Simplex APOGEE User manual

Film-Tech
The information contained in this Adobe Acrobat pdf
file is provided at your own risk and good judgment.
These manuals are designed to facilitate the
exchange of information related to cinema
projection and film handling, with no warranties nor
obligations from the authors, for qualified field
service engineers.
If you are not a qualified technician, please make no
adjustments to anything you may read about in these
Adobe manual downloads.
www.film-tech.com

STRONG
INTERNATIONAL
a division of Ballantyne of Omaha, Inc.
4350 McKinley Street
Omaha, Nebraska 68112 USA
Tel 402/453-4444 • Fax 402/453-7238
www.strong-cinema.com
INSTRUCTION MANUAL
and PARTS LIST
35mm UNITIZED PROJECTOR

This equipment is intended
FOR PROFESSIONAL USE ONLY
Read and understand all instructions before using
EXERCISE CAUTION WHEN
WORKING AROUND MOVING
PARTS
WARNING
To avoid risk of fire, do not use
nitrate or other flammable film.
Use safety film only.
SAVE THESE INSTRUCTIONS

TABLE OF CONTENTS
PREFACE 1
FIGURE 1 3
FIGURE 2 4
INSTALLATION
Unpacking 5
Mounting 5
LamphouseAlignment 6
Lamphouse Light Shield 6
Picture Changeover 6
Lens Turret 6
Projection Lenses 7
Flywheel 7
Sound ReaderAssembly 8
Analog 9
Digital 10
START-UP PROCEDURES
InitialOiling 15
Threading 16
Initial Operation 17
MAINTENANCE
Lubrication 18
Sprockets 18
Pad Rollers 18
Fastening Hardware 18
Film Gate 18
FilmTrap 18
Lens Turret 19
OverallAppearance 19
i

TABLE OF CONTENTS (continued)
FIGURE 3 20
FIGURE 4 21
ADJUSTMENTS & REPLACEMENTS
Intermittent Shoe Replacement 22
Film Trap &Aperture Changer 22
Pressure Strap Replacement 22
Studio Guide Replacement 22
Aperture PlateAdjustment 22
Gear Compartment Cover 23
Intermittent Movement 23
Intermittent Sprocket 24
FramingLight 24
Pad RollerAssemblies 24
ShutterTiming 25
Shutter Replacement 25
Film Gate Replacement 25
Film Sprocket Replacement 26
Sprocket Gear Replacement 26
Automatic Lens Turret 26
PARTS LISTS 28
STRONG INTERNATIONAL
a division of Ballantyne of Omaha, Inc.
Engineering/Sales
July 1, 2004
ii

PREFACE
THE SIMPLEXAPOGEE PROJECTOR, combining rugged construction with ease of opera-
tion, provides theatre owners with a superior mechanism, engineered to the high standards set for all Strong
International products. The following design features illustrate why the Simplex Apogee Projector is able
to provide continuously excellent performance throughout its long operating life:
UNIT DESIGN
Unit method of design simplifies part replacement and maintenance. All units may be quickly
removed and replaced. Components within a particular unit are just as easily handled.
SOUND READER
The analog and digital sound reader components are mounted to the same main frame as the optical
elements, insuring a straight film path. Minimal flutter and “wow” comply with all SMPTE standards.
MAIN DRIVE
The projector main drive is connected directly to the drive motor without pulleys and belts, eliminating the
need to adjust tension and/or replace these components.
OPTICS
A conical shutter, positioned close to the picture aperture, provides very high light efficiency. Optical
design is compatible to modern xenon lamphouse systems.
LENS TURRET
The Apogee Lens Turret is available in either Automatic or Manual configurations. The standard
turret accommodates (1) each 2-25/32" (71mm) diameter Wide Screen (flat) andAnamorphic (CinemaScope)
lens without use of a MagnaCom. A three-lens turret is available for export applications. Individual focus
controls permit concise focusing of each lens independently.
FILM COMPARTMENT
The roomy film compartment permits ease of threading and cleaning. The lens turret is hinged and
swings open for added convenience.
GEAR COMPARTMENT
The gear compartment has a removable cover, rounded corners, and an enameled finish which simplifies
cleaning and service.
1

