SynthCube Fuzzbass TTSH Version 4 User manual

1
TTSH Version 4 Build Guide
By Fuzzbass, for Synthcube
Version 1.2 September 2019

2
Contents
About This Guide.....................................................................................................................................3
Transistor Coupling and Matching ...........................................................................................................4
Part Substitution .....................................................................................................................................5
New in TTSH V4.......................................................................................................................................6
Known issues in TTSH V4 .........................................................................................................................6
Quirks......................................................................................................................................................7
Main Board Power System.......................................................................................................................7
Planning for Modifications.......................................................................................................................8
Construction –Getting Started ................................................................................................................8
Construction –Main Board Phase 1....................................................................................................... 14
Construction –Main Board Phase 2.......................................................................................................20
Construction –Main Board Finishing Up................................................................................................23
Check out and Calibration...................................................................................................................... 25
Fuzzbass TTSH VCO Pitch Calibration Routine ........................................................................................26
Putting It All Together ........................................................................................................................... 30
Modification: Add Power Taps for Future Mods..................................................................................... 31
Modification: AC Coupling on the VCF Audio Mixer Inputs.....................................................................31
Modification: Gate Booster Installation .................................................................................................32
Modification: External Control –Electronic Switch.................................................................................33
Modification: Adding a MIDI-Implant.....................................................................................................34
Modification: Improving Calibration Accuracy .......................................................................................35
Modification: Reverb Improvements ..................................................................................................... 36

3
About This Guide
This document presents one approach to building the TTSH. There are other approaches that are
perfectly valid. This approach is designed to minimize the time for construction. These steps have
been used to successfully build a large number of TTSH units. Typical build time for the author,
using this method, is 32 hours.
The TTSH is not a beginner’s project, and this guide assumes general knowledge of through hole
electronics construction on the part of the builder. It does not describe how to make solder joints,
or how to identify parts. It describes a certain order to install parts, and then test and calibrate the
synth.
It cannot be overstated the importance of using a good quality, temperature-controlled soldering
system to build this project. There are 3175 solder connections to be made. Use of a craft grade
iron will exponentially increase the time to build, and result in countless connections of poor quality
or non-connections, and possible component damage. If your soldering skills are not well
developed, you will have gained proficiency by the end. If necessary, refer to videos on YouTube
with explainers for through-hole soldering technique, and the various fault scenarios to watch out
for.
During the main board construction, the soldering is split into two phases. The first phase includes
immersible parts only. This is to facilitate a process using organic / water wash flux. This phase may
also be built with no clean flux.
This document lays out an approach to soldering that is considered best practice. When through
hole components are installed, the tailings for these parts are cut to length prior to soldering. The
benefits of this approach are two-fold. First, cutting after soldering can shock or damage solder
joints. Second, waste material removed and disposed of will not be contaminated with solder. This
is of particular value if you use solder containing lead.
Cutting and then soldering necessitates immobilizing components, or moving them into place as
solder is applied. Both methods are used here. The bulk of the solder joints will be formed using a
backer board to press components flush with the PCB. Various components are installed in groups,
based on their profile in relation to the PCB. For example, horizontally oriented resistors and diodes
hug very close to the board, and are installed in the first pass. This process will be described in
detail further down. Resistors and diodes that are vertically oriented, or located on the front side of
the PCB (LED circuits) are set aside at first, and installed later.
The board is silkscreened with component values, and not component numbers (ex: 1K, not R1). A
separate document has been produced showing the count of each component type and value
(resistors, diodes, capacitors and transistors) for each section of the synth. This will speed the
builder up locating footprints and installing the parts.
If you purchased the Synthcube kit, you received quantity 8 50mm M3 M-F nylon standoffs. These
are intended as stilts to raise the main board from your bench so through hole components can be

4
stuffed. These are used only during construction. If you purchased the BOM components yourself,
it is recommended you obtain these as well. Brass or aluminum standoffs work even better if you
want to spring for them.
Required non-kit items:
•Temperature controlled Soldering system.
•Flux Core Solder wire (lead free or leaded). Expect to consume about 75 feet of .031 solder
wire.
•Nylon cable ties - small
•Isopropyl Alcohol and cotton swabs
•¼ inch Heat shrink tubing (can be subbed with cable ties)
•Cutters
•#2 Phillips driver
•Nut drivers 5/16 and 1/2 inch. (Synthcube kit includes hex nuts for the 3.5mm jacks)
•2.5M hex key
•Fine tip needle nosed pliers
•Voltmeter or Multimeter, with frequency counter capability
•Oscilloscope
oA very basic kit scope such as the DSO138 is sufficient.
•ARP 2600 Service Manual
•Corrugated cardboard –continuous and unbent or creased, at least as big is the main PCB.
Useful non-kit items to have on hand:
•Liquid flux or flux pen
•Desoldering braid
•Dust-off (compressed air).
•Magnifiers
•Lead forming tool for ¼ watt resistors (Mouser part 5166-801). You will be sorry if you
embark without one of these.
Transistor Coupling and Matching
Footprints showing transistors face-to-face indicate locations for thermally coupled transistor pairs.
When such transistors are of the same type, matching them is highly recommended.
To thermally couple two transistors, place them, and add a small amount of thermal paste between
them. Place a small (3/16) length of ¼ inch heat shrink tubing over them and apply heat. Do this
before soldering. Alternatively, you can couple them using small nylon cable ties. When you are
matching transistors, you can couple them off-board. But for locations with NPN-PNP pairs that are
coupled, do this on-board, to avoid getting them reversed later during assembly.

