Patterson RC User manual

OPERATION & MAINTENANCE
MANUAL
For
VIL VERTICAL INLINE PUMPS
Types RC, CC, and CS
PATTERSON PUMP COMPANY
A SUBSIDIARY OF THE GORMAN
-
RUPP COMPANY
PO Box 790
9201 Ayersville Road
Toccoa, Georgia 30577
Telephone: 706
-
886
-
2101
Fax: 706
-
886
-
0023

SA
FETY
PRECAUTIONS
WARNING
Do not operate this equipment in excess of its rated speed or other than in accordance with the
instructions contained in this manual.
The equipment has been found satisfactory of the conditions for which it was sold, but its operation in
excess of these conditions may subject it to stresses and strains which it was not designed to withstand.
For equipment covered by this instruction book, it is important to observe safety precautions to protect
personnel from possible injury.
Among the many considerations, personnel should be instructed to:
avoid contact with rotating parts
avoid bypassing or rendering inoperative any safeguards or protective devices
avoid extended exposure in close proximity to machinery with high noise leve
ls
use proper care and procedures in handling, lifting, installing, operating and maintaining the
equipment
do not modify this equipment consult factory if modification is deemed necessary
do not substitute for repair parts which can be provided by the e
quipment manufacturer.
Safe maintenance practices with qualified personnel are imperative.
Failure to heed this warning may result in an accident causing personal injury.
.

TABLE OF CONTENTS
SECTION I:
General Information
................................................................................
1
SECTI
ON II:
Storage & Protection
...............................................................................
1
SECTION III:
Installation
3-
1 Location
..............................................................................................
2
3-
2 Mounting
............................................................................................
2
3-
3
Piping
..................................................................................................
2
3-
4
Wiring and Controls
............................................................................
2
SECTION IV:
Operation
4-
1 Starting
...............................................................................................
2
4-
2 Shutdown
...........................................................................................
3
SECTION V:
Maintenance
..............................................................................................
4
SECTION VI:
Repairs & Rep
lacement
6-
1
Disassembly
.......................................................................................
5
6-2
Cleaning
.............................................................................................
5
6-3
Inspection
..........................................................................................
6
6-
4 Assembly
............................................................................................
6
Locating Operation Difficulties
..............................................................
7
Recommended Spare Parts
...................................................................
9
Typical Assembly Section
s
......................................................
1
0, 11, 12
Notes
.......................................................................................................
13

1
SECTION I
GENERAL INFORMATION
This manual covers the installation, operation and maintenance of Patterson Pump vertical inline pumps.
The pump is a centrifugal, single stage close-coupled type. When properly installed and when given
reasonable care and maintenance, centrifugal pumps should operate satisfactorily for a long period of
time. Centrifugal pumps use the centrifugal force principal of accelerating the liquid within a rotating
impeller, and then collecting it and converting it to pressure head in a stationary volute.
The pump consist
s of two assemblies:
1.
Volute assembly or stationary part
2.
Rotating element or moving part
The back pullout design casing allows removal of the impeller and rotating element without disturbing
suction and discharge piping. The suction and discharge flanges are on a common centerline 180
degrees apart. Suction and discharge flanges are drilled and tapped for gauge connections. The volute
is drilled and tapped on the underside for complete pump drain. Casing wear rings are provided as
standard equipment.
SECTION II
STORAGE & PROTECTION
All pumps are shop serviced and ready for operation when delivered, but there is occasions when
considerable time elapses between the delivery date and the time the pump is put into operation.
Equipment, which is not in service, should be kept in a clean, dry area. If equipment is to be stored for
long periods of time (six months or more), the following precautions should be taken to insure that the
equipment remains in good condition.
1.
Unpainted
-machined surfaces, which are subject to corrosion, should be protected by
some corrosive resistant coating.
2.
The shaft should be rotated 10 to 15 revolutions by hand periodically in order to spread
the lubricant over all the bearing surfaces. Suitable intervals are from one to three
months, depending on atmospheric conditions, etc. In order to insure that the pump shaft
does not begin to sag, do not leave the shaft in the same position each time.
3.
Space heaters on motors and controllers should be connected and fully operable if
atmospheric conditions approach those experienced in operation. Consult instruction
manuals for other precautions concerning storage of individual components of pumping
unit.
4.
Fresh lubricant must be applied to bearings upon removal of equipment from storage.
Refer to
motor manual.

