SCHABMULLER TSA Series Manual

Version 1.0
Operating and maintenance instructions
(translation of original instructions)
Motor, pump unit, motor unit, servo unit

Operating and maintenance instructions
Imprint
Version 1.0 Page 2 of 56
Imprint
Schabmüller GmbH
Industriestraße 8
92334 Berching
Germany
Tel.: +49 8462 204-0
Fax: +49 8462 1841
E-mail: info@schabmueller.de
Homepage: www.schabmueller.de
© Schabmüller GmbH 2019
Distribution as well as duplication of the instructions, use and communication of the
contents are forbidden. Violation will result in claims for damages. All rights reserved
in the event of patent or utility model registration.
Technical changes
We reserve the right to make technical changes in production, processing and
appearance of all editions.
Record of changes
Version
Date
Changes
1.0
22/03/2019
New creation

Operating and maintenance instructions
Table of contents
Version 1.0 Page 3 of 56
Table of contents
1General information............................................................................................................................ 5
1.1 About these operating instructions ...................................................................................... 5
1.2 Further product documentation ........................................................................................... 5
1.3 Motor type-dependent descriptions..................................................................................... 6
1.4 Rating plates........................................................................................................................ 7
1.5 Options and attachments..................................................................................................... 9
1.6 Variant examples............................................................................................................... 10
2Safety ............................................................................................................................................... 12
2.1 General safety instructions................................................................................................ 12
2.2 Safety instructions in these operating instructions ............................................................ 12
3Transport and storage...................................................................................................................... 14
3.1 Transport ........................................................................................................................... 14
3.2 Incoming inspection........................................................................................................... 14
3.3 Storage.............................................................................................................................. 15
4Installing the motor........................................................................................................................... 17
4.1 Tightening torques for fastening elements ........................................................................ 17
4.2 Mounting the shaft sealing rings........................................................................................ 18
4.3 Installing O-rings................................................................................................................ 21
4.4 Installing shafts with gearing ............................................................................................. 21
4.5 Installing a motor without A-bearing plate......................................................................... 23
5Electrical connection ........................................................................................................................ 24
5.1 Overview............................................................................................................................ 24
5.2 Asynchronous motor, synchronous motor, reluctance motor............................................ 24
5.3 DC motor ........................................................................................................................... 28
6Installing optional attachments......................................................................................................... 30
6.1 Incremental encoder.......................................................................................................... 30
6.2 Tachometer........................................................................................................................ 33
6.3 Electromagnetic brake....................................................................................................... 34
6.4 Pump ................................................................................................................................. 38
6.5 Gearing.............................................................................................................................. 39
7Commissioning................................................................................................................................. 44
7.1 Preparation........................................................................................................................ 44
7.2 Checklist............................................................................................................................ 44
7.3 Initial start .......................................................................................................................... 45
8Maintenance..................................................................................................................................... 46
8.1 Safety instructions ............................................................................................................. 46
8.2 Regular inspection............................................................................................................. 46
8.3 Maintenance schedule....................................................................................................... 48
8.4 Inspection .......................................................................................................................... 49

Operating and maintenance instructions
Table of contents
Version 1.0 Page 4 of 56
9Troubleshooting................................................................................................................................ 50
10 Customer Service and Support........................................................................................................ 52
11 Disposal............................................................................................................................................ 53
11.1 Cleaning agents, auxiliary materials and operating materials........................................... 53
11.2 Scrapping........................................................................................................................... 53
11.3 Electrical and electronic components................................................................................ 53
12 Standards......................................................................................................................................... 54

Operating and maintenance instructions
General information
Version 1.0 Page 5 of 56
1 General information
1.1 About these operating instructions
The information in these operating and maintenance instructions (hereinafter:
operating instructions) has been compiled with great care to ensure that it
corresponds to the specifications and use of the motor. These operating instructions
for Schabmüller GmbH motors are intended to assist persons entrusted with the
corresponding tasks in correctly installing, operating and maintaining this electrical
machine.
All instructions and standards given in these operating instructions must be strictly
observed for reasons of personal and material safety when transporting, assembling,
commissioning, servicing or repairing Schabmüller GmbH motors.
The warranty of the products depends on the observance of the operating instructions
and the safety instructions.
If these operating instructions are lost, the electronic file is available in PDF format on
the website www.schabmueller.de.
A new printed version can also be requested.
If you have any questions, please contact Schabmüller GmbH.
1.2 Further product documentation
These operating instructions refer only to standard motors.
More detailed instructions can be found in the documentation specially prepared for
your motor, motor unit or power unit.
If additional information on motors with special designs is required, please contact
Schabmüller GmbH.
If specific or extended documents, such as the product documentation, are available,
these must be read and taken into account together with these operating instructions
prior to installation, operation and maintenance of the motor.
Those responsible for the safety of the installation and/or the vehicle must ensure that
the operating instructions and other documents supplied with the product
documentation are always available for all relevant work and must oblige their
employees to observe these documents consistently.
Particular attention must be paid to the following:
The technical data and information on the permissible use (assembly, connection,
ambient and operating conditions) contained in the order documents and other
product documentation, among other things
Local plant- or vehicle-specific regulations
The proper use of tools, lifting and transport equipment

