NOVAK ESC PROFILE SOFTWARE User manual

NOVAK ELECTRONICS • PROFILE SOFTWARE 1
Introduction .....................................................................................2
What’s Included ...............................................................................2
Adjustable Parameters.....................................................................3
Hardware Installation ....................................................................11
Operating System Requirements ..................................................12
Running From 3.5” Floppy Drive...................................................12
Installing/Running Software .........................................................13
Windows 3.1® & Windows 95® ....................................................13
MS® DOS .......................................................................................13
Precautions ....................................................................................14
Acquiring Default Parameters .......................................................14
Uploading Parameters From Cyclone ...........................................15
Editing Parameters ........................................................................16
Downloading Parameters To Cyclone ...........................................18
Saving Parameters To Disk ............................................................19
Reading Parameters From Disk .....................................................19
Monitoring Transmitter Trigger....................................................20
Sample Profile Data .......................................................................20
Service Procedures ........................................................................21
Service Return Sheet .....................................................................22
Trouble-Shooting Guide ................................................................23
Software License & Product Warranty ..........................................23
Profiles ...........................................................................................24
Profiles ...........................................................................................25
Index ..............................................................................................26
Notes..............................................................................................28
Complete Instruction Manual for
the Novak ESC Profile Software
Program.
CONTENTS

NOVAK ELECTRONICS • PROFILE SOFTWARE 2
INTRODUCTION
When designing an electronic speed control, the Novak engineers
are put to the task of setting design parameters such as how wide
the Deadband should be, what percentage of Full Drive should be
applied with the first pulse of transmitter information, or what
Brake and Drive Frequencies to use. In the past our engineers would
determine the best possible compromise for these parameters
based on different vehicles and driving styles. While these fixed
designs were perfect for some applications and some drivers, they
were not right for others. It became clear that a speed control was
needed that allowed the driver to modify several of the design
parameters to fit their differing applications and needs.
During testing, our engineers found that different vehicles required
different parameter values, just as each individual driver required
different parameters to obtain the type of feel that they desired.
With this criteria in mind, Novak proudly brings you the Cyclone
Programmable Speed Control and the Profile Software (#1030).
WHAT’S INCLUDED
• PROFILE SOFTWARE
Specialized profiling software that allows you to customize the
adjustable parameters of the Novak Cyclone Electronic Speed
Control (ESC), including the Deadband width, Minimum Drive
percentage, Drive & Brake PWM Frequencies, and more.
• DATALINK HARDWARE
Comes with everything needed to hook-up your Cyclone speed
control to an IBM®-compatible personal computer. Including
DataLink for connecting to speed control, DB9/RJ11 adaptor
for connecting to the communications serial port of computer,
and an RJ11 (6-conductor) cable for connecting the DataLink
to the DB9/RJ11 adaptor.
• ELECTRONIC INSTRUCTION MANUAL
Complete instruction manual is included on disk as a PDF file.

NOVAK ELECTRONICS • PROFILE SOFTWARE 3
ADJUSTABLE PARAMETERS
Novak’s Profile Software allows you to access the Cyclone speed
control’s previously hidden fourth Profile. This user-programmable
Profile gives you the ability to customize several of the design
parameters of the speed control. This adjustability will allow you
to custom tailor the speed control’s response and feel to your
preference for different applications. This section lists the user-
adjustable parameters, their descriptions, and applications:
• NEUTRAL
–Measured in microseconds (µs).
–Position at which the speed control is at rest, with no Drive or
Brake being applied.
–Initial value is taken from the transmitter, as recorded in the One-
Touch Set-Up memory of the speed control.
• FULL THROTTLE
–Measured in microseconds (µs).
–Trigger position at which speed control reaches Full Drive.
–Initial value is taken from the transmitter, as recorded in the One-
Touch Set-Up memory of the speed control.
• FULL BRAKE
–Measured in microseconds (µs).
–Trigger position at which speed control reaches Full Brake.
–Initial value is taken from the transmitter, as recorded in the One-
Touch Set-Up memory of the speed control.
Note: For optimum performance from your Cyclone, the values for Full Throttle
and Full Brake should be at least 350µs.
Figure 1: Neutral, Full Throttle, and Full Brake shown graphically by percent of
drive or brake applied at a given trigger position.
DEADBAND
TRIGGER POSITION
Neutral
Full
Brake Full
Throttle
10 10
20
50
100
20
50
100
% FULL DRIVE
% FULL BRAKE

NOVAK ELECTRONICS • PROFILE SOFTWARE 4
ADJUSTABLE PARAMETERS (CONT.)
• DEADBAND
–Measured as percentage (%) of Full Throttle trigger position.
–Space between Minimum Brake and Minimum Drive, with
Neutral located at the center of this space (Figure 2).
–Changing the Deadband value will change the point at which
forward Drive begins with respect to Neutral.
–Increasing Deadband will require more trigger movement away
from Neutral to reach both the first pulse of Drive and the first
pulse of Brake. Example: Adding 10% to the value of Deadband
will in turn add 5% Deadband in the Full Throttle trigger
direction, and 5% Deadband in the Full Brake trigger direction.
–Decreasing Deadband will require less trigger movement to
reach the first pulses of Drive and Brake.
Figure 2: Deadband graphically displayed as a percentage of the Full Throttle
trigger position, which is measured in microseconds.
DEADBAND
18%
TRIGGER POSITION
Neutral Full
Throttle
10 10
20
50
100
20
50
100
100%18%
% FULL DRIVE
% FULL BRAKE
Minimum
Drive
Minimum
Brake

NOVAK ELECTRONICS • PROFILE SOFTWARE 5
• DRIVE PWM FREQUENCY
–Measured in Hertz (Hz).
–Frequency at which the duty cycle information is being sent
from speed control to motor (How many times per second the
motor is being cycled on and off to control it’s speed).
–Drive PWM Frequency controls acceleration characteristics of
your vehicle with respect to trigger movement in the Full
Throttle direction (Figure 3). By changing the value of Drive
PWM Frequency you change the manner in which the vehicle
responds to transmitter trigger input.
–Increasing Drive PWM Frequency requires more initial trigger
movement to obtain the same given speed. Light
vehicles feel
more controllable / Heavy vehicles more sluggish.
–Decreasing Drive PWM Frequency requires less initial trigger
movement to obtain the same given speed. Light vehicles are
harder to control at the low end (possibly spinning the rear
wheels) / Heavy vehicles are more reactive.
–
This parameter can be used as a valuable tuning asset for
different types of motors and track conditions.
ADJUSTABLE PARAMETERS (CONT.)
Figure 3: Graphical location of area affected by Drive PWM Frequency.
DEADBAND
TRIGGER POSITION
Neutral
Full
Brake Full
Throttle
10 10
20
50
100
20
50
100
DRIVE PWM
FREQUENCY
% FULL DRIVE
% FULL BRAKE