MAIN FRAME
The main frame casting forms a single unit that is noteworthy for its simplicity and strength. A single
thread path serves all film-handling elements for both precise projection and sound reproduction.
FILM SPROCKETS
The upper feed and lower holdback sprockets, having twenty-four teeth each, reduce shaft speeds to
prolong operating life, permit smoother wraparound, and lessen the danger of splice breakage. Exclusive use
of VKF®sprockets insures minimum film wear. The pad rollers are made of durable, lightweight nylon.
FILM TRAP
The film trap conforms to the curved film gate, and accommodates the multiple-aperture plate used
with the lens turret. Film tension can be easily adjusted while the machine is running. The trap is readily
removed and replaced for routine cleaning and maintenance.
FILM GATE
The curved gate, together with the film trap, controls the movement of the film past the aperture. Gate
curvature provides compensation for heat-induced warping of the film at the aperture, thus insuring a sharper
image on the screen. The film gate runner is easily removed, cleaned, and replaced.
INTERMITTENT MOVEMENT
The intermittent movement features a webbed starwheel for high strength, long life, and positive
registration. The VKF®intermittent sprocket is adjustable, making absolute alignment possible.
LUBRICATION
A Spray-O-Matic Lubrication System, with a gear-driven oil pump, completely lubricates all moving
components. The moving parts inside the gear compartment are visible through the full-vision, oil-sealed
plexiglass window on the off-operator side of the mechanism. The intermittent movement lubricates itself by
pump action, and the Spray-O-Matic system. An oil level sight glass in the film compartment permits a visual
check of the oil level.
COOLING
The Simplex Apogee Projector includes a heat sink positioned behind the shutter blade and aperture to
absorb radiant heat and protect the trap and film. Cooling fans further reduce heat at the film plane.
VKF® is a registered trademark of LaVezzi Precision, Inc. Elmhurst, Illinois
2

FIGURE 1
3
CONTROL
CABINET
FOCUS
KNOB
PICTURE
CHANGEOVER
DEVICE
FOCUS
KNOB
FILM TRAP
COOLING FANS
RESET LEVER, INDEX
STOP PIN
SHUTTER ADJUSTING
KNOB
DRIVE
MOTOR
TURRET “OPEN”
LEVER
DEADSTOP
ADJUST
OIL FILL
CUP

FIGURE 2
4
APERTURE LOGIC
SENSING SWITCH
UPPER FEED
SPROCKET
FILM TENSION
ADJUSTING
KNOB
GATE
RELEASE
PIN
INTERMITTENT
SPROCKET
HOLDBACK
SPROCKET
APERTURE
CUE
OIL DRAIN
ANALOG
SOUND
READER
DIGITAL
SOUND
READER
SHUTTER
GUARD
FRAMING
HANDLE
CHANGEOVER
DEVICE
OIL SIGHT
GLASS
TURRET
RESET
SWITCH
RELEASE,
APERTURE
MOTOR
COVER
FRAMING
LIGHT

INSTALLATION
EACH SIMPLEX APOGEE PROJECTOR is carefully inspected and film-tested before
leaving the factory. Carefully inspect the unit on receipt for any shipping damage, and file any damage
claims with the carrier immediately. It is the responsibility of the consignee, not Strong International or its
dealers, to file such claims.
THE FOLLOWING RECOMMENDATIONS should be studied carefully prior to installa-
tion. Even if received mounted and prewired to a Strong console, it is advisable to review and inspect the
following steps prior to energizing the system. Your Strong International Dealership may wish to assist in
installing those projection booth products supplied by their firm.
UNPACKING
The Simplex Apogee projector is shipped in a sturdy wooden crate. TOP and OPEN THIS SIDE are
marked on the carton. The projector is mounted to the base of the crate with (2) 5/16-18 hex head screws.
An accessory kit is shipped with each SimplexApogee projector. The kit includes the following:
(1) Can Simplex Projector Oil
(1) Oiler
(1) SetAllen Wrenches
The tools and accessories are required for adjustments and routine maintenance after installation. Store
them in a secure location in the projection booth.
MOUNTING
Mount the Apogee to the mounting arm on the front of the console or pedestal. Some consoles will
require spacer block(s) to position the projector’s picture aperture at the correct working distance; see the
console installation instructions. Start the top two bolts, through the washers and spacer block (if required),
into the back of the main frame casting. The projector can then be lifted into place, and the top two bolts into
the casting lowered into the slotted holes in the projector mounting arm. In this manner, the mounting arm
will bear the weight of the projector while the two bottom bolts are started.
To avoid crossthreading, the 3/8-16 mounting bolts should be screwed in fingertight as far as possible.
Before tightening the bolts, check that both the lamphouse/console and projector are on the same, level plane.
Terminals for the drive motor power leads are provided in the projector control cabinet. See the following
section detailing Electrical Connections.
5

