Viadrus S.Control Touch Instruction Manual

CONTROL UNIT S.Control
for boilers VIADRUS A0C and VIADRUS A2C
M
Touch
anual for operation
GB_2016_47
GB_2017_30

2
TABLE OF CONTENT
page
1
SAFETY INSTRUCTIONS...........................................................................................................................................................................3
2
General information.....................................................................................................................................................................................3
3
Information about documentation.................................................................................................................................................................3
4
Documentation archiving .............................................................................................................................................................................3
5
Used symbols and marking..........................................................................................................................................................................3
6
Directive 2002/96/ES on waste electric and electronic equipment (WEEE)..................................................................................................3
7
USER MENU STRUCTURE........................................................................................................................................................................4
8
Regulator servicing......................................................................................................................................................................................5
8.1
Control description.................................................................................................................................................................................5
8.2
Boiler switching-on and switching-off......................................................................................................................................................5
8.3
IGNITION mode.....................................................................................................................................................................................6
8.4
OPERATION mode................................................................................................................................................................................6
8.5
EXTINGUISHING mode.........................................................................................................................................................................7
8.6
STANDBY mode....................................................................................................................................................................................7
8.7
IDLE mode.............................................................................................................................................................................................7
9
Boiler setting................................................................................................................................................................................................7
9.1
Required boiler temperature setting .......................................................................................................................................................7
9.2
Setting of the fuel level in the boiler fuel reservoir ..................................................................................................................................7
10
Hot water settings........................................................................................................................................................................................8
10.1
Hot service water (HW) settings........................................................................................................................................................8
10.2
HW required temperature settings.....................................................................................................................................................8
10.3
HW reservoir hysteresis....................................................................................................................................................................8
10.4
HW reservoir disinfection...................................................................................................................................................................8
11
SUMMER/WINTER function switching-on....................................................................................................................................................9
12
Mixer circuit settings (MIX)...........................................................................................................................................................................9
12.1
Equithermal regulation ......................................................................................................................................................................9
13
Description of night standby adjustment.....................................................................................................................................................10
14
Manual control...........................................................................................................................................................................................11
15
Favorite menu............................................................................................................................................................................................11
16
Hydraulic schemes ....................................................................................................................................................................................11
16.1
Scheme 1........................................................................................................................................................................................11
16.2
Scheme
2
........................................................................................................................................................................................12
16.3
Scheme 3........................................................................................................................................................................................13
16.4
Orientational electric scheme (auxiliary)..........................................................................................................................................14
16.5
Connection of temperature sensors.................................................................................................................................................15
16.6
Outdoor sensor connection .............................................................................................................................................................15
16.7
Check of temperature sensors.........................................................................................................................................................16
16.8
Connection of a thermostat of the mixers ........................................................................................................................................16
16.9
Connection of a boiler room thermostat...........................................................................................................................................16
16.10
Connection of a reserve boiler (a reserve source)...........................................................................................................................17
16.11
Connection of alarm signalization....................................................................................................................................................17
16.12
Mixer connection.............................................................................................................................................................................18
16.13
Connection of a circulating pump ....................................................................................................................................................18
16.14
Connection of ecoSTER TOUCH room panel.................................................................................................................................18
16.15
Access to parameters of the regulator through internet....................................................................................................................19
16.16
Feeder calibration ...........................................................................................................................................................................19
17
Structure- service menu............................................................................................................................................................................19
18
SERVICE SETTINGS - code 1992.............................................................................................................................................................20
18.1
Burner service settings....................................................................................................................................................................20
18.2
Boiler service settings .....................................................................................................................................................................21
18.3
CH and HW service settings............................................................................................................................................................21
18.4
Service settings of the heat-exchanger............................................................................................................................................22
18.5
Service settings of the mixer...........................................................................................................................................................22
18.6
Service settings - others..................................................................................................................................................................22
19
Advanced parameters................................................................................................................................................................................22
20
DESCRIPTION OF ALARMS.....................................................................................................................................................................23
20.1
Alarm 2 - Max. boiler temperature exceeding ..................................................................................................................................23
20.2
Alarm 3 - Max. burner temperature exceeding.................................................................................................................................23
20.3
Alarm 4 - Damaged boiler temperature sensor................................................................................................................................23
20.4
Alarm 5 - Damaged burner temperature sensor...............................................................................................................................23
20.5
Alarm 6 - Unsuccessful attempt to ignite the boiler..........................................................................................................................23
20.6
Alarm 7 - Damaged fan...................................................................................................................................................................24
20.7
Alarm 8 - Min. or max. vacuum exceeding.......................................................................................................................................24
20.8
Alarm 9 - Loss of communication.....................................................................................................................................................24

3
1 SAFETY INSTRUCTIONS
Requirements related to the safety are specified in separate parts of this manual. Together with them, i tis necessary to observe
mainly the following requirements.
•Before beginning mounting, repairs or maintenance and during performance of all works related to connection, it is unconditionally
necessary to disconnect the power supply and make certain that terminals and electric cables are without voltage.
•Having switched-off the regulator into the standby mode, danger voltage may occur on the regulator’s terminals.
•It is prohibited to use the regulator in violation with its designation.
•It is necessary to select a value of programmable parameters in accordance with the given type of the boiler and the given fuel with regard
to all operational conditions of the boiler. An incorrect selection of parameters may cause an emergency status of the boiler (boiler
overheating, flame lashing-up into the fuel feeder, etc.).
•The regulator is not intrinsically safe equipment, and in case of a failure it can be a source of a spark or high temperature, which in the
presence of flammable dust or gas can cause a fire or an explosion.
•The programmed parameters may be only modified by a person, who is acquainted with this manual.
•The regulator may be only used in heating circuits produced in accordance with legal regulations.
•Electric installations, in which the regulator is operated, have to be protected by a protecting element properly selected according to the used
loading.
•It is not allowed to use the regulator with the damaged box.
•In no case it is allowed to modify the structure of the regulator.
•An electronic disconnection of connected devices is used in the regulator (a function of type 2Y according to EN 60730-1) and a micro-
disconnection (a function of type 2B according to EN 60730-1).
•No access to the regulator may be allowed for children.
2 General information
The regulator is determined for control of operation of the pellet boiler with using an optical flame brightness sensor. The device has a compact
box, which is easy installable.
It can control operation of a direct circuit of the central heating, operation of the circuit of hot service water and also operation of three heating
circuits with a mixer. Adjustable temperature of the heating circuits may be entered on the basis of data from the extern sensor. A possibility of
cooperation with room thermostats, independent for each heating circuits, helps to maintain a comfort temperature in heated premises. Beside
of that, if needed the device switches-on a reserve boiler (gas or oil one). The regulator can cooperate with an additional control panel placed
in habitable rooms, or an internet module. . The regulator can be used in households and similar units, as well as in light industry buildings.
3 Information about documentation
The instruction manual of the regulator is an addition for the boiler documentation. Together with instructions in this manual, it is necessary to
proceed mainly in accordance with the boiler documentation. The instruction manual of the regulator is divided into two parts: for users and for
an installer. However the both parts contain important information, which influence the safety, that’s why the user is obliged to acquaint with the
both part of the manual.
The manufacturer is not responsible for damages caused by breach of this manual.
4 Documentation archiving
We kindly ask you to archive properly this manual for mounting and operation and all other valid documentation in order to have it at the
disposal when needed.
In case of removal or selling the device, it is necessary to handover the attached documentation to a new user of an owner.
5 Used symbols and marking
The following graphic symbols and marking is used in the manual:
This symbol means useful information and instructions
The symbol means important information, which could be essential from the point of view of property damaging, protection of health
or life of people or domestic animals.
Warning: important information was marked by symbols to simplify work with the manual. However it doesn’t relieve a user and an
installer of the obligation to observe requirements, which are not marked by graphic symbols!
6 Directive 2002/96/ES on waste electric and electronic equipment (WEEE)
•Dispose packages and the product after finishing its usable life in a proper recycling company.
•Don’t throw up the product together with usual waste.
•It is not allowed to combust the product.

