Ingersoll-Rand TRANE AFDJ Installation and operating instructions

SAFETY WARNING
Only qualified personnel should install and service the equipment. The installation, starting up, and servicing of heating, ventilating, and air-
conditioning equipment can be hazardous and requires specific knowledge and training. Improperly installed, adjusted or altered equipment
by an unqualified person could result in death or serious injury. When working on the equipment, observe all precautions in the literature and
on the tags, stickers, and labels that are attached to the equipment.
Remote-Mounted Medium Voltage Air-Cooled
Adaptive Frequency™ Drive
with Tracer AdaptiView™ Control
Installation, Operation,
and Maintenance
Models: AFDJ X39641166040
AFDJ-SVU01D-EN
March 2015

© 2015 Trane All rights reserved AFDJ-SVU01D-EN
Introduction
Readthismanualthoroughlybeforeoperatingorservicing
this unit.
Warnings, Cautions, and Notices
Safety advisories appear throughout this manual as
required.Yourpersonalsafetyandtheproperoperationof
this machine depend upon the strict observance of these
precautions.
Important Environmental Concerns
Scientific research has shown that certain man-made
chemicals can affect the earth’s naturally occurring
stratospheric ozone layer when released to the
atmosphere. In particular, several of the identified
chemicals that may affect the ozone layer are refrigerants
that contain Chlorine, Fluorine and Carbon (CFCs) and
those containing Hydrogen, Chlorine, Fluorine and
Carbon (HCFCs). Not all refrigerants containing these
compounds have the same potential impact to the
environment.Traneadvocatestheresponsiblehandlingof
all refrigerants-including industry replacements for CFCs
and HCFCs.
Important Responsible Refrigerant Practices
Trane believes that responsible refrigerant practices are
important to the environment, our customers, and the air
conditioning industry. All technicians who handle
refrigerants must be certified. The Federal Clean Air Act
(Section 608) sets forth the requirements for handling,
reclaiming, recovering and recycling of certain
refrigerants and the equipment that is used in these
service procedures. In addition, some states or
municipalities may have additional requirements that
must also be adhered to for responsible management of
refrigerants. Know the applicable laws and follow them.
Important:
•Before servicing, disconnect all power sources and
allow at least 40 minutes for capacitors to discharge.
•All electrical enclosures—unit or remote—are IP2X.
•Customers are responsible for all field wiring in
compliance with local, national, and/or international
codes.
The three types of advisories are defined as follows:
WARNING Indicates a potentially hazardous
situation which, if not avoided, could
result in death or serious injury.
CAUTIONsIndicates a potentially hazardous
situation which, if not avoided, could
result in minor or moderate injury. It
could also be used to alert against
unsafe practices.
NOTICE: Indicatesasituationthatcouldresultin
equipment or property-damage only
accidents.
WARNING
Proper Field Wiring and Grounding
Required!
Failure to follow code could result in death or serious
injury. All field wiring MUST be performed by qualified
personnel. Improperly installed and grounded field
wiring poses FIRE and ELECTROCUTION hazards. To
avoid these hazards, you MUST follow requirements for
field wiring installation and grounding as described in
NEC and your local/state electrical codes.
WARNING
Personal Protective Equipment (PPE)
Required!
Installing/servicing this unit could result in exposure to
electrical, mechanical and chemical hazards.
• Before installing/servicing this unit, technicians
MUST put on all PPE required for the work being
undertaken (Examples; cut resistant gloves/sleeves,
butyl gloves, safety glasses, hard hat/bump cap, fall
protection, electrical PPE and arc flash clothing).
ALWAYS refer to appropriate Material Safety Data
Sheets (MSDS)/Safety Data Sheets (SDS) and OSHA
guidelines for proper PPE.
• When working with or around hazardous chemicals,
ALWAYS refer to the appropriate MSDS/SDS and
OSHA/GHS (Global Harmonized System of
Classification and Labelling of Chemicals) guidelines
for information on allowable personal exposure
levels, proper respiratory protection and handling
instructions.
• If there is a risk of energized electrical contact, arc, or
flash, technicians MUST put on all PPE in accordance
with OSHA, NFPA 70E, or other country-specific
requirements for arc flash protection, PRIOR to
servicing the unit. NEVER PERFORM ANY
SWITCHING, DISCONNECTING, OR VOLTAGE
TESTING WITHOUT PROPER ELECTRICAL PPE AND
ARC FLASH CLOTHING. ENSURE ELECTRICAL
METERS AND EQUIPMENT ARE PROPERLY RATED
FOR INTENDED VOLTAGE.
Failure to follow instructions could result in death or
serious injury.

Introduction
AFDJ-SVU01D-EN 3
Copyright
Thisdocumentandtheinformationinitarethepropertyof
Trane, and may not be used or reproduced in whole or in
part without written permission. Trane reserves the right
torevisethispublicationatanytime,andtomakechanges
to its content without obligation to notify any person of
such revision or change.
Trademarks
All trademarks referenced in this document are the
trademarks of their respective owners.
Revision History
AFDJ-SVU01D-EN (31 Mar 2015)
• Revisedspecifications for conduitusedwithcustomer
wiring in “CE for MV Drives,” p. 7
•Updated“Model Number,” p. 15
WARNING
Refrigerant May Be Under Positive
Pressure!
Failure to recover refrigerant to relieve pressure or the
use of non-approved refrigerants, refrigerant
substitutes, or refrigerant additives could result in an
explosion which could result in death or serious injury
or equipment damage. System contains oil and
refrigerant and may be under positive pressure.
Recover refrigerant to relieve pressure before opening
the system. See unit nameplate for refrigerant type. Do
not use non-approved refrigerants, refrigerant
substitutes, or refrigerant additives.

