Power Tec Ferrite F Series User manual

© copyright 2012 by POWERTEC Industrial Motors, Inc
Brushless Motor Manual
Ferrite “F” Series Motors
Installation and Operation Manual
Powertec Industrial Motors [email protected]
13509 South Point Blvd
Suite 190
Charlotte, NC 28273
www.powertecmotors.com


POW ERTEC “F” Series Motor Manual Page 1
© copy right 2012 by P O WE R TEC Industrial Motors, Inc.
WARNING!!! IF YOU DO NOT INSTALL AND SERVICE THIS EQUIPMENT CORRECTLY,
YOU OR SOMEONE ELSE COULD GET HURT.
APPLICATION CHECKLIST
1. UPON RECEIPT
Our Quality Control Department inspects the motors
and packing before shipment. When you receive it,
inspect your order. Look for any mechanical
damage that may have occurred during shipment. Report any
damage you find to the freight carrier FIRST. Then call
POWERTEC for help in assessing the damage.
2. STORAGE
You should store a motor in its original packaging. Keep it in a
clean, dry location, protected from extremes in temperature and
humidity. Rotate the shaft of a stored motor monthly. The grease
may settle in the bearings and harden over time. Do not remove
the cosmoline rust prevention coating from the shaft extensions
until installation.
3. HANDLING
Use care in handling the motor. Avoid dropping it. Prevent
sudden impacts, especially on the shaft. The lifting lugs are
designed to lift the weight of the motor ONLY. DO NOT use the
lifting lugs of the motor as the sole means to lift other devices, such
as gearboxes, attached to the motor.
4. ENVIRONMENT
The motor ratings are for an altitude of less than 3300 feet (1000
meters). You must derate the motor for higher altitudes.
1.20
1.10
1.00
0.90
0.80
0.70
0.60
0.50
0.40
0.30
0.20
0.10
0.00 02 4 6 8 10 12 14 16 18 20 22 24
DERATING FACTOR
ALTITUDE (X 1000) in feet above sea level
Motors are rated in accordance with NEMA Standard MG1-14.04.
For altitudes below sea level, use standard ratings.
For altitudes above 24,000 feet, consult the factory.
At a specified altitude: Multiply the motor HP by the de-rating factor.
ALTITUDE DERATING CHART
Install the motor in a clean, dry, well-ventilated area away from
heat sources. Air temperature should not exceed 40 °C (104°
Fahrenheit). For higher ambient temperatures, you must derate
the motor. See the graph below.
1.20
1.10
1.00
0.90
0.80
0.70
0.60
0.50
0.40
0.30
0.20
0.10
0.00 20 25 30 35 40 45 50 55 60 65 70 75 80
DERATING FACTOR
TEMPERATURE °C
Motors are rated in accordance with NEMA standard MG1-12.43.
For ambient temperatures below 40°C, use the 40°C rating.
For ambient temperatures below 0°C, consult the factory.
At a given ambient temperature: Multiply the motor HP by the derating factor.
AMBIENT TEMPERATURE DERATING CHART
De-rating is cumulative.
First de-rate for altitude; then de-rate for temperature.
5. GENERAL MECHANICAL INSPECTION
Before you install the motor, verify that the motor shaft is free to
turn and all mechanical parts are in their proper position. Turn the
motor shaft by hand to check for damage to the rotor. Remove the
Cosmoline coating on the shafts with a suitable solvent, before
installation.
NOTE: If you have power leads shorted together in the
junction box, the motor shaft will not turn.
6. MOUNTING
You can mount the motor in any shaft position as long as you
keep radial and thrust loads within limits. Install foot-mounted
motors on a rigid foundation. You must use shims if the motor
mounting base is uneven. Do not cause unnecessary stress on
feet, frame and bearings by using poor mounting practices.
After installation, make sure that all bolts that hold the motor in
place are tight. See Mounting Bolt Torques on page 14.

Page 2POW E RTEC “F” Series Motor Manual
© copy right 2012 by P O WE R TEC Industrial Motors, Inc
7. ALIGNMENT
If the motor is directly coupled to the load, alignment is very
important. The type of coupling device determines alignment
tolerances. Poor alignment allows vibration, resulting in damage
to the coupling, bearings, rotor, or accessory devices.
8. BELTED APPLICATIONS
It is important that you use the correct sheave size and type. You
must select the proper belts. See the Maximum Shaft Radial
Loading Table on page 14. When you size the sheaves wrong
or tension the belts improperly, premature bearing or shaft failure
may occur. Mount the sheave as close as you can to the motor
housing. If you need help on sheave sizing, call POWERTEC.
WHEN REMOVING PULLEYS FROM THE MOTOR SHAFT,
USE A PROPER PULLER. DO NOT PRY PULLEYS OFF BY
LEVERAGE AGAINST THE FRAME. YOU MAY DAMAGE THE
BEARINGS OR THE RETAINER PLATES BY PLACING STRESS
ON THE MOTOR SHAFT RELATIVE TO THE FRAME.
9. OPERATION
After you complete the mounting and alignment steps, you may
make electrical connections. You must follow the connection
diagrams exactly or the motor will not operate.
If turning the wrong way will damage the equipment, verify motor
direction before connecting the load. Monitor motor current during
the first operation of the motor. Compare it to the motor nameplate
value.
Check the motor cooling right after the start-up. Check it at
fifteen-minute intervals until the motor gets to normal temperature
(about four hours at full load).
10. MAINTENANCE
Make the first inspection within a few hours after placing the motor
in service, to catch problems caused by the installation. Check the
motor at least once per month after start-up.
Preventive maintenance means checking the motor often. Make
frequent checks for excess vibration, loose mounting bolts and
belts, odd noises (a steady hum is normal), and high heat output.
FRAME OPERATING TEMPERATURES MAY BE
HIGH ENOUGH TO CAUSE BURNS! KEEP
ALL COMBUSTIBLE MATERIALS AWAY
FROM THE MOTOR!
!
SUMMARY OF WARRANTY
Brushless DC motors built by POWERTEC Industrial
Motors, Inc.are warranted against defects in materials and
workmanship for a period of two years from the date of shipment
from the factory. If a motor fails for any of these reasons during
this period of time, we will repair the motor or, at our option,
replace the motor. We reserve the right to determine who will
make repairs, and where the repairs will be made. Claims for
repairs under warranty must be submitted within 30 calendar
days from the first indication of the defect. Unauthorized repairs
are not covered by the warranty.
WARRANTY PROCEDURE
1. When a problem with the motor is confirmed, write down the serial
number, model number, and job number of the motor. This information is
listed on the nameplate.
2. Call your distributor, or our Service Department. at (803) 328-1888
or FAX the information to (803) 328-1870.
3. Our service personnel will attempt to resolve the problem over the
phone. They may ask for information on the machine, environment, and
operation.
4. If the problem cannot be resolved over the phone, we will
determine the best course of action to resolve the problem. This may
consist of sending parts, or returning the motor for repairs.
5. If parts are to be sent, a purchase order will be required. A
Merchandise Return Authorization (MRA) number will be issued for the
parts. If the service is covered by warranty, credit for the parts will be
issued upon inspection of the old parts at the factory.
6. Before the motor is returned to the factory for repair, an MRA
number must be issued by the service department.
7. The MRA number must be displayed on the packaging of the
motor and on all paperwork. The paperwork must include a description of
the problem and return shipping instructions. Motors returned without an
MRA will not be acknowledged, and we are not responsible for them.
8. On repairs covered by warranty, there will be no charges for
materials and labor at the factory. The repaired or replacement motor will
be sent freight collect to the user.
9. Repairs and replacements will be made in a timely manner. If the
user requires expedited service, there will be a charge for the expedited
service.
The warranty does not cover failures due to misapplication,
improper installation, accidental or intentional abuse, incorrect electrical
connections, and damages due to transportation or handling. The warranty
does not apply if any unauthorized alteration has been done to the motor.
POWERTEC is not responsible for removal or re-installation
costs, shipping charges, nor consequential costs or losses. There is no
other warranty, expressed or implied, including fitness for the purpose
intended. The maximum liability of POWERTEC shall be limited to
the purchase price of the motor.

