AJ M Series User manual

MAR 2021
Hydraulic Breaker
Operation Manual
& Parts List
M SERIES
(MEDIUM & LARGE RANGE)
600M,710M,810M,1000M,
1200M,1400M,1500M

Contents
1. Safety Precautions ····································································································································· 4
2. Storage ························································································································································ 6
3. Preparation for Installation and Operation ······························································································ 7
(1) Checking instructions before installation ··························································································· 7
(2) General view of breaker installed ·································································································· 7
(3) Hydraulic pipe lines for exclusive use ······························································································ 8
(4) Inspecting and charging N2 gas into the back head ······································································ 9
(5) Inspecting and charging N2 gas into the accumulator ································································ 11
(6) Hydraulic oil ······································································································································· 13
4. Precautions for Safe Operation ·············································································································· 14
5. Underwater Operation ···························································································································· 21
6. Maintenance ············································································································································· 25
(1) Daily breaker inspection ················································································································· 25
(2) Tightening torque & gas pressure ································································································· 27
(3) Regular breaker inspection and maintenance ··············································································· 28
(4) Replacement of chisel ····················································································································· 28
(5) Chisel claim judgment criteria ········································································································ 29
7. Trouble Shooting Guide ························································································································· 30
(1) Problems in operation ··············································································································· 30
(2) Gas leakage ···························································································································· 31
(3) Oil leakage ······························································································································· 32
8. Wear Tolerance ······································································································································· 33
9. Warranty Policy ······································································································································ 37

Preface
We totally appreciate your purchasing AJCE Hydraulic Breaker.
The Hydraulic Breaker, developed by AJCE's plentiful experiences and know-hows for
many years, will satisfy customers under any working conditions with its highest
power and long-time durability. However, without proper handling, regular inspection,
the advanced demolition tool fails to display its excellent quality, resulting in various
problems.
This operation manual shall be thoroughly read by customers before the first
installation and operation in order to prevent any mishandling of hydraulic breakers.
We guarantee that a faithful understanding of the operation manual shall contribute
to its best capacity.
If you have any further questions about operation of hydraulic breakers, please do
not hesitate to contact local dealers or visit our website(www.ajce.co.kr) or email to
We wish you a great success with us.

1. Safety Precautions
DO NOT OPERATE THE BREAKER UNLESS THE FOLLOWING SAFETY INSTRUCTIONS
HAVE BEEN THOROUGHLY READ AND UNDERSTOOD.
READ THIS MANUAL BEFORE INSTALLING, OPERATING OR MAINTAINING
THIS EQUIPMENT!
∎ Flying debris from the breaker, chisel, rock or other material may cause serious or fatal
injury to the operator. Personal protection equipment must be used. Never operate the
breaker when bystanders are in the work area.
∎ When operating the breaker, ear, eye, and breathing protection must be used at all times.
∎ The breaker will become very hot during the operation. Allow some times for the breaker
to cool down before touching breaker parts.
∎ Operate the breaker in accordance with all laws and regulations which affects you, your
equipment, and the work site.
∎ Know the limitation of your equipment.
∎ Do not operate the breaker unless thoroughly trained or under the supervision of an instructor.
∎ While learning about the breaker and the carrier, please do so at a slow pace. If necessary, set
the carrier mode selector to slow working position.
∎ Make sure all control (levers and pedals) are in neutral position before starting the carrier.
∎ Stop the engine before attempting to make any repairs, adjustments, or servicing to either the
carrier or the breaker.
∎ Do not operate the breaker at oil temperature above 175°F/80°C. Operation at higher temperatures
can damage the internal components of the breaker and as well as the carriers, and result in low
breaker performance.
∎ Do not operate the breaker in severe conditions such as, damage, leaking, improperly adjusted,
or an incompletely assembled breaker.
∎ Do not operate this equipment if you are taking medication which may affect your mental
judgment or physical performance.

This safety symbol may
appear on the breaker. It is
used to alert the operator
of an action that could
place him/her or other in a
life threatening situation.
This safety symbol appears in
these instructions to identify
an action that could cause
bodily injury to the operator
or other personnel.
This safety symbol appears in
these instructions to identify
an action or condition that
could result in damage to
the breaker or other
equipment.
GREASING
∎ Grease every 2 hours and whenever chisel looks dry.
∎ When installing a new chisel, liberally coat the upper 1/3 of the chisel
with grease before inserting.
∎ Failure to comply with these instruction can result in damage to the
breaker and will void the warranty.
∎ Warning sticker
Hearing Protection Eye Protection Breathing Read the manual
Protection before use
∎ Safety symbols
Safety symbols are to emphasize all operator, maintenance, and repair action, which, if not strictly
followed, could result in a life-threatening situation, bodily injury or damage to equipment.
Always observe safety symbols. They are symbols for your safety.
∎ Greasing sticker

