Welker CP2GM User manual

© 2011 Welker, Inc. All rights reserved.
Installation, Operation, and
Maintenance Manual
Welker® Constant Pressure Cylinders
with Tracker Tube
(with Gravity Mixer)
Model
CP2GM & CP5GM
The information in this manual has been carefully checked for accuracy and is intended to be used as a guide for
the installation, operation, and maintenance of the Welker equipment described above. Correct operating and/or
installation techniques, however, are the responsibility of the end user. Welker reserves the right to make changes
to this and all products in order to improve performance and reliability.
13839 West Bellfort St.
Sugar Land, TX 77498-1671
(281) 491-2331 - Office
(800) 776-7267 - USA Only
(281) 491-8344 - Fax
http://www.welkereng.com

TABLE OF CONTENTS
IOM-013 Page 2 of 18
CP2 & CP5GM
Rev: D
Last updated: 4/14/2011
1. SPECIFICATIONS 3
1.1 INTRODUCTION 3
1.2 DESCRIPTION OF PRODUCT 3
1.3 IMPORTANT INFORMATION 4
1.4 SPECIFICATIONS 5
2. INSTALLATION &OPERATIONS 6
2.1 IMPORTANT INFORMATION 6
2.2 PRE-CHARGING THE CYLINDER 6
2.3 INSTALLATION 8
2.4 SPOT SAMPLING 9
2.5 CONTINUOUS SAMPLING 9
2.6 MIXING THE COLLECTED SAMPLE 10
3. MAINTENANCE 11
3.1 GENERAL 11
3.2 MAINTENANCE PARTS DIAGRAM 12
3.3 DISASSEMBLY 13
3.4 MAINTENANCE 13
3.5 REASSEMBLY 14
3.6 CYLINDER CLEANING 15
SAFTEY WARNING 16
4. TROUBLE SHOOTING GUIDE 17
Welker®, Welker Jet®, and WelkerScope®are Registered Trademarks owned by Welker, Inc.

SPECIFICATIONS
IOM-013 Page 3 of 18
CP2 & CP5GM
Rev: D
Last updated: 4/14/2011
1. GENERAL
1.1 INTRODUCTION
We appreciate your business and your choice of Welker products. The installation,
operation and maintenance liability for this product becomes that of the purchaser at the
time of receipt. Reading the applicable Installation, Operation and Maintenance (IOM)
Manual prior to installation and operation of this equipment is required for a full
understanding of its application and performance prior to use.
If you have any questions, please call 1-800-776-7267 in the USA or 1-281-491-2331.
Notes, Cautions, and Warnings
Notes emphasize information or set it off from the surrounding text.
Caution messages appear before procedures that, if not observed, could
result in damage to equipment.
Warnings are alerts to a specific procedure or practice that, if not
followed correctly, could cause personal injury.
*The following procedures have been written for use with standard Welker parts and equipment.
Assemblies that have been modified may have additional requirements and specifications that are not listed
in this manual.
1.2 DESCRIPTION OF PRODUCT
The Constant Pressure Sample Cylinder is
designed for use in systems where it is necessary to
extract and isolate accurate product samples by
maintaining a steady pressure from the pipeline to
the cylinder. The cylinders are equipped with a
magnetic indicator and a graduated scale set to
specify the capacity of the device.
During continuous sampling, when the magnetic
indicator reaches the 80% mark, all sampling
should be stopped. A pneumatic supply pre-
charges the cylinder with pressure to correspond
with pipeline pressure. Pre-charging allows the
sample to be transferred to the cylinder without