4AFDJ-SVU01D-EN
Table of Contents
Introduction . . . . . . . . . . . . . . . . . . . . . . . . . . . . . 2
Warnings, Cautions, and Notices . . . . . . . . 2
Important Environmental Concerns . . . . . 2
Important Responsible Refrigerant Practices
. . . . . . . . . . . . . . . . . . . . . . . . . . . . . . . . . . . 2
Overview . . . . . . . . . . . . . . . . . . . . . . . . . . . . . . . 6
CE for MV Drives . . . . . . . . . . . . . . . . . . . . . . 7
Checks . . . . . . . . . . . . . . . . . . . . . . . . . . . . . . . 7
Motor Checks . . . . . . . . . . . . . . . . . . . . . . . 7
Controller Checks . . . . . . . . . . . . . . . . . . . . 7
AFDJ Checks . . . . . . . . . . . . . . . . . . . . . . . . 8
Rockwell Medium Voltage PowerFlex 7000
Drives . . . . . . . . . . . . . . . . . . . . . . . . . . . . . . . . 8
Typical Configurations . . . . . . . . . . . . . . . . 9
Cabinet . . . . . . . . . . . . . . . . . . . . . . . . . . . . . . . 9
Cabinet Energy Sources . . . . . . . . . . . . . . 9
Cabinet Design . . . . . . . . . . . . . . . . . . . . . . 9
Cabinet Voltage Levels . . . . . . . . . . . . . . . 9
PowerFlex 7000 Medium Voltage Cabinet 9
Control Voltage Power De-energization . . 10
Back-feed Sources of Hazardous Electrical En-
ergy . . . . . . . . . . . . . . . . . . . . . . . . . . . . . . . . 11
General Information . . . . . . . . . . . . . . . . . . . . 12
About This Manual . . . . . . . . . . . . . . . . . . . 12
Other Required Manuals . . . . . . . . . . . . . . . 12
Cabinet Servicing . . . . . . . . . . . . . . . . . . . . . 12
Service Information . . . . . . . . . . . . . . . . . . . 12
Parts Ordering Information . . . . . . . . . . . . 12
Scope of Installation and Commissioning Re-
sponsibilities . . . . . . . . . . . . . . . . . . . . . . . . . 13
About the AFDJ Drive . . . . . . . . . . . . . . . . . 14
Drive Identification . . . . . . . . . . . . . . . . . . . . 14
Model Number . . . . . . . . . . . . . . . . . . . . . . . . . 15
Trane Service Model Number . . . . . . . . . . 15
Model Number Digit Identification . . . . . 15
Cabinet . . . . . . . . . . . . . . . . . . . . . . . . . . . . . . . . 16
A-Frame and B-Frame Notes . . . . . . . . . . 18
Pre-Installation . . . . . . . . . . . . . . . . . . . . . . . . . 27
Receipt Inspection . . . . . . . . . . . . . . . . . . . . 27
Scope . . . . . . . . . . . . . . . . . . . . . . . . . . . . .27
Receiving . . . . . . . . . . . . . . . . . . . . . . . . . .27
Export Crating . . . . . . . . . . . . . . . . . . . . . . . .27
Accessories . . . . . . . . . . . . . . . . . . . . . . . . .28
Rigging . . . . . . . . . . . . . . . . . . . . . . . . . . . . . .29
General Handling Procedures for Medium
Voltage Drives . . . . . . . . . . . . . . . . . . . . . .29
Rigging Contractor . . . . . . . . . . . . . . . . . . .29
Overhead Lifting . . . . . . . . . . . . . . . . . . . . .29
Removal of Lifting Angles . . . . . . . . . . . . .30
Storage . . . . . . . . . . . . . . . . . . . . . . . . . . . . . .30
Planning . . . . . . . . . . . . . . . . . . . . . . . . . . .31
Neutral Resistor Assembly (A-Frame only) 31
Installation of Neutral Resistor Assembly 31
Re-installing a Common Mode Choke (CMC)
. . . . . . . . . . . . . . . . . . . . . . . . . . . . . . . . . . . . . .32
Safety . . . . . . . . . . . . . . . . . . . . . . . . . . . . .32
Background . . . . . . . . . . . . . . . . . . . . . . . . .32
Definitions . . . . . . . . . . . . . . . . . . . . . . . . . .32
Siting . . . . . . . . . . . . . . . . . . . . . . . . . . . . . .32
Removing CMC Cabinet Access Plates . .32
Removing CMC Cabinet Access Plates . .33
Preparing the CMC . . . . . . . . . . . . . . . . . . .33
Preparing the CMC Cabinet . . . . . . . . . . . .33
Installing the CMC . . . . . . . . . . . . . . . . . . .34
Wiring . . . . . . . . . . . . . . . . . . . . . . . . . . . . . . . . . .38
Input Power, Drive-to-Motor, and Control Wir-
ing . . . . . . . . . . . . . . . . . . . . . . . . . . . . . . . . . .38
Installing Input Power Wiring Standard Cabi-
net . . . . . . . . . . . . . . . . . . . . . . . . . . . . . . . . . .38
Torquing Electrical Power Connections . .39
Cabinet Wire Routing . . . . . . . . . . . . . . . . .39
Wire Routing . . . . . . . . . . . . . . . . . . . . . . . . . .39
Wire Sizing . . . . . . . . . . . . . . . . . . . . . . . . .39
Grounding the Cabinet . . . . . . . . . . . . . . .39
Detailed Field Wiring Points . . . . . . . . . . . . .43
Input Power and Interconnection Wiring .43
UC800 AFD Operation . . . . . . . . . . . . . . . . . . . .45
Adaptive Frequency Drive Control . . . . . . .45

Table of Contents
AFDJ-SVU01D-EN 5
Introduction . . . . . . . . . . . . . . . . . . . . . . . 45
Chiller and AFD Sequence of Operation 45
Compressor Pressure Coefficient . . . . . . 45
Surge Boundary . . . . . . . . . . . . . . . . . . . . 45
AFD Speed Control . . . . . . . . . . . . . . . . . . 46
Startup . . . . . . . . . . . . . . . . . . . . . . . . . . . . 46
Re-optimization . . . . . . . . . . . . . . . . . . . . 47
Surge Recovery . . . . . . . . . . . . . . . . . . . . 48
Surge Detection . . . . . . . . . . . . . . . . . . . . 48
UC800 Interface to Adaptive Frequency Drive
. . . . . . . . . . . . . . . . . . . . . . . . . . . . . . . . . . 49
Pre-Commissioning Start-Up . . . . . . . . . . . . 50
Trane AFDJ MV Drive . . . . . . . . . . . . . . . . . 50
Check List . . . . . . . . . . . . . . . . . . . . . . . . . 50
Commissioning . . . . . . . . . . . . . . . . . . . . . . 50
Start-up Commissioning Services . . . . . 50
Drive Commissioning . . . . . . . . . . . . . . . 51
Startup Test Log . . . . . . . . . . . . . . . . . . . . . . 52
Maintenance . . . . . . . . . . . . . . . . . . . . . . . . . . . 53
Preventive Maintenance Check List . . . . . 53
Operational Maintenance . . . . . . . . . . . . 53
Annual Maintenance . . . . . . . . . . . . . . . . 53
Chiller Operator Display Content . . . . . . . 54
Troubleshooting . . . . . . . . . . . . . . . . . . . . . . . . 55
Alarms . . . . . . . . . . . . . . . . . . . . . . . . . . . . . . 55
Troubleshooting . . . . . . . . . . . . . . . . . . . . . . 55
LED Usage . . . . . . . . . . . . . . . . . . . . . . . . . 56

6AFDJ-SVU01D-EN
Overview
All electrical circuits shall be treated as energized until all
lockout/tagout procedures are in place and the circuit has
been tested to verify that it is de-energized. The medium
voltage motor terminal box cover must not be removed if
powerispresent,orifthereisapossibilitythatpowermay
bepresent.Workingonenergizedmediumvoltagecircuits
isnotanapprovedpracticefornormalHVACmaintenance
or service.
Important:
•Before servicing, disconnect all power sources and
allow at least 40 minutes for capacitors to discharge.
•All electrical enclosures-unit or remote-are IP2X.
WARNING
Hazardous Service Procedures!
Failure to follow all precautions in this manual and on
the tags, stickers, and labels could result in death or
serious injury.
Technicians, in order to protect themselves from
potential electrical, mechanical, and chemical hazards,
MUST follow precautions in this manual and on the
tags, stickers, and labels, as well as the following
instructions: Unless specified otherwise, disconnect all
electrical power including remote disconnect and
discharge all energy storing devices such as capacitors
before servicing. Follow proper lockout/tagout
procedures to ensure the power can not be
inadvertently energized. When necessary to work with
live electrical components, have a qualified licensed
electrician or other individual who has been trained in
handling live electrical components perform these
tasks.
WARNING
Hazardous Voltage!
Failure to disconnect power before servicing could
result in death or serious injury. Disconnect all electric
power, including remote disconnects before servicing.
Follow proper lockout/tagout procedures to ensure the
power can not be inadvertently energized.
WARNING
Hazardous Voltage w/Capacitors!
Failure to disconnect power and discharge capacitors
before servicing could result in death or serious injury.
Disconnect all electric power, including remote
disconnects and discharge all motor start/run
capacitors before servicing. Follow proper lockout/
tagout procedures to ensure the power cannot be
inadvertently energized. For variable frequency drives
or other energy storing components provided by Trane
or others, refer to the appropriate manufacturer’s
literature for allowable waiting periods for discharge of
capacitors. Verify with an appropriate voltmeter that all
capacitors have discharged. If this equipment is
interlocked with other equipment, 115 volt AC may be
present in the cabinet even though the main power is
disconnected. If this is the case, these interlock signals
should be deactivated before any work is performed on
this equipment. Suitable warning tags or disconnects
should be added to these circuits and all circuits should
be tested before attempting to energize or service the
controller.
For additional information regarding the safe discharge
of capacitors, see PROD-SVB06*-EN
WARNING
Capacitors Must be Allowed to
Discharge!
Failure to disconnect power and discharge capacitors
before servicing could result in death or serious injury.
Each time power is removed, allow at least 40 minutes
for DC units to discharge after power is disconnected
before servicing. Use extreme caution when applying
power. Equipment terminals and other internal parts of
the controller are at line voltage when ac power is
connected to the controller. All ungrounded conductors
of the ac power line must be disconnected from the
controller before it is safe to touch any internal parts of
this equipment.