Operating and maintenance instructions
General information
Version 1.0 Page 6 of 56
1.3 Motor type-dependent descriptions
These operating instructions apply to all Schabmüller GmbH standard motors.
Note: Electrical connections, attachments, maintenance measures, etc. may differ
depending on the type of drive or motor. An overview can be found on page 9.
To better understand these operating instructions, please first identify your motor type
using the information on the rating plate (see page 7and page 8).
The motor type is indicated by the following code:
Item
Designation
Comment
1
Motor type
TSA = asynchronous motor
TSL = DC motor
TSS = synchronous motor
TSR = synchronous reluctance
motor
2
Size
Stator diameter/TSL housing
diameter
3
Iron length
Stator length or rotor length (this
size specification can be omitted for
DC motors)
4
Electrical number
Consecutive number of the electrical
calculation
Examples:
TSA 200-100-220
1. Asynchronous motor
2. 200 mm stator diameter
3. 100 mm iron length
4. 220 electrical calculation number
TSL 240-354
1. DC motor
2. 240 mm housing diameter
3. –not applicable –
4. 354 electrical calculation number

Operating and maintenance instructions
General information
Version 1.0 Page 7 of 56
1.4 Rating plates
1.4.1 Asynchronous motor / Permanent magnet motor / Synchronous
reluctance motor
The standard rating plates for asynchronous motors, permanent magnet motors and
synchronous reluctance motors contain the following information (customer-specific
rating plates may differ):
Item
Designation
1
Serial number
2
Material number
3
Type designation
4
Voltage
5
Output
6
Frequency
7
Production week
8
Degree of protection
9
Number of poles
10
RPM
11
Duty cycle
12
Power factor
13
Bar code
14
Direction of rotation
15
Quality sticker with the number of the final inspector

Operating and maintenance instructions
General information
Version 1.0 Page 8 of 56
1.4.2 DC motor
The standard rating plate for DC motors contains the following information (customer-
specific rating plates may differ):
Item
Designation
1
Serial number
2
Material number
3
Type designation
4
Voltage
5
Output
6
Production week
7
RPM
8
Duty cycle
9
Direction of rotation
10
Quality sticker with the number of the final inspector

Operating and maintenance instructions
General information
Version 1.0 Page 9 of 56
1.5 Options and attachments
Depending on the drive type or motor type (see page 6), the following combinations
are possible:
Sealing
elements
Optional
attachmen
ts
Protection
class
of terminal
board
Drive type
Motor type
Motor without A-bearing
plate
O-ring
Shaft seal
Tachometer
Encoder
Pump
Brake
Gearing
Motor with gearing
IP6k9k
IP64-67
IP43/54
IP00/20
Carbon
Collector
Drive
motor
TSL
x
x
x
x
x
x
x
x
x
x
x
TSA
x
x
x
x
x
x
x
x
x
x
x
TSS
x
x
x
x
x
x
x
x
x
x
x
x
TSR
x
x
x
x
x
x
x
x
x
x
x
x
Pump
unit
TSL
x
x
x
x
x
x
x
x
TSA
x
x
x
x
x
x
x
TSS
x
x
x
x
x
x
x
x
TSR
x
x
x
x
x
x
x
x
Motor
unit
TSL
x
x
x
x
x
x
x
x
x
x
x
TSA
x
x
x
x
x
x
x
x
x
x
x
TSS
x
x
x
x
x
x
x
x
x
x
x
x
TSR
x
x
x
x
x
x
x
x
x
x
x
x
Servo
unit
TSL
x
x
x
x
x
x
x
x
x
x
TSA
x
x
x
x
x
x
x
x
x
TSS
x
x
x
x
x
x
x
x
x
x
TSR
x
x
x
x
x
x
x
x
x
x
TSA = asynchronous motor
TSL = DC motor
TSS = synchronous motor
TSR = synchronous reluctance motor
x = combination possible

Operating and maintenance instructions
General information
Version 1.0 Page 10 of 56
1.6 Variant examples
Schabmüller GmbH produces hundreds of motor variants for a wide variety of
applications. Here you will find examples and excerpts of various applications and
motor variants:
Application
Figure showing motor
Characteristics
Drive motors
Asynchronous, PM synchronous
Battery voltage: 24 V…80 V
Stator diameter:
120, 135, 170, 200, 240, 270, 300 mm
Output: 5…20 kW
RPM range:
2,000…5,000 rpm
Air-cooled
Integrated speed direction encoder and
temperature sensor
Optional brake attachment
Mounting and shaft ends according to
customer specification
DC motor
Battery voltage: 24 V…80 V
Stator diameter:
112, 125, 140, 150, 160, 178, 190, 210,
240, 325 mm
Output: 5…30 kW
RPM range:
1,000…5,000 rpm
Air-cooled
Integrated speed direction encoder and
temperature sensor
Optional brake attachment
Mounting and shaft ends according to
customer specification
Steering units
Asynchronous, PM synchronous
Battery voltage: 24 V…80 V
Stator diameter:
106, 120, 135, 150 mm
Output: 0.2…2 kW
Gear translation: 18:1…93:1
Drive rpm: 2…40 rpm
Air-cooled
Integrated speed direction encoder and
temperature sensor
Mounting and shaft ends according to
customer specification

