TestEquity F4T Installation and operating instructions

Copyright © 2014-19 TestEquity LLC Rev. 4.5 – July 29, 2019
Portions of this manual are used with permission from Watlow Electric Manufacturing Company, 2014-19
F4T Touch Screen Controller
Cascade Control Addendum
Revision 4.05 and higher Firmware
TestEquity LLC
6100 Condor Drive
Moorpark, CA 93021
Support: 877-512-3457 Toll Free
805-480-0638
Corporate: 800-732-3457
805-498-9933
http://www.testequity.com


Table of Contents
Chapter 1 – Safety Instructions__________________________________________________5
Introduction _____________________________________________________________________ 5
Safety Notices ____________________________________________________________________ 5
Chapter 2 – Using Cascade Control ______________________________________________7
Overview ________________________________________________________________________ 7
Navigating and Understanding the User Interface ______________________________________ 8
Home Screen – No Profile Running __________________________________________________________8
Part Control vs. Air Temperature Control ____________________________________________ 9
Part Control Mode________________________________________________________________________9
Part Control Mode During a Profile __________________________________________________________9
Air Control Mode _______________________________________________________________________10
Air Control Mode During a Profile __________________________________________________________10
Simple Set Point Enable __________________________________________________________________10
Data Logging____________________________________________________________________ 11
Logged Parameters ______________________________________________________________________11
More Information _______________________________________________________________________11
Chapter 3 – Communications __________________________________________________13
Ethernet Parameters _____________________________________________________________ 13
Changing Ethernet Parameters _____________________________________________________________13
Ethernet Parameters and Settings ___________________________________________________________13
RS-232 Parameters_______________________________________________________________ 14
Changing RS-232 Parameters ______________________________________________________________14
RS-232 Parameters and Settings ____________________________________________________________14
Common Modbus Registers________________________________________________________ 15
F4T Mode _____________________________________________________________________________15
F4 Compatibility Mode (Data Map 3)________________________________________________________17
SCPI Programming Mode _________________________________________________________ 18
GPIB and Ethernet Modbus Interface Converters (optional) ____________________________ 20
Serial Modbus-to-GPIB Converter (Options 1052 and 0003)______________________________________20
Serial Modbus-to-Ethernet Converter (Option 1056) ____________________________________________20
Programming Syntax for the F4T Controller __________________________________________________21
Chapter 4 – Retransmit Option TE-F4T-RETRANSMIT ___________________________23
Introduction ____________________________________________________________________ 23
Connections _____________________________________________________________________ 23


Chapter 1 – Safety
TestEquity F4T Controller Page 5
Chapter 1 – Safety Instructions
Introduction
Follow all CAUTION notices to prevent damage to the chamber or your test sample. Failure to
follow all CAUTION notices may void your warranty. CAUTION may also indicate a
potentially hazardous situation which, if not avoided, may result in minor or moderate personal
injury.
The safety alert symbol !precedes a general CAUTION statement.
Safety Notices
!CAUTION: The Watlow F4T Manuals are written by the manufacturer, Watlow, for a
wide variety of applications and configurations. Not all features or functions
are applicable. Only the capabilities of model F4T1L2EAA2D7030 are
applicable.
!CAUTION: The Series F4T “Alarm” functions are NOT used in the chamber’s safety
system. TestEquity does NOT recommend using the Series F4 alarm function
as the main protection device. The independent EZ-Zone Limit Controller
functions as the main protection device.
!CAUTION: When using Part Temperature Control, the Part Thermocouple must always be
attached to the device under test (DUT). Failure to do this will result in erratic
temperature control. If you do not want to attach the thermocouple to the
DUT, then select “Air Control” on the F4T.
!CAUTION: When using Part Temperature Control, the Part Thermocouple must never be
placed outside the chamber. Failure to do this will result a thermal runaway,
up to the limits set on the Limit Controller.
!CAUTION: The Series F4T Temperature Controller has been properly configured by
TestEquity to match the chamber’s system requirements and to perform
optimally over a wide range of operating conditions. Improper modifications
to these setup values can result in erratic performance and unreliable
operation. Setup examples in the Watlow Series F4T Manuals are NOT
applicable to this chamber. Do not attempt to modify the setup values, unless
you thoroughly understand what you are doing. If there is any doubt, please
call TestEquity before proceeding.
!CAUTION: Configuration files are unique to each particular model chamber and must
NEVER be transferred to a different model chamber.
!CAUTION: NEVER select “Factory” in the “Restore Settings From” prompt in the Device
Details menu in Composer Software. This will erase all controller
configuration settings. The chamber will not work if you do this.


