PiezoMotor Microstep Driver 206 User manual

PiezoMotor Microstep Driver 206/236
Technical Manual

ii
Imprint
Revision 02
05.25.2013
Document number 150087-02
© Copyright by PiezoMotor Uppsala AB
Stålgatan 14, SE-754 50 Uppsala, Sweden
All rights reserved, icluding those to the translation. No part of this description may be duplicated,
reproduced, stored in an information system or processed or transferred in any other form without prior
express written permission of PiezoMotor Uppsala AB.

Chapter Contents iii
Overview
This document is a guide to the technical aspects of installing and using the PiezoMotor Microstep Driver 206 and
the PiezoMotor Microstep Driver 236 (hereafter referred to as PMD206 and PMD236). The PMD206 is an advanced
6-axis driver for Piezo LEGS linear and rotary motors from PiezoMotor. The PMD236 is basically six PMD206’s
packaged in a rack, forming a 36-axis driver. The drivers will give the motors resolution down in the sub-nanometer/
sub-microradian range by dividing every full wfm-step into small and precise microsteps.
Detailed information about the different Piezo LEGS motors can be found on our homepage:
www.piezomotor.com
Contents
1 ‒ Important Information
1.1 Symbols Used in this Document.................................................................................................................................1
1.2 Safety Instructions ......................................................................................................................................................2
2 ‒ Delivery
2.1 Packaging and Delivery Contents...............................................................................................................................3
3 ‒ Functional Principle
3.1 Piezo LEGS Linear and Rotary Motors......................................................................................................................5
3.2 Motor Drive Principle.................................................................................................................................................5
3.3 PiezoMotor Microstepping Driver..............................................................................................................................6
3.4 Waveforms and Voltages.............................................................................................................................................6
4 ‒ Quick Start
4.1 Getting Started ............................................................................................................................................................7
4.2 Installation...................................................................................................................................................................8
4.2.1 Cooling
4.2.2 Power Supply
4.2.3 Host Communication
4.2.4 Motor Connection
4.2.5 Sensor Connection
4.2.6 Example of System Conguration
PMD206 PMD236

iv
5 ‒ Detailed Technical Description
6 ‒ Commands
6.1 Introduction...............................................................................................................................................................13
6.2 Power On ..................................................................................................................................................................13
6.3 Host Communication ................................................................................................................................................14
6.4 Basic Settings............................................................................................................................................................15
6.5 Controller Parameter Settings...................................................................................................................................16
6.6 Sensor Board Parameter Settings..............................................................................................................................18
6.7 Run Commands.........................................................................................................................................................20
6.8 Controller Status .......................................................................................................................................................22
6.9 Error Codes ...............................................................................................................................................................24
6.10 Firmware Version....................................................................................................................................................24
7 ‒ Installation and Assembly
7.1 Installation.................................................................................................................................................................25
7.2 Main Dimensions......................................................................................................................................................25
7.2.1 Main Dimensions PMD206
7.2.2 Main Dimensions PMD236
7.3 Motor and Sensor Connectors...................................................................................................................................26
7.3.1 Pinout on the Motor Ports
7.3.2 Pinout on the Sensor Ports
7.4 Communication.........................................................................................................................................................28
7.4.1 Serial Communication
7.4.2 Communication via TCP/IP
7.5 Miscellaneous ...........................................................................................................................................................29
7.5.1 USB Port
7.5.2 Power Supply
8 ‒ Operation
8.1 Driving a Piezo LEGS Motor ...................................................................................................................................31
8.2 Closed Loop..............................................................................................................................................................31
8.3 Open Loop ................................................................................................................................................................32
8.4 Homing .....................................................................................................................................................................32
9 ‒ Settings
9.1 Closed Loop Target Mode Parameters......................................................................................................................33
9.1.1 StepsPerCount Parameter
9.1.2 Target Mode Position Limits A and B
9.1.3 Target Mode Minimum and Maximum Speed
9.1.4 Target Mode Speed Ramp Up
9.1.5 Target Mode Speed Ramp Down
9.1.6 Target Mode Stop Range
9.1.7 Encoder Direction
9.2 Other Settings............................................................................................................................................................35
9.2.1 Parking and Initialization
9.2.2 Encoder Type
9.2.3 External Limits
9.2.4 Position Offset
10 ‒ Maintenance
10.1 General Maintenance Instructions ..........................................................................................................................37
10.2 Troubleshooting ......................................................................................................................................................37
10.3 Firmware Updates...................................................................................................................................................37
11 ‒ Warranty
11.1 Warranty Conditions ...............................................................................................................................................39

