Tsubaki TD Series User manual

GP22AE-1
Printed October 1, 2021
Tsubaki Troi Drive
TD series
Instruction Manual
TSUBAKIMOTO CHAIN CO.
Thank you for purchasing Worm power drive, Troi Drive, TD series.
Please read this instruction manual carefully and fully understand the reducer specifications for the
products installation and inspection. An experienced worker should handle the products carefully
with referring to instruction manual.
For model-to-order products, use this instruction manual with referring to drawings (specification
drawings or approval drawings) for your reducer. If you have any points unclear on this instruction
manual, please contact your supplier that you sourced the reducer, Tsubaki sales office, or
customer service.
Please ensure that this instruction manual is delivered to the end user who will use the reducer.
Carefully keep this instruction manual to be referred at any time in need.

2
Contents
Safety precautions ······························································································· P 3
1. When the gear box delivered, ············································································· P 5
1-1. What to be checked ·············································································· P 5
1-2. When inquiring ································································································ P 5
1-3. Models············································································································ P 6
2. Transportation ································································································ P10
3. Installation ····································································································· P10
3-1. Solid output shaft type ····················································································· P12
3-2. Hollow output shaft type ·················································································· P13
4. Connection ···································································································· P13
4-1. Direction of output shaft rotation ········································································ P13
4-2. Connection ··································································································· P13
5. Lubrication ····································································································· P13
5-1. Recommended lubrication oil ····························································································· P13
5-2Approximate oil volume ······································································································ P13
5-3. Lubrication oil replacement period ······················································································· P14
5-4.Applying grease (option item) ····························································································· P14
6. Operation ······································································································ P16
6-1. Check before operation ····································································································· P16
6-2. Test drive ························································································································ P16
6-3. Load ······························································································································ P16
6-4. Verification after operation starts ························································································· P16
7. Maintenance ·································································································· P17
7-1. Caution on maintenance ··································································································· P17
7-2. Daily inspection ················································································································ P17
7-3. Inspection and replacement of the oil seals ··········································································· P17
8. Disassemble/assemble ···················································································· P18
9. Troubleshooting ······························································································ P19
10. Internal structure and parts lists ········································································ P19
10-1. Internal structure ············································································································· P19
10-2. Parts lists ······················································································································ P21
11. Storage ······································································································· P22
12 Others ········································································································· P22
13. Warranty ····································································································· P22

3
Safety precautions
In order to use this reducer safely, always be aware of the followings.
●An experienced worker should handle the reducer carefully. The content listed in this instruction manual must be carefully read and fully
understood before using the reducer.
●Please ensure that this instruction manual is delivered to the end user who will use the reducer.
●Carefully keep this instruction manual to be referred at any time in need.
●The level of harm and damage while reducer mishandled is classified into "WARNING" and "CAUTION". These are indicated in the
instruction manual. The definitions and indications are as follows.
WARNING
This indicates the possibility that a dangerous situation may occur, it causes the critical case of death or
heavy injury when the reducer is mishandled.
CAUTION
This indicates the possibility that a dangerous situation may occur, it causes moderate injury or physical
damage, when the reducer is mishandled.
Depending on the situation, even items listed under CAUTION may result in serious consequences.
Both indicate important content that must always be observed.
WARNING
(Overall)
●
Work to transport, install, wiring, run/operate, and maintain/inspect the reducer must always be performed by a technician with
specialized knowledge and skills. Otherwise, there is a risk of explosion, combustion, fire, electric shock, injury, and damage to
equipment.
●
When the reducer is installed in equipment to transport people, always install protective devices for safety on the equipment side.
Otherwise, there is a risk of accidents due to run away or falling equipment and damage to equipment.
●
When the reducer is used in lift equipment, always install safety devices to prevent drops on the equipment side. Otherwise, there is a
risk of accidents due to the lift falling and damage to equipment.
●
Do not work when the wires are live. Always turn off the power before working. Otherwise, there is a risk of electric shock.
●
Special skills and experience are required when overhauling the reducer, so always return it to a dedicated Tsubakimoto Chain Co.
factory for o
verhaul.
(Transport)
●
When hoisting the reducer to transport it, do not enter the area underneath it. Otherwise, there is a risk of accidents due to the reducer
falling.
(Operation)
●
During operation, do not get near or touch any rotating bodies (shafts or other parts). Otherwise, there is a risk of being caught in those
parts resulting in injury.
(Daily inspection and maintenance)
●
In maintenance and inspection during operation, do not touch any rotating bodies (shafts or other parts). Otherwise, there is a risk of
being caught in those parts resulting in accident.
●
Do not remove the pressure vent during operation. High temperature lubrication oil will spray resulting in burns.
●
When inspecting the condition of the gear teeth when stopped, ensure that the rotation of the motor and driven machine has stopped.
Otherwise, there is a risk of being caught in the gear meshing sections resulting in accident.
●
Loading the reducer above its rated capacity can affect the life of the motor and gears and result in damage.

4
CAUTION
(Overall)
●
Do not use the reducer outside of the specifications listed on the nameplate or the specifications in the manufacturing specification
document. Otherwise, there is a risk of injury and damage to equipment.
●
Do not insert fingers or objects into the openings on the reducer. Otherwise, there is a risk of electric shock, injury, and damage to
equipment.
●
Do not use the reducer when damaged. There is a risk of injury and fire.
●
Do not remove the nameplate.
●
Alterations to the reducer by the customer are not covered by the warranty and Tsubakimoto Chain Co. assumes no responsibility for
them.
(Upon receipt of your reducer)
●
Check the orientation of the packaging and open it. Otherwise, there is a risk of injury.
●
Make sure the model number of the unit delivered matches your order. If the wrong reducer is installed, there is a risk of injury and
damage to equipment.
(Transport)
●
Use caution when transporting the reducer as it is dangerous if it drops or falls over. If the reducer has lifting rings, always use those lifting
rings. However, after the reducer is installed in the machinery, do not hoist the machinery itself with the lifting rings. Otherwise, there is a
risk of damaging the lifting rings, injury from the reducer falling over, and damage to equipment. Before hoisting the reducer, check the
weight on the nameplate, packaging, external diagram (specification diagram, final drawings), or catalog, and do not suspend a reducer
that exceeds the weight rating of the lifting rings. Otherwise, there is a risk of damaging the bolts, injury from the reducer falling over, and
damage to equipment.
(Installation)
●
Do not place obstructions around the reducer that will interfere with ventilation. This will hinder cooling and may result in burns or a fire
due to abnormal overheating.
●
Do not get on the reducer or hang from it under any circumstances. Otherwise, there is a risk of injury.
●
Do not touch the shaft ends or the bore section keyways on the reducer with bare hands. Otherwise, there is a risk of injury.
●
For equipment that is averse to greasiness such as food machinery, take precautions for an accidental oil leak due to breakdown or
service life and install damage prevention equipment such as an oil pan. Otherwise, there is a risk the reducer may become faulty due to
an oil leak.
(Connection)
●
When connecting the reducer to a motor and the driven machine, pay careful attention to centering, belt tension, and the parallelism of
the pulleys. When directly connected, pay careful attention to the accuracy of the direct connection. When belt driven, correctly adjust the
belt tension. Before operation, ensure that the tie bolts for the pulleys and couplings have been fully tightened. Otherwise, there is a risk of
injury due to flying debris and damage to equipment.
●
Install a cover so that rotating components will not be touched. Otherwise, there is a risk of injury.
●
When the reducer will rotate independently, remove the key that is temporarily installed to the output shaft. Otherwise, there is a risk of
injury.
●
Check the direction of rotation before connecting the reducer to the driven machine. There is a risk of injury and damage to equipment by
mistaking the direction of rotation.
(Operation)
●
Do not insert your hand in the fan cover. Otherwise, there is a risk of being caught in those parts resulting in injury.
●
During operation, the reducer reaches high temperatures. Use caution not to touch the reducer with your hands or body. Otherwise,
there is a risk of burns.
●
When a problem occurs, immediately stop operation. Otherwise, there is a risk of electric shock, injury, and fire.
●
Do not use the reducer with a load that exceeds the rated load. Otherwise, there is a risk of injury and damage to equipment.
●
Do not loosen the oil plugs during operation. Otherwise, lubrication oil may spray out resulting in burns.
●
When running the reducer in reverse, first stop it, and then run it in reverse. Forward and reverse operation by plucking may damage the
reducer and the driven machine.
(Disassembly/assembly)
●
Repair, disassembly, and assembly should always be performed by a specialist. Otherwise, there is a risk of electric shock, injury, and
fire.
(Daily inspection and maintenance)
●
Change the lubrication oil and grease according to the instruction manual. Always use the type of oil recommended by the manufacturer.
Otherwise, there is a risk of damage to equipment.
●
The surface of the reducer reaches high temperatures, so do not touch it bare hands. Otherwise, there is a risk of burns.
●
Do not change the lubrication oil during operation or immediately after stopping. Otherwise, there is a risk of burns.
●
Diagnose problems that occur based on the instruction manual. Do not operate the reducer until the cause of the problem has been
determined and action has been taken.
(Disposal)
●
The reducer and its lubrication oil should be treated as general industrial waste.

