PEMTECH PT900-8FG User manual

MODEL PT900-8FG
8 CHANNEL
GAS MONITOR & CONTROLLER
Operator’s
Manual
Revision 2.0
March 2001
Pem-Tech, Inc.
Houston, Texas
U.S.A.

2
NOTICE
PEM-TECH INCORPORATED SHALL NOT BE LIABLE FOR
TECHNICAL OR EDITORIAL ERRORS OR OMISSIONS MADE
HEREIN, NOR FOR INCIDENTAL OR CONSEQUENTIAL
DAMAGES RESULTING FROM THE FURNISHING,
PERFORMANCE, OR USE OF THIS MATERIAL.
LIMITED WARRANTY
Pem-Tech, Incorporated warrants all the equipment to be free from defects in
workmanship and material. The products will operate in conformance with the
published specifications when subjected to intended and proper usage for the
period of one (1) year from the date of shipment.
The warranty provides only the benefits specified and does not cover defects
which result from acts beyond the control of PEM-TECH including, but not
limited to: damage by accident, negligence, tampering, or failure to operate in
accordance with the procedures outlined in the Operations Manual. PEM-
TECH’s liability under no circumstances will exceed replacement of the unit
claimed to be defective.
Tampering with the equipment and altering it for uses other than the intended
use or replacement of parts not supplied by the company, shall immediately
void and cancel all the warranties with respect to the affected products.
The warranties specified herein are in lieu of any and all other warranties,
express or implied. In no event, whether as a result of breach of warranty or
alleged negligence, shall PEM-TECH be liable for special or consequential
damages, including, but not limited to, loss of profits or revenue, loss of
equipment or down time costs.

3
SERVICE POLICY
Pem-Tech has service facility at the factory. For all the repairs contact at our toll
free number 1-800-379-3894 or visit our website www.pem-tech.com
For all repairs call us for a Return Material Authorization number (RMA).
Inform us briefly the nature of the problem and obtain shipping address.
Properly pack the equipment before shipping. Also include your complete
shipping address and contact name and phone number.
For non-warranty repairs you must provide the limit to repair costs. State if a
quote for repair cost is required before you can authorize the repair cost. For this
an additional charge may be applicable.
NOTE:
1. For all the repairs under warranty, serial number must be legible on the items
being repaired.
2. Shipping point is FOB Houston.

4
TABLE OF CONTENTS
Specifications 5
Specifications for PT900-8FG Rack assembly 5
Specifications for Model PT950-B Control monitor 6
Overview 7
Programmable Relays 7
Figure 1. PT950-B Control module Front Panel diagram 8
Installation and Startup 9
Figure 2. PT900-8FG Enclosure dimension 9
Figure 3. System Overview drawing, 10
User termination, control modules in
Rack assembly
AC or DC power Input 11
Connecting sensors to monitor 11
Alarm wiring 11
Figure 4. Sensor and alarm wiring diagram 12
Figure 5. Wiring auxiliary relay board for common 13
Alarm contacts
Startup 14
Apply Power 14
Normal Operation and alarms
Normal Operation 15
Alarms 15
Alarm Reset 15
Alarm Bypass 15
Programming Alarms 16
Programming Alarm Levels 17
Setting alarms as Latching or Non-Latching 17
Setting alarm contacts as Normally Open or 18
Normally Closed
Figure 6. PT950-B Control Monitor circuit diagram 19
Malfunction Condition 20
Parts List 21

5
SPECIFICATIONS
For PT900-8FG Rack Assembly with Power Supply
MOUNTING: Wall or Panel Mount
ENCLOSURE: NEMA 4X Fiberglass Enclosure with clear
window
DIMENSIONS: 16” Wide x 20” High x 10”Deep
WEIGHT: 38 Lbs.
OPERATING -40 °F to +170 °F.
TEMPERATURE
POWER INPUT: 117-220 VAC or 24-28 VDC
HUMIDITY: 0 to 95% non condensing
AUXILIARY ALARM 4 Common alarm relays
RELAYS Form “C” type rated 10Amps
TERMINATIONS Terminal blocks for sensor and alarm
connections for wire size 16-22 AWG
ALARM RESET Master alarm Reset switch to Reset or
SWITCH Acknowledge alarms on all control modules

6
SPECIFICATIONS
For PT950-B Control Module
Display Range: 0 to 99 for Toxic and Combustibles
0 to 25.0 % for Oxygen deficiency
Others depend on the range of the Sensor.
Input Signal: 4-20mA (Optional 1-5 VDC)
Analog Output: Linear 4-20mA output. < 1.5mA when remote
sensor in malfunction.
Maximum of 350 Ohms loop resistance.
Relay Ratings: 4 each Form “C” type relay contacts
Rated 5 Amps each
Low, High, High-High, and Malfunction
Field programmable alarm levels, Latching or
non-latching, Normally open or Normally
Closed contact
Visual Indicators: 4 Bright LEDs on the front panel to indicate
alarm status. Amber LED for Low Alarm
Red LEDs for High and High-High and
Malfunction Alarm
Power Input: 24 VDC power input. Power is supplied
to remote sensor & transmitter through a 2
Amp miniature fuse
Power Consumption: < 1.2 Watt normal operation for each control
module. Max of 2.4 watt with all relays active.