POW E RTEC “F” Series Motor Manual Page 3
© copy right 2012 by P O WE R TEC Industrial Motors, Inc.
Frame NEMA Stack
Diameter Frame Length
42 A42 A
B42 B
C42 C
14 143 3
145 5
L145 7
18 182 2
184 4
21 213 3
215 5
218 8
219 9
25 254 4
256 6
259 9
2512 C
28 287 7
288 8
2810 A
2812 C
32 328 8
3211 B
3213 D
50 502 2
504 4
506 6
508 8
F 2 5 4 E 1 J 0 N 0 0 1 0 0 0
F = Ferrite
Motor Type
25 = Nema 250
Frame Diameter
4 = 254
Stack Length
Assigned by
Factory
Winding Letter
1 = 1D
2 = 2D
3 = 1Y
4 = 2Y
Winding
Connection
J = DPBV
Enclosure
0 = NEMAFoot Mount
Face and Shaft
N = No Brake
B = 90-100VDC
Brake
1 = Terminal Box F1
2 = Terminal Box F2
3 = MS Feedback F1
4 = MS Feesback F2
7 = Terminal Box Top
8 = MS Feedback Top
Terminations
0 = Hall Sensors
2 or 5 = Resolver
Primary Feedback
0 =Standard
Bearings
0 = None
A= 600 PPR
B = 1024 PPR
Secondary
Feedback
00 = All standard
Factory Assigned
Quick Reference - - Model Numbering System - - Ferrite Motors
Enclosures
A TENV (IP44)
B TENV (IP56)
C TEFC
D TEAO
E TEPV
F DPFG
G DPSV
H DPBV (w/o filter)
J DPBV (w/ filter)
K SPFG
L TENV (washdown)
M TEXP (MSHA)
W TEWC
X TEXP (UL)
Z SPECIAL
Face and Shaft
0 StdBracket andShaft w/feet
1 NEMA "C" face w/ feet
2 NEMA "D" flange w/ feet
3 NEMA "P" base flange
4 IEC (metric) square flange w/ feet
5 IEC (metric) roundflangew/ feet
6 NEMA "C" face w/o feet
7 NEMA "D" flange w/o feet
8 IEC (metric) roundflangew/ofeet
9 Special
A IEC (metric) squareflangew/o feet
Drive End Bearing
0 StdDbl ShieldedBall
1 MaxCapacityBall
2 Roller Bearing
9 Special
PrimaryFeedback
0 Hall Switch/Thermal Switch
1 Tachsyn
2 Small Bore Resolver (std) / NTC's
3 Optical Encoder
5 Large Bore Resolver (dbl shaft) / NTC's
6 No feedback
7 Resolver (special) /Thermal Switches
9 Special
SecondaryFeedback
0 None
A 600PPR Optical Encoder
B 1024PPR Optical Encoder
M Encoder Kit w/oencoder
N Resolver, secondary
L Special Encoder
9 Special Feedback

Page 4POW E RTEC “F” Series Motor Manual
© copy right 2012 by P O WE R TEC Industrial Motors, Inc
1. Key
2. Rotor Assembly
3. Bearing Retainer (End Cap)
4. Bearing
5. Cover Gasket
6. Cover
7. Hex Head Screw
8. Grease Fitting
9. -----
10. Flat Washer
11. Hex Head Screw
12. Grease Fitting
13. Socket Head Screw
14. Feedback End Bracket
15. Feedback Stator Assembly (Resolver Shown)
16. Set Screw
17. Feedback Rotor Assembly (Resolver Shown)
18. Hex Washer Head Tapping Screw
19. Stamped Rear Cover
20. Hex Head Tapping Screw
21. Lifting Lug
22. Drive End Bracket
23. Wave Washer
24. Air Baffle
25. Frame/Wound Stator Assembly
26. Hex Washer Head Screw
27. Base (Foot mount)
28. Terminal Box Gasket
29. Terminal Box
30. Hex Washer Head Screw
31. Cable Termination Strip
32. Hex Washer Head Screw
33. Terminal Strip
34. Terminal Box Cover Gasket
35. Terminal Box Cover
36. Hex Head Tapping Screw

POW E RTEC “F” Series Motor Manual Page 5
© copy right 2012 by P O WE R TEC Industrial Motors, Inc.
ELECTRICAL CONNECTIONS
All connections for the motor are in the main terminal box, except
on 320 frame and 500 frames. On these frames, the feedback
connections are in a separate conduit box.
POWER LEADS
The motor ships from the factory already connected for the
speed, voltage, and power listed on the nameplate. The correct
connection of the motor is shown on the nameplate as
"CONNECTION _ D _ Y". There will be a number “1” or “2”
in front of one of these symbols.
T1 T1
T4
T7
T10
T12
T11
T9
T6
T3
T8 T5T2 T2
T3
1-YCONNECTION 1- CONNECTION
T12
T9
T6
T3
T1
T4
T7
T10
T11 T8 T5 T2
2-YCONNECTION 2- CONNECTION
T1
T4
T6
T3
T5T2
T7
T10
T12 T11
T9 T8
T1
T2
T3
T1
T2
T3
T1
T2
T3
T12
T9
T6
T3
T1
T4
T7
T10
T11 T8
T5
T2
Possible motor connections.
Whatever the motor connections, you must connect the T1 motor
lead to the T1 or U terminal on the motor control. You must
connect the motor T2 to the T2 or V terminal on the motor control.
You must connect the motor T3 to the T3 or W terminal on the
motor control. Wire size must be based on the RMS current on
the nameplate of the motor. The motor may draw up to 150% of
this value for periods of up to one minute.
In addition to the wiring of T1, T2, and T3, you must install a
ground wire, which may be one size smaller than the power
leads. It must run from a ground bolt in the motor's junction box to
a ground bolt on the motor control. This ground wire is in addition
to required grounding of the motor to its frame.
Electrical connections to the motor must be tight and well insulated
from each other and from the frame.
NOTE: Drives with IGBT output devices generate higher
voltages at the motor terminals than are normally seen with
bipolar transistor types. Additional care must be taken in taping
and insulating of motor leads in the motor junction box.
MOTOR PROTECTION
POWERTEC Series motors come in two types:
Resolver type motors are equipped with an integral resolver
mounted in the rear of the motor (non-drive end), and with two
thermal switches in the windings. See page 3.
Encoder type motors are equipped with a hall-effect encoder
mounted in the non-drive end of the motor and a bi-metallic
thermal switch in the windings. See page 3.
Thermal switches may be used in separate control circuits up to
240 VAC. Failure to connect the motor protection properly may
result in damage to the motor, or drive, or both.
BLOWER MOTOR CONNECTIONS
Cooling blowers are supplied on DPBV and TEAO motors.
Blower motor connections are located in their own box on the
blower motor. Blowers will vary on non-standard motors.
L1 L2 L3
T1
U1 T2 T3
V1 W1
T4 T5 T6
U2 V2 W2
SIZES 2 AND 3
3 PHASE
BLOWER MOTORS
200-230 VAC
L1 L2 L3
T1
U1 T2 T3
V1 W1
T4 T5 T6
U2 V2 W2
380-460 VAC
NUMBERS ARE PRINTED ON THE WIRES
WIRE COLOR:T1 or U1 -- BLACK T5 or V2 -- WHITE
T4 or U2 -- GREEN T3 or W1 -- BROWN
T2 or V1 -- BLUE T6 or W2 -- YELLOW
Size 2 blowers are single phase, 115VAC. These motors are
impedance protected. Size 3 blowers supplied on 210T through
256T series motors are 3 phase, dual voltage design. For 200 or
230VAC input, they are connected in a delta configuration. For
380 or 460VAC operation they are connected in a star
configuration. Size 8, 9, and 10 blowers use standard AC motors.
They are dual voltage motors that operate on 208-230 or
460VAC. Special motors are supplied on 380VAC. Check blower
motor nameplate for rating data.
If starters, fuses and overloads are not supplied with a motor
control, blower motors must be supplied by proper disconnect
and protective devices.

