SMC Networks CRP10 Series User manual

Doc. no.DIY-26000-OM006
- 1 -
PRODUCT NAME
Compact Compressor
MODEL / Series / Product Number
CRP10---

- 2 -
Contents
Safety Instructions
3
1. Outline
1.1 How to oder
8
1.2 Accessories
9
1.3 Compressor construction
10
1.4 Specifications
11
1.5 Parts description
12
1.6 Outline dimensions
14
2. Installation
2.1 How to install the compressor
16
2.2 How to install the controller
17
3. Wiring and Piping
3.1 Pressure switch setting
19
3.2 Wiring
21
3.3 Piping
22
4. Construction and parts
23
5. Alarm details and troubleshooting
24

- 3 -
Safety Instructions
These safety instructions are intended to prevent hazardous situations and/or equipment damage.
These instructions indicate the level of potential hazard with the labels of “Caution,” “Warning” or “Danger.”
They are all important notes for safety and must be followed in addition to International Standards
(ISO/IEC)*1) , and other safety regulations.
*1) ISO 4414: Pneumatic fluid power -- General rules relating to systems.
ISO 4413: Hydraulic fluid power -- General rules relating to systems.
IEC 60204-1: Safety of machinery -- Electrical equipment of machines .(Part 1: General requirements)
ISO 10218: Manipulating industrial robots -Safety.
etc.
Caution
Caution indicates a hazard with a low level of risk which, if not avoided, could result
in minor or moderate injury.
Warning
Warning indicates a hazard with a medium level of risk which, if not avoided, could
result in death or serious injury.
Danger
Danger indicates a hazard with a high level of risk which, if not avoided, will result
in death or serious injury.
Warning
1. The compatibility of the product is the responsibility of the person who designs the equipment or
decides its specifications.
Since the product specified here is used under various operating conditions, its compatibility with specific
equipment must be decided by the person who designs the equipment or decides its specifications based on
necessary analysis and test results.
The expected performance and safety assurance of the equipment will be the responsibility of the person who
has determined its compatibility with the product.
This person should also continuously review all specifications of the product referring to its latest catalog
information, with a view to giving due consideration to any possibility of equipment failure when configuring the
equipment.
2. Only personnel with appropriate training should operate machinery and equipment.
The product specified here may become unsafe if handled incorrectly.
The assembly, operation and maintenance of machines or equipment including our products must be
performed by an operator who is appropriately trained and experienced.
3. Do not service or attempt to remove product and machinery/equipment until safety is confirmed.
1.The inspection and maintenance of machinery/equipment should only be performed after measures to
prevent falling or runaway of the driven objects have been confirmed.
2.When the product is to be removed, confirm that the safety measures as mentioned above are implemented
and the power from any appropriate source is cut, and read and understand the specific product precautions
of all relevant products carefully.
3. Before machinery/equipment is restarted, take measures to prevent unexpected operation and malfunction.
4. Contact SMC beforehand and take special consideration of safety measures if the product is to
be used in any of the following conditions.
1. Conditions and environments outside of the given specifications, or use outdoors or in a place exposed to
direct sunlight.
2. Installation on equipment in conjunction with atomic energy, railways, air navigation, space, shipping,
vehicles, military, medical treatment, combustion and recreation, or equipment in contact with food and
beverages, emergency stop circuits, clutch and brake circuits in press applications, safety equipment or
other applications unsuitable for the standard specifications described in the product catalog.
3. An application which could have negative effects on people, property, or animals requiring special safety
analysis.
4.Use in an interlock circuit, which requires the provision of double interlock for possible failure by using a
mechanical protective function, and periodical checks to confirm proper operation.

- 4 -
Safety Instructions
Caution
The product is provided for use in manufacturing industries.
The product herein described is basically provided for peaceful use in manufacturing industries.
If considering using the product in other industries, consult SMC beforehand and exchange
specifications or a contract if necessary.
If anything is unclear, contact your nearest sales branch.
Limited warranty and Disclaimer/Compliance Requirements
The product used is subject to the following “Limited warranty and Disclaimer” and “Compliance
Requirements”.
Read and accept them before using the product.
Limited warranty and Disclaimer
1.The warranty period of the product is 1 year in service or 1.5 years after the product is
delivered,whichever is first.2)
Also, the product may have specified durability, running distance or replacement parts. Please
consult your nearest sales branch.
2. For any failure or damage reported within the warranty period which is clearly our responsibility,
a replacement product or necessary parts will be provided.
This limited warranty applies only to our product independently, and not to any other damage
incurred due to the failure of the product.
3. Prior to using SMC products, please read and understand the warranty terms and disclaimers
noted in the specified catalog for the particular products.
2) Vacuum pads are excluded from this 1 year warranty.
A vacuum pad is a consumable part, so it is warranted for a year after it is delivered.
Also, even within the warranty period, the wear of a product due to the use of the vacuum
pad or failure due to the deterioration of rubber material are not covered by the limited
warranty.
Compliance Requirements
1. The use of SMC products with production equipment for the manufacture of weapons of mass
destruction(WMD) or any other weapon is strictly prohibited.
2. The exports of SMC products or technology from one country to another are governed by the
relevant security laws and regulation of the countries involved in the transaction. Prior to the
shipment of a SMC product to another country, assure that all local rules governing that export
are known and followed.
Caution
SMC products are not intended for use as instruments for legal metrology.
Measurement instruments that SMC manufactures or sells have not been qualified by type approval tests
relevant to the metrology (measurement) laws of each country.
Therefore, SMC products cannot be used for business or certification ordained by the metrology
(measurement) laws of each country.
! Caution
SMC products are not intended for use as instruments for legal metrology.
Measurement instruments that SMC manufactures or sells have not been qualified by type approval tests
relevant to the metrology (measurement) laws of each country.
Therefore, SMC products cannot be used for business or certification ordained by the metrology
(measurement) laws of each country.

