Newall C80 User manual

N
C80 Digital Readout System
Instruction Manual
Newall Measurement Systems Ltd

N
Notes

N

N
Display Keypad
Axis
Label
Displays
Axis
Select
Keys
Axis
Displays
Function Display
Units Key Mode Key Numeric
Keypad
Function
Keys
Navigation
Keys
Sleep Key Setup Key Enter
(Store Changes)
Clear Entry

Contents
2
N
Specifications . . . . . . . . . . . . . . . . . . . . . . . . . . . . 1-1
Electrical . . . . . . . . . . . . . . . . . . . . . . . . . . . . . . . . . 1-1
Physical. . . . . . . . . . . . . . . . . . . . . . . . . . . . . . . . . . 1-1
Environmental. . . . . . . . . . . . . . . . . . . . . . . . . . . . . 1-1
Input . . . . . . . . . . . . . . . . . . . . . . . . . . . . . . . . . . . . 1-2
Resolutions . . . . . . . . . . . . . . . . . . . . . . . . . . . . . . . 1-2
Connections . . . . . . . . . . . . . . . . . . . . . . . . . . . . . 2-1
Cable connections. . . . . . . . . . . . . . . . . . . . . . . . . . 2-1
Mountings . . . . . . . . . . . . . . . . . . . . . . . . . . . . . . . 3-1
Arm mounting (non-adjustable). . . . . . . . . . . . . . . . 3-1
Arm mounting (adjustable) . . . . . . . . . . . . . . . . . . . 3-1
Face mounting (adjustable). . . . . . . . . . . . . . . . . . . 3-1
Lathe mounting (adjustable) . . . . . . . . . . . . . . . . . . 3-2
Lathe mounting (adjustable) . . . . . . . . . . . . . . . . . . 3-2
Display and keypad. . . . . . . . . . . . . . . . . . . . . . . . 4-1
Display . . . . . . . . . . . . . . . . . . . . . . . . . . . . . . . . . . 4-1
Using the keypad . . . . . . . . . . . . . . . . . . . . . . . . . . 4-1
Set up . . . . . . . . . . . . . . . . . . . . . . . . . . . . . . . . . . . 5-1
Setup mode. . . . . . . . . . . . . . . . . . . . . . . . . . . . . . . 5-1
Machine type. . . . . . . . . . . . . . . . . . . . . . . . . . . . . . 5-2
Encoder. . . . . . . . . . . . . . . . . . . . . . . . . . . . . . . . . . 5-2
Radius / diameter . . . . . . . . . . . . . . . . . . . . . . . . . . 5-3
Direction . . . . . . . . . . . . . . . . . . . . . . . . . . . . . . . . . 5-3
Error compensation. . . . . . . . . . . . . . . . . . . . . . . . . 5-3
RS232 options. . . . . . . . . . . . . . . . . . . . . . . . . . . . . 5-9
Axis summing . . . . . . . . . . . . . . . . . . . . . . . . . . . . .5-12
Zero approach . . . . . . . . . . . . . . . . . . . . . . . . . . . . .5-12
Taper display axis . . . . . . . . . . . . . . . . . . . . . . . . . .5-12
Reset . . . . . . . . . . . . . . . . . . . . . . . . . . . . . . . . . . . .5-13
Store . . . . . . . . . . . . . . . . . . . . . . . . . . . . . . . . . . . .5-13
Standard functions . . . . . . . . . . . . . . . . . . . . . . . .6-1
Setting the datum for each axis. . . . . . . . . . . . . . . .6-1
Digifind. . . . . . . . . . . . . . . . . . . . . . . . . . . . . . . . . . .6-1
Centerfind . . . . . . . . . . . . . . . . . . . . . . . . . . . . . . . .6-2
Special functions. . . . . . . . . . . . . . . . . . . . . . . . . .7-1
Mill functions . . . . . . . . . . . . . . . . . . . . . . . . . . . . . .7-1
Lathe functions . . . . . . . . . . . . . . . . . . . . . . . . . . . .7-1
Generic functions. . . . . . . . . . . . . . . . . . . . . . . . . . .7-1
Menu function . . . . . . . . . . . . . . . . . . . . . . . . . . . . .7-2
Mill functions . . . . . . . . . . . . . . . . . . . . . . . . . . . . .8-1
Bolt hole circle . . . . . . . . . . . . . . . . . . . . . . . . . . . . .8-1
Arc contouring . . . . . . . . . . . . . . . . . . . . . . . . . . . . .8-3
Line hole . . . . . . . . . . . . . . . . . . . . . . . . . . . . . . . . .8-5
Polar coordinates. . . . . . . . . . . . . . . . . . . . . . . . . . .8-7
Lathe functions . . . . . . . . . . . . . . . . . . . . . . . . . . .9-1
Taper . . . . . . . . . . . . . . . . . . . . . . . . . . . . . . . . . . . .9-1
Tool offsets . . . . . . . . . . . . . . . . . . . . . . . . . . . . . . .9-2
Summing . . . . . . . . . . . . . . . . . . . . . . . . . . . . . . . . .9-4
Vectoring . . . . . . . . . . . . . . . . . . . . . . . . . . . . . . . . .9-5