Chapter 2 – Using Cascade Control
TestEquity F4T Controller Page 7
Chapter 2 – Using Cascade Control
Overview
Cascade Control is the technical
name for a multi-loop control
system where the air temperature
set point (Inner Loop) is
determined by deviation of the
part temperature (Outer Loop)
from its set point. The graph
shown here represents Air
Temperature vs. Part Temperature
when Cascade Control is used.
The Air Temperature is allowed to
overshoot or under shoot as
required in order to achieve the
desired Part Temperature while
minimizing lag time.
The controller is configured at the factory to allow the Air Temperature to deviate no more than
+15°C or –15°C from the Part Temperature set point. This means if the set point is 85°C, the Air
Temperature could go as high as 100°C if the Part Temperature lagged sufficiently during a heat
up condition. In the example shown here, the Air Temperature went as high as 90.7°C when the
Product Temperature achieved 83.0°C. Conversely, the Air Temperature went as low as 18.6°C
when the Product Temperature achieved 23.4°C in order to reach a 23.0°C set point. In both
instances, The Air Temperature then began to approach the Part Temperature as the part began to
stabilize, until the two temperatures were ultimately nearly identical.
Without Cascade Control the Part Temperature will take longer to stabilize due to its thermal
mass as shown in the graphs below.
Air Temperature vs. Part Temperature without Cascade Control
Part Temperature’s approach to set point with and without
Cascade Control

Chapter 2 – Using Cascade Control
Page 8 TestEquity F4T Controller
Navigating and Understanding the User Interface
Home Screen – No Profile Running
After powering up the controller a white screen will appear first while initializing. Once the
startup process is complete the Home Screen will be presented as shown below. The image
below shows the Home screen for a TestEquity Temperature Chamber with Cascade Control
while it is NOT running a profile.
①Temperature PV (Process Value):The Temperature page displays the actual Part
Temperature for PV. This is the Outer Loop.
②Air Sensor PV (Process Value):The Air Sensor page indicates the actual Air Temperature
for PV. This is the Inner Loop.
③Output Widget Bar:Function keys or output status (ON/OFF). The control mode can be
easily changed from Part Temperature Control or Air Control by pressing the Air Control
key. The default condition is shown above, with the controller operating in Part Temperature
Control mode (no green check mark in the Air Control box). See page 9 for more
information.
④Next Page: The Home screen has been setup to display multiple pages (loops). The left and
right arrows on each side of the home screen provide navigation from one to the other. Each
of the subsequent two pages has been configured by TestEquity to be a full-screen view of
just the Temperature page or the Air Sensor page respectively.
Please refer to the F4T Touch Screen Controller User’s Guide for further details on how to
navigate and use the F4T Controller.
User
2. Air Sensor
PV
4. Next Page
1. Temperature
PV
3. Output
Widget

Chapter 2 – Using Cascade Control
TestEquity F4T Controller Page 9
Part Control vs. Air Temperature Control
The control mode can be easily changed from
Part Temperature Control or Air Control by
pressing the Air Control button. The default
condition is shown below, with the controller
operating in Part Temperature Control mode (no
green check mark in the Air Control box). Air
Control will always be OFF any time the power is
recycled.
Part Control Mode
When configured for Part Control (Air Control button has no green check mark), the F4T will
attempt to control the temperature at the Part Sensor. In this mode, the Part Sensor must always
be attached to your test sample. Failure to do this will result in erratic temperature control.
The Air Sensor screen will always indicate chamber’s Air Temperature. This will usually be
different from the Part Temperature, especially during temperature transitions. The Air
Temperature will tend to approach the Part Temperature as the part begins to stabilize. The two
temperatures may never be the same, especially with a heavy test sample or an energized test
sample.
The F4T is configured at the factory to allow the Air Temperature to deviate no more than +15°C
or –15°C from the Part Temperature set point. This means if the set point is 85°C, the Air
Temperature could go as high as 100°C if the Part Temperature lagged sufficiently during a heat
up condition, or as low as –55°C if the set point is –40°C.
Part Control Mode During a Profile
Part Control mode has an impact on these profile parameters:
Guaranteed Soak Deviation/Guaranteed Soak Values: The amount by which the actual part
temperature is allowed to differ from the set point for steps with Guaranteed Soak Enable set to
On. In such steps when the actual part temperature differs from the set point by more than this
value, the step timer stops running until the actual part temperature returns to within the band
defined by the set point plus or minus this value. Each profile can have its own set of Guaranteed
Soak values.
Wait For Process:Holds the profile until the part temperature reaches the specified value.

