UAS CLARCOR MCB Series User manual

Cross Ventilation Cartridge Dust Collector l MCB SerieS
OWNER'S MANUAL

KNOW YOUR EQUIPMENT
READ THIS MANUAL FIRST.
Your MCB system should provide many years of trouble-free service. This manual will
help you understand the operation of your MCB unit. It will also help you understand how
to maintain it in order to achieve top performance. For quick future reference, fill in the
system and filter information in the spaces below. Should you need assistance, call the
customer service number shown below. To expedite your service, have the following
information available when contacting UAS.
UAS ORDER #:_________________________________________________________
UNIT MODEL #: ________________________________________________________
UNIT SERIAL #: ________________________________________________________
CARTRIDGE FILTER PART #: _____________________________________________
SYSTEM ACCESSORIES:
______________________________________________________________________
______________________________________________________________________
______________________________________________________________________
INSTALLATION DATE: ___________________________________________________
UNITED AIR SPECIALISTS, INC. CUSTOMER SERVICE
1-800-252-4647

TABLE OF CONTENTS
Page
1 IMPORTANT NOTICE ......................................................................................1
2 INTRODUCTION..............................................................................................1
2.1 Unit Nomenclature......................................................................................1
2.2 Description and Operation .........................................................................1
2.3 Air Filtering Operation ................................................................................1
2.4 Filter Cleaning Cycle ..................................................................................1
3 SPECIFICATION TABLE ..................................................................................4
4 INSTALLATION ................................................................................................4
4.1 Off Loading and Inspection ........................................................................4
4.2 Installation Planning ...................................................................................4
4.3 Module Installation .....................................................................................4
4.3.1 Compressed Air Connection ...................................................................4
4.4 Motor/Blower Installation............................................................................6
4.5 Booth Assembly/Installation .......................................................................6
4.5.1 Wall/Roof Panel Assembly ......................................................................6
4.5.2 Booth Trim...............................................................................................6
4.5.3 Acoustical Curtain....................................................................................6
4.5.4 Booth Lights ............................................................................................6
5 ELECTRICAL INSTALLATION .......................................................................10
5.1 Mounting The Controls.............................................................................10
5.1.1 Digital Pulse Monitor (DPM) Panel Installation .....................................10
5.1.2 Digital Pulse Control (DPC) Panel Installation......................................10
5.1.3 Final Connections For All Gauge Options.............................................10
5.2 Electrical Connections For Booth Lights ..................................................10
5.3 Solenoid Valve Enclosure Wiring .............................................................10
6 OPERATION...................................................................................................10
6.1 Start-Up ....................................................................................................10
6.2 Operating Adjustments.............................................................................12
6.2.1 Digital Pulse Monitor Panel (DPM) .......................................................12
6.2.2 Digital Pulse Control Panel (DPC) ........................................................12
7 SERVICE........................................................................................................12
7.1 Cartridge Filter Removal and Replacement.............................................12
7.2 Dust Drawer Removal ..............................................................................14
7.3 Servicing the Direct Drive Motor and Blower Wheel................................14
8 TROUBLESHOOTING GUIDE.......................................................................15
9 ILLUSTRATED PARTS - 6 and 9 Foot Wide Modules...................................16
10 MCB Parts List - 6 and 9 Foot Wide Modules ...............................................17
11 ILLUSTRATED PARTS - 3 Foot Wide Modules.............................................18
12 MCB Parts List - 3 Foot Wide Modules..........................................................19
Warranty .......................................................................................... Back Cover
ii

ii
SAFETY PRECAUTIONS
We have provided many important safety messages in this manual and on the MCB unit. Always read and obey all safety
messages.
• Use two or more people to move and install the
MCB system.
• The air cleaner must be properly grounded.
• Disconnect power before servicing.
• Replace all access panels before operating.
• Wear protective clothing and safety glasses when handling
collection components or servicing the air cleaner.
• Electrical connections should only be made by qualified
personnel, and be in accordance with local and national
codes and regulations.
• Do not use in explosive atmospheres.
• Use nonflammable cleaners.
• Do not collect emissions which are explosive.
• Keep flammable materials and vapors, such as gasoline,
away from air cleaner.
• The unit should be inspected frequently and dirt removed
to prevent excessive accumulation which may result in
flash-over or fire damage.
• The MCB system should not be used for
support of personnel or material.
• Operate only in safe and serviceable condition.
!
!DANGER
!WARNING
!CAUTION
CAUTION
This is the safety alert symbol.
This symbol alerts you to potential hazards that can kill or hurt you and others. All safety messages will follow the
safety alert symbol and the word “DANGER”, “WARNING”, or “CAUTION”. These words mean:
Indicates a hazardous situation which, if not avoided, will result in death or
serious injury.
Indicates a potentially hazardous situation which, if not avoided, could result
in death or serious injury.
Indicates a potentially hazardous situation which, if not avoided, may result
in minor or moderate injury.
CAUTION used without the safety alert symbol indicates a potentially
hazardous situation which, if not avoided, may result in property damage.
IMPORTANT SAFETY INSTRUCTIONS
To reduce the risk of fire, electric shock, or injury when using the air cleaner, follow these basic precautions:
!WARNING