LAMPHOUSE OPTICAL ALIGNMENT
Carefully follow the lamphouse manufacturer’s instructions regarding correct optical alignment
between the lamphouse and projector. The lamphouse is generally aligned to the projector aperture, but
some consoles require positioning the projector to the optical center of the lamphouse. Never operate the
lamphouse with the douser open unless the projector is running.
LAMPHOUSE LIGHT SHIELD
Light shields, or nose cones, supplied by the lamphouse manufacturer, may be installed between the
projector shutter guard and the lamphouse snood. Make certain that the nose cone does not obstruct the rotation
of the shutter. Trim or otherwise modify the nose cone as required.
ELECTRICAL CONNECTIONS
All electrical connections to the Apogee terminate in the cabinet mounted on the side of the projector
adjacent to the gear compartment. Loosen the quarter-turn fastener and open the door to access the terminals.
Inputvoltageis user-selectable by connectingthetransformerplug
to one of the two receptacles located on the top of the “Power” printed
circuit board. Connect the plug to J7 for 110 volt operation, or to J8 for
220 volt. After selecting the voltage, applyAC phase and neutral to the
two uppermost terminals on the right barrier strip. This AC input
powerstheturretcontroller, theturretandaperturemotors, and the L.E.D.
framing light. An earth ground must be connected to the ground lug at
the lower right corner of the cabinet.
The lower five terminals of the right barrier strip allow power
connections from the automation controller to the picture changeover
and the projector drive motor. The lower five terminals of the left
barrier strip provide connection points to the devices. Voltage to these
devices is generally supplied by, or switched through, the automation
controller. All NEUTRALconnections are common.
Turret inputs connect to the (4) marked terminals on the lower
part of the turret control PCB mounted to the cabinet door.
Picture Changeover
The Apogee is normally shipped with a Strong International
115 V.AC (52-60325) or 230 V.AC (52-60326) picture changeover de-
vice. If ordered separately, connect the changeover leads as follows:
Blk - OPEN Wht - COMMON
Red - CLOSE Grn - GROUND
NOTE: These changeover devices require an AC pulse to operate.
Connecting the changeover device to a sustainedAC circuit willdestroy
the electrical coil(s). Check carefully the instructions supplied with the
automation controller and/or the (installer-supplied) switching circuit.
6

Lens Turret
The MANUAL lens turret requires no electrical connections. Installer connections to the AUTO-
MATIC turret are made to the J4 terminals located on the printed circuit board on the control box door adjacent
to the gear compartment coveron the side ofthe projector. The inputs (FEED,SPECIAL, FLAT,and SCOPE)
are derived from an automation controller and/or other installer-supplied circuitry. NOTE: “SPECIAL”input
applies only to a third lens in a three-lens turret.
LENS INSTALLATION
The lens barrels are individually marked to designate their screen format. The barrels of the standard
two-lens turret are marked SCOPE (CinemaScope, or anamorphic) and FLAT (“wide screen,” or non-
anamorphic). Lens barrels on the three-lens turret are marked SC (CinemaScope), FL (Flat), and SP (Special).
The lenses must be installed in their designated barrels for correct aperture logic. Magnacom lenses are not
required in any configuration.
Rotate the turret to the SCOPE position. The automatic turret can be indexed to this position by pressing
the reset switch; the manual turret must be indexed by hand. Make certain the SCOPE aperture plate is in
position. Center thefocus adjustment screw,allowing equal travel forward and back. Insert the CinemaScope
lens and anamorphic adapter into the SCOPE barrel. Start the projector, ignite the lamphouse, and project
a picture to the screen. Move the lens inside the barrel until a sharply focused picture is projected, and rotate
the lens and adapter to set the anamorphic correction on the horizontal plane. Securely tighten the lens locking
knob on the top of the SCOPE barrel. Close the lamphouse douser.
Reset the turret to FLAT format, and make certain the FLAT aperture is in position. Install the FLAT
lens, and center its focus adjustment screw. Open the lamphouse douser and move the lens inside the barrel
until a sharply focused picture is projected. Tighten the lens locking knob above the FLAT barrel.
Repeat the above procedures as required for the “special” lens used in a three-lens turret. Once
installed, DO NOT remove the lenses for cleaning. The turret is hinged, and opens to permit cleaning the rear
surfaces of the lenses.
File the aperture plates to size the picture to the screen and/or masking. NOTE: When projecting a
white light while filing apertures, close the lamphouse douser frequently to allow the lens to cool.
DO NOT attempt to correct “keystoning” by shimming the turret or offsetting the position of the lenses.
The lenses must be positioned on optical center to project an acceptable image.
SOUND READER FLYWHEEL INSTALLATION
The sound reader flywheel is dismounted for
shippingto avoid damageto the impedance drum shaft.
Assembletheflywheeltotheend of the impedance drum
shaft using the wave spring washer and spacer in the
sequence shown (spring washer against the flywheel,
spacer next to bearing seal). Secure the flywheel to the
shaft with the 1/4 inch hex head screw. Note LEFT-
HAND THREAD; turn counterclockwise to tighten.
7
Shaft Spring Washer
Spacer
Flywheel