Chapter 2 – Using Cascade Control
Page 10 TestEquity F4T Controller
Air Control Mode
When configured for Air Control (Air Control
button has a green check mark), the F4T will
attempt to control the temperature at the Air
Sensor, shown at the PV (Process Value) in the
Air Sensor screen. This is how a chamber without
cascade control ordinarily works. In this mode,
the Part Sensor does not have to be attached to
anything.
If you press the arrow on the right side of the
display you will get a screen that displays the Air Sensor and Part Sensor. You can use this
screen to monitor the Part Sensor even if you are in Air Control Mode. Pressing the arrow on the
left side of this screen will return you to the Home Screen.
In Air Control Mode, the PV (Process Value) in the Temperature screen is the Air Temperature.
Air Control will always be OFF any time the power is recycled.
Air Control Mode During a Profile
Part Control mode has an impact on the following profile parameters:
Guaranteed Soak Deviation/Guaranteed Soak Values: The amount by which the actual air
temperature is allowed to differ from the set point for steps with Guaranteed Soak Enable set to
On. In such steps when the actual air temperature differs from the set point by more than this
value, the step timer stops running until the actual air temperature returns to within the band
defined by the set point plus or minus this value. Each profile can have its own set of Guaranteed
Soak values.
Wait For Process:Holds the profile until the air temperature reaches the specified value.
Simple Set Point Enable
This function is similar to turning Air Control ON. If you leave Air Control OFF and turn Simple
Set Point Enable ON, the F4T will attempt to control the temperature at the Air Sensor.
However, the Guaranteed Soak and Wait For Process will be controlled by the Part Sensor.
This function is located in the Temperature Loop Operational Parameter screen. Pressing the
vertical ellipsis or anywhere within the outlined box shown below will provide access to the
Loop Operational Parameter screen.

Chapter 2 – Using Cascade Control
TestEquity F4T Controller Page 11
Data Logging
Logged Parameters
You can select the parameters which get logged. TestEquity has pre-configured the controller to
log the Set Point, Inner Process Value (air temperature sensor), and Outer Process Value (part
temperature sensor).
More Information
See the main F4T manual for more information about Data Logging.


Chapter 3 – Communications
TestEquity F4T Controller Page 13
Chapter 3 – Communications
Ethernet Parameters
This section describes how to configure the Ethernet Communications settings in the F4T
controller.
Changing Ethernet Parameters
1. Press the Menu, Settings and Network buttons, in that order.
2. Under Communications Channels press Ethernet.
3. Change the desired settings.
4. Recycle the power to put the new settings into effect.
Ethernet Parameters and Settings
The bracketed bold settings below represent the defaults as delivered from the factory:
•IP Address Mode: [DHCP], Fixed
-DHCP, Dynamic Host Configuration Protocol, allows for dynamic distribution of
network settings by a DHCP server.
-Fixed, also referred to as a static IP address, is configured manually for a specified
network.
•Actual IP Address: [192.168.0.222]
•Actual IP Subnet: [255.255.255.0]
-Subnet, a method used to logically divide and isolate networks.
•Actual IP Gateway: [0.0.0.0]
-Gateway, is a device used on the network to route messages with IP addresses that do
not exist on the local network.
•MAC Address: xx:xx:xx:xx:xx:xx (Will be different and unique for each controller)
-MAC address, is a manufacturer supplied address for the network interface card.
•Display Units: °F, °C [configured by TestEquity for °C]
•Modbus® TCP Enable: [Yes], No
-Modbus is an industrially hardened field bus protocol used for communications from
the controller to other devices on the network.
•Modbus Word Order: [Low High], High Low
-Modbus allows a user to select the word order of two 16-bit words in floating point
values.
•Data Map: [1], 2, 3
-Data Map, the user can switch Modbus registers from the comprehensive listing of
F4T registers.
-Map 1 = F4T registers (default)
-Map 2 = Not applicable to controllers with Cascade Control (Part Temperature
Control).
-Map 3 = For controllers with Cascade Control (Part Temperature Control). Limited
set of F4 compatible registers (for compatibility with software written for the F4).