5
□
1 When delivered
1-1. What to be checked at first
Check the following points upon receipt of your reducer.
If it has any problem, please contact the supplier where the reducer was sourced or Tsubakimoto Chain Co. customer service.
CAUTION
● Make sure the model of the unit delivered matches your order. If the wrong reducer is installed, there is a risk of injury and damage to
equipment.
● Check the orientation of the packaging and open it. Otherwise, there is a risk of injury.
(1) Verify the specifications on the nameplate that correspond to your order. Pay special attention to the shaft arrangement and
rotational direction, the position of the input and output shafts, oil gauge and plugs.
(2) Make sure all accessories, such as pressure vents, are attached.
(3) Visual inspection if it has any damage on the reducer during transportation.
(4) Make sure there are no loose on any screws or nuts.
Nameplate
(1) Type, models (2) Gear ratio (3) Manufacturing number (4) Drawing number.
1-2. When inquiring
If the content on the nameplate does not match the reducer that you ordered, or when ordering the replacement reducer and spare parts,
please inform us the following information.
(1)
Type
(2)
Ratio
(3)
Manufacturing number
(4)
Drawing number
1-3. Models
The symbols the models are described on the following page. Make sure the models of the reducer are matched with delivered product.

6
1-3-1. Models, TD series
Single reduction
(1) Solid output shaft type
TD 280
S 30 B R
Product
series
Size
125
150
175
200
225
250
280
315
Output shaft
S: Solid shaft
Nominal
reduction ratio
10: 1/10
20: 1/20
30: 1/30
40: 1/40
50: 1/50
60: 1/60
Mounting position
T: T type
B: B type
V: V type
Shaft arrangement
Refer to page 8
(2) Hollow output shaft type
TD 250 H 60
T LF
Product
series
Size
125
150
175
200
225
250
280
315
Output shaft
H: Hollow shaft
Nominal
reduction ratio
10: 1/10
20: 1/20
30: 1/30
40: 1/40
50: 1/50
60: 1/60
Mounting position
T: T type
B: B type
V: V type
Shaft arrangement
Refer to page 8

7
Double reduction
(1) Solid output shaft type
TD 200 S 100 B L-R
Product
series
Size
125
150
175
200
225
250
280
315
Output shaft
S: Solid shaft
Nominal
reduction ratio
100: 1/100
150: 1/150
200: 1/200
250: 1/250
300: 1/300
450: 1/450
600: 1/600
750: 1/750
900: 1/900
1200: 1/1200
1500: 1/1500
1800: 1/1800
2400: 1/2400
3000: 1/3000
Input shaft position
B: B type
V: V type
Shaft arrangement
Refer to page 9.
(2) Hollow output shaft type
TD 250 H 300 B R-LF
Product
name
Size
125
150
175
200
225
250
280
315
Output shaft
H: Hollow shaft
Nominal
reduction ratio
100: 1/100
150: 1/150
200: 1/200
250: 1/250
300: 1/300
450: 1/450
600: 1/600
750: 1/750
900: 1/900
1200: 1/1200
1500: 1/1500
1800: 1/1800
2400: 1/2400
3000: 1/3000
Input shaft position
B: B type
V: V type
Shaft arrangement
Refer to page 9.

8
1-3-2. Shaft arrangements
Single reduction
(1) Solid output shaft type (S) (common to all sizes)
B
type
BL
BR
BLR
T
type
TL
TR
TLR
V
type
VLU
VLD
VLUD
VRU
VRD
VRUD
(2) Hollow output shaft type (H)
B
type
BLF
(TD125 to TD200)
BRF
(TD125 to TD200)
BDF
(TD225 to TD315)
T
type
TLF
(TD125 to TD200)
TRF
(TD125 to TD200)
TDF
(TD225 to TD315)
V
type
VLF
(TD125 to TD315)
VRF
(TD125 to TD315)

9
Double reduction
(1) Solid output shaft type (S) (common to all sizes)
B
type
B L-R
B L-LR
T
type
B R-L
B R-LR
V
type
V L
-
R
U
V L
-
RD
V L
-
RUD
V R
-
LU
V R
-
LD
V R
-
LUD
(2) Hollow output shaft type (H)
B
type
B L
-
RF
(
TD125 to TD200)
B L-DF
(TD225 to TD315)
B R-LF
(TD125 to TD200)
B R
-
DF
(TD225 to TD315)
V
type
V L
-
RF
(TD125 to TD315)
V R-LF
(TD125 to TD315)
Top
Bottom
Bottom
Top
Top
Bott
o
m
Botto
m
Top