SOUND READER ASSEMBLY
ADJUSTMENTS to those components relevant to scanning the optical soundtrack are best
performed by qualified personnel equipped with the necessary test equipment. Attempts to effect field repairs
without use of the required test equipment are generally detrimental to sound quality.
1. An L.E.D.(Light Emitting Diode) is positioneddirectly behind the film plane to illuminatethe soundtrack.
The horizontal and vertical positioning is adjustable. The distance of the L.E.D. from the film plane is
factory set. The L.E.D. is powered by a remote, low-voltage, current regulated power supply.
2. AnAnalog Signal Pick-UpAssembly is mounted in front of the film plane, and contains the lensing, the
solar cells, pre-amps, and terminals for the cell output. This assembly is factory-set to maximize the
reception of the signal generated by the L.E.D.
3. A second L.E.D. illuminator and signal pick-up are required for scanning Dolby®digital prints. These
components are mounted adjacent to the analog elements, 45° off the analog axis. Asecond L.E.D. power
supply is also required.
An L.E.D. features a much longer life than an incandescent exciter lamp, and eliminates signal loss
because of sagging or aging bulb filaments. The one-piece Signal Pick-Ups detect only L.E.D. inputs, and
stray booth lighting does not affect the solar cell output. Channel separation is enhanced by incorporating the
solar cells within the sealed lens assembly.
Film Path IN
Film Path OUT
Signal Pick-Up Assembly, DIGITAL
Signal Pick-Up Assembly, ANALOG
L.E.D. Illuminators
8
Impedance Drum
Holdback
Sprocket

The duty cycle (time ON) of the L.E.D. is the same as the projector motor and should parallel that of the
xenon bulb; the lamphouse elapsed hour meter should indicate approximate L.E.D. hours. L.E.D. manufactur-
ers have noted a 10-20% drop in light output after prolonged operation. If a sound signal loss cannot be
corrected by fader gain, it may be necessary to replace the L.E.D. head.
WIRING
Install the LS-40 L.E.D. Power Supply to the projection console, pedestal, or to a rack adjacent to the
soundhead. Setthe slide switch forthedesiredACpower, and connecttoACsource. Routethepowerleads to the
soundhead-mounted L.E.D. illuminator assembly using 18 gauge wires for short runs; 16 gauge wires for exces-
sively long runs. Other installer connections are made to the clearly-marked terminals on the back of the unit.
The L.E.D.’s are bipolar; the power supply cannot damage an L.E.D. through reversed polarity. It is safe
to try reversing the polarity if you have power but no light. Accidental connection of theL.E.D. to the pre-
amppowerterminalswill damagethe L.E.D. The pre-amp power to the analog reader(Signal Pick-Up) is12
V.DC+, ground, and 12 V.DC-. The ground must be connected at both ends as it is circuit reference zero volts.
It is recommended to use (2) shielded two-conductor cables to connect the solar cell outputs, but
use of a three-conductor, single-shield cable is permitted. If using three-conductor cable, strap the two “LO”
terminals together. Since very little current is required, 22 gauge wire is adequate. DO NOT interconnect
input and output grounds.
Digital readers utilize a second LS-40 Power Supply. Use 16 or 18 gauge hookup wire between the
L.E.D. and the LS-40 power supply, depending on the length of the run. Pre-terminated digital output cables
(51-98272) are supplied, and should be connected to the processor as instructed in the Dolby manual.
ANALOG ALIGNMENT
Energize the LS-40 and check for 450 mAoutput to the analog (inner) L.E.D. Connect test equipment to
solar cell output terminals. Turn the sound processor’s level and high frequency adjustment to minimum
settings.
Loosen, butdo not remove, the socket head screwclamping the inner L.E.D. head to itsmounting post and
bracket. Loosening this screw permits moving the L.E.D. head up and down, and on the horizontal plane (in
and out). Position the L.E.D. head to visually locate the light source directly opposite the lens opening of the
analog signal pickup assembly.
Run a loop of level set (“Dolby Tone”) film and observe the output of the LEFT and RIGHT channels.
When the highest output is seen, move the L.E.D. head horizontally (in and out) inside the impedance drum.
DO NOT permit the L.E.D. head to touch the inside of the impedance drum. Observe the output and secure the
L.E.D. head when the highest output is achieved. Refer also to the sound processor manual.
Run a “Buzz Track” (SMPTE No. 35-BT) loop and check for correct sound track alignment. It is recom-
mendedto splicetogether a loop of half “Buzz Track” film and half “Left/RightAlignment”(Dolby Cat. No. 97)
test film. This permits centering the soundtrack and checking for cross-talk simultaneously. If correction is
required, loosen or tighten the 1/4-20 locknut to move the spring-loaded pickup assembly horizontally.
9