Operating and maintenance instructions
General information
Version 1.0 Page 11 of 56
Application
Figure showing motor
Characteristics
DC motor
Battery voltage: 24 V…80 V
Housing diameter: 100, 102, 112, 125,
150, 178, mm
Output: 0.5…10 kW
Pump mounting, mounting and shaft
ends according to customer specification
Pump units
Asynchronous, PM synchronous
Terminal voltage: 16 V...480 V 3~
Stator diameter:
150, 170, 200 mm
Output: 5…15 kW
RPM range: 2,000…4,000 rpm
Air-cooled
Integrated speed direction encoder and
temperature sensor
Pump mounting according to customer
specifications
Mounting and shaft ends according to
customer specification
DC motor
Battery voltage: 24 V…80 V
Housing diameter: 112, 125, 150, 178,
190, 210, 240, 315 mm
Output: 0.5…10 kW
Pump mounting, mounting and shaft
ends according to customer specification

Operating and maintenance instructions
Safety
Version 1.0 Page 12 of 56
2 Safety
2.1 General safety instructions
2.1.1 Obligations of the operating company
Only qualified persons who carry out work on the motors and consistently observe and
implement the supplied operating and maintenance instructions as well as the
standards and safety instructions mentioned may install, commission and service the
motors.
Before any work is carried out on the motors, it is the responsibility of the supervisor to
draw the attention of his qualified personnel to the dangers that could occur during this
work. Improper use of the motors or improper maintenance by unqualified personnel
can lead to serious damage to health and material damage.
2.1.2 Qualified personnel
Qualified personnel are persons who, on the basis of their training, experience and
instruction as well as their knowledge of relevant standards, accident prevention
regulations and corresponding operating conditions, are authorised to carry out the
necessary activities.
2.2 Safety instructions in these operating instructions
The motor corresponds to the state of the art and the recognised safety regulations.
Nevertheless, dangers can arise during operation and during maintenance and repair
work.
These dangers are pointed out in these operating instructions with safety instructions.
The safety instructions precede the relevant descriptions or work steps.
2.2.1 Structure of the safety instructions
The safety instructions consist of the following elements:
1. Danger signs
2. Signal word
3. Nature and source of the danger
4. Possible consequences of non-observance
5. Measures for the avoidance/avoidance of danger
Danger
sign
SIGNAL WORD
Nature and source of the danger
Possible consequences of non-observance
Measure for the avoidance/avoidance of danger

Operating and maintenance instructions
Safety
Version 1.0 Page 13 of 56
2.2.2 Danger signs
Danger symbols are used to draw attention to the danger of personal injury.
Danger signs
Meaning
General danger sign
Failure to observe the warnings may result in death, serious
injury or serious damage.
Suspended loads
Failure to observe the warnings may result in death, serious
injury or property damage due to falling loads.
Electricity
Failure to observe the warnings may result in death or serious
injury from dangerous voltage.
2.2.3 Signal words
Signal words indicate the level of risk and the severity of the possible damage. The
following signal words are used in these operating instructions:
Signal word
Meaning
DANGER
Death or serious injury will result
WARNING
Death possible, serious injury foreseeable
CAUTION
Injury or slight injury possible
NOTE
Danger of property damage

Operating and maintenance instructions
Transport and storage
Version 1.0 Page 14 of 56
3 Transport and storage
Warranty
If any damage is discovered after delivery, report it immediately to the transport
company, the insurance company and Schabmüller GmbH.
Failure to report the discovered damage will void the warranty.
The motors are tested and delivered ready for installation. The machined surfaces are
protected against rust with a corrosion inhibitor. Immediately after receipt, the
packaging and the motor must be inspected for external transport damage.
3.1 Transport
Observe the following safety instructions for each transport:
CAUTION
Danger of injury from falling objects.
Only lift packaging or our products at the lifting points provided for this purpose
Take into account the weight indicated on the packaging or on our products
and the lifting capacity of the lifting device
Do not tip the packaging
Put down the packaging or our products gently (without impact) to avoid
storage damage
Replace the corrosion protection or protective devices that were removed for
the incoming inspection immediately after the inspection
Do not remove any protective devices until shortly before installation
3.2 Incoming inspection
Proceed in the order given:
Step
Procedure
1
Check all parts (also parts in additional packaging).
2
Unpack the motor and inspect it thoroughly for damage.
3
Reprocess any damage to the paint coat or rust protection on machined
surfaces.
NOTICE

Operating and maintenance instructions
Transport and storage
Version 1.0 Page 15 of 56
3.3 Storage
Danger of property damage
Improper handling during transport and storage can cause damage.
Avoid vibrations, falls and humidity during transport
Strictly follow all instructions in these operating and maintenance instructions
and document this to maintain the manufacturer's warranty
If the motor is exposed to external influences such as temperature fluctuations,
humidity, aggressive chemicals, etc. during storage, damage can occur inside
the motor, in the roller bearings, in the terminal box and in the winding;
the components oxidise, the grease ages and the insulation resistance drops to
an inadmissible value
3.3.1 Ambient conditions
The motor must be stored in a dry, vibration-free and dust-free location in a building at
an ambient temperature above 5 °C. If other conditions apply, please contact
Schabmüller GmbH.
3.3.2 Storage location for prolonged storage
The following instructions apply to motors that are stored for long periods of time or
are taken out of service for more than two months.
The following points must be taken into account when selecting the storage location:
The room must be closed and covered
The room must be protected against moisture, vapours, rodents and insects
The room must not contain any corrosive gases such as chlorine, sulphur dioxide
or acids
The room must not be subject any heavy continuous or intermittent vibrations
The ambient temperature must be between 5 °C and 60 °C
The ambient temperature must not fluctuate suddenly
The relative humidity must be less than 50%
The room must be protected against dirt and dust deposits
The room must be equipped with a fire protection system
If the storage room does not meet one of these requirements, Schabmüller GmbH
proposes to provide the packaging with special protective measures during the
storage period:
Closed box or similar packaging
If there is a risk of fungal attack or formation, the box must be protected at the
storage location by spraying or painting with suitable chemical agents
The packaging must be carried out with great care by qualified persons
3.3.3 Logging during storage time
The motor in storage must be checked at regular intervals. A log should be kept of the
findings. The following points must be checked:
Damage
Soiling
Condensation formation
NOTICE