- 5 -
Design/Selection
Danger
1. Use this product only for general industrial applications.
Do not use for any life-supporting applications such as respiratory equipment. Any damage to this product
may result in a critical accident.
2. Do not intake and compress fluid other than air.
It could lead to fire or explosion.
3. Do not install the product in an environment containing flammable gas, explosive gas, the organic
solvents, explosive dust or corrosive gas.
It may cause fire or explosion.
4. This product (compressor and controller) does not have a waterproof structure.
Do not use this product in an area where it could get wet, or in environments of high humidity and heavy
condensation. This may cause an electric shock, earth leakage, or fire.
5. Do not disassemble the product or make any modifications.
It may cause human injury and/or an accident.
Warning
The caution label shown below is attached to this product. Read and understand the warnings to ensure
work safety.
The product becomes hot during operation. Touching it may cause burn injuries. In addition,
residual heat after turning off the power may cause burn injuries. Avoid touching the product until
it has cooled down sufficiently.
The product contains a fan and parts that rotate at high speeds during operation. There is a risk
of fingers or hand being cut or getting caught by rotating objects. Avoid touching the product
during operation.
1. Keep the manual in a safe place for future reference.
The product should be mounted and operated only after thoroughly reading the operation manual and
understanding its contents.
2. When using this product in critical applications, make sure to provide a spare device or auxiliary
equipment.
This prevents damage when the operation is stopped due to failure or activation of the safety system.
3. Do not install these products in corrosive gases such as ammonia, acids, salts, ozone gas,
sulfurous gas, etc.
It may cause rusting, reduced product life and damage.
4. Install an emergency stop circuit.
Install an emergency stop outside of the enclosure so that the system operation can be stopped
immediately and the power supply can be intercepted.
5. Consider emergency stops.
Design so that human injury and/or damage to machinery and equipment will not be caused when
machinery is stopped by a safety device under abnormal conditions, such as a power outage or a manual
emergency stop.
6. Consider the whole system.
Design the system so that human injury or equipment damage will not occur upon the restart of operation
of the whole system.
7. Make sure to connect the outlet of the PNP-type digital pressure switch to the PNP terminals on
the controller. This product controls the pressure to unload / load by connecting the digital
pressure switch to the controller.
Use of this product when pressure outside the operating range is applied may reduce the life or damage
the product.

- 6 -
Caution
1. Use the product in an area that is free of dust.
Presence of dust may reduce life or cause product failure due to abnormal wear and other factors.
2. Use the product at an ambient temperature between 5oC and 40oC during operation.
Use of the product outside this temperature range may reduce life or cause product failure. In addition,
the temperature protection system may activate to prevent motor burnout and stop the operation.
When using the product in close proximity to a heat source or in an enclosed storage space consider
methods to cool and ventilate to maintain the ambient temperature at 40oC or less.
3. The surface temperature of the product can reach up to approx. 90oC depending on operating
conditions. Check that the heat emanated will not affect the surrounding.
4. Provide measures to treat the drain according to the use of compressed air.
This product does not use any lubricating oil during the compression process. However, the compressed
air generated contains a drain made of impurities such as moisture, oil content, dust, and wear particles
from the atmosphere.
Make sure to consider methods of treating this drain as it may cause malfunction if it flows into pneumatic
equipment such as cylinders.
Mounting
Warning
1. Installation, inspection, or wiring should be conducted after the power supply to this product has
been turned off.
Electrical shock, malfunction, or damage can result.
2. Before modifying or checking the wiring, the voltage should be checked with a tester 5 minutes
after the power supply has been turned off.
Failure to do so may result in electrical shock.
3. Maintenance space
Reserve sufficient space for maintenance and wiring.
4. Install the compressor body in an area with a solid surface and fasten it in place firmly.
Any displacement by vibration during operation may cause injury or product damage.
5. Do not carry the product by holding its cables.
It may cause an injury or damage to the product.
6. Shade the product from direct sunlight.
7. If the vibration transferred to the embedded structure deemed large, provide appropriate vibration-
proof treatment when fastening the product.
Vibration may transfer to the structure and increase the noise level.
Caution
1. This product exhausts heat using an axial flow fan. Make sure the suction and exhaust grill are
unobstructed when installing the product.
The temperature protection system will activate if the motor overheats and stop the operation.
2. Install the controller and its peripheral devices on a flat surface.
If the mounting surface is distorted or uneven, an unacceptable force may be added to the housing, etc.,
causing problems.
Wiring
Warning
1. Do not connect wires while power is being supplied.
It may cause the controller to break or its peripheral devices could be damaged, causing a malfunction.
2. Before wiring, check that the power supply has sufficient capacity and that the voltage is at the
specified value.
3. Never disassemble the cable. Use only the specified cables.
4. Never connect or disconnect the cable or connector with the power on.

