.navitron.co.uk
1120/1

NT888G MK2 AUTOPILOT OPERATING MANUAL
IMPORTANT APPLICATION & OPERATING NOTE:-
The NT888G MK2 Autopilot System is Type Approved and Wheelmarked
compliant with IMO A342 (ix) as amended by MSC 64/67 Annexe 3 which is
applicable to vessels up to 30 knots (non High Speed Craft).
It is also Type Approved for high Speed Craft (HSC) compliant with ISO 16329
to provide an overall speed application range for vessels to 70 knots.
Since the Control parameters – conventional displacement vessels versus High
Speed Craft – are very different, it is essential that the correct vessel type (DISP
or HSC) is correctly entered in the Autopilot SET UP Menu during installation
and calibration (see Section 2.16)
- Contents -
Section 1: Short Operating Instructions.
Section 2: Operator Controls and Sea Trials.
Section 3: Display Messages, Alarms and Status Indicators.
NB: Whilst all efforts have been made to ensure the safety and reliability of
the NT888G MK2 Autopilot system, it should be noted that the installation of
any such system should never be permitted to detract from the adequate
provision of sound and continuous watch keeping duties.

NT888G MK2 AUTOPILOT OPERATING MANUAL
Section 1: Short Operating Instructions.
1.1 Control Unit Display Data & Initial Control Settings.
1.2 Switching to Standby or OFF.
1.3 Engaging Autopilot (ON).
1.4 Adjusting Steering Performance (Manual Adjustment of Controls).
1.5 Matching Heading Steered with Heading Set.
1.6 Avoiding Unnecessary Rudder Correction.
1.7 Altering Course to a New Heading.
1.8 The Rudder Limit Control.
1.9 Programmable Automatic Rate of Turn Control.
1.10 Programmable Automatic Radius of Turn.
1.11 Adjusting Overshoot and Undershoot.
1.12 Using the Track Function.
1.13 Cancelling an Audible Alarm.
1.14 Testing Alarms.
1.15 Keypad Turns:-
(i) ‘U’ Turn.
(ii) Next Course.
(iii) ±1° / ±5° Step Course Changes.
1.16 The CONTROLS Menu.
1.17 The LIMITS Menu.
1.18 The REMOTE Key.
1.19 The Illumination Control.
1.20 The CANCEL and CONFIRM Keys.
1.21 Using NT920NFU Dodge and Power Steer Functions (If fitted).
1.22 Using NT990FU Power Steer Functions (If fitted).
1.23 Using Proprietary Power Steer & Override Functions

NT888G MK2 AUTOPILOT OPERATING MANUAL
Section 1: Short Operating Instructions.
These Short Operating Instructions provide a quick reference guide to setting up and
operating the NT888G MK2 Autopilot. The locations in the manual where more
detailed descriptions can be found are shown against each heading in brackets, e.g.
(Section X.XX).
1.1 Control Unit Display Data & Initial Control Settings - (Section 2.4).
The NT888G MK2 Autopilot is Speed Adaptive and – provided it is used in adaptive
mode and calibrated for the correct vessel type (DISP or HSC per 2.16) – will
automatically set its own control parameters for optimum steering performance.
Adaptive/non adaptive operation is selectable via CONTROLS key operation and
entry to the Controls Menu which is shown on the right of the main display.
Unless alternative settings have been established from experience during sea
passages with the Autopilot in operation, selection of the non adaptive mode will be
necessary to enable primary control settings (YAW, RUDDER, COUNTER RUDDER)
to be manually adjusted.
If conducting first time sea trials or - if unfamiliar with NT888G MK2 Autopilot
operation – see section 2.4.
1.2 Switching to STANDBY (or OFF) – (Section 2.1).
(i) Use the STANDBY key to enter the
STANDBY Mode.
(ii) Wait for self test to complete which will be
followed by the operational Control Unit
display screen.
In this mode, the Control Unit tracks and displays “Actual Heading”, Rate of Turn
(“ROT”) and “Rudder Angle” etc. and will continue in a tracking mode until the
Autopilot is engaged (“ON” key operation).
NB. The Autopilot can be switched OFF at any time by a continuous 2 second “OFF”
key operation.