5
Some builders have reported good results without hand matching the transistors. Doing so
increases the risk of poor performance (especially in the filter) or tracking. At a minimum, buy name
brand (ex: Fairchild/On) transistors from a reputable source, and use units from the same batch.
Buying them on feed tape for automated assembly machines ensures the units come from the same
batch. Matching will also go faster with tape feed transistors.
While some may forego matching, every location showing transistors face-to-face requires thermal
coupling.
There are many ways to match transistors, and all of them require a moderately precise voltmeter
(4.5 digits), and a process to minimize your body heat from affecting the results. The author uses
the Ian Fritz transistor matching method with a home-built rig constructed on protoboard, and
employing a Ziff Socket.
https://dragonflyalley.com/synth/images/TransistorMatching/ianFritz-transmat0011_144.pdf
The Synthcube kit contains the exact number of transistors needed to complete the build. It may or
may not yield the required number of matched pairs. The Synthcube kit used in preparation of this
document did yield all the required matches.
There are six locations that indicate a complementary pair (NPN + PNP): the 4027-1 sub boards,
4012, 4072 and VCA. These can be filled with randomly selected units, and no matching process has
been identified to improve results.
Recommended matched pairs:
•2N5087 –four pairs, 4072x4
•2N3904 –eight pairs, RMx2, VCAx1, 4012x5
•2N3906 –six pairs, RMx2, VCAx2, 4012x1, 4072x1
Part Substitution
If you are fulfilling the BOM yourself, here are some notes regarding part adjustments.
All resistors are ¼ watt through hole types and for the sake of consistency are stated as metal foil
1%. Synthcube may pack a few in the kits that are 5%, or 1/8 watt, and this is fine. It is assumed
that most of the resistors used in the ARP 2600 were 5% carbon composition types, with probably a
small number either higher precision, or hand selected. Generally you can get away with using
carbon comp resistors, but there are no guarantees, and most carbon comp type resistors have a
way of soaking up moisture and degrading slowly over time. The only resistors dissipating an
appreciable amount of wattage are the four 10R units in the Amp section, and the 100R unit
preceding the output to the reverb pan. Any others around the synth should be swappable with 1/8
watt types if you have those on hand.

6
All Electrolytic capacitors are polarized, and must have 5mm or less diameter and 2mm lead spacing.
For longer life, they should be rated for 105c operation, although only the capacitors on the DC-DC
converter sub-board will be exposed to any significant heat. The 47u units should be rated for 25V
operation, and the rest may be 25V or 50V. You will find the best selection of caps with the correct
dimensions will be rated 50V. The best choice of the 10u caps have 5x7mm dimensions, 105c and
50V rating, and 2mm lead spacing. If you get caps here that are max 7mm tall, they will fit better on
the sub boards. If you have some caps that meet all these, except are 11mm tall, you can install
them on the back sides of the VCO and VCF cores.
With one exception, all non-polarized caps have 5mm footprint, so try to get units with legs formed
to that. The exception is the two .022u box film capacitors in the Noise and S&H sections, which
have 7.5mm lead spacing. For the sake of consistency and cost, most of the non-polarized
capacitors are listed as MLCC-COG types. There are a few .1u MLCCs that are X7R rated, including
the 0805 SMD capacitors on the VCO cores. Excepting the SMD caps, any of the MLCCs can be
replaced with box film types if you have those on hand. Any type listed as film should not be subbed
with a ceramic cap of any rating.
Generally (and where available values overlap):
•A C0G MLCC is an improvement over X7R, X5R or disc capacitor;
•A box film capacitor is an improvement over a C0G MLCC;
•A polystyrene film capacitor is an improvement over a box film type.
If you are a confident builder, you may elect to omit the IC sockets. If you do, buy a couple of extra
op amp chips, in case you mangle one removing it. If you are socketing, don’t buy low cost sockets
with leaf type contacts. Just DON’T. Use only machined contact sockets.
New in TTSH V4
•All but one of the many bugs in the V3 boards have been resolved (see next section).
•The unused PDIP8 pad in LED section has been removed.
•A field change of one 220R resistor to 680R is formalized (clock rate indicator).
•Mounting points for the Fuzzbass Gate Booster PCB have been added to the EG section.
Known issues in TTSH V4
•TTSH V3 was revision 8 of the main board. This designation should have been updated for
V4, but was overlooked. V4 main boards can be identified by the lack of a DIP8 footprint in
the main LED section (front of the board, near the Ring Modulator inputs) and the word
“REV8” silkscreened on the back of the main PCB, top right corner.
•The 2N3954 dual JFET footprint in the VCO2 section (still) has reversed pins 5 and 6.
Instructions are included below to correct for this during construction.

