Vari VARIMATIC 300 User manual

FOR YOUR SAFETY
READ AND UNDERSTAND THE ENTIRE MANUAL
BEFORE OPERATING THE MACHINE
MODEL: VARIMATIC 300
SERIAL NUMBER:
Both model number and serial number may be found on the main label.
You should record both of them in a safe place for future use.
Save This Manual for Future Reference
WOOD PROCESSOR
Instructions for use (Original instructions for use) 2019

2
TABLE OF CONTENTS
INTRODUCTION ........................................................................................................ 2
RECYCLING AND DISPOSAL ................................................................................... 3
SYMBOLS .................................................................................................................. 3
SAFETY...................................................................................................................... 5
SPECIFICATIONS...................................................................................................... 8
APPLICATION CONDITIONS .................................................................................... 8
ELECTRICAL REQUIREMENTS................................................................................ 9
CONTENTS SUPPLIED ........................................................................................... 10
ASSEMBLY .............................................................................................................. 10
DELIVERING WOOD PROCESSOR TO WORK SITE ............................................ 14
OPERATION ............................................................................................................ 14
FREE A JAMMED LOG............................................................................................ 19
REPLACING OIL ...................................................................................................... 19
MAINTENANCE ....................................................................................................... 20
STORAGE................................................................................................................ 22
TROUBLESHOOTING ............................................................................................. 22
WIRING DIAGRAM .................................................................................................. 23
PLUMBING DIAGRAM ............................................................................................. 24
PART LIST ............................................................................................................... 25
DISPOSAL OF PACKAGING AND MACHINE AFTER THE END OF SERVICE LIFE
................................................................................................................................. 33
INSTRUCTIONS FOR ORDERING SPARE PARTS................................................ 34
ADDRESS OF THE MANUFACTURER ................................................................... 34
ADDRESS OF THE IMPORTER AND DISTRIBUTOR ............................................ 34
EC DECLARATION OF CONFORMITY ................................................................... 35
Edition 2019. The manufacturer reserves the right to introduce technical modifications and
innovations, which do not affect the function and safety of the machine. These modifications may not
necessarily be specified in this user manual. Printing errors reserved.
INTRODUCTION
Your new wood processor will more than satisfy your expectations. It has been
manufactured under stringent quality standards to meet superior performance
criteria. You will find your new unit easy and safe to operate, and with proper care, it
will give you many years of dependable service.
The wood processor is designed to cut and split large volumes of wood efficiently
and safely. It consists of a log cutter and a log splitter. The log is cut to length, and a
hydraulic ram pushes the cut portion against a cross wedge, which splits the log in 4
sticks.
Carefully read through this entire operator’s manual before using your
new wood processor. Take special care to heed the cautions and
warnings.

3
RECYCLING AND DISPOSAL
This marking indicates that this product should not be disposed with
other household wastes. To prevent possible harm to the
environment or human health from uncontrolled waste disposal,
recycle it responsibly to promote the sustainable reuse of material
resources. To return your used device, please use the return and
collection systems or check with your local authority or local stores
for advice of environmental safe recycling.
SYMBOLS
The rating plate on your machine may show symbols. These represent important
information about the product or instructions on its use.
Read these instructions in full before using the machine.
Wear eye protection.
Wear hearing protection.
Wear dustproof mask.
Wear safety footwear.
Wear safety gloves.
Keep your work space tidy!
Untidiness may result in accidents.
Do not remove or tamper with any protection or safety devices.

4
Don not smoke or have open flames.
Dispose of the used oil in an environment-friendly way.
Do not use in the rain.
Do not remove jammed logs with your hands.
Always pay full attention to the movement of the log pusher.
Keep hands out of the way of all moving parts.
Do not attempt to load or unload logs until the log saw has
stopped
Caution! Thrown objects.
Before starting any repairs, maintenance or cleaning, always
disconnect the power.

5
Keep bystanders away from the working area.
SAFETY
SAFETY WARNINGS & INSTRUCTIONS
•
UNDERSTAND YOUR WOOD PROCESSOR
Read and understand the owner’s manual and labels affixed to the wood processor.
Learn its application and limitations as well as the specific potential hazards peculiar
to it. Be thoroughly familiar with the controls and their proper operation.
•
DRUGS, ALCOHOL AND MEDICATION
Do not operate the wood processor while under the influence of drugs, alcohol or
any medication that could affect your ability to use it properly.
•
AVOID DANGEROUS CONDITIONS
Always operate your wood processor on dry, solid, level ground. Never operate your
wood processor on slippery, wet, muddy or icy surfaces. The location you choose
should be free from any tall grass, brush or other interferences. There should be
plenty of room for handling, and help the operator stay alert. Keep your work area
clean and well lighted. Cluttered areas invite injuries. To avoid tripping, do not leave
tools, logs or other components lying around the work area. Do not use the wood
processor in wet or damp areas or expose it to rain. Do not use it in areas where
fumes from paint, solvents or flammable liquids pose a potential hazard.
•
INSPECT YOUR WOOD PROCESSOR
Check your wood processor before turning it on. Keep guards in place and in
working order. Form a habit of checking to see that keys and adjusting wrenches are
removed from tool area before turning it on. Replace damaged, missing or failed
parts before using it. Make sure all nuts, bolts, screws, hydraulic fittings, hose
clamps, etc. are securely tightened. Always check the oil level in the hydraulic oil
tank. Never operate your wood processor when it is in need of repair or is in poor
mechanical condition. Before starting work, test the stopping devices to keep them in
safe working condition.
•
DRESS PROPERLY
Do not wear loose clothing, gloves, neckties or jewellery (rings, wrist watches). They
can be caught in moving parts. Protective, electrically non-conductive gloves, non-
skid footwear, hearing protection and dustproof mask are recommended when
working. Wear protective hair covering to contain long hair, preventing it from get
caught in machinery.