10
□
2 Transportation
WARNING
●When hoisting the reducer to transport it, do not enter the area underneath it. Otherwise, there is a risk of accidents due to the reducer falling.
CAUTION
(Transport)
●
Use caution when transporting the reducer as it is dangerous if it drops or falls over. If the reducer has lifting rings, always use those lifting rings.
However, after the reducer is installed in the machinery, do not hoist the machinery itself with the lifting rings. Otherwise, there is a risk of
damaging the lifting rings, injury from the reducer falling over, and damage to equipment. Before hoisting the reducer, check the weight on the
nameplate, packaging, external diagram (specification diagram, final drawings), or catalog, and do not suspend a reducer that exceeds the
weight rating of the lifting rings.
Otherwise,
there is a risk of damaging the bolts, injury from the reducer falling over, and damage to equipme
nt.
Be sure to use the eye-nut on the top surface of the housing (fastened with a hex bolt in the drilled hole) when transporting the
reducer. Never hook wires or slings to the input/output shafts. Doing so may cause unexpected load to the shaft/bearing and shorten
the life of the reducer or cause a malfunction.
□
3 Installation
CAUTION
●Do not place obstructions around the reducer that will interfere with ventilation. This will hinder cooling and may result in burns or a fire due to abnormal
overheating.
●Do not get on the reducer or hang from it under any circumstances. Otherwise, there is a risk of injury.
●Do not touch the shaft ends, the bore section keyways, or the cooling fin edges on the reducer with bare hands. Otherwise, thereis a risk of injury.
●For equipment that is averse to greasiness such as food machinery, take precautions for an accidental oil leak due to breakdown or service life and
install damage prevention equipment such as an oil pan.
Otherwise,
there is a risk the reducer may become faulty due to an oil leak.
The area of installation should be an ambient temperature between 0 to 40°C, well-ventilated, low in humidity, and have a little or no
dust. Do not use the reducer in locations with corrosive liquids or gases, or in flammable or explosive conditions.
If the reducer is to be used outdoors, cover the reducer or have some protection to avoid direct exposure to rain.
(1) When installing or removing the reducer from the driven shaft, make sure to shut off the power source before working.
(2) Always use the lifting bolt on the top surface of the reducer housing when installing or removing it from the driven shaft. Never
hook wires or slings to the input/output shafts.
(3) Make sure the reducer is balanced and stable when installing or removing it from the driven shaft. Working with the reducer
in an unbalanced position is extremely dangerous as it may turn over.Always maintain the reducer in a stable position.
3-1. Solid output shaft type
The solid output shaft type is foot-mounted type.
- Refer to the following installation as standard.
B type
(input shaft is bottom)
T type
(input shaft is top)
V type
(output shaft is vertical)
Single
reduction
Top ↑
Bottom ↓
Top ↑
Bottom ↓
Top ↑
Bottom ↓
Double
reduction
Top ↑
Bottom
↓
------
Top ↑
Bottom ↓
- If the installation is not as standard and made-to-order products, refer to the outline drawing or contact Tsubaki representative for
the volume and type of lubrication.
- Install on firm and flat installation surface that has enough strength and the installation mounting flatness should be within ±1°.
- Use bolts of JIS strength class 10.9T for installation.

11
Recommended bolts size and length for mounting
Reducer size 125 150 175 200 225 250 280 315
Recommended bolts
M16 x 55
M20 x 60
M20 x 70
M24 x 80
M24 x 80
M30 x 100
M30 x 100
M30 x 110
-Avoid the deformation while installing reducer.
3-2. Hollow output shaft type
It has three options to install reducer against rotating: torque arm mount, flange mount, foot mount (EW-hollow shaft only).
(1) Before inserting the driven shaft into the output hollow shaft, make sure the outside of the driven shaft and the inside of the hollow
shaft are free from scratches or any dust.
(2) Apply grease or molybdenum disulfide on the driven shaft, it makes easier to install.
(3) If the shafts fit very tight, tapping its opposite side of hollow shaft by a plastic hammer. It has to be done carefully not to damage the
oil seal at output shaft.
(4) The hollow shaft keyway is finished with New JIS standards for normal grade keyways. As for key length, refer to the following table.
Recommended driven shaft lengths
Reducer size 125 150 175 200 225 250
280
315
Output shaft length: A 200 250 270 290 320 356 404 454
Recommended driven shaft lengths: L
170 220 238 258 272 303 344 386
3-2-1. Installation/removal of torque arm
1. Installation procedures
(1) Fix the torque arm to the reducer with bolts.
Note) If the torque arm is purchased from Tsubakimoto Chain Co., use the attached bolts. When the torque arm is prepared by customer, use a
bolt strength class of 10.9 or equivalent.
(2) Insert the reducer onto the driven shaft.
(3) Fix the reducer to the driven shaft in the axial direction.
Tsubakimoto Chain Co. recommends using the stop ring groove on the hollow output shaft as shown in the figure below
and fixing the driven shaft with the stop ring and end plate.
(Refer to technical data on catalogue "Detailed dimensions of hollow output shaft")
(4) Once fix the position of the reducer, install the torque arm to prevent the reducer and driven shaft from rotating.
Keep sufficient space for the torque arm is free to move in the axial direction.
Note) Do not fix the torque arm position before fixing it to the reducer. Doing so may damage the reducer. Follow the work procedure as outlined
here.
(Table 1) The dimensions and configurations given in the following table are recommended for the end plate preparation, which
also serves as a draw plate.
Output shaft bore
diameter Recommended plate dimensions Bolt for plate
(with spring washer) Stop ring size
ΦD
T
H
Z
Y hole
P
125
Φ70
69.5
14
62
M24
2
-
14
44
2
-
M12 × 60
C70
150
Φ80
79.5
17
7
0
M24
2
-
14
52
2
-
M12 × 65
C80
175
Φ90
89.5
17
80
M30
2
-
1
4
60
2
-
M12 × 65
C90
200
Φ100
99.5
17
89
M30
2
-
18
65
2
-
M16 x 75
C100
225
Φ110
109.6
20
99
M30
2
-
18
65
2
-
M16 x 85
C110
250
Φ125
124.4
20
113
M30
2
-
18
70
2
-
M16 x 8
5
C125
280
Φ130
129.4
24
118
M36
2
-
2
2
80
2
-
M20 x 100
C130
315
Φ160
15
9.4
24
146
M36
2
-
22
85
2
-
M20 x 100
C160
(Output shaft length)
Output shaft
D
riven shaft
(Recommended
driven shaft length)
Z tap
2
-
Y hole

12
2. Removal procedures
(1) Lift the reducer using the lifting bolts.
(2) Loosen the end plate bolt which fixes (axial direction) the reducer to the driven shaft.
(3) Remove any attachments on the tip of the torque arm, which stops the shaft from rotating, so that it moves freely.
(4) Remove the hollow output shaft from the driven shaft so as to prevent the application of excessive force between it and the
housing. Prepare a draw plate (Table 1) and jack bolt (Table 2). Removal is much easier when the jack bolt is attached as shown
in Figure 3.
Table 2 Jack bolt dimensions Figure 3
Size Output shaft
bore diameter
Jack bolt
(fully threaded)
125
φ70
M24 x 150
150
φ80
M24 x 150
175
φ9
0
M3
0 x 180
200
φ100
M30 x 180
225
φ110
M30 x 180
250
φ125
M30 x 180
280
φ130
M36 x 250
315
φ160
M36 x 250
3-2-2. Installation/removal for flange mounting
1. Installation procedures
Mounting the reducer to the driven machine (mounting without radial load onto the reducer)
(1)
Insert the reducer onto the driven shaft.
(2)
Use the screw taps on the flange surface of the housing for mounting.
Use bolts as JIS strength class 10.9T or equivalent for installation. The recommended bolt and mounting dimensions are
as in the following table.
(Bolt sizes in table: depths are tapping depths.)
Recommended bolt sizes for flange surface
Reducer size
125
150
175
200
225
250
280
315
Bolt
size
M12 25 deep
M12 25 deep
M14 30 deep
M16 30 deep
M16 28 deep
M20 35
dee
p
M20 35 deep
M20 35 dee
p
Mounting PCD
255
300
350
380
390
430
490
550
Number used 6 evenly
spaced
8 evenly
spaced
8 evenly
spaced
8 evenly
spaced
8 evenly
spaced
8 evenly
spaced
8 evenly
spaced
8 evenly
spac
ed
Bolt strength class
10.9 or
greater
10.9 or
greater
10.9 or
greate
r
10.9 or
greater
10.9 or
greater
10.9 or
greater
10.9 or
greater
10.9 or
greater
Tightening torque
N·m (kgf·m)
84 to 118
(8.6 to 12)
84 to 118
(8.6 to 12)
137 to 186
(14 to 19)
206 to 294
(21 to 30)
206 to 294
(21 to 30)
402 to 559
(41 to 57)
402 to 559
(
41 to 57)
402 to 559
(41 to 57)
(3)
Use the step on the housing for positioning.
Note) The end plate is not necessary for flange mounting. If the shaft is fixed by end plate, it causes the additional thrust load on the
bearing and it gives damage to the bearing at hollow shaft.
Mounting the reducer by its flange to the driven machine (mounting with radial load onto the reducer)
(1)
Insert the reducer onto the driven shaft.
(2)
Adjust the radial alignment with the driven shaft and install the reducer without load and have some play in the thrust direction.
(3)
Use the taps on the flange side of the reducer housing while using the spigot facing on the housing for positioning.
(4)
After fixing the reducer, fix the driven shaft in the thrust direction.
Note) If the driven shaft is fixed in the thrust direction first, the bearing may be damaged due to the thrust to the bearing on the hollow
output shaft.
2. Removal procedures
The reducer is mounted to the driven machine (mounting without radial load onto the reducer)
(1)
Loosen the flange bolts which fix the reducer to the driven machine.
(2)
Remove the hollow output shaft from the driven shaft without any load between housing and output shaft. Prepare a draw
plate (Table 1) and jack bolt (Table 2). Removal with the jack bolt makes easier process as shown in Figure 3.
Output sha
ft
Jack bolt
Stopper
Stop ring
Driven shaft
Draw plate (end plate)