Operating and maintenance instructions
Transport and storage
Version 1.0 Page 16 of 56
Condition of the protective coating
Condition of the paintwork
Signs of larvae and insects
Ambient temperature
Humidity
Conditions at the storage location (see page 15)
Instructions in the maintenance schedule (see page 46)
3.3.4 Other motor-dependent storage measures
Motor characteristic
Storage measures
DC motor
If stored for more than two months:
Lift off the carbon brushes and remove them from their
holders to prevent oxidation at the contact points with the
slip rings
Before operation, reinstall the carbon brushes and check
that the brush holders run smoothly
Water-cooled motors
Do not allow the ambient temperature to fall below +5 °C
At temperatures below +5 °C, add an antifreeze to the
water in the cooling circuit
Separately supplied
components
If components are supplied separately (terminal boxes,
bearing plates, etc.), these parts must also be packed and
protected
If the manufacturer has his own operating instructions,
these must be followed
Do not allow the relative humidity in the original packaging
to exceed 50%
Machined surfaces
All machined surfaces (shaft ends, flanges, etc.) are supplied
ex works with a rust inhibitor.
This protective film should be reapplied at least every six
months or in case of removal or damage
Recommended rust inhibitor: Gunex 2000, Manufacturer:
Klever
Grease-lubricated
rolling bearings
The rolling bearings are factory lubricated. To avoid bearing
damage:
During the storage period, turn the rotor/armature by hand
every two months
Turn the rotor/armature at a speed of 30 rpm for one
minute in order to achieve even grease distribution
If stored for three years or longer:
Replace the rolling bearings before commissioning

Operating and maintenance instructions
Installing the motor
Version 1.0 Page 17 of 56
4 Installing the motor
4.1 Tightening torques for fastening elements
Danger of property damage
For attachments, use the tightening torques specified by the manufacturer
If no tightening torques are specified by the manufacturer, refer to the drawing
or the table below for tightening torques
The tightening torques indicated on the drawing have priority
Thread
Production class according to DIN 267
Width
across
flats
4.8
8.8
10.9
12.9
Tightening torques [Nm]
M 3
0.6
1.4
1.9
2.2
5.5
M 4
1.3-1.5
3-3.6
4.3-5.3
5.1-6.1
7
M 5
2.6-3.1
6-7.1
8.5-10
10.2-12
8
M 6
4.5-5.2
10.3-12
14.7-18
17.6-21
10
M 8
10.8-12.5
25.5-30
35.3-44
42.2-52
13
M 10
21.6-25.8
50-60
70.6-87
85.3-100
15
M 12
38.2-45
87.3-105
122-151
147-177
18
M 16
90-100
200-220
290-320
345-380
24
These tightening torques are standard values for metric standard threads according to
DIN 13 and head support dimensions according to DIN 912; 931; 934; 6912; 7994 and
79xx. They result in a 90% utilisation of the bolt yield strength. A coefficient of friction
of 0.14 to 0.20 was assumed (new screw, without post-treatment, unlubricated).
NOTICE

Operating and maintenance instructions
Installing the motor
Version 1.0 Page 18 of 56
4.2 Mounting the shaft sealing rings
Danger of property damage
Do not scratch or damage the sealing surfaces during disassembly
Do not tilt the sealing ring when pressing it in
4.2.1 Removal and replacement
The removal of sealing rings is generally not difficult. Usually a screwdriver or similar
is sufficient for disassembly. However, this will damage the sealing ring. After a
machine has been repaired or overhauled, new rotary shaft seals must always be
installed.
If there is a disassembly hole on the housing, the shaft seal can be pressed out with a
pin.
Item
Designation
1
Disassembly hole on housing
2
Shaft seal
NOTICE

Operating and maintenance instructions
Installing the motor
Version 1.0 Page 19 of 56
4.2.2 Installation
The sealing edge of the new shaft seal should not come into contact with the old
raceway.
This can be achieved by:
Pressing into the locating bore at different depths
Reworking the shaft and assembly of a shaft sleeve
Proceed in the order given:
Step
Procedure
1
Clean installation spaces before assembly.
2
For rubber seals: Grease or oil shafts and seals.
3
For shaft seals that cannot be lubricated by external media:
Fill the shaft seal with grease (PETAMO GY193).
4
Cover sharp-edged transitions (e.g. at indentions) with a phase or round
or feather key grooves or hub grooves and threads with an adhesive tape,
sleeve or similar.
5
Place the sealing ring centrically and perpendicular to the shaft.
Apply the press-in force as close as possible to the outer diameter.
6
Push the sealing ring up to the adjusted stop (usually the end face of the
receiving bore) or fix the sealing ring with a shoulder or a spacer washer.