Chapter 1 ‒ Important Information 1
1.1 Symbols Used in this Document
Caution!
This pictogram with the wording “Caution!” indicates an imminent danger which can result in slight physical injuries
or material damage.
►This arrow points out the appropriate precautions.
Regulation!
This pictogram with the wording “Regulation!” indicates a statutory regulation, guideline or directive which must be
observed in respective context of the text.
Note!
This pictogram with the wording “Note” provides tips and recommendations for use and handling of the component.
1 ‒ Important Information

2
1.2 Safety Instructions
Note!
The PMD206 / PMD236 driver is a high-end product intended for use with PiezoMotor’s Piezo LEGS product line. In
order to get best performance and reliability it is important that the driver unit is handled according to the instructions
given in this manual and other delivery documents.
Caution!
The piezoceramic elements in a Piezo LEGS motor act as capacitors and can sometimes hold substantial electrical
charge.
► Make sure motors are discharged through suitable discharge resistors.
Caution!
Incorrect installation using improper mounting materials or methods can cause damage to the driver unit.
► Observe the installation instructions.
Caution!
Depending on its use the driver unit can get very hot.
► The unit should be installed in a clean and dry environment with access to proper ventilation. On installation,
ensure that air can ow around the unit without obstruction. The driver is intended for indoor operation.
Caution!
Electrostatic discharges at the driver unit connectors can cause irreparable damage to the electronics.
► Note and follow the ESD protective measures
Caution!
Incorrect connection of motor leads may cause irreparable damage to both motor and driver unit electronics.
► Connect in accordance with the specied pin assignment (see section 7.3 on page 26).

Chapter 2 ‒ Delivery 3
2.1 Packaging and Delivery Contents
The PMD206 driver unit has been cleaned prior to packaging, but does not carry any clean room classications. The
unit is shipped in a cardboard box with foam packaging material.
These items are included in the box at delivery:
1 x PMD206 driver unit
1 x 2 meter power cord with CEE 7/7 plug
1 x CD with PiezoMotor Motion System software and pdf-version of this document
(latest version of software and manual is available on the PiezoMotor homepage)
2 ‒ Delivery

4

Chapter 3 ‒ Functional Principle 5
3.1 Piezo LEGS Linear and Rotary Motors
The PMD206 / PMD236 driver unit is made to control PiezoMotor’s linear and rotary Piezo LEGS motors. The
Piezo LEGS technology is characterized by its outstanding precision and high resolution. The motors are backlash free
because of the friction based direct drive. There is no need for gearboxes or linear screws, and the motor is very strong
compared to its size.
The performance of a Piezo LEGS motor is different from that of a DC or stepper motor in several aspects. A
Piezo LEGS motor is friction based, meaning motion is transferred through contact friction between the drive leg and
the drive rod (Piezo LEGS Linear), or between the drive leg and drive disc (Piezo LEGS Rotary). You cannot rely on
each step being equal to the next. This is especially true if the motor is operated under varying loads/torques.
3.2 Motor Drive Principle
You need to feed 4 electrical drive signals to the motor in order to activate the legs and start moving. The actuation
of the legs will lift and push the drive rod forward, or in case of a rotary motor, lift and spin the drive disc and axle
around. For each waveform signal period the legs will complete one full step (see illustration below). To alter the
speed of the motor the frequency of the electrical signals is changed. The motor speed will depend on the magnitude
of external force/torque. The maximum speed is limited to a few thousand steps per second, which translates to
movements in the range of millimeters per second (linear motion).
1 When all legs are electrically
activated they are elongated
and bending. As we shall see
below, alternate legs move as
pairs. Arrows show the direction
of motion of the tip of each leg.
2 The rst pair of legs
maintains contact with the rod
and moves towards the right.
The second pair retracts and
their tips begin to move left.
3The second pair of legs has
now extended and repositioned
in contact with the rod. Their
tips begin moving right. The
rst pair retracts and their tips
begin to move left.
4 The second pair of legs has
moved right. The rst pair
begins to elongate and move up
towards the rod.
Denition
One waveform-step (wfm-step) is the step taken by the drive legs for each waveform signal period.
Note!
The wfm-step length/angle is not constant. Step length/angle will depend on external force/torque, and
therefore the drive rod/disc will not always travel the same distance for one wfm-step.
Example
Piezo LEGS Linear: When taking a wfm-step the drive rod will move several micrometers.
Piezo LEGS Rotary: When taking a wfm-step the drive disc will rotate. The step angle depends on the
diameter of the drive disc.
If there is an external force/torque present and the force/torque is opposing the direction of motion, the wfm-step
length/angle will be decreased (shorter step). If the force/torque is working in the same direction as the direction of
motion, the wfm-step length/angle will be increased (longer step). The speed of a Piezo LEGS motor is a product of
the actual wfm-step length/angle (long or short) and the frequency of the drive signals. For varying loads/torques,
using constant waveform frequency will not give a constant speed, simply because the wfm-step length is not constant.
3 ‒ Functional Principle