6
•
PROTECT YOUR EYES AND FACE
Any wood processor may throw foreign objects into the eyes. This can cause
permanent eye damage. Always wear safety goggles. Everyday eyeglasses have
only impact resistant lenses. They are not safety glasses.
•
EXTENSION CORDS
Improper use of extension cords may cause inefficient operation of the wood
processor, which can result in overheating. Be sure the extension cord is not longer
than 10 m and its section is not less than 2,5 mm
2
to allow sufficient current flow to
the motor. Avoid use of free and inadequately insulated connections. Connections
must be made with protected material suitable for outdoor use.
•
AVOID ELECTRICAL SHOCK
Check that the electric circuit is adequately protected and that it corresponds with
the power, voltage and frequency of the motor. Check that there is a ground
connection. Ground the wood processor. Prevent body contact with grounded
surfaces. Never open the electric box. Should this be necessary, contact a qualified
electrician. Make sure your fingers do not touch the plug’s metal prongs when
plugging or unplugging the wood processor.
•
PREVENT FIRES
Do not smoke or have open flames when operating or refilling the wood processor.
Never operate the wood processor near a flame or candle. Oil is flammable and can
explode.
•
KEEP BYSTANDERS AWAY
Allow only one person to load and operate the wood processor. Always keep
bystanders, including visitors, children and pets away from the work area, especially
when the wood processor is under operation. Only the operator should stand near
the machine and only within the safe operating area prescribed in this manual.
Never use another people to help you with freeing jammed log. No one under the
age of 18 should be allowed to operate the wood processor. Any individual to
operate the wood processor should have the necessary training, skills to perform the
functions properly and safely.
•
INSPECT YOUR LOG
Never attempt to cut or split logs containing nails, wire or debris. Always make sure
that both ends of the log you are splitting are cut as square as possible. Branches
must be cut off the trunk.
•
DON’T OVERREACH
Keep proper footing and balance at all times. Never stand on wood processor.
Serious injury could occur if the tool is tipped or if the cutting tool is unintentionally
contacted. Do not store anything above or near the wood processor where anyone
might stand on the tool to reach it.

7
•
AVOID INJURY FROM UNEXPECTED ACCIDENT
Do not attempt to load or unload logs until the log saw has stopped. Keep hands out
of the way of all moving parts. Never use a damaged saw blade or chain. Do not
reach around the saw blade with either hand while the cutter is running. Do not
stand or have any part of your body in line with the path of the saw blade. Avoid
awkward cutting operations and hand positions where a sudden slip could cause
your hand to move into the saw blade. Never pile logs to be split in a manner that
will cause you to reach across the log saw. Only use your hands to operate the
control handle. Never use your foot, knee or any other extension device. Never
attempt to free a stalled saw chain without first turning the log saw off.
•
PROTECT YOUR HANDS
Keep your hands away from splits and cracks which open in the log. They may close
suddenly and crush or amputate your hands. Do not remove jammed logs with your
hands.
•
DON’T FORCE TOOL
It will do a better and safer job at its design rate. Don’t use wood processor for a
purpose for which it was not intended. Do not alter the equipment, or use the
equipment in such a way as to circumvent its design capabilities and capacities.
Never try to split logs larger than those indicated in the specifications table.
•
DISCONNECT POWER
Unplug when not in use, before making adjustments, changing parts, cleaning or
working on the wood processor. Consult technical manual before servicing.
•
NEVER LEAVE TOOL RUNNING UNATTENDED
Don’t leave tool until it has come to a complete stop.
•
MAINTAIN YOUR WOOD PROCESSOR WITH CARE
Before cleaning, repair, inspecting or adjusting, shut off the machine and make
certain all moving parts have stopped. Always clean the unit after each use. Keep
the wood processor clean for best and safest performance. Follow instructions for
lubricating. Inspect all hydraulic seals, hoses and couplers for leaks prior to use.
Control levers and power switch must be kept clean, dry and free from oil and
grease at all times.
•
PROTECT THE ENVIRONMENT
Take used oil to an authorized collection point or follow the stipulations in the
country where the wood processor is used. Do not discharge into drains, soil or
water.
•
MAKE THE WORKSHOP CHILDPROOF
Lock the shop. Store the wood processor away from children and others not
qualified to use it.