4
INSTRUCTION MANUAL FOR S.Control REGULATOR
7 USER MENU STRUCTURE
Informa
tion
Boiler settings
•Adjusted boiler temperature
•Equithermal boiler control
−Switched-off
−Switched-on
•Equithermal boiler curve
•Parallel displacement of equithermal curve
•Thermostat selection
•Power modulation
−Max. burner power
−Correction of pr. fan for max. power
−50% Hysteresis H2
−Middle burner power
−Correction of pr. fan for middle power
−30% Hysteresis H1
−Min. burner power
−Correction of pr. fan for min. power
−Boiler hysteresis
•Regulation mode
−Standard
−Fuzzy Logic
•Fuel level
−Fuel reserve
−Fuel level calibration
•The degree of cleaning
−Normal
−Increased
−Intensive
•Burner cleaning-up
•Boiler night decreasing
−Ignition
−Decreasing
−Schedule – Monday to Sunday
HW settings
•Adjusted HW reservoir temperature
•HW pump mode
−Switched-off
−Priority
−Without priority
•HW reservoir hysteresis
•HW disinfection
−No
−Yes
•HW reservoir night decreasing
−Ignition
−Decreasing
−Schedule – Monday to Sunday
Summer
/
Winter
•Summer mode
−Winter
−Summer
−Auto
•Switch-on temperature for SUMMER mode
•Switch-off temperature for SUMMER mode
MIX 1 – 3 settings*
•Adjusted MIX temperature
•Thermostat selection
•MIX room thermostat
•MIX equithermal control
−Switched-off
−Switched-on
•MIX equithermal curve
•Parallel displacement of equithermal curve
•Room temperature coefficient
•MIX night decreasing
−Ignition
−Decreasing
−Schedule – Monday to Sunday
General settings
•Hours
•Date
•Brightness
•Alarm noise
−Switched-off
−Switched-on
•Language
•Program update
−Update module A
−Update module B
−Update ecoSTER T1
−Update panel
•WiFi settings
−SSID
−Security
−Password
Manual control
Chimney-sweeper
•Chimney-sweeper
•Boiler power
•Time work
Alarms
Regulator turn on
Servis settings
* Unavailable, if a corresponding sensor or an additional module is not connected, or if the parameter is hidden.

5
8 Regulator servicing
8.1 Control description
1. Boiler operation mode: FLAME TEST, INGNITION, STABILIZATION, OPERATION, EXTINGUISHING, CLEANING, STANDBY, IDLE,
ALARM, MANUAL
2. Real boiler temperature
3. Required boiler temperature
4. Enter to Menu
5. Information field:
fan
feeder 1 (at the fuel reservoir)
feeder 2 (at the boiler burner)
CH and HW pump
ignitor
Grate mode
6. HW reservoir required temperature
7. HW reservoir real temperature
8. Week day and time
9. Outdoor temperature
10. A field of functions, which influence the required boiler temperature
decrease of the boiler required temperature by the room thermostat – the required temperature in the room is
reached
decrease of the boiler required temperature according to the time schedules
increase of the boiler required temperature for the period of filling the reservoir of HW
increase of the required temperature by the mixer
boiler control according to the outdoor curve
increase of the boiler required temperature for the period of heating the accumulating reservoir
The right and left window on the main display can represent different information. By touching, you can change the viewed information between
the circuits of the mixer (1, 2, 3), the information window and the HW window.
8.2 Boiler switching-on and switching-off
After you touch any place of the display with the description „Boiler is switched-off“, a
message is displayed: „Switch-on regulator?".
After confirmation, the boiler is gone over into the firing phase.
Or it is possible to switch-on the boiler by clicking to the icon and afterward confirm
it in the sliding menu to the icon - Switch-on the regulator.
Proceed by the same way while switching-off the boiler. The regulator will go over into
the extinguishing process. Not until its finishing, a screen with a message „Boiler is
switched-off“ is displayed.

6
8.3 IGNITION mode
The Ignition mode serves for automatic firing in the furnace of the boiler. The total duration of the firing-up procedure depends on the setting of
the regulator (feeder running time, heater running time, heating body operation time, ect.) and on which state the boiler was before ignition. The
parameters influencing the ignition procedure are concentrated in the menu Service settings/Burner settings/Ignition.
In case that the firing of the heating chamber was unsuccessful, then the next attempts to fire it will be performed, during which a fuel dose
(feeding time) is decreased to 10 % of the dose in the first attempt.
Other attempts to ignite the boiler are signalized by numbers near the ignitor symbol
Having performed three unsuccessful attempts, the Alarm 6 – Unsuccessful attempt to ignite the boiler is announced. Automatic
continuation of the boiler running is blocked – an intervention of personnel is required. After removal the causes, which disabled the ignition, it
is possible to put the boiler into operation again.
8.4 OPERATION mode
The fan works continually, and it is demonstrated on fig. 1. The fuel feeder switches-on periodically. The cycle consists of the feeder running
time and the feeding stop time.
Fig. №. 1
We can choice two modes of regulation responsible for stabilization of the required boiler temperature, Standard or Fuzzy Logic Boiler
settings/Regulation mode.
Operation in Standard mode
As far as the temperature achieves the required value, the regulator goes into the STANDBY mode.
The regulator is equipped with a mechanism for modulation of the boiler power, which enables to decrease gradually its power, when the boiler
temperature approaches the required value. Three power stages are defined:
-
maximum power,
-
middle power,
-
minimum power.
Values of separate levels of the power are set in the menu Service settings/Burner settings/Operation.
The regulator modulates the power of the burner depending on the required temperature of the boiler and defined hysteresis of Hysteresis H2
and Hysteresis H1 (see fig. 2).
Hysteresis H1 and Hysteresis H2 are accessible in the menu Boiler settings/Power modulation
Configuration of the value of H1 and H2 is possible so that the modulation will go on without an inter-state, i.e. the transition from 100% to 30%
with an omission of 50% power.
Fig. №. 2 Hysteresis H1 and H2 of power modulation
Operation in Fuzzy Logic mode
In Fuzzy Logic mode the regulator makes decision about the burner power, with which the boiler would work so that it keeps the boiler
temperature on the required level. The regulator uses defined power levels as in Standard mode. Parameters Hysteresis H2 and Hysteresis
H1 cannot be adjusted for this mode. Thanks to it, reaching the required temperature is not influenced by a possible incorrect setting the
parameters of Hysteresis H2 and Hysteresis H1. In addition, it enables quicker achievement of the required temperature.
Fuel feeding time
Feeding stop time
Fuel feeding time
Feeding stop time
3 power levels 2 power levels
Required boiler temperature
T=85 °C
Required boiler temperature
T=85 °C

7
provided the boiler works without thermal accumulation reservoir, and the regulator will be switched over to SUMMER mode,
we recommend operating the regulator in STANDARD mode.
After exceeding the required boiler temperature by o 5 °C the regulator goes over to STANDBY mode.
8.5 EXTINGUISHING mode
After-combustion of remnants of pellets and preparation of the boiler to the idle or the switching-off goes on in EXTINGUISHING mode.
All parameters influencing the extinguishing process are concentrated in the menu:
Service settings →Burner settings →Extinguishing
The regulator stops the fuel feeding and performs cyclic blowdowns for the purpose of after-combustion of the fuel remnants. After dropping
the flame brightness or after the maximum extinguishing time, the regulator goes over into IDLE mode.
8.6 STANDBY mode
The regulator goes over into STANDBY mode automatically and without an intervention of the user:
-
In case of the regulation mode STANDARD – after reaching the required boiler temperature,
-
In case of the regulation mode Fuzzy Logic – after exceeding the required boiler temperature by 5 °C.
In STANDBY mode the regulator keeps the boiler on the minimum power in order to avoid extinguishing. For this purpose the burner works at a
low power, what under condition of correctly chosen parameters will not cause other temperature growing. The burner power in STANDBY
mode and also other parameters of STANDBY can be displayed in the menu Service settings/ Burner settings/Standby.
The maximum boiler operation time in the Idle mode is defined in the parameter Standby time.If after the lapse of this time, from the moment of
a transition of the regulator into Standby mode, a neediness of repeated operation of the boiler doesn’t occur, then the regulator starts the
extinguishing process of the boiler.
After adjustment of Standby time = 0, the regulator will omits STANDBY mode and goes over immediately into
EXTINGUISHING mode.
8.7 IDLE mode
In IDLE mode, the boiler is extinguished and is waiting for a signal to start operation. The signal to start operation can be as followed:
•decreasing the required boiler temperature under the value of the required temperature reduced by a value of the boiler hysteresis (Boiler
hysteresis),
•at configuration of the boiler operation with an accumulating reservoir, dropping the upper temperature of the accumulating reservoir
under the required value (Accumulating reservoir heating start temperature).
9 Boiler setting
9.1 Required boiler temperature setting
The boiler required temperature can be adjusted in the menu Boiler settings/Required boiler temperature. The adjusted values of these
temperatures are limited by the range of corresponding service parameters of the regulator.
The parameter values: Required boiler temperature,is ignored by the regulator in case that the required temperature of the boiler is controlled
by an extern sensor. Regardless that the temperature adjusted on the boiler is increased automatically in order to enable to heat up the HW
reservoir and heat up the mixers heat circuits.
9.2 Setting of the fuel level in the boiler fuel reservoir
Fuel level indicator switching-on
To switch-on the display of the fuel level, it is necessary to set the value of the parameter Boiler settings/Fuel level/Fuel reserve to the value
higher than 0 (OFF), for example, 10%.
By touching the left or right window on the main screen, you can choose the fuel level indicator.
Recommendation: the fuel level can be also visible on the room panel ecoSTER-Touch (the room panel is not a standard accessories of the
regulator).
Manipulation with the fuel level indicator
After each filling the fuel into the fuel reservoir, it is necessary to press and hold the actual value of the fuel level; afterward the following
message should be displayed:
„Set the reservoir to full 100%“. After selection and confirmation by the button „YES“, the fuel level is set to 100%.
ATTENTION:
You may add fuel in whenever; it means that you don’t need to wait for a total emptying the fuel reservoir. However fuel has to
be always added up to the level corresponding to 100% and set the fuel level on the regulator to 100% - see the description
above.

