THORLABS ELL15 User manual

ELL15 and ELL15K
SM1 Motorized Iris Kit
User Guide
Original Instructions

Table of Contents
Chapter 1 Safety Information .............................................................................................1
Chapter 2 Introduction ........................................................................................................3
Chapter 3 Overview .............................................................................................................4
Chapter 4 Operation ............................................................................................................7
4.1.1 Homing........................................................................................................................................................ 8
4.2.1 Hand-held Controller................................................................................................................................. 8
4.2.2 Software Control...................................................................................................................................... 10
4.2.3 Communications Protocol ...................................................................................................................... 11
4.2.4 Connecting Multiple Devices.................................................................................................................. 12
4.2.5 Controlling the Iris Without the Handset............................................................................................... 12
Chapter 5 Troubleshooting and FAQ ..............................................................................15
Chapter 6 Specifications...................................................................................................18
Chapter 7 Certifications and Compliance ......................................................................19
Chapter 8 Thorlabs Worldwide Contacts .......................................................................20

ELL15 and ELL15K SM1 Motorized Iris Chapter 1: Safety Information
Rev. A, August 31, 2023 Page 1
Chapter 1 Safety Information
For the continuing safety of the operators of this equipment, and the protection of the equipment itself, the
operator should take note of the Warnings, Cautions and Notes throughout this handbook and, where visible,
on the product itself.
Warning: Risk of Electrical Shock
Given when there is a risk of electrical shock.
Warning
The equipment is for indoor use only. The equipment is not designed for use in an explosive
atmosphere.
Warning
Given when there is a risk of injury to the user.
Caution
Given when there is a possibility of damage to the product.
Note
Clarification of an instruction or additional information.

ELL15 and ELL15K SM1 Motorized Iris Chapter 1: Safety Information
Page 2 DTN000949-D02
General Warning and Cautions
Warning: Risk of Electrical Shock
When connecting the iris to a PC, ensure that the PC is switched ON before connecting the
stage to the USB port. Failure to do this could damage the PC.
If this equipment is used in a manner not specified by the manufacturer, the protection
provided by the equipment may be impaired. Excessive moisture may impair operation.
The equipment is susceptible to damage from electrostatic discharge. When handling the
device, anti-static precautions must be taken, and suitable discharge appliances must be
worn.
Spillage of fluid, such as sample solutions, should be avoided. If spillage does occur, clean up
immediately using absorbent tissue. Do not allow spilled fluid to enter the internal
mechanism.
If the device is operated over a prolonged time, the motor housing may become hot. This
does not affect motor operation but may cause discomfort if contacted by exposed skin.
Do not bend the Printed Circuit Board (PCB). A bending load more than 500 g applied to the
board may cause the PCB to deform, which will degrade the performance of the controller.
Do not expose the stage to magnetic fields as this could affect the positioning and homing
sensor operation. An external magnetic field close to the sensor should be below +/- 5 mT.
Do not expose the stage to a strong infrared light (e.g., direct sunlight) as it could interfere
with the operation of the position sensor.
During use do not place the PCB directly onto electro-conductive material e.g., an optical
tabletop or breadboard.
Caution
The home sensor of the device relies on a 950 nm LED which can leak from the device. This
should be taken into consideration for environments that are especially sensitive to foreign
light sources.
During installation and transport, the iris should be set to the Home position to prevent
damage on the iris blades. Electrical shock or direct physical contact with the iris could
damage the blades and internal mechanism of the device.

ELL15 and ELL15K SM1 Motorized Iris Chapter 2: Introduction
Rev. A, August 31, 2023 Page 3
Chapter 2 Introduction
The ELL15 Motorized Iris is a part of the Thorlabs series of resonant piezo motor circuits and bare modules for
OEM applications. This motorized SM1 iris is post mountable with a CP33B bracket and compatible with SM1
threaded optics and tubes, 30 mm and 60 mm cage systems. Refer to Mounting for more details.
This motor’s resonant piezo design allows quick response times and precise positioning, making them
especially effective in scanning applications.
The high-speed digital signal processing (DSP) architecture supports a multi-drop serial communication
protocol, and a set of digital IO lines allows the user to manually control the movement and state by switching
the lines between high (5 V) or low (0 V) voltage.
The ELL15 has a central SM1-thread on both sides for mounting accessories like tubes or lenses. Ticks on the
inner ring of the device indicate an aperture position. The device is designed for applications requiring a 0.1
mm aperture resolution.
A reflecting optical sensor (IR) for coarse positioning and a magnetic sensor for fine positioning are used in
tandem to achieve homing. The Home Offset feature in the ELLO software allows the user to change the
homing position.
Note
The module must be powered via an external 5 V power supply unit (PSU). A suitable PSU
is supplied in the ELL15K iris kit or ELLC2 upgrade kit. The interface board has a DC Jack
connector with dimensions of 6.3 mm OD (GND), 2.1 mm ID (+5V) for users who want to
utilize a third-party PSU.
A hand-held controller is supplied with the ELL15K evaluation kit to allow homing and manual jogging,
positioning, and memorizing one custom position. The unit can also be driven remotely via PC-based software,
downloaded from www.thorlabs.com. A compatible USB driver and source code are included in the software
download package.

