Termodinamik EKY/B 20 Setup guide

EKY/B 20 - 60
SOLID FUEL HOT WATER BOILER
INSTALLATION AND USAGE MANUAL
(20 kW - 60kW)
HEATING SYSTEMS

FOREWORD
Dear Customer;
First of all, thank you for choosing our product. We hope you will get
complete satisfaction from EKY/B Natural Draft Solid Fuel Boiler.
We would like you to use your device with maximum efficiency, therefore
please read this instruction book carefully before you start using the
product and save it to refer to in the future.
This manual will help you to operate your device safely and efficiently. For
this reason you should pay attention to these:
Please read this instruction book carefully before you install and operate
the product.
Follow the instructions and the rules on safe usage.
The instruction book may apply to other models as well; the differences
between the models are clearly described inside.
HEATING SYSTEMS
Form No: 14KL.0.1.14 REV001609

CONTENT
Foreword
EKY/B 20-60 Technical Specification......................................................................1
Appliance Information..........................................................................................3
Expansion Tank Selection......................................................................................5
EKY/B 20-60 Installation Chart..............................................................................6
EKY/B 20-60 Expansion Tank Connection Chart....................................................8
Chimney................................................................................................................9
Operation of the Boiler........................................................................................11
Malfunctions and Troubleshooting.....................................................................16
HEATING SYSTEMS

EKY/B 20-60 TECHNICAL SPECIFICATION
1
EKY/B 20-60 SIDE VIEW
B
F
I
A
G
H
J
K
HEATING SYSTEMS
D

EKY/B 20-60 TECHNICAL SPECIFICATION
We are reserved the right to make changes in dimensions and appearance.
EKY/B 20
EKY/B 30
EKY/B 40
EKY/B 50
EKY/B 60
1135
1135
1285
1285
1285
590
730
790
930
1060
158
158
158
158
158
F Flue
Diameter
(mm)
G (Boiler
Inlet-Outlet)
H (Boiler
Filling-Discharge)
I (Safety
Input-Output)
kg
Weight
Water
Volume
20
30
40
50
60
EKY/B 20
EKY/B 30
EKY/B 40
EKY/B 50
EKY/B 60
3
3
3
3
3
4,5
4,5
4,5
4,5
4,5
60
75
85
100
115
235
280
320
350
390
394x330
394x330
394x460
394x460
394x440
425
425
530
530
510
500
640
700
840
970
J GRILLE
HEIGHT
(mm)
K GRILLE
DEPTH
(mm)
Capacity
(Coal)
Kw
(bar)
Operating
Pressure
(bar)
Test
Pressure
Fuel Loading
Lid Dimensions
(mm)
2
HEATING SYSTEMS
R 1 1/4"
R 1 1/4"
R 1 1/4"
R 1 1/4"
R 1 1/4"
530
530
530
530
530

APPLIANCE INFORMATION
ASSEMBLY INSTRUCTIONS
EKY/B series boilers are designed to burn different types of fuels such as wood, walnut coal,
quince coal and low-calorie brown coal in ranging capacities. As it is known, the shaft gasses
which occur as a result of burning wood and coal, and condensation of water vapors shall take
place. Make sure not to operate the boiler below 45°C. In case of operation below 45°C, the
temperature of the shaft will be low and this will cause the shaft draft to be insufficient and result
in condensation. Therefore, the life span of the boiler shall be shorter due to corrosion in short
time. This is designed to prevent the substantial decrease in the boiler outlet water temperature
and acid drop (sulfuric acid) resulting from condensation by means of cooling the firebox.
In order to increase the combustiom efficiency adjust the placement of the air supply window om
the upper door of the boiler.
3
The boiler should be leveled and installed at least at a distance of 20 cm from ground in boiler
rooms on a durable surface.
The boiler room should be regularly ventilated according to regulations and rule.
When assembling EKY/B series boilers, it is required to use open expansion tank. The
expansion tank should be located at the top of the installation and the safety pipes should be
connected to the inputs and outputs of the boiler in the shortest route possible. There should never
be any flow control units (valve, check valve, etc.) over the safety pipes. Make sure that the open
expansion tank is always full. The expansion tank volumes suitable for each boiler are given in
the table (at the page 5).
WRONG
CORRECT
WRONG
CORRECT
HEATING SYSTEMS

