VC VC20 series User manual

Vision
Components®
The Smart Camera People
VC20XX Operating Manual
Hardware Specifications and special Software Functions of
VC20XX Smart Cameras
Revision 2.2 October 2007
Document name: VC20XX_HW.pdf
©Vision Components GmbH Ettlingen,
Germany

VC20XX Operating Manual
II
Foreword and Disclaimer
This documentation has been prepared with most possible care. However Vision Components GmbH
does not take any liability for possible errors. In the interest of progress, Vision Components GmbH
reserves the right to perform technical changes without further notice.
Please notify support@vision-components.com if you become aware of any errors in this manual or
if a certain topic requires more detailed documentation.
This manual is intended for information of Vision Component’s customers only. Any publication of this
document or parts thereof requires written permission by Vision Components GmbH.
Trademarks
Code Composer Studio and TMS320C6000, Windows XP, Total Commander, Tera Term, Motorola
are registered Trademarks. All trademarks are the property of their respective owners.
References
Since the VC4XXX smart camera family employs a TI processor, the programming environment and
functions for the VC20XX cameras can be used for this camera.
Further References under “Support + Download” on www.vision-components.com:
„Support News“– for up to date information on VC Software and Documentation.
„Knowledge Base / FAQ“ - searchable Database with latest software developments, frequently asked
questions and demo programs.
“Download Areas” for all documentation and Software downloads – refer to the following table:
Description Title on Website Download Area
Schnellstart VC . Schnellstart VC Smart
Kameras Registered User Area
Getting Started VC SDK TI
Getting Started VC Smart Cameras
.Getting Started VC Smart
Cameras Registered User Area
Getting Started VC SDK TI
Introduction to VC Smart Camera
programming Programming Tutorial for
VC20XX and VC40XX Cameras
Registered User Area
Getting Started VC SDK TI
Demo programs and sample code
used in the Programming Tutorial Tutorial_Code Registered User Area
Getting Started VC SDK TI
VC4XXX Hardware Manual VC4XXX Smart Cameras
Hardware Documentation
Public Download Area Hardware
Documentation VC Smart Cameras
VCRT Operation System Functions
Manual VCRT 5.0 Software Manual Registered User Area Software
documentation VC Smart Cameras
VCRT Operation System TCP/IP
Functions Manual VCRT 5.0 TCP/IP Manual Registered User Area Software
documentation VC Smart Cameras
VCLIB 2.0 /3.0 Image Processing
Library Manual VCLIB 2.0/ 3.0 Software
Manual Registered User Area Software
documentation VC Smart Cameras
The Light bulb highlights hints and ideas that may be helpful for a development.
This warning sign alerts of possible pitfalls to avoid. Please pay careful attention to sections
marked with this sign.
!
©1996-2007 Vision Components GmbH Ettlingen, Germany VC20XX_HW.pdf

VC20XX Operating Manual
III
Table of Contents
1General Information 1
1.1 Overview Camera Types 2
2Basic Structure 4
3Boards 5
3.1 Sensor Boards 5
3.1.1 C6SEN084 6
3.1.2 C6SEN204 6
3.1.3 C6SEN205 7
3.1.4 C6SEN311 7
3.1.5 C6SEN415 8
3.2 CPU Board 8
3.3 DAC Board 9
3.4 Power Board 10
4PLC I/O Signals 11
4.1 Input Signals 11
4.2 Output Signals 12
4.3 Trigger input and trigger output 12
5Pin Assignments Camera Interfaces 14
5.1 Pin Assignment Trigger / Keypad Plug Signal 14
5.2 Pin Assignment for the I/O Plug 14
5.3 Pin Assignment for the RS232 (V24) 15
5.4 Pin Assignment LAN/Ethernet 15
5.5 Pin Assignment for the XGA/SVGA Video Output 15
6Technical Specifications VC20XX Smart Cameras 16
6.1 Technical Specifications VC2028 16
6.2 Technical Specifications VC2038 17
6.3 Technical Specifications VC2038/E 18
6.4 Technical Specifications VC2048/E 19
6.5 Technical Specifications VC2065 20
6.6 Technical Specifications VC2065/C 21
6.7 Technical Specifications VC2065/E 22
6.8 Technical Specifications VC2065/EC 23
6.9 Technical Specifications VC2066 24
6.10 Technical Specifications VC2066/E 25
6.11 Technical Specifications VC2068 26
6.12 Technical Specifications VC2068/E 27
7Accessories 28
7.1 Trigger Cable 28
7.2 RS232(V24) Cable 28
©1996-2007 Vision Components GmbH Ettlingen, Germany VC20XX_HW.pdf

VC20XX Operating Manual
IV
7.3 Ethernet patch cable 29
7.4 Power / PLC Cable 29
7.5 SVGA Monitor Cable 29
7.6 Power adapter 30
7.7 Power adapter for rail mounting 30
7.8 VC Keypad C6 30
7.9 Y-cable 30
8Connecting the Camera 31
8.1 Connecting the camera power 31
8.1.1 Single voltage, with or without PLC signals, no shutdown: 31
8.1.2 Shutdown Function for VC20XX Smart Cameras 32
8.2 Connecting the RS232 Interface 33
8.2.1 Connecting a compatible PC with a 9-pin D sub plug 33
8.3 Connecting the Ethernet Cable 33
8.4 Connecting the VC keypad 33
8.5 Connecting the external trigger 34
8.6 Connecting the external trigger and the VC keypad 34
9Programming 35
Appendix A: Blockdiagram VC20XX Smart Cameras A
Appendix B: Housing Dimensions VC20XX Smart Cameras B
Appendix E: Drawing Camera Head VC40XX C
Appendix C: Spectral Transmission of IR Filter D
Appendix D: CE Compliance of VC20XX Smart Cameras E
INDEX G
©1996-2007 Vision Components GmbH Ettlingen, Germany VC20XX_HW.pdf