NT888G MK2 AUTOPILOT OPERATING MANUAL
1.3 Engaging Autopilot (ON) – (Section 2.2 & 2.18).
The NT888G MK2 Autopilot can only be switched ON via the Standby condition thus
switching directly from OFF to ON is not possible.
To engage the Autopilot:-
(i) Steady the vessel on the required heading.
(ii) Use the “ON” key to engage the Autopilot.
NB. Single press of the “ON” key engages the Autopilot in Rudder control mode only, a
continuous 2 second press is Thruster mode only and a further 2 second
continuous press is Rudder AND Thruster mode.
1.4 Adjusting Steering Performance – (Section 2.19 – 2.22)
(Manual Adjustment of Controls).
If the Autopilot has been programmed with Speed Adaptive values based on earlier
sea trials or prior seagoing operational performance – no initial adjustment will be
required.
If no predetermined values have been stored, it will not be possible to enter - or
operate – in the Adaptive Mode (until calibrated per Section 2.29) and manually
entered operational control settings will be required via access to the Controls Menu
as follows:-
(i) With the Autopilot in the “STANDBY” mode
(access also available from “ON” or “Track”
modes), use the “CONTROLS” key to display the
Controls Menu.
(ii) Note the position of the blue band highlighting the
Controls Menu item “ADAPT ON/OFF” which
should be “OFF” in the absence of Adaptive Data.
Also, when no Speed Data is available, non
Adaptive (OFF) Autopilot operation is necessary
and PID Control is required involving manual
RUDDER, YAW & COUNTER Control adjustment.
(iii) Select ADAPT “OFF” via the rotary (+/-) illum.
control then note that the “CONTROLS” key is
again used to select RUDDER, YAW or
COUNTER (as required) so that adjustment can
be made to the value (1 to 9) of the selected
control via the rotary (+/-) illum. control.
NB. The Controls Menu display will timeout and revert to the normal operational
display if no adjustments are made for a period of 30 seconds. Re-entry to
the Controls Menu is by “CONTROLS” key operation.

NT888G MK2 AUTOPILOT OPERATING MANUAL
1.4 Adjusting Steering Performance – (Section 2.19 – 2.22) … (Continued).
(Manual Adjustment of Controls).
(iv) Use the “CONTROLS” key to select “YAW” and
set a value of “1” using the rotary (+/-) illum. key.
(v) Use the “CONTROLS” key to select “COUNTER”
and set a value of “1” using the rotary (+/-) illum.
key.
The vessel should now be steady on the required heading under manual steering
(Autopilot STANDBY Mode) or engaged (Autopilot ON).
(vi) Check that the Autopilot is ON (engaged) and note the steering
performance in terms of Understeer or Oversteer as follows:-
(vii) Use the “CONTROLS” key to select “RUDDER” and increase or
decrease the Rudder Control value (1 to 9) using the rotary (+/-) illum.
key to optimise the straight line steering performance in terms of
Understeer/Oversteer.
Large deviations or protracted
periods off the Heading Set due to
insufficient rudder application in
response to Yaw: -
Typical stretched
‘S’ characteristic
of Understeer
Action required: -
Increase Rudder
Control Setting.
(Clockwise)
Understeer Characteristics Oversteer Characteristics
Autopilot applying too much rudder
causing vessel ‘weave’ which may
increase to a tight ‘S’ pattern: -
Typical tight ‘S’
characteristic of
Oversteer
Action required: -
Reduce Rudder
Control Setting.
(Anticlockwise)

NT888G MK2 AUTOPILOT OPERATING MANUAL
1.5 Matching Heading Steered with Heading Set (Section 2.23).
When the Autopilot is engaged, the AUTOTRIM (Automatic Permanent Helm – APH)
function continuously monitors any long-term differences between the heading set
and the mean course actually steered. Any long-term difference is automatically
adjusted by the Autotrim (APH) function applying the appropriate amount of
permanent helm.
To speed up this automatic (APH) process: -
(i) Wait for vessel to settle on steady heading.
(ii) Single Press the AUTOTRIM SET key.
(Pressing and holding down the AUTOTRIM key for 5 seconds will switch the
AUTOTRIM function OFF as confirmed by illumination of the corner keypad LED).
1.6 Avoiding Unnecessary Rudder Correction (Section 2.25).
Frequent rudder movements when the vessel is yawing either side of the set heading
in a seaway indicates that the autopilot sensitivity is set too high for the sea
conditions being experienced. This can cause premature wear of the steering gear
and, whilst an automatically adjusted feature of the full Adaptive operating mode, will
require manual adjustment in the non Adaptive (PID) mode.
To manually decrease the frequency of rudder movement due to yawing: -
(i) Use the “CONTROLS”key to display the controls menu.
(ii) Use the “CONTROLS” key again to select “YAW” and increase the Yaw
value (1 to 9) using the rotary (+/-) illum. key.
(The normal operational display will resume automatically after a
timeout period of 30 secs.).
NB. Don’t forget to reduce the YAW setting when yawing decreases as the
vessel moves from rougher to calmer sea conditions.
1.7 Altering to a New Heading (Section 2.36).
In full Adaptive operational mode, a course change executed by the Autopilot system
may be controlled by preprogrammed Rate or Radius of Turn data.
These limiting factors can also apply in the non Adaptive (PID) operating mode
provided the Autopilot CONTROLS and LIMITS menus have been programmed and -
for Radius controlled turns - that Speed (SOG) input data is available.
If the existence of safe limiting factors is uncertain, the RUDDER LIMIT function –
which otherwise limits the maximum permissible angle of rudder applied by the
Autopilot – can be employed to produce small rudder angles/slow turns.