3
N
Generic functions . . . . . . . . . . . . . . . . . . . . . . . . . 10-1
Sub-datums. . . . . . . . . . . . . . . . . . . . . . . . . . . . . . . 10-1
Jobs. . . . . . . . . . . . . . . . . . . . . . . . . . . . . . . . . . . . . 10-3
Troubleshooting . . . . . . . . . . . . . . . . . . . . . . . . . . 11-1
Cleaning. . . . . . . . . . . . . . . . . . . . . . . . . . . . . . . . . 12-1

Specifications
1-1
N
Specifications
This chapter details the specifications for the C80.
Electrical
EMC compliance
BS EN 61000-6-4:2001
BS EN 61000-6-2:2001
Power supply unit (supplied)
100 – 240V (47 – 63Hz)
External switch-mode
Conforms to Low Voltage Directive
EN 60 950-1:2001
Physical
Height
265mm (10.43”)
Width
180mm (7.09”)
Depth
(not including connectors)
50mm (1.97”)
Weight
2.9kg (6.38lb)
Environmental
Operating temperature
0 to 45°C
Storage temperature
−20 to 70°C
Environmental conditions
Indoor Use, IP20 (IEC 529)
Relative humidity
Maximum 80% for temperatures up to 31°C decreasing linearly
to 33% at 45°C

Specifications
1-2
N
Disposal
At the end of its life, you should dispose of the C80 system in a
safe manner applicable to electronic goods.
Do not burn.
The casework is suitable for recycling. Please consult local
regulations on disposal of electrical equipment.
Input
Spherosyn or Microsyn encoders.
Resolutions
Spherosyn or Microsyn 10
(menu selection)
5µm (0.0002”)
10µm (0.0005”)
20µm (0.001”)
50µm (0.002”)
Microsyn 5
(menu selection)
1µm (0.00005”)
2µm (0.0001”)
5µm (0.0002”)
10µm (0.0005”)
Spherosyn and Microsyn are registered trademarks of Newall
Measurement Systems Limited.
Newall Measurement Systems Limited reserves the right to
make changes to this document.

Connections
2-1
N
Connections
This chapter shows the cable connections for the C80.
Cable connections
Power Indicator Lamp
2.5mm Power Inlet
15 Vdc ±10% @1A
Equipotential Terminal
(Should be grounded to
machine, using the
lead provided)
RS232 Connection
Cable Anchor
(The power cable should
be secured)
Blanking Plug
(Do not remove these, as they
prevent you accidentally
connecting incorrect encoders)
Encoder Inputs
9-way ‘D’
(All plugs should be
screwed finger tight)

Connections
2-2
N
You can only use the C80 with Newall Spherosyn and Microsyn
analogue encoders.
You need to ensure that:
• You secure all the cables to prevent the connectors from
dropping into hazardous positions (for example the floor or
coolant tray) when you unplug them.
• You route all the cables to prevent them from being caught
on moving parts.
• The C80 is grounded to the machine, using the braided
grounding lead provided, before you turn on the machine
supply.
• You turn off the power by disconnecting the power supply
connector, before you connect the encoder.
Do not connect this unit directly to the mains supply.
If your Newall encoder is not fitted with a D-type connector, then
you can buy an adaptor cable (part no. 307-80980). Contact
your supplier for details.