ELL15 and ELL15K SM1 Motorized Iris Chapter 3: Overview
Page 4 DTN000949-D02
Chapter 3 Overview
Environmental Conditions
Warning
Operation outside the following environmental limits may adversely affect operator safety.
The unit is designed for indoor use only.
To ensure reliable operation, the unit should not be exposed to corrosive agents or excessive moisture, heat
or dust.
Do not expose the stage to magnetic fields or strong infrared light (e.g., direct sunlight) as this could affect the
positioning and homing sensor operation.
The unit is not designed to be used in explosive environments.
If the unit has been stored at a low temperature or in an environment of high humidity, it must be allowed to
reach ambient conditions before being powered up.
Caution
If the unit is integrated inside an enclosure, it can become very hot under certain conditions.
Avoid placing the enclosure close to a heat source.
Mounting
Warning
The safety of any system incorporating this equipment is the responsibility of the person
performing the installation.
Caution
Although the module can tolerate up to 8 kV of air discharge, it must be treated as ESD
sensitive device. When handling the device, anti-static precautions must be taken and
suitable discharge appliances must be worn.
The ribbon cable connector is made of plastic and is not particularly robust. Do not use force
when making connections. Avoid plugging and unplugging repeatedly or unnecessarily to
prevent connector failure.
The following actions could damage the performance of the unit:
•Do not touch the motor track during installation and operation.
•Make sure to prevent the wires from contacting the motors, springs, or any other
moving components while handling the stage.

ELL15 and ELL15K SM1 Motorized Iris Chapter 3: Overview
Rev. A, August 31, 2023 Page 5
Figure 1 ELL15 Motorized Iris Showing its 3 Possible Mounting Hole Patterns
Figure 2 ELL15 Mounted in a 60 mm Cage System
The unit can be mounted directly into a 60 mm cage system using the Ø3.0 mm through holes in the PCB.
(Use 4-40 3/8” setscrew to mount the 60 mm cage rods).
When combined with four SR-series posts, the iris can be fitted to our ER-series cage rods within a 30 mm cage
system.

ELL15 and ELL15K SM1 Motorized Iris Chapter 3: Overview
Page 6 DTN000949-D02
Figure 3 ELL15 Mounted in a 30 mm Cage System
Figure 4 ELL15 Post-Mounted With CP33B Bracket

ELL15 and ELL15K SM1 Motorized Iris Chapter 4: Operation
Rev. A, August 31, 2023 Page 7
Chapter 4 Operation
Getting Started
Caution
Although the module can tolerate up to 8 kV of air discharge, it must be treated as an ESD
sensitive device. When handling the device, anti-static precautions must be taken, and
suitable anti-discharge appliances must be worn.
Do not expose the stage to magnetic fields as this could affect the positioning and homing
sensor operation.
When power is applied, do not connect or disconnect the ribbon cable connecting the
USB/PSU adapter to the iris PCB. Always remove power before making connections.
Warning
If the device is operated over a prolonged time, the motor housing may become hot. This
does not affect motor operation but may cause discomfort if contacted by exposed skin.
Caution
During normal operation each motor is protected with a time out of 3 seconds to avoid
overheating. The recommended duty cycle is 40%.
1. Perform the mechanical installation as detailed in Mounting.
2. Turn on and boot up the host PC.
3. Connect the handset to the stage if required.
Caution
The unit is easily damaged by connections with incorrect polarity. Pin 1 of the connector on
the PCB is marked with an arrow (refer to Figure 5 and Figure 8) which should be adjacent to
the red wire in the connecting cable.
4. Connect the stage to 5 V supply and switch ‘ON’. (A 5 V PSU is supplied with the ELL15K and ELLC2).
Caution
Boot up the PC before connecting the USB cable. Do not connect a powered ELL to a PC that is
not active.
5. Connect the handset to the PC with the supplied USB cable.
6. If required, wait for the drivers to be installed.