7
If a subsequent run of V4 boards has the 2N3954 bug fixed, the revision number will be changed as
well. It may not be worthwhile fixing these, however. Every time the board design is changed, that
risks introducing new bugs. One bug on a board of this size is actually pretty good.
Quirks
Questions may arise due to some of the silkscreened information on the boards.
•As stated above, the main board is marked “REV8”whereas the 4V TTSH is a subsequent
revision.
•In the speaker amp section, there are two capacitor footprints marked “u1”. These are .1u
(100n) film capacitors.
•There are some resistors marked with an alternate value in parentheses. Ignore the
alternate value.
•Many low value capacitor values are screened with uncommon values. A more conventional
value capacitor is included in the BOM / Kit. For example, the footprint indicating “3p”
accepts a 3.3p capacitor. See notes in the Synthcube published BOM for more information.
Main Board Power System
The power rails are distributed to all sections in a middle layer of the main board. This is hidden
from view, and cannot be modified. This means you cannot drill holes in the main board without
risk of permanent damage to the system. It also means you cannot selectively power individual
sections.
There are two power distribution systems. Power rails are tapped on the DC-DC converter both pre
and post the LDO regulators. On the 5 pin headers that connect the DC-DC converter to the main
board, the pre-regulator rails are identified as +15.00V and -15.00V. When you measure them, you
will find them to be more like +/-15.8V. This is intentional, and provides for the ~.5V drop incurred
by the LDO regulators. The regulated outputs are V+ and V-. All of these are referenced to the “0”
pin. Misleadingly, there are two test points on the DC-DC converter marked +15.00 and -15.00,
when in reality they are V+ and V-, respectively. These test points are used to initially set the
regulated output voltages for V+ and V-, via the 500R trimmers. +15.00 and -15.00 power the LED
sections. V+ and V- power everything else.
Although the power and ground planes are internally routed in the board, the old power connector
pads from TTSH V1 (where power was wired up with jumpers) are still in the design, and now
function as vias from the internal power layer. These consist of twelve sets of pads for .1 pitch 2x3
pin headers. There is one in each of the major sections on the main board. Nothing needs to be
installed in these locations, but they can be used to tap power and route it to optional boards. This
is how the Gate Booster and VCO sync modifications are powered.
The location/footprint on the main board for the .156 five pin locking (Amphenol) header for power
connection to the DC-DC converter board is silkscreened backwards. If the header is installed in the

8
indicated orientation, the wires coming of the connector may create a problem with case fitting.
Install this header backwards to avoid problems.
Planning for Modifications.
A selection of common TTSH mods are presented at the back of this guide. Glance through this and
decide if any of them interest you. Almost every builder adds the Gate Booster. Some mods are
more esoteric or involved. The Electronic Switch mod is easy, has zero cost, requires no trace cuts,
sacrifices no functionality, and gets you a sub-oscillator! This one is highly recommended, and it
remains a mystery why ARP didn’t implement the Electronic Switch this way to begin with.
For mods requiring trace cuts, these cuts should be made before building commences.
Mods included in the guide:
•Extra power taps
•AC Coupling –VCF Audio Input Mixer
•Gate Booster
•Midi Implant
•Improved Calibration Accuracy
•External Clock capability –Electronic Switch
•Noise Improvements for Reverb
See these sections for installation steps and BOM info.
Construction –Getting Started
1. Whether you purchased a full kit, or assembled the BOM components yourself, refer to the
Master BOM document and verify you have all the required parts on hand. There is generally no
need to test the components. Nonetheless it is a good idea to count them and verify at least
one of the components in each bag is marked with the correct value. If you have not
memorized the resistor color codes, this will help you to do so. Alternatively, use your meter.
You can embark on the build if there are some parts yet to be received, but doing so will
increase the risk of an error or omission during the build. If you purchased the Synthcube kit,
you will want to report any missing parts as soon as possible.
2. Visually inspect all PCBs and look for physical damage, scratches that cut through traces, illegible
screen printing, cracks, etc.
3. Visually inspect the panel for damage, paint or silkscreen problems. It is likely that some of the
paint has gone into the drilling and needs to be filed or removed. Using a 3.5mm Jack, the
6.3mm TRS jack, and one of the sliders, check each hole and slider groove to make sure there is
clearance for the parts. Where issues are found, file out the openings to resolve this. The
evaluation panel sent to the author for review had a few paint problems with jack and slider
openings near the left and right edges of the panel. You want to make sure you are not dealing
with obstructed openings when you get to fitting the panel to the main board.

9
4. If you are planning to build with hand-matched transistor pairs, match them now.
Recommended matched pairs:
a. 2N5087 –four pairs, 4072x4
b. 2N3904 –eight pairs, RMx2, VCAx1, 4012x5
c. 2N3906 –six pairs, RMx2, VCAx2, 4012x1, 4072x1
5. Cut apart the 4027-1 boards and the VCF/PSU boards (which are scored). Carefully bend and
break apart the boards. Use sandpaper or a Dremel tool to smooth the edges. There are six
little riser boards intended for the slide switches, on the main PCB, next to one of the speaker
cutouts. You can cut these away with nippers or the Dremel. Discard them –they won’t be
used in this build process. Lightly clean each PCB with isopropyl (not rubbing) alcohol and wipe
dry.
6. If you plan to install the optional Gate Booster, or add AC coupling to the inputs of the audio
mixer in the VCF, there are some trace cuts to be made for these mods. A Dremel tool with a
small cutoff wheel is a good way to make these trace cuts. Be careful to make these cuts very
shallow, to ensure no damage to the center layer of the main board.
a. The standard install for the Gate Booster requires that the trace running from the tip in
of the Gate jack to pin 1 of the Gate Select switch be cut. The booster will be inserted
in-line here. See the picture below for reference.
Figure 1 Trace Cut for Gate Booster
b. To implement AC coupling for the VCF audio mixer, the board is marked for these four
trace cuts en route from the mixer’s audio input jacks, at the footprints for the required

