Vexta CFK II Series User manual

HP-4164-2
Thank you for purchasing an Oriental Motor product.
This Operating Manual describes product handling procedures and safety precautions.
• Please read it thoroughly to ensure safe operation.
• Always keep the manual where it is readily available.
CFK II Series
5-Phase Stepping Motor Unit
zPhotocoupler Input
OPERATING MANUAL
Table of Contents
Introduction .......................................................... Page 2
Safety precautions ............................................... Page 3
Preparation .......................................................... Page 6
Checking the product ...................................... Page 6
Names and functions of parts ......................... Page 7
Main specifications .......................................... Page 8
Installation............................................................ Page 11
Location for installation ................................... Page 11
Installing the motor .......................................... Page 12
Installing a load ............................................... Page 13
Overhung load and thrust load........................ Page 14
Installing the driver .......................................... Page 15
Connection........................................................... Page 16
Terminal blocks................................................ Page 16
Connecting the motor ...................................... Page 16
Connecting to the power supply...................... Page 16
Connecting the I/O signals .............................. Page 17
Terminal blocks pin assignments .................... Page 17
Connecting the CFK513-type motor ............... Page 18
Connection examples...................................... Page 19
Explanation of I/O signals ............................... Page 20
Timing chart..................................................... Page 24
Setting.................................................................. Page 25
Step angle ....................................................... Page 25
Motor current ................................................... Page 26
Pulse input modes........................................... Page 29
Inspection............................................................. Page 30
Troubleshooting and remedial actions................. Page 31

2
Introduction
Before using the motor unit
Only qualified personnel should work with the product.
Use the product correctly after thoroughly reading the section “Safety precautions.”
The product described in this manual has been designed and manufactured for use in
general industrial machinery, and must not be used for any other purpose. For the driver’s
power supply, use a DC power supply with reinforced insulation on its primary and
secondary sides. Oriental Motor Co., Ltd. is not responsible for any damage caused
through failure to observe this warning.
Overview of the product
The CFKII series is a unit comprising of an open-case, high-performance micro-step driver
and high-torque, low-vibration design 5-phase stepping motor. The use of micro-stepping,
which gives the basic step angle of the motor greater precision, electrically provides lower
vibration and lower noise with accurate angle operation without the need for a speed-
reduction mechanism.
Conformance with EC directives
Take the following measures to ensure conformance with the EC’s low voltage directive
and EMC directive.
For low voltage directive
This product is not subject to the EC’s low voltage directive because its input power
supply voltage is 24 VDC. However, the user is advised to perform the following actions
when conducting product installation and connection.
• This product is designed for use within machinery, so it should be installed within an
enclosure.
• For the driver’s power supply, use a DC power supply with reinforced insulation on its
primary and secondary sides.
For EMC directive
The EMC measurement is not performed on the individual motor or driver. The customer
is required to conduct the EMC measures on the final product incorporating the unit.

3
•PK513,PMM3H,PK54,PK56Hand PK59do not comply with CSA standards.
•PK513,PMM3H,PK56Hand PK59are not recognized by UL.
Applicable standards (Recognized by UL for CSA standards)
Applicable standards
UL1004, UL519
CSA C22.2 No.77
CSA C22.2 No.100
-
Stepping
motor
Driver
Standard file No.
File No. E64199
-
Certification body
UL
-
Safety precautions
The precautions described below are intended to prevent danger or injury to the user and
other personnel through safe, correct use of the product. Use the product only after
carefully reading and fully understanding these instructions.
Warning
Handling the product without observing the instructions that accompany a “Warning”
symbol may result in serious injury or death.
Caution
Handling the product without observing the instructions that accompany a “Caution”
symbol may result in injury or property damage.
Note
The items under this heading contain important handling instructions that the user should
observe to ensure safe use of the product.

4
Warning
General
• Do not use the product in explosive or corrosive environments, in the presence of
flammable gases, locations subjected to splashing water, or near combustibles. Doing
so may result in fire or injury.
• Assign qualified personnel the task of installing, wiring, operating/controlling, inspecting
and troubleshooting the product. Failure to do so may result in fire or injury.
Installation
• Install the motor and driver in their enclosures in order to prevent injury.
Connection
• Keep the driver’s input-power voltage within the specified range to avoid fire.
• For the driver’s power supply, use a DC power supply with reinforced insulation on its
primary and secondary sides. Failure to do so may result in electric shock.
• Connect the cables securely according to the wiring diagram in order to prevent fire.
• Do not forcibly bend, pull or pinch the power cable or motor lead wire. Doing so may
result in fire.
Operation
• Turn off the driver power in the event of a power failure, or the motor may suddenly start
when the power is restored and may cause injury or damage to equipment.
• If this product is used in an elevator application, be sure to provide a measure for the
position retention of moving parts. The motor loses its holding torque when the power is
turned off. Failure to provide such a measure may cause the moving parts to fall off,
resulting in injury or damage to the equipment.
• Do not turn the A.W.OFF (All Windings Off) input to “ON” while the motor is operating.
The motor will stop and lose its holding ability, which may result in injury or damage to
the equipment.
Repair, disassembly and modification
• Do not disassemble or modify the motor or driver. This may cause injury. Refer all such
internal inspections and repairs to the branch or sales office from which you purchased
the product.

