WP XACT PRO 7448 User manual

OWNER'S MANUAL
XACT PRO 7448
Art. no. 53000180en
http://www.wp-suspension.com


DEAR WP CUSTOMER
*53000180en*
53000180en
07/2019
DEAR WP CUSTOMER
Congratulations on your decision to purchase a WP chassis component. You are now the owner of a state-of-
the-art sports chassis that you will continue to enjoy for a long time if you maintain it properly.
We wish you good and safe riding at all times!
The Owner's Manual contained the latest information for this model series at the time of going to print. How-
ever, minor differences due to further developments in design cannot be ruled out completely.
All specifications contained herein are non-binding. WP Suspension GmbH specifically reserves the right to
modify or delete technical specifications, prices, colors, forms, materials, services, designs, equipment, etc.,
without prior notice and without providing reasons, to adapt these to local conditions, as well as to stop the
production of a particular model without prior notice. WP accepts no liability for delivery options, deviations
from figures and descriptions, misprints, and other errors. The models portrayed partly contain special equip-
ment that does not belong to the regular scope of supply.
© 2019 WP Suspension GmbH, Mattighofen Austria
All rights reserved
Reproduction, even in part, as well as copying of all kinds, is permitted only with the express written permission
of the copyright owner.
WP Suspension GmbH
Stallhofnerstraße 3
5230 Mattighofen, Austria
This document is valid for the following models:
XACT PRO 7448 (34.18.2T.07)

TABLE OF CONTENTS
2
TABLE OF CONTENTS
1 MEANS OF REPRESENTATION........................ 3
1.1 Symbols used ....................................... 3
1.2 Formats used........................................ 3
2 SAFETY ADVICE ............................................... 4
2.1 Use definition –intended use ............... 4
2.2 Misuse................................................... 4
2.3 Safety advice ........................................ 4
2.4 Degrees of risk and symbols ................ 4
2.5 Safe operation....................................... 4
2.6 Work rules............................................. 5
2.7 Environment.......................................... 5
2.8 Owner's Manual.................................... 5
2.9 Correct installation................................ 5
2.10 Chassis tightening torques ................... 5
3 IMPORTANT NOTES ......................................... 6
3.1 Manufacturer and implied warranty...... 6
3.2 Fuel, auxiliary substances..................... 6
3.3 Spare parts, accessories ...................... 6
3.4 Service .................................................. 6
3.5 Figures .................................................. 6
3.6 Customer service.................................. 6
4 SERIAL NUMBERS............................................ 7
4.1 Fork article number............................... 7
5 PREPARING FOR USE...................................... 8
5.1 Advice on preparing for first use........... 8
6 RIDING INSTRUCTIONS ................................... 9
6.1 Checks and maintenance measures
when preparing for use......................... 9
7 SERVICE SCHEDULE...................................... 10
7.1 Additional information......................... 10
7.2 Required work..................................... 10
7.3 Recommended work........................... 10
8 SERVICE WORK ON THE CHASSIS ............... 11
8.1 Raising the motorcycle with a lift
stand ................................................... 11
8.2 Removing standard fork legs .......... 11
8.3 Installing the WP PRO
COMPONENTS fork legs ................ 11
8.4 Bleeding the fork legs ......................... 12
8.5 Cleaning the dust boots of the fork
legs ..................................................... 12
8.6 Removing the motorcycle from the
lift stand .............................................. 13
9 TUNING THE CHASSIS................................... 14
9.1 Checking the basic chassis setting
with the rider's weight......................... 14
9.2 Checking the basic setting of the
fork...................................................... 14
9.3 Adjusting the compression damping
of the fork............................................ 14
9.4 Adjusting the rebound damping of
the fork................................................ 15
9.5 Setting the fork air pressure of the
positive chamber ................................ 15
9.6 Setting the fork air pressure of the
negative chamber ............................... 18
9.7 Measuring the visible inner tube
length of the fork................................. 20
10 TECHNICAL DATA .......................................... 21
10.1 Fork..................................................... 21
11 SUBSTANCES................................................. 23
12 AUXILIARY SUBSTANCES.............................. 24
13 STANDARDS ................................................... 25
14 LIST OF ABBREVIATIONS .............................. 26
INDEX ...................................................................... 27

