Reliance electric RPM AC Installation and operating instructions

Installation, Operation
and Maintenance of
RPM AC¥
INDUCTION MOTORS
• FRAMES 56-L440
• SPECIFICALLY DESIGNED FOR OPERATION
WITH ADJUSTABLE FREQUENCY
CONTROLLERS
Instruction Manual B-3682-3

Table of Contents
GENERAL DESCRIPTION
Receiving and Handling.............................................................................................................................................1
INSTALLATION
Location.....................................................................................................................................................................2
Drain Plugs................................................................................................................................................................2
Mounting....................................................................................................................................................................2
Stub Shaft..................................................................................................................................................................3
Connections...............................................................................................................................................................3
Direction of Rotation..................................................................................................................................................4
Grounding..................................................................................................................................................................5
Drive ..........................................................................................................................................................................5
Shipping Blocks.........................................................................................................................................................5
Encoder Connections - Dynapar H2O and Lakeshore Products...............................................................................5
MOTOR APPLICATION DATA
Maximum Safe Speed ...............................................................................................................................................6
Minimum V-Belt Sheave Diameter.............................................................................................................................6
Shaft Extension and Method of Drive........................................................................................................................6
Shaft Loads - Axial and Radial ..................................................................................................................................6
OPERATION
Motor Start-Up...........................................................................................................................................................8
Balance......................................................................................................................................................................8
MAINTENANCE...............................................................................................................................................................9
Lubrication...............................................................................................................................................................10
Bearings .................................................................................................................................................................11
Disassembly and Reassembly.................................................................................................................................12
Stub Shaft Removal.................................................................................................................................................12
Replacement Bearings/Spare Parts ........................................................................................................................13
PARTS IDENDIFICATION.............................................................................................................................................14
TOTAL SERVICE CAPABILITY.....................................................................................................................................15
REGIONAL SERVICE CENTERS .................................................................................................................................16

1
General Description
The products described in this instruction manual are manufactured by Reliance Electric Industrial Company.
RPM AC™ motors are high performance motors specifically designed for use with adjustable frequency controllers.
The basic design includes Class H insulation (Class F for 56, 140T and W180T frames), 1.0 service factor, 40
R
C
ambient, con tinuous duty. Standard enclosures are totally enclosed blower cooled, totally enclosed fan-cooled, non-
ventilated and drip-proof force ventilated. Many modifications, and accessories are available.
NOTE: RPM AC motors are
equipped with metric hardware.
Receiving and Handling
Acceptance
Thoroughly inspect this equipment
before accepting shipment from the
transportation company. If any of the
goods called for in the bill of lading
or express receipt are damaged or
the quantity is short, be sure the
freight or express agent makes an
appropriate notation on your freight
bill or express receipt. If any
concealed loss or dam age is
discovered, notify your freight or
express agent at once and request
him to make an inspection.
Reliance Electric will assist you in
collecting claims for loss or damage
in shipment. However, this does not
re move the transportation
company's responsibility in
reimbursing you for collection of
claims or replacement of material.
Claims for loss or damage in
shipment
must not
be deducted from
the Reliance Electric invoice, nor
should payment of the Reliance
Electric invoice be withheld awaiting
adjustment of such claims, as the
carrier guarantees safe delivery.
If considerable damage has been in
incurred and the situation is urgent,
con tact the nearest Reliance
Electric District Office for assistance.
Please keep a writ ten record of all
such communications.
Handling
In all cases, care should be taken to
assure lifting in the direction
intended in the design of the lifting
means. If multiple eyebolts are
provided, lift using diagonally
opposite eyebolts. Likewise,
precautions should be taken to
prevent hazardous overloads due to
deceleration, acceleration or shock
forces.
Angle of lift with rope or chain must
be greater than 45
R
from horizontal.
For unusual conditions, such as
side-wall and ceiling mounting of
horizontal motors and installation of
vertical motors shipped in a
horizontal position, special
precautions must be taken and it is
recommended that an experienced
rigger be employed.
Storage
Motors must be stored in a clean,
dry area protected from extremes of
temperature, moisture, shock and
vibration. Storage temperatures of
50
R
F to 120
R
F with a maximum
relative humidity of 60% must be
observed. In addition, motors
subjected to extended storage must
be handled and treated per the
requirements of Reliance Electric
Service Bulletin A-8018 available
from your Reliance Electric District
Sales Office.
All drains to be full
y
operable
while in stora
g
e, and/or the drain
plu
g
s removed. The motors must
be stored so that the drain is at
the low est point. All breathers
and automatic “T” drains must be
operable to allow breathin
g
at
points other than throu
g
h the
bearin
g
fits.
DANGER
ONLY QUALIFIED ELECTRI-
CAL PERSONNEL FAMILIAR
WITH THE CONSTRUCTION
AND OPERATION OF THIS
EQUIPMENT AND THE HAZ-
ARDS INVOLVED SHOULD
INSTALL, ADJUST, OPERATE,
AND/OR SERVICE THIS
EQUIPMENT. READ AND
UNDERSTAND THIS MANUAL
IN ITS ENTIRETY BEFORE
PROCEEDING. FAILURE TO
OBSERVE THIS PRECAUTION
COULD RESULT IN SEVERE
BODILY INJURY OR LOSS OF
LIFE.
WARNING
EYEBOLT(S) OR LIFTING
LUG(S) ARE INTENDED FOR
LIFTING THE MOTOR ONLY
WITH THE STANDARD ACCES-
SORIES SUCH AS TACHOME-
TER, BRAKES, ETC.,
MOUNTED BY RELIANCE
ELECTRIC. THE LIFTING
MEANSONTHEMOTORMUST
NOT BE USED TO LIFT THE
UNIT PLUS ADDITIONAL
EQUIPMENT FAILURE TO
OBSERVE THIS PRECAUTION
COULD RESULT IN BODILY
INJURY.
WARNING
EYEBOLTS MAY UNSCREW
DURING LIFTING. CHECK EYE-
BOLTS TO INSURE THAT THEY
ARE TIGHT AND SECURE
EYEBOLTS FROM TURNING,
OR LIFT THE UNIT ON A SLING
OR PLATFORM. FAILURE TO
OBSERVE THIS PRECAUTION
COULD RESULT IN BODILY
INJURY.

2
Installation
RELIANCE® AC MOTORS ARE DE
SIGNED AND BUILT IN AC
CORDANCE WITH
SAFETY STAN
DARD FOR CONSTRUCTION AND
GUIDE FOR SELECTION,
INSTALLATION AND USE OF
ELECTRIC MO\TORS AND
GENERATORS
PUBLISHED BY
THE NATIONAL ELECTRICAL
MANUFACTURERS ASSOCIATION
(NEMA) PUBLICATION MG-2-1983
(ANSI C51.5). RELIANCE
ELECTRIC RECOMMENDS THAT
THIS PUBLICATION BE
REFERRED TO WHENEVER YOU
SELECT OR INSTALL ANY AC
MOTOR. COPIES MAY BE
OBTAINED FROM NEMA, 2101 L.
STREET, WASHINGTON, D.C.,
20037.
The application of motors and other
electrical equipment in hazardous
locations is restricted by the National
Electric Code. Users must observe
these regulations and consult with lo
cal code inspection and enforcement
agencies to insure compliance.
Location
Locate the machine where the
ambient temperature is not over
40
R
C or 104
R
F and where clean air
has free access to ventilating intake
and outlet openings. Except for
machines with a suitable protective
enclosure, the location should be
clean and dry.
NOTE: The cooling system on
standard RPM AC totally enclosed,
blower cooled motors requires clean
air to be forced through ducts which
are integral to the frame. It is
important that these air passages be
kept clean and that sufficient
clearance be provided on the blower
motor air inlets and outlets for
unrestricted flow of air.
For Drip-Proof Force Ventilated
Enclosures sufficient clearance must
be provided on all inlet and outlet
openings to provide for unrestricted
flow of air. Separately ventilated
motors with exhaust to ambient
(pipe-in only) must have at least 6
inches of clearance between the
opening and adjacent walls or floor.
NOTE: Motors located in a damp,
moist environment must have space
heaters to protect against
condensation when motor is not
operating.
Drain Plugs
If motor is totall
y
enclosed it is
recommended that condensation
drain plu
g
s be removed. These
are located in the lower portion of
the end-shields or bottom of
frame on each end for L180 frame.
Totall
y
enclosed “XT” motors are
equipped with automatic drains
which should be left in place as
received.
Power Supply
The RPM AC motor is an adjustable
speed motor designed for operation
with adjustable frequency
controllers.
Verify that the motor nameplate data
corresponds to the controller output
rating and follow the Controller
Instruction Manual for motor
installation and connection.
Conduit Box
The standard conduit box location
for totally enclosed motors is top
mounted for F1-F2 versatility without
motor disassembly. For drip-proof
force ventilated, F1 is standard.
Conduit box can be rotated in 90
degree increments for lead outlet at
front, back or sides. On L180 motors
the conduit box is integral to the top
of the frame with F1 and F2 outlets.
Mounting
Motors must be mounted on a rigid,
solid base or foundation. Poor base
construction may cause resonances
in the motor/base assembly which
can result in bearing failure and
other mo tor damage. All hold down
bolts must be the correct grade for
the type of mounting and must be
torqued to their recommended
value.
Belted Drive
Motor slide bases or rails, when
used, must be securely anchored to
the foundation with the proper bolts.
NOTE: The motor shaft and the load
shaft must be parallel and the
sheaves aligned. Refer to Motor
Application Data Section of sheave
and belt data.
DANGER
ONLY QUALIFIED ELECTRI-
CAL PERSONNEL FAMILIAR
WITH THE CONSTRUCTION
AND OPERATION OF THIS
EQUIPMENT AND THE HAZ-
ARDS INVOLVED SHOULD
INSTALL, ADJUST, OPERATE,
EQUIPMENT READ AND
UNDERSTAND THIS MANUAL
AND/OR SERVICE THIS IN ITS
ENTIRETY BEFORE PRO-
CEEDING. FAILURE TO
OBSERVE THIS PRECAUTION
BODILY INJURY OR LOSS OF
LIFE.
Frame
Hole
Dia.
H (Inch)
Bolt
Size
and
Thread
Recommended
Torque
Foot - Pounds
Bolt Grade
SAE 5 SAE 8
L180 .44 3/8-16 33-37 47-53
L210 .44 3/8-16 33-37 47-53
L250 .56 1/2-13 83-93 117-132
L280 .56 1/2-13 83-93 117-132
L320 .69 5/8-11 155-176 200-249
L360 .81 3/4-10 274-310 389-440
L400 1.06 7/8-9 434-486 616-689

