Shopsmith MARK V Model 520 User manual

WARNING
Read the SAFETY information
in the Introduction section and
complete the ASSEMBLY AND
ALIGNMENT procedures before
operating the Shopsmith Mark
V.
Use only Shopsmith parts and
accessories on your Mark V. Us-
ing non-Shopsmith parts may
create a hazardous condition
and will void your warranty.
Shopsmith Mark V
Home Workshop System
®
MARK V Model 520
Summary Manual
Designed and Built in Dayton, Ohio.

SM - 2
Summary Manual Mark V Model 520
Safety First
The Shopsmith Mark V has many built-in safety
features. But, the effectiveness of these features
depends on you. To protect yourself from injury:
KNOWING YOU CAN BE HURT IS MORE
IMPORATNT THAN THE MOST EFFI-
CIENTLY DESIGNED GUARD ON A TOOL.
THIS MACHINERY MAY CAUSE SERIOUS
INJURY IF THE SAFETY RULES ARE NOT
STUDIED AND FOLLOWED.
READ, UNDERSTAND AND FOLLOW ALL
THE INFORMATION IN THIS OWNER'S
MANUAL.
The meanings of WARNINGS, CAUTIONS,
AND NOTES are:
WARNING
A WARNING is given when failure to follow the
directions could result in injury, loss of limb, or
life.
CAUTION
A CAUTION is given when failure to follow the directions
could result in temporary or permanent damage to the
equipment.
NOTE
A NOTE is used to highlight an important pro-
cedure, practice or condition.
Eye Protection
•Always wear eye protection when you use
power equipment. Use goggles, safety glasses
or a face shield to protect your eyes.
Ear Protection
•Prolonged exposure to high noise levels from
high speed power equipment can damage your
hearing.
NOTE
It is important to provide adequate lighting in
your shop area.
Sawdust and Chips
NOTE
Shopsmith Mark V's are fitted to use with Dust
Collection equipment. We recommend the
Shopsmith DC3300 Dust Collection System.
•Sawdust and chips can be fire hazards and
breathing sawdust can be a health hazard. Saw-
dust may cause you physical discomfort, espe-
cially if you have emphysema, asthma, or an
allergicreaction.Thesawdustfromsomewoods
can also be toxic. When sawing or sanding:
Saw Guards
•Most shop accidents happen on the table saw.
For this reason, always keep the upper and
lower saw guards in place whenever you oper-
ate the Mark V in the table saw mode. The
ONLY exception to this rule is when you need to
saw part way through stock– such as when
cutting a rabbet or groove, or when using the
dado or molder accessory. Then you must re-
move the upper saw guard. Whenever you re-
move the upper saw guard, KEEP the lower
saw guard in place and work with extreme
caution.
Table Saw Kickback
•Table saw accidents are often associated with
kickback. Kickback is the ejection of the stock
from the saw back toward the operator. Kick-
back causes loss of control and your hand could
be thrown into the blade or you could be hit by
flying stock. Never stand directly in the line of
rotation of a moving blade. This lessens your
chances of being hit by flying stock, if a kickback
occurs.
To Prevent Kickback:
•Always keep the upper and lower saw guards
in place. An anti-kickback mechanism on the
guards helps prevent the stock from binding the
bade and the stock from being thrown back
SAFETY

Mark V 520 Summary Manual
SM - 3
toward the operator. Make sure the riving knife
is aligned properly with the blade.
Electrical Requirements
•Pay particular attention to the connection be-
tween your power equipment and your power
source. Before you plug in your Mark V, check
the voltage and the amperage of the circuit you
will be using. The wall receptacle and wires in
the circuit must be rated for at least 15 amps.
Circuit
•The Mark V 115-volt motor is rated at 1-1/8 hp.
It develops more than 1-1/2 hp in use and
"pulls"13-14 amps when running under aheavy
load. The headstock motor runs on standard
U.S. house current– 120 volts, 60 hz. The wire
size (gauge) in the circuit you use must be rated
for at least 15 amps. Using wire and receptacles
rated to handle 20 or 25 amps will give you an
even bigger safety margin.
Fuses
•We recommend you install circuit breakers or
fuses which are time-delayed. Fusetron T-15
fuses are recommended. Do not use fuses or
circuit breakers larger than 15 amps. When
you first turn on the machine, the motor pulls
high amperage to get up to running speed. A
time delay fuse or circuit breaker won't blow
during this initial surge. Always start the Mark
V at "Slow" speed setting to prevent blowing
fuses and tripping the circuit breaker.
•If you need to run a new circuit to operate the
Mark V, be sure that the wire and receptacle you
use is rated to handle the amperage of the head-
stock motor, and is at least 15 amps.
Grounding
•Thecircuityouseeshould beproperlygrounded.
Extension Cords
•If you use an extension cord to plug in your
Mark V, be sure it is a three-conductor cord with
a grounding plug and receptacle.
•The wire gauge must be thick enough to prevent
loss of power and overheating– the longer the
cord, the thicker the wire should be. Use the
chart to determine the American Wire Gauge
wire size required:
Cord Minimum
Length Wire Size
25 ft. 14 AWG
50 ft. 12 AWG
100 ft. 10 AWG
•Before using an extension cord, inspect it for
loosewires or damage insulation.Replace dam-
aged cords immediately.
•Do not let the connection between the power
cord and an extension cord lie on a damp or wet
surface.
Shopsmith Safety Kit
WARNING
DO NOT TRY TO MAINTAIN OR REPAIR YOUR
PUSH BLOCKS, PUSH STICKS, FENCE STRAD-
DLERS, OR FEATHER BOARDS. WORN OR
VISUALLY DEFECTIVE SAFETY EQUIPMENT
NEEDS TO BE REPLACED IMMEDIATELY.
•These safety devices are designed to hold or
maneuver stock close to moving blades, cutters
and discs. They give you better control over the
stock which helps achieve a more accurate cut.
Depending on the operation, use one or more
safety devices. Choose the device that gives you
the most control and keeps your hands out of
danger.
•Usea push stick to guide stock 1-1/2"to 5" wide.
Place the foot on top of the stock and hook the
heel over the back edge.
•Use the push block to hold down and guide
stock over 5" wide. As you press down, for-
ward, and to the side, the rubber pad grips the
wood. The handle is tilted to help keep your
hands away from the blade, cutter or disc.
•Use the fence straddler to hold down and push
stock narrower than 1-1/2" past a blade or cut-
ter. The body rides on the rip fence, while the
heel hooks over the back edge of the stock. To
change the height of the heel, loosen the locking
knob. To reverse the heel, rotate the side 180°.
Keep the locking knob secure.
•Use the feather board to press stock against the

