Trident AirPrime Series Quick start guide

™
Air Operated Priming System
AirPrime™
Operation and Installation Guide
All AirPrime Models
Automatic
Controls
Manual
Controls
tLift Gauge Option
Standard Control q
Lift Gauge Option u
qStandard Control
AIRPOWER™
™™
SC
1901
Self Contained Priming System
™SC
1906
Self Contained Priming System
™
AirPrime Pressure Regulator
For use with high pressure SCBA cylinders

Trident Emergency Products, LLC
2940 Turnpike Drive | Suite #9 | Hatboro, PA 19040 USA
2
AirPrime™ Fire Pump Priming System
™
AirPrime™ Overview
Trident has several AirPrime models to meet your specic
operational requirements.
Base Models: All models available in 2 or 3 barrel design
(depending on your water pump capacity and chassis air
compressor size CFM).
Direct Mount: Models bolt directly to a Hale Q Model midship
pump’s priming port with two bolts. The Hale pump model name
must begin with a Q. e.g. Qmax.
Remote Mount: This type can be used with any pump, have a
3⁄4" female NPT connection and require a simple bracket to hold the
unit to the frame.
Multi-Location: Priming from multiple locations.
Variations and Options:
1. The AirPrime is available in either manual and automatic single
location models.
1. Multi-Location AirPrime is available in manual or automatic
models.
2. Automatic versions are available in 12 and 24 Volt models.
3. Lift Gauge which indicates how much vacuum (in feet-of-
water) the primer is creating to prime the pump.
4. Conversion Kits for Manual to Automatic and for adding more
locations are available. Refer to Page 16.
5. AirPrime is also available for small trucks without air brakes.
See Page 5 for additional information.
For more information on all available models please visit:
www.TridentDirect.com or www.TridentAutoAirPrime.com
Contents
Available Models ��������������������������������������������������������������������������������������������������������������������������������������������������������������������2
AirPrime™ Overview ��������������������������������������������������������������������������������������������������������������������������������������������������������������2
AirPrime™ - How Does It Work����������������������������������������������������������������������������������������������������������������������������������������������3
Installer Responsibilities���������������������������������������������������������������������������������������������������������������������������������������������������������4
Air Schematic, PPV, Air Hose and Connections���������������������������������������������������������������������������������������������������������������������5
Automatic Single Location AirPrime™ System ����������������������������������������������������������������������������������������������������������������������6
Automatic Single Location AirPrime™ System with Optional Vacuum Gauge ����������������������������������������������������������������������7
Manual Single Location AirPrime™ Systems�������������������������������������������������������������������������������������������������������������������������8
Multi Location Installation and Operating Instructions�����������������������������������������������������������������������������������������������������������9
Multi Location Automatic AirPrime™ System Diagram��������������������������������������������������������������������������������������������������������10
Multi Location Manual AirPrime™ System Diagram ������������������������������������������������������������������������������������������������������������11
Trouble Shooting Guide��������������������������������������������������������������������������������������������������������������������������������������������������������12
Trouble Shooting Guide (Continued) ������������������������������������������������������������������������������������������������������������������������������������13
AirPrime™ Industrial and SC Systems���������������������������������������������������������������������������������������������������������������������������������13
Annual Primer Testing�����������������������������������������������������������������������������������������������������������������������������������������������������������14
Warranty and Product Information ���������������������������������������������������������������������������������������������������������������������������������������15
Repair/Replacement Parts ���������������������������������������������������������������������������������������������������������������������������������������������������16
Available Models
Automatic Control
Automatic Base Model
Automatic Base Model with Lift Gauge
Automatic Multi Location
Automatic Multi Location with Lift Gauge
Manual Control
Manual Base Model
Manual Base Model with Lift Gauge
Manual Multi Location
Manual Multi Location with Lift Gauge

( 215-293-0700 7 215-293-0701
Installation and Operation Guide
AirPrime™- How Does It Work
NFPA #1901 and #1906 – Fully Compliant to Standards
Pump Panel Noise Level – Lowest dB in the Industry
Strainer Cleanout
Air In
From Chassis
Air Brake
System Used For Additional Priming
Points To Be Pre-Primed
Vacuum Inlet from
Priming Points
Discharged Air Out
Manifold
Control Solenoid
Piston Valve
Opens With
Air Pressure
Orange Arrows…
Air Flows Through
The Primer Body In 3
Stages for Maximum
Flow and Vacuum.
The Venturi Action
Creates the Vacuum
to Prime the Pump.
1
2
3
White Arrows
Indicate Debris
Into Strainer Area
How Does It Work?
AirPrime utilizes air supplied from the chassis air brake
compressor to operate the re pump primer� This is
proven to be far more efcient and reliable than electric
motor driven rotary vane primers�
AirPrime virtually eliminates the impact load on the
electrical system improving vehicle reliability�
AirPrime also improves performance in the elapsed time
for establishing water supply resulting in improved re
ground operations and safety�
Auto Prime Move Switch to the upper position� The
Green LED light will illuminate� The primer will activate
when the OK TO PUMP light is ON and the Pump
Pressure is below 20 PSIG�
The Auto Mode only operates when the re pump is
engaged�
AirPrime Primers can be used for both New and Retro-Fit installations. In Retro-Fit scenarios, AirPrime may be used to augment the
existing primer or as a complete replacement. Automatic AirPrime models provide instant re-priming of the pump when required.
An existing rotary vane primer can be upgraded to an Automatic Primer by adding a single location Auto AirPrime.
Auto Prime PositionOff Position
Primer switch shown
in OFF position. LED
indicator light is OFF.
Switch will illuminate
when in AUTO PRIME
position.
Primer switch shown in
AUTO PRIME position.
Green LED indicator light
is ON.
1. Press switch DOWN
and hold for Manual
Prime.
2. Press switch UP for
AUTO PRIME.
3. Center position is OFF.
1⁄4" NPT Air Supply Inlet 1⁄4" NPT Air Supply Inlet
To
Water Pump
Priming Point
Discharged Air
To
Water Pump
Priming Point
Air supply from chassis
brake system is OFF.
Incoming Air Flow OFF.
Air supply from chassis
brake system is ON.
Air enters and activates
primer.
Incoming Air Flow OPEN.
OK TO PUMP