Operating and maintenance instructions
Installing the motor
Version 1.0 Page 20 of 56
Examples of the assembly of shaft seals
Item
Designation
1
Press-in tool
2
Shaft seal
This manual suits for next models
5
Table of contents
Popular Engine manuals by other brands

Northern Lights
Northern Lights NL673L4 Operator's manual
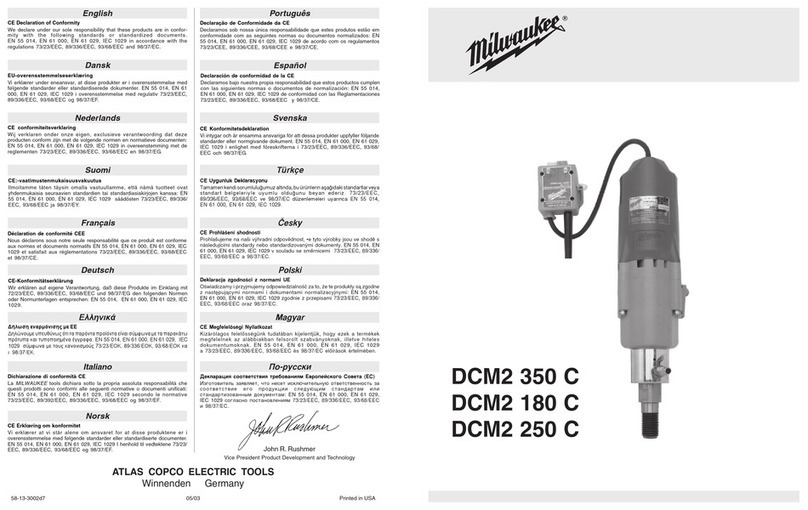
Milwaukee
Milwaukee DCM2 350 C manual