NOVAK ELECTRONICS • PROFILE SOFTWARE 6
• MINIMUM DRIVE
–Measured as percentage (%) of the Full Drive value.
–Amount of Drive applied with the first pulse of transmitter
throttle information (Figure 4).
–Increasing the Minimum Drive will make the speed control
begin at a greater percentage of Full Drive. This is useful for
tracks with good traction and for heavier vehicles to eliminate
‘dead’ trigger movement before the motor can actually move
the vehicle (and will increase the vehicle’s minimum rolling speed).
–Decreasing the Minimum Drive will make the speed control
start at a smaller percentage of Full Drive. This is useful for
tracks with low-bite and lighter vehicles where lower initial
power will give more controllability. This parameter is also a
valuable tuning asset for different types of motors.
ADJUSTABLE PARAMETERS (CONT.)
Figure 4: Graphical representation of Minimum Drive and Minimum Brake as
percentage of Full Drive and Full Brake, respectively.
DEADBAND
TRIGGER POSITION
Minimum
Drive
[10%]
Minimum
Brake
[20%]
10 10
20
50
100
20
50
100
256 DISCRETE BRAKE STEPS
256 DISCRETE FORWARD STEPS
% FULL DRIVE
% FULL BRAKE

NOVAK ELECTRONICS • PROFILE SOFTWARE 7
• BRAKE PWM FREQUENCY
–Measured in Hertz (Hz).
–Frequency at which the duty cycle information is being sent
from speed control to motor for braking.
–Brake PWM Frequency controls deceleration characteristics of
your vehicle with respect to trigger movement in the Full Brake
direction (Figure 5). Changing Brake PWM Frequency allows
you to change the manner in which the vehicle responds to
brake trigger input.
–Increasing the Brake PWM Frequency will require more initial
trigger movement to obtain the same amount of braking. Light
vehicles brake more controllably under initial braking / Heavy
vehicles brake less reactively.
–Decreasing the Brake PWM Frequency will require less initial
trigger movement to obtain the same amount of braking. Light
vehicles are harder to control under initial braking (possibly
locking up the wheels) / Heavier vehicles are more reactive to
initial braking efforts.
ADJUSTABLE PARAMETERS (CONT.)
Figure 5: Graphical location of area affected by Brake PWM Frequency.
DEADBAND
TRIGGER POSITION
Neutral
Full
Brake Full
Throttle
10 10
20
50
100
20
50
100
BRAKE PWM
FREQUENCY
% FULL DRIVE
% FULL BRAKE

NOVAK ELECTRONICS • PROFILE SOFTWARE 8
• DRAG BRAKE VALUE
–Measured as percentage (%) of Full Brake value.
–Adjusts amount of Drag Brake applied within the Deadband
when throttle trigger is in the Neutral position (Figure 6).
–When the Drag Brake value is greater than zero, Drag Braking
is applied in the Deadband area. When the throttle trigger is
returned to Neutral, braking information is sent to the motor.
This can be used to obtain Drag Brakes without shifting the
Neutral position of the transmitter with the throttle trim, and
will in turn eliminate the Deadband (now ‘dead’ trigger) space
that has also been shifted toward the Full Throttle side of the
trigger movement before Drive can be applied.
–When the Drag Brake Toggle is set to ON position, the Brake
Pot on the Cyclone adjusts the Drag Brake Value. Drag Brakes
during Neutral/Deadband are now set at the same level as
Minimum Brake. With Drag Brake Toggle ON, the Drag Brake
Value can NOT be set with the ESC Profile Software, only with
the Brake Pot on the Cyclone.
–When Drag Brake Toggle is OFF, the Brake Pot on the Cyclone
adjusts only the Minimum Brake value. Drag Brake Value can
now be set above zero with the Profile Software to obtain
Drag Brakes. Minimum Brake value can now be independently
set higher or lower than the Drag Braking (Figure 8).
ADJUSTABLE PARAMETERS (CONT.)
Figure 6:
Graphical representation of Drag Brake Value as a percentage of Full Brake.
DEADBAND
TRIGGER POSITION
Minimum
Brake
[20%]
10 10
20
50
100
20
50
100
30
Drag Brake Value
[30%]
% FULL DRIVE
% FULL BRAKE

NOVAK ELECTRONICS • PROFILE SOFTWARE 9
• DRAG BRAKE TOGGLE
–Switches Brake Pot of the Cyclone ESC from Minimum Brake
adjustment to Drag Brake Value & Minimum Brake adjustment.
–When Drag Brake Toggle is ON, Drag Braking is applied in the
Neutral/Deadband area at the same frequency as Brake PWM
Frequency is set (Figure 7). When the trigger is returned to
the Neutral position, braking information is sent to the motor.
ADJUSTABLE PARAMETERS (CONT.)
Figure 7: Drag Brake Toggle ON––Drag Brake Value = Minimum Brake (Both are
set with Brake Pot). Drag Brake Frequency = Brake PWM Frequency
(Both are set with Brake PWM Frequency adjustment).
Figure 8: Drag Brake Toggle OFF––Independent adjustment of Minimum Brake
via Brake Pot, and Drag Brake Value, Brake PWM Frequency, and Drag
Brake Frequency with Profile Software.
DEADBAND
TRIGGER POSITION
Drag Brake Value equals
Minimum Brake =[30%]
10 10
50
100
50
100
30
% FULL DRIVE
% FULL BRAKE
DEADBAND
TRIGGER POSITION
Minimum
Brake [20%]
10 10
20
50
100
20
50
100
30 Drag Brake Value [30%]
% FULL DRIVE
% FULL BRAKE

NOVAK ELECTRONICS • PROFILE SOFTWARE 10
• DRAG BRAKE FREQUENCY
–Measured in Hertz (Hz).
–Frequency at which duty cycle information is being sent from
Cyclone to motor for Drag Braking during Neutral/Deadband.
–The Drag Brake Frequency (Figure 9) controls deceleration
characteristics of vehicle with Drag Brake during Neutral/
Deadband. Changing the Drag Brake Frequency changes the
manner in which the vehicle responds to Drag Brake.
–The Drag Brake Frequency affects the Drag Brake only when
the Drag Brake Toggle is OFF.
–Decreasing the Drag Brake Frequency makes the braking more
reactive during the Neutral/Deadband.
–Increasing the Drag Brake Frequency makes the braking more
subtle during Neutral/Deadband.
–With Drag Brake Toggle OFF, Drag Brake can be used with a
higher setting of Drag Brake Value (on PC) along with a high
setting of Brake PWM Frequency, and an increased Minimum
Brake setting (Brake Pot), to obtain battery regeneration with-
out noticeable increased braking effects. With Drag Brake
Toggle ON, Brake PWM Frequency is adjusting frequency of
both the brakes in the Neutral/Deadband area and the brakes
controlled by brake trigger movement.
ADJUSTABLE PARAMETERS (CONT.)
Figure 9: Graphical location of area affected by Drag Brake Frequency when the
Drag Brake Toggle is OFF.
DEADBAND
TRIGGER POSITION
Neutral
Full
Brake Full
Throttle
10 10
20
50
100
20
50
100
DRAG BRAKE
FREQUENCY
% FULL DRIVE
% FULL BRAKE

NOVAK ELECTRONICS • PROFILE SOFTWARE 11
HARDWARE INSTALLATION
1. Install 9V Battery
–Remove the four (4) screws from bottom of DataLink case
with a number 1 phillips screwdriver.
–Connect a 9 volt battery (Not included) to the battery harness.
–Position battery in battery box and replace bottom of case.
–Replace the four (4) screws, being careful not to overtighten.
2. Connect the DB9 end of the included DB9/RJ11 adaptor to the
communications serial port (#1 or #2) of your computer.
3. Connect the included RJ11 cable between the RJ11 side of the
DB9/RJ11 adaptor and the RJ11 port on the side of DataLink case.
Note: Any RJ11 (6-
conductor) cable
may be used if the
included cable gets
damaged or if a
longer or shorter
cable is desired.
Figure 10: Photo showing hook-up
of DataLink hardware.
RJ11 Cable
D•LINK harness
Cyclone

