AEM 30-8402 User manual

AEM Performance Electronics
2205 W 126th Street, Unit A
Hawthorne, CA 90250
Phone (8am-5pm M-F PST): 310-484-2322
Fax: 310-484-0152
sales@aemev.com
tech@aemev.com
Page 1 of 23
AEM EV
Tesla LDU Inverter Control Board
Installation Manual

AEM Performance Electronics
2205 W 126th Street, Unit A
Hawthorne, CA 90250
Phone (8am-5pm M-F PST): 310-484-2322
Fax: 310-484-0152
sales@aemev.com
tech@aemev.com
Page 2 of 23
Table of Contents 3
Disclaimer 4
Introduction 5
Information
___________________________________________________________________________________________5
Revision History
___________________________________________________________________________________________5
Document Conventions
___________________________________________________________________________________________5
Reference Files and Documents
___________________________________________________________________________________________6
Cautions and Warnings
___________________________________________________________________________________________7
Electrical Safety Insulation Monitoring
___________________________________________________________________________________________7
Hardware Overview
___________________________________________________________________________________________8
CAN Network Configuration
___________________________________________________________________________________________9
Hardware Pinout
10
Tesla LDU Inverter Control Board Installation
___________________________________________________________________________________________14
Drive Unit Harness Installation
___________________________________________________________________________________________16
Temperature and Analog Inputs
___________________________________________________________________________________________17
Control Board Parameter Settings
___________________________________________________________________________________________19
Using the Programming Cable
___________________________________________________________________________________________20
Flashing Control Board Firmware
___________________________________________________________________________________________21
Using RMS GUI Software
___________________________________________________________________________________________22
Regen Torque Limit Profile
23
Warranty

AEM Performance Electronics
2205 W 126th Street, Unit A
Hawthorne, CA 90250
Phone (8am-5pm M-F PST): 310-484-2322
Fax: 310-484-0152
sales@aemev.com
tech@aemev.com
Page 3 of 23
Disclaimer
DANGER!
USE THIS PRODUCT WITH EXTREME CAUTION. MISUSE AND/OR IMPROPER INSTALLATION CAN CAUSE SIGNIFICANT DAMAGE
TO YOUR VEHICLE AND PROPERTY BELONGING TO YOU OR OTHERS, AS WELL AS PERSONAL INJURY OR DEATH. IF YOU ARE NOT
TRAINED IN ELECTRICAL ENGINEERING OR COMPLETELY FAMILIAR WITH THE SAFETY REQUIREMENTS OF HIGH VOLTAGE
ELECTRIC VEHICLES, AND/OR ARE NOT WELL-VERSED IN CONFIGURING THE NECESSARY CONTROL CALIBRATIONS IN THE AEM
VEHICLE CONTROL UNIT (VCU), DO NOT UNDER ANY CIRCUMSTANCES ATTEMPT TO INSTALL OR USE THIS PRODUCT. REFER THE
INSTALLATION AND CALIBRATION TO A REPUTABLE INSTALLATION FACILITY, OR CONTACT AEM EV FOR A REFERRAL IN YOUR
AREA. IT IS THE RESPONSIBILITY OF THE INSTALLER TO ULTIMATELY CONFIRM THAT THE INSTALLATION AND CALIBRATIONS ARE
SAFE FOR ITS INTENDED USE.
THE AEM LDU INVERTER CONTROL BOARD (“ICB”) WAS DEVELOPED TO ENABLE QUALIFIED INSTALLERS AND USERS TO INSTALL
A USED TESLA LARGE DRIVE UNIT (“LDU”) INTO ANY VEHICLE. TESLA LDU’S USED IN EV CONVERSIONS AND PURPOSE-BUILT
RACE VEHICLES ARE USED PRODUCTS AND THEIR CONDITION CANNOT BE EASILY VERIFIED. AEM’S ICB MAKES MORE TORQUE,
ALLOWS HIGHER MOTOR SPEED AND MAY ALLOW FOR HIGHER DC CURRENT DRAWS THAN THOSE OF A STOCK TESLA LDU
INVERTER. AEM HOLDS NO RESPONSIBILITY FOR ANY DAMAGE OR MECHANICAL DEGRADATION TO A TESLA LDU AND RELATED
DRIVETRAIN COMPONENTS, OR VEHICLE HIGH VOLTAGE SYSTEMS AS A RESULT OF THE INSTALLATION OR USE OF THIS
PRODUCT.
AEM AND ITS AFFILIATES, SHAREHOLDERS, DIRECTORS, OFFICERS, AGENTS, REPRESENTATIVES, SUCCESSORS AND ASSIGNS
(COLLECTIVELY, THE “AEM PARTIES”) HOLD NO RESPONSIBILITY FOR ANY DAMAGE OR INJURY THAT RESULTS FROM
INSTALLATION OR MISUSE OF ANY AEM PRODUCTS. EXCEPT FOR, TO THE EXTENT APPLICABLE TO THE PRODUCTS YOU HAVE
PURCHASED, AEM’S 12 MONTH LIMITED WARRANTY (WHICH CAN BE FOUND AT https://www.aemelectronics.com/about-
us/warranty-returns, ALL AEM PRODUCTS ARE PROVIDED “AS IS” AND THE AEM PARTIES EXPRESSLY DISCLAIM ALL
WARRANTIES, WHETHER EXPRESS, IMPLIED, STATUTORY OR OTHERWISE. THE AEM PARTIES SPECIFICALLY DISCLAIM ALL
IMPLIED WARRANTIES OF MERCHANTABILITY AND FITNESS FOR A PARTICULAR PURPOSE, AND ALL WARRANTIES ARISING FROM
COURSE OF DEALING, COURSE OF PERFORMANCE, USAGE OR TRADE PRACTICE. UNDER NO CIRCUMSTANCES SHALL ANY AEM
PARTY BE LIABLE TO YOU OR ANY OTHER PERSON OR ENTITY FOR ANY DAMAGES OF ANY AMOUNT OR CHARACTER
(INCLUDING, WITHOUT LIMITATION, ANY GENERAL, INDIRECT, SPECIAL, INCIDENTAL, EXEMPLARY, CONSEQUENTIAL OR
PUNITIVE DAMAGES) ARISING OUT OF, RELATED TO, OR IN CONNECTION WITH (1) YOUR INSTALLATION OF ANY AEM
PRODUCTS OR (2) YOUR MISUSE OF ANY AEM PRODUCTS. IN NO EVENT SHALL ANY AEM PARTY BE LIABLE TO YOU OR ANY
OTHER PERSON OR ENTITY FOR ANY LOST OR CORRUPTED DATA, LOST PROFITS, LOST REVENUES, LOSS OF USE, DIMINUTION IN
VALUE, LOSS OF OTHER INTANGIBLES OR ANY SPECIAL, INCIDENTAL, INDIRECT, EXEMPLARY, PUNITIVE OR CONSEQUENTIAL
DAMAGES, WHETHER ARISING OUT OF BREACH OF CONTRACT, TORT (INCLUDING NEGLIGENCE) OR OTHERWISE, REGARDLESS
OF WHETHER SUCH DAMAGES WERE FORESEEABLE AND WHETHER OR NOT THE AEM PARTIES WERE ADVISED OF THE
POSSIBILITY OF SUCH DAMAGES. SOME JURISDICTIONS MAY NOT ALLOW THE EXCLUSION OR LIMITATION OF INCIDENTAL OR
CONSEQUENTIAL DAMAGES, SO THE ABOVE EXCLUSIONS SHALL ONLY APPLY TO THE EXTENT PERMISSIBLE UNDER APPLICABLE
LAW.