Mountings
3-1
N
Mountings
This chapter shows the various options for mounting the C80.
You can mount the C80 in a variety of ways. The one that you
use depends on the mounting assemblies that you purchased
with the unit:
Arm mounting (non-adjustable)
Arm mounting (adjustable)
Face mounting (adjustable)
Mounting Arm Assembly
UK part no. 294-35675
US part no. FX0000SS-N
M10 stud & fixings,
supplied as standard
Arm Mount Adjustable Pivot
Assembly
Part no. 600-80290
Mounting Arm Assembly
UK part no. 294-35675
US part no. FX0000SS-N
Face Mount Adjustable
Pivot Assembly
Part no. 600-80270

Mountings
3-2
N
Lathe mounting (adjustable)
with arm assembly Lathe mounting (adjustable)
Arm Mount Adjustable Pivot
Assembly
Part no. 600-80290
Lathe Headstock with Arm
Assembly
UK part no. 600-80300
US part no. FX000LHM-N
Lathe Carriage Mount with
Arm Assembly
UK part no. 600-80310
US part no. FX000LCM-N
Lathe Mount Adjustable
Pivot Assembly
Part no. 600-80280
Lathe Carriage
Assembly
Part no. 294-61695
Lathe Headstock
Mount Assembly
Part no. 294-60675

Display and keypad
4-1
N
Display and keypad
This chapter explains how to interpret the display and use the
keypad.
You should refer to the diagrams at the front of this manual for
information on the layout of the display and keypad.
Display
Axis displays
The three Axis displays normally show the positions of the X, Y
and Z axes.
The three Axis Label displays normally show X, Y and Z, (in
Lathe Mode X, Z and Z’).
Function display
While any axis is moving, the Function display shows the
Feedrate of the fastest moving axis. The feed indicator next to
the display is illuminated. The feedrate is displayed in mm/sec
(to a resolution of 0.5) or inches/min (to a resolution of 1.0).
If the lathe indicator is illuminated, then the lathe functions are
available; if the mill indicator is illuminated, then the mill
functions are available; if the lathe and mill indicators are
illuminated, then both the mill and lathe functions are available.
During Setup and Special Functions, the displays may show
information other than that described on this page. See the Set
up and Special functions chapters of this manual for further
information.
Using the keypad
You use the keypad to enter data and control information for the
C80. The keys can have different functions depending on the
operating mode, but in normal operation the keys work as
follows:
Unit Key. Toggles the display units between inches and
millimetres.
Mode Key. Toggles the C80 between Absolute Mode and
Incremental Mode.
Absolute mode
In this mode, the C80 displays the positions of the three axes
relative to a fixed datum.
Incremental mode
In this mode, the C80 displays each position relative to the last
position. This is also known as point-to-point use.
At the beginning of each working session, set the
datum in Absolute Mode, then switch the C80 to
Incremental Mode. By using the C80 in this way, you
can return the machine to its absolute datum at any
time, simply by switching back to Absolute Mode.

Display and keypad
4-2
N
Sleep mode
Press the [Sleep Key] to temporarily turn off the displays and
the keypad.
While the unit is in Sleep Mode, all the settings are preserved,
but the positions of the three axes are updated.
If you move any of the axes while in Sleep Mode, the centre
display shows ‘diSPLACd’.
If someone touches any of the keys, the centre display shows
‘touchEd’.
See the Set up and Special functions chapters of this
manual for more explanation of the use of the
Navigation and Function Keys.