Trident Emergency Products, LLC
2940 Turnpike Drive | Suite #9 | Hatboro, PA 19040 USA
4
AirPrime™ Fire Pump Priming System
™
Installer Responsibilities
Air Compressor Size
1. The 2-barrel AirPrime must be used only on re pumps rated 1000 GPM [3800LPM] and less. The chassis shall be equipped with a
minimum of 13.2 CFM [0.374 Cubic Meters per Minute] air compressor.
2. The 3-barrel AirPrime must be used only on re pumps rated 1250 GPM [4700LPM] and more. The chassis shall be equipped with a
minimum of 15.6 CFM [0.442 Cubic Meters per Minute] air compressor.
3. For Industrial Pumpers The Dual Unit requires an air compressor with greater than 20 CFM [6.09 Cubic Meters per Minute] capacity. The
Triple Unit requires an air compressor with greater than 30 CFM [9.14 Cubic Meters per Minute] capacity.
NOTE: For operations above 4000 feet [1219 meters] of elevation and lifts greater than 15 feet [4.5 meters], a minimum air compressor size
of 18 CFM [0.510 Cubic Meters per Minute] or larger is required.
Basic Materials Supplied by Installer
1. A 3/8"OD (.251 ID) air hose from the air tank (primary or auxiliary tank) with 1/4" NPT connections (length determined by installer).
2. Primer mounting bracket. (Only required for remote mount.) See Figure #2.
3. Non-collapsible 3/4" minimum inside diameter (ID) air hose from primer to re pump with 3/4" NPT connections.
4. A Pressure Protection Valve (PPV) (Optionally available from Trident, Part # 30.053.0).
5. A 1-1/4" [32 mm] inside diameter hose may be connected to the primer outlet using a hose clamp to secure it in place. NOTE: Loosely
tighten this hose clamp to avoid damage to the primer discharge ports. This hose can direct the water that is discharged from the
primer to any convenient location under the vehicle. Be sure this hose is properly secured, kept as short as possible, free of any kinks,
sharp bends and pitched to allow drainage.
6. Liquid thread sealant or Teon tape is required for all threaded pneumatic ttings.
NOTE: Use sparingly while applying sealant to avoid blockage of the internal mesh air lter. See Page 5, Figure #5.
Remote Primer Mounting
1. An installer supplied primer bracket shall be installed to secure the primer within the pump enclosure. The mounting height for all
priming components must be ABOVE the highest priming point on suction side of re pump (or above the highest remote priming valve
for multiple location systems) to permit air removal and allow for complete drainage. See Figure #2 for mounting bolt hole template.
NOTE: Primer MUST be mounted VERTICALLY with the Primer Outlet discharge (round) ports facing downward as shown in Figure #1.
2. Hose from the 3/4" NPT cleanable wye strainer on the primer inlet to the 3/4" NPT re pump priming port shall be non-collapsible 3/4"
minimum inside diameter.
3. The AirPrime and attached wye strainer shall be installed in an accessible location for serviceability per Figure #3 on Page 5. The
installer may choose from one of the options below as a method of draining the strainer:
a) Remove threaded plug on wye strainer for draining during annual pump service. Refer to Page 13 for Troubleshooting Guide.
b) For draining purposes, the strainer may be piped to the Master Drain of the re pump system by the installer, especially helpful in
climates with freezing conditions.
c) Alternatively a separate drain with valve and label may be piped to the bottom of the pump enclosure by the installer.
NOTE: If a front suction inlet is provided, a REMOTE PRIMER mounting is required. Refer to drawings of front suction plumbing on Pages 11
and 12.
1.563"
2.00"
2.00"
.625"
(4) Mounting Holes
1/4"-20TPI x 5/8" Deep
Primer
Outlet
Primer Body
Mounting Template
Pump
Body
O-Ring
Hale
Black
Plastic
Strainer
Primer
Outlet
Hale Direct Mounting
Figure 2Figure 1
Primer Mounting
Figure #1 illustrates the proper mounting
of the primer to a Hale Q Series cross-frame
midship re pump. Use the black plastic
strainer provided with the re pump from
Hale.
Figure #2 shows the dimensions for the
tapped holes in the primer body.

( 215-293-0700 7 215-293-0701
Installation and Operation Guide
Air Schematic, PPV, Air Hose and Connections
Air Supply Schematic
The AirPrime must be connected to the vehicle’s air brake system exactly as shown
in Figure 4 below. The schematic below is typical for most trucks built today.
1. Air compressor supply is shown as .
2. Supply reservoir (wet tank) is shown as .
3. Primary reservoir (typically for the rear brakes) is shown as .
4. Pressure Protection Valve (PPV) is shown as and in photo at right.
5. Figure ashows a customer supplied SCBA Cylinder used with the Trident
Pressure Regulator for use on trucks without airbrakes.
The regulator is available separately as Part #14.013.0.
Air Supply, Hose and Connections
The air source used to supply the AirPrime shall be from the primary air reservoir in Figure #4 or a secondary air reservoir (normally
used for air horns, air accessories or re pump shifting system).
The supply line from the Pressure Protection Valve (PPV) in Figure #4 to the primer control should be a minimum size of 3/8" OD air
brake tubing and connected at both ends with 1/4" NPT ttings (connections and tubing must be rated for air brake service). The tubing
should be kept as short as possible, secured at regular intervals, free of any kinks or bends and must not be run near exhaust pipes
(Stay 6" [150 mm] away from any exhaust or hot components), mufer, or rotating shafts. Use grommets to protect the tubing lines from
contacting sharp edges at hole locations.
When the length of tubing required exceeds 20 feet [6.1 m], a minimum size of 1/2” OD air brake tubing should be used.
Pressure Protection Valve (PPV)
The Pressure Protection Valve (4) is not supplied with the basic primer kit. A Trident PPV, Part #30.053.0
may be purchased separately, a Bendix PPV, Style PR-4, Part #288323 or its equivalent may be used.
The PPV valve must be installed per Figure #4 between the primary air supply reservoir and the
AirPrime primer air inlet. The valve protects the air brake system from any leaks that may occur in the
primer control or the line from the PPV to the primer control. The pressure setting for the PPV is 80 PSIG
maximum.
Air Filter Port
This cleanable porous lter is located inside the top of the primer body, below the threaded area on the
air supply connection or solenoid connection. See Figure #5.
A replacement lter is available as Part #21.002.0. When replacing, the domed side faces up.
Figure 4
3/4" NPT
Hose
Strainer
Inlet Strainer Mounting
™
Primer Outlet
Point
Straight
Down
Figure 3
Figure 5
Typical Chassis
Air Supply System
From Engine Air Compressor
Primary
Reservoir
PPV
Supply
Reservoir
Minimum 3/8" Air Brake Tubing
3
4
1 2
1
5
5
To AirPrime Primer Air Inlet
Figure 4a
PPV
#30.053.0
Sold Separately
Alternate Air Supply and Regulator

Trident Emergency Products, LLC
2940 Turnpike Drive | Suite #9 | Hatboro, PA 19040 USA
6
AirPrime™ Fire Pump Priming System
™
Automatic Single Location AirPrime™System
Installation
1. Install the AirPrime unit within pump enclosure. Unit must be VERTICALLY mounted ABOVE the highest priming point in suction piping.
2. Install 3/8" OD air hose piping from the Pressure Protected (PPV) air tank to the primer solenoid (See Figure #7).
3. Install the rocker switch electric primer control on pump panel (See Figure #8).
4. Install the pump pressure switch in a 1/4" NPT pressure opening on the top of the re pump.
Install switch in a vertical orientation and in a position that allows for proper drainage (See Figure #6).
5. Install the Automatic AirPrime wiring harness as follows: (See Page 7 and Figures 10, 11, 12)
Gray 5-prong plug to rocker switch control in pump panel bezel, and connect 6" pigtail to wiring harness
(gray plug).
White wire to the OK TO PUMP light circuit or to re pump shift control circuit (PTO or split shaft)
(1-1/2 feet long) [.5 m].
Red (+) and Black (-) wires to power supply (1 foot long) (Wiring and 1 amp fuse by installer).
Plug in to AirPrime solenoid connection (5 feet of cable) [1.8 m].
Plug in to re pump discharge pressure switch (5 feet of cable) [1.8 m] (See Figure #6).
Operation: Automatic Priming Control
AUTO PRIME Mode (Top Position)
1. Normally, leave the AirPrime rocker switch in AUTO PRIME mode.
2. If drafting, connect all suction hoses, strainer, and tighten accordingly. Utilize wheel chocks. In cab: Apply parking brake, Engage
pump per manufacturers recommendations (AirPrime will start priming automatically when the pump is engaged). NOTE: Never run a
re pump dry for more than 45 seconds.
3. Pump Panel: Verify that the green OK TO PUMP light is ON and then increase RPM. When the discharge pressure increases above 20
PSIG [1.4 Bar] the primer will disengage. When master gauge indicates greater than 20 PSIG [1.4 Bar] pressure, the discharges can be
opened and pumping operations established.
4. Automatic Operation: If the pump prime is lost, AirPrime will automatically start and re-prime the re pump. It will automatically turn
off when the pump pressure reaches 20 PSIG [1.4 Bar].
OFF Mode (Center Position)
1. Disengages the AirPrime pump primer at all times.
PRIME Mode (Lower Position)
1. Push and Hold the momentary switch for manual engagement of the primer at any time.
2. For Operation: Properly engage the re pump, verify that the green OK TO PUMP light is on, advance the throttle to 1000 RPM, push
and hold the AirPrime momentary switch until pump is primed, open discharges slowly. Rocker switch can be changed to AUTO mode
at any time.
3. The manual mode can be used without having the re pump engaged for vacuum testing or training on the primer system.
2.00"
Panel Cutout Dimensions
.281"Diameter
1.00"
1.00"
1.50"
3.22"
1.125"
3.22
Figure 7 Figure 8
Pressure
Protection
Valve
Air Supply
3/8" Air Hose
Solenoid
™
5a
5b
5c
5d
5e Figure 6