10
capacitors. Four 1uF box film capacitors are recommend, and these are included in the
Synthcube BOM and full parts kit.
Figure 2 - Locations for trace cuts to implement AC Coupling for VCF Audio Mixer
7. Select a piece of cardboard larger than the main PCB, that is flat and without bends or creases.
Mark the outline of the main PCB on this board and cut it out. This will be the backer board for
installing the bulk of through hole components on the main PCB. You will also want a roll of
masking or painter’s tape on hand to use the backer board.
8. Build the 4027-1 VCO cores. Start with the 0805 SMD capacitors on the bottom side of the
boards. This can be done with a standard soldering iron, but be sure to dial the temperature
down to 600f/315c for the caps. SMD caps can be cracked or damaged from excessive heat –
work fast. Apply liquid flux or flux pen (not included in kit) to the pads, place the part, and bring
the iron to it with a small bead of solder on the tip. You will need to hold the capacitor in place
using tweezers while doing this. When done, inspect under magnification. If you have a
capacitance meter, you can now measure between the pads on the 3-position header location
(this is the power inlet). You should see 100n between 0V (center) and the rails. Now, test for
shorts between the pads on the power header footprint.
The 2N3904 and 2N3906, and the 1k87 tempco are to be thermally coupled using paste.
Do not install the pin headers at this stage.
4027-1
Resistors
Sockets
220r
3
DIP14 socket
3
1k
9
1k37
3
Capacitors
1k5
3
5p (C0G)
3
1k65
3
680p (Styrene)
3
1k87 (tempco)
3
10n (C0G)
6
3k9
3
100n (0805 X7R)
6

11
8k87
3
12k
6
Capacitors (electrolytic)
15k
3
10u
6
30k1
3
33k2
3
Active Components
45k3
3
CA3046
3
47k
3
2N3904
3
61k9
6
2N3906
3
68k
3
2N4125
3
100k
3
2N5459
6
121k
3
475k
3
3M3
3
Table 1 - 4027-1 VCO Cores BOM
9. Build the PSU sub-board, starting with the SMD LDO Regulator chips. The heavy tab at the top
of them needs to be soldered to the large pad footprint. First, solder one or two of the smaller
pins. The apply a generous amount of flux to the tab, turn up your iron to 630f / 325c and heat
the tab+pad for a bit before introducing solder. The time to do this depends on the heat of your
iron, and the size of your tip. Larger tips will heat the work faster and produce better results.
Maintain constant and firm pressure on the part with tweezers as you do this, and when you
remove the iron, keep the pressure on until you are sure the solder has solidified. This pressure
ensures that your iron heats the tab, and the tab heats the pad. If the pad does not heat up, it
won’t accept solder. When the work cools, make sure the chip is bonded to the big pad by
pulling up on it. Under magnification, inspect the smaller pins to make sure they are all soldered
and there aren’t gobs of solder bridging the pins. Then, install the remaining PSU parts. Install
two wire jumpers as shown. Trimmed rectifier diode (ex: 1N4001) leads are a good choice for
these jumpers, due to their increased thickness.

12
Figure 3 - Jumpers on PSU Board
PSU
Resistors
Inductors
240r
2
100uh
2
2k4
2
27k
2
Active Components
580-SPM15-150-Q12P-C
2
Trimmers
LM2991
1
500r
2
TL1963A
1
Capacitors (ceramic/film)
Locking Headers
4n7
4
.156 x 2
1
220n
2
.156 x 5
1
Capacitors (electrolytic)
10u
2
47u
3
Table 2 –PSU BOM
10. Build the 4012 VCF Core. There are five matched transistor pairs (4x 2N3904 and 1x 2N3906).
Additionally, there is one thermally coupled NPN-PNP pair. If possible, try to thermally couple
the 1k87 tempco resistor to the NPN-PNP pair.
Do not install the pin headers at the stage.
4012
Resistors
Sockets
220r
1
DIP8 socket
1
470r
6

13
820r
1
Capacitors
1k
1
10p
1
1k8
1
47p
3
1k87*
1
10n (film)
4
2k2
1
100n
2
3k32
4
10k
1
Active
Components
15k
3
1N4148
4
23k2
1
BC558
1
30k1
4
LM301
1
56k
1
2N3904
14
100k
3
2N3906
4
196k
1
2N3958
1
220k
1
Table 3 - 4012 VCF Core BOM
11. Build the 4072 VCF Core. There are five matched transistor pairs (4x 2N5087 and 1x 2N3906).
Additionally, there is one thermally coupled NPN-PNP pair. Thermally couple the 1k87 tempco
resistor to the NPN-PNP pair.
Do not install the pin headers at the stage.
4072
Resistors
Sockets
100r
1
DIP14 socket
1
220r
9
DIP8 socket
1
1k
1
1k3
1
Capacitors
1k87*
1
4n7 (Film)
4
2k2
5
10n C0G
1
4k7
1
10k
3
Capacitors (electrolytic)
12k1
7
10u
4
13K
3
39k
1
Active Components
56k
1
1N4148
1
100k
4
LM1458
1
196k
1
LM3900N
1
220k
1
2N3904
1
270k
1
2N3906
6
22M
4
2N5087
8
Trimmers
100k (Piher)
1
Table 4 - 4072 VCF Core BOM