Page 6POW E RTEC “F” Series Motor Manual
© copy right 2012 by P O WE R TEC Industrial Motors, Inc
RESOLVER EQUIPPED MOTORS
The resolver supplied with POW E RTEC motors is a
frameless, single speed, transmitter type, mounted on the back of
the motor. The rotor element is mounted on the shaft.
See the table at the right for resolver specifications.
R1
R2
S1
S3
S4 S2
Resolver Wiring Configuration
+
Positive resolver rotation is CW facing the resolver end of the motor.
Excitation
Winding
(Primary)
Sine
Output
(Secondary)
Cosine
Output
(Secondary)
The resolver puts out two sinusoidal waves which are in
quadrature, i.e., 90° out of phase with each other. The leading
wave is called the SIN output (S1 and S3) and the trailing wave
is called the COS output (S2 and S4).
There is one electrical cycle of each signal for each revolution of
the motor. The difference between the two waves reveals the
position of the motor. By looking at the period of the waveforms,
the drive can determine the speed of the motor. And by looking
at which waveform is leading, the drive knows in which direction
the motor is turning.
1 Mechanical Revolution
V
T1-T2
V
T2-T3
V
T3-T1
S1-S3
(SINE)
S2-S4
(COSINE)
Resolver Output
Phasing Voltage for 8 Pole Motor
for clockwise rotation at drive end
Primary Feedback Devices - - Technical
Data
Frameless Resolvers
typical output @ 25°C
Parameter
Units
R1
R2
R1*
Frame Size
31
49
31
Ty pe
Transmitter
Transmitter
Transmitter
Primary
Rotor
Rotor
Rotor
Speeds
1
1
1
Input Voltage
Vrms
8
8
4
Frequency
kHz
6.5
6.5
5
Input Current, max
mA
68
85
46
Input Pow er, nom
mW
404
510
100
Transformation
Ratio
0.5 :1
0.5 : 1
0.4856:1
Phase Shift
Deg
-3
-5
-5
Impedances
ZRO
ohms
87+j82
84+j59
49+j73
ZRS
ohms
82+j79
83+j59
45+j67
ZSO
ohms
298+j519
905+j1860
131+j248
ZSS
ohms
278+j497
885+j850
122+j230
DC Resistances
Stator
ohms
42
195
52
Rotor
ohms
57
62
33
Null Voltage
mV
45
30
15
Max Electrical
Error
minutes
±20
±20
±20
Output Voltage
Vrms
4.0
4.0
1.94
Weight
lb.
1
2.43
1.3
NOTES:
R1 resolvers are used in standard motors except as follows:
R2 resolvers are used in all double shaft and TEFC 280 and 320
frames and all single shaft 500 frames.
R1* resolvers are used with special drive excitation conditions.
Data is for estimation purposes only. For certified data, consult the
factory.
PHASING DIAGRAM OF MOTOR STATOR
Phase T1
Phase T2Phase T3
CW

POW E RTEC “F” Series Motor Manual Page 7
© copy right 2012 by P O WE R TEC Industrial Motors, Inc.
THERMISTORS AND THERMAL
SWITCHES
Motors with R3 Resolvers have two thermal switches connected
in series embedded in the windings.
Motors equipped with R1 and R2 Resolvers have two Negative
Temperature Coefficient (NTC) thermistor probes. They are
10,000 ohms each @ 25°C, connected in parallel to terminals 8
and 9 in the motor junction box. Thermistor leads are labeled P1
and P2. At Room temperature (25°C) the resistance between P1
and P2 should be 5000 ohms.
The Overtemperature threshold for totally enclosed motors is
145°C (104.2 0hms). The threshold for drip proof and blower
ventilated motors is 130°C (150.5 ohms).
Since the potential exists for a thermistor to open up, Motor
Overtemperature Warnings should be set no higher than 80% of
Fault Temperature on totally enclosed motors, and no higher than
80% for drip proof and blower ventilated motors.
Thermistor Resistance Table
Nominal Resistance between P1 and P2 in ohms
Resistance tolerance is +/- 5%
Winding
Temp.
RP1-P2
Winding
Temp.
RP1-P2
°C
ohms
°C
ohms
-30
88500
90
459
-20
48535
100
340
-10
27665
110
255.5
0
16325
120
194.5
10
9950
130
150.5
20
6250
140
117.5
30
4028
150
92.5
40
2663
160
74
50
1801
170
59.5
60
1244
180
48.5
70
876
190
39.7
80
629
200
32.8
RESOLVER MOTORS - - CONNECTIONS AND TERMINAL MARKINGS
MOTOR CASE
GROUND RESOLVER THERMISTORS
3 4
S2
YEL
S4
BLU
1 2
S1
RED
S3
BLK
R1
RED/WHT
R2
BLK/WHT
5 6 7
SHIELDS
NTC NTC
8 9 10
P1
BLK
P2
BLK
NC
T1
T4
T2
T5
T3
T6
T7
T10
T8
T11
T9
T12
MOTOR / RESOLVER LEADS
Motors are shipped with nameplate connections (i.e., 1-Y, 1-D, 2Y, or 2-D)
Check Motor nameplate for correct connections.
See page 4 for connection diagrams.
Consult drive manual for motor / drive interconnections.
When supplied, will have leads tagged H1 and H2. Check nameplate for voltage and current ratings.
SPACE HEATERS
OTHER ACCESSORIES
Check motor nameplate and accessories nameplates for connections and ratings.
CAUTION :
Connect cable shields to designated points only. DO NOT connect shields to ground.