( 215-293-0700 7 215-293-0701
Installation and Operation Guide
5.22"
1.50"
2.00"
1.00"
2.50"
2.38"
1.125"
.281" Hole
Panel Cutout Dimensions
3.22"
1.00"
Automatic Single Location AirPrime™System with Optional Vacuum Gauge
Installation
1. Install AirPrime primer within pump enclosure. Unit must be VERTICALLY mounted ABOVE the highest priming point in suction piping.
2. Install 3/8" OD air hose piping from the PPV valve protected air tank to the primer.
3. Install the rocker switch electric primer control with lift gauge on the pump panel (See Figure #9).
4. Install the pump pressure switch in a 1/4" NPT pressure opening on the top of the re pump (See Figure #6 on Page 6).
5. Install the Automatic AirPrime wiring harness as follows (See Figures 10, 11, 12):
Gray 5-prong plug to rocker switch control in pump panel bezel, and connect 6" pigtail to wiring harness (gray plug).
White wire to Hot (+) Side of OK TO PUMP light circuit or to re pump shift control circuit (PTO or split shaft) (1.5 feet long) [.5 m].
Red (+) and Black (-) wires to power supply (1 foot long) (wiring and 1 amp fuse by installer).
Plug in to AirPrime solenoid connection, 5 feet of cable [1.8 m].
Plug in to re pump discharge pressure switch, 5 feet of cable [1.8 m] (See Figure #6 on Page 6).
6. Connect a 1/4" OD [6.35 mm] tubing line (Not supplied) from the push-to-connect tting supplied on the back of the panel lift gauge to
the 1/8" NPT connection on side of the primer body using the 1/8" male NPT x 1/4" push-to-connect swivel elbow provided with the
AirPrime unit. See photo below.
Figure 9
Figure 11
Figure 12
Wiring Harness
Part #41.001.2
Figure 10
5b 5c 5d 5e
5a
Part Numbers: #41.001.2 (12V)
#41.001.3 (24V)
The lift gauge provides the following features:
a) Indication of the vertical lift of water during priming operation.
b) Lift gauge will not be damaged by positive water pressure supply line.
c) Lift gauge can be used for positive periodic in-service ramp test without having the re pump engaged.
d) Operation is the same as Automatic AirPrime without a lift gauge.
Swivel Connection for
1/4" OD Lift Gauge Tubing
5a
5b
5c
5d
5e
6
™

Trident Emergency Products, LLC
2940 Turnpike Drive | Suite #9 | Hatboro, PA 19040 USA
8
AirPrime™ Fire Pump Priming System
™
5.22"
2.00"
1.00"
2.50"
2.38"
1.125"
.281" Hole
Panel Cutout
3.22"
.781"
Manual Single Location AirPrime™Systems
Installation
1. Install the AirPrime unit VERTICALLY within the pump enclosure. Unit must be mounted ABOVE the highest point in suction piping.
2. Install the manually operated primer push-to-operate air control on pump panel (see Figure #13).
3. Install 3/8" OD air hose piping with 1/4" NPT ttings from the PPV protected air tank to the primer manually operated push-to-operate
control and then to the primer unit. (See Figure #14).
4. If the AirPrime is equipped with an optional lift gauge, connect a 1/4" tubing line from the push-to-connect tting supplied on the back
of the panel lift gauge to the 1/8" NPT connection on side of the primer body using the 1/8" male NPT x 1/4" push-to-connect swivel
elbow provided with the AirPrime unit. (See photo bottom right for tubing connection location).
2.00"
Panel Cutout
.281" Diameter
.781"
1.00"
3.22"
3.22
1.125"
OPERATION: Manual Priming Control
The manual AirPrime pump primer is operated simply by increasing the engine speed to a maximum of 1000 RPM and depressing the push
button on the panel. Hold the button down until the discharge pressure gauge begins to rise. The primer will stop running when the push
button is released. The push button will operate the primer regardless of whether the re pump is engaged or not.
1. Depressing the Push-To-Prime button directs air to the primer inlet.
2. An internal valve to the water pump is opened with air pressure from chassis air system.
3. Vacuum for drafting is created by air-ow through multi-stage internal venturi nozzles.
4. The Panel Control Valve has no water, plumbing or electrical lines.
5. Never run a dry pump at engine speeds above 1200 RPM for more than 45 seconds in accordance with re pump manufacturer's
operating instructions.
Figure 13 Figure 14
Primary Air Supply
Panel
Push
Button
™
Pressure
Protection
Valve
Plugged
Opening Filter
Port
Figure 15
The lift gauge provides the following features:
a) Visual indication of the vertical lift of water during priming operation.
b) Lift gauge will not be damaged by positive water pressure supply line.
c) Lift gauge can be used for positive periodic in-service ramp test without
pump engagement.
d) Operation is the same as a manual
AirPrime without a lift gauge.
Swivel Connection for
1/4" OD Lift Gauge Tubing

( 215-293-0700 7 215-293-0701
Installation and Operation Guide
Multi Location Installation and Operating Instructions
Key Points for All Installations
1. The AirPrime unit MUST be VERTICALLY mounted ABOVE the highest point in suction piping.
2. Remote Priming Valves MUST be mounted ABOVE the highest priming point in the suction plumbing.
3. If the RPV priming valve is mounted below the AirPrime unit, add drain lines from all low points to a drain valve to prevent freezing.
4. It is common to have up to four (4) remote locations with the AirPrime Multi-Location priming system.
5. If front suction pre-priming is required, refer to drawings on the bottom Pages 11 and 12 for installation recommendations.
Installation Notes for Multi-Location Priming Systems
1. Automatic System: Follow the instructions on Page 6 and Page 7 with lift gauge for mounting the rst control on the pump panel.
2. Automatic System: Refer to schematics in Figure 17 on Page 11 for air lines, electric wiring and suction plumbing.
3. Automatic AirPrime Connections: See Figure 7 on Page 6 and information on Page 5.
4. Manual System: Follow the instructions on Page 8 for mounting the rst control on the pump panel.
5. Manual System: Refer to schematics in Figure 16 on Page 10 for air lines, electric wiring, and suction plumbing.
6. For additional priming locations mount a push-button control as shown in Photo 5.
7. Gold labels are provided for LEFT, RIGHT, FRONT and REAR remote priming locations as shown in Photo 6.
8. See Photos 3 and 4 to note that the cast in arrows on the RPVs and Check Valves are in the proper direction of ow.
Operating Instructions for Multi-Location Automatic Priming System
1. See operating instructions for automatic priming system on Page 6 for the initial re pump priming procedures.
2. Be sure the AirPrime switch is in the AUTOMATIC position when opening the remote location valve control.
3. To pre-prime a remote location, push the PRIME button of that location for 45 seconds or until water appears at top of hose.
Operating Instructions for Multi-Location Manual Priming System
1. See operating instructions for manual priming system on Page 8 for the initial re pump priming procedures.
2. To pre-prime a remote location, push the manual button for that location for 45 seconds or until water appears at top of hose.
3. Be prepared to push the Fire Pump manual AirPrime Push-To-Prime button when remote location valve control is opened to remove
any trapped air.
Multi-Location Components
1. Primer solenoid and Multi Location air inlets are shown below in Photos 1 and 2.
2. RPV Valve and Air Check Valve noted with directional arrows as shown below in Photos 3 and 4.
3. Additional pre-priming panel control and choice of appropriate labels shown in Photo 5 and 6.
Front View of
AirPrime Pump
Solenoid
Air Supply
Connection Additional
Air Inlets
Plug the
Unused Ports
123
456
Flow
Direction
Air Flow

