Thermo Electron NESLAB System III Service manual

Visit our Web site at:
http://www.thermo.com/tchttp://www.thermo.com/tc
http://www.thermo.com/tchttp://www.thermo.com/tc
http://www.thermo.com/tc
Product Service Information, Applications
Notes, MSDS Forms, e-mail.
Voice Info: (800) 258-0830
NESLABNESLAB
NESLABNESLAB
NESLAB
SS
SS
System IIIystem III
ystem IIIystem III
ystem III
Heat ExchangerHeat Exchanger
Heat ExchangerHeat Exchanger
Heat Exchanger
Thermo Manual P/N U00678 Rev. 08/19/05
Installation-Operation-Installation-Operation-
Installation-Operation-Installation-Operation-
Installation-Operation-
Basic ServiceBasic Service
Basic ServiceBasic Service
Basic Service

© 2005 Thermo Electron Corp. 623-2087
All rights reserved. This document is for informational purposes only and is
subject to change without notice.
Thermo Electron Corporation
Control Technologies
25 Nimble Hill Road
Newington, NH 03801
(800) 258-0830 or
(603) 436-9444
Fax : (603) 436-8411
Control Technologies
Main Service Center
The Main Service Center is open
8:00 am to 5:00 pm (Eastern
Time), Monday through Friday.
Thermo NESLAB
25 Nimble Hill Road
Newington, NH 03801
(800) 258-0830 or
(603) 436-9444
Fax : (603) 436-8411
West Coast
355 River Oaks Parkway, Door 10
San Jose, CA 95134
United States
Tel : (800) 423-7831 or
(408) 965-6050
Fax : (408) 965-6051
South
8711 Burnet Road
Suite F69
Austin, TX 78757-7065
(512) 459-2167
Fax : (512) 459-1731
Netherlands
Takkebijsters 1
Breda 4817 BL
Netherlands
Tel : +31 76 587 9888
Fax : +31 76 579 5610
Germany
Dieselstrasse 4
Karlsruhe 76227
Germany
Tel : +49 (0) 721 4094 0
Fax : +49 (0) 721 4094 300
France
16 Avenue du Québec - Silic 765
Courtaboeuf Cédex 91963
France
Tel : 33 (0) 1 60 92 48 00
Fax : 33 (0) 1 60 92 49 00
United Kingdom
Ion Path, Road Three
Winsford CW7 3GA
United Kingdom
Tel : +44 1606 548749
Fax : +44 1606 548712

- 1 -
System III Liquid to Liquid Heat Exchanger
Instruction and Operation Manual
Table of Contents
PREFACE Compliance ............................................................................................ 3
WEEECompliance................................................................................. 3
Unpacking .............................................................................................. 4
Warranty................................................................................................. 4
NES-care................................................................................................ 4
After-saleSupport ................................................................................... 4
Feedback ............................................................................................... 4
SECTION I
Safety Warnings ................................................................................................ 5
SECTION II
GeneralInformation Description ............................................................................................. 6
Specifications ......................................................................................... 6
SECTION III
Installation Site......................................................................................................... 8
FacilityWaterRequirements................................................................... 8
ElectricalRequirements.......................................................................... 9
VoltageSelection ................................................................................... 9
PlumbingRequirements.......................................................................... 9
Fluids ..................................................................................................... 10
FillingRequirements ............................................................................... 11
AutomaticRefillDevice(Optional) ........................................................... 11
FlowControl ........................................................................................... 11
AutoRestart ........................................................................................... 11
SECTION IV
Operation StartUp.................................................................................................. 12
TemperatureController............................................................................ 13
SetupLoop ............................................................................................. 14

- 2 -
SECTION V
Maintenance& Service ServiceContracts ................................................................................... 15
PumpStrainer ........................................................................................ 15
Facility Water Strainer ............................................................................ 15
Algae ...................................................................................................... 16
Configuration........................................................................................... 16
VoltageSelection ................................................................................... 16
PressureReliefValve .............................................................................. 16
FaultInterlockContact............................................................................ 17
Fuses ..................................................................................................... 17
PhaseRotation ....................................................................................... 17
PumpMotorOverloadProtector .............................................................. 17
DisplayingSoftwareVersion ................................................................... 18
SECTION VI
Troubleshooting ErrorCodes ............................................................................................ 19
PoorTemperatureStability ..................................................................... 20
ServiceAssistance ................................................................................. 20
Parts List................................................................................................ 20
SECTION VII
Diagrams TUPumpFlowDiagram .......................................................................... 21
FrontView .............................................................................................. 22
RearView ............................................................................................... 22
LargeVolumeUnits ................................................................................ 23
APPENDIX Water Quality and Standards
WARRANTY

