Acuity AccuRange Series User manual

Limited Use License Agreement
YOU SHOULD CAREFULLY READ THE FOLLOWING TERMS AND CONDITIONS BEFORE OPENING THE PACKAGE
CONTAINING THE COMPUTER SOFTWARE AND HARDWARE LICENSED HEREUNDER. CONNECTING POWER TO THE
MICROPROCESSOR CONTROL UNIT INDICATES YOUR ACCEPTANCE OF THESE TERMS AND CONDITIONS. IF YOU DO NOT
AGREE WITH THEM, YOU SHOULD PROMPTLY RETURN THE UNIT WITH POWER SEAL INTACT TO THE PERSON FROM
WHOM IT WAS PURCHASED WITHIN FIFTEEN DAYS FROM DATE OF PURCHASE AND YOUR MONEY WILL BE REFUNDED BY
THAT PERSON. IF THE PERSON FROM WHOM YOU PURCHASED THIS PRODUCT FAILS TO REFUND YOUR MONEY, CONTACT
SCHMITT INDUSTRIES INCORPORATED IMMEDIATELY AT THE ADDRESS SET OUT BELOW.
Schmitt Industries Incorporated provides the hardware and computer software program contained in the microprocessor control unit, and licenses
the use of the product to you. You assume responsibility for the selection of the product suited to achieve your intended results, and for the
installation, use and results obtained. Upon initial usage of the product your purchase price shall be considered a nonrefundable license fee unless
prior written waivers are obtained from Schmitt Industries incorporated.
LICENSE
a. You are granted a personal, nontransferable and non-exclusive license to use the hardware and software in this Agreement. Title and
ownership of the hardware and software and documentation remain in Schmitt Industries, Incorporated;
b. the hardware and software may be used by you only on a single installation;
c. you and your employees and agents are required to protect the confidentiality of the hardware and software. You may not distribute,
disclose, or otherwise make the hardware and software or documentation available to any third party;
d. you may not copy or reproduce the hardware and software or documentation for any purpose;
e. your may not assign or transfer the hardware and software or this license to any other person without the express prior written consent of
Schmitt Industries Incorporated;
f. you acknowledge that you are receiving only a LIMITED LICENSE TO USE the hardware and software and related documentation and that
Schmitt Industries Incorporated retains title to the hardware and software and documentation. You acknowledge that Schmitt Industries
Incorporated has a valuable proprietary interest in the hardware and software and documentation.
YOU MAY NOT USE, COPY, MODIFY, OR TRANSFER THE HARDWARE AND SOFTWARE, IN WHOLE OR IN ANY PART,
WITHOUT THE PRIOR WRITTEN CONSENT OF SCHMITT INDUSTRIES, INCORPORATED.
IF YOU TRANSFER POSSESSION OF ANY PORTION OF THE HARDWARE OR SOFTWARE TO ANOTHER PARTY, YOUR LICENSE
IS AUTOMATICALLY TERMINATED. TERM
The license is effective until terminated. You may terminate it at any other time by returning all hardware and software together with all copies
of associated documentation. It will also terminate upon conditions set forth elsewhere in this Agreement or if you fail to comply with any term
or condition of this Agreement. You agree upon such termination to return the hardware and software together with all copies of associated
documentation. In the event of termination the obligation of confidentiality shall survive.
12 MONTH LIMITED WARRANTY
EXCEPT AS STATED BELOW IN THIS SECTION THIS PRODUCT IS PROVIDED “AS IS” WITHOUT WARRANTY OF ANY KIND,
EITHER EXPRESSED OR IMPLIED, INCLUDING, BUT NOT LIMITED TO, THE IMPLIED WARRANTIES OF MERCHANTABILITY
AND FITNESS FOR A PARTICULAR PURPOSE.
Schmitt Industries Incorporated does not warrant that the functions contained in the product will meet your requirements or that the operation of
the product will be uninterrupted or error free.
Schmitt Industries Incorporated does warrant as the only warranty provided to you, that the product which is furnished to you, will be free from
defects in materials and workmanship under normal use for a period of twelve (12) months from the date of delivery to you as evidenced by a
copy of your warrant receipt. LIMITATIONS OF REMEDIES
Schmitt Industries Incorporated’s entire liability and your exclusive remedy shall be:
1. the replacement of any hardware and software not meeting Schmitt Industries’ “Limited Warranty” and which is returned to Schmitt
Industries Incorporated or an authorized Schmitt Industries dealer with a copy of your purchase receipt, or
2. if Schmitt Industries Incorporated or the dealer is unable within ninety (90) days to deliver a replacement product which is free of defects in
material or workmanship, you may terminate this Agreement by returning the product and your money will be refunded to you by the dealer
from whom you purchased the product.
IN NO EVENT WILL SCHMITT INDUSTRIES INCORPORATED BE LIABLE TO YOU FOR ANY DAMAGES, INCLUDING ANY LOST
PROFITS, LOST SAVINGS OR OTHER INCIDENTAL OR CONSEQUENTIAL DAMAGES ARISING OUT OF THE USE OR INABILITY
TO USE SUCH PRODUCTS EVEN IF SCHMITT INDUSTRIES INCORPORATED OR AN AUTHORIZED DEALER HAD BEEN
ADVISED OF THE POSSIBILITY OF SUCH DAMAGES, OR FOR ANY CLAIM BY ANY OTHER PARTY.
SOME AREAS DO NOT ALLOW THE LIMITATIONS OR EXCLUSION OF LIABILITY FOR INCIDENTAL OR CONSEQUENTIAL
DAMAGES SO THE ABOVE LIMITATION OR EXCLUSION MAY NOT APPLY TO YOU.
GENERAL
You may not sublicense, assign or transfer the license or the hardware, software, and documentation except as expressly provided in this
Agreement. Any attempt otherwise to sublicense, assign or transfer any of the rights, duties or obligations hereunder is void.
This Agreement will be governed by the laws of the United States and the State of Oregon, United States of America.
Should you have any questions concerning this Agreement, you may contact Schmitt Industries Incorporated by writing to:
Schmitt Industries Incorporated
2765 NW Nicolai St.
Portland, Oregon 97210 USA
YOU ACKNOWLEDGE THAT YOU HAVE READ THIS AGREEMENT, UNDERSTAND IT AND AGREE TO BE BOUND BY ITS
TERMS AND CONDITIONS. YOU FURTHER AGREE THAT IT IS THE COMPLETE AND EXCLUSIVE STATEMENT OF THE
AGREEMENT BETWEEN YOU AND SCHMITT INDUSTRIES INCORPORATED AND ITS DEALER (“US”) WHICH SUPERSEDED
ANY PROPOSAL OR PRIOR AGREEMENT, ORAL OR WRITTEN, AND ANY OTHER COMMUNICATIONS BETWEEN US RELATING
TO THE SUBJECT MATTER OF THIS AGREEMENT.