SPECIFICATIONS
IOM-013 Page 4 of 18
CP2 & CP5GM
Rev: D
Last updated: 4/14/2011
taking a pressure drop. An internal piston in the cylinder helps to purge out air and contaminants
prior to taking the sample by displacement. The stainless steel gravity-action mixer works in
conjunction with the cylinder rod; mixing is accomplished by inverting the cylinder several times.
Welker CP-2 & CP-5 Premium Purge model cylinders have valves built into the pre-charge and
product end cap ports. They are also included with product purge and pre-charge purge valves.
During the purge process, the piston is pushed to the end of the cylinder, also preventing any
other possible contaminants from entering. Burst discs and gauges are also included on each end
cap of the device. In the event that the cylinder is overpressurized, these discs will rupture,
relieving excess pressure from the cylinder. Welker CP-2 & CP-5 Premium Purge model
cylinders have valves built into the pre-charge and product end cap ports. They are also included
with product purge and pre-charge purge valves.
Adjustable relief valve (optional)
The adjustable relief valve functions as a safety device for the unit.
During continuous sampling and transportation of the cylinder, the relief
valve assures that the device maintains a constant pressure and does not
exceed maximum allowable pressure. The valve will relieve any pressure
that exceeds the set pressure.
1.3 IMPORTANT INFORMATION
Please read the following information in its entirety before using the Welker equipment
described above. Failure to adhere to the recommendations could result in injury.
Never fill a cylinder completely full of hydrocarbon liquid or refrigerated gas. Always
allow for at least 20% expansion.
Protect the cylinder at all times and handle with care. It is a precision instrument and may
contain a flammable or hazardous product as well as a valuable representation of your
company’s product.
When analysis is complete, the cylinder should be emptied safely and in a safe area by opening
the product inlet valve, allowing the pre-charge pressure to push the piston to the product end
cap, emptying the cylinder.
Welker recommends cleaning and leak testing of the cylinders after each use.
Because of the design of the cylinder and the incorporated seals, the process of emptying the
cylinder will simultaneously wipe the walls of the device clean. The end cap will also be
purged clean with the next use.
Never transport a cylinder with pressure exceeding D.O.T. regulations (see U.S. Government
CFR 49 for D.O.T. regulations). In cases where the cylinders are exposed to varying
temperatures, do not allow the cylinder to exceed the maximum allowable operating
pressure indicated in Table 1 on page 5.
Figure 2
Figure 1

SPECIFICATIONS
IOM-013 Page 5 of 18
CP2 & CP5GM
Rev: D
Last updated: 4/14/2011
1.4 SPECIFICATIONS
The specifications listed in this section are generalized for this equipment. Welker can
modify the equipment according to your company’s needs. However, please note that
*the specifications may vary depending on the customization of your product.
Table 1
SPECIFICATIONS
Products Sampled: Light liquid hydrocarbons, refined products, liquid
petroleum gas, natural gas liquids, light crude and
condensate
Materials of Construction: 316 stainless steel, aluminum, Viton, and PTFE; others
available.
Maximum Allowable Operating
Pressure*:
CP2
1,800 psi @ -20°F to 120°F
(124 bar @ -28.9°C to 37.8°C)
CP5
600 psi @ -20°F to 120°F
(41 bar @ -28.9°C to 37.8°C)
Sample Inlet & Outlet Connections: ¼” NPT (others available)
Relief Valve Connection: ½” NPT (¼” NPT available)

INSTALLATION & OPERATIONS
IOM-013 Page 6 of 18
CP2 & CP5GM
Rev: D
Last updated: 4/14/2011
2. INSTALLATION &OPERATIONS
2.1 IMPORTANT INFORMATION
After unpacking the unit, check it for compliance and for any damages that may have
occurred during shipment.
Claims for damages caused during shipping must be initiated by the receiver and
directed to the shipping carrier. Welker is not responsible for any damages caused from
mishandling by the shipping company.
When sealing fittings with PTFE tape, refer to the proper sealing instructions for the
tape used.
There are two ends to the cylinder, separated internally by a floating piston. One end is
marked PRODUCT INLET; this end can easily be identified by the blue vertical line on
the tracker tube. The other end of the cylinder is marked PRE-CHARGE END, and it
is marked on the tracker tube with a red vertical line at both 80% full and 100% full.
A sample probe should be located in the least turbulent area available of the flowing
stream; i.e., not in a header or blow-down stack and away from obstructions, elbows or
partially closed valves. The sample probe should be installed reaching approximately
into the center one-third of the pipeline.
The sample cylinder should be located as close to the sample point as is possible.
Recommended Tools
It would be advisable to have the following tools available for installation of the unit.
However, tools used will vary depending on cylinder model.
Flexible hose or tubing
6” adjustable wrench
Tubing cutters
Small diameter stainless steel tubing
2.2 PRE-CHARGING THE CYLINDER
The pre-charge gas being used must be compatible with the seals in the cylinder. The
relief valves and gauges must also be adequate for the pressures used when pre-
charging.