VC20XX Operating Manual
1
1 General Information
The VC20xx Series smart cameras are compact, light-weight black-and-white or color video cameras
with video memory and an image processor.
They integrate a high-resolution CCD sensor with one of the fastest 32 bit image-processing signal
processors (TMS320C6211). SDRAM memory is used to store program code, data and video images.
Interfaces allow communication with the outside world. The cameras set standards for performance
and integration density.
These cameras are built for industrial deployment. High goals were set as regards the image
resolution, the computational speed, the sturdiness of the casing, and the electromagnetic
compatibility, as mere examples. The cameras are insensitive to vibrations and shocks, while
permitting precise measurements and tests. They are ideally suited as OEM cameras for mechanical
engineering applications.
Only one supply voltage is required to operate the cameras (24 volts). An image processing system or
a PC with a frame grabber board is not necessary. Simple control problems can even be implemented
with the integrated process interfaces. For more complex control tasks, the cameras can be connected
to a PLC.
This documentation describes the camera hardware. However, in many cases the software
documentation is decisive. For this, please consult the software manuals.
©1996-2007 Vision Components GmbH Ettlingen, Germany VC20XX_HW.pdf

VC20XX Operating Manual
2
1.1 Overview Camera Types
All VC20XX Cameras contain the following features:
-16 MB SDRAM
-2 MB Flash Eprom
-8 bit overlay (translucent overlay possible)
-integrated 4 Digital Inputs, 4 Digital Outputs, 24V
-Texas Instruments CPU TMS 320C62XX; 1200MIPS
-Low speed shutter up to 10 seconds
-Programmable gain and offset
-24V Power Supply
The following table shows the different features of each camera model:
VC20XX SELECTION
TABLE VC2028 VC2038
VC2038E VC2048E VC2065
VC2065E V2065C
VC2065CE VC2066
VC2066E VC2068
VC2068E
Sony 1/3" Progressive Scan
CCD640x480 pixel
Kodak 1/3" Progressive
Scan CCD 640x480 pixel
Sony 1/2" Progressive Scan
CCD 782x582 pixel
Sony 1/3" Progressive Scan
CCD 1024x768 pixel
Sony 1/2" Progressive Scan
CCD 1280x1024 pixel
14 Hz full Frame, 28 Hz 2x
Binning
17 Hz full Frame, 34 Hz 2x
Binning
25 Hz full Frame
40 Hz full Frame
45 Hz full Frame
110 Hz full Frame
Color
16 MB Multimedia Card
SVGA (800x600 Pixel)
output, noninterlaced
SXVGA (1280x1024 Pixel)
output, noninterlaced
©1996-2007 Vision Components GmbH Ettlingen, Germany VC20XX_HW.pdf

VC20XX Operating Manual
3
VC20XX SELECTION
TABLE VC2028 VC2038
VC2038E VC2048E VC2065
VC2065E V2065C
VC2065CE VC2066
VC2066E VC2068
VC2068E
integrated Fast Trigger
contact (external contact) 1)
High speed shutter down to
33 microseconds
High speed shutter down to
9 or 10 microseconds
High speed shutter down to
5 microseconds
RS232 up to 115.200 Baud
(optional)
Fast Ethernet 100MBit
(optional) 2)
Size: 110x50x36mm+foot/
Weight: 488g 3)
1) The use of the VC2028 is recommended for imaging static (non moving) objects only.
2) If ordering a camera with Ethernet interface please add the suffix "/E" to the camera name (i.e.
VC38/E, VC2065/EC).
3) Dimension of housing VC2048: 111x80x36 + mounting plate, weight: 516g
©1996-2007 Vision Components GmbH Ettlingen, Germany VC20XX_HW.pdf

VC20XX Operating Manual
4
2 Basic Structure
The image is formed by a high-resolution progressive scan CCD sensor. One or two channels of video
output are digitized. An input lookup-table is available for basic pixel-preprocessing. The image is
stored in SDRAM memory using one of the 16 DMA channels (EDMA).
The video and graphics display on the monitor is performed in a very similar way: Data is stored in the
main SDRAM memory, either due to a previous video capture or to computing by the DSP. Graphics
data is then transferred to the graphics refresh buffer (SGRAM). This may happen periodically or on
demand. The SGRAM is read out at a fast refresh rate to provide a high-quality, flickerfree display.
A dual 3x256x8 output lookup-table gives you abundant choices for the appearance of images and
graphics.
The video capture and graphics output channels are completely independent. The storage area for
each may be chosen to be identical (necessary for live image display) or completely different. If the
latter is chosen, you may capture an image "in the background" while displaying a completely different
one.
The TMS320C6211 DSP is one of the fastest 32 DSPs. It features a RISC-like instruction set, up to 8
instructions can be executed in parallel, two L1 cache memories (4KBytes each) and a 64 KByte L2
cache on chip. Its high speed 16-channel DMA controller gives additional performance. The DSP uses
fast external SDRAM as main memory. A flash EPROM and a built-in multi-media card provide non-
volatile memory.
See Appendix A: Blockdiagram VC20XX Smart Cameras.
©1996-2007 Vision Components GmbH Ettlingen, Germany VC20XX_HW.pdf