5
Caution
General
• Do not use the motor and driver beyond their specifications, or injury or damage to
equipment may result.
• Do not touch the motor or driver’s heat sink during operation or immediately after
stopping. The surfaces are hot and may cause a burn.
Transportation
• Do not hold the motor output shaft or motor lead wire. This may cause injury.
Installation
• Keep the area around the motor and driver free of combustible materials in order to
prevent fire or a burn.
• To prevent the risk of damage to equipment, leave nothing around the motor and driver
that would obstruct ventilation.
• Provide a cover over the rotating parts (output shaft) of the motor to prevent injury.
Operation
• Use a motor and driver only in the specified combination. An incorrect combination may
cause a fire.
• To avoid injury, remain alert during operation so that the motor can be stopped
immediately in an emergency.
• Before supplying power to the driver, turn all input signals to the driver to “OFF.”
Otherwise, the motor may start suddenly and cause injury or damage to equipment.
• Before moving the motor directly with the hands (as in the case of manual positioning),
confirm that the driver A.W.OFF (All Windings Off) input is “ON” to prevent injury.
• When an abnormality is noted, stop the operation immediately, or fire or injury may
occur.
Disposal
• When disposing of the motor or driver, treat them as industrial waste.

6
Preparation
This section covers the points to be checked along with the names, functions and main
specifications of the respective parts.
Checking the product
Upon opening the package, verify that the items listed below are included.
Report any missing or damaged items to the branch or sales office from which you
purchased the product.
• Motor 1 unit
• Driver 1 unit
• Motor cable 24 in. (600 mm) 1 piece (CFK513-type only)
• Operating manual 1 copy
Motor rated
current Unit model Driver model
DFC5128T
Motor model
Double shaft
PK566H-NBA
PK569H-NBA
PK596-NBA
PK599-NBA
PK5913-NBA
Single shaft
CFK566HAT
CFK569HAT
CFK596HAT
CFK599HAT
CFK5913HAT
Double shaft
CFK566HBT
CFK569HBT
CFK596HBT
CFK599HBT
CFK5913HBT
Single shaft
PK566H-NAA
PK569H-NAA
PK596-NAA
PK599-NAA
PK5913-NAA
2.8 A/phase
Combinations of motors and drivers
Standard type
High-speed type
Driver model
DFC5103T
DFC5107T
DFC5114T
Motor rated
current Unit model Motor model
Double shaft
PK513PB
PMM33BH2
PMM35BH2
PK543NBWA
PK544NBWA
PK545NBWA
PK564NBWA
PK566NBWA
PK569NBWA
Single shaft
CFK513PAT
CFK533AT
CFK535AT
CFK543AT
CFK544AT
CFK545AT
CFK564AT
CFK566AT
CFK569AT
Double shaft
CFK513PBT
CFK533BT
CFK535BT
CFK543BT
CFK544BT
CFK545BT
CFK564BT
CFK566BT
CFK569BT
Single shaft
PK513PA
PMM33AH2
PMM35AH2
PK543NAWA
PK544NAWA
PK545NAWA
PK564NAWA
PK566NAWA
PK569NAWA
0.35 A/phase
0.75 A/phase
1.4 A/phase
0.35 A/phase
0.75 A/phase
1.4 A/phase

7
Names and functions of parts
This section covers the names and functions of parts in the driver and motor.
Note
• Even when the motor is stopped, the current remains on and the motor continues to
generate heat.
• While the motor is in the stopped state, the current is automatically reduced to a value
preset by the motor-stop current-adjustment control (STOP) to limit the generation of
heat. The motor’s holding torque is also reduced in proportion to the stopped-state
current. Adjust the motor-stop current-adjustment control (STOP) setting to ensure the
necessary load-holding torque.
Motor
Illustration typical for the PK56and PK59.
VEXTA
DA 10
XL1 C.C.
SW3
Mounting holes
Power-supply terminal block (TB1)
Motor terminal block (TB2)
Motor-run current-adjustment control (RUN)
Motor-stop current-adjustment control (STOP)
Step-angle setting switches (DATA1, DATA2)
Sets the current for when the motor is running.
The factory setting is the motor’s rated
current (2.8 A/phase).
Sets the current for when the motor is stopped.
The factory setting is about 50%
of the motor’s rated current.
DATA1 and DATA2 each set one of 16 step angles.
DATA1 and DATA2 are select with the C/S (step-angle switching) input.
The factory setting is [0: 0.72˚] for both DATA1 and DATA2.
Mounting cutout
Pulse input mode selector switch (1P/2P)
DC check switch (C.C.)
Heat sink
Switches between 1-pulse input mode
and 2-pulse input mode.
The factory setting is 1P: 1-pulse input mode.
Switch used when adjusting the motor’s running current.
When running the motor, always have this switch set to OFF.
The factory setting is OFF.
I/O signal terminal block (TB3)
Pilot
Output shaft
Mounting holes
(4 locations)
Motor leads
(5 wires: blue, red, orange, green and black)
Driver
Illustration shows the DFC5128T.