INSTALLATION & OPERATIONS
IOM-013 Page 7 of 18
CP2 & CP5GM
Rev: D
Last updated: 4/14/2011
Figure 4 -
Product End Cap
1. Connecting the cylinder pre-charge valve to the pipeline (pressurized gas pipeline
only):
1. Use small diameter stainless steel tubing to
connect from an available pipeline valve to
the pre-charge inlet valve. (See Figure 3).
2. Make sure all valves are closed on the
sample cylinder.
3. Open the pipeline isolation valve.
4. Slowly open the pre-charge inlet valve.
5. Slowly open the product inlet valve (see
Figure 4), to relieve any pressure buildup.
6. The piston will begin to move.
Always open valves slowly to avoid slamming the piston from one end to the
other.
7. The pre-charge gauge should begin to read pressure and will eventually reach pipeline
pressure.
8. Once the piston has reached the end of the cylinder, close all valves and check for
leaks.
9. Disconnect the tubing from the cylinder and from the pipeline isolation valve.
2. Connecting the pre-charge valve to the return port on a sampler probe (for
continuous sampling of pressurized gas pipeline only):
1. Install a valve into the return port of the
sampler probe.
2. Make sure all valves are closed on the
sample cylinder.
3. Use small diameter stainless steel tubing
to connect from the cylinder’s pre-charge
inlet valve (see Figure 3), to the valve on
the return port of the probe (not shown).
4. Open the valve on the return port of the
sampler probe.
5. Slowly open the pre-charge inlet valve
on the sample cylinder (see Figure 3).
6. Slowly open the product inlet valve on
the sample cylinder (see Figure 4) to relieve any pressure buildup.
7. The pre-charge gauge should begin to read pressure and will eventually read the
pipeline pressure.
8. Leave the pre-charge valve on the sample cylinder open during the sampling
procedure.
9. Leave the return port valve on the probe open during the sampling procedure.
10. Check for leaks.
Figure
3
-
Pre-Charge End Cap

INSTALLATION & OPERATIONS
IOM-013 Page 8 of 18
CP2 & CP5GM
Rev: D
Last updated: 4/14/2011
3. Using an auxiliary pre-charge gas:
When using an auxiliary gas, the pre-charge side of the cylinder should be pressurized
with a regulated gas supply (i.e., nitrogen or helium) and set 50-100 psi above pipeline
operating pressure, not to exceed the maximum allowable pressure of the device.
1. Make sure all valves on the sample cylinder are closed.
2. Use small diameter stainless steel tubing to connect the pre-charge valve to the
regulated auxiliary gas supply. (See Figure 3).
3. Open the valve on the gas supply.
4. Slowly open the pre-charge inlet valve on the sample cylinder.
5. Slowly open the product inlet valve on the sample cylinder (see Figure 4) to relieve
any pressure buildup. The piston will begin to move.
6. The pre-charge gauge should begin to read pressure and will eventually read the
designated pressure.
7. Once the piston has reached the end of the cylinder, and obtained between 50-100 psi,
close all valves and check for leaks.
8. Disconnect the tubing from the cylinder and from the pipeline isolation valve.
2.3 INSTALLATION
If steps 2.2 Section 1 or 2.2 Section 3 are used to pre-charge, or if the cylinder is being
used for continuous sampling and the pre-charge is not connected to the pipeline, it will
be necessary to install an adjustable, resetting relief valve in order to relieve pre-charge
pressure while continuous sampling.
1. If your cylinder is equipped with an adjustable relief valve
(see Figure 5), use an auxiliary gas supply to set the valve
at least 50-100 psi above pipeline pressure, not to exceed
the maximum allowable working pressure indicated in
Table 1 on page 5 (refer to IO&M for relief valve).
2. If your cylinder is not equipped with a product purge valve (see Figure 4), create a purge
valve by tubing a T-fitting and valve inline between the sample point and the cylinder in
order to provide a way to purge it.
Purging the system of excess air is important to ensure the system is not contaminated
from the previous sample.
3. Close the product inlet valve.
4. Connect the product inlet valve to the sample point (i.e., probe or sampler).
5. Proceed to Section 2.4 for instructions on how to spot sample the product, or Section 2.5
for instructions on how to continuously sample the product.
Figure 5 -
Adjustable
Relief Valve

INSTALLATION & OPERATIONS
IOM-013 Page 9 of 18
CP2 & CP5GM
Rev: D
Last updated: 4/14/2011
2.4 SPOT SAMPLING
1. Open the product purge valve on the sample
cylinder (see Figure 4) to purge the system of any
contaminants. Close the purge valve.
2. After pre-charging the cylinder above pipeline
pressure (see Section 2.2), connect the product
inlet valve of the cylinder to the sampler outlet
port (see Figure 6).
3. Slowly open the sampler outlet valve.
4. Slowly open the product inlet valve on the product end cap of the sample
cylinder (see Figure 4). The piston will not yet move because pre-charge pressure
is above pipeline pressure.
5. With the sampler valve and product valve fully open, slowly open the pre-charge
valve to relieve pre-charge pressure. This will allow the sampled product to enter
the cylinder and push against the piston. Thus, no pressure loss is encountered.
Relieving the pre-charge too quickly can result in a pressure drop and an
inaccurate sample. A bleed plug can be installed on the pre-charge valve to
regulate the relieving rate. The bleed plug will allow only a small amount of
pressure to exit; ensuring that pre-charge pressure is relieved steadily.
6. When the desired amount of sample is extracted, close all valves on the cylinder.
7. Close the probe outlet valve.
8. Carefully disconnect the cylinder from the probe, allowing the trapped product between
the probe and cylinder valves to vent.
9. Plug or cap all valves on the cylinder.
10. Make a note of pressure, locations, etc., on the information tag according to company
policy.
11. Check all fittings for leaks.
12. The cylinder is now ready for product removal.
2.5 CONTINUOUS SAMPLING
1. Pre-charge the sample cylinder (see Section 2.2) and connect the product inlet end (see
Figure 4) of the cylinder to the sampler outlet port.
2. Open the product purge valve on the sample cylinder to purge the system of any
contaminants. Close the purge valve. Welker recommends plugging the purge valve when
not in use.
3. Open the sampler outlet valve.
4. Slowly open the product valve on the product end cap of the sample cylinder. The piston
will not yet move because pre-charge pressure is above pipeline pressure.
The automatic sampler will push product against the piston, causing the pre-charge
pressure to relieve from the adjustable relief and/or to be pushed into the pipeline.
Figure 6 -
Product Inlet
to Sampler
Outlet