VC20XX Operating Manual
5
3 Boards
The electronic circuitry of the camera contains four printed curcuit boards (PCB).
The following presents an overview of the boards:
Description Designation Function
Sensor boards C6SEN084, C6SEN204
C6SEN205, C6SEN311
C6SEN415
CCD sensor, driver & controller,
digitization of the video signal, black-
and-white and color versions
CPU board C6CPU TMSC6211 signal processor with
SDRAM, FLASH memory, multi-media
card adaptor
DAC board C6DAC SVGA quality video output with graphics
memory, video capture, interfaces
(RS232, etc.)
Power board C6PWR Power supply, PLC interfaces
3.1 Sensor Boards
Camera Type Sensor Board
VC2028 C6SEN084
VC2038 C6SEN084
VC2038/E C6SEN084
VC2048/E C6SEN311
VC2065 C6SEN415
VC2065/E C6SEN415
VC2065/C C6SEN415
VC2065/EC C6SEN415
VC2066 C6SEN204
VC2066/E C6SEN204
VC2068 C6SEN205
VC2068/E C6SEN205
©1996-2007 Vision Components GmbH Ettlingen, Germany VC20XX_HW.pdf

VC20XX Operating Manual
6
3.1.1 C6SEN084
This board takes the picture. It is used in the VC2028, VC2038 and VC2038/E
The CCD sensor 1/3" SONY ICX424AL (B/W) is used. The board controls the CCD sensor and
processes the analog signal.
The progressive scan type CCD sensor used is ideally suited for industrial machine vision tasks. In
contrast to the conventional technique it provides the following features:
•1/3" sensor
•resolution: 640x480 pixels
•square pixel format, 7.4(H) x 7.4(V) µm
•full-frame shutter
•can be triggered externally (except VC2028)
•sensor read out in full-frame mode (non-interlaced)
•shutter speed down to 30,80,... µsec in steps of 50 microseconds up to 20 sec
•40fps @ 640x480 (VC2028 : 25fps@640x480)
•CCD processors providing CDS, programmable gain and offset, auto black level
compensation and 10 bit AD-conversion
The diverse features of this board (high-speed and low-speed shutter, external trigger, etc.) are
configured via software.
For the exact setting of the configuration, refer to the description of the configuration program in the
software documentation.
3.1.2 C6SEN204
This board takes the picture. It is used in the VC2066 and VC2066/E
The CCD sensor ICX204AL (B/W) is used. The board controls the CCD sensor and processes the
analog signal.
The progressive scan type CCD sensor used is ideally suited for industrial machine vision tasks. In
contrast to the conventional technique it provides the following features:
•1/3" sensor
•higher resolution: 1024x768 pixels
•square pixel format, 4.64 µm
•full-frame shutter
•can be triggered externally
•sensor read out in full-frame mode (non-interlaced)
•shutter speed down to 10 µsec and up to 20 sec
•16fps @ 640x480 or 2 x binning @ 32fps
•CCD processors providing CDS, programmable gain and offset, auto black level
compensation and 10 bit AD-conversion
The diverse features of this board (high-speed and low-speed shutter, external trigger, etc.) are
configured via software.
©1996-2007 Vision Components GmbH Ettlingen, Germany VC20XX_HW.pdf

VC20XX Operating Manual
7
For the exact setting of the configuration, refer to the description of the configuration program in the
software documentation.
3.1.3 C6SEN205
This board takes the picture. It is used in the VC2068 and VC2068/E
The CCD sensor ICX205AL (B/W) is used. The board controls the CCD sensor and processes the
analog signal.
The progressive scan type CCD sensor used is ideally suited for industrial machine vision tasks. In
contrast to the conventional technique it provides the following features:
•1/2" sensor
•higher resolution: 1280x1024 pixels
•square pixel format, 4.65 µm
•full-frame shutter
•can be triggered externally
•sensor read out in full-frame mode (non-interlaced)
•shutter speed down to 9 µsec and up to 20 sec
•13,75fps @ 1280x1024 or 2 x binning @ 27,5fps
•CCD processors providing CDS, programmable gain and offset, auto black level
compensation and 10 bit AD-conversion
The diverse features of this board (high-speed and low-speed shutter, external trigger, etc.) are
configured via software.
For the exact setting of the configuration, refer to the description of the configuration program in the
software documentation.
3.1.4 C6SEN311
This board takes the picture. It is used in the VC2048/E
The CCD sensor KAI0330D (B/W) is used. The board controls the CCD sensor and processes the
analog signal.
The progressive scan type CCD sensor used is ideally suited for industrial machine vision tasks. In
contrast to the conventional technique it provides the following features:
•1/2" sensor
•resolution: 640x480 pixels
•square pixel format, 9(H) x 9(V) µm
•full-frame shutter
•can be triggered externally
•sensor read out in full-frame mode (non-interlaced)
•shutter speed down to 18,36,72, µsec then steps of 36 microseconds up to 20 sec
•112fps @ 640x480 !!!
•CCD processors providing CDS, programmable gain and offset, auto black level
compensation and 10 bit AD-conversion
©1996-2007 Vision Components GmbH Ettlingen, Germany VC20XX_HW.pdf