Hyundai Seasall
Hyundai Seasall D170 Series Installation and operating manual
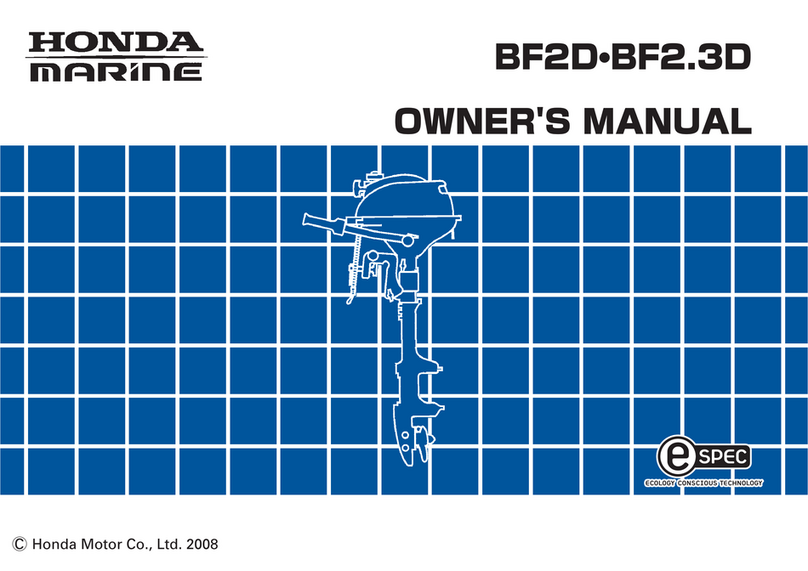
Honda
Honda Marine BF2D owner's manual
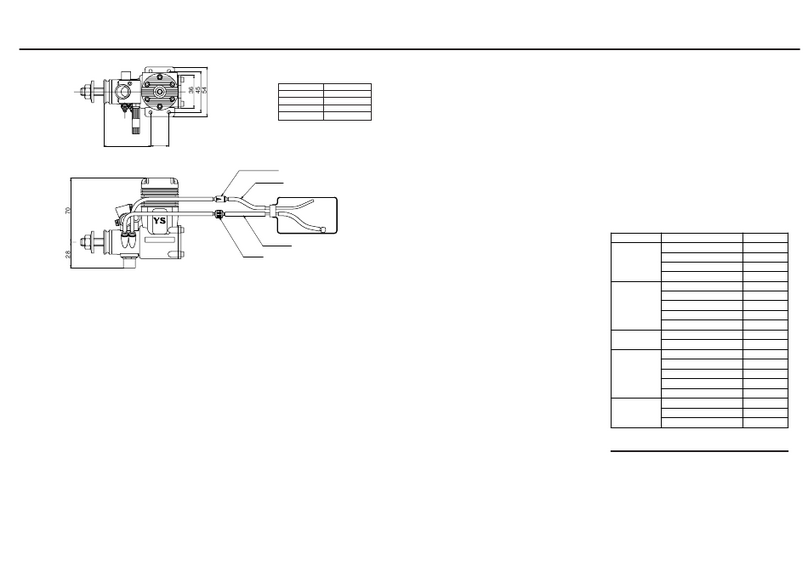
YS Performance
YS Performance YS45FS Operator's manual
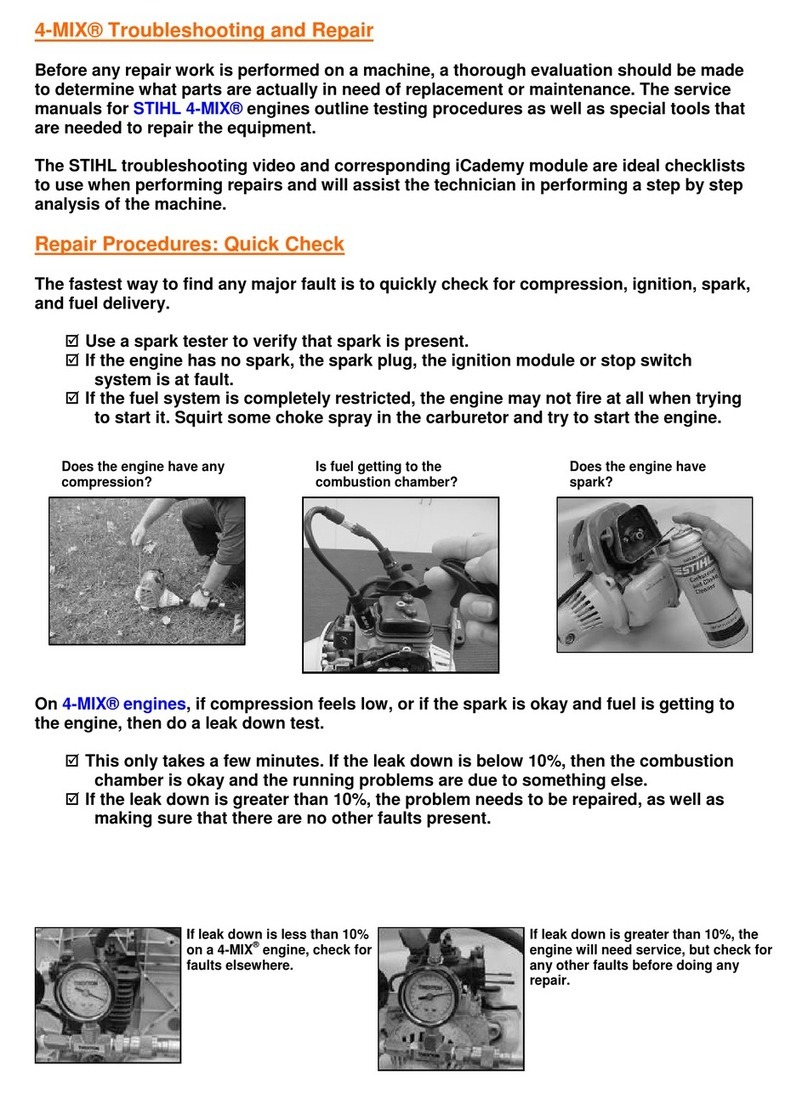
Stihl
Stihl 4-MIX Troubleshooting and repair instructions
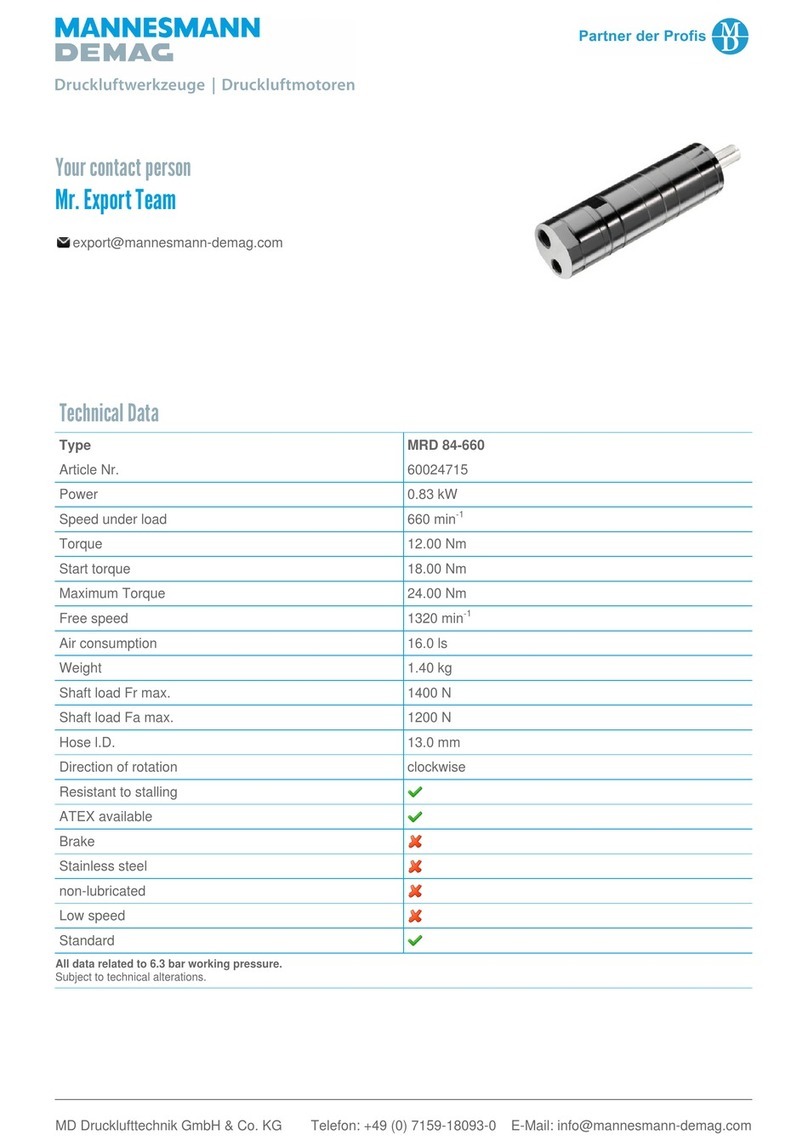
