SICK IVP Ruler E User manual

REFERENCE MANUAL
Ruler E
Reference Manual

Please read the complete manual before attempting to operate your Ruler.
WARNING
%Laser radiation
$Avoid direct exposure to the beam
$Avoid direct eye exposure
The Ruler is a laser product and operation using procedures other than those specified
herein may result in hazardous radiation exposure.
Do not open the Ruler
The Ruler unit should not be opened, the Ruler contains no user serviceable parts inside.
Opening the ruler unit may result in hazardous radiation exposure.
Turn off the laser power to the Ruler before maintenance
The power to the laser in the Ruler must be turned off before any maintenance is per-
formed. Failure to turn this power off when maintaining the unit may result in hazardous
adiation exposure.r
Please read and follow ALL Warning statements throughout this manual.
Windows and Visual Studio are registered trademarks of Microsoft Corporation.
All other mentioned trademarks or registered trademarks are the trademarks or registered trademarks of their
respective owner.
© SICK IVP 2005-11-22
All rights reserved
Subject to change without prior notice.

Reference Manual
Ruler E
Contents
Contents
1Overview......................................................................................................................................... 5
1.1 Configuration Using Ranger Studio......................................................................................... 7
1.2 Measurement Methods........................................................................................................... 8
1.2.1 Range Resolution....................................................................................................... 9
1.2.2 Performance............................................................................................................. 10
1.3 Developing Applications ........................................................................................................11
1.4 Triggering ...............................................................................................................................12
2Laser Safety .................................................................................................................................13
2.1 Laser Safety Classification .................................................................................................... 13
2.1.1 Classification............................................................................................................ 13
2.2 Installation Considerations ...................................................................................................14
3Configuring the Ruler..................................................................................................................15
3.1 Configuration Hierarchy.........................................................................................................18
3.2 Ethernet Configuration ..........................................................................................................18
3.3 System Configuration ............................................................................................................18
3.4 Image Configuration ..............................................................................................................19
3.5 Measurement Configuration .................................................................................................20
3.6 Measurement Components ..................................................................................................21
3.6.1 Horizontal Threshold (HorThr) .................................................................................22
3.6.2 Horizontal Max (HorMax) .........................................................................................24
3.6.3 Horizontal Max and Threshold (HorMaxThr) ...........................................................25
3.6.4 Hi-res 3D (Hi3D) .......................................................................................................26
3.7 Details on 3D Profiling Algorithms ........................................................................................27
4Ranger Studio..............................................................................................................................31
4.1 Ranger Studio Main Window................................................................................................. 31
4.2 Visualization Windows...........................................................................................................32
4.2.1 Zoom in Visualization Windows...............................................................................33
4.3 Parameter Editor ...................................................................................................................34
4.4 Using Ranger Studio ..............................................................................................................35
4.4.1 Connect and Get an Image...................................................................................... 35
4.4.2 Adjust Exposure Time ..............................................................................................35
4.4.3 Set Region-of-Interest ..............................................................................................36
4.4.4 Collection of 3D Data............................................................................................... 37
4.4.5 Getting a Complete Object In One Image ...............................................................38
4.4.6 Save Visualization Windows ....................................................................................38
4.4.7 Save and Load 3D Data...........................................................................................39
5Ruler API ......................................................................................................................................40
5.1 Connecting to the Camera ....................................................................................................40
5.2 Retrieving Measurement Data.............................................................................................. 41
5.3 Changing Camera Configuration...........................................................................................44
5.4 Transforming Measurement Values .....................................................................................44
5.5 Field-of-View...........................................................................................................................46
5.6 Rectifying Measurement Values ...........................................................................................47
SICK IVP • Industrial Sensors • www.sickivp.com • All rights reserved 3

Reference Manual
Ruler E
Contents
6Examples ..................................................................................................................................... 48
6.1 ruler_ex.....................................................................................................................................48
6.2 RulerNetConsoleExample......................................................................................................50
7Hardware Description .................................................................................................................52
7.1 Measurement Set Up ............................................................................................................ 52
7.2 Electrical Connections........................................................................................................... 54
7.3 Technical Data ....................................................................................................................... 56
7.4 Dimensional Drawings...........................................................................................................57
Appendix ............................................................................................................................................58
ARuler E Models and Type Codes ...........................................................................................58
BRecommended Network Cards ............................................................................................. 59
CRecommended Switches....................................................................................................... 60
DiCon Device Configuration.....................................................................................................60
EEncoder Wire Diagram...........................................................................................................61
FLaser Safety Box .................................................................................................................... 64
4SICK IVP • Industrial Sensors • www.sickivp.com • All rights reserved

Reference Manual Chapter 1
Ruler E
Overview
1Overview
The Ruler measures the shape of object by using laser triangulation, which means that it
analyzes images of the object as it passes under a laser line. Each image shows the laser
as a cross-section of the object viewed from an angle. Since the optics in the camera is
mounted at a fixed distance and angle from the laser, the height of each point of the
cross-section can be calculated by detecting the laser in the image.
Depending on the model of the Ruler, it can make two or three different types of meas-
urements:
Range Measures the height of the object along the laser line.
Intensity Measures the amount of light that is reflected by the object along the
laser line.
Scatter Measures how the incoming laser light is distributed beneath the surface
of the object. This is useful for example for finding the orientation of fibers
in wood. (Only available for Ruler with the scatter option.)
Figure 1.1 – Measuring a cross-section of an object in 3D
Profile
SICK IVP • Industrial Sensors • www.sickivp.com • All rights reserved 5