Page 8POW E RTEC “F” Series Motor Manual
© copy right 2012 by P O WE R TEC Industrial Motors, Inc
ENCODER EQUIPPED MOTORS
The encoder connections must be run in a shielded cable. There
are seven connections to the encoder. When the motor thermal is
run in the 24VDC or 48VDC control circuit, it may also be run in
the cable (except on the 320 frame motors where the thermal
connections are not in the same junction box). A cable such as
BELDEN®part #9539 may be used.
A connection diagram is supplied with each motor control. The
shield should be connected at the drive end at TB1 terminal 1.
The shield on the motor end should be connected to the terminal
strip in the motor at terminal 10. DO NOT GROUND THE
SHIELD AT ANY POINT. If there are junction boxes between the
motor and the control, install a terminal to continue the shield
through the junction box.
ENCODER ALIGNMENT PROCEDURE
If a motor has been disassembled, the encoder must be lined up
again so that it is properly aligned with the magnets on the rotor
and the windings of the stator. Also, if the encoder has been
replaced, adjustment of the assembly is necessary.
There are two types of feedback assemblies. F1 encoders are
used for motors with the junction boxes mounted on the left side of
the motor (facing the drive end with the feet down) and for motors
with junction boxes on the right side of the motor near the back. A
top mounted box uses the F1 assembly.
F2 assemblies are for older motors motors with the junction box
on the right side of the motor near the drive end. These encoders
are for replacement use only.
PROCEDURE
1. The encoder feedback assembly mounts in the back of the
motor. The hole in the end bell on the junction box side locates
the cable breakout point from the feedback assembly. An end bell
mark shows the notch location.
2. After the feedback assembly is mounted, but before the
magnetic wheel is mounted on the shaft of the rotor, it is
necessary to align the rotor with the stator. The connections on
the power leads must be made according to the nameplate (see
Page 3). Start with the keyway of the motor shaft in the 12 o'clock
position (up) with the motor standing on its feet.
3. The alignment of the rotor may be done on small motors by
attaching any battery (such as a 9 volt cell) to the power leads.
The positive terminal should be connected to the T1 lead of the
motor, and the negative terminal of the battery should be
connected to the T2 lead of the motor. The rotor will move to the
nearest pole. Do not leave the battery connected or it will quickly
be drained.
On larger motors, the Genesis Series motor control may be used
to align the rotor. Turn off the motor control and turn the current
limit (both current limits on a regenerative drive) potentiometer(s)
fully counter-clockwise. Disconnect the wires on the motor
control at TB1 terminals 2, 3, and 4. Connect a jumper wire from
TB1 terminal 16 to TB1 terminal 3 on the motor control. Turn
on the motor control; give it a speed command of about 10% , and
turn the current limit (motoring) up about 30°. The motor will align
to the nearest pole. Return the motor control to its proper
connections and adjustments.
With an LED box or meter on the diode scale, put the encoder
wheel on the shaft with the white mark near the cable breakout
and turn the wheel on the shaft to obtain the following results (on
the meter, an on sensor will have a low impedance):
F1 Junction Box F2 Junction Box (old motors)
HS1 ON OFF
HS2 OFF ON
HS3 Changing Changing
When this condition is obtained, fasten down the encoder
magnetic wheel on the shaft with the two set screws (90° apart)
on the hub. The motor should now be aligned within 3° of its
rotation to the stator.

POW E RTEC “F” Series Motor Manual Page 9
© copy right 2012 by P O WE R TEC Industrial Motors, Inc.
SETTING NEUTRAL
The preceding procedure is used at the factory to do the
initial setting of the encoder alignment. Then factory alignment
marks are placed on the end bell for the position of the notch on
the feedback assembly, and on the motor shaft and encoder
magnetic wheel to show the alignment of the encoder parts. The
previous procedure can be bypassed if the factory marks are
plainly evident and the motor has not been rewound.
Installing a new encoder on the motor or reinstalling the old
one may be done by the factory marks as long as the motor is
properly assembled. Then it is necessary to set the actual position
of the feedback assembly to set the neutral of the encoder. This is
the fine tuning of the encoder alignment.
PROCEDURE
Connect a true RMS AC voltmeter to motor leads T1 and
T2. Do not use a peak-reading meter.
Run the motor with no load at rated RPM in the forward
direction and note the AC voltage level on the meter.
3. Run the motor in the reverse direction at rated RPM
and note the voltage on the meter.
Adjust the feedback assembly (by loosening the two
mounting screws) a few degrees left or right to equalize the AC
voltage in both directions within one percent.
MOTOR THERMAL SWITCH
-- There is a motor temperature thermal switch in the motor,
inserted in the stator windings. The motor thermal switch leads
are located in the main junction box. THIS MOTOR THERMAL
SWITCH MUST BE USED TO PROPERLY PROTECT THE
MOTOR! Failure to use this switch may result in the destruction of
the motor. Brushless DC motor thermal switches work better than
their brush-type DC motor counterparts because the heat in a
Brushless DC motor is produced in the stator, where the switch is
located.
The motor thermal switch is rated as follows:
MAX AMPS BREAK: 12 amps @ 120VAC
8 amps @ 240VAC
2 amps @ 24VDC
CONTINUOUS AMPS: 2 amps at all voltages above.