Set up
5-1
N
Set up
This chapter describes how to set up the C80.
Setup mode
Normally, you only need to set up the C80 once. You may find
that the factory default settings are suitable so you do not need
to change them.
To enter Setup Mode:
1. Leave any Special Function that is running.
2. Press [set up].
The centre display shows ‘SEt Up’.
3. Press the up or down navigation key to cycle through the
list of options.
The following table lists the options. The following sections
describe each of the options in detail.
The options available depend on the setting of other options. For
example, the Zero Approach Limit option is not present if Zero
Approach is off.
Option Default Display
Machine Type Generic gEnEric
Encoder Type all axes: Spherosyn SPHEroSn
Encoder Resolution all axes: 0.005mm 0.005
Radius / Diameter all axes: Radius rAD
Direction all axes: 1 dir. 1
Error Compensation all axes: Off Err OFF
Linear Compensation see note below
Segmented
Compensation see note below
Axis Summing X and Z’ axes Addition
RS232 Options None nOnE
Serial Rate 1.0 1.0
Baud Rate 9600 9600
Parity None nOnE
Zero Approach On / Off all axes: Off ZErO OFF
Zero Approach Limit see note below
Taper Display Axis X axis tAPEr On
Reset rESEt
Store StorE
Option Default Display

Set up
5-2
N
The following instructions are important and should be
followed carefully.
When you have finished setting all the options:
1. Press the down navigation key until ‘StorE’ appears in
the middle display.
2. Press [ent] to store any changes that you have made.
The middle display shows ‘StorEd’ for a few seconds as
your settings are stored.
The C80 leaves Setup Mode.
Alternatively, you can press [set up] at any time to leave the
Setup Mode and abandon any changes.
Machine type
You use this option to choose whether the special functions for
Mill or Lathe are available.
There are three possible settings:
Press the Select Key next to the ‘t’ to cycle through these
settings.
Encoder
The Encoder settings must match the actual encoder in use,
or the C80 will not display correctly.
Encoder type
There are three possible settings for each axis:
Press the Select Key next to the ‘X’, ‘Y’ or ‘z’ to cycle through
these settings.
Encoder resolution
The Resolution settings available for each axis depend on the
encoder type and the [in/mm] setting.
Generic gEnEric all functions available
Mill miLL mill functions only
Lathe LAtHE lathe functions only
Spherosyn SPHEroSn
Microsyn 10 uSn 10
Microsyn 5 uSn 5
Display Spherosyn Microsyn
10 Microsyn
5
µm mm in
1 0.001 0.00005 X
2 0.002 0.0001 X

Radius / diameter
5-3
N
Press the Select Key next to the ‘X’, ‘Y’ or ‘z’ to cycle through
the available settings for each axis.
Radius / diameter
The Diameter setting is useful for lathes, and other turning
applications to display the diameter reading rather than the
radius.
When you select the Diameter setting the C80 displays double
the actual movement on any axis.
There are two settings for each axis:
Press the Select Key next to the ‘X’, ‘Y’ or ‘z’ to cycle through
these settings.
Direction
You use the Direction setting to match the C80 to the actual
direction of travel of any axis.
There are two settings for each axis: ‘dir. 0’ and ‘dir. 1’.
Press the Select Key next to the ‘X’, ‘Y’ or ‘z’ to cycle through
these settings.
The Direction setting is arbitrary. You should set it to whichever
option makes most sense for the machine.
The Direction depends on where the scale is mounted.
Error compensation
Your digital readout (DRO) system helps you to improve
productivity. It decreases the number of scrapped parts, as you
no longer have to be concerned about making mistakes related
to counting the revolutions on the dials. Your DRO system also
helps to eliminate some errors related to ballscrew backlash.
Your DRO system will operate to its published accuracy,
provided all components are in working order and properly
installed. Field calibration is not necessary.
Accuracy problems with machined parts may be caused by
machine error, DRO system error, or a combination of both. The
first step in determining the source of error is to check the DRO
system. You do this by comparing the movement of the Newall
reader head to the position reading shown on the display. You
5 0.005 0.0002 X X X
10 0.01 0.0005 X X X
20 0.02 0.001 X X
50 0.05 0.002 X X
Radius rAd
Diameter diA
Display Spherosyn Microsyn
10 Microsyn
5
µm mm in