VC20XX Operating Manual
8
The diverse features of this board (high-speed and low-speed shutter, external trigger, etc.) are
configured via software.
For the exact setting of the configuration, refer to the description of the configuration program in the
software documentation.
3.1.5 C6SEN415
This board takes the picture. It is used in the VC2065, VC2065/E, VC2065/C and VC2065/EC.
The CCD sensor ICX415AL (black-and-white) or ICX415AK (color) is used. The board controls the
CCD sensor and processes the analog signal.
The progressive scan type CCD sensor used is ideally suited for industrial machine vision tasks. In
contrast to the conventional technique it provides the following features:
•1/2" sensor
•higher resolution: 782x582 pixels
•square pixel format
•full-frame shutter
•can be triggered externally
•sensor read out in full-frame mode (non-interlaced)
•shutter speed down to 5 µsec and up to 20 sec
•double speed video capture @ 45fps
•CCD processors providing CDS, programmable gain and offset, auto black level
compensation and 10 bit AD-conversion
The diverse features of this board (high-speed and low-speed shutter, external trigger, etc.) are
configured via software.
For the exact setting of the configuration, refer to the description of the configuration program in the
software documentation.
3.2 CPU Board
The "C6CPU" Board
The TMS320C6211 DSP is one of the fastest 32 bit DSPs. It features a RISC-like instruction set, up to
8 instructions can be executed in parallel. Turthermore it features two L1 cache memories (4KBytes
each) and a 64 KByte L2 cache on chip.
The DSP uses fast external SDRAM as main memory. Up to 4 memory banks can be permanently
open providing fast access without unnecessary RAS commands.
A flash EPROM and a built-in multi-media card provide for non-volatile memory.
Most of the I/O functions (graphics display, video capture, etc.) are performed by Vision Components'
proprietary DMA Hardware without overhead for the CPU.
©1996-2007 Vision Components GmbH Ettlingen, Germany VC20XX_HW.pdf

VC20XX Operating Manual
9
The location of the SDRAM buffers for graphics display, overlay display and video capture can be
selected independently.
Identical SDRAM buffers for graphics display and video capture may be chosen to produce live video
display.
Board C6CPU
processor TMS320C6211 150MHz
SDRAM 16 Mbytes (400 MB/sec)
Flash-EPROM 2 Mbytes (16bit wide)
Multi-Media Card Adaptor 8-256 MBytes
Clock Real time clock, battery backed-up
DMA 16 independent DMA channels (EDMA) 1 very high speed
DMA (QDMA)
special features on-board temperature sensor
3.3 DAC Board
The "C6DAC" Board
The "C6DAC" board is practically the periphery for the CPU board. Here, the digital video signal from
the sensor board is the input using an input lookup-table and buffered with FIFO memory.
The board is also responsible for the SVGA graphics output. Graphics (8 bits per pixel) and overlay
data (8 bits per pixel) are stored in the on-board SGRAM. 2 independent lookup-tables for graphics
and overlay data together with a 3x8 bits D/A converter produce the RGB analog video for the SVGA
output.
The 8 bit pixel-mask register allows for individual selection of overlay planes.
Overlay data have priority over graphics data. Graphics pixels are displayed only if all unmasked
overlay bits for that pixel are zero.
Functions of the board:
•video capture with input LUT, FIFO buffer
•graphics and overlay display with 16 Mbytes refresh memory,
•2 independent LUTs for graphics and overlay, 8bit overlay mask register
•3x8bit video D/A (SVGA output)
•UART and driver for RS232 (Ethernet versions : Ethernet PHY)
•UART receiver for VC Keypad (9600 baud)
•Trigger In/Out signals
•PLC communication interface
•Status & Control Register
•Interrupt controller for CPU
•DMA Controller
©1996-2007 Vision Components GmbH Ettlingen, Germany VC20XX_HW.pdf

VC20XX Operating Manual
10
The technical specifications for the SVGA output signals :
Horizontal frequency: 45.072 kHz VBP: 32 lines
Vertical frequency: 67.68 Hz VFP: 46 lines
Resolution SVGA: 600x800 HSYNC width: 120 pixels
Resolution eff. hor.: 752 HBP: 94 pixels
Resolution eff. ver.: 582 HFP: 74 pixels
VSYNC width: 6 lines Pixel frequency: 46.875 MHz
Polarity HSYNC: positive Polarity VSYNC: positive
The technical specifications for the SXGA output signals :
Horizontal frequency: 64 kHz VBP: 37 lines
Vertical frequency: 60 Hz VFP: 2 lines
Resolution SXGA: 1280x1024 HSYNC width: 130 pixels
Resolution eff. hor.: 1280 HBP: 487 pixels
Resolution eff. ver.: 1024 HFP: 55 pixels
VSYNC width: 3 lines Pixel frequency: 125 MHz
Polarity HSYNC: positive Polarity VSYNC: positive
3.4 Power Board
The "C6PWR" Board
This board contains the power supply for the entire camera. It is also responsible for the galvanic
separation of the signals, and tailors the levels of the PLC-signals (4 inputs, 4 outputs).
The camera is supplied with a nominal voltage of 24 V (+/- 20%). An electronic stabilization of the
supply voltage is not necessary. The camera is internally galvanically separated from the supply
voltage by means of a DC/DC converter, to avoid common ground loops and electromagnetic
interference. A reverse-voltage protection diode protects the camera in case the supply voltage poles
are swapped.
An I/O processor performs PLC I/O , and also monitors PLC voltage failures and overcurrent.
©1996-2007 Vision Components GmbH Ettlingen, Germany VC20XX_HW.pdf