Page 10 POW E RTEC “F” Series Motor Manual
© copy right 2012 by P O WE R TEC Industrial Motors, Inc
MOTOR ENCLOSURES
The enclosure type is determined by whether the motor is cooled
by air moving through it, or by convection to the ambient air
around it, or by air moving over it. CONSTANT TORQUE
SPEED RANGE (CTSR) is a thermal consideration. The constant
torque speed range is the range of speeds (based on base
speed) over which the motor will run at full load without
overheating or de-rating. De-rating the motor beyond its speed
range does not mean it will not put out full torque. It means the
motor cannot thermally support full torque output continuously.
DPFG -- DRIP PROOF, FULLY GUARDED
The drip proof fully guarded motor moves air through the motor
by means of an internal, shaft driven fan. Louvered covers in the
front and rear of the motor prevent foreign matter from entering
the motor when dropped from above or at an angle of up to 18°
from the vertical. The Constant Torque Speed Range of the
DPFG motor may be 2:1 or 100: 1, depending upon the frame
size.
DPBV -- DRIP PROOF, BLOWER VENTILATED
The drip proof, blower ventilated motor uses forced air through
the motor to cool it. The blower is generally mounted at the rear of
the motor (at the non-drive end) and the forced air is exhausted
out the front of the motor. The blower is separately powered. The
CTSR is normally 100:1 or better.
TENV -- TOTALLY ENCLOSED, NON-VENTILATED
The totally enclosed non-ventilated motor is dust-tight with no
openings to the ambient air. The motor is cooled by natural
convection and radiation. The CTSR of the TENV motor is
100:1 or greater, but the horsepower range is limited to smaller
sizes.
TEFC -- TOTALLY ENCLOSED, FAN COOLED
The totally enclosed fan cooled motor is dust-tight with no
openings to ambient air. A shaft-mounted fan on the non-drive
end of the motor cools the motor. This allows higher horsepowers
than TENV. The CTSR of TEFC motor is 2:1.
TEAO -- TOTALLY ENCLOSED, AIR OVER, OR
TEBC –TOTALLY ENCLOSED, BLOWER COOLED
If a totally enclosed applications requires a wider speed range
and larger horsepowers, the totally enclosed, air over (blower
cooled) motor has a constant speed fan, which blows air over the
motor’s external surface to cool it. Since the air volume is constant
with speed, the Constant Torque Speed Range of the TEAO
motor is 100:1.
TEWC -- TOTALLY ENCLOSED, WATER COOLED
For still larger sizes of totally enclosed motors, the totally
enclosed, water cooled motor removes heat by means of a water
jacket. Cooling water, or other liquid, may be used in a closed or
open system. The CTSR is 100:1 or greater.
This list is not a complete listing of all types, nor is the description
complete. For further information on motor enclosures, consult
NEMA Publication No. MG1.
MOTOR COOLING REQUIREMENTS
FORCED AIR COOLING
DPBV and TEAO motors require forced-air cooling, which is
accomplished by a centrifugal blower and AC motor. Separately
Ventilated motors (DPSV) require the user to supply a forced
air stream to cool the motor. Whether supplied by
POW E RT EC or others, the cooling blowers must have
minimum specifications as follows:
AIRFLOW STATIC BLOWER
FRAME CFM PRESSURE SIZE
inches of water
182T, 184T 100 0.9 2
213T,215T, 219T 200 1.9 3
254T,256T 223 1.6 3
259T, 2512T 270 2.6 8
287T,288T,2810T,2812T 425 4.6 9
328T,3211T,3213T 660 4.0 10
504ATZ, 506ATZ, 508ATZ 1500 1.1 12
Check the motor blower nameplate for the voltage and current
requirements of your blower.
WATER COOLING
Cooling water for TEWC motors must enter the motor at no more
than 40 °C. To maintain a maximum temperature at the water
outlet of 55 °C, the following minimum flow rates must be
maintained for each frame size listed:
FRAME FLOW RATE (GPM)
254T 0.8
256T 1.3
259TZ 1.7
288TZ 1.8
2810TZ 2.2
2812TZ 2.7
328TZ 3.4
3211TZ 4.0
3213TZ 4.0
Other cooling liquids and/or additives may be used. Consult
the factory for the required flow rates.

POW E RTEC “F” Series Motor Manual Page 11
© copy right 2012 by P O WE R TEC Industrial Motors, Inc.
MOTOR SERVICE PROCEDURE
Any competent motor shop that can overhaul AC induction motors
may service Brushless DC motors. There are differences that
must be observed in the permanent magnet rotor, the feedback,
and the bearings.
PERMANENT MAGNET ROTOR - Permanent magnets used in
the Brushless DC motor are constructed of a highly stable
material and will not demagnetize under normal conditions. The
motors can be disassembled and reassembled without affecting
the strength of the magnets.
HANDLE THE ROTOR WITH GREAT CARE SINCE THE
MAGNETS ARE BRITTLE AND CAN BE DAMAGED IF
DROPPED! DO NOT SET ON A STEEL SURFACE!
RESOLVER - The resolver consists of two parts: a rotor
mounted on the shaft and the stator attached to the motor's end
bell at the non-drive end. These components must line up
properly if the motor is to operate correctly. See page 8 for the
encoder alignment procedure after re-assembling an encoder
equipped motor.
BEARINGS -- Bearings are press-fit on the rotor shaft. The rear
(non-drive end) bearing is fixed in place by a bearing retainer
plate, and both bearings are slip fit into their housings. When
replacing bearings, they must be positioned up against the
bearing shoulder on the shaft.
DIS-ASSEMBLY OF THE MOTOR
Refer to exploded view drawing and parts list on page 4. This is
a general drawing, and not all details are shown.
1. Before disassembling the motor, remove the rear cover
(#19) from the bracket (# 14) to expose the resolver.
2. Make sure that there are marks on the end bells (#14
and #22), frame (#25), resolver assembly (#15), resolver rotor
(#17), and motor shaft (#2) to locate parts when the motor is
reassembled. Be sure those marks will not be obscured in the
process.
3. Remove the resolver rotor (#17) from the shaft. It is
secured by two set screws (#16) 90° apart on the hub.
4. Remove the two bearing retainer plate screws (#13) in
the non-drive end. In some cases this may require loosening the
two set screws (#18) holding the resolver assembly (#15) and
moving the resolver stator out of the way. This releases rear
bearing (#4) and allows removal of the shaft or end bell.
5. Remove four bolts (#11) that hold the drive end bracket
(#22) on. Some motors have hex nuts on overbolts that run the
length of the motor. Note the location of the lifting lugs (#21).
6. Carefully slide the drive end bracket (#22) off of the
shaft (#2). Don't allow the end bell to scrape the shaft as it is
removed. Note carefully the location of parts that come loose as
the end bell is removed, such as the wave washer (#23) in the
front housing. The rotor stays in the frame assembly.
7. The rotor (#2) may now be removed by sliding it
slowly out. The banding will protect the magnets against damage
while sliding out straight. Avoid jerky side to side movements.
While the rotor is out of the motor, protect the banding and
magnets from sharp blows and pointed objects.
8. If only the rotor assembly is to be serviced, it is not
necessary to remove the resolver end bracket (#14). If the motor
stator is to be rewound, then the resolver end bracket should be
removed. Remove the two set screws (#18) holding the resolver
(#15) in place. Before removing the resolver, disconnect the
wires from the block (#31) in the motor junction box and tie a
string onto the wires. This will help cable reinstallation. Remove
the assembly.
DO NOT PULL ON THE WIRES OF THE CABLE OR ON
THE ASSEMBLY. Pull the outside cable jacket only.
RE-ASSEMBLY OF THE MOTOR
1. Make sure the inside surface of the stator is smooth with
no foreign material (such as metal shavings) in the area. Also
check rotor assembly for foreign matter (like metals).
2. Carefully slide the rotor (#2) into the stator assembly
(#25) slowly, BEING VERY CAREFUL TO AVOID INJURY TO
THE HANDS OR ARMS. Make sure you insert the rotor from the
drive end of the frame.
3. Once the rotor is inside the stator assembly, the
resolver end bracket (#14) may be installed. Make sure the
marks made before disassembly line up properly. Use long
screws to position the bearing retainer plate before pushing end
bell in. Replace bearing retainer plate screws (#13).
4. Position the air baffle (#24 - not TENV motors), and
place the wave washer (#23) in position in the front housing.
Replace drive end bracket (#22) according to the marks made
before disassembly, being careful not to scratch the shaft.
5. Reinsert four bolts (#11) into holes in the end bells of
the motor (don't forget the lifting lugs - #21), making sure the end
bells are seated properly in the ends of the frame.
6. Install the resolver (#15) according to the orientation
marks and connect cable leads to the block in the junction box
(#31) according to the drawing on page 7.
7. Reinstall rotor (#17) on the shaft aligning the marks.
8. Turn the motor by hand to check for rubbing, scraping,
and make sure the shaft turns freely. Check for lengthwise and
sideways movement of the shaft.
9. Torque down all bolts and screws, and proceed to motor
resolver alignment or motor encoder alignment.