NT888G MK2 AUTOPILOT OPERATING MANUAL
1.7 Altering to a New Heading (Section 2.36) … (Continued).
To alter course to a new heading using the Autopilot: -
(i) Use the “LIMITS” key to enter the Limits Menu where the Rudder Limit
value is the first item shown and should now be highlighted by a blue
band.
NB. Each parameter in the Limits Menu is selectable via step by step
use of the LIMITS keypad and is confirmed by the blue band moving to
the appropriate box.
(ii) Set the Rudder Limit value (RUD LT) to a safe value (range 5° to 50°)
via the rotary (+/-) illumination control.
(iii) Turn the Course Selector (“Set Course” Control) clockwise to alter
course to Starboard or anticlockwise to alter course to Port. The Port &
Starboard demand chevrons will flash & an audible bleep will be heard.
(iv) Press the “CONFIRM” key to execute the turn. As a safety precaution to
prevent accidental course selector operation the course change will be
cancelled if the confirm key is not pressed within the timeout period
(nominally 30 sec). Without confirmation within 30 seconds the new
course demand will automatically cancel and the original set course will
be maintained. Pressing the “CANCEL” key will also cancel the course
change.
NB. The Autopilot will order the vessel to turn in the same direction as the
Course Selector knob is turned for any amount of Course change up to 359°.
The result is that if the course change is more than 180° the vessel will
continue to take the “long way” round to the new course.
1.8 Adjusting Rate of Turn using the Rudder Limit Control (Section 2.31).
To adjust (simple) Rate of Turn when altering course using the Autopilot: -
If vessel turns too quickly - reduce Rudd Limit (RUD LT) value 1 - 9 per 1.7 (ii).
If vessel turns too slowly - increase Rudd Limit (RUT LT) value 1 - 9 per 1.7 (ii).
1.9 Programmable Automatic Rate of Turn (ROT) Control (Section 2.6, 2.32 & 2.33).
The Autopilot Rate of Turn (ROT) control function can operate – as programmed via
the CONTROLS and LIMITS Menus – in both the Adaptive and non Adaptive (PID)
modes:-
To select Rate of Turn control vs Radius of Turn:-
(i) Use the “CONTROLS” key to select the Controls Menu.
(ii) Use the “CONTROLS” key again to step through the Menu listing until
the “TURN TYPE” box is higlighted.

NT888G MK2 AUTOPILOT OPERATING MANUAL
1.9 Programmable Automatic Rate of Turn (Section 2.6, 2.32 & 2.35) … (Continued).
(iii) Use the rotary (+/-) illumination control to select “ROT”.
To select required Rate of Turn (6 – 300 deg/min or 0.1 – 5 deg/sec):-
NB. ROT can be expressed (and displayed) in °/min or °/sec as preferred and can be
selected accordingly via the Set Up Menu. (Section 2.6(v) refers).
(iv) Use the “LIMITS” key to display the Limits Menu.
(v) Use the “LIMITS” key again to step through the Menu listing until the
“ROT°/S” box is highlighted.
(vi) Use the rotary (+/-) illumination control to select the required ROT in
°/min or °/sec (noting that 6–300°/min = 0.1-5°/sec).
Using the Turn Rate control.
Provided the Rate of Turn function is enabled and specified with a value in °/min or
°/sec, it will automatically control the vessel’s rate of turn during course changes.
When the vessels Rate of Turn is being limited by this function the SET ROT display
box will flash alternating between the value set (i.e. 1°/SEC) and “MAX”. As the
vessel approaches the new set heading and the Rate of Turn decreases, the MAX
display indication will automatically extinguish.
NB. During Track Steering Mode using the HTC sentence (Section 2.9 & 2.38) it is
possible for the Track Controller to override the Autopilot programmed (internal)
value. However, this is only possible up to any maximum permissible ROT value set
within the Autopilot. In this (HTC sentence) Track Steering Mode, it is not possible to
manually Adjust ROT.
1.10 Programmable Automatic Radius of Turn (Section 2.6 & 2.34).
The Autopilot Turn Radius Control function can operate in both the Adaptive and non
Adaptive Modes but it is essential to note that Speed over the Ground (SOG) input
data must be present – without which Radius control will not exist.
To select Radius of Turn Control vs Rate of Turn:-
(i) Use the “CONTROLS” key to select the Controls Menu.
(ii) Use the “CONTROLS” key again to step through the Menu listing until
the “TURN TYPE” box is highlighted.
(iii) Use the rotary (+/-) illumination control to select “RAD”.
To select required Radius of Turn (0.1 - 9.9Nm):-
(iv) Use the “LIMITS” key to display the Limits Menu.
(v) Use the “LIMITS” key again to step through the Menu listing until the
“RAD:nm” box is highlighted.