5
Revised 03/15 MCB
Crossflow Dust Collector
1. IMPORTANT NOTICE
This manual contains important safety information and
precautionary measures. Read this manual thoroughly
and comply with the instructions given. It is impossible
to list all potential hazards associated with every dust
collection system in each application. Proper use of
the equipment should be discussed with United Air
Specialists, Inc. (UAS) or your local representative.
Operating personnel should be aware of, and adhere to,
the most stringent safety procedures.
EXPLOSION HAZARD
• Avoid mixing combustible materials such as
aluminum, paper, wood or other organic dusts with
dusts generated from grinding metals. A fire hazard
could develop from sparks entering the dust
collector.
• When collecting emissions from spark-producing
processes, care must be taken to reduce any
potential fire hazards. System design should
include methods to prevent sparks from entering
the dust collector. Dust collectors do not contain
fire-extinguishing equipment.
• Do not allow any machine operator to put lit
cigarettes or any burning object into the dust
collector.
• Your dust collector was selected for a particular
application. Consult UAS prior to making any
application or system changes.
2. INTRODUCTION
Thank you for selecting UAS dust collection equipment
to assist you in your commitment to a clean and safe
environment. We trust that in purchasing our product
you have recognized our commitment to continually
offer dust collection equipment engineered to each
dust collection need and manufactured to the
highest standards.
2.1 UNIT NOMENCLATURE
2.2 DESCRIPTION AND OPERATION
MCB cartridge units are used for the collection of
airborne dust and particulate. The MCB cartridge
system provides continuous-duty air cleaning in the
work environment or as part of your manufacturing
process. As you review this manual, refer to Figure 1
and 2 for assistance in locating unit parts.
2.3 AIR FILTERING OPERATION
During the air filtering operation, contaminated air
enters the MCB dust collector through the door louvers.
The inlet louvers allows heavier particles to fall into the
dust storage drawer. The contaminated air then passes
through the cartridge filters. The filter media strips the
dust from the airstream allowing only clean air to pass
through the filter. The air then passes into the clean air
plenum, through the fan enclosure and is discharged
from the unit. Refer to Figure 1.
2.4 FILTER CLEANING CYCLE
During normal operation, the surface of the cartridge
filters become loaded with contaminants. The reverse
pulse cleaning mechanism provides brief bursts of
compressed air, directed through cleaning nozzles, into
the interior of the cartridge filters. This pulsing action
dislodges the collected particulate from the media
where it falls into the dust storage drawer.
Refer to Figure 1.
During the cleaning cycle, two cartridge filters
are cleaned at a time. The solid-state sequential
timer actuates a solenoid valve which allows an
air diaphragm valve to open for approximately 100
milliseconds. High pressure air from the air manifold
reservoir is directed through the cleaning nozzles to the
cartridge centers. The quick blast of compressed air
induces additional air from the clean air plenum which
combine to produce a shock wave, dislodging the dust
from the filters being cleaned.
The dislodged dust removed from the filters falls into
the dust storage drawers. The remaining filters are
cleaned sequentially. The sequencing is factory preset
at 10-second intervals and is adjustable to adapt to your
particular cleaning needs.
EXAMPLE: MCB-XX-XX-X
}
Number of 6' modules
Number of 9' modules
Width in feet i.e. 03 = 3 feet
Flow i.e. S = STANDARD
H = HIGH
06 = 6 feet
12 = 12 feet
!DANGER
1

2
Revised 03/15 MCB
Crossflow Dust Collector
Figure 1.
MCB Operation Detail
44-10343-0001

3
Revised 03/15 MCB
Crossflow Dust Collector
Figure 2.
Typical MCB Dust Collector With Booth Enclosure Installation
44-10344-0003