Page 12 POW E RTEC “F” Series Motor Manual
© copy right 2012 by P O WE R TEC Industrial Motors, Inc
TROUBLESHOOTING
When a motor does not operate as expected, there
may be a valid reason other than that the motor is
bad. Troubleshooting involves looking at the
entire system of motor, control and
environment. Problems that occur when a motor is
first put into service are most likely caused by
misapplication, improper connection or lack of
understanding. Problems that occur after a motor
has been in service for some time period may be due
to motor, control or environment.
These troubleshooting tips cover possible problems
as well as problems which were seen in the past.
PROBLEM SHAFT ROCKS BACK AND FORTH
1. Motor leads T1, T2, and T3 are not connected to the
corresponding terminals on the motor control. T1 MUST be connected to
T1, T2 MUST be connected to T2 and T3 MUST be connected to T3.
2. Encoder cable is connected to control improperly . Check the
connections to the control per the card supplied w ith the control. The main
connections inv olv ed are the connections inv olv ing HS1, HS2, and HS3.
PROBLEM ERRATIC SPEED
1. Motor is going at or abov e base speed w hile cold. Allow
motor to warm up before adjusting max imum speed.
2. Feedback cable from motor to control is improperly shielded,
run w ith pow er cables, or defective. Check the cable connections per the
card supplied w ith the control.
3. Feedback signals are improper or missing. Check resolv er
signals against w av e forms on page 6. Check encoder w av eforms
against draw ing below . The draw ing below is for a four pole motor. An
eight pole motor w ill hav e the same w av eforms, but the interval marked
as being 1/2 rev olution of the motor in the draw ing below w ill be 1/4
rev olution in an eight pole motor.
4. Bearings are w orn. This w ill likely show up as increased
current and an ov erheating motor, but sev ere bearing problems may
affect speed control of the drive.
5. Sev ere load v ariations, such as a high inertia load changing
speeds quickly may result in speed being erratic. Consult POWERTEC.
6. Driv e is unstable. Adjust gain and/or stability
OFF
ON
OFF
ON
OFF
ON
OFF
ON
OFF
ON
Encoder waveforms
PROBLEM EXCESS END PLAY OF THE SHAFT
Check for excessive thrust loading on the shaft.
1. Check the tightness of the bearing retainer plate by checking
the bearing retainer plate screw s on the non-driv e end. (On some motors,
these screw s may be partially or completely hidden by the feedback
assembly .)
2. The bearings may be ex cessiv ely w orn.
3. The shaft bearing journals may be shot.
PROBLEM EXCESS RADIAL SHAFT PLAY
* Make sure radial loading on shaft is not
excessive.
1. The shaft may be loose in the bearing I.D.
2. The bearings may be ex cessiv ely w orn.
3. The bearing housing may be w orn.
PROBLEM EXCESS VIBRATION
1. The load may be out of balance. Check the load balance.
2. The motor mounting bolts may be loose. Check for tightness.
3. The rotor may be unbalanced. Run the motor unloaded.
4. There may be ex cessiv e radial play . See abov e.
5. The bearings may be w orn. Listen for bearing noise.
6. Noise on driv e speed reference.
PROBLEM MOTOR RUNS HOT LOADED
DO NOT JUDGE MOTOR TEMPERATURE BY TOUCH.
USE ATEMPERATURE MEASURING DEVICE.
1. Check ambient temperature. It must be less than rated (40°C).
2. Check the load on the motor. Do not ex ceed rated current.
3. Check the duty cy cle of the motor. It may not exceed 100%
RMS.
4. The brake, if there is one, may not be releasing.
5. The bearings may be w orn. Run motor unloaded.
6. The rotor may be rubbing the stator. Listen for noise.
PROBLEM MOTOR RUNS HOT UNLOADED
1. Check all items under Motor runs hot loaded.
2. The motor control may be misadjusted. Check motor control.
3. The encoder or resolv er may be improperly set up. See Page
6.
4. The motor may be demagnetized. Check terminal v oltages.
PROBLEM MOTOR RUNS TOO FAST
1. Check the max imum speed setting on the motor control.
2. HS4 and HS5 on the encoder signals may be sw apped.
3. Resolv er or encoder misaligned.
4. Motor may be demagnetized. Check terminal v oltages.

POW E RTEC “F” Series Motor Manual Page 13
© copy right 2012 by P O WE R TEC Industrial Motors, Inc.
PROBLEM LOW OUTPUT TORQUE
1. Improper alignment of feedback dev ice
2. Open pow er connection.
3. Open or shorted stator w indings.
4. Motor may be partially demagnetized.
ROUTINE MAINTENANCE
Observe the motor during operation, checking for excess
vibration, unusual noises and excess heat.
1. VIBRATION
1. Check for signs of excess vibration. It may be the result of
poor alignment, worn or loose couplings or sheaves, or
damaged bearings. It may be a poorly designed base. Excess
vibration causes damage to the bearings, shaft, mounting feet and
accessories.
2. Noise on the speed reference input to high performance
drives has been known to cause vibration in motors.
3. When checking balance on an unloaded motor, install a half
key in the shaft keyway.
2. NOISE
1. Listen for noise in the area of the bearing housings.
Rubbing noises may be a sign of internal damage.
2. A steady high pitched hum is normal in a BLDC motor, and
there may be short interruptions of this hum under no load
conditions. If you hear growling or an erratic hum above 20
RPM, check the drive.
3. TEMPERATURE
1. Drip Proof Fully Guarded (DPFG), Drip Proof Blower
Ventilated (DPBV), and Totally Enclosed Air Over (TEAO)
motors may run at surface temperatures in excess of 85°C.
2. Totally Enclosed motors (TENV) may have surface
readings as high as 100 °C. Before checking the temperature of
a motor, check the load on the motor.
Use a thermal probe for an objective reading
DO NOT CHECK MOTOR TEMPERATURE WITH YOUR
BARE HAND!!! HIGH TEMPERATURES MAY CAUSE
BURNS!
4. FEEDBACK DEVICE
1. The feedback device is located inside the motor. It requires
no maintenance unless you disassemble the motor.
2. The alignment of the motor feedback device is important. If it
is removed, it must be re-installed correctly.
5. BRAKES
1. Brakes supplied on "F" series Brushless DC motors are
fail-safe, disk type brakes. You release the brake by energizing
the brake coil. There may be a manual release.
2. The brakes do not normally require adjustments, but the
pads may have to be changed periodically if the brake is used for
stopping duty.
6. SECONDARY FEEDBACK DEVICE
Check externally mounted encoders (coupling and mounting
bolts) periodically for tightness.
7. COOLING BLOWERS AND FILTERS
Cooling blowers are AC motors that require little maintenance.
They have a lubrication life of 15,000 to 40,000 hours.
ATTEMPTING TO SERVICETHEFILTERWHILETHEBLOWER
MOTORIS RUNNING MAY CAUSEINJURY.
1. Be sure the blower is running in the correct direction, which
is in the direction of the arrow on the blower scroll.
2. Clean out multi-crimp filters with a solvent. Let dry
thoroughly. Spray with an air filter adhesive and drain excess.
3. Before re-mounting the filter, be sure that there is no
build-up of material inside or on the blades of the impeller.
8. BEARINGS AND RE-LUBRICATION
1. 42, 140, and 180 frame motors have permanently
lubricated bearings. Replace damaged or worn bearings.
2. Frames 210 and larger are lubricated at the factory with
Chevron SRI #2 grease. Suitable substitutes are Amoco’s
RYKON Premium #2, Texaco's Polystar B, or EXXON’s Polyrex.
Do not use the “EP” versions of these greases. High-speed
motors use Kluber HB72-52.
3. Use the table below for bearings of standard motors with
standard or maximum capacity bearings. These motors have a
"0" or "1" as the 10th digit in the Model Number. Re-lubricate
vertically mounted motors at 1/2 the table interval.
4. Roller bearings are indicated by a "2" in the tenth position
of the Model Number. Re-lubricate these at 1/2 of the table
interval. For vertically mounted motors, use ¼ of the interval. For
high speed motors, consult the graph on page 16. High-speed
motors have a "9" in the tenth position.