NT888G MK2 AUTOPILOT OPERATING MANUAL
1.10 Programmable Automatic Radius of Turn (Section 2.6 & 2.34) … (Continued).
(vi) Use the rotary (+/-) illumination control to select the required Radius of
Turn between the limits 0.1–9.9Nm.
1.11 Adjusting Overshoot and Undershoot (Section 2.4 & 2.24).
This performance aspect is based on Counter Rudder Control settings and, if
operating in the full Adaptive mode, is unlikely to require manual adjustment.
If manual adjustment is required (more likely in the non Adaptive PID mode) the
“COUNTER” Rudder value is changed as follows:-
(i) Use the “CONTROLS”key to display the controls menu.
(ii) Use the “CONTROLS” key again to select “COUNTER” and increase or
decrease the value (1-9) using the rotary (+/-) illum. key based on the
following:-
To adjust overshoot (vessel goes past new heading) or undershoot (vessel stops
short of new heading) when altering course using the Autopilot: -
If vessel overshoots - increase COUNTER RUDDER value.
If vessel undershoots - reduce COUNTER RUDDER value.
1.12 Using the Track Function (Section 2.9 & 2.38).
The Autopilot is equipped with a comprehensive Track Steering facility which is
activated by operation of the “TRACK” key provided the Autopilot System is engaged
(ON) and suitable Track data is available from a proprietary approved GPS/Track
Control system/ECDIS etc.
Track Operation is confirmed by
corner LED illumination of the Track
key and additional display information
for TRACK Steering Mode.
Three Track sentence types are
accepted ($XXHTC, $XXHSC,
$XXAPB) all three of which provide
the “Heading to Steer” data required
for single or multi waypoint route
steering by the Autopilot system.
When operating in conjunction with an approved Track Control system sending the
comprehensive “HTC” sentence, complex manoeuvres based on externally ordered
ROT & Radius controlled turns to new headings can be acknowledged and executed
by the Autopilot.

NT888G MK2 AUTOPILOT OPERATING MANUAL
1.12 Using the Track Function (Section 2.9 & 2.38) … (Continued).
To engage the Track function:-
(It is assumed that valid track data is available to the Autopilot system).
(i) With the Autopilot engaged
(ON) use the “TRACK” key to
accept data.
NB. In the event that no data is
available, the “HCS fault: Track
steering failed. No input data”
alarm will be generated (visual
and audible).
(ii)
Valid Track data acceptance will
be confirmed below the Track
graphic as “HTC DATA”,
“HSC DATA” or “APB DATA” as appropriate and the New Heading to
Waypoint (NEW HDG TO WP) display area flashing accompanied by the
red and green control panel chevrons requesting Confirm or Cancel
action.
(iii) If the Track Mode Heading to Waypoint is to be accepted – use the
“CONFIRM” key.
(If the “Confirm” key is used, the vessel will immediately turn to take up
the ordered new Heading to Waypoint and the Track graphic will show
vessel icon left or right of heading with the error angle below).
If the Track Mode Heading to Waypoint is to be rejected – use the
“CANCEL” key.
(If the “Cancel” key is used, a silent period will follow beyond which the
Cancel/Confirm request will be repeated and this sequence will continue
until the Track Heading is accepted or Track Mode is set to “OFF”).
(iv) To disengage the Track Mode at any time, use the “TRACK” key when it
will be noted that the Track graphic will automatically be removed from the
Control Unit display and the corner LED in the “TRACK” key will turn off.
NB. Track data failure during Track Mode operation is signalled by a
Control Unit generated alarm. Further operational alarms requesting
Operator action (CONFIRM/CANCEL) will also be generated as follows:-
$XXHSC & $XXAPB Operation – Confirm/Cancel action required for any
New Heading to Waypoint change in excess of 10°.
$XXHTC Operation – No Cancel/Confirm action required – New Heading
change to next waypoint will be executed automatically.

NT888G MK2 AUTOPILOT OPERATING MANUAL
1.13 Cancelling an Audible Alarm (Section 2.8).
In Autopilot ‘ON’ mode a new (unacknowledged) alarm message will be shown
flashing accompanied by an audible alarm. Audible alarms can be acknowledged by
operation of the “TEST” key. Alarm conditions that persist will continue to be shown in
the alarm list.
Audible alarms may be permanently muted by 5 second continuous operation of the
“TEST” key confirmed by the alarm off icon in the bottom left display corner. Audible
alarms are re-enabled by further 5 second continuous operation of the “TEST” key.
NB. Audible alarms may be permanently muted but this function should be used with
extreme caution since a permanently muted alarm may result in a missed alarm
condition with dire consequences.
To cancel an audible alarm:-
(i)
Use the “TEST” key.
X 1
1.14 Testing Alarms (Section 2.8).
The alarms may be tested by double press of the
“TEST/OFF” keypad, if the alarm function is muted
audible alarms will be automatically re-enabled
X 2
To test Alarms:-
(i) Double press the “TEST/OFF” key.
(Each Control Unit keypad corner LED will now be illuminated in turn
accompanied at each step by audible alarm bleep).
1.15 Keypad Turns (Sections 2.11 & 2.36).
Two types of turn can be selected using the “U TURN” or “NEXT COURSE” keys as
required confirmed in either case by illumination of the corner LED as appropriate.
(i) “U TURN”(Section 2.11 & 2.36):-
Operation of this keypad makes the Autopilot ready to produce a 180° turn from
current heading (to reciprocal heading) which is executed when turn direction is first
specified by “CANCEL” (PORT) or “CONFIRM” (STBD) key operation followed by
second “CANCEL” (abort) or “CONFIRM” (execute U TURN) key use.
To use the “U TURN” function:-
Press the “U TURN” key confirmed by flashing
corner LED illumination.
(i)
NB. “U TURN” request cancelled - if required - by
second press of “U TURN” key.