Trident Emergency Products, LLC
2940 Turnpike Drive | Suite #9 | Hatboro, PA 19040 USA
10
AirPrime™ Fire Pump Priming System
™
Multi Location Automatic AirPrime™System Diagram
Compressed
Air In
Automatic
AirPrime
Pressure Switch, Pump Discharge
41.003.0 Jumper Wire Harness
41.001.0 Wire Harness
Connect to
"Pump Engaged"
Light Circuit
Top View of AirPrime Pump
Shown for Electrical Wiring
Strainer
Open
Plumb to Drain Valve
Closed
Connect to
Center Port
of Solenoid Valve
RPV
Intake 3
3/4" Tubing (Minimum)
From
Intake #2
Priming Tap
From
Intake #3
Priming Tap
Intake #3
In
Up to 4 Ports
are Available
for Air Inlets
Intake #2
From
Main Pump
Priming Tap
Mufers
Panel
Valve
Closed Position
Open
Panel
Valve
RPV 2
RPV 1 (Remote Priming Valve)
Main Fire Pump
Closed
Check
Valve
3/4" Tubing (Minimum)
1/4" Tubing (Minimum)
3/8" Tubing (Minimum)
3/8" Tubing (Minimum)
3/8" Tubing (Min)
3/4" Tubing (Minimum)
3/8" Tubing (Min)
Drawing Denotes Two (2) Additional
Multi-location Priming Points.
Check
Valve
Panel Switch
Color Key
Electric Lines
Air Supply Lines
Vacuum Priming Lines
Multi Location Wiring Harness
3/4" Tubing (Minimum)
(See photo inset, lower left corner)
™
Out
Figure 16
™
Color Key
3/4" ID External Flex Line
3/4" ID External Flex Line
3/4" ID External
Flex Tubing
Merge All "High Point" Pick-ups
At The Valve Location
(Higher Than The "High Points")
Priming
Valve
Closed
5" or 6"
Buttery Valve
By OEM
Front Axle Area
3/4" ID External
Flex Tubing
Through Bumper Installation
NOTES:
1. More than two valve sets may be ganged in a
similar manner with kit 27.005.1 for each.
2. If priming valve is mounted below AirPrime, add
line(s) from low point(s) to drain valve(s).
Front Suction Plumbing
Highest Point Above Front Axle
Jumper
Wiring
Harness
Part #
41.003.0
Use one of these ports
for Green Air Supply line.
Plug the unused 1/8" NPT Port.
Leave Open
for vent.

( 215-293-0700 7 215-293-0701
Installation and Operation Guide
Multi Location Manual AirPrime™System Diagram
Figure 17
™
3/4" Tubing (Minimum)
Plumb To
Drain Valve
Strainer
3/8" Tubing (Minimum)
3/8" Tubing
(Minimum)
1/4" Tubing (Minimum)
3/8" Tubing (Minimum)
Check Valve
From
Fire Pump
RPV
Fire Pump
Open
3/4" Tubing (Min)
Closed
Compressed
Air In
From
Remote Location
Panel Valve
Fire Pump
RPV
Remote Location
Open
Closed
1/4" Tubing (Minimum)
3/8" Tubing (Minimum)
3/4" Tubing (Minimum)
3/4" Tubing (Min)
Check Valve
Color Key
Air Supply Lines
Vacuum Priming Lines
Panel Valve
Remote
Drawing Denotes One (1)
Additional Priming Location
™
Color Key
3/4" ID External Flex Line to Low Point Drain
1/2" ID Internal Flex Line
3/4" ID External Flex Lines
1/2" or 5/8" ID External Flex Line
1/2" ID Internal
Flexible Tubing
**
Priming Line
Drain Valve
**
1/2" or 5/8" ID
External Flexible Tubing
**
3/4" Weld Coupling
**
3/4" ID External Flex Tubing**
Merge All "High Point" Pickups
At The Valve Location (Higher Than The "High Points")
Fittings In Kit From
Outside Of Pipe
To Inside
*
Priming
Valve
Closed
5" or 6"
Buttery Valve
By OEM
** Front Axle Area
3/4" ID External Flex Tubing**
Special Strainer
*
*Trident Kit Supplied Items
** Installer Supplied Items
Kit Part Numbers
5" NH Kit: #27.011.1
6" NH Kit: #27.011.0
Contact Trident for Front Suction Kits.
Front Suction Plumbing
Highest Point at Front Inlet
Use one of these ports
for Green Air Supply line.
Plug the unused 1/8" NPT Port.
Leave Open
for vent.

Trident Emergency Products, LLC
2940 Turnpike Drive | Suite #9 | Hatboro, PA 19040 USA
12
AirPrime™ Fire Pump Priming System
™
Trouble Shooting Guide
Problem Likely Cause Corrective Action
System Does Not
Hold Vacuum.
• Master Drain Valve Open.
• Discharge or Intake Valves Open.
• Bleeder or Drain Valves Open.
• Relief Valve Drain Open.
Double check all drains, discharge and intake valves to make sure all are
closed.
Intake Relief Valve Allowing Air Into
Pump System.
a) Adjust intake valve to closed position (be careful to count the number of
turns to close and re-open the same number of turns).
b) Cap the discharge side of the intake relief valve (NPT or NH).
Be sure to remove cap after testing.
AirPrime Exhaust Outlets Drawing
Back Vacuum.
The integral priming valve is not closing all the way, air is moving upward into
the barrels, into the pump, as the water falls back into the hard suction hose to
the water level or as vacuum is lost through the re pump system.
System Will Not
Reach 22" Hg.
Inadequate air supply.
a) Check the CFM rating of the engine air compressor. See Page 4.
b) Check air pressure at “supply” side of AirPrime (should be over 70-PSIG/
[3.8 Bar]). Install a tee and air gauge in input for test purposes. If the air
pressure is not the same as the cab dash air pressure gauge, check for
under sized airline, kinks or obstructions in air line, or air line is too long
(under 20 ft [6 m] from primary tank.
Pressure Protection Valve.
Check Pressure Protection Valve air on/off settings (should shut-off in the 60
to 80-PSIG / [4.2 to 5.5 Bar] range) and OPEN no higher than 80-PSIG / [5.5 Bar]
to AirPrime.
Air lter on intake side of air supply
connection to AirPrime body.
For details on lter inspection/
replacement visit/click QR codes at right.
a) Manual AirPrime: Remove air supply piping, remove ne mesh lter, clean
or replace. Part#: 21.002.0
b) Automatic AirPrime: Remove air supply piping, remove air solenoid
assembly, remove ne mesh lter, clean or replace. Part #: 21.002.0
Slight air leak in discharge or intake
valves in re pump plumbing.
Hydrostatic test the plumbing system to NFPA #1901 standard with wet re
pump and closed valves: 250-PSIG [17.2 Bar] for 10 minutes w/ pressure loss.
Check the interior check valves
inside the primer.
Remove and disassemble primer to inspect the (3) small rubber check valves
to venturi orices.
Check the interior primer body
venturi nozzles for foreign material
or blockage.
Remove and disassemble primer to inspect venturi nozzle openings or clean
with small wire to assure open orices.
Defective Primer. Replace or rebuild primer with Kit #27.003.3. See Instructions Here
AirPrime Leaks
Water.
Check the AirPrime integral priming
valve.
a) The priming valve is not seating in the shut-off position: Remove primer,
disassemble, and check the priming valve spring, seat and operation.
b) The priming valve is “stuck”, check for damaged O-Ring or check to see if
piston is fully threaded on the valve stem.
Manual System:
Air continues to
ow when button
is released.
Bad push button manual valve.
Push button air plumbing installed
incorrectly.
Replace the Push Button with a new valve, Part #27.003.1.
Refer to air schematic drawing, Figure 14 on Page #8 of this manual.
Automatic
System: Air
continues to ow
when button is
released.
Panel switch inoperable.
Air solenoid on top of primer is
defective.
Solenoid is on backwards.
Refer to parts list on Page 16, order replacement switch, Part #27.003.2.
Refer to parts list, order replacement solenoid, Part #30.003.0 (12 Volt) or
#30.003.1 (24 Volt).
Reverse orientation of solenoid on top of manifold. Ports on solenoid and
manifold should be on the same side.
Visit www.TridentAutoAirPrime.com for additional AirPrime information.