3
Coupled Drive
Standard RPM AC Motors will
operate successfully mounted on the
floor, wall or ceiling, and with the
shaft at any angle from horizontal to
vertical. Special mountings, duty or
thrust demands may, however,
require a different bearing system.
Stub Shaft Installation
Procedure
Screw-in Stub Shaft
1. Turn off and lockout power to the
motor.
2. Remove in-line blower motor and
cover assembly by removing the
Hex head cap screws on cover(if
enclosure is TEAO-Blower
cooled).
NOTE:
An extended blower cover
may be required when a feedback
device is installed. See Reliance
catalog or contact Renewal Parts
forassistancewithanin-lineblow-
er.
3. Check the motor shaft center
hole for chips, dirt, or other
residue and clean as required.
NOTE:
56 and 140T - Some 180
have integral stub shaftwith cover
plate. Remove cover plate and
skip to 8.
4. Obtain the stub shaft to be
screwed into the motor shaft.
ObtainLoctite®Number 271
(Red thread-lock)
5. Apply even coat of Loctite®
Number 271 to stub shaft thread.
Place stub shaft in motor shaft
threaded hole and hand tighten.
6. Using a spanner wrench on
motor shaft drive end (or
alternate means of locking motor
shaft), torque the stub shaft to 20
ft-lbs.
7. Using a dial indicator with .0005
graduations, indicate the stub
shaft to within .002" T.I.R., except
when Inland tachometers are
used. In land tachometer stub
shafts must indicate to within
.001" T.I.R.
8. Mount feedback device per
manufacturer's instructions.
Connections
Bypass Mode
If an RPM AC motor is to be used in
by pass mode, the user must select
a motor starter and overcurrent
protection suitable for this motor and
its application. Consult motor starter
application data as well as the
National Electric Code and/or other
applicable local codes. Consult
Reliance Electric to determine
suitability of motor for specific
applications in bypass mode
.
1. RPM AC motor - POWER
LEADS Sin
g
le Volta
g
e/Three
LeadMotors
Connect leads marked U/T1 V/T2
W/T3 to the appropriate controller
outputterminalspertheController
Instruction Manual. See Connec-
tion Diagram 422927-1 below.
Dual Voltage Motors
Be sure the motor leads are
connected properly for the desired
“Low” or “High” voltage connection
per the motor connection diagram on
the motor. Follow the Controller
Instruction Manual for proper
connection to the controller output
terminals. See diagram 422927-1
below.
Connection Diagram 422927-1.
WARNING
MOTOR C-FACE IS INTENDED
FOR MOUNTING AUXILIARY
EQUIPMENT SUCH AS PUMPS
AND GEARS. WHEN
MOUNTED HORIZONTALLY, C-
FACE MOTORS SHOULD BE
SUPPORTED BY THE FEET
AND NOT BY THE C-FACE.
INSTALLATIONS REQUIRING A
HORIZONTALLY MOUNTED
MOTOR IN FRAMES L280C -
L440 MUST BE SUPPORTED
BY THE FEET AS WELL AS C-
FACE OR D-FLANGE. FAILURE
TO OBSERVE THESE PRE-
CAUTIONS CAN RESULT IN
DAMAGED EQUIPMENT AND
BODILY INJURY. THE USER IS RESPONSIBLE
FOR CONFORMING WITH THE
NATIONAL ELECTRICAL
CODE AND ALL OTHER
APPLICABLE LOCAL CODES.
WIRING PRACTICES,
GROUNDING, DISCONNECTS,
AND OVERCURRENT PRO-
TECTION ARE OF PARTICU-
LAR IMPORTANCE. FAILURE
TO OBSERVE THESE PRE-
CAUTIONS COULD RESULT IN
SEVERE BODILY INJURY OR
LOSS OF LIFE.
THIS EQUIPMENT IS AT LINE
VOLTAGE WHEN AC POWER
IS CONNECTED. DISCONNECT
AND LOCKOUT ALL
UNGROUNDED CONDUC-
TORS OF THE AC POWER
LINE. FAILURE TO OBSERVE
THESE PRECAUTIONS COULD
RESULT IN SEVERE BODILY
INJURY OR LOSS OF LIFE.
3 PHASE-DUAL VOLTAGE
422927-1
THERMOSTAT
LEADS
ASE- SINGLE VOLTAGE3 PH
P2
U/T1
W/T3
V/T2 L1
L2
L3
P1
`
THERMOSTAT
LEADS
HIGH VOLTAGE
P2
U/T1
W/T3
T5
T7
T4
V/T2
T9
L1
L2
L3
P1
`
LOW VOLTAGE
THERMOSTAT
LEADS L1
L2
P2
U/T1
V/T2
T9
W/T3
T8
T7
T4
T5
T6
L3
P1
`