SM - 4
Summary Manual Mark V Model 520
rip fence. Mount the feather board in either
table slot. The fingers must be angled in the
same direction that you feed the stock– use the
arrow on top of the feather board as a guide.
Position the fingers so they press against the
stock just before it gets to the blade or cutter,
then tighten the locking knobs. See Figure A-7.
To reverse the direction of the fingers, remove
the mounting bar, turn the feather board over,
then replace the mounting bar.
Safety Rules for the
Shopsmith Mark V
Read, understand and follow the Mark V
Owner's Manual and the manual for every
power tool you use.
Additional warnings, cautions and instructions
and operating techniques are provided in the
Shopsmith book, Power Tool Woodworking
for Everyone. (A copy is included with your
new Mark V, and is also available from
Shopsmith.)
Keep your hands, fingers and other parts of
your body at least 3" away from any moving
blade, cutter or disc.
Wear proper eye and ear protection. Also,
wear a dust mask.
Ground all equipment (unless double insu-
lated.)
Use clamps, fixtures or the miter gauge to
secure stock. When appropriate, use a push
stick, push block, fence straddler, feather board,
miter gauge with safety grip or other safety
devices to maneuver stock past a moving blade,
cutter or disc.
Keep all guards in place and in working order.
Most injuries occur on unguarded power equip-
ment.
Never stand directly in the line of rotation of a
moving blade, cutter, disc.If a kickback occurs,
you could be hit by the stock or injured by
contacting a moving blade, cutter or disc.
Do not wear loose clothing, ties, gloves, or
jewelry. Roll sleeves up above your elbows,
wear non-slip footwear, and tuck long hair
under a hat.
Never operate power equipment if you are
fatigued, taking medication, or under the in-
fluence of alcohol or drugs.
Do not work with stock that is too small or too
large to handle safely, or that has loose knots or
other defects.
Plan the operation and safety precautions be-
fore you begin.
Turn off the Mark V and wait until all cutters,
blades or discs come to a complete stop before
removing stock and scraps.
Turn off and unplug the Mark V before making
adjustments, changing modes or performing
maintenance.
Make sure the switch is in the "off" position
before plugging or unplugging the Mark V.
Secure the headstock lock, carriage lock, table
height lock, table tilt lock and quill lock (if quill
is used), before turning on the Mark V.
Make sure accessories, safety devices and fix-
tures are properly adjusted and secured before
turning on the Mark V. Also, check the arbor
set screw periodically.
Remove adjusting keys and wrenches from the
Mark V before turning it on.
Never exceed the maximum recommended
speed for the operation. When using "combina-
tion" setups (such as table saw– jointer), never
exceed the maximum speed for the slowest
accessory.
Never try to stop the Mark V or accessory by
grabbing the stock, any part of the machine, or
by forcing material against a cutter, blade or
disc.
Never leave the Mark V running unattended.
Turn off the power. Don't leave until the ma-
chine comes to a complete stop.
Do not overreach or hurry. Keep proper foot-
ing and balance at all times.
Never reach under the worktable while the
machine is running.
Never use a carbide-tipped blade or cutter to
machine second-hand lumber. You could be
hit by pieces of metal.
Repair or replace damaged parts before fur-
ther use. If a strange noise or vibration devel-
ops, turn off and unplug the machine. Correct
the problem.
Use only recommended Shopsmith parts and
accessories on your Mark V. NEVER use non-
Shopsmith replacement parts or accessories.
Use only tools made in conformity to EN-847-
1. They are not designed like Shopsmith parts.
Using non-Shopsmith parts may create a haz-
ardous condition and will void your warranty.
Keep all tools, cutters and blades for the Mark
V and accessories sharpened.
Keep all hand tools and power tools cleaned
and maintained.
Do not use the Mark V or an accessory to do a
job for which it was not designed.
Never mount an accessory on an auxiliary
spindle unless it is designed to operate there.
Consult the accessory's manual for the proper

Mark V 520 Summary Manual
SM - 5
spindle on which to mount the accessory.
Make sure the machine rests firmly on the floor
when in use– not up on the retractable casters.
Do not force the stock. Always feed stock against
the rotation of the blade, cutter or disc. Let the
blade, cutter or disc get up to full speed before
you feed the stock.
Make sure the stock rests firmly against the
worktable, miter gauge, and/or rip fence.
Do not use warped or twisted stock.
Whenever you extend the quill, do not let go of
the quill lever unless you first secure the quill
feed lock.
Do not work with long boards or sheet materi-
als by yourself, unless you use a large rear
support table or roller stands. Never try to
work with boards the are too large for you to
handle safely. It is best to have a helper.
Never stand or lean on the machine. You could
fall on it or it could tip over.
Keep work areas well lit, clean and free from
clutter.
Do not use power equipment in damp, wet or
explosive atmospheres.
Keep visitors a safe distance from power equip-
ment, and make them wear eye and ear protec-
tion.
Make your workshop "child-proof." Unplug
equipment, use padlocks and master switches,
and remove switch keys.

SM - 6
Summary Manual Mark V Model 520
2
4
5
7
12
13
14
15
16
18
19
21
22
1
8
11
96320 11 10
17
7. Headrest– Holds the tie bar.
8. Headrest Lock– Secures the Mark V in the horizon-
tal position.
9. Power Mount– Holds the extension table and the
majoraccessories (ShopsmithBandsaw, Jointer, Belt
Sander, Scroll Saw, Strip Sander and Planer).
10. Base Mount– Holds the extension table and lathe
tailstock.
11. AccessoryMount Locks– Secure the extensiontable,
Major Accessories, and the lathe tailstock.
12. Main Spindle– Mounts the saw blades, sanding
discs, and other accessories.
13. Quill– Extends and retracts up to 4-1/4".
14. Quill Lock– Secures the quill.
15. Quill Feed Lever– Extends the quill and main
spindle out from the headstock.
16. Quill Feed Stop– (hidden from view) Stops the quill
at predetermined distances out from the headstock.
17. Power Switch– Turns the Mark V on and off. Has a
removable safety key to prevent unauthorized use
of the Mark V.
18. Headstock Lock– Secures the headstock on the way
tubes.
19. Speed Dial– controls the speed of the main and
auxiliary spindles. ONLY turn the speed dial when
the Mark V is running. Otherwise, you will damage
thespeed changingmechanism. Thenturn thespeed
dial to "Slow" after every operation, then turn off
the Mark V.
20. Auxiliary Spindles– The upper spindle powers the
Bandsaw, Belt Sander, Strip Sander and Thickness
Planer. The lower spindle powers the Jointer and
Scroll Saw.
21. Logo Cover– (hidden from view) Allows access to
the wiring and speed changer mechanism.
22. Belt Cover– Allows access to the belts and sheaves.
Terms to Know
Right
Side
Left Side
The Shopsmith Mark V will perform all the func-
tions of a table saw, disc sander, drill press, hori-
zontal boring machine, and wood lathe.
Basically, the Mark V is a rigid bench that holds
the headstock and the worktable system. The
upper part of this bench can be positioned hori-
zontally or vertically. The headstock and the
worktableslide independently and are positioned
along the upper tubes.
You can mount accessories to the headstock and
operate them at different speeds. The worktable
can be positioned over, under or beside these
accessories to hold stock at various angles. In this
way, the bench, headstock, worktable, and acces-
sories combine to make a unique, capable and
versatile woodworking system.
Before you proceed, familiarize yourself with the
Mark V’s basic parts:
1. Legs -- Support the way tubes and bench tubes.
2. Bench Tubes – Hold the Mark V rigid.
3. Way Tubes – Allow the headstock and carriage to
slide.
4. Base – Allows the way tubes to pivot to either a
horizontal or vertical position.
5. Base Lock– Secures the Mark V in the vertical
position.
6. Way Tube Tie Bar– Holds the free end of the way
tubes.