Overview
AFDJ-SVU01D-EN 7
CE for MV Drives
Important:
•All Trane-supplied remote drives used in conjunction
withCVHHorCDHHTranechillerswillbeCE-compliant
perEUdirectivesandIECstandardstowhichtheCVHH
and CDHH chillers also comply. All Trane-supplied
remotestartersanddrivesmustbeusedwith CVHHor
CDHH Trane chillers to ensure CE compliance
•For remote drives, basic details are provided on drive
nameplate. Please refer to the chiller unit nameplate
locatedonthechiller-mountedcontrolpanelfordetails
on wire sizing (minimum current ampacity) and
overcurrent protection sizing upstream of unit
(maximum overcurrent protection).
•Always refer to as-built schematic wiring diagram and
the chiller Installation, Operation, and Maintenance
manual located inside the chiller-mounted control
panel(regardlessof unitorremote-mountedstarteror
drive) for details on wiring, safety, installation, and
warnings.
•Customers are responsible for all field wiring with
respect to EMC and EMI interference. Customers are
responsible for mitigating the risks associated with
EMC and EMI interference that can occur as a result of
customer-provided field wiring as dictated by
international, national, and local codes. This also
impliesthatforremote-mounteddrives,customersare
responsible for the entire field wiring into the drive as
well as between the drive and the chiller/compressor
terminals with respect to EMC and EMI interference. It
also implies that customers are responsible for
incoming power wiring to the drive with respect to
EMC and EMI interference.
All customer wiring, including power wiring to drives,
must be separated: 24–27 Vdc, 110–120 Vac, 460 V, and
2300–6600 Vac each must be in separate conduit runs.
For remote drives interfacing with Trane CVHH and CDHH
chillers, all wiring must be run in conduit. Any Ethernet
cables being used by the customer to interface with the
Trane chiller must be shielded Ethernet cabling.
The customer is required to provide an overcurrent
protectivedeviceupstreamofalldrivesinaccordancewith
IECstandardsand/oranyapplicablenationalandlocaland
codes.
Service personnel must use proper PPE for servicing and
must also use proper lockout/tagout procedures during
servicing: lock the drive disconnect handle before
servicing to prevent accidental pulling of disconnect
handle at the drive panel.
Inaddition,servicepersonnelshoulddisconnectthemain
supply disconnectingdevice upstream of the drive before
performing any service on any part of the chiller.
Checks
Motor Checks
1. Check the motor for proper horsepower and voltage
ratings. Verify that the chiller rated load amps do not
exceed the nameplate rating of the controller.
2. Checkthatthemotorterminalsarecorrectlyconnected
to the controller’s power terminals for the proper
voltage and motor rotation.
3. Use an ohmmeter to check for any short circuits
between the motor frame and the motor power leads.
If a short circuit exists, it must be corrected before
proceeding.
Controller Checks
1. Check thatlocal,stateandnationalelectriccodeshave
been observed for the installation and wiring of this
equipment.
2. Check thatall externalpowerwiringhasbeenproperly
routed through the cabinet.
3. Check all input power and output power connections
for tightness.
4. Check the chassis ground and other connections for
tightness.
5. Check all external control connections (this includes
the operator station connections) for tightness.
6. Check toassure incomingpowertothedriveisphased
A, B, C.
WARNING
Lockout/Tagout Before Removing Touch-
Safe Covers!
Failure to follow instructions regarding touch-safe
covers could result in death or serious injury. Touch-safe
covers inside panels are there for protection and may
be removed if necessary for service only and only after
disconnection of main power supply. Before removing
any touch-safe cover, ensure that there is no line power.
Removal of touch-safe covers would be at the
customer/service personnel’s own risk. After any
service is completed, if the touch-safe covers have been
removed, the touch-safe covers must be replaced to
ensure safety and protection.
NOTICE:
Do Not Megohm Test!
Using a megger to perform continuity checks in the
drive equipment could result in damage to the
controller circuitry.
NOTICE:
Disconnect Motor Leads!
Failure to disconnect all motor leads at the AFD prior to
megging the motor could result in equipment damage.

Overview
8AFDJ-SVU01D-EN
AFDJ Checks
Important:
•Before servicing, disconnect all power sources and
allow at least 40 minutes for capacitors to discharge.
•All electrical enclosures-unit or remote-are IP2X.
Safety Precautions
1. This equipment must be adjusted and serviced by
qualified personnel familiar with the construction and
operation of the equipment and the hazards involved.
2. Be sure the input disconnect is in the correct position,
either “on” or “off” depending on the work to be
performed.
3. Check the status of the drive shutdown interlocks, if
used.Theseinterlockscanbelimit switches,guards or
safetyswitchesinstalledaroundthedrivenmachineor
the system interface controller.
4. Check to seethatthe AFDJis properlygroundtoearth.
Refer to “Grounding the Cabinet,” p. 39 in “Input
Power, Drive-to-Motor, and Control Wiring,” p. 38.
Important:
•Before servicing, disconnect all power sources and
allow at least 40 minutes for capacitors to discharge.
•All electrical enclosures-unit or remote-are IP2X.
•Specific safety training for medium-voltage (MV)
equipment, specialized tools and instruments for
working on MV products, and enhanced personal
protective equipment (PPE) that is designed to
mitigate the hazards of arc flash injuries are required
forworkingontheproductsdescribedinthisliterature.
Only medium-voltage trained, certified engineers are
allowed to work on MV products.
Please refer to Rockwell’s MV product manual for details
on recommendations to be followed for different
components.
Rockwell Medium Voltage
PowerFlex 7000 Drives
NOTICE:
Perform Visual Inspection!
The conditions noted below could cause equipment
damage. Before powering up this drive for the first time
conduct a visual inspection for the following:
• Shipping damage.
• Signs of moisture.
• Signs of debris or dust from storage.
• Signs of corrosion on components and/or enclosure.
Do not power up equipment if you have concerns
regarding equipment condition. Upon initial power up,
remain in the area for the first two hours of operation
and observe the chiller and drive for any abnormalities.
Contact CenTraVac™ Technical Support for assistance if
needed.
WARNING
Hazardous Voltage!
Failure to close all enclosure doors and properly secure
with fasteners before operating equipment could result
in death or serious injury due to hazardous voltage.
WARNING
Bypassed Electrical Interlocks!
Failure to follow instructions below could result in
death, serious injury or equipment damage. The
electrical interlocks provide machine and personal
protection. If deactivated or bypassed for servicing, use
extreme caution when performing the start-up. Return
all interlocks to operation when the start-up is
completed.
WARNING
Proper Field Wiring and Grounding
Required!
Failure to follow code could result in death or serious
injury. All field wiring MUST be performed by qualified
personnel. Improperly installed and grounded field
wiring poses FIRE and ELECTROCUTION hazards. To
avoid these hazards, you MUST follow requirements for
field wiring installation and grounding as described in
NEC and your local/state electrical codes.
WARNING
Insert Control Boards or Fuses!
Do not remove or insert control boards or fuses while
input power is connected to the controller because
doing so could result in death, serious injury, and
equipment damage.
WARNING
Read and Understand All Safety
Procedures in this Manual!
Failure to read and understand the following
information could result in death or serious injury. The
information contained in this section of the manual is
very important. It describes safety procedures that
MUST be followed. For your safety you MUST read and
understand them. If you have any questions, please
contact your local Trane/Rockwell office.