( 215-293-0700 7 215-293-0701
Installation and Operation Guide
Trouble Shooting Guide (Continued)
Problem Likely Cause Corrective Action
Slow Prime Time.
Leaking air into the
plumbing system.
Double check all drains, discharge, and intake valves to make sure all are
closed.
Low air pressure.
Check air pressure at supply side of AirPrime (Should be over 70-PSIG/[3.8
Bar]). Install a tee and air gauge in input for test purposes. If the air pressure
is not the same as the cab dash air pressure gauge, check for an under sized
airline, kinks or obstructions in air line. Or the air line may be too long (Must be
under 20 feet [6 m] from primary tank).
Pressure Protection Valve.
Check Pressure Protection Valve air on/off settings (should shut-off in 60 to
80-PSIG / [4.2 to 5.5 Bar] range) and OPEN no higher than 80-PSIG / [5.5 Bar] to
AirPrime.
Check wye strainer on
intake from re pump,
could be clogged.
Remote primer installation: The line from the re pump to the AirPrime has
a wye type strainer just before connecting into the primer body. Remove the
plug, then strainer, and clean the strainer of debris, reinstall strainer and plug.
a) Direct mount on Hale pump installation: Remove the primer from the Hale Q
re pump, check the black plastic strainer (Supplied by Hale).
Check Air line to the
AirPrime.
The air supply line from the air tank is either kinked, undersized or over length.
Replace air line accordingly (NOTE: Found mainly on new installations).
Check discharge and
intake valves.
Cap or plug the discharge and intake valves to prove the valves are not leaking
air into the plumbing system (Hydrostatic pump test is useful for such testing).
Check gated Master Intake
Valves on suction intakes.
a) Remove the MIV and cap intake.
b) Install a cap on the discharge side of the relief valve.
c) Cap the Storz or NH intake.
Check the AirPrime integral
priming valve.
a) The priming valve is not seating in the shut-off position, remove primer,
disassemble, and check the priming valve spring, seat, and operation.
b) The priming valve is “stuck”, check for damaged O-Ring or check to see
that the piston is still fully threaded on the valve stem.
Suction lift too high. Do not attempt lifts exceeding 24 feet.
Blocked suction strainer. Remove any obstructions or debris from hose strainer, do not allow suction
hose or strainer to rest on the bottom of water supply.
Leaking Suction Hose
connections.
Clean and tighten all suction hose connections, check hose washers and
replace as necessary.
Air Trap in suction line.
Suction hose should be positioned with a constant decline to the water supply.
If a trap is unavoidable, repeated priming may be required to eliminate air
pocket.
Multi Location Specic
Problem Likely Cause Corrective Action
Trouble Priming
or Pre-Priming
from Locations
Other Than
Pump.
Not priming from highest
suction plumbing point.
Check suction plumbing elevations, shown on bottom of Pages 10 and 11.
Check for changes in suction high point when truck is drafting on an incline.
Remote Priming Valve
(RPV) not opening.
Defective RPV, defective panel push button, check system plumbing using
schematics on Page 10 (Automatic) Figure 16 and Page 11 (Manual) Figure 17.
Water trap in RPV line. Lines must ascend from highest suction plumbing points to RPV(s) for natural
drainage and to avoid water traps.
AirPrime™Industrial and SC Systems
AirPrime units are available for high volume Industrial Pumpers/Trailers with engine driven air compressors and small Wildland Trucks
without air brakes. Contact Trident for more information.

Trident Emergency Products, LLC
2940 Turnpike Drive | Suite #9 | Hatboro, PA 19040 USA
14
AirPrime™ Fire Pump Priming System
™
Annual Primer Testing
The AirPrime™ primer is designed to meet the NFPA requirements of: Dry Vacuum (TEST #1)and Priming Time (TEST #2). These tests
should be performed on an annual basis, or whenever major repairs or modications have been made to the re pump, plumbing or primer.
TEST #1 Dry Vacuum Test: Checks the primer’s ability to produce 22 inches (Hg) [.745 Bar] of vacuum, and the pump and plumbing’s
ability to hold that vacuum. The test may be run with the pump in gear or not engaged. Never run a dry pump at engine speeds above
1200 RPM. There is no time requirement for the vacuum to reach 22 inches. If the compressor has a capacity of 13.2 CFM [374 cu. cm.
displacement], it can take several minutes to reach 22 inches [.75 Bar]. This time can be shortened by not engaging the pump and increasing
the engine speed to 1200 RPM. The test process is as follows:
1. Drain all water from pump and plumbing.
2. Close all valves and drains. Cap all suction openings and the outlet off of the suction side relief valve (if so equipped).
3. Connect a test vacuum gauge to the intake test gauge connection on the pump panel.
4. Operate the AirPrime with the air system at over 100 PSIG [ 7. 0 B ar ] pressure, air tanks lled to capacity, and at 1000 RPM engine
speed; until the vacuum gauge indicates 22 inches (Hg) [.75 Bar] or more of vacuum. (If the primer is an Automatic AirPrime, use the
PRIME mode switch position to engage the primer).
5. Watch the gauge, if the vacuum falls more than 10 inches in 5 minutes the test has failed and is a certain indication of an air leak(s).
Vacuum leaks may be detected by ear, with the engine turned off. Correct leaks immediately and test the priming system again.
TEST #2 Priming Time Test: This test is to prove that the re pump and primer has the capability of attain a prime and creating
discharge water pressure in a set period of time. This test is also conducted by the apparatus builder prior to delivery. The re pump shall
be engaged and primer actuated. The test is part of an annual pump performance test and is performed as follows:
1. Set up the apparatus in accordance with the pumping test outlined in the NFPA standards.
2. Engage the pump, and increase the throttle to a maximum engine speed of 1000 RPM.
3. Operate the AirPrime with the air system at over 100 PSIG [ 7. 0 B ar ] pressure, air tanks lled to capacity, and at 1000 RPM engine
speed.
• For the Manual controlled primer, release the push button when a discharge pressure over 20 PSIG [1.4 Bar] is obtained.
• For the Automatic AirPrime, place the switch in the AUTO position, it will turn the primer off automatically when priming is attained.
4. The time to prime should not exceed 30 seconds for 1250 GPM [4700 LPM] and smaller pumps. The time to prime should not exceed
45 seconds for 1500 GPM [5600 LPM] and larger pumps. An additional 15 seconds is allowed for pumps with auxiliary suctions using
4" or larger piping.
Higher lifts and operating at higher elevations will slow down time to prime. The air compressor rating should be a minimum of 18 CFM
[410 cu. cm. displacement] for elevations over 4000 feet [1200 m] and lifts in excess of 15 feet [4.5 m]. Operation at these extremes may
require the primer to be operated at engine speeds in excess of 1000 RPM without engaging the pump, until water reaches the impeller.
Never run a dry pump at engine speeds above 1200 RPM.
IN-SERVICE OPERATIONAL TEST (Ramp Test)
The integrity and operation can be quickly checked (on a daily or weekly basis) as outlined below, without re pump engagement:
1. Drain all water from pump and plumbing.
2. Close all valves and drains. Cap all suction openings.
• Operate the AirPrime with the air system at over 100 PSIG [7.0 Bar] pressure, air tanks lled to capacity, and the engine running at
1000 RPM (with an Automatic AirPrime electrically controlled model, use the PRIME mode switch position).
3. Stop running the primer.
Time to reach 15 inches HG [.50 Bar] or 17 feet [5.0 m] on lift gauge should be within the time allowed in list below for the pump tested.
Small Body Pump (Up To 1250 GPM): Vacuum Time
10 inches HG [.33 Bar] (11 feet) 6 Seconds
15 inches HG [.50 Bar] (17 feet) 15 Seconds
Large Body Pump (Over 1250 GPM): Vacuum Time
10 inches HG [.33 Bar] (11 feet) 8 Seconds
15 inches HG [.50 Bar] (17 feet) 20 Seconds
Note: Vacuum Time listed in the table at left are for operations up
to 2000 feet [609 m] of elevation. When running this In-Service
Operational Ramp Test at higher elevations, the vacuum should be
reduced by 1 inch (1.13 feet) for each 1000 feet [304 m] of elevation
over 2000 feet [609 m].

