NT-MDT NTEGRA Solaris Probe NanoLaboratory User manual

Read me First!
Observe safety measures for operation with devices containing sources of laser radiation.
Do not stare into the beam. A label warning about the presence of laser radiation is
attached to the laser sources (Fig. 1).
Fig. 1
Before you start working with the instrument, get acquainted with the basic safety
measures and the operation conditions for the instrument!
If you are a beginner in scanning probe microscopy, we recommend you to familiarize with
basic SPM techniques. “Fundamentals of Scanning Probe Microscopy” by V.L. Mironov
gives a good introduction to the subject. This book is available free of charge at
http://www.ntmdt.com/manuals.
Feedback
Should you have any questions, which are not explained in the manuals, please contact the
comprehensive answers. Alternatively, you can contact our staff on-line using the ask-on-
line service (http://www.ntmdt.com/online).

User’s documentation set
The following manuals are included into the user‟s documentation set:
●Instruction Manual –is the guidance for the preparation of the instrument and other
equipment for operation on various techniques of Scanning Probe Microscopy. The
contents of the user‟s documentation set may differ in dependence on the delivery set
of the instrument.
●SPM Software Reference Manual –is the description of the control program
interface functions, all commands and functions of the menu and, also a description of
the Image Analysis module and the Macro Language “Nova PowerScript”.
●Control Electronics. Reference Manual –is the guide to SPM controller,
Thermocontroller and Signal Access module.
Some equipment, which is described in the manuals, may not be included into your
delivery set. Read the specification of your contract for more information.
The manuals are updated regularly. Their latest versions can be found in the site of the
company, in the section “Customer support” (http://www.ntmdt.com/support).

NTEGRA Solaris Probe NanoLaboratory
4
NTEGRA Solaris Probe NanoLaboratory
Table of Contents
1. BASIC INFORMATION ......................................................................................................................... 5
1.1. PURPOSE OF THE NTEGRA SOLARIS................................................................................................ 5
1.2. DESCRIPTION OF MAIN COMPONENTS .............................................................................................. 6
1.2.1. Inverted Optical Microscope Olympus IX71......................................................................... 7
1.2.2. NTEGRA Base Unit............................................................................................................... 8
1.2.3. XY Scanning Exchangeable Mount ....................................................................................... 9
1.2.4. SNOM Measuring Head...................................................................................................... 11
1.2.5. Optical Fiber Probe ............................................................................................................ 13
1.2.6. Laser Module ...................................................................................................................... 14
1.2.7. Photomultiplier Modules..................................................................................................... 15
1.2.8. SPM Controller ................................................................................................................... 17
1.2.9. Vibration Isolation Table .................................................................................................... 17
1.2.10. Optical Viewing System.................................................................................................. 18
1.3. THEORY OF OPERATION OF NTEGRA SOLARIS.............................................................................. 18
1.4. SAFETY MEASURES ........................................................................................................................ 23
1.5. OPERATING CONDITIONS ................................................................................................................ 25
1.6. STORAGE AND TRANSPORT INSTRUCTIONS ..................................................................................... 27
2. FIRST TIME INSTALLATION ........................................................................................................... 28
2.1. ASSEMBLY OF MAIN MODULES ...................................................................................................... 28
2.2. INSTALLATION OF INTERCONNECTIONS BETWEEN PARTS OF THE INSTRUMENT .............................. 32
3. PREPARATION OF THE NTEGRA SOLARIS PNL FOR OPERATION ..................................... 33
3.1. MAIN STEPS OF PREPARATION FOR OPERATION ............................................................................. 33
3.2. CABLE CONNECTIONS..................................................................................................................... 33
3.3. INSTALLATION OF THE PROBE INTO THE MEASURING HEAD ........................................................... 36
3.4. ASSEMBLY OF THE LASER MODULE................................................................................................ 39
3.5. PREPARATION AND INSTALLATION OF THE OPTICAL FIBER IN THE LASER MODULE ....................... 42
3.6. LOADING THE SAMPLE.................................................................................................................... 44
3.7. INSTALLATION OF THE MEASURING HEAD ON THE SCANNING MOUNT .......................................... 44
3.8. ASSEMBLY OF OPTICAL SCHEME FOR TRANSMISSION MODE.......................................................... 46
3.9. ASSEMBLY OF OPTICAL SCHEME FOR REFLECTION MODE.............................................................. 49
4. MEASUREMENT PROCEDURE ........................................................................................................ 54
4.1. SETTING OF THE INSTRUMENT CONFIGURATION ............................................................................. 54
4.2. LOADING SCANNER CALIBRATION PARAMETERS ........................................................................... 55
4.3. SETTING OF THE PHOTOMULTIPLIER MODULE PARAMETERS .......................................................... 57
4.4. SEARCH FOR RESONANCE FREQUENCY........................................................................................... 59
4.5. PROBE LANDING ............................................................................................................................. 62
4.6. SCANNING....................................................................................................................................... 64
4.6.1. Setting of Scanning Parameters .......................................................................................... 64
4.6.2. Triggering of Scanning ....................................................................................................... 66
4.6.3. Methods of Improving Image Quality ................................................................................. 67
4.7. SAVING OF MEASUREMENT RESULTS ............................................................................................. 68
4.8. TERMINATION OF MEASUREMENTS................................................................................................. 68
5. MAINTENANCE.................................................................................................................................... 70
5.1. ADJUSTING THE DISPLACEMENT SENSORS...................................................................................... 70
5.2. SCANNER CALIBRATION.................................................................................................................. 73