NT888G MK2 AUTOPILOT OPERATING MANUAL
1.15 “U TURN” function (Section 2.11 & 2.36) … (Continued).
a) Use the “+” (STBD) or “-“ (PORT) “TURN” key to specify the direction of “U
TURN” required.
=
=
NB.
Unless U Turn follow up action is taken within 30 seconds, U Turn
selection will be cancelled.
b) Use the “+” (CONFIRM) or “-“ (CANCEL) “TURN” key to execute or cancel
the “U TURN” order.
(ii) “NEXT COURSE" (Section 2.11(ii))
Operation of this keypad allows a new (NEXT) course to be stored and shown on the
display in advance of actual turn to the next course. Once ready (Next Course stored)
CANCEL/CONFIRM key operation actions the turn to Next Course.
To use the “NEXT COURSE” function:-
a) Press the “NEXT COURSE” key confirmed
by flashing corner LED illumination.
NB. “NEXT COURSE” request cancelled - if
required - by 2nd press of “NEXT
COURSE” key.
b) Note the “NEXT COURSE” area of the
Control unit display and turn the SET
COURSE knob until the display shows
required “NEXT COURSE”.
c) Use the “+” (STBD) or “-“ (PORT) “TURN”
key to specify the direction of turn required to
the “NEXT COURSE” heading displayed.
d) Use the “+” (CONFIRM) or “-“ (CANCEL)
“TURN” key to execute or cancel the “NEXT
COURSE” order.
(iii) “±1° / ±5°” Step Turns (Section 2.13 & 2.36):-
Under normal operating conditions (no U TURN, NEXT COURSE or NEW COURSE
sequences in process) the “TURN” + (Stbd) or “TURN” – (Port) keys can be used to
order small permanent course changes in 1°/5° steps etc.

NT888G MK2 AUTOPILOT OPERATING MANUAL
(iii) “±1° / ±5°” Step Turns (Section 2.13 & 2.36) … (Continued):-
To use the “±1°/±5°” function:-
a) Use the “+” (STBD) or “-“ (PORT) “TURN” key
to specify the direction of turn required in single
presses (for 1° course change steps) or hold
the key down to produce an increase in the
new heading step values automatically from 1°
to 5° to 10° etc.
b) Note that the actual amount of course change
ordered using the “TURN” keys is always
confirmed by the new permanent heading
shown in the “SET COURSE” area of the
display.
1.16 The Controls Menu (Section 2.4).
This Menu can be conveniently displayed during normal “STANDBY” or “ON”
operating modes by use of the “CONTROLS” key:-
Entry to the CONTROLS Menu is confirmed by a listing
from “ADAPT” to “TURN TYPE” (as shown) and selection
of the parameter required is via further CONTROL key
operation.
When the required item is highlighted by the blue bar, the
value – or state – of that item is set by movement (+/-) of
the rotary illumination control.
NB. In the event that the CONTROLS Menu has been entered but no change has
been made for timeout period of 30 seconds, the display will revert automatically to its
normal operating mode.
1.17 The Limits Menu (Section 2.6).
This Menu can be conveniently displayed during normal “STANDBY” or “ON”
operating modes by use of the “LIMITS” key:-
Entry to the LIMITS Menu is confirmed by a listing from
“RUD LT” to “RAD:NM” (as shown) and selection of the
parameter required is via further LIMIT key operation
When the required item is highlighted by the blue bar, the
value – or state – of that item is set by movement (+/-) of
the rotary illumination control.
STEP ALIGN
002.5

NT888G MK2 AUTOPILOT OPERATING MANUAL
1.17 The Limits Menu (Section 2.6)…(Continued).
NB. In the event that the LIMITS Menu has been entered but no change has been
made for timeout period of 30 seconds, the display will revert automatically to its
normal operating mode.
1.18 The Remote Key (Section 2.10 & 2.40).
Where more than one Control Unit is installed in the Autopilot system, or, where
Remote Power Steer Controls are involved, the “REMOTE” key provides
unconditional Enable (Remote ON) or Disable (Remote OFF) legislation.
REMOTE On (corner LED on) – Remote Stations permitted to work.
REMOTE Off (corner LED off) – Remote Stations not permitted to work.
1.19 The Illumination Control (Section 2.5).
In the normal Autopilot Operating Mode, the rotary (+/-) illumination control is adjusted
clockwise (+) or anticlockwise (-) for brighter or dimmer control panel and display
illumination respectively.
When either the LIMITS Menu or CONTROLS Menu
is entered and displayed, the illumination control is
used to change the state of – or adjust the value of –
the Menu item selected.
1.20 The Cancel and Confirm Keys (Section 2.13).
The CANCEL (TURN/-) and CONFIRM (TURN/+) keys
are mainly concerned with new Autopilot headings
which may be automatically (Track Mode Waypoint
Steering etc.) or manually (Dodge/Custom Turns etc.)
entered.