7
OVERVIEW
Pem-Tech model PT950-B is a microprocessor based single channel
monitor that utilizes the latest digital design techniques in
instrumentation. The monitor uses an 8-bit high speed RISC processor
with a highly accurate analog to digital logic. The controller module
receives signals from remote gas transmitters, displays the gas
concentration, generates 4-20mA analog output for recorders and relay
outputs for alarm warning devices. Each control module uses 24VDC
power and supplies power to the remote gas transmitter connected.
Standard features are:
•Displays current gas concentration on two (2) Digit Bright LED
display
•Provides a 4-20mA output.
•Low, High, & High-High fully programmable alarm relay contacts.
•Alarms programmable via switches on the front panel
•Sensor Malfunction relay contact.
•Visual alarm indicators on the front panel.
•Alarm RESET and BYPASS switch.
•RS485 Serial Communication for Remote data display
•Master Alarm Reset on the main rack assembly to Reset Alarms.
Programmable Relays
Each control module has three (3) programmable relays for Low, High,
and High-High alarms. The alarm relay set points can be programmed
via pushbutton switch provided on the front panel. On the main
termination board of PT900-8 rack system alarm terminals are provided
for each of the control module. A common terminal is also provided for
sensor malfunction (or fault). This terminal is common to the Fail relays
on all the control modules in the system. The terminal can, therefore, be
used as dry contact for a local audible alarm. In addition jumper blocks
are also provided to common all the relays on the control modules in
order to use an auxiliary relays.
For further details refer to section on Programming alarm Relays later in
this manual.

8
ALARMS
NORMAL
BYPASS
PEM−TECH, INC.
LOW
HIGH
HI−HI
MALF
MODEL PT 950
MONITOR
HOUSTON, TEXAS
Di
g
ital Displa
y
Visual Alarm LED indicators
Alarm B
yp
ass Switch
Pushbutton switch
(Alarm Reset & Adjust)
Captive Screw
Handle
Figure 1. PT950-B Control Module

9
INSTALLATION AND START UP
Model PT950-B Control Module is suitable to mount in any PT900 Series
Rack assembly with card guides for main circuit board mounting. On the
front panel a captive screw is provided to secure the control module to the
rack. Do not use excessive force to tighten the screw. Also a handle is
provided to facilitate for insertion and removal of the module from the
rack assembly.
PT900-8 FG enclosure must be installed in a safe area. Figure 2 shows the
mounting holes for the fiberglass enclosure.
Figure 2. Dimensions for PT900 Series Fiberglass enclosure
4 MOUNTING HOLES
DIA = 0.35"
FIBERGLASS ENCLOSURE
16" WIDE x 20" HIGH x 10" DEEP
18.75"
12.0"

10
Figure 3. User termination – PT900-8FG
8 Each PT950 series control modules in Fiber
g
lass
DRAWINGNO.
REV.
SHEET
+
E
−
EXTRESET
G
L2
L1
ACIN
FROM
PWRSUPPLY
18−28VDC
POS
NEG
RESET
ALARMS
POWERSUPPLY
PANELSCREWS(4EACH)
MASTERALARMRESETSWITCH
EXTERNALALARMRESET
117−220VACINPUT
FORONBOARD
POWERSUPPLY
18−28VDCFROM
ONBOARDAC/DC
POWERSUPPLY
+==>SENSORSUPPLY
−==>SENSORGND
E==>SENSORSIGNALIN
B2003230
1.0
1OF1
USERTERMINATION−MODELPT900−8FG
8EACHPT950BCONTROLMODULES
INFIBERGLASSENCLOSURE
1
0
POWERON/OFF
CH1
E
−
CH2
+
E
−
CH3
+
E
−
CH4
+
E
−
CH5
+
E
−
CH6
+
E
−
CH7
+
E
−
CH8
+AUX.RELAY
POWER
POS
NEG
RS485
8REMOTESENSORCONNECTION
MOUNTEDBEHINDFRONTPANEL
3CONDUCTORCABLE
10AMPAUXRELAYBD.
DATE:03/20/03
(optional)
4−20mAOutput
LOW,HIGH,HI−HI
ALARMRELAYCONTACTS
CONNECTIONTO
REMOTEREADOUT
(2CONDUCTORSHIELDEDCABLE)
SWITCH