Chapter 1. Basic Information
5
1. Basic Information
1.1. Purpose of the NTEGRA Solaris
The NTEGRA Solaris PNL is a specialized SPM measurement system built on the
NTEGRA platform. A SNOM measuring head lies in the basis of this system.
SNOM techniques are used to study near-surface optical characteristics (including
luminescent and spectral) of various objects with resolution much greater than the
diffraction limit. The higher resolution is gained by exposing samples with light going
through a diaphragm whose aperture is much less than the wavelength of the radiation
detected. The surface under study lies in the near field of the diaphragm (at distances of
about 10 nm).
The most advanced technologies used in the design of the system and the powerful
software make the NTEGRA Solaris PNL easy to adapt it to a broad variety of research
tasks and to use it in research laboratories, universities and scientific centers. For example,
to study biological objects, for optics quality control, to study light emitting semiconductor
structures, properties of nano-optical and integrated optics components, to investigate
characteristics of nano-electronic elements and quantum dots spectra, in particular.
The NTEGRA Solaris PNL can be used to solve the following problems:
●Measure surface topography of the sample under investigation;
●Measure surface optical properties (reflection and transmission coefficients,
distributions of luminescent characteristics);
●Carry out measurements for local spectral characteristics;
●Perform nano-lithography operations (including optical lithography on photosensitive
samples and thermo-lithography).

NTEGRA Solaris Probe NanoLaboratory
6
1.2. Description of Main Components
Main components of the NTEGRA Solaris PNL
The following parts are included in the basis configuration of the NTEGRA Solaris PNL:
1. Inverted Optical Microscope Olympus IX71 (item. 1.2.1 on page 7).
2. NTEGRA Base Unit (item. 1.2.2 on page 8).
3. XY Scanning Exchangeable Mount (item. 1.2.3 on page 9).
4. SNOM Measuring Head (item. 1.2.4 on page 11).
5. Optical Fiber Probe (item. 1.2.5 on page 13).
6. Laser Module (item. 1.2.6 on page 14).
7. Photomultiplier Modules (item. 1.2.7 on page 15).
8. SPM Controller (item. 1.2.8 on page 17).
9. Vibration Isolation Table (item. 1.2.9 on page 17).
10. Optical Viewing System (item. 1.2.10 on page 18).
An overall view of the NTEGRA Solaris PNL in given in Fig. 1-1.
Fig. 1-1. Overall view of the NTEGRA Solaris PNL
1 –microscope Olympus IX71; 2 –NTEGRA base unit; 3 –scanning mount;
4 –scanning measuring head; 5 –optical viewing system; 6 –laser module

Chapter 1. Basic Information
7
Investigation of optical characteristics with resolution better than the diffraction limit is
performed with a SNOM scanning measuring head equipped with an optical fiber probe.
The probing beam is coupled into the probe by means of a laser module. An optical
viewing system is employed both to select an area of the sample for investigation and to
control the approach of the probe to the sample. The scanning mount of an original design
makes it possible to obtain both SMOM images of the sample under study and its optical
images using the inverted microscope. The objective of the inverted microscope is located
in the scanning mount, which incorporates systems of coarse and fine focusing. This gives
the opportunity to use high-resolution objectives (including immersion ones). In addition to
the system of coarse manual positioning of the sample, the scanning mount incorporates a
system of precision XY positioning, which can be used for XY scanning. A vibration
isolation table equipped with a dynamic vibration protection system also contributes to
getting high resolution during measurements.
1.2.1. Inverted Optical Microscope Olympus IX71
The inverted optical microscope Olympus IX71 is used to obtain both SNOM (or other
SPM) images and ordinary optical images. This microscope incorporates an optical system,
which, in the case of transparent samples, can be used for visual control of the approach
process and to read optical signals by means of a photomultiplier unit.
Fig. 1-2. Inverted optical microscope Olympus IX71

NTEGRA Solaris Probe NanoLaboratory
8
1.2.2. NTEGRA Base Unit
The NTEGRA base unit is used to install the scanning mount on it. In addition,
the measuring head and the scanning mount are connected to the controller by means of
this unit.
The base unit accommodates the approach system, which is used to perform both the
motorized approach of the objective to the sample by means of a stepper motor and manual
using the drive knob 1.
Fig. 1-3. Main components of the base unit
1 –approach system drive knob; 2 –approach lever;
3 –temperature and humidity sensor; 4 –LC-display,
The LC-display 4 contains information about ambient temperature and humidity, which is
measured by sensor 3.
Connectors of the base unit
Connectors for the devices mounted on the base unit:
HEAD –two identical connectors for connecting measuring heads;
SCANNER –for connecting scanners. It is used for connecting either
changeable scanners or the measuring head scanner;
SCAN+SENSOR –for connecting scanners / scanners with built-in sensors. It is used
for connecting either changeable scanners or the measuring head
scanner;
T–for connecting the heater. It is used to connect heating stages, liquid flow cells
with heaters etc;
SM –for connecting the stepper motor of the measuring head motorized stage;
AFAM –for connecting the ultra-sonic transducer;
BV –for feeding the bias voltage.

Chapter 1. Basic Information
9
Connectors for connecting the base unit with the controllers of the control system:
CONTROLLER 1 –for connecting the SPM controller;
CONTROLLER 2 –for connecting the SPM controller;
CONTROLLER T–for connecting the thermo-controller.
NOTE. Connectors BV, SCANNER and HEAD (located closer to the central aperture of
the base unit) are not used in this configuration due to specifics of the design of the
instrument.
1.2.3. XY Scanning Exchangeable Mount
The XY scanning exchangeable mount (further in the text called “scanning mount”)
(Fig. 1-4) is installed on the NTEGRA base unit. The measuring head is, in turn, mounted
on the scanning mount.
PNL NTEGRA Solaris is supplied with a scanning mount of one of two modifications
providing different XY scan ranges, 50×50 mm or 100×100 mm.
a) with the sample holder
б) without the sample holder
Fig. 1-4. XY scanning optical exchangeable mount
1 –measuring head seats; 2 –measuring head positioning screws;
3 –XY positioner microscope screws; 4 –sample holder; 5 –spring clips;
6 –auxiliary mirror slots; 7 –XY scanner; 8 –spring stops;
9 –inside “cup”; 10 – outside “cup”
When setting the scanning mount on the inverted optical microscope for optical
measurements on transparent samples, a microscope objective is placed into the scanning
mount.