VC20XX Operating Manual
11
4 PLC I/O Signals
The camera has four optically decoupled inputs and four decoupled outputs for controlling machines
and processes.
An I/O processor is responsible for the handling of the PLC I/O signals.
The PLC-compatible inputs (24-V level, the positive signal is connected) include input protection
circuits. A minimum voltage of 14V is required to reliably sense a logic high signal.
The PLC outputs feature a highly integrated MOSFET, high-side switch with built-in protection . It is
possible to switch inductive or capacitive loads. The protective feature of the outputs will produce
pulses on the outputs, if the limiting values are exceeded.
A protective diode ensures, the poles of the supply voltage from the power supply of the PLC can not
be swapped. It is important to connect both the external supply voltage of the outputs (+24V) as well
as GND (GNDIn) of the power supply of the PLC.
The complete circuitry, including the I/O processor, is galvanically separated from the rest of the
camera electronics.
If DC failure of the PLC power is detected, this information is forwarded to the DSP (PLC power failure
interrupt)
Output drivers feature short circuit end thermal overload protection
For additional protection of the output drivers, the I/O processor monitors the total PLC current, and
switches off all outputs if the maximum threshold value is exceeded.
Technical data of the I/O signals:
Inputs
Outputs
Trigger input and trigger output
4.1 Input Signals
Nominal voltage: 24 V +/- 20%
Absolute maximum voltage: voltages greater than 40 V can destroy the inputs
Type: galvanically separated by optocoupler (PLC
communication interface)
Input current: 1 mA @ 24V
Threshold value: 14 V
Internal signal delay: 100 µsec (signal) + 0..200 µsec (polling) + DSP interrupt
latency
©1996-2007 Vision Components GmbH Ettlingen, Germany VC20XX_HW.pdf

VC20XX Operating Manual
12
4.2 Output Signals
Operating voltage: 24 V +/- 20%, external source
Absolute maximum voltage: voltages greater than 40 V can destroy the outputs
Type: galvanically separated by MOSFET optocouplers
Switching voltage: positive switching
Current: max. 400 mA per output
Absolute maximum current: total currents greater than 1000 mA can destroy plugs and
cables
Always consider the total sum of all output currents
Switching power: max. 9.6 W (24 V * 400 mA) per output
Reverse voltage protection yes, for external voltage
Protection against inductive
loads: yes
Resistance when switched on: 0.2 - 0.8 Ohm
Short circuit protection: full protection
4.3 Trigger input and trigger output
The board features a dedicated fast TTL trigger input (for use as image capture trigger) and a fast TTL
trigger output (as strobe-light trigger). Since both signals are fast at a very low noise margin, it is
recommended to keep the cable as short as possible. Use twisted pair or even coaxial cable for this
purpose. The trigger input has a built-in photocoupler to eliminate ground loops with the external
circuitry. The trigger output, however, is not galvanically separated. The receiving circuit should,
therefore, have a photocoupler of its own.
Please note that input and output are not protected against overcurrent. The output is neither
protected against short circuit nor reverse voltage spikes from inductive loads.
Trigger input assures constant delay without jitter.
Technical data of trigger input:
input voltage: 3-5 V (TTL, CMOS)
input current: 5mA @ 3V / 11mA @ 5V
limiting resistor: built in, 330 Ohm
knee voltage: 1.5 V
reverse voltage protection: shunt diode
switching delay: max. 2µsec + interrupt latency
Trig. In+
yellow cable
Trig. In-
green cable
330 R
©1996-2007 Vision Components GmbH Ettlingen, Germany VC20XX_HW.pdf

VC20XX Operating Manual
13
Technical data of trigger output:
output voltage: max. 7V
output current: max. 50mA
pull-up resistor: none, external resistor required
©1996-2007 Vision Components GmbH Ettlingen, Germany VC20XX_HW.pdf

VC20XX Operating Manual
14
5 Pin Assignments Camera Interfaces
The cameras have four connectors on the rear side:
RS232(V24) or
100MBd Ethernet HR10A-7R-6PB 6-pin Hirose plug pin contact
Trigger / Keypad HR10A-7R-6SB 6-pin Hirose plug jack contact
SXGA/SVGA/Video HR10A-10R-10SB 10-pin Hirose plug jack contact
DC IN/PLC-I/O HR10A-10R-12PB 12-pin Hirose plug pin contact
5.1 Pin Assignment Trigger / Keypad Plug Signal
rear view (jack):
Signal Pin
GND 3
5V Out 2
Trigger IN - 1
Trigger IN + 6
Trigger Out 5
Keypad IN 4
They Keypad IN operates with 3.3V TTL @9600 baud / 8 / N / 1
5.2 Pin Assignment for the I/O Plug
Rear view: (pin)
Signal Pin
IN0 12
IN1 4
IN2 11
IN3 10
24V IN / Cam 2
GND IN (common) 3
24V IN/ PLC 1
24V IN/ PLC 9
OUT0 8
OUT1 7
OUT2 6
OUT3 5
©1996-2007 Vision Components GmbH Ettlingen, Germany VC20XX_HW.pdf

VC20XX Operating Manual
15
5.3 Pin Assignment for the RS232 (V24)
Rear view: (pin)
Signal Pin
V24 RTS 1
V24 TxD 2
V24 GND 3
NC V24 4
V24 CTS 5
RxD 6
5.4 Pin Assignment LAN/Ethernet
Rear view: (pin)
Signal Pin
T- 1
T+ 2
- 3
- 4
R- 5
R+ 6
5.5 Pin Assignment for the XGA/SVGA Video Output
rear view (jack):
Signal Pin
G GND 1
G Out 2
R GND 3
R Out 4
VS GND 5
VS Out 6
HS GND 7
B GND 8
B Out 9
HS Out 10
©1996-2007 Vision Components GmbH Ettlingen, Germany VC20XX_HW.pdf