Page 14 POW E RTEC “F” Series Motor Manual
© copy right 2012 by P O WE R TEC Industrial Motors, Inc
Lubrication Interval in Operating Hours - STANDARD BALL BEARINGS only
HORIZONTALLY MOUNTED, AVERAGE MOTOR SPEED (RPM)
FRAME
1150
1750
2500
3600
42
28,000
18,000
13,000
8,500
140
23,000
14,000
10,000
6,700
180
19,000
12,000
8,000
5,400
210
16,000
10,000
6,300
3,800
250
13,500
8,000
5,000
2,900
280
11,500
6,600
3,900
2,200
320
9,600
5,600
3,000
1,400
500
6,400
3,200
500
N/A
If a motor has no grease fittings, the bearings must be replaced.
MOUNTING BOLT TORQUES
Motors must be mounted on a solid, rigid base or foundation.
Poor base design can result in resonance in the motor/base
system that can result in bearing, motor feet, frame to foot
fasteners, or other, and motor damage.
All hold-down bolts must be of the correct grade for the type of
mounting, and for the method of coupling the motor to the load.
Some considerations are:
1. Direct coupled or belt drives
2. Motor feet orientation (horizontal, wall, or ceiling
mounting).
Bolts must be evenly torqued to their recommended value.
Recommended bolt torques for SAE grade foot bolts are given
below in foot-pounds. (All components are dry, i.e., not
lubricated):
Foot Bolt Steel Steel
Frame Hole Size Grade Grade Socket
Size Diam & Third 1 5 Head
42 .34 5/16-18 10 15 25
140 .34 5/16-18 10 15 25
180 .41 3/8-16 16 26 42
210 .41 3/8-16 16 26 42
250 .53 1/2-13 39 63 100
280 .53 1/2-13 39 63 100
320 .69 5/8-11 77 125 200
500 1.19 1-8 320 500 820
Motors with aluminum feet require a suitable heavy flat steel
washer between the foot and the mounting fasteners to spread
the bolt-clamping load out over a suitable area.
The above values are suitable for most applications. Heavily
loaded systems and systems that are dynamic may require
careful study in choosing a suitable mounting system, grade of
bolt to be used, and hence the required bolt torques.

POW E RTEC “F” Series Motor Manual Page 15
© copy right 2012 by P O WE R TEC Industrial Motors, Inc.
RADIAL LOADING OF THE MOTOR
When a motor is driving a belt-driven load, care must be taken to
prevent the side pulling forces to damage the bearings and/or the
shaft of the motor.
MAXIMUM SHAFT RADIAL LOADING
TABLE
Standard Ball Bearings and standard shaft extension
Radial Load Centered at tip of Shaft
Expected L10 life at 1750 RPM average speed of 20,000 hours
Frame/ Series
Shaft Diam
Bearing #
Max Radial Load
(lbs.)
Min Sheave Dia
(in.)
42
0.625
203
90
0.9
140
.875
205
180
2.4
182/184
1.125
207
280
4.6
213/215
1.375
209
440
4.4
219
1.625
209
650
4.0
254/256
1.625
211
600
6.5
259/2512
2.125
M211
1100
6.0
287
2.125
313
1100
6.0
288/2810/2812
2.375
313
1350
9.6
328/3211/3213
2.875
315
1800
12.0
504
3.25
6222 / 6222W
1500 / 2200
21.6 / 14.7
506
3.625
6222 / 6222W
1400 / 2100
30.9 / 20.6
508
4.125
6222 / 6222W
1300 / 2000
41.5 / 27.0
If radial loads exceed the "Max Radial Load", or the sheave diameter is too
small roller bearing are required.
500 frames with ball bearings are recommended for direct coupled service only.
Belt drives with 500 frame motors require roller bearings in the drive end.

Page 16 POW E RTEC “F” Series Motor Manual
© copy right 2012 by P O WE R TEC Industrial Motors, Inc
MOTOR NAMEPLATE DATA
FRAME
An alphanumeric designation of the size of a motor. These designations
are standardized in the USA by the National Electrical Manufacturers
Association (NEMA). For standard NEMA frames140 and larger, the first
two numbers are four times the height of the center of the motor shaft
above the feet. The third and fourth (if used) numbers indicate the distance
between the mounting holes on the feet lengthwise, but a table is
necessary to find the actual distance.
MODEL
The MODEL number of the "F" series motors is a description of how the
motor is put together. The model number describes the windings and
connections as well as frame size, configuration, and options.
HP
The rated output horsepower of the motor is listed in the HP block. This
value of horsepower is only valid at base speed, or above base speed, if
the drive is equipped to operate in extended speed range.
RPM
The base speed of the motor, the speed at which rated horsepower is
developed. From zero to this speed is the CONSTANT TORQUE
speed range. If there are two numbers in this block with a slash between
them, the first number is the base speed and the second number is the top
speed. Between these two speeds is the CONSTANT HORSEPOWER
range.
BUS VDC
For a Brushless DC motor, this is the voltage level of the DC supply
from which the drive operates the motor. In most cases, this value is the
nominal capacitor bank voltage level, which is about 1.4 times the RMS
value of the AC input to the drive.
DUTY
This is a rating which may limit how the motor is used. If the designation
CONT is in this block, the motor may be used for continuous duty up to
its full ratings. A 30 MIN rating in the DUTY block indicates that the motor
may be run to its full rating for 30 minutes, after which it must cool to
ambient temperature.
RMS AMPS
This is the per phase motor current (in RMS AC amperes) required to
develop full load torque on a motor that has reached its steady state
operating temperature.
S.F.
The SERVICE FACTOR is a multiplier to the HP, indicating how much
power may be used under rated conditions.
INSUL. CL.
INSULATION CLASS "F" is rated for 105°C rise above an ambient
temperature of 40°C. Class "H" is rated for 125°C rise. The motor over-
temperature protector is set to correspond.
AMB °C
The AMBIENT TEMPERATURE in which the motor operates should not
exceed this number.
ENCL
This is the type of enclosure of the motor. In Europe, it is called the
PROTECTION CLASS. There are two basic types: OPEN and
CLOSED. See "MOTOR ENCLOSURES" on page 6 for a description
of the standard NEMA motor enclosures.
C.T. SPD. RANGE
This is the ratio of speeds, based on BASE SPEED, over which the
motor may be operated at full torque continuously. This is a THERMAL
limitation. This does not guarantee smooth operation, only that the motor is
able to cool itself at full torque over this range.
CONNECTION
This is either 1-D or 2-D, 1-Y or2-Y. (D = delta; Y = wye) This refers to
the connection of the windings. See "Motor Winding Connections" for
details on the connections.
PEAK RMS AMPS
Do not exceed this value at any time. This is the maximum safe current
which will not affect the permanent magnets.
INTEGRAL ENCODER
This number is the pulses per revolution (PPR) which will be seen in
one channel of the speed feedback (HS4 or HS5) from the internal
encoder. The two channels are 90° out of phase with each other, i.e.,
they are in QUADRATURE. For small motors the number should
be 30. Large motors should be 60.
KE V/KRPM
This is the RMS voltage which should be observed between any two
power leads of the motor at 1000 RPM. This measurement is taken with
the windings at room temperature (25 °C). Actual voltage at operating
temperature may be as low as 90% of the 25 °C value.
SERIAL NO.
Use when calling to ask questions or to order spare parts. This number is
also stamped into the frame near the junction box.
JOB NO.
This is a factory in-house number for the factory build job that included this
motor.