ELL15 and ELL15K SM1 Motorized Iris Chapter 4: Operation
Page 8 DTN000949-D02
4.1.1 Homing
Homing is achieved using a combination of a reflecting optical sensor (IR) for coarse positioning, then a
magnetic sensor for fine positioning (the magnetic sensor is also used for positioning during subsequent
moves). Using the ELLO software, the user can modify the homing position using the home offset.
Caution
The home sensor of the device relies on a 950 nm LED which can leak from the device. This
should be taken into consideration for environments that are especially sensitive to foreign
light sources.
At startup, the device's default setting is auto-homing. This function can be deactivated using
the command indicated in the Communications Protocol Manual.
Controlling the Iris
The iris can be controlled in the following ways:
•PC runs the Elliptec software with the handset.
•Develop a custom application using the messages stated in the communications protocol document.
•Apply voltages into Connector J1’s digital lines. Refer to Figure 8. It provides jogging and homing
functionality.
•Manually rotating the iris to reach a desired aperture.
To improve repeatability for a given position, absolute movements should be made from an aperture greater
than 1 mm to the target position.
Caution
In all modes, the iris aperture is requested and displayed from 1 to 11.5 mm. The aperture
cannot be driven past 11.5 mm or 1 mm. The iris is limited mechanically and by the encoder.
An error message appears if a request is outside the acceptable range.
The black motor track should be cleaned when turning the aperture manually, before
actuating the stage with motors again. Refer to Chapter 5.
4.2.1 Hand-held Controller
Caution
On power up the stage will move while the unit checks the sensors and then searches for
the home position.
At startup, the device's default setting is auto-homing. This function can be deactivated using
the command indicated in the Communication Protocol Manual.
The hand-held controller supplied with ELL15K Evaluation Kit and ELLC2 features three buttons (marked JOG,
FW and BW) that allow control of the iris aperture position. Button JOG (hold) + FW (open) can be used to
increase the aperture up to 11.5 mm and JOG (hold) + BW (close)to decrease the aperture down to 1 mm. The

ELL15 and ELL15K SM1 Motorized Iris Chapter 4: Operation
Rev. A, August 31, 2023 Page 9
handset also connects to the host PC and to the external 5 V power supply. The external PSU connector allows
the unit to be used in the absence of a PC, with control being provided via the handset buttons.
The PWR LED (LED1) is lit green when power is applied to the unit. The INM LED (LED2) is lit red when the
device being driven is in motion. A blinking INM LED (LED2) means that the memory function has been
activated.
Figure 5 Handset Details
Caution
By default, the device is set to auto-homing at start-up. This function can be deactivated using
the command indicated in the communication protocol manual. The stage must be homed
before performing any jog moves.
1. Home the stage by pressing the BW (backward) button.
2. To close the iris (jog backward) press and hold JOG and then press BW. The default jog step value is
0.5 mm aperture. The jog step size can be changed in the ELLO software, refer to the help file in the
installation folder for details.
3. To open the iris (jog forward) press and hold JOG and then press FW (forward).
4. One custom aperture setting can be saved using the handset.
5. Press and hold FW until the red LED on the interface blinks 3 times along with making 3 beeps.
6. The custom aperture can be recalled by pressing FW briefly. The red LED will blink once. (The custom
setting will only remain saved while the device is powered). If a custom position has not yet been
saved, pressing the FW on the handset will, by default, open the iris to 11.5 mm aperture.
7. The saved position can be overwritten by repeating step 5.

ELL15 and ELL15K SM1 Motorized Iris Chapter 4: Operation
Page 10 DTN000949-D02
4.2.2 Software Control
When connected to the host PC, the iris can be controlled remotely, via the Elliptec software.
1. Download the ELLO software from the downloads section at www.thorlabs.com . Double click the
saved .exe file and follow the on-screen instructions.
2. Connect the hand-held controller to the unit.
3. Connect the hand-held controller to the 5 V Power Supply and switch on.
4. Connect the hand-held controller to the PC USB port and wait for the drivers to be installed.
5. Run the ELLO software.
Figure 6 Software Control Main Window
6. In the top left of the GUI panel displayed, select the COM port to which the device is connected, and
click ‘Connect’. The software will search the comms bus and enumerate the device.
Note
To accelerate the search, the maximum search range can be limited from F to 0, depending
on the number of units connected.
7. By default, the unit is set to perform auto-homing. This function can be deactivated using the
command ‘ah’ indicated in the communication protocol manual. When auto-homing is deactivated,
the unit must be homed before using the ‘Home’ button.
8. The GUI and device are now ready for use. Refer the help file supplied with the software for more
information.

ELL15 and ELL15K SM1 Motorized Iris Chapter 4: Operation
Rev. A, August 31, 2023 Page 11
Figure 7 Output Window
F-Stop Function:
The iris can be set automatically to an F-Stop position using the F-Stop function in ELLO.
•Set the focal length of the optical system manually.
•Choose the F-stop using the drop-down menu (only feasible F-Stop values are shown).
(There is no automatic check in the sequencer. All F-Stops are shown).
•The unit will move to the desired position.
4.2.3 Communications Protocol
Custom move applications can be written in languages such as C# and C++.
The communication bus allows multi-drop communication with speeds at 9600 baud, 8-bit data length, 1 stop
bit, no parity.
Protocol data is sent in ASCII HEX format, while module addresses and commands are mnemonic character
(no package length is sent). Modules are addressable (default address is “0”) and addresses can be changed
and/or saved using a set of commands. Lower case commands are sent by the user while upper case
commands are replies by the module.
Please refer to the Communications Protocol manual for more details about commands and data packet
formats.