2
SECTION III
INSTALLATION
3-1
Location:
Several factors should be considered when selecting a location for the pumping. The unit should be
accessible for both inspection and maintenance. Headroom should be provided for the use of crane,
hoist or other necessary lifting devices. The pump should be located as close as possible to the liquid
supply so that the suction line is short and direct. Location should require a minimum of elbows and
fittings in the discharge line t
o minimize friction losses. The unit should be protected against flooding.
3-2
Mounting:
The pump unit is designed to be installed in the pipeline. Standard piping supports on either side of the
pump should be us
ed to eliminate pipe stresses.
3-3
Piping:
The suction and discharge pipes must be in line, and the pump must not be used to pull the piping into
place
by
tightening
the flange bolts. Pipes should be supported near the pump.
3-4
Wiring and Controls:
The electric motor power supply connections mush conform to national and local codes. The
motor ratings stamped on the motor nameplate must match the line voltage and wire capacity
.
DO
NOT USE ANY OTHER VOLTAGE
SECTION IV
OPERATION
4-1
Starting:
Turn the pump shaft by hand to insure that the parts do
not bind
Open the valve in the pump suction line, if fitted
Close discharge valve
Prime the pump in one of the following ways:
1.
If the pump operates under positive pressure, open vent valve on top of the pump casing. After
all entrained air has escaped, close the vent valves. Rotate the shaft, if possible, to allow any air
trapped in the impeller passages to escape.
2.
If the pump operates on a suction lift and a foot valve is included in the system, fill the pump and
the suction line with liquid from an outside source. Trapped air should be allowed to escape
through the vent valve while filling.

3
3.
If the pump operates on a suction lift and no foot valve is provided, use a vacuum pump or ejector operated
by air, steam, water, etc. to evacuate air from the pump case and suction line by connecting the ejector to
the priming connection on top of the pump case.
Check direction of rotation before starting pump. Rotation should be the same as the direction
arrow on the case.
CAUTION:
Do not operate without l
iquid. Pump seals depend on the liquid being pumped for lubrication.
Make sure pump is primed and that no air is in the suction piping and the pump case.
Make sure all valves open or closed as required by your specific requirements.
Start driver:
Open
discharge valve slowly when the pump is up to speed.
CAUTION:
Overheating and/or loss of prime will result if the pump is operated against a closed valve for
more than a few minutes.
NOTE:
Should the pump fail to build up pressure or discharge water when the discharge valve is
opened, stop the pump and read
Section Locating Operating Difficulties
.
4-2
Shutdown:
The pump may be stopped with the discharge valve open without causing damage. However, in
order to prevent water hammer effects, as a general re
commendation
the discharge valve should
be closed first.
1.
Close discharge valve.
2.
Stop driver.
3.
If danger of freezing exists, isolate the pump by closing a valve in the pump suction line, if fitted,
and drain the pump completely

4
SECTION V
MAINTENANC
E
1.
There should be no mechanical seal leakage except for a brief break in period. Mechanical seals
should be replaced if they are leaking
3.
Refer to the motor manufacturer s instructions for periodic maintenance requirements.
4.
Check that electrical contro
l equipment contacts are in good condition and clean.
5.
Bearing relubrication requirements
refer
to the motor manufacturer s instructions
.
Do not
overlubricate the bearings.. Such action will cause bearings to overheat.
6.
Refer to the
General Pump Inspec
tion and Maintenance Schedule
for best results.
General Pump Inspection and Maintenance Schedule
VIL Pumps
, Types RC, CC, and CS
Excludes motors, VFD s, and controls.
Contact Patterson Pump Company if assistance is needed to determine the inspection
and service
requirements for a specific pump.
Inspect (
) or service (
) at the indicated calendar
time or run time interval
whichever comes first
Routinely
Monthly
2000
hours
or 3
months
4000
hours
or 6
months
8000
hours
or 12
months
Unusual noise
Unusual vibration
Unusual temperature
Leaks in pump or piping
Pressure gauge readings
Visual inspection of equipment general condition
Anytime a pump is opened, inspect the running
clearances and restore them to or
iginal specifications if
the running clearances have doubled
.
Anytime a pump is opened, inspect the impeller for
corrosion or excessive wear.
Mechanical seal (should be no leakage)
Drain lines are working properly
Coupling integrity (Type RC only)
Operate the pump
Add grease to motor anti-friction bearings
(maintain records)
Refer to
motor manufacturer s instructions.
Perform a comparative field test (flow, pressures, and
power) with calibrated instruments. Resto
re internal
running clearances if results are unsatisfactory (install
new wear rings).
Perform a comparative vibration test
Inspect sleeve. Replace if worn.