Chapter 3 – Communications
Page 14 TestEquity F4T Controller
RS-232 Parameters
This section describes how to configure the RS-232 Modbus Communications settings in the
F4T controller.
Changing RS-232 Parameters
1. Press the Menu, Settings and Network buttons, in that order.
2. Under Communications Channels press Modbus.
3. Change desired settings.
4. Recycle the power to put the new settings into effect.
RS-232 Parameters and Settings
The bracketed bold settings below represent the defaults as delivered from the factory:
•Modbus Address: [1]
-Each device is given a unique address. Up to 247 devices can be on the same data
link.
•Baud Rate: [9600]
-Must match the baud rate of your computer’s serial port and software.
•Parity: [None]
-Must match the parity of your computer’s serial port and software.
•Display Units: °F, °C [configured by TestEquity for °C]
•Modbus Word Order: [Low High], High Low
-Modbus allows a user to select the word order of two 16-bit words in floating point
values.
•Data Map: [1], 2, 3
-Data Map, the user can switch Modbus registers from the comprehensive listing of
F4T registers.
-Map 1 = F4T registers (default)
-Map 2 = Not applicable to controllers with Cascade Control (Part Temperature
Control)
-Map 3 = For controllers with Cascade Control. Limited set of F4 compatible registers
(for compatibility with software written for the F4).

Chapter 3 – Communications
TestEquity F4T Controller Page 15
Common Modbus Registers
F4T Mode
The following registers are applicable in the F4T Mode (Data Map 1). These are the most
common registers that would need to be used in an automation environment. Some of these
registers are different from F4T controllers that do not have Cascade Control.
Some F4T parameters are contained within 32 bits (IEEE Float). Notice that only one (low order)
of the two registers is listed. By default, the low order word contains the two low bytes of the 32-
bit parameter. As an example, in the table below see Actual Air Temperature. Note that it lists
register 4182. Because this parameter is a float, it is represented by registers 4182 (low order
bytes) and 4183 (high order bytes).
Parameter Name Register Data Type and Access (Read or Write)
Temperature Set Point 4042 IEEE Float RW
Closed Loop Set Point* 4190 IEEE Float R
Target Set Point** 16602 IEEE Float R
Actual Part Temperature (PV) 4180 IEEE Float R
Actual Air Temperature (PV) 4182 IEEE Float R
Simple Set Point 4200 16-bit RW Off = 62, On = 63
(Disables Cascade Control)
Event 1 16594 16-bit RW
Event 2 16596 16-bit RW
Event 3 16598 16-bit RW
Event 4 16600 16-bit RW
Event 5 16822 16-bit RW
Event 6 16824 16-bit RW
Event 7 16826 16-bit RW
Events 1-7 Off = 62, On = 63
* Instantaneous Set Point during a ramp or profile
** Set Point target during a ramp or profile
Manual Ramp Parameters (Ramp to Set Point without a profile)
The manual ramp parameters are all 16-bit RW.
Ramp Action 4054
Off = 62
Startup = 88
Set Point = 85
Both = 13
Ramp Scale 2956
°/Minutes = 57
°/Hours = 39
Ramp Rate 4058

Chapter 3 – Communications
Page 16 TestEquity F4T Controller
Profile Parameters - All 16-bit R or RW
Parameter Name Register Range
Start Profile 16558 (RW) 1 to 40
Start Step 16560 RW) 1 to max step # in profile
Profile Action Request 16562 (RW) None = 61
Start = 1782
Calendar Start = 1783
Profile Action Request 16564 (RW) None = 61
Resume = 147
Profile Action Request 16566 (RW) None = 61
Pause = 146
Terminate = 148
Profile State 16568 (R) Off = 62
Running = 149
Pause = 146
Not Started = 251
Completed Normal = 252
Terminated = 253
Calendar Start = 1783
Current Profile 16588 (R) 0 to 40
Current Step 16590 (R) 0 to 50
Step Type 16592 (R) Soak = 87
Wait For = 1542
Instant Change = 1927
Ramp Time = 1928
Ramp Rate = 81
End = 27

Chapter 3 – Communications
TestEquity F4T Controller Page 17
F4 Compatibility Mode (Data Map 3)
The following common registers are available in the F4 Compatibility Mode (Data Map 3). This
will allow you to use software that was written for the original F4 Controller. Only a limited set
of parameters are available in this compatibility mode, but it should be sufficient for most
applications. This register list is only valid for Firmware Revision 03:06:0011, released May 5,
2017 and higher. Older firmware revisions do not have an F4 Compatibility Mode for controllers
with Cascade Control.
Parameter Name Register Data Type and Access (Read or Write)
Temperature Set Point 300 16-bit Signed RW
Air Temperature 100 16-bit Signed R
Air Temp Input Precision 606 16-bit Signed RW 0 (0), 0.0 (1), 0.00 (2), 0.000 (3)
Part Temperature 108 16-bit Signed RW
Part Temp Input Precision 626 16-bit Signed RW 0 (0), 0.0 (1), 0.00 (2), 0.000 (3)
°C or °F 901 16-bit Signed RW °C (1), °F (0)
Air Temp Input Error 101 16-bit R No Error = 0, Error = 1
Part Temp Input Error 109 16-bit R No Error = 0, Error = 1
Event 1 2000 16-bit RW Off = 0, On = 1
Event 2 2010 16-bit RW Off = 0, On = 1
Event 3 2020 16-bit RW Off = 0, On = 1
Event 4 2030 16-bit RW Off = 0, On = 1
Event 5 2040 16-bit RW Off = 0, On = 1
Event 6 2050 16-bit RW Off = 0, On = 1
Event 7 2060 16-bit RW Off = 0, On = 1
Profile Action:
Resume Profile 1209 16-bit R
Hold Profile 1210 16-bit W
Terminate Profile 1217 16-bit W
Profile Start:
Profile Start File # 4000 16-bit W
Profile Start Step # 4001 16-bit W
Profile Action Start: 4002 16-bit W Create (1)
Insert Step (2)
Delete Current profile (3)
Delete Step (4)
Start Profile (5)
Delete all Profiles (256)