- 3 -
Preface
Compliance Products tested and found to be in compliance with the requirements defined in the EMC
standardsdefined by89/336/EECas wellasLow VoltageDirective(LVD) 73/23/EECcan be
identified by the CE label on the rear of the unit. The testing has demonstrated compliance with
thefollowingdirectives:
LVD,73/23/EEC ComplieswithUL3101-1:93
EMC,89/336/EEC EN 55011, Class A Verification
EN50082-1:1992
IEC1000-4-2:1995
IEC1000-4-3:1994
IEC1000-4-4:1995
Forany additionalinformation referto theLetter ofCompliancethat shippedwith theunit
(DeclarationofConformity).
WEEE Compliance
This product is required to comply with the European Union’s Waste Electrical & Electronic
Equipment(WEEE) Directive2002/96/EC. It ismarked withthe followingsymbol:
ThermoElectron has contracted withone or morerecycling/disposal companies ineach EU
Member State, and this product should be disposed of or recycled through them. Further
informationon ThermoElectron’scompliance withthese Directives,the recyclersinyour
country, and information on Thermo Electron products which may assist the detection of
substancessubject totheRoHS Directiveare availableat:
www.thermo.com/WEEERoHS

- 4 -
After-saleSupport
ThermoElectronCorporationiscommitted tocustomerservice bothduringandafter thesale.If
youhave questionsconcerningthe operationofyour unit,contact ourSalesDepartment. Ifyour
unitfails to operateproperly, or ifyou have questionsconcerning spare parts,contact our
CustomerServiceDepartment.Beforecalling,pleaseobtainthefollowinginformation:
- BOM number
- Serial number
-Softwareversion
The BOM and serial number are on a label on the rear of the unit. To display the software
versionseepage17.
Unpacking Retain all cartons and packing material until the unit is operated and found to be in good
condition.If the unitshows externalor internal damagecontact thetransportation companyand
file a damage claim. Under ICC regulations, this is your responsibility.
Warranty Unitshaveawarrantyagainstdefectivepartsandworkmanshipforonefullyearfromdateof
shipment. See back page for more details.
NES-care Extended
Warranty Contract
•Extendpartsand laborcoverageforan additionalyear.
•Worry-freeoperation.
• Control service costs.
•Eliminate theneed togeneraterepair orders.
• No unexpected repair costs.
Othercontractoptionsareavailable.PleasecontactThermousformoreinformation.
Feedback We appreciate any feedback you can give us on this manual. Please e-mail us at
[email protected].Besuretoincludethemanualpartnumberandtherevisiondate
listedonthe frontcover.

- 5 -
Section I Safety
Warnings
Make sure you read and understand all instructions and safety precautions
listed in this manual before installing or operating your unit. If you have any
questions concerning the operation of your unit or the information in this
manual, contact our Sales epartment.
Performance of installation, operation, or maintenance procedures
other than those described in this manual may result in a hazardous
situation and may void the manufacturer s warranty.
Observe all warning labels.
Never remove warning labels.
Never operate damaged or leaking equipment.
Always turn off the unit and disconnect the line cord from the power
source before performing any service or maintenance procedures, or
before moving the unit.
Always empty the reservoir before moving the unit.
Never operate equipment with damaged line cords.
Never operate without fluid.
Refer service and repairs to a qualified technician.
In addition to the safety warnings listed above, warnings are posted throughout
the manual. These warnings are designated by an exclamation mark inside an
equilateral triangle with text highlighted in bold print. Read and follow these
important instructions. Failure to observe these instructions can result in
permanent damage to the unit, significant property damage, or personal injury
or death.