AR4000 User’s Manual i
LLL004001 – Rev 2.7
Procedures for Obtaining Warranty Service
1. Contact your Acuity distributor or call Acuity to obtain a return merchandise
authorization (RMA) number within the applicable warranty period. Acuity will
not accept any returned product without an RMA number.
2. Ship the product to Acuity, postage prepaid, together with your bill of sale or
other proof of purchase. your name, address, description of the problem(s). Print
the RMA number you have obtained on the outside of the package.
This device complies with part 15 of the FCC Rules. Operation is subject to
the following two conditions:
(1) This device may not cause harmful interference, and (2) this device must
accept any interference received, including interference that may cause
undesired operation.
Note: This equipment has been tested and found to comply with the limits for a
Class A digital device, pursuant to part 15 of the FCC rules. These limits are
designed to provide reasonable protection against harmful interference when the
equipment is operated in a commercial environment. This equipment generates,
uses, and can radiate radio frequency energy and, if not installed and used in
accordance with the instruction manual, may cause harmful interference to radio
communications. Operation of this device in a residential area is likely to cause
harmful interference in which case the user will be required to correct the
interference at their own expense.
Copyright 2012 Acuity, product line of Schmitt Industries, Inc.

AR4000 User’s Manual ii
LLL004001 – Rev 2.7

AR4000 User’s Manual iii
LLL004001 – Rev 2.7
Table of Contents
1. INTRODUCTION.........................................................................................................1
2. GENERAL DESCRIPTION .........................................................................................2
2.1 MECHANICAL DIMENSIONS......................................................................................3
3. OPERATING GUIDELINES ........................................................................................4
4. SIGNAL AND POWER INTERFACE ..........................................................................5
4.1 8WIRE POWER AND SIGNAL CABLE ........................................................................5
4.1.1 POWER AND SIGNAL CABLE WIRE DESCRIPTIONS ............................................5
4.2 POWER SUPPLIES AND SAFETY INTERLOCKS............................................................7
4.2.1 LIR AND LV POWER SUPPLIES........................................................................7
4.2.2 IR INTERLOCK BOX.........................................................................................9
5. SERIAL INTERFACE SPECIFICATION ..................................................................11
5.1 HARDWARE PORT.................................................................................................11
5.1.1 OUTPUT FLOW CONTROL...............................................................................11
5.1.2 INPUT FLOW CONTROL .................................................................................11
6. INSTALLATION........................................................................................................12
6.1 CABLING ..............................................................................................................12
6.1.1 STANDALONE CABLING..................................................................................12
6.1.2 CONNECTION TO A HOST COMPUTER .............................................................12
7. INITIAL CHECKOUT ................................................................................................13
7.1 4000-LV.............................................................................................................13
7.2 4000-LIR............................................................................................................13
7.2.1 VERIFYING OPERATION.................................................................................13
7.3 TROUBLESHOOTING..............................................................................................13
7.3.1 SERIAL COMMUNICATIONS CHECK..................................................................14
7.3.2 RANGE OUTPUT CHECK................................................................................14
7.3.3 ANALOG OUTPUT CHECK..............................................................................14
7.3.4 RANGE MEASUREMENT QUALITY CHECK........................................................15
8. PERFORMANCE AND MEASUREMENT ACCURACY...........................................16
8.1 DETECTOR THERMAL NOISE..................................................................................17
8.2 LASER DIODE NOISE.............................................................................................17
8.3 MAXIMUM RANGE SPECIFICATION..........................................................................17
8.4 SAMPLING RESOLUTION........................................................................................17
8.5 OTHER FACTORS AFFECTING PERFORMANCE.........................................................18
8.6 SENSOR LINEARITY...............................................................................................18