NTEGRA Solaris Probe NanoLaboratory
10
The objective is placed into the inside “cup” 9 of the scanning mount, which is a part of the
approach system. Coarse focus of the objective on the area of interest is adjusted by means
of the approach system of the base unit. Fine focus of the objective is adjusted by means of
the Z-scanner of the scanning mount. Such a system makes it possible to employ high-
resolution objectives, including immersion ones. To achieve high resolution, it is essential
to integrate the objective and the sample holder into a single mechanical system so as to
reduce relative vibrations and drifts.
The sample is placed on a microscope slide, which in turn is fixed on the sample holder 4
(Fig. 1-4) by means of spring clips 5. The measuring head is placed on seats 1 of the
scanning mount. Translation of the sample with respect to the objective in the XY plane is
done by means of the microscope screws 3 and spring stops 8. Screws 2 are used to
translate the measuring head in the XY plane with respect to the sample surface. The
optical viewing system, whose auxiliary mirror is fixed in slots 6, is recommended for
more accurate selection of an area for investigation.
The scanning mount is used to solve the following problems:
●Translate the sample with respect to the probe and the objective (if available) to select
an area for investigation;
●Scanning;
●Focus the objective onto the sample surface.
The XY scanner 7 is employed to translate the sample of interest in the XY plane under the
measuring head probe to select an area for investigation, and also during scanning. The
built-in position sensors make it possible to move the sample with high linearity and
repeatability as they minimize the influence of piezo-ceramics hysteresis and creep.
Scanning by means of the XY scanner is more linear compared with scanning-by-probe,
especially when using SNOM techniques as the scanned area can be always kept in the
focus of the objective.
Scanning mount technical specifications
Measuring head travel, XY 5×5 mm;
Sample travel 5×5 mm;
Sample minimum step resolution 5 µm;
Scanning range, XY 50×50 µm/100×100 μm;
Objective travel by means of the Z-scanner 45 µm.

Chapter 1. Basic Information
11
1.2.4. SNOM Measuring Head
The SNOM measuring head (Fig. 1-5) is used for both measurements of surface
topography of the sample and for measurements of its near-surface optical properties.
Oscillation amplitude and phase of the probe can also be registered during these
measurements.
Fig. 1-5. Measuring head
1 –output orifice for the optical fiber; 2 –leveling posts;
3 –probe holder; 4 –housing; 5 –PMT connector; 6 –motorized leveling post
All elements of the SNOM measurement head are assembled on the mounting plate.
The scanner is contained within the housing 4. The capacitance sensors are fixed to the
bottom part of the scanner. The end of the scanner has a special holder for the optical fiber
probe 3. The top part of the housing 4 has an output orifice 1 for the free end of the
optical fiber.
There are three leveling posts to secure installation, horizontal leveling and delivery of the
measuring head to the sample. Two of them are ordinary screws, 2, with fastening nuts.
The third post is a micrometer screw driven by a stepper motor (motorized leveling post) 6,
which provides the motorized translation of the probe towards the sample.
The probe is fixed in the holder 1 (Fig. 1-6) with spring clips 2, which also serve as
electrical contacts to acquire signal from the sensor. During installation of the sensor, the
optical fiber is put through the orifice 5. The scanner 3 provides scanning of a given XY
area of the sample by probe and it reads variations of the surface in the Z direction.
Observation of the probe tip both during the approach procedure and while selecting the
area for measurement is available through a special groove in the protective case 4.

NTEGRA Solaris Probe NanoLaboratory
12
Fig. 1-6. Probe holder assembly
1 –probe holder; 2 –spring clips; 3 –bottom part of the scanner;
4 –protective case; 5 –optical fiber input orifice
Movements of the scanner in the XY plane are controlled by means of the capacitance
sensors (Fig. 1-7).
Fig. 1-7. Functional schematics of the SNOM measuring head

Chapter 1. Basic Information
13
Technical specifications of the SNOM measuring head
Scanning range in the XY plane 100x100 μm;
ShFM resolution:
●in the XY plane <20 nm;
●in the Z direction <0.1 nm;
SNOM resolution in the XY plane <100 nm;
Number of pixels up to 1024x1024;
Probe-to-sample approach mode motorized;
Probe-to-sample distance control method Shear Force Microscopy.
1.2.5. Optical Fiber Probe
Optical fiber probe (Fig. 1-8) makes it possible to control the distance between the probe
tip and the sample and it is used to deliver laser beam to the sample surface.
Fig. 1-8. Optical fiber probe assembly
1 –quartz resonator; 2 –optical fiber; 3 –contact areas
The probe consists of the following parts: quartz resonator 1, single-mode optical
fiber 2 glued to the resonator and the textolite base with contact areas 3. The end of the
fiber, which is fixed to the quartz resonator with glue, is sharpened by chemical etching or
other methods so that a tip with the radius of curvature of about 50†100 nm is formed.
A metal layer is deposited on the end of the fiber so that the very tip, of 50†100 nm
diameter, remains clear.
The sensor used to control the distance between the tip and the sample is a U-shape quartz
resonator (tuning fork). The sharpened end of the optical fiber is glued to one of the
resonator‟s shoulders so that it comes out by 0.5†1.0 mm. The force interaction occurs
between this sharpened end (probe tip) and the surface under investigation.
Signal generated by the quartz resonator is received through the contact areas.