5
SECTION VI
REPAIRS AND REPLACEMENT
WARNING!!!
Whenever any disassembly work is to be done on the pump, disconnect the power source to the driver to
eliminate any possibility of starting unit. It is advisable that a qualified Pump service technician does the
disassembly and reassembly of the pump.
6-1
To Remove Impeller
and Mechanical Seal
Reference: Pump Assembly Section for the particular pump type
Types
CC and CS
-
To Remove Impeller and Mechanical Seal
1.
Remove bolting holding volute (1) to volute cover (11).
2.
Pull motor and impeller assembly from the volute.
3.
Rem
ove impeller (2) from the motor shaft by turning the impeller screw (26)
counterclockwise.
4.
Mechanical seal (65) may now be removed.
Type RC
-
To Remove Mechanical Seal
1.
Remove bolting holding rigid coupling (314) to motor shaft (10) and pump shaft (6).
2.
Remove bolting holding gland (17) to volute cover (11).
3.
Mechanical seal (65) may now be removed.
Type RC
-
To Remove Impeller
5.
Remove bolting holding volute (1) to volute cover (11).
6.
Pull motor and impeller assembly from the volute.
7.
Remove impeller (2) from the motor shaft by turning the impeller screw (26)
counterclockwise.
6-2
Cleaning:
WARNING!!!
Petroleum based cleaning solvents are flammable. Smoking or open flames in the vicinity of these
solvents is extremely hazardous and must not be permitted. Disregarding this warning could result in
grave personal injury.

6
Clean all metal parts with a solvent. Use a bristle brush (not metal or wire) to remove tightly adhering
deposits. A fiber scraper may be used to remove the gasket and shellac from cas
ing flange. Blow dry with
clean dry compressed air.
CAUTION:
Never use hydrocarbon liquids (oil or solvent) to clean mechanical seal parts
.
Use of oil or solvent
will deteriorate material used on the seal.
Use mild soap solution to clean seal parts. Use only your finger to remove dirt. Rinse with clean
water and dry with mild air stream. Use care not to damage or scratch lapped surfaces.
6-3
Inspection:
Visually inspect parts for damage affecting serviceability. Check o-rings and gaskets for cracks, nicks, or
tears; packing rings for excessive compression, fraying or shredding, and embedded particles. Replace if
defective in any way. Mount shaft between lathe centers and check eccentricity for entire length of the
shaft. Eccentricity should not exceed .002 inches. Bearing surfaces should be smooth; shoulders square
and free of nicks.
Measure OD of impeller hub and ID of pump casing. Compute diametrical clearance (ID minus OD) and
compare with the original pump specifications. Surfaces must be smooth and concentric. Examine
impeller passages for cracks, dents or embedded material. Examine shaft sleeves for wear
6-4
Assembly:
Assembly is the reverse of the disassembly procedure. The following should prove helpful in
reassembling the pump:
1.
All parts, inside and out, should be clean. Dirt and grit will cause excessive wear, plus needless
shutdown.
2.
Make certain that the keys are in their proper position.
3.
Rotate by hand to insure that the parts do not bind.
4.
Use sealant between the shaft sleeve and shaf
t whenever the sleeve has been removed.

7
LOCATING OPERATING DIFFICULTIES
In the majority of cases, operating difficulties are external to the pump and the following causes should be
carefully investigated before undertaking repairs:
No W
ater Delivered
Pump not primed
indicated by no pressure on discharge.
Speed too low
indicated by low pressure on discharge.
Valve closed
indicated by high discharge head.
Impeller completely plugged up
indicated by low discharge pressure.
Abno
rmally Small Quantities Delivered
Air leaks in suction pipe or stuffing boxes.
Speed too low.
Discharge head higher than anticipated.
Impeller partially plugged up.
Obstruction in suction line.
Mechanical defects: casing rings worn, impeller damaged
, casing or seal defective.
Insufficient Pressure
Speed too low. Might be caused by low voltage or current characteristics different from
nameplate reading on the motor.
Air in water will cause the pump to make a cracking noise.
Mechanical defects: w
orn casing rings, damaged impeller, defective casing or seal.
Intermittent Operation
Leaky suction line.
Water seal plugged (hence, a leaky stuffing box).
Suction lift too high.
Air, gas or vapor in liquid.