AR4000 User’s Manual iv
LLL004001 – Rev 2.7
9.0 SERIAL COMMUNICATIONS.................................................................................19
9.1 OUTPUT DATA FORMATS.......................................................................................19
9.1.1 ASCII DATA FORMAT,CALIBRATED DISTANCE ONLY ......................................19
9.1.2 ASCII DATA FORMAT,LOW LEVEL SENSOR OUTPUTS ONLY ...........................19
9.1.3 ASCII DATA FORMAT,DISTANCE PLUS LOW LEVEL SENSOR OUTPUTS ............20
9.1.4 BINARY DATA FORMAT,CALIBRATED DISTANCE ONLY.....................................20
9.1.5 BINARY DATA FORMAT,LOW LEVEL SENSOR OUTPUTS ONLY .........................20
9.1.6 BINARY DATA FORMAT,DISTANCE PLUS LOW LEVEL SENSOR OUTPUTS..........20
10. CURRENT LOOP AND PULSE WIDTH OUTPUTS...............................................21
10.1 PULSE WIDTH OUTPUT .......................................................................................21
10.2 CURRENT LOOP OUTPUT ....................................................................................21
11. SERIAL AND ANALOG OUTPUT PERFORMANCE SPECIFICATIONS ..............22
11.1 SAMPLE RATE.....................................................................................................22
11.2 RESOLUTION ......................................................................................................23
12. CONFIGURATION AND NON-VOLATILE STORAGE............................................24
12.1 EEPROM OPERATION........................................................................................24
13. ACCURANGE 4000 COMMAND SET ...................................................................25
13.1 COMMAND QUICK REFERENCE ............................................................................26
13.2 COMMAND DESCRIPTIONS...................................................................................29
14. DATA SHEET: SUMMARY OF SPECIFICATIONS ................................................37
15. ACCURANGE LINE SCANNER .............................................................................38
15.1 GENERAL DESCRIPTION......................................................................................38
15.2 SCANNER PERFORMANCE SPECIFICATIONS..........................................................38
15.3 SCANNER INSTALLATION AND USE .......................................................................39
15.4 LINE SCANNER DATA SHEET ...............................................................................40

AR4000 User’s Manual 1
LLL004001 – Rev 2.7
1. Introduction
This section is a guide to getting started with the AccuRange 4000 and this
manual. The AR4000 has a number of configurable parameters, but many
applications can use it in its default configuration.
The first sections of the manual that should be read are the General Description
and the Operating Guidelines. After that Installation, with reference to the Signal
and Power Interface section for specific cable descriptions, should provide the
information necessary to connect the sensor and verify its operation, either with a
serial terminal program at 9600 baud, or by connecting the current loop interface.
To understand more about the format of the serial data, read the Serial
Communications chapter. For details on the current loop and pulse width outputs,
read the chapter titled Current Loop and Pulse Width Outputs.
For custom configuration, the AccuRange Command Set section provides
information on setting up the AccuRange for specific application requirements.
The remaining sections deal with specifics of the outputs and interfaces and with
general performance characteristics of the sensor.

AR4000 User’s Manual 2
LLL004001 – Rev 2.7
2. General Description
The AccuRange 4000 is a laser diode based distance measurement sensor for
ranges up to 50 feet, with 0.1 inch accuracy. There are three models, the 4000-
LV, 4000-LIR, and 4000-RET. The 4000-LV emits visible light (red, 670 nm
wavelength), while the 4000-LIR and 4000-RET uses near infrared light (780 nm
wavelength). The 4000-LIR is a Class IIIb laser product, available in power
levels of 8 mW (standard), or up to 20 mW with the High Power Laser option.
The 4000-LV is a Class IIIa laser product. The 4000-RET is a Class I eye safe
product for use with retroreflective tape. The labels shown below appear on the
AccuRange 4000-LV and 4000-LIR.
The 4000-LIR and 4000-RET have lower measurement noise and greater
sensitivity and maximum range. The 4000-LV features visible light output. See
the relevant descriptions in the Performance and Measurement Accuracy section
for noise and range information. Custom configurations of the AccuRange 4000
are also possible.
The AccuRange 4000 operates by emitting a modulated, collimated beam of laser
light and converting the distance to the target surface to an RS-232 or RS-
422/485 output. The range may be read via the serial cable as digital data, or
from the optional analog current loop output. A second cable supplies power to
the AccuRange 4000 and brings out other signals, which include reflected signal
strength, sensor temperature, and background light level. When configured for
use with the AccuRange 4000 High-Speed Interface and host-resident calibration
software, uncalibrated pulse-width modulated output is also available on this
cable.
4000-LIR: Emitter: 780 nm IR laser diode
Optical power 20 milliwatts max.
Effective Range: 50 feet
4000-LV: Emitter: 670 nm red laser diode
Optical power: 5 milliwatts max.
Effective Range: 40 feet
INVISIBLE LASER RADIATION
AVOID
DIRECT EXPOSURE TO BEAM
Class IIIb
780 nm Laser Product
DANGER
DANGER
LASER RADIATION
AVOID DIRECTEYE EXPOSURE
Class IIIa
670 nm Laser Product

AR4000 User’s Manual 3
LLL004001 – Rev 2.7
2.1 Mechanical Dimensions
Figure 1 shows the mechanical dimensions for the AccuRange. The laser beam is
emitted from the center of the front panel, and the central 2.5 inch diameter of the
front panel is a collector for return light. The bottom of the sensor has 4 blind
holes which are threaded for 6-32 bolts for mounting the sensor. The back of the
sensor has a switch for configuration and reset, LED, and two 6 foot cables. The
first is for serial communication, the second contains power and analog signals.
The weight of the AccuRange 4000 is 22 ounces.
Figure 1. Mechanical Specifications
The outer case of the sensor is .125” aluminum. The acrylic front window and the
back panel are sealed to the case, creating a watertight enclosure.

AR4000 User’s Manual 4
LLL004001 – Rev 2.7
3. Operating Guidelines
Use protective eyewear whenever there is a risk of being exposed to the
output beam of the 4000-LIR or 4000-LV. Use eyewear specifically designed
to block laser radiation of the frequency used by the sensor.
Do not point the sensor at any person, particularly a person’s eyes or face.
Laser radiation can damage the eyes without sensation or warning.
Do not attempt to disassemble the sensor. Improper disassembly will destroy
the optical alignment of the sensor and necessitate factory repairs.
Do not operate the sensor in areas where the sensor case is exposed to direct
sunlight for more than a minute or where the air temperature is more than
45
°
C (113
°
F). If the sensor is to be used in temperatures below 0°C (32°F),
apply power to the heater power supply lines. This will allow the sensor to
maintain a constant internal temperature, ensuring optimum operation.
Do not point the sensor at the sun or other intense heat sources. The sensor
will operate when pointed at sunlit areas, although sensitivity is reduced. The
optional optical filter is recommended for use on sunlit target areas.
Avoid excessive vibration and shocks. The sensor contains securely mounted
but precisely aligned optical components. These components are isolated from
the case with shock mounting, which protects them from all but severe shocks to
the case.
Do not scratch the front face of the sensor, particularly in the central area.
Keep the front face clean with a damp cotton cloth. The face is acrylic with an
anti-abrasion coating. Avoid the use of cleaning solvents other than alcohol.