13
The reducer is mounted by its output flange direct to the machine (mounting with radial load onto the reducer)
(1)
Hold the driven shaft steady and balanced.
(2)
Loosen the flange which fixes the reducer to the machine.
(3)
Remove the hollow output shaft from the driven shaft without any load between housing and output shaft. Prepare a draw
plate (Table 1) and jack bolt (Table 2). Removal with the jack bolt makes easier process as shown in Figure 3.
□
4 Connection
CAUTION
●
W
h
en connecting the reducer to a motor and the driven machine, pay careful attention to centering, belt tension, and
the parallelism of the pulleys. When directly connected, pay careful attention to the accuracy of the direct connection.
When belt driven, correctly adjust the belt tension. Before operation, ensure that the tie bolts for the pulleys and
couplings have been fully tightened. Otherwise, there is a risk of injury due to flying debris and damage to equipment.
●
Install a cover so that rotating components will not be touched. Otherwise, there is a risk of injury.
●
When the reducer will rotate independently, remove the key that is temporarily installed to the output shaft. Otherwise,
there is a risk of injury.
●
Check the direction of rotation before connecting the reducer to the driven machine. There is a risk of injury and
damage to equipment by mistaking the direction of rotation.
4-1. Verifying the direction of rotation
Worms are always a right-handed helix. Verify the rotational direction of the input and output shafts.
4-2. Connection
Connecting the reducer's input and output shafts
Do not apply impacts or excessive thrust loads to the shaft when installing pulleys, sprockets, or couplings to the reducer input/output
shafts.
Align accurately. Refer to catalogs/manuals of those pulley, sprocket, or coupling, and keep alignment accuracy.
Shaft eccentricity, and radial and axial loads that exceed allowable values may cause vibration or noise, possibly shortening gear,
bearing, and shaft life.
□
5 Lubrication
The worm reducer has been filled with lubrication oil when shipped from the factory. The reducer does not need to oil to be filled, it can be used
as shipped.
5-1. Recommended lubrication oil (standard):
Single reduction: Idemitsu DaphneAlpha Oil TE260
Double reduction: Idemitsu DaphneAlpha Oil TE380
Lubrication oil is the one of the most important factors for reducer performance, life, and efficiency. Use only lubrication oil
recommended by Tsubakimoto Chain Co. Do not mix the oil with other brands.
In case using other brands, Exxon Mobile oil,
Single reduction: Mobile SHC632
Double reduction: Mobile SHC634.
Do not mix and use other lubrication oils. Gear box performance and operation life may decrease significantly.
Single reduction reducers running at an input speed of 500 r/min or slower, change the lubrication to Daphne Alpha Oil TE380, it
gives longer operation life.
Do not change the brand of lubrication oil. Please contact to supplier where the product was purchased or contact toTsubaki.
For DaphneAlpha Oil TE, please contact to supplier where the product was purchased or contact to Tsubaki.
Note) Contact Tsubaki if the ambient temperature is below -10°C or above 50°C.
5-2Approximate oil quantity
Even with the same size reducer, oil quantity varies depending on the reduction ratio. Refer to the quantity in the following tables as a
guideline, and always check the oil level with the oil gauge. (The oil quantity should be checked through the oil gauge while the
reducer is not working, and oil level is still. Note) Do not mix the brand of oil used for the single and double reduction.

14
- Single reduction
(1) Solid output shaft type (S) Unit: L
Size
Type 125 150 175 200 225 250 280 315
Type B 3.1 5.1 8.4 13.0 9.0 13.0 18.0 29.0
Type T 6.5 11.0 16.0 25.0 24.0 35.0 49.0 75.0
Type V 4.8 8.2 12.0 19.0 16.0 22.0 31.0 46.0
(2) Hollow output shaft type (H) Unit: L
Size
125 150 175 200 225 250 280 315
Type B 2.2 4.2 6.5 8.5 9.0 13.0 18.0 29.0
Type T 5.1 8.0 13.0 15.0 20.0 27.0 38.0 58.0
Type V 3.7 5.9 9.6 12.0 15.0 20.0 28.0 44.0
- Double reduction
(1) Solid output shaft type (S) Unit: L
Size
125 150 175 200 225 250 280 315
Type B 4.1 7.0 11.0 17.0 13.0 19.0 28.0 39.0
Type V 5.8 10.0 13.0 22.0 20.0 28.0 41.0 56.0
(2) Hollow output shaft type (H) Unit: L
Size
125 150 175 200 225 250 280 315
Type B 3.2 6.0 9.0 13.0 13.0 19.0 28.0 39.0
Type V 4.7 8.0 12.0 16.0 19.0 26.0 38.0 54.0
5-3. Lubrication oil replacement, period and notes
(1) Lubrication oil is the one of the most important factors for the reducer performance, life, and efficiency. Use only lubrication oil
recommended by Tsubaki.
(2) Procedures of the lubrication oil replacement
•First replacement: 1000 hours or three months after operation, whichever comes first.
•Regular maintenance: oil replacement every 5000 hours or one year of whichever comes first.
•While in the replacement, if the drastic spoil of oil performance (viscosity, color or any) is found, plan the maintenance interval more
frequently and replace the oil earlier.
•It is easier to drain oil while it is warm just after operation. However, hot oil may injure like burns and is extremely dangerous. Keep
the housing surface temperature at cooler around 40 to 50°C before draining the oil.
•Tsubaki recommends flushing the inside of the housing with the new oil when replacing the oil.
Note) Do not mix the oil with other brands.
(3) Please check and keep the oil level higher position than center of oil gauge.
When the oil level is or comes lower below the oil gauge window, but some case it shows the oil at oil gauge due to the oil surface
tension or remaining oil in the oil gauges.
5-4. Greasing (made to order specification)
When the mounting direction of the reducer causes shafts to be vertical (where the bearing is located above the oil level), the bearing
must be greased periodically.
Models that must be greased are provided with a tapped hole for mounting a grease port.
(This is indicated on the drawings as the grease nipple. Refer to the outside drawing such as specification drawing or final drawings).
A stopper plug (M6 fine threaded hex bolt) is mounted before shipment to prevent oil leakage during transport. Replace it with the
grease nipple supplied with the reducer during installation and before operation. Note, the bearings are greased before shipment.
Follow the procedures every 1000 hours of operation, before initial use and after operations.