INSTALLATION & OPERATIONS
IOM-013 Page 10 of 18
CP2 & CP5GM
Rev: D
Last updated: 4/14/2011
5. Turn the sampler off when the cylinder is at 80% capacity. This allows a 20% margin for
possible expansion due to temperature changes.
6. When the desired amount of sample is extracted, close all valves on the cylinder.
7. Close the sampler outlet valve.
8. Carefully disconnect the cylinder from the sampler, allowing the trapped product between
the sampler outlet valve and the product inlet valve to vent.
9. Plug or cap all valves on the cylinder.
10. Record pressure, locations, etc., on the information tag according to company policy.
Check all fittings for leaks.
11. The cylinder is now ready for product removal.
2.6 MIXING THE COLLECTED SAMPLE
12. Prior to the analysis of the sample, hold the
cylinder vertically so the pre-charge end is up
and the product end is down.
13. Allow a moment for gravity to pull the
mixer, which will slide down the mixing rod.
14. Invert the cylinder so that the product end is
up and the pre-charge end is down.
15. Allow a moment for gravity to pull the
mixer, which will slide down the mixing rod.
16. Repeat this process several times (5-10) to
mix the contents of the product end of the
cylinder.
Figure
7
–
M
ixing the Product

MAINTENANCE
IOM-013 Page 11 of 18
CP2 & CP5GM
Rev: D
Last updated: 4/14/2011
3. MAINTENANCE
3.1 GENERAL
Prior to maintenance or disassembly of the unit, it is advisable to have a repair kit handy
in case of unexpected wear or faulty seals.
We recommend that the unit have annual maintenance under normal operating
conditions. In the case of severe service, dirty conditions, excessive cycling usage, or
other unique applications that may subject the equipment to unpredictable
circumstances, a more frequent maintenance schedule may be appropriate.
Recommended Tools
It would be advisable to have the following tools available for installation of the unit.
However, tools used will vary depending on cylinder model and connectors used.
Small hex key set
6” adjustable wrench
10” adjustable wrench
10” channel lock pliers
Fine-grit sandpaper
Flat blade screwdriver
Torque wrench
O-Ring kit
New seals supplied in spare parts kits are not lubricated. They should be lightly coated
with lubrication grease (silicone grease or other) before they are installed into the
equipment. This helps in the installation of the seals while reducing the risk of damage
when positioning them on the parts. After the seals are installed, some additional
lubrication can be applied to shafts or cylinder inner diameters to allow smooth transition
of parts. While lubrication should be thorough, only a minimal amount should be applied.
Wipe excess lubrication from the seals, as it may have an adverse effect on sampling.
In the case of constant pressure cylinders, the lubrication grease should be applied
sufficiently but lightly (Krytox®is preferred). When using lubrication other than Krytox,
wipe excess lubrication from the seals as it may have an adverse effect on some
analytical instrument results.
Do not dig into the metal surfaces of the parts when removing O-rings from the O-ring
grooves. Scratching the sealing surface can result in a leak. If necessary, dig into the O-
ring, and replace it during reassembly. If the sealing surface becomes damaged, use a
600-grit wet sandpaper strip to smooth the surface, and then clean it. Check the ball
bearing for any signs of wear or damage. Replace if necessary.