Chapter 1Reference Manual
Ruler E
Overview
The result from measuring one cross-section of the object – the measurement data – is
collected into a profile. These profiles are sent to a computer connected to the camera
through an Ethernet network. The computer runs a custom application that takes care of
the profiles from the camera. This application can for example analyze the data to find
defects in the objects and control a lever that pushes faulty objects to the side.
Before the Ruler can be put into production you must write such an application. It is devel-
oped in for example Microsoft Visual Studio, using one of the APIs delivered with the
software for the camera.
Figure 1.2 – Profiles are sent from the Ruler to a PC, where they are analyzed by a custom
application.
Note that the output from the camera is not actual images of the object, but a set of
height, intensity or scatter values – one value for each point along the cross section of the
object. If desired, these measurements can be visualized as a profile plot showing the
shape of the cross section, or – by combining several profiles – as a complete 3D image of
the object.
6
SICK IVP • Industrial Sensors • www.sickivp.com • All rights reserved

Reference Manual Chapter 1
Ruler E
Overview
1.1 Configuration Using Ranger Studio
Before the data from the Ruler can be used in an application, the Ruler should be config-
ured to deliver profiles with sufficient quality and speed. This is usually done by setting up
the camera in a production-like environment and evaluating different measurement meth-
ods and parameter settings until the result is satisfactory.
The Ranger Studio application that is delivered with the Ruler can be used for evaluating
different set-ups of the camera. With Ranger Studio, you can change the settings for the
camera and instantly see how the changes affects the measurement result from the Ruler.
Once the Ruler has been set up to deliver measurement data that meets the require-
ments, the settings can be saved in a parameter file from the Ranger Studio. This parame-
ter file is later used when connecting to the Ruler from the application to be developed.
Figure 1.3 – Configuring the Ruler with Ranger Studio.
SICK IVP • Industrial Sensors • www.sickivp.com • All rights reserved 7

Chapter 1Reference Manual
Ruler E
Overview
1.2 Measurement Methods
When configuring the Ruler for measurement, you can choose any of the camera’s built-in
measurement methods – or components:
HorThr Horizontal threshold, a fast method for measuring range values using one
or two thresholds.
HorMax Horizontal max, measures the maximum intensity of the laser, and de-
termines the position of the maximum intensity.
HorMaxThr Horizontal max and threshold, measures range values using one thresh-
old, and measures the maximum intensity of the laser.
Hi3D High-resolution 3D, measures range values with high resolution, as well
as the maximum intensity. Can also measure scatter when used with a
Ruler with Scatter option.
Figure 1.4 – Threshold locates the laser in each column of the sensor image by searching
for intensities above a certain level, while Max searches for the maximum intensity in each
column.
Which component to use is of course depending on what to measure – range, intensity or
scatter – but also on the required speed and resolution of the measurements, as well as
the characteristics of the objects to measure and the conditions in the environment.
For each measurement method, there are a number of parameters that can be changed
for further fine-tuning the quality and performance of the measurements. These parame-
ters specifies for example exposure time and in which area of the image to search for the
laser line.
Columns
Rows
Projected
laser line
Sensor image
Columns
Columns Threshold
Max
Rows
Rows
Intensity
Intensity
HorThr HorMax
8SICK IVP • Industrial Sensors • www.sickivp.com • All rights reserved

Reference Manual Chapter 1
Ruler E
Overview
1.2.1 Range Resolution
When measuring heights, the resolution depends on which algorithm that is used when
detecting the laser line. For example the HorMaxThr method returns the location of the
line with 1/2 pixel resolution, while the Hi3D method has a resolution of 1/16th of a pixel.
Besides the measurement method, the actual measurement accuracy in millimeters
depends on the distance between the Ruler and the object. The further away the object,
the lower the accuracy.
This is because the object is viewed from a perspective, and therefore a pixel at the bot-
tom of the image shows a larger area of the object than pixels at the top of the image.
Therefore, one way of increasing the accuracy in the measurements is to move the Ruler
closer to the objects to measure.
Figure 1.5 – The laser line seen from a perspective, on the sensor, and the resulting
profile
Millimeters
V
iewed from
the Ruler
(world)
Millimeters
Columns
Rows
Sensor image
Range
(mm)
Resulting
Profile
Width
(
mm
)
SICK IVP • Industrial Sensors • www.sickivp.com • All rights reserved 9

Chapter 1Reference Manual
Ruler E
Overview
1.2.2 Performance
The performance of the Ruler – that is, the maximum number of profiles it can deliver
each second – depends on the chosen measurement method, but also on the size of the
sensor image in which to search for the profile. The larger the image, the longer it takes to
search.
Therefore, one way of increasing the performance of the Ruler is to use a smaller part of
the sensor.
Figure 1.6 – A small image may be faster to analyze than a high
Note that the maximum usable profile rate is usually limited by the characteristics of the
object’s surface and conditions in the environment.
10 SICK IVP • Industrial Sensors • www.sickivp.com • All rights reserved