Set up
5-4
N
need a high accuracy standard, such as a laser interferometer.
You can use a dial indicator to check short distances, but a laser
provides the best results. If you have to use a dial indicator, be
sure it is the highest available accuracy.
To check the accuracy of the DRO system:
1. Place the target of the laser or the needle of the dial
indicator directly on the Newall reader head.
It is absolutely critical that you take the readings directly
from the Newall reader head.
If you have to use a dial indicator, be sure that the needle of
the indicator is perpendicular to the reader head and not
angled.
If you take readings anywhere else on the machine,
machine errors may distort the results.
2. When the reader head moves, the movement registers on
the laser / indicator and DRO display.
3. Set the laser / dial indicator and DRO display position
displays to 0.
4. Make a series of movements and compare the position
readings between the laser / dial indicator and the DRO
display.
If the readings match within the accuracy specificed, then
you know that the DRO system is operating properly. If this
is the case, you can proceed to the next step: evaluating the
machine errors. If the readings do not match, you must
repair the DRO system before proceeding with error
compensation.
To evaluate machine errors:
1. Put the laser target / dial indicator on the part of the
machine where the machining is done.
2. Make a series of movements and compare the position
readings between the laser / dial indicator and the DRO
display.
The difference between the laser / dial indicator reading
and the reading on the DRO display is your machine error.
3. Plot the machine error along the entire axis of travel to
determine the nature of the error.
If it is a linear error, you can use linear error compensation.
If the error is not linear, you should use segmented error
compensation.
There are many types of machine error, including pitch, roll,
yaw, flatness, straightness, and Abbe error. The diagrams below
demonstrate these errors.

Error compensation
5-5
N
Way errors
Abbé error
There are three settings for each axis:
Press the Select Key next to the ‘X’, ‘Y’ or ‘z’ to cycle through
these settings.
Once you have set the error compensation you want to use on
all the axes, press the down navigation key. The middle display
changes to ‘Err SEt’.
If you set one or more axes to Segmented Error
Compensation, or Linear Error Compensation, then your
next set up option is to configure the compensation for each of
those axes.
If you apply Error Compensation, then you must ensure that it
is absolutely correct. If it is not correct, then errors could be
increased rather than reduced.
Once you have set up the Error Compensation, we advise you
to check its effect in normal operation.
Segmented error compensation
In this mode, you can break down the scale travel for each axis
into as many as 99 user-defined segments, with each segment
having its own correction factor. The correction factors are
Pitch
Axis
Yaw
Axis
Typical Yaw
Deviation Straightness
Roll Axis
Travel
Flatness
Typical Pitch
Deviation
A
B
C2
C2
B2
A2
B1
C1
B1
A1
C1
A1
Shown with encoder on concave side
of bearing path Shown with encoder on convex side of
bearing path
greater than
End Effector Linear
encoder
Encoder
End Effector Linear
encoder
Encoderless than
encoder
Off Err OFF
Segmented Compensation SEG Err
Linear Compensation Lin Err