- 6 -
Section II General Information
Description
The NESLAB System III Liquid to Liquid Heat Exchanger is designed to
remove heat from water-cooled instruments. The unit consists of a heat
exchanger, recirculation pump, PVC reservoir, and a microprocessor controller.
Specifications
Temperature Range
Temperature Stability
Cooling Capacity1
Heat Removal (KW)
510152025
A= 6gpm pump flow
B= 10 gpm pump flow
C= 12gpm pump flow
AB
C
70
60
50
40
30
20
10
acility Water low GPM
1 2 2.4 3.5 5 6 8 10
Pressure Drop (PSI)
Reservoir Volume2
Gallons
Liters
Dimensions3
(H x W x D)
In hes
Centimeters
Shipping Weight4
Pounds
Kilograms
1.25
4.7
20¾ x 173/8 x 27
52.7 x 44.1 x 68.6
206
93.4
1. Cooling capacity is based in a 10°C difference between the temperature of the cooling
water supply and the cooling fluid flowing from the System III
to the instrument being cooled (see
Section III, acility Water Requirements). Pressure drop obtained with the System III modulating
valve fully open.
2. Larger volume reservoir units are available.
3. Units with CP-55 and TU-3 pumps. Other larger volume units measure 33¾ x 23 x 27¼
(85.7 x 58.4 x 69.2). or complete dimensions see pages 22-23.
4. Approximate. Larger volume units weigh approximately 355 pounds (161 kilograms).
+5°C to +40°C
±1.0°C

- 7 -
Pressure (psi)
low (gallons/minute)
70
60
50
40
30
20
10
5101520
A
D
C
B
A=TU-7, 60Hz
B=TU-7, 50Hz
C=TU-3, 60Hz
D=TU-3, 50Hz
E=CP-55, 60Hz
=CP-55, 50HZ
5.TU-7, TU-8, and TU-9 pumps require 3Ø power.
6.TU-5 pumps are rated 9 gpm @ 50 psi, TU-6 pumps are 12 gpm @ 50 psi, TU-8 pumps
are 20 gpm @ 50 psi, and TU-9 pumps 23 gpm @ 50 psi.
Pump Capacity5,6
E

- 8 -
Section III Installation
Site
The unit should be located in a laboratory or clean industrial environment with
easy access to a facility cooling water supply and a drain. Never place the unit
in a location where excessive heat, moisture, or corrosive materials are
present.
Refer to the pump label on the rear of the unit to identify the specific type of
pump in your unit. Units with a TU-7, TU-8 or TU-9 pump are equipped with a
pump motor fan. The fan is used to cool the pump motor and prevent the motor
from overheating. Air is drawn through the front of the unit and is discharged
through the rear of the unit. A minimum clearance of 6 inches (0.15 meters) at
the front and rear of the unit is necessary for ventilation.
Facility Water
Req irements
Limit the facility water inlet pressure to less than 150 psi (10,2 Bar) and
limit the facility water inlet pressure to outlet pressure differential
across the System III to less than 35 psid (2,4 Bar).
Refer to the Cooling Capacity chart in Section II, Specifications. The flow rate of
the cooling water supply must meet or exceed these requirements for the unit
to operate at its full rated capacity. If the cooling water does not meet these
standards, the cooling capacity will be derated. The chart is based on a
difference between the temperature of the cooling water supply (House Water)
and the cooling fluid flowing from the System III to the instrument being cooled.
As the heat load increases, the required flow rate of the cooling water supply
increases. For example, on a System III with a 6 gpm pump flow, if the heat
load is 12 kilowatts, approximately 3 gpm of cooling water flow is required to
remove the heat. However, if the heat load is increased to 36 kilowatts, about 8
gpm of cooling water flow is required.
The flow meter on the front of the unit does not measure the flow rate of the
cooling water supply. The flow meter measures the flow rate of the cooling
fluid returning to the instrument being cooled.