NOVAK ELECTRONICS • PROFILE SOFTWARE 12
OPERATING SYSTEM REQUIREMENTS
Your computer must meet the following system requirements in
order to install and run the Profile Software:
Computer IBM PC/Compatible
(80386, 80486, & Pentium)
Memory 640K minimum
Disk Space 200K minimum (can run from 3.5” floppy drive)
Disk Drive 3.5” floppy disk drive
Hard drive (for Profile storage)
Operating System MS®DOS or Windows®(Windows®runs in
DOS––create short-cuts to run from main desktop)
Monitor Black & White, Color, or VGA
Serial Port DB9 communications port (Use a DB25/DB9
adaptor if your computer does not have a DB9 port)
Mouse Not supported
(with Version 1.0 Profile Software)
Note: For your protection, we suggest that you make a copy of the
Profile Software diskette before running or installing software.
RUNNING FROM 3.5” FLOPPY DRIVE
If you do not want to install the software onto the hard drive, you
can run from the 3.5” floppy disk drive by following these steps:
1. Insert the included diskette into the 3.5” floppy disk drive.
2. At the indicated computer prompts, enter the given responses:
Computer prompts are shown for drive A, if you are using drive B then “B:” will
be displayed. The “RUN1” statement instructs the computer to use serial port
#1, if you connected the DataLink to serial port #2 then you will type “RUN2”.
Computer Prompt Enter the Following
A: {press Enter}
A:\ RUN1 {press Enter}
This will execute the SPDCTRL.EXE program and you are ready to
use the Profile Software to upload, download, customize, and store
Profiles for your Cyclone Programmable speed control.

NOVAK ELECTRONICS • PROFILE SOFTWARE 13
INSTALLING/RUNNING SOFTWARE
This procedure will copy all of the files from the included diskette
onto the hard drive in a sub-directory titled “Novak”:
WINDOWS 3.1®& WINDOWS 95®
1. Insert the included diskette into the 3.5” floppy disk drive.
2. Click on the “Start” icon, and select the “RUN” option.
(Select “File” option then “Run” option for Windows 3.1®)
3. At the indicated computer prompt, enter the given response:
If you are using drive B then “B:” will be displayed.
Computer Prompt Enter the Following
Open: A:SETUP {click OK}
Note: There is no space between “A:” and “SETUP”.
(“Command:” is computer prompt shown for Windows 3.1®)
4. To run the Profile Software program, execute the program file
“SPDCTRL.EXE” by clicking on “RUN1” or “RUN2”, depending
on which serial port you connected the DataLink to.
MS®DOS
1. Insert the included diskette into the 3.5” floppy disk drive.
2. At the indicated computer prompts, enter the given responses:
Computer prompts are shown for drive A, if you are using drive B then “B:” will
be displayed. The “INSTALL A: C:” statement instructs the computer to install
the files onto hard drive C, if you wish to use a different hard drive location then
you will type the command with the desired drive, such as “INSTALL A: D:”, etc.
Computer Prompt Enter the Following
A: {press Enter}
A:\ INSTALL A: C: {press Enter}
Note: There is a space between “INSTALL” and “A:”, and before “C:”.
3. To run the Profile Software program, execute the SPDCTRL.EXE
program by entering the given response:
The “RUN1” statement instructs the computer to use serial port #1, if you con-
nected the DataLink to serial port #2 then you will type “RUN2”.
Computer Prompt Enter the Following
C:\Novak RUN1 {press Enter}
This will execute the SPDCTRL.EXE program and you are ready to
use the Profile Software to upload, download, customize, and store
Profiles for your Cyclone Programmable speed control.

NOVAK ELECTRONICS • PROFILE SOFTWARE 14
PRECAUTIONS
In addition to using basic common sense, please take special note
of the following precautions:
• Make a back-up copy of the Profile Software diskette before
attempting to run or install software.
• Water and electronics DO NOT mix.
• DO NOT allow connector pins on D•LINK harness to contact
transistor tabs or heat sinks on speed control.
• DO NOT touch connector pins on D•LINK harness to avoid
static electricity damage to the electronics.
• Be careful when connecting or disconnecting D•LINK harness
to DataLink socket on speed control to avoid damage.
• Motor cleaner and solvents may damage DataLink case and
D•LINK harness.
ACQUIRING DEFAULT PARAMETERS
In order to edit and customize Profiles, you must first upload the
default parameter values from your Cyclone speed control (Next
section). When you upload the default parameters for the first
time, you will be reading Profile 1, 2, or 3 from your Cyclone,
depending on which Profile is currently active. Neutral, Full
Throttle, and Full Brake are the default parameter values that were
programmed into the One-Touch memory of your Cyclone, based
on the available throw of your transmitter. These values are the
standards for what will be the newly created Profile 4.
In most cases, you will not want to modify the values for Neutral,
Full Throttle, and Full Brake. These values set the exact point of
Neutral, and give you the complete range of throttle in both the
forward and brake directions. However, there are some instances
(To be discussed later in the Editing Parameters section) in which
changing these values could be useful.

NOVAK ELECTRONICS • PROFILE SOFTWARE 15
UPLOADING PARAMETERS FROM CYCLONE
The following steps will allow you to upload the Parameters from
the Cyclone speed control. The values for the Profile (1, 2, 3, or 4)
that is currently active in the Cyclone will be uploaded.
1. With DataLink connected as previously instructed, turn on the
DataLink’s power switch. Red power LED will blink on and off.
Note: We recommend that you turn off the DataLink’s power when
not in use to extend the life of the 9V battery.
2. Start your computer and Run the Profile Software program as
previously instructed.
3. Turn on your transmitter, then turn on your speed control.
Note: Use a DSC cord to disable the transmitter’s RF section to avoid
radio interference. If you do not have your transmitter or a DCS cord,
disconnect the servo from receiver and lift the vehicle’s wheels into the
air until D•LINK is connected.
Note: Motor will be disabled as soon as D•LINK harness is connected.
4. Connect the DataLink’s D•LINK harness to your Cyclone’s
DataLink socket located on the top of the speed control. The
D•LINK connector can only clear the transistors on the speed
control if the “D•LINK” lettering is right side up. If you have
external heat sinks installed, be sure that they do not extend
beyond the front edge of the transistors––You may need to
reposition heat sinks to gain proper access to the connector.
At this time the Cyclone’s LED should be illuminated solid red.
5. From the main menu, use the up { ↑ } or down { ↓ } arrow keys
to highlight “Upload Parameters From Cyclone”, then press
{Enter} or {Return} to select.
6. Press {Enter} or {Return} to upload the parameters from the
Cyclone.
7. Press {Enter} or {Return} again to return to the main menu.