In order to provide for the safety of the boiler and the assembly in case of power outages,
the installation should have a by-pass line.
Make sure to use a suitable check valve for all solid-fuel boilers and the pressure of the
check valve should be equal to the maximum operating pressure of the boiler. On boilers
operating with 3 bar working pressure 3-bar safety valves should be used.
In regions prone to risk of freezing, expansion tank and insulation should be used.
The diameter of the shaft should not be smaller than the output diameter of the boiler shaft
and the instructions on the shaft assembly specified in this manual should be followed.
Expansion tank flow and return pipes should be installed with continuous upward
inclination from the boiler to the tank without any downward bending.
4
The boiler should be connected to the chimney of the building without narrowing the
diameter at the flue outlet and through pipes having minimum the same or larger diameter at
the flue outlet and through pipes having minimum the same or larger diameter as the boiler
flue outlet.
For installation of the boiler warning points indicated in the user manual must be
taken into consideration. The supplier will not take any responsibility for wrong
installation of the boiler and chimney.
During the installation of the appliance, make sure to leave some space around the
appliance depending on the properties of the appliance enough for the technical service to
handle the appliance.
Make sure the location where the appliance and the waste gas disposal line are situated is
not a living space.
In order to minimize the heat loss, the installation pipes should be heat-insulated.
Connectors and valves should be placed on inlet and outlet lines.
HEATING SYSTEMS

EXPANSION TANK SELECTION
The values given above are intended for nominal conditions. The contractor company shall
perform the precise evaluation and calculations depending on the location and operation
conditions of the boiler.
5
Boiler Capacity
(Kcal/h)
Boiler Capacity
(kW)
If Cast Sectional
Heating Radiators
are used
If Panel Radiators
are used
45 L
65 L
87 L
108 L
17.000
25.800
34.400
43.000
20
30
40
50
26 L
42 L
58 L
72 L
HEATING SYSTEMS
60 51.600 129.6 L 86.4 L

EKY-B 20-60 INSTALLATION CHART
5
A. Inlet to the Radiators
B. Outlet from the Radiators
C. Open Expansion Tank
D. Inlet to the Expansion Tank
E. Outlet from the Expansion Tank
F. Messenger Line
G. Radiators
H. Air-Purge Valve
I. By-Pass Line Valve
J. Main Pump Valve
K. Main Pump
L. Filling Valve
C
H
A
B
E
F
I
L
G G
D
PUMP ON OUTLET
K
JJ

A. Inlet to the Radiators
B. Outlet from the Radiators
C. Open Expansion Tank
D. Inlet to the Expansion Tank
E. Outlet from the Expansion Tank
F. Messenger Line
G. Radiators
H. Air-Purge Valve
I. By-Pass Line Valve
J. Main Pump Valve
K. Main Pump
L. Filling Valve
C
H
B
F
GG
D
PUMP ON INLET
E
K
JJ
I
6
EKY-B 20-60 INSTALLATION CHART
A
L
I

In places where the weather is very cold or there is risk of freezing, the expansion tank,
expansion input and output pipes should be insulated.
The input pipes connecting to the expansion tank should be assembled without turning
downwards and should steadily level up when going from the boiler to the expansion tank.
A hydrometer should be installed to the assembly in order to control the water level of the
system.
Make sure not to install units like valves, filters, check valve, etc. over the safety pipes
between the expansion tank and the boiler.
When water comes out of the messenger pipe, it means that the expansion tank is full and
the boiler has reached a specific pressure level. This should be checked at times when water
is pumped to the boiler from the main water supply.
EKY/B 20-60 EXPANSION TANK CONNECTION CHART
POSTURE OF THE SHAFT ON THE ROOF
8
These are containers open to
atmosphere and they should be
installed a distance from the top of the
pipe system for hot water systems or at
a distance from the radiator level at the
top.
For the manual feeding boiler, open
expansion tank must be used.
AIR VENT
MESSENGER
PIPE
OUTPUT
FROM
EXPANSION
INPUT TO
EXPANSION
The shaft opening should be at a distance from
the roof ridge for slant tiled roofs.
The shaft opening at a distance from the roof
ridge (only tiled roofs).
The shaft opening should be at a distance
from of at least 80 cm from the roof ridge
for slant roofs.
Roofs with little slant.
HEATING SYSTEMS