14
12. If you plan to install a Gate Booster, build the PCB now. The Fuzzbass Gate Booster is
silkscreened with reference designators for parts (ex: R1). The parts list below assumes you are
performing the standard install, and does not include optional parts for LED gate indication.
Ferrites may be replaced with wire jumpers. 10u Electrolytic capacitors may be replaced with
1U 50V types.
Fuzzbass Gate Booster
Resistors
1k
2
R7, R15
15k
1
R11
18k
5
R3, R4, R5, R12, R13
47k
3
R6, R8, R14
82k
1
R2
100k
3
R1, R9, R10
1m
1
R16
Ferrites
2
L1, L2
DIP8 Socket
1
IC1
Capacitors
330p (film)
1
C1
100n (x7r)
2
C4, C5
10u (electrolytic)
2
C2, C3
Actives
1N4148
1
D1
2N3904
2
Q1, Q2
TL072
1
IC1
Locking Headers
1x2
3
1x3
1
Table 5 - Fuzzbass Gate Booster BOM
Construction –Main Board Phase 1
This phase will affect a bulk installation of parts that can be immersed in a water bath. If you are
using organic flux solder, phase 1 can be completed with it before washing the board and
proceeding to completion.
1. From the hardware parts, identify 4x M3 screws and 4x M3 x 50mm nylon hex standoffs. Install
the four standoffs to raise the board from your work surface, rear side of the board facing up.

15
2. Lay out parts from the table “Main Phase 1”, all resistors and 1N4148 diodes. Omitted from this
list are parts from the LED sections (front side of the board), sub boards, and vertically oriented
resistors. Stuff all parts as shown in the table. When done, you should have almost all of the
resistors and all diodes in place on the back of the main board. Take a minute to double-check
the orientation of all diodes.
Val
RM
VCO1
VCO2
VCO3
VCF
EG
VCA
MIX
Noise
VP
S&H
Amp
Total
10r
2
4
6
56r
2
2
100r
1
1
2
120r
1
1
220r
2
2
2
6
330r
1
1
470r
1
1
2
680r
2
1
3
820r
2
2
1k
4
3
4
2
3
4
3
1
3
1
28
1k2
2
2
1k5
1
1
2
1k8
2
2
2k2
3
1
4
2k7
1
1
3k3
1
1
3k9
1
1
1
1
1
1
6
4k7
2
1
3
2
8
5k36
2
2
6k8
1
1
2
8k2
1
1
9k1
1
1
10k
2
1
4
1
4
1
13
12k
1
1
15k
3
1
2
1
7
18k
4
1
5
22k
1
1
1
6
9
27k
2
2
30k1
3
1
2
6
33k
2
2
1
1
2
1
9
39k
1
1
1
3
40k2
1
1
45k3
1
1
47k
1
1
1
1
4
8
54k9
1
1
56k
2
2
61k9
2
2
68k
1
2
2
1
6
68k1
1
1

16
Val
RM
VCO1
VCO2
VCO3
VCF
EG
VCA
MIX
Noise
VP
S&H
Amp
Total
82k
2
2
4
84k5
1
1
1
3
100k
7
1
1
1
8
2
4
9
1
9
5
2
50
120k
1
1
1
3
121k
1
1
150k
1
1
1
2
1
3
9
180k
1
1
2
1
2
7
182k
1
1
196k
1
1
220k
3
3
3
1
5
2
17
270k
1
1
1
3
470k
1
1
1
1
3
2
9
680k
1
1
1M
2
1
2
1
6
1M5
3
1
4
2M2
2
2
3M3
1
1
1
1
2
6
4M7
2
2
5M6
2
2
10M
1
1
22M
4
4
1N4148
8
1
1
2
13
10
2
6
4
47
Table 6 Main Phase 1 (resistors and diodes)
3. Place your cardboard backer board over the work, and using tape, secure the edges. While
supporting the cardboard in the middle with one hand, carefully flip the work over and place it
down flat on your work surface, pressing down across it to eliminate any gaps between resistor
bodies and the main board.
4. Working from one side and moving across the board, clip all the component tails so they are ~1-
2mm proud of the board. Remove the clipped tailings, and solder everything. Inspect carefully
under good illumination to find any missed solder joints. When I do this, I move section by
section, but you may also just move across the entire board in one pass.
5. Flip the board back over and remove the cardboard. Check by feel for any loose components.
Hold the board up to a light source. Any holes that permit light yet appear to be obstructed
indicate a missed solder joint.
6. Remove the four M3 screws holding the stilts on, and replace them with 50mm stilts (front
side).
7. Referring to the LED Section table, install all parts (resistors, diodes and transistors) for the LED
sections, front side of the board. Reach under and splay the legs out to keep the parts in place
(don’t use the backing board here). Don’t miss the two resistors and one diode that are
vertically oriented, located next to the clock rate slider footprint. Double check your diode
orientation.
Slider LED sections, Front Side