NOVAK ELECTRONICS • PROFILE SOFTWARE 16
EDITING PARAMETERS
This function of the Profile Software is where you will be able to
edit and customize Profile 4 of the Cyclone and it’s parameters.
You are able to work in the Edit Current Parameters mode at any
time, you do not need to have the speed control connected to
the DataLink.
1. From the main menu, use the up { ↑ } or down { ↓ } arrow keys
to highlight “Edit Current Parameters”, then press {Enter} to
select. Edit Current Parameters refers to the version of Profile 4
that is currently active in the Profile Software.
2. Use the up { ↑ } or down { ↓ } arrow keys to highlight the
available parameters, then press {Enter} to modify the value.
3. For Deadband, Drag Brake Value, and Minimum Drive the
values are entered as percentages measured to the nearest tenth
of one percent (0.1%), and the decimal place is fixed and does
not need to be entered. So values will be entered as 100 for
10.0%, 101 for 10.1%, 102 for 10.2%, etc.
Note: To enter values less than 10.0% you will need to include the
leading zero (051 for 5.1%, 052 for 5.2%, 099 for 9.9%, etc.) or
move the cursor one position to the right, using the right {→} arrow
key, before entering the value.
4. To modify Drive PWM Frequency, Brake PWM Frequency,
Drag Brake Frequency, or Drag Brake Toggle use the up { ↑}
or down { ↓} arrow keys to highlight one of these four param-
eters. The pop-up list shows the available choices.
•To change the frequency, hold down the Control {Ctrl} key
and use the up { ↑} or down { ↓} arrow keys to highlight the
desired frequency, then press {Enter} or {Return} to select it.
Note: If you do not press {Enter} or {Return}, the program will
revert to the previously entered frequency.

NOVAK ELECTRONICS • PROFILE SOFTWARE 17
EDITING PARAMETERS (CONT.)
5. The Neutral, Full Throttle, and Full Brake parameters should
not be modified for typical applications. However, there may
be a few situations where changing these values can be helpful.
•One example for changing these parameters would be for
Drag Racing, where a shorter trigger throw may be desirable
in order to reach Full Drive faster by pulling the trigger a shorter
distance. You would do this by decreasing the value for Full
Throttle (Figure 11).
•To change parameter values, use the up { ↑} or down { ↓}
arrow keys to highlight the desired parameter, type in the
desired value, then press {Enter} or {Return} to enter.
Note: The standard One Touch Set-Up value for Full Throttle throw
should always be greater than that of Full Brake throw. If, before
modifying these values, this is not the case you should change the set-
up of your transmitter (Refer to transmitter’s owner manual).
6. Once you have modified the given parameters, use the up { ↑ }
or down { ↓ } arrow keys to move to the last parameter and
press {Enter} or {Return} to exit to the main menu of the Profile
Software.
Figure 11: Graphical display of the Full Throttle position shifted toward Neutral
for Drag Racing.
DEADBAND
TRIGGER POSITION
Neutral
Full
Brake Full
Throttle
10 10
20
50
100
20
50
100
% FULL DRIVE
% FULL BRAKE

NOVAK ELECTRONICS • PROFILE SOFTWARE 18
DOWNLOADING PARAMETERS TO CYCLONE
The following steps will allow you to download the Profile that is
currently displayed in the Edit Current Parameters mode of the
software to the Cyclone. The downloaded Profile will always be
the active Profile in the Cyclone even if this is the first time Profile
4 has been activated. You will now have the original three Profiles
that came with the Cyclone, plus the custom Profile (Profile 4) to
choose from through the One-Touch button.
Refer to your Cyclone Owner’s Manual for instructions on selecting Profiles.
1. With DataLink connected as previously instructed, turn on the
DataLink’s power switch. Red power LED will blink on and off.
2. Turn on your transmitter, then turn on your speed control.
Note: Use a DSC cord to disable the transmitter’s RF section to avoid
radio interference. If you do not have your transmitter or a DSC cord,
disconnect servo from receiver and lift vehicle’s wheels into the air
until D•LINK is connected.
Note: Motor will be disabled as soon as D•LINK harness is connected.
3. Connect the DataLink’s D•LINK harness to your Cyclone’s
DataLink socket located on the top of the speed control. The
D•LINK connector will only clear the transistors of the speed
control if the “D•LINK” lettering is right side up. If you have
external heat sinks installed, be sure that they do not extend
beyond the front edge of the transistors, as they may have to
be repositioned to gain access to the connector.
At this time the Cyclone’s LED should be illuminated solid red.
4. From the main menu, use the up { ↑ } or down { ↓ } arrow keys
to highlight “Download Parameters To Cyclone”, then press
{Enter} or {Return} to select.
5. Press {Enter} or {Return} to download the parameters to the
Cyclone.
6. After the downloading process is complete, the software will
return you to the main menu.

NOVAK ELECTRONICS • PROFILE SOFTWARE 19
SAVING PARAMETERS TO DISK
Any Profile created or uploaded can be saved to your hard drive
using these steps. Each Profile can be given a name of up to eight
characters long for future reference.
Tip: You can use names like “OFFRD–LB” for your Offroad Buggy on Low
Bite tracks, or “TRCK–WET” for your Truck and Wet conditions.
1. Upload or use the Edit Current Parameters mode to create the
Profile you would like to save, and return to the main menu.
2. From the main menu, use the up { ↑ } or down { ↓ } arrow keys
to highlight “Save Parameters To Disk”, then press {Enter} or
{Return} to select.
3. Type in the eight character name for the new Profile and press
{Enter} or {Return} to save.
4. After the saving process is complete, the software will return
you to the main menu.
READING PARAMETERS FROM DISK
Any Profile saved to the hard drive can be retrieved by following
these steps. The Profile can then be viewed, modified, or down-
loaded from the Edit Current Parameters mode.
1. From the main menu, use the up { ↑} or down { ↓} arrow keys
to highlight “Read Parameters From Disk”, then press {Enter}
or {Return} to select.
2. Use the up { ↑ } or down { ↓} arrow keys to highlight the Profile
to be retrieved, then press {Enter} or {Return} to select.
3. After the retrieving process is complete, you will return to the
main menu.
4. To view the retrieved Profile, use the up { ↑} or down { ↓}
arrow keys to highlight “Edit Current Parameters”, then press
{Enter} or {Return} to select.