Chapter 3 – Communications
Page 18 TestEquity F4T Controller
SCPI Programming Mode
SCPI commands are ASCII text strings with a wide array of defined SCPI commands, all of
which are not included in this implementation. The SCPI protocol is only available over Ethernet
port 5025. The only available SCPI commands for the F4T are shown below. This complete list
is only valid for Firmware Revision 04:05:0007, released May 23, 2019 and higher. Older
firmware versions do not include all these commands. This list only applies to the native F4T
Ethernet interface, NOT the external Serial Modbus-to-Ethernet Converter.
Description
SCPI Command
SCPI Values
R/W
Comments
Commands for Process Units
Query Comm. Temperature units
:UNIT:TEMPERATURE?
C|F
R
Ethernet units
Set Comm. Temperature units to F
:UNIT:TEMPERATURE F
W
Ethernet units to Fahrenheit
Set Comm. Temperature units to C
:UNIT:TEMPERATURE C
W
Ethernet units to Celsius
Query Display Temperature units
:UNIT:TEMPERATURE:DISPLAY?
C|F
R
Front panel display units
Set Display Temperature units to F
:UNIT:TEMPERATURE:DISPLAY F
W
Front panel display units to Fahrenheit
Set Display Temperature units to C
:UNIT:TEMPERATURE:DISPLAY C
W
Front panel display units to Celsius
This list is ONLY for versions WITH Cascade Control (Part Temperature Control). NOT for standard Temperature or Temperature/Humidity chambers.
Read Set Point (Cascade)
:SOURce:CAScade1:SPOint?
<floating point value>
R
User set point
Write Set Point (Cascade)
:SOURce:CAScade1:SPOint <value>
W
User set point
Read Outer Loop PV (Cascade)
:SOURce:CAScade1:OUTer:PVALue?
<floating point value>
R
Source Value A
Query Outer Loop Input Error (Cascade)
:SOURce:CAScade1:OUTer:ERRor?
ERROR|NONE
R
Input error status
Read Inner Loop PV (Cascade)
:SOURce:CAScade1:INNer:PVALue?
<floating point value>
R
Source Value B
Query Outer Loop Input Error (Cascade)
:SOURce:CAScade1:INNer:ERRor?
ERROR|NONE
R
Input error status
Read Outer Loop Set Point (Cascade)
:SOURce:CAScade1:OUTer:SPOint?
<floating point value>
R
Read Inner Loop Set Point (Cascade)
:SOURce:CAScade1:INNer:SPOint?
<floating point value>
R
Query cascade loop function
:SOURce:CAScade1:FUNCtion?
R
Set cascade loop function to PROCESS
:SOURce:CAScade1:FUNCtion PROCESS
W
Not recommended, do not enter this
Set cascade loop function to DEVIATION
:SOURce:CAScade1:FUNCtion DEVIATION
W
Query cascade range low
:SOURce:CAScade1:RANGe:LOW?
<floating point value>
R
Set cascade range low
:SOURce:CAScade1:RANGe:LOW <value>
<floating point value>
W
Query cascade range high
:SOURce:CAScade1:RANGe:HIGH?
<floating point value>
R
Set cascade range high
:SOURce:CAScade1:RANGe:HIGH <value>
<floating point value>
W
Query cascade simple set point control
:SOURce:CAScade1#:SSPoint:CONTrol?
R
Set cascade simple set point control OFF
:SOURce:CAScade1:SSPoint:CONTrol OFF
W
Turns OFF Cascade Control mode
Set cascade simple set point control ON
:SOURce:CAScade1:SSPoint:CONTrol ON
W
Turns ON Cascade Control mode
Commands for Manual Ramp Parameters (ramping without running a profile)
Set ramping off
:SOURce:CLOop#:RACTion OFF
W
controls instantly to set point
Set ramping on startup
:SOURce:CLOop#:RACTion STArtup
W
ramps to set point on controller power
on
Set ramping on set point change
:SOURce:CLOop#:RACTion SETPoint
W
ramps to set point on change of set
point
Set ramping on both events
:SOURce:CLOop#:RACTion BOTH
W
ramps to set point on controller power
on OR change of set point
Write ramp scale to minutes
:SOURce:CLOop#:RSCAle MINutes
W
ramp rate is per minute
Write ramp scale to hours
:SOURce:CLOop#:RSCAle HOURS
W
ramp rate is per hour
Read ramp rate
:SOURce:CLOop#:RRATe?
<floating point value>
R
rate that controller ramps to set point
Read ramp time
:SOURce:CLOop#:RTIMe?
<floating point value>
R
time that controller ramps to set point
Write ramp rate
:SOURce:CLOop#:RRATe <value>
W
rate that controller ramps to set point
Read ramp time
:SOURce:CLOop#:RTIMe <value>
W
rate that controller ramps to set point
Commands for Event Outputs
Query output name
:OUTPut#:NAME?
# = outputs 1-7
Set event output ON
:OUTPut#:STATe ON
W
# = outputs 1-7
Set event output OFF
:OUTPUT#:STATE OFF
W
# = outputs 1-7
Query event output state
:OUTPut#:STATe?
OFF|ON
R
# = outputs 1-7
Continued on next page…