Reference Manual Chapter 1
Ruler E
Overview
1.3 Developing Applications
Once the quality of the measurement data is sufficient, you need to write an application
that takes care of the measurement data, analyzes it and makes the decisions based on
the measurements. This application is developed in Visual Studio 7, using one of the APIs
that are delivered with the Ruler.
There are two APIs included with the development software for Ruler, to be used in Visual
Studio: RulerNet API for use with.Net, and Ruler C++ API for use with C++. Both APIs
contain the same functions but differ in the syntax.
The APIs handles all of the communication with the Ruler, and contain functions for:
$retrieving profiles from the Ruler
$starting and stopping the Ruler
$changing Ruler configuration
Most of these functions are encapsulated in a Ruler class, and your application estab-
lishes contact with the Ruler camera by creating a Ruler object.
When the Ruler is measuring, it will send a profile to the PC as soon as it has finished
measuring a cross-section. On the PC, the profiles are collected and placed in a buffer by
the Ruler object. When your application needs measurement data, it requests data from
the Ruler object, which will then return a full buffer of profiles.
Figure 1.7 – All communication with the Ruler is handled by the API. Your application
retrieves buffers of profiles from a Ruler object.
Your application can specify the size of the buffers, and it is possible to set the buffer size
to 1 in order to receive one profile at a time. However, this will also add overhead to the
application, and put extra load on the CPU.
The profiles that your application receives are calibrated – that is, the measurement
values are given in a metric coordinate system local to the Ruler. You can translate these
measurement values to a different coordinate system by setting a Transformation for the
Ruler object in your application.
This could be useful for example if you have several Rulers mounted around a conveyor
belt where the objects are passing by. By setting transformations for each Ruler, your
application will receive all measurements given in a common coordinate system, relieving
your application from having to recalculate each value itself.
Profiles
request()
Ruler API
Application
buffers
Control
SICK IVP • Industrial Sensors • www.sickivp.com • All rights reserved 11

Chapter 1Reference Manual
Ruler E
Overview
1.4 Triggering
The Ruler can be triggered by external signals in two different ways:
Enable Triggers the Ruler to start measuring a series of profiles. As long as
the Enable signal is low, the Ruler will not measure anything. This sig-
nal could for example come from a photo switch located along the
conveyor belt.
The Enable signal is also useful for synchronizing two or more Rulers.
Pulse triggering Triggers the Ruler to measure one profile. This signal could for exam-
ple come from an encoder on the conveyor belt.
Figure 1.8 – Triggering the Ruler with Enable and Pulse triggering signals.
The Ruler must be configured to use these external signals for triggering. This is done by
setting the Enable and Trig mode parameters with Ranger Studio.
If pulse triggering is not used for triggering profiles, the Ruler will measure in free-running
mode – that is, make measurements with a regular time interval determined by the Ruler’s
cycle time. The actual distance on the object between two profiles is then determined by
the speed of the object – that is, how far the object has moved during that time.
When measuring the true shape of an object, you should always use an encoder with the
Ruler. With the signals from the encoder as pulse triggering signals, it is guaranteed that
the distance that the object has moved between two profiles is well known.
You can find the actual distance between two profiles even if the Ruler is measuring in
free-running mode, as long as you have an encoder connected to the Ruler. The encoder
information can then be embedded in the profiles sent to the PC, where your application
can use this information to calculate the distance.
Enable
Profiles
Pulse
triggering
12 SICK IVP • Industrial Sensors • www.sickivp.com • All rights reserved

Reference Manual Chapter 2
Ruler E
Laser Safety
2Laser Safety
The Ruler E is an OEM component.
When the Ruler is incorporated into any machine or installation several laser safety re-
quirements must be fulfilled.
2.1 Laser Safety Classification
The United States Center for Devices & Radiological Health (CDRH) enforces strict safety
requirements for lasers and laser products.
Recommended reading: Laser Institute of America Laser Safety Guide.
Since the Ruler unit is intended to be incorporated into a measurement system, where it
may be partially hidden, it is important to understand the safety issues regarding laser
systems. This is so that the complete installation can be performed in accordance with the
laser safety regulations.
The CDRH classifies lasers into several categories, and the regulations regarding the two
classes applicable to Ruler systems are given here.
2.1.1 Classification
The classification is based on the laser power measured in a certain way (for complete
information, please refer to http://www.fda.gov/cdrh).
For the Ruler this corresponds to the maximum light power measured through a 7 mm
aperture 100 mm away from the laser aperture.
The limitations for the classification of the laser classes is then
$Class II / 2M 1 mW
$Class IIIb / 3B 500 mW for emission duration ≥0.06 sec
Class II / 2M – "Caution"
This applies to Ruler E 600/1200 (II / 2M laser)
Considered eye-safe with caution, but may
present a greater hazard if viewed using
collecting optics. Focusing of this light into
the eye could cause eye damage.
Class II / 2M laser products must bear
warning and certification labels.
Class IIIb / 3B – "Danger"
This applies to the Ruler E 600/1200 B (IIIb / 3B laser)
Considered dangerous to your retina if
exposed. This includes looking directly into
a reflection from a specular (mirror-like)
surface. Normally, class IIIb / 3B lasers
will not produce a hazardous diffuse
reflection. Certification is given on prod-
ucts that have a key box and remote
interlock connector.
Class IIIb / 3B laser products must bear
warning and certification labels.
SICK IVP • Industrial Sensors • www.sickivp.com • All rights reserved 13