NT888G MK2 AUTOPILOT OPERATING MANUAL
1.21 Using NT920NFU Dodge and Power Steer (if fitted).
NT920NFU Operating Instructions: -
NB. The NT920NFU(s) will only function when the Autopilot “REMOTE” key is set to
enable Remote inputs (REMOTE key corner LED on). If the “REMOTE” key is off
(no corner LED) the NFU(s) will be disabled.
DODGE MODE: -
(i) Check that the Autopilot “REMOTE” key is activated.
(ii) Select DODGE on the NT920NFU selector switch.
(Confirmed by illumination of DODGE READY LED).
(iii) Move and hold the NT920NFU Jog Lever right (STBD) or Left (PORT) to
apply corresponding rudder and override the Autopilot.
(iv) Release the Jog Lever to centre when ready for the Autopilot to return
the vessel to the original Autopilot heading.
NFU MODE: -
(i) Check that the Autopilot “REMOTE” key is activated.
(ii) Select NFU on the NT920NFU selector switch.
(Confirmed by illumination of the POWER STEER LED).
(iii) Move the NT920NFU Jog Lever Right (STBD) or Left (PORT) and
release the Jog lever to centre when the required angle of applied
rudder is attained.
(iv) Repeat Jog Lever operation as necessary to align the vessel on the new
heading required.

NT888G MK2 AUTOPILOT OPERATING MANUAL
1.21 Using NT920NFU Dodge and Power Steer (if fitted)…(Continued).
(v) Select DODGE or OFF on the NT920NFU selector switch to return
heading control to the Autopilot which will maintain the vessel on the
new (current) heading.
1.22 Using the NT990FU Power Steer (if fitted).
Engaging Follow Up Power Steer.
NB. The NT990FU will only function when the Autopilot “REMOTE” key is set to
enable Remote inputs (REMOTE key corner LED on). If the “REMOTE” key is off (no
corner LED) the NT990 FU(s) will be disabled.
(i) Check that the Autopilot “REMOTE” key is activated.
(ii) Press the ON/OFF key on the NT990 FU.
(iii) If the ALIGN LED flashes, move the lever in the direction towards the
flashing MAX LED to pick up the current rudder position.
(iv) When power steer mode is engaged the POWER STEER LED will
illuminate.
(v) Move the lever Port or Stbd to achieve the desired angle of Port or Stbd
rudder.

NT888G MK2 AUTOPILOT OPERATING MANUAL
1.22 Using the NT990FU Power Steer (if fitted) … (Continued).
Disengaging Follow Up Power Steer:-
(vi) Press the ON/OFF key on the NT990FU or use the “REMOTE” key on
the Autopilot Control Unit to disable Remote Station operation.
(The NT990 FU POWER STEER LED will extinguish, the OTHER
STATION LED will illuminate and the Autopilot will maintain the vessel
on the current heading).
1.23 Using Proprietary Power Steer and Override functions
(i) Standard Dodge, Non Follow Up & Follow Up Functions:-
Non Navitron (proprietary) Power steer Controls may be connected to the
Autopilot System and are discussed and detailed in Section TM3.4.1 – 4 of the
Installation & Technical manual
(ii) Override Power Steer Functions:-
Latched and Non Latched Override Power Steer controls allow the immediate
Override of the Autopilot System and are discussed and detailed in Section 2.43.

NT888G MK2 AUTOPILOT OPERATING MANUAL
Section 2: Operator Controls and Sea Trials.
Operator Controls and Displays Defined: -
2.1 The Autopilot STANDBY / OFF Key & Modes.
2.2 The Autopilot ON Key Modes (Rudder / Thruster).
2.3 The Adaptive & Non Adaptive (PID) Autopilot Modes.
2.4 The CONTROLS Menu.
(i) Adaptive / Non Adaptive Selection.
(ii) Rudder Control.
(iii) Yaw Control.
(iv) Counter Control.
(v) Autothrust.
(vi) Turn Type (ROT or RAD).
2.5 The Rotary (+/-) Illumination Control.
2.6 The LIMITS Menu.
(i) Rudder Limit.
(ii) Off Heading Alarm.
(iii) Course Comparator Alarm.
(iv) Watch Alarm.
(v) Rate of Turn (ROT) Calibration & Display (°/sec or °/min).
(vi) Radius of Turn (RAD) Calibration.
(vii) Step Heading Source Alignment.
2.7 The AUTOTRIM Key (Automatic Permanent Helm).
2.8 The Alarm TEST / OFF Key.
2.9 The TRACK Key.
2.10 The REMOTE Key.
2.11 The TURN MODE Keys.
(i) U TURN.
(ii) NEXT COURSE.
2.12 The Rotary SET COURSE Control.
2.13 The CANCEL & CONFIRM Keys.
2.14 The Control Unit Start Up Display (Splash Screen).
2.15 The Control Unit Operational Display.