- 7 -
5. Do not perform the operation or setting of the product with wet hands.
Doing so may cause an electric shock.
6. Operate with cables such that they are not easily moved.
Avoid contact with this compressor.
7. Avoid twisting, folding, rotating, or applying external force to the cable.
Electric shock, wire breakage, contact failure, or a loss of product control may occur.
8. In case of power supply has overcurrent protection function, Automatic recovery type and
Constant current type are adequate.
Caution
1. When plugging or unplugging the cable connector, release the detachment prevention mechanism
while manually supporting the plug. Connect or disconnect the connector in the same direction
as the connector pin to prevent the application of excessive force.
It may cause malfunctions.
2. Wiring should be done correctly. For each terminal, voltages other than those stipulated in the
operation manual should not be applied.
3. Connect the connector securely.
Check for correct connector wiring and polarity.
4. Be sure to carry out grounding in order to ensure the noise tolerance.
The ground points should be near the compressor or the controller to make the wire length shorter.
Piping
Warning
1. Start-up of this product may be unstable or disabled while it is still pressurized.
Release the pressure inside before restarting the product.
2. Make sure to mount a silencer to the inlet port.
This will reduce the noise and prevent intrusion of any foreign matter.
3. Use piping materials that can accept the rise in temperature that can result from use of this product.
Handling
Warning
1. If a danger of human injury is expected due to abnormal heat generation, smoking, ignition, etc.,
of the controller and its peripheral devices, cut off the power supply of the product and the system
immediately.
2. Do not operate in series or apply pressure to the inlet port.
The discharge pressure will exceed the specifications and may cause damage or accidents.
3. When using in an environment with high humidity, regularly perform flushing and discharge the
condensed water to prevent accumulation of condensed water inside the product.
Otherwise, the performance will significantly deteriorate.
[Storage]
1. Do not store the product in a place in direct contact with rain or water drops or where it is exposed
to harmful gas or liquid.
2. Store in an area that is shaded from direct sunlight and has a temperature and humidity within the
specified range (10°C to 30°C and 35 to 85% no condensation or freezing).
3. Do not apply vibration or impact to the product during storage.
Caution
1. Do not switch the suction and exhaust ports to change from a positive pressure (compressor)
application to a negative pressure (vacuum pump) application.
The performance will be significantly reduced. This warning also applies in the opposite situation.

- 8 -
1.Outline
1.1 How to order
CRP
10
-
S
1
-
A
P
-
K
V
Controller mounting
Symbol
Mounting
S
Screw mounting
D
DIN rail mounting Note1
Cable length
Symbol
Length
1
1m
Solenoid valve
for exhausting residual pressure Note4
Symbol
Solenoid valve
Nil
None
V
V124-5LU-M5
Check valve
for exhausting residual pressure Note3
Symbol
Check valve
Applicable
tubing O.D.
Nil
None
-
K
AKH06-00
6mm
Silencer for inlet port
Symbol
Silencer
Noise
Nil
None
75dB
A
AN10-01
62dB
B
ANB1-01
55dB
Digital pressure switch
Symbol
Digital pressure switch
Nil
None
P
ISE20A-Y-01-J-X603 Note2
Note1) DIN rail mounting bracket is included in the package. DIN rail is not supplied.
Note2) Items below are set as the default setting for ISE20A-Y-01-J-X603.
-Reversed output setting; Reversed output
-Pressure setting; n_1, n_2=0.3(MPa)
-Hysteresis; H_1, H_2=0.2(MPa)
Order separately for piping specifications other than M5 and for options.
Note3) AKH06-00, which is the check valve with One-touch fittings (straight type) is selected.
A separate order is necessary when selecting different piping diameters, male connector types,
and other specifications.
Note4) It is of a direct operated 3-port solenoid valve V100 series and the normally open specification.
In addition, the read wire length of the connector assembly is 300 mm and a silencer AN05-M5
for the exhaust port is included in the package.
Select the direct operated type when using other solenoid valves.
This product controls pressure by connecting the pressure switch to the controller
and performs stop and startup (unload/load).
Select a PNP output specification when ordering separately.
Configure a residual pressure relief circuit. See section 21, piping.
It does not start up or restart when pressure is remaining in the compressor.

- 9 -
1.2 Accessories
1) Controller
2) DIN rail mounting bracket (P/N P604010-1)
Provided when D is selected for the controller mounting method.
3) Motor cable 1m
4) Senser cable 1m
Longer hooks
Longer hooks
Cross recessed binding head screw; 4pcs
M3x0.5x6

- 10 -
1.3 Compressor construction
To MOTOR
Motor cable 1m
To SENSOR
Senser Cable 1m
To PRESSURE SWITCH
COM -
IN
COM +
DC(+)
OUT
DC(-)
OUT
To Inlet port
AN10-01
Silencer
AKH06-00
Check valve
2
3
ISE20A-Y-01-J
Digital pressure switch
AN05-M5
Silencer
V124-5LU-M5
Solenoid valve
Pneumatic equipment
Refer to the catalog and operation manual of the individual components when using them.
Provided by the customer
Power supply
24VDC
To POWER
24V
GND
GND