8
Fig. №. 3 Manipulation with the fuel level
Description of function
The regulator calculates the fuel level on the basis of its continuous consumption. Production settings doesn’t need always to correspond to the
real fuel consumption on the boiler, that’s why this method requires a function of the level calibration for its correct function performed by a user
of the regulator. There is no need to use whatever additional sensors of the fuel level.
Fuel level calibration
Fill up the fuel reservoir up to the level, which complies with the full filling-up to 100%, afterward set the value of the parameter Boiler settings
→Fuel level →Fuel level calibration →Full 100%.
Fill up the fuel reservoir up to the level, which complies with the full filling-up to 100%, afterward set the value of the parameter Calibration near
the fuel level indicator. The message Calibration will blink till the time of the programmed point, which corresponds to the minimum fuel level. It
is necessary to check regularly how the fuel level decreases in the reservoir. At the moment when the level drops to the expected level, it is
necessary to set the value of the parameter Boiler settings →Fuel level →Fuel level calibration →Empty 0%.
10 Hot water settings
10.1 Hot service water (HW) settings
The device corrects the hot service water (HW) temperature, provided a HW temperature sensor is connected.
With help of the parameter HW settings →HW pump mode a user may:
•switch-off the HW reservoir heating-up mode, the parameter Switched-off,
•set the HW priority by the parameter Priority – the CH pump will be switched-off to enable quicker filling-up the HW reservoir,
•set the simultaneous operation of the CH pump and HW by the parameterWithout priority
.
10.2 HW required temperature settings
The required HW temperature is defined by the parameter:
HW settings →Adjusted HW reservoir temperature.
10.3 HW reservoir hysteresis
At temperature lower than HW adjusted reservoir temperature minus HW reservoir hysteresis, the HW pump is switched-on to fill up the HW
reservoir.
In case of setting a low hysteresis value, the HW pump is switched-on quicker after dropping the HW temperature.
10.4 HW reservoir disinfection
The regulator is equipped with a function of regular heating-up the HW reservoir to temperature of 70 °C. The target of this function is to
liquidate bacterial flora in the HW reservoir. The reservoir disinfection settings are placed in the menu:
HW settings →HW disinfection →Switched-on
It is unconditionally necessary to inform all of users due to a danger of scalding by hot water.
Once a week, at night from Sunday to Monday at 02:00, the regulator increase HW temperature.
After a period of 10 min., during which water in the reservoir is maintained at the temperature of 70 °C, the HW pump is switched-off and the
boiler is returned to the normal operation. Don’t switch-on the disinfection function at the switched-out HW control.

9
11 SUMMER/WINTER function switching-on
To switch-on the SUMMER function, which enables filling-up the HW reservoir in the summer without necessity of heating the central heating
installation, it is necessary to set the parameter in the mode Summer/Winter →Summer mode.
All heat consumers in the Summer mode may be switched-off, that’s why it is necessary to ensure even before its switching-on,
whether the boiler is not overheated.
Provided an extern sensor is connected, the SUMMER function may be switched-on automatically by means of a parameter Auto with regard of
other adjusted parameters, at which the function has to be switched on/off in dependence on a value of the extern temperature adjusted in the
parameters: SUMMER switching-on temperature, SUMMER switching-off temperature.
12 Mixer circuit settings (MIX)
Settings of the first mixer circuit are situated in themenu:
Menu →MIX 1 settings
Settings for other mixers are situated in other items of the menu and they are the same for each circuit.
Settings of the mixer without an extern sensor
It is necessary to set the required hot water in the heating circuit manually by means of the parameter Required MIX temperature, for example
to a value of 50 °C. The value has to be on such value, which ensures achievement of the required room temperature.
Having connected a room thermostat, it is necessary to set a value of the decrease of the required mixer temperature by a thermostat
(parameter MIX room thermostat) for example, to a value of 5 °C. This value has to be chosen by a trial and error method. A room thermostat
can be a traditional thermostat (NO and NC) or a room panel ecoSTER TOUCH. After reaction of the thermostat, the required temperature in
the mixer circuit is decreased, which at a sufficient choice of the value of the decreasing can cause a deceleration of the temperature growth in
the heated room.
Settings of the mixer with an extern sensor and with a room thermostat
Set the parameter Equithermal MIX control to Switched-on. Select an equithermal curve according to chapter 12.1. Set the required room
temperature with help of a parameter Parallel displacement according to the formula:
The required room temperature = 20 °C + parallel displacement of the heating curve.
Example:
To achieve a room temperature of 25 °C, the value of the parallel displacement of the heating curve has to be set to 5 °C. To achieve a room
temperature of 18 °C, the value of the parallel displacement of the heating curve has to be set to -2 °C.
In this configuration a room thermostat may be connected, which will balance an inaccuracy of the heating curve in case that the selected value
of the heating curve is too high. In this case it is necessary to set a value of decreasing the required mixer temperature by a thermostat, for
example, to a value of 2 °C. Having opened the thermostat contacts, the required temperature of the mixer circuit would be decreased, which at
a correct selection of the decreasing value causes the deceleration of growth of temperature in the heated room.
Settings of the mixer with an extern sensor and with a room panel ecoSTER TOUCH
Set the parameter Equithermal MIX control to Switched-on. Select an equithermal curve according to chapter 12.1. The regulator ecoSTER
TOUCH shifts the heating curve in dependence on a required room temperature. The regulator deduces the setting from 20 °C, for example, for
the required room temperature = 22°C the regulator shifts the heating curve by 2 °C, for the required room temperature = 18 °C the regulator
shifts the heating curve by -2 °C. In some cases described in chapter 12.1 it would be necessary to shift additionally the heating curve.
In this configuration, the room thermostat can decrease the heating circuit temperature by a constant value, provided that the required
temperature in the room would be achieved. Similarly, as it was described in the previous chapter (it is not recommended), or automatically it
can continually correct the heating circuit temperature.
We don’t recommend applying the both options at the same time.
Automatic correction of the room temperature proceeds according to the formula: Correction = (Required room temperature – Measured room
temperature) x room temperature coefficient /10.
Example:
The required temperature in the heated room (adjusted in ecoSTER TOUCH) = 22 °C.
The measured temperature in the room (through ecoSTER TOUCH) = 20 °C.
The room temperature coefficient = 15.
The required temperature in the heated room (adjusted in ecoSTER TOUCH) = 22 °C. The measured temperature in the room (through
ecoSTER TOUCH) = 20 °C. The room temperature coefficient = 15. The required temperature of the mixer will be increased by (22 °C - 20 °C)
x15/10 = 3 °C. It is necessary to find out a correct value of the parameter Room temperature coefficient. Range: 0…50. The higher a coefficient
value, the higher a required temperature correction. In case of setting to a value „0”, the required mixer temperature would not be corrected.
Warning: Adjustment of too high value of the room temperature coefficient can invoke regular fluctuations of the room temperature!
12.1 Equithermal regulation
Depending on the temperature measured out of the building, it is possible to control both the required boiler temperature, and the mixer circuits’
temperature. In case of a correct heating curve, the heating circuits’ temperature is adjusted in dependence on a value of the outdoor
temperature. Thanks to it, provided that there is selected a heating curve suitable for the given building, the temperature in the room remains
more or less constant – independently from the outdoor temperature.
In case of connection of the room panel, it is necessary to set timely the parameter Room temperature coefficient = 0.