MEANS OF REPRESENTATION 1
3
1.1 Symbols used
The meaning of specific symbols is described below.
Indicates an expected reaction (e.g. of a work step or a function).
Indicates an unexpected reaction (e.g. of a work step or a function).
All work marked with this symbol requires specialist knowledge and technical understand-
ing. In the interest of your own safety, have these jobs performed by a WP Authorized Cen-
ter! There your WP chassis will be treated with the optimum care and attention by specially
trained experts using the necessary special tools.
Indicates a page reference (more information is provided on the specified page).
Indicates information with more details or tips.
Indicates the result of a testing step.
Indicates the end of an activity, including potential rework.
1.2 Formats used
The typographical formats used in this document are explained below.
Proprietary name Indicates a proprietary name.
Name®Indicates a protected name.
Brand™ Indicates a brand available on the open market.
Underlined terms Refer to technical details or indicate technical terms, which are explained
in the glossary.

2 SAFETY ADVICE
4
2.1 Use definition –intended use
This chassis component is designed and built to withstand the normal stresses and strains of regular racing.
Info
Only use this chassis component in closed-off areas remote from public road traffic.
Only use this chassis component in the vehicle for which the chassis component is approved and/or
recommended.
2.2 Misuse
The chassis component must only be used as intended.
Dangers can arise for people, property and the environment through use not as intended.
Any use of the chassis component beyond the intended and defined use constitutes misuse.
Misuse also includes the use of operating and auxiliary fluids which do not meet the required specification for
the respective use.
2.3 Safety advice
A number of safety instructions need to be followed to operate the product described safely. Therefore read
this instruction and all further instructions included carefully. The safety instructions are highlighted in the text
and are referred to at the relevant passages.
Info
Various information and warning labels are attached in prominent locations on the product described.
Do not remove any information or warning labels. If they are missing, you or others may not recognize
dangers and may therefore be injured.
2.4 Degrees of risk and symbols
Danger
Identifies a danger that will immediately and invariably lead to fatal or serious permanent injury if the
appropriate measures are not taken.
Warning
Identifies a danger that is likely to lead to fatal or serious injury if the appropriate measures are not
taken.
Note
Identifies a danger that will lead to considerable machine and material damage if the appropriate measures are
not taken.
2.5 Safe operation
Danger
Danger of accidents A rider who is not fit to ride poses a danger to him or herself and others.
–Do not operate the vehicle and use chassis components if you are not fit to ride due to alcohol,
drugs or medication.
–Do not operate the vehicle and use chassis components if you are physically or mentally impaired.
Only use the chassis component when it is in perfect technical condition, in accordance with its intended use,
and in a safe and environmentally compatible manner.

SAFETY ADVICE 2
5
If there are faults, which impair safety, have them immediately remedied in a WP Authorized Center.
Adhere to the information and warning labels on the chassis component.
2.6 Work rules
Special tools are necessary for certain tasks. The tools are not a component of the chassis component, but can
be ordered using the number in parentheses.
During assembly, use new parts to replace parts which cannot be reused (e.g., seals, seal rings, O-rings).
In the case of certain screws, a thread locker (e.g. Loctite®) is required. Observe the manufacturer's instruc-
tions.
After disassembly, clean the parts that are to be reused and check them for damage and wear. Change dam-
aged or worn parts.
After completing a repair or service work, check the operating safety of the chassis component.
2.7 Environment
If you use your chassis component responsibly, you can ensure that problems and conflicts do not occur.
When disposing of used oil, other operating and auxiliary fluids, and used components, comply with the laws
and regulations of the respective country.
2.8 Owner's Manual
It is important that you read this Owner's Manual carefully and completely before making your first trip. The
Owner's Manual contains useful information and many tips on how to operate, handle, and service your motor-
cycle. This is the only way for you to find out how to set up the chassis component ideally and how to protect
yourself from injury.
Keep the Owner's Manual in an accessible place to enable you to refer to it as needed.
If you would like to know more about the chassis component or have questions on the material you read,
please contact a WP Authorized Center.
The Owner's Manual is an important part of the chassis component and must be handed over to the new
owner if the vehicle is sold.
2.9 Correct installation
Correct installation analogously to original components and in accordance with the instructions of the vehicle
manufacturer is essential for ensuring maximum safety and functionality.
It is therefore strongly recommended that you have the chassis component installed at a WP Authorized Cen-
ter.
2.10 Chassis tightening torques
Unless otherwise stated, the tightening torques that apply are those in the vehicle manufacturer's instructions.