- 11 -
1.4 Specifications
Items
Specifications
Compressor
Compression method
Reciprocating (oil-free)
Max. discharge/ vacuum pressure
0.55MPa/ -70kPa
Max. discharge/ vacuum flow rate
10L/min (ANR)
Unloader method
Digital pressure switch
Duty cycle
Continuous
Noise Note1
AN10-01: 62dB or less
ANB1-01: 55dB or less
Operating temperature range
5 to 40oC
Operating humidity range
80%RH or less (No condensation)
Weight
3.1kg
Controller
Installation
Separation
Power supply
DC24V±10% Note2
Rated current
4.5A
Instantaneous current consumption
Max. 8A
LED display
Function
status
POWER (green)
Power ON: Light
ALARM (red)
Alarm: Light or flashing
Pressure switch input
IN (Input for Pressure switch)
1 PNP input
Input current 3.5mA±20% at DC24V
COM+, COM- (
Power supply output for Pressure switch
)
DC24V+10%-15%, Max. supply current 200mA
Pressure switch compatible part number
High-Precision Digital Pressure Switch ISE20 series,
PNP open collector output type
ISE20A-Y---J-X603
Mounting
Screw mounting / DIN-rail mounting
Cable length
1m or less
Cooling system
Natural air cooling
Operating temperature range
5 to 40oC
Operating humidity range
80%RH or less (No condensation)
Insulation resistance
Between batch of external terminals and case
50MΩ (DC500V)
Weight
Screw mounting 340g
DIN rail mounting 360g
Note1) Reference values based on a position 1 m away from the intake port in an anechoic chamber at positive
pressure.
Note2) In case of power supply has overcurrent protection function, Automatic recovery type and Constant
current type are adequate.
-80
-60
-40
-20
00246810
Vaccum pressure kPa
Flow rate L/min(ANR)
0
0.1
0.2
0.3
0.4
0.5
0.6
0 5 10
Pressure MPa
Flow rate L/min(ANR)
Compressor flow characteristic
Vacuum flow characteristic

- 12 -
1.5 Parts description
The detailed descriptions of each part of the compressor are follows:
No.
Name
Description
1
Motor power connector
(3 pins)
Use to connect motor cable.
2
Motor sensor connector
(6 pins)
Use to connect sensor cable.
3
FE
Function earth
Use to connect the earth wire.
4
Caution label
Do not remove the caution label under any circumstance.
5
Inlet port
When using the product as a compressor, mount the silencer
AN10-01or ANB1-01 here (supplied as an accessory).
6
Discharge port
When using the product as a vacuum pump, mount the
silencer AN10-01 here (supplied as an accessory).
7
Air intake
An axial flow fan exhausts heat through the vent.
Be aware that when the vent is blocked, the product can
overheat, and operation will be stopped by a safety function.
8
Heat vent

- 13 -
The detailed descriptions of each part of the controller are follows:
No.
Label
Name
Description
1
POWER
Power supply connector
(2 pins)
Use to connect the controller power supply (DC24V).
24V: Connect to the 24 VDC of the power supply
GND: Connect to the 0 VDC of the power supply
2
PRESSUE
R SWITCH
Pressure switch
connector
(3 pins)
Connect the output of the pressure switch and the power
supply input.
IN: Connect to the output of the pressure switch.
COM+: Connect to the + side of the power supply input of
the pressure switch.
COM-: Connect to the + side of the power supply input of the
pressure switch.
3
MOTOR
Motor power connector
for compressor
(3 pins)
Use to connect the motor cable.
4
SENSOR
Motor sensor connector
for compressor
(6 pins)
Use to connect the sensor cable.
5
POWER
LED
Power supply LED
(green)
Power ON: Green light
6
ALARM
LED
Alarm LED (red)
Alarm: Red light or flashing
7
-
FE
Functional earth
Fasten it with the controller mounting screw when mounting
the controller and connect the grounding cable. See page 17.
To controller
To compressor
Motor cable
Sensor cable
terminal
controller
24V output
0V output

- 14 -
1.6 Outline dimensions
The dimensions of the compressor are shown in the diagram below.

- 15 -
The dimensions of the controller are shown in the diagram below.
1) Screw mounting
2) DIN rail mounting

- 16 -
2. Installation
2.1 How to install the compressor
1) Installing the compressor
Air intake and heat exhaust functions use a fan to cool down the compressor. Ensure a clearance of
30mm or more from the installation surface, 30mm or more around the product, and enough space for
maintenance.
Use M6x1 stud bolts and M6 nuts for fastening the product to the installation surface. Use anti-vibration
rubber if a large amount of vibrations are transferred to the embedded surface.
2) Ground wire connection
Connect the grounding cable to the compressor to shield the brushless motor from noise.
Use M3 x 0.5 screws.
fu
Caution
The M6 stud bolts, M6 Nuts, or the anti-vibration rubber, and the cable with crimping terminal, M3
screw should be obtained separately.
Ground the compressor to shield it from electric noise.
30mm or more
30mm or more + space for maintenance
Intake air
Exhaust heat
Exhaust heat
Mounting surface
Stud bolt or Anti-vibration rubber
M3x0.5 depth 6
Cable with crimping terminal
When using a stud bolt, tighten the nut with a
torque of between 5.2 and 7.3 N·m.
When using an anti-vibration rubber, fasten it
according to its specification.

- 17 -
2.2 How to install the controller
1) How to install
The controller can be direct mounted using screws or mounted on a DIN rail.
The followings are the descriptions on how to install each type.
2) Ground wire connection
Connect the grounding cable with any of the screws used in mounting the controller to any of the four
screw holes of the controller. Note that M4 nuts need to be obtained separately when using the DIN rail
mounting. See below for examples of both mounting types.
1) Screw mounting
2) DIN rail mounting
Installation with four M4 screws
Installation with the DIN rail
Caution
The M4 screw, cable with crimping terminal, toothed lock washer, M4 nut should be obtained separately.
Ground the controller to shield it from electric noise.
Caution
The earthling should be the dedicated grounding point as function grounding.
The cross section of the grounding wire should be greater than 2mm2.
The ground point should be near this controller to make the wire length shorter.
Other device
Controller
Compressor
Controller
Compressor
Other device
Not Recommended grounding
Recommended Functional grounding
Screw direction
Ground wire
Screw direction
controller
When Screw mounting
Cable with crimping terminal
When DIN rail mounting
Cable with crimping terminal
Toothed lock washer
M4 screw
M4 nut
controller
DIN rail mounting bracket
Mount the DIN rail bracket the
controller using M3x6 screws
supplied with the product (use
tightening torque of 0.4N·m).
Mount the Mount the controller onto
the DIN rail plate using M4 screws
supplied with the DIN rail mounting
bracket. (use tightening torque of
0.6N·m).