NTEGRA Solaris Probe NanoLaboratory
14
Optical fiber probe technical specifications
Optical fiber type single-mode;
Accepted wavelengths 480†550, 600†680, 780†1050 nm;
Fiber length 2 m;
Fiber transmission coefficient, K ~10-3†10-5;
Output aperture diameter ~100 nm;
Radius curvature of the tip ~100 nm;
Metal coating Va-Al;
Resonator operating frequencies, Fres1, Fres2 ~33 kHz, ~190 kHz.
1.2.6. Laser Module
The laser module is intended to couple laser radiation into the optical fiber. An overall
view of the module equipped with a solid-state 488 nm laser is given in Fig. 1-9.
Fig. 1-9. Overall view of the laser module
1 –base; 2 –positioning stage; 3 –optical fiber fastening system;
4 –objective; 5 –laser source; 6 –power supply
The module incorporates the base 1. This base is used for mounting the laser source 5
and the positioning stage 2 with a microscope objective 4 and the optical fiber fastening
system 3.
Laser module technical specifications
Focusing objective:
●Magnification 40x;
●Aperture 0.65 mm;
●Operating segment 0.4 mm.

Chapter 1. Basic Information
15
Positioning stage:
●Translation resolution 1 μm, along X, Y, Z;
●Travel 4 mm, along X, Y, Z.
NOTE. The laser module assembly can vary. It can be equipped with different lasers: gas,
solid-state, with different power characteristics and operating wavelengths (see data
sheets).
1.2.7. Photomultiplier Modules
Photomultiplier modules are intended for converting optical radiation acquired from the
sample into electrical signals.
Depending on configuration of the NTEGRA Solaris, a PMT of the following types is
used:
●PMT module for installation in the optical microscope (see Fig. 1-10a) –used in the
Transmission Mode optical scheme
●PMT module for installation on the optical attachment of the measuring head (see.
Fig. 1-10b) –used in the Reflection Mode optical scheme.
An overall view of the photomultiplier modules is given in Fig. 1-10.
a) Photomultiplier module for installation in
the optical microscope
b) Photomultiplier module for installation on
the optical attachment
Fig. 1-10. Overall view of the photomultiplier modules
1 –photomultiplier; 2 –cable for connecting to the controller; 3 –shutter

NTEGRA Solaris Probe NanoLaboratory
16
ATTENTION! Photomultiplier is a photosensitive device. To avoid
permanent damage and earlier degradation, do not expose it to high
intensity radiation even if it is not connected. Open the shutter only for
measurements. Avoid overloading the photomultiplier.
Parameters of the photomultiplier at 25 °C
Sensitivity (at 420 nm) 3.0×1010 V/W;
Output voltage shift ±3 mV;
Current-to-voltage conversion gain 1x106V/A;
Frequency range from 0 to 20 kHz.
Effective spectral range: 185†850 nm (Fig. 1-11).
Fig. 1-11. Effective spectral range

Chapter 1. Basic Information
17
1.2.8. SPM Controller
The SPM controller provides control of the probe measurement system. Its main functions
are:
●Processing signals received from measuring heads;
●Conversion of signals generated by the computer control program Nova;
●Generating signals for scanners and probe;
●Auxiliary devices control.
The more detailed description of the SPM controller is provided in the manual “Control
Electronics”.
1.2.9. Vibration Isolation Table
Scanning probe microscope systems are vulnerable to external vibrations, which distort
images of surfaces and also deteriorate their quality. A special vibration protection table
equipped with a system of dynamic vibration isolation is utilized to protect this system
from external vibrations.
Fig. 1-12. Vibration isolation table
Vibration isolation table technical specifications
Vibration isolation:
●Dynamic 0.7†1000 Hz;
●Passive >1000 Hz.
Transmissibility above 10 Hz <0.01 (-40 dB);
Size 400×450×75 mm;
Maximum load 150 kg.

NTEGRA Solaris Probe NanoLaboratory
18
1.2.10. Optical Viewing System
The video viewing system is intended to perform visual control over the following
processes:
●selection of an area of the sample for measurement;
●approach of the probe to the sample;
●scanning.
Optical viewing system technical specifications
●Magnification from 85× to 1050×;
●Resolution3 μm;
●Focusing manual;
●Numerical aperture up to 0.1;
●Monitor 19”, color;
●CCD camera 1/3”, color.
The more detailed description of the optical viewing system is provided in the manual
“Performing Measurements” (see Appendix).
1.3. Theory of Operation of NTEGRA Solaris
The optical fiber probe is fixed to the scanner, which is installed inside the measuring
head. A piezo vibrator is located at the place where the probe is fixed to the scanner. It
oscillates at the resonance frequency of the system consisting of the probe, quartz resonator
and probe holder. Signal is read from the contacts of the quartz resonator. It is proportional
to the oscillation amplitude of the resonator. During the approach of the probe to the
sample surface, the resonance frequency of the system changes due to the influence of
atomic interactions between the probe tip and the surface (Shear Force Microscopy
(ShFM)). This induces a rapid drop of the oscillation amplitude and an alteration of the
oscillation phase of the quartz resonator. Consequently, the magnitude of the signal
acquired from the resonator changes. These variations are detected by the lock-in amplifier
incorporated into the feedback system, which drives the piezo tube of the scanner along the
Z axis. Thus the feedback system keeps the magnitude of interaction between the probe
and sample constant during scanning. The value of this magnitude of interaction can be
indirectly set by means of the parameter Set Point in the program of computer control of
scanning. The driving signal applied to the Z-section of the scanner is used as the source of
data to reproduce surface topography of the sample.
The sample (normally placed on a substrate) is placed on the sample stage. The measuring
head is mounted on the scanning mount. Then, using the motorized leveling post, the probe
is landed onto the sample at the distance defined by the parameter Set Point and, then, the
scanning procedure starts in the plane of the sample.