∎ Short term storage
1. Store breaker in dry and flat area. Rain or snow may cause a rust in the
breaker.
2. Using your excavator, place the breaker horizontal on wooden pallet.
3. The breaker mount cap area shall be positioned higher than the chisel.
4. Remove the chisel and make sure the chisel pins, bushes are well greased.
5. Be sure that the hydraulic hoses are plugged to prevent dirty stuffs from
getting into breaker.
∎ Long term storage
1. Store breaker in dry and flat area. Rain or snow may cause a rust in the
breaker.
2. Discharge N2 gas in back head.
3. Remove the chisel and push the piston up into cylinder. Otherwise, the piston
bottom may get rusted.
4. Make sure the chisel pins, bushes are well greased.
5. Be sure that the hydraulic hoses are plugged to prevent dirty stuffs from
getting into breaker.
6. Breaker must be stored in the vertical position. Otherwise, the breaker may
cause oil leakage due to the seal damage.
2. Storage

∎ Check the specifications to determine correct carrier sizes, hydraulic pressure,
and hydraulic flow requirements.
∎ If the hydraulic pressure and hydraulic flow has exceeded, the breaker
warranty is not applied.
∎ Check the N
2 gas in the back head and the accumulator.
∎ Be sure that the fluid in the hydraulic system is clean.
∎ Check the hydraulic filter. Replace the filter if dirty or deteriorating.
Hose and piping must be flushed.
∎ The contaminated part must be cleaned without delay.
3. Preparation for Installation & Operation
(1) Checking instructions before installation
(2) General view of breaker installed

The circuit relief setting pressure is not fixed. However, it will be adjusted
by pump capacity.
(3) Hydraulic pipe lines for exclusive use
Operation of the hydraulic breaker requires installation of hydraulic pipe lines for exclusive use of
the hydraulic breaker. As hydraulic pipe lines are depending on base machines, our service engineer
must firstly check hydraulic pressure, oil capacity, pressure loss and other conditions. Use only
genuine parts in case of replacement because hydraulic pipe lines(hoses, pipes and fittings) are made
of materials carefully selected in consideration of durability.
∎ Recommended back pressure is 10 kg/㎠ for all AJCE hydraulic breakers.

∎ Lay down the breaker and let the chisel extend fully to charge gas.
∎ Stay clear of the chisel while charging the breaker with gas. The chisel may
be impacted by the piston and forced out abruptly.
∎ Take care when the through bolts are changed or the breaker body is
disassembled.
∎ Use special care to handle and store the N2 cylinder as it is a
High-pressurized container
∎ Use N
2 only.
(4) Inspecting and charging N2 gas into the back head
∎ Charging N2 gas into the back head
① Remove gas valve plug ② Insert 3-way valve ③ If gas is insufficient, adjust to specified
with pressure gauge valve as shown in the previous page
assembled
④ Adjust the pressure ⑤ Tighten gas valve plug
slowly by decreasing it (Do not cut O-ring)
through using the pressure
gauge if gas is sufficient.

∎ Insert 3-way valve after its handle is fully turned counterclockwise.
∎ Turn the 3-way valve handle clockwise slowly. Stop turning it when the
needle of the gauge starts to move. If it is turned clockwise too tightly,
the valve may easily be damaged. Pay special attention to ensure that
the nitrogen gas is not charged excessively.
ONLY FILL WITH N2 GAS!
GAS CHARGE PRESSURE : 6.8kg/㎠(97 PSI)
CAUTION - THIS VESSEL CONTAINS HIGH PRESSURE GAS.
REMOVE REMAINING GAS BEFORE DISASSEMBLY.
ONLY FILL WITH N2 GAS!
GAS CHARGE PRESSURE : 16.5kg/㎠(235 PSI)
CAUTION - THIS VESSEL CONTAINS HIGH PRESSURE GAS.
REMOVE REMAINING GAS BEFORE DISASSEMBLY.
∎ Back head sticker symbol
- Appears on the back head charging valve

∎ Use special care to handle and store the N2 gas cylinder as it is a high
pressurized container.
∎ Use N
2 gas only.
(5) Inspecting and charging N2 gas into the accumulator
∎ Inspection of N2 gas pressure in the accumulator
① Remove the charging valve plug and tighten the charging valve fully.
(Ensure that O-rings are installed in the plug.)
② Remove the charging cap and install the charging adapter.
③ Install the charging kit to the adapter.
④ Loosen the valve gradually. The gas pressure is indicated on the gauge.
⑤ Close the valve when the gas pressure is normal. If the gas pressure is hgiher,
repeat loosening and tightening the relief valve of charging kit.
⑥ Remove the N2 charging kit and tighten the charging cap and plug.
∎ Charging N2 gas pressure into the accumulator
① Connect the charging hose to the N2 charging kit and to the N2 gas cylinder.
② Remove the charging valve plug and tighten the charging valve fully.
(Ensure that O-rings are installed in the plug.)
③ Remove the charging cap and install the charging adapter.
④ Install the charging kit to the adapter.
④ Loosen the valve gradually. The gas pressure is indicated on the gauge.
⑤ Turn the handle of the N2 gas cylinder counter clockwise slowly to charge the gas.
⑥ Charge N2 gas in accordance with the specification table.
⑦ Turn the handle of the N2 gas cylinder clockwise to close.
⑧ Close the charging valve. If the gas pressure is higher, repeat loosening and tightening the relief
valve of charging kit.
⑨ Remove the charging hose, N2 charging kit, adapter and tighten the charging cap and plug.