10
Fig. №. 4 Heating curves.
Instructions for selection of an optimal heating curve:
- If the outdoor temperature is decreasing, but the room temperature is increasing, it means that the value of the selected heating curve is
too high,
- If the outdoor temperature is decreasing and the room temperature is decreasing as well, it means that the value of the selected heating
curve is too low
- If the room temperature is optimal at the frost weather, but is too low at the warm weather – we recommend increasing the parameter
heating curve parallel displacement and selecting a lower heating curve,
- If the room temperature is too low at the frost weather, and is too high at the warm weather – we recommend decreasing the parameter
heating curve parallel displacement and selecting a higher heating curve.
Buildings with insufficient heat-cladding require settings of the heat curves with higher values, while a heating curve for buildings with good heat-
cladding has a lower value.
The required temperature, calculated according to a heating curve, can be decreased a increased by the regulator, if it exceeds the
temperature range for the given circuit.
13 Description of night standby adjustment
The menu enables setting the time schedules of decreasing of the required temperature.
Time intervals enable to enter decreasing of the required temperature within a specified time interval – for example at night or if a user leaves
the heated rooms (for example, departure to work or school). Thanks to it the required temperature may be decreased automatically without a
loss of the temperature comfort with a simultaneous fuel consumption decreasing.
To activate time intervals, it is necessary to set the parameter Night decreasing to the option Inclusion/Yes. With this parameter you can
adjust by how many °C you want to decrease the temperature. The decreased temperature value is just unique for all time intervals.
It is possible to program a time schedule for each day of the week with an interval of 30 min. (48 changes of the level per day).
The time schedule settings are accessible through the option Schedule.
•Selection of a day in the week, for which you want to set/modify the time schedule.
•Viewing the window of the time schedule setting.
Required time schedule settings:
•set the indicator (2) tot the start of the time interval with the use of the buttons and
•press the button and adjust the required comfort (daily) or economic (night) temperature
•set the indicator (2) tot the end of the time interval with the use of the buttons and
•finish the modification of the given time schedule by pressing the button
•if needed, repeat the above mentioned instructions for the next time schedule
•the button (8) enables copying the time schedule for the next two days in the week
Fig. №. 5 Time interval selection window
Decreasing of the boiler required temperature from a time interval is signalized by the symbol: in the main window of the
display.
teplota zadaná ekvitermně(°C)
venkovní teplota (°C)
1. interval line
2. actually modified interval
3. night temperature
4. daily temperature
5,7 interval selection
6. required temperature selection
8. enter into menu of schedules copying
Equithermal required temperature
(°C)
Outdoor temperature (°C)
Night boiler decreasing/Monday
Instructions for correct the heating curve adjustment:
- floor heating 0,2 -0,6
- heating by radiators 1,0 - 1,6
- boiler 1,8 - 4

11
14 Manual control
It is possible to switch-on different working devices in the regulator, such as pumps, the feeder’s or the fan’s motor. In this way you can check
whether these devices are operable and correctly connected (OFF – switched-off, ON – switched-on).
You may only enter into the manual control menu in the standby STAND-BY mode, it means while the boiler is switched-off.
A long-term run of the fan, the feeder or other working device can cause a danger situation.
15 Favorite menu
An icon is on the bottom line of the display in the menu. After pressing the icon, the quick selection menu is displayed. Elements of this
menu are added to it by means of holding the icon in the floating menu.
To remove a selected item from the Favorite menu, it is necessary to hold this item (icon) in this menu and consequently confirm the intention of
its removal.
Service
16 Hydraulic schemes
The hydraulic scheme of connection of the boiler is in the Instructions for operation and installation of the boiler
VIADRUS A0C and A2C.
16.1 Scheme 1
Fig. №. 6 Scheme with a four-way valve, which controlls the central heating circuit
1
To improve the water circulation in a gravitational circuit of the boiler (the reinforced circuit on the picture), it is necessary to: use
big nominal cross-sections DN of the pipe and the four-way valve, avoid a big number of elbows and reductions of the cross-
section, use other rules for construction, such as keeping slopes, etc. As far as the sensor in the return pipeline is monitored by a
surface method, it is necessary to insulate it thermally from the environment and improve the thermal contact with the pipe with
using a thermal-conductive paste. The boiler required temperature has to be set on such level to ensure a thermal power for the
mixer circuit at the simultaneous heating water returning to the boiler.
PROPOSED SETTINGS:
Param
e
t
e
r
Adjusted value
M
E
N
U
Adjusted boiler temperature
75-80 °C boiler settings
Mixer 1 servicing Switched-on Central
heating service settings →mixer 1 servicing
MIX 1 max. temperature 70 °C service settings →mixer 1 settings
MIX 1 equithermal curve 0.8 – 1.4 MIX 1 settings
MIX 1 equithermal control Switched-on MIX 1 settings
1
The specified hydraulic scheme doesn’t replace a central heating project and only serves for visualization!
1. boiler,
2. burner,
3. regulator,
4. boiler temperature sensor CT4,
5 . flue gases temperature sensor CT2S
(only a review of temperature),
6 . four-way valve servomotor,
7 . mixer circuit pump,
8. mixer circuit temperature sensor CT4,
9. hot service water reservoir,
10. hot service water pump,
11. hot service water temperature sensor
CT4,
12. outdoor temperature sensor CT4-P,
13. room panel ecoSTER Touch or standard
room thermostat,
14. return pipeline temperature sensor
Pt1000

12
16.2 Scheme
2
Module B is not a part of delivery of the boiler – only on request.
1. boiler,
2. burner,
3. regulator,
4. boiler temperature sensor CT4,
5. flue gases temperature sensor CT2S (only a review of temperature),
6. boiler pump,
7. thermal accumulating reservoir,
8. hot service water pump,
9. hot service water reservoir,
10. hot service water temperature sensor CT4,
11. mixer valve servomotor,
12. mixer circuit temperature sensor CT4,
13. mixer pump,
14. room panel ecoSTER Touch with a room thermostat function or a standard room thermostat (NO and NC),
15. thermostatic three-way valve protecting against low temperature in the return pipeline,
16. accumulating reservoir upper temperature sensor CT4,
17. accumulating reservoir lower temperature sensor CT4,
18. outdoor temperature sensor,
19. auxiliary module B (is situated in the boiler control box).
Fig. №. 7 Scheme with an accumulating thermal reservoir
2
PROPOSED SETTINGS:
Param
e
te
r
Adjusted value
M
E
N
U
Adjusted boiler temperature
80 °C boiler settings
Temperature of the boiler CH pump switching-on 55 °C service settings →CH and HW settings
Accumulating reservoir operation switching
-off YES service settings →accumulating reservoir settings
Accumulating reservoir warming
-up start
temperature 50 °C service settings →accumulating reservoir settings
Accumulating reservo
ir warming-up finish
temperature 75 °C service settings →accumulating reservoir settings
Mixer 1 servicing Switched-on
Central heating service settings →mixer 1 settings
MIX 1 max. temperature 70 °C service settings →mixer 1 settings
MIX 1 equithermal curve 0.8 – 1.4 MIX 1 settings
MIX 1 equithermal control Switched-on MIX 1 settings
Selection of MIX 1 thermostat ecoSTER T1 service settings →mixer 1 settings
2
The specified hydraulic scheme doesn’t replace a central heating project and only serves for visualization!

13
16.3 Scheme 3
Module B is not a part of delivery of the boiler – only on request.
1. boiler,
2. burner,
3. regulator,
4. boiler temperature sensor CT4,
5. flue gases temperature sensor CT2S,
6. boiler pump,
7. thermal accumulating reservoir,
8. hot service water pump,
9. hot service water reservoir,
10. -
11. three-way valve with a servomotor,
12. mixer circuit pump,
13. mixer circuit temperature sensor CT4,
14. standard room thermostat (NO and NC),
15. standard room thermostat (NO and NC),
16. accumulating reservoir upper temperature sensor CT4,
17. accumulating reservoir lower temperature sensor CT4,
18. outdoor temperature sensor CT4-P,
19. room panel ecoSTER Touch with a room thermostat function or a standard
room thermostat (NO and NC),
20. -
21. auxiliary module B (is situated in the boiler control box),
22. -
23. hot service water temperature sensor CT4.
Fig. №. 8 Scheme with a thermal accumulating thermal reservoir and with three mixing heating circuits
3
,
PROPOSED SETTINGS:
Param
e
te
r
Adjusted value
M
E
N
U
Adjusted boiler temperature
80 °C boiler settings
Temperature of the boiler CH pump switching-on 55 °C service settings →CH and HW settings
Accumulating reservoir operation switching
-off Switched-on service settings →accumulating reservoir settings
Accumulating reservoir warming
-up start
temperature 50 service settings →accumulating reservoir settings
Accumulating re
servoir warming-up finish
temperature 75 service settings →accumulating reservoir settings
Mixer 1,2,3 servicing Switched-on
Central heating service settings →mixer 1,2,3 settings
Mixer 1,2,3 max. required temperature 70 °C service settings →mixer 1,2,3 settings
MIX 1,2,3 equithermal curve 0.8 – 1.4 MIX 1,2,3 settings
MIX 1,2,3 equithermal control Switched-on MIX 1,2,3 settings
Selection of mixer 1 thermostat ecoSTER T1 service settings →mixer 1 settings
Selection of mixer 2 thermostat Universal service settings →mixer 2 settings
Selection of mixer 3 thermostat Universal service settings →mixer 3 settings
3
The specified hydraulic scheme doesn’t replace a central heating project and only serves for visualization!