Overview
AFDJ-SVU01D-EN 9
Typical Configurations
The Trane-supplied Medium Voltage PowerFlex®7000
drives is available in two air-cooled versions, called
Frames: 1) 7000 A-Frame, and 2) 7000 B-Frame. Each
Frame is specified based on the physical size and horse
power (HP) or KW rating of the equipment. Generally, A-
Frame is thesmallest frame air-cooleddrive, andB-Frame
isthelargestair-cooleddrive.ThefollowingRockwellSafe
Electric Work Practices (SEWP) applies to typical
configurationsforPowerFlex7000drivesregardlessofthe
frame size1.
Cabinet
Cabinet Energy Sources
A typical PowerFlex 7000 drive has a main medium
voltage power supply and two other secondary control
voltages power supply. In addition, a customer may
specify a configuration with additional energy sources
such as a UPS back-up power supply.
• Your responsibility is to look for all sources of
hazardousenergyto confirm thedrive youwillservice
or maintain matches the drawing.
• Youmustidentifyeachsourceofpowersuppliedtothe
cabinetandimplementstepstocontroltheeachpower
source prior to performing your work.
• Other safety measures may have to be implemented
for work such as removing cabinet tray covers/power
cages to check the condition of “snubber capacitors”
prior to performing the work.
Cabinet Design
Mediumvoltagecabinetdoorsarekeyinterlockcontrolled
and designed to open in sequence.
• Cabinet doors must only be opened in the engineered
sequence and must be treated as if they are live until
de-energization is verified.
• Controlvoltagecabinetdoorareblackin colorandcan
be opened without a key. The inside of the control
voltage cabinet must be treated as if they are live until
de-energization is verified.
The key interlocking scheme is a cornerstone of the safety
devicesbuiltintoaproduct.Youarenotauthorizedtowork
on, and must refuse to work on any installed MV product
where the key interlocks are missing, damaged or
compromised in any way. Keys can never be duplicated
withouttheowneroftheproductsigningawaiver.Service
personnel should never be in possession of their own
duplicate keys.
Matchthepersonalprotectiveequipment(PPE)youuseto
thevoltagelevelandthehazardcategorytomakesurethat
you have the correct protection for the specific work you
are doing. The PPE must be adequate to protect against
shock as well as arc flash injury.
Cabinet Voltage Levels
For the purpose of medium voltage technical work,
mediumvoltageisdefinedas1,000–15,000volts.Rockwell
Automation medium voltage products presently range
from 2,300–7,200 volts. The control voltage is defined as
600 volts or less. It is typically 480 or 120 volts. Some
cabinets also have 5–24 Vdc power supply hooked up to
them for logic circuit boards or indicator meters.
The voltages upstream to the Rockwell medium voltage
product can be higher than 7,200 volts. You are not
authorized/trained or equipped to work on these systems.
The customers’ staff that are trained and authorized to de-
energize the equipment must be used for this work.
PowerFlex 7000 Medium Voltage Cabinet
Medium Voltage Power De-energization
Drive, Disconnect, or Breaker
• Put on the Personal Protective Equipment (PPE)
necessary to protect from the shock and arc flash
hazards from both medium and control voltages.
• Disconnect the MV input power source to the
PowerFlex 7000 drive cabinets by placing the drive
control; disconnect handle or circuit breaker switch in
the “off” position.
– Apply the Lockout-Tagout device(s) and lock(s).
– The drive cabinet doors are locked and the input
power control box must remain closed when de-
energizing the MV power source.
•Placingthecontrol,handleorswitchin the“Off”
position should de-energized the power only
down stream from the cabinet.
•Medium voltage power remains energized
upstream of the control, handle or switch.
• Use a properly rated meter to verify the medium
voltage power on the downstream side of the drive/
disconnect/breaker is de-energized.
– Follow meter test procedures to confirm the meter
is reading accurately prior to verifying de-
energization.
1Rockwell also manufactures a C-Frame, which is liquid-cooled, but which is larger than our applications.

Overview
10 AFDJ-SVU01D-EN
Important:
•Before servicing, disconnect all power sources and
allow at least 40 minutes for capacitors to discharge.
•All electrical enclosures-unit or remote-are IP2X.
• Remove the key from the de-energized drive/
disconnect/breaker and use the key control procedure
to open the MV cabinet access door(s).
• Use a medium voltage rated Potential Indicator tool
(“hot stick”) to confirm the medium voltage power
inside the PowerFlex 7000 cabinet is de-energized.
– Follow Potential Indicator tool test procedures to
confirm the tool is working properly prior to
verifying de-energization.
• The PPE for medium voltage safety can only be
removed once the MV power de-energization is
verifiedandconfirmed.ThePPEforcontrolvoltagecan
only be removed once the control voltage de-
energization is verified.
Control Voltage Power De-
energization
• Wear the PPE that is necessary to protect from the
shock and arc flash hazards.
• Disconnect the control voltage. Apply the lockout
lock(s) and/or the tagout device(s).
• Identify the PowerFlex 7000 cabinet control power
supply.
– The source may be a disconnect switch on an
electric circuit, an input contactor mounted on the
side of the cabinet or similar power disconnect
device.
– Identify other sources of control voltage by
reviewing the system drawings and looking at the
equipment for secondary power sources.
• Some cabinets are equipped with a UPS battery
backup 120 volt AC power supply for control voltage.
– The control voltage from the UPS battery backup
will not be de-energized by disconnecting the
control voltage disconnect switch. It is designed to
energizeoncetheprimary control voltagesourceis
de-energized.
– Use the PPE necessary to protect against UPS
power.
• Useaproperlyratedmetertoverifythecontrolvoltage
power on the downstream side of the disconnect
device is de-energized.
• Place the control voltage from the Rockwell
Automation installed circuit breaker on the panel
inside the control voltage supply cabinet in the “off”
position.
– The circuit breakers are normally located at the
bottom of the circuit breaker terminal block strip.
– Lockout-Tagout the switch. If a lockout is not
feasible then tagout the circuit breaker to warn
other people working in the same area not to turn
the switch back on as it will re-energize the control
WARNING
Hazardous Voltage w/Capacitors!
Failure to disconnect power and discharge capacitors
before servicing could result in death or serious injury.
Disconnect all electric power, including remote
disconnects and discharge all motor start/run
capacitors before servicing. Follow proper lockout/
tagout procedures to ensure the power cannot be
inadvertently energized. For variable frequency drives
or other energy storing components provided by Trane
or others, refer to the appropriate manufacturer’s
literature for allowable waiting periods for discharge of
capacitors. Verify with an appropriate voltmeter that all
capacitors have discharged. If this equipment is
interlocked with other equipment, 115 volt AC may be
present in the cabinet even though the main power is
disconnected. If this is the case, these interlock signals
should be deactivated before any work is performed on
this equipment. Suitable warning tags or disconnects
should be added to these circuits and all circuits should
be tested before attempting to energize or service the
controller.
For additional information regarding the safe discharge
of capacitors, see PROD-SVB06*-EN
WARNING
Capacitors Must be Allowed to
Discharge!
Failure to disconnect power and discharge capacitors
before servicing could result in death or serious injury.
Each time power is removed, allow at least 40 minutes
for DC units to discharge after power is disconnected
before servicing. Use extreme caution when applying
power. Equipment terminals and other internal parts of
the controller are at line voltage when ac power is
connected to the controller. All ungrounded conductors
of the ac power line must be disconnected from the
controller before it is safe to touch any internal parts of
this equipment.
WARNING
Read and Understand All Safety
Procedures in this Manual!
Failure to read and understand the following
information could result in death or serious injury. The
information contained in this section of the manual is
very important. It describes safety procedures that
MUST be followed. For your safety you MUST read and
understand them. If you have any questions, please
contact your local Trane/Rockwell office.