4
Revised 03/15 MCB
Crossflow Dust Collector
3. SPECIFICATION TABLE
MCB 3 Foot Modules
MCB 6 Foot Modules
MCB 9 Foot Modules
4. INSTALLATION
4.1 OFF LOADING AND INSPECTION
UAS recommends using a forklift during unloading,
assembly and installation of the MCB dust collector.
A crane can be used for the individual modules.
Lifting lugs have been provided for each module.
Upon receipt of your unit, check for any shipping damage.
A damaged carton indicates that the equipment may have
received rough handling during shipping that may have
caused possible internal damage. Notify your delivery
carrier and enter a claim if any damage is found.
4.2 INSTALLATION PLANNING
For best installation and operation results, the MCB
booth should be installed on a flat concrete foundation
inside the factory. If the surface is not flat, modules and
booth walls must be shimmed to align bolt holes.
When calculating for the foundation, the weight of the
dust collector, material collected, MCB, booth and all
auxiliary equipment must be considered together for
seismic loads. Refer to individual specification drawing
for the MCB weight.
Choose the collector module location with consideration
for access to the dust collector, access to the dust
storage drawers located inside each module, creation
of the shortest run for electrical and air connections,
and ease of maintenance. If hazardous dust is involved,
consult local authorities for the best location for
the unit.
4.3 MODULE INSTALLATION
Each module comes in a 3’, 6’ or 9’ module width and
can be installed on either end or center interchangeably.
The booth assembly builds upon the modules,
therefore, it is important to locate the modules on a flat
surface. Refer to Figure 3 for assistance for both the
module and compressed air connection.
1. Position one of the modules as an "end unit" with
the inlet louver side facing the inside of the booth.
No rear or side access is required for the MCB dust
collector so the modules can be placed with the rear
or side against a wall if necessary.
2. If multiple modules are to be installed, the modules
need to be spaced with a 1" gap between side
panels. A UAS supplied trim strip will bridge
the gap between the units.
3. To install the trim strip, remove all fasteners
on the front panel of the adjoining corner from
both cabinets. Locate the trim strip so as to
match the cabinet bolt pattern and re-fasten
the screws. Repeat as necessary for
additional modules.
4.3.1 COMPRESSED AIR CONNECTION
1. Each MCB dust collector comes with four possible
compressed air supply points: two on the air inlet
side and two on the side panels of each module.
Each cabinet connection point is covered with a
removable finishing plug. To remove the plugs,
remove the front access panel and simply tap the
plugs out from the inside of the cabinet.
!WARNING
For lifting slings, use spreader bars and clevises, not hooks. Do not
lift the unit from any point other than the lifting lugs. Connect the
lifting sling to the four cabinet lifting lugs to distribute the load equally.
!WARNING
MCB dust collectors are not designed as explosion proof and/
or spark resistant units. Do not locate dust collector near dust
source in cases where the dust is explosive or a fire hazard.
Unit CFM # Filters
Total sq. ft.
of Media
Face
Velocity ft/m
Booth Size
W’xH’xD’
MCB-06-01-H 9,000 8 2,720 200
150
200
150
200
150
150
200
6x7.5x8
6x7.5x8
12x7.5x8
12x7.5x8
18x7.5x8
18x7.5x8
24x7.5x8
24x7.5x8
6,750 8 2,720
5,440
5,440
8,160
8,160
10,880
10,880
18,000 16
13,500 16
627,000 24
20,250 24
36,000 36
27,000 36
MCB-06-01-S
MCB-12-02-H
MCB-12-02-S
MCB-18-03-H
MCB-18-03-S
MCB-24-04-H
MCB-24-04-S
Unit CFM # Filters
Total sq. ft.
of Media
Face
Velocity ft/m
Booth Size
W’xH’xD’
MCB-09-10-H 13,500 12 4,080 200
150
200
150
200
150
150
200
9x7.5x8
9x7.5x8
18x7.5x8
18x7.5x8
27x7.5x8
27x7.5x8
36x7.5x8
36x7.5x8
10,125 12 4,080
8,160
8,160
12,240
12,240
16,320
16,320
27,000 24
20,250 24
40,500 36
30,375 36
54,000 48
40,500 48
MCB-09-10-S
MCB-18-20-H
MCB-18-20-S
MCB-27-30-H
MCB-27-30-S
MCB-36-40-H
MCB-36-40-S
!CAUTION
Shut off and slowly release the pressure in the compressed
air piping and/or the MCB compressed air reservoir
manifold prior to servicing this equipment.
Unit CFM # Filters Total sq. ft.
of Media
Face
Velocity ft/m
MCB-03 4,500 4 1,360 200