NT888G MK2 AUTOPILOT OPERATING MANUAL
Section 2: Operating Controls and Sea Trials (Continued).
Sea Trials:-
2.16 Sea Trials and Autopilot Type Selection.
2.17 Mag/True Heading Assessment.
2.18 Autopilot Engagement (ON).
PID Adjustments for Adaptive Mode Calibration:-
2.19 Initial Course Keeping Performance.
2.20 Optimising the Rudder Control Setting.
2.21 Optimising the Rudder Control Band.
2.22 Loop Gain Calibration.
2.23 Autotrim (Automatic Permanent Helm) Assessment.
2.24 The Counter Rudder Control Setting.
2.25 Optimising the Yaw Control Setting.
Adaptive Mode Calibration:-
2.26 STW Speed Data Input (Speed through the Water).
2.27 SOG Speed Data Input (Speed over the Ground).
2.28 Draft Input (Laden State).
2.29 Calibration of Steering Performance & Override Controls vs Speed.
2.30 Calibration of Steering Performance vs Draft.
Adaptive & Non Adaptive (PID) Adjustments:-
2.31 Setting the Rudder Limit Control.
2.32 Setting Rate of Turn Control.
2.33 Setting Maximum Safe Rate of Turn.
2.34 Setting Radius of Turn Control.
2.35 Optimising the Off Heading Alarm.
2.36 Setting and Confirming New Autopilot Courses.
2.37 Setting the Watch Alarm Period.
2.38 The Track Function.
2.39 Manual & Auto Deviation Correction.
Optional Units:-
2.40 NT888G MK2 Second Station Control Units.
2.41 NT920 NFU Power Steering.
2.42 NT990 FU Power Steering.
2.43 Special Latched & Non Latched Power Steer Controls.
Table of contents
Other Navitron Autopilot System manuals
Popular Autopilot System manuals by other brands