Overview
AFDJ-SVU01D-EN 11
circuit and may cause harm or injury to the person
working on the equipment.
• If the primary and secondary control voltage sources
are not de-energized during the work, you must
continue to use your PPE while performing the work.
Back-feed Sources of Hazardous
Electrical Energy
• Back-feed power caused by a fan that rotates from
ambient wind blowing on it, electric motor(s) rotating
when equipment manually moves it and other
potential sources of back-feed power may be
downstream from the MV cabinet.
– Identify sources of potential back-feed power
downstream from the MV cabinet.
– Prevent back-feed power by locking, blocking or by
other measures to positively control back-feed
power sources.
• Verify these sources are positively controlled to
prevent back-feed.
WARNING
Read and Understand All Safety
Procedures in This Manual!
Failure to read and understand the following
information could result in death or serious injury. The
information contained in this section of the manual is
very important. It describes safety procedures that
MUST be followed. For your safety you MUST read and
understand them. If you have any questions, please
contact your local Trane/Rockwell office.

12 AFDJ-SVU01D-EN
General Information
About This Manual
This manual is intended for use by experienced service
personnel, qualified electrical personnel, Trane service
personnel, and Rockwell global technical service
personnel who are familiar with the features described.
The instructions in this manual outline the procedures for
operating the Adaptive Frequency Drive. Operation and
maintenance of the controls are also explained in this
manual.
Other Required Manuals
Rockwell provides drive-size order-specific literature that
ships with the drive from the Rockwell factory.
Cabinet Servicing
For information regarding the servicing of drive
components, please refer to the appropriate Rockwell
literature that ships with the drive.
Service Information
Thisequipmentshouldbeinstalled,adjustedandserviced
by qualified electrical maintenance personnel who are
familiar with the construction and operation of the
equipment and the hazards involved, as defined in the
National Electrical Code. Trane assumes no liability for
installation or service procedures performed by
unqualified personnel.
Parts Ordering Information
Refer to themodel number printed on the Trane Adaptive
Frequency Drive nameplate when ordering replacement
partsorserviceforthedrive.Whenorderingparts,contact
the local Trane Parts Office in your area. For service,
contact a qualified service organization.

General Information
AFDJ-SVU01D-EN 13
Scope of Installation and
Commissioning Responsibilities
Table 1. Scope of installation and commissioning responsibilities
Item Others Trane Rockwell See Figures/Pages
Chiller (provided by Trane) X
Inspect chiller for shipping damage X Assist if any questions
Drive (provided by Trane from Rockwell) Direct ship from
Rockwell
Inspect drive for shipping damage X
Provide drive foundation X
Uncrate/package drive and inspect X
Rig drive into place X
Provide power wires and installation to drive and
terminate: X
• Line 3-phase voltage to drive; be sure to do this
before fan shroud installation (A-Frame only)
• Fan 3-phase voltage to drive (B-Frame)
• Drive to motor power wiring
• Control power drive to chiller; interconnect (LV)
Install fan shroud boxes X
Install resistor box X
Provide adequate ventilation for heat rejection of drive X
Precommision chiller; refer to chiller IOM forms X
Fill out drive precommision check sheet Assist Trane X
Precommision drive X Assist
Apply 120 V Assist X
Apply power (3-phase) Assist X
Check/Configure drive controls setpoints with Trane
Service Tool XAssist
3-phase power (DO NOT APPLY) Present at start-up
Drive/chiller start-up Assist X
Annual inspections X X As specified

General Information
14 AFDJ-SVU01D-EN
About the AFDJ Drive
TheAFDJTraneAdaptiveFrequencyDrive isanair-cooled
drive which utilizes Pulse Width Modulation (PWM) high
switching frequency Symmetric Gate Commutated
Thyristors (SGCT). Both the inverter and the rectifier use
SGCTs, and both operate at optimal switching frequency
to minimize the switching losses. These SGCTs are an
integration of the power semiconductor and the gate
driver electronics. The close proximity of the gate driver
and power semiconductor provides a superior switching
patternthatpreventsthe drivefromproducinghighlevels
of line current harmonics and minimizes snubber
requirements. The Total Harmonic Distortion (THD) of the
inputcurrentiswithinIEEE-519harmonicguidelines.Both
current and voltage waveforms are near sinusoidal,
reducing stress on the motor windings.
A combination of two distinct operating modes make up
the control within the chiller’s UC800 control: first, by
controlling the inlet guide vanes and second, by
modulatingtheimpellerspeedfrom38–60hertz.Thedrive
controls the speed in response to the UC800 compressor
control signal.
The CenTraVac control panel has full control of unit
operation, including the start and stop functions. If a fault
condition is encountered, or an alarm on the drive, the
Tracer AdaptiView display will indicate “alarm” and an
“Alarm message”.
Other Features
• Totally isolated low voltage and medium voltage
compartments.
• Mechanical and electrical interlocks between the drive
and input disconnecting means.
• Double offset ventilation pattern on the drive doors to
ensure operator safety.
• InputVoltageTolerance:±10%ofNominalLine Voltage
• Input Frequency: 50/60 Hz, ±10%
• OutputVoltageRating:0–2300,0–3300,0–4160,0–6600
• Input Protection: Metal Oxide Varistors
• Control Method: Sensorless Direct Vector (Full Vector
Control Optional)
• Ambient Temperature: 32°F–104°F (0°C– 40°C)
• Cooling: Forced Air
• Relative Humidity: 95% Non-condensing
• Altitude: 3300 feet (1000 m) above sea level without
derating.
Drive Identification
ThedrivehasaTranemodelnumberandaRockwellseries
number. Both these are extremely important when
identifying the drive for service or parts. Refer to “Model
Number,” p. 15 for more information about the Trane
model number.
The Rockwell series number is shown on the Rockwell
drive nameplate (see Figure 1), which is located on the
outside of the drive enclosure.This series number should
be available for reference in any correspondence with
Trane and/or Rockwell. The chiller series number and
chiller sales order number should also be available for
reference.
Figure 1. Example: MV Rockwell drive nameplate
Note: This 700XXXX-XXX-XX number identifies the drive. Always
have this number ready when service is required.
1

AFDJ-SVU01D-EN 15
Model Number
Trane Service Model
Number
Anexampleof atypicalchillerstarter
model number is:
AFDJ0035HA0B00CD
Model Number Digit
Identification
Model number digits are selected
and assigned in accordance with the
following definitions using the
model number example shown
above:
Digit 1, 2, 3 — CenTraVac
Starter
AFD= Adaptive Frequency Drive
Digit 4— Development
Sequence
J = Medium Voltage Air-Cooled
Digit 5, 6, 7, 8 — Starter Size
Use Rated Load Amps (RLA) value
Digit 9 — Unit Voltage
K = 2300V-60Hz-3Ph
L = 2400V-60Hz-3Ph
N = 4160V-60Hz-3Ph
P = 3300V-60Hz-3Ph
X = 6600V-60Hz-3Ph
V = 3300V-50Hz-3 Ph
W= 6000V-50Hz-3Ph
Z = 6600V-50Hz-3 Ph
S=Special
Digit 10, 11 — Design Sequence
A0 = First Design
Digit 12 — Starter Type
B = Remote Mounted
Digit 13 — Agency Listing
0 = UL and CUL Listed
(Standard on All Units)
1=CE
Digit 14 — Special Options
0=None
S = Special Options
Digit 15 — VFD Frame Size
(SSRL)
A=40
B=50
C=60
D=61
E=70
F=80
G=81
H=90
J=93
K=100
L=105
M= 120
N=140
P=160
R=185
T=215
U = 250
V = 285
W = 325
X = 375
Z=53
Digit 16 — Display
0=None
D=Display