Chapter 2Reference Manual
Ruler E
Laser Safety
2.2 Installation Considerations
Class II / 2M
$Laser warning and aperture labels in conformance with the labels below should be
present on the complete system.
$If possible the laser radiation from the laser should be terminated with a diffuse reflect-
ing material.
$Eye protection – during installation and alignment operations appropriate eye protec-
tion should be used. The eye protection should be designed to reduce the laser power
in the wavelength region 600-700 nm. If uncertain, contact SICK IVP for information
regarding acquisition of such eye protection.
$Visible and/or audible indication of operation of the laser (Ruler) should be present in
the installation. The indication should be activated before the Ruler is powered on.
$A beam attenuator, which reduce the laser emission down to class I limits should be
present in the system.
Lack of beam attenuator and emission indicator is accepted by CDRH according to "Guid-
ance on Laser Products - Conformance with IEC 60825-1, Am. 2 and IEC 60601-2-22
(Laser Notice No. 50)".
Class IIIb / 3B
In addition to the considerations for class III/2M lasers, the following also applies:
$A key-box with a removable key must be present in the system. Without the key it
should not be possible to power-on the laser unit of the Ruler.
$Remote interlock connector – a connector readily available for connecting a remote
emergency stop or remote barrier interlock.
The remote interlock connector having an electrical potential difference of no greater
than 130 root-mean-square volts between terminals. When the terminals of the con-
nector are not electrically joined, no human access to laser radiation from the laser
product in excess of the accessible emission limits of Class I is possible.
Figure 2.1 – Placement of the laser warning and certification labels
Class II / 2M
Class IIIb / 3B
14 SICK IVP • Industrial Sensors • www.sickivp.com • All rights reserved

Reference Manual Chapter 3
Ruler E
Configuring the Ruler
3Configuring the Ruler
The Ruler can be configured to fit many different applications. This enables testing of
different set-ups and fine-tuning of the parameter values, in purpose to optimize the
measurement loop.
The Ranger Studio is used for changing the parameters. The Parameter editor in Ranger
Studio retrieves the current parameters from the Ruler and allows you to modify them.
Configurations can be stored on file for later use.
When configuring the Ruler there are some basic concepts necessary to be familiar with:
$Region-of-Interest
$External Triggering
$Cycle Time and Exposure Time
Region-of-Interest
The Region-of-Interest (ROI) is used to define what part of the sensor to be used in a
measurement. The ROI is defined in two dimensions, ROI-width and ROI-height.
Figure 3.1 – ROI-width and ROI-height
The ROI-width is defining which columns to use in a configuration and is set by a start
column and number of columns. The ROI-width is common to all components in a configu-
ration.
The ROI-height is defining which rows to use for a specific component. It is set by a start
row and number of rows. Using a smaller region on the sensor enables measurements at a
higher rate.
Columns
Rows
ROI-height
ROI-width
SICK IVP • Industrial Sensors • www.sickivp.com • All rights reserved 15

Chapter 3Reference Manual
Ruler E
Configuring the Ruler
External Triggering
There are two ways to trigger the Ruler using external signals:
Enable Triggers the Ruler to start measuring a series of profiles. This signal
could for example come from a photo switch located along the con-
veyor belt.
This signal is connected to In1 on the Power I/O connector.
Pulse triggering Triggers the Ruler to measure one profile. This signal could for exam-
ple be the differential signals Phase 1 and Phase 2 coming from an
encoder on the conveyor belt.
This signal is connected to In1 and In2 on the Encoder connector.
The Ruler is configured to use these external signals for triggering by setting the Enable and
Trig mode parameters.
When using enable, you set the Scan height parameter to specify the number of meas-
urements that the Ruler should make after the Enable signal goes high. After the specified
number of measurements, the Ruler checks the enable signal again, and if it is high
continues to make another series of measurements.
When using pulse triggering, you set the Number of pulses per trig parameter to specify
the number of pulses on the signal before a measurement is made. The Ruler counts the
number of pulses received on the pulse triggering inputs using an internal counter, which
is reset every time a measurement is made.
When you connect both In1 and In2 on the Ruler’s Encoder connector to signals from the
encoder, the signal on In2 can be used for detecting when the object moves backwards. If
so, the Ruler will decrement the counter instead. This way the object can move backward
and forward under the Ruler, but the Ruler will not measure any section of the object more
than once.
Figure 3.2 – Using In1 and In2 to detect movements in both directions.
The pulse triggering counter will also be reset every time the Enable signal goes high.
If pulse triggering is not used, the Ruler will measure in free-running mode, make meas-
urements with a regular time interval determined by cycle time. The distance on the object
between two measurements is then determined by the speed of the object – that is, how
far the object has moved during that time.
To find the actual distance between two measurements when measuring in free-running
mode, you can connect an encoder to the Ruler and set the Mark parameter. This will
make the Ruler embed the encoder information in the profiles sent to the PC.
Forward Backward Forward
In1
(pulse trig)
In2
(direction)
Increment No. of
pulses
per trig
Decrement Increment
Pulse trig
counter
Profiles
16 SICK IVP • Industrial Sensors • www.sickivp.com • All rights reserved