Boiler Shaft Pipe Diameter
Shaft pipes should be connected to the
shaft in a way having the same diameter
with the boiler shaft output as much as
possible.
In order to intensify the shaft draft, do
not install shaft extractor hoods, fans, etc.
to the output of the shaft.
Make sure not to use bendy pipes at the
distance where the pipes shall be installed
to the shaft from the shaft output of the
boiler.
Shaft is one of the most important units of the system. When the shaft is
not high-quality, the burning is not sufficient and no efficiency is
obtained. And this results in smoking and soot.
9
Connecting two solid fuel boilers to the same chimney is not recommended. Where this is
not achievable and if calculations based to chimney cross section and height also allow
using of other solid fuel boilers, then it is possible to connect multiple boilers into a common
flue system. In such cases the configuration indicated in the figure should be considered.
Another point to be observed is that, the
angle of the flue connection with
horizontal axis of the second boiler to be
connected should be less than the first one.
The second boiler’s flue connection to
main flue connection should be in “swept
connection” as shown in the picture.
CHIMNEY
Keep easily flammable materials away from boiler flue connections and hot areas,
which may occur around the boiler.
Minimum 50 cm
Fire proof metarial must be used for flue pipe and chimney should have
enough resistance to restrain the fire outside the chimney into the other
parts of the building through the chimney for certain time.
Do not install an aluminium folding pipe between boiler’s and
building’s flue.
Do not install any apparatus such as windrose/weathercock at outlet of
chimney.
HEATING SYSTEMS

If the shaft is made of iron sheet material, insulate the surrounding of the shaft and prevent
the heat loss.
The shaft should not have a sectional narrowness at any spot.
Make sure not to install another appliance or more than one boiler to the same shaft.
The boiler should not be installed to the shaft at a reverse angle preventing draught (see
page 16).
The shaft should be periodically cleaned not allowing for the formation of tarry soot
inside which makes it impossible to clean the shaft.
The flue pipe (chimney) mustn’tbe mounted with level which prevent the drought of it.
End of the chimney must be 40 cm higher than tip of the roof.
Chimney should be well insulated and heat losses should be reduced. When the chimney
cools down the draught also decreases and in the cooled chimney the formed acids
combined with the effect of condensation can lead corrosion on the inner surfaces of the
chimney or down inside the boiler, therefore chimneys should also be insulated.
10
HEATING SYSTEMS

1. Fully open the shaft valve before operating the boiler.
2. Make sure that the system is full of water and the air in the system is removed before
operation. The system should be slowly supplied with water to prevent air formation in the system.
3. The system should be supplied with water until water comes out of the messenger pipe for the
systems with open expansion tank.
4. After the system is filled with water, the system should be removed from air and it should be
inspected for any possible leakages.
5. In the systems with open expansion tank, the base pressure level on the hydrometer should be
marked.
6. The user of the boiler should be informed on the boiler settings, operation of the boiler and
what to do in case of emergencies.
7. Place the fuel on the sieves as shown in the burning instructions which is provided with the
boiler. Place igniting materials such as pieces of wood, firewood, etc. on the fuel to light it
manually and close the feeding lid. After it catches fire, close the lower lid and turn adjust the air
supply window on the upper door of the boiler.
8. Note that the quality of the fuel you shall use shall directly affect the efficiency of the boiler,
quality of the burning, amount of ashes and cleaning periods and the amount of bunt coal.
Therefore, we recommend you to buy some amount of sample fuel to check the performance of
the coal before purchasing large amounts.
9. The lever located near the boiler, which allows for the movement of the sieve, allows for the
ashes accumulated on the sieve to fall down. Thus, the contact of the air with fuel is minimized
and the burning quality increases
10. Do not use high-calorie brown coals in the boiler. This may cause the sieves to melt and
damage the firebox sheet.
11. For the boiler to have a long life span and for its durability, the water used should have the
nominal hardness.
12. Do not operate the boiler without water and regularly control the level of water.
13. When the boiler is operating, do not touch the hot spots with bare hands (smoke box, front lid
and interior parts of the boiler). Use protective equipments.
14. Do not open the covers of the smoke box when the boiler is operating.
15. Perform the periodical cleanings. Such cleanings shall allow you to obtain efficient and
OPERATION OF THE BOILER:
11
HEATING SYSTEMS