11
AC or DC Power Input
A black terminal block is provided at the lower left corner inside the
enclosure. The connections on the terminal block are labeled L N G.
Connect the external 117-220 VAC power to this terminal.
If the unit is powered by DC, connect 24 VDC supply to the 2 pin green
terminal labeled DC power input on the termination board.
Refer to figure 3 for the location of AC and DC terminals
Connecting Sensors to the Monitor
Three (3) pin screw type terminals are provided on the termination board
for remote sensor connection. The terminals are labeled as SENSOR and
each pin is identified as +, -, & E for sensor DC supply, ground, and
signal respectively. The DC is supplied to the sensor by the control
module. The supply is fused through a 2 amp miniature fuse on the
control module.
Each remote sensor should be connected by a 3 conductor shielded cable.
See figure 4 for remote sensor connection.
Alarm Wiring
Figure 4 shows a typical wiring diagram for connecting alarm devices to
relay contacts on the control module. Note that contacts are dry or
potential free contacts. Refer to the wiring details provided by the
manufacturer of alarm devices.
Figure 4 shows the wiring of alarm devices to the relay contacts of a
control module. Similar wiring procedure should be followed if the
auxiliary relay board is used to connect to the alarm devices. The
auxiliary relays interface board is located in lower right corner of the
termination board.
The auxiliary relay board is pre-wired at the factory and all jumpers on
JMP1 thru JMP-11 are installed. The jumpers are used to connect each
contact of the alarms (Low, Hi & Hi-Hi) to common auxiliary alarms.
Auxiliary relay will be energized if the corresponding alarm relay is
activated on any of the 8 control modules in the rack assembly.
Refer to figure 5.

12
Figure 4. Remote Sensor connection.
Alarm wiring to control modules.
EXTERNAL PWR
SOURCE FOR ALARMS
CH1 CH2 CH8
+ (+24VDC)
− ( COMMON / GND )
E (mA OUTPUT)
+
−
E
SENSOR
4−20mA
LOW
HI
HI−HI
ALARM 3
DEVICE
DEVICE
ALARM 2
ALARM 1
DEVICE
COM
OUT
COM
OUT
COM
OUT
+VSUPPLY
RETURN
+
−ANALOG OUTPUT
PT900−8 TERMINATION BOARD
4−20mA
TERMINATION BOARD
FOR REMOTE
SENSOR & TRANSMITTER
NOTE:
COMPLETE TERMINATION BOARD
IS NOT SHOWN.
CONNECTIONS FOR ALL CONTROL
MODULES ARE SIMILAR

13
Figure 5. Wiring Auxiliary relay board for common alarm
contacts
10A
RELAY
RELAY
10A
RELAY
10A
RELAY
10A
AL1
AL2
AL3
AL4
COM
GND
+V
AL1
AL2
AL4
AL3
24VDC
COM
OUT
COM
OUT
COM
OUT
COM
OUT
LOWHIGHHI−HI
SENSOR4−20
COM
OUT
OUT
COM
OUT
COM
OUT
OUT
OUT
COM
COM
COM
LOWHIGHHI−HI
OUT
COM
JMP−1 JMP−2 JMP−7
NOTE:
INSTALL JUMPERS JMP−1 THRU JMP−7
TO TIE ALARM CONTACTS OF EACH
CONTROL MODULE TO AUXILIARY
RELAY BOARD
CONNECT ALARM TERMINALS OF CH8 TO
AUXILIARY RELAY BOARD AS SHOWN
*
*
GND
+V
COM
OUT
COM
OUT
AUX RELAY
COIL PWR
AUXRELAYBOARD
SENSOR4−20
SENSOR4−20

14
Start Up
Complete the following procedures for the normal unit operation.
1. Complete the mounting and wiring procedures described in earlier
sections.
2. Follow gas sensor & transmitter operation manual for proper wiring of
sensors with the monitor.
3. Verify all the wiring connections to be correct and secure.
4. Verify that all the control modules are secured with captive screws on
the front panel.
Apply Power
Before connecting the AC power to the AC terminal on the termination
block make sure that POWER Switch on the unit is in OFF or ‘0’ position.
Flip the Power switch to ON or ‘1’ position to turn on the power to the
monitor and verify following conditions.
1. All the installed control modules will display their corresponding
channel number on the display (channel 1 thru 8). For example the
control module in the slot 1 will display 01, module in slot 2 will
display 02 and so on. The channel number will rapidly flash for few
seconds.
2. Each control module will then display low, high and High-High alarm
set points. The visual alarm LED indicator will be lit while the unit
displays the alarm set point.
3. The control module goes into normal operation and starts reading
signal from the sensor / transmitter.
Note: If a control module display remains blank upon power up or the
channel number flashing is incorrect then remove the control module and
reinsert into card guides in order to properly snap into the card edge
connectors on the termination board.

15
NORMAL OPERATION AND ALARMS
Normal Operation
During normal operation each control module will display the current gas
concentration on the display. If the sensor reading is below alarm level
then all the alarm relays and the visual alarm LED indicators on the front
panel should be off.
Alarms
Each PT950-B control monitor is equipped with four (4) alarm relay
contacts. The alarms are labeled as Low, High & High-High. The fourth
alarm contacts is for sensor malfunction. The monitor activates the alarm
relays when the sensor reading exceeds the programmed alarm set point.
Also LEDs on the front panel will also light up for visual alarm indication.
Standard alarm set points are programmed at the factory before shipment.
The user must verify the alarm set points and make changes if desired.
Refer to section on Programming Alarm Set points.
Factory Alarm Settings are:
Alarm # Alarm Level Alarm Type Contact Type
Low Alarm 10 Non-Latching Normally Open
High Alarm 15 Non-Latching Normally Open
High-High 20 Non-Latching Normally Open
Alarm Reset
Once the gas concentration has dropped below the alarm level the relay
will deactivate itself. However, this is true only of the relay is configured
as non-latching (NL). If the relay is configured latching then it must be
deactivated manually. To deactivate the latching alarm press and hold the
push button on the front panel until relays and LED indicators turn off. A
master alarm reset switch on the control module rack assembly can also be
used to reset the alarms. This will reset alarms on all control modules.
Note: If the gas concentration continues to be higher than the programmed alarm
set point the alarm will be activated again.