17
Value
Qty
220r
6
680r
1
3k3
1
10k
1
12k
1
47k
8
1N4148
2
2N3906
1
BC337
8
Table 7 LED Sections
8. Flip the board face down, cut and solder the LED section parts.
9. Remove the four stilts on the front side, replace with M3 screws.
10. If you elect to omit the DIP8 sockets, install the op amps now. Otherwise, proceed to the next
section. Install the backer board, tape, and flip the work. Solder all pins at 600f/315c. In the
following step you will be installing capacitors only.
11. Place the DIP8 sockets. Then, place all of the ceramic/C0G capacitors. Sockets and ceramic caps
have roughly the same board profile so can be soldered at the same time. If you purchased the
Synthcube full kit, the 10uF electrolytic capacitors included have a lower profile than other
polarized caps. They can be worked in with this batch.
Val
RM
VCO1
VCO2
VCO3
VCF
EG
VCA
MIX
Noise
VP
S&H
Amp
Total
Socket
6
1
4
1
2
1
7
3
3
3
2
33
3p3
1
1
2
5p
1
1
10p
1
1
5
2
4
13
12p
1
1
20p
3
2
1
4
3
2
15
33p
2
3
1
1
4
1
3
2
17
47p
5
1
1
5
1
13
100p
1
2
2
2
2
9
220p
1
1
2
330p
1
1
1
3
1n
1
1
4
6
2n2
1
1
1
3
3n3
1
1
10n
1
1
2
1
6
11
15n
1
1
1
3
100n
2
1
1
4
10u
6
1
2
9
Table 8 Main Phase 1 Ceramic Capacitors (10u are electrolytic)
12. Install the backer board, tape, and flip the work. Find and clip the leads to all the capacitors.
You can find the count of caps in each section looking at the table. Solder everything, inspect,
flip the board back over and remove the cardboard.

18
13. Using the same process as above, place all the small signal transistors (singles, duals types and
matched pairs). Set aside the MJE172 and MJE182 transistors for now –as they stand much
higher from the board.
Note that in the first batch of V4 (Synthcube) boards, the footprint of the 2N3954 in the
VCO2 section has pins 5 and 6 reversed. If you are building this main board, be sure to
form those pins on the 2N3954 to fix that bug. This dual JFET is used to shape the
triangle wave into a sine wave.
Figure 4 - Reversed Pins 2N3954 in VCO2. Note the image shows a different transistor, but the reversed pins are as
indicated.
When all transistors (singles and pairs) are in place, place the film caps in the Amp section. Put
on the cardboard, flip it over, clip the leads, and solder. Solder the capacitors first, then proceed
to the transistors. When soldering these parts, keep your iron temperature at or below
600f/315c, and work quickly. Going section by section, solder the first lead of each transistor,
then go back and do the second leg of each, then the third. This will reduce heat stress on the
transistors, and this is especially important for matched pairs and JFETs.
Val
RM
VCO1
VCO2
VCO3
VCF
EG
VCA
MIX
Noise
VP
S&H
Amp
Total
BC558
3
1
4
8
2N3904
6
2
4
12
2N3906
6
1
3
5
15
2N3954
1
1
2N3958
1
1
2N4392
1
3
4
2N4870
1
1
2N5172
1
3
1
2
1
7
2
17
2N5460
2
2
100n(film)
2
2
Table 9 Man Phase 1 - small signal transistors (100n are film capacitors)

19
•2N3904 Matched pairs: RMx2, VCAx1.
•2N3906 Matched pairs: RMx2, VCAx2
•There are complementary pairs (2N3904+2N3906):VCAx1, (2N5172+2N3906): VCO2,
that must be thermally coupled before soldering.
14. Repeat the same process to install all remaining electrolytic/polarized capacitors on the main
board. Pay attention to orientation when placing these parts. When done, take a minute to
double-check the orientation, to avoid smoke and fire later. After this stage, you are done with
the backer board, and it can be discarded. This assumes you have previously installed the 10u
capacitors, since they stand 7mm tall, whereas all of the below are 11mm tall. If you have
11mm 10u capacitors (see table 8), add them to this lot.
Val
RM
VCO1
VCO2
VCO3
VCF
EG
VCA
MIX
Noise
VP
S&H
Amp
Total
100n
1
1
1u
4
2
2
2
2
5
2
2
5
2
4
32
1u5
1
1
Table 10 Main Phase 1 - Electrolytic Capacitors
15. Install reserved parts: vertically oriented resistors, the MJE172 and MJE182 transistors and the
22n film caps with 7.5 LS in the Noise and S&H sections.
Val
RM
VCO1
VCO2
VCO3
VCF
EG
VCA
MIX
Noise
VP
S&H
Amp
Total
100r
1
1
470r
1
1
1k5
1
1
4k7
1
1
10k
1
1
15k
1
1
22k
1
1
1M2
1
1
22n
1
1
2
MJE172
2
2
MJE182
2
2
Table 11 Main Phase 1 - Oversized parts
16. In you intend to install the four optional film capacitors to AC couple four of the inputs of the
audio mixer in the VCF, install these caps now. Remember that for them to function, traces
running under them must be cut.
This concludes Phase 1 Main Board. If you are using organic flux-based solder, now is the time to
remove it and change to no-clean solder. Use compressed air to blow water out of the nooks and
crannies, and allow the board to dry completely.