( 215-293-0700 7 215-293-0701
Installation and Operation Guide
Customer Service Phone (215) 293-0700
We pride ourselves with exceptional customer service and are available to answer questions pertaining to new or existing orders and any of your after the sale
support concerns. If a product needs to be returned, please call and request a Returned Goods Authorization (RGA) number. Warranty claims must be made by
an authorized TRIDENT employee. Be prepared to provide the product model number and purchase invoice number. Replacement parts ordered will be invoiced
to your account. Once an RGA number is received, you must write it on all boxes and paperwork. TRIDENT will not accept your returned goods without an RGA
number. Upon receiving the return, if it is determined to be covered under warranty, a credit memo will be issued and mailed to you for your records.
Warning ‐ User Responsibilities
The customer, installer and end-user shall assume sole responsibility in making the nal selection of products and accessories. Furthermore, these parties shall
hold TRIDENT harmless for all liability, claims, suits and expenses incurred. These parties shall ensure maintenance, safety precautions and warnings regarding
the application are enforced at all times. TRIDENT is not responsible for use of products in excess of rated and recommended capacities, design functions or
abnormal conditions.
Caution ‐ Proper Selection of Accessories
TRIDENT offers a wide variety of accessory items and optional features for its products. It is the sole responsibility of the customer, installer and end users to
ensure that the proper items and features have been selected to t the application.
Warning ‐ Follow Instructions
The customer, installer, and end users shall ensure that all potential users of these products receive continual training and access to all relevant product manuals
and safety instructions. This information should be thoroughly reviewed prior to installation, stored and reviewed continually during use of the product. TRIDENT
assumes no responsibility for tness of installation and continued use in specic applications.
Note: All designs, specications, and dimensional data contained in this catalog are subject to change without notice. No additional warranties, express or
implied, including warranties of merchantability for tness for a particular purpose, are created by the descriptions and depictions of the products on or in this
catalog. Not responsible for typographical errors.
Safety First!!!
Serious Injury and Destruction of Property can result from improper selection or improper use of products
described in this instruction manual. Since TRIDENT has no control over the number and variety of applications
for which its products may be purchased or the conditions under which they may be used, TRIDENT liability on
any claim, whether in contract, tort (including negligence), or otherwise, for any loss or damage shall in no case
exceed the price paid for the product or any part thereof which give rise to claim. As always, TRIDENT technical
assistance and support is available for your convenience.
5 Year Warranty
For ve years after the date of purchase, Trident Emergency
Products, LLC warrants its products to be free from defects in
materials and workmanship when properly installed, operated,
and maintained.
If during the warranty period, a product is discovered to be
defective, Trident will, at its option, replace or repair the warranted product or grant the
purchaser a credit for the product claimed to be defective. Trident will have the sole
discretion to determine whether the product was defective.
This warranty is null and void if the product is damaged due to abuse, misuse,
negligence or accidental causes.
No warranty of merchantability or tness for a particular purpose, nor any warranty,
express or implied, is made by Trident. The foregoing states Trident Emergency Products,
LLC's entire and exclusive liability and buyer's exclusive remedy for any claim or
damages In connection with the sale of its products. In no event shall Trident be liable for
any special incidental, or consequential damages whatsoever.
Ordering
Please use Trident part numbers and descriptions when placing orders.
to (215) 293-0701 or placed online at www.tridentdirect.com.
All orders will be acknowledged by Trident within 2-days and shall
become nal after acknowledgment, if not challenged.
No verbal orders will be accepted.
Terms
1%10-NET30 days on approved credit, or with MC/Visa credit card.
Service charge 1.5% on past due accounts.
Freight
F.O.B. Hatboro, PA, USA. Our responsibility ceases upon delivery to common carrier.
Consignee must le claim for storage and damaged freight with the carrier.
Delivery
Most standard items are shipped in ve business days or less. Consult with customer
service for availability, special threads, or special order products.
Return Policy
No material will be accepted for return without authorization by the factory, and a return
goods authorization number assigned. Materials must be returned prepaid. A 20%
restocking fee normally applies. No material will be accepted for a credit after one year
from the date of purchase.
Custom products and special orders are not returnable.
5
Warranty and Product Information