8
Main specifications
This section covers the main specifications.
Refer to the catalog for detailed specifications and torque characteristics.
Motor specifications
Standard type
• The maximum holding torque represents the value of 5-phase excitation at the rated
current of the motor.
When the motor is combined with a dedicated driver, the value will decrease in
proportion to the motor’s stopped-state current setting.
Single shaft
Double shaft
Maximum holding
torque oz-in (N·m)
Rotor inertia
oz-in2(kg·m2)
Basic step angle
Rated current
A/phase
Mass lb. (kg)
Insulation class
Ambient
temperature range
PK545NAWA
PK545NBWA
34 (0.24)
0.37
(68 × 10-7)
0.75
0.77 (0.35)
PK564NAWA
PK564NBWA
59 (0.42)
0.96
(175 × 10-7)
1.32 (0.6)
PK566NAWA
PK566NBWA
117 (0.83)
1.53
(280 × 10-7)
1.4
1.76 (0.8)
PK569NAWA
PK569NBWA
230 (1.66)
3.1
(560 × 10-7)
2.86 (1.3)
Class B [266°F (130°C)] UL/CSA: Class A [221°F (105°C)]
+14°F to +122°F (
-
10°C to +50°C)
0.72°
Motor
model
Single shaft
Double shaft
Maximum holding
torque oz-in (N·m)
Rotor inertia
oz-in2(kg·m2)
Basic step angle
Rated current
A/phase
Mass lb. (kg)
Insulation class
Ambient
temperature range
PK513PA
PK513PB
3.12 (0.022)
0.014
(2.6 × 10-7)
0.35
0.11 (0.05)
PMM33AH2
PMM33BH2
4.6 (0.033)
0.049
(9 × 10-7)
0.22 (0.1)
PMM35AH2
PMM35BH2
8.5 (0.06)
0.098
(18 × 10-7)
0.72°
0.374(0.17)
PK543NAWA
PK543NBWA
18.4 (0.13)
0.191
(35 × 10-7)
0.462 (0.21)
Motor
model PK544NAWA
PK544NBWA
25 (0.18)
0.3
(54 × 10-7)
0.594 (0.27)
0.75
+14°F to +122°F (
-
10°C to +50°C)
Class B [266°F (130°C)]
UL/CSA: Class A
[221°F (105°C)]
Class B [266°F(130°C)]

9
High-speed type
• The maximum holding torque represents the value of 5-phase excitation at the rated
current of the motor.
When the motor is combined with a dedicated driver, the value will decrease in
proportion to the motor’s stopped-state current setting.
Single shaft
Double shaft
Maximum holding
torque oz-in (N·m)
Rotor inertia
oz-in2(kg·m2)
Basic step angle
Rated current
A/phase
Mass lb. (kg)
Insulation class
Ambient
temperature range
PK566H-NAA
PK566H-NBA
117 (0.83)
1.53
(280 × 10-7)
1.76 (0.8)
PK569H-NAA
PK569H-NBA
230 (1.66)
3.1
(560 × 10-7)
2.83 (1.3)
PK596-NAA
PK596-NBA
290 (2.1)
7.7
(1400 × 10-7)
3.74 (1.7)
PK599-NAA
PK599-NBA
580 (4.1)
14.8
(2700 × 10-7)
6.16 (2.8)
0.72°
2.8
Class B [266°F (130°C)]
+14°F to +122°F (
-
10°C to +50°C)
Motor
model PK5913-NAA
PK5913-NBA
890 (6.3)
22
(4000 × 10-7)
8.36 (3.8)

10
Driver specifications
24 VDC ±10%
Microstep (Maximum 250 divisions)
Photocoupler input
Signal voltage Photocoupler ON: +4.5 to +5 V
Photocoupler OFF: 0 to +1 V
PLS, DIR: 5 VDC, 20 mA maximum, Input resistance 220 Ω
A.W.OFF, C/S: 5 VDC, 15 mA maximum, Input resistance 470 Ω
Open-collector output
TIMING: 24 VDC maximum, 10 mA maximum
The signal is output when the excitation sequence is in step “0”.
(Photocoupler ON)
Division of 1: The signal is output once every 10 pulses.
Division of 10: The signal is output once every 100 pulses.
Natural ventilation
+32°F to +104°F (0°C to +40°C)
Driver model
Power input voltage
Excitation mode
Input signal
Output signal
Driver cooling method
Mass lb. (kg)
Ambient temperature range
DFC5107T
0.44 (0.2)
DFC5114T DFC5128T
0.484 (0.22)
DFC5103T
• The input-power current supplied to the driver represents the maximum input value
(which varies with pulse speed).