Chapter 1. Basic Information
19
Due to the modular design of the system, the instrument can be configured to operate in
different scanning modes:
●Scanning by probe;
●Scanning by sample.
During scanning-by-probe the sample does not move, while the scanner of the measuring
head performs the procedure. The scanner is equipped with capacitance sensors to improve
linearity and accuracy of movements of the probe in the XY plane. The capacitance sensor
is a capacitor, whose one plate is fixed to the base of the head and does not move. The
second plate is fixed to the bottom part of the scanner and, therefore, can move with
respect to the first one. The distance between the plates changes during the process of
scanning and, therefore, it changes the value of capacitance of the capacitor. This effect
makes it possible to track all movements of the scanner.
During scanning-by-sample the sample is translated by means of a precision
XY positioning device of the scanning stage in the XY plane, while the probe is translated
in the Z direction by means of the Z-section of the measuring head scanner. Scanning-by-
sample is more linear compared to scanning-by-probe and, in addition, the tip of the fiber
probe is always kept at the optical axis of the objective, which provides more accurate
optical measurements and is important for SNOM techniques.
To provide coupling the laser beam into the optical fiber, the acrylic coating is stripped
from the free end of the fiber and, then, this end is cleaved. Then it is fixed to the
positioning stage of the laser module. The laser beam is focused onto the face of the fiber
by means of a microscope objective. The radiation propagates along the optical fiber
towards the output aperture of the sharpened tip of the fiber. Due to the small gap between
the tip and the surface of the sample under study, the surface lies within the near field of
the optical radiation coming out from the fiber.
The light coming out from the tip is scattered on the sample. Part of this scattered light is
collected by the optical system and is fed to the photomultiplier. Signals from the
photomultiplier are used as a source of data to reproduce an optical image of the surface.
For convenience, the main module of NTEGRA, or the microscope, can be connected with
a CCD camera and video monitor.
The NTEGRA Solaris PNL can operate in two principal optical schemes, which are based
on Shear Force Microscopy:
●Transmission Mode, which is used for transparent (semitransparent) samples;
●Reflection Mode, which is used for non-transparent samples.
These schemes employ the Laser Mode: all radiation transmitted through the sample, or
reflected from it, is directed to the photo-detector.

Fig. 1-13. Block diagram of the NTEGRA Solaris PNL
Table of contents
Other NT-MDT Measuring Instrument manuals
Popular Measuring Instrument manuals by other brands