Trident Emergency Products, LLC
2940 Turnpike Drive | Suite #9 | Hatboro, PA 19040 USA
215-293-0700 Phone
215-293-0701 Fax
TridentDirect.com
™
World Class
Fire Industry
Products
AirPrime™ is a trademark of
Trident Emergency Products, LLC
Repair/Replacement Parts
#02.003.1e •06/25/2019
REF # DESCRIPTION PART #
1a Solenoid Valve 12-Volt 30.003.2
1b Solenoid Valve 24-Volt 30.003.3
2 Air Filter Replacement for 1/4" NPT Bore 21.002.0
3Piston 11.001.0
4Valve Stem 05.002.0
5Seal Washer 04.004.0
63/4" Wye Strainer (Replacement Screen: 21.003.1) 21.003.0
7 Rebuild Kit (Seals, Mesh Filter, Spring Valve Plate, Fasteners) 27.003.3
8 Pressure Protection Valve (PPV) 30.053.0
9Lift Gauge 14.006.0
10a Rocker Switch 12-Volt and Label Assembly 27.00 3.5
10b Rocker Switch 24-Volt and Label Assembly 27.00 3.6
11 Label Only: Rocker Switch 02.004.2
12 Pressure Switch and Connector 40.002.1
13a Rocker Switch 12-Volt, Label, Mounting Plate, Lift Gauge Assembly 27.00 3.7
13b Rocker Switch 24-Volt, Label, Mounting Plate, Lift Gauge Assembly 27.00 3.8
14 Label Only: Rocker Switch with Lift Gauge 02.004.4
REF # DESCRIPTION PART #
15a Rocker Switch 12-Volt Replacement 40.001.2
15b Rocker Switch 24-Volt Replacement 40.001.3
16 Wiring Harness for Auto AirPrime 41.001.0
17 Push Button, Label, and Mounting Plate Assembly 27.00 3.1
18 Label Only: Push Button 02.006.4
19 Push Button Replacement 30.005.3
20 Push Button, Label, Mounting Plate and Lift Gauge Assembly 30.005.4
21 Label Only: Push Button with Lift Gauge 02.006.10
22 Remote Priming Valve (RPV) 30.035.1
23 1/4" NPT Air Check Valve 30.012.0
24a Remote Priming Valve with 12-Volt Solenoid 30.035.10
24b Remote Priming Valve with 24-Volt Solenoid 30.035.11
25 Multi-Location Push-Button w/ Mounting Plate 27.003.9
26a Label Only: Primer Front Intake 02.006.5
26b Label Only: Primer Rear Intake 02.006.6
26c Label Only: Primer Left Side 02.006.7
26d Label Only: Primer Right Side 02.006.8
AirPrime Conversion Kits and Rebuild Kit
Conversion Kit: Single Location AirPrime System, Converts Manual to Automatic 27.014.0
Conversion Kit: Multi-Location AirPrime System, Converts Manual to Automatic 27. 014.1
Conversion Kit: Manual AirPrime System, Converts Single (1) Location to Dual (2) Location 27. 0 0 5.2
Conversion Kit: Automatic AirPrime System, Converts Single (1) Location to Dual (2) Location 27. 0 0 5.3
Conversion Kit: Multi-Location AirPrime System, Adds Additional Locations Going From (2) Location to (3) Location. Or From (3) Location to (4) Location 27. 0 0 5.1
Conversion Kit: Automatic AirPrime System, Adding a Lift Gauge to existing Automatic AirPrime. Requires .125" NPT Port. Contact Factory for Details 27. 0 0 5.5
Conversion Kit: Manual AirPrime System, Adding a Lift Gauge to existing Manual AirPrime. Requires .125" NPT Port. Contact Factory for Details 27. 0 0 5.4
Conversion Kit: Manual AirPrime, Converting to Auto with Lift Gauge. Requires .125" NPT Port. Contact Factory for Details 27. 0 0 5.6
Rebuild Kit: Contains Seals, O-Rings, Spring Valve Plate, Domed Inlet Filter and Fasteners 27. 0 0 3 .3
26
6
7
8 9
12
15
16
19
22
24
25
1 5
4
6
2
10
a,b 11
13
a,b 14
17 18
20 21
Automatic
AirPrime Parts
Manual
AirPrime Parts
Multi-Location
AirPrime Parts
Air Flow
23
3
21.003.1
a,b
a,b,c,d
a,b
a,b
Other manuals for AirPrime Series
1
Table of contents
Popular Security Sensor manuals by other brands
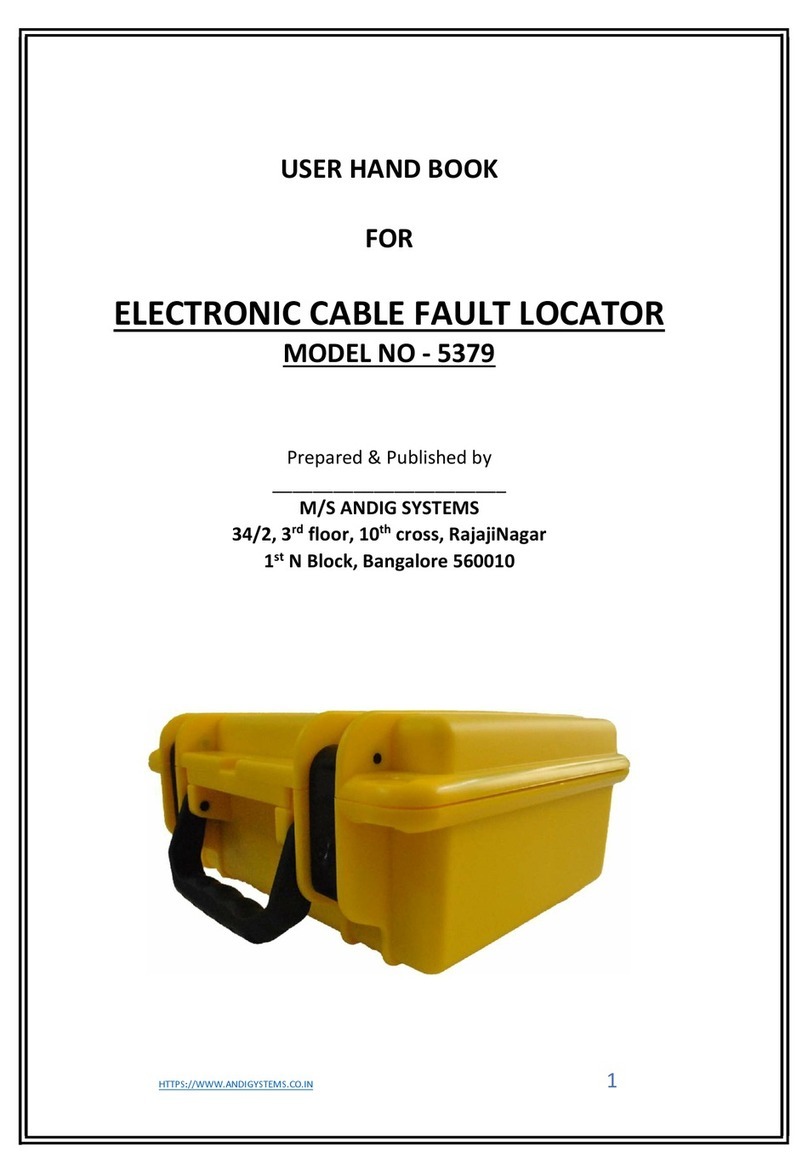
ANDIG
ANDIG 5379 User handbook
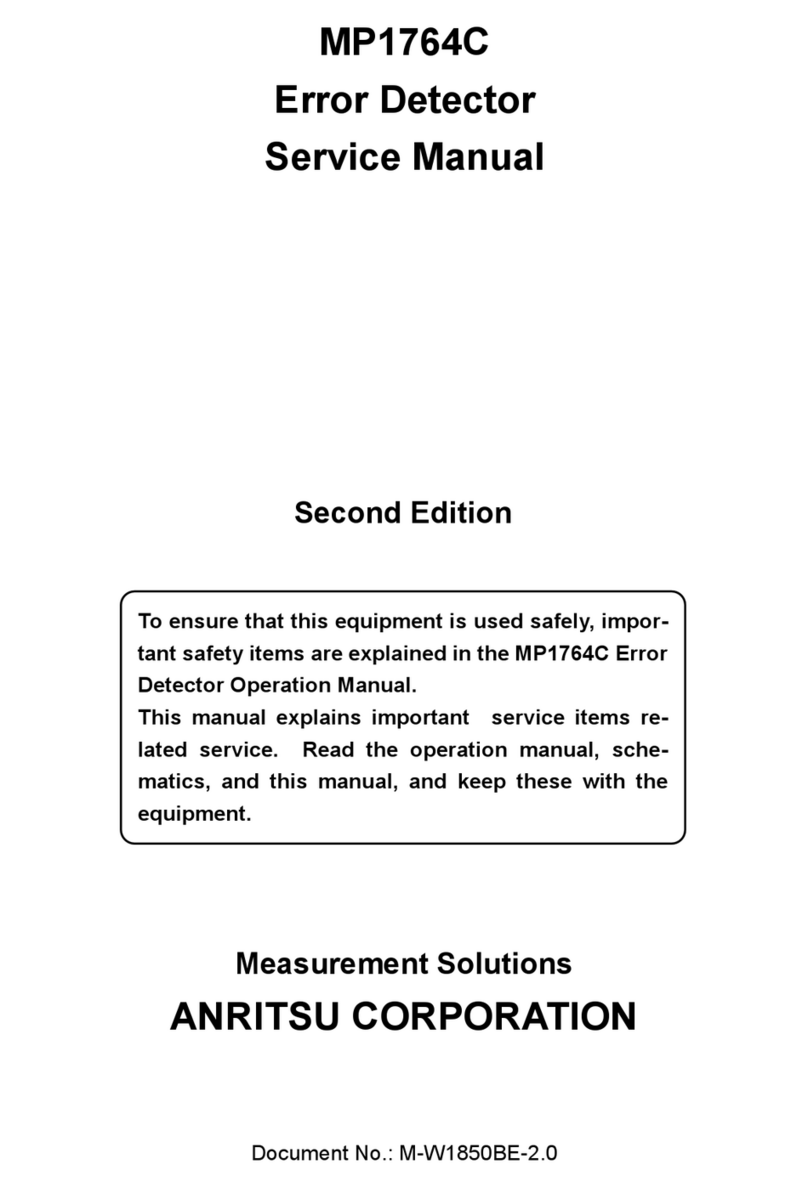
Anritsu
Anritsu MP1764C Service manual
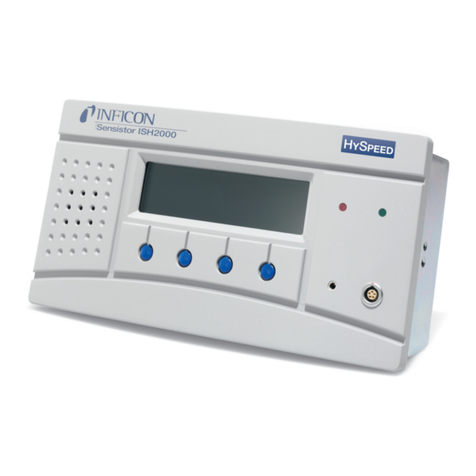
Inficon
Inficon Sensistor ISH2000 HySpeed operating instructions