AR4000 User’s Manual 5
LLL004001 – Rev 2.7
4. Signal and Power Interface
The 4000 has 2 cables. In the default configuration, the cable with the 9 pin
connector is a standard RS-232 serial port. If the 4000 is ordered with the RS-422
option, this cable is used for that. The other cable is an 8 pin power/signal cable.
If the 4000 is ordered with a power supply, the power/signal cable will pass
through the power supply. All wires are passed through the power supply except
the red, orange, and brown power lines which are connected only between the
power supply and the sensor. Connection and termination according to the
instructions is essential for correct sensor operation. Read the wire descriptions
for connection information.
4.1 8 Wire Power and Signal Cable
The table below shows the wiring on systems ordered without power supplies.
See the section on power supplies and safety interlocks for the wiring on systems
ordered with power supplies.
4.1.1 Power and Signal Cable Wire Descriptions
Line 1: +5V power at 300 milliamps. Maximum noise: 10 millivolts p-p.
Color: Red
Power supplies from 5 to 6 volts may be used. Higher voltages will result in
excessive current drawn by the overvoltage protection circuitry and may cause
permanent damage. Voltages less than 5.0 Volts at the cable end may result in
inaccurate range readings.
Line 2: Ground
Color: Black
Return for the 5V supply.
Wire Function Direction
Red Power, +5V (5-6V) In
Black Ground
Orange Heater Power, +5V (4.5-7V) In
Brown Heater Power Return
Yellow Temperature, 0-5 V Out
Blue Pulse Width Range
or Optional Current Loop Range Out
Green Ambient light signal, 0-5 V Out
Purple Amplitude signal, 0-5 V Out
Shield Ground at Supply End
Power and Signal Cable Wiring

AR4000 User’s Manual 6
LLL004001 – Rev 2.7
Line 3: Heater Power, 5 to 7 volts at 0-2 amperes, temperature dependent.
Color: Orange
Heater power and return may be optionally connected to supply power for
temperature regulation within the sensor. The current drawn by the heater power
circuitry depends on the difference between the ambient temperature and the hold
temperature for which the sensor is configured. It may be as high as 2 amperes in
extreme cases. The sensor power and ground lines should only be connected to
the heater power and ground at the source of a low impedance power supply, to
prevent high heater current from causing significant voltage drops in the supply
lines for the sensor electronics. This line should be left disconnected if heater
power is not used.
Line 4: Heater Power Return
Color: Brown
Return for the optional heater power. If heater power is used, connect to the
sensor electronics ground at the power supply. This line should be left
disconnected if heater power is not used.
Line 5: Temperature output: 0 to 4 volts. 5 mA max.
Color: Yellow
The temperature output is a linear indication of internal sensor temperature. This
may be used to monitor the internal temperature and to make range corrections
due to changes in temperature, although the temperature dependence of the
indicated range is typically small. The temperature output will change
approximately 29 millivolts for each 1°F change in sensor temperature, and
should read about 2.5 volts when the sensor is at 85°F. This output should be left
open when not in use.
Line 6: Pulse Width Range Signal: Pulse width square wave
OR: Optional Current Loop Range Output: 4-20 milliamps, 10 V max
output
Color: Blue
In the standard AccuRange 4000 configuration, this output provides an
uncalibrated measure of range. The period of the pulse is the sample interval for
which the sensor has been configured with the Sample Rate command. The
duration of the low portion of the pulse is proportional to measured range, scaled
by the sample rate and maximum range for which the sensor is configured. The
appearance is that of a square wave signal. See the Current Loop and Pulse
Width Outputs section for details. The pulse width signal is used by the
AccuRange High-Speed Interface to make range measurements at high sample
rates. It may be timed by sampling hardware to determine indicated
(uncalibrated) range. You need a 50 Ohms (51 Ohms +/-5% ok) between Signal
(blue) and Ground Reference (black). If you don’t have this resistor, the voltage
goes up and you see saw-tooth shape on the signal.
If the sensor was ordered with the optional current loop output, this line will
deliver a current proportional to the measured range. The zero range current,
offset of the zero range point, and the span (point of full scale output) may be set
using the appropriate commands. If calibrated output mode is enabled, the output
will be the actual distance to the target. Otherwise, the output will be the raw
sensor range, uncompensated for temperature, signal strength, and other effects.