Century
Century 2000 Pilots operating manual
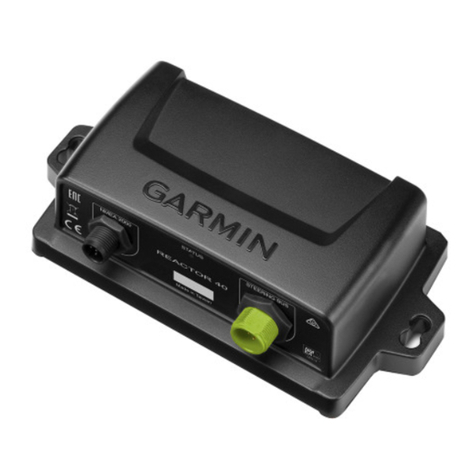
Garmin
Garmin GHP Reactor Mechanical installation instructions
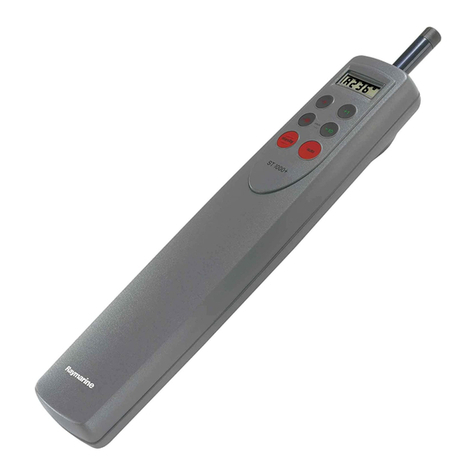
Raymarine
Raymarine ST1000 Plus Tiller Pilots Owner's handbook
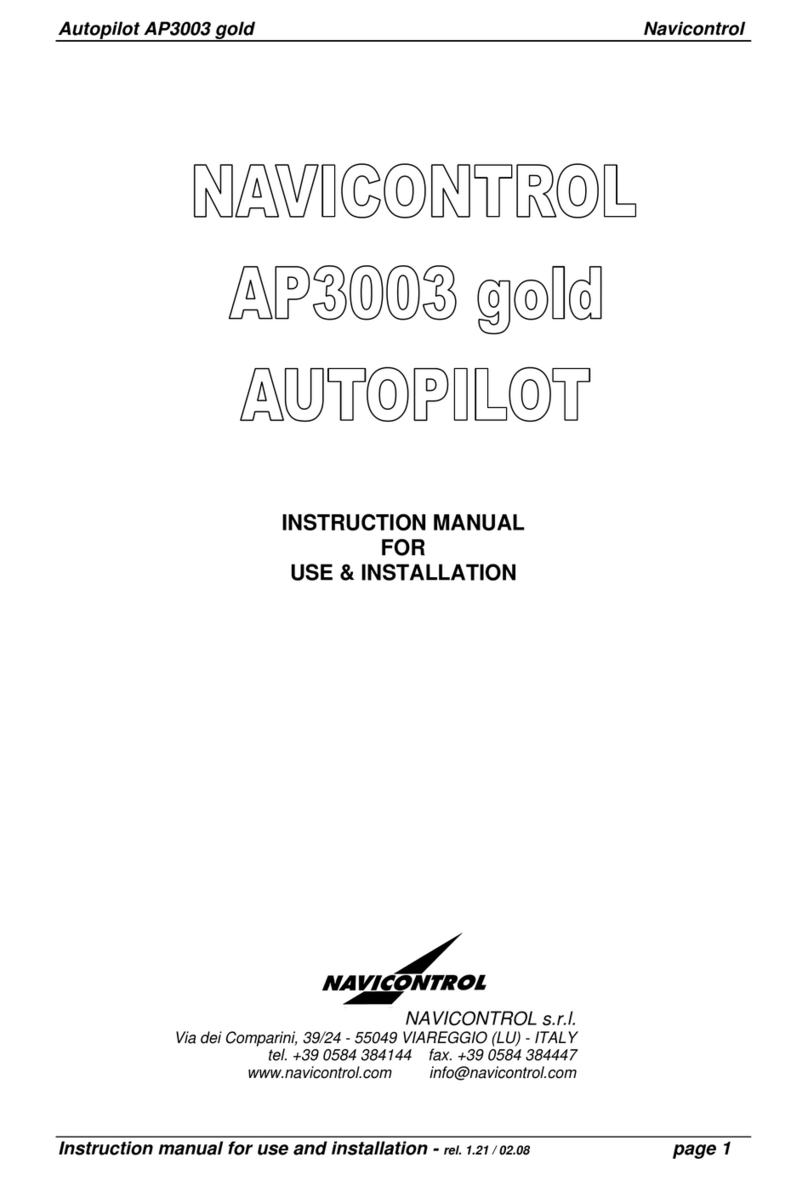
Navicontrol
Navicontrol AP3003 gold Instruction manual for installation and use
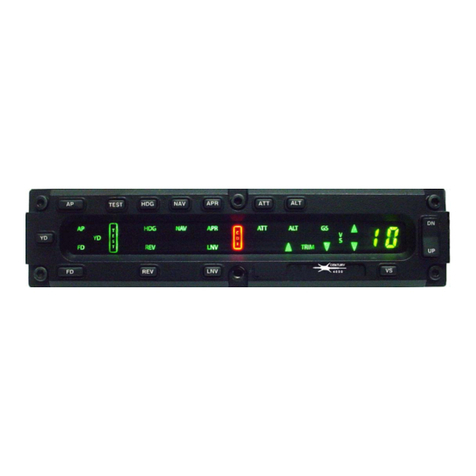
Century
Century 4000 Pilots operating manual
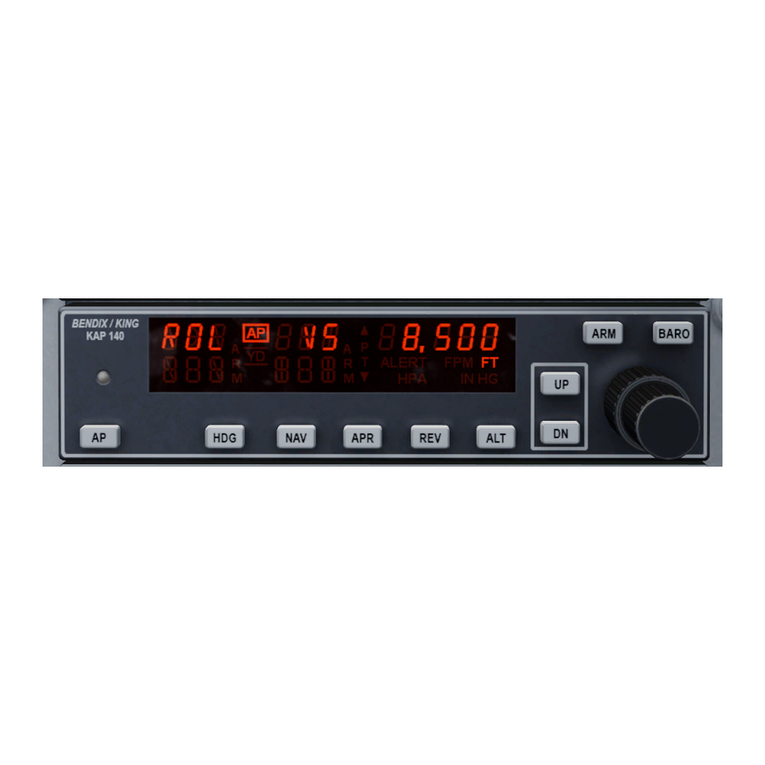
Honeywell
Honeywell KAP 140 installation manual