ELL15 and ELL15K SM1 Motorized Iris Chapter 4: Operation
Page 12 DTN000949-D02
4.2.4 Connecting Multiple Devices
When a device is first connected to the PC, it is assigned the default address '0'. The software can run multiple
devices; however, before more than one device can be recognized, each device must be assigned a unique
address. See below for a brief overview; detailed instructions are contained in the help file supplied with the
software.
1. Connect the first unit to the PC USB port, wait for the frequency search to finish, then run the ELLO
software and load the unit.
2. Change the address of the first device in the Address Manager (refer to Figure 7) and press “Set”.
3. Save the address of the unit (using save user, command “us”) or click “Save User Data” in the Settings
section.
4. Connect the next device to the ELLB Control Bus Distributor (refer user manual on www.thorlabs.com)
or to a daisy chain (refer to Figure 12).
5. Change the address of the second device and repeat the above steps for additional units.
6. Multiple devices can be controlled individually, either via the ELLO software or by a third-party
application written using the messages detailed in the protocol document. Control via the handset is
applied to all devices simultaneously. While using several units, sufficient power supplies must be used
with maximum 4.0 A.
Note
If the changes are not saved the unit will revert to the previous settings.
4.2.5 Controlling the Iris Without the Handset
In the absence of the handset, the iris is controlled via digital lines: Forward, Backward and Jog/Mode (J1 pins
7, 6 and 5) by shorting the corresponding line to ground (pin 1).
When the stage is moving, the open drain IN MOTION digital line (pin 4) is driven low (active low) to confirm
movement. The IN MOTION line goes high (inactive) when the move is completed or the maximum time-out
(3 seconds) is reached.
Warning
Do not exceed the voltage and current ratings stated in Figure 8.
Do not reverse polarity.

ELL15 and ELL15K SM1 Motorized Iris Chapter 4: Operation
Rev. A, August 31, 2023 Page 13
Figure 8 Connector J1 Pin Out Details
Pin
Type
Function
1
PWR
Ground
2
OUT
ODTX - open drain transmit 3.3 V TTL RS232
3
IN
RX receive - 3.3 V TTL RS232
4
OUT
In Motion, open drain active low max 5 mA
5
IN
JOG/Mode, active low max 5 V
6
IN
BW Backward, active low max 5 V
7
IN
FW Forward, active low max 5 V
8
PWR
VCC +5 V +/-10% 800 mA
Connector model number MOLEX 90814-0808 Farnell order code 1518211
Mating connector model number MOLEX 90327-0308 Farnell order code 673160
Frequency Search
Due to load, build tolerances and other mechanical variances, the default resonating frequency of a particular
motor may not be that which delivers best performance. A frequency search can be performed using the Main

ELL15 and ELL15K SM1 Motorized Iris Chapter 4: Operation
Page 14 DTN000949-D02
GUI Settings panel in the ELLO software, or by using the serial communication line (SEARCHFREQ_MOTORX
message), which offers a way to optimize the operating frequencies for backward and forward movement.
This search can also be performed manually by restoring the factory settings – refer to Restoring Factory
Settings below.
Periodic Cycling of Devices Over Full Range of Travel
Caution
Periodically, devices should be moved over the full range of travel, from one end to the other.
This will minimize the buildup of debris on the track and will prevent the motors digging a
groove over the most used area of contact. The Clean Mechanics function in the ELLO
software or ‘cm’ command can be used to perform this task. For continuous operation, it is
advised to execute Clean Mechanics weekly.
Restoring Factory Settings
Factory settings can be restored during the startup (calibration) test as follows:
1. Disconnect the USB cable and remove power from the unit.
2. Press and hold the BW button (do not release until step 5).
3. POWER UP with a 5 V power supply.
4. WAIT for red LED to switch on.
5. Release BW. The unit will reboot and load the default factory values.
Simultaneous Movement of Devices
If more than one device is connected to the comms bus, the movement of the devices can be synchronized.
This can be achieved either by using the handset, or by software. Refer the Communications Protocol manual
for details on how to use the ‘ga’ message to synchronize moves. If using the handset, synchronized movement
is hard wired, so pressing the JOG, FW or BW buttons will move all devices if multiple devices are connected.