AEM Performance Electronics
2205 W 126th Street, Unit A
Hawthorne, CA 90250
Phone (8am-5pm M-F PST): 310-484-2322
Fax: 310-484-0152
sales@aemev.com
tech@aemev.com
Page 4 of 23
Introduction
This document describes the installation, setup and configuration of the AEM EV Tesla LDU Inverter Control Circuit Board
(Control Board). It describes the new functionality and required configuration that exists with the replacement of the OE Tesla
Control Board.
The OE Tesla LDU inverter works by taking “throttle” commands directly from the accelerator pedal along with commands via
CAN to control vehicle direction, etc. All torque mapping and limiting is hard coded within the Tesla inverter itself and can never
be changed.
The AEM LDU Control Board works differently in that no direct accelerator pedal input to the inverter is required and that all
control commands are executed via CAN with an AEM VCU. The AEM VCU is the main vehicle control module that receives all
driver control inputs (accelerator pedal, drive direction, variable regen, etc) that allows for direct user adjustable torque mapping
and then executes the motor torque control commands to the inverter purely by CAN.
The scope of this document is limited to just the install and setup of the AEM LDU Control Board. It is assumed that all other e-
propulsion systems including HV ESS (including management, charging & safety systems), contactors, driver interface devices,
thermal management and other general vehicle requirements (drivetrain integration, steering, brakes, safety, etc) are already
established and correctly installed into the vehicle.

AEM Performance Electronics
2205 W 126th Street, Unit A
Hawthorne, CA 90250
Phone (8am-5pm M-F PST): 310-484-2322
Fax: 310-484-0152
sales@aemev.com
tech@aemev.com
Page 5 of 23
Information
Revision History
Revision
Date
Change Description
A
9/13/2021
Initial Release
Document Conventions
Information Type
Font Convention
VCU calibration options, channels, and tables
Italics
VCU calibration option value
Bold
Symbol
Information
When you see this sign, PAY ATTENTION! This indicates that something important is about to be said that
concerns your safety and the proper operation of the product. Use caution and be conservative. Use the
product in the manner described.
When you see this sign, you are being alerted to an IMMEDIATE DANGER. You MUST review these sections
carefully and do everything possible to comply with installation and operation requirements or you risk injury
or even death. Failure to comply with safety requirements will void all warranties and could expose you as the
installer to liability in the event of an injury.
Reference Files and Documents
File Name
Location
AEM EV Tesla LDU Control Board CAN Protocol
AEM LDU ICB 30-8402 CAN Protocol