Loosen the focus/azimuth clamping screw and set the focus and azimuth by running the “pink noise” loop
and adjusting the signal pickup assembly in the same manner as a conventional slit lens. Finalize the “A”
chain installation by again checking the L.E.D. adjustment using Dolby Cat. No. 566 “illumination unifor-
mity” test film. Perform a final “Dolby” level set, and complete any other steps specified by the manufacturer
of the sound processor.
DIGITAL ALIGNMENT
Preliminary Adjustment
• Power up the second LS-40 Power Supply and theAudio Processor.
• Check for 550 mA output to the digital (outer) L.E.D.
• Connect a dual-trace oscilloscope to the left and right test points of the
processor pre-amp.
• Thread and run Dolby Tone Test film (Cat. No. 96t).
• Observe oscilloscope traces and “Dolby” level indicators in the processor.
• If tone is visible on both channels, set to “Dolby” level.
• If not, check the L.E.D. alignment and focus the optics. Then set
“Dolby”level.
• Thread and run SMPTE “Buzz” track.
• Adjust horizontal positioning locknut as required to obtain (2) very low,
equal residual signals.
Analog L.E.D. Alignment
The analog L.E.D. must be aligned before the digital.
• Turn both left and right channel pre-amp gain adjustments on your cinema
processor to full down; if using a Dolby CP-500, turn to 50%. The goal is to
have equal gain on both channels.
• Thread and run Dolby Tone Test film (Cat. No. 96t).
• View the pre-amp outputs on the oscilloscope screen.
• Rotate the analog L.E.D. mount assembly to reach the maximum ampli-
tude of both traces.
• Move the assembly laterally to get both traces as high and equal as possible.
• Complete the standard “A” chain alignment.
L.E.D. Head
Clamping Screw
Focus/Azimuth
Clamping Screw
Impedance Drum
Azimuth Adjust
Focus Adjust
Horizontal
Positioning
Locknut
Analog Soundtrack
Digital Soundtrack
Analog Signal
Pickup Assembly
10

To minimize microphonics, the L.E.D. must be very accurately aligned.
• With the power amplifiers OFF, turn the processor and monitor gains FULL UP. Select a film format and
the correct projector on the processor. Run the projector with no film. Fine-adjust the L.E.D. mount
rotation to a point where the sound of the projector running is not heard through the sound system. The
optimal adjustment will be found between two positions where the projector vibration can be heard quite
clearly. Run Dolby Tone again to give the system a final adjustment. The final result will be projector
noise that is below the noise floor of the processor.
• Optionally, connect an AC millivolt meter to one of the pre-amp test points. Rotate the L.E.D. mount to
achieve highest output to three decimal places on the AC millivolt meter. Careful peaking will achieve
the same result.
Digital Reader Alignment
• Thread and run a reel of Dolby-encoded film.
• Connect a dual-trace oscilloscope to the Dolby Digital Processor per the following instructions.
• Refer to the oscilloscope traces “A” - “D” on the following page in reference to the following instructions:
Figure B is in optimal alignment.
• In Figure A, the top of the sprocket hole has (12) large saw teeth. The differential between the high and
low points is 1/3 volt.
• Figure B shows more saw teeth with less differential. This is obtained by fine-adjusting the rotation of the
L.E.D. holder.
• In Figure C, the sprocket hole is falling off on the left, indicating uneven light. This is improved by
moving the L.E.D. holder laterally until a flatter trace is obtained.
• In Figure D, the CCD board is misaligned laterally. Dimension X2 is smaller than X1. This can be
improvedby loosening the moving the board untilthe X1 and X2 dimensionslook like Figure B. The correct
alignment is offset to the left by one minor division. That is, the sprocket hole will be 1/5 of a square off-
center toward the left “goal post”on the ‘scope screen.
Instructions forAlignment of Readers for Dolby Digital
1. Connect a dual-trace oscilloscope to test points on VideoAcquisition Card (Cat. No. 605 or 670). Oscillo-
scope should be 20 MHz. minimum.
a) Connect Channel 1 to Video test point; connect this probe ground only to Gnd. test point.
b) Connect Channel 2 to Clamp test point.
c) Set both channels Volt/Div. controls to 1 volt/div. Set vernier to calibrate. Ensure that probes are
not at X10.
d) Set horizontal sweep rate to 2 usec/div.
e) Set trigger to channel 2 and positive polarity, adjust trigger level, and lock on signal.
11