Mannesmann Demag
Mannesmann Demag MUD 9-2300 Installation and Maintenance
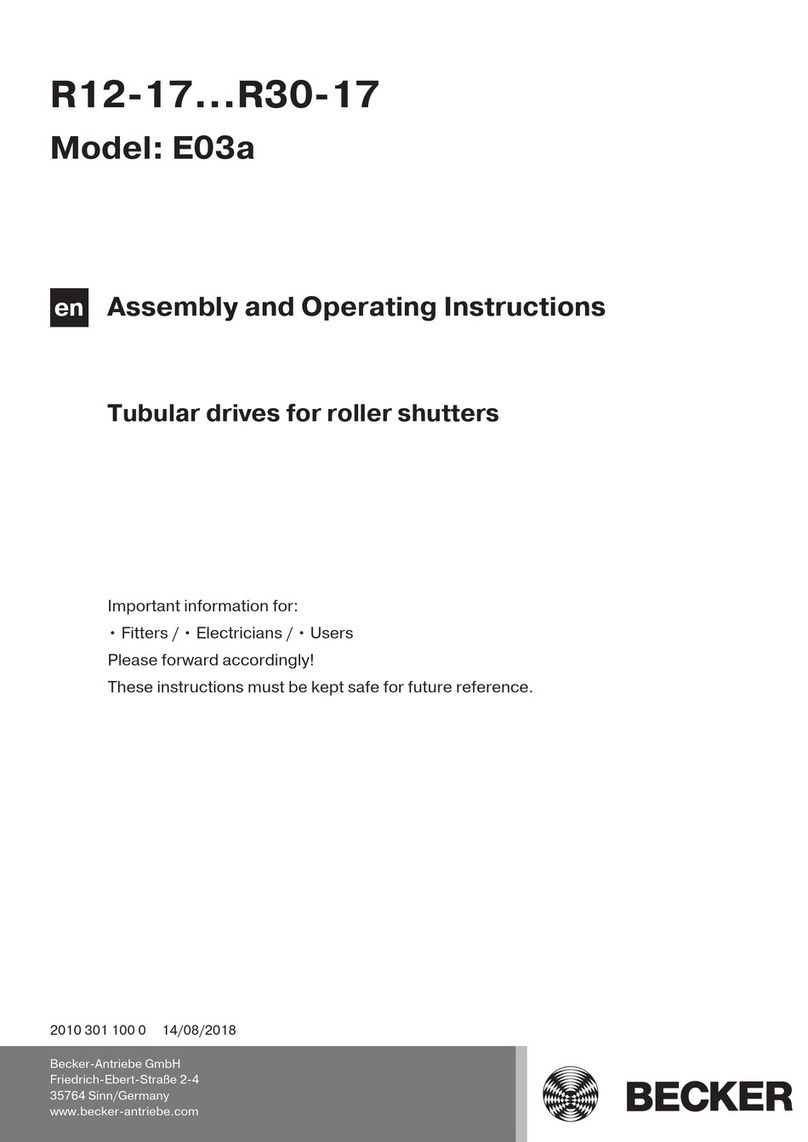
Becker
Becker E03a Assembly and operating instructions
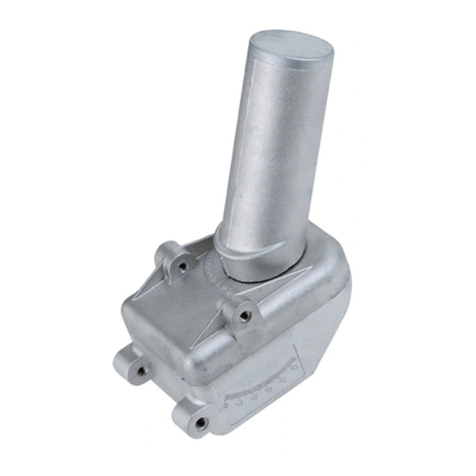
Stab
Stab ROTOR SAT HH100 instruction manual
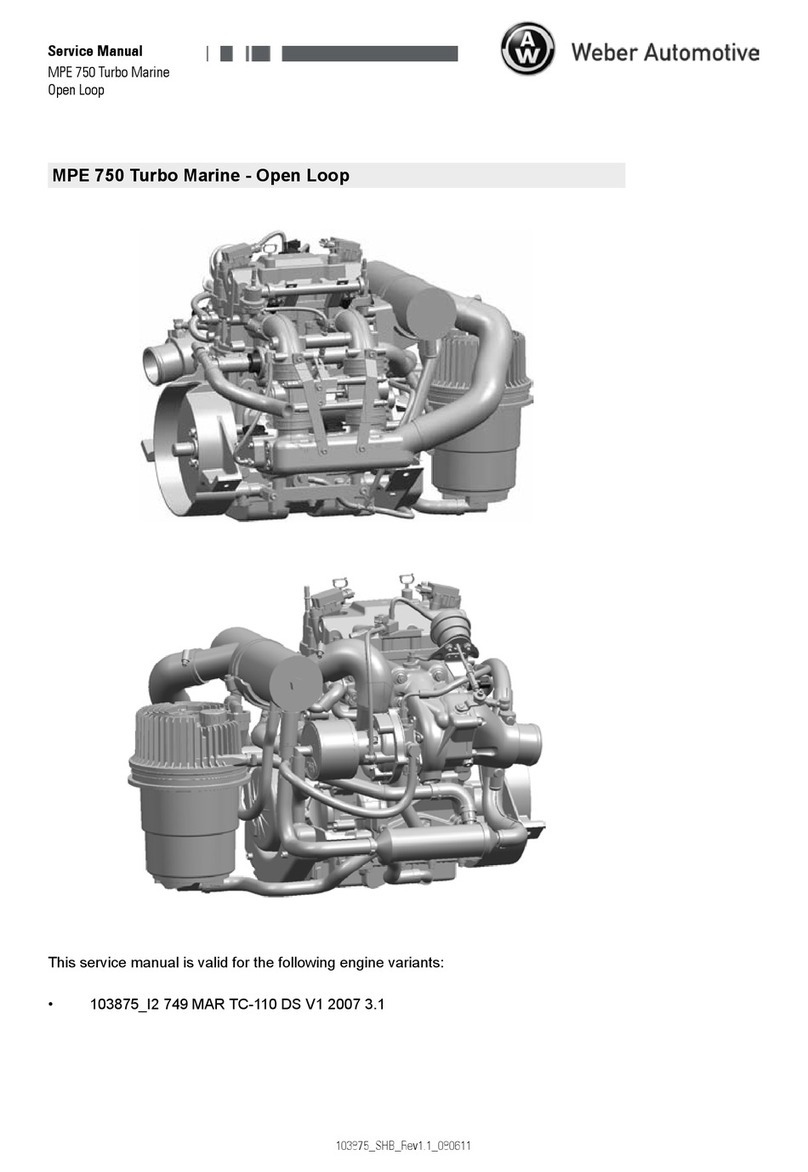
Weber Automotive
Weber Automotive MPE 750 Turbo Marine Service manual