VC20XX Operating Manual
16
6 Technical Specifications VC20XX Smart Cameras
Technical Specifications VC2028
Technical Specifications VC2038 Technical Specifications VC2038/E
Technical Specifications VC2048/E
Technical Specifications VC2065 TechnicalSpecifications VC2065/E
Technical Specifications VC2065/C Technical Specifications VC2065/EC
Technical Specifications VC2066 Technical Specifications VC2066/E
Technical Specifications VC2068 Technical Specifications VC2068/E
6.1 Technical Specifications VC2028
Sensor: 1/3" SONY ICX424AL
eff. no. of pixels: 640(H) x 480(V)
Pixel size: 7.4(H) x 7.4(V) µm
Chip size: 5.79(H) x 4.89(V) mm
High-speed shutter: 30,80,... microseconds in steps of 50 microseconds (full-
frame shutter)
Low-speed shutter: up to 20 sec. adjustable integration time
Integration: full-frame
Picture taking: with 15msec delay, program-controlled ; full-frame / 25
frames per second, no external highspeed trigger 1
Clamping: zero offset digital clamping
A/D conversion: 15.625 MHz / 10 bit,
Input LUT 1024x8 bit (10bit →8 bit)
Image display: black-and-white, Pseudo Color from color lookup table
3x8Bit RGB:live image, still image, graphics
Overlay: 8-bit overlay with LUT, maskable
Processor: Texas Instruments TMS320C6211 signal processor 150
MHz
RAM: 16 MBytes SDRAM (synchronous dynamic RAM)
Display memory: 16 MBytes SGRAM (synchronous graphics RAM)
Memory capacity: 40 full-size images in format 640x480
Flash EPROM: 2 MBytes flash EPROM (nonvolatile memory) for
programs and data,in-system programmable, 16 bit wide
MMC: Not available
Process interface: 4 inputs / 4 outputs, optically decoupled 24 V, outputs
4x400 mA
Serial interface: V24 (RS232) max. 115200 baud
Video output: RGB, 3x75 Ohm, 1 Vpp, SVGA 800x600 output, HSYNC,
VSYNC separate
Horizontal frequency: 45.072 kHz
Vertical frequency: 67.68 Hz
Resolution SVGA: 600x800
Pixel frequency: 46.875 MHz
!
1Use VC2038 instead of VC2028 for imaging moving objects.
©1996-2007 Vision Components GmbH Ettlingen, Germany VC20XX_HW.pdf
Table of contents
Other VC Security Camera manuals
Popular Security Camera manuals by other brands