12
(Figure B is in optimal alignment)

2. Calibrate oscilloscope to processor:
a) Thread a loop of Cat. No. 69P test film into projector and reader; start machine.
b) Select Channel 2 for display.
c) Adjust the horizontal position to line up the inside edge of the left “goal post” with the left edge
of the graticule.
d) Adjust thesweep vernier to line upthe inside edge of the right “goalpost” with the right edge ofthe
graticule.
e) Adjust the vertical position for the baseline of the clamp signal (Channel 2) to coincide with
a line in the lower section of the graticule.
f) Select either Alternate or Chop to give the brightest display of both channels.
g) Adjust the vertical position of the video signal (Channel 1) to coincide with the same line as the
clamp signal.
3. Alignment of the Reader:
a) Rotate the horizontal positioning locknut and roughly adjust the lateral position of the CCD board
so that the outer trace (perf) is centered between the “goal posts.” This is approximate, and will
be repeated later for accurate positioning.
b) Rotate the L.E.D. mounting assembly for maximum amplitude on the upper trace without
sacrificing flatness. The trace should vary one block or less (± .5 volt). As shown, Figure B is
improved from Figure C. Amplitude, as measured with the top trace, should be between 2-5
volts from baseline. Adjust the digital L.E.D. for minimum ripple on the upper trace of the video
signal. As shown, Figure B is improved from FigureA.
c) If available, use DRAS10 software and a laptop computer to view the adjustment of azimuth for a
zero degree reading. Or, center the reader rotation between sync lost points using the error rate
of the Digital Processor to indicate lost sync.
d) Adjust focus for darkest center in area of bits (grass). Confirm highest reading with DRAS.
e) Confirm calibration of oscilloscope as above. Readjust the lateral position to align the outer
trace to one minor division (2/10) left of center between the “goal posts.” Figure B is improved
from Figure D.
4. FinalAnalog:
Check the lateral alignment, as initially set using the “Buzz Track,” and correct as required.
Confirm the L.E.D. positioning by setting the oscilloscope for “X-Y” display and running the
Dolby Cat. No. 97 loop. A “cross” should appear on the screen. When both the horizontal and
vertical lines are straight and of uniform length, the optimum position has been reached. Repeat
the tests for focus, azimuth, equalization, and “Dolby” level set. Adifference may be noted in that
the high frequency range is extended, and very little high frequency boost will be required.
13

L.E.D. Head
Clamping Screw
Horizontal Positioning Locknut
Azimuth Adjust
Focus Adjust
Focus/Azimuth
Clamping Screw
Impedance Drum
Digital Signal Pickup
Assembly
14

START-UP PROCEDURES
ALL SIMPLEX PROJECTORS are carefully “run-in” at the factory before shipping. No
“run-in” period at the installation site is required. Some gear whine may be noticed initially, but should
disappear after a few hours of operation.
INITIAL OILING
One quart of Simplex Projector Oil is included in the accessory kit supplied with new equipment. USE
ONLY GENUINE SIMPLEX PROJECTOR OIL IN THE MECHANISM. Use of other lubricants may
inhibit oil pump operation and damage moving parts. Additional oil is available through authorized Strong
International Dealers; order Simplex Part No. 52-00400 for one-quart quantities, 52-00410 for a half-gallon
can, or 52-00420 for a one-gallon can.
DO NOT, at any time, operate the projector without oil.
With the projector level (0° projection angle), add oil through the filler located at the front of the gear
compartment. Look into the gear compartment while adding oil; the correct amount of oil will touch the bottom
of the horizontal drive shaft. No air bubble should be visible in the sight glass inside the film compartment.
Unless the machine is operated at a severe upward angle, no air should be visible in the sight glass. If
bubbles are seen, add oil to maintain a safe level. Always check the oil level with the motor off.
15
Rotate the motor flywheel by hand to turn the projector mechanism. It should turn freely and smoothly.
Start the projector motor and run for at least one minute. Check for an oil splash against the gear compartment
cover glass.
Normal Add Oil
Table of contents
Popular Projector manuals by other brands