Heuresis
Heuresis Pb200i Alpha user guide

Kanomax
Kanomax 3887 Operation manual
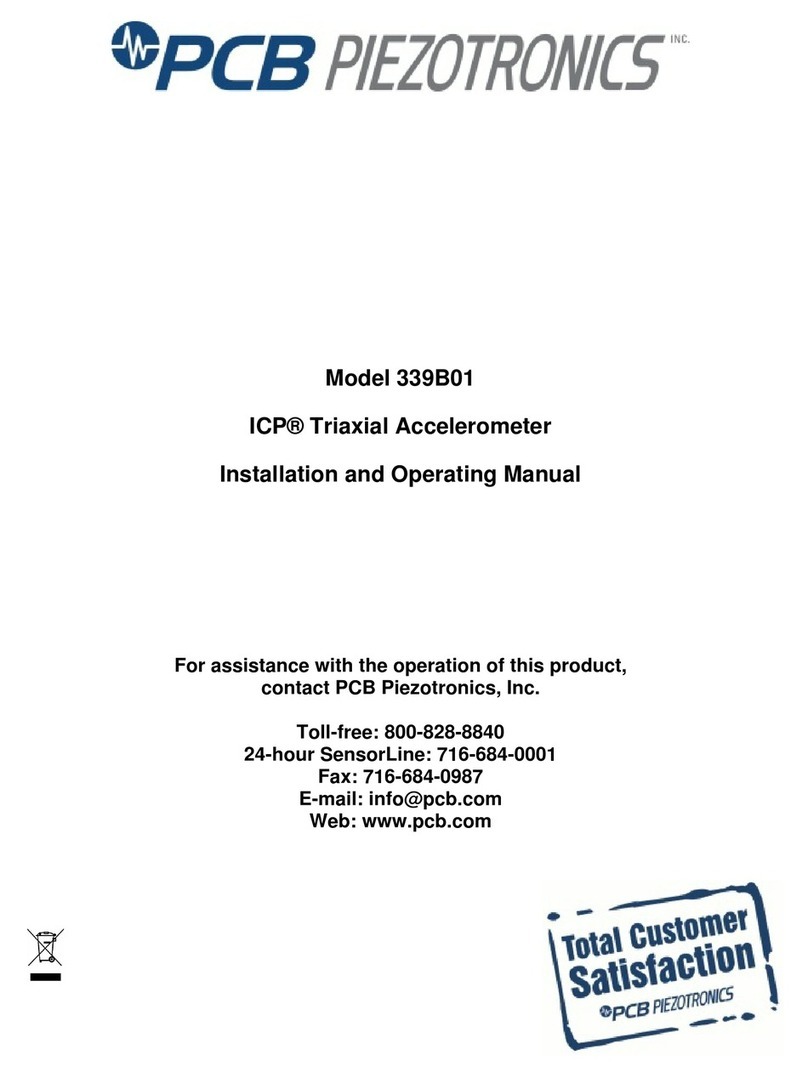
PCB Piezotronics
PCB Piezotronics 339B01 Installation and operating manual
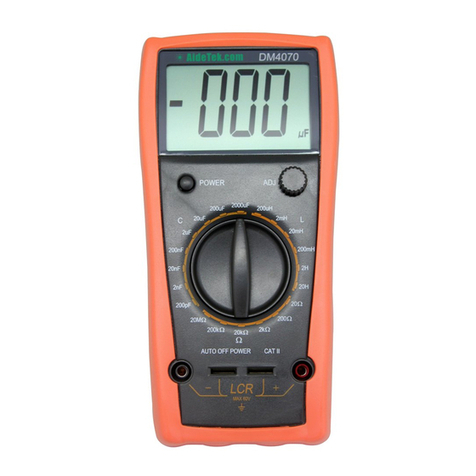
AIDETEK
AIDETEK DM4070 Operation manual
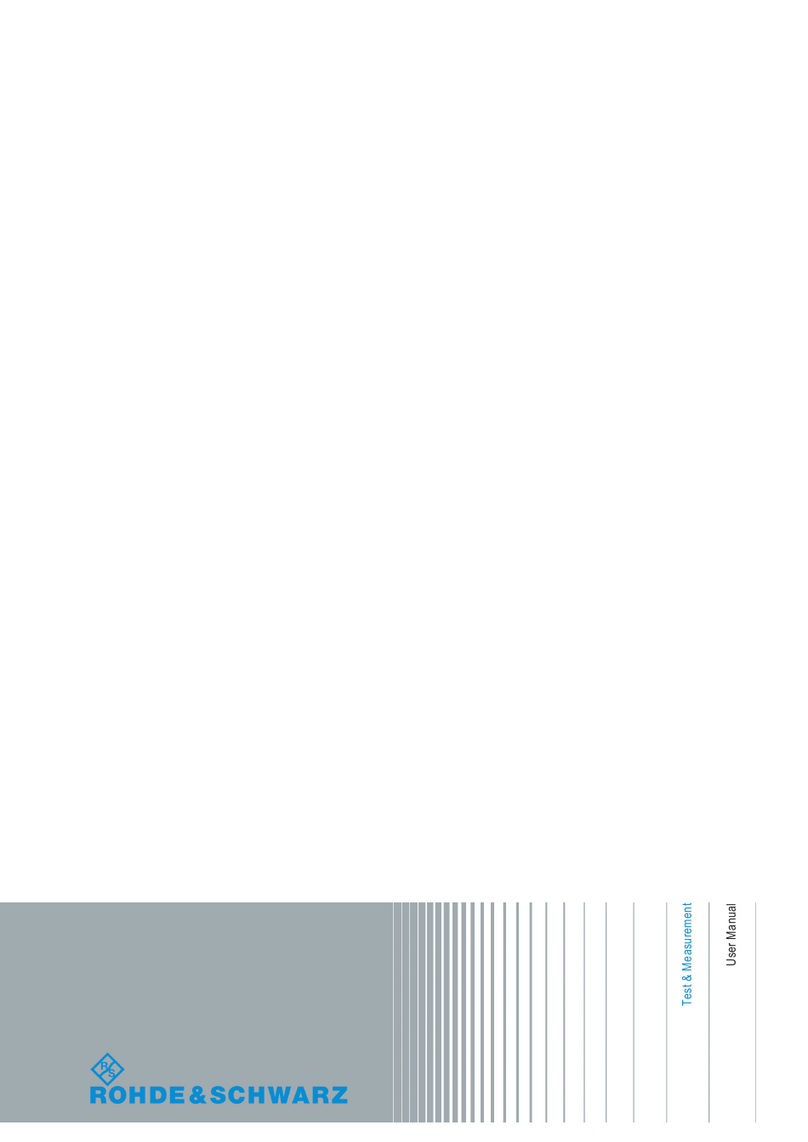
Rohde & Schwarz
Rohde & Schwarz R&S CMW-KN200 user manual
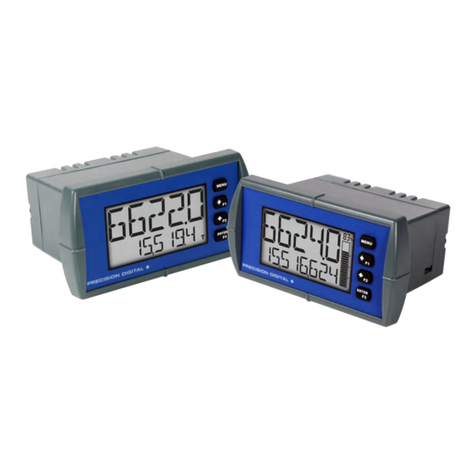
PRECISION DIGITAL