11
Installation
This section covers the environment and method of installing the motor and driver, along
with load installation.
Location for installation
The motor and driver are designed and manufactured for installation in equipment.
Install them in a well-ventilated location that provides easy access for inspection. The
location must also satisfy the following conditions:
• Inside an enclosure that is installed indoors (provide vent holes)
• Operating ambient temperature Motor: +14°F to +122°F (-10°C to +50°C) (non-freezing)
Driver: +32°F to +104°F (0°C to +40°C) (non-freezing)
• Operating ambient humidity 85%, maximum (no condensation)
• Area that is free of explosive atmosphere or toxic gas (such as sulfuric gas) or liquid
• Area not exposed to direct sun
• Area free of excessive amount of dust, iron particles or the like
• Area not subject to splashing water (storms, water droplets), oil (oil droplets) or other
liquids
• Area free of excessive salt
• Area not subject to continuous vibration or excessive shocks
• Area free of excessive electromagnetic noise (from welders, power machinery, etc.)
• Area free of radioactive materials, magnetic fields or vacuum

12
Note
Insert the pilot located on the motor’s installation surface into the mounting plate’s
countersunk or through hole.
Installing the motor
Direction of installation
The motor can be installed in any direction.
Mounting plate
Washer
Spring washer
Hexagonal socket
screw
Tapped hole
Spot facing or
through hole for pilot
Mounting plate
Spring washer
Hexagonal socket
screw
Spot facing or
through hole for pilot
Tapped hole
How to install the motor
Install the motor onto an appropriate flat metal plate having excellent vibration resistance
and heat conductivity.
When installing the motor, secure it with four bolts (not supplied) through the four
mounting holes provided. Do not leave a gap between the motor and plate.
• Types of installation
AB
Bolt size
M2
M2.5
M3
M4
M5
Motor model Tightening
torque
2.3 Ib-in
(0.25 N·m)
4.4 lb-in
(0.5 N·m)
8.8 lb-in
(1 N·m)
17.7 lb-in
(2 N·m)
26 lb-in
(3 N·m)
PK513PA
PMM33AH2
PMM35AH2
PK543NAWA
PK544NAWA
PK545NAWA
PK564NAWA
PK566NAWA
PK569NAWA
PK566H-NAA
PK569H-NAA
PK596-NAA
PK599-NAA
PK5913-NAA
PK513PB
PMM33BH2
PMM35BH2
PK543NBWA
PK544NBWA
PK545NBWA
PK564NBWA
PK566NBWA
PK569NBWA
PK566H-NBA
PK569H-NBA
PK596-NBA
PK599-NBA
PK5913-NBA
Type of
installation
A
A
A
B
B
Effectine
depth of bolt
0.1 in.
(2.5 mm)
0.1 in.
(2.5 mm)
0.17 in.
(4.5 mm)
-
-

13
Installing a load
When connecting a load to the motor, align the centers of the motor’s output shaft and
load shaft.
Direct coupling
Align the centers of the motor’s output shaft and load shaft in a straight line.
Using a belt drive
Align the motor’s output shaft and load shaft in parallel with each other, and position both
pulleys so that the line connecting their centers is at a right angle to the shafts.
Using a gear drive
Align the motor’s output shaft and gear shaft in parallel with each other, and let the gears
mesh at the center of the tooth widths.
Note
• When coupling the load to the motor, pay attention to the centering of the shafts, belt
tension, parallelism of the pulleys, and so on.
Securely tighten the coupling and pulley set screws.
• Be careful not to damage the output shaft or bearings when installing a coupling or
pulley to the motor’s output shaft.
• Do not modify or machine the motor’s output shaft.
Doing so may damage the bearings and destroy the motor.

14
Overhung load and thrust load
The overhung load on the motor’s output shaft must be kept under the permissible values
listed below.
The thrust load must not exceed the motor’s mass.
Note
Failure due to fatigue may occur when the motor bearings and output shaft are subject to
repeated loading by an overhung or thrust load that is in excess of the permissible limit.
[Unit: lb. (N)]
0 (0)
2.6 (12)
5.6 (25)
4.5 (20)
14.1 (63)
58 (260)
Motor model Overhung load
Distance from the tip of motor’s output shaft [inch (mm)]
0.2 (5)
3.3 (15)
7.6 (34)
5.6 (25)
16.8 (75)
65 (290)
0.39 (10)
-
11.7 (52)
7.6 (34)
21 (95)
76 (340)
0.59 (15)
-
-
11.7 (52)
29 (130)
87 (390)
0.79 (20)
-
-
-
42 (190)
108 (480)
PK513PA
PMM33AH2
PMM35AH2
PK543NAWA
PK544NAWA
PK545NAWA
PK564NAWA
PK566NAWA
PK569NAWA
PK566H-NAA
PK569H-NAA
PK596-NAA
PK599-NAA
PK5913-NAA
PK513PB
PMM33BH2
PMM35BH2
PK543NBWA
PK544NBWA
PK545NBWA
PK564NBWA
PK566NBWA
PK569NBWA
PK566H-NBA
PK569H-NBA
PK596-NBA
PK599-NBA
PK5913-NBA