6
To exemplify, the Piezo LEGS Linear 20N motor has a typical step length of ~5 µm when there is no external load
present. Running 2000 wfm-steps per second will generate a speed of ~5 µm • 2000 Hz = ~10 mm/s. When the
motor is loaded with 10 N of force opposing the direction of motion, the wfm-step length is decreased to ~4 µm, and
resulting speed when driving at 2 kHz is of course ~4 µm • 2000 Hz = ~8 mm/s. When the motor is loaded with 10 N
of force in the same direction as the direction of motion, the wfm-step length is increased to ~6 µm. Resulting speed
for 2 kHz drive frequency is ~6 µm • 2000 Hz = ~12 mm/s. To conclude, with an unbalanced load the resulting speed
will be different for forward and reverse motion.
3.3 PiezoMotor Microstepping Driver
The PMD206 / PMD236 is a high resolution microstepping driver made for Piezo LEGS linear and rotary motors.
The driver generates suitable waveforms to control six individual motors. Each waveform signal is constituted of
numerous predened discrete points. These points are voltage targets occurring at specic times along the waveform.
When going from one point to the next, the legs of the motor are bent just a little bit, and the drive rod or drive disc is
moved by so called microsteps. The PMD206 / PMD236 driver has a resolution of 8192 microsteps per 1 wfm-step.
With typical wfm-step length of ~5 µm (at no load), the microstep length at maximum resolution is ~5 µm / 8192 =
~0.6 nm.
Denition
One microstep is a small fraction of a full wfm-step. The theoretical hardware limit is 65536 microsteps
within 1 wfm-step, however with the currently implemented rmware code the actual resolution is
limited to 8192 microsteps/wfm-step.
Note!
The microstep length is not constant. Microstep length will depend on external forces/torques.
Note!
The resolution is currently limited to 8192 microsteps/wfm-step, but the Run Steps command (RS=)
operate according to the microstep theoretical range of 65536 microsteps/wfm-step. Therefore, you
always need to take at least 8 microsteps (i.e. 65536/8192=8) to make an actual movement.
Example
Piezo LEGS Linear: The drive rod will not always travel the same distance for one microstep.
Microsteps are close to 0.6 nm (with a resolution of 8192 microsteps/wfm-step).
Piezo LEGS Rotary: The drive disc will not always rotate the same distance for one microstep. The
angular rotation of the drive axle for one microstep will depend on diameter of the
drive disc.
3.4 Waveforms and Voltages
The driver unit delivers approximately 44 VPP drive signals with optimal waveforms to operate the Piezo LEGS
motors. Each repeating waveform signal period is constituted of numerous predened discrete voltages. The
maximum resolution of the PMD206 / PMD236 is 8192 target points per signal period, giving the Piezo LEGS motor
resolution in the sub-nanometer range (linear motion).
The microstep function means the motor can stop anywhere in the motion, with sub-nanometer resolution, and hold
position. When stopped on a specic microstep, the driver must be powered and the motor can of course not be
disconnected. If you want to power down in a controlled manner, there is a parking command which will give little
positional disruption. Still the position might change by fractions of a wfm-step (depending on external loads/torques)
when going from an unparked to a parked state. When parked, the motor can be disconnected and still hold position.

Chapter 4 ‒ Quick Start 7
4.1 Getting Started
1. Unpack the PMD206 / PMD236 unit and verify that no damage has occurred during transportation. Place unit
so that it gets sufcient cooling.
2. Run SetupMotionSystem.msi from the CD to install PiezoMotor Motion System software and the
FTDI communication drivers. Latest version of the software can always be found online at:
www.piezomotor.com
3. Connect your Piezo LEGS motor(s) to the driver. If you are using a Piezo LEGS Linear Twin motor, it
needs to be connected with two cables in parallel (for example using the Twin Connect Card).
4. If you want to be able to run motor in closed loop, you will need to connect an encoder. The
PMD206 / PMD236 supports quadrature and serial SSi encoders directly connected to the internal sensor
board (via connectors S1-S6 on the front panel). The PMD206 also supports some sensors connected via the
serial interface (COM2), and Ethernet sensors (transferring data via TCP/IP).
5. Connect to the driver unit using RS485 or TCP/IP.
6. Connect the power cord and switch on the driver.
7. Start PiezoMotor Motion System software and scan for driver units. Software will detect and list all
connected driver units.
8. Double click on the driver unit in the list to start wizard. The Wizard will help you congure the
basic settings.
9. When the wizard is completed, the motor can be tested in open loop and/or in closed loop operation
(closed loop only if an encoder is connected). The software can also be used to send commands
directly to the driver in order to verify function and congure parameter settings. The software
can also run command sequences with one or several drivers to perform simple automation tasks.
4 ‒ Quick Start