proper burning from your boiler.
16. If you observe an abnormal condition regarding the boiler, take the necessary precautions
immediately and contact our authorized services.
17. After the initial ignition of the boiler, the temperature of the boiler water must reach
temperature of 60°C. As soon as the temperature has been reached, set the thermostat's value as
60°C to open the air supply window for 2 mm. Further control of the air supply window will be
done mechanically in respect with the settings of the thermostat.
18. In order to set the highest value of the temperature, use the thermostat.
In order to benefit from the maximum efficiency of the boilers, regulate the air supply window on
the upper door of the boiler.
19. Pay attention to the structure of the smoke pipe in order to benefit from the maximum
efficiency of the boiler.
20. Do not leave the boiler unattended for a long time, since it's required to change the settings of
the thermostat regularly.
You should contact Termodinamik Company for appliance fuel conversion. You
should be informed by the Company on the conditions of conversion and the
procedure to be followed.
12
Boiler must be operated according to the operation instructions.
Inside of the boiler any petrolium metarials (such as styrofoam, nylon, cloth etc...)
which will cause pitch, should not be burned.
Smooth surfaces should be used as far as possible in order to reduce friction on the
inside surfaces of the chimney.
The Company cannot be held liable if the boiler consumes too much fuel in case the
boiler is not used according to the user and maintenance manual provided with the
boiler or the desired comfort temperature is not reached, of heat loss due to the
heated area and of low calorific value of the fuel that is being used.
Hydrometer must be installed to an easly visible location.
Open expansion tank must be used for EKY/B boilers.
Gas tightness of the chimney must be ensured.
HEATING SYSTEMS

13
HEATING SYSTEMS
DRAFT REGULATOR INSTALLATION
AIR
LOW
TEMPERATURE
HIGH
TEMPERATURE
BOILER
CHAIN
DOOR
a
b
COAL
c
Regulator installation:
Screw the regulator with its 3/4" outer thread into the boiler socket with
3/4" inner thread. Seal the thread (e.g. with Siseal sealant, Teflon tape…).
Turn the regulator so that for horizontal installation (a) the protrusion for
bar placing pinpoints downwards, for vertical installation (b) it pinpoints to
the front
and for horizontal side installation (c) it pinpoints upwards.
Remove the plastic transport tube and insert the hole-free end of the
hexagonal lever in itsplace. Tighten the screw in order to fix the lever in
such a position that its free end is above the fixture on the boiler door and
the lever is as close to the
horizontal position as
possible (as much the
hexagon allows).
Attach the chain to the
lever opening by means of
the bigger hook fixed to the chain. Pass the other chain
end through the fixture on the boiler door and fix this
free end on the hanging chain. Check if the chain is
hanging freely and the lever moves freely (when turning
the knob).
If the regulator is installed in the (a) position, the white
scale applies. For installations in the (b) and (c)
positions, the red scale applies.
Regulator calibration:
Fire the boiler with door manually open. Set the
regulator knob to 60. When the water temperature
reaches 60
°C, let it stabilize for a couple minutes and
then adjust the chain fixture so that the door gap is
about 1-2 mm. Now you can select the desired
temperature. If the real boiler temperature was lower
during stable operation than set, shorten the chain, if the
real temperature was higher than set,extend the chain.
Please take into account also other factors thaotucld
influence the temperature inside the boiler disregarded
of the regulator - esp. the quantity of fuel and ashes
inside the boiler, position of the secondary-air damper,
thermal lag of the boiler and of the whole heating plant.