ELL15 and ELL15K SM1 Motorized Iris Chapter 5: Troubleshooting and FAQ
Rev. A, August 31, 2023 Page 15
Chapter 5 Troubleshooting and FAQ
Frequently Asked Questions
Iris moving slowly or times out.
Check that the track is not contaminated. Do not touch the moving parts (motor, track and moving world) to
avoid grease contamination.
Check the powering order (refer to section 4.1) and ensure the recommended power supply is used as the
power supply is critical (refer to Chapter 1). Ensure that the power supply is plugged in before the USB cable.
Iris not moving.
Check power supply lines ratings (polarity, voltage drop or range, available current) or reduce cable length.
Check module is not in boot loader mode (power cycle the module to exit boot loader). Current consumption
must be higher than 36 mA at 5 V.
Make sure the device address is entered correctly if using ELLO or custom software.
Make sure that the unit is not mechanically blocked.
Iris does not complete homing commands.
Power cycle the unit.
Perform a frequency search on both motors.
Reset home offset to 0.
Iris switching time increased / max load decreased.
Check power supply voltage provided on J1 connector, increase voltage within specified limits if voltage drop
along cable goes below 5 V during system operation.
Clean the moving surfaces. Do not touch the moving parts (motor, track and moving world) to avoid grease
contamination.
Temperature change may affect the device performance. The software's frequency search function will make
necessary adjustments (required current could reach 1.2 A during frequency search, use an additional 5 V 2A
power supply and a USB connection).
Integrators should search for optimal frequency on every power up sequence (commands “s1”, “s2” refer to
the Communications Protocol Manual).
How do I restore the factory (default) settings?
Factory settings can be restored during initialization (refer to section 4.5).
The unit is not responding after powering up.
If the user holds down the JOG, BW and FW lines to ground and initiates the power sequence, the module will
enter into a boot loader (firmware update) mode.
Power cycle the unit again without pressing the 3 buttons at the same time to exit from the boot loader mode.
The device is not responding during cleaning.
This is normal.
The cleaning routines block a device and the associated communication bus for several minutes. When routine
is initiated, the bus is unavailable until the routine is completed, and the device replies busy ‘0GS09’ to all
commands except the stop command ‘0st’ (for a unit at address 0). The stop request can take up to 5 seconds
to abort the operation.
During this routine, the unit may increase in temperature by several degrees. Consecutive cleaning routines
should be avoided due to the inherent temperature increase.
After cleaning, allow a 20 min cool down period before use.

ELL15 and ELL15K SM1 Motorized Iris Chapter 5: Troubleshooting and FAQ
Page 16 DTN000949-D02
Is the device suitable for continuous operation?
Users should aim for a duty cycle of less or equal to 40% wherever possible, and never exceed a duty cycle of
60% for continuous high frequency operation.
What is the typical product lifetime?
ELL15 product lifetime is restricted by the wearing of moving surfaces and the motor contact as motion is
started (due to resonance build up) and performed (due to friction). Lifetime will depend on several factors
(e.g., high duty cycles, number of frequency searches, number of homing operations, load etc.) and users must
consider all these factors when considering lifetime. For example, homing often requires more travel than a
simple motion, and a frequency search may not generate any motion at all, but still energizes the motors fully.
A typical lifetime is 1 million iris movements.
Handling
Warning
The equipment is susceptible to damage from electrostatic discharge. When handling the
device, anti-static precautions must be taken, and suitable discharge appliances must be
worn.
The stage and interface board are robust to general handling. To ensure reliable operation, keep the surface
of the plastic track contacted by the motors free of oils, dirt, and dust. It is not necessary to wear gloves while
handling the unit, but avoid touching the track to keep it free of oils from fingerprints. If it is necessary to clean
the track, it may be wiped with isopropyl alcohol or mineral spirits (white spirit). Do not use acetone, as this
solvent will damage the plastic track.
Notes on Making a Picoflex Cable for Use when Daisy Chaining Devices
The multi-drop communications bus offers the option of connecting the stage to a hybrid network of up to 16
Elliptec resonant motor products and controlling the connected units with a device such as a microprocessor.
When multiple units are connected to the same interface board, all can be controlled simultaneously using
either the software or the buttons on the interface board.
When making a cable to operate multiple devices it is important to observe the correct pin orientation. The
following procedure offers guidance in making such a cable.
1. Gather the parts required.
a) Ribbon cable 3M 3365/08-100 (Farnell 2064465xxxxx).
b) Female crimped connectors as required – model number MOLEX 90327-0308 (Farnell order code
673160) (Qty 1 female connector above is shipped with each ELL15).
c) Suitable screwdriver and scissors or another cutting tool.
Figure 9 Suitable Tools

ELL15 and ELL15K SM1 Motorized Iris Chapter 5: Troubleshooting and FAQ
Rev. A, August 31, 2023 Page 17
2. Orientate the first connector to correctly mate with the connector on the stage, then arrange the
ribbon cable as shown with the red wire aligned with pin 1 (identified on the PCB by a small triangle
shown in the yellow circle in Figure 10). Slide the connector onto the ribbon cable as shown.
Figure 10 Slide the Connectors Onto the Ribbon Cable
3. Using a screwdriver or other suitable tool, push down the crimp of each pin to make connection with
the ribbon cable.
Figure 11 Push Down Crimp
4. If other connectors are required, they should be fitted at this point. Slide each connector onto the
cable, paying attention to the orientation as shown below, then crimp as detailed in step (3).
Figure 12 Slide Connector
5. Fit the terminating connector which will mate with the interface board, taking care to align the cable
red wire with pin 1 as detailed in step (2).