POW E RTEC “F” Series Motor Manual Page 17
© copy right 2012 by P O WE R TEC Industrial Motors, Inc.
BEARING RELUBRICATION INTERVAL CHART
USE THIS CHART TO ESTIMATE THE RELUBRICATION INTERVAL AT SPEEDS OTHER THAN BASE
SPEED AND FOR HIGH SPEED MOTORS.
This chart is based on the use of Mobil SHC 1500 or Klubersynth HB 72-52 (high speed) grease.
320
280
250
210
180
140
42
500
HOURS OF
OPERATION
100,000
80,000
60,000
40,000
30,000
20,000
10,000
8,000
6,000
4,000
3,000
2,000
1,000
800
600
400
300
200
100
100,000
80,000
60,000
40,000
30,000
20,000
10,000
8,000
6,000
4,000
3,000
2,000
1,000
800
600
400
300
200
100
SPEED RPM

POWERTEC Industrial Motors
13509 South Point Blvd. • Suite 190 • Charlotte, NC USA 28273 • PHONE: 704-227-1580
Internet: powertecmotors.com • E-mail: [email protected]
2012
P/N 2093-000000-002
Table of contents
Other Power Tec Engine manuals
Popular Engine manuals by other brands
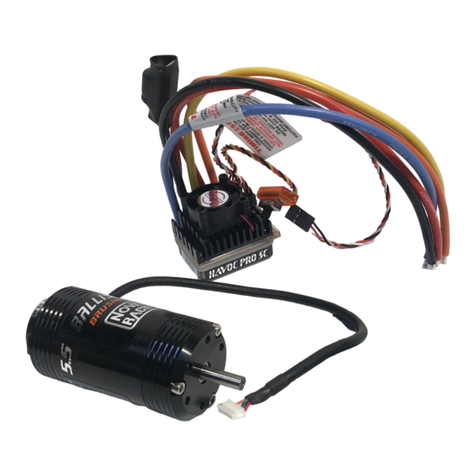
NOVAK
NOVAK BALLISTIC BRUSHLESS - MOTOR INSTRUCTIONS REV... instructions

TOHATSU
TOHATSU MFS 5C LPG owner's manual

Briggs & Stratton
Briggs & Stratton 120000 Operating and maintenance instructions
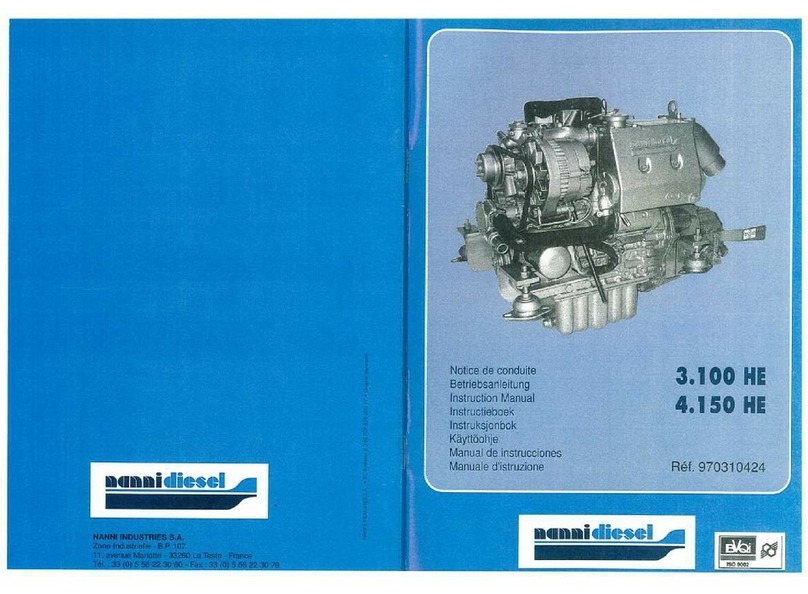
Nanni
Nanni 3.100 HE instruction manual
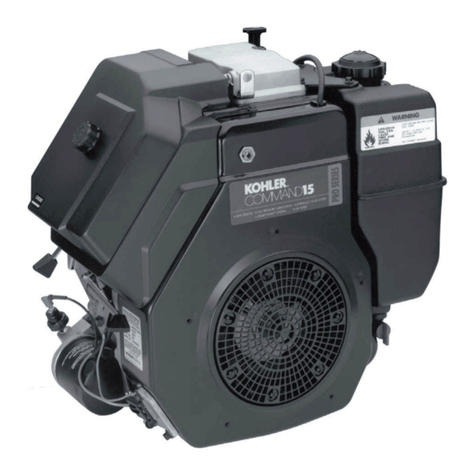
Kohler
Kohler CH-11-16 owner's manual
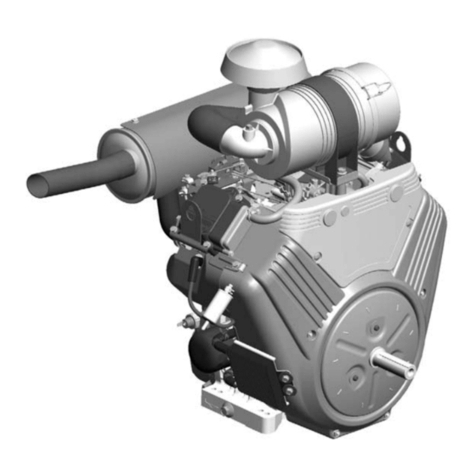
Briggs & Stratton
Briggs & Stratton Vanguard 610000 Operator's manual