3 IMPORTANT NOTES
6
3.1 Manufacturer and implied warranty
The work prescribed in the service schedule must be carried out in a WP Authorized Center only, since other-
wise no warranty claims will be recognized. Damage or secondary damage caused by tampering with and/or
conversions on the chassis component are not covered by the warranty.
3.2 Fuel, auxiliary substances
Use operating and auxiliary substances (such as fuel and lubricants) as specified in the Owner's Manual.
3.3 Spare parts, accessories
For your safety, only use spare parts and accessory products that are approved and/or recommended by WP
and have them installed in a WP Authorized Center. WP accepts no liability for other products and any resulting
damage or loss.
Certain spare parts and accessory products are specified in parentheses in the descriptions. Your WP Autho-
rized Center will be pleased to advise you.
3.4 Service
A prerequisite for perfect operation and prevention of premature wear is that the service, care, and tuning work
is properly carried out as described in the Owner's Manual. Incorrect adjustment and tuning of the chassis and
suspension can lead to damage and breakage of components.
Use of the chassis component under difficult conditions, such as on sand or on wet and muddy surfaces, can
lead to considerably more rapid wear. For this reason, it may be necessary to inspect or replace parts before
the next scheduled service.
It is imperative that you adhere to the stipulated service intervals. If you observe these exactly, you will ensure a
much longer service life for your chassis component.
3.5 Figures
The figures contained in the manual may depict special equipment.
In the interest of clarity, some components may be shown disassembled or may not be shown at all. It is not
always necessary to disassemble the component to perform the activity in question. Please follow the instruc-
tions in the text.
3.6 Customer service
If you have any questions about your chassis component or WP, your WP Authorized Center will be pleased to
advise you.
A list of WP Authorized Centers can be found on the WP website.
International WP Suspension website: http://www.wp-suspension.com

SERIAL NUMBERS 4
7
4.1 Fork article number
401947-10
The fork article number 1is stamped on the inside of the axle
clamp.
Info
The fork article number consists of an eight figure number
with a single letter in the sixth position.

5 PREPARING FOR USE
8
5.1 Advice on preparing for first use
Warning
Danger of accident Modifications to the suspension setting may seriously alter the handling charac-
teristic.
Extreme modifications to the suspension setting may cause a serious deterioration in the handling
characteristic and overload components.
–Only make adjustments within the recommended range.
–Ride slowly to start with after making adjustments to get the feel of the new handling characteristic.
–Adjust the compression damping of the fork. ( p. 14)
–Adjust the rebound damping of the fork. ( p. 15)
–Set the fork air pressure of the positive chamber. ( p. 15)
–Set the fork air pressure of the negative chamber. ( p. 18)
–Set the fork air pressure of the positive chamber. ( p. 15)
–Measure the visible inner tube length of the fork. ( p. 20)

RIDING INSTRUCTIONS 6
9
6.1 Checks and maintenance measures when preparing for use
Info
Before every use, check the condition of the chassis component and ensure that it is safe to operate.
The chassis must be in perfect technical condition when it is being operated.
H02539-01
–Check chassis component for damage.
–Clean the dust boots of the fork legs. ( p. 12)
–Bleed the fork legs. ( p. 12)
–Check all screw connections to ensure that they are tight.

7 SERVICE SCHEDULE
10
7.1 Additional information
Any further work that results from the required work or from the recommended work must be ordered sepa-
rately and can be invoiced separately.
Different service intervals may apply in your country, depending on the local operating conditions.
7.2 Required work
Every 40 operating hours
Service the fork. ●
●Periodic interval
7.3 Recommended work
After 10 operating hours
Service the fork. ○
○One-time interval

SERVICE WORK ON THE CHASSIS 8
11
8.1 Raising the motorcycle with a lift stand
Note
Danger of damage The parked vehicle can roll away or fall over.
–Park the vehicle on a firm and level surface.
401942-01
–Raise the motorcycle in accordance with the instructions of
the vehicle manufacturer.
Neither wheel is in contact with the ground.
–Secure the motorcycle against falling over.
8.2 Removing standard fork legs
H03150-10
–Remove the standard fork legs as per the instructions of the
vehicle manufacturer.
8.3 Installing the WP PRO COMPONENTS fork legs
M01743-10
–Install the fork legs in accordance with the instructions of the
vehicle manufacturer.
Bleeder screws 1are positioned toward the front.
The second milled groove (from the top) is flush with the
upper edge of the upper triple clamp.