AR4000 User’s Manual 7
LLL004001 – Rev 2.7
Best accuracy is obtained by loading the line with a 500 ohm resistor to ground at
the measurement point.
Line 7: Ambient light output: 0 to 4 volts. 5 mA max.
Color: Green
This output provides a measure of the total optical energy received by the sensor,
which is a combination of external illumination and the laser beam energy. This
may be used to make range corrections due to changes in ambient light levels at
the target location, although range dependence on ambient light is small unless
high ambient light levels such as sunlight are encountered. This output should be
left open when not in use.
Line 8: Amplitude output: 0 to 4 volts. 5 mA max.
Color: Purple
This output provides a measure of the strength of the signal received by the
sensor,
the amount of output laser light reflected back and collected by the sensor. This
may be used to make corrections to variations in the range reading caused by
changes in reflectance of the target. This output should be left open when not in
use.
Outer shield: Not connected. Should be grounded at supply end.
4.2 Power Supplies and Safety Interlocks
4.2.1 LIR and LV Power Supplies
The optional AC to DC power supplies for the AccuRange 4000-LV and 4000-
LIR supply operating power and temperature stabilization heater power to the
sensors. They are housed in NEMA-4 polycarbonate enclosures and are
permanently attached to the AccuRange 4000 power/signal cable, with 6 feet of
cable between the sensor and power supply. An additional 4 feet of cable extends
beyond the power supply for reading the sensor’s optional current loop and other
outputs.
The LIR Power Supply also includes the keyswitch and interlock jack required
for CFR certification for Class IIIb lasers. In the LIR Power Supply the
keyswitch and interlock jack located inside the box must be turned on and
installed to complete the laser power supply circuit.
To access the switch and jack, remove the four screws in the power supply case
and lift the top half of the case. When the circuit is complete, the indicator lamp
on the box will light, and power is applied to the sensor. After a 5 second delay,
the 4000-LIR laser will come on.
The wiring for the 8 line power and signal cable extending from the power
supplies is the same as for the AccuRange 4000LV and LIR, except that the 5

AR4000 User’s Manual 8
LLL004001 – Rev 2.7
volt power and heater lines, and the heater return line, are not connected. The
table below shows the wiring for the 8 wire cable extending from the LIR and
LV power supply boxes.
AR4000 Power Supply Dimensions
Wire Function Direction
Red No Connection
Black Ground
Orange No Connection In
Brown No Connection
Yellow Temperature, 0/5 Volt Out
Blue Pulse Width Range
or Optional Current Loop Range Out
Green Ambient light signal, 0-5 V Out
Purple Amplitude signal, 0-5 V Out
Shield No Connection
LIR and LV Power Supply Signal Cable Wiring

AR4000 User’s Manual 9
LLL004001 – Rev 2.7
AR4000 With Power Supply
4.2.2 IR Interlock Box
The IR Interlock box contains the same keyswitch and removable jack as the IR
Power Supply. To access the switch and jack, remove the four screws in the
power supply case and lift the top half of the case.
All of the lines in the AccuRange Power and Signal cable are connected straight
through, except that the red power line passes through the keyswitch and jack
before powering the laser. Removing either the key or the jack or turning off the
key breaks the sensor power circuit. When the circuit is complete, the indicator
lamp on the box will light, and power is applied to the sensor. After a 5 second
delay, the 4000-LIR laser will come on.

AR4000 User’s Manual 10
LLL004001 – Rev 2.7
IR Interlock Box Mechanical Dimensions
4000 LIR with Interlock Box

AR4000 User’s Manual 11
LLL004001 – Rev 2.7
5. Serial Interface Specification
5.1 Hardware Port
The default serial port in the AccuRange 4000 is a standard RS-232 port, which
can be connected to an IBM or compatible 9 pin serial port. If the 422/485 option
is ordered, the serial cable contains the wire pairs for point-to-point full duplex
RS-422 communication. Data can be transferred at any of several baud rates, in
binary or ASCII format.
RS-232 and RS-422 Serial Port Wiring
5.1.1 Output Flow Control
If configured for RS-232, The interface board responds to two types of flow
control: Ctrl-S/Ctrl-Q and hardware CTS/DTR. If configured for RS422, only
Ctrl-S/Ctrl Q can be used, since wire pairs for CTS-DTR are not included. The
interface will always stop transmission if Ctrl-S is received, and will resume
when Ctrl-Q is received. RS-232 interface response to the DTR flow control
input is controlled by the Flow Control configuration parameter. If flow control
is enabled and the host computer sets DTR false, the sensor will stop
transmitting. If flow control is disabled, DTR will be ignored. If output is
suspended in the middle of a sample, the remainder of the sample will be
transmitted when DTR is asserted by the host, but subsequent samples may be
lost.
5.1.2 Input Flow Control
The sensor does not transmit Ctrl-S/Ctrl-Q. In the RS-232 configuration, if the
input buffer is in danger of overflowing, the CTS line will be brought false. To
assure no loss of command string data, the host system should respond to this
signal if transmitting command strings of more than 10 bytes, or allow 0.1
seconds between commands for command completion. The Flow Control
configuration parameter has no effect on the interface’s assertion of CTS.
Pin # RS-232 Function RS-422 Function
1 NC TxData-
2 TxData TxData+
3 RxData RxData+
4 DTR RxData-
5 GND GND
6 DSR (Connected to CTS) NC
7 NC NC
8 CTS NC
9 NC NC

AR4000 User’s Manual 12
LLL004001 – Rev 2.7
6. Installation
6.1 Cabling
6.1.1 Standalone Cabling
To use the AccuRange 4000 without a serial connection to a host computer, the
only connections necessary are the power and ground lines, and the pulse width
or current loop signal connection to your data display or recording equipment.
See the Signal and Power Interface for wire connections. In its default
configuration, the AccuRange 4000 will begin measuring and transmitting range
on power-up (following a 6 second laser power-on delay for the 4000-LIR).
Depending on the configuration ordered, the range output line will have either
the current loop or pulse width output on it. The best accuracy and linearity for
the current loop is obtained with a 500 ohm load to ground at the measurement
point.
The signal strength, background light, sensor temperature, and/or the optional
current loop range output may be connected to analog input hardware. Use of a
temperature stabilization power supply is also recommended for maximum
accuracy. If you want to use temperature stabilization, attach the heater power
lines to a 5 volt supply.
The AR4000 requires at least 5 volts for sensor power, so if the same supply is
used for the sensor power as for the heater power, make sure that the lines are
connected together at the supply. Tying them together at a distance from the
supply may cause voltage drops in the power lines due to the heavy currents (up
to 4A in cold conditions) drawn by the heaters.
6.1.2 Connection to a Host Computer
Unless ordered with the RS-422 option, the cable with the 9 pin connector is the
RS-232 serial connection to the sensor. This may be directly connected to an
IBM-PC compatible serial port. Connect a 5 to 6 volt power supply to the power
and ground lines of the Power/Signal cable. See the Signal and Power Interface
for wire connections. Only the power and ground need be connected for
operation with the serial interface. Temperature stabilization power may also be
connected, as described above. For testing use a terminal emulation program
such as the Windows terminal, set to 9600 baud, 8 bits, no parity, 1 stop bit.
Sensors configured with the RS-422 option behave identically in software, and
any of several commercially available RS-22 cards may be used to support the
sensor on a PC communcations port.