16 AFDJ-SVU01D-EN
Cabinet
The cabinet has a NEMA 1 enclosure rating.
Environmental Conditions
Important: Location of the AFDJ drive is important if
proper performance and operating life is to
be expected. Therefore, unless designated
for special environments, the controller
should be installed in an area where the
following conditions exist.
• VerifythattheNEMA 1enclosurecanbekeptcleanand
dry.
• The area chosen should allow the space required for
proper air flow. Refer to Table 2, p. 16 and Table 3,
p. 17. Ensure the equipment room addresses the heat
rejections requirements.
• Be sure the enclosure is installed in a non-corrosive
location that is away from oil, coolants, or other
airborne contaminants.
• Verify and maintain design hertz and voltage inputs.
Table 2. A-Frame weights(a) and heat rejection
Subframe Line Voltage VFD
Amps hp kW
Max. Heat Rejection Weight
Btu/h kW lb kg
94 3300 V - 50/60 Hz 81 500 373 68000 19.9 6500 2948
94 3300 V - 50/60 Hz 93 560 418 72000 21.1 6500 2948
94 3300 V - 50/60 Hz 105 600 448 76000 22.3 6500 2948
94 3300 V - 50/60 Hz 120 750 560 94000 27.5 6500 2948
94 3300 V - 50/60 Hz 140 800 597 101000 29.6 6500 2948
94 4160 V - 60 Hz 61 450 336 74000 21.7 6500 2948
94 4160 V - 60 Hz 70 500 373 76000 22.3 6500 2948
94 4160 V - 60 Hz 81 600 448 80000 23.4 6500 2948
94 4160 V - 60 Hz 93 700 522 84000 24.6 6500 2948
94 4160 V - 60 Hz 105 800 597 87000 25.5 6500 2948
94 4160 V - 60 Hz 120 900 671 110000 32.2 6500 2948
94 4160 V - 60 Hz 140 1000 746 116000 34.0 6500 2948
110 6600 V - 50/60 Hz 40 500 373 87000 25.5 7500 3402
110 6600 V - 50/60 Hz 53 600 448 92000 27.0 7500 3402
110 6600 V - 50/60 Hz 61 750 560 98000 28.7 7500 3402
110 6600 V - 50/60 Hz 70 900 671 104000 30.5 7500 3402
110 6600 V - 50/60 Hz 81 1000 746 110000 32.2 7500 3402
110 6600 V - 50/60 Hz 93 1200 895 116000 34.0 7500 3402
(a) Weights do not include 500 lb (226.8 kg) maximum shipping skid.

Cabinet
AFDJ-SVU01D-EN 17
Table 3. B-Frame weights(a) and heat rejection
Subframe Line Voltage VFD
Amps hp kW
Max. Heat Rejection Weight
Btu/h kW lb kg
166 2300/2400 V - 60 Hz 160 700 522 78000 22.9 11770 5339
174 2300/2400 V - 60 Hz 185 800 597 83000 24.3 11270 5112
174 2300/2400 V - 60 Hz 215 900 671 90000 26.4 11270 5112
174 2300/2400 V - 60 Hz 250 1000 746 108000 31.7 11270 5112
174 2300/2400 V - 60 Hz 285 1250 933 115000 33.7 11270 5112
174 2300/2400 V - 60 Hz 325 1500 1119 122300 35.8 11270 5112
174 2300/2400 V - 60 Hz 375 1750 1306 133000 39.0 11270 5112
182 3300 V - 50/60 Hz 160 1000 746 104000 30.5 14120 6405
182 3300 V - 50/60 Hz 185 1100 821 110000 32.2 14120 6405
182 3300 V - 50/60 Hz 215 1250 933 123000 36.0 14120 6405
182 3300 V - 50/60 Hz 250 1500 1119 144000 42.2 14120 6405
182 4160 V - 60 Hz 160 1250 933 110000 32.2 14120 6405
182 4160 V - 60 Hz 185 1450 1082 117000 34.3 14120 6405
182 4160 V - 60 Hz 215 1500 1119 126000 36.9 14120 6405
182 4160 V - 60 Hz 250 2000 1492 164000 48.1 14120 6405
190 6600 V - 50/60 Hz 105 1250 933 126000 36.9 12270 5566
190 6600 V - 50/60 Hz 120 1500 1119 138000 40.4 12270 5566
197 6600 V - 50/60 Hz 140 1750 1306 151000 44.3 18070 8196
197 6600 V - 50/60 Hz 160 2000 1492 160000 46.9 18070 8196
197 6600 V - 50/60 Hz 185 2250 1679 175000 51.3 18070 8196
197 6600 V - 50/60 Hz 215 2750 2052 193000 56.6 18070 8196
205 6600 V - 50/60 Hz 250 3000 2238 241000 70.6 18070 8196
205 6600 V - 50/60 Hz 285 3600 2686 266000 78.0 18070 8196
(a) Weights do not include 500 lb (226.8 kg) maximum shipping skid.

Cabinet
18 AFDJ-SVU01D-EN
A-Frame and B-Frame Notes
General Notes
Note: Refer to Figure 3, p. 19 through Figure 12, p. 25.
1. Connections are spaced horizontally with dimension/
location shown in the front view.
2. NEMA 1 enclosure.
3. Maximumremotedistancebetweendriveandchilleris
150 ft (45.72 m).
Cable Notes
1. Top entry conduit openings standard.
2. Field-configurable for bottom entry line power.
3. Allcableconnectionsareboltedtype;lugsprovidedby
others.
4. Cable space designed for non-shielded cable or
shielded cable with prefabricated stress cones.
5. Maximum line shielded cable sizeis 1/0 MCM,oneper
phase for top entry; or 1/0 MCM, one per phase for
bottom entry. For AWG/MCM equivalents in mm2,
refer to Table 7, p. 38.
Maximum load shielded cable size is 500 MCM, two
perphasefortopentry;or500 MCM,twoperphasefor
bottom entry. For AWG/MCM equivalents in mm2,
refer to Table 7, p. 38.
6. Maximumlinenon-shieldedcablesizeis1/0 MCM,one
perphasefor topentry;or1/0 MCM, oneperphasefor
bottom entry. For AWG/MCM equivalents in mm2,
refer to Table 7, p. 38.
Maximum load non-shielded cable size is 500 MCM,
two per phase for top entry; or 500 MCM, two per
phase for bottom entry. For AWG/MCM equivalents in
mm2, refer to Table 7, p. 38.
Shipping Note
• Mounted on a (500 lb [226.8 kg] max) wooden skid
with provisions for a fork truck. Lifting means also
supplied on top.
Table 4. A-Frame: Dimensions (see Figure 2, p. 18 through Figure 6, p. 21)
Subframe A B C D E F G H J K L M N
94 in. 94.49 33.07 11.35 16.35 21.35 14.63 19.13 23.63 14.29 27.38 21.57 44.92 35.42
mm 2400 840 288 415 542 372 486 600 363 695 548 1141 900
110 in. 110.24 44.88 15.28 20.28 25.28 18.56 23.06 27.56 18.22 39.20 25.50 56.74 47.24
mm 2800 1140 388 515 642 471 586 700 463 996 648 1441 1200
Figure 2. A-Frame: Top view, in. (mm)
3.70 (94)
4.10 (104)
(4.00 X 4.00
[102 X 102])
(4.00 X 4.00
[102 X 102])
26.94
(684)
34.17
(868)
39.38
(1000)
40.73
(1035)
(3.94 X 4.73
[100 X 120]) 4.92
(125)
(3.94 X 4.73
[100 X 120])
24.83
(631)
34.10
(866)