- 18 -
3) Mounting location
Design the size of the control panel and the installation so that the temperature surrounding the
controller is 5 to 40oC or less. Allow 60 mm minimum space between the front of the controller and
the door (lid) so that the connectors can be connected and disconnected as shown below.
Avoid mounting the controller near a vibration source, such as a large electromagnetic contactor or
circuit breaker on the same panel.
Caution
If the mounting surface for the controller is not flat or is uneven, excessive stress may be applied to
the enclosure, which can cause failure. Be sure to mount on a flat surface.
Door (Lid)
60mm minimum
Controller

- 19 -
3. Wiring and Piping
3.1 Pressure switch setting
This product controls the pressure and performs stop / start (unload / load) by connecting the pressure
switch to the controller. Use the designed setting when transmitting the output of the pressure switch to
PLC and receiving from the PLC to the controller.
Recommended pressure switch product number: ISE20A-Y-*-*-J**
1) Supply 24 VDC power source to the controller and the pressure switch. At this time, do not connect to IN.
Blue
DC(-)
Brown
DC (+)
24V
GND
Pressure switch
ISE20A-Y-*-*-J**
DC24V
+
-
Caution
In case of power supply has overcurrent protection function, Automatic recovery type and Constant
current type are adequate.
Reverse connection of supply power voltage may result in a malfunction.
Lead wire
Lock
Locking
lever
Connect the blue lead wire [DC (-)] of the pressure switch to the controller [COM-].
Connect the brown lead wire [DC (+)] of the pressure switch to the controller [COM+].
Insert the lead wire.
The lead wire is not secured when
the white lock is down.
Use a tool, such as a watchmaker’s
screwdriver to lock by pushing upwards.
Push down the locking lever to unlock.
Insert the lead wire and return the
lever to its locked position.