PRECISION DIGITAL Loop Leader PD6620 Series instruction manual
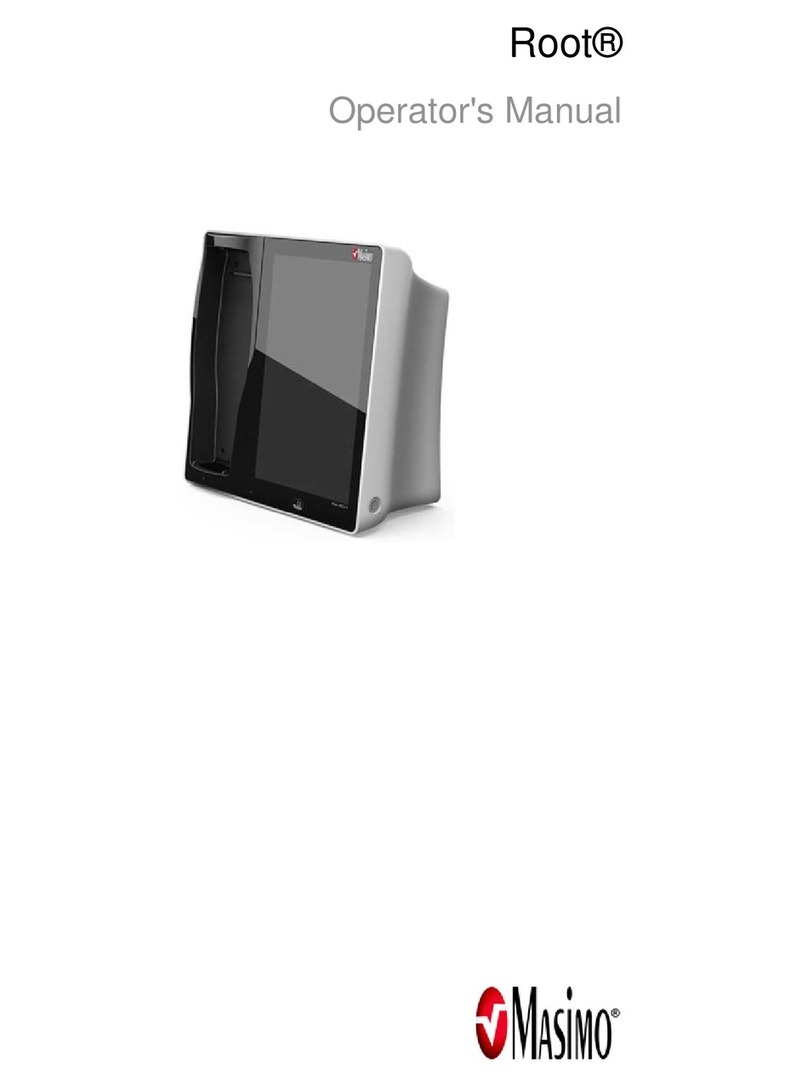
Masimo
Masimo Root RDS7A Operator's manual
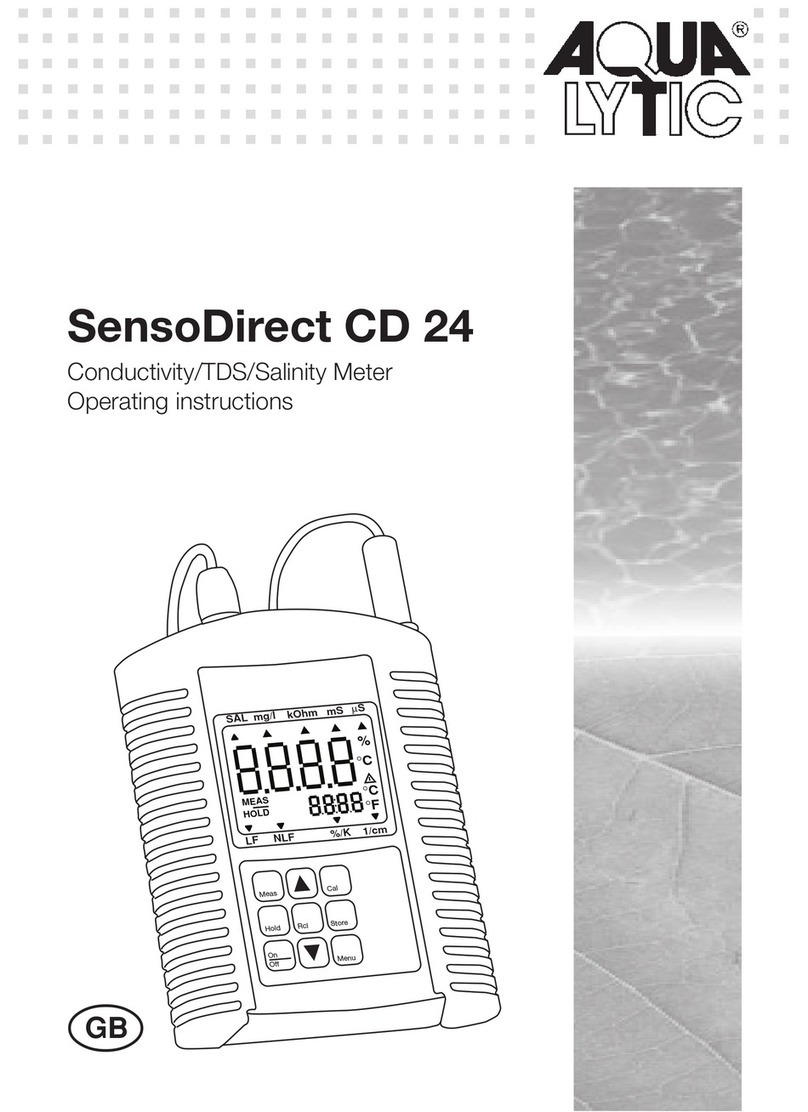
Tintometer
Tintometer AQUALYTIC SensoDirect CD 24 operating instructions
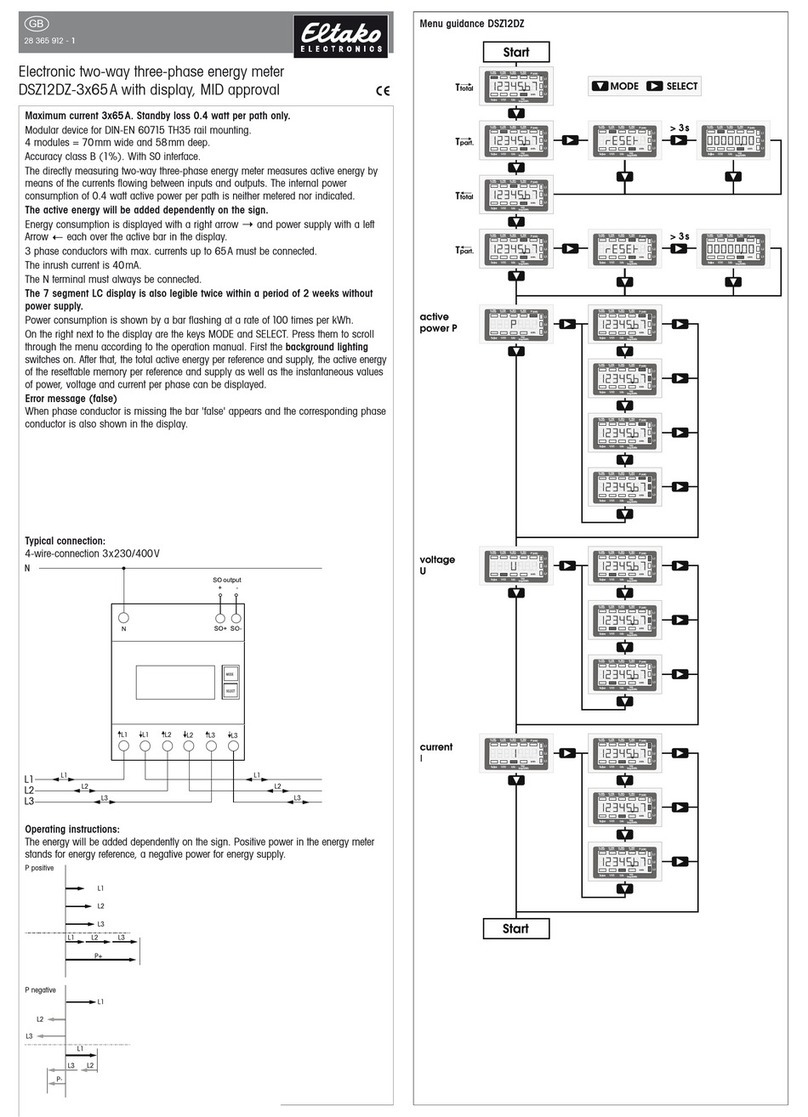
Eltako electronics
Eltako electronics DSZ12DZ-3x65A operating instructions
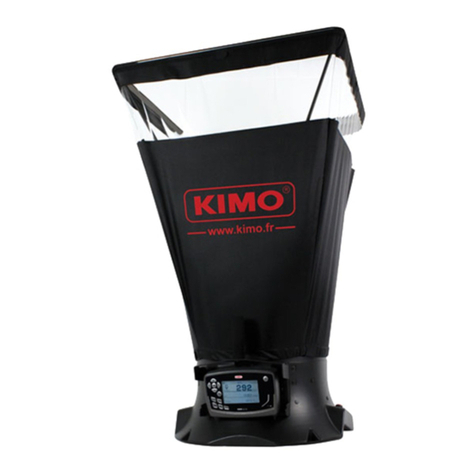
Kimo
Kimo DBM610 user manual