5
Revised 03/15 MCB
Crossflow Dust Collector
Figure 3.
MCB Installation Detail
44-10360-0001

6
Revised 03/15 MCB
Crossflow Dust Collector
2. Within the cabinet each side of the compressed
air manifold is equipped with (4) plugged, 1" NPT
couplings. After selecting the appropriate connection
points, remove the corresponding plug(s). Adjoining
modules are supplied with a piping connection kit as
shown in Figure 3 to supply air to each module. Pipe
plugs can be removed using a wrench on the inside
of the cabinet through the access panel or by using
a 15/16" socket wrench through the cabinet holes
vacated by the finishing plugs.
3. Check the nylon tubing which runs between the
solenoid enclosure and bulkhead fittings then finally
to the diaphragm valves to ensure the fittings hold
the tubing firmly in place.
4. Clean, dry, 90-110 PSIG compressed air is required
for the pulse cleaning system to properly function.
A shut-off valve, pressure regulator and pressure
gauge should be installed close to the unit. United
Air Specialists, Inc. recommends dedicated oil and
water removal filters be used to ensure clean, dry
air is delivered to the pulse system. Contact your
local representative for information on the United
Air Specialists, Inc. pneumatic valve kit. Refer to
Figure 3 for compressed air piping connection.
5. UAS recommends 1" diameter air line to supply the
unit. A flexible pipe grommet is provided to seal the
cabinet once the connection is made. Refer to
Figure 3.
4.4 MOTOR/BLOWER INSTALLATION
1. The MCB is provided with a blower that is shipped
separately. The blower package contains the
motor, motor mounting plate, fan wheel, gasket and
mounting hardware.
2. The blower assembly mounts on the top panel of
the MCB cabinet with the fan wheel inside the
cabinet. Using provided hardware, mount the blower
as shown in Figure 4. There should be a 1/4"
overlap of the wheel and cone.
3. The motor and wheel should be rotating in a
clockwise direction when looking directly down
onto the motor (drive side).
Caution: To avoid wheel damage, never rest the
assembly on the fan wheel.
4. Note: Orientation of blower assembly. The electrical
connection box should face the front (door-side) of
the unit.
5. Prior to start-up, rotate the blower wheel after
assembly to ensure there is no interference with the
inlet cone.
4.5 BOOTH ASSEMBLY/INSTALLATION
Refer to the booth installation drawing in Figure 5 for
set-up and assembly.
4.5.1 WALL/ROOF PANEL ASSEMBLY
1. On the "end" modules, remove the column of fasteners
towards the inlet side of the module. Place the spacer
strip between the wall mounting bracket and the cabinet
and then replace the fasteners. The right wall bracket
has two notches near the bottom of the bracket, where
the left wall bracket only has one. See Figure 5.
2. On the inlet side of all modules, remove the top row of
fasteners excluding the ones holding the trim strip in
place. Locate the top panel support bracket, using the
fasteners attach to each module.
3. Starting at a corner, lay the wall base channel in place,
squared to the unit and against the vertical corner
channel. Sections of the base channel should fit tightly
together. Secure with drive nails on 18" centers along
the centerline of the base channel. If anchor bolts are
used, locate 5/16" anchor bolts on 18" centers with 3/8"
bolt projection above the surface.
4. Insert wall panels into the base channel (with the
perforated metal side toward the booth interior) of the
first corner.
5. Insert next panel into base channel with tongue end
mating with groove end on previously installed panel
(refer to Figure 6). Panels are pushed together to allow
snap-lock. UAS-provided caulking placed on the tongue
self-locking recess will exude as panels lock together.
6. As each panel is installed, secure the base channel to
each wall side panel with the UAS-provided #10 sheet
metal screws.
7. Review the roof plan shown on the installation drawing
provided with the unit and locate roof panels and front
horizontal channel. Place roof panels in position, one
at a time, and lock together in same method as side
panels.
4.5.2 BOOTH TRIM
1. Mount outside trim pieces in place using the UAS
provided #10 sheet metal screws.
2. After all outside trim has been installed, install inside
trim at wall-to-roof corners. Anchor the inside trim at all
tongue and groove panel joints and at all internal panel
stiffeners. Tighten all screws.
4.5.3 ACOUSTICAL CURTAIN
1. Secure the filter booth curtain bracket assembly in place
on the top panel using 1/4-20 x 3/4" self-tapping screws.
Tighten all screws.
2. Install acoustical curtains on the curtain bracket. Secure
in place with 3/8" plastic cap nuts. Join the Velcro
edges together.
4.5.4 BOOTH LIGHTS
1. For the corner mounted lights, bolt the supplied
mounting brackets through the booth roof and wall
panels in four places with 5/16-18" x 2 1/2" bolts, lock
washers and nuts. Place the brackets on 40-1/2" centers
to match the lighting fixtures.
2. Bolt the fluorescent light fixture to the mounting brackets
in two places each using 3/8" –16 x 3/4" bolts and lock
washers with bolt heads inside fixture.
3. For booths wider than two modules, flat lights are
provided. Bolt to roof panel in center of module with
3/8"-16 x 3/4" bolts and lock washers with bolt heads
inside the fixture.
!CAUTION
Do not allow water and/or oil from the compressed air
system into the compressed air manifold on the unit. To
ensure a water-free air supply, a water filter with automatic
drain or a condensation trap with automatic drain must be
installed just before the piping enters the MCB unit.

7
Revised 03/15 MCB
Crossflow Dust Collector
Figure 4.
Motor Installation Diagram
44-10342-0001

8
Revised 03/15 MCB
Crossflow Dust Collector
Figure 5.
MCB Booth Assembly
44-10361-0001

9
Revised 03/15 MCB
Crossflow Dust Collector
Figure 6.
Booth Panel Interlock Connection

10
Revised 03/15 MCB
Crossflow Dust Collector
5. ELECTRICAL INSTALLATION
Several types of standard electrical components can
be installed to control and monitor your MCB system,
ensuring proper cleaning of the cartridge filters.
A blower motor starter (combination starter panel)
is required to start and stop the system. The motor
starter circuit should consist of a properly-sized,
main fused disconnect or circuit breaker, short circuit
protective device(s), contactor(s) and overload relay(s)
for protection of the blower(s). A 115V/1PH/60Hz
low voltage control (2 amp) circuit is required for the
pulse control panel. Any one of the following control
configurations can be used:
• Motor starter(s) with a Digital Pulse Monitor for
continuous pulse (DPM).
• Motor starter(s) with a Digital Pulse Control for
setpoint pulse cleaning (DPC).
• VFD with DPM for continuous pulse cleaning.
• VFD with DPC for on-demand pulse cleaning.
Refer to UAS sales order to verify the number of motor
branch circuits (number of modules) and the pulse
control configuration purchased with your unit.
5.1 MOUNTING THE CONTROLS
Mount the combination starter panel for the fan motor
control in a convenient location. The panel is provided
by the customer, unless specifically ordered from UAS.
Mounting hardware for a UAS combination starter panel
is provided by the customer or contractor.
Mount the cleaning panel in a convenient location. It is
recommended that the controls be mounted on
a wall or pedestal in a convenient area subject to
minimal vibration and electrical noise.
5.1.1 DIGITAL PULSE MONITOR (DPM)
PANEL INSTALLATION
If your system was ordered with a Digital Pulse Monitor
(DPM) panel, remove it from the box. Instructions for
mounting and connecting the panel are available in the
DPM/DPC Installation and Owner’s Manual. The panel
should be installed within close proximity of the unit as
shown in Figure 7.
5.1.2 DIGITAL PULSE CONTROL (DPC)
PANEL INSTALLATION
If your system was ordered with a Digital Pulse Control
(DPC) panel, remove it from the box. Instructions for
mounting and connecting the panel are available in the
DPM/DPC Installation and Owner’s Manual. The panel
should be installed within close proximity of the unit as
shown in Figure 7. The DPM/DPC panel requires field
electrical connections.
5.1.3 FINAL CONNECTIONS FOR ALL GAUGE
OPTIONS
For all pulse control panels, connect the black, plastic
pressure tubing (25' [7.5 meters] provided by UAS) from
the clean air plenum of the MCB to the low pressure
port (clean air) on the panel. The high pressure post/
dirty air is vented to atmosphere.
5.2 ELECTRICAL CONNECTIONS FOR
BOOTH LIGHTS
Follow local codes for wiring lights in parallel. Light
wiring and on/off switch are not provided by UAS.
Mount the on/off switch in a convenient location.
5.3 SOLENOID VALVE ENCLOSURE WIRING
The solenoid valves at the MCB must be wired correctly
to the pulse control panel. Refer to Figure 8 when
making connections from the pulse control panel to the
solenoid valve enclosure(s). The system pulses with "1"
as the first pulse, "2" as the second pulse, "3" as the
third pulse, etc.
Unless specified on the UAS sales order, the customer
will supply interconnecting material (conduit, wiring,
etc.) from the pulse controls to the dust collector.
6. OPERATION
6.1 START-UP
1. Inspect the installation area and make certain no
tools, parts, etc. have been left on or inside the
MCB unit. Check each blower discharge
to make certain it is free from all debris.
!DANGER
ELECTRIC SHOCK HAZARD
All electrical work should be performed by a qualified
electrician in accordance with local electrical codes.
Disconnect electrical power before installing or
servicing any electrical component.
CAUTION
Avoid mounting the cleaning panel on the collector due
to vibration generated from blower assembly and the
pulsing system.
!WARNING
Never operate the dust collector without the front
access panel properly installed.
Prior to unit start-up, all installation set-up instructions
must be completed as specified by this manual and
DPM/DPC Controls Installation and Operation Manual,
as well as any manuals supplied by other equipment
manufacturers, as they apply to your dust collector.