- 9 -
Electrical
Req irements
The unit construction provides protection against the risk of electric
shock by grounding appropriate metal parts. The protection may not
function unless the power cord is connected to a properly grounded
outlet. It is the user s responsibility to assure a proper ground connec-
tion is provided.
Refer to the serial number label on the rear of the unit for the specific
electrical requirements of your unit.
Ensure the voltage of the power source meets the specified voltage, ±10%.
Voltage Selection
If the unit is to be operated from a 220 to 240V source, a voltage range selector
switch inside the unit must be reset. See Maintenance and Service section for
instructions on changing the voltage selector.
Pl mbing
Req irements
Before installing the unit to an instrument that previously used tap water as a
cooling fluid, flush the instrument several times to remove any rust or scale
that has built up. The manufacturer of the instrument should be able to recom-
mend a cleaning fluid for their equipment.
The plumbing connections are located on the rear of the unit and are labelled
FACILITY WATER and RECIRCULATING CLEAN FLUI . The top fittings are
outlets and the bottom fittings are inlets.
These connections are 1 inch FPT.
A basket strainer is supplied with the unit to protect the heat exchanger from
becoming clogged by dirty cooling water. Install this strainer on the FACILITY
WATER inlet. A clogged strainer can adversely affect cooling capacity. See
Section V, Facility Water Strainer for cleaning instructions.
Connect the FACILITY WATER connections to the cooling water supply and
the drain.Connect the RECIRCULATING CLEAN FLUI connections to the
instrument being cooled.
Flexible tubing, if used, should be of heavy wall or reinforced construction.
All tubing should be rated to withstand 80 psi at +40°C. Make sure all tubing
connections are securely clamped. Avoid running tubing near radiators, hot
water pipes, etc. If substantial lengths of tubing are necessary, insulation
may be required to prevent the loss of cooling capacity.

- 10 -
Tubing and insulation are available from Thermo. Contact our Sales epartment
for more information (see Preface, After-sale Support).
It is important to keep the distance between the unit and the instrument being
cooled as short as possible, and to use the largest diameter tubing practical.
Tubing should be straight and without bends. If reductions must be made, they
should be made at the inlet and outlet of the instrument being cooled, not at
the unit.
If substantial lengths of cooling lines are required, they should be pre-filled
with cooling fluid before connecting them to the unit.
Fl ids
Never use flammable or corrosive fluids with this unit. Do not use
automotive anti-freeze. Commercial anti-freeze contains silicates that
can damage the pump seals. Use of automotive anti-freeze will void the
manufacturers warranty.
We recommend using distilled/deionized water with a 0.05 to 0.1 megohm-cm
reading.
Highly distilled/deionized water, above the 3 megohm-cm region, may
become aggressive and is not recommended for use with units with
wetted parts other than stainless steel. Distilled/deionized water in the
15 megohm-cm region is definitely aggressive and should not be used.
Units operating in these regions should be closely monitored. See
Water Quality Standards and Recommendations in the Appendix.
If you do not have access to distilled/deionized water we recommend using
filtered tap water. Thermo cannot recommend any custom fluids, these fluids
are too dependent on your particular application.
Below +8°C, a non-freezing solution is required. The selected cooling fluid
must have a viscosity of 50 centistokes or less. A 50/50 mixture, by volume, of
distilled/deionized water and laboratory grade ethylene glycol is suggested.

- 11 -
Filling
Req irements
Remove the reservoir cover. Fill the reservoir with clean cooling fluid to
within 1 inch of the top of the reservoir. Have extra cooling fluid on hand and
follow the steps described in Section IV, Start Up.
A tomatic Refill
Device (Optional)
The automatic refill device maintains the correct level of cooling fluid in the
reservoir. The device consists of a float switch in the reservoir and a solenoid
valve at the rear of the unit. If the cooling fluid level falls, the float switch will
drop, opening the solenoid valve and allowing make-up fluid to fill the reservoir.
Once the cooling fluid reaches the proper level, the float switch will rise and the
solenoid valve will close.
NOTE: For the solenoid valve to close properly, the minimum supply flow rate
should be 2.2 gallons per minute.
Connect the 3/8 inch O stainless steel barbed fitting on the solenoid valve
to the make-up fluid source using 5/16 or 3/8 inch I flexible tubing.
Tubing is available from Thermo. Contact our Sales epartment for more
information (see Preface, After-sale Support).
Flow Control
The RECIRCULATING FLOW CONTROL handle is connected to a three-way
valve that controls the flow of the cooling fluid to the instrument being cooled.
The handle is located on the front of the unit.
When the handle is in the + position, the valve is open and all available cool-
ing fluid is supplied to the instrument being cooled. When the handle is in the
0 position, the valve is closed and no cooling fluid is supplied to the instru-
ment being cooled. When the handle is between these two positions, the flow
rate of the cooling fluid is between full flow and no flow. Use the flow meter to
adjust the desired flow rate.
The gauge next to the flow control handle indicates the operating pressure.
A to Restart
Units are equipped with an auto restart feature. If power is lost, the unit will
automatically restart when power is restored. This feature is enabled/disabled
using the controller's Setup Loop, see page 14.