Reference Manual Chapter 3
Ruler E
Configuring the Ruler
Cycle Time and Exposure Time
The cycle time – that is the time between two profiles – and the exposure time – the time
during which the sensor is measuring the light from the object – can be set separately
when configuring the Ruler.
However, the exposure time cannot be longer than the cycle time. Therefore, if the expo-
sure time is set to be longer than the cycle time, the cycle time will be used as the actual
exposure time.
If the exposure time instead is set to be shorter than the cycle time, the Ruler will reset the
sensor at the beginning of each cycle and then read the exposure after the specified time.
The Ruler uses a rolling shutter – that is, it reads out the exposure on the sensor one row
at a time, and at the same time resets that sensor row. Thus, reading the entire sensor
image takes a certain amount of time.
When the exposure time is equal to the cycle time, the Ruler only needs to go over the
sensor once every cycle. Therefore the shortest possible cycle time would be the same as
the time it takes to read the sensor.
But when the exposure time is shorter than the cycle time, the Ruler needs to go over the
sensor twice – once for resetting the sensor and once for reading the exposure. Resetting
the sensor takes just as long time as it takes to read the exposure, which means that the
shortest possible cycle time would in this case be two times the read-out time.
When triggering profiles with pulse triggering, the exposure time should be set to be
shorter than the cycle time, otherwise the sensor will be exposed during the entire cycle.
This time may vary since it is depending on the pulse trigger signal, leading to varying
exposure times.
Figure 3.3 - Exposure time when set to longer and shorter than the cycle time.
Read-out
Cycle time
Used exposure
time
Read-out
Cycle time
Reset
Exposure time
SICK IVP • Industrial Sensors • www.sickivp.com • All rights reserved 17

Chapter 3Reference Manual
Ruler E
Configuring the Ruler
3.1 Configuration Hierarchy
The following information uses the same hierarchy as in the parameter editor in Ranger
Studio. This means that the settings are grouped into the following configurations:
Ethernet Set-up of the communication between the Ruler and the PC.
System Set-up of the Ruler system.
Image Used when the Ruler is running in Image mode, for example for setting up
of Region-of-Interest.
Measurement Selection and set-up of the measurement method to use when measuring
profiles.
Which measurement method to use is specified by the measurement
component that is included in this configuration.
3.2 Ethernet Configuration
The Ethernet configuration is used for communication set-up.
Redundancy packages are used for recovering lost packages and can be used for safer
communication between the Ruler and the PC. Each redundancy package can be used for
recovering one lost package since the previous redundancy package was sent. For exam-
ple, if Redundancy frequency is set to 10, one package out of ten can be lost without
losing any data.
The maximum package size depends on whether or not the Network Interface Card in the
PC and all other equipment involved in the communication can handle Ethernet “Jumbo
frames”.
Input parameters
Redundancy frequency Number of data packages sent between each redundancy
package 0 – 100. Default value 10.
A low value means higher security but also higher load on
the PC.
Max package size States the maximum size of the Ethernet data package.
The bigger the package – the lower the CPU overhead for
the communication. 100 – 4054 bytes.
Default value 1472.
1472 Maximum size without Ethernet Jumbo frames.
4054 Maximum size if all equipment can handle
Ethernet Jumbo frames.
3.3 System Configuration
The System settings are used for switching the laser off in order to increase the laser’s life
time.
Input parameters
Laser On Laser Off/On. 0 – 1. Default value 1.
0 = Laser Off.
1 = Laser On.
18 SICK IVP • Industrial Sensors • www.sickivp.com • All rights reserved

Reference Manual Chapter 3
Ruler E
Configuring the Ruler
3.4 Image Configuration
The image settings are intended for evaluation purposes. It is used for set-up of one gray-
scale region of the sensor, with a common exposure time for the whole region.
The following parameters are common for all the components in the Image configuration:
Input parameters
Use enable States if enable signal should be used or not.
Default value 0.
0 = disabled
1 = enabled
Start column The first sensor column to acquire data from.
0 – 1280 (for Ruler E 600)
0 – 768 (for Ruler E 1200)
Number of columns The number of columns to acquire (a multiple of 8).
256 – 1536 (for Ruler E 600). Default value 1536.
256 – 1024 (for Ruler E 1200). Default value 1024.
Trig mode Triggering mode:
0 = Free-running/No triggering
1 = Not applicable in Ruler E
2 = Pulse triggering
Number of pulses per trig Only valid for pulse triggering. 1 – 65535
Image 1 Component
Image 1 is an Image configuration component. Image 1 is used for evaluation purposes
when tuning in the sensor region and the exposure time for the 3D measurement configu-
ration.
To help setting the height of the ROI, the current ROI can be shown in the images sent
from the Ruler by setting the Measurement ROI overlay parameter. When set, the top and
bottom row of the ROI is marked with a dashed line in the images.
Image 1 is reflecting the measurement 3D configuration. Following parameters are avail-
able for the Image 1 component:
Input parameters
Measurement ROI overlay States if the ROI overlay function for the measurement
configuration is enabled or not. Default value 0.
0 = not enabled
1 = enabled
Start row The first sensor row to acquire data from. 0 – 511.
Number of rows The number of rows to acquire data from. 1 - 512. Default
value 512.
Exposure time The time in micro seconds that the sensor is exposed to
light.
10 – 200000. Default value 10000.
Gain The amplification of the analog sensor data before AD
conversion.
1 = No amplification
3 = 3 times
4 = 4 times
SICK IVP • Industrial Sensors • www.sickivp.com • All rights reserved 19