11
Revised 03/15 MCB
Crossflow Dust Collector
Figure 7.
MCB Pressure Gauge Installation
44-10350-0001

12
Revised 03/15 MCB
Crossflow Dust Collector
2. Open the louver doors and verify the filters
are properly installed. See section 7.1 for filter
installation.
3. Turn on the blower(s). On initial start-up, make
certain the blower rotation is correct. All blower
wheels rotate in a clockwise rotation as viewed from
the drive end.
NOTE: Proper blower rotation is required to move
the designed amount of air. A blower rotating
in the incorrect direction will only move about
40% of design airflow.
4. Turn on the compressed air supply to the unit.
Adjust the pressure regulator until the gauge
reads 90-110 PSIG (6.2-7.7 BAR).
5. Check the exhaust. Exhausting air should remain
visibly clean. If a leak develops, it will be first noticed
after cleaning pulsation as a puff of dust.
6. Check the pressure differential reading on the
pressure measurement device (DPM/DPC panel).
7. Check the cleaning system for proper operation.
The compressed air pressure should be between
90-110 PSIG (6.2-7.6 BAR). UAS’ pulse control
panels are factory set to pulse every 10 seconds.
Refer to the DPM/DPC Installation and Operation
Manual specified with the dust collector to change
these initial settings. Check to ensure the pulse
(diaphragm) valves are “firing” at approximately
10-second intervals and delivering a “cri sp” sounding
pulse to each filter. The valves should not deliver a
weak or lingering pulse. To check the pulse sequence
for proper firing, perform the following:
• If your system is supplied with a DPM/DPC panel,
place the “Continuous Clean/PS” switch on the
timerboard to the “Continuous Clean” position. The
MOT AUX terminals at the timerboard should be field
wired for the pulsing to become active. To activate,
energize the motor starter to close the isolated
auxiliary contact wired to the timerboard MOT AUX
terminals. Verify consistent pulse firing of each
solenoid valve exhaust port.
6.2 OPERATING ADJUSTMENTS
Confirm the type of pulse cleaning controller delivered
with the system. The system is typically provided with
one of the following:
• DPM Digital Pulse Monitor Panel
• DPC Digital Pulse Control Panel
NOTE: It is important that the compressed air pressure is in
the 90-110 PSIG range (6.2-7.6 BAR) immediately
prior to a pulse. If the delivery capability of your
compressed air source cannot return the manifold
pressure to above 90 PSIG during the “Pulse Delay”
(factory set at 10 sec.) interval, adjust the pulse
delay at the timerboard and monitor the pressure.
A longer interval will raise the operating pressure,
which is the pulse delay. (Adjust from position 2 or
position 3 on the timerboard.) Allow sufficient time
for the system to stabilize after each adjustment
before further adjustment is made. Adjust until the
desired pressure differential is reached.
6.2.1
DIGITAL PULSE MONITOR PANEL (DPM)
THE DPM is always set to “Continuous Clean” pulse
mode, which means pulse cleaning is operating
continuously when the system is on line. Refer to
the DPM/DPC Installation and Operations Manual for
detailed information.
6.2.2
DIGITAL PULSE CONTROL PANEL (DPC)
The DPC is set for “Pressure Switch” or “PS” pulse
mode. With the DPC, the desired pressure can be
maintained by adjusting the high and low setpoints on
the panel. The factory setting is 3.0 (high setpoint) and
2.5 (low setpoint). This allows a 0.5" “deadband” where
the pulse system will maintain the desired pressure.
The high and low setpoints on the DPC can be adjusted
as the filters season and continuous pulsing occurs.
Adjust setpoints upward in 0.5" increments until pulsing
stops. Continue adjustments, when required, until the
high setpoint reaches 5". No further adjustments should
be made above 5" w.g.
7. SERVICE
7.1 CARTRIDGE FILTER REMOVAL AND
REPLACEMENT
1. Protura®Nanofiber cartridge filters are the only
replacement filters that will provide the highest level
of performance expected from the dust collector.
!CAUTION
Shut off and slowly release the pressure in the
compressed air piping and/or the MCB compressed air
reservoir manifold prior to servicing this equipment.
Disconnect all electrical power to the unit and
control panel.
Shut off and slowly bleed the compressed air supply
from the manifold.
Collected dust may be hazardous. Consult proper
authorities for handling and disposal.
Collected dust may be a potential fire hazard.
Grinding or operations involving open flames should
not be performed without fire protection measures in
place. Refer to Section 1 for additional precautions.
Wear appropriate protective clothing when servicing
the dust collector.
Disposal of collected dust must be according to state
and local environmental regulations.
!DANGER