ELL15 and ELL15K SM1 Motorized Iris Chapter 6: Specifications
Page 18 DTN000949-D02
Chapter 6 Specifications
Item #
ELL15 and ELL15K
Iris Aperture Range
Ø1.0 - Ø11.5 mm
Minimum Lifetime
1 million Iris Movements
Recommended Duty Cyclea
40%
Maximum Closing Speedb
500 ms
Unidirectional Repeatability
± 0.10 mm
Homing Repeatability
± 0.10 mm
Backlash
0.20 mm
Encoder Resolution
1,000 counts/mm
Minimum Incremental Motion
0.01 mm
Minimum Motor Holding Torque
(Both Motors Engaged)
0.01 N•m
Limit Switches
Electronic and Mechanical
Mounting
30 mm Cage System: 4-40 Tapped Holes (4 Places)
60 mm Cage System: 3.0 mm Thru Holes (4 Places)
Fixed Internal SM1 Threads (2 Places)
Rated Voltage
4.5 to 5.5 V
Typical Current Consumption During Movement
800 mA
Standby Current
50 mA
Motor Type
Elliptec Resonant Piezo
8-Conductor Ribbon Cable Length (Supplied)
250 mm
8-Conductor Ribbon Cable Length (Maximum)
3 m
Operating Temperature Range
15 to 40 °C (59 to 104 °F)
Dimensions
66.0 mm x 82.5 mm x 19.1 mm
(2.60” x 3.25” x 0.75”)
Weight (ELL15 only)
0.1 kg
a. We recommend a duty cycle of 13 seconds running, followed by 20 seconds cooling down period. If running time is shorter,
then so is the required cool down time.
b. Some natural variability in the maximum speed may be experienced. Max speed will increase with usage.
This manual suits for next models
1
Table of contents
Popular Camera Lens manuals by other brands
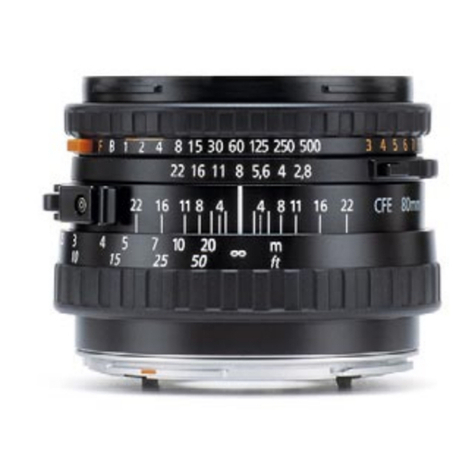
Hasselblad
Hasselblad Planar CFE 2.8/80 Specification sheet
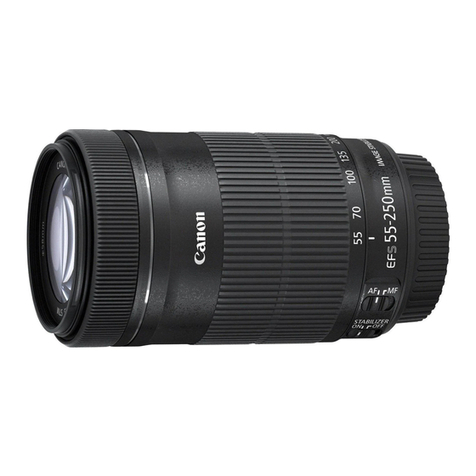
Canon
Canon EF-S 55-250mm f/4-5.6 IS Instruction
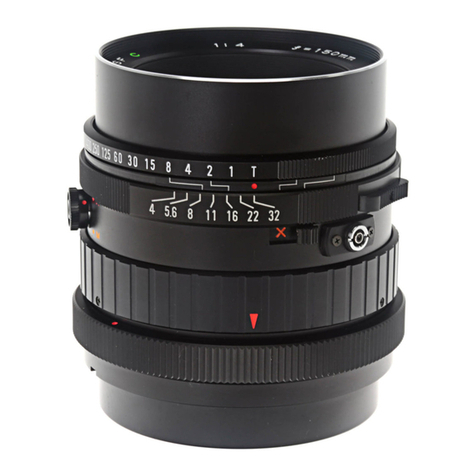
Mamiya
Mamiya Sekor SFC 150mm f/4 instructions
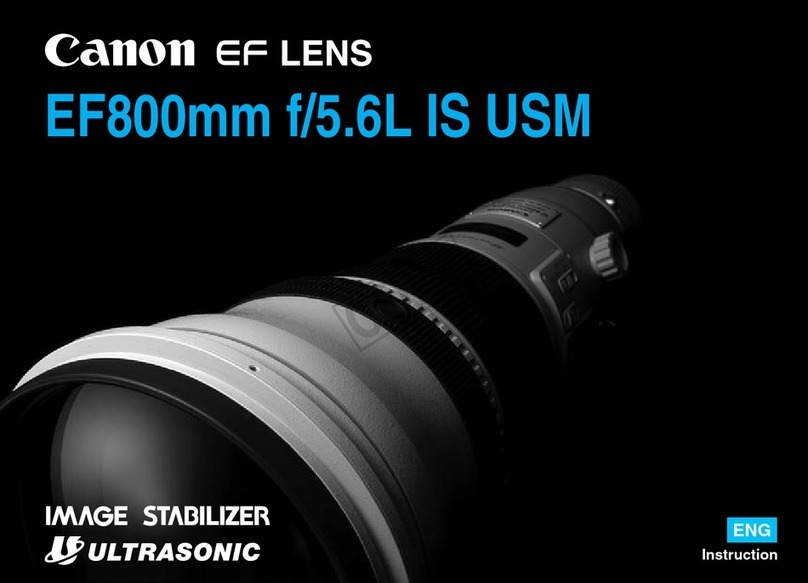
Canon
Canon EF 800mm f/5.6L IS USM Instruction