8
Pump Overloads Driver
Speed too hig
h.
Head lower than rated, hence, pumping too much water. (This is valid for low specific speed
pumps).
Mechanical defects: stuffing boxes too tight, shaft bent, rotating element binds.
Rubbing due to foreign matter in the pump between the case rings an
d the impeller.
Pump Vibrates
Misalignment.
Foundation not sufficiently rigid.
Impeller partially clogged.
Mechanical defects: bent shaft, rotating element binds, bearings worn, coupling defective.
Suction and discharge pipes not anchored.
Pump cav
itating from too high a suction lift.
Air entrainment in the pump suction due to low submergence.

9
RECOMMENDED SPARE PARTS FOR VIL PUMPS
, Types RC, CC, and CS
Reference: Assembly Section
for the Pump Type
INTERMITTENT DUTY
Number
Description
7
Casing Ring
14
Shaft Sleeve
(Type CC only)
65
Mechanical Seal
Gasket
(casing)
CONTINUOUS DUTY
Number
Description
2
Impeller
6
Shaft
(Types RC and CS only)
7
Casing Ring
14
Shaft Sleeve (Type CC only)
26
Impeller Screw
40
Deflector
(Types CC and CS only)
65
Mechanical Seal
314
Coupling and
bolts
All Hardware (not shown)
Gasket (casing)