AEM Performance Electronics
2205 W 126th Street, Unit A
Hawthorne, CA 90250
Phone (8am-5pm M-F PST): 310-484-2322
Fax: 310-484-0152
sales@aemev.com
tech@aemev.com
Page 6 of 23
Cautions and Warnings
Working on tractive systems (which includes but is not limited to motor(s), inverter(s), high voltage battery packs
and high voltage cables) requires special experience and training. AEM EV has implemented fault detection and
failsafe logic into its vehicle control units (“VCU”), however this does not mean that your VCU installation will be safe
or effective, or that your VCU installation will not interfere with other systems on your vehicle and create a
hazardous situation. It is the responsibility of the installer to understand the implications of each stage of tractive system
installation and testing and to recognize what might be unique about your application that presents potential hazards or safety
issues – and it is the responsibility of the installer to solve or address any such hazards or issues.
The following list includes basic recommended practices. This is not a comprehensive list; as noted below, if you are not well-
versed in the appropriate installation and testing procedures, you should refer the installation and calibration to a
reputable installation facility or contact AEM EV for a referral in your area.
·
When access is required near the battery pack, the cell segments must be separated by using an appropriate
maintenance disconnect plug.
·
When working on the battery pack or tractive system, safety gloves with side shields and appropriate insulated tools
must be used.
·
Always wear Class 0 gloves rated at 1000V with leather protectors.
·
Only use CAT III rated digital multimeters (DMM) and test leads.
·
When working on the battery pack or tractive system, work with one hand while keeping the other behind your back.
·
During initial system power up and testing, the vehicle must be raised off the ground and supported appropriately.
Wheels and tires should be removed.
·
During the VCU firmware upgrade process, battery cell segments must be separated using an appropriate maintenance
disconnect plug.
·
Do not make calibration changes when the inverter pulse width modulation (PWM) is enabled.
USE THIS VCU WITH EXTREME CAUTION. MISUSE AND/OR IMPROPER INSTALLATION CAN CAUSE SIGNIFICANT
DAMAGE TO YOUR VEHICLE AND PROPERTY BELONGING TO YOU OR OTHERS, AS WELL AS PERSONAL INJURY OR
DEATH. IF YOU ARE NOT WELL VERSED IN THE INSTALLATION OF TRACTIVE SYSTEMS OR CONFIGURING THE
CALIBRATIONS IN THE AEM EV VCU THAT ARE NECESSARY TO CONTROL THE VEHICLE, YOU SHOULD REFER THE
INSTALLATION AND VCU CALIBRATION TO A REPUTABLE INSTALLATION FACILITY, OR CONTACT AEM EV FOR A REFERRAL IN
YOUR AREA. IT IS THE RESPONSIBILITY OF THE INSTALLER TO ULTIMATELY CONFIRM THAT THE INSTALLATION AND
CALIBRATIONS ARE SAFE FOR ITS INTENDED USE.
ADVANCED ENGINE MANAGEMENT CO., INC. (“AEM”) AND ITS AFFILIATES, SHAREHOLDERS, DIRECTORS, OFFICERS, AGENTS,
REPRESENTATIVES, SUCCESSORS AND ASSIGNS (COLLECTIVELY, THE “AEM PARTIES”) HOLD NO RESPONSIBILITY FOR ANY
DAMAGE OR INJURY THAT RESULTS FROM INSTALLATION OR MISUSE OF ANY AEM PRODUCTS. EXCEPT FOR, TO THE EXTENT
APPLICABLE TO THE PRODUCTS YOU HAVE PURCHASED, AEM’S 12 MONTH LIMITED WARRANTY (WHICH CAN BE FOUND AT
https://www.aemelectronics.com/about-us/warranty-returns ), ALL AEM PRODUCTS ARE PROVIDED “AS IS” AND THE AEM
PARTIES EXPRESSLY DISCLAIM ALL WARRANTIES, WHETHER EXPRESS, IMPLIED, STATUTORY OR OTHERWISE. THE AEM PARTIES
SPECIFICALLY DISCLAIM ALL IMPLIED WARRANTIES OF MERCHANTABILITY AND FITNESS FOR A PARTICULAR PURPOSE, AND ALL
WARRANTIES ARISING FROM COURSE OF DEALING, COURSE OF PERFORMANCE, USAGE OR TRADE PRACTICE.
UNDER NO CIRCUMSTANCES SHALL ANY AEM PARTY BE LIABLE TO YOU OR ANY OTHER PERSON OR ENTITY FOR ANY DAMAGES
OF ANY AMOUNT OR CHARACTER (INCLUDING, WITHOUT LIMITATION, ANY GENERAL, INDIRECT, SPECIAL, INCIDENTAL,