Olympus
Olympus Zuiko Digital ED 9-18mm f4.0-5.6 instructions
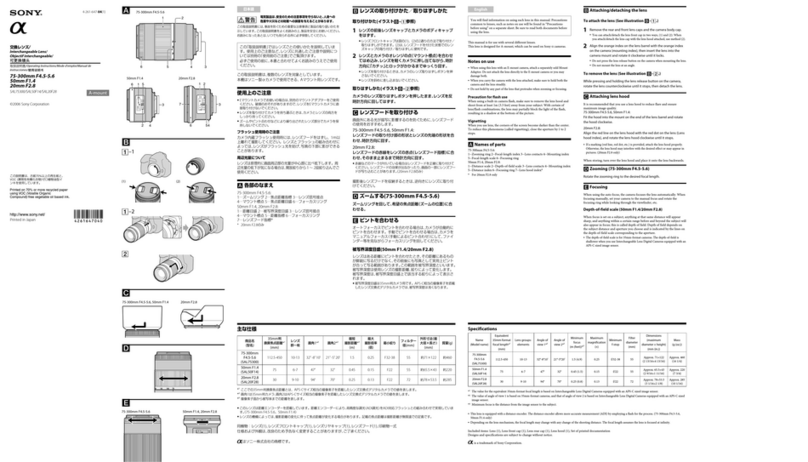
Sony
Sony SAL20F28 - Wide-angle Lens - 20 mm operating instructions
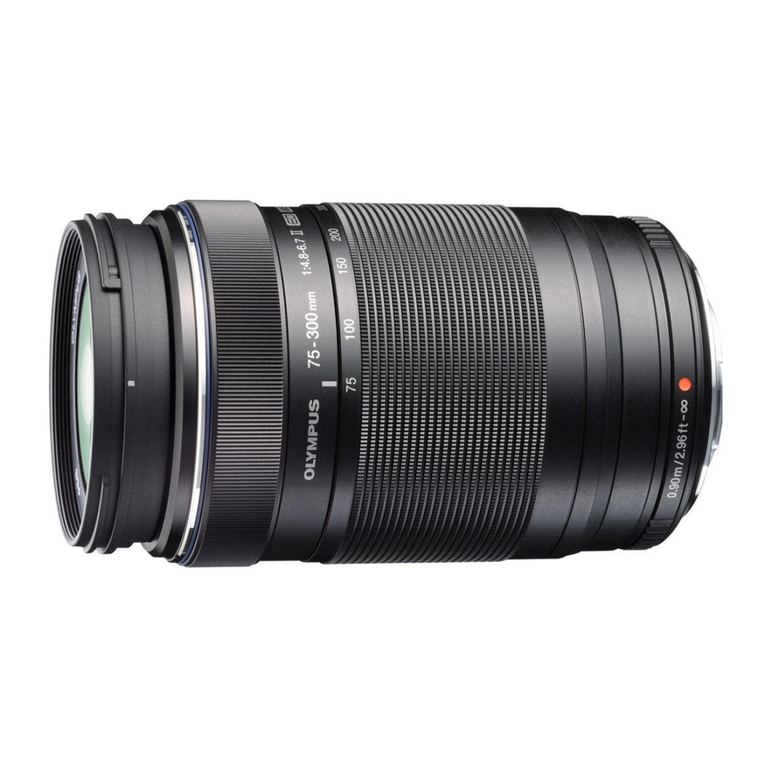
Olympus
Olympus ED75-300mm f4.8-6.7 ? instructions