- 20 -
2) Operate the pressure switch and configure it to the settings similar to the example below.
Refer to the ISE20 series, catalog, and Operation Manual for information on how to configure.
Example of positive pressure
Load pressure = 0.3MPa, Unload pressure = 0.5MPa:
-Output mode: Hysteresis mode
-Normal or reversed output: Reversed output
-Set pressure value (Threshold value): n_1, n_2=0.3 (Load pressure)
-Hysteresis value: H_1, H_2=0.2 (Unload pressure– Load pressure)
-Delay time: Optional
-Display color: Optional
The ISE20A-Y-01-J-X603 digital pressure switch has the reverse output and pressure setting in the above
example as default.
Example of negative pressure:
Load pressure = -50kPa (-0.050MPa), Unload pressure = -70kPa (-0.070MPa):
-Display unit selection: kPa or MPa
-Output mode: Hysteresis mode
-Normal or reversed output: Normal output
-Set pressure value (Threshold value): P_1, P_2= -50kPa (0.05MPa) (Load pressure)
-Hysteresis value: H_1, H_2=20kPa ( |Unload pressure – Load pressure| )
-Delay time: Optional
-Display color: Optional
Function
Content
Setting
Value
F1
Reversed
output setting
1ot
1_n
(Reversed output)
Pressure
setting
n_1
0.300(MPa)
Hysteresis
setting
H_1
0.200(MPa)
F2
Reversed
output setting
2ot
2_n
(Reversed output)
Pressure
setting
n_2
0.300(MPa)
Hysteresis
setting
H_2
0.200(MPa)
Refer to the operation manual PS**-OMU0003.
Hysteresis H
(0.2MPa)
ON
OFF
n_1, n_2
(0.3MPa)
Switch output
Positive
pressure
(0.5MPa)
Function
Content
Setting
Value
F0
Display unit
selection
Unit
kPa
MPa
F1
Reversed
output setting
1ot
1_P (Normal output)
Pressure
setting
P_1
-50(kPa)
-.050(MPa)
Hysteresis
setting
H_1
20(kPa)
0.020(MPa)
F2
Reversed
output setting
2ot
2_P (Normal output)
Pressure
setting
P_2
-50(kPa)
-.050(MPa)
Hysteresis
setting
H_2
20(kPa)
0.020(MPa)
Hysteresis H
(20kPa)
ON
OFF
P_1, P_2
(-50kPa)
Negative
pressure
Switch output
(-70kPa)
Table of contents
Popular Air Compressor manuals by other brands
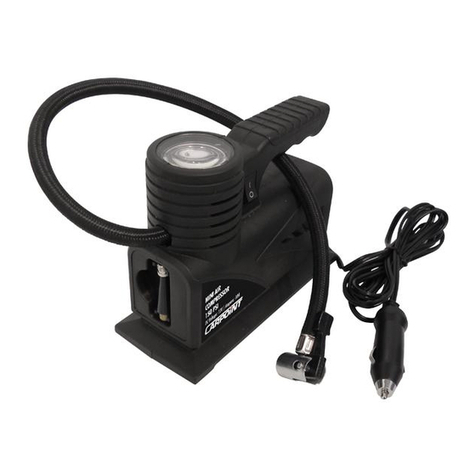
CARPOINT
CARPOINT 0623213 user manual