13
Notes
This manual suits for next models
2
Table of contents
Popular Power Pump manuals by other brands
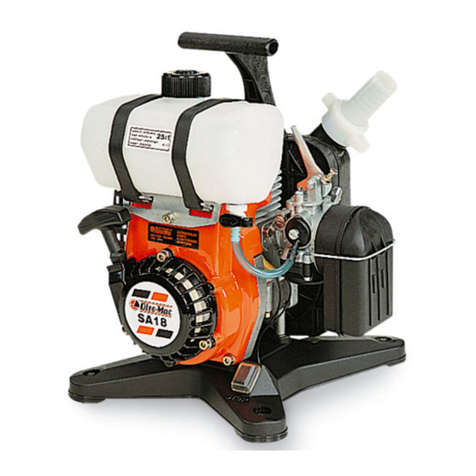
Oleo-Mac
Oleo-Mac SA 18 Operators instruction book
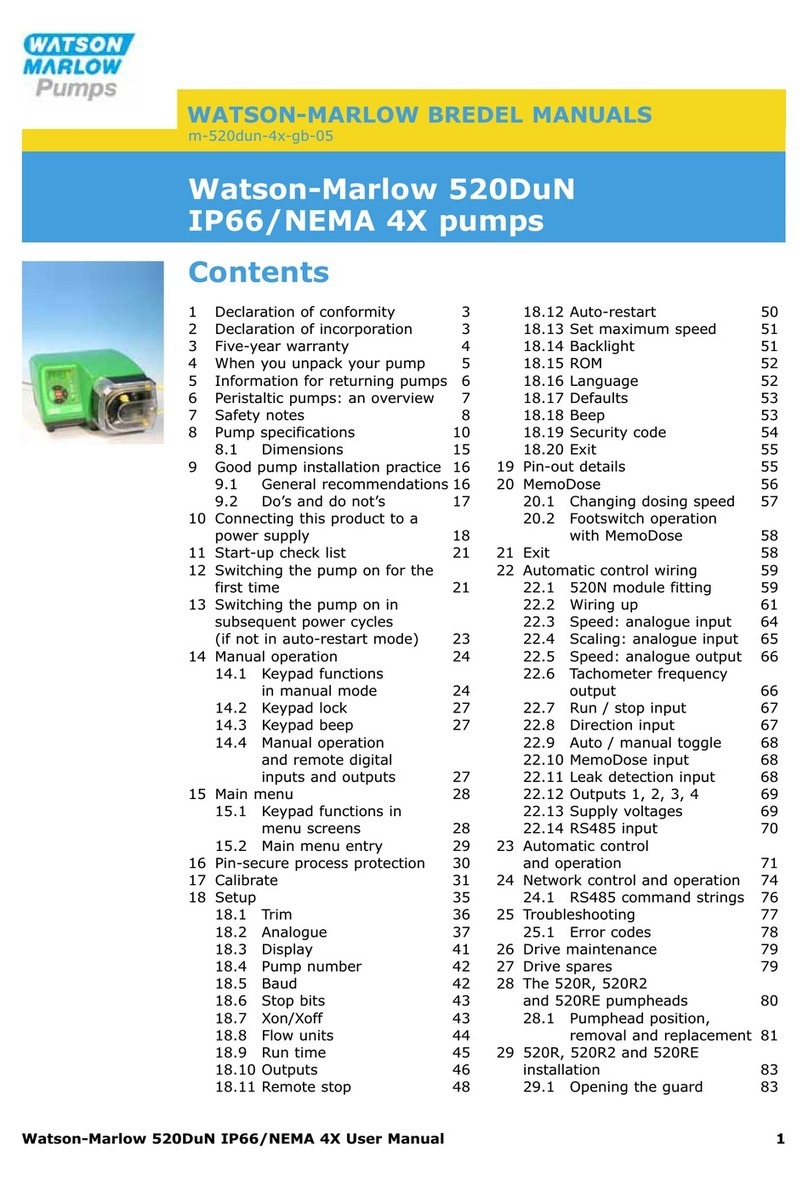
Watson-Marlow
Watson-Marlow 520DUN user manual
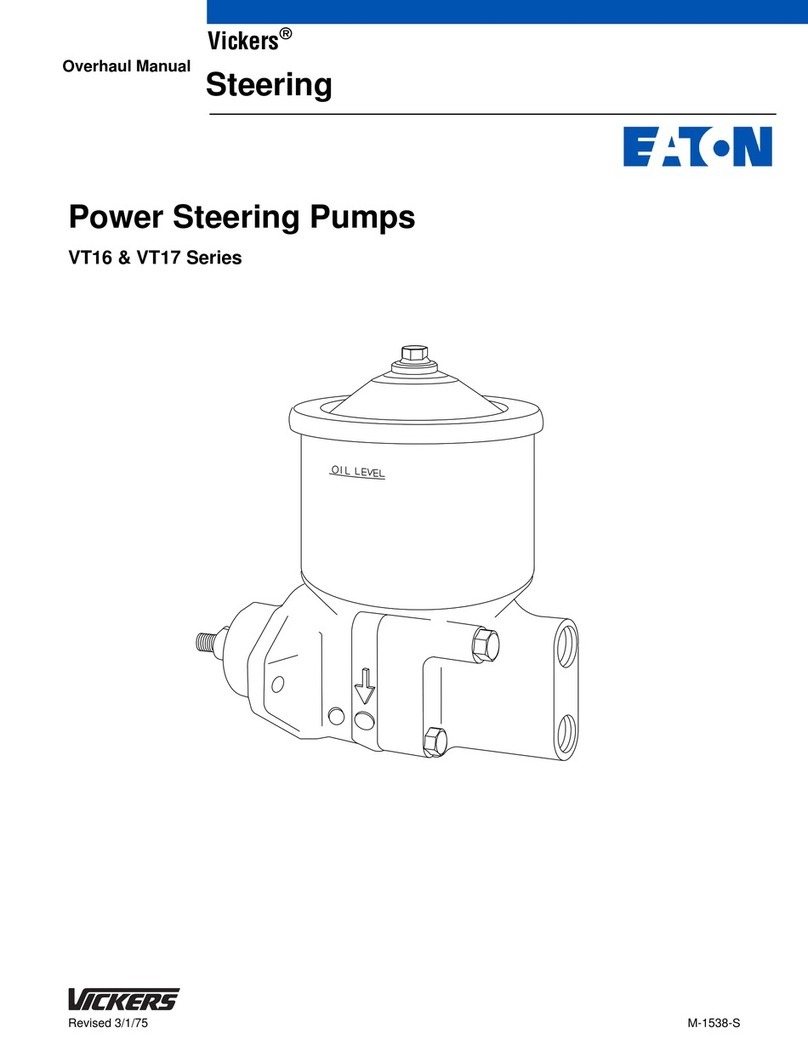
Eaton
Eaton Vickers VT16 Overhaul manual

Waterra
Waterra POWERPUMP 2 owner's manual

Chemtech Scientific
Chemtech Scientific 1402N owner's manual
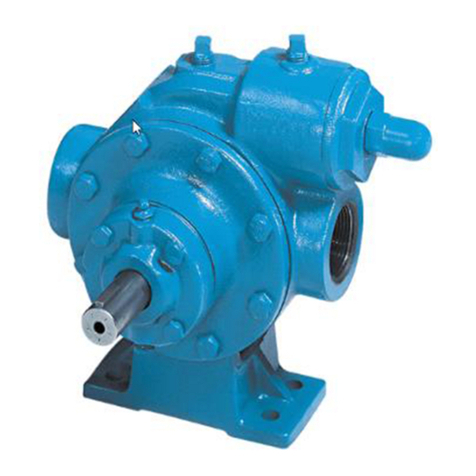
BLACKMER
BLACKMER XRLW1.25A Installation, operation and maintenance instructions