15
Installing the driver
Installation method
Install the driver on a flat metal plate having superior capacity to withstand vibration as
well as a high heat-conductance effect. Always install the driver using the driver’s
installation holes and install and fasten it either vertically or horizontally with the two screws
(M3; not supplied with unit) so that there is no gap between the driver and the metal plate.
Any other installation method will reduce the heat-radiating effect for the driver.
There must be a clearance of at least 0.98 in. (25 mm) and 1.97 in. (50 mm) in the
horizontal and vertical directions, between the driver and enclosure or other equipment.
When two or more drivers are to be installed side by side, provide 0.79 in. (20 mm)
clearances in the horizontal.
Note
• Do not install any equipment that generates a large amount of heat near the driver.
• Check ventilation if the ambient temperature of the driver exceeds 104°F (40°C).
VEXTA
DA10
XL1 C.C.
SW3
Spring washer
M3 screw
Washer
M3 tapped hole
VEXTA
Spring washer
M3 screw
Washer
M3 tapped hole
0.79 in. min.
(20 mm)
Illustrations show the DFC5128T.

16
Connection
This section covers the methods of connecting the driver, motor, power and controller, as
well as the connection examples and I/O interface.
Terminal blocks
Screw terminals are used.
Remove the insulation from the core, then insert the core into the terminal and tighten with
terminal screws.
Strip 0.24 to 0.31 in. (6 to 8 mm) of insulation.
Tighten the terminal screw at the specified tightening torque.
Connecting the motor
Connect the motor leads into the driver’s motor terminal block (TB2).
The CFK513 model has a connector with motor leads. Use the supplied motor cable with
connector.
Note
If the noise generated from the motor leads becomes a problem, shield the motor leads
with electrically conductive tape, wire mesh or the like.
Connecting to the power supply
The input power-supply voltage is 24 VDC ±10%. Use a power supply capable of
supplying the power/current capacity as shown below.
Driver model DFC5103T, DFC5107T
1 A min. DFC5114T
2 A min. DFC5128T
4 A min.
Connecting the power-supply wires into the driver’s power-supply terminal blocks (TB1).
Note
• For the power-supply cable, use a cable with a diameter equivalent to AWG20 (0.5 mm2)
for the standard type (DFC5103T, DFC5107T, DFC5114T), and AWG20 to 18 (0.5 to
0.75 mm2) for the high-speed type (DFC5128T). Be sure to connect the power supply
using the correct polarity. If the power supply’s polarity is reversed, the driver may be
damaged.
• Do not route the power-supply cables in the same conduits as other power-supply lines
and motor leads.
• Always wait at least 5 sec. after switching off the power before switching it back on
again or connecting/disconnecting the motor-lead connector.

17
Connecting the I/O signals
Connecting the I/O wires into the driver’s I/O signal terminal blocks (TB3).
Note
• For the I/O signal cable, use twisted pair with a diameter equivalent to at least AWG24 to
22 (0.2to 0.34 mm2). To suppress the effect of noise, make the cable as short as
possible [6.6 ft. (2 m) max.].
• Separate I/O signal cables at least 12 in. (300 mm) from electromagnetic relays and
other than inductance loads. Additionally, route I/O signal cables perpendicular to power-
supply cables and motor leads, rather than in a parallel fashion.
Terminal blocks pin assignments
∗Depends on the setting of the pulse-input selector switch.
• When this switch is set to 1-pulse input mode, the inputs are the pulse input and the
rotation-direction input.
• When this switch is set to 2-pulse input mode, the inputs are CW and CCW.
Terminal
blocks
TB1
TB2
TB3
Explanation
+24 VDC ±10%
GND
Blue motor lead
Red motor lead
Orange motor lead
Green motor l ead
Black motor lead
Pulse (CW pulse) input ∗
photocoupler anode side
Pulse (CW pulse) input ∗
photocoupler cathode side
Rotational direction (CCW pulse)
input ∗anode side
Rotational direction (CCW pulse)
input ∗cathode
All windings off input anode side
All windings off input cathode side
Excitation timing output collector side
Excitation timing output emitter side
Step-angle switching input anode side
Step-angle switching input cathode
side
Pin
No.
1
2
1
2
3
4
5
1
2
3
4
5
6
7
8
9
10
I/O
Input
Output
Input
Output
Input
Signal
name
POWER
MOTOR
PLS+
(CW+)
PLS
-
(CW
-
)
DIR+
(CCW+)
DIR
-
(CCW
-
)
A.W.OFF+
A.W.OFF
-
TIMING+
TIMING
-
C/S+
C/S
-
Power-supply
terminal blocks
Motor terminal
blocks
I/O terminal
blocks