NOVAK ELECTRONICS • PROFILE SOFTWARE 20
MONITORING TRANSMITTER TRIGGER
This function allows you to monitor the values of your transmitter’s
throw for Full Brake and Full Drive, as measured in microseconds.
1. Turn on your transmitter, then turn on your speed control. The
Cyclone’s LED should be illuminated solid red.
2. Connect the DataLink’s D•LINK harness to your Cyclone’s
DataLink socket, then turn on the DataLink’s power switch.
3. From the main menu, use the up { ↑ } or down { ↓ } arrow keys
to highlight “Monitor Transmitter Trigger”, then press {Enter}
or {Return} to select.
4. Move transmitter trigger to Full Drive, Full Brake, or Neutral to
measure position. Difference between Neutral and Full Drive value
gives the transmitter’s Drive throw, to Full Brake gives Brake throw.
SAMPLE PROFILE DATA
Included below (and in the software) is sample data for Profiles
developed by the Novak Racing Team at various racing events
with different vehicle/motor combinations. Use these Profiles as
they are, or as references for creating your own custom Profiles.
DR. PWM MIN. BR. PWM DRAG BR. DRAG BRAKE
PROFILE •VEHICLE •CONDITIONS FREQ. DRIVE FREQ. TOGGLE FREQ./VALUE
kHz %Full Fwd kHz ON/OFF kHz/%Full Br.
01. Buggy–Modified–High Traction 11.7 4.0 3.9 OFF –/0%
02. Buggy–Modified–Low Traction 15.6 2.0 3.9 OFF –/0%
03. Buggy–Stock 11.7 8.5 3.9 OFF –/0%
04. Truck–Modified 11.7 6.5 3.9 OFF –/0%
05. Truck–Stock 7.8 9.0 3.9 OFF –/0%
06. 1/10 OnRoad–Modified 23.4 7.5 3.9 OFF –/0%
07. 1/10 OnRoad–Mod–Drag Brake 23.4 7.5 3.9 OFF 5.86/4.0%
08. 1/10 OnRoad–Stock 15.6 9.0 3.9 OFF –/0%
09. 4WD Touring Sedan–Modified 23.4 5.5 3.9 OFF –/0%
10. Formula 1 23.4 2.5 5.86 OFF –/0%
11. 1/12 OnRoad–Modified–6 Cell 23.4 3.7 3.9 OFF –/0%