Parameter Unit Boiler Feeding
Water
Boiler Filling
Water
Appearance
-
Clean, clear. There are solid materials and
stabile foam in it.
Conductibility at 25°C
iletkenlik µS/cm <1500
pH value at 25°C
-
Total hardness (Ca+Mg)
> 7,0 From 9,0 115ª
mmol/l <0,05
Iron concentration mg/l
<5
Compound alkaline
value mmol/l
-
Diesel/oil concentration
mg/l <1
<0,2
-
Organic particles
-
See the footnoteb
BOILER WATER PROPERTIES
14
TS EN 12953-10 Boilers: Properties of boiler and feeding water as per the Feeding and Boiler Water
Quality
aIf there are units made of materials other than steel found in the heating system (copper pipes,
aluminum radiators, etc.), they may require lower pH values and conductivity. However, the
protection of the boiler is primary in the system and the abovementioned values should be followed.
b Organic materials are generally formed by several compounds. It is hard to specify before the
effects of such compounds and their each component on the boiler. Organic compounds may
decompose and may form carbonic acid and other acidic compounds ad these may cause corrosion
and punctures in the boiler. This may cause the formation of materials such as limestone and foaming
which should be experienced at the minimum level.
It should be considered that waters with high level of hardness shall cause
calcification. The malfunctions and low performance due to calcification are not
covered in the warranty.
The problems resulting from the use of the appliance for the purposes not
intended for use (industrial use, etc.) are not covered by the warranty.
The appliance is not covered by the warranty if types of water other than
potable water are used in the boiler (artesian water, waste water, etc.).
In order to prevent calcification of water inside of the boiler and pipes, not so hard water
should be used. (The water used in system must be over FS 25 which is international
standarts for water hardness.)
HEATING SYSTEMS

CLEANING AND MAINTENANCE
15
In order to obtain efficient burning from the boiler and allow the boiler operate efficiently,
the ashes accumulated on the sieves should be periodically let down by means of moving the
ashes with the help of sieve discharge lever before adding fuel to the boiler for prismatic
boilers.
When the flames become glowing in the cylindrical boilers, the fuel should be added to the
boiler after the ashes among the glows are let down with the help of fire rake. This way, the
ashes preventing the burning air shall be removed from the sieve.
For a more efficient burning, regularly clean the ash sieve. Also;
Check the water level in the boiler before each operation.
The boiler should be operated as per the burning instructions and the flame in the burning
chamber should be controlled and full burning should be provided.
Smoke pipes, the turbulators inside the smoke pipes and the smoke box where the boiler
is connected to the shaft should be cleaned at least once a week.
Clean the shaft at least 3 times in a season.
Clean the ashes accumulating in the shaft daily. You may want to perform the cleaning
two times a day depending on the quality of the coal used (ash rate).
Make sure that dust and burning coals do not fall onto the electrical equipments of the
boiler and the fan.
Do not clean the boiler when it is operating.
You are recommended to get your boiler maintained and controlled (paid) by the
TERMODINAMIK AUTHORIZED SERVICE before the winter.
HEATING SYSTEMS

ROOM HEATER INSTALLATION CHART
RADIATOR INSTALLATION CHART FOR MULTIPLE-STORE BUILDINGS
1
OPEN EXPANSION
TANK
3
RADIATOR
BOILER
2
3
BOILER
1
OPEN EXPANSION
TANK
RADIATOR
2
16
HEATING SYSTEMS