18
5 4 3 2 1
A
D
C
E
B
1
2
3
4
5
Connecting the CFK513CFK513
CFK513CFK513
CFK513-type motor
The CFK513-type motors are of the connector type having no leads.
To connect these motors, use the supplied motor cable.
The applicable connector housing/contact, crimping tool and connector configuration are
shown below.
Connector housing/contact, crimping tool
Connector housing MOLEX 51065-0500
Contact MOLEX 50212-8xxx
Crimping tool MOLEX 57176-5000
Connector configuration
Terminal No. 12345
Motor lead color Blue Red Orange Green Black
Note
When connecting to the CFK513-type motor, arrange the cable at the connector such
that the connected part will not be overly stressed as a result of bending of the cable.
Set the cable’s radius of curvature as large as possible.

19
Blue
Red
Orange
Green
Black
1
2
3
4
5
Driver
GND
24 VDC ±10%
+5 V
+5 V
5
4
3
2
1
2
1
5
4
3
10
9
6
8
7
2
1
PLS+
R1
R1
R2
R2
R3
PLS
-
DIR+
DIR
-
A.W.OFF+
A.W.OFF
-
C/S+
C/S
-
TIMING+
TIMING
-
CN2
CN3
CN1
220 Ω
220 Ω
470 Ω
Controller
(NPN-type)
470 Ω
Controller
(PNP-type)
+5 V
+5 V
Connector terminal No.
(-type) Motor lead color
(Lead-type)
Note
• Make the input-signal voltage 5 VDC minimum and 24 VDC maximum.
When the input-signal voltage is 5 VDC, external resistors R1 and R2 in the diagram are
not necessary. If the input-signal voltage is greater than 5 VDC, connect external
resistors R1 and R2, as shown in the diagram, to restrict the input current as follows:
PLS, DIR: 20 mA max.
A.W.OFF, C/S: 15 mA max.
• Use an output-signal voltage of 5 VDC minimum and 24 VDC maximum, and use
output-signal current of 10 mA max.
If the output-signal current is greater than 10 mA, connect external resistor R3, as shown
in the diagram, to restrict the current to no more than 10 mA.
Connection examples
Examples of connections with the motor, power supply and controller are shown below.