12. 1/12 OnRoad–Modified–4 Cell 5.86 6.9 3.9 OFF –/0%
13. 1/12 OnRoad–Stock–4 Cell 2.93 8.0 3.9 OFF –/0%
14. 4WD Buggy–Mod–Lo.Trac.–Dr.Br. 11.7 5.9 3.9 OFF 3.9/15.1%
15. Buggy–Mod–Low Traction–Dr.Br. 11.7 2.0 3.9 OFF 3.9/15.1%
16. Buggy–Mod–High Traction–Dr.Br. 11.7 4.0 5.86 ON N/A
17. Buggy–Mod–Low Traction–Dr.Br. 15.6 2.0 5.86 ON N/A
18. 1/10 OnRoad–Mod–Drag Brake 23.4 7.5 5.86 ON N/A
19. 4WD Touring Sedan–Mod–Dr.Br. 23.4 5.5 3.9 ON N/A
20. Formula 1–Drag Brake 23.4 2.5 11.7 ON N/A
*Deadband Value is 4.9% for all listed Profiles.
Table of contents
Popular Software manuals by other brands
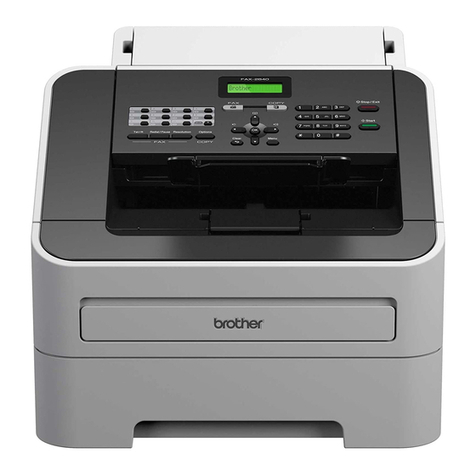
Brother
Brother IntelliFax-2840 user guide
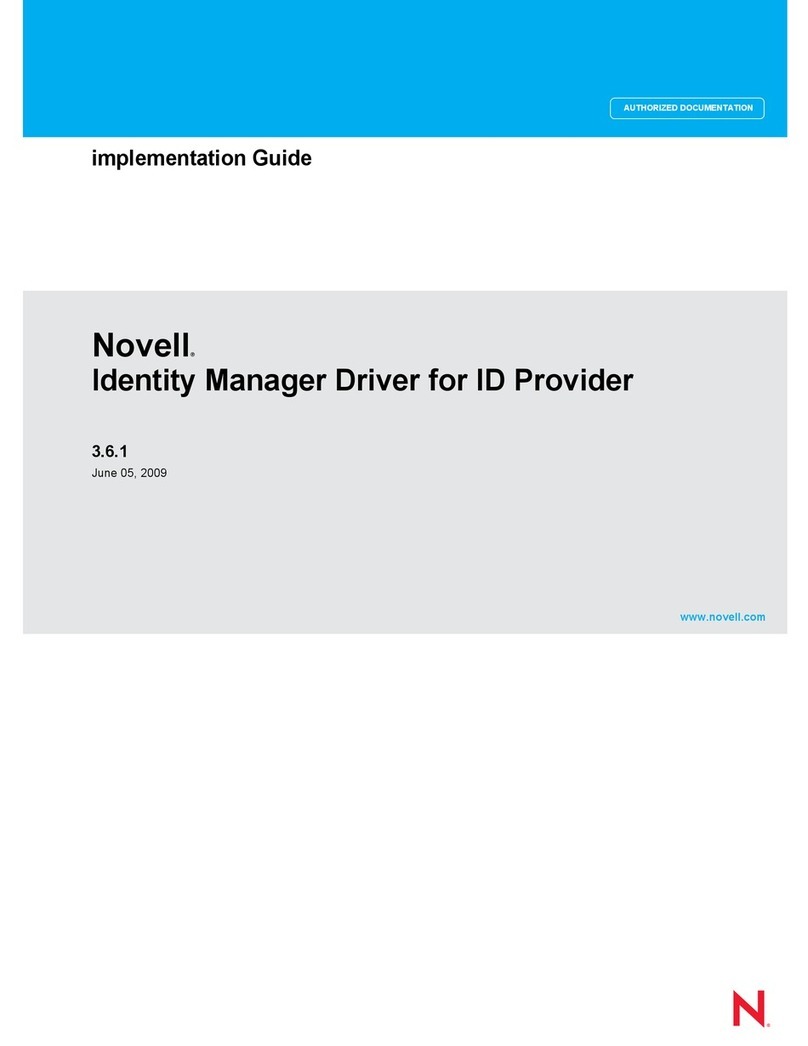
Novell
Novell IDENTITY MANAGER DRIVER FOR ID PROVIDER 3.6.1 -... manual
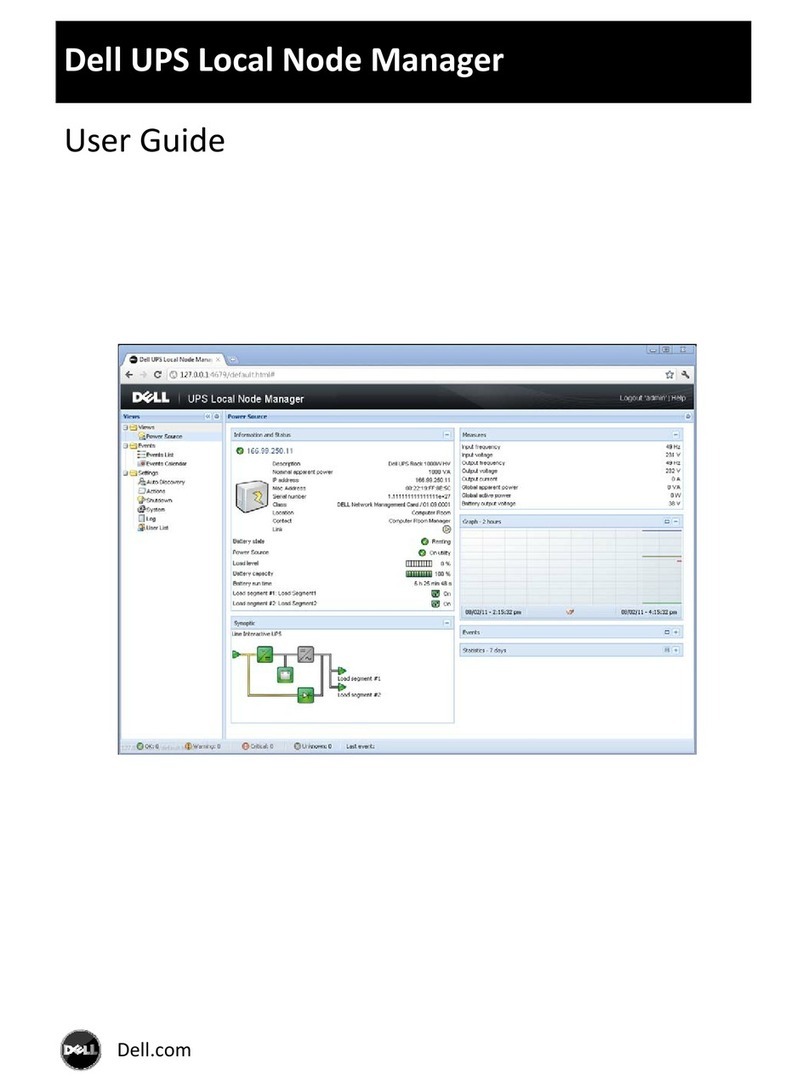
Dell
Dell PowerEdge UPS 500T user guide