13
Revised 03/15 MCB
Crossflow Dust Collector
Figure 8.
Solenoid Wiring to Pulse Controls
61-10017-0001 REV. B

14
Revised 03/15 MCB
Crossflow Dust Collector
When both filters are in place, lift the left handle
(pivoting counter-clockwise) into a horizontal position.
Next, lift the right handle (pivoting clockwise) taking
care that the retaining clip (on the backside of the
handle) grabs the left handle. Finally, lift the right
handle above the left handle retaining clip and rest in a
horizontal position as shown in Figure c.
Figure c.
The filters should be firmly compressed against the tube
sheet and ready for operation.
7.2 Dust Drawer Removal
1. As the cartridges are cleaned, dust will collect in
drawers located at the base of the module. Handles
are provided on the front and rear of each drawer for
easy handling.
2. When the drawers are full, simply remove from unit
and empty contents.
3. To replace the drawers, align the “V-notch” (on the
bottom of the drawer) with the tracks on the models
base panel and slide the drawer in place.
7.3 SERVICING THE DIRECT DRIVE MOTOR
AND BLOWER WHEEL
Periodically inspect the fan blades to ensure proper
fan life. Grease the motor every 2,000 hours with high
grade ball and roller bearing grease. The recommended
grease is Chevron SRI#2.
Periodically inspect the fan wheel coupling mounting
bolts for tightness. Re-tighten as necessary to ensure
the fan wheel does not loosen and come in contact
with and rub the inlet bell.
!CAUTION
Drawers may be heavy due to weight of
collected dust.
2. Replacement cartridge filters should be ordered
when the differential pressure across the filter is
consistently above 5" w.g. (127 mmAq) or system
airflow is inadequate. To order filters contact UAS
at 888-515-8800.
3. To remove the filters:
Lift the right handle out of the retaining clip as shown in
Figure a.
Figure a.
Once the right handle has cleared the retaining clip,
lower both handles to a vertical position as shown in
Figure b.
Figure b.
Using the tab on the underside of the filter end cap,
slide the filter out of the unit (also shown in Figure 2).
Once the front filter is removed, reach back into the
cabinet and remove the rear filter in the same manner.
4. To replace filters:
Place the Protura®cartridge filter with the square end
cap resting on the locking bar rails. Slide the rear filter
until running in to backstop at rear of cabinet. Place
front filter on rails and slide into cabinet until filter
touches rear filter.
!CAUTION
The filter may be heavy due to the weight of the
collected dust.

15
Revised 03/15 MCB
Crossflow Dust Collector
PROBLEM POSSIBLE CAUSE POSSIBLE SOLUTIONS
Blower motor won’t start or will
not stay running.
No voltage to system. Check primary voltage to motor circuits for
proper voltage on all legs.
Improper electrical wiring. Check and correct internal motor wiring for
proper connections based on the incoming
line voltage. Wiring diagram is found on
lead access plate.
Starter overloads tripped. Check for proper motor starter overload
rating against full load amps on the motor
nameplate. Adjust or replace overloads as
required.
Dust emissions from clean air
discharge.
Filters installed improperly. Inspect and reinstall cartridge filters. Make
sure the cambars are engaged.
Filters damaged. Replace the damaged filter(s) with new
Nanofiber®cartridge filters.
Insufficient airflow. Blower rotation is running in reverse. Ensure blower is circulating clockwise from
drive side.
Air inlet(s) obstructed. Inspect and clean all louver doors.
Filters plugged. Refer to troubleshooting procedures for
continual pressure drop.
Continual, excessive pressure
drop (over 5") on filter monitor
panel.
Compressed air supply problems. Check incoming compressed air for proper
pressure (90-110 PSIG [6.4-7.2 BAR]),
pulse flow (1.7 SCF standard cubic feet
[48.1 liters] per pulse) and pulse duration
(100 milli-seconds). Correct any problems.
Pulse cleaning system not
functioning properly.
Check incoming 110-115 VAC power to
cleaning control panel. Check for blown
fuse on panel. Replace if necessary.
Check for 110V output from timerboard. If
incoming voltage is correct and fuse is not
blown, replace timerboard.
DPC Panel not adjusted properly. Refer to Section 6.2.2 of this manual for
proper setting of DPC Panel.
8. TROUBLESHOOTING GUIDE
Use the troubleshooting guide to correct any problems that occur with your dust collection unit. If the problem or
condition continues, contact UAS customer service at 1-800-252-4647.
Pulse system not adjusted
properly.
Pulse settings incorrect. Adjust pulse duration to 0.100 seconds
(position 3). Adjust pulse delay to
10 seconds (position 2).
Filters are at the end of their
service life.
Replace filters with Protura® Nanofiber
filters from UAS. Each cartridge filter has a
part number affixed to the end cap.
Check for proper pulse valve operation.
Replace damaged parts as required.