AEM Performance Electronics
2205 W 126th Street, Unit A
Hawthorne, CA 90250
Phone (8am-5pm M-F PST): 310-484-2322
Fax: 310-484-0152
sales@aemev.com
tech@aemev.com
Page 7 of 23
EXEMPLARY, CONSEQUENTIAL OR PUNITIVE DAMAGES) ARISING OUT OF, RELATED TO, OR IN CONNECTION WITH (1) YOUR
INSTALLATION OF ANY AEM PRODUCTS OR (2) YOUR MISUSE OF ANY AEM PRODUCTS. IN NO EVENT SHALL ANY AEM PARTY BE
LIABLE TO YOU OR ANY OTHER PERSON OR ENTITY FOR ANY LOST OR CORRUPTED DATA, LOST PROFITS, LOST REVENUES, LOSS
OF USE, DIMINUTION IN VALUE, LOSS OF OTHER INTANGIBLES OR ANY SPECIAL, INCIDENTAL, INDIRECT, EXEMPLARY, PUNITIVE
OR CONSEQUENTIAL DAMAGES, WHETHER ARISING OUT OF BREACH OF CONTRACT, TORT (INCLUDING NEGLIGENCE) OR
OTHERWISE, REGARDLESS OF WHETHER SUCH DAMAGES WERE FORESEEABLE AND WHETHER OR NOT THE AEM PARTIES WERE
ADVISED OF THE POSSIBILITY OF SUCH DAMAGES. SOME JURISDICTIONS MAY NOT ALLOW THE EXCLUSION OR LIMITATION OF
INCIDENTAL OR CONSEQUENTIAL DAMAGES, SO THE ABOVE EXCLUSIONS SHALL ONLY APPLY TO THE EXTENT PERMISSIBLE
UNDER APPLICABLE LAW.
Electrical Safety Insulation Monitoring
The high voltage system in an electric vehicle is designed to be ungrounded (floating) with respect to the vehicle
chassis (frame). Insulation faults can cause electric shock, personal injury and even death. An insulation monitoring
device (IMD) must be used to protect against these faults. See Bender https://www.benderinc.com/ for more
information.
Hardware Overview
AEM EV Part Number
30-8402
Inverter LV DC Voltage
10-16
Volts
Inverter LV DC Current
61
Amps
Base LDU
Sport LDU
Min HV DC Voltage
250
Volts
Max HV DC Voltage
4502
Volts
Nominal HV DC Voltage
350
Volts
Max Speed
180003
RPM
Max DC Current, Motoring
1060
-
Amps
Max DC Current, Generating
160
-
Amps
Max DC Power, Motoring
390
-
kW
Max DC Power, Generating
60
-
kW
Max Torque Command, Motoring
450
-
Nm
Max Torque Command, Generating
704
-
Nm
Max Stator Temp
180
-
°C
Max Inverter Temp
80
-
°C
Pre-Charge Resistor, Resistance
30-100
Ohms
110 amp fuse recommended.
2LDU inverter DC link capacitors show rating of 450v. DC voltages >400v have not been tested by AEM.
3Possible drive unit degradation due to extended high rpm motor usage has not been thoroughly tested by AEM.
4Inverter Control Board is hardcoded with variable regen torque limit based on rpm - see Regen Torque Limit Profile .
22

AEM Performance Electronics
2205 W 126th Street, Unit A
Hawthorne, CA 90250
Phone (8am-5pm M-F PST): 310-484-2322
Fax: 310-484-0152
sales@aemev.com
tech@aemev.com
Page 8 of 23
CAN Network Configuration
The following diagram describes the basic network requirements. Four separate CAN networks are represented. The
network channel assignment for each device is not reconfigurable by the end user. All CAN channels in the VCU200
are internally terminated. The VCU must always be located at the physical end of a bus. All busses must be
terminated with a 120 ohm resistor at the physical end. CAN network wiring should be accomplished by a skilled
harness builder familiar with vehicle networking.
Network Summary
CAN1 – PC comms
CAN2 – Inverter, EMP Pump(s), PDU-8(s) & AEM CD Dash Port 1
CAN3 – CAN Keypad, Orion BMS2 (optional), VCU Data Transmit & AEM CD Dash Port 2
CAN4 – AEM CD Dash Port 2

AEM Performance Electronics
2205 W 126th Street, Unit A
Hawthorne, CA 90250
Phone (8am-5pm M-F PST): 310-484-2322
Fax: 310-484-0152
sales@aemev.com
tech@aemev.com
Page 9 of 23
Hardware Pinout
Pin #
Pin Function
Application Notes
1
12V Power
Switched 12v power, fuse to 10A
2
-
Not used
3
-
Not used
4
CAN Hi
Connect to VCU CAN 2, also internally connected to Pin 19
5
CAN Lo
Connect to VCU CAN 2, also internally connected to Pin 20
6
-
Not used
7
HVIL In
High Voltage Interlock Loop safety input
8
HVIL Out
High Voltage Interlock Loop safety output
9
Encoder 5V Power
5v power for encoder, 5v ref for GUI mode
10
Encoder Ch. A/RS232 Serial Tx
Encoder channel A, serial comms tx in program or GUI mode
11
Ground
Chassis ground
12
5v
5v analog sensor power
13
Analog In 1
0-5v input, 300kOhm pull up, voltage tx’ed over CAN
14
Analog In 2
0-5v input, 300kOhm pull up, voltage tx’ed over CAN
15
Sensor Ground
Use for sensor 0v reference only, do not connect to chassis
16
Encoder Ch. B/RS232 Serial Rx
Encoder channel B, serial comms rx in program or GUI mode
17
Encoder Ground
Sensor ground for encoder, ground ref for Program Enable mode
18
Shield Drain
Encoder cable shield drain
19
CAN Hi
Same CAN network as Pin 4
20
CAN Lo
Same CAN network as Pin 5
21
Program Enable
Ground = firmware flash mode, 5v = GUI mode
22
-
Not used
23
-
Not used