4
For 56, 140T and W180T frame size
connection see diagram 219P036.
Connection Diagram 219P036
II. Direction of Rotation
RPM AC motors are designed to
be capable of bi-directional shaft
rotation.WhenvoltagesinanA-B-
C phase sequence are applied to
leads U/T1, V/T2, W/T3 clockwise
shaft rotation facing the opposite
drive end will result.
If shaft rotation is incorrect,
change the direction of rotation as
follows:
1. Turn off and lockout all power to
the motor.
2. Beforeproceeding, verify that the
voltage at the motor leads is
zero.
3. Reverse any two of three motor
power leads.
III. RPM AC Motor - THERMOSTAT
LEADS (THERMAL
PROTECTOR)
As a standard feature, RPM AC
motors have three (3) normally
closed thermostats (one per
phase) connected in series, with
leadsP1 and P2 terminated in the
main conduit box.
Toprotectagainstmotoroverheat-
ing,thermostatsmustbeconnect-
edtotheappropriatecontrollercir-
cuit (function loss). Failure to
connect the thermostats will
void the motor warranty.Follow
the controller instruction man-
ual for correct thermostat lead
connections.
IV. BLOWER MOTOR
RPMACmotorswhichareblower
cooled incorporate an indepen-
dently powered three-phase AC
blower motor to assure continu-
ous cooling air flow regardless of
RPM AC motor speed.
.
NOTE:
RPM AC blower motor fuse
protection kits are required for
blower motor overload protection.
Blower Motor Connection
The specific RPM AC blower motor
will vary depending on frame size
and enclosure. Follow the
connection diagram supplied with
the blower motor, which in general
will be one of the following:
1.
2.
NOTE: 56, 140T and W180T frames
have single phase 115V blower
motors. See connection diagram
219P108.
3. Connection Diagram 422927-1
under dual voltage motors above.
THIS EQUIPMENT IS AT LINE
VOLTAGE WHEN AC POWER
IS CONNECTED. DISCONNECT
AND LOCKOUT ALL UN-
GROUNDED CONDUCTORS
OF THE AC POWER LINE.
FAILURE TO OBSERVE THESE
PRECAUTIONS COULD RE-
SULT IN SEVERE BODILY
INJURY OR LOSS OF LIFE.
3 PHASE-DUAL VOLTAGE
219P36
LEADS P1 & P2 ARE THERMOSTAT LEADS.
THEY ARE TO BE CONNECTED IN SERIES WITH
THE HOLDING COIL OF THE MOTOR CONTROLLER,
WHICH USES A MANUAL MOMENTARY START
SWITCH.
TO REVERSE DIRECTION OF ROTATION INTER-
CHANGE ANY TWO LINE LEADS.
THERMOSTAT
LEADS
ASE- SINGLE VOLTAGE3 PH
P2
T1
T3
T2
L1
L2
L3
P1
`
THERMOSTAT
LEADS
HIGH VOLTAGE
P2
T1
T3
T5
T7
T4
T2
T9
L1
L2
L3
P1
`
LOW VOLTAGE
THERMOSTAT
LEADS L1
L2
P2
T1
T2
T9
T3
T8
T7
T4
T5
T6
L3
P1
`
DANGER
THE CONTROLLER MAY AP-
PLY HAZARDOUS VOLTAGES
TO THE MOTOR LEADS AFTER
POWER TO THE CONTROL-
LER HAS BEEN TURNED OFF.
VERIFY THAT THE CONTROL-
LER IS INCAPABLE OF
ELIVERING HAZARDOUS
VOLTAGES AND THAT THE
VOLTAGE AT THE MOTOR
LEADS IS ZERO BEFORE
PROCEEDING. FAILURE TO
OBSERVE THIS PRECAUTION
MAY RESULT IN SEVERE
BODILY INJURY OR DEATH.
DANGER
THE BLOWER MOTOR IS TYPI-
CALLY WIRED TO THE AC
INPUT OF THE CONTROLLER
AND WILL BE ENERGIZED
EVEN WHEN THE CONTROL-
LER IS NOT RUNNING. TURN
OFF AND LOCKOUT OR TAG
MAIN POWER SUPPLY BE-
FORE TOUCHING BLOWER
COMPONENTS. FAILURE TO
OBSERVE THIS PRECAUTION
COULD RESULT IN SEVERE
BODILY INJURY OR LOSS OF
LIFE.

5
Procedure:
1. Connect for low or high voltage
as shown.
2. Check that the direction of air
flow is in agreement with the
“direction of air flow” arrows
mounted on the motor. If
directional flow is incorrect
interchange power leads to T1
and T2 or U1 and V1.
Grounding
The user is responsible for insuring
that the grounding method is in
accordance with the National
Electric Code and the applicable
local codes. The ground connection
should be a solid and permanent
metallic connection between the
ground point, the motor terminal
housing and the motor frame. A
ground lead or bolt is provided in
side the terminal box.
Due to the need to carry higher
frequency ground currents (from
switched voltage waveforms) the
ground connection/path must be low
impedance, not only low resistance.
Such ground currents exist during
normal operation on switched
(inverter) power.
Drive
RPM AC motors 56-L320 are sup
plied with a shaft suitable for a belt
or coupled drive.
Belt loads should be checked
against maximum allowable radial
loads under “Shaft Loads” section.
Contact Reliance Electric sales
office to deter mine L440 frame belt
load requirements.
Frames L360S and L400S are
suitable for coupled duty only; larger
shafts are supplied for belted duty.
Proper alignment is a key step for
long life of bearings, shafts and
belts, and minimum downtime.
Misalignment can cause excessive
vibration and damaging forces on
shaft and bearings. For direct
coupled drives, flexible couplings
facilitate alignment. For belt drives,
the sheave must be placed as close
as possible to the motor bracket.
Shipping Blocks
Motors supplied with roller bearings
at the drive end are shipped with
wooden blocking to prevent axial
movement of the shaft during
shipment. Remove the blocking and
bolts securing it and discard. Make
sure motor shafts turn freely. If motor
is to be reshipped, blocking of
bearing is required.
Encoder Connection
Diagrams
1. Dynapar H20 - 10 pin M/S con-
nector
2. Lakeshore - Epic connector or
pigtail cable
The following chart is a universal
wiring guide for the latching Epic
connector or a pigtail cable. Wires
that are not used should be left
floating and should never be con-
nected to power or common. For
optimum EMI noiseimmunity con-
nect the encoder shield (pin 10 or
the braid wire) to the cable shield.
The encoder shield is internally
isolated from the encoder frame.
The cable shield should still be
connectedtogroundatthereceiv-
ing end. This encoder has a line
driver output. A pull-up resistor is
not required.
PIGTAIL CABLE
Connect the color coded wires to
match the individual signal
requirements.
DANGER
CONNECT AN APPROPRIATE
EQUIPMENT GROUNDING CON-
DUCTOR TO THE CONTROLLER
AND TERMINAL, THE MOTOR
FRAME, THE TRANSFORMER
ENCLOSURE IF USED, THE
CONTROLLER ELECTRICAL EN-
CLOSURE AND AN
APPROPRIATE GROUNDING
ELECTRODE. FAILURE TO OB-
SERVE THESE PRECAUTIONS
COULD RESULT IN SEVERE
BODILY INJURY OR LOSS OF
LIFE.
WARNING
INCORRECT MOTOR ROTATION
MAY CAUSE PERSONAL
INJURY OR DAMAGE THE
EQUIPMENT. CHECK DIREC-
TION OF MOTOR ROTATION
BEFORE COUPLING MOTOR TO
LOAD.
WARNING
INSURE THAT ALL GUARDS
ARE PROPERLY INSTALLED
BEFORE PROCEEDING. EXER-
CISE EXTREME CARE TO AVOID
CONTACTING ROTATING
PARTS. FAILURE TO OBSERVE
THESE PRECAUTIONS COULD
RESULT IN BODILY INJURY.
PIN# SIGNAL COLOR
1 Common Black
2BGreen
3ABlue
4 Z Violet
5 No Connection -
65-15VRed
7 /B Yellow
8/AGray
9/ZOrange
10 Shield Braid

6
Motor Application Data
Maximum Safe Speed
The speeds given in Table I are the
maximum mechanically safe
operating speeds for frames with
standard construction. These
speeds must not be exceeded under
any condition. Motor control must
hold the maximum speed under any
load condition including no-load
within the maximum safe speed.
Drive systems whose de sign
characteristics inherently prevent the
AC motor from exceeding the Mo tor
Maximum Safe Operating Speed
must prevent the motor from
exceeding the Maximum Safe
Speed if a single component failure
should occur.
Table I - Maximum Safe Speed
With special construction maximum
safe speed may differ from the
above values. In all cases, the
maximum safe speed is indicated on
the motor name plate.
NOTE: Normal operating speeds
must be limited to those listed in
order to meet nameplate rating and
assure validity of warranty.
Minimum V-Belt Sheave
Diameters
Application of Pulleys, Sheaves,
Sprockets and Gears on Motor
Shafts
To avoid excessive bearing loads
and shaft stresses, belts should not
be tightened more than necessary to
transmit the rated torque. The pre-
tensioning of the V-belt drive should
be based on the total tightening
force required to transmit the
horsepower divided by the number
of belts. This procedure avoids the
excessive load caused by tightening
individual belts to a prescribed level
recommended by belt
manufacturers.
Mounting
In general, the closer pulleys,
sheaves, sprockets or gears are
mounted to the bearing on the motor
shaft, the less will be the load on the
bearing. This will give greater
assurance of trouble-free service.
The center point of the belt, or
system of V-belts, must not be
beyond the end of the motor shaft.
The inner edge of the sheave or
pulley rim should not be closer to the
bearing than the shoulder on the
shaft but should be as close to this
point as possible.
The outer edge of a chain sprocket
or gear must not extend beyond the
end of the standard motor shaft.
Shaft Extension and
Method of Drive
RPM AC frames 56-L320 are
supplied with a shaft and bearing
system suitable for either coupled or
belted drives. Belt loads should be
checked against maximum allowable
radial loads under “Shaft Loads”
section. Frames L360-L440 are
supplied with larger shafts and roller
bearings when belted drives are
specified.
Shaft Loads - Axial and
Radial
RPM AC motors are suitable for
limited shaft loads as shown in
Tables III and IV. Recommended
maximum thrust loads depend on
the mounting position, either
horizontal or vertical. For
recommendations for loads in
excess of those shown, refer to the
local Reliance Electric office. For
higher speeds and special shaft
extensions please refer to the local
Reliance Electric sales office.
ONLY QUALIFIED ELECTRI-
CAL PERSONNEL FAMILIAR
WITH THE CONSTRUCTION
AND OPERATION OF THIS
EQUIPMENT AND THE HAZ-
ARDS INVOLVED SHOULD
INSTALL, ADJUST, OPERATE,
AND/OR SERVICE THIS
EQUIPMENT. READ AND
UNDERSTAND THIS MANUAL
IN ITS ENTIRETY BEFORE
PROCEEDING. FAILURE TO
OBSERVE THIS PRECAUTION
COULD RESULT IN SEVERE
BODILY INJURY OR LOSS OF
LIFE.
WARNING
THE MACHINERY BUILDER
AND/OR USER ARE RESPON-
SIBLE FOR INSURING THAT
ALL DRIVE TRAIN MECHA-
NISMS, THE DRIVEN
MACHINE, AND PROCESS
MATERIAL ARE CAPABLE OF
SAFE OPERATION AT THE
MAXIMUM SPEED AT WHICH
THE MACHINE WILL OPER-
ATE. FAILURE TO OBSERVE
THESE PRECAUTIONS COULD
RESULT IN BODILY INJURY.
Frame Diameter Maximum Safe
Speed RPM
56, 140T, W180T 5400
L180 7200
L210 5000
L250 5000
L280 5000
L320 4000
L360 3750
L400 3750
L440 2700