16
Alarm Bypass
In the Alarm Bypass mode the monitor will not activate the alarm relays if
any of the sensor reading exceeds the programmed alarm level. However,
the visual alarm LED indicators will be activated.
To put the alarms in bypass mode move the ALARM toggle switch on the
front panel of the control module to BYPASS position. If the gas reading
is above alarm level the visual alarm LED indicators will flash once every
second indicating that the alarms are in bypass mode. The switch must be
returned to NORMAL to end alarm bypass mode and for normal
operation.
Programming Alarms
Alarm levels must be programmed in order to activate the dry relay
contacts on the main control board. Alarm levels can be set anywhere
between 0 and the full scale of the sensor. Alarm relays can also be
selected as Latching or non-latching type. Also jumpers on the control
module can be selected to program the relay contacts to be Normally Open
or Normally Closed.
If any alarm level is set to 00 then that relay will not be activated any time
during normal operation.
Note
•Non-Latching alarm is self resetting. Alarm relay will be de-activated if gas
concentration falls below the alarm set point.
•Latching alarm on the other hand will not self reset if concentration falls
below alarm set point. The alarm relays must be manually reset by pressing
the RESET switch on the front panel

17
Programming Alarm Levels
1. Move the toggle switch on the front panel to BYPASS position.
2. Press and hold the pushbutton switch (above the toggle switch) until
the Low alarm LED starts flashing. Release the switch.
3. While the LED is flashing the display will show the current alarm
level. To change the level press and hold the pushbutton switch until
the display reads the desired alarm setting. The alarm level can be
adjusted between 0 and the full scale of the sensor. For example, for
H2S or LEL the alarm level can be set between 0 and 99. If the desired
alarm level is below current settings press and hold the switch. The
displayed alarm level will start over from 0 after 99.
4. Release the switch when alarm level set.
5. About five (5) seconds after the switch has been released the Low
alarm LED will be turned off. Low alarm level is set. Now High alarm
LED starts flashing and the display will show the High alarm level.
The monitor is ready for High alarm level. Repeat steps 3 and 4 to set
High and High-High alarm levels.
6. After setting High-High alarm level the monitor will return to normal
operation.

18
Setting Alarm as Latching or Non-Latching
The alarms can be set as latching or Non-Latching by setting the Dip-
Switch located on upper left corner of the control module. See figure 6.
The dip-switch is labeled as Relays with arrow indicating the switch
selection for latching or non-latching. Position 1 of the Dip-switch is for
Low alarm , position 2 is for High alarm and position 3 for High-High
alarm. Position 4 is not used for standard application and is reserved for
custom application or future use.
To set the alarm as latching move the dip-switch up or move the dip
switch down for non-latching alarms.
The dip-switch positions in the diagram below shows Low and High
alarm configured as non-latching and High-High alarm set as latching
Setting alarm contacts as Normally Open or Normally Closed
To set the alarm contacts as normally open or normally closed set the
jumpers for each relay located right above the relay on the control
module. See figure 6. Each jumper is a 3 pin header with a mating
connector to connect any two of the three pins. To set the contact type set
the jumpers as show below.
RELAYS
LATCHING
NON−LATHING 123 4
NO NC NO NC
Jump Pin 2 and 3 for
Normally closed contacts
Jump Pin 1 and 2 for
Normally Open contacts

19
D10
K4
K3
K2
K1
DIPSWITCHFOR
LATCHINGOR
NON−LATCHINGRELAYCONTACTS
JUMPERSELECTIONFOR
NORMALLYCLOSED
OR
NORMALLYOPEN
RELAYCONTACTS
NC=NORMALLYCLOSED
NO=NORMALLYOPEN
RELAYS
LATCHING
NON−LATHING
ADJ4−20
OFST
SPAN
SENSOR
FUSE
HI−HI
HIGH
LOW
MALF
NONC
NONC
NONC
NONC
4AMPMINI
SENSORFUSE
SETJUMPER
NORMALLYCLOSED
OR
NORMALLYOPEN
NONCNONC
SWITCHPOSITIONUPFORLATCHING
DOWNFORNON−LATCHINGPOTENTIOMETERSTO
FINETUNE4−20mA
ANALOGOUTPUT
PUSHBUTTONSWITCH
ALARMRESET/BYPASS
TOGGLESWITCH
Figure 6. PT950-B Control Module