8
4.2 Installation
4.2.1 Cooling
The driver unit is cooled by convection with internal fans, and therefore needs free space for this purpose. If the driver
gets overheated it will automatically stop running the motor.
4.2.2 Power Supply
The driver unit is powered with 90-264 V AC, 50/60 Hz. The PMD206 is fused at 5 A, and the PMD236 at 10 A.
4.2.3 Host Communication
The driver unit connects to a host (e.g. a PC) via serial RS485 or Ethernet. See chapter 7 ‒ Installation and Assembly,
on page 25.
4.2.4 Motor Connection
The connection to the motor is via a straight ve pole cable with D-sub connectors on driver side. All Piezo LEGS
twin motors need a Twin Connect Card in order to split the signal to the two motor connectors. Recommended motor
cable is shielded with multistrand wires 0.34 mm2(22 AWG). For short distances a smaller cable area is possible. The
shield should normally be connected to the connector housing.
Caution!
Failure to connect all motor phases, or switching phases, can permanently damage the motor. Functional wiring can be
veried by measuring motor phase capacitances through the motor cable from the driver side before attempting to run
motor.
4.2.5 Sensor Connection
Encoder for position feedback may be connected to the dedicated sensor port, or sensor data can be transferred to the
unit via serial interface (RS422) or via Ethernet (TCP/IP). Read more about supported encoder types and connection
options in chapter 7 ‒ Installation and Assembly, on page 25.
It is recommended to study the sensor manufacturer’s installation guidelines.
4.2.6 Example of System Conguration
The following schematic illustrations show different ways to establish host and sensor communication. The motor is of
course always connected to one of the motor ports on the driver front panel (and is not included in these illustrations).
The illustrations show:
1. Host connection via RS485, and sensor (quadrature or SSi) connected directly to the internal sensor board.
2. Host connection via RS485, and external sensor via TCP/IP.
3. Host connection via RS485, and external sensor via RS422.
4. Host connection via TCP/IP, and sensor (quadrature or SSi) connected directly to the internal sensor board.
5. Host connection via TCP/IP, and external sensor via TCP/IP.
6. Host connection via TCP/IP, and external sensor via RS422.

Chapter 4 ‒ Quick Start 9
Host (PC)
PMD206
RS485 Switch
TCP/IP
TCP/IP
External
Sensor
Host (PC)
RS485
RS422
External Sensor
PMD206
Host (PC)
RS485
PMD206
Direct
(Quadrature or SSi)
Sensor
2
1
3

10
RS422
External Sensor
PMD206
Switch
Host (PC)
PMD206
TCP/IP TCP/IP
Direct
(Quadrature or SSi)
Sensor
Switch
Host (PC)
TCP/IP TCP/IP
Switch
External Sensor
Host (PC)
PMD206
TCP/IP
TCP/IP
TCP/IP
4
5
6

Chapter 5 ‒ Detailed Technical Description 11
5 ‒ Detailed Technical Description
Editorial note - this chapter will be included in a later revision of this document.

12

Chapter 6 ‒ Commands 13
6 ‒ Commands
6.1 Introduction
Each command to the driver starts with the letters PM followed by one digit <ID>, and one digit <axis>. All
commands shall end with ‘Carriage Return’ character (CR), i.e. ASCII character 13. A command time-out (300 ms)
silently rejects a command and sets an internal error code. Unknown header will be silently rejected. A matching
header, but with wrong command or syntax, will return an error code. All characters are given in ASCII format. All
values must always be given in hexadecimal form, (lower case 0...f). For example, if the returned value is 10001, the
value is 0x10001=65537. The data is not signed, e.g. fffffff = -1.
The PMD206 is by default identied by <ID> = 1. The user may assign a different identier to the unit if necessary.
The driver card has six axes, each addressed separately with a second digit <axis>, 1...6. Sending one command
simultaneously to all axis on the PMD206 is possible by addressing axis 0 (broadcast).
The PMD236 rack has 6 separate driver modules, each with 6 individual axes. Each driver module has a unique
identier, or <ID>, which is related to the slot number on the common backplane. The identier contains one
digit 1...6. A second digit, <axis>, species the axis on the separate module (digits 1...6). Sending one command
simultaneous to all axis on the same driver module can be done by addressing axis 0 (broadcast mode). There is no
way to control all six driver modules at once. Each driver module needs to be controlled separately.
Examples of header strings
PM51 where 5 is <ID>, i.e. driver module with identier 5,
and 1 is <axis>, i.e. axis number 1 on the addressed driver module.
PM20 where 2 is <ID>, i.e. driver module with identier 2,
and 0 is <axis>, i.e. broadcast command to all broadcast enabled axis on the addressed driver module.
Examples of valid commands
PM12TP=f2 addressing axis 2 on module 1, and setting the target position to 242 (i.e. 0xf2).
PM60TP=f2 addressing all broadcast enabled axes (0) on module 6, and setting the target position to 242 (i.e. 0xf2)
Note!
In the following text all examples are given only for <ID> = 1. The header needs to be changed for addressing driver
modules with other identier.
Note!
All set commands sent to the driver will be echoed back with an identical string (if accepted).
6.2 Power On
At power on, controller parameter settings (CP2...b), encoder type setting (SB1), and latest TCP/IP settings are
restored to values stored in non volatile memory (Flash/EEPROM). Controller mode (CM) is set to target mode
enabled and motors are parked. If the controller parameters or the encoder type setting are changed during operation,
be sure to save to Flash/EEPROM using the CC command.