7
Table III - Axial Thrust Capacity in Pounds/Kilograms - No Radial Load
(1) Thrust capacityfor vertical mounting includes a constant whose valueis plus or minus depending on the directionof thethrust load. Theconstant
is plus for thrust loads acting upward against the force of gravity and minus for loads acting downward with gravity.
Table IV - Radial Load Capacity* - No Axial Load
(1) Data for motors with roller bearings at the drive end (back end). Motors with ball bearings at the drive end are for coupled duty only.
*Contact Reliance Electric sales office to determine L440 frame belt load requirements.
Horizontal Mounting Vertical Mounting (1)
Frame 2500 rpm 1750 rpm 1150 rpm 850 rpm 2500 rpm 1750 rpm 1150 rpm 850 rpm
L180 pounds 430 500 600 675 430 + 60 500 + 60 600 + 60 675 + 62
kilograms 195 227 272 306 198 + 27 227 + 27 272 + 27 306 + 27
L210 pounds 477 551 662 742 498 + 61 564 + 61 676 + 61 756 + 61
kilograms 217 251 301 338 227 + 28 257 + 28 308 + 28 344 + 28
L250 pounds 509 600 722 828 541 + 86 629 + 86 755 + 86 865 + 86
kilograms 231 272 327 376 245 + 39 285 + 39 342 + 39 392 + 39
L280 pounds 590 700 850 975 644 + 122 754 + 122 905 + 122 1038 + 122
kilograms 268 318 386 442 292 + 56 342 + 56 411 + 56 471 + 56
L320 pounds 705 835 1020 1170 770 + 175 905 + 175 1095 + 175 1250 + 175
kilograms 320 379 463 531 349 + 80 411 + 80 497 + 80 567 + 80
L360 pounds 875 1075 1350 1525 830 + 293 1020 + 293 1300 + 293 1475 + 293
kilograms 397 488 612 692 376 + 133 463 + 133 590 + 133 669 + 133
L400 pounds 1350 1630 2000 2250 1470 + 352 1820 + 352 2210 + 352 2475 + 352
kilograms 612 740 908 1021 667 + 160 826 + 160 1003 + 160 1123 + 160
L440 pounds 1300 1550 1800 2050 1365 + 1085 1600 + 1085 1865 + 1085 2080 + 1085
kilograms 590 703 816 930 619 + 492 726 + 492 846 + 492 943 + 492
Caution: The use of these radial load capacities requires the accurate calculation of the radial load for the application.
Radial loads for gears, sprockets, and flywheel are usually accurately determined but the radial loads due to V-belt
drives are subject to miscalculations because they do not include all of the pre-tension load (belt tightening). The
calculations of the radial load for a V-belt drive must include the pre-tension for transmitting the horsepower,
pretension for centrifugal force on the belts, pre-tension for high start torques, rapid acceleration or deceleration, pre-
tension for drives with short act-of-contact between the V-belt and sheave, and low coefficient of friction between belt
and sheave caused by moisture, oil or dust. Failure to observe these precautions could result in damage to or
destruction of the equipment.
Frame
Radial Load Capacities
at the End of the Shaft in Lbs.
2500 rpm 1750 rpm 1150 rpm 850 rpm
56, 140T, W180T 85 85 85 85
L180 445 445 445 445
L210 875 875 875 875
L250 1375 1525 1525 1525
L280 1550 1755 1755 1755
L320 1685 1800 1800 1800
UL360(1) 2550 2875 3300 3310
UL400(1) 3625 4090 4700 5190

8
Operation
Motor Start-Up
In addition to observing the above
pre cautions, the following items
must be checked before starting.
• Stop and remove power from the
motor per the Controller
Instruction Manual directions.
• Verify the DC bus voltage is zero
per the Controller Instruction
Manual.
1. The interior of the motor should
be clean and dry.
2. Connections should be tight.
3. The driven machine should be un
loaded if possible.
NOTE: Machines designed for
cooling by a separate source of
forced ventilation must not be
operated without the air supply. Be
sure blower is running in proper
direction.
While operating the motor, observe
the performance. It should run
smoothly with little noise. The
bearings should not overheat and
should reach a leveling off
temperature. Any undue noise,
overheating, or erratic performance
should be investigated and
necessary corrective action taken
immediately to prevent serious dam
age. Before attempting any repairs,
please contact the local Reliance
Electric Sales/Service office.
All RPM AC motors are lubricated be
fore shipment and will operate for a
long period before regreasing is
required. The period will vary
depending on environmental and
service conditions. Refer to
Maintenance Section.
Balance
Motors are dynamically balanced to
commercial limits unless ordered
differently. Balance is done with a full
length 1/2height shaft key. A full
shaft key is shipped with motor.
Sheave or coupling should be
balanced with a 1/2height shaft key.
Std. Dynamic Balance Limits
DANGER
ONLY QUALIFIED ELECTRICAL
PERSONNEL FAMILIAR WITH
THE CONSTRUCTION AND
OPERATION OF THIS EQUIP-
MENT AND THE HAZARDS
INVOLVED SHOULD INSTALL,
ADJUST, OPERATE, AND/OR
SERVICE THIS EQUIPMENT.
READ AND UNDERSTAND THIS
MANUAL IN ITS ENTIRETY
BEFORE PROCEEDING. FAIL-
URE TO OBSERVE THIS PRE-
CAUTION COULD RESULT IN
SEVERE BODILY INJURY OR
LOSS OF LIFE.
WARNING
BEFORE INITIAL START-UP
OBSERVE THE FOLLOWING
PRECAUTIONS.
1. REMOVE ALL UNUSED SHAFT
KEYS AND LOOSE ROTATING
PARTS TO PREVENT THEM
FROM FLYING OFF. REPLACE
COVERS AND PROTECTIVE
DEVICES.
2. WHEN THE RPM AC MOTOR IS
SUPPLIED AS PART OF DRIVE
SYSTEM, REFER TO THE
DRIVE SYSTEM INSTRUC-
TION MANUAL FOR OPERAT-
ING INSTRUCTIONS.
TACHOMETER FEEDBACK
MUST BE PROPERLY CON-
NECTED FOR CLOSED LOOP
OPERATION. REVERSE
POLARITIES OR BROKEN
CONNECTIONS CAN CAUSE
DANGEROUSOVERSPEEDS.
FAILURE TO OBSERVE THESE
PRECAUTIONS COULD RESULT
IN BODILY INJURY.
DANGER
THE EQUIPMENT IS AT LINE
VOLTAGE WHEN AC POWER IS
CONNECTED. DISCONNECT
AND LOCKOUT ALL
UNGROUNDED CONDUCTORS
OF THE AC POWER LINE. FAIL-
URE TO OBSERVE THESE PRE-
CAUTIONS COULD RESULT IN
SEVERE BODILY INJURY OR
LOSS OF LIFE.
DANGER
THE CONTROLLER MAY APPLY
HAZARDOUS VOLTAGES TO
THE MOTOR LEADS AFTER
POWER TO THE CONTROLLER
HAS BEEN TURNED OFF. VER-
IFY THAT THE CONTROLLER IS
INCAPABLE OF DELIVERING
HAZARDOUS VOLTAGES AND
THAT THE VOLTAGE AT THE
MOTOR LEADS IS ZERO
BEFORE PROCEEDING. FAIL-
URE TO OBSERVE THIS PRE-
CAUTION COULD RESULT IN
SEVERE BODILY INJURY OR
LOSS OF LIFE.
WARNING
SURFACE TEMPERATURE OF
MOTOR ENCLOSURE MAY
REACH TEMPERATURES
WHICH CAN CUASE DISCOM-
FORT OR INJURY TO PERSON-
NEL COMING INTO CONTACT
WITH HOT SURFACES. THE
USER MUST APPLY APPROPRI-
ATE GUARDS AND/OR SHIELDS
TO PROTECT AGAINST ACCI-
DENTAL CONTACT WITH
MOTOR SURFACE. FAILURE TO
OBSERVE THIS PRECAUTION
MAY RESULT IN BODILY INJURY.
Highest Rated
Speed, rpm Max. Amplitude in
Inches
3.000 - 4,000
1,500 - 2,999
1,000 - 1,499
Up to 999
0.0010
0.0015
0.0020
0.0025