Chapter 3Reference Manual
Ruler E
Configuring the Ruler
3.5 Measurement Configuration
The measurement configuration is designed for measurements on the sensor.
The following parameters are common for all the components in the Measurement con-
figuration:
Input parameters
Use enable States if enable signal should be detected or not. Default
value 0.
0 = disabled
1 = enabled
Cycle time In free-running mode; the time in micro seconds between
each measurement.
In pulse triggering mode; the shortest possible time between
two measurements – that is, between two trig pulses.
Start column The first sensor column to acquire data from.
0 – 1280 (for Ruler E 600).
0 – 768 (for Ruler E 1200).
Number of columns The number of columns to acquire (a multiple of 8).
256 – 1536 (for Ruler E 600). Default value 1536.
256 – 1024 (for Ruler E 1200). Default value 1024.
Trig mode Triggering mode:
0 = Free-running/No triggering
1 = Not applicable in Ruler E
2 = Pulse triggering
Number of pulses per
trig
Only valid for pulse triggering. 1 – 65535
Scan height Number of profiles delivered per buffer when Use enable is
set to 1. 1 – 65535
This value should be the same as the ProfilesPerBuffer
property set for the Ruler object in the application.
Mark States if encoder values and input status information should
be inserted in the profile or not.
0 = No.
1 = Values inserted.
20 SICK IVP • Industrial Sensors • www.sickivp.com • All rights reserved
Table of contents
Popular Scanner manuals by other brands
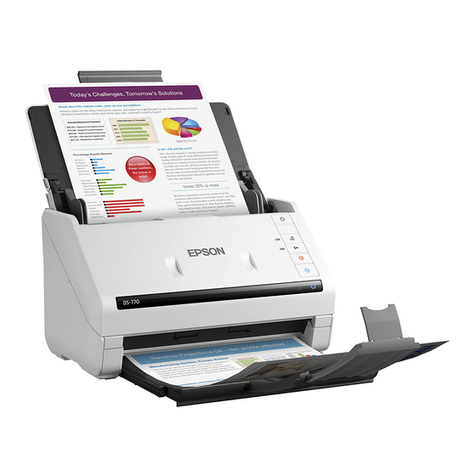
Epson
Epson B11B248401 user guide
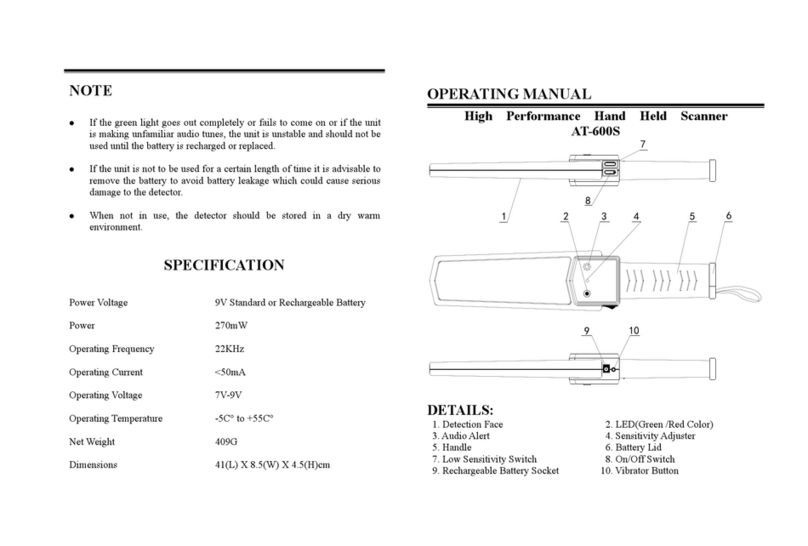
Aoteng
Aoteng AT-600S operating manual
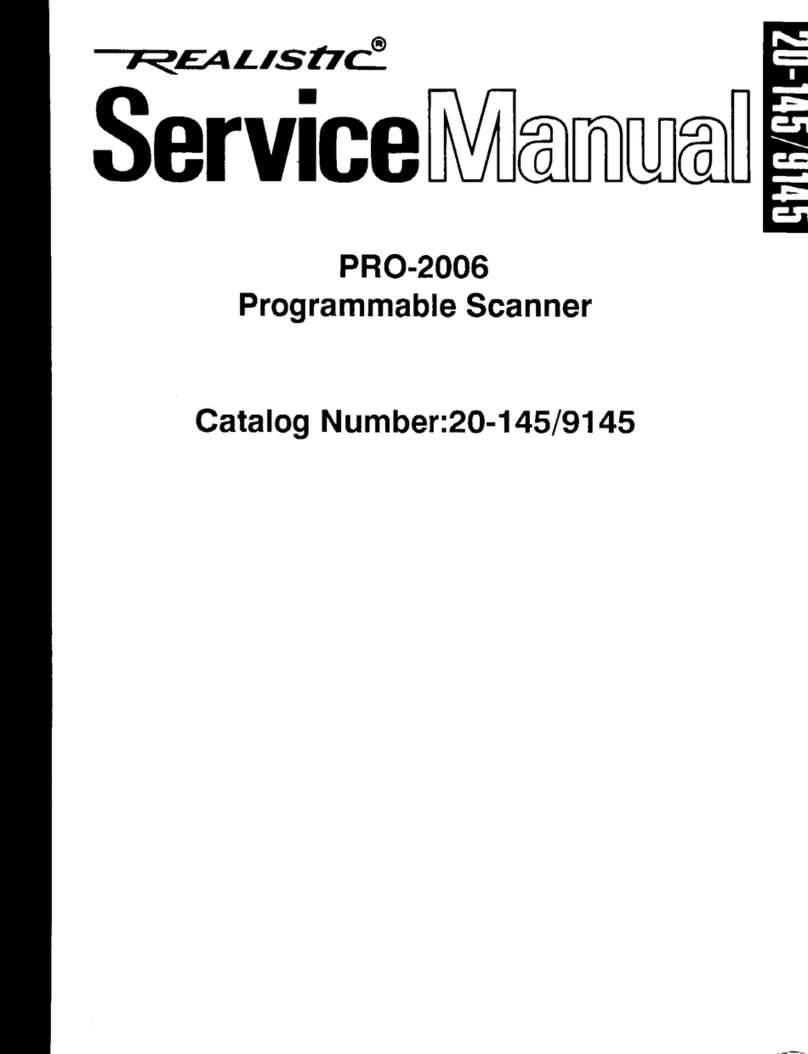
Tandy
Tandy Radio Shack Realistic PRO-200G Service manual