AEM Performance Electronics
2205 W 126th Street, Unit A
Hawthorne, CA 90250
Phone (8am-5pm M-F PST): 310-484-2322
Fax: 310-484-0152
sales@aemev.com
tech@aemev.com
Page 10 of 23
Tesla LDU Inverter Control Board Installation
The following describes how to install the Control Board into the Tesla inverter. Start by putting the drive unit on a steady work
surface in a position that allows access to the bottom side of the inverter. The motor end of the drive unit is very heavy and will
allow the drive unit to be placed on a strong work bench with the inverter end hanging off. Alternatively, the drive unit can be
suspended using an engine hoist, etc.
Be sure to exercise great caution when working beneath the drive unit.
The drive unit must be completely disconnected from any high voltage source.
Tools Required
·
4 mm Hex Key
·
Pry Tool
·
13mm Socket
·
T-30 Torx
·
T-10 Torx
Use hex key to completely unscrew protective cover retaining
screw.
Behind the cover are two rubber o-rings that seal passageways.
Carefully pry the cover away to disengage the o-rings and then
fully remove cover.

AEM Performance Electronics
2205 W 126th Street, Unit A
Hawthorne, CA 90250
Phone (8am-5pm M-F PST): 310-484-2322
Fax: 310-484-0152
sales@aemev.com
tech@aemev.com
Page 11 of 23
Use T-10 Torx to remove the inverter connector mounting
screws.
Use 13mm socket to remove HV cable mounting bolts.
Remove both HV cables.
Note – cables are different lengths which prevents
them from being re-installed in the wrong polarity.
Use T-30 Torx to remove the inverter cover attachment screws.

AEM Performance Electronics
2205 W 126th Street, Unit A
Hawthorne, CA 90250
Phone (8am-5pm M-F PST): 310-484-2322
Fax: 310-484-0152
sales@aemev.com
tech@aemev.com
Page 12 of 23
Gently move the end of the cover up/down & left/right to
release it from the sealing o-ring. While doing this, give
attention to also disengage the inverter connector from the
end of the cover. Once fully released, completely remove the
cover by sliding it straight off.
Start the removal of the stock Tesla board by removing the
screws indicated (green).
Leaving the connectors plugged in will hold the
board in place allowing for easier removal once all
the screws have been removed.
Carefully unplug all the connectors and then remove the board.
The board will come off with a metal EMI shield attached
behind it.

AEM Performance Electronics
2205 W 126th Street, Unit A
Hawthorne, CA 90250
Phone (8am-5pm M-F PST): 310-484-2322
Fax: 310-484-0152
sales@aemev.com
tech@aemev.com
Page 13 of 23
Remove the remaining screw, remove the Tesla board, put the
AEM Control Board in place, and secure with the one hold
down screw. Line up the other Control Board mounting holes
with the EMI shield and then lightly snug up the screw. This will
allow adjustment of the Control Board and shield while
remounting.
Position the Control Board back in the inverter and plug in
connectors to hold it in place.
Align the screw holes and install the mounting screws. Be sure
to tighten the one shield mounting screw. Double check that all
connectors have been plugged in.
Control Board installation complete. Re-install inverter cover, HV cables, all mounting screws and orange plastic protective cover.
Installation is the reverse of removal.

AEM Performance Electronics
2205 W 126th Street, Unit A
Hawthorne, CA 90250
Phone (8am-5pm M-F PST): 310-484-2322
Fax: 310-484-0152
sales@aemev.com
tech@aemev.com
Page 14 of 23
Drive Unit Harness Installation
INVERTER
Plug 23 way connector into inverter.
Route encoder branch toward motor end of drive unit.
Route all other branches to most convenient location to make
remaining connections.
PWR/GND
Connect RED to 10A fused power that turns on with VCU
Wake.
Connect BLACK to chassis ground.
Do NOT power the inverter using the power/ground circuits
from an AEMnet cable.
Deutsch DT plug and terminals included in kit.

AEM Performance Electronics
2205 W 126th Street, Unit A
Hawthorne, CA 90250
Phone (8am-5pm M-F PST): 310-484-2322
Fax: 310-484-0152
sales@aemev.com
tech@aemev.com
Page 15 of 23
ENCODER BREAK OUT
The encoder break out connection serves two purposes.
First is to connect to the encoder sensor itself.
Second is to provide an interface point for directly
programming the Control Board.
ENCODER
Plug 4 way connector into encoder sensor. Plug 6 way DTM
connector into encoder break out connection.
Note that encoder must be connected in order for the motor
to operate.
CAN 1/2
High speed CAN bus network into and out of the inverter. One
CAN lead will have 120 Ohm CAN termination plug installed.
Other open CAN connection should be connected to VCU CAN
2 for inverter control.
Leave the CAN termination plug in place if the inverter is the
node that’s physically furthest away from the VCU.
Deutsch DTM plug and terminals included in kit.
HVIL
High Voltage Interlock Loop. Optional but highly
recommended.
ORG/RED is HVIL In and ORG/BLK is HVIL Out. Connect
accordingly for VCU being used.
Deutsch DTM receptacle and terminals included in kit.