8 SERVICE WORK ON THE CHASSIS
12
H03779-10
–Apply the sticker for measuring sag at distance Afrom the
fork protector screw.
Guideline
Distance A2 mm (0.08 in)
–Apply the remaining stickers included in the scope of supply.
8.4 Bleeding the fork legs
Preparatory work
–Raise the motorcycle with a lift stand. ( p. 11)
M01744-10
Main work
–Release bleeder screws 1.
Any excess pressure escapes from the interior of the
fork.
–Tighten the bleeder screws.
Finishing work
–Remove the motorcycle from the lift stand. ( p. 13)
8.5 Cleaning the dust boots of the fork legs
Preparatory work
–Raise the motorcycle with a lift stand. ( p. 11)
–Remove the fork protector.
M01745-10
Main work
–Push dust boots 1of both fork legs downward.
Info
The dust boots remove dust and coarse dirt parti-
cles from the inside fork tubes. Over time, dirt can
accumulate behind the dust boots. If this dirt is not
removed, the oil seals behind can start to leak.
Warning
Danger of accidents Oil or grease on the brake
discs reduces the braking effect.
–Always keep the brake discs free of oil and
grease.
–Clean the brake discs with brake cleaner when
necessary.
–Clean the dust boots and inner fork tubes of both fork legs.
–Press the dust boots back into their installation position.
–Remove excess oil.

SERVICE WORK ON THE CHASSIS 8
13
Finishing work
–Install the fork protector.
–Remove the motorcycle from the lift stand. ( p. 13)
8.6 Removing the motorcycle from the lift stand
Note
Danger of damage The parked vehicle can roll away or fall over.
–Park the vehicle on a firm and level surface.
H03151-01
–Remove the motorcycle from the lift stand as per the instruc-
tions of the vehicle manufacturer.
–Remove the lift stand.

9 TUNING THE CHASSIS
14
9.1 Checking the basic chassis setting with the rider's weight
401030-01
–For optimal motorcycle riding characteristics and to avoid
damage to forks, shock absorbers, link fork and frame, the
basic settings of the suspension components must match the
rider's weight.
–This chassis component is factory set to a standard rider's
weight.
Guideline
Standard rider weight 75 … 85 kg (165 … 187 lb.)
–If the rider's weight is above or below this range, the basic
setting of the suspension components must be adjusted
accordingly.
–Weight differences can be compensated for by changing the
fork air pressure.
9.2 Checking the basic setting of the fork
Info
For various reasons, no exact riding sag can be determined for the fork.
401000-01
–Weight differences can be compensated for by changing the
fork air pressure.
–However, if the fork frequently bottoms out (hard end stop on
compression), the fork air pressure must be increased, within
the specified values, to avoid damage to the fork and frame.
–If the fork feels unusually hard after extended periods of
operation, the fork legs need to be bled.
9.3 Adjusting the compression damping of the fork
Info
The hydraulic compression damping determines the fork suspension behavior.
M01746-10
–Turn adjusting screw 1clockwise up to the last perceptible
click.
Info
Adjusting screw COMP 1is located at the upper
end of the right fork leg.
–Turn counterclockwise by the number of clicks correspond-
ing to the fork type.

TUNING THE CHASSIS 9
15
Guideline
Compression damping
125/150/250 SX EU,
450 SX‑F EU
TC 125/250 EU,
FC 450 EU
18 clicks
250/350 SX‑F EU
FC 250/350 EU
14 clicks
All US versions 15 clicks
Info
Turn clockwise to increase damping; turn counter-
clockwise to reduce damping during compression.
9.4 Adjusting the rebound damping of the fork
Info
The hydraulic rebound damping determines the fork suspension behavior.
M01747-10
–Remove protection cap 1.
–Turn adjusting screw 2clockwise up to the last perceptible
click.
Info
Adjusting screw 2is located at the lower end of the
right fork leg.
–Turn counterclockwise by the number of clicks correspond-
ing to the fork type.
Guideline
Rebound damping 20 clicks
Info
Turn clockwise to increase the damping; turn
counterclockwise to reduce damping when the shock
absorber rebounds.
–Mount protection cap 1.
9.5 Setting the fork air pressure of the positive chamber
Warning
Danger of accident Modifications to the suspension setting may seriously alter the handling charac-
teristic.
Extreme modifications to the suspension setting may cause a serious deterioration in the handling
characteristic and overload components.
–Only make adjustments within the recommended range.
–Ride slowly to start with after making adjustments to get the feel of the new handling characteristic.