14
6.3 Host Communication
Communication with the driver is via serial line (4-wire RS485), or via Ethernet (TCP/IP socket). Several PMD206
units may be connected on the same RS485 line, provided that they have different identier <ID> and that responses
are allowed to nish before addressing the next module. These are the settings for serial communication:
RS485 Communication Settings
Baud Rate Start Bit Data Bits Parity Stop Bits Handshaking Duplex Text
115200 1 8 none 1 none Full duplex ASCII
By default the driver is set to dynamic IP allocation (DHCP), so when connecting via Ethernet you will need to look
for the driver module(s) in your local area network. You can assign a static IP address to the driver module(s) using the
commands in the table below. Setting IP/GW/IM will immediately save the new settings to Flash/EEPROM.
TCP/IP Settings
Cmd Description Examples Notes
IP Settings
IP= Asigns a static IP
address for the
specic driver
module, and the
port number for host
communication.
Static IP PM10IP=c0,a8,0a,01,2620
example: Corresponding to IP address
192.68.10.1 and port 9760
Dynamic IP PM10IP=00,00,00,00,0000
example:
If the port number is set to
0000, the default socket port
number 9760 will be assigned,
i.e. 0x2620.
Static IP address is not valid
until a gateway and a mask has
been assigned (using GW and IM
commands).
If you use dynamic IP, the DHCP
server will provide the IP mask
and gateway.
Use XV? command for current IP
mode.
IP? This command returns
the currently used
IP address and port
number of the driver
module (hex values).
Command: PM10IP?
Response: For example
PM10IP?:c0,a8,0a,01,2620
Gateway Settings
GW= Sets the gateway
address to be used for
static IP address.
Example: PM10GW=c0,a8,0a,0a
Corresponding to gateway address
192.68.10.10
Should not be necessary to set
when host is on the same subnet.
GW? This command returns
the currently used
gateway address (hex
values).
Command: PM10GW?
Response: For example
PM10GW?:c0,a8,0a,0a
Will return the gateway for static
IP, not for DHCP.
Mask Settings
IM= Sets the mask address
to be used for static IP
address.
Example: PM10IM=ff,ff,ff,00
Corresponding to IP mask address
255.255.255.0
IM? This command returns
the currently used
mask address (hex
values).
Command: PM10IM?
Response: For example
PM10IM?:ff,ff,ff,00
Will return the mask for static IP,
not for DHCP.

Chapter 6 ‒ Commands 15
Basic Settings
Cmd Description Examples Notes
Controller Mode
CM= Target mode enable Example: PM10CM=0 Target mode
disabled
PM10CM=1 Target mode
enabled
When target mode is disabled
(0) you will not be able to run
closed loop run commands
(TP and TR)
CM? Read currently used
controller mode.
Command: PM10CM?
Response: For example PM10CM?:01
when target mode is enabled
Response will be 2when
running homing command.
Broadcast Enable
CE= Each axis on the unit
can be enabled or
disabled for broadcast
run commands (TP, TR
and RS).
Example: PM10CE=1,1,1,1,1,1 0 for broadcast disabled
1 for broadcast enabled
The enable/disable function
only applies for run commands
(TP, TR and RS)
CE? Reads the broadcast
enable settings.
Command: PM10CE?
Response: For example, when all axis enabled
PM10CE?:01,01,01,01,01,01
Sensor Interface
SI= Denes the sensor
interface.
Options:
• Internal sensor
board
• Serial sensor
(RS422)
• Ethernet sensor
(TCP/IP)
Internal sensor PM10SI=00,00,00,00,0001
board:
Serial sensor: PM10SI=00,00,00,00,0000
Ethernet sensor PM10SI=c0,a8,0a,02,2711
example: Corresponding to IP address
192.68.10.2 and port 10001
SI? Report sensor interface
setting.
Command: PM10SI?
Response: For example
PM10SI?:c0,a8,0a,02,2711
Slot Identier
ID= A set command to
change the <ID>
identier.
Example: PM10ID=7
to change the identier from 1 to 7.
Example: PM70ID=1
to change the identier from 7 to 1.
Can be 0...f (default is 1).
The PMD236 has xed
identiers 1...6 which are
related to the physical
backplane. These cannot be
changed.
6.4 Basic Settings
The basic settings denes how the driver will interact in the system. For example, you need to enable closed loop
operation, and assign the sensor interface (e.g. an encoder connected to the internal sensor board, or data collection
from an external sensor via RS422 or Ethernet).