AEM Performance Electronics
2205 W 126th Street, Unit A
Hawthorne, CA 90250
Phone (8am-5pm M-F PST): 310-484-2322
Fax: 310-484-0152
sales@aemev.com
tech@aemev.com
Page 16 of 23
Temperature and Analog Inputs
The Control Board uses the LDU’s internal temperature sensors for referencing temperatures from different points within the
drive unit. These temperatures are transmitted out over the Control Board CAN datastream – see Reference Files and
Documents for CAN protocol. Additional external temperature sensors are not required.
CAN Channel
Description
i1_Power_Stage_A_Temp
Phase A transistor temperature, limit to 70°C, inverter faults at 80°C
i1_Power_Stage_B_Temp
Phase B transistor temperature, limit to 70°C, inverter faults at 80°C
i1_Power_Stage_C_Temp
Phase C transistor temperature, limit to 70°C, inverter faults at 80°C
i1_Motor_1_Temp
Stator temperature, limit to 170°C, inverter faults at 180°C
i1_Motor_2_Temp
Stator temperature, limit to 170°C, inverter faults at 180°C
i1_Motor_Temp
The higher of Motor 1 & 2 Temp, used by VCU as motor temp reference
i1_Housing_Temp_Inlet
Coolant temperature before inverter, used by VCU as inverter temp
reference
i1_Housing_Temp_Outlet
Coolant temperature after inverter
i1_Micro_Temp
Control Board temperature
The Control Board has two available 0-5v analog inputs – see Hardware Pinout . The inputs have a 300kOhm pull up resistor
and may be connected to any standard 0-5v output sensor such as a pressure transducer or can be connected to a temperature
sensor (additional pull up resistor may be required). Additionally, switches that connect to ground when on (open circuit when
off) may also be used. These inputs are NOT 12v tolerant. The voltage of these inputs is transmitted out over the Control Board
CAN datastream.
CAN Channel
Description
i1_Analog_Input_1
0-5v analog input voltage for add-on sensor inputs
i1_Analog_Input_2
0-5v analog input voltage for add-on sensor inputs
5
9

AEM Performance Electronics
2205 W 126th Street, Unit A
Hawthorne, CA 90250
Phone (8am-5pm M-F PST): 310-484-2322
Fax: 310-484-0152
sales@aemev.com
tech@aemev.com
Page 17 of 23
Control Board Parameter Settings
The Control Board comes from the factory pre-loaded with firmware and initial configuration parameter settings and is
essentially ready to use right from the package. The following is a list of configurable parameters that may be adjusted using the
Cascadia RMS GUI (Graphic User Interface) software. See Appendix at end of this manual for more info.
Active inverter HV discharge is disabled by default. It is imperative that active discharge only be enabled once
correct VCU contactor sequencing control has been established. Having HV contactors closed with HV still present to
the inverter will damage the inverter’s discharge hardware. The active discharge is triggered via an on-board relay
output. This output will go into an uncontrolled state during programming thus it is imperative that HV not be
present to the inverter any time the inverter is put into programming mode.
Except for enabling active HV discharge, setup changes to the Control Board using the RMS GUI is typically not
needed in most cases and the default settings should work very well as they are.
Motor Type EEPROM
Used to select different motor types (Base vs Sport) or different pre-programmed
motor control settings.
Base LDU =XXX
Relay Output State EEPROM
Relay output to trigger inverter HV discharge. Default setting is OFF. Must be
enabled for active HV discharge to function – see WARNING above. Value is
shown in Hex. Default value is 0x000C. Change to 0x002C to enable.
Discharge Enable EEPROM
Must be enabled for active inverter HV discharge to function – see WARNING
above. Default setting is OFF.
CAN ID Offset EEPROM
Used to set CAN ID offset if using multiple controllers on the same CAN network.
Default offset is 0x0A0. Range of CAN IDs is 0x0A0 – 0x0CF.
DC UnderVolt Thresh EEPROM
Sets the HV under-voltage fault threshold voltage. Set to 0 to disable HV under-
voltage fault function. HV under-voltage protection typically handled by VCU.
Inv OverTemp Limit EEPROM
Sets the inverter temperature limit in °C x 10. The inverter temp is sampled from
each of the 3 power phase module temp sensors. If temperature exceeds this
value, the inverter will go into a fault state. Hard coded with a max value of 80°C.
Mtr OverTemp Limit EEPROM
Sets the motor temperature limit in °C x 10. There motor temp is sampled from
each of the 2 stator temp sensors. If temperature exceeds this value, the inverter
will go into a fault state. Hard coded with max value of 180°C.
Full Torque Temp EEPROM
Sets the temperature threshold below which full torque is available. As the motor
temperature increases from Full Torque Temp to Zero Torque Temp, the allowed
motor torque is decreased linearly. Temp based derating typically handled by
VCU – can use this function as a backup.
Zero Torque Temp EEPROM
Sets the temperature where motor torque will be limited to zero. Temp based
derating typically handled by VCU – can use this function as a backup.