20
Explanation of I/O signals
Input signals
The signal states indicate the state of the internal photocoupler (ON: power conducted;
OFF: power not conducted).
PLS input and DIR input
This driver can select either 1-pulse input mode or 2-pulse input mode as the pulse-input
mode to match the controller used. For details on how to set the pulse-input mode, see
page 29, “Pulse input modes.”
1-pulse input mode (factory setting)
The controller pulses are connected to the PLS+ input (pin No.1) or the PLS
-
input (pin
No.2), and the rotation direction is connected to the DIR+ input (pin No.3) or DIR
-
input
(pin No.4).
1.When the DIR input is “ON,” a fall of the “PLS input” from “ON” to “OFF” will rotate the
motor one step in the CW direction.
2.When the DIR input is “OFF,” a fall of the “PLS input” from “ON” to “OFF” will rotate the
motor one step in the CCW direction.
+5 V
1, 3
2, 4
PLS
-
DIR
-
NPN-type PNP-type
+5 V
1, 3
2, 4
PLS+
DIR+
1 µs
min.
2 µs max.
90%
10%
300 µs min.
1 µs
min.
2 µs max.
CCW CW
H
L
DIR input
H
L
PLS input
Note
• Do not allow the driver temperature to exceed 158°F (70°C), which is the heat-radiating
plate’s saturation temperature during operation.
• The minimum value for the interval time when switching the rotational direction depends
on the motor’s size, running speed and load moment of inertia.
This manual suits for next models
28
Table of contents
Other Vexta Engine manuals
Popular Engine manuals by other brands
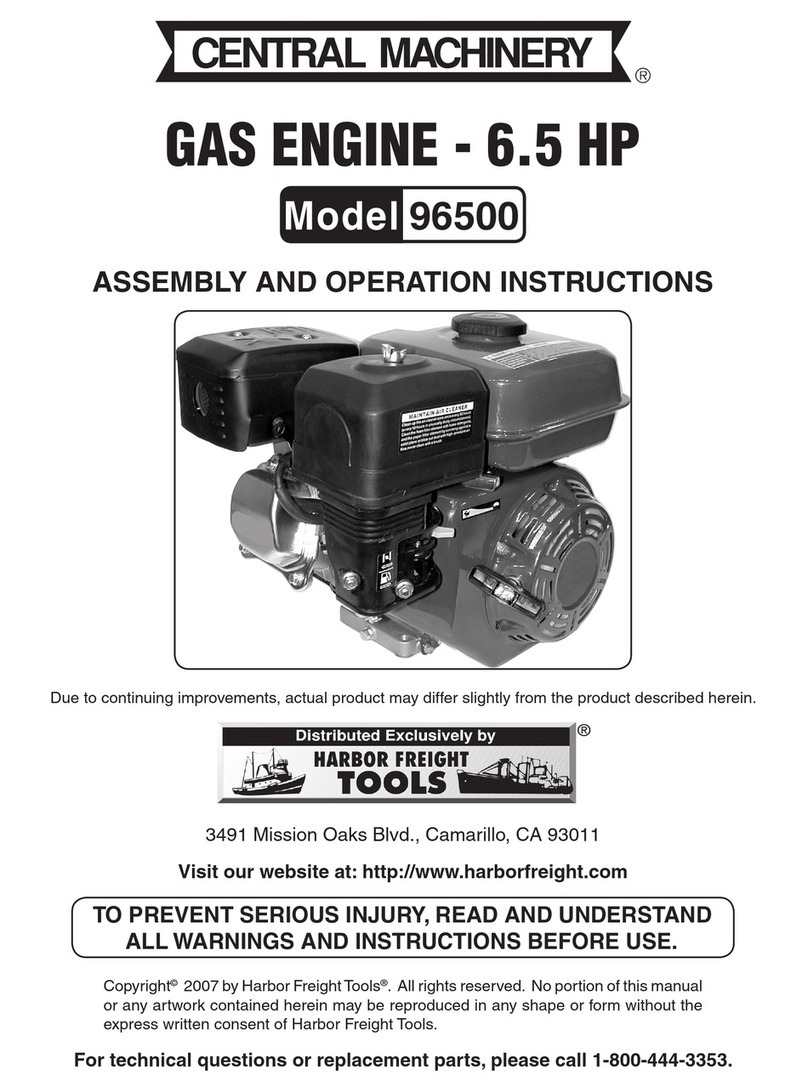
Central Machinery
Central Machinery 96500 Assembly and operation instructions
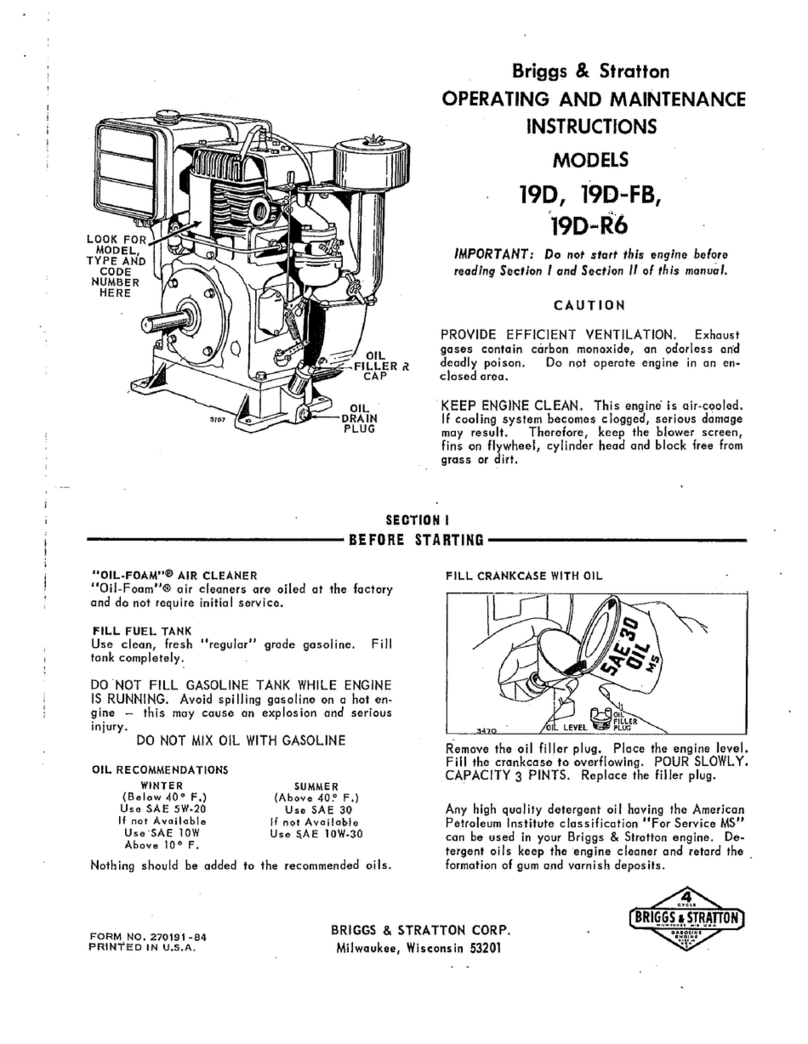
Briggs & Stratton
Briggs & Stratton 19D Operating and maintenance manual