AR4000 User’s Manual 13
LLL004001 – Rev 2.7
7. Initial Checkout
7.1 4000-LV
When power is applied the green LED on the back panel should flash briefly and
then stay on, and a bright red beam should be emitted from the center of the front
aperture. The sensor should give reasonable range information immediately,
although it will take 5-10 minutes for the internal temperature and range readings
to stabilize fully.
7.2 4000-LIR
When power is applied the green LED on the back panel should come on. After
approximately 6 seconds, the LED will flash briefly and the laser will come on.
The beam will be invisible or just barely visible. Use an IR viewing card in the
path of the beam for viewing. The sensor should give reasonable range
information after the 6 second delay has passed and the laser turns on, although it
will take 5-10 minutes for the range readings to stabilize fully.
7.2.1 Verifying Operation
In its default configuration, the 4000 transmits 5 samples per second at 9600
baud over the serial line, and transmits measured distance over the current loop
output (if installed) with the same update rate. The frequency of the pulse width
output will be higher: See the Pulse Width Output section. The current loop
should put out 4 mA at zero range, and 20 mA at 650 inches. Check either or
both of these signals to verify basic sensor operation.
7.3 Troubleshooting
If the LED does not come on, then blink once and stay on, check the power
supply wiring. If the laser does not come on (after 6 seconds for the 4000-LIR),
or the LED blinks rapidly (several times a second) check the power supply
voltage. If the LED blinks continuously about once a second after power-up, the
EEPROM has lost its configuration and/or calibration data. Pressing the switch
will allow power-up to continue, but configuration information and measurement
accuracy may have been affected. Messages will be transmitted over the serial
port describing the failure (see the section on Configuration and Non-Volatile
Storage). Configuration information may be restored by re-entering the desired
configuration. Contact Acuity in the event of calibration data loss.
In the event of slightly low voltage from the power supply, the sensor will stop
transmitting data and the LED will blink rapidly (several times a second) until
the power supply level is restored.