15
Step
Greasing
procedures
1
Add grease
w
hile
the machine is
all
stopped
and no
t in the
operation.
2 Greasing by the grease gun through grease port or grease nipple that located on the top of the housing. Use only the recommended grease.
Note) Do no
t
app
ly
over grease. Doing so may cause the reducer to heat up
and cause the lubrica
tio
n oil to deteriorate prematurely.
Grease nipple size:A-M6F
5-4-1. Recommended grease (standard specification, ambient temperature: -10°C to 40°C)
Manufacturer
Brand (industrial all
-
purpose grease JIS grade 2)
EMG
Lubricants
Mobilux EP2 (factory filled)
Idemitsu
Daphne
Epo
nex No.
2
Note) A different brand of grease may be used for special specifications (high temperature, freezing, etc.) Always supply with the type of lubricant
appropriate for the specifications. Also take note of any precautions documented on the external diagrams (specification diagrams, final
drawings).
5-4-2.Approximate greasing volume (* Grease input shaft on top side.)
(1) Input shaft on top
・Reduction ratio 1/10 to 1/60 Unit: g
Sol
id type (S type)
Hollow type (H type)
Size
125 150 175 200 225 250 280 315
Size
125 150 175 200 225 250 280 315
19
28
36
46
44
64
96
127
19
28
36
46
44
69
99
127
・Double reduction ratio 1/100 to 1/3600 Unit: g
Solid type (S type)
Hollow type (H type)
Size
125 150 175 200 225 250 280 315
Size
125 150 175 200 225 250 280 315
- 20
25
25
25
25
30
30
- 20
25
25
25
25
30
30
(2) Input shaft at bottom
・Reduction ratio 1/10 to 1/60 Unit: g
Solid type (S type)
Hollow type (H type)
Size
125 150 175 200 225 250 280 315
Size
125 150 175 200 225 250 280 315
17
45
60
72
47
67
98
127
28
40
47
74
47
67
98
127
・Double reduction ratio 1/100 to 1/3600 Unit: g
Solid type (S type)
Hollow type (H type)
Size
125 150 175 200 225 250 280 315
Size
125 150 175 200 225 250 280 315
- 15
21.5
37
37
56
79
79
- 15
21.5
37
37
56
79
79
Greasenipple(oppositesurface)
Grease nipple
Grease nipple
Greasenipple
Grease nipple
Grease nipple
Grease nipple

16
□
6 Operation
WARNING
(Operation)
●
During operation, do not get near or touch any rotating bodies (shafts or other parts). Otherwise, there is a risk of being caught in those parts
resulting in injury.
CAUTION
(Operation)
●
Do not insert your hand in the fan cover. Otherwise, there is a risk of being caught in those parts resulting in injury.
●
During operation, the reducer reaches high temperatures. Use caution not to touch the reducer with your hands or body. Otherwise, there is a risk of
burns.
●
When a problem occurs, immediately stop operation. Otherwise, there is a risk of electric shock, injury, and fire.
●
Do not use the reducer with a load that exceeds the rated load. Otherwise, there is a risk of injury and damage to equipment.
●
Do not loosen the oil plugs during operation. Otherwise, lubrication oil may spray out resulting in burns.
●
When running the reducer in reverse, first stop it, and then run it in reverse. Forward and reverse operation by plucking may damage the reducer
and the driven machine.
The reducer is filled with lubrication oil and plugged before shipment. Replace the plug with the supplied pressure vent before use.
Note 1) If the reducer is operated without replacing the plug, oil may leak due to high internal pressure.
6-1. Double checking before operation
6-1-1. Checking the reducer
Upon completing the installation, check the following prior to operation:
(1) Is the reducer filled with the correct amount of lubrication oil? (The amount of lubrication oil is correct if it can be seen in the
oil gauge.)
(2) Has the pressure vent been installed? (If the reducer mounting direction is a special design and comes with a grease
nipple, install it as well.)
(3) Is the reducer properly connected properly to the driven machine?
(4) Are the mounting bolts fully tightened?
(5) Is the direction of rotation being correct?
Make sure the equipment incorporates failsafe measures due to the use of the reducer, or in the event the reducer malfunctions.
6-2. Trial run
No trial run is made prior to shipment. For best results, operate the reducer for roughly one day under 1/2 to 1/3 load.
6-3. Load
Loading the reducer above its rated capacity can affect its life and result in damage.
Do not load the reducer above its rated capacity.
6-4. Verification after operation starts
Verify the following after starting production:
a) There is no abnormal vibration, noise, heat, etc.
b) The reducer is not subject to shock or overloads.
c) The temperature is not unusually high.
Note) The reducer may generate heat during the first two or three days of operation. This is expected and does indicate a problem.
However, if the housing temperature exceeds 100°C, it could indicate insufficient capacity, incorrect oil level, or improper
installation. Check each location. Note, do not touch the reducer with your bare hands when checking. Doing so may cause
burns.

17
□
7 Maintenance
WARNING
●
In maintenance and inspection during operation, do not touch any rotating bodies (shafts or other parts). Otherwise, there is a risk of being caught in
those parts resulting in accident.
●
When entering the inside of the product to inspect it while stopped, first confirm that the rotation of the motor and the driven machine has stopped,
and sufficiently cool the inside of the product, and then you must work while ventilating the interior. While performing the inspection work, arrange
personnel for confirming safe working conditions on the exterior, and always confirm safety with the worker. Be aware that the product interior is
slippery from lubrication oil and take sufficient safety precautions.
Otherwise,
there is a risk
accid
ent
.
CAUTION
(Daily inspection and maintenance)
●
Change the lubrication oil and grease according to the instruction manual. Always use the type of oil recommended by the manufacturer. Otherwise,
there is a risk of damage to equipment.
●
The surface of the reducer reaches high temperatures, so do not touch it bare hands. Otherwise, there is a risk of burns.
●
Do not change the lubrication oil during operation or immediately after stopping. Otherwise, there is a risk of burns.
●
Diagnose problems that occur based on the instruction manual. Do not operate the reducer until the cause of the problem has been determined and
action has been taken.
7-1. Maintenance
When performing maintenance, wear suitable clothing and use protection including safety glasses, gloves, safety shoes, etc.
To prevent secondary accidents, keep the surrounding area safe and tidy.
Always turn the power off and wait for the machine to come to a full stop.Also, use lock-outs to prevent unintentional power supply.
The reducer reaches extremely high temperatures during operation. Do not touch with your bare hands.
Read and follow labor safety codes and standards.
7-2. Daily inspection
Make daily inspections using appropriate measuring instruments with the following procedures and take note of operating conditions.
Failure to do so may result in problems.
Inspection items
Inspection details
Noise
Is the noise louder than usual?Are there any unusual noises?
Vibration
Are there any unusual vibrations?Any rapid changes in vibration?
Temp
erat
ure
Is the surface temperature of the reducer higher than usual?Any rapid temperature rises?
Oil level
Is the oil level correct when the machine is stopped?
Mounting bolts
Are any of the bolts loose?
Chain/belt
Are the chains/belts loose?
Lubrican
t co
ndition
Has the lubricant blackened due to abrasion powder?
Oil leakage
Are there any leakages from the connection points on the reducer, oil seals, caps?
Pressure vent
Are the holes for air bleeding clogged?
Note) When a problem occurs, immediately stop operation and perform a detailed inspection.
Note) If the cause is unclear or repair is not possible, please contact the dealer where the reducer was purchased or Tsubakimoto Chain
Co. customer service.
7-3. Inspection and replacement of the oil seals
Oil seals wear and have a service life which may eventually lead to oil leakage. The service life may be shorter when used at high
temperatures, high rotating speeds, outdoors, or otherwise harsh conditions. Inspect the oil seals at regular intervals and replace
immediately if oil leaks exist. Always replace the oil seals with the same model number and material. (Do not use oil seals made of
different materials as this can cause oil leakage.) Refer to the oil seal manufacturer's catalog when replacing. The procedures for
replacing oil seals and filters are listed on the next page. (TD225 to TD315 do not have a filter construction.)
Occasionally, during the first few hours of operation, grease filled during the assembly process may seep out of the oil seal lip. This is
normal and does not affect the performance of the reducer.