LONCIN
LONCIN G250F Service manual
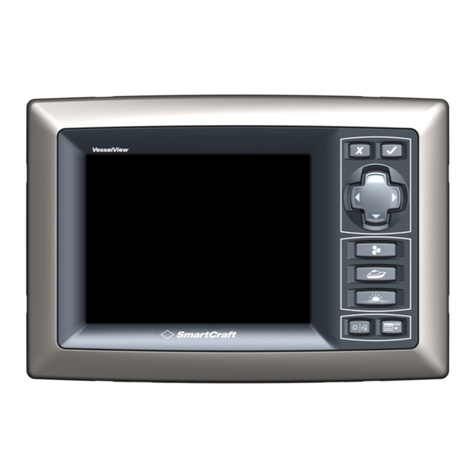
Mercury
Mercury 92-813054A2 manual
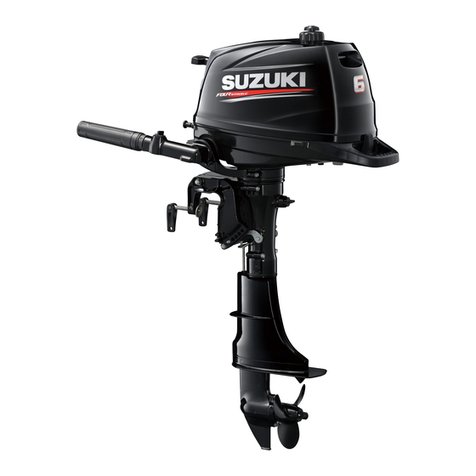
Suzuki
Suzuki DF 25 General information
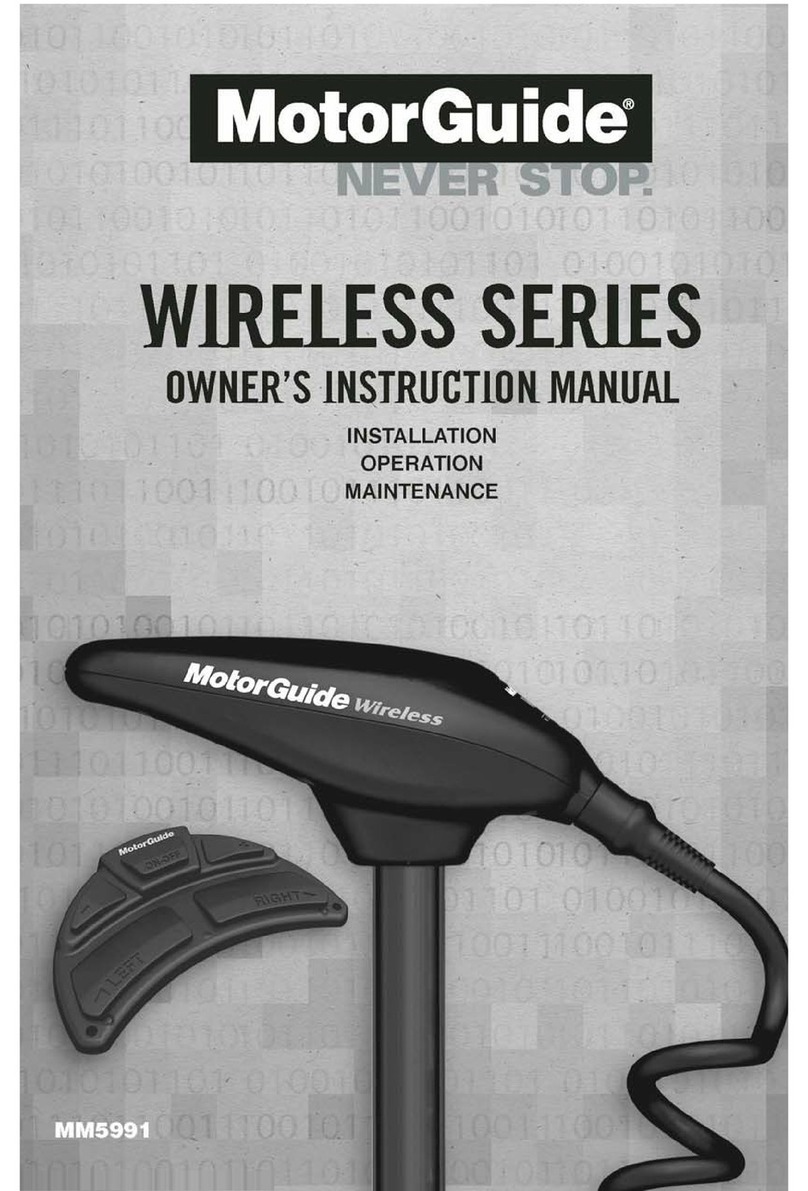
MotorGuide
MotorGuide Wireless Series Owner's instruction manual