- 12 -
Section IV Operation
Start Up
Before starting the unit, double check all electrical and plumbing connections
and make sure the circulating system (the System III, your application, and the
tubing that connects them) has been properly filled with cooling fluid.
Turn the RECIRCULATING FLOW CONTROL to 0. Press START/STOP. The
pump starts and the controller displays the reservoir fluid temperature.
The low fluid level monitor in the reservoir prevents the unit from operating if the
fluid level in the reservoir is below the safe operating level. By slightly, and/or
intermittently opening the RECIRCULATING FLOW CONTROL (toward +) and
using extra cooling fluid to keep the reservoir topped off, the system can be
filled without repeated tripping of the low fluid level monitor.
If the unit shuts down, top off the reservoir and restart it. When the system is
full, the reservoir level will no longer drop when the RECIRCULATING FLOW
CONTROL valve is opened (toward +).
A control valve, located in the FACILITY WATER inlet line, regulates the flow
rate of the cooling water supply as it enters the unit. The valve regulates the
flow rate based on the heat load. Flow through the unit stops automatically
when the unit is shut off.
Temperature Controller
To turn the unit off, press START/STOP. The recirculation pump will stop.
The I LE and COOL lights indicate the control valves status. When the
temperature control valve is wide open (for maximum cooling), the COOL light
is on steady. When the control valve is closed, the I LE light is on. As the
control valve moves between these extremes, the two lights flash with varying
on-time to indicate the approximate position of the control valve.

- 13 -
Temperat re Controller
The microprocessor controller controls temperature using a PI (Proportional-
Integral- erivative) algorithm. It is designed with self-diagnostic features and
easy to use operator interface.
NEXT ENTER
Use this key to accept and save changes.
YES,
This key is used to increase numerical values.
NO,
This key is used to decrease numerical values.
When the controller is powered it displays the reservoir fluid temperature.
Press the NEXT ENTER key to view the setpoint. The display flashes between
SP and the actual setpoint number. If desired, use the YES and NO keys to
change the setpoint. The display flashes as soon as either key is depressed.
Once the desired setpoint is displayed, press NEXT ENTER.
When selecting an operating temperature, remember that the lowest achiev-
able temperature is a function of the available flow rate, the temperature of the
cooling water supply and the heat load.
The temperature control system actuates a control valve in the FACILITY
WATER line. The control valve adjusts the flow of the cooling water supply to
produce the desired operating temperature.
NOTE: The controller does not use the new value until the NEXT ENTER key is
depressed and the display stops flashing. The controller will not allow you to
enter a value above the maximum or below the minimum value, or any illegal
value. If you try to enter an illegal value the display will revert to its original
value when the last digit was entered.
If the NEXT ENTER key is not depressed within one minute, the controller will
time out and the new value will not be accepted. The controller will revert to the
previous value.
NOTE: Error codes are addressed in Section V, Maintenance and Service.

- 14 -
Set pLoop
The controller is used to tune the COOL PI values; configure the unit to
continue to run (Indc) or shut down (FLt) in the event of a fault; set the high
(Hit) and low (Lot) temperature limits; and enable/disable auto restart (Auto). If
a temperature limit is exceeded the controller will display an error code, see
Section VI.
NOTE: Serial Communication (SEr) is not operational. Ensure the display
indicates OFF.
Setup Loop
CooL is used to adjust the controller's PID values. However,
Thermo recommends only a qualified technician change the PID
values. Incorrect values will hamper unit performance. actory set
values are: P = 15; I = 0.3; D = 0.0.
With the controller displaying the fluid temperature, press and
hold the NO key and then press the NEXT ENTER key. The
controller will display tunE. Press YES to display CooL.
Press NEXT ENTER to display Stor, press YES
to accept all the changes, press NO to abort
all changes and restore all the previous
values. The controller will again display the
fluid temperature.
Press NEXT ENTER to display the
alarm (ALr) prompt. Press YES to
display Indc and have the unit
continue to run in the case of a fault.
Press NO to display FLt and have the
unit shut down in the case of a fault.
The factory preset is FLt.
Press NEXT ENTER to display the
high temp (Hit) alarm setting. If
desired, use the arrow keys to
change the value. The factory
preset value is 55°C.
Press NEXT ENTER to display the
low temp (Lot) alarm setting. If
desired, use the arrow keys to
change the value. The factory
preset value is -10°C.
Press NEXT ENTER to display
the auto restart (Auto) prompt.
Use the arrow keys enable/
disable this feature. The factory
preset is O .
Press NEXT ENTER to display the
serial comm (SEr) prompt. The
display should flash NO. If not,
use the arrow keys until NO is
displayed.