16
Controller Parameter Settings
Cmd Description Examples Notes
CP= Sets various parameters
in the driver. You can set
parameters for a single
axis, or on all broadcast
enabled axis by using
broadcast command.
Send to axis 1: PM11CP=<par>,<value>
...
Send to axis 6: PM16CP=<par>,<value>
Send broadcast: PM10CP=<par>,<value>
<par> is the parameter identier
<value> is the parameter value
CP? Reads various parameters
in the driver.
Send to axis 1: PM11CP?<par>
...
Send to axis 6: PM16CP?<par>
Send broadcast: PM10CP?<par>
Response: For example
PM11CP?<par>:<value>
<par> is the parameter identier
Broadcast only works up to
parameter 1c.
6.5 Controller Parameter Settings
The PMD206 / PMD236 must be congured correctly in order to get best performance out of the Piezo LEGS motor
in your application. For instance, to run in closed loop you need to have ramping parameters set according to the
actual external loads in your application. Most important for closed loop operation is to have the StepsPerCount
properly set up. The Piezo LEGS motor will perform very differently depending on external load/torque because the
step length/angle is not constant. With target mode parameters properly congured, you will get the desired function in
closed loop operation. See table below for explanation of each setting. More detailed information given in chapter 9.1.
<par> <value> Notes
0Cycle counter
There is a continuous counter which keeps track of microsteps and wfm-steps. With
the set command the user can set the wfm-step counter. With the read command the
user can read out the total microstep counter (1 wfm-step = 65536 µsteps).
Read (U32)
Write (U16)
1Parking and initialization
<value> for set: <value> for read:
0 to unpark 00 - unparked (ready to run)
1 to park 01 - parked (powered down)
2 to initiate from Flash/EEPROM * 11 - parking/unparking is ongoing
3 to initiate default values **
* CP-parameters 2, 3, 4, 5, 6, 7, 8, 9, a, b, SB-parameter 1.
** CP-parameters 3, 4, 5, 6, 7, 8, 9, a, b.
Any run command will also
unpark, but stop command
will not park. When issuing
the park command (1) it
will take around 300 ms to
complete.
Save to Flash/EEPROM with
CC=4 command.
2External limits
0 for limit switches disabled
1 for limit switches enabled
See chapter 7.3.2 for information on which pins to connect!
(U16)
3Position limit A - target mode will stop when position <A Default value: ffffd8f0 (I32)
(decimal -10000)
4Position limit B - target mode will stop when postition >B Default value: 2710 (I32)
(decimal +10000)
5Stop range - how many counts (±) from target position should the regulation stop Default value: 0 (U16)
6Encoder direction - to dene the expected encoder counting direction for target loop
0 for positive counting when running in forward direction
1 for negative counting when running in forward direction
Default value: 0 (U16)
7Minimum speed in target mode - wfm-steps per second Default value: 2 (U16)
8Maximum speed in target mode - wfm-steps per second Default value: 32 (U16)
9Speed ramp up in target mode - wfm-steps per second per millisecond Default value: 30 (U16)
This manual suits for next models
3
Table of contents
Popular Controllers manuals by other brands
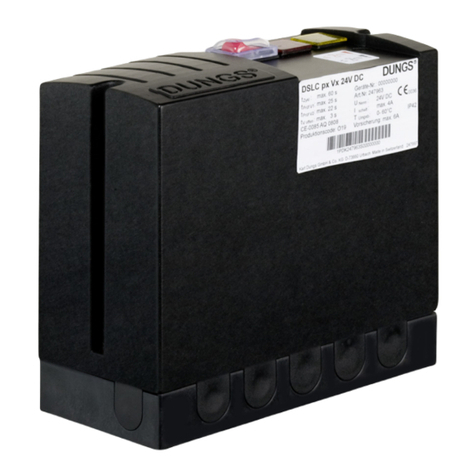
Dungs
Dungs DSLC px Vx Operation and assembly instructions
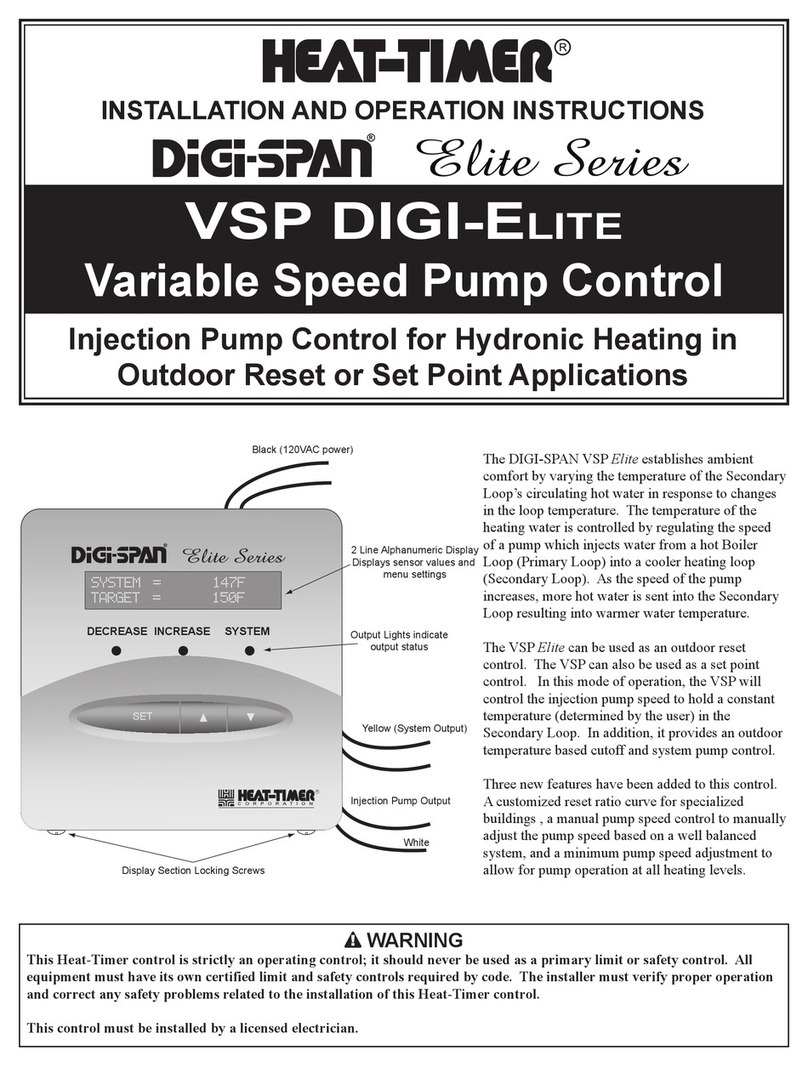
heat-timer
heat-timer DIGI-SPAN VSP Elite Installation and operation instructions