MAINTENANCE
IOM-013 Page 12 of 18
CP2 & CP5GM
Rev: D
Last updated: 4/14/2011
3.2 MAINTENANCE PARTS DIAGRAM

MAINTENANCE
IOM-013 Page 13 of 18
CP2 & CP5GM
Rev: D
Last updated: 4/14/2011
3.3 DISASSEMBLY (Refer to Diagram on Page 12)
1. Make sure the unit is depressurized prior to maintenance.
2. Remove the two cylinder feet (Part 23).
3. Remove the six nuts (Part 22) and carefully slide the product end cap (part 1) off the six
tie bolts (Part 21).
4. Remove the tracker tube clips (Part 3) and tracker tube seats (Part 2).
5. Remove the tracker tube (Part 5).
6. When necessary, replace the burst discs (Parts 16 and 17) located on the end caps.
Burst discs should be replaced after 6-10 cylinder fillings or at least once a year. While the
discs do help to maintain the product, they are designed as a safety device to prevent over-
pressurization of the cylinder.
Insert the clear seal.
Insert the rupture disc after the clear seal. The dome should face out.
Torque the bursting relief caps to the proper specification (see Table 2).
1. Carefully remove the cylinder (Part 6) by sliding it out of the pre-charge end cap (Part 15)
and the six tie bolts (Part 21).
2. Push the piston (Parts 9, 12, and 14), mixing rod (Part 8), and mixer (Part 7) out of the
cylinder using a stick of wood or PVC. Be careful not to scratch the surface of the
cylinder or the piston!
3. Loosen the set screw (Part 20) in the piston assembly. Disconnect the male piston (Part
14) from the ring magnet (Part 12) and female piston (Part 14).
4. Slide the piston off the mixing rod.
3.4 MAINTENANCE INSTRUCTIONS
Do not dig into the metal surfaces of the parts when removing O-rings from the O-ring
grooves. Scratching the sealing surface can result in a leak. If necessary, dig into the O-
ring, and replace it during reassembly. If the sealing surface becomes damaged, use a
600-grit wet sandpaper strip to smooth the surface, and then clean it. Check the ball
bearing for any signs of wear or damage. Replace if necessary.
1. Remove and replace the backups (Parts 25 and Part 10) on the male and female piston,
and remove and replace the O-rings (Parts 4, 11, and 15) in the male and female piston.
(See Figure 8 on next page).
2. Remove and replace the O-rings (Part 4) in each end cap.
3. Remove and replace the backups and O-ring (Parts 18 and 19) on the mixing rod.
4. Wipe down the inside of cylinder and dry carefully (also see Section 3.6).
Table 2

MAINTENANCE
IOM-013 Page 14 of 18
CP2 & CP5GM
Rev: D
Last updated: 4/14/2011
Figure 8 -
Piston Assembl
y
5. Wipe down all other parts and dry carefully.
6. Closely examine the honed surface of the cylinder. Scratches and pits will cause the seals
to leak.
The following are causes to return the device to the manufacturer:
Scratches or pitting that allow migration of gas from one side to the other.
Any damage to the outside cylinder shell that may compromise the cylinder wall
thickness.
3.5 REASSEMBLY INSTRUCTIONS
1. Slide the mixing rod back into
the piston assembly and
reassemble the piston
assembly. (See Figure 8 at
right).
2. Replace the piston inside the
cylinder carefully. Again, be
careful not to scratch the
cylinder or damage the seals,
and make sure that the
direction of piston insertion is
correct. The female end (Part
14) of piston goes toward the
pre-charge end cap (Part 15)
and the male end (Part 9) goes toward the product side end cap (Part 1).
3. Carefully slide the cylinder (Part 6) to the pre-charge end cap (Part 13), then carefully
slide the six tie bolts (Part 17) back into the product end cap (Part 13) so that the nuts are
facing the outside of the end cap.
4. Replace the tracker tube clips (Part 3), tracker tube magnet (Part 10), and the tracker tube
(Part 5), and slide the product end cap (Part 2) back onto the six tie bolts.
5. Tighten the nuts (Part 1) to the correct torque using a cross bolting sequence:
Torque Specifications for Tie Bolts
Diameter of Tie Bolt Foot Pounds KG/M
3/8” (CP-2, etc.) 5-6 .69-.82
1/2” (CP-7, CP-24, etc.) 15-20 2.07-2.76
5/8” (CP-5, etc.) 23-30 3.45-4.14
7/8”or 1” (CP-11, LS-7, CP-80etc.) 55-65 7.60-8.98
6. Pressure up cylinder at one end with an inert gas supply and test for leaks. Repeat the
process from the opposite end. Pressurize slowly to avoid the slamming the piston from
one end to the other.
Welker recommends using helium to test for leaks.