- 15 -
Section V Maintenance & Service
For personal safety and equipment reliability, the following procedure
should only be performed by a qualified technician. Contact our
Service Department for assistance (see Preface, After-sale Support).
Service Contracts
Thermo offers on-site Service Contracts that are designed to provide extended
life and minimal down-time for your unit. For more information, contact our
Service epartment (see Preface, After-sale Support).
P mp Strainer
Units with TU pumps have a wire mesh pump strainer is located at the bottom
of the reservoir. If debris is drawn into the reservoir, the strainer will prevent the
material from being sucked into the pump and damaging the pump vanes.
After initial installation, the strainer may become clogged with debris and
scale within the first week. Therefore, the strainer must be cleaned after the
first week of installation. After this first cleaning, the frequency of cleaning
depends on the purity of the cooling water. We recommend a visual inspection
of the reservoir be made monthly after the initial cleaning. After several months,
the frequency of cleaning will be established.
If the strainer is visibly clogged, cleaning is required.
isconnect the power cord from the power source and drain the reservoir before
cleaning the strainer.
Cover the strainer with a plastic bag to help trap any particles which may
become dislodged, and then remove the strainer by unscrewing it.
Clean the strainer by rinsing it with water.
Refer to Section III, Filling Requirements for instructions on replacing the cool-
ing fluid.
Facility Water
Strainer
The facility water strainer is the user-installed basket strainer on the
FACILITY WATER inlet. NOTE: The strainer is designed to be used only with
water. Clean the strainer when it becomes visibly clogged or dirty.
isconnect the power cord from the power source and turn off the facility
cooling water.

- 16 -
Place a container under the strainer to collect any water that spills out of the
basket when it is removed.
Unscrew the clear plastic basket. Remove the screen and rinse it with water.
Replace the screen and the basket.
Algae
To restrict the growth of algae in the reservoir, it is recommended that the res-
ervoir cover be kept in place and that all circulation lines be opaque. This will
eliminate the entrance of light which is required for the growth of most com-
mon algae.
We recommend the use of Chloramine-T, 1 gram per 3.7 liters.
Config ration
The unit top is secured to the cabinet by four ball stud retainers; one at each
corner. Remove cabinet top by prying upward gently (cover pops off) in
order to perform the following adjustments.
In some cases, the side access panels may need to be removed. The
access panels are secured using screws installed through the bottom of the
cabinet. NOTE: Some models have a one piece cover rather than separate top
and side panels. This type of cover is secured by five screws on each side of
the case.
Voltage Selection
Remove the top cover from the cabinet.
The VOLTAGE SELECT toggle switch is located on the right side of the
control box. Two ranges are available: 200-208V and 220-240V. Set the
switch for the appropriate range.
Replace the top cover.
Press re Relief
Valve
Units with TU pumps have a pressure relief valve is located on the pump
discharge line. The relief valve establishes the maximum operating pressure of
the unit. If the pressure of the fluid leaving the pump exceeds the valve setting,
the relief valve will bypass the fluid within the unit to relieve to the pressure. The
relief valve does not determine the actual operating pressure; the actual
operating pressure is determined by the flow control valve setting and pressure
drop through the instrument being cooled.
If adjustment is necessary, consult our Service epartment for assistance
(see Preface, After-sale Support).