Chapter 3 – Communications
TestEquity F4T Controller Page 19
SCPI commands (continued)
Description
SCPI Command
SCPI Values
R/W
Comments
Commands to Support Profiles
Select a profile
:PROGram:SELected:NUMBer <value>
1-40
W
Set the current profile number
Query the current profile name
:PROGram:SELected:NAME?
<string value>
R
Set the current profile step
:PROGram:SELected:STEP <value>
1-50
W
Start the current profile
:PROGram:SELected:STATe STArt
W
Terminate the current profile
:PROGram:SELected:STATe STOP
W
Pause the current profile
:PROGram:SELected:STATe PAUSe
W
Resume the current profile
:PROGram:SELected:STATe RESume
W
Query active profile number
:PROGram[:SELected]:NUMBer?
R
Query profile state
:PROGram[:SELected]:STATe?
R
Query current profile set point
:PROGram[:SELected]:SPOint#?
R
# = 1 for Temp or 2 for Humidity
Query current profile step number
:PROGram[:SELected]:STEP?
R
Query current profile step type
:PROGram[:SELected]:STEP:TYPE?
R
Query current profile step time elapsed
:PROGram[:SELected]:STEP:TIME:ELApsed?
R
Query current profile step time remain
:PROGram[:SELected]:STEP:TIME:REMain?
R
Identification
*IDN?
"Watlow Electric",<string value>,<integer value>,<string value>
(manufacturer)
R
(model number)
(serial number)
(firmware level)

Chapter 3 – Communications
Page 20 TestEquity F4T Controller
GPIB and Ethernet Modbus Interface Converters (optional)
Serial Modbus-to-GPIB Converter (Options 1052 and 0003)
Your chamber may have been ordered with a GPIB Interface option. GPIB communications is
achieved through an ICS Electronics 4899A (external, TestEquity Option 1052) or 4809A
(internal, TestEquity Option 0003) GPIB-to-Modbus Interface Converter. The ICS 4899A
converts GPIB commands to serial Modbus commands that are transmitted over RS-232. The
GPIB Converter also takes care of calculating block checksums that are required for
communications to and from the F4T Controller. For more details, see the documentation that
came with the GPIB interface option.
NOTE: Composer software will only work with the native F4T Ethernet interface and
Data Map 1, not the Serial Modbus-to-GPIB Converter.
Serial Modbus-to-Ethernet Converter (Option 1056)
Your chamber may have been ordered with a Serial Modbus-to-Ethernet Interface option. GPIB
communications is achieved through an ICS Electronics 9099 (TestEquity Option 1056). The
programming syntax is the same as the GPIB Interface Converter mentioned above. For more
details, see the documentation that came with the Ethernet interface option.
Why use the Ethernet Converter when the F4T Controller has an Ethernet Interface?
The native F4T Ethernet Interface uses the Modbus TCP protocol. The 1056 Ethernet Interface
Converter converts the controller’s RS-232 Modbus interface to Ethernet. The converter takes
care of the Modbus packet formatting, so the command structure is simplified. The most
compelling reason why you would want to use 1056 Ethernet Interface Converter instead of the
F4T's native Ethernet interface is if you wanted to program using simple ASCII commands
instead of Modbus packets.
NOTES:
Composer software will only work with the native F4T Ethernet interface and Data Map 1,
not the TE-1056 Serial Modbus-to-Ethernet Converter.
The F4T’s native Ethernet Interface accepts both Modbus and SCPI commands. You do
not need the TE-1056 Serial Modbus-to-Ethernet Converter if you want to send SCPI
commands directly to the F4T’s native Ethernet Interface! F4T native SCPI commands will
not work with the TE-1056 Serial Modbus-to-Ethernet Converter.
Other manuals for F4T
1
Table of contents
Other TestEquity Controllers manuals
Popular Controllers manuals by other brands
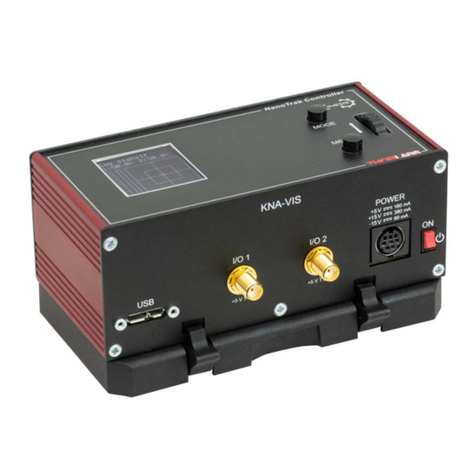
THORLABS
THORLABS NanoTrak KNA-IR APT User Guide