AEM Performance Electronics
2205 W 126th Street, Unit A
Hawthorne, CA 90250
Phone (8am-5pm M-F PST): 310-484-2322
Fax: 310-484-0152
sales@aemev.com
tech@aemev.com
Page 18 of 23
Shudder Compensation Enable EEPROM
Used to enable or disable shudder compensation.
Kp Shudder EEPROM
Sets the control gain x 100 of the shudder compensation function. Default value
is 20 (parameter setting of 2000).
TCLAMP Shudder EEPROM
Defines the maximum amount of shudder compensation torque x 10 to be
applied. Default value is 19.1 (parameter setting of 191).
Shudder Filter Freq EEPROM
Defines the low-pass filter frequency x 10 used for shudder compensation
calculation. Default value is 3.0 (parameter setting of 30).
Shudder Speed Fade EEPROM
Defines the point in RPM where maximum shudder torque compensation is
applied for low RPM usage. Between this value and Shudder Speed Lo, full
shudder torque is applied. Must be lower than Shudder Speed Lo value. Default
value is 20.
Shudder Speed Lo EEPROM
Defines the start point in RPM where shudder torque begins to ramp out
(decrease). Shudder torque ramp out is reduced linearly between Shudder Speed
Lo & Shudder Speed Hi. Must be higher than Shudder Speed Fade but lower than
Shudder Speed Hi. Default value is 300.
Shudder Speed Hi EEPROM
Defines the end point in RPM where shudder torque is reduced to zero and
shudder compensation is turned off. Must be higher than Shudder Speed Lo.
Default value is 400.

AEM Performance Electronics
2205 W 126th Street, Unit A
Hawthorne, CA 90250
Phone (8am-5pm M-F PST): 310-484-2322
Fax: 310-484-0152
sales@aemev.com
tech@aemev.com
Page 19 of 23
Using the Programming Cable
HV must NOT be present at the inverter when in programming mode!
With the Control Board mounted inside the inverter cover, direct physical access for programming or firmware updates is not
possible. Some means for communicating with the Control Board is necessary and this was accomplished by re-purposing the
original encoder A & B signal input circuits to also act as the serial communication interface (SCI). The main LDU harness has a
connection break in the encoder branch that allows for SCI connection. This is where the programming cable is plugged in to
interface with the control board.
Along with the encoder A & B circuits, the programming cable also makes use of the encoder sensor ground and 5v circuits. In the
encoder branch of the main LDU harness is the Program Enable circuit. If Program Enable is put to ground, the Control Board will
go into programming mode and is readied to receive firmware. If Program Enable is put to 5v, the Control Board will go into GUI
mode to allow parameter changes using RMS GUI software. The programming cable has a switch built into it to toggle between
ground for programming mode or 5v for GUI mode.
PROGRAMMING MODE
Point switch towards PURPLE wire for
PROGRAMMING mode.
GUI MODE
Point switch towards GREEN wire for GUI mode.
When putting the Control Board into programming mode, the programming cable switch should be put to PURPLE and the
inverter must be power cycled before programming mode will be active.