Pentax
Pentax DA operating manual
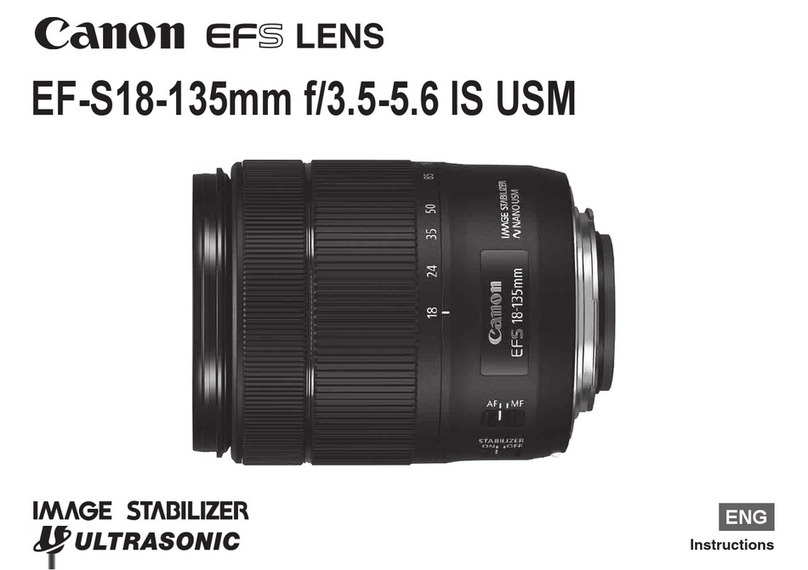
Canon
Canon EF-S18-135mm f/3.5-5.6 IS STM user manual

Sony
Sony SAL55200-2 Service manual
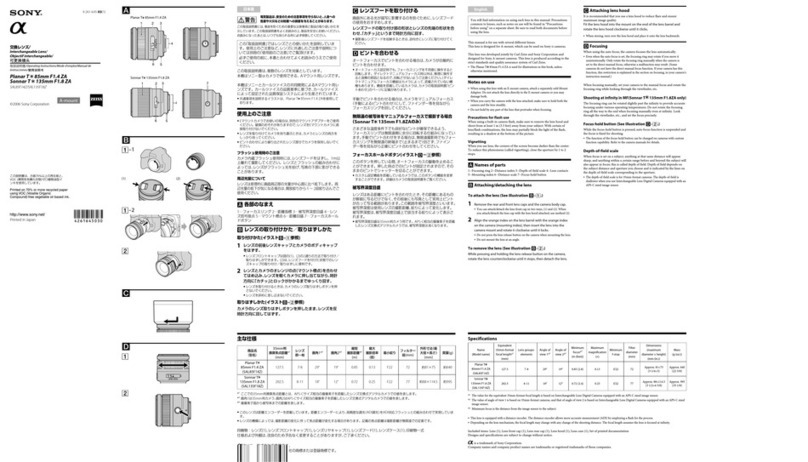
Sony
Sony SAL-135F18Z - 135mm f/1.8 Carl Zeiss Sonnar T Telephoto... instruction & operation manual
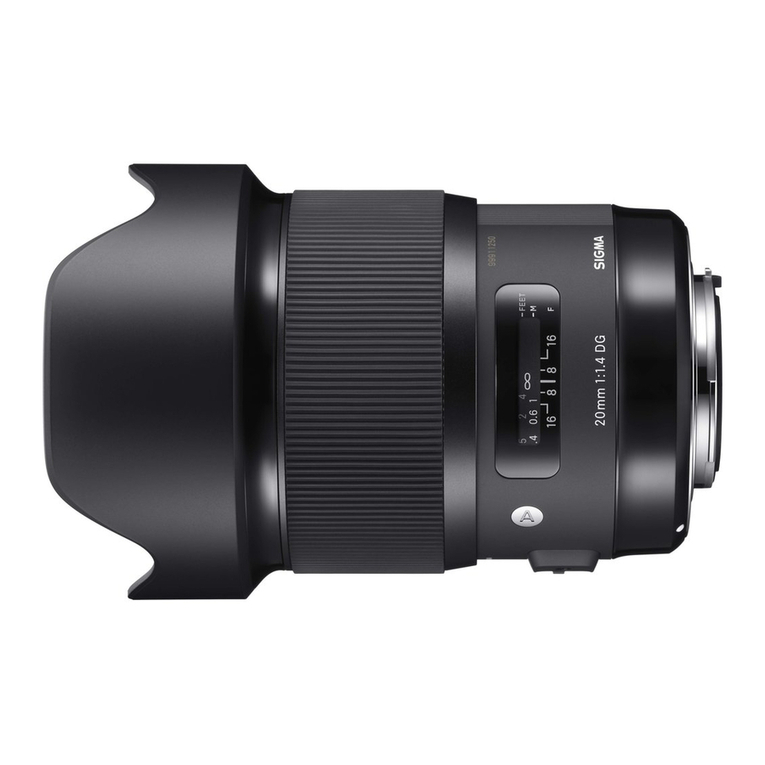
Sigma
Sigma 20mm F1.4 DG HSM user manual