MALFUNCTIONS AND TROUBLESHOOTING
17
PROBLEM REASON SOLUTION
Inefficient burning in the
burning chamber.
- Inefficient draught - Calibrate the draft regulator
- Clean the boiler.
- Use high-quality and dry fuel.
- Low-calorie or non-quality fuel
- Improper draft regulator settings
HEATING SYSTEMS
This manual suits for next models
4
Table of contents
Other Termodinamik Boiler manuals
Popular Boiler manuals by other brands
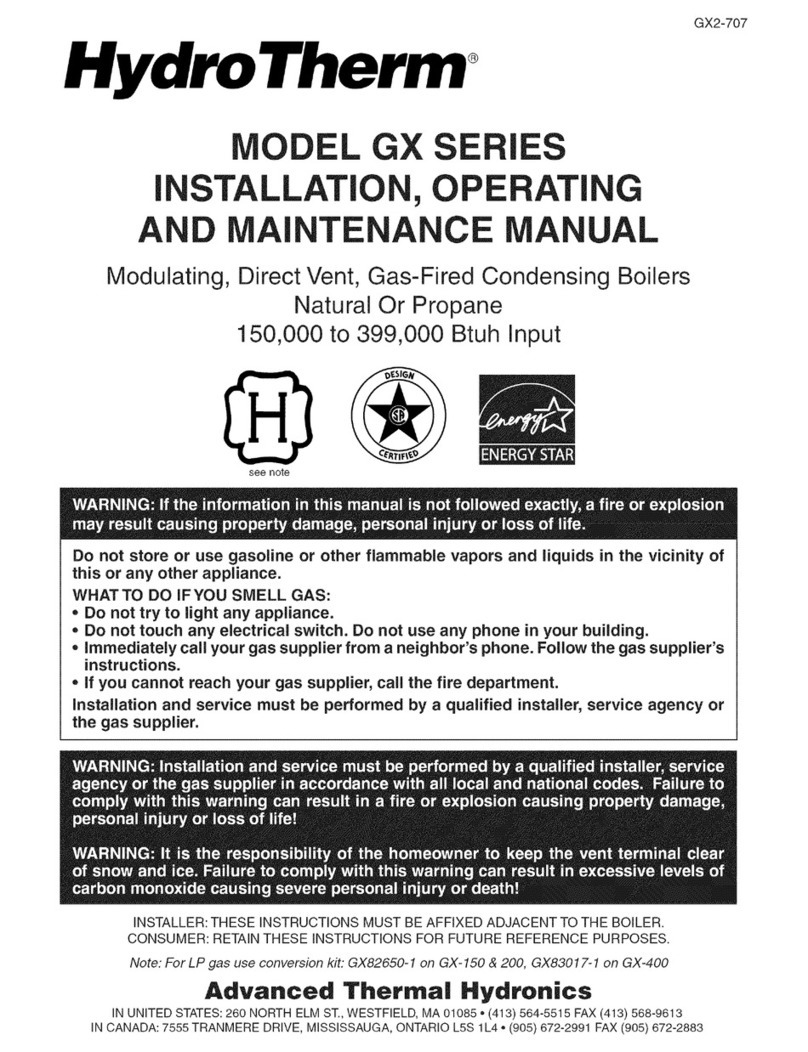
HydroTherm
HydroTherm GX Series Installation, operation and maintenance manual
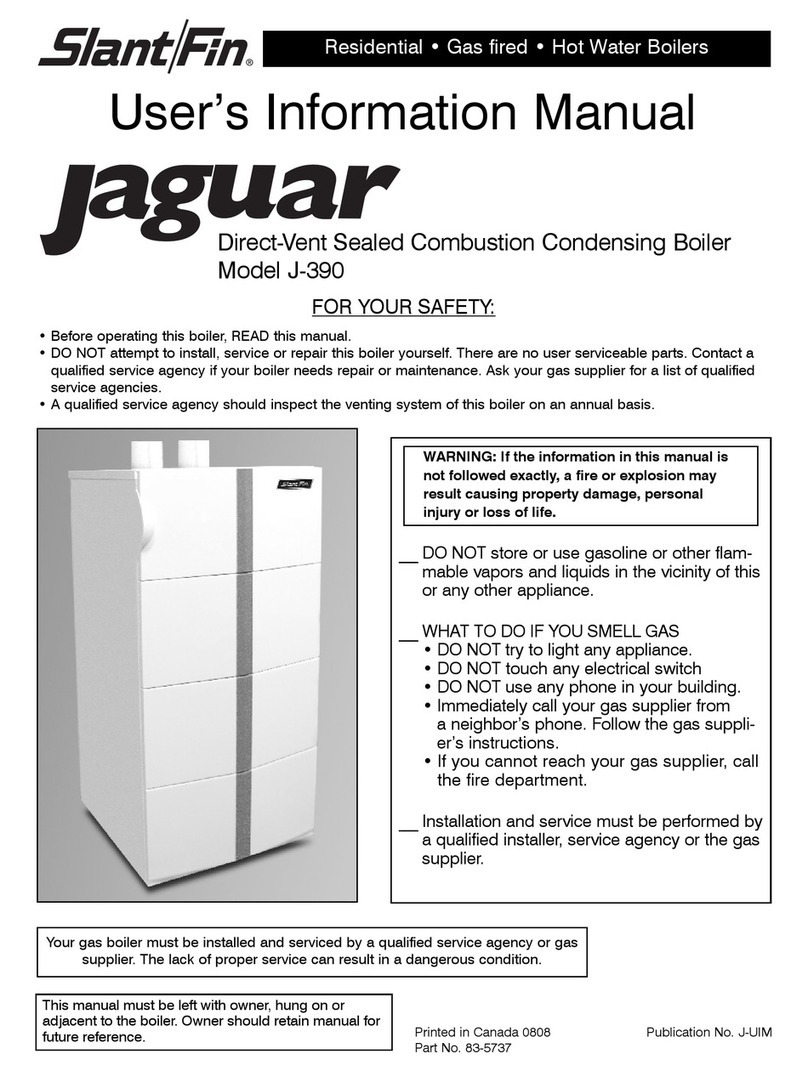
Slant/Fin
Slant/Fin J-390 User's information manual
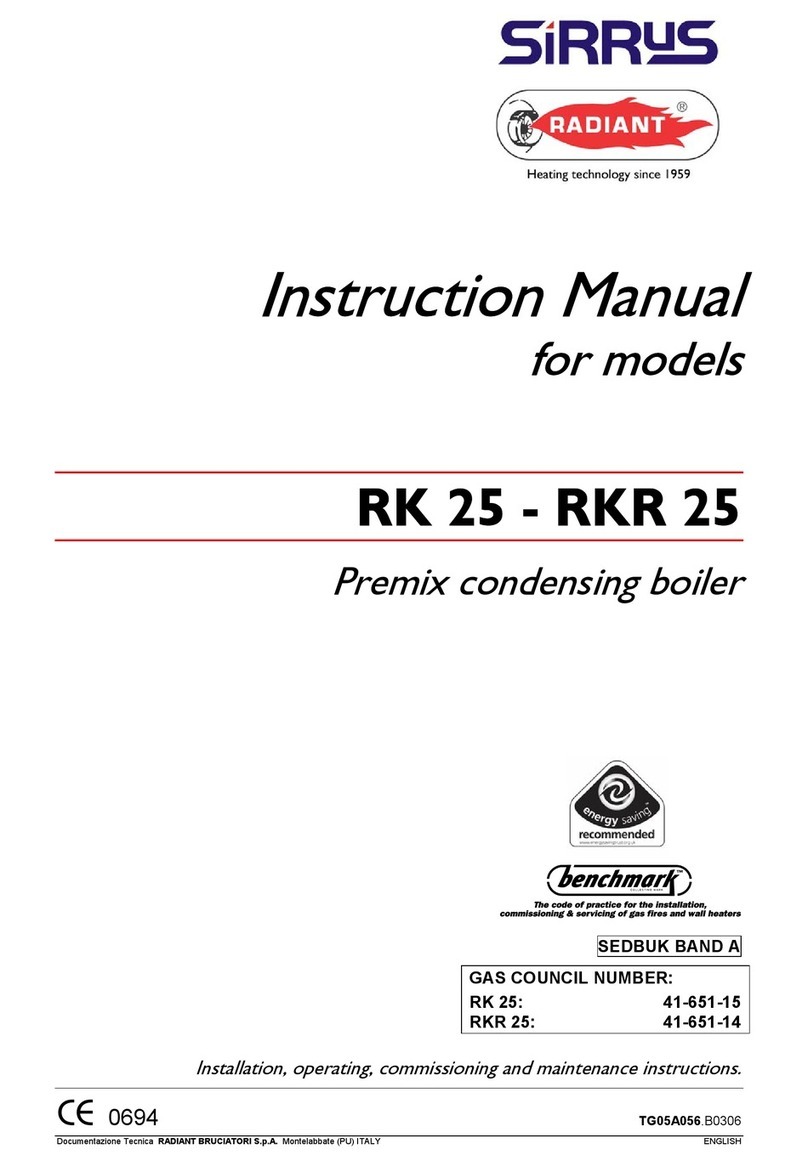
Sirrus
Sirrus RK 25 instruction manual