Buckingham
Buckingham Buck Hook Instructions & warnings
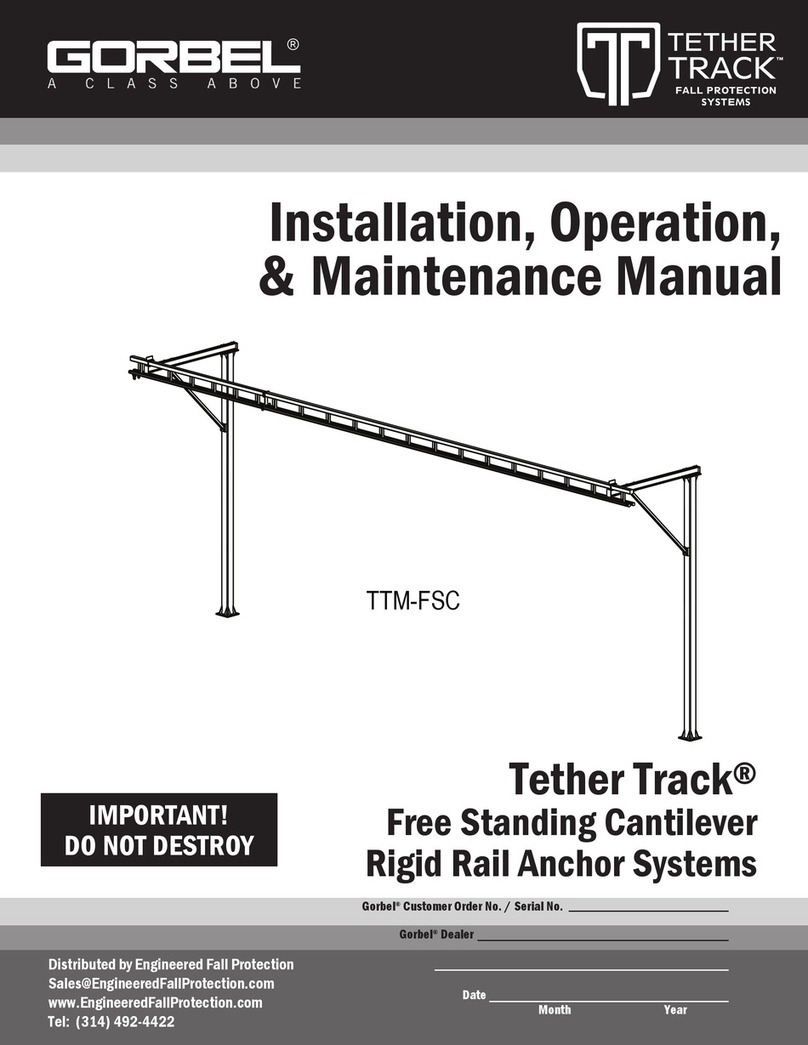
GORBEL
GORBEL Tether Track TTM-FSC Installation, operation & maintenance manual
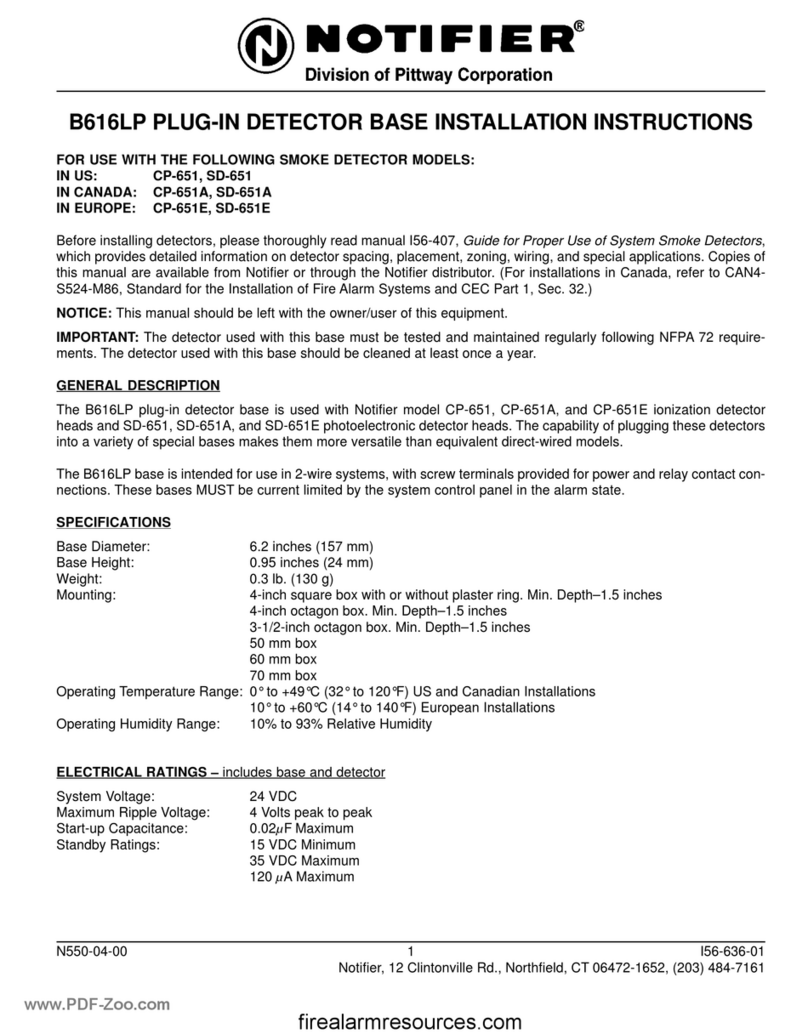
Notifier
Notifier B616LP installation instructions