AR4000 User’s Manual 14
LLL004001 – Rev 2.7
If the power supply falls below 5 volts for more than 100 microceconds, the
sensor will be reset to avoid unreliable operation that could damage it. If this
occurs, the quality of the power supply and its ability to provide a constant
voltage when there is noise on the AC line. If the power supply output voltage
can be increased to 5.5 volts, this may provide enough margin to prevent resets,
unless the supply has very poor line regulation.
7.3.1 Serial Communications Check
If no information is received over the serial port, check the power supply and
serial cable connection. The sensor may in a configuration that prevents serial
communication, such as being set at the wrong baud rate. Turn the power off,
press the button on the back panel of the 4000, and turn the power on with the
button held down. The LED should stay off until the button is released, and then
flash briefly (after a 5 second pause on the 4000-LIR). This will reset the sensor
to the factory default configuration (9600 baud, 8 bits, no parity, 1 stop bit), and
should enable serial communication with the host system.
If no serial data is being received and the LED is blinking several times a second,
the power supply voltage is low. It should be at least 5.0 volts at the end of the 6
foot sensor cable.
7.3.2 Range Output Check
If the range output is in error, check that the sensor and target are stationary and
stable, that the target is about 8 feet from the sensor as an initial test range, and
that the beam is hitting the target. The sensor may need to warm up before
reaching full accuracy: leave it on for a few minutes and re-check the range
accuracy.
One way to check the basic ranging operation of a sensor configured with pulse
width output is with an oscilloscope. Check the waveform on the pulse width
output. It should be a square wave swinging from 0.4 to 0.9 volts, with at rise/fall
time of about 20 nanoseconds. The duration of the low portion of this signal
should increase as the distance to the target surface increases. The signal repeats
approximately 200 times per second at low sample rate settings, depending on
the maximum range configured. For high sample rate settings, the signal will
repeat once per sample interval.
7.3.3 Analog Output Check
The analog signal outputs can be tested with a voltmeter or oscilloscope. Each
should be between 0 and 5 volts. Amplitude should change as the target is
moved, or as the target color changed. The ambient light output will also change,
to a lesser degree. Pointing the sensor at a brightly lit surface should raise the
ambient light output. Temperature should rise gradually for the first 15 minutes
or so from a cold start, or more rapidly if the heater power is applied.
This manual suits for next models
2
Table of contents
Other Acuity Measuring Instrument manuals
Popular Measuring Instrument manuals by other brands
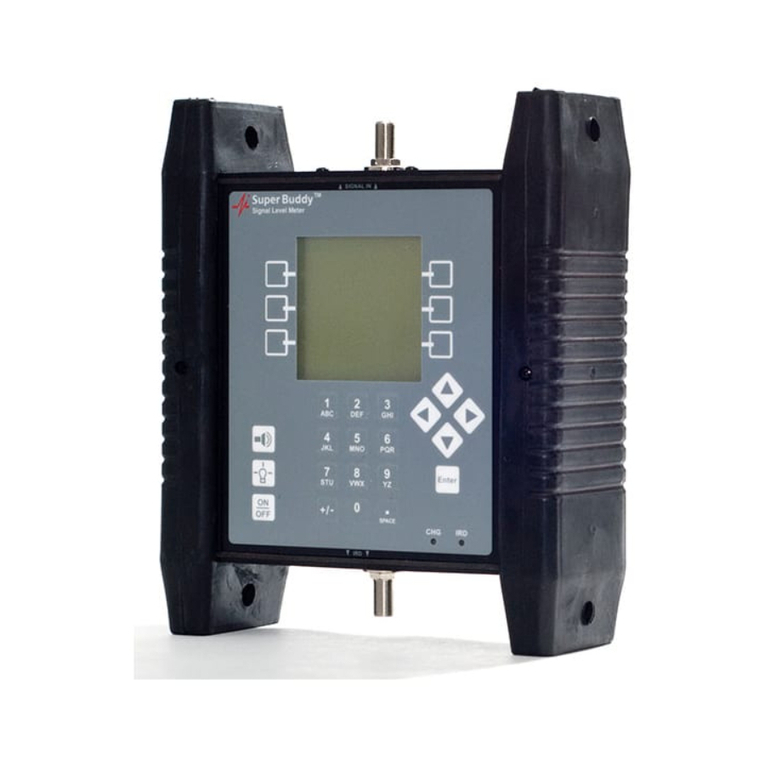
Applied Instruments
Applied Instruments Super Buddy 1000.4 East Application note
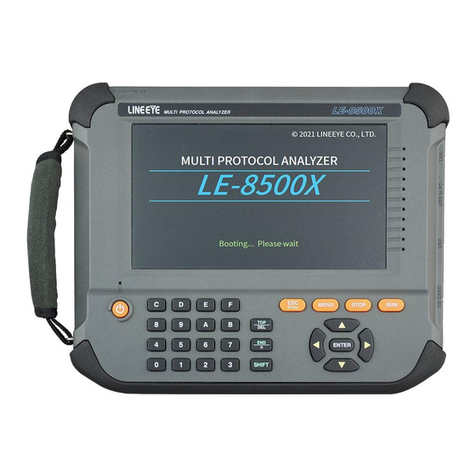
LineEye
LineEye LE-8500X quick start guide
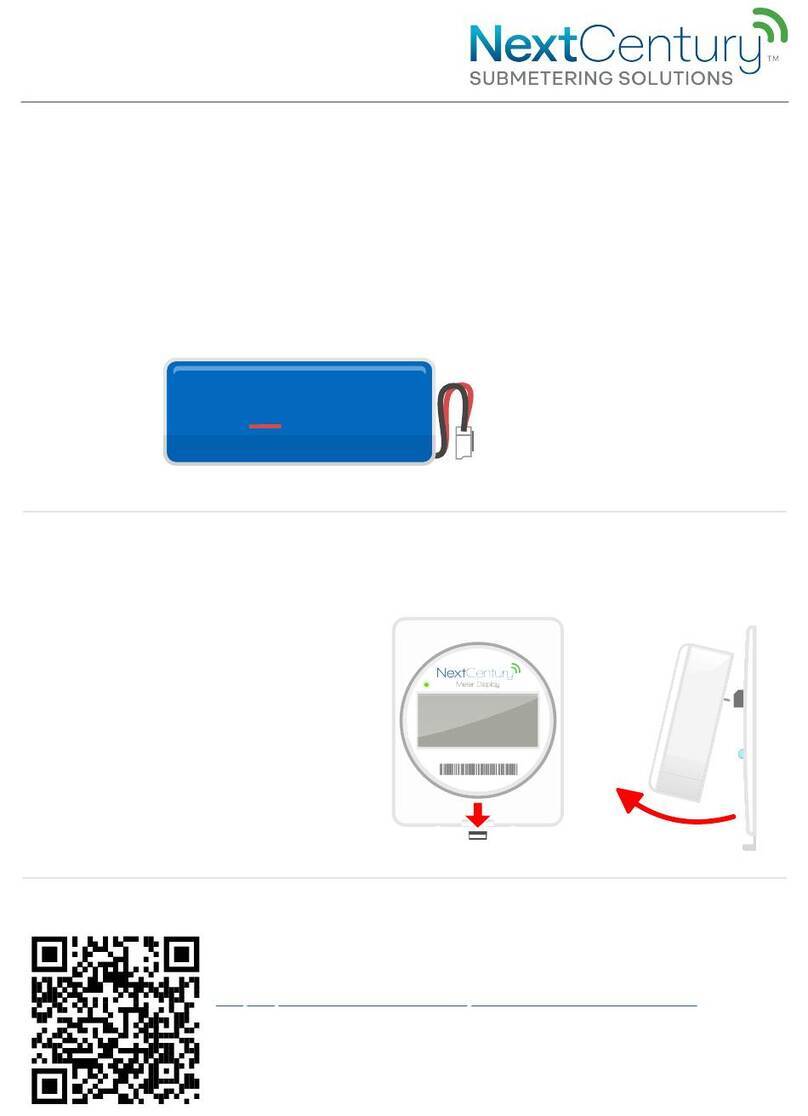
Next Century
Next Century BAT-301 quick start guide