MAINTENANCE
IOM-013 Page 15 of 18
CP2 & CP5GM
Rev: D
Last updated: 4/14/2011
3.6 CYLINDER CLEANING
Regular cleaning of the cylinder is essential for the proper functioning of the device. Solvent
cleaning is normally done during scheduled maintenance; however, some companies require
this before each cylinder is put into service. Any debris or residue that is not removed from
the cylinder will contaminate the results of the next sample extracted from the cylinder.
Welker recommends cleaning and leak testing of the cylinder after each use.
Cleaning a constant pressure sample cylinder can be done one of three ways:
1. Purging with helium
Fill and empty the cylinder with helium repeatedly.
Take a sample of the helium to test for trace amounts of hydrocarbons.
If hydrocarbons are present in the analysis, the system has not been adequately cleaned,
and further purging will be necessary. If hydrocarbons or contaminants remain present, a
solvent cleaning may be required (see step 3.5.3). After cleaning with solvent, purge with
helium to remove the solvent and analyze the helium to verify the solvent and
hydrocarbons have been removed.
If no hydrocarbons are found, cleaning is complete.
Repeat step 7 of Section 3.4.
2. Purging with new product
Purge the cylinder using the product to be sampled. This can be accomplished each
time the cylinder is put into service.
Repeat step 7 of Section 3.4.
This method is acceptable only if the cylinder will be used in one location.
3. Cleaning with solvent
Fill and empty the cylinder repeatedly with solvent.
Use an inert gas to dry and purge the cylinder.
Use method 3.5.1 to verify the system is free of contaminants.
Repeat step 7 of Section 3.4

SAFETY WARNING
IOM-013 Page 16 of 18
CP2 & CP5GM
Rev: D
Last updated: 4/14/2011
SAFETY ISSUE WARNING FOR LIQUID SAMPLE CYLINDERS
After drawing the sample into the cylinder, the inlet and pre-charge valves should be
closed. The sample line is then disconnected from the cylinder and the cylinder is
completely isolated from the process. Paperwork is processed and the cylinder is
prepared for transport. Prior to transporting the cylinder, it is a common and
recommended practice to plug or cap the valves on the cylinder. These valves may
terminate with a female NPT or a male NPT. The female valves are typically plugged,
while the male valves are typically capped.
In the case of liquid sampling and due to the potential extremes of thermal expansion of
many LPG products, caution should be taken to ensure that any residual liquid is drained,
blown, or absorbed from the accessible exterior dead volume of the valve body
(downstream of the seat) prior to plugging or capping the valve.
It is common to see temperature differentials of as much as 100° F (38° C) or more.
Liquid samples that are drawn at -40 to -50° F (-40 to -46° C) can be transported in
shipping cases that may see ambient temperatures as high as 100° F to 160° F (38° to 71°
C), and at times may exceed 160° F (71° C).
Operators should be familiar with the basic and general physical properties of the product
that they are sampling so that they can adequately estimate the expansion potential of the
sampled product within the cylinder and therefore have them allow ample outage for
expansion to occur. In a majority of cases, 80% fill and 20% pre-charge is acceptable,
but certain products may require a larger inert gas pre-charge ratio – i.e., 70%-30% or
60%-40%.
Burst discs are installed on these cylinders to protect them from structural failure. The
operator must be aware that flammable product will be released in the event of
overpressurization of the working pressure of the cylinder and therefore it is important
to allow for ample expansion within the cylinder prior to attainment of the rupture disc
activation.
If you have any questions, please contact Welker at 1-800-776-7267 in the USA or 1-
281-491-2331.

TROUBLESHOOTING
IOM-013 Page 17 of 18
CP2 & CP5GM
Rev: D
Last updated: 4/14/2011
4. TROUBLESHOOTING GUIDE
The following is a troubleshooting table of issues most commonly associated with the
Welker® Constant Pressure Cylinder models. If you are having a problem that is not
listed, or if the solution provided does not repair the problem, please call Welker for
service options.
PROBLEM POSSIBLE
CAUSE
SOLUTION
Gauge indicates a loss of
pressure.
There is a leak from one
of the fittings.
There is a leak from the
burst discs.
The cylinder experienced
a temperature drop.
There is a defective
valve.
Check all fittings for leaks
with leak detector. Replace
thread sealant.
Make sure the burst discs
are torqued properly. If the
problem persists, the discs
may need replacement.
See Table 2.
Restore the temperature to
pipeline temperature.
Repair or restore the
defective valve.
Pressure is leaking across the
piston. Seals in the piston are leaking. Disassemble and clean the unit.
Inspect cylinder for scratches.
Replace seals in the piston and
reassemble.
See Sections 3.2-3.4.
The pre-charge or product end
cap is leaking.
The burst disc is leaking.
There is a loose fitting.
The seat on purge valve is
leaking.
Replace the burst disc.
See step 3.2 Section 13.
Tighten the fittings.
Replace the seat.