18
Oil seal and filter replacement procedures
Replace the oil seals and filters attached to the various covers such as the housing, input seal support, output seal support, output bearing
support, and the motor flange with the following procedure. Check the model and dimensions in the catalog and instruction manual to
confirm that the oil seals and filters to replace are correct. They cannot be replaced if the model and dimensions are different. For the filters,
please consult with Tsubakimoto Chain Co.
Note) Failures that are caused by the customer replacing the oil seals are not covered by the Tsubakimoto Chain Co. warranty.
Item Details
Item Details
Remove
reducer equipment
Remove the reducer from the equipment. Remove all parts
incorporated on the input and output shafts of the reducer. Prepare a
sufficient maintenance space so that the work can be safely done.
Perform the maintenance work with the reducer in a stable position.
When the covers (seal support, output bearing support, motor
flange) are removed when they are mounted on the equipment,
there is a risk that internal components such as the shaft may drop
or fly off due to the mounting position.
How to attach the oil seals,
filters
●Apply a liquid gasket to the mating portion of the covers (seal
support, output bearing support, motor flange). (See the figure
above)
Check before
removal
●Before removing the housing and covers (seal support, output
bearing support, motor flange), check that the lubrication oil in the
reducer has been drained.
●Check that no load is applied to the shafts as they may start
moving by removing the covers (seal support, output bearing
support, motor flange) when there is a load applied to them,
which may result in injury.
Protection from the shaft
●
When incorporating the covers (seal support, output bearing
support, motor flange), the oil seal lip may be damaged by the
shoulder edge of the shaft. Before incorporating them, wrap
the shaft with vinyl tape, and after incorporating them, remove
the vinyl tape.
(Use caution as the shaft keyway may also damage the lip in the
same manner.) The same procedure also applies for the
housing.
Remove the oil seals,
filters
●Remove the covers (seal support, output bearing support, motor
flange).
●Remove the old oil seal using the groove for oil seal remove on
the inside of the cover.
The filter and shim can
also be removed at this
time.
●Clean off the liquid
gasket that is attached to
the cover, reducer
housing, and polyester
shim.
●For the housing, remove in the same order as the covers.
Attach the
seal support
●Attach the covers (seal support, output bearing support, motor
flange) to the reducer housing. When doing so, do not forget to
attach the polyester shim.
●Bolt the bolts and tighten them to the correct torque.
How to attach the oil seals,
filters
●
Before pressing the oil seal into the covers (seal support, output
bearing support, motor flange), insert the filter and shim into the
oil seal press section in that order. (For the housing, insert in the
same order.)
●Before pressing the oil seal, always fill the oil seal lip groove with
a mineral-based lithium grease. (Approximately 50% of the lip
space)
●Apply a liquid gasket to the circumference of the oil seal. (Not
necessary when the circumference of the oil seal is rubber)
●When pressing the oil seal, use a flat press fixture to press in the
oil seal so that it is not slanted, as shown in the figure below. * For
attaching the oil seal, also refer to the oil seal manufacture's
catalog.
Check seal performance
If the liquid gasket was not properly applied when attaching the
covers (seal support, output bearing support, motor flange), oil
may leak from the mated surface of the reducer housing and
cover.
Approximately 24 hours after changing the oil seal, check if any oil
is leaking from the mated surface. If any oil is leaking, remove the
covers once again, remove the liquid gasket, and re-apply it.
□
8 Disassembly/assembly
CAUTION
(Disassembly/assembly)
・Repair, disassembly, and assembly should always be performed by a specialist. Otherwise, there is a risk of electric shock, injury,
and fire.
(1)Never disassemble the reducer except for repairs (replacing the oil seals, other components).
(2)Tooth contact and bearings have been adjusted for optimal performance.
(3)Contact us if the reducer needs to be disassembled.
Oil seal
Shim
Filter
Stand(holdon machinedsurfac
e)
Pressoilseal withpressor plastichammer
(Firmlypressinto edge)
Installationfixture(push plate)
Oilseal
Applyliquid gasket
Vinyl tape
Cover

19
□
9 Troubleshooting
If a problem occurs with the reducer, refer to the table below to troubleshoot the problem.
Problem
Possible cause
Action
Abnormal
temperature rise
Overload operation
Check and apply the correct load.
Insufficient or too much lubricant
Fill with the appropriate volume.
Oil contamination or wrong oil
Replace
d
with new and co
rrect oil.
Bearings are overtightened
Contact
Tsubakimoto Chain Co
.
for adjustment.
Loud noise
Strong vibration
Damaged bearings
Contact Tsubakimoto Chain Co. for repair.
Bad tooth contact
Bearings are overtightened
Damage to th
e
teeth
Insuff
icient oil
Contact
Tsubakimoto Chain Co
.
for repair and lubrication.
Contaminated with foreign objects Contact Tsubakimoto Chain Co.for repair and oil
replacement.
Oil leak
Oil seal wear/damage
Replace the oil seal (including filter, dep
e
nding on model)
Damaged oil gauge
Replace the oil gauge
Bolts/plugs ha
ve become loose
Retighten loose bolts/plugs.
Output shaft does not
rotate
Worm wheel wear
Contact Tsubakimoto Chain Co. for repair.
Breakage of worm shaft or worm wheel
Breaka
g
e of worm wheel
hub and output shaft key
Both input and output
shafts do not rotate
Jammed
with foreign objects
Contact Tsubakimoto Chain Co. for repair.
Damaged or broken bearings
Seized gear teeth
□
10 Internal construction and parts lists
10-1. Internal construction
This section lists representative examples. Please use it as a reference.
(1) Single reduction
・This drawing shows the internal construction of the TD250 (single reduction).
・This drawing is representative and may differ slightly depending on the model and size.
(The TD125 to TD200 have a filter construction.)