Mark V 520 Summary Manual
SM - 7
23
24
25 26
27 28 29
30
31
32
33
34
35
36
37
37
39
41
38
40
34. Table Height Lock– Secures the table at any
height.
35. Carriage– Slides along the way tubes and holds
the table support tubes and the lathe tool rest.
36. Carriage Lock– Secures the carriage on the way
tubes.
37. Trunnions– Allows the table to tilt up to 90° left
and 45° right.
38. Table Tie Bar– Supports the table support tubes
and the trunnions.
39. Table Tilt Indicator– This vernier scale indicates
the table angle.
40. Table Tilt Lock– Secures the table at any angle, up
to 90° left and 45° right.
41. TableStops– When properlyadjusted, these bolts
stop the table at 90° left, 45° right and 0°. (Note:
the two 90° table stop bolts are shown.)
The following accessories come with
the Mark V, but are not shown on the
illustrations. Refer to the PARTS
LISTS to identify them.
Sanding Disc– Mounts to the main spindle and is
used for disc sanding.
DrillChuckandKey– Mounts to the main spindle.
The key locks the bit in the chuck.
Lathe Tool Rest Assembly– Mounts in the car-
riage to support and guide lathe chisels. It has
two mounting positions.
23. Worktable – Holds the stock and provides a
working surface.
24. Table Insert– Used for sawing, sanding, drilling
and boring. It can be replaced with inserts for
dadoing, molding, drum sanding and shaping.
25. Miter Gauge Slots– Guide and secure the miter
gauge.
26. MiterGauge withSafety Grip–Holds stockfirmly
at various angles. It slides freely or locks in the
miter gauge slots.
27. Rip Fence– Mounts to the table and is used as a
guide, support or stop. It automatically aligns
itself parallel to the blade. Holes in the fence are
used to mount fixtures and fence extensions.
28. 10" Saw Blade– Mounts to the 1-1/4" arbor which
then mounts to the main spindle. This saw blade
is use for both crosscutting and ripping.
29. Upper Saw Guard– Provides a physical barrier
between you and the part of the blade above the
table. An anti-kickback mechanism helps con-
trol kickbacks.
30. Lower Saw Guard– Protects you from the part of
the blade or cutter below the table. The saw
guard has a dust chute. The lower saw guard is
also used with the sanding disc.
31. Extension Table– Mounts in either the power
mount or the base mount to provide extra sup-
port for the stock.
32. Table Support Tubes– Support the table above
the bench. Each tube has racks that mesh with
pinions in the carriage to raise and lower the
table.
33. Table Height Crank– Turns the pinions in the
carriage which raise and lower the table.

SM - 8
Summary Manual Mark V Model 520
Lathe Drive Center– Mounts to the main spindle
and turns the stock when the spindle is turning.
Lathe Cup Center– Mounts in the tailstock and
supports stock when spindle turning.
Tailstock– Mounts in the base mount and holds
the cup center in line with the drive center.
Coupling Kit– Connects the Major Accessories to
the headstock.
Safety Kit– Includes a push stick, push block,
feather board and fence straddler. Used to help
guide and hold stock safely during operations.
Goggles– For protection of your eyes. To be worn
during all operations.
Arbor Wrench and Allen Wrenches– Used for
alignment, adjustment and to mount accessories.
Specifications
The specifications of the Shopsmith Mark V will give
you an idea of its capabilities—
Capacities
The work capacity of the Mark V depends on these five
modes:
• Table Saw
As a table saw, the Mark V accepts 10" saw blades. The
maximum depth of cut at 0° is 3-1/4". With the table
tilted at 45°, the maximum depth of cut is 2-3/8".
• Disc Sander
As a disc sander, the Mark V mounts a 12" diameter
sanding disc, giving you 113 square inches of sanding
surface. The size of stock that you can sand is limited
only by what you can safely handle.
• Drill Press
As a drill press, the Mark V used a chuck that accepts
drill bits with shanks 5/64" to 1/2" in diameter. The
throat capacity is 8-1/4", enabling you to drill the
center of a 16-1/2" circle. With a 5-1/2" long bit
mounted in the chuck, the maximum distance from the
bit to the table is 22". If you remove the table, the
maximum distance from the bit to the floor is 54".
• Horizontal Boring Machine
The Mark V uses the same drill chuck used in the drill
press mode. The table can be lowered
2-3/8" below the chuck, enabling you to bore the center
of boards up to 4-3/4" thick. The width and length of
boards that you can bore is limited only by what you
can safely handle.
• Lathe
As a lathe, the Mark V handles both spindle and
faceplate turning. The swing over the way tubes is 16-
1/2", and the maximum distance between centers is
34". The tool rest and arm will pivot a full 360°, and
can be locked in place in any position between the
centers.
Bench
The Mark V is mounted on two steel legs and is held
rigid by four steel tubes. The two upper tubes, or way
tubes, can be locked in either a horizontal or vertical
position.
Headstock
The Mark V is powered by a 1-1/8" hp motor. This
turns three spindles– one main spindle and two auxil-
iary spindles. All three spindles revolve on
permanently-lubricated, sealed ball bearings.
Speed
A system of variable-diameter pulleys makes it pos-
sible to adjust the speed of the main and upper auxiliary
spindle from 700 rpm to 5,200 rpm. The lower
auxiliary spindle turns 1.6 times faster than the other
two, or between 1,120 rpm and 8,320 rpm.
Worktable
The Mark V worktable is made of die-cast aluminum
grooved and machined smooth. It can be tilted from
90° left to 45° right, and raised from 2-3/8" below the
center of the main spindle to 8-1/4" above it with the
work angle set at 0°.
Overall Dimensions of the
Mark V
Overall, the Mark V is 71" long, 25-1/2" wide, and 46-
1/2" high in the table saw mode, or 76-1/4" high in the
drill press mode.

Mark V 520 Summary Manual
SM - 9
Also, remember that your Mark V could possibly go
out of alignment if it is moved to an area with
varying floor levelness. Remember to recheck align-
ment and make needed adjustments after moving
your Mark V, if needed.
ADJUST THE HEADREST LOCK
1. To check the headrest lock, grasp the way
tubes near the tie bar and pull up, as demon-
strated by the right hand in Figure B-44.
SAFETY
WARNING
Make sure the speed dial is set to "Slow", then
turn off and unplug the Mark V before performing
any ALIGNMENT procedure.
1. Complete ALL of the following procedures–
and then recheck them at regular intervals.
You MUST use an accurate combination
square for alignment and adjustment. To
check that your square is accurate, select a
board with at least one straight and true edge.
Place the square against the good edge and
draw a line across the width. Flop the square
over and hold it against the same edge and
draw another line next to the first one. If the
lines are parallel, your square is accurate.
2. All the parts and accessories which support or
guide the stock MUST be aligned parallel
with or perpendicular to the main spindle's
plane of rotation. During the following align-
ment procedures the saw blade (provided in
the accessories box) will represent the main
spindle's plane of rotation.
NOTE
If you have installed casters (optional) on your
Mark V, make sure they are retracted and the legs
on the Mark V sit firmly on a level floor. Do this
now.
Tools Needed:
3/16" Allen wrench
5/32" Allen wrench, long handle (provided)
5/32" Allen wrench, short handle (provided)
5/16" Allen wrench (provided)
9/16" wrench
Arbor wrench (provided)
1/2" wrench
Adjustable wrench (optional)
1/2" socket/ratchet wrench w/short extension
3/8" to 1/2" drill bit
Small Straightblade screwdriver
Medium Straightblade screwdriver
Medium Phillips screwdriver
High quality combination square
Alignment of Mark V
Figure B-44
2. If there is "give" in the lock, unlock the handle
and use a medium Phillips screwdriver to
turn the lock shaft clockwise, as done by the
left hand in Figure B-44. If the lock is difficult
to operate, the shaft is too tight. To loosen,
unlock the handle and turn the shaft counter-
clockwise.
ADJUST THE CARRIAGE LOCK
3. If the carriage lock handle does not lock into
thehorizontalpositionorthecarriagemoves
out of position, the lock needs adjusting. To
adjust the lock, use a 1/2" socket with an
extension and ratchet handle to tighten or
loosen the nut located at the back of the
carriage assembly, as shown in Figure B-45.
Figure B-45