Christie
Christie DWU951 user manual
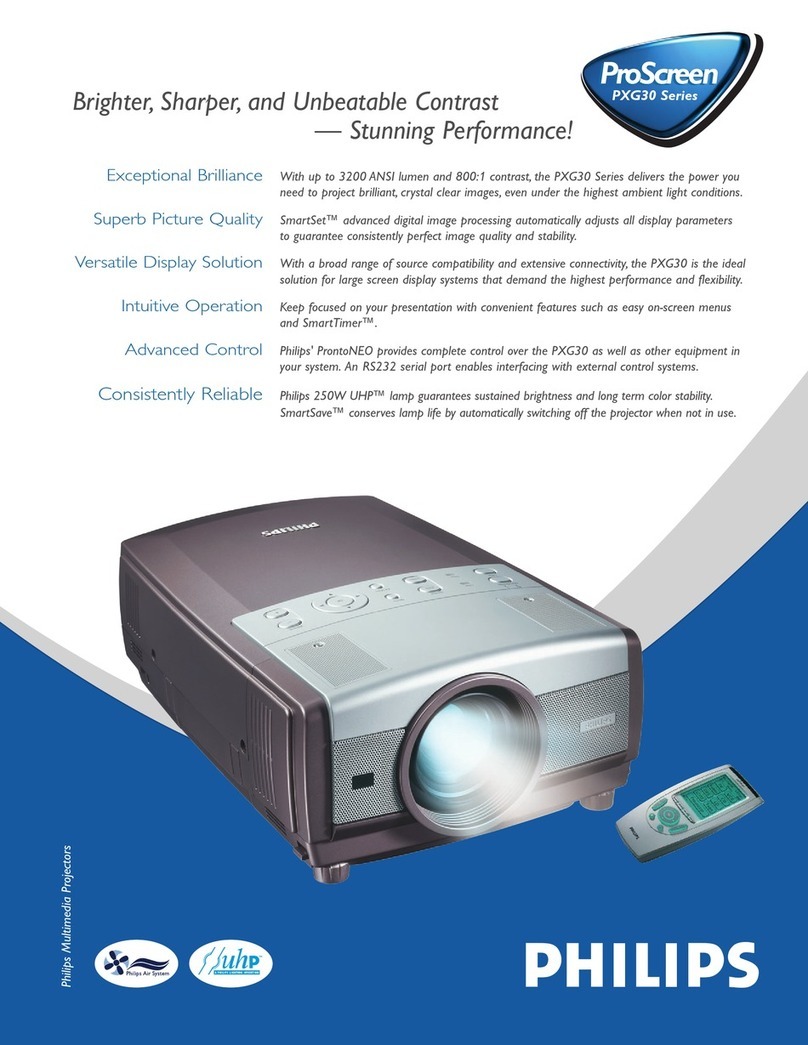
Philips
Philips ProScreen PXG30 Series Specifications
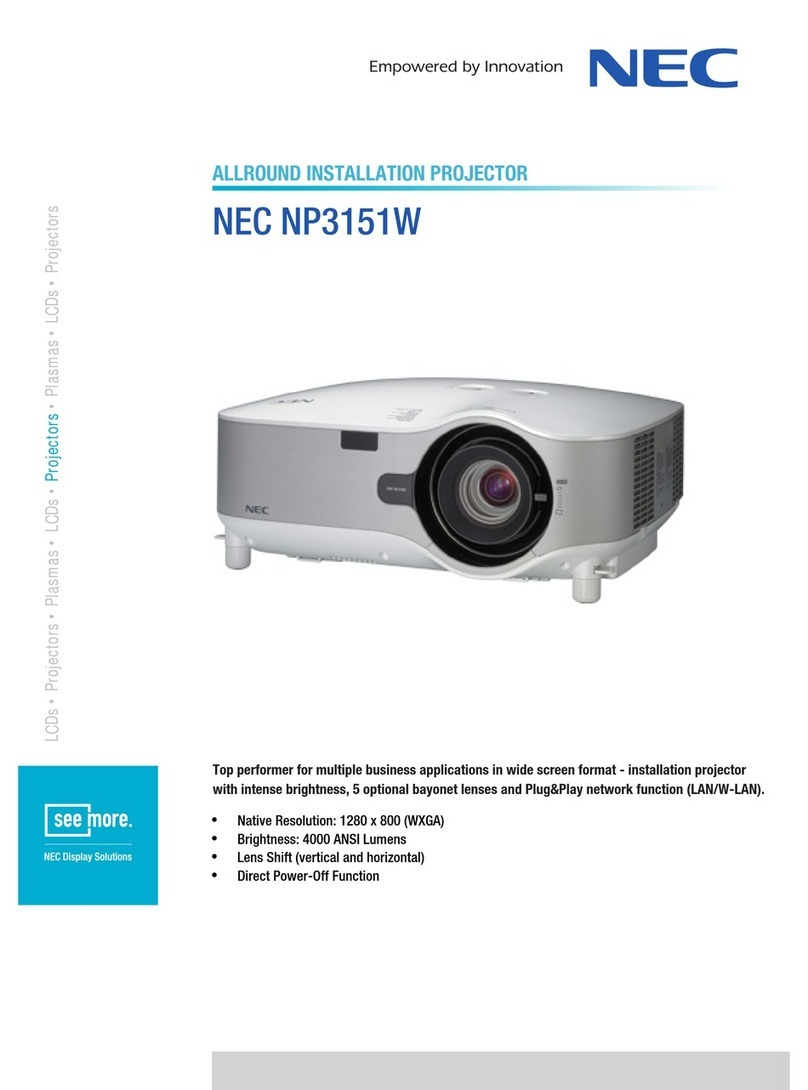
NEC
NEC NP3151W WXGA specification