9
Maintenance
(1) Motors must be specially designed for operation in ambient outside the range of -25
R
C to 40
R
C (-13
R
F to 104
R
F.). Special grease is required.
(2) "EXTREME” service conditions are rare in actual practice. Corresponding lubrication cycles should therefore be applied with caution. In addition,
it is advisable to check with Reliance Electric (Cleveland Service Department) for related special instructions.
DANGER
ONLY QUALIFIED ELECTRI-
CAL PERSONNEL FAMILIAR
WITH THE CONSTRUCTION
AND OPERATION OF THIS
EQUIPMENT AND THE HAZ-
ARDS INVOLVED SHOULD
INSTALL, ADJUST, OPERATE,
AND/OR SERVICE THIS
EQUIPMENT. READ AND
UNDERSTAND THIS MANUAL
IN ITS ENTIRETY BEFORE
PROCEEDING. FAILURE TO
OBSERVE THIS PRECAUTION
COULD RESULT IN SEVERE
BODILY INJURY OR LOSS OF
LIFE.
DANGER
INTERNAL PARTS OF THIS
MOTOR MAY BE AT LINE
POTENTIAL EVEN WHEN IT IS
NOT ROTATING. BEFORE
PERFORMING ANY MAINTE-
NANCE WHICH COULD
RESULT IN CONTACTING ANY
INTERNAL PART, BE SURE TO
DISCONNECT ALL POWER
FROM THE MOTOR. FAILURE
TO OBSERVE THIS PRECAU-
TION COULD RESULT IN
SEVERE BODILY INJURY OR
LOSS OF LIFE.
WARNING
SURFACE OF MOTOR ENCLO-
SURE MAY REACH HIGH TEM-
PERATURES. AVOID COMING
INTO CONTACT WITH MOTOR
SURFACES AND WEAR SUIT-
ABLE PROTECTIVE EQUIP-
MENT.
Table V
Amount of grease to be added to RPM AC motors. See Table VIII for relubrication interval. Use Chevron SRI-2 or
equivalent grease unless motor nameplate specifies special grease.
Frame Size
Coupled Duty / Belted or Tandem Duty
Volume Weight
Cubic
Inches Cubic
Centimeter Ounces Grams
L180 - L280 1.0 16 .5 14
L320 - L400 2.0 32 1.0 28
L440 3.0 48 1.5 42
NOTE: 56, 140T and W180T have permanently lubricated ball bearings.
Table VI - Service Condition
Determine service condition on the basis of the most severe operating parameter; that is
temperature, bearing load, atmosphere, or operating hours per day.
Service Condition Ambient Temperature Bearing Load Atmosphere Operating Hrs. Per Day
Standard -18
R
C to 40
R
C
(0
B
F to 104
B
F) Steady Clean 8
Severe -30
R
C to 50
R
C
(-22
R
F to 122
R
F) (1)
Medium Shock, Vibration
(less than .2 in/sec.) Medium Dirt, Abrasives,
Corrosion 8 to 24
Extreme (2) -54
R
C to 65
R
C
(-65
R
F to 149
R
F) (1)
Heavy Shock, Vibration
(more than .44 in/sec) Heavy Dirt, Abrasives,
Corrosion 8 to 24

10
(1) Maximum speed occupying more than 30%of operating time.
(2) For Tandem drives increase frequency of lubrication by multiplying values by .8.
Lubrication - Frames
L180 - L440
RPM AC machines are designed
with the exclusive Reliance Electric
Positive Lubrication System PLS
5
which routes new grease directly
into the bearing. The relubrication
periods shown in Table VII are
offered as a guide for varying
service conditions, speeds, bearing
types and operating hours.
NOTE: Certain special motors may
have a lubrication instruction plate
permanently attached. These
specific lubricating instruction must
be followed.
Lubrication Procedure
1. Relubrication with the shaft sta-
tionary and a warm motor is rec-
ommended. Iflubrication must be
done with motor running, stay
clear of rotating parts and electri-
cal circuits.
2. Locate the grease inlet at the top
of the bearing hub, clean the
area and replace the 1/8-inch
pipe plug with a grease fitting if
the motor is not equipped with
grease fitting.
3. Remove grease drain plug
located opposite the grease inlet.
4. Using a manual grease gun,
pump in the recommended
g
rease in the amount shown in
Table V. This amount of grease
will provide an ample supply of
lubricant between lubrication
periods as determinedfrom Table
VII for the service condition listed
in Table VI.
Use Chevron SRI-2 grease or
equivalent unless motor name
plate specifies special grease.
Use only clean, fresh grease from
cleancontainersandhandlesoas
to keep it clean.
In general, mixing of greases is
notrecommended.Ifanincompat-
ible grease is used, the lube sys-
tem must be repacked completely
with the new grease.
5. Wipe away any excess grease at
the grease drain or relief and re
place drain plugs.
Repacking Bearings or
Greasing New Bearings
When existing bearings have been
completely cleaned of old grease or
when bearings are replaced, use this
procedure for packing the bearing.
1. Apply one bead of grease all
around inboard side of bearing
between bearing and inner cap
Table VII - Relubrication Periods For RPM AC Motors - Frames L180 - L440
Refer to Table VII for definition of service conditions.
Maximum Normal
Operating Speed rpm (1) Frame
Relubrication Interval in Months (2)
Standard Service Severe Service Extreme Service
3450 and higher All 9 4 1
2400 thru 3449 L180 thru L250
L280 thru L440 24
9 9
33
1
1700 thru 2399 L180 thru L320
L360 thru L440
UL360 thru UL440
36
18
9
12
6
3
3
2
1
800 thru 1699 L180 thru L320
L360 thru L440
UL360 thru UL440
36
36
9
24
12
6
8
3
1
500 thru 799 L180 thru L320
L360 thru L440
UL360 thru UL440
48
36
18
36
24
12
12
8
4
499 and lower L180 thru L440
UL360 thru UL440 48
24 36
18 12
6
WARNING
IF RELUBRICATION IS DONE
WHILE MOTOR IS RUNNING,
STAY CLEAR OF ROTATING
PARTS. FAILURE TO
OBSERVE THIS PRECAUTION
COULD RESULT IN BODILY
INJURY.

11
making sure that grease adheres
to balls or rollers.
2. Apply one bead of grease all
around outboard side of bearing,
making sure grease adheres to
balls or rollers.
3. Completely fill grease inlet and
out let passage holes with
grease.
4. Fill outboard bearing cavity 60%
to 90% full of grease.
5. If possible, rotate shaft of
assembled machine at least
three revolutions by hand to
distribute grease within bearings
before starting motor.
Bearings
RPM AC Bearing Housing Designs
provide protection to windings and
interior of machine by minimum
grease leakage. They also provide
good protection against external
contamination.
Various types of anti-friction
bearings are used in the wide range
of RPM AC frames as needed to
meet specific load, speed and
service requirements.
Most commonly used bearings are:
1. Single row, open ball bearings for
coupled and belted duty for
frames L180 thru L320.
2. Single row, open ball bearings for
coupled duty forframes L360 and
L400.
3. Cylindrical roller bearings atdrive
end for belted duty on frames
UL360 and UL400.
Frequent bearing checks are
recommended. If temperatures
become excessive, investigate
immediately for the cause. Total
bearing temperatures should not
exceed 90
R
C (194
R
F). Causes for
high bearing temperature are:
1. Contaminated grease.
2. Insufficient grease or excessive
amount.
3. Incorrect grease.
4. Excessive load or thrust due to
misalignment or motor overload.
5. Loose bearings.
6. Bearing failure.
7. Excessive ambient temperature.
Replacement bearings should be
ordered from Reliance Electric in
order to obtain the same carefully
selected bearing as the original.
RPM AC bearings should never be
exposed by disassembly of the
motor unless absolutely necessary
for inspection or re placement of the
bearing or maintenance in other
parts of the machine. Protect good
bearings from dirt and contamination
at all times. Most bearing failures are
caused by dirt.
The open ball bearings for the
RPMAC motors frames L180 thru
L320 are the same regardless of
whether application is coupled or
belted. Belted duty for frames UL360
and UL440 re quires the use of roller
bearings. Coupled duty uses ball
bearings.
Lubrication - Frames 56,
140T and W180T
The ball bearings are deep grooved,
double shielded bearings with
sufficient lubricant packed into the
bearings by the manufacturer for
"life Lubrication". The initial lubricant
is supplemented by a supply packed
into larger reservoirs in the end
shield at time of assembly. No
grease fittings are provided as the
initial lubrication is adequate for up
to 10 years of operation under
normal conditions.