SM - 10
Summary Manual Mark V Model 520
8. Move the worktable into the 90° position by
loosening the table tilt lock, as seen in Figure
B-49, then putting the worktable in the hori-
zontal 90° position, as shown in Figure B-50.
Retighten the table tilt lock only enough to
allow movement with firm pressure.
4. When the carriage lock handle locks into the
horizontal position and the carriage no longer
moves when the handle is in the horizontal
position, tighten the nut a final 1/4 turn.
WARNING
The carriage lock handle MUST lock into the
horizontal position, otherwise the carriage lock
may vibrate loose.
SET THE WORKTABLE'S 90° LEFT STOP
WARNING
Always make sure the Mark V headstock and
carriage are locked and all casters are raised off
the floor before lifting the Mark V into the vertical
drill press position.
5. Unlock the carriage and headstock. Move the
headstock to the middle of the way tubes.
Then move the carriage between the head-
stock and base mount (right side).
6. Tightenthe headstockandcarriage locks. Place
the Mark V in the vertical position by loosen-
ing the headrest handle, firmly grasping the
way tubes near the headrest end, and lifting
the tubes into the 90° position, as demon-
strated in Figure B-46.
Figure B-51
Figure B-49
Figure B-50
Figure B-46
Figure B-47
7. See Figure B-47. Use your fingers to screw in
the base lock. Note the base lock is slightly
off center to the countersink found in the
bench base, as shown in Figure B-48. This
offset allows the base lock to more firmly
hold the base in place.
Figure B-48
9. Use a 5/32" Allen wrench to remove the table
insert, as demonstrated in Figure B-51.

Mark V 520 Summary Manual
SM - 11
10. To install the drill chuck, mount the chuck on
the spindle and align the chuck's set screw
with the spindle knob's set screw, as shown in
Figure B-52. This allows the chuck's set screw
to set on the flat part of the spindle. Use a 5/
32" Allen wrench to securely tighten the drill
chuck's set screw.
13. Set the combination square against the bit and
table, as shown in Figure B-55. The square
should contact the bit along its entire length.
When the table is exactly perpendicular to the
drill bit, lock the table, as seen in Figure B-56.
Figure B-52
Figure B-54
Figure B-53
11. Install a 3/8" to 1/2" straight drill bit in the
drill chuck and use the chuck key to lock it
place. See Figure B-53.
NOTE
Check the straightness of the drill bit by rolling it on
a flat surface. You can also hand-rotate the drill
chuck while holding the combination square against
the drill bit and the table. If the bit is not straight
DO NOT use it for these alignment instructions.
12. With the drill bit above the table opening, use
the quill feed to extend the bit 1/2" into the
table opening, as in Figure B-54.
Figure B-56
Figure B-55
14. Both 90° stops (shown in Figs. B-57 and B-58)
should contact the underside of the table. If
they don't, use a 1/2" wrench to adjust the
stops.
15. Recheck the setting by loosening the tilt lock,
moving the table, and then repeating Steps 13
and 14. (Rechecking the settings is very im-
portant!)
Figure B-57
Figure B-58

SM - 12
Summary Manual Mark V Model 520
d. Hold the arbor with an adjustable wrench
and tighten the arbor nut with the arbor
wrench, as demonstrated in Figure B-59d.
Another way to tighten the arbor nut is to
clamp the arbor in a bench vise, as illus-
trated in Figure B-59e, and tighten the nut
with the arbor wrench.
NOTE
The only time the saw blade is used without the
upper or lower saw guards is during alignment and
only after the Mark V is turned off and unplugged.
20. Mount the saw blade on the spindle and align
the arbor set screw with the spindle knob's set
screw,then use a 5/32" Allen wrenchtotighten
the arbor set screw, as seen in Figure B-60.
SET THE WORKTABLE'S 0° STOPSET THE WORKTABLE'S 0° STOP
SET THE WORKTABLE'S 0° STOPSET THE WORKTABLE'S 0° STOP
SET THE WORKTABLE'S 0° STOP
16. Remove the drill bit and drill chuck from the
spindle.
17. Loosen the base lock. Firmly grasp the way
tubes and lower the headstock into the hori-
zontal position, then engage the head rest.
18. Loosen the table tilt lock and place the table in
the horizontal "0" position. Retighten the table
tilt lock only enough to allow movement with
firm pressure.
19. Mount the saw blade on the arbor:
a. Remove the arbor nut by turning it clock-
wise, as seen in Figure B-59a. Hold the
arbor with the threaded part pointing to
the left.
Figure B-59e
Figure B-60
Figure B-59d
Figure B-59c
Figure B-59b
Figure B-59a
b. Hold the blade with the teeth pointing
toward you, as shown in Figure B-59b,
then insert the arbor through the hole.
Replace the nut and finger tighten it, as in
Figure B-59c.
c. Place the blade and arbor on your work-
bench with the nut pointing up.
21. Reinstall the table insert in the worktable.
22. Raise the worktable so that it clears the top of
the saw blade.
23. Loosen the carriage lock and slide the carriage
so the saw blade is directly beneath the slot in
the table insert. See Figure B-61.

Mark V 520 Summary Manual
SM - 13
24. Lower the worktable (but not all the way
down) so the saw blade comes through the
slot. Lock the table height, as seen in Figure B-
62.
25. Tighten the carriage lock, as shown in Figure
B-63.
26. Place the combination square against both the
saw blade and worktable, as seen in Figure B-
64. Make sure the square's blade does not
touch a saw tooth and does rest in a gullet
between teeth.
27. If the worktable is not exactly perpendicular
to the saw blade, adjust the worktable so it is
perpendicular to the saw blade, then tighten
the tilt lock.
28. To adjust the 0° stop, simultaneously depress
the table stop pin and use a 1/2" wrench to
adjust the stop bolt. The stop bolt should just
contact the side of the stop pin. Once the stop
bolt is adjusted, the stop pin will "lock" back
when the tilt lock is tightened. See Figure B-
65.
Figure B-61
Figure B-62
Figure B-63
Figure B-66
Figure B-65
Figure B-67
Figure B-64
29. Loosen the tilt lock, move the worktable, then
depress the 0° stop pin until the stop bolt
contacts it. Tighten the tilt lock, and recheck
the setting by repeating Steps 26 through 28.
See Figure B-66. (It is very important to re-
check the setting!)
ADJUST THE TABLE TILT INDICATOR
30. Tighten the table tilt lock and check that the
"0" mark on the indicator aligns with the "0"
mark on the trunnion.
31. To adjust the scale, use a medium Phillips
screwdriver to loosen the two screws which
hold the indicator to the tie bar. See Figure B-
67. Then while holding the indicator in posi-
tion so the "0"s are aligned, retighten the
screws.