20
Malfunction Condition
The malfunction alarm is activated when the 4-20ma analog output from
the sensor transmitter falls below 2.0mA. This is caused if the sensor
requires calibration. The malfunction also occurs if wires connecting the
sensors are broken. The fault relay is always non-latching and has a
common alarm contact on the PT900-8FG termination board. The relay
however, can be programmed as normally open or normally closed.
If a fault condition occurs:
1. Make sure the wires on the sensor input terminal of the main
connection board are secure and connected properly.
2. Check if the sensor supply fuse located on the control module is OK.
The fuse can be checked by verifying the DC power on the sensor
terminal using a digital voltmeter. If the + and - pin on the sensor
terminal reads 24VDC then the fuse is OK. See figure 6 for the location
of the fuse on the control module.
3. Refer to the reference manual of the remote sensor for the problems the
sensor transmitter may have.
Table of contents
Other PEMTECH Controllers manuals
Popular Controllers manuals by other brands
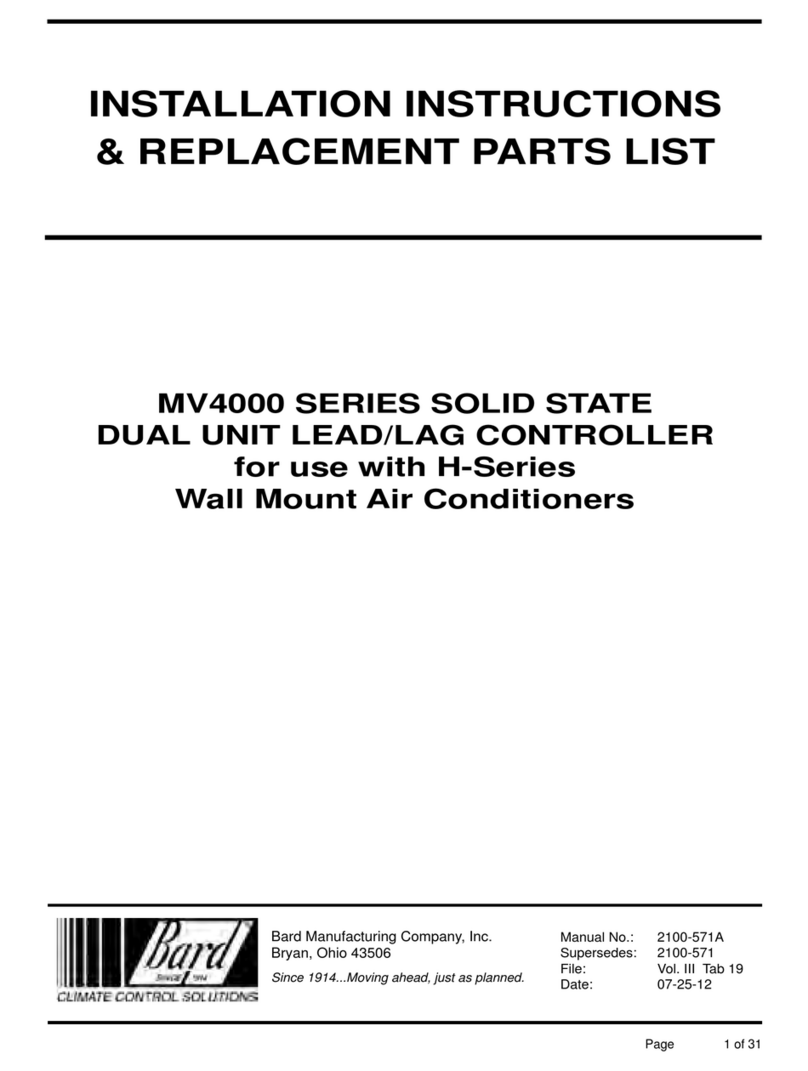
Bard
Bard MV4000 SERIES Installation & parts manual
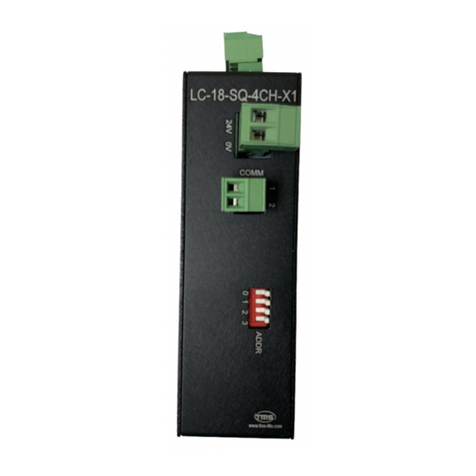
TMS Lite
TMS Lite LC-18-SQ-4CH user manual
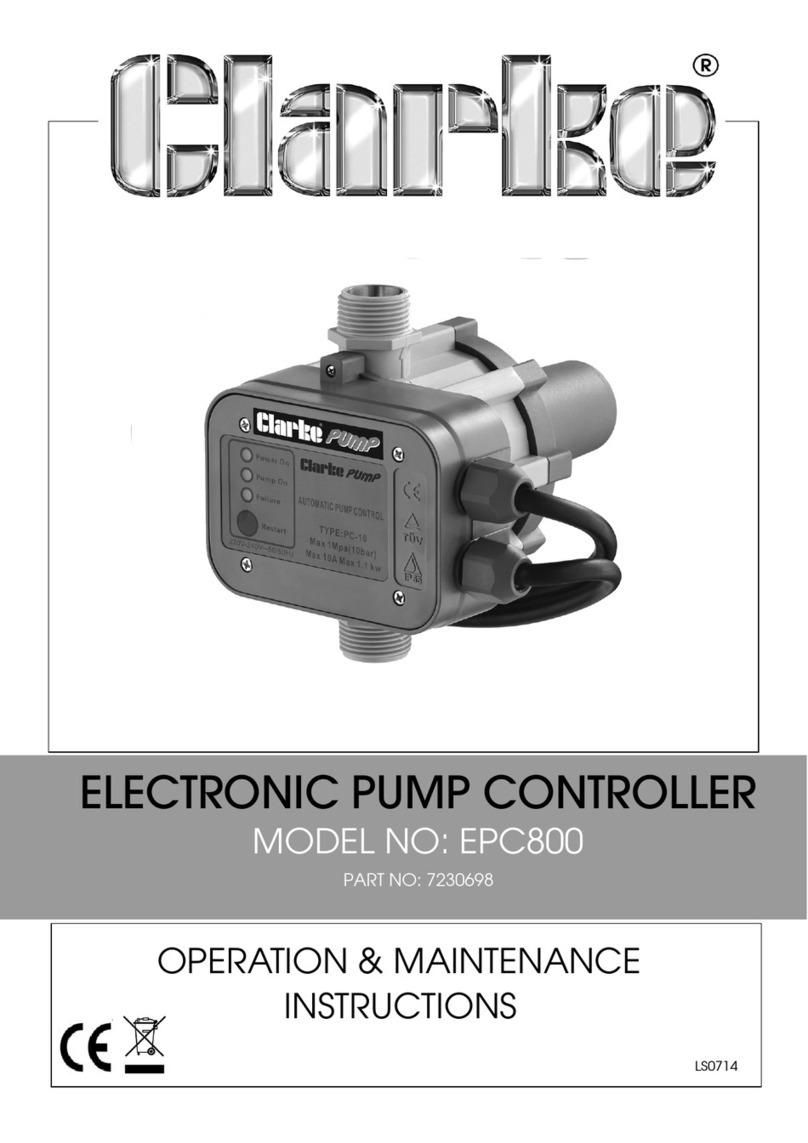
Clarke
Clarke EPC800 Operation & maintenance instructions
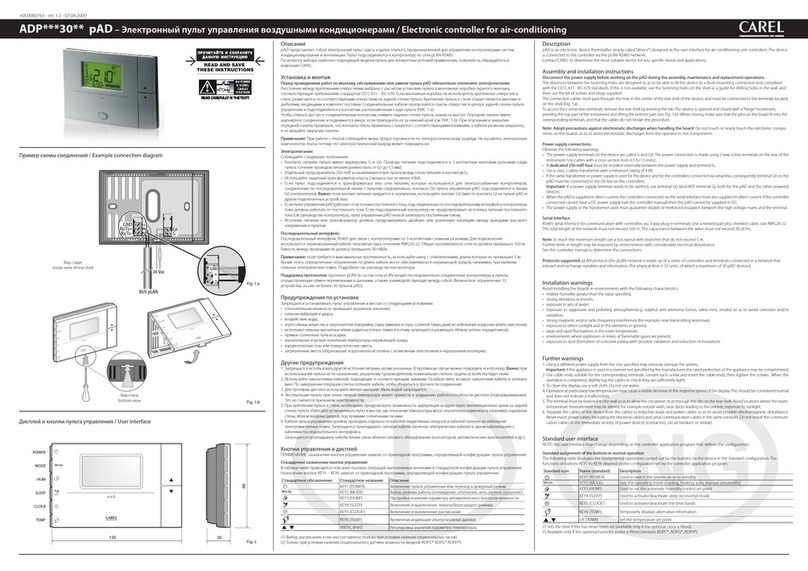
Carel
Carel ADP 30 pAD Series quick start guide
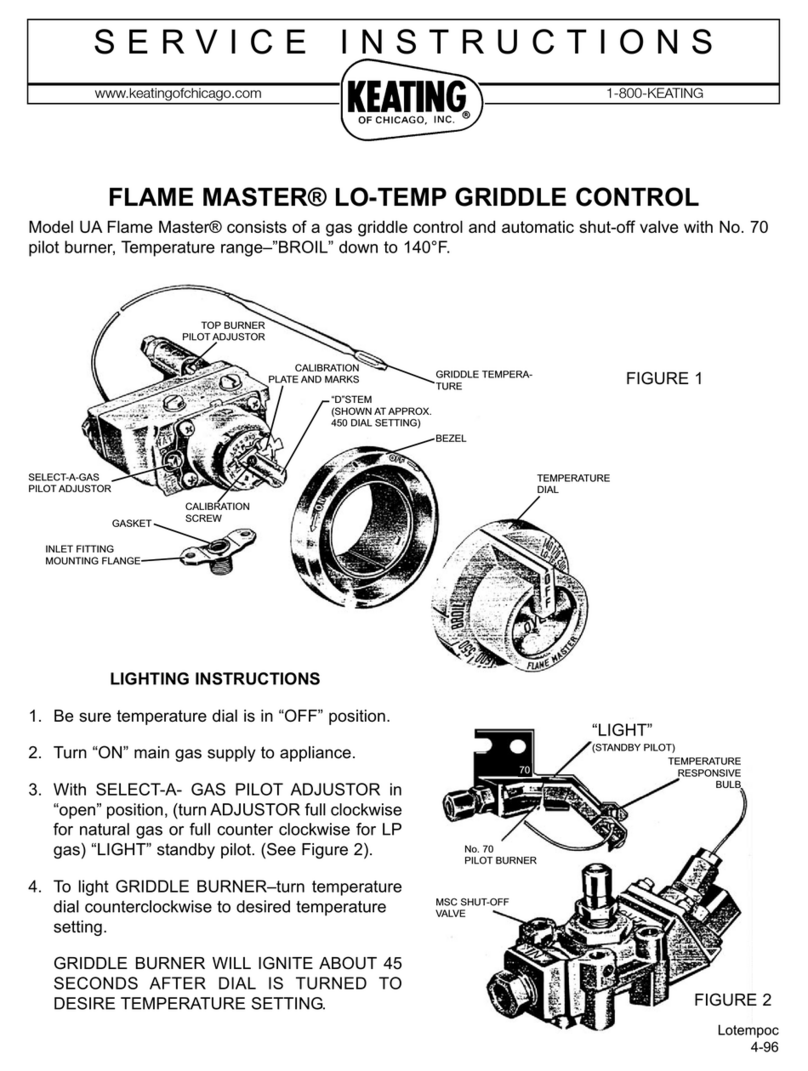
Keating Of Chicago
Keating Of Chicago UA Flame Master Lo-Temp Griddle Service instructions