12
Disassembly And Reassembly Instructions
Axial Float
RPM AC motors have a wave spring
washer between the drive end
bracket and bearing. The opposite
drive end bearing is positioned
axially by a float restricting inner
cap. Axial float (including bearing
internal clearance) should be within
the limits listed on the chart below.
The 56, 140T, W180T and L440
frame wavy spring is located on the
opposite drive end.
Anti-Friction Bearing
Assemblies
The bearings are positioned and
secured in a machined cavity in the
end brackets. Open type ball
bearings are used for direct coupled
and belt drive applications for frames
L180 thru L320 (employ ball
bearings at both ends) and are
protected by inner caps at both
ends.
Frames UL360, UL400 and UL440
employ a cylindrical roller bearing on
the drive end for belt drives, and a
ball bearing for coupled service.
56, 140T and W180T have double
shielded bearings.
Bearing Replacement
Remove bearing by means of
bearing puller. Clean bearing
housing and bearing seat prior to
assembly of bearing. Place new
bearing in a bake oven for 1/2hour
@ 250
R
F. Place bearing onto shaft
and push home to bearing shoulder
and hold it in place for a minimum of
30 seconds.
After bearing has cooled down for
about 1 minute add 1/2cu. in. of
fresh grease into back of bearing.
Once mo tor becomes assembled
grease per instructions found herein.
Bracket Re-Assembly
To obtain proper planity between the
integral mounting feet on the front
and back end brackets of L210-
L440, a smooth level surface should
be used to align the brackets when
they are assembled to the frame.
Check for proper shaft alignment
after reinstalling the motor.
Stub Shaft Removal Procedure - L180-L440
Drive-in Stub Shaft
1. Turn off and lockout power to the
motor.
2. Remove in-line blower motor and
cover assembly by removing the
Hex head cap screws on cover
(if enclosure is TEAO-Blower
cooled).
3. After removal of blower
assembly, obtain the stub shaft
puller back plate (available from
Reliance Renewal Parts), and
assemble over the stub shaft
against the end of the motor
shaft.
4. Obtain the stub shaft puller plate
(available from Reliance
Renewal Parts) and assemble
over the stub shaft, and up
against thepullerbackplate. Note
7/16 set screws must be backed
out enough to clear the stub shaft
O.D., and 1/2" jack screws
should be backed out to allow
puller plate to fit up flush against
the backplate.
5. Screw the 7/16" set screws in on
each side of the puller plate until
they contact the stub shaft. Keep
the stub shaft reasonably
centered between the jack
screws. Tighten screws securely.
6. Using a 3/8" allen wrench, turn
the jack screws, in equal
amounts, in a clockwise manner
to remove the stub shaft. If the
set screws slip, re tighten and
repeat process.
7. Replace blower motor and cover
assembly (if TEAO - blower
cooled) withthe correct extended
blower cover, using the hex head
cap screws previously removed.
Screw-in Stub Shaft
1. Turn off and lockout power to the
motor.
2. Remove in-line blower motor and
cover assembly by removing the
Hex head cap screws on cover
(if enclosure is TEAO-Blower
cooled).
3. After removal of blower
assembly, motor shaft will need
to be locked from turning. The
use of a spanner wrench on
motor drive shaft or al ternate
means can be used. Place an
open-end wrench on stub shaft
flats and turn counter clockwise
(right-hand) threads).
4. Replace blower motor and cover
assembly (if TEAO - blower
cooled) withthe correct extended
blower cover, using the hex head
cap screws previously removed.
NOTE: 56, 140T and W180T have
permanent stub shaft which is part of
main motor shaft.
Axial Float - In./Min.
Maximum Minimum
Frame
Size In. mm. In. mm.
L180 thru
L440 .051 1.29 .013 .33

13
Replacement Bearings / Spare Parts
Your maintenance program will not
be complete without including spare
bearings. It must be remembered
that the bearing is a wearable
component and therefore must
eventually be re placed. To insure
that you are able to maintain original
operation, we recommend the
purchase of spares directl
y
from
Reliance Electric.
All bearings used in Reliance motors
are subject to exact specifications
and tests necessary to satisfy
performance requirements. In this
manner, it is possible to duplicate
your present bearing. Markings on
the bearing do not indicate complete
specifications.
A detailed parts list, which gives
Reliance Electric recommendations
for spare parts that should be
stocked for your equipment, can be
ordered from the:
1. Nearest Reliance Electric Sales
Office
2. Nearest Reliance Electric
Distributor
3. Reliance Electric Renewal Parts,
Cleveland, Ohio
Be sure to include complete
nameplate data - serial number,
model number, rating, etc. - for your
equipment when ordering the spare
parts list.
Detailed information on renewal
parts including recommendations on
spare parts for various numbers of
motors in operation is contained in
NEMA Standards Publication No.
RP1-1981 Renewal Parts for Motors
and Generators (Performance,
Selection and Maintenance). Copies
are available from NEMA, 2101 L
Street, N.W., Washington, D.C.
20037.
Additional Literature
Additional literature covering AC
machines can be obtained from the
Reliance Service Department upon
request through your nearest
Reliance Electric Sales Office.

14
Parts Identification Drawing
(Totally Enclosed Blower Cooled)
(Typical L210-L320Frame)
*Blower cover and grill may be one-piece design
ITEM
NO. PART DESCRIPTION ITEM
NO. PART DESCRIPTION
1 FRAME/STATOR 13 GRILL, BLOWER*
2 ROTOR 14 EYEBOLT
3 BRACKET, B.E. 15 CONDUIT BOX, MAIN MOTOR
4 BRACKET, F.E. 16 GREASE FITTING, B.E.
5 SHAFT 17 GREASE FITTING, F.E.
6 BALL BEARING, B.E. 18 KEY, SHAFT EXTENSION
7 INNER CAP, B.E. 19 FEEDBACK DEVICE (WHEN SUPPLIED)
8 BALL BEARING, F.E. 20 CONNECTOR, FEEDBACK DEVICE
9 INNER CAP, F.E. 21 COUPLING, FEEDBACK DEVICE
10 WAVE WASHER, B.E. 22 MOUNTING ADAPTER, FEEDBACK DEVICE
11 BLOWER MOTOR 23 BLOWER MOTOR CONDUIT BOX
12 COVER, BLOWER*

15
Reliance Electric Total Service Capabilities
No matter where you’re located, or
what time of day or night it is,
Reliance Electric is ready to assist
you. With Field Service Engineers,
Repair Centers, Parts Centers, and
Electronic Re pair Facilities.
Our total service capabilities include
motor and equipment repair,
electronic control repair, genuine
Reliance re placement parts, field
services, preventive maintenance,
and customer maintenance training.
All to protect you against
unscheduled downtime. And to
protect your equipment investment.
Field Services
Reliance Electric provides a wide
range of technical services to help
improve you productivity,
complement your maintenance
efforts, and reduce you upkeep
costs. Our Technical Service
Agreements give you prescheduled
services that pinpoint potential
problems BEFORE they become
downtime problems. Field Services
include:
• Technical Service Agreements
• Start-Up Service
• Breakdown Service
• Customer Maintenance
Programs
• Maintenance PLUS
• Resident Service
• 724 Service (7-day, 24-hour over
the-phone assistance)
• Equipment Upgrades
Renewal Parts
Reliance Electric’s nationwide
Partservice™ network features local
stocking Reliance Parts Centers and
Key Parts Distributors to assure that
you get the spare parts you need
when you need them. The
Partservice network includes:
• National Parts Warehouse
• Local Key Parts Distributors
• Local Parts Centers
• 24-Hour Emergency Breakdown
Service
• Parts Audits
• Part Kits
For emergency spare parts, after
working hours, weekends and
holidays, call (216) 861-6434.
For more information or normal
parts service, call your local Key
Parts Distributor.
Motor and Equipment
Repair Services
Reliance Electric Service Centers
are fully equipped to repair or rebuild
your Reliance®, Dodge®, Master®,
Reeves®, and Kato® products, as
well as similar products from other
manufacturers. Our services include:
• AC & DC Rotating Equipment
Repair
• ATO Generator Repair
• Coil Manufacturing
• Mechanical Equipment Repair
• Compressor Repair
• Marine Motor & Generator Repair
• Approved NAVSCA Repair
• Core Loss Testing
• Traction Motion Repair
• Electric Wheel Drive Repair
• Servo Motor Repair &
Remagnetizing
• Nuclear Motor Repair
• Lifting Magnet Repair
• Tocco® High-Frequency
Alternator Repair
• Enduraseal® Insulation
• VPI (Vacuum Pressure
Impregnation) Insulation
• Bearing Rebabbitting
• Metalizing
• Welding, Fabricating and
• Machining
• Computerized Dynamic
Balancing
• Dynamometer Load Testing
• Diagnostic & Efficiency Testing
• On-Site Repair Service
• 24-Hour Emergency Service
• Recertification Repair
R