SM - 14
Summary Manual Mark V Model 520
ADJUST THE WORKTABLE'S 45°
STOPS
32. Loosen the table height lock and raise the table
until it clears the saw blade. Tighten the
height lock.
33. Loosen the tilt lock and tilt the worktable to
the right until it makes contact with the two
45° stop bolts.
34. Tighten the tilt lock only enough to allow
movement with firm pressure.
35. Loosen the quill feed (shown in Figure B-68)
and extend the quill so the saw blade is cen-
tered beneath the slot in the table insert. When
it is centered, lock the quill feed. 38. If the worktable is not exactly 45° to the saw
blade, adjust the worktable so it is.
39. Tighten the tilt lock, then use a 1/2" wrench to
adjust the 45° stop on the front side of the
worktable (shown in Figure B-71) and the
back side of the worktable (shown in Figure B-
72). The stops should just contact the under-
side of the table.
40. Loosen the tilt lock and move the table. To
recheck the 45° stops, repeat Steps 35 through
39. (It is very important to recheck the set-
ting!)
ALIGN THE MITER GAUGE SLOTS
41. Return the worktable to the horizontal "0"
stop and tighten the tilt lock. The carriage lock
and headstock lock should also be tightened.
Remove the table insert.
42. Place the miter gauge in the right miter gauge
slot, and use a 5/32" Allen wrench to remove
the quick clamp from the safety grip, as shown
in Figure B-73.
36. Lower the worktable so the saw blade extends
through the slot. See Figure B-69. Lock the
table height.
37. Removethe bladefromthecombinationsquare
and place the square against the saw blade
and the worktable, as shown in Figure B-70.
Make sure the combination square doesn't
rest on the table insert.
Figure B-68
Figure B-69
Figure B-70
Figure B-71
Figure B-72
Figure B-73

Mark V 520 Summary Manual
SM - 15
44. Move the miter gauge from front to back
along the saw blade, as shown in Figs. B-75
and B-76. If it hangs up on the blade or a gap
develops, the miter gauge slots need to be
aligned. Make sure the Allen wrench does not
contact a saw blade tooth, because the tooth
"set" will cause misalignment.
43. Insert the long 5/32" Allen wrench through
the miter gauge. Borrow a set screw from the
lathe tool rest and use the short 5/32" Allen
wrench to install it in either top miter gauge
hole, as seen in Figure B-74. Place the tip of the
long wrench against the front side of the saw
blade and tighten the set screw.
45. If the miter slots need to be aligned, do the
following:
a. Tilt the table to 45° and tighten the tilt lock.
b. Use a 5/16" Allen wrench to loosen all four
bolts (147) which hold the worktable to the
trunnions, as pointed out in Figure B-77.
Loosen the bolts only enough to allow
movement with firm pressure. See Figure
B-78.
NOTE
If you find it difficult to loosen the bolts, consider
using a T-handle Allen wrench, or use a boxed
wrench for extra torque. Another alternative is to
use the hanging hole in an adjustable wrench, as
demonstrated in Figure B-78a.
Figure B-74
Figure B-76
Figure B-78
Figure B-75
Figure B-77
c. Position the worktable back to the hori-
zontal "0" and tighten the tilt lock.
c. Position the worktable back to the hori-
zontal "0" and tighten the tilt lock.
d. Adjust the worktable, then again move the
miter gauge and wrench along the face of
the saw blade until the wrench tip consis-
tently contacts the entire blade surface.
e. When the miter gauge slot is aligned, use
the 5/16" Allen wrench to retighten the
two trunnion bolts which are closer to the
headstock. Then loosen the table tilt lock,
tilt the worktable to 45°, and retighten the
table tilt lock. Use the 5/16" Allen wrench
to retighten the other two trunnion bolts.
f. Loosen the table tilt lock and move the
table, then return it to the horizontal "0"
position. Recheck the slot alignment. If it
is off, repeat Steps dand e.
NOTE
Tighten the bolts only after the table tilt lock is secured.
Otherwise the worktable will bow or bind the next time
the table tilt lock is tightened.
Figure B-78a

SM - 16
Summary Manual Mark V Model 520
INSTALL THE TABLE INSERT IN THE
WORKTABLE
46. Place the table insert in the worktable recess.
Use a 5/32" Allen wrench to start both screws.
47. First tighten the rear screw. Then the front of
the insert will be sprung slightly above the
table. Level the insert by placing your hand on
the front of the insert, as in Figure B-79, and
slowly turning the front screw until it draws
the front of the insert flush with the worktable
surface.
ADJUST THE MITER GAUGE FACE
51. Remove the safety grip from the miter gauge.
Make sure you keep the small, thin washer.
52. Put the miter gauge in the right slot and place
the combination square against the saw blade
and miter gauge face, as seen in Figure B-82.
ADJUST THE MITER GAUGE GLIDES
48. Place the miter gauge in the worktable's miter
gauge slot. See Figure B-80.
Figure B-79
Figure B-80
Figure B-81
53. If the miter gauge face is not perpendicular
to the saw blade, do the following:
a. Use a long Allen wrench to loosen the
lock knob (268) and adjust the miter
gauge so it is perpendicular to the saw
blade, then tighten the lock knob. See
Figure B-83.
Figure B-83
Figure B-84
Figure B-82
b. Use a medium screwdriver, loosen the
screw(273) which holds the indicator plate
(275 ), and set its "0" to the miter gauge's
"90". Tighten the screw. See Figure B-84.
49. Check to see if the miter gauge wobbles side-
to-side. Also, slide it back and forth in the slot
to check if the miter gauge scrapes against the
table. If the miter gauge rocks or scrapes the
table, adjust the glides.
50. If the glides need to be adjusted, do the follow-
ing:
a. Remove the miter gauge from the slot and
turn it over.
b. Use a medium screwdriver to screw the
glides in or out, as illustrated in Figure B-
81, so that the glides hold the miter gauge
1/64" to 1/32" off the worktable and the
miter gauge does not rock in the slots.
c. Return the miter gauge to the slot and
recheck and re-adjust it, if needed.