Mitsubishi Electric
Mitsubishi Electric WD385U-EST Specifications
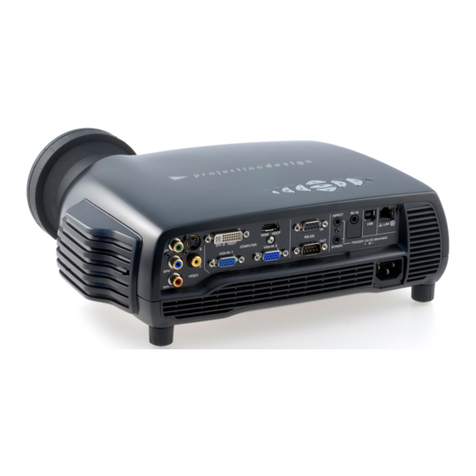
Projectiondesign
Projectiondesign F12 WUXGA user guide
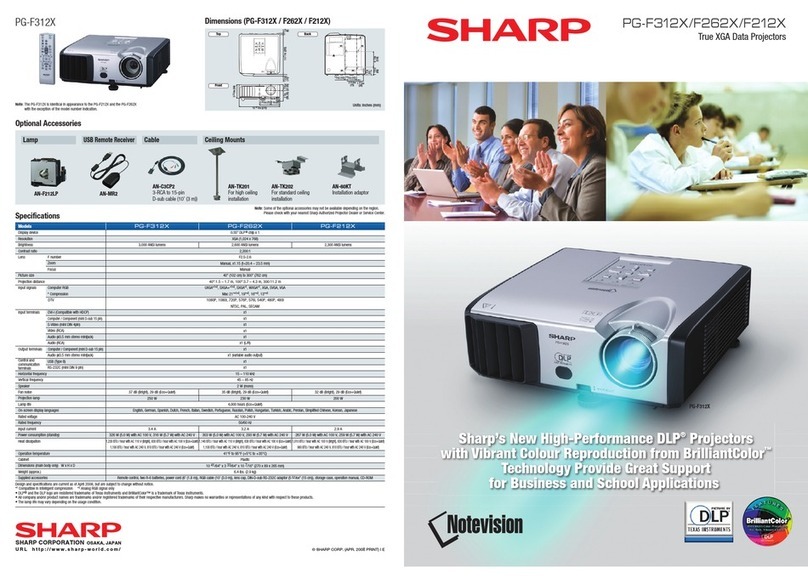
Sharp
Sharp PG-F312X - Notevision XGA DLP Projector Specification sheet