CKD
CKD ECG Series instruction manual
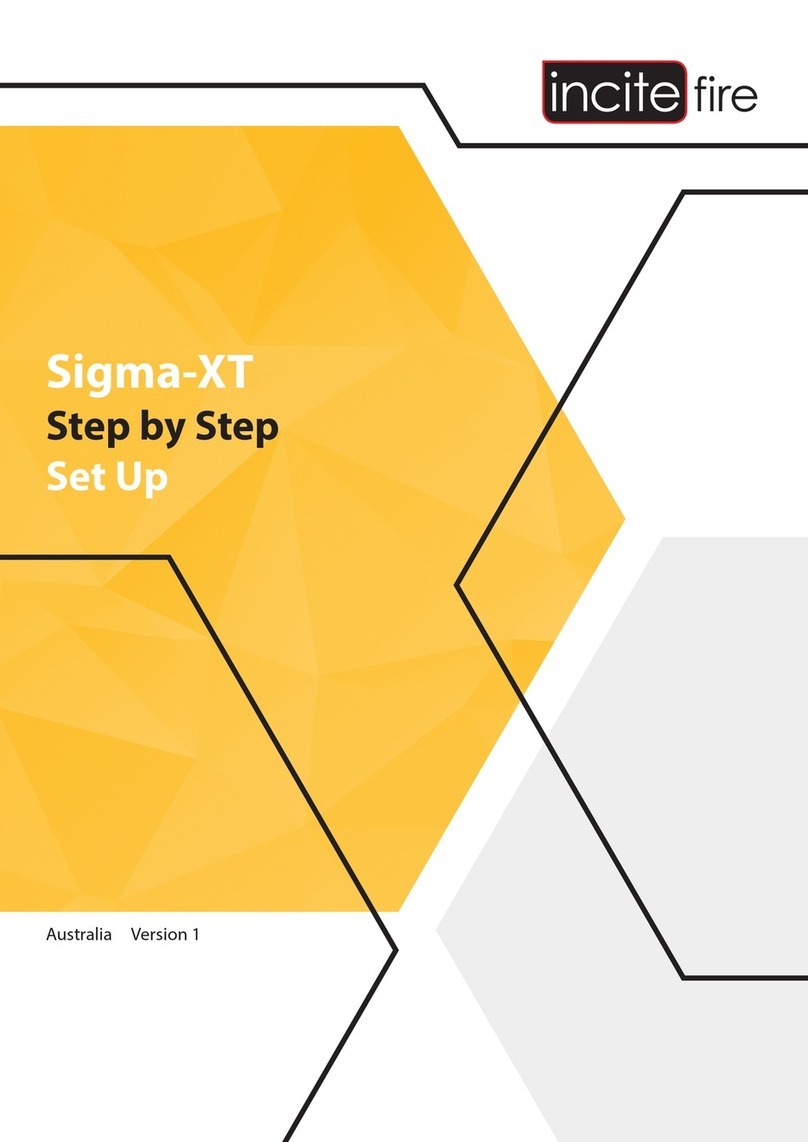
Incite Fire
Incite Fire Sigma-XT Setup
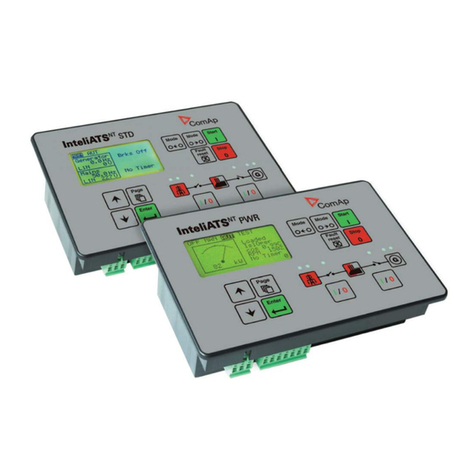
ComAp
ComAp InteliATS NT PWR reference guide
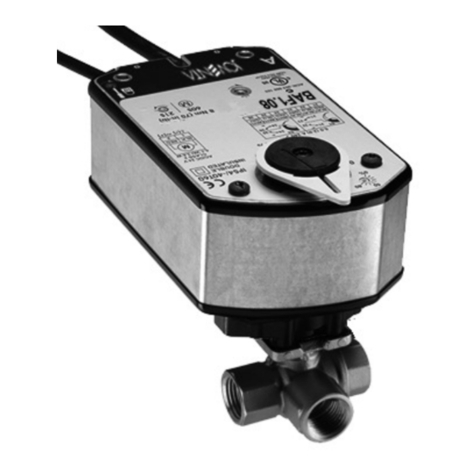
JOVENTA
JOVENTA BMF1.08 installation instructions
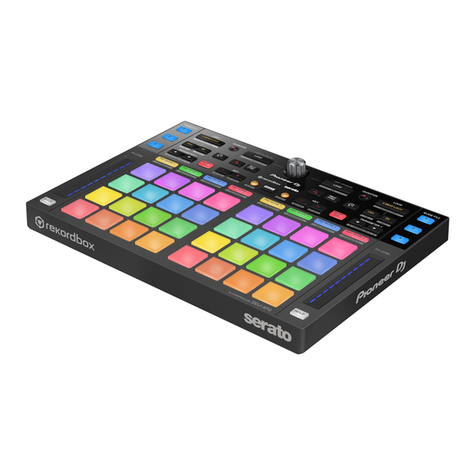
PIONEER DJ
PIONEER DJ DDJ-XP2 operating instructions