8
•
DEAL WITH ACCIDENT
Always have a fire extinguisher and a first aid kit available for use should the need
arise. In emergency always know the location of the nearest phone or keep a phone
on the job site. Also know the phone numbers of the nearest ambulance, doctor and
fire department. This information will be invaluable in the case of an emergency.
•
SPECIAL WARNING
•
The splitting operation of the machine is designed to be activated by one person.
While there is the possibility that additional operators could be working with the
machine (e.g. for loading and unloading), only one operator should activate
splitting operations;
•The machine shall not be used by children;
•Description of functional tests of the machine;
•The installation and maintenance requirements including a list of those devices
e.g. two-hand control device which should be verified, how frequently the
verification shall be carried out and by what method.
SPECIFICATIONS
Model
number
65638
Trade Name
VARIMATIC 300
Splitter Motor
5000 W 400 V 3~ 50 Hz
9,1 A S6 40 % IP54
Splitting Force
7 ton ± 10 %
Splitting
Capacity
Diameter
5-30 cm
Length
20-55 cm
Hydraulic Pressure
17,8 MPa
Hydraulic Oil Capac
ity
18 l
Ram Travel
94,5 cm
Speed
Forward
32 cm/s
Retract
110 cm/s
Chain Saw Motor
4000 W 400 V 3~ 50 Hz
7 A S6 40 % IP54
Cutting
Capacity
Diameter
5-30 cm
Length
30-110 cm
Noise Pressure Level (LpA)
≤109 dB (A)
Vibration
3 m/s
2
Overall Sizes
(LxWxH)
289 x 93 x 165 cm
Weight
353 kg
* S6 40%, continuous operation periodic duty: time of one load cycle is 10 minutes,
operation time at constant load is 4 minutes, operation time at no-load is 6 minutes.
APPLICATION CONDITIONS
This wood processor is designed for operating under ambient temperatures between
+5°C and +40°C and for installation at altitudes not more than 1000 m above M.S.L.
The surrounding humidity should be less than 50 % at 40°C. It can be stored or
transported under ambient temperatures between –25°C and +55°C.

9
ELECTRICAL REQUIREMENTS
With 3 phase 400 Volt / 50 Hz motor, the wood processor should be connected to
standard 400 V ± 10 % / 50 Hz ± 1 Hz electrical supply which has protection devices
of under-voltage, over-voltage, over-current as well as a residual current device
(RCD) with maximum residual current rated at 0,03 A.
The mains connection and extension cable must have 5 wires = 3P + N + PE
(3/N/PE). The mains connection must have maximum 8 (saw) / 10 (splitter) A fuse.
Electrical connection rubber cables must comply with IEC 60245, which are always
marked with symbol H 07 RN. Cables should be identified, as it is a legal
requirement. The cable is not supplied with the machine.

10
CONTENTS SUPPLIED
1. Main body
2. Protecting wire net
3. Transport wheel
4. Side rail
5. Wheel shaft
6. Nose wheel
7. Support leg
8. Bent bar
9. Log lock handle
10. Processor coupler assembly
11. Connecting piece
12. Operator’s manual
13. Hardware bag
ASSEMBLY
Following the assembly directions below, you will assemble the wood processor in a
few minutes.

11
The processor can be lifted with ropes
suitable to support its weight. When
lifting the machine, firmly tie up the ropes
at work table (1) and tail plate (2).
When the processor is
lifted, there is a danger of
its falling down.
Therefore, never come
too close.
Insert the wheel shaft (3) to square tube
sleeve (4) as shown. Secure the
transport wheels (5) on both sides of the
wheel shaft with two washers and M20
lock nuts. Adjust the transport wheels on
both sides of the chassis (6) to a proper
position and secure the wheel shaft on
square tube sleeve with two M10x25
bolts and M10 lock nuts.

12
Loosen the locking handles (7) in the
anticlockwise direction. Install the
support legs (8) to U-clamps (9). Fasten
the locking handles in the clockwise
direction. Lower the machine on the
ground and release the ropes. Loosen
the locking handles in the anti-clockwise
direction to adjust the support legs on
the same level of the transport wheels
until processor is level. Fasten the
locking handles in the clockwise
direction.
The support legs can be
lowered to stand on the
ground during the work
and lifted to the air during
the transportation.
Fasten the connecting piece (10) to the
front stand with M10x60 bolts (11), M10
lock nuts and washers (12).
Install the nose wheel (13) to U-clamp
(14) and adjust it on the same level of
the transport wheels and support legs.
Fasten the locking handle in the
clockwise direction.
The nose wheel can be
lowered to the ground for
minor moving of the
processor and should be
lifted to the air during the
work and transportation.

13
Unfold the roller conveyor (15)
horizontally and fix the support stands
(16) to square tube sleeves (17) as
shown.
Fix the bent bar (18) to machine case
and machine body with three pieces of
M16x10 screws as shown.
Insert the side rail (19) to U-type groove
and fix it. Fasten the protecting wire net
(20) onto the side rail (19) with washers,
bolts and nuts.