14
16.4 Orientational electric scheme (auxiliary)
Electric scheme of boiler connection is in the Instructions for operation and installation of the boiler VIADRUS A0C
and A2C.
T1 boiler temperature sensor CT4,
OS optical flame sensor (placed in the boiler burner),
T2 temperature sensor (placed in the boiler burner),
H voltage output for signalization of alarms or signalization of operation status of the regulator or for control of a reserve boiler,
T3 hot service water temperature sensor CT4,
T4 outdoor temperature sensor CT4-P,
T5 flue gases temperature sensor CT2S,
T6 mixer temperature sensor CT4,
RT room thermostat,
HS fan rpm sensor (placed in the boiler burner),
P boiler display,
ecoSTER Touch room panel with a function of room thermostat (replaces RT),
D-D+ connector for auxiliary modules,
B module enables servicing other two mixing circuits and servicing the thermal accumulating reservoir,
L N PE mains power supply 230V~,
FU line fuse 6,3 A,
STB boiler safety thermostat,
FO burner fan (placed in the boiler burner),
FG burner feeder,
FH burner feeder or rotate grate cleaning mechanism,
FV flue gases fan,
I ignitor (placed in the boiler burner),
PB boiler’s or accumulating reservoir’s pump,
PHD hot service water pump,
PM mixer pump,
SM mixer servomotor,
CPU control.
Fig. №. 9 Scheme of electric connection of the regulator

15
Module B is not a part of delivery of the boiler – only on request.
Fig. №. 10 Scheme of electric connection of the module B
16.5 Connection of temperature sensors
Cables of the sensors may be prolonged by conductors with the cross-section at least 0,5 mm
2
. However, the total length of cables for each
sensor mustn’t be longer than 15 m.
The boiler temperature sensor is to be mounted in a thermowell placed in the boiler cladding. The hot service water temperature sensor in the
thermowell is welded to the reservoir. We recommend installing the mixer temperature sensor in a case placed in the flow of water flowing
through the pipe, but it is also allowed to mount the sensor on the pipe surface under condition of using a thermal insulation, which protected the
sensor together with the pipe.
Sensors have to be protected against falling-off from the surfaces, to which they are fixed.
It is necessary to provide a good thermal contact between the sensors and the measured surface. Use thermally conductive paste for these
purposes. It is forbidden to pour oil or water to the sensors.
Cables of the sensors have to be separated from mains cables. Otherwise an error during measurement can occur. The minimum distance
between these cables has to be at least 10 cm.
It is necessary to prevent from a contact of the sensors cables with hot parts of the boiler and the heating system. The cables of the
temperature sensors are resistant against temperature up to 100 °C.
16.6 Outdoor sensor connection
The regulator only interoperates with an extern sensor with type of CT4-P. The sensor has to be placed on the coldest wall of the building;
usually it is the Nord wall in a roofed place. The sensor mustn’t be influenced by the direct effect of sunshine and rain.
The sensor has to be fixed on the height at least 2 m above the landscape, far from windows, chimneys and other heat sources, which may
falsify temperature measurement (at least 1,5 m).
You should use for connection a cable with the cross-section of the conductors at least 0,5 mm
2
with the length up to 25 m. Conductors polarity
is not important.Connect the second end to the terminals of the regulator according to fig. 11.
The sensor has to be screwed to a wall with mounting screws. To access to the mounting screws holes, unscrew the cover of the sensor box.
Module B (A2) expansion module for two heating
circuits, the accumulating reservoir and alarm
signalization
T1 boiler temperature sensor CT4
T2 mixer 1 circulation temperature sensor CT4
T3 accumulation temperature sensor (upper) CT4
T4 HW temperature sensor CT4
T room thermostat of mixer (MIX) of heating
circuit TO2 or TO3
RE relay
R reserve source (reserve boiler)
AL alarm signalization
PC circulating pump
SM mixing valve (MIX) of heating circuit TO2 or
TO3
PM mixer pump (MIX) of heating circuit TO2 or TO3
A1 boiler control unit (regulator)
GR earthing shunt (green)

16
Fig. №. 11 Connection of the outdoor sensor CT4-P.
16.7 Check of temperature sensors
The temperature sensors CT4/CT4-P can be checked by means of measurement of their resistance at the given temperature. In case you find
out a significant difference between a value of the measured resistance and the values from the following table, it is necessary to replace the
sensor.
C
T4
Environment
temperature (°C) Min. (Ω) Nominal (Ω) Max. (Ω)
0
802
815
828
10
874
886
898
20
950
961
972
25
990
1000
1010
30
1029
1040
1051
40
1108
1122
1136
50
1192
1209
1225
60
1278
1299
1319
70
1369
1392
1416
80
1462
1490
1518
90
1559
1591
1623
100
1659
1696
1733
16.8 Connection of a thermostat of the mixers
The room thermostat after disconnection of the contacts decreases the required temperature of the mixer circuit by a value of the mixer required
temperature decreasing by a thermostat. The parameter is placed in the menu:
Service settings →Mixer settings 1-3 →Thermostat selection →Universal
The value of the parameter has to be chosen so that the room temperature decreases after a reaction of the room thermostat (opening the
contacts). The remaining adjusted values – according to chapter 12. In case of connection of a room panel ecoSTER TOUCH it is necessary to
ensure that the parameter Thermostat selection in the menu Service settings →Mixer settings 1-3 →Thermostat selection →ecoSTER
was correctly chosen.
16.9 Connection of a boiler room thermostat
The room thermostat for the boiler circuit may switch-off the burner operation or the CH boiler pump. In order to enable switching-off the boiler
operation by the room thermostat, it is necessary to set a value Thermostat selection to universal or ecoSTER T1 (provide a room panel
ecoSTER TOUCH was connected):
Boiler settings →Thermostat selection.
In order to provide that a room thermostat switches-off the CH boiler pump (without switching-off the boiler), it is necessary to set the value of
the parameter Pump switching-off by a thermostat to YES.
Service settings →Boiler settings →Pump switching-off by a thermostat.
C
T
4
-
P
(venkovní)
Temperature (°C) Min. (Ω) Nom. (Ω) Max. (Ω)
-
30
609
624
638
-
20
669
684
698
-
10
733
747
761
0
802
815
828
10
874
886
898
20
950
961
972
Mounting screw
holes
Mounting screw 2 pcs
Cable 2x0,5 mm
2
Max. length 25 m
Cable Ø 3-6,5 mm

17
16.10 Connection of a reserve boiler (a reserve source)
The regulator can control the operation of a reserve boiler (gasous or oil one). In this case there is no necessity to switch-on or switch-off
manually this boiler. A reserve boiler would be switched-on in case of decreasing the pellet boiler temperature and will switched-off when the
pellet boiler achieves the required temperature. A connection to the reserve boiler, for example, a gas one, has to be made by a qualified
installer in accordance with technical documentation of this boiler.
Warning: A reserve boiler must be connected by means of a relay to the regulator A1 (terminals 39-40, output voltage DC 12
V).
Fig. №. 12 Visible scheme how to connect a reserve boiler to the regulator,
Mounting of the relay in accordance with valid regulations has to be performed by a person with a proper qualification.
The reserve boiler control can be set by means of a parameter:
Service settings →Boiler settings →Reserve boiler →Reserve source switch-on temperature
The reserve boiler is switched-off after setting the zero value (Off) - switching-off this parameter.
The control output of the reserve boiler is also shared with the alarm output. Having switched-off the control of the reserve boiler,
this output is controlled by a module for alarm control.
After kindling the pellet boiler, when its temperature exceeds the required value, for example, 25 °C, the regulator switches-off the reserve boiler
(it brings DC voltage 12V to the terminals 39-40). As a result of it, the relay coil is powered and its contacts are disconnected. Having dropped
the boiler temperature under the value of the parameter Reserve boiler switch-off temperature, the regulator stops to increase voltage to the
terminals 39-40, which switches-on the reserve boiler.
After switching-over the regulator to stand-by mode, the reserve boiler is switched-on.
16.11 Connection of alarm signalization
The regulator can signalize alarm situations by means of switching-on extern devices, for example, a bell or a GSM device to send SMS – short
text messages. The alarm signalization device has to be connected according to fig. 15 through a relay. Taking into consideration that this
output is shared with the control output of the reserve boiler for the purpose of activation of the alarm function on this output, it is firstly
necessary to switch-off the reserve boiler control. To do it, it is necessary in the menu:
Service settings →Boiler settings →Reserve source →Reserve source switch-on temperature →OFF
to set the zero value of its switching-off.
The selection of an alarm for signalization:
Service settings →Boiler settings →Alarms signalization
1 regulator module,
2 reserve boiler (gas or oil one),
3 relay RM 84-2012-35-1012 and foot GZT80 ELPOL.
The regulator usually doesn’t contain a relay.