Canon
Canon DR-2020U - imageFORMULA - Document Scanner Brochure & specs
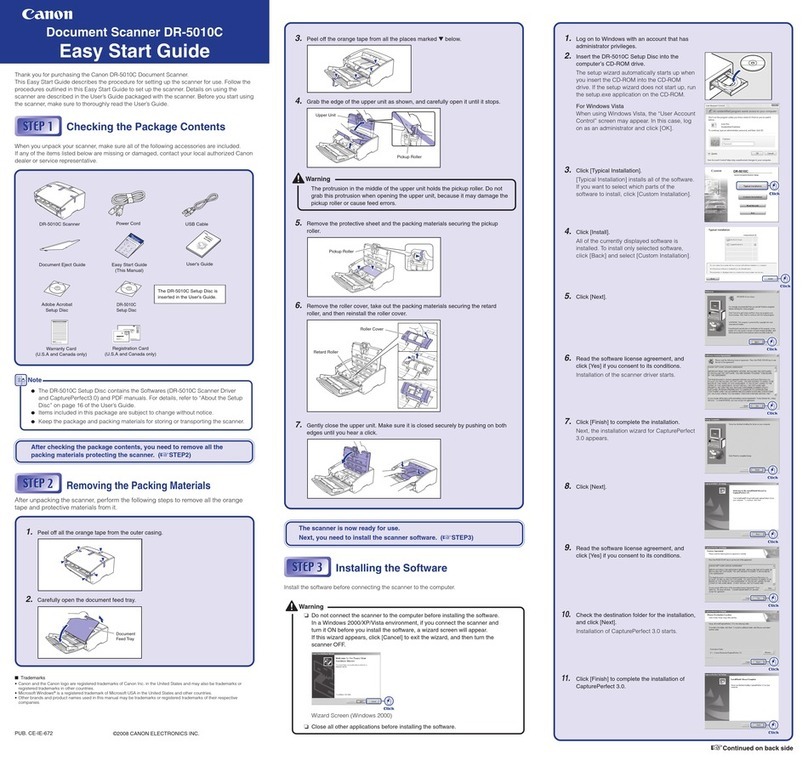
Canon
Canon DR 5010C - imageFORMULA - Document Scanner Easy start guide
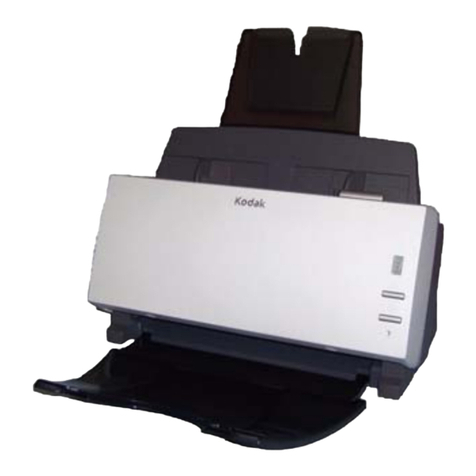
Kodak
Kodak Scanmate i1120 user guide
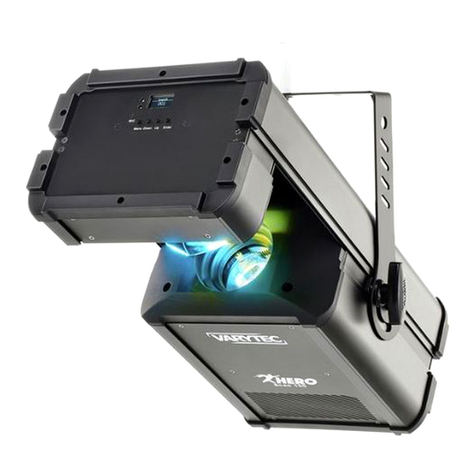
Varytec
Varytec Hero Scan 150 user manual
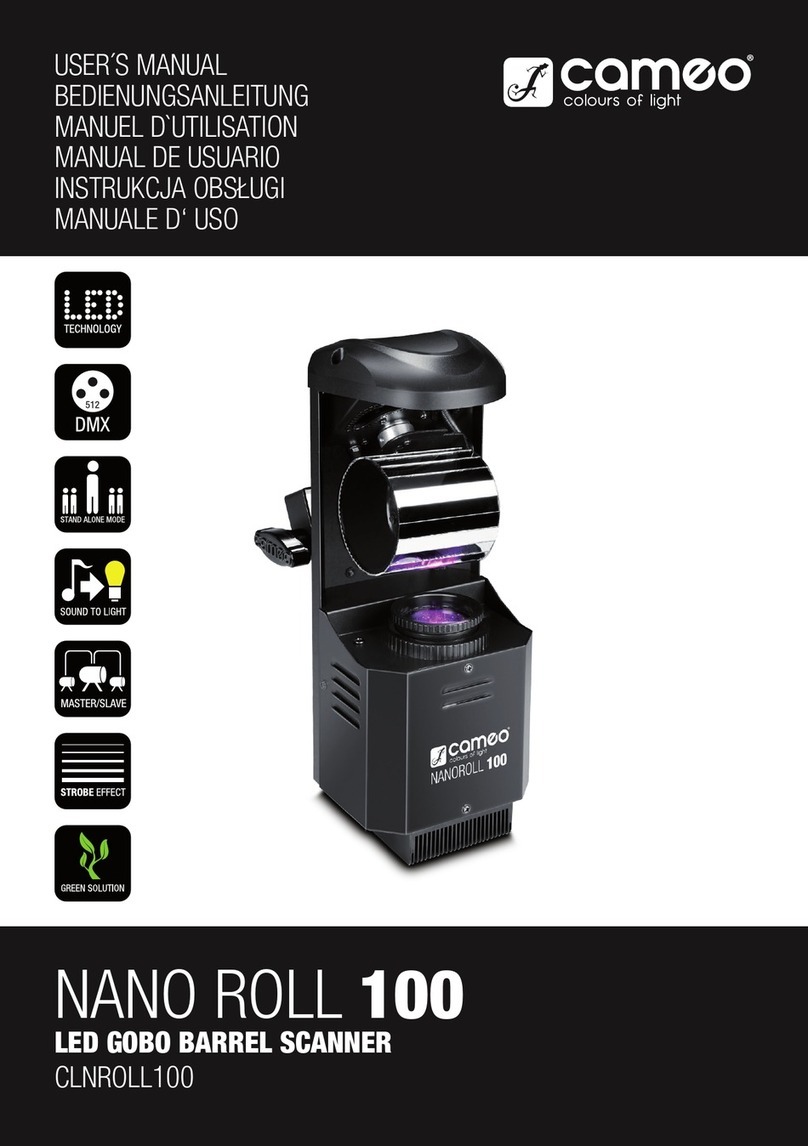