9 TUNING THE CHASSIS
16
Info
Check or adjust the air pressure under the same conditions at the earliest 5 minutes after switching off
the engine.
The air suspension is located in the left fork leg. The rebound and compression damping is located in
the right fork leg.
When changing the air pressure, always observe the correct value of the visible inner tube length and
only proceed in small steps.
First set the positive chamber, then the negative chamber and finally the positive chamber again.
Preparatory work
–Raise the motorcycle with a lift stand. ( p. 11)
M01748-10
Main work
–Remove valve cap 1.
–Push together fork airpump 2fully.
Fork airpump (79412966100)
Info
The fork airpump is included.
–Mount adapter 3on the fork airpump.
Adapter (T14086E)
Info
The adapter is included.
–The adapter is connected to the valve.
–Rotate the upper part of the adapter clockwise.
The interior valve opens.
The fork airpump switches on automatically.
A little air escapes from the fork leg when connecting.
Info
This is due to the volume of the hose and not due to a
defect in the fork airpump or the fork.
Read the accompanying instructions.
–Adjust the air pressure as specified.

TUNING THE CHASSIS 9
17
Guideline
Air pressure, positive chamber
125/150 SX EU
TC 125 EU
8.6 bar (125 psi)
250 SX EU
TC 250 EU
10.0 bar (145 psi)
250 SX‑F EU
FC 250 EU
10.6 bar (154 psi)
350 SX‑F EU
FC 350 EU
10.8 bar (157 psi)
450 SX‑F EU
FC 450 EU
10.5 bar (152 psi)
125 SX US
TC 125 US
10.3 bar (149 psi)
250 SX US
TC 250 US
11.3 bar (164 psi)
250/350/450 SX‑F US
FC 250/350/450 US
11.5 bar (167 psi)
Gradual changing of the air
pressure in steps of
0.05 … 0.1 bar (0.7 … 1 psi)
Minimum air pressure 5 bar (73 psi)
Maximum air pressure 15 bar (218 psi)
Info
Never adjust the air pressure to a value outside the
stated range.
–Rotate the upper part of the adapter anticlockwise.
The interior valve closes.
–Disconnect the adapter from the left fork leg.
When disconnecting, excess pressure will escape from
the hose –the fork leg does not lose any air.
The fork pump airpump switches off automatically after
80 seconds.
–Remove the adapter from the fork airpump.
–Mount valve cap.
Guideline
Only mount the valve cap by hand.
Finishing work
–Remove the motorcycle from the lift stand. ( p. 13)