18
Fig. №. 13 Connection of an extern alarm,
16.12 Mixer connection
To activate a mixer function, it is necessary to ensure that the mixer temperature sensor is connected (without connection of a
sensor, this function is hidden).
The regulator only interconnects with such servomotors of the mixing valves, which are equipped with end-limit switches. Electric connection for
the servomotor opening or closing is 230 V. Usage of other servomotors is forbidden. Servomotors with the opening time range from 30 to 255
may be used.
Description of the mixer connection:
−connect the mixer temperature sensor,
−electrically connect the mixer pump,
−switch-on the regulator and select in the service mode a proper Mixer servicing Service settings →Mixer 1 settings
−enter in the mixer service settings a proper Valve opening time (the time should be presented on the production label of the servomotor,
for example, 120 s).
−electrically connect the mixer servomotor:
- opened: in the regulator it corresponds to the position of 100 % ON (temperature in the mixer circuit is the maximum)
- closed: in the regulator it corresponds to the position of 0 % OFF (temperature in the mixer circuit is the minimum).
−open the function Main menu →Manual control of correct connection of the electric device.
−set other mixer parameters according to chapter 18.5.
16.13 Connection of a circulating pump
The circulating pump has to be connected by means of a relay to the regulator A1 (clamps 39-40, output voltage DC 12 V) or the auxiliary
module B - A2 (clamps 30-31, output voltage DC 6 V). The value of Output H or Output H mode B/C has to be set to Circulating pump.
16.14 Connection of ecoSTER TOUCH room panel
The regulator can be equipped with a room panel ecoSTER TOUCH, which can fulfill functions of:
- a room thermostat,
- a control panel of the boiler,
- alarm signalization,
- a fuel level indicator.
Four-conductors connection: Connect in accordance with the electric scheme.
Two-conductors connection: Two conductors connection requires usage of a power supply source with DC voltage +12 V with
nominal current at least 0,5 A.
Supply places of ecoSTER TOUCH:
Connect GND and VCC to an extern power supply source. A power supply source is not a part of equipment of the regulator. Connect
conduction D+ and D- as is specified in the electric scheme.
The maximum length of the cables to the auxiliary panel mustn’t exceed 30 m, the cross-section of their conductors mustn’t be lower than
0,5 mm
2
.
1 – regulator,
2 – extern alarm,
3 – relais.

19
16.15 Access to parameters of the regulator through internet
In using an auxiliary internet module Net Control, the device enables a remote control to the data containing in the device through the WiFi and
LAN networks. In this case the regulator can be maintained with help of a standard internet browser of WWW pages installed in PCs and mobile
devices.
A method of connection of the Net Control module is described in a corresponding manual for operation for this module.
16.16 Feeder calibration
To provide economic and ecological operation of the boiler, it is important to dose correctly fuel to the burner. The control unit itself on the basis
of entered parameters evaluates how much fuel has to be delivered to the burner, that’s why it is necessary to perform a calibration of the
feeder.
The feeder calibration has to be performed during commissioning the boiler or at changing the fuel during operation of the boiler (for example, a
change of a supplier, a type or the diameter of pellets).
The procedure of calibration:
−the feeder auger has to be fully filled up by fuel;
−pull out the orifice of the conveyance hose from the filler neck of the burner and insert it into the reservoir (or into a PE pack);
−the control unit has to be in the stand-by mode;
−by selection of Main menu →Service settings →Burner settings →Others →Feeder calibration →START, start the fuel feeder for
15 min;
−having finished the calibration, weight up the pellets weight (don’t remember to deduct the weight of the vessel or a PE pack);
−enter the fuel weight in grams to the parameter Enter fuel weight and confirm it by pressing OK;
−enter fuel heating power in kWh/kg according to the fuel manufacturer and confirm it by pressing OK;
−set the Maximum burner power:
VIADRUS A0C X20P. - 23 kW
VIADRUS A0C X28P - 31 kW
VIADRUS A2C S20P - 23 kW
VIADRUS A2C S30P - 33 kW
and confirm it by pressing .
17 Structure - service menu
Service settings
„1992“
Burner settings
•Ignition
−Ignition test time
−Flame detection
−Fan power during firing-up
−Firing-up time
−Pressure fan after firing-up
−Pressure fan running time after firing-up
−Ignition time
−Operation time with minimum power
−Initial dose correction
•Operation
−Working mode ON/OFF
−Feeder power
−Fuel heating power
−Reservoir capacity
•Extinguishing
−Maximum extinguishing time
−Minimum extinguishing time
−Blowdown power
−Blowdown time
−Blowdown interruption
−Blowdown start
−Blowdown stop
•Cleaning-up
−Cleaning time after extinguishing
−Blowing at cleaning
•Standby
−Burner power in standby mode
−Standby time
•Grate
•Others
−Minimum fan power
−Fuel detection time
−Burner max. temperature
−Maximum flue gases temperature
−Additional feeder operation time
−Flue gases exhaust fan
−Feeder calibration
Boiler settings
•Thermostat selection
•Boiler min. temperature
•Boiler max. temperature
•Reserve source
•Alarms
•Boiler cooling-down temperature
•Pump switching-off by thermostat
•Boiler effectiveness
CH and HW settings
•Boiler pump switch-on temperature
•CH and HW idle
•HW reservoir minimum temperature
•HW reservoir maximum temperature
•Boiler temperature increase towards HW and MIX
•HW pump run-out
Accumulating reservoir settings
•Accumulation reservoir operation switch-off
•Warming-up start temperature
•Warming-up finish temperature
−
Mixer settings 1 (2,3)*
•Mixer servicing 1 (2, 3)
•Switched-off
•CH is switched-off
•Floor heating is switched-on
•Only pump
•MIX 1 (2, 3) minimum temperature
•MIX 1 (2, 3) maximum temperature
•MIX opening time
•Pump switching-off by thermostat
Output H1
•Reserve boiler
•Alarms
•Circulating pump
Display advanced
Renew the initial settings
Touch panel calibration
* Unavailable, if a corresponding sensor or an additional module is not connected, or if the parameter is hidden.

20
18 SERVICE SETTINGS - code 1992
18.1 Burner service settings
Ignition
Ignition test time The time of checking, whether the heating chamber has been already ignited. Only a fan is in operation.
Flame detection A flame detection threshold in % of light, at which the regulator finds out that the fire in the heating chamber is
already burning. It is also used for location of a lack of fuel and at the end of extinguishing.
Fan power during firing-up % of rpm of the fan during firing-up. Too high value prolongs an ignition procedure or would cause an
unsuccessful attempt of ignition.
Firing-up time A time of other attempts to ignite (3 attempts). After finishing this time, the regulator goes over to another attempt
of ignition
Pressure fan after firing-up % of the fan rpm after the flame detection.
Pressure fan running time
after firing-up A time of the fan operation with the power Pressure fan after firing-up. It enables a better firing-up of the heating
chamber before the entrance into the STABILIZATION mode.
Ignition time An ignitor operation time without a fan. It mustn’t be too long in order to avoid a damage of the ignitor. After the
lapse of this time, the ignitor continues to work till the moment of the flame detection.
Operation time with
minimum power Duration of STABILIZATION operation mode.
Operation
Thermostat mode
It switches-over the burner into the THERMOSTAT mode, for example, for operation in a bakery. The burner
works on the maximum power without power modulation. The burner is switched-off at the moment of
disconnection of the thermostat contacts 28-29. The boiler temperature sensor has no influence to the burner
operation.
Feeder power Fuel feeder power in kg/h.
Fuel heating power Fuel heat power in kWh/kg.
Min. burner power Minimum burner power in kW.
Middle burner power Middle burner power in kW.
Max. burner power Maximum burner power in kW.
Reservoir capacity Fuel reservoir capacity for calculation of the fuel level. After entering a correct value, a user doesn’t need to
perform a fuel level calibration. The regulator uses these data when no fuel level calibration was performed. After
a successful fuel level calibration, the regulator doesn’t use this value.
Extinguishing
Extinguishing max. time After this time, the boiler is goes over to IDLE mode, although the flame sensor signalizes the presence of flame.
Extinguishing min. time Extinguishing will last at least for this time, although flame is not already detected by the flame sensor.
Blowdown power Fan power at blowdown during extinguishing in %.
Blowdown time Blowdown duration at fuel residual burning during extinguishing.
Blowdown interruption Interruption between blowdowns at fuel residual burning during extinguishing.
Blowdown start Flame intensiveness in %, at which blowdown starts at fuel residual burning during extinguishing.
Blowdown stop Flame intensiveness in %, at which the fan switches-off at fuel residual burning during extinguishing.
Cleaning
-
up
Cleaning time after
extinguishing Fan operating time during extinguishing the heating chamber.
Blowing during cleaning-up Fan power in % at the heating chamber cleaning-up during extinguishing and firing-up.
Standby
Burner power in standby
mode Burner power in STANDBY mode.
Standby time After this time from the moment of going-over the regulator into the STANDBY mode, an automatic burner
extinguishing is following on. In case of the setting = 0 the STANDBY mode would be fully switched-off.
Grate
Blowdown operation Duration of the fan blowdown during STANDBY during operation in the GRATE mode.
Blowdown interruption Interruption time between blowdowns during STANDBY during operation in the GRATE mode.
Others
Minimum fan power Minimum fan power in %, which may be chosen by a user of the regulator. It is only used for limitation of the
accessible range of the fan power. It is not used for the algorithm for the fan control. It has to be – if possible – so
small to ensure slow rotation of the fan, as well as freely and without “roar”.
Fuel detection time The time is counted-down after dropping the flame brightness under the value of Flame detection. Having
counted-down this time, the regulator would try to ignite the burner, and after 3 unsuccessful attempts, it would
announce an alarm "Unsuccessful attempt to ignite".
Burner max. temperature It determines the maximum temperature of the feeder, at which an alarm of exceeding the maximum temperature
of the feeder will be invoked.
Flue gases max.
temperature It determines the maximum flue gases temperature, at which an alarm of exceeding the maximum flue gases
temperature will be invoked.
Additional feeder operation
time
It determines a working time of the auxiliary feeder (the feeder of the bunker). The feeder is connected to the
auxiliary module B. After the lapse of this time, the auxiliary feeder would be stopped, though the fuel level sensor
contacts are opened. The fuel level sensor contacts are placed in the auxiliary module B.
Flue gases exhaust fan It enables connection of the flue gases exhaust fan.
Feeder calibration It serves for performance of calibration of the feeder power, see chapter 16.16 – Feeder calibration.
Table of contents
Popular Control Unit manuals by other brands