Vivotek
Vivotek IB9367-HT Quick installation guide
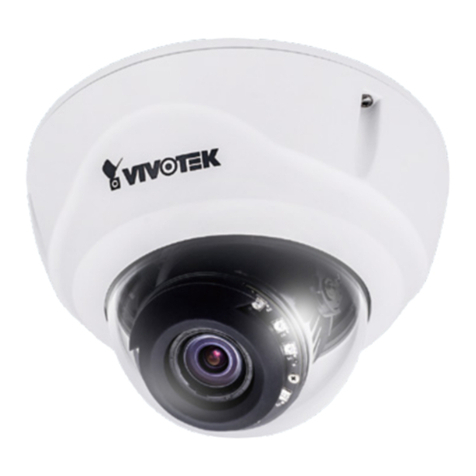
Vivotek
Vivotek V Series Quick installation guide
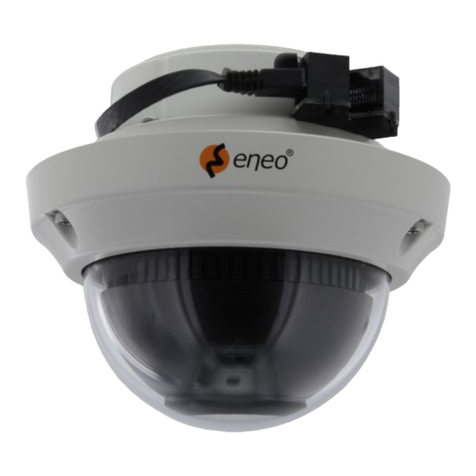
Eneo
Eneo IPD-72M2713MAA Quick installation guide
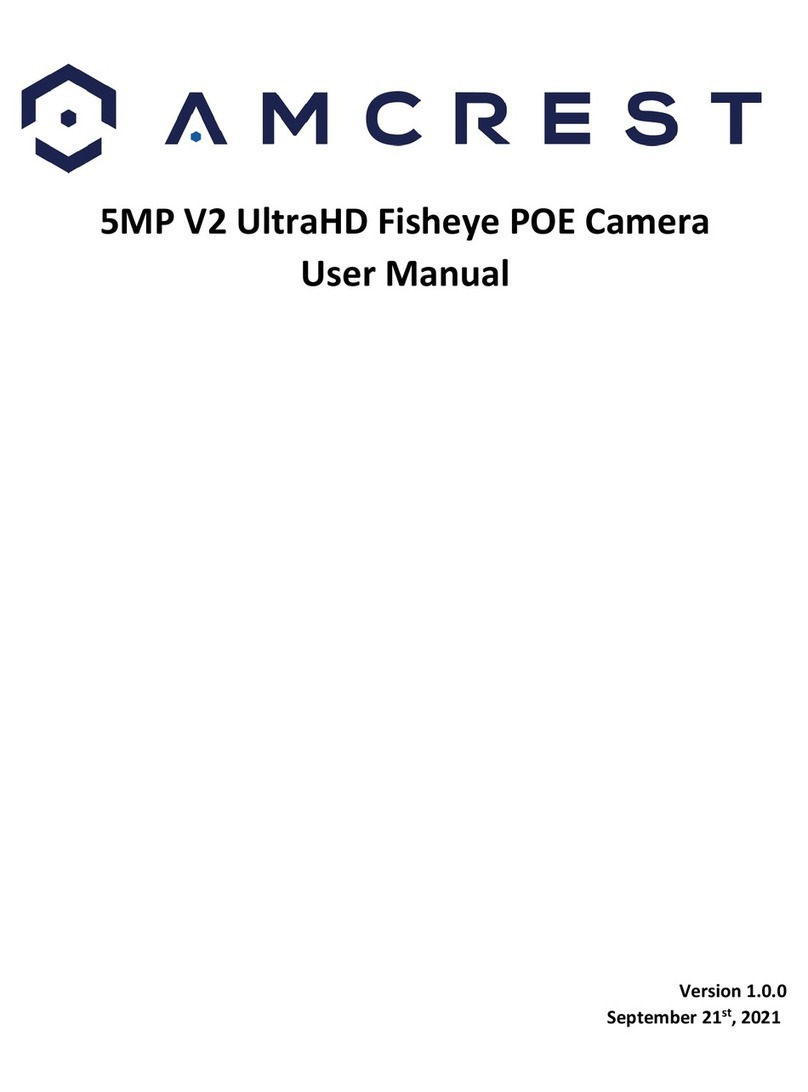
Amcrest
Amcrest IP5M-F1180EW-V2 user manual
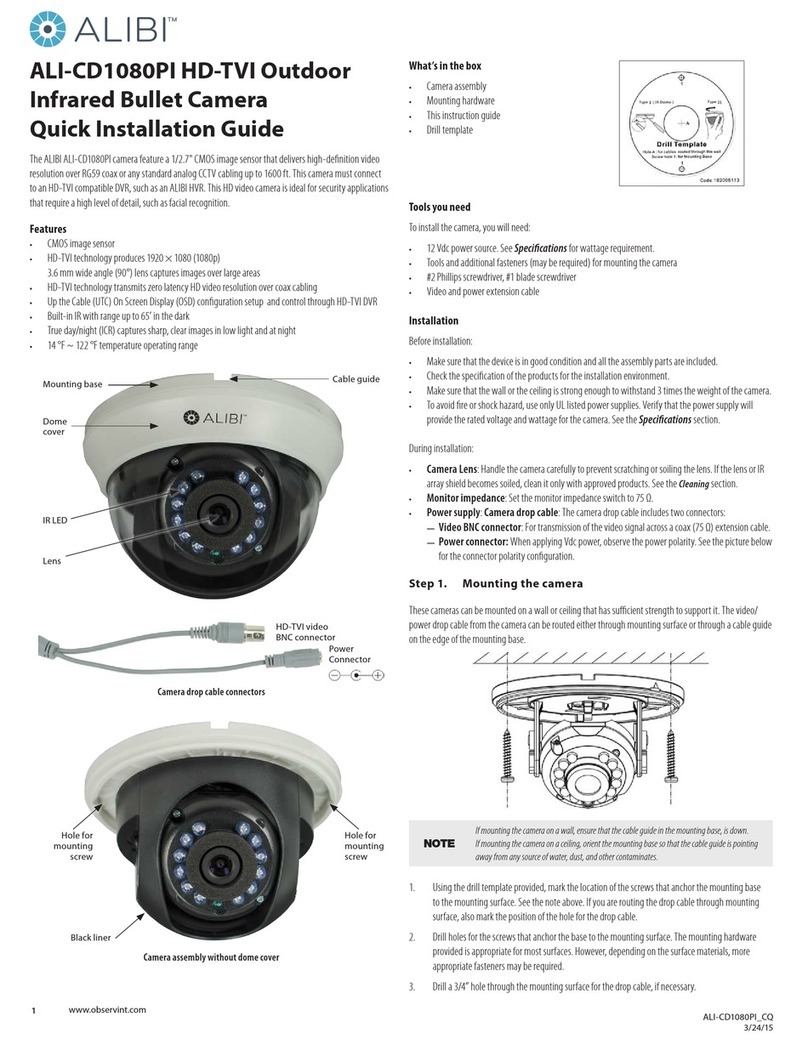
ALIBI
ALIBI ALI-CD1080PI Quick installation guide

Samsung
Samsung SCC-641 - 22x Zoom Smart Dome Camera Specification sheet

Panasonic
Panasonic WV-CW474AFE operating instructions
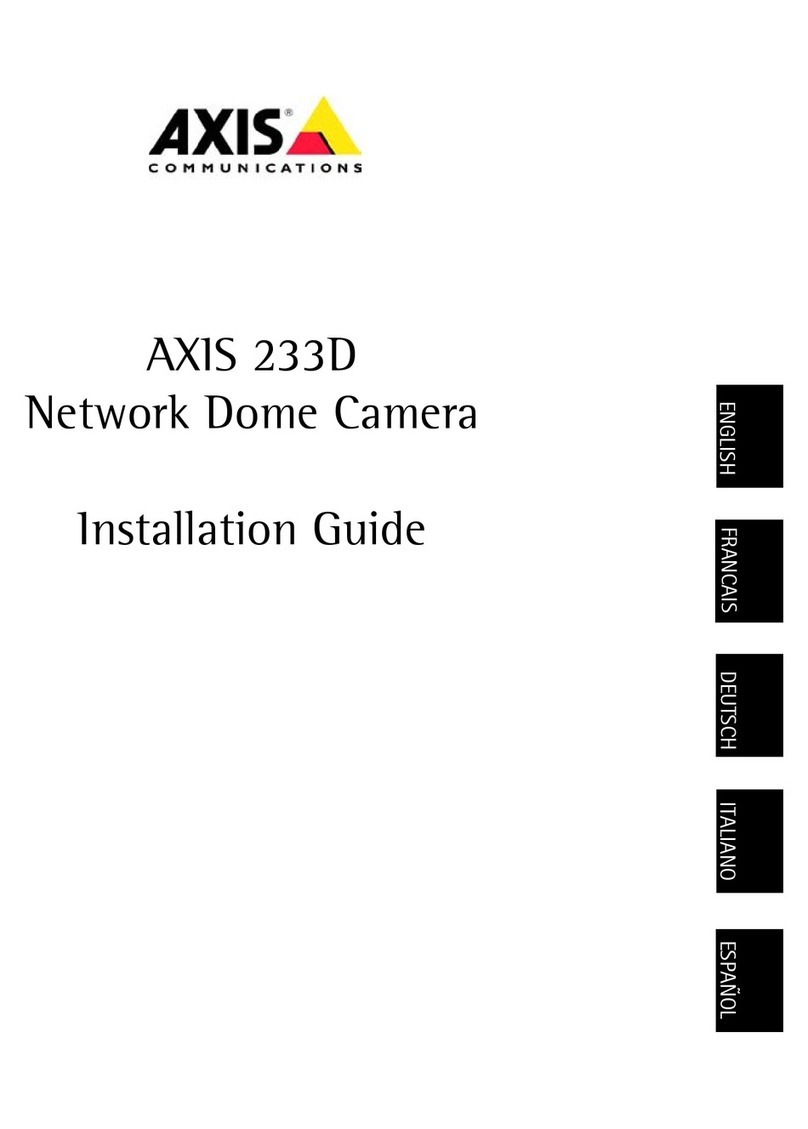
Axis
Axis 233D installation guide