Wabtec
Wabtec Ricon 55914 installation instructions
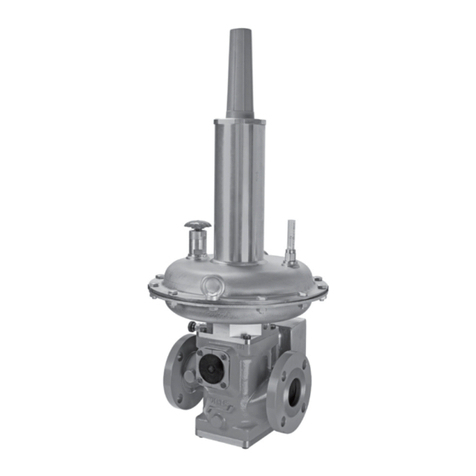
Emerson
Emerson Fisher LS200 Series instruction manual
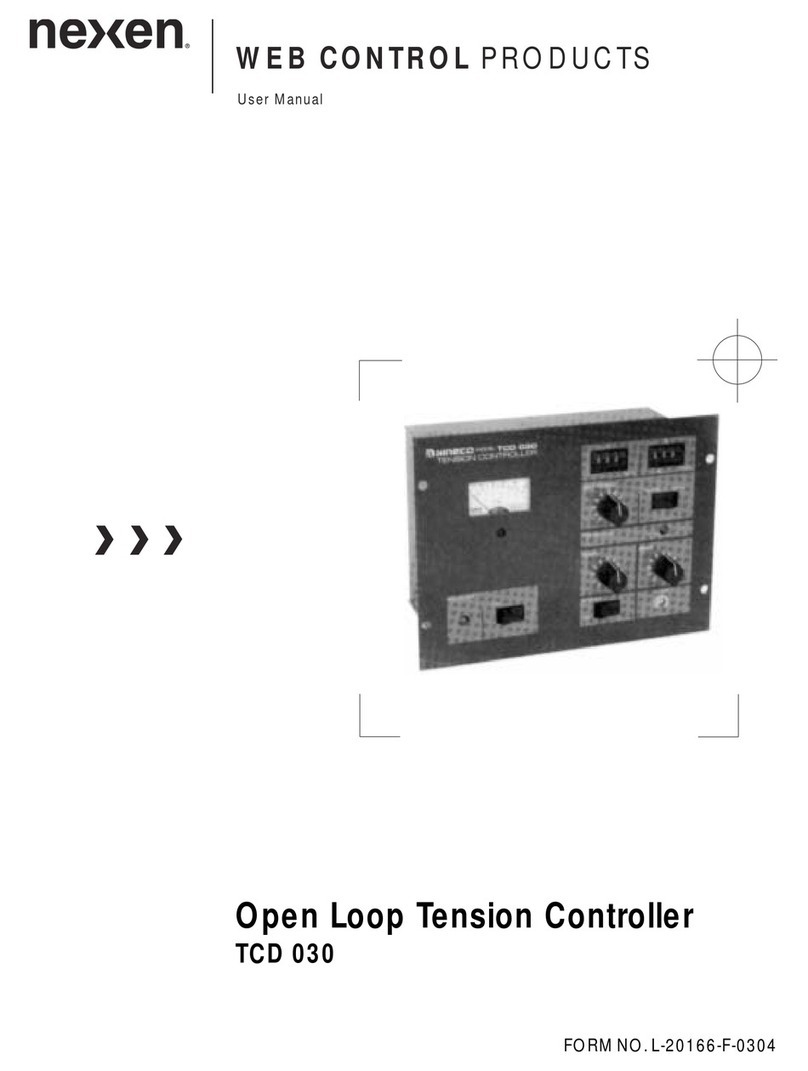
Nexen