Mark V 520 Summary Manual
SM - 17
ADJUST THE 90° POSITIVE STOP
54 Use a small screwdriver to back out the 90°
stop screw 2 to 3 turns, as shown in Figure B-
85.
Figure B-85
55. Depress the plunger, then turn the stop screw
until you feel it touch the plunger.
56. To re-check the stop setting, repeat Steps 52
through 55.
ADJUST BOTH 45° STOPS
57. Loosenthe lock knob and pull out theplunger.
Then, at the same time, rotate the miter gauge
and push in the plunger until it hits the 45°
stop (there is one on each side of the 90° stop).
58. Use a combination square to set the miter
gauge face at 45° to the saw blade. If the 45°
stop needs adjustment, use a medium screw-
driver to back out the 45° screw 2 to 3 turns.
59. Depress the plunger, then turn the stop screw
until you feel it touch the plunger.
60. To recheck the stop setting, repeat Steps 54
through 59.
61. To adjust the other 45° stop, repeat Steps 57
through 60.
REMOVE THE SAW BLADE
62. Loosen the table height lock and raise the table
so that it clears the saw blade, then tighten the
lock. Unlock the carriage lock and move the
worktable to the right.
63. Use the 5/32" Allen wrench to loosen the
arbor set screw. Remove the saw blade.
64. Unlock the table height lock and lower the
tabletoa comfortable working height. Tighten
the lock.
ALIGN THE PRO FENCE PARALLEL
WITH THE WORKTABLE
55. Place the miter gauge in the left slot of
the worktable on the infeed side. Place
the Pro Fence on the right side of the saw
table.
56. Insert the long 5/32" Allen wrench
through the miter gauge and secure it
using the short 5/32" Allen wrench and
a set screw borrowed from the tool rest.
57. Move the fence toward the Allen wrench
until it just touches it.
58. Lock the lower fence lock handle first,
then lock the upper fence lock handle to
secure both ends of the pro fence.
59. Slide the miter gauge back and forth in
the slot. The tip of the Allen wrench
should keep in slight contact with the
fence. Watch that you don't scratch the
fence.
60. If the allen wrench pulls away from or
binds against the fence, the fence needs
aligning. If so, do the following:
a. Using the short 5/32” short Allen
wrench, loosen the four button head
cap screws (3), located on the top of
the fence, slightly. They should be
justtight enoughtorequire firmpres-
sure to align the fence.
b. Raise the upper fence lock handle
only to unlock the rear of the fence.
c. Adjust the rear end of the fence so
that it just touches the allen wrench
as the miter guage slides along the
fence.
d. When alignment is reached, lock the
upper fence lock handle. Slide the
mitergaugeback and forth to double
check your alignment. Using the
short 5/32” Allen wrench, tighten
the four button head cap screws (3)
completely.

SM - 18
Summary Manual Mark V Model 520
Figure B-108
Figure B-106
Figure B-107
MOUNT THE SAW GUARD
63. Loosen the accessory mount lock and remove
the extension table. Loosen the table height
lock and remove the worktable. Place the
saw blade and arbor in the lower saw guard
cover.
65. Use the 5/32" Allen wrench to tighten the
socket head screw on the saw guard collar,
as seen in Figure B-107.
INSTALL THE RIVING KNIFE
Figure B-110
Figure B-109
Figure B-99
62. The worktable should already be mounted
in the carriage mount. Move the worktable
next to the extension table and adjust it to
about 1/4" above the extension table, as
seen in Figure B-100.
ALIGN THE EXTENSION TABLE
NOTE
These instructions are for aligning the extension
table on the right side of the headstock. You can
also follow these same procedures to align it to the
left side of the headstock.
For most projects, align the extension table on the
right side, since it can usually be used when placed
on the left side. However, once the extension table
is aligned on the right side, it cannot be transferred
to the left side and still maintain precise alignment.
If you wish precise alignment on the left side, repeat
the following instructions– but place the extension
table on the left side in the headstock.
61. Mount the extension table in the Mark V's
accessory base mount (on the right side) at a
comfortable height, as shown in Figure B-
99. Use a 1/2" wrench to loosen the bottom
nuts holding the table base to the table ap-
proximately 1/4" from the table. This will
allow you room for later adjustment.
Figure B-100
66. Loosen the guard
lock knob and in-
sert the upper saw
guard's riving
knife between the
guardand the lock
plate, as demon-
stratedin FigureB-
108.
67. Make sure the riving knife is fully seated
between the guard and the lock plate, as in
Figure B-109. The curved portion of the
riving knife should be very close to the saw
blade teeth (about 1/8"), as illustrated in
Figure B-110. Tighten the guard lock knob.
Look to see if the riving knife is centered
with the saw blade, as shown in Figure B-
111.
64. Fit the lower saw guard's clamp on the spindle
quill. Line up the arbor set screw with the
spindle knob's set screw (where the spindle
flat is located). Use a 5/32" Allen wrench to
tighten the arbor set screw, as shown in
Figure B-106.

Mark V 520 Summary Manual
SM - 19
Figure B-112
Figure B-111
68. If the riving knife is not centered with the
saw blade, follow these steps:
a. Notice which way the riving knife is not
centered with the saw blade.
b. Unclamp and remove the upper saw guard,
then remove the saw blade and lower saw
guard.
c. Use a 5/32" Allen wrench to adjust the stop
screw located below the lower saw guard's
collar, as seen in Figure B-112.
• If the riving knife is to the left of the
saw blade, back out the stop screw
(counter-clockwise).
• If the riving knife is to the right of the
saw blade, screw in the stop screw
(clockwise).
d. Re-install the saw blade, lower saw guard
and riving knife. MAKE SURE the riving
knife is still centered on the saw blade.
ALIGN THE LATHE CENTERS
59. Remove the saw guards and the saw blade,
thenloosen the carriage and headstock locks.
Move the headstock and carriage all the way
to the right and lock them in place.
60. Mount the drill chuck on the spindle, as
shown in Figure B-113. Completely close
the chuck jaws, as in Figure B-114.
Figure B-117
Figure B-116
Figure B-115
Figure B-113
Figure B-114
61. Mount the cup center into the tailstock's
adjustable center, as seen in Figure B-115,
then mount the tailstock into the base mount
(right side). Tighten the mount lock.
62. Loosen the quill lock. Extend the quill (seen
in Figure B-116), so the drill chuck almost
touches the cup center point and the center
point could fit into the chuck jaws.
63. If the center point does not "fit" into the
chuck jaws, determine whether you need to
adjustthe cup center point horizontally and/
or vertically. Then do the following:
a. To adjust the cup center point horizon-
tally, loosen the set screw that locks the
adjustable center, as seen in Figure B-117.
Rotate the adjustable center as needed to
line up the cup center with the drill chuck,
then tighten the set screw.
b. To adjust the cup center point verti-
cally, loosen the mount lock, then loosen the
tailstock stop collars. Raise or lower the
tailstock in the base mount until the cup
center point vertically lines up with the drill
chuck, then tighten the mount lock. Press
the stop collars down firmly against the base
mount and tighten the collar set screws.