Cabinet
AFDJ-SVU01D-EN 19
Figure 3. A-Frame: Front view, in. (mm)
5.50 (140)
83.50
(2121)
86.00
(2184)
8.00 (203)
19.00 (483)
26.00 (660)
5.00 (127)
112.11
(2848)
91.25
(2318)
54.50
(1384)
47.00
(1194)
31.00
(787)
2.67
(68)
International
Symbols Label
(for CE
applications)
International
Symbols Label
(for CE
applications)
(for non-CE
applications);
Figure 4. A-Frame: Bottom view, in. (mm)
(4.00 X 4.00
[102 X 102])
3.79 (96)
34.72
(882)
25.12
(638)
3.00 (76)
6.64
(169)
10.68
(271)
(3.50 X 3.12
[89 X 79])
10.83
(275)
17.80
(452)
(6.87
[175])
28.05 (712)
35.48
(901)
5.90 (150)
(6.50
[165])
18.50
(470)
(4.00 X 4.00
[102 X 102])
(38.38
[975])
36.64
(931)

Cabinet
20 AFDJ-SVU01D-EN
Figure 5. A-Frame: Door-swing requirements
Table of contents
Popular DC Drive manuals by other brands

Uniblitz
Uniblitz VincentAssociates VED24 instructions
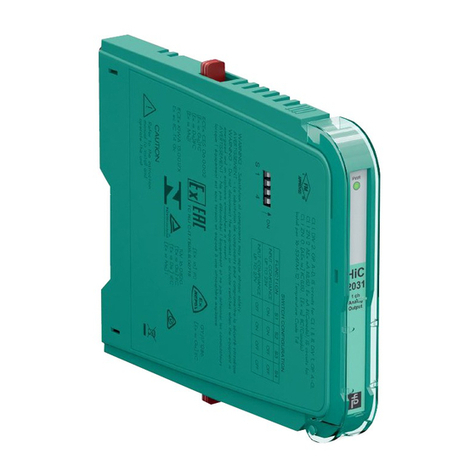
Pepperl+Fuchs
Pepperl+Fuchs HiC2031 instruction manual
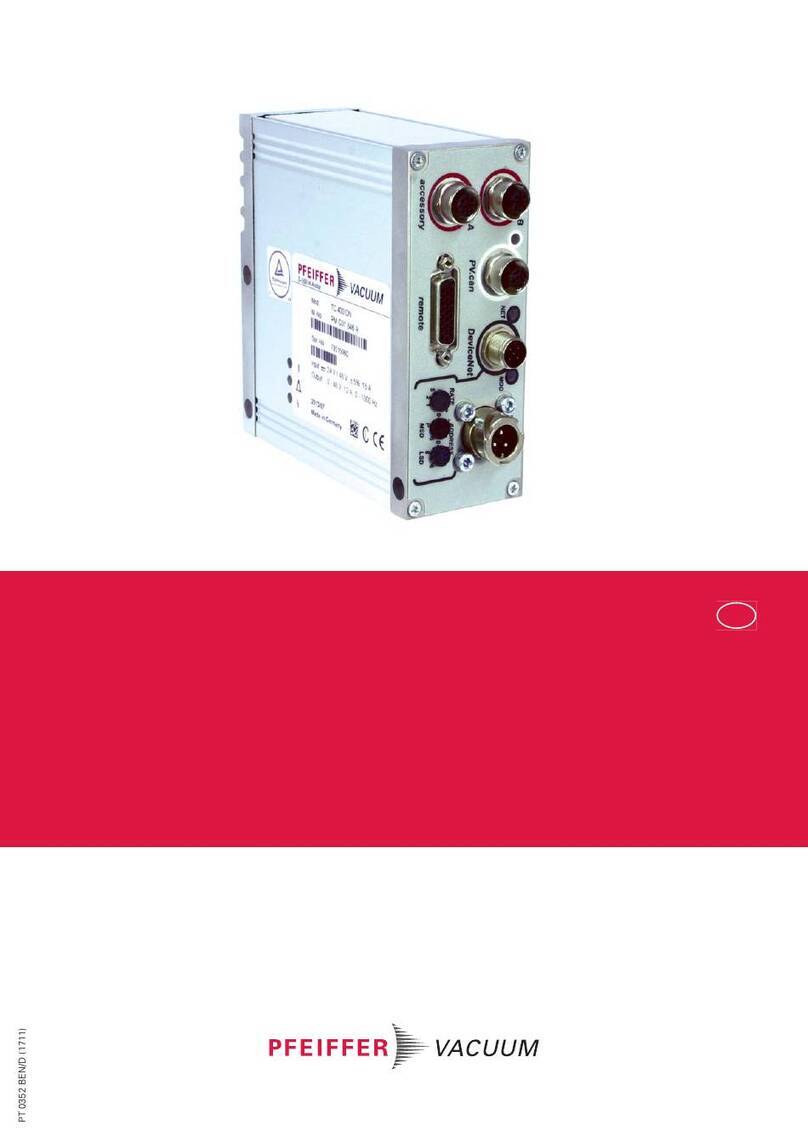
Pfeiffer Vacuum
Pfeiffer Vacuum TC 400 DN operating instructions
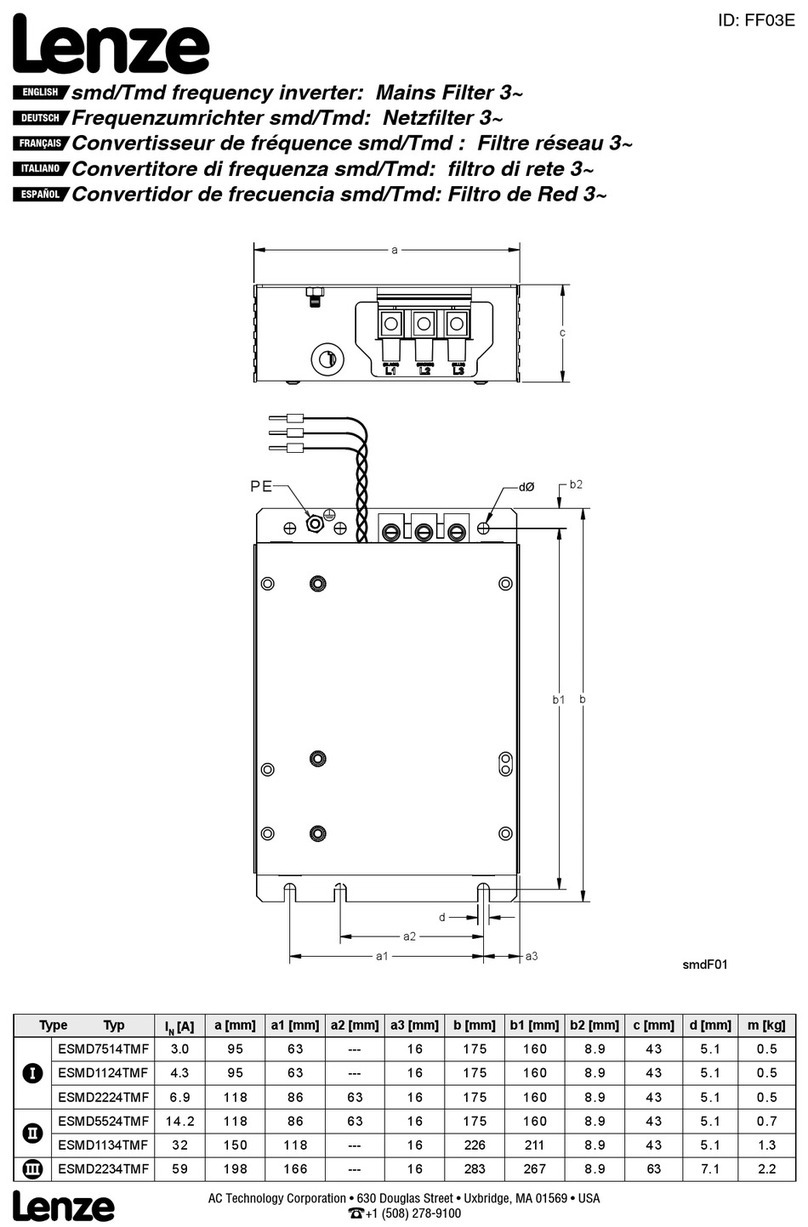
Lenze
Lenze ESMD7514TMF Installation