PEUGEOT
PEUGEOT XS1P52QMI-3B Workshop manual
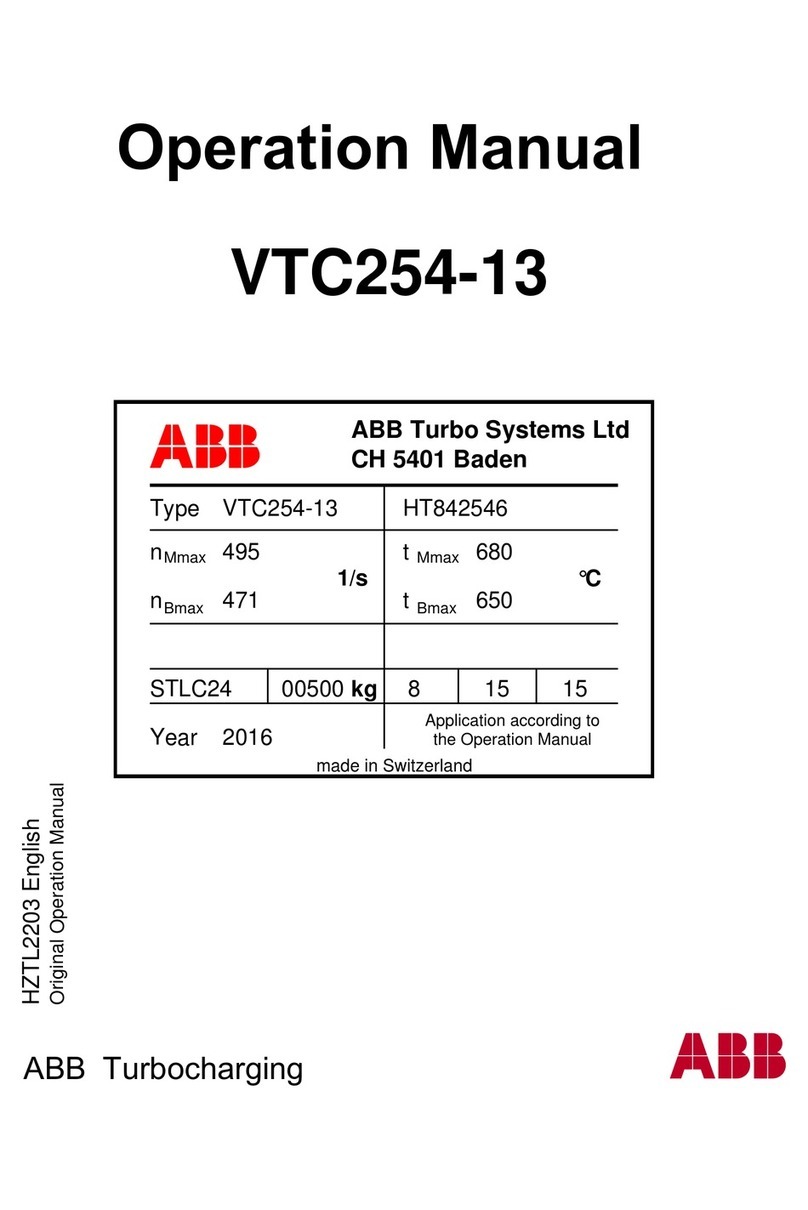
ABB
ABB HT842546 Operation manual