13839 West Bellfort St., Sugar Land, Texas 77498-1671
Phone: (281) 491-2331
Fax: (281) 491-8344
Toll Free: (800) 776-7267
Web Page: www.welkereng.com
This manual suits for next models
1
Table of contents
Other Welker Sampler manuals
Popular Sampler manuals by other brands
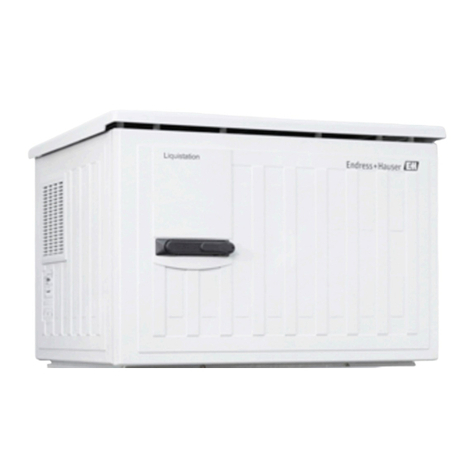
Endress+Hauser
Endress+Hauser Liquistation CSF28 operating instructions

Lambda
Lambda OMNICOLL Operation manual
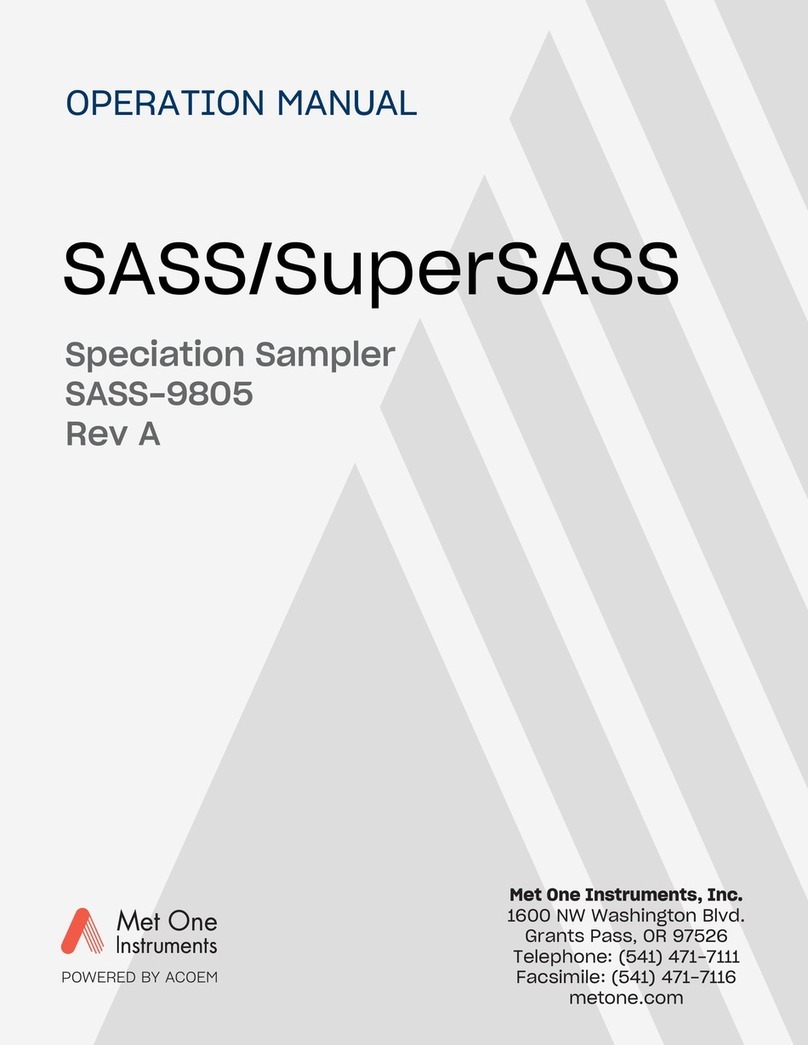
Met One Instruments
Met One Instruments SASS Operation manual