Bosch
Bosch BL 40 VHR PROFESSIONAL operating instructions
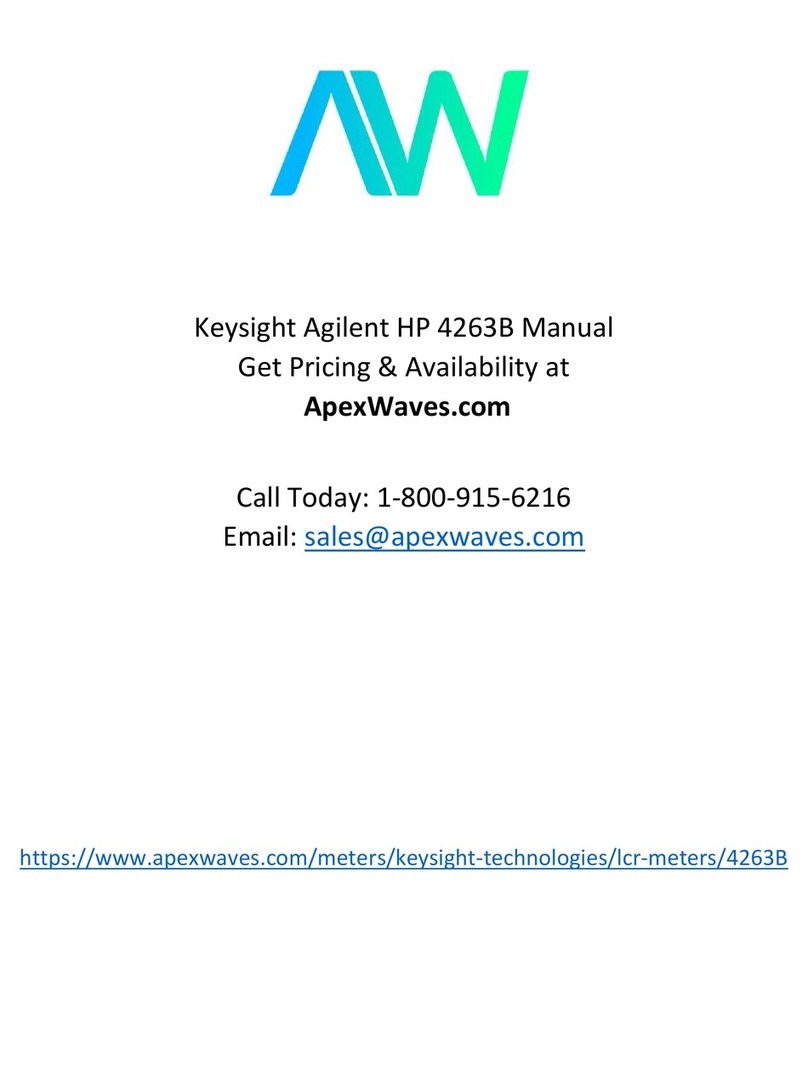
Agilent Technologies
Agilent Technologies 4263B Operation manual