16
Regional Service Centers
United States
ALABAMA
Birmingham
205/841-8377
FAX:205/841-8035
ARIZONA
Phoenix
602/243-1791
FAX:602/243-3267
CALIFORNIA
Anaheim
714/772-4773
FAX: 714/778-4621
San Jose408/287-4060
FAX: 408/275-6291
COLORADO
Denver
303/935-4615
FAX: 303/935-0129
ILLINOIS
Thornton
312/821-0050 (Chicago)
708/877-5310 (Suburban)
219/883-3100 (Indiana)
FAX: 708/877-6516
LOUISIANA
Monroe
318/322-1474
FAX: 318/322-4572
Shreveport
318/222-9431
FAX: 318/424-1702
NORTH CAROLINA
Burlington
919/228-7060
FAX: 919/227-4334
OHIO
Cleveland
216/266-7274
FAX: 216/266-6475
Cincinnati
513/863-8816
FAX: 513/863-7679
Columbus
614/548-5733
FAX: 614/890-4970
OREGON
Portland
503/226-4951
FAX:503/273-8874
PENNSYLVANIA
Philadelphia
215/365-1500
FAX: 215/365-1530
Washington
412/225-2900
FAX: 412/225-4309
SOUTH CAROLINA
Rock Hill
803/324-3700
FAX: 803/324-0434
TEXAS
LaPorte
713/471-4611
FAX: 713/471-3120
WYOMING
Gillette
307/682-0035
FAX: 307/682-0049
Rock Springs
307/362-6697
FAX: 307/382-2618
MEXICO
Mexico City
(5) 822-4999
FAX: (5) 822-9744