Nexen WEB CONTROL TCD 030 user manual
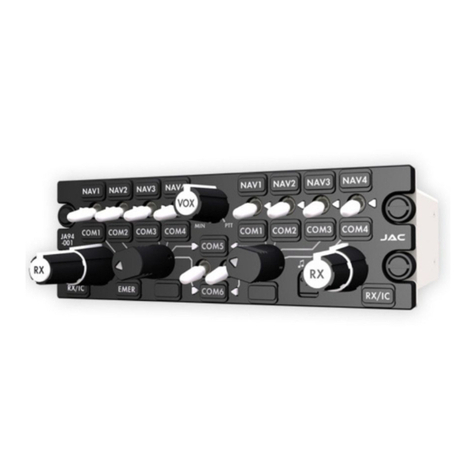
Jupiter Avionics
Jupiter Avionics JA94-001A Installation and operating manual
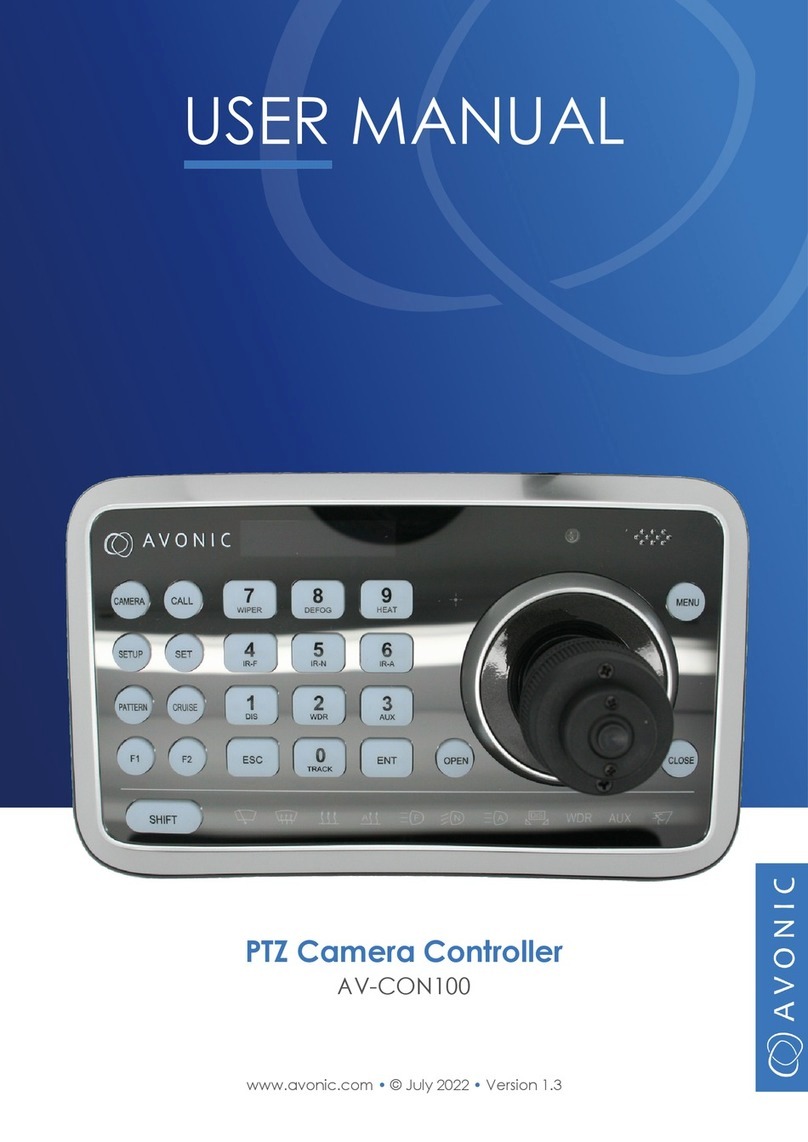
Avonic
Avonic AV-CON100 user manual