9 TUNING THE CHASSIS
18
9.6 Setting the fork air pressure of the negative chamber
Warning
Danger of accident Modifications to the suspension setting may seriously alter the handling charac-
teristic.
Extreme modifications to the suspension setting may cause a serious deterioration in the handling
characteristic and overload components.
–Only make adjustments within the recommended range.
–Ride slowly to start with after making adjustments to get the feel of the new handling characteristic.
Info
Check or adjust the air pressure under the same conditions at the earliest 5 minutes after switching off
the engine.
The air suspension is located in the left fork leg. The rebound and compression damping is located in
the right fork leg.
When changing the air pressure, always observe the correct value of the visible inner tube length and
only proceed in small steps.
First set the positive chamber, then the negative chamber and finally the positive chamber again.
Preparatory work
–Raise the motorcycle with a lift stand. ( p. 11)
–Set the fork air pressure of the positive chamber. ( p. 15)
M01749-10
Main work
–Remove protection cap 1.
–Remove screw cap 2.
–Push together fork airpump 3fully.
Fork airpump (79412966100)
Info
The fork airpump is included.
–Mount adapter 4on the fork airpump.
Adapter (T14086E)
Info
The adapter is included.
–The adapter is connected to the valve.
–Rotate the upper part of the adapter clockwise.
The interior valve opens.
The fork airpump switches on automatically.
A little air escapes from the fork leg when connecting.
Info
This is due to the volume of the hose and not due to a