AEM Performance Electronics
2205 W 126th Street, Unit A
Hawthorne, CA 90250
Phone (8am-5pm M-F PST): 310-484-2322
Fax: 310-484-0152
sales@aemev.com
tech@aemev.com
Page 20 of 23
Flashing Control Board Firmware
Firmware is uploaded to the Control Board over SCI using C2Prog software. Use the following steps to load new firmware onto
the control board.
1. Download and install C2Prog_v1.7e-b5721 from https://www.cascadiamotion.com/documents > General Link to All Files >
02 Tools > C2000Prog > C2Prog_v1.7e-b5721.zip
2. Launch C2Prog and configure as shown:
a. Set Target to 28375,7,9S and set Options to 20MHz.
b. Enable only Smart Sector Selection.
Table of contents
Other AEM Controllers manuals
Popular Controllers manuals by other brands
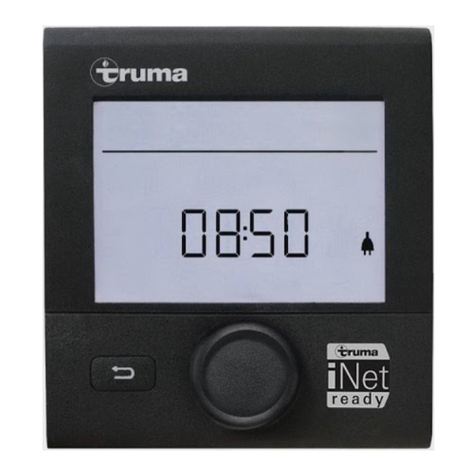
Truma
Truma DIGITAL TIMER CONTROL User instruction manual
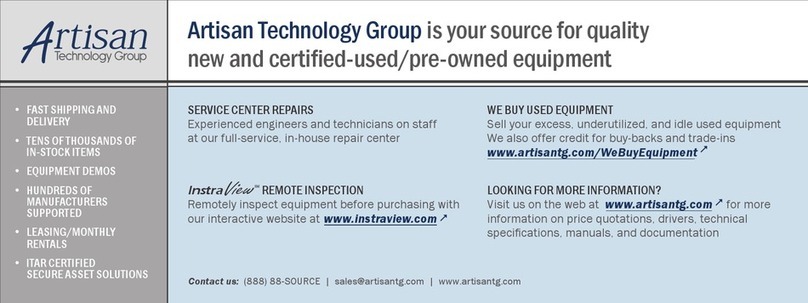
Rockwell Automation
Rockwell Automation Allen-Bradley PLC-2/30 Assembly and installation manual
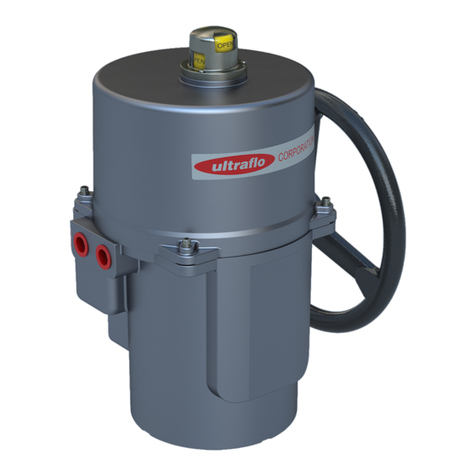
Ultraflo
Ultraflo 200 Series Installation and operation manual
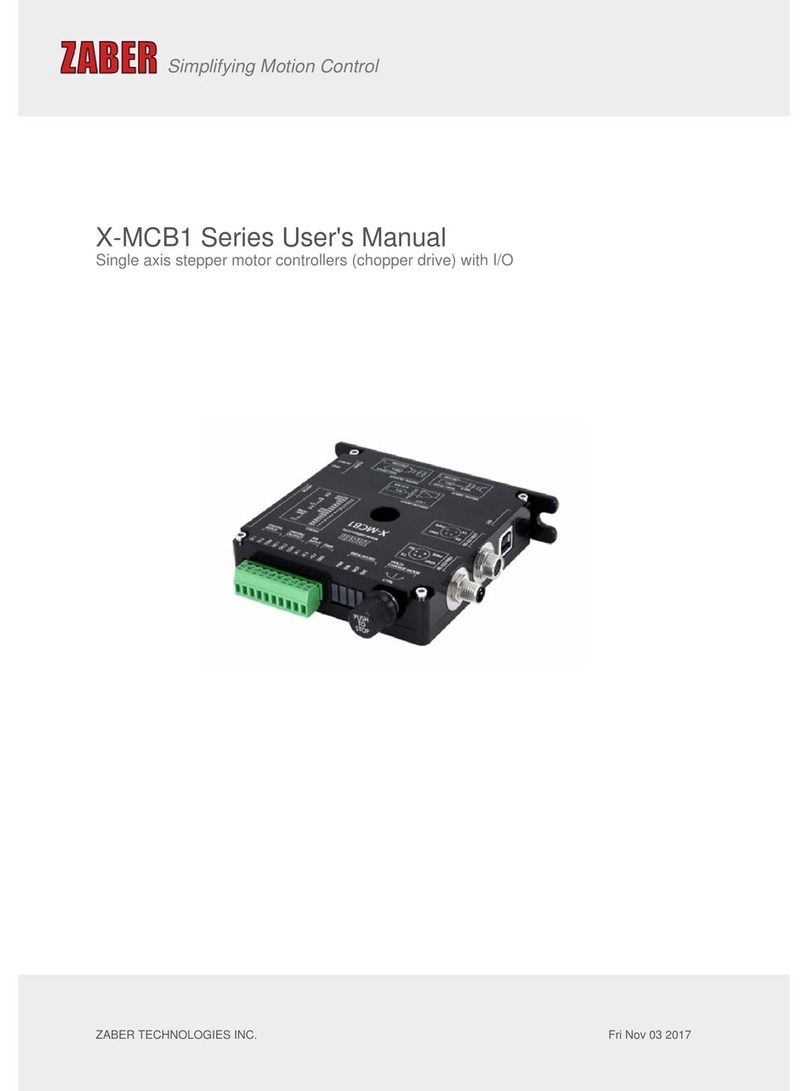
Zaber Technologies Inc.
Zaber Technologies Inc. X-MCB1 Series user manual
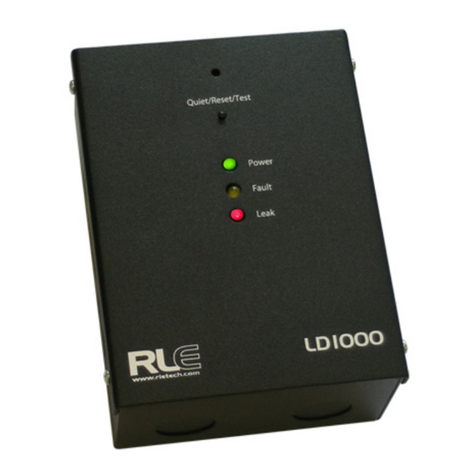
RLE
RLE SeaHawk LD1000 quick start guide

Siemens
Siemens 7SC80 manual