ECR International
ECR International Dunkirk DCC-150F User's information manual
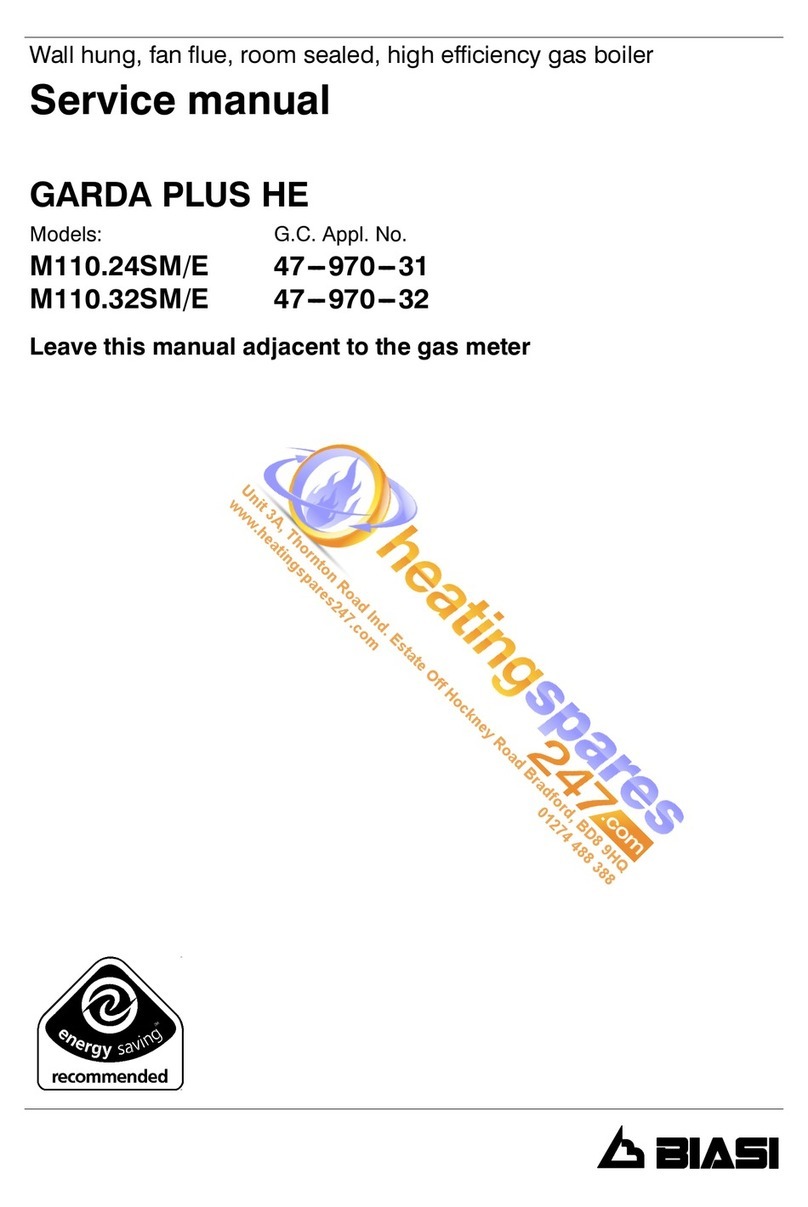
Biasi
Biasi M110.24SM/E Service manual

NTI
NTI Tft60 - 399 Installation and operation instructions