Set up
5-6
N
calculated by the C80 by comparison against known standards
that you supply.
When you apply power, the display for any axis that is set to use
Segmented Compensation shows ‘rESEt’.
If the machine has not been moved since the power was turned
off, press [ce], and the C80 restores the last positions that were
recorded.
Alternatively, you can set each axis close to the Reference
Point, to within: 6.3mm (0.25”) for a Spherosyn encoder or
2.5mm (0.1”) for a Microsyn encoder, and press the Select Key
next to the ‘X’, ‘Y’ or ‘z’. The C80 re-establishes alignment with
the correction parameters.
You need not apply Segmented Compensation over the entire
scale length. You can apply it to a length of high importance, or
to just one segment.
To ensure that you apply the correct compensation, you should
always reset the datum when you turn on the C80.
If you set one or more axes to Segmented Error Compensation,
then you need to carry out the following procedure to configure
the compensation for each of those axes.
Identifying the correction parameters
The scale travel is broken down into a number of segments that
you define, each with its own correction factor, measured
against a high-accuracy standard. You need to identify the
following parameters:
You measure each Correction Point with respect to the
Starting Point, zero. You usually set this close to one end of the
scale. You can set the Reference Point anywhere along the
scale. It does not need to coincide with either the absolute
datum or any of the correction points. However, you may find it
convenient to make the absolute datum and the reference point
the same.
Setting the correction points
As you follow the procedure you must ensure that you always
approach the Starting Point, Correction Points and
Reference Point from the same direction. If you do not, then the
size of the tool or probe renders the measurement inaccurate.
1. Set one or more axes to Segmented Compensation as
described in Error compensation on page 5-3.
The display shows ‘Err SEt’.
Error
0
Starting point - zero
16
2
3
45
Travel
Reference point Correction points
Other manuals for C80
1
Table of contents
Popular Control Unit manuals by other brands
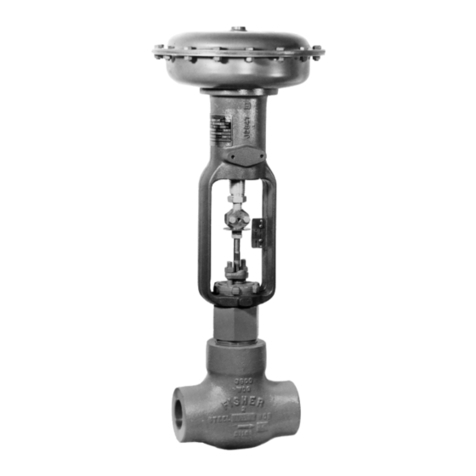
Fisher
Fisher D Series instruction manual
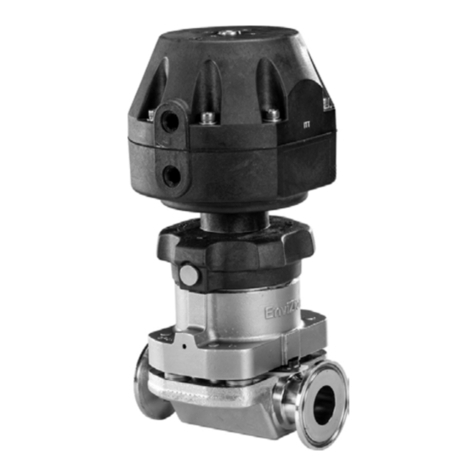
ITT
ITT Engineered Valves EnviZion Installation, operation and maintenance manual
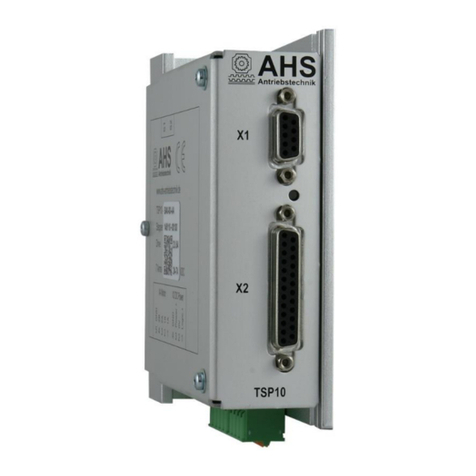
AHS Antriebstechnik
AHS Antriebstechnik 6410 Application note
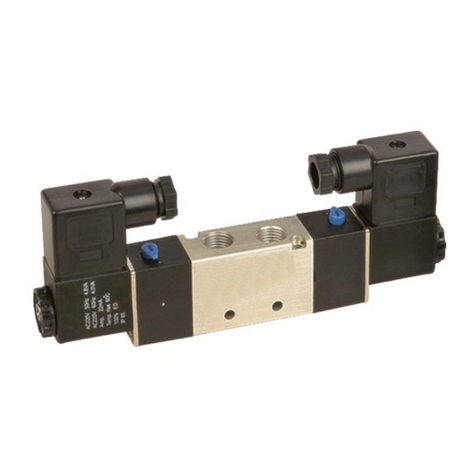
STC
STC 4V130P Series quick start guide
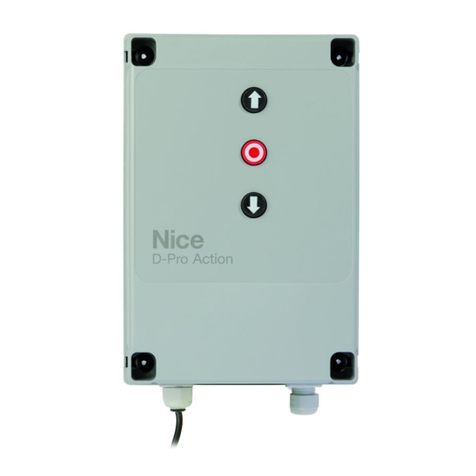
Nice
Nice D-Pro Action Series Instructions and warnings for installation and use
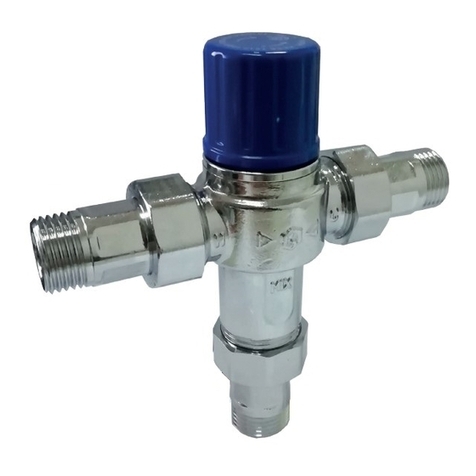
Albion
Albion TMV2 Installation & operating manual
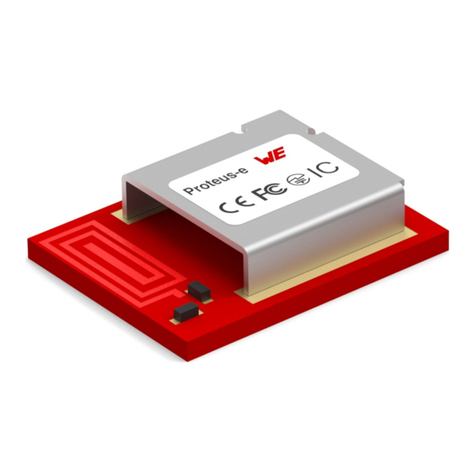
Wurth Elektronik
Wurth Elektronik Proteus-E Reference manual