14
Install the processor coupler assembly
(21) into the connecting piece. Line up
the holes in the processor coupler
assembly and the connecting piece.
Insert the clevis pin (22) through the
holes in the processor coupler assembly
and the connecting piece. Insert lock pin
through the hole in the clevis pin to
secure it.
The installation of the
processor coupler
assembly is only
necessary for
transportation. It should
be detached from the
processor in work.
DELIVERING WOOD PROCESSOR TO WORK SITE
For long-distance transportation, complete the installation of the processor coupler
assembly. Connect the coupler to tow vehicle’s trailer hitch. Lift the support legs and
nose wheel to the air and drive tow vehicle to work site. Please pay attention that
nose wheel should be off the ground during transportation. Position the processor in
the selected location and then disconnect the coupler from tow vehicle’s trailer hitch.
Drive tow vehicle clear. Detach the processor coupler assembly. Adjust the support
legs until processor is level.
The machine is not approved for travelling on roads and public
areas. Transportation of the machine using a towing vehicle is not
permitted on roads and public areas.
For minor moving at work site, lower the nose wheel to the ground and lift the support
legs off the ground. Move the processor by nose wheel and transportation wheels for
relocation. And then adjust the support legs until processor is level and lift the nose
wheel off the ground. Block the transportation wheels firmly so the processor cannot
roll in either direction.
OPERATION
Plan your work site. Work safely and save effort by planning your work beforehand.
Have your logs positioned where they can be easily reached. Have a site located to
stack the split wood or load it onto a nearby truck or another carrier. Position the
wood processor on solid level ground.
Applying a thin coat of grease to the surfaces of the ram before operation will
lengthen the durability of the ram.

15
Test whether the emergency stop switch functions properly. Once the emergency
stop switch is pushed down, pressing down the button switches on the log lock
handle and the log saw handle simultaneously cannot activate the rotation of the
chain saw to cut wood and pushing down the cylinder control switch on the electric
box cannot activate the push block into forward stroke to split wood, although the
machine is still in power.
Turn the emergency stop switch in the clockwise direction and return to its original
position. Press down both of the button switches simultaneously, and the chain saw
returns to its normal cutting rotation. Push down the cylinder control switch on the
electric box, the push block returns to its normal splitting movement.
Bleed the air out of the hydraulic system
before starting the wood processor. The cover
of the hydraulic oil tank should be loosened
by some rotations until air can go in and out of
the oil tank smoothly.
Air flow thru the oil tank filler should be
detectable during the operations.
Before moving the wood processor, make
sure the cover of the oil tank is tightened to
avoid oil leaking from this point.
FAILED TO LOOSEN THE OIL TANK COVER WILL KEEP THE
SEALED AIR IN HYDRAULIC SYSTEM BEING COMPRE
SSED
AFTER BEING DECOMPRESSED. SUCH CONTINUOUS AIR
COMPRESSION AND DECOMPRESSION WILL BLOW OUT
THE SEALS OF THE HYDRAULIC SYSTEM AND CAUSE
PERMANT DAMAGE TO THE WOOD PROCESSOR.
Turn the motor switch to the ON position to start the wood processor. To stop the
machine, just turn the motor switch to the OFF position.
Make sure the direction of motor
rotation is correct. Turn the motor
on and hold the log saw handle
and the log lock handle
respectively with each hand and
press down the button switches
C/D on both handles
simultaneously to activate the
rotation of the chain saw.
If no rotation motion is detected
after the motor starts, power off the
motor immediately to change motor polarity by turning the pole switching device
inside the plug with a screwdriver.

16
400 V 3N
Never allow motor running at counter direction. This will damage
the pump and will void the warranty.

17
1. Test whether the emergency stop switch functions properly. Once the
emergency stop switch is pushed down, pressing down the button switches on
the log lock handle and the log saw handle simultaneously cannot activate the
rotation of the chain saw to cut wood and pushing down the cylinder control
switch on the electric box cannot activate the push block into forward stroke to
split wood, although the machine is still in power.
2. Turn the emergency stop switch in the clockwise direction and return to its
original position. Press down both of the button switches simultaneously, and
the chain saw returns to its normal cutting rotation. Push down the cylinder
control switch on the electric box, the push block returns to its normal splitting
movement.
3. After assembly, make sure that all the parts are tight to exclude dangerous
factors.
4. Take the use of the correct power supply and cables. Put the plug in the
socket and turn on the motor switch. Close the steel mesh, insert the key (part
of the steel mesh) into the limit switch A for steel mesh, hook the steel mesh.
5. Place the log on the roller conveyor and adjust the log cut length by the cut-off
length gauge. Hold the log saw handle and the log lock handle respectively
with each hand and press down the button switches C/D on both handles
simultaneously to activate the rotation of the chain saw. Press down evenly
until the log is sawed and dropped right into position in the splitting area.
Release the button switches C/D to stop the chain saw which returns to its
original position automatically.
Do not start the day with a dull or damaged chain. If the chain is
loose, turn the chain tension bolt in the clockwise direction to
tighten it. Grease the chain saw mount every 4 to 6 hours of
operation.