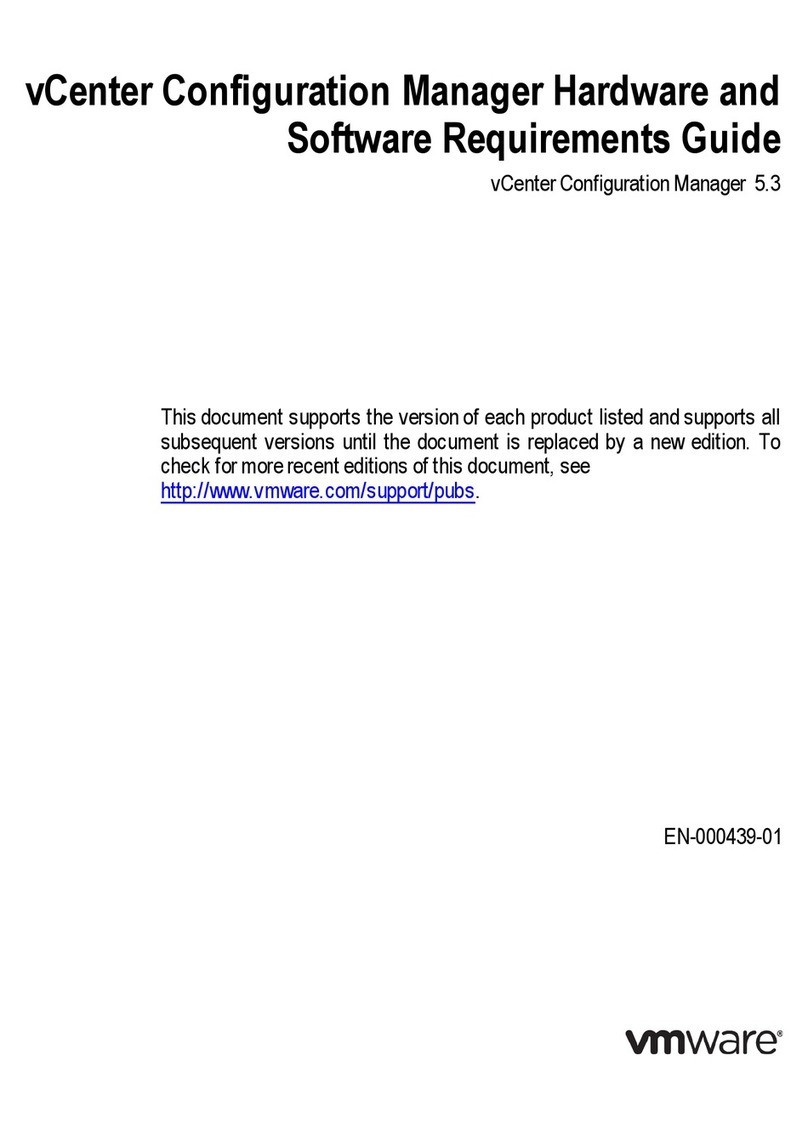
VMware
VMware VCENTER CONFIGURATION MANAGER 5.3 - SOFTWARE REQUIEREMENTS... Configuration
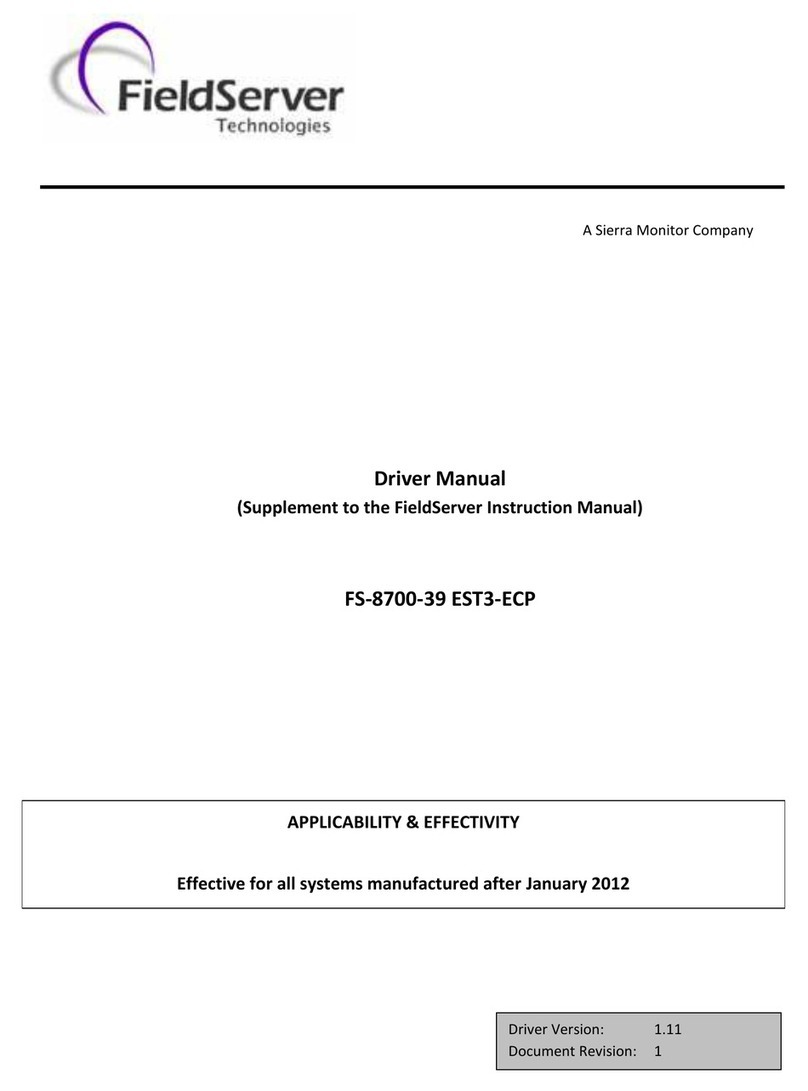
FieldServer
FieldServer FS-8700-39 Driver manual
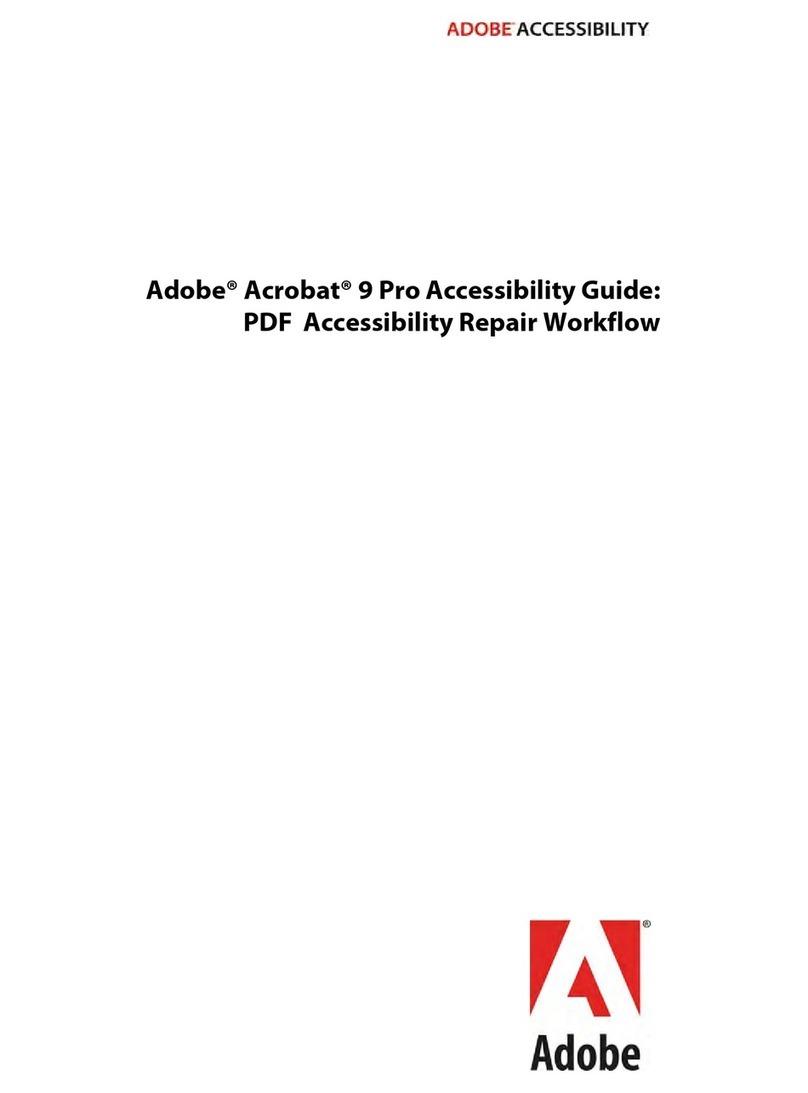
Adobe
Adobe 22020403 - Acrobat Professional - PC manual
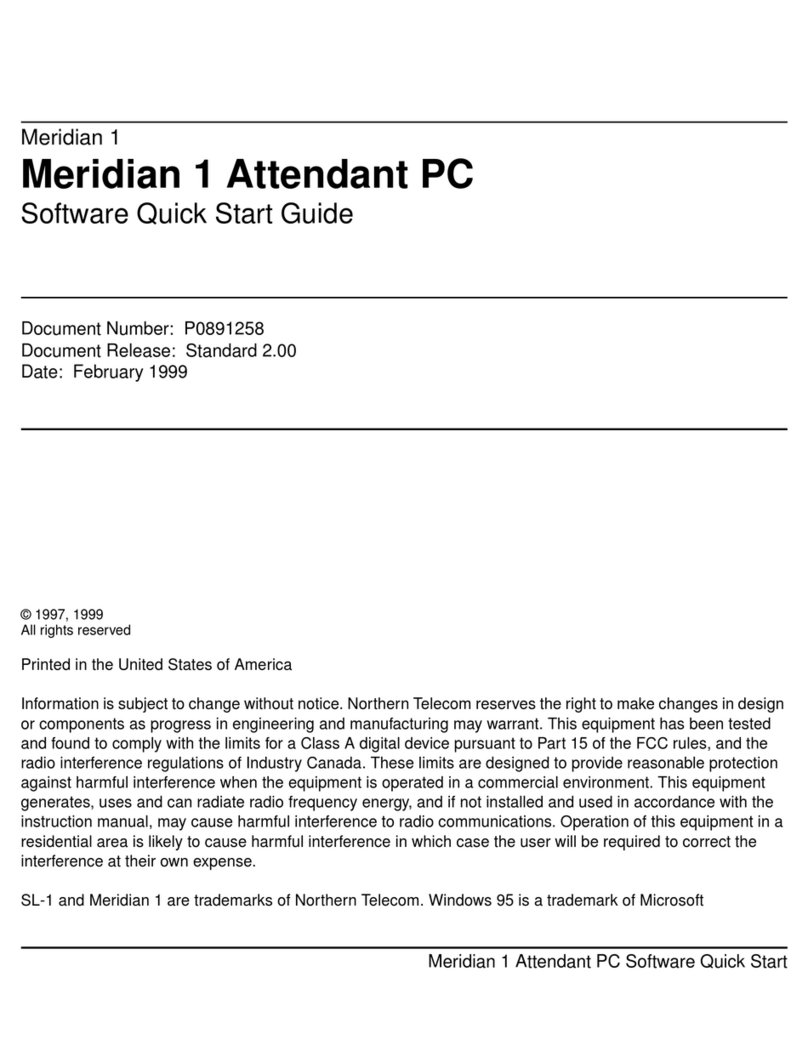
Nortel
Nortel Attendant PC quick start guide
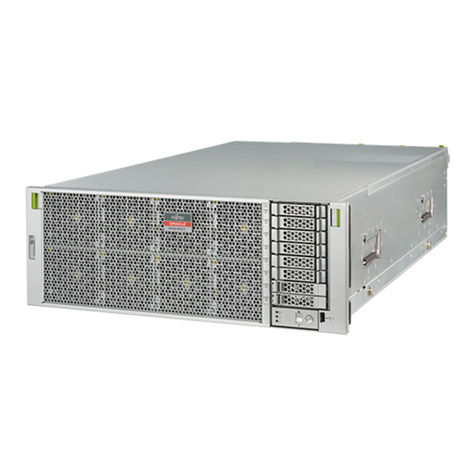
Fujitsu
Fujitsu Solaris 10 Hardware platform guide
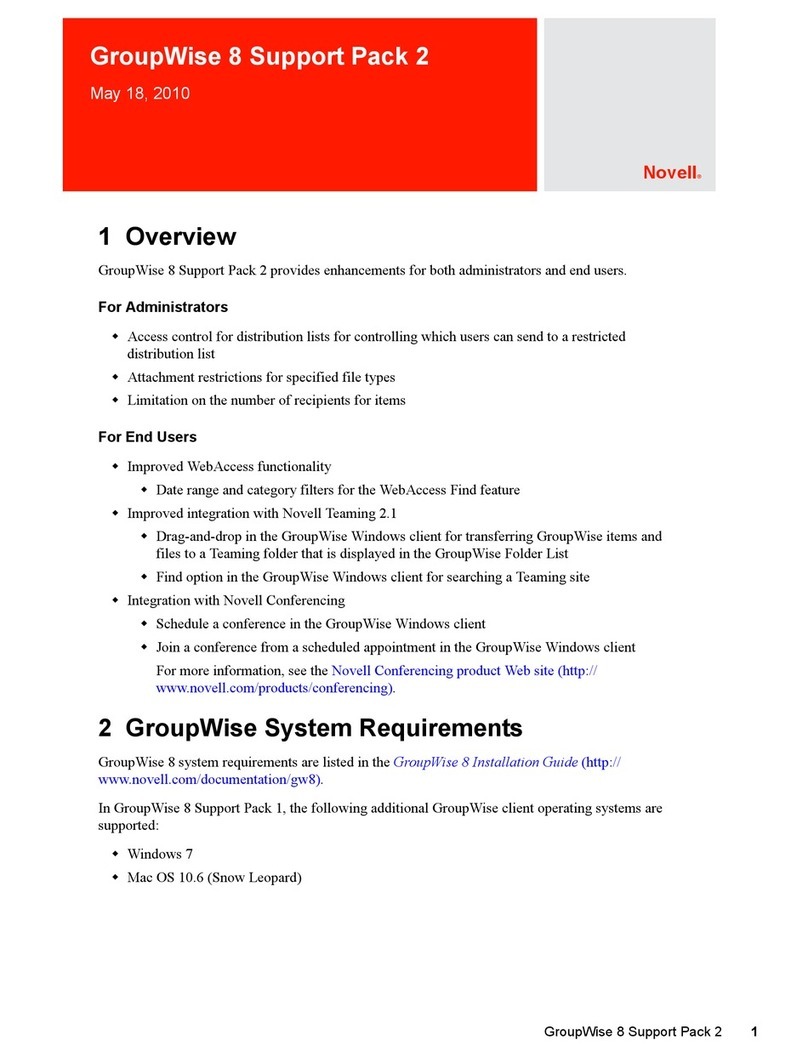
Novell
Novell GROUPEWISE 8 - SUPPORT PACK 2 05-2010 manual
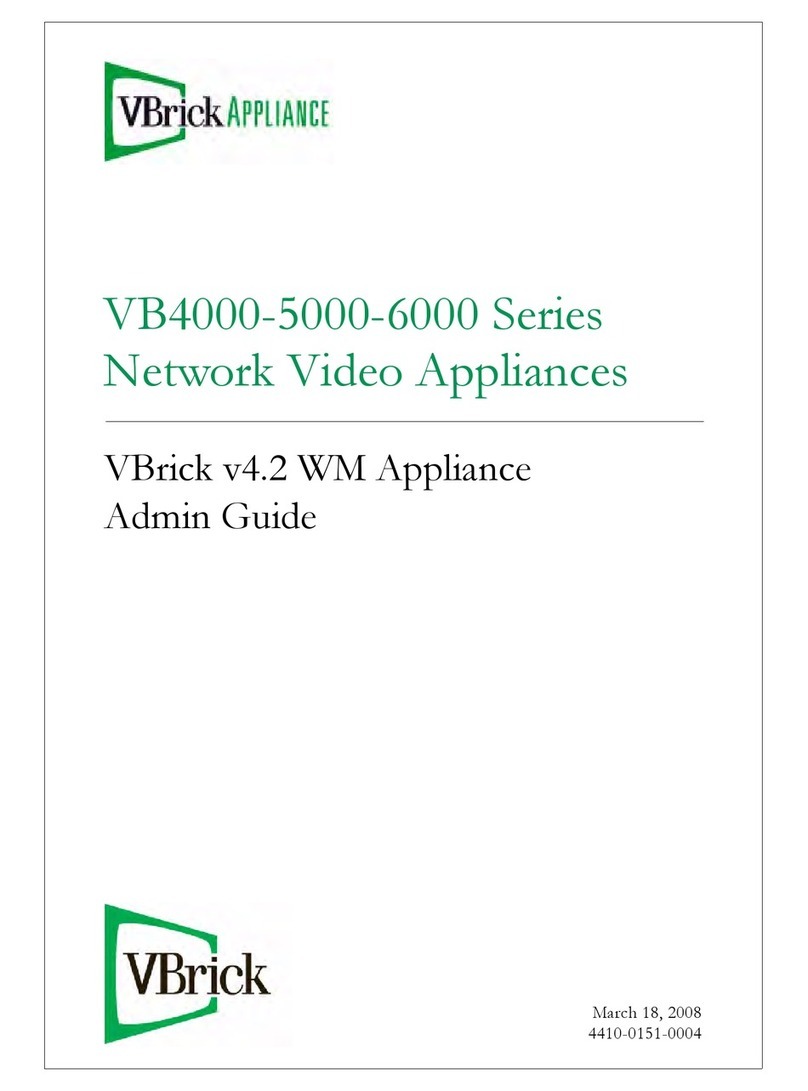
VBrick Systems
VBrick Systems VBRICK APPLIANCE VB4000 Admin guide
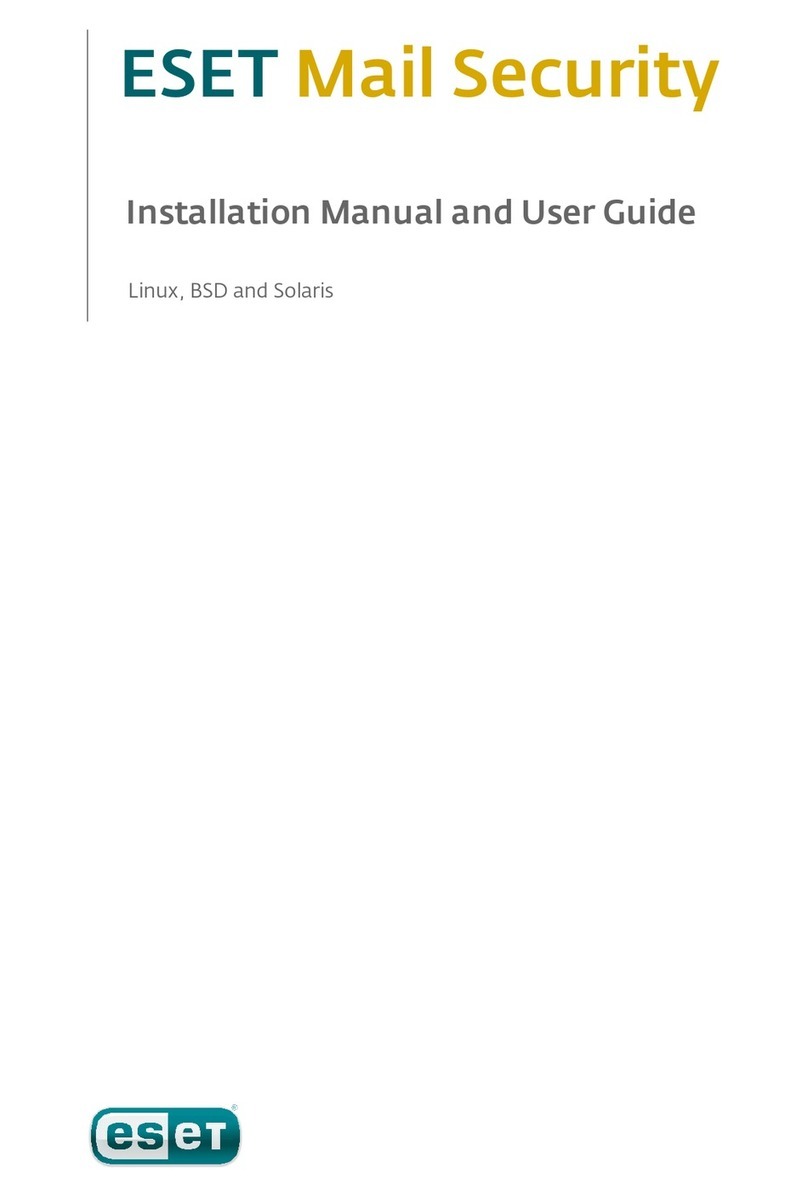
ESET
ESET MAIL SECURITY - FOR LINUX BSD AND SOLARIS installation manual

Mitsubishi Electric
Mitsubishi Electric DX-PC55E Operation manual