Leuze electronic
Leuze electronic AC-CPB quick start guide
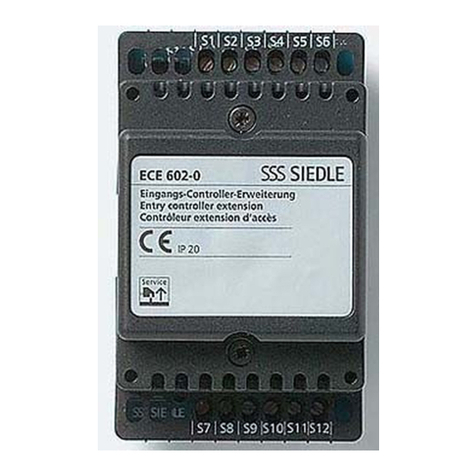
SSS Siedle
SSS Siedle ECE 602-0 Product information
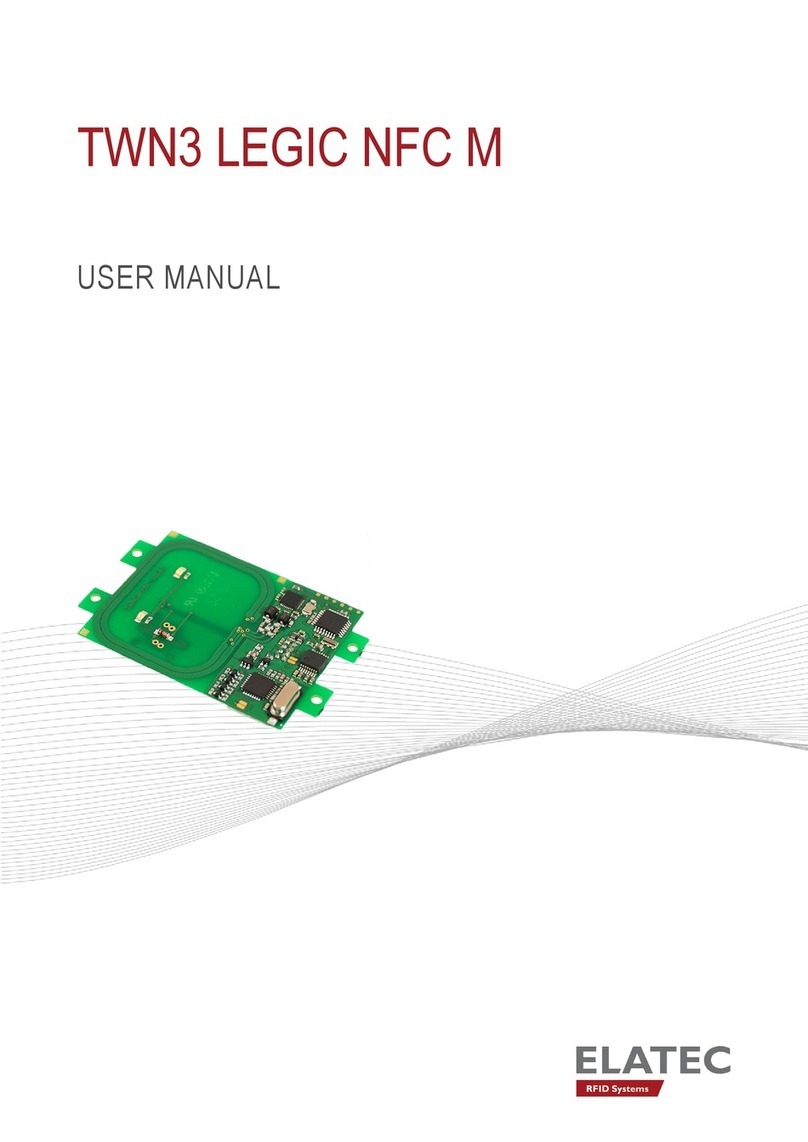
Elatec
Elatec TWN3 LEGIC NFC M user manual
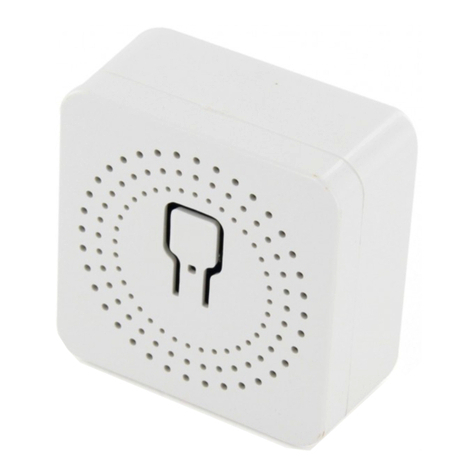
edisio
edisio EMV-400M manual
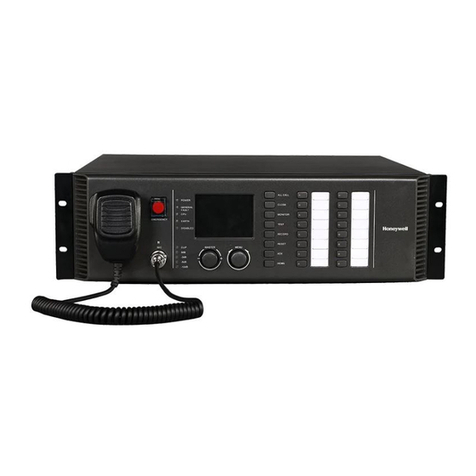
Honeywell
Honeywell RK-MCU Product instructions
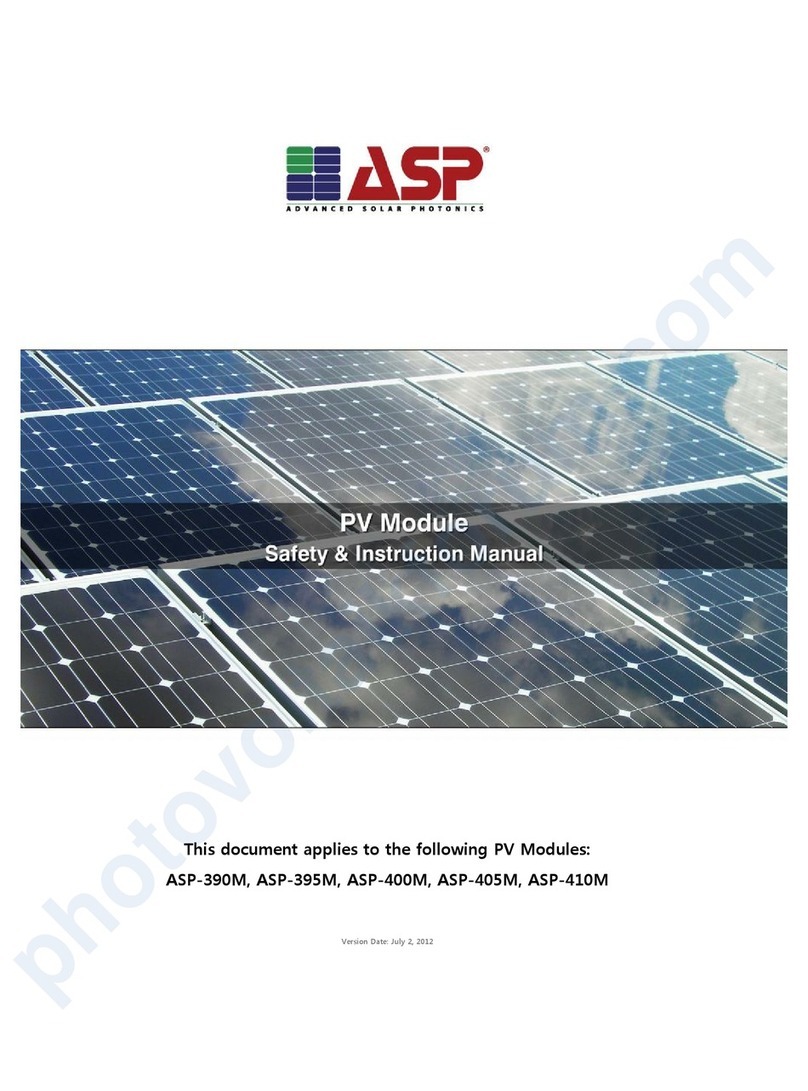
Advanced Solar Photonics
Advanced Solar Photonics ASP-390M Safety & instruction manual
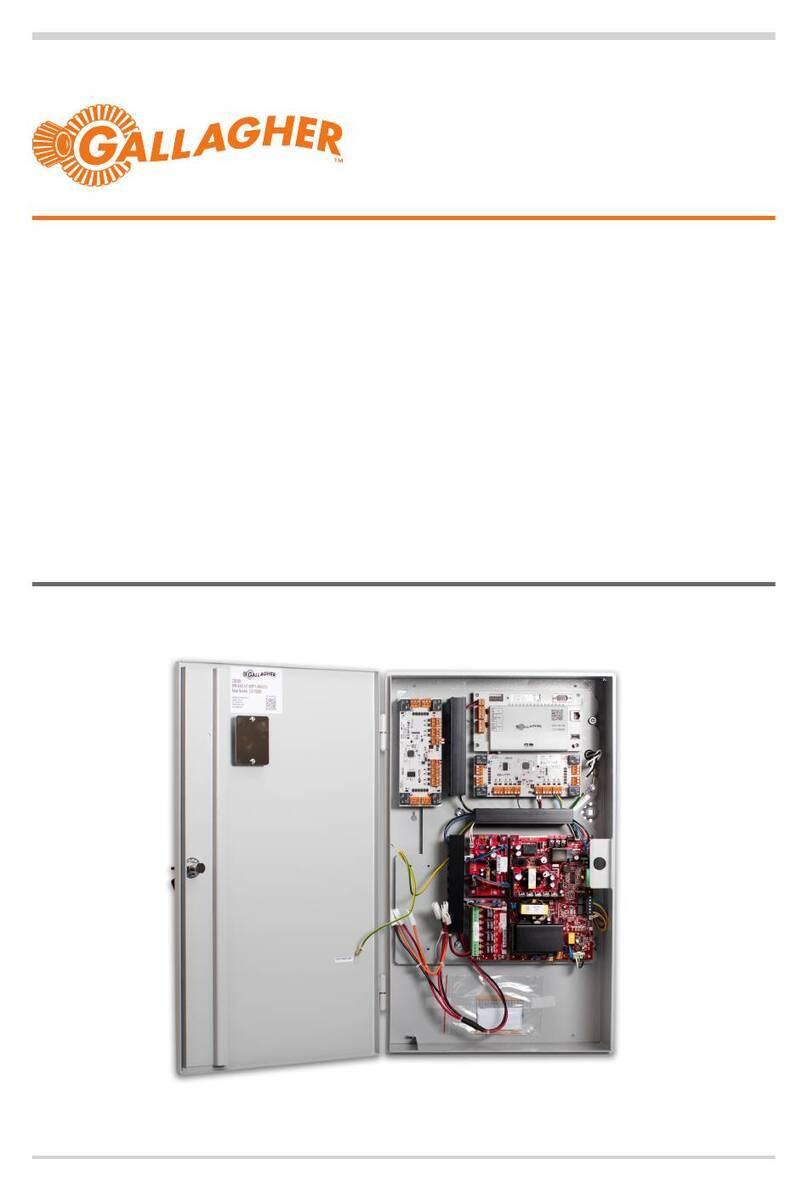
Gallagher
Gallagher C500306 Installation notes