Mitsubishi Electric
Mitsubishi Electric TC-24A Setting manual
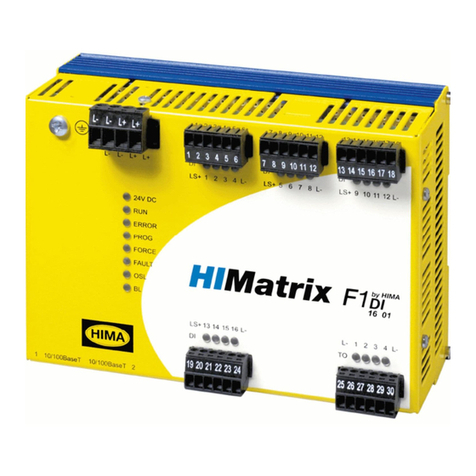
HIMA
HIMA HIMatrix F1 DI 16 01 manual
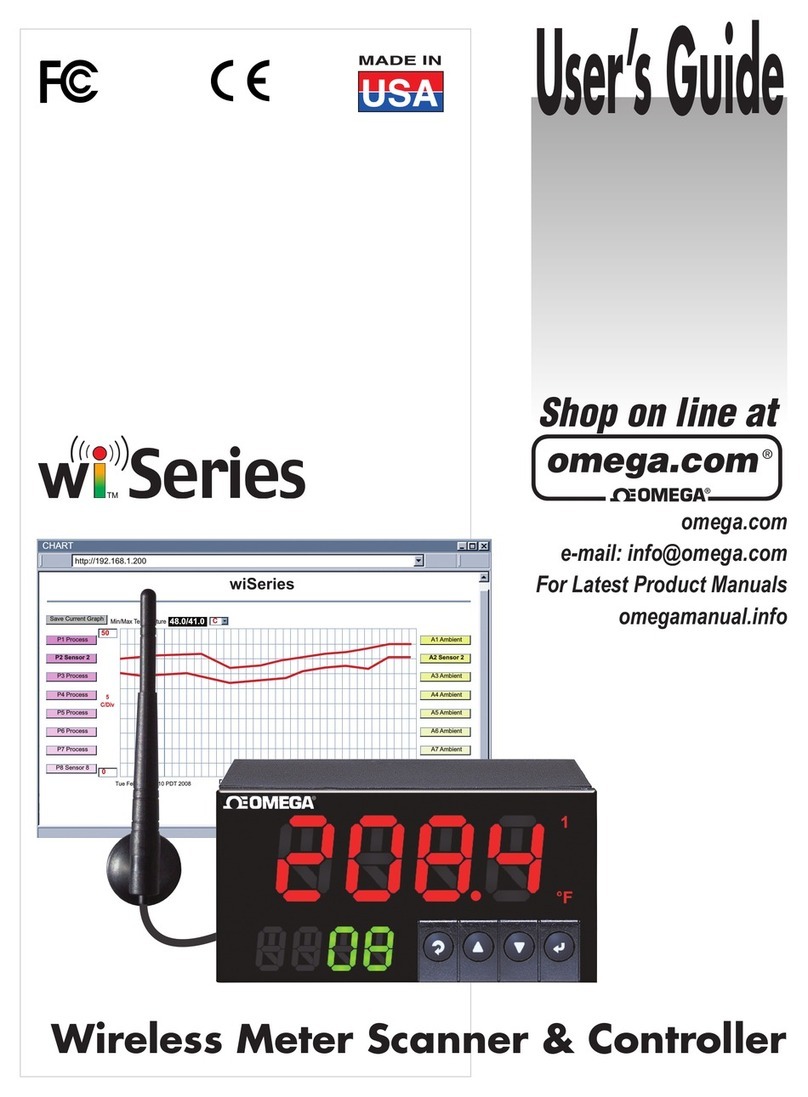
Omega Engineering
Omega Engineering Wireless Meter Scanner & Controller wi... user guide
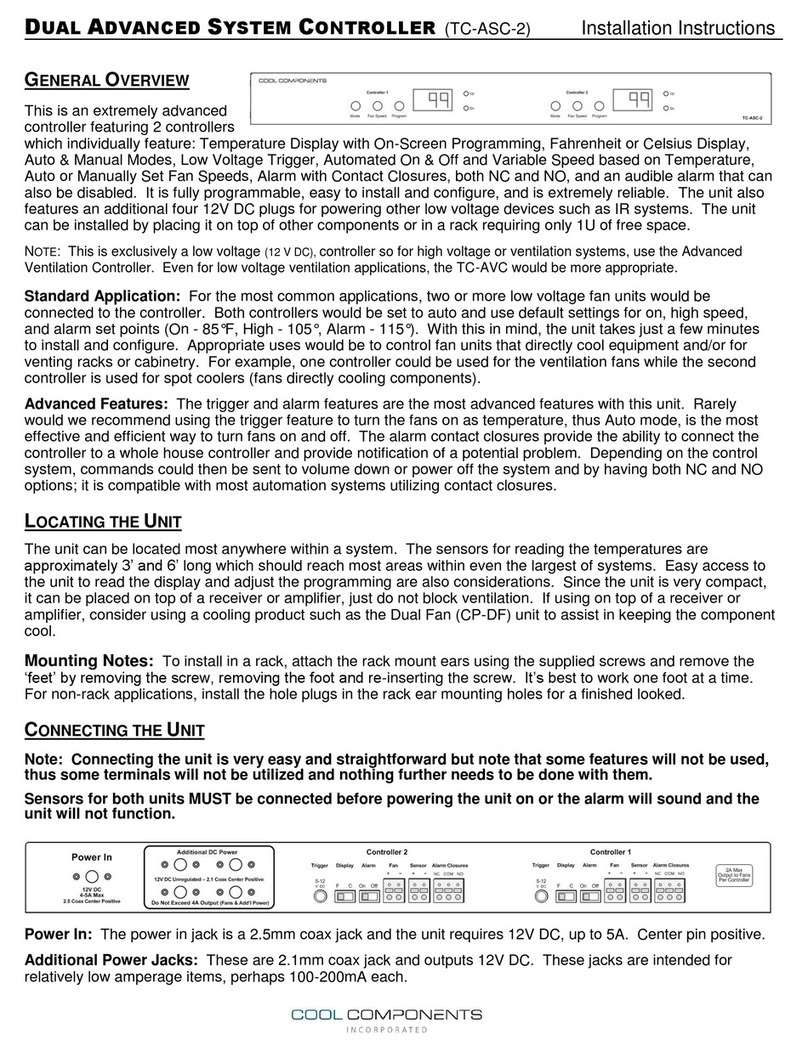
Cool Components
Cool Components TC-ASC-2 installation instructions