20
<
Major parts table> For consumables by size (bearings/oil seals), see the parts lists.
No.
Part name No.
Part name
1 Housing 11
Fan
2 Worm shaft 12
Fan cover
3 Worm wheel 13
Input shaft bearing
4 Output shaft 14
Input shaft bearing
5 Input seal support 15
Output shaft bearing
6 Input bearing support I 16
Input shaft oil seal
7 Input bearing support III 17
Output shaft oil seal
8 Output seal support 18
Oil gage
9 Output cap 19
Pressure vent
10
Inspection cap 20
Drain oil port
(2) Double reduction
・This drawing shows the internal construction of the TD225 (double reduction).
・This drawing is representative and may differ slightly depending on the model and size.
(The TD125 to TD200 have a filter construction.)
<
Major parts table> For consumables by size (bearings/oil seals), see the parts lists.
No.
Part name No. Part name
1 Input housing 14 Output cap
2 Housing 15 Inspection cap
3 I Worm 16 Intermediate collar
4 I Wheel 17 Input shaft bearing
5 II Worm 18 Input shaft bearing
6 II Wheel 19 Intermediate shaft bearing
7 Output shaft 20 Intermediate shaft bearing
8 Input seal support 21 Output shaft bearing
9 Input bearing support II 22 Input shaft oil seal
10
Intermediate bearing support III 23 Output shaft oil seal
11 Intermediate cap 24 Oil gage
12
Intermediate seal support 25 Pressure vent
13
Output seal support 26 Drain oil port
Table of contents
Other Tsubaki DC Drive manuals
Popular DC Drive manuals by other brands