18
6. Lock the cross wedge to the proper position by the wedge adjusting handle
and the wedge lock handle based on the log’s size. Check whether the sawed
log that drops into the splitting area needs to be repositioned. If necessary,
open the steel mesh to place the sawed log to the proper position for splitting
and then hook the steel mesh to hold down the limit switch.
7. Push down the cylinder control switch on the electric box and activate the
hydraulic driven push block into forward stroke. The log is pushed against the
cross wedge which splits the log in 4 sticks. After forward stroke is completed,
the push block returns to fully retracted position automatically, which activates
the limit switch B for cylinder backstroke to make the hydraulic system idle.
Take off the split log and clean the splitting area.
Applying a thin coat of grease to the surfaces of the push block
before operation will lengthen the durability of the push block.
Good maintenance keeps the push block sliding smoothly for
efficient operation and reduced wear.
Log splitter is equipped with auto cycle valve for hands-free
operation. With auto-cycle valve engaged, splitter automatically
completes forward stoke and returns to fully retracted position.
Stay clear of the wedge area once a log begins to split.
Keep hands away from the splitter during the return stroke.
8. Continue next cycle until the work is accomplished. To stop the machine,
detach the key and open the steel mesh. Turn the motor switch off and put the
plug out of the socket and clean the machine with cloth.
Stack as you work. This will provide a safer work area, by keeping it uncluttered, and
avoid the danger of tripping, or damaging the power cord.
Accumulated split wood and wood chips can create a hazardous
work environment. Never continue to work in a cluttered work
area which may cause you to slip, trip or fall.

19
FREE A JAMMED LOG
Open the main steel mesh, dismantle the protecting wire net and take out the
jammed log and cross wedge.
Knock the jammed log with a hammer off the cross wedge.
Put the cross wedge into the groove.
REPLACING OIL
The hydraulic system is a closed system with oil tank, oil pump and control valve.
Low oil levels can damage the oil pump.
Check oil level regularly with dipstick. The oil should be completely changed once a
year.
Following hydraulic oils or equivalent are recommend for the wood processor’s
hydraulic transmission system:
SHELL Tellus 22
MOBIL DTE 11
ARAL Vitam GF 22
BP Energol HLP-HM 22
Mogul/Paramo OTHP 3