defect in the fork airpump or the fork.
Read the accompanying instructions.
–Adjust the air pressure as specified.
Table of contents
Other WP Chassis manuals
Popular Chassis manuals by other brands
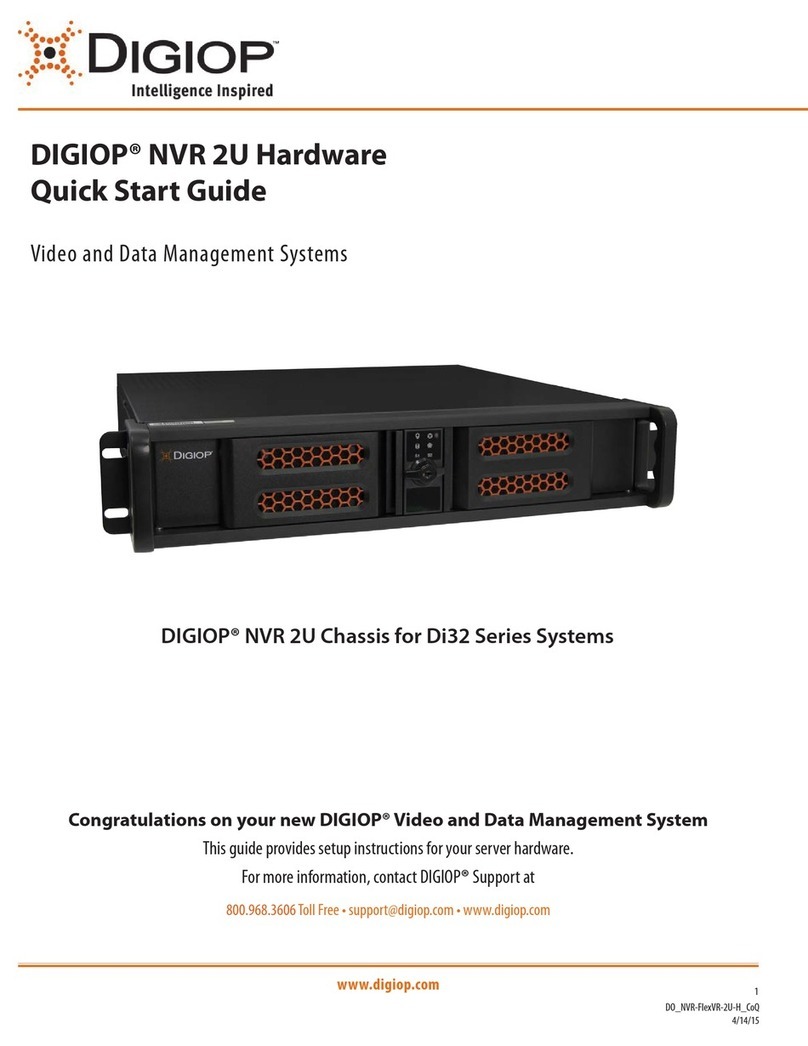
Digiop
Digiop NVR 2U quick start guide
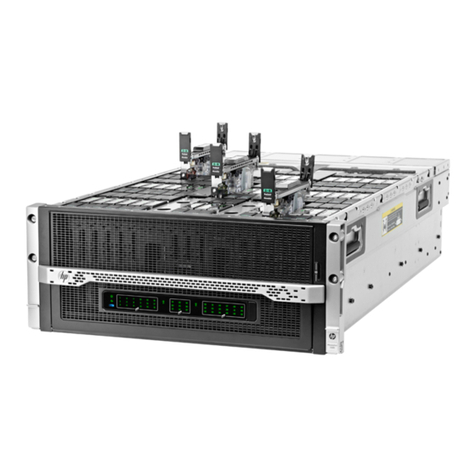
HP
HP Moonshot 1500 Setup and installation guide
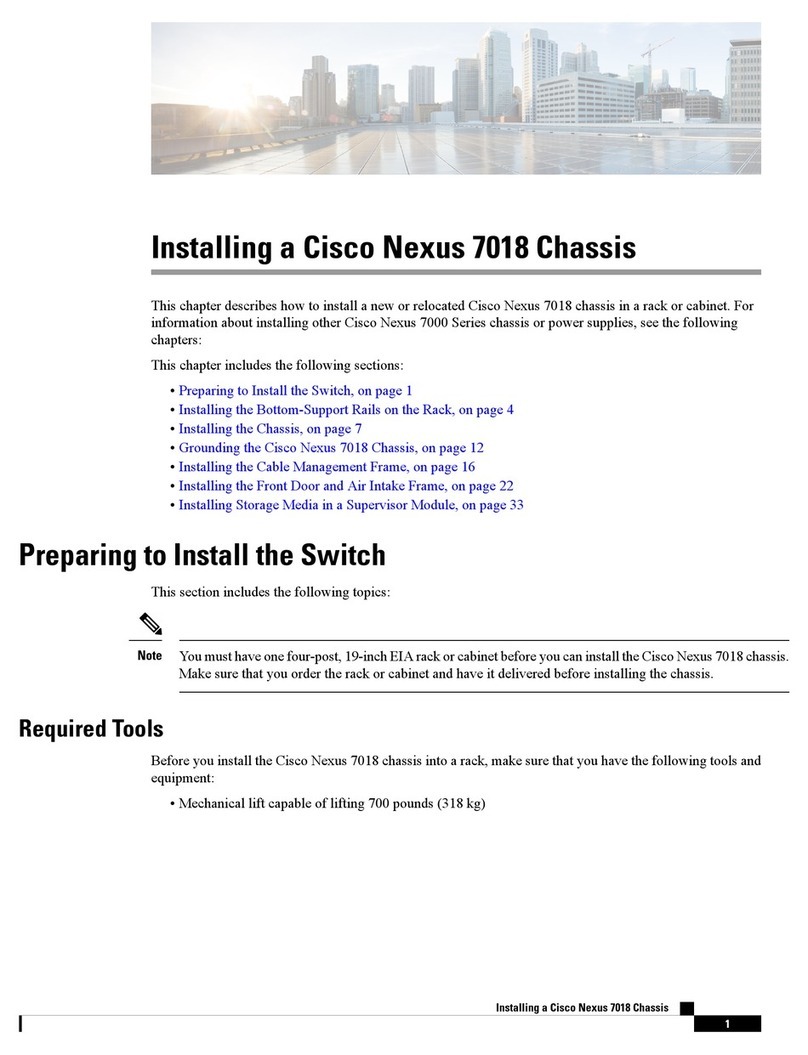
Cisco
Cisco Nexus 7018 manual
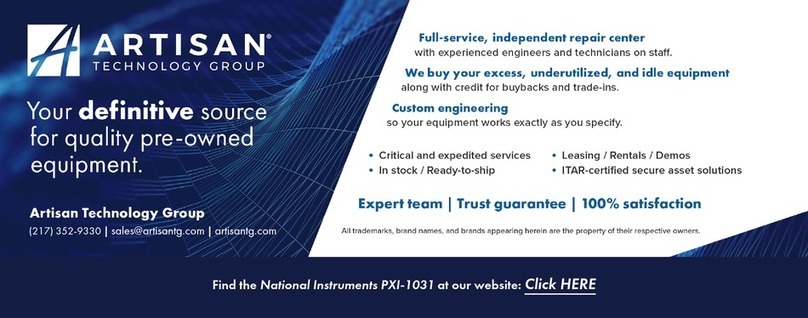
National Instruments
National Instruments PXI-1031DC user manual
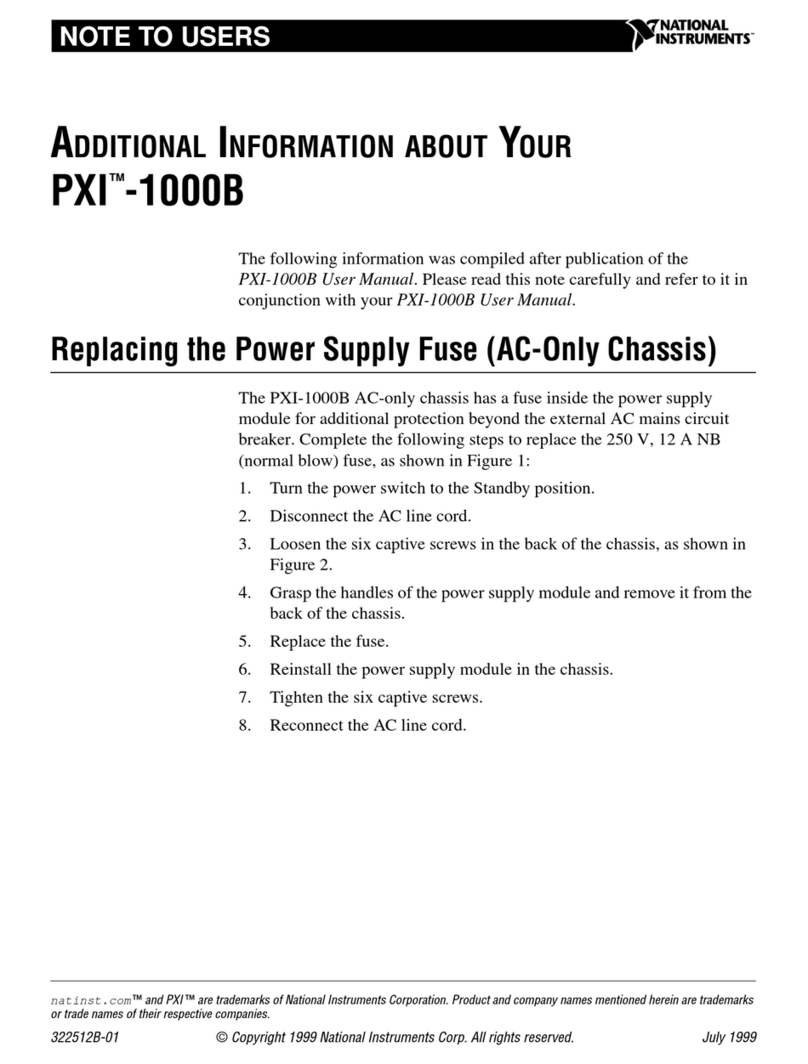
National Instruments
National Instruments PXI 1000B Additional information
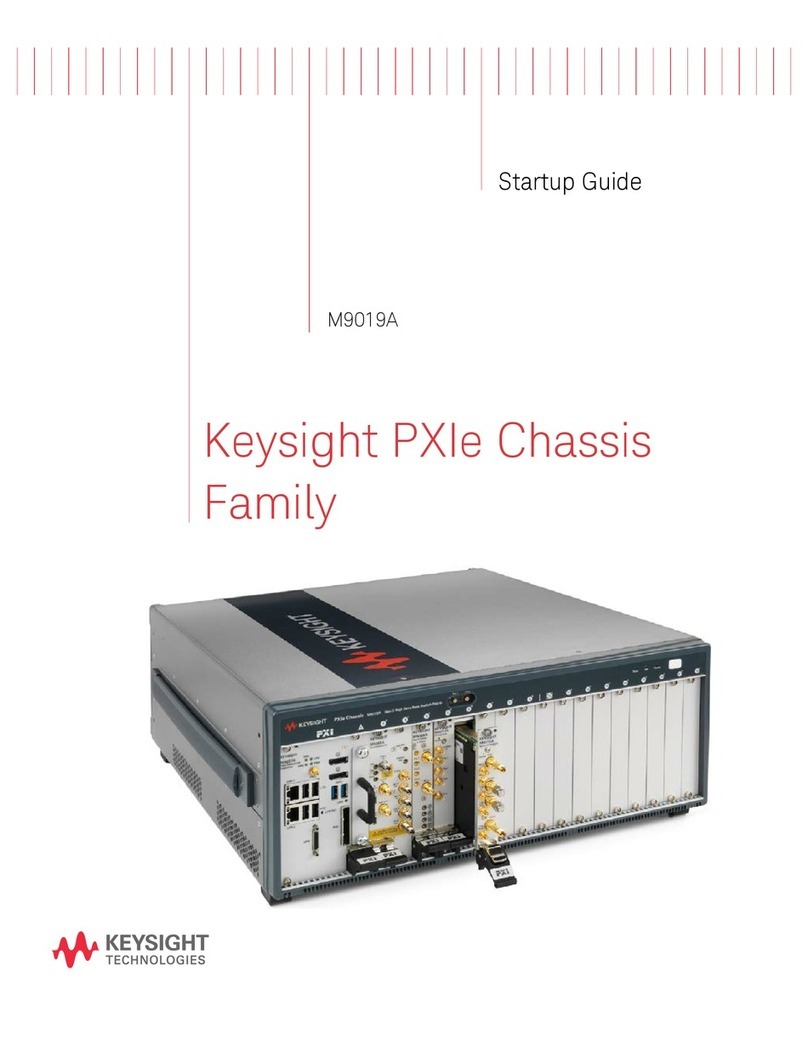
Keysight Technologies
Keysight Technologies PXIe Series Startup guide