Panasonic
Panasonic BB-HCM381A - Network Camera Service manual
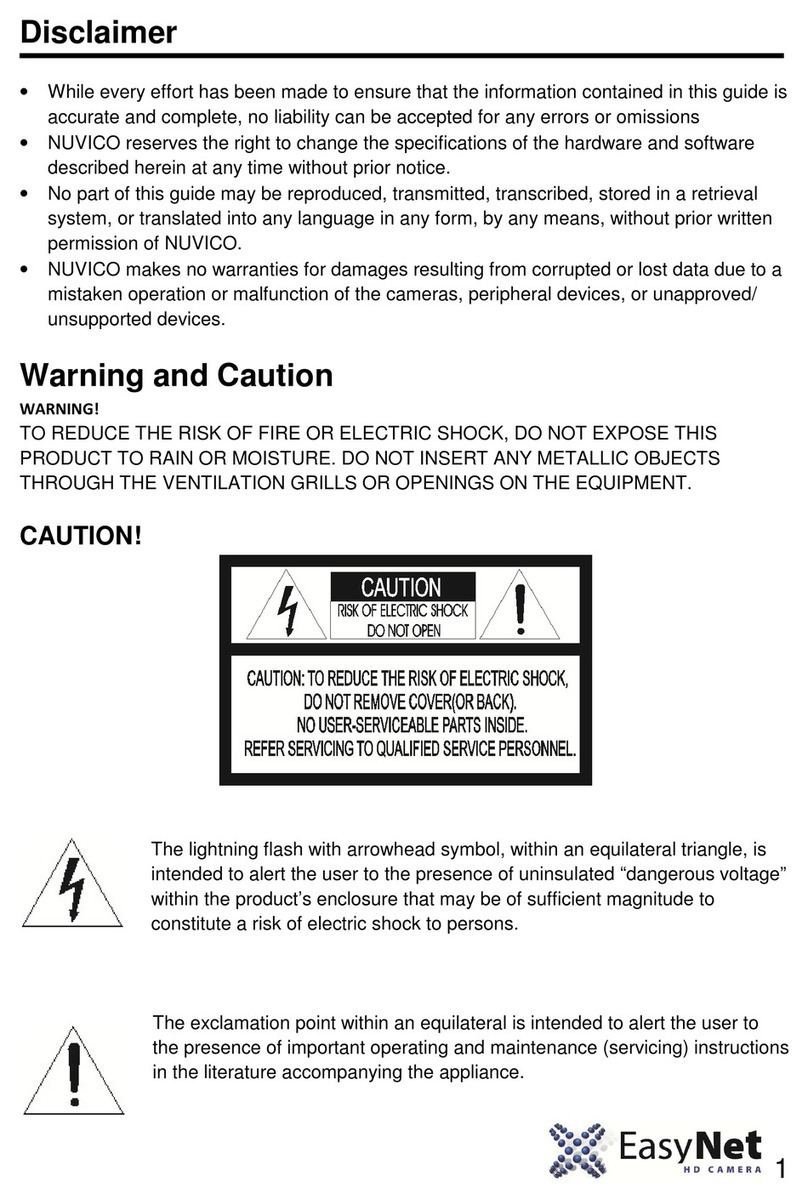
easynet
easynet EC-2M-OV39N-ONV Setup guide
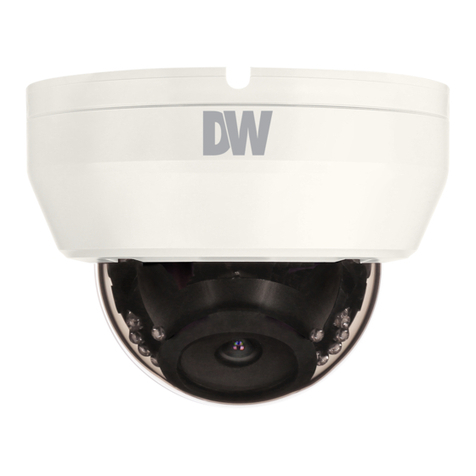
Digital Watchdog
Digital Watchdog DWC-D3263WTIR quick start guide

Optex
Optex InSight Series installation instructions