SM - 20
Summary Manual Mark V Model 520
The Mark V Model converts to five modes– table
saw, disc sander, drill press, horizontal boring,
and lathe.
NOTE
These Mode Setup procedures assume that there is
nothing mounted to any spindle and all alignments
and adjustments have been completed.
One of the most useful features about the Mark V
is that you can "borrow" angles and setups from
one mode to the other. This greatly improves the
accuracy of your woodworking.
To "borrow" a setup, don't break down the ma-
chine completely as you change from mode to
mode. For example, if you need to cut a miter,
sand it smooth, and then bore for dowels, keep
the table and the miter gauge in the same position
as you move from table sawing to disc sanding to
horizontal boring. This will ensure that your
stock is cut, sanded, and bored precisely the
same. It also saves you setup time.
As you change from one mode to another, keep
these four safety rules in mind:
1. Turn the speed dial to "Slow," then turn off
and unplug the Mark V before you break
down one mode and set up another. Al-
ways have the speed dial set to "Slow." It is
dangerous for both you and your electrical
circuit to start accessories at high speed (i.e.,
the sanding disc can blow fuses at table saw
speed and the lather will throw stock at
rout-shape speed).
2. Make sure that accessories are properly
mounted on the main spindle. The flat on
the main spindle is ground with a "reverse
taper" to keep accessories secured.
a. To properly mount an accessory,
push it onto the main spindle all the way.
Then use a 5/32" Allen wrench to tighten the
setscrew against the flat of the spindle. (See
Figure B-119.) To make sure the accessory is
securely mounted, rock the accessory back
and forth slightly as you tighten the set-
Figure B-119
Mode Setups
screw and then again after it is tight, while
keeping the spindle from turning. If the
accessory seems to loosen, tighten the set-
screwagain untilyou'veremoved any"play."
3. Check all locks before turning on the ma-
chine. To properly secure a lock, spin it until
it stops, then tighten it an extra 1/4 turn.
CAUTION
Be careful not to overtighten locks. Overtightening
locks may damage the way tubes, table support tubes,
or other parts of the machine.
To be sure all locks are as they should be, make a
five-point check before you turn on the Mark V.
With a clockwise sweep of your hand, check each
of these locks in succession: table tilt lock, car-
riage lock, table height lock, headstock lock, and
quill lock. See Figure B-120. The carriage lock
handle must be secured in the horizontal posi-
tion. The quill lock should be loose in the drilling
and boring modes, and for some sanding opera-
tions. In the lathe mode, this procedure becomes
a four-point check, since the table has been re-
moved.
Reverse
taper
Set-
screw
Carriage
Lock
Table height
Quill lock
Head-
stock
Table tilt lock
Figure B-120
When changing from a horizontal to a vertical
position, secure the base lock. When changing
from vertical to horizontal, secure the headrest
lock. If you're mounting accessories in the power
mount or base mount, secure the mount locks.
Table of contents
Popular Tools Storage manuals by other brands