Cameo
Cameo NANO ROLL 100 user manual
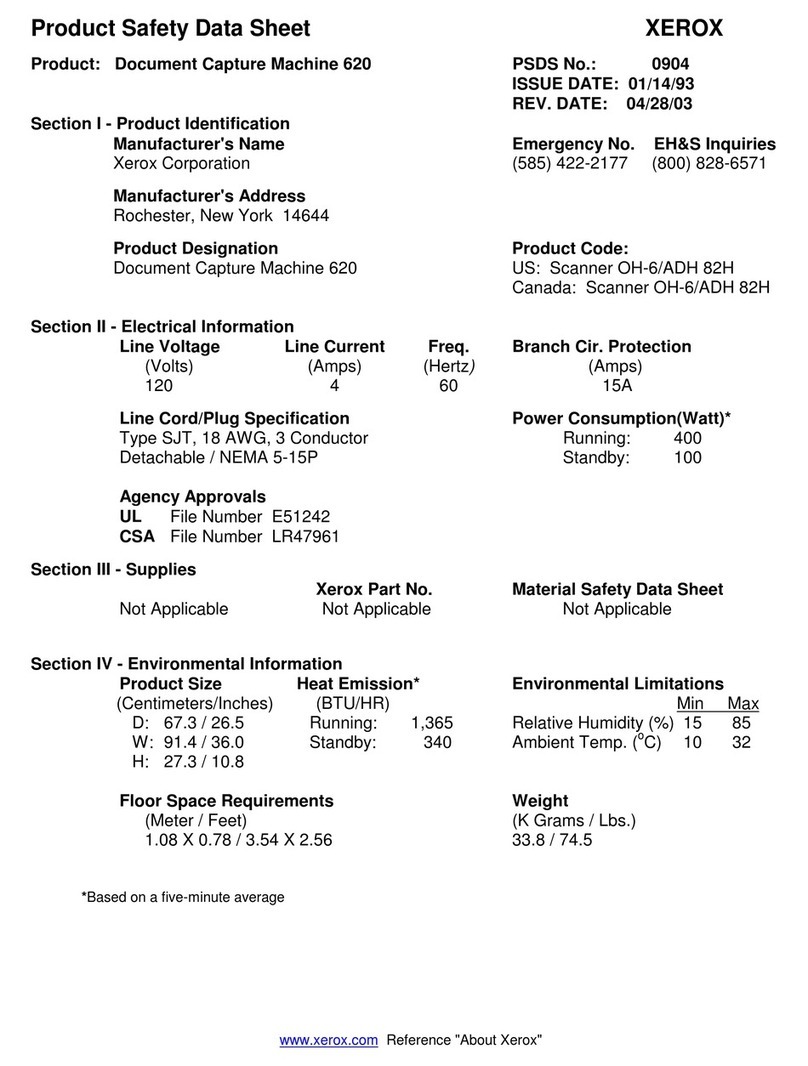
Xerox
Xerox Document Capture Machine 620 Product safety data sheet
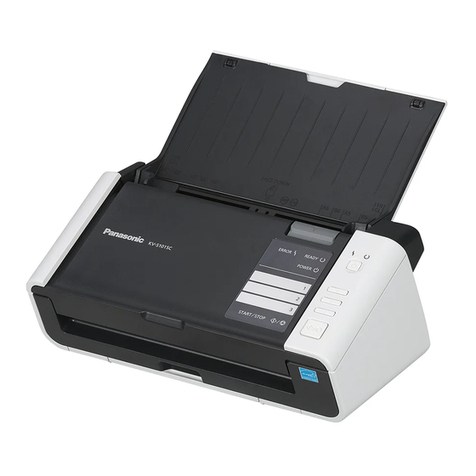
Panasonic
Panasonic KV-S1015C operating manual

Canon
Canon 0080B002 user guide

Deister electronic
Deister electronic Logident UDL 250 Wiring and Installation Instructions