InnovaPrep
InnovaPrep ACD-200 user guide
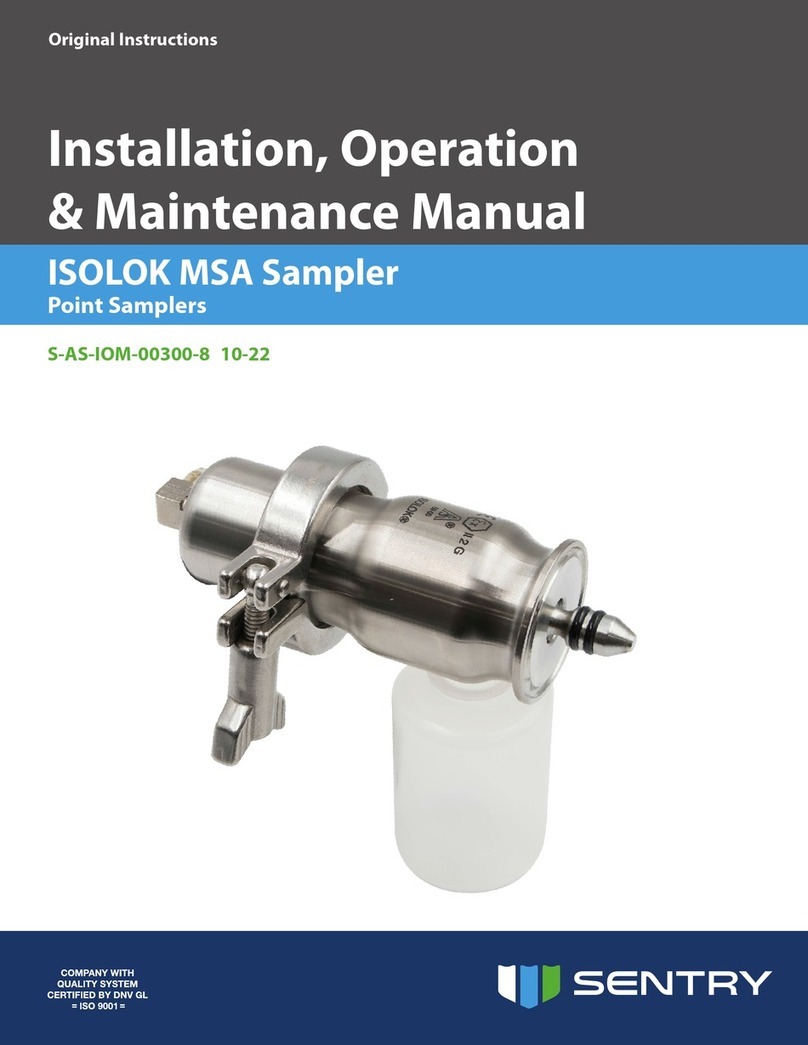
Sentry
Sentry ISOLOK MSA Installation, operation & maintenance manual
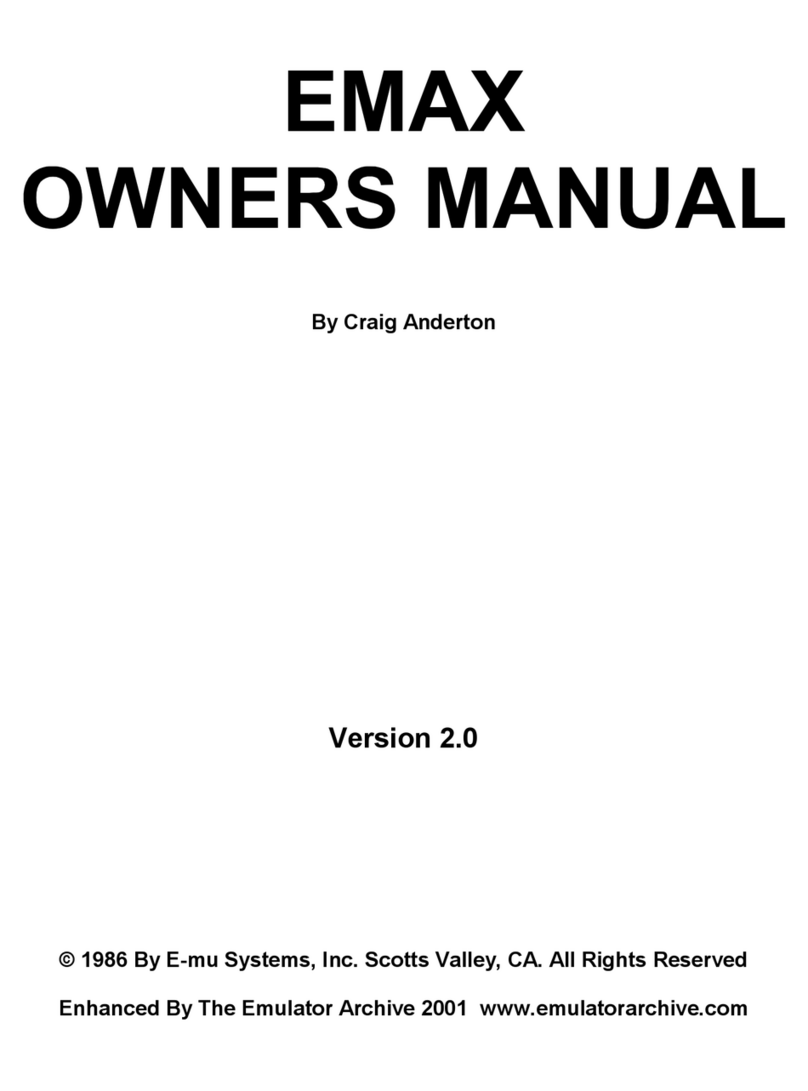
EMU
EMU EMAX owner's manual