Genie CCTV
Genie CCTV KB-1000/JS instruction manual
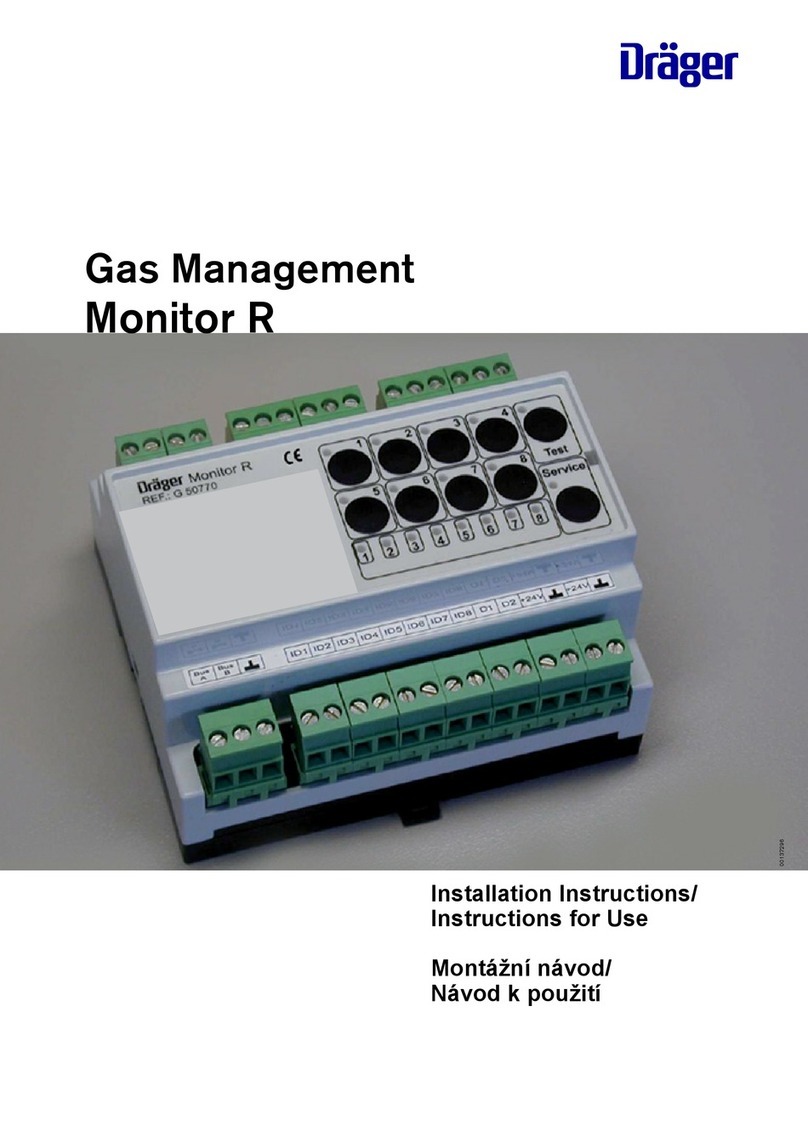
Dräger
Dräger Monitor R Installation instructions & instructions for use