- 17 -
Fa lt Interlock
Contact
A set of contacts is connected to a receptacle on the control panel. The con-
tacts are rated 10A/240V. This is not a power inlet or outlet. The receptacle is
isolated from the circuitry. Its ground pin is connected to the chassis. The
contacts are closed during normal operation and open when the unit is turned
off or when a fault is detected.
F ses
Three-phase units have fuses. Refer to the serial number label on the rear of
the unit for the specific electrical requirements of your unit.
Remove the top cover, the right access panel and the control box cover. The
fuses are located inside the control box.
Phase Rotation
Three phase units with three phase pump motors are equipped with a phase
rotation interlock. If the phasing is wrong, the controller will display PHEr and
the unit will not start.
Unplug the unit. Reverse any two power cord wires in the power cord plug.
Never remove the green ground wire.
Plug in the unit. The PHEr display should be off and the unit should start.
P mp Motor
Overload Protector
Three phase units with three phase pump motors have a pump motor
overload protector.
The overload protector prevents the pump motor from exposure to excessively
high current. If an overload fault occurs, due, for example, to a heavy work load,
the controller will display OL and the unit will shut down. The overload protector
will automatically reset after about two minutes. The unit must be manually
restarted.

- 18 -
Displaying Software
Version
This procedure will display the software version number on the units display. In
the event the unit is not operational, the software version (and the checksum)
can also be read from the label which is on the microprocessor chip itself.
The following chart uses an example of software version 000507.84A
begin at the reservoir temperature display 20.3°C
Press and hold NO for at least 10 seconds. 0507
displays software version digits to left of decimal. Note the two leading zeros
do not display.
Press NEXT 84
displays software version digits to right of decimal.
Press NEXT 1
displays software version revision letter (as its equivalent number - display
cannot show letters. A=1, B=2, etc.)
Press NEXT 0000
displays checksum - this can be disregarded
Press NEXT 20.3°C
returns to reservoir temperature display
Table of contents
Popular Heater manuals by other brands

Goldair
Goldair GFH225 operating instructions

Dimplex
Dimplex Studio G DXSTG25 Installation and operating instructions
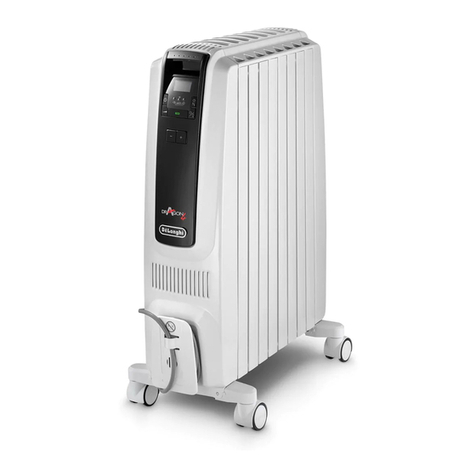
DeLonghi
DeLonghi DRAGON 4 TRDS4 0820E user guide

Rointe
Rointe Impero electric OVAL 500 instruction & installation guide
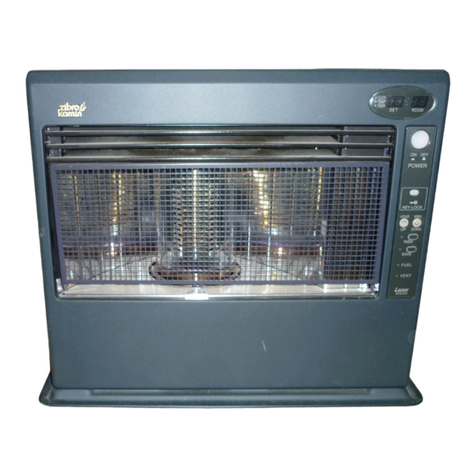
Zibro
Zibro SRE 250 operating manual
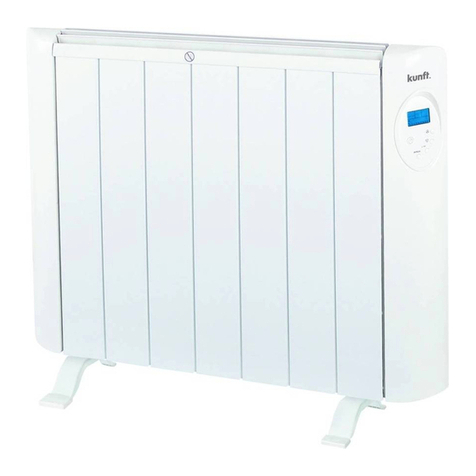
Kunft
Kunft KTE3781 instruction manual