Nakamichi
Nakamichi SoundSpace 10 Service manual
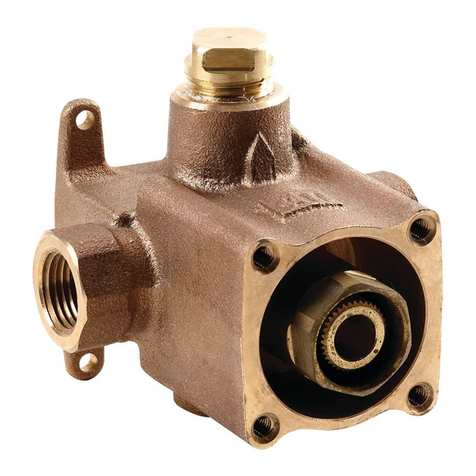
Toto
Toto TS2A Installation and owner's manual

Mitsubishi Electric
Mitsubishi Electric WD8700U user manual
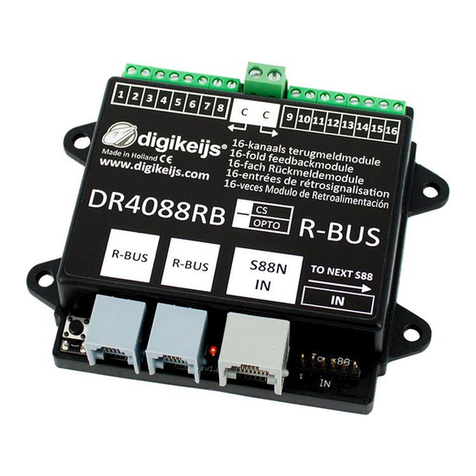
Digikeijs
Digikeijs DR4088RB Series manual
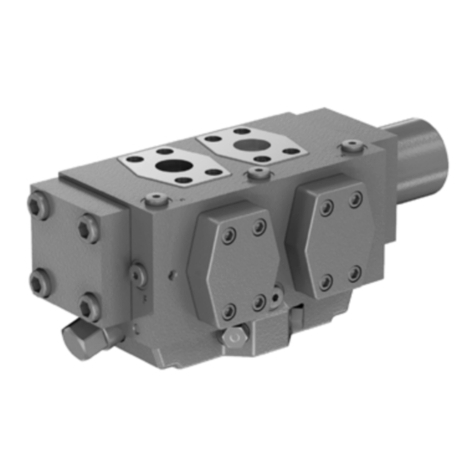
Bosch
Bosch Rexroth BVD 52 Series quick start guide