20
Use a drain pan to aid in the removal of all used oil and particles.
Dismantle hydraulic oil filter to take out filter net, lift nose wheel, and place a drain
pan under oil outlet to drain oil from the hydraulic transmission system. Examine oil
for metal chips as a precaution to future problems.
Plan to replace hydraulic filters every 150 hours of operation
(roughly monthly).
Changing hydraulic oil filter regularly can help keep the processor
running well and reduce downtime.
Read dipstick to determine
the maximum and minimum
of the oil level. Low oil can
damage the oil pump.
Overfilling can result in
excessive temperature in the
hydraulic transmission
system.
Apply sealant to filler plug and reinstall it.
Following an oil change, activate the wood processor a few times without actually
cutting or splitting.
MAINTENANCE
Maintaining your wood processor will insure long life to the machine and its
components.
Table of contents
Popular Computer Hardware manuals by other brands
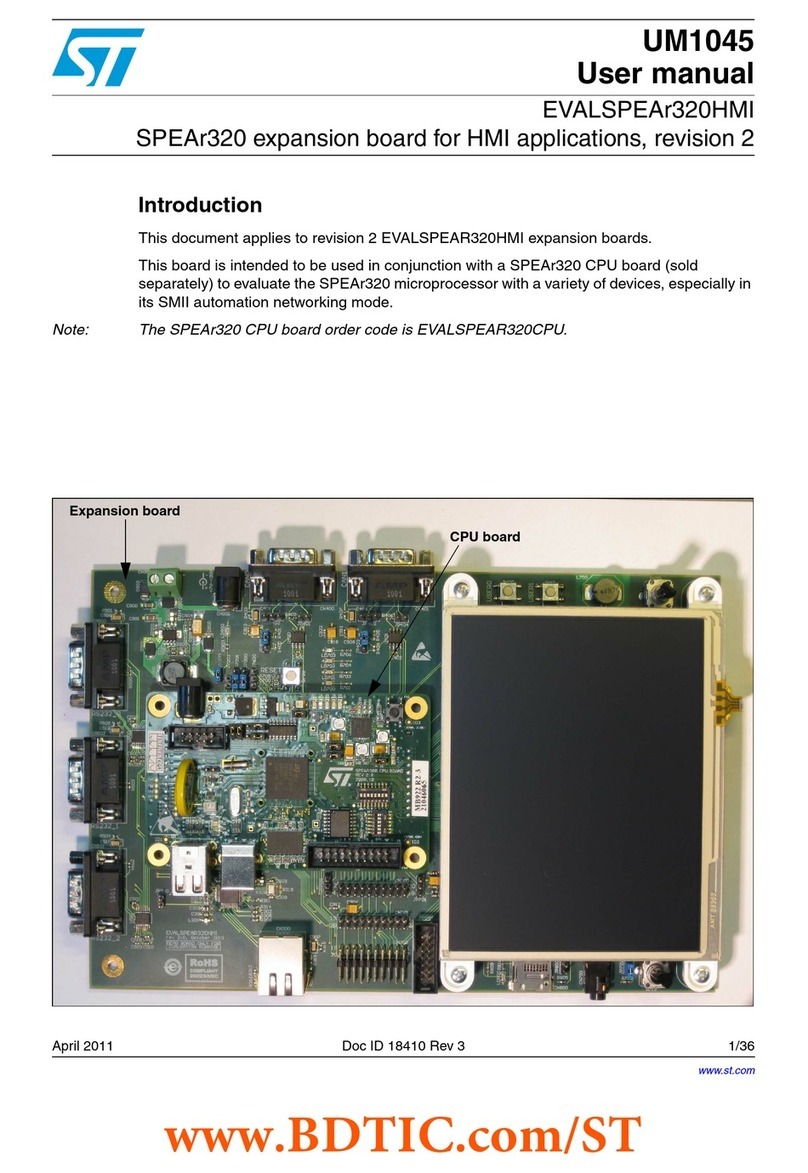
ST