16
Revised 03/15 MCB
Crossflow Dust Collector
9. ILLUSTRATED PARTS
6 and 9 Foot Wide Module
This manual suits for next models
17
Table of contents
Other UAS Dust Collector manuals
Popular Dust Collector manuals by other brands
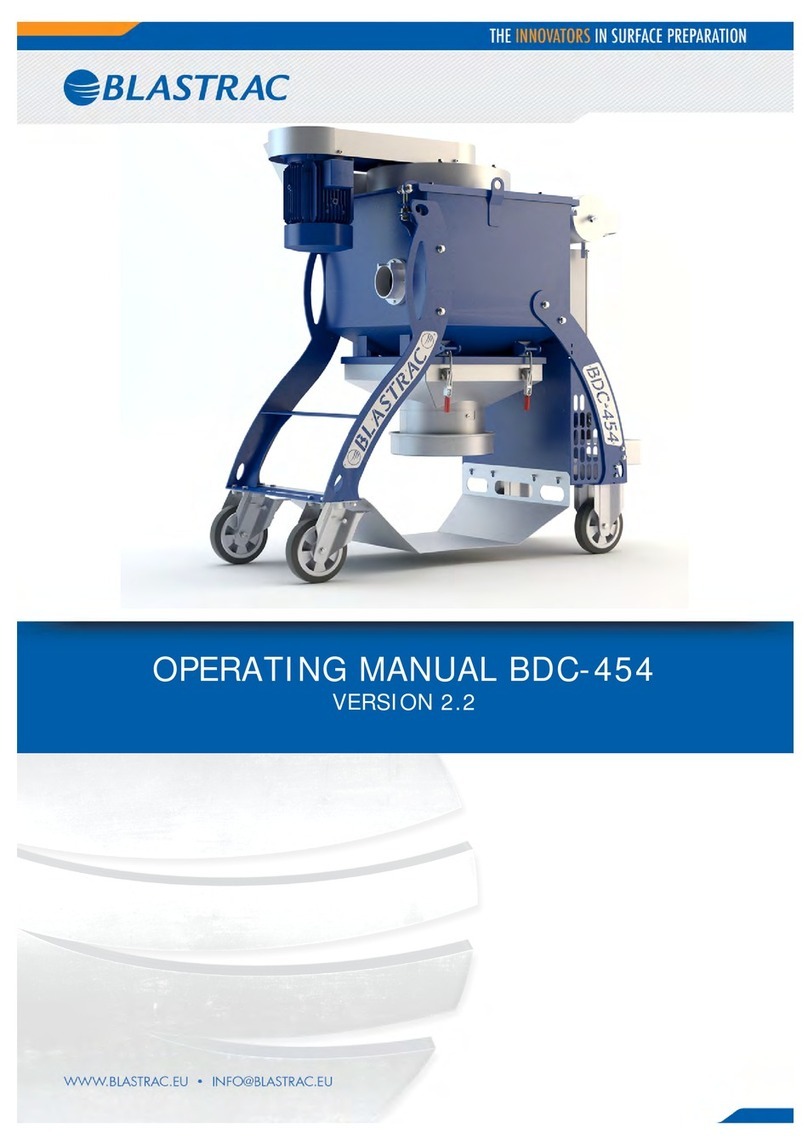
Blastrac
Blastrac BDC-454 operating manual
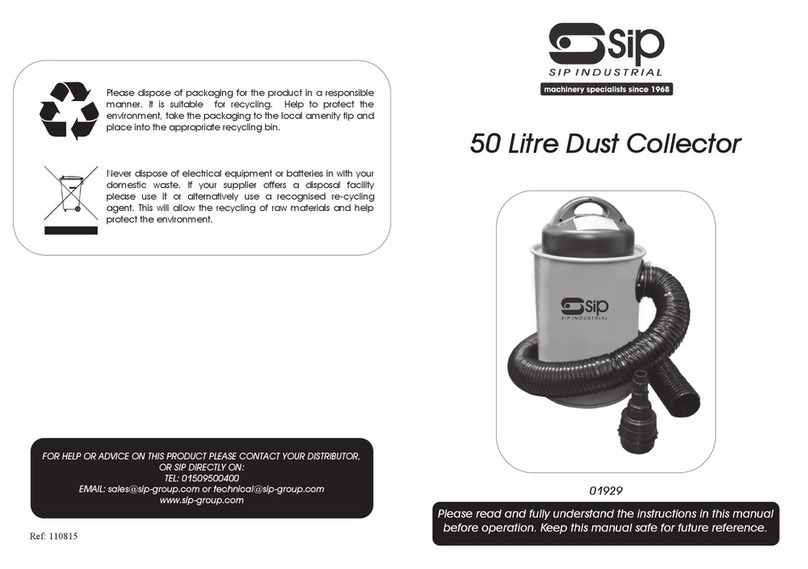
SIP
SIP 01929 manual