We
We TARVOS-III Migration guide
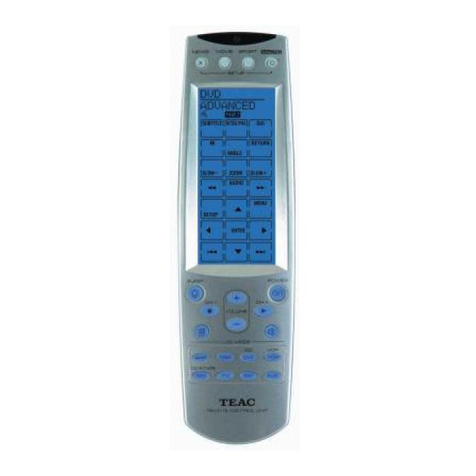
Teac
Teac RC-L800 owner's manual
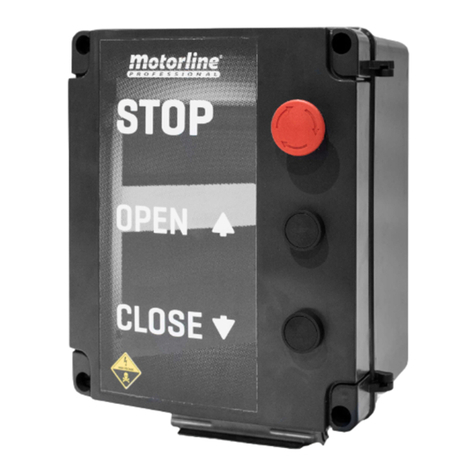
Motorline professional
Motorline professional MC112PR Use and care guide
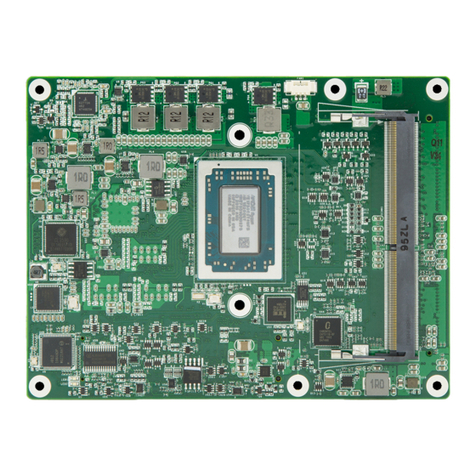
Arbor Technology
Arbor Technology EmETXe-a10M3 Quick installation guide
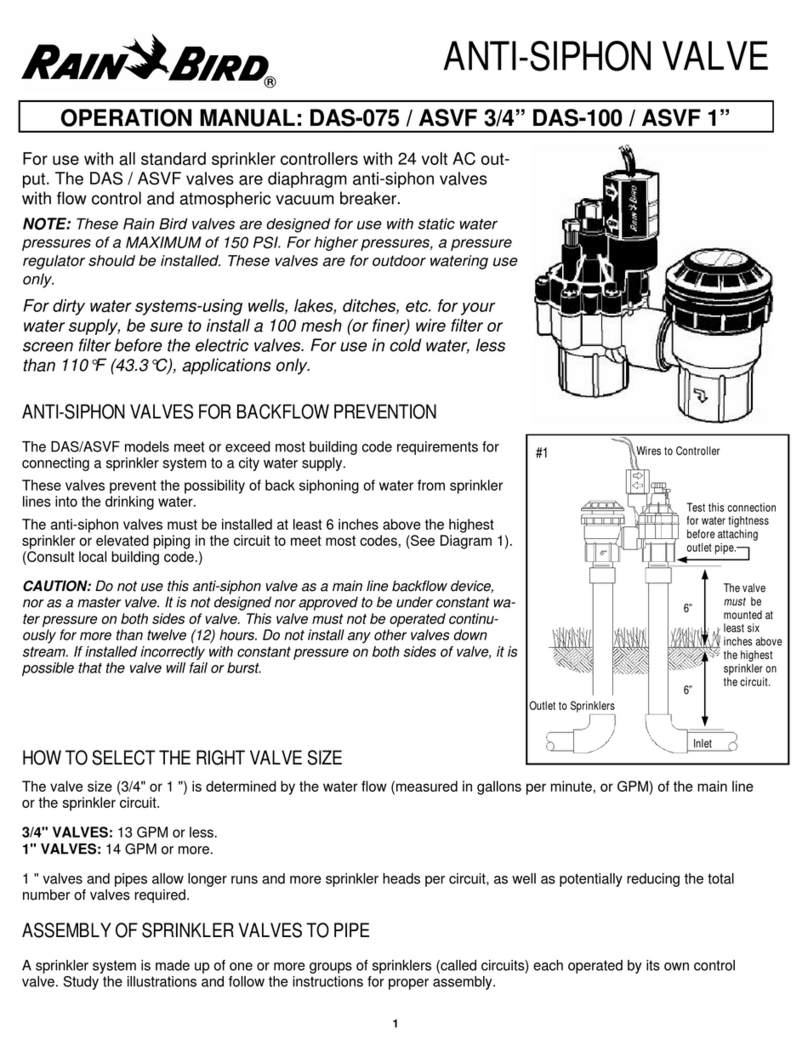
Rain Bird
Rain Bird DAS-075 / ASVF 3/4 Operation manual