Siemens
Siemens Sinamics SM150 6SL3845-2NN41-8AD0 Operating and installation instructions

Hayward
Hayward ColorLogic WFCLSYNC manual

SEW-Eurodrive
SEW-Eurodrive Movidrive MDX61B operating instructions
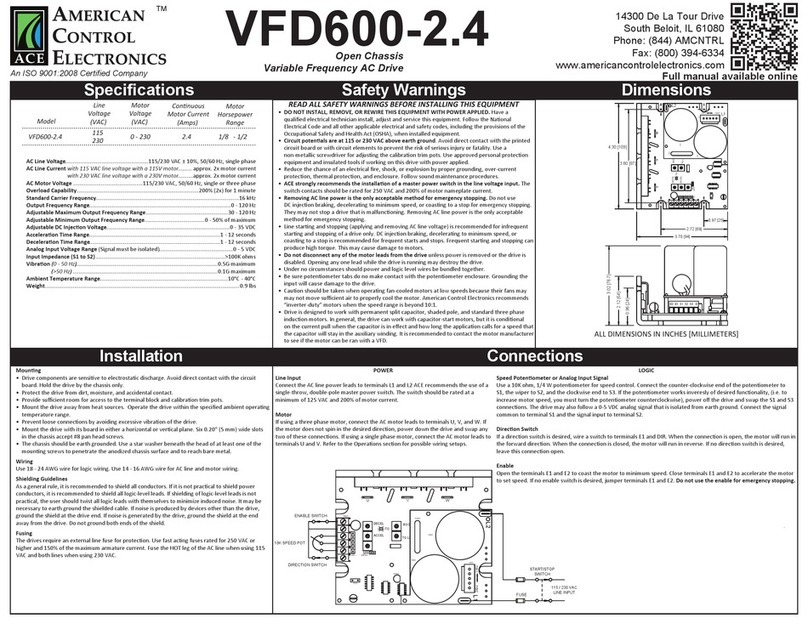
American Control Electronics
American Control Electronics VFD600-2.4 instructions
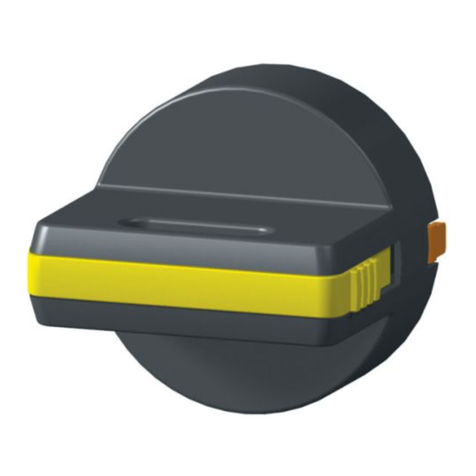
OEZ
OEZ RP-BC-CP10 Instructions for use
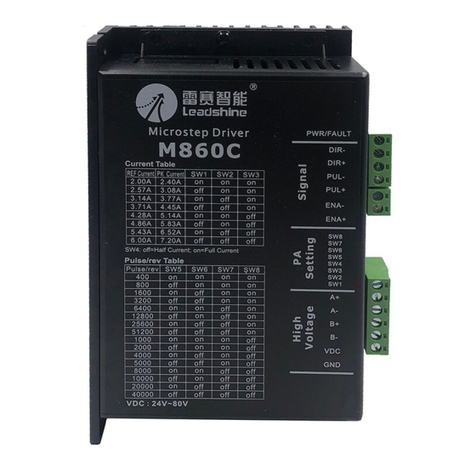
Leadshine
Leadshine M860C instruction manual
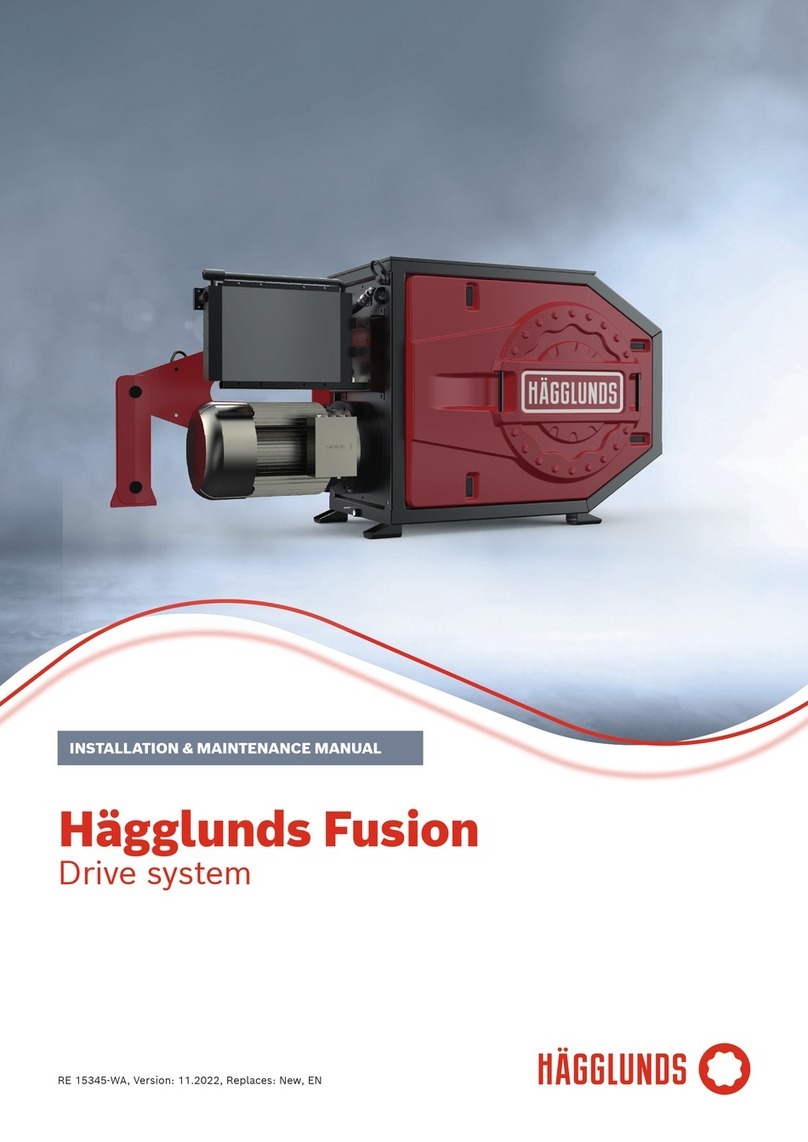
Hägglunds
Hägglunds Fusion Installation & maintenance manual

Iomega
Iomega Zip 250 owner's manual