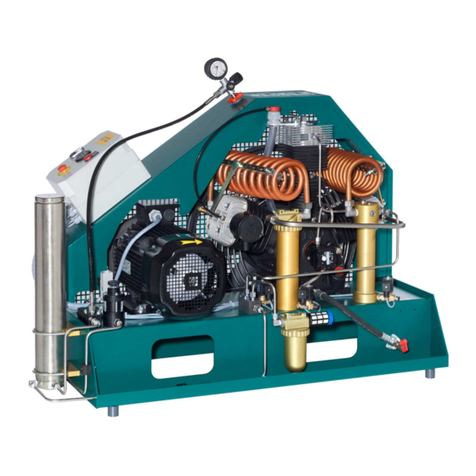
L&W Compressors
L&W Compressors LW 300 EC III operating instructions
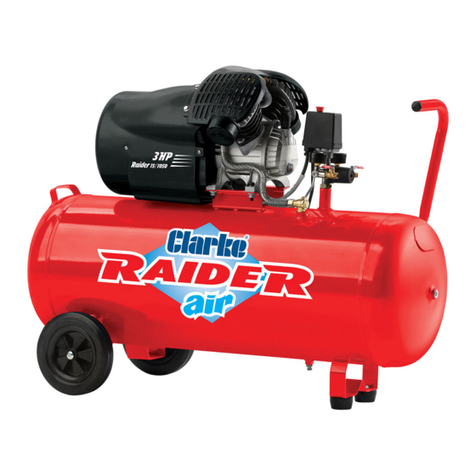
Clarke
Clarke RAIDER 15/1050 Operation & maintenance instructions
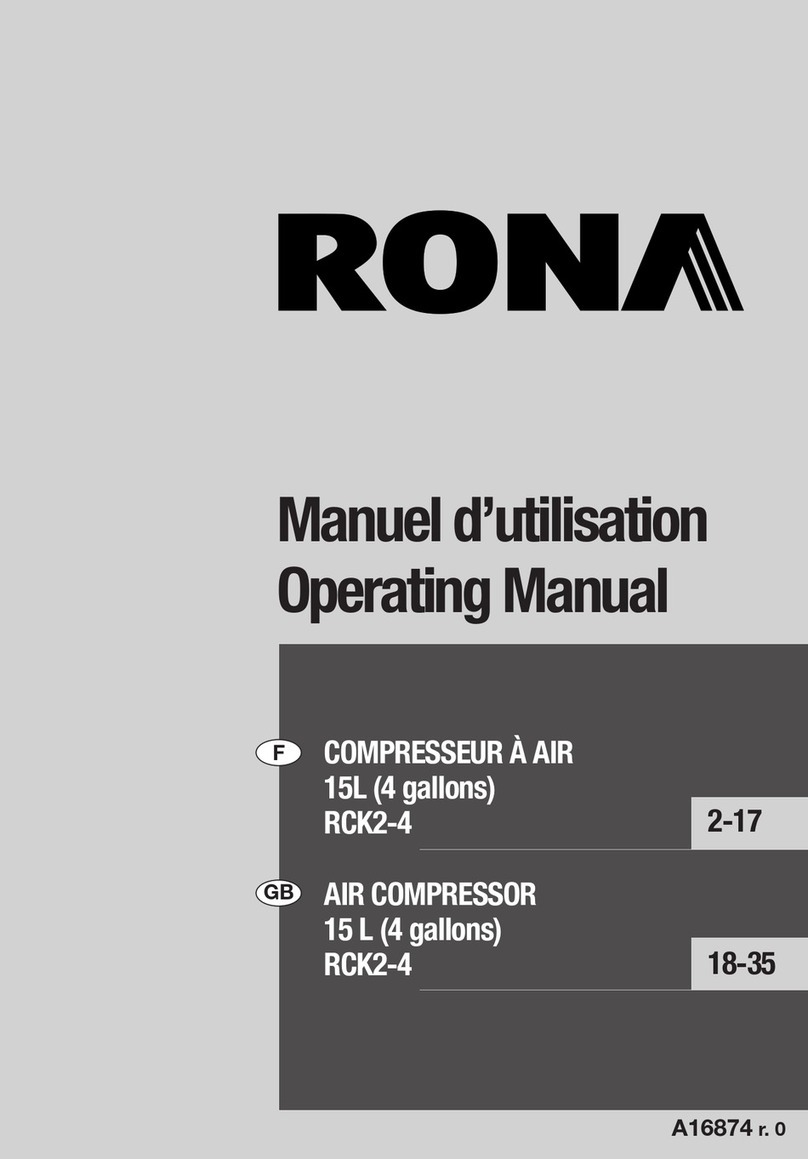
Rona
Rona RCK2-4 operating manual
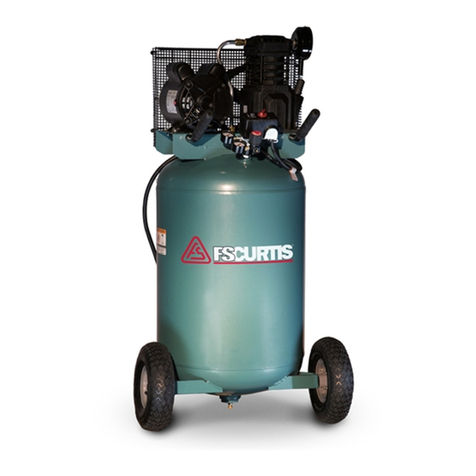
FScurtis
FScurtis FCT02C48V3X-A1X1XX Operating instructions and parts manual
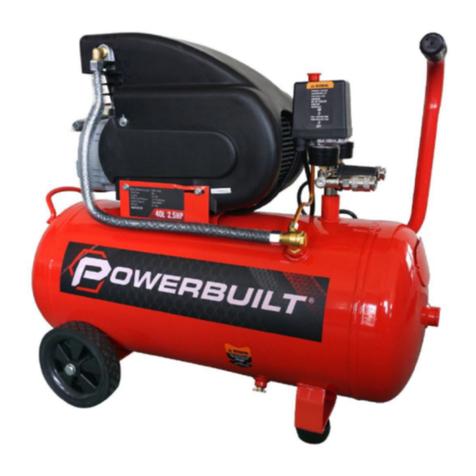
Powerbuilt
Powerbuilt AC4025 Owner's Manual and Operating Instructions
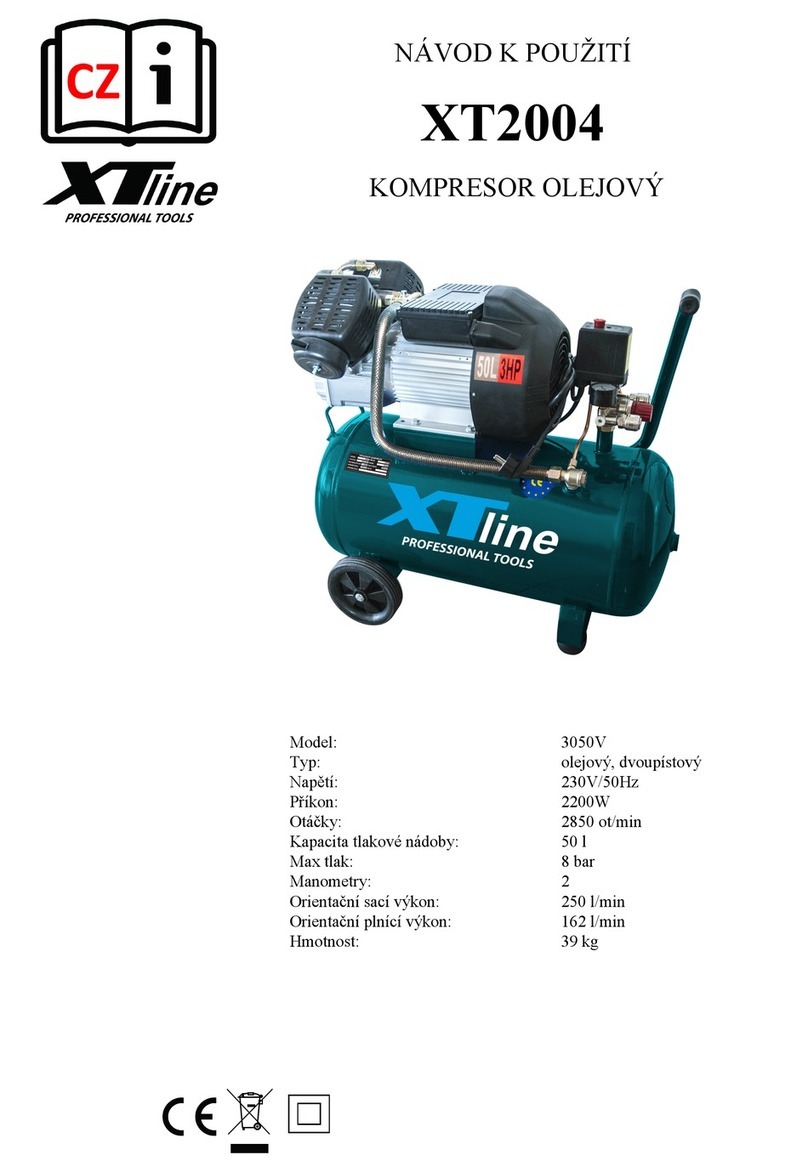
XTline
XTline XT2004 manual
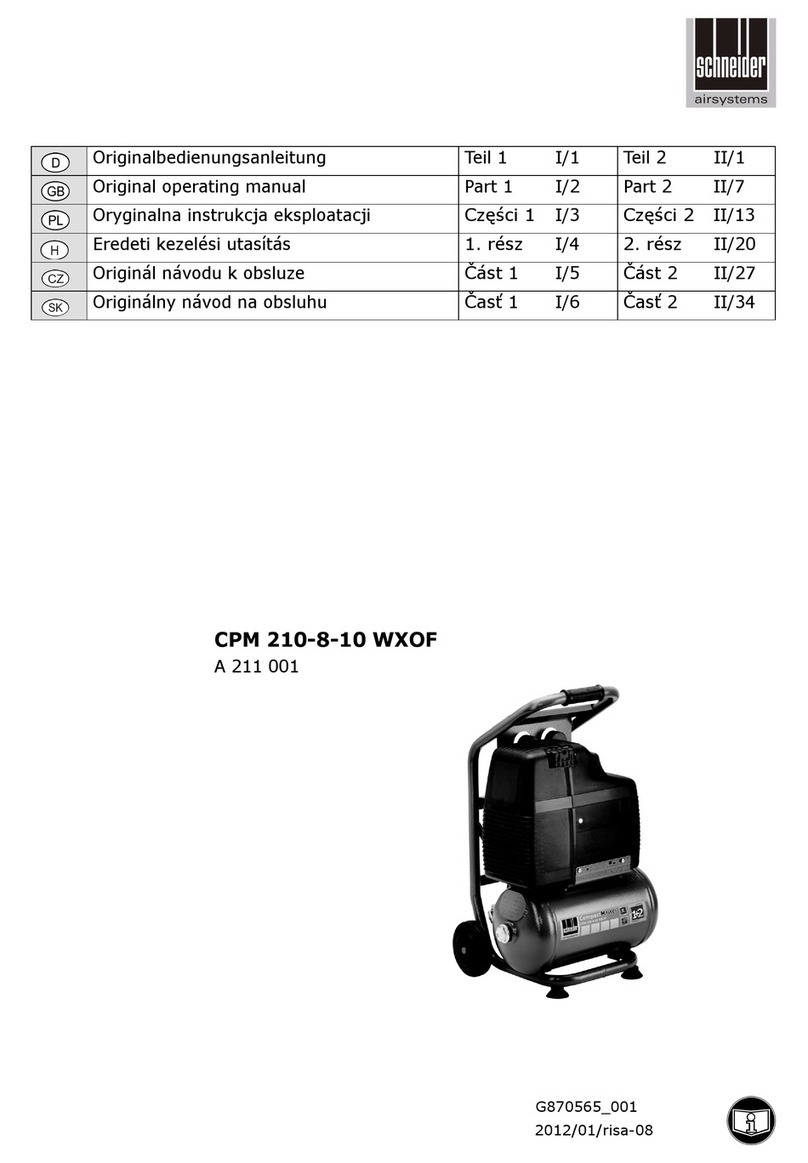
Schneider Airsystems
Schneider Airsystems CPM 210-8-10 WXOF Original operating manual
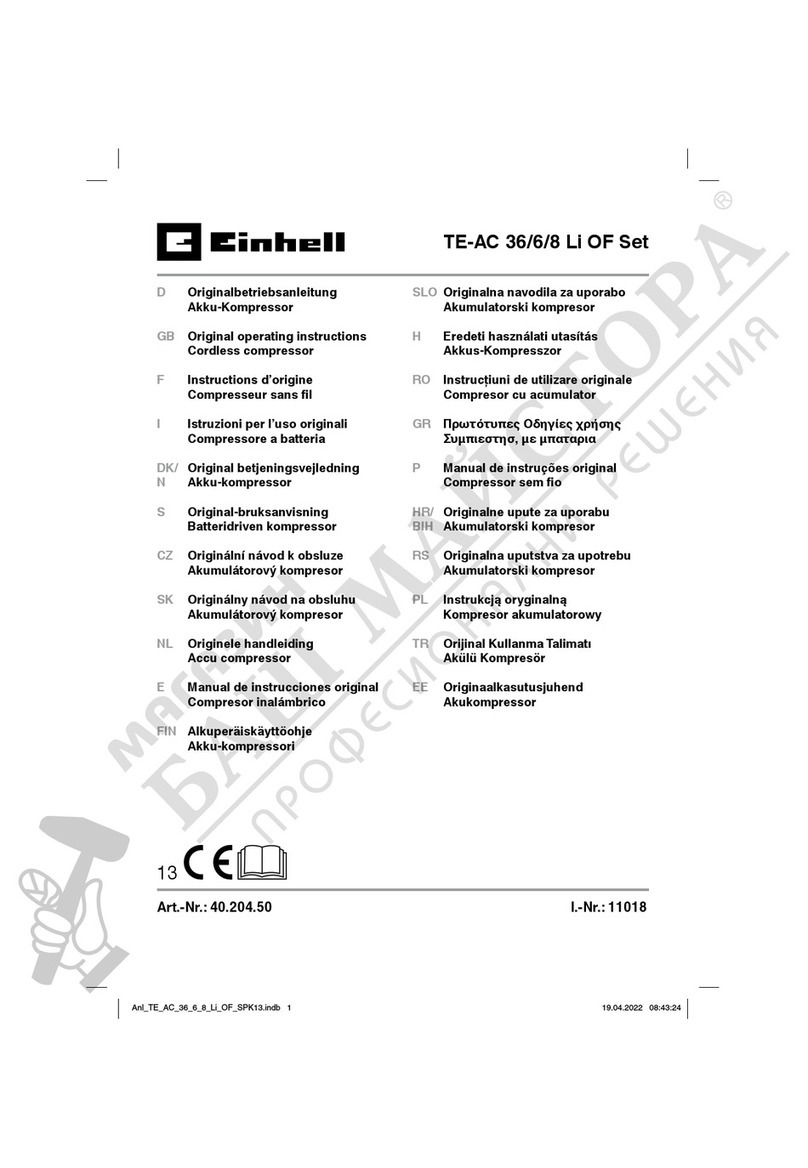
EINHELL
EINHELL TE-AC 36/6/8 Li OF Set-Solo Original operating instructions

Clarke
Clarke AIRMASTER 18/150 Operation & maintenance instructions

Keiser
Keiser 1021 Operator's manual
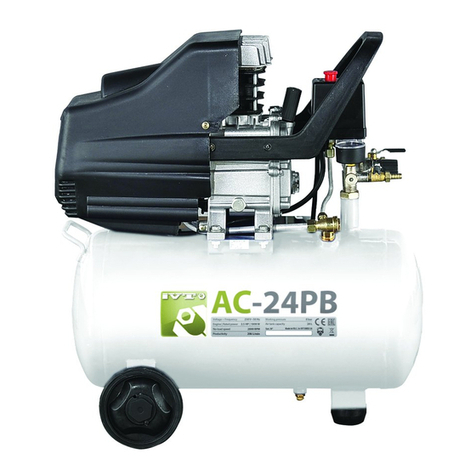
IVT
IVT AC-24PB manual