i-PRO
i-PRO WJ-NU301K Series installation guide
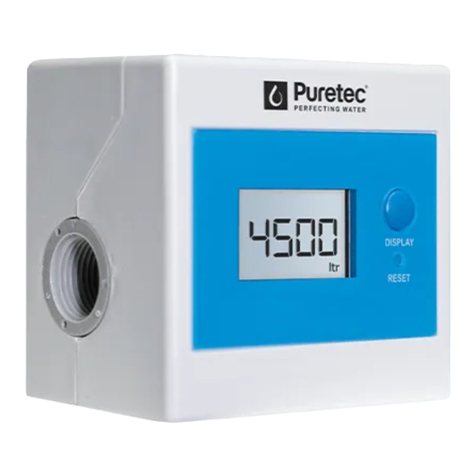
Puretec
Puretec PTE80 user guide
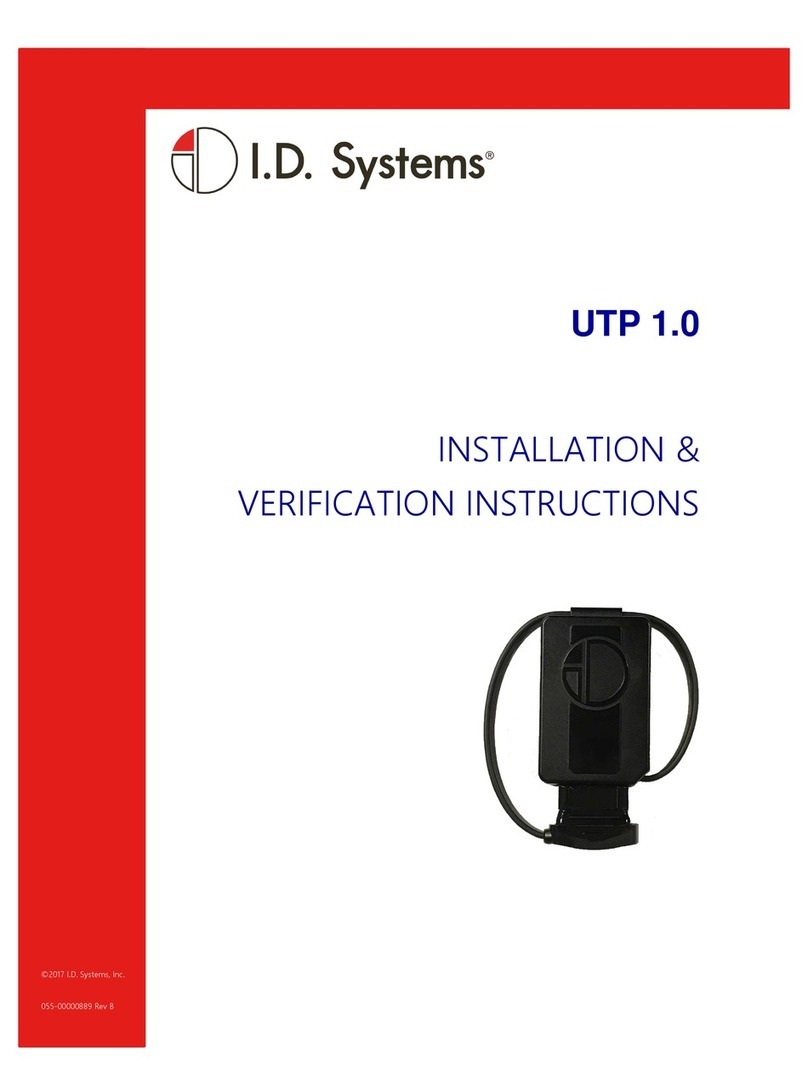
I.D. Systems
I.D. Systems UTP 1.0 INSTALLATION & VERIFICATION INSTRUCTIONS

Schonstedt Instrument
Schonstedt Instrument GA-72Cd instruction manual

Hitachi
Hitachi EUP-C514 instruction manual
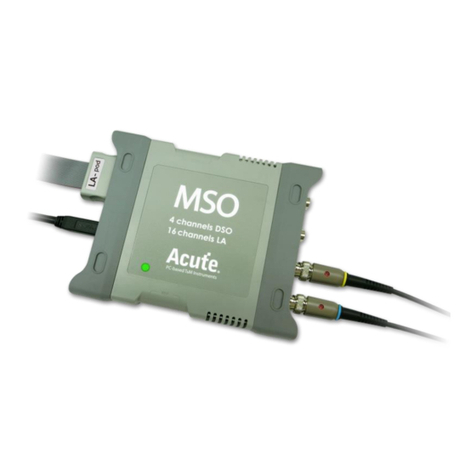
Acute
Acute MSO1000 Series manual

Rigaku
Rigaku 4364F501 instruction manual
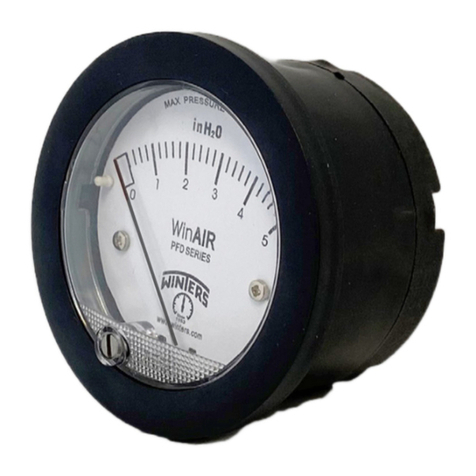
Winters
Winters WinAIR PFD Series Instruction and maintenance manual
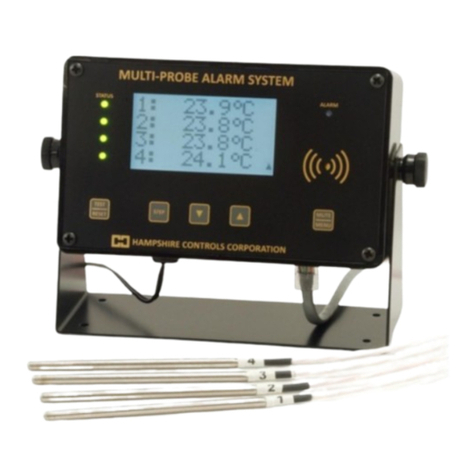
Hampshire Controls
Hampshire Controls MPS operating instructions