ST EVALSPEAr320HMI user manual
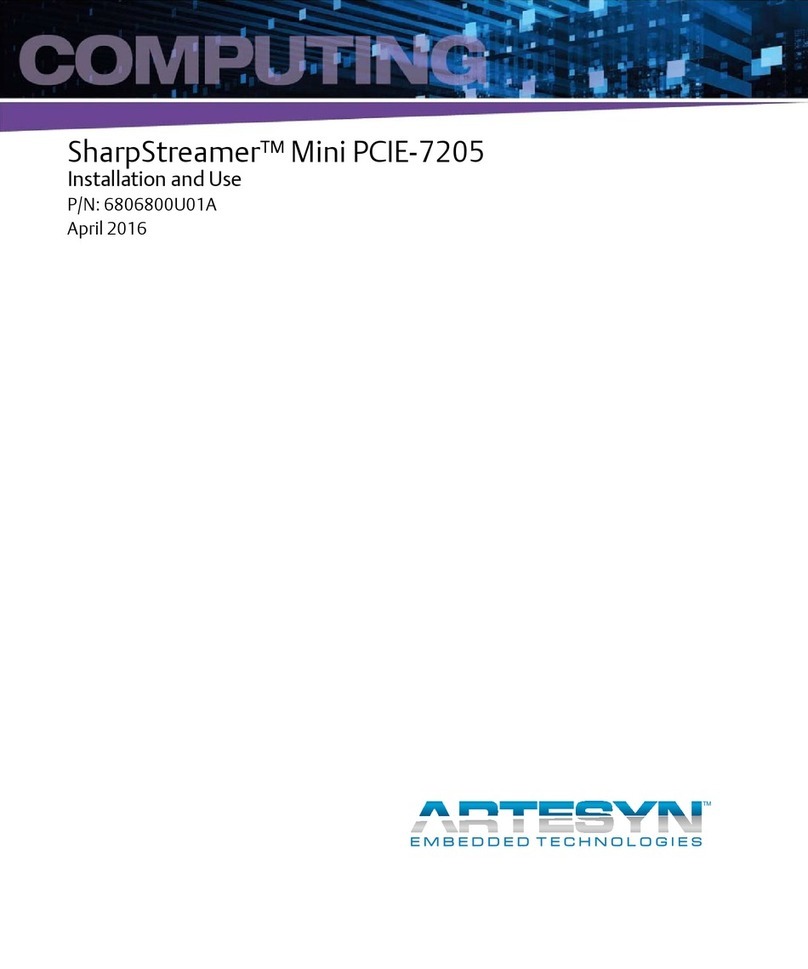
ARTESYN EMBEDDED TECHNOLOGIES
ARTESYN EMBEDDED TECHNOLOGIES SharpStreamer Mini PCIE-7205 Installation and user
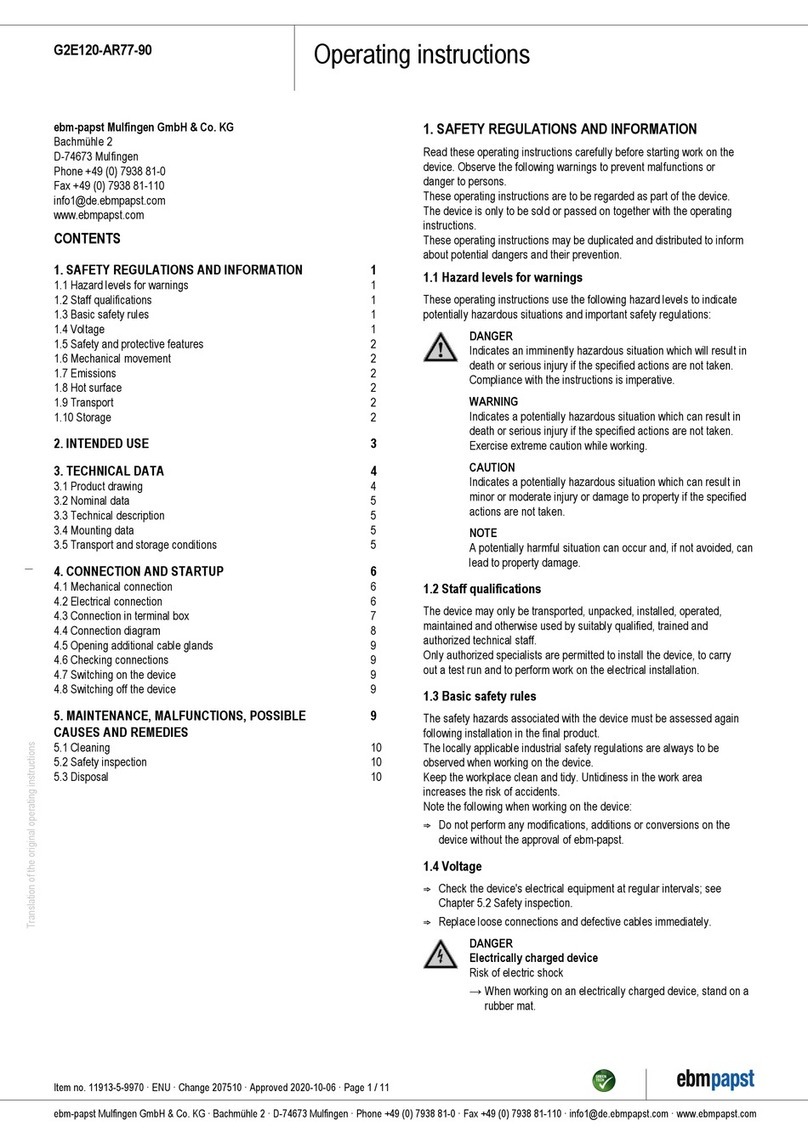
Ebmpapst
Ebmpapst G2E120-AR77-90 operating instructions
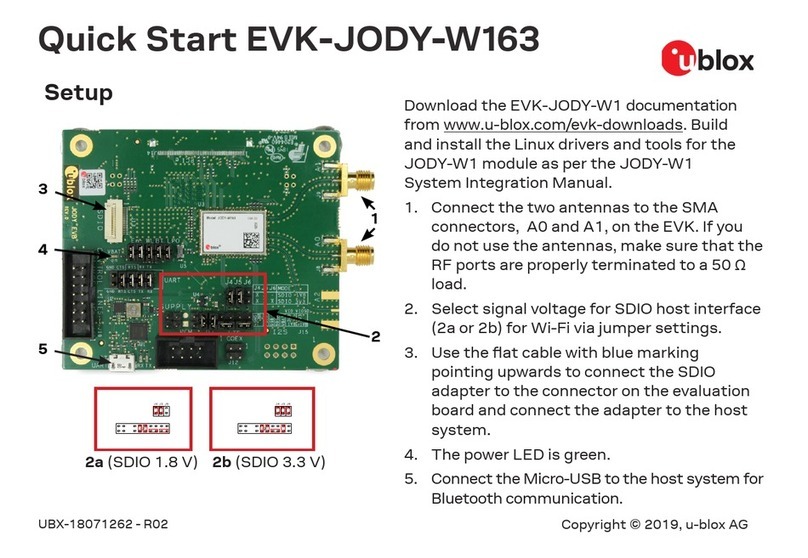
Ublox
Ublox EVK-JODY-W163 quick start
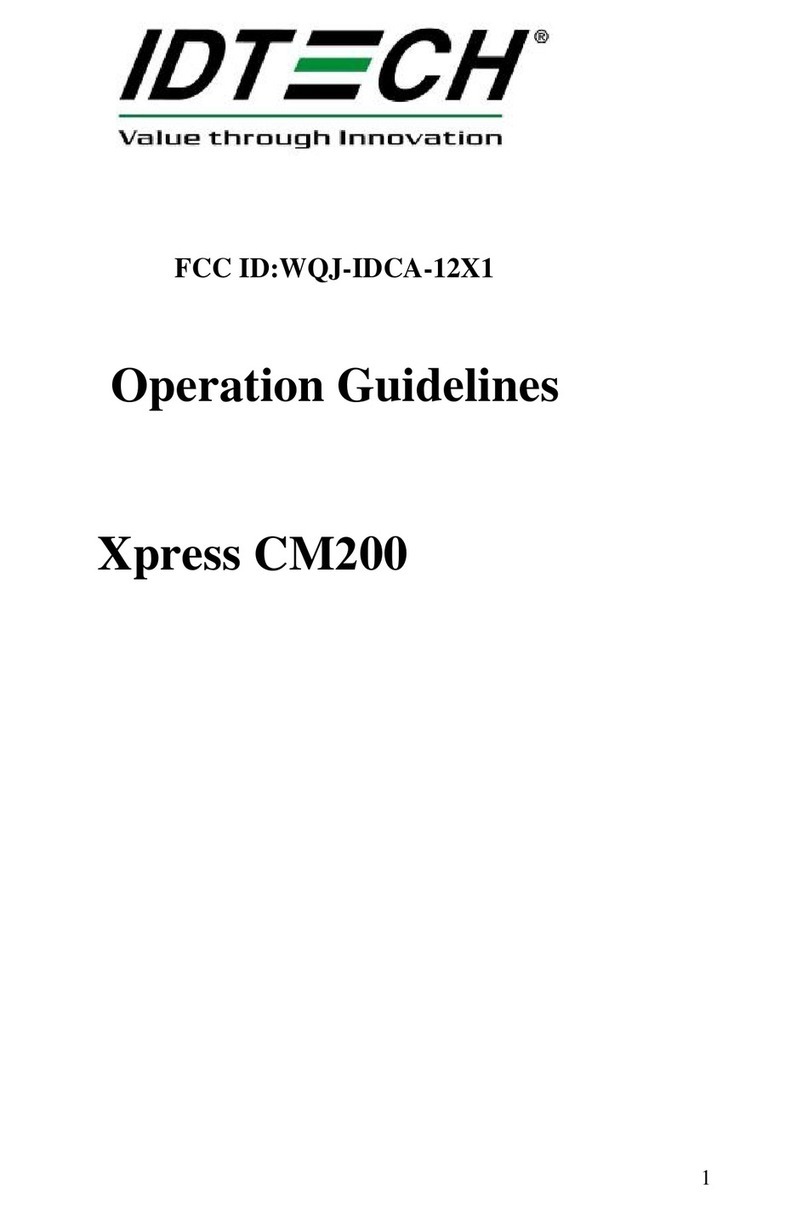
IDTECH
IDTECH Xpress CM200 Operation guidelines
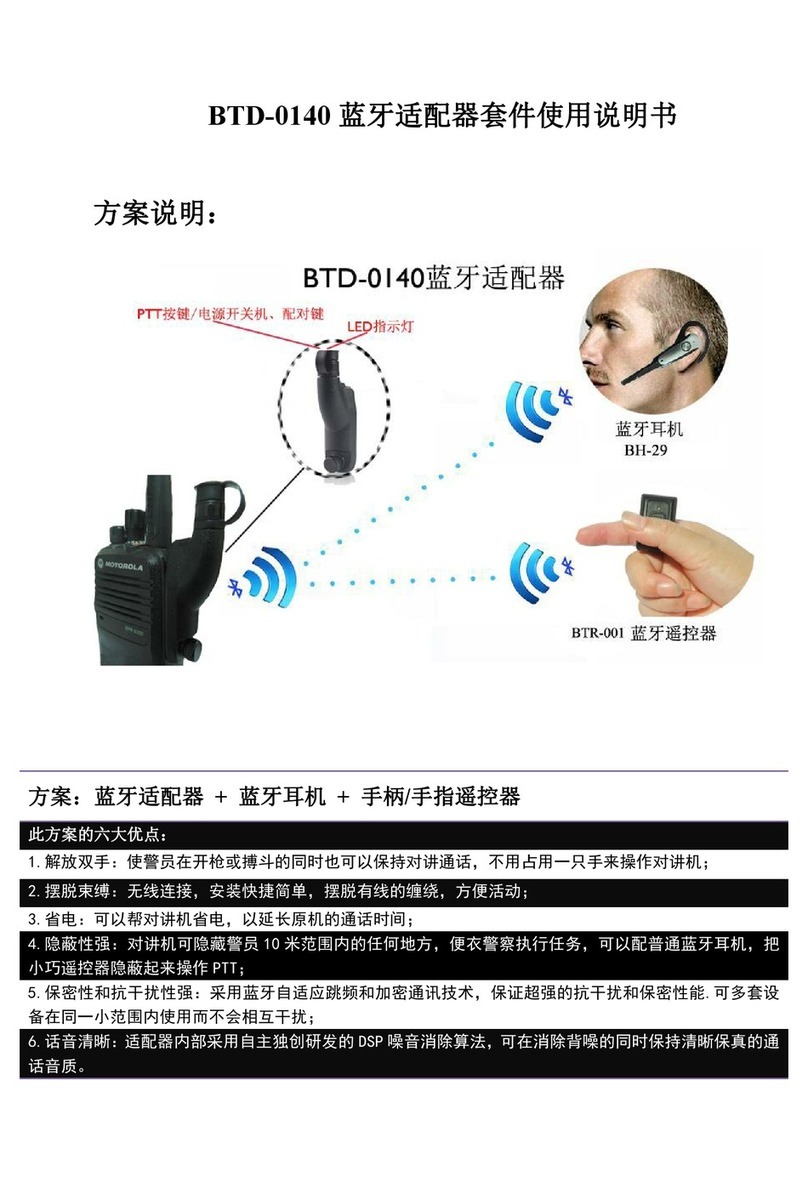
Global Sources
Global Sources BTD-0140 user manual