Printed in U.S.A. B-3682-3
Rockwell Automation - Dodge / Reliance 6040 Ponders Court Greenville, SC 29615 USA Tel: (864) 297-4800 / http://www.reliance.com
Table of contents
Popular Engine manuals by other brands
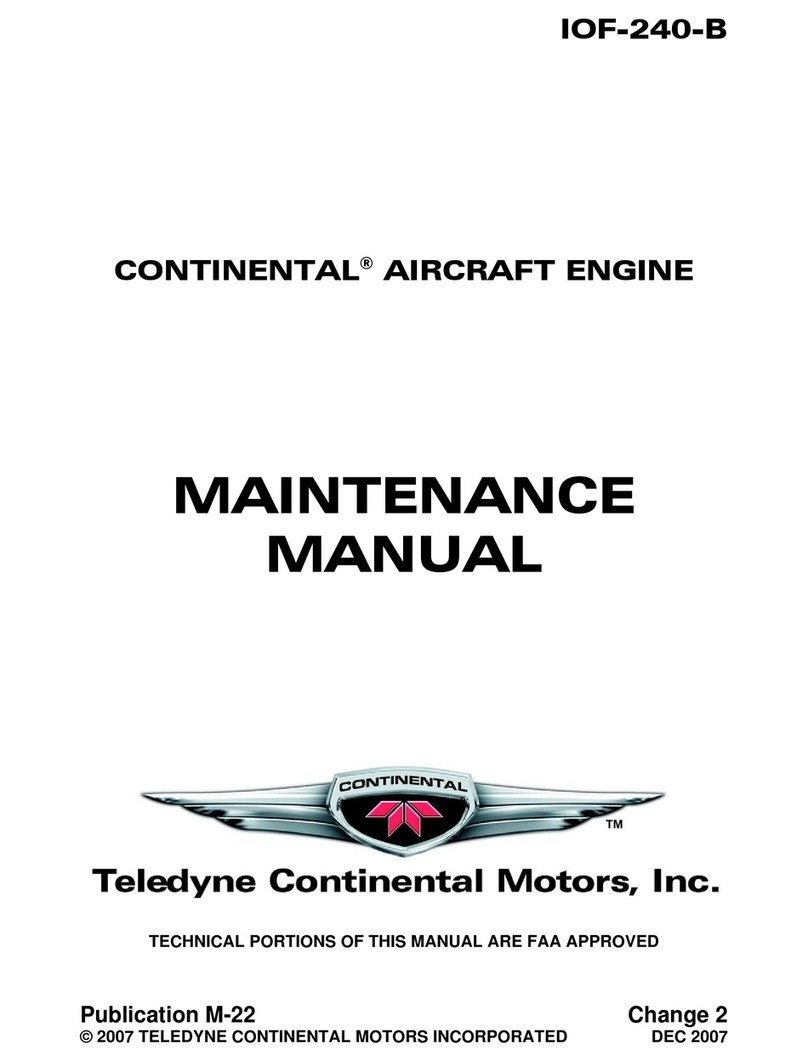
Continental Refrigerator
Continental Refrigerator IOF-240-B Maintenance manual
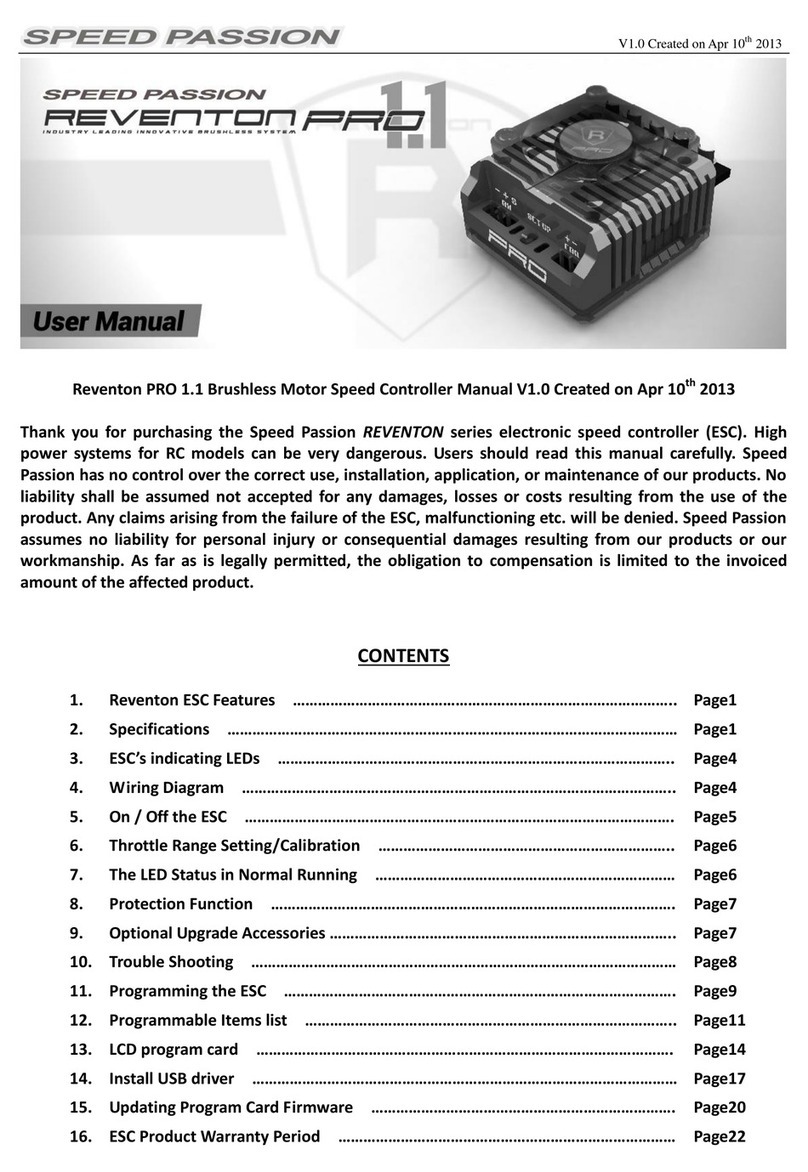
Speed Passion
Speed Passion Reventon Series user manual
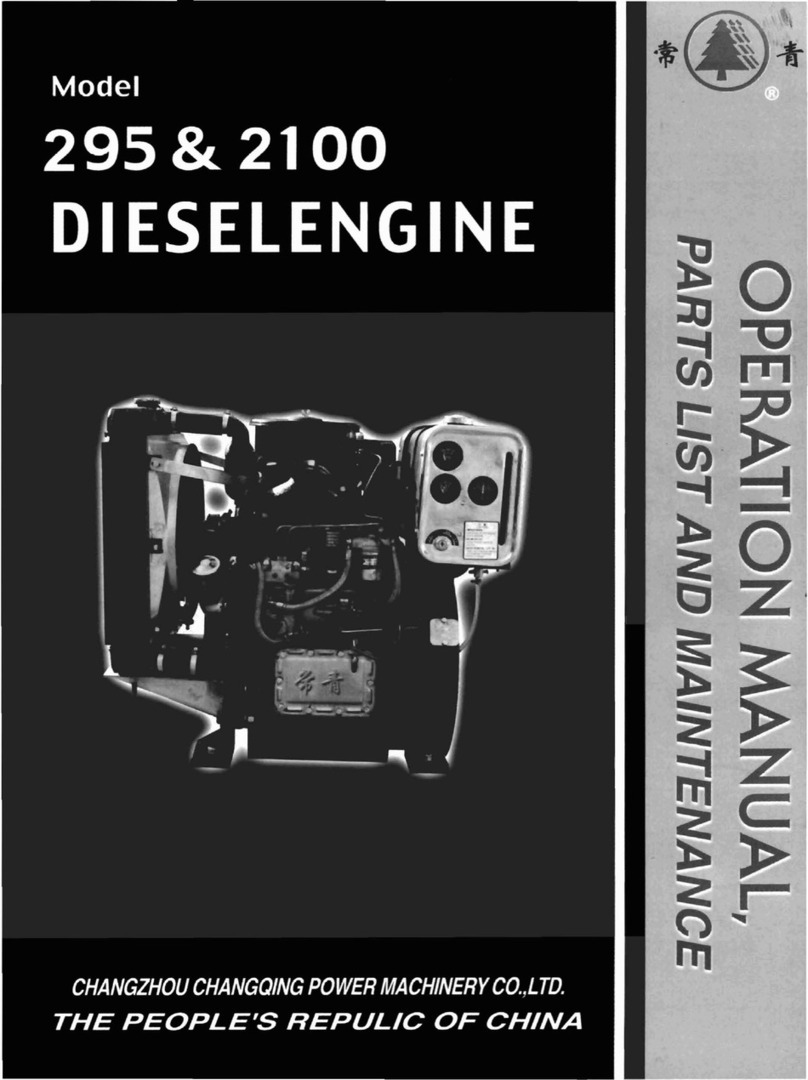
Rotek
Rotek 295 Operation manual
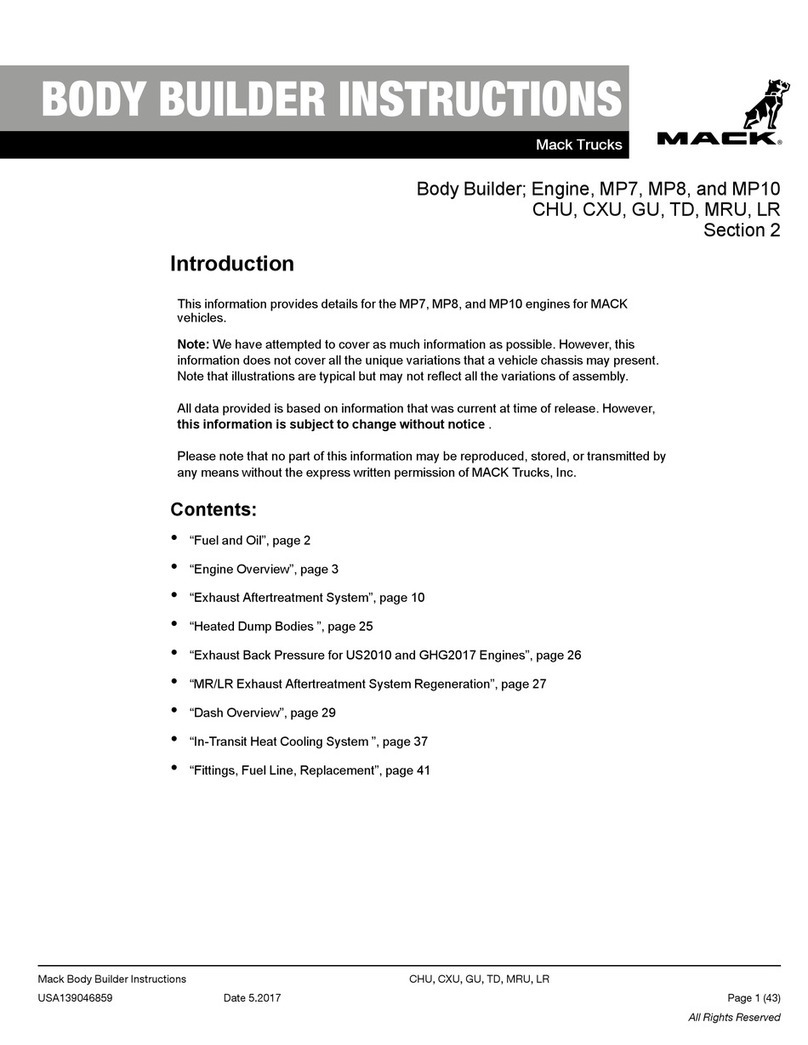
Mack
Mack MP8 Body builder instructions
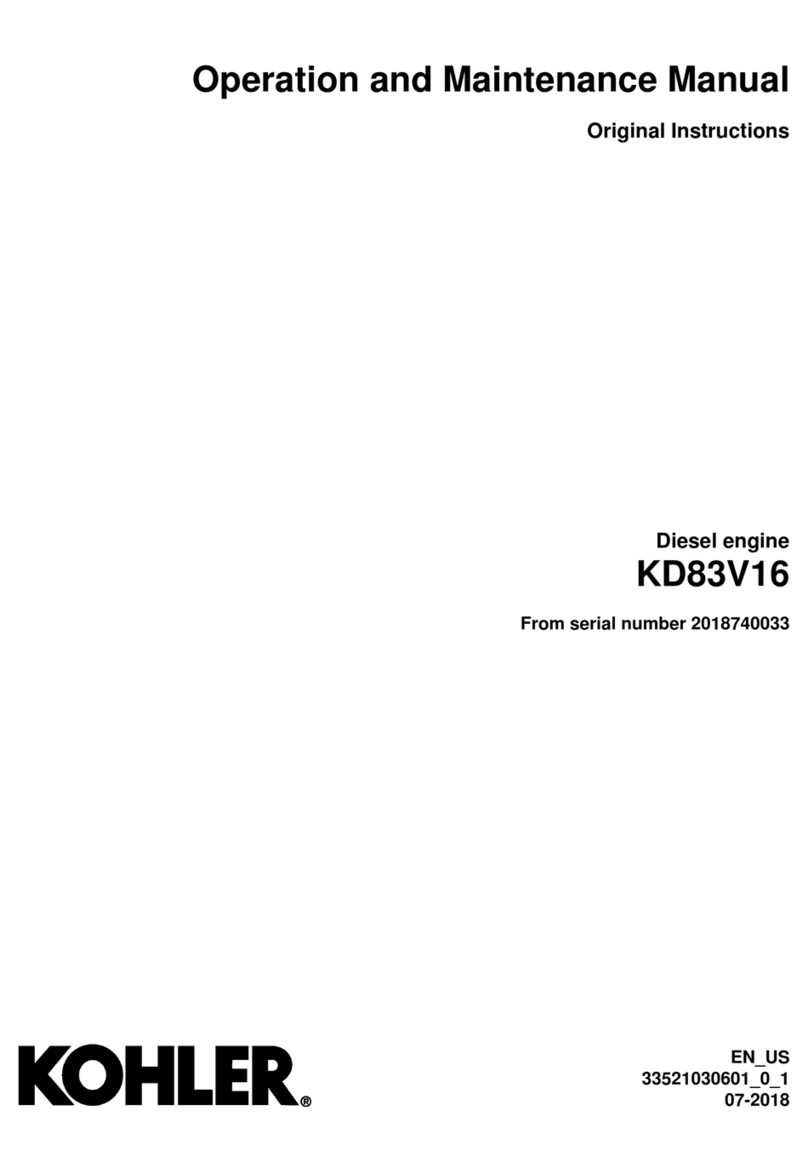
Kohler
Kohler KD83V16 Operation and maintenance manual

Volvo Penta
Volvo Penta V8-380 Operator's manual