DIVERSIFIED WOODCRAFTS
DIVERSIFIED WOODCRAFTS 0313-W-7230L Assembly instructions
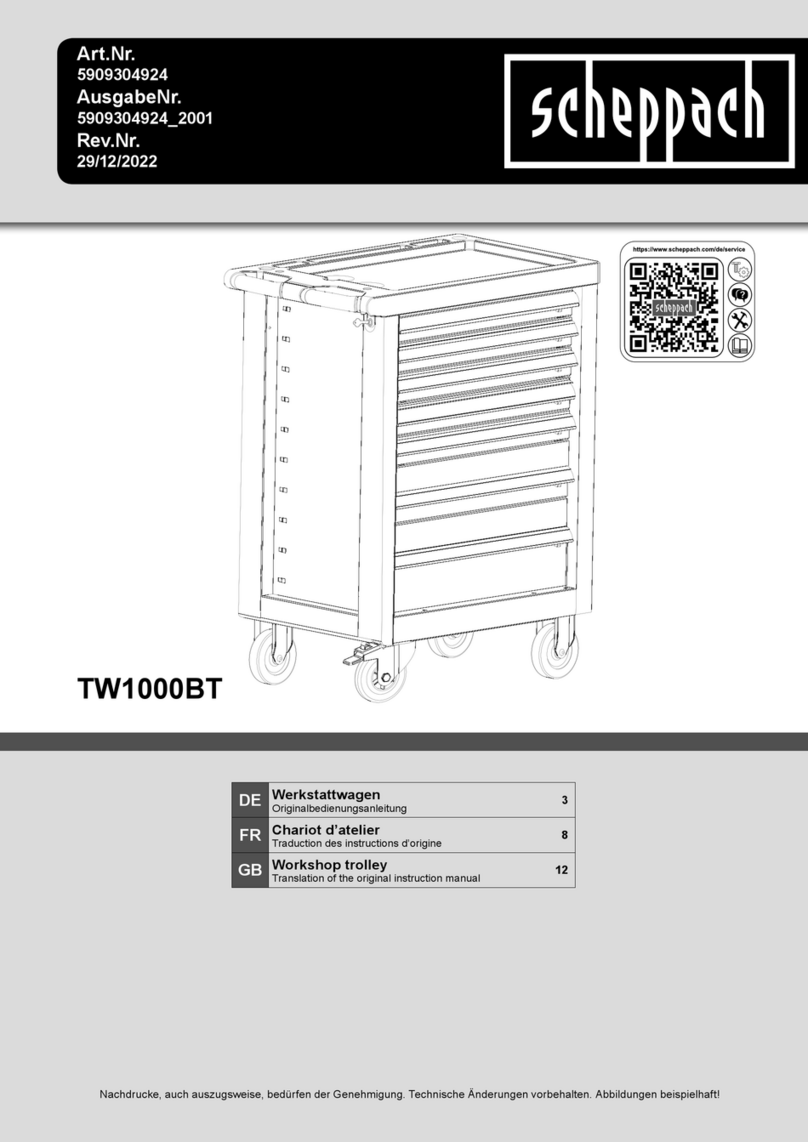
Scheppach
Scheppach TW1000BT Translation of the original instruction manual
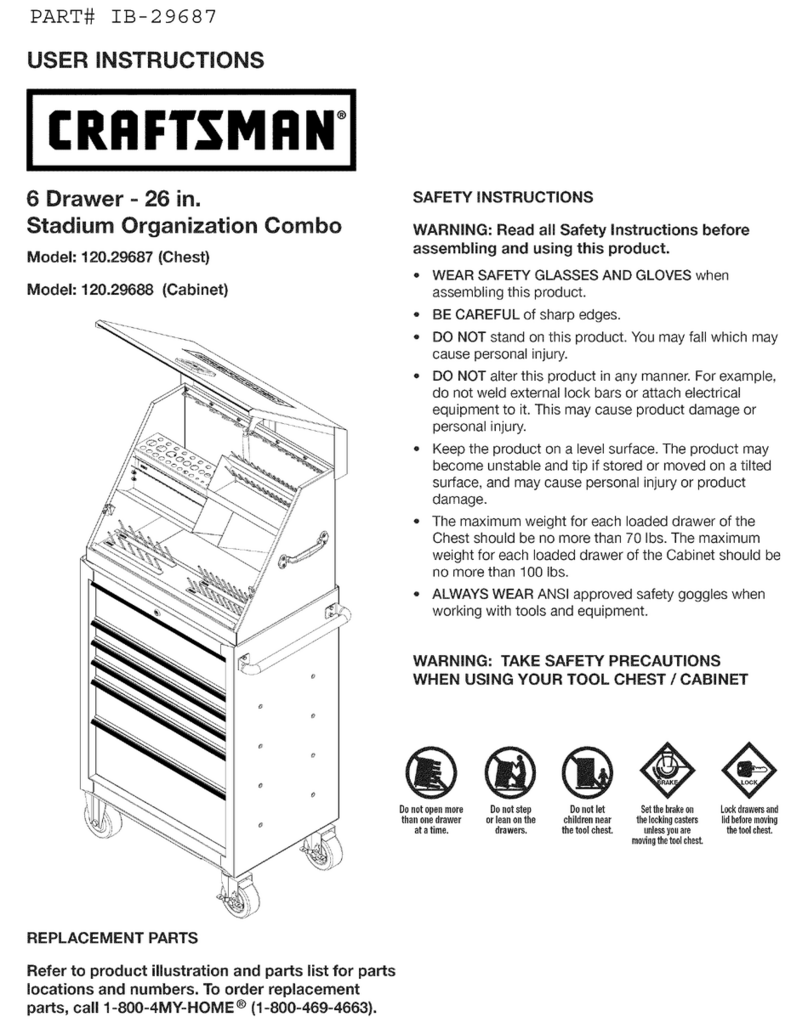
Craftsman
Craftsman 120.29687 User instructions
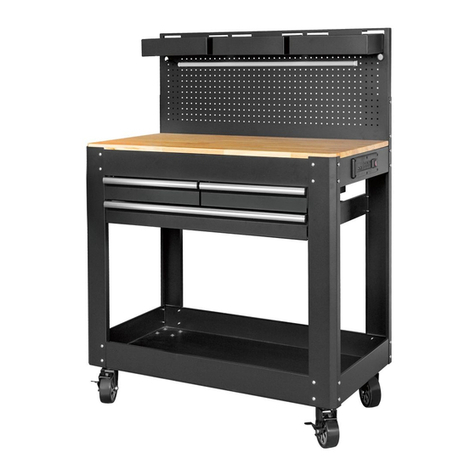
Husky
Husky TSA4524 Use and care guide
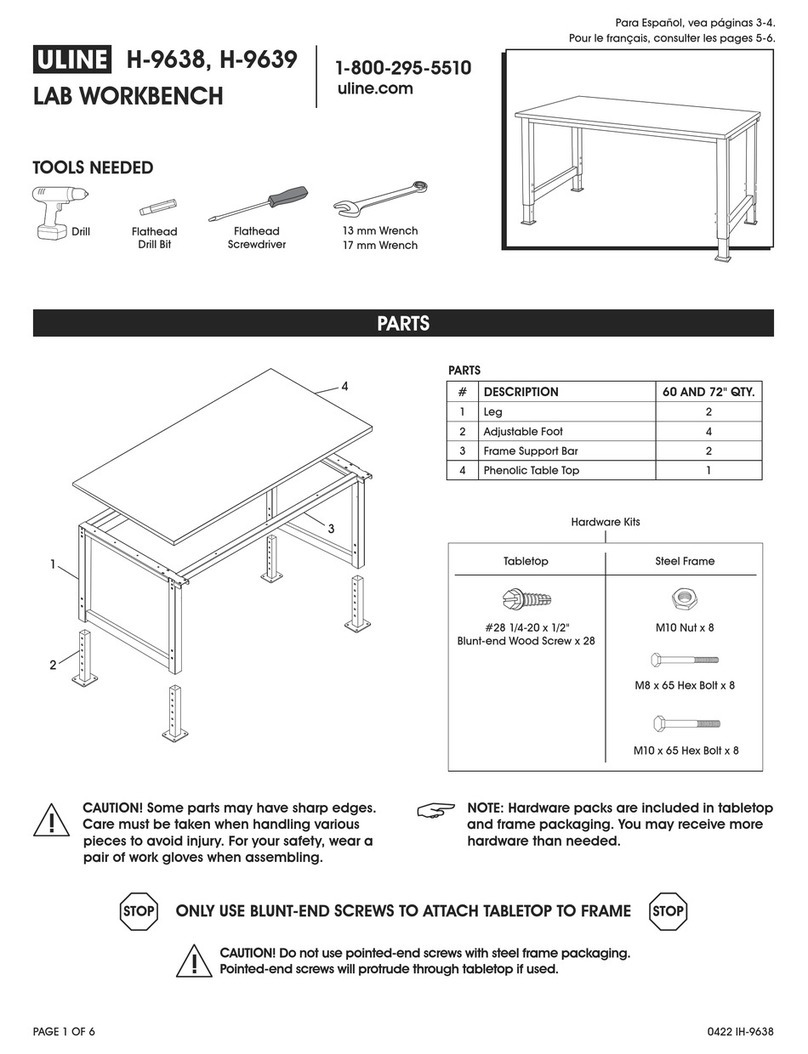
U-Line
U-Line H-9638 Assembly instructions
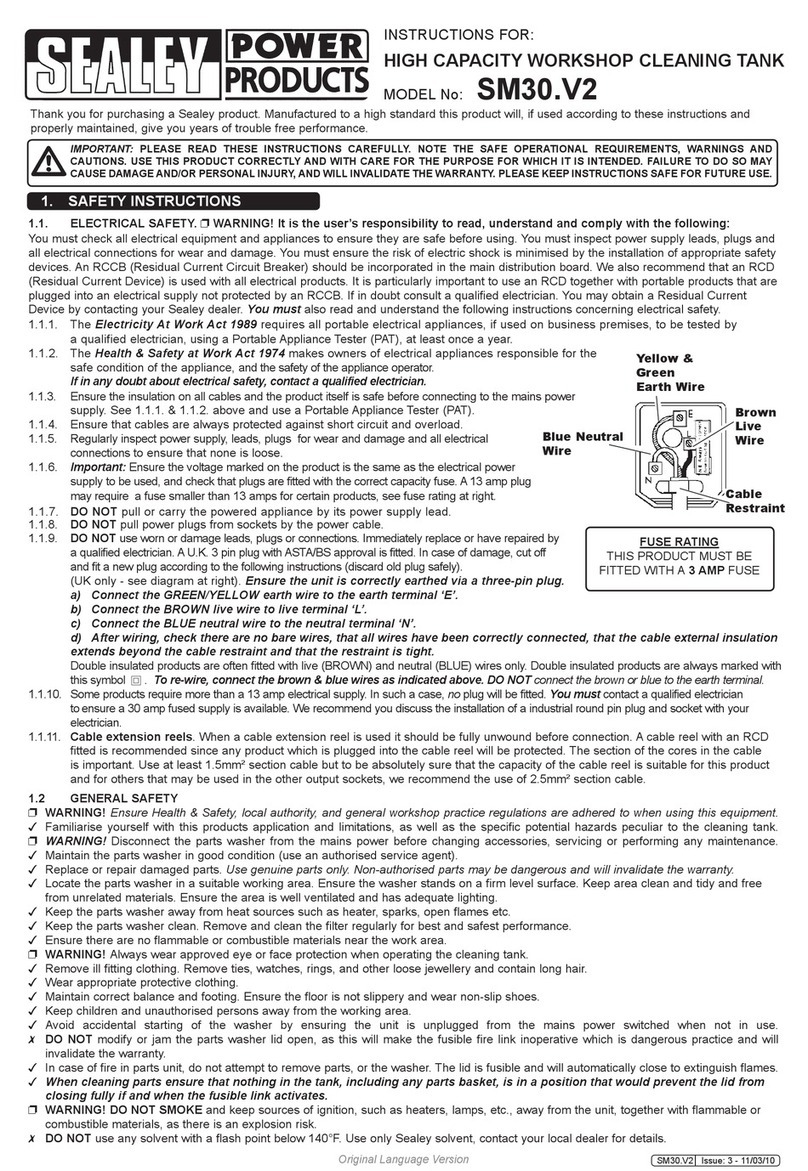
Sealey
Sealey SM30.V2 instructions