20
Construction –Main Board Phase 2
1. Start by installing the stilts, both sides.
2. Install the Amphenol headers (1x5 .156 (qty 1), 1x2 .1 (qty 5) and 1x3 .1 (qty 1). The large five
pin header for the power input should be installed reversed from the orientation indicated in
the silkscreening. This will avoid problems fitting the synth into its case. The 1x3 .1 header goes
onto the 2x3 header pad in the EG section. This will be used to power the Gate Booster. It helps
to put the headers and wire housing together before soldering them in, to avoid burning your
fingers while making final positioning adjustments.
Figure 5 - Install Power Header as shown, not as indicated in silkscreen
3. Install the .1 pin headers (males and females). Start by cutting the bulk pin header material
from the 40 pin sticks provided. You will need sections of (6) 2-pin, (3) 3-pin, and (6) 6-pin. Fit
these together with the pre-cut female headers provided. Place the headers such that the
female section is soldered to the main board, and the male section is soldered to the sub board.
Double check this before soldering –a mistake here can lead to pain later. Without going into
detail, the idea is to set the sub board on the headers, and immobilize it (cable ties for the 4027-
1s, and 12mm spacers with screws for the VCF cores). Once you have them positioned and held
in place, solder the headers –both sides. Don’t forget that there are two VCF cores that need
pin headers soldered in.
4. Install the reverb jacks. The red one goes in the location marked “to out”.
5. Install the trimmers.
6. Install the 100k audio rotary potentiometer in the Preamp section.
7. Install the sliders. Working in small groups or quadrants of the board, place the sliders and then
turn the board up 90 degrees to access the back side. While holding each slider down to the
board, and using fine tipped plyers, bend one pin at each end of the slider outward. This works
best if the pins are diagonally opposed. Lower the board down and check that each slider is
Table of contents
Popular Measuring Instrument manuals by other brands
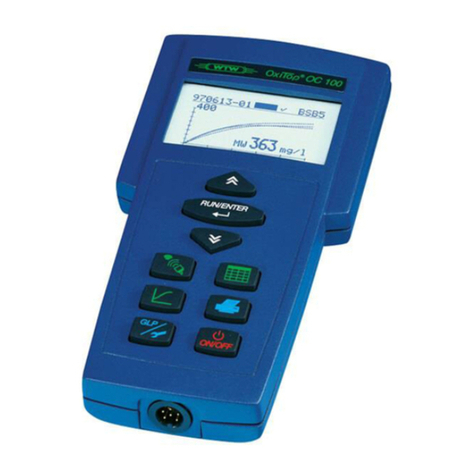
Xylem
Xylem OxiTop Control OC 100 operating manual

FISCHER
FISCHER DA09 series operating manual
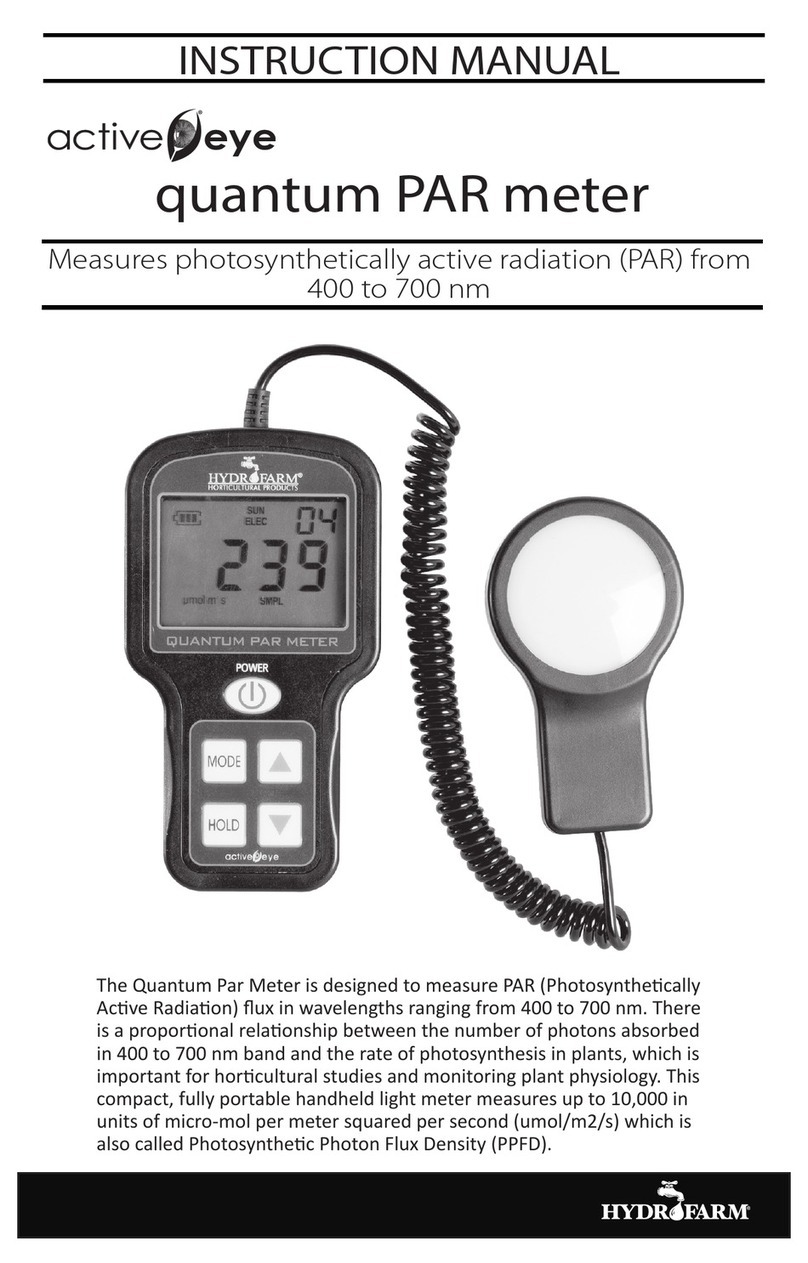
Hydrofarm
Hydrofarm Active Eye LGBQM Quantum PAR Meter instruction manual