GFA
GFA ELEKTROMAT SE 9.24 WS-25,40 installation instructions
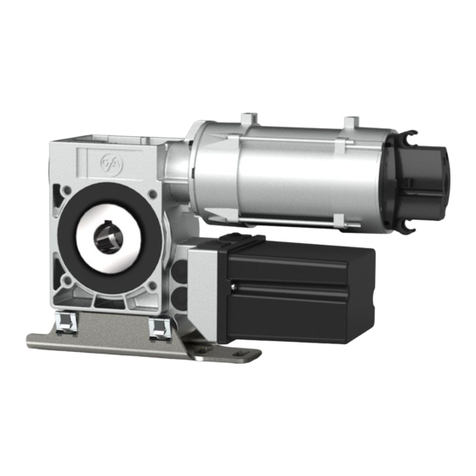
GFA
GFA ELEKTROMAT SI 25.15-30,00 installation instructions
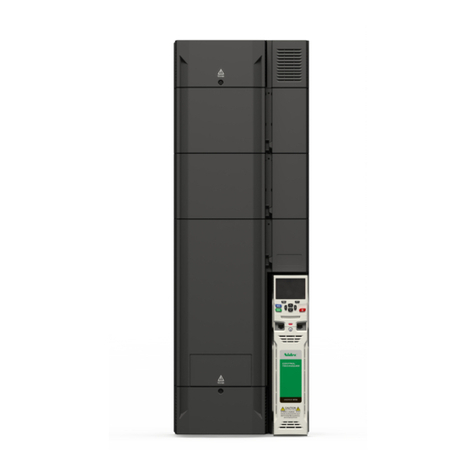
Nidec
Nidec Control Techniques Unidrive M Modular installation guide
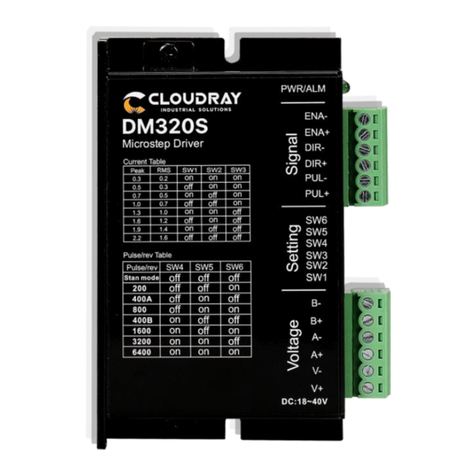
Cloudray
Cloudray DM Series user manual
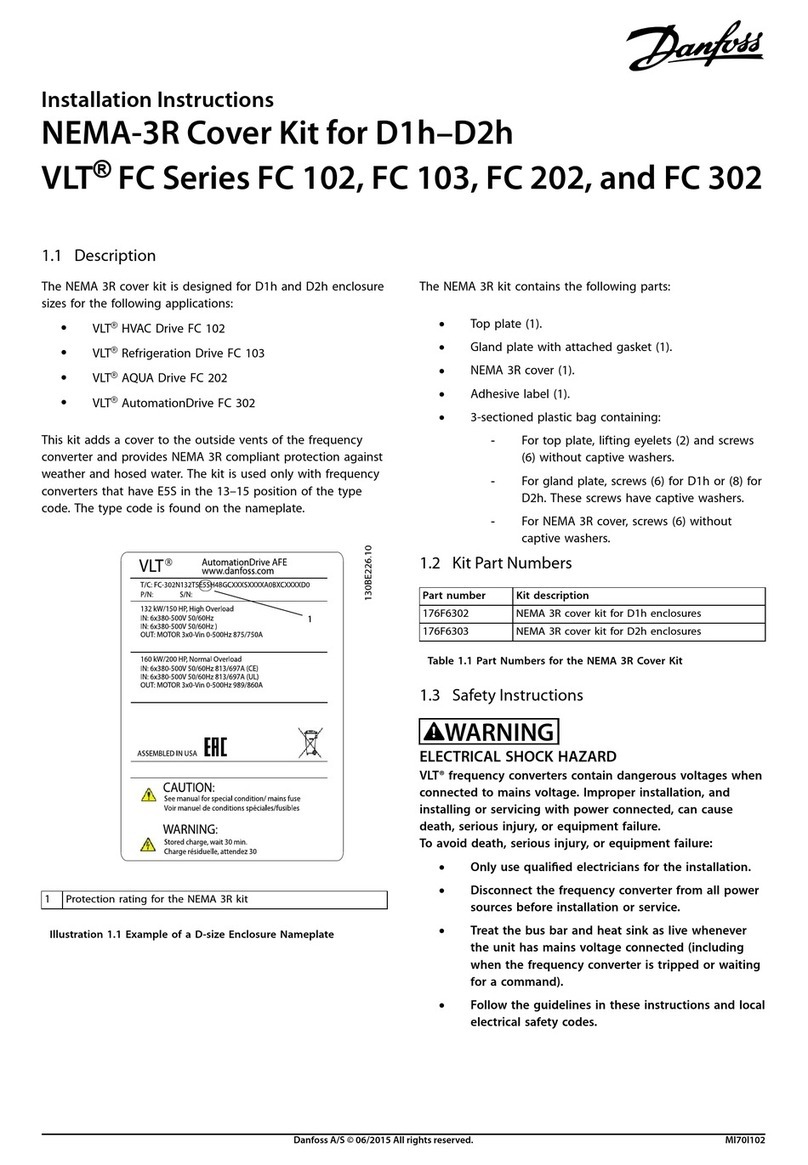
Danfoss
Danfoss NEMA-3R installation instructions
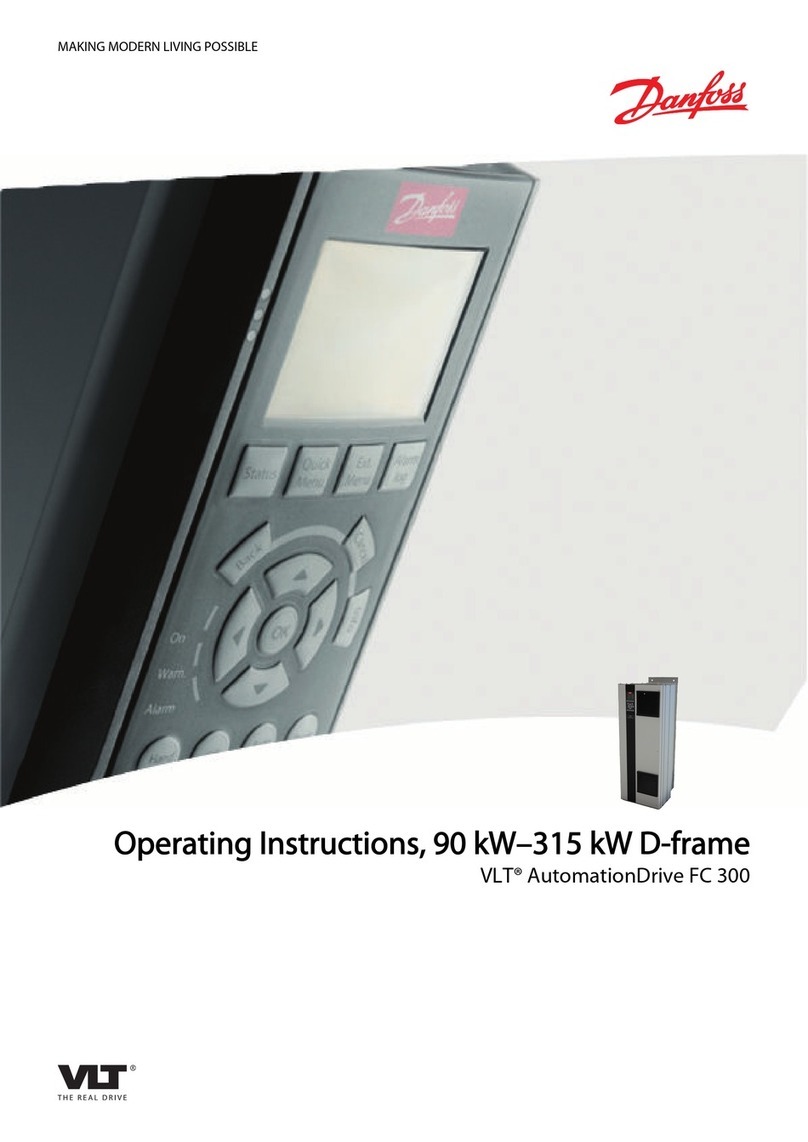
Danfoss
Danfoss VLT AutomationDrive FC 300 operating instructions
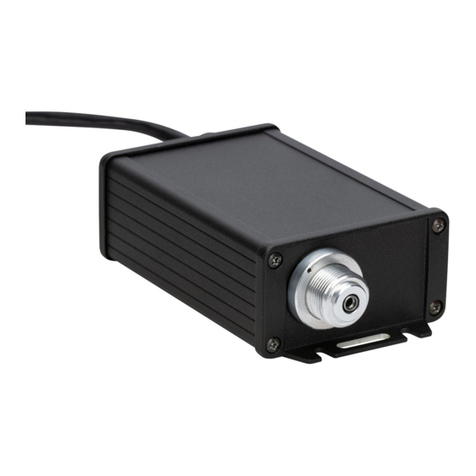
Dakota Digital
Dakota Digital ECD-200BT manual
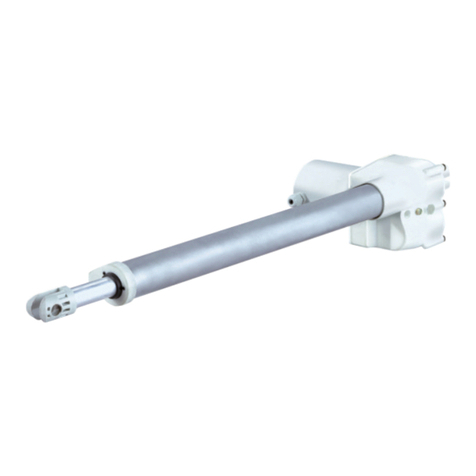
Phoenix Mecano
Phoenix Mecano DewertOkin MEGAMAT P installation instructions
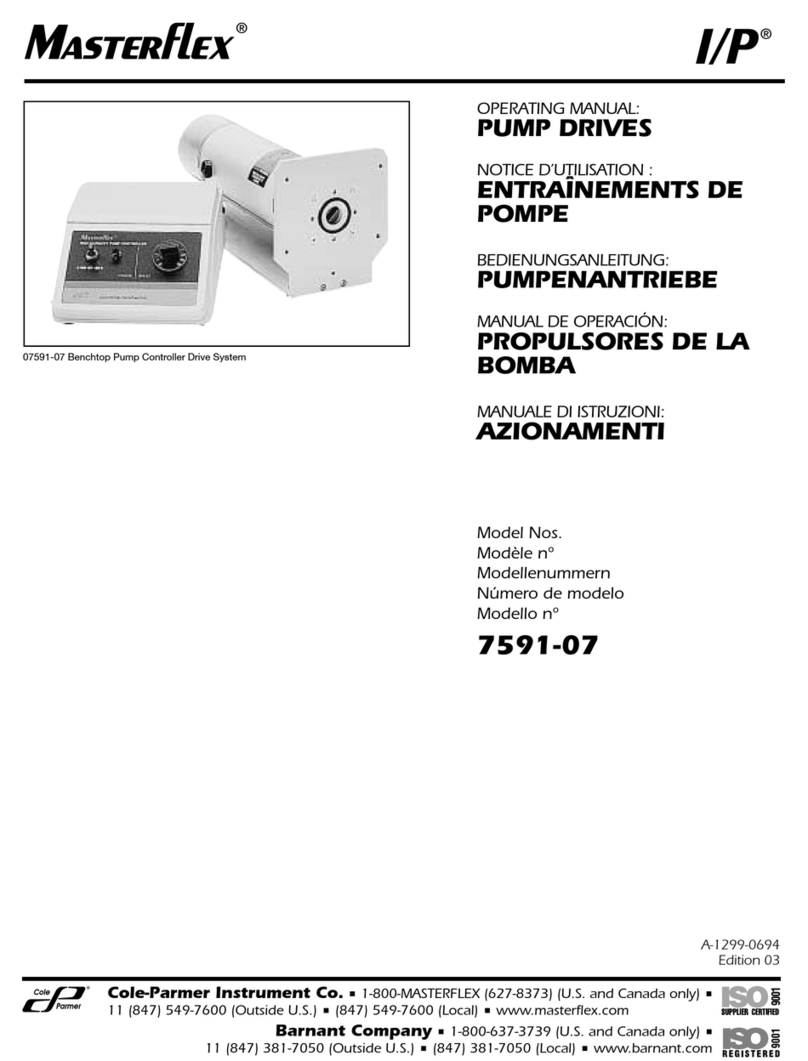
Cole Parmer
Cole Parmer MasterFlex I/P 7591-07 operating manual
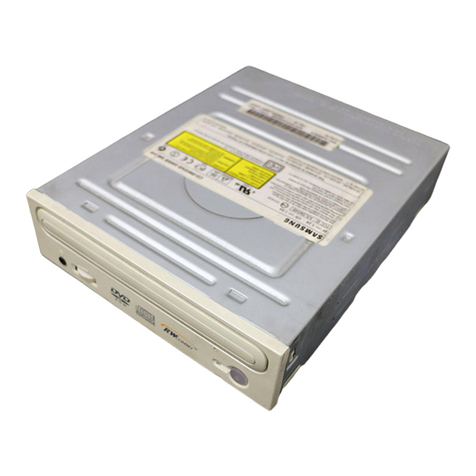
Samsung
Samsung SM-348 user guide

DoorHan
DoorHan SHAFT-50 Installation and operating manual
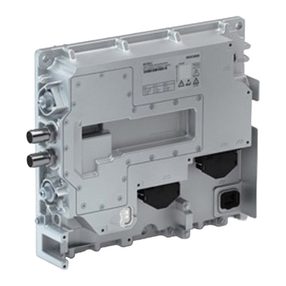
Lenze
Lenze MOBILE DCU Hardware manual