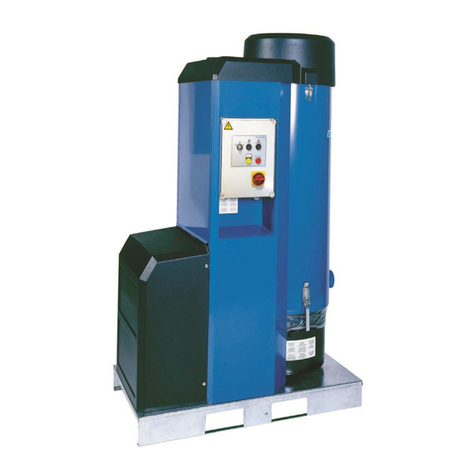
Nederman
Nederman E-PAK 300 DX instruction manual
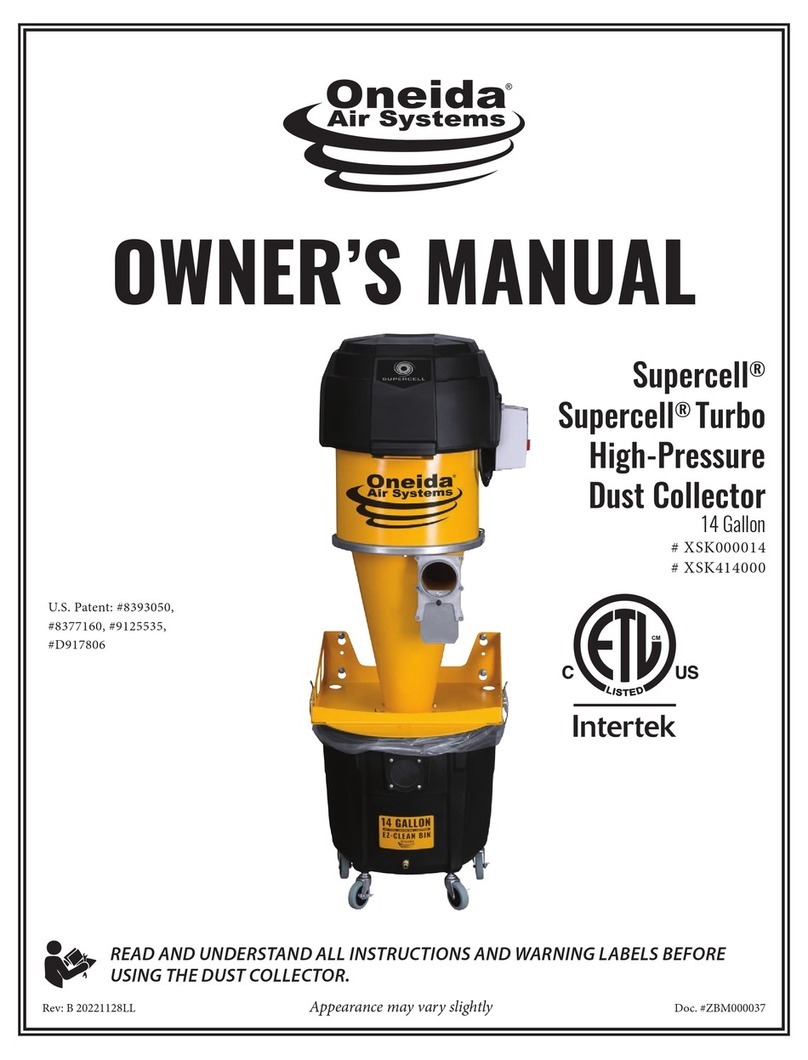
Oneida Air Systems
Oneida Air Systems Supercell Mobile owner's manual
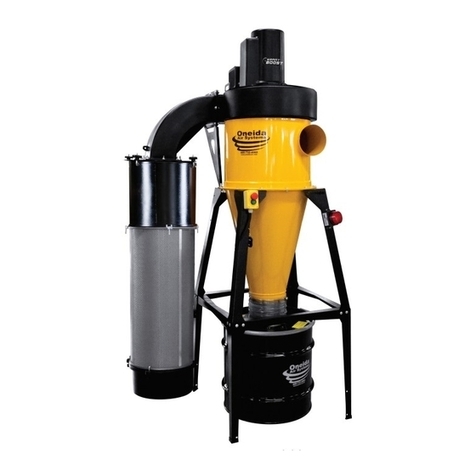
Oneida Air Systems
Oneida Air Systems Dust Gorilla Pro owner's manual
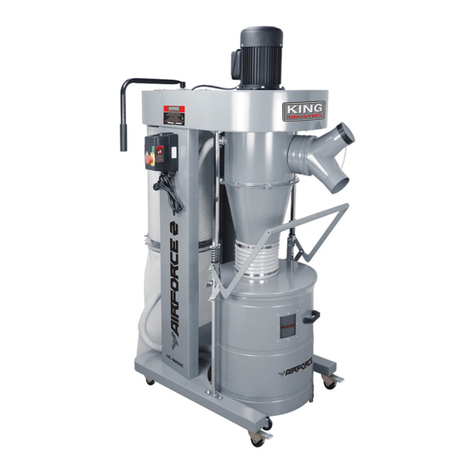
King Industrial
King Industrial KC-8150C instruction manual