Mars Labs
Mars Labs Titan CAI user manual
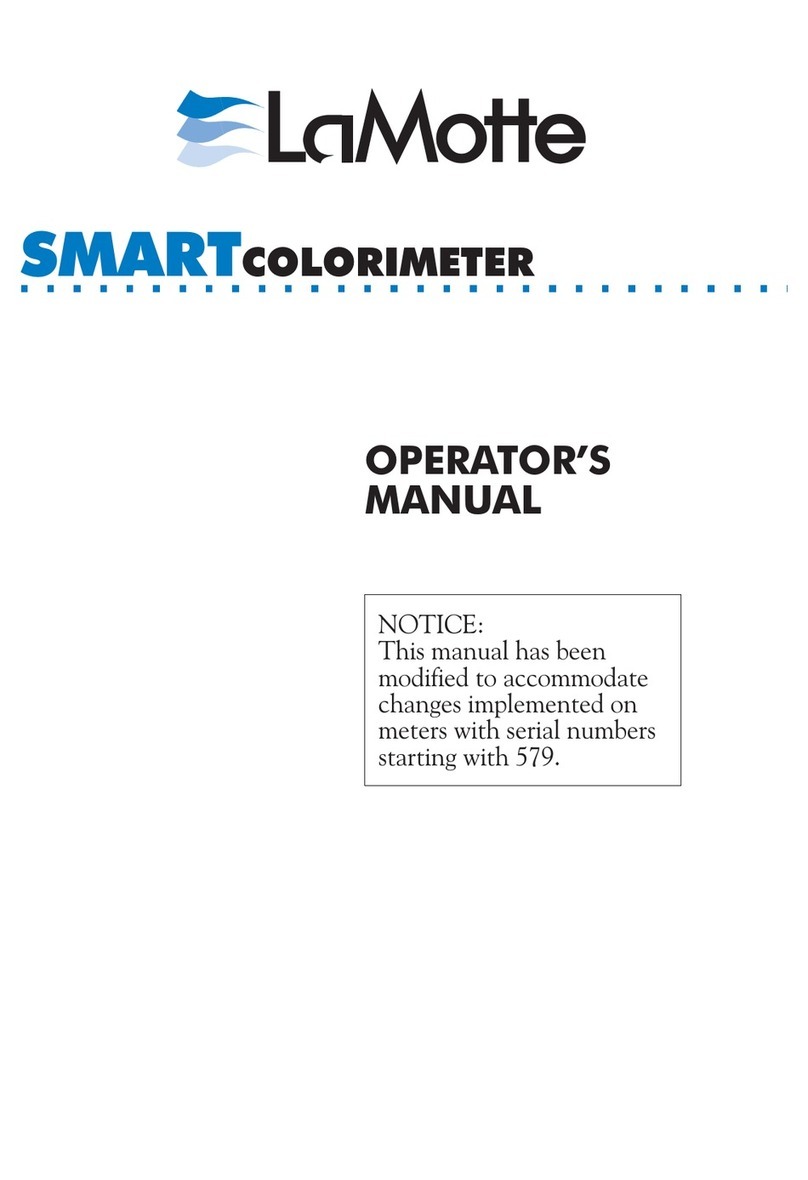
LaMotte
LaMotte SMART Colorimeter Operator's manual
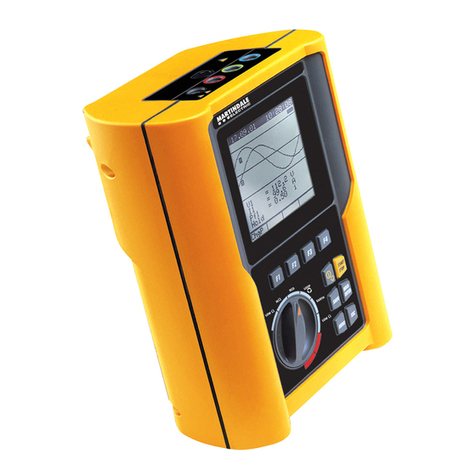
MARTINDALE
MARTINDALE VR2250 User instruction manual