Accumulator
gas pressure
Ambient Temperature(℃/℉)
0/32 10/50 20/68 30/86 40/104
kg/㎠ 50 52 55 58 61
psi 711 739 780 824 867
PRESSURIZED CONTAINER!
DISCHARGE PRIOR TO DISASSEMBLY! DO NOT OPEN
WITHOUT READING THE OPERATION MANUAL OR
CONSULTING AUTHORIZED SERVICE PERSONNEL!
Temperature(Max.) 80⁰C/175⁰F
Volume 0.78/1.33/1.48
Fill Material Only N2 gas
Accumulator
Precharge Pressure
55kg/cm², 780psi
(at 20°C/68°F)
∎ N2 gas pressure into the accumulator
* Each specifications are shown in the accumulator sticker below.
∎ Accumulator sticker(A) symbol
- Appears on the back head charging valve
∎ Accumulator sticker(B) symbol
- Appears on the accumulator charging valve

SPEC
Company
Hydraulic Oil Grease
Summer Winter All Season (MOS2)
ISO VG 46 ISO VG 32 ISO VG 46 NLGI No2
MOBIL
MOBIL
DTE 25
MOBIL
DTE 24
MOBIL
DTE 15M
MOBIL GREASE
SPECIAL
MOBIL SHC 525*
MOBILTH SHC 220**
MOBIL EAL SYNDRAULIC 46**
LG-CALTEX RANDO HD 46 RANDO HD 32 RANDO HD CZ MOLYTEX EP2
BP ENERGOL
HP 46
ENERGOL
HP 32
ENERGOL
HP 46 -
SHELL TELLUS 46 TELLUS 32 TELLUS T 46 RETINAX HDX-2
(6) Hydraulic oil
∎ Recommended hydraulic oils and greases for hydraulic breakers by AJCE
* : Synthetic Lubricant ** : Environmentally Friendly Synthetic Lubricant
∎ Oil Contamination
- Contaminated oil results in malfunctions of the breaker as well as the base machine and may
cause damage to parts. Pay special attention to oil contamination. Contaminated oil should be
changed without any delay. When changing oil, thoroughly wash oil tank, cylinder and pipes.
Cleaning or replacing oil filter also requires check for oil contamination.
- Replacement of filter : after first 50 hours and every 100 hours thereafter
- Replacement of hydraulic oil : every 500 hours
∎ Oil temperature
- The temperature of hydraulic oil shall not exceed 80°C/176°F. If higher temperature, oil cooler
is to fitted.

4. Precautions for safe operation
∎ Proper position must be applied for an effective use of breaking force. When position is incorrect,
the blowing energy of the piston is too weak to break rocks. Instead, blowing force applies shocks to
the breaker body, chisel and boom of the base machine, thereby resulting in damage to those parts.
∎ On the contrary, when position is excessive enough to break rocks with front of the base machine
raised, the machine may suddenly tilt forward the moment rocks are broken then the breaker's body
or the end of bracket may violently hit against rocks and result in damage.

∎ It is undesirable to carry out hammering under the below condition, because vibrations during
hammering may be transmitted to tracks of the base machine. During hammering, however, proper
position must be always applied to the breaker. Special care must be taken not to hammer under
abnormal condition.
∎ Apply same direction of boom force in line with the chisel, and place the chisel in the rock with
hammering surface as vertical as possible. If hammering surface is oblique, the chisel may slip during
hammering. This causes the chisel to seize and to be broken and piston to be damaged. When
breaking, fully stabilize the chisel first and then select the point of the rock on which hammering can
be performed in a stable condition.

∎ Stop operation as soon as hose vibrate excessively.
Excessive vibration of high and low-pressure hoses of breaker calls for an instant disassembly and
repair. Contact the nearest service station appointed by AJCE. For caution’s sake, check oil leakage
at the back head. The operator is required to pay attention to follow points during operation.
∎ Greasing
With breaker mounted on carrier, apply down pressure on the chisel and fill the cavity with
recommended grease through the grease nipple.
∎ When operating the breaker, you must use ear and body protection.
You must use ear and breathing protection when the breaker is operating.
∎ Accumulator type - Danger
Pay Attention to pressurized container! Do not open without reading the manual or consulting with
the authorized service personnel.
∎ Do not touch chisel while breaker is working.
While the breaker is working, high temperature of the chisel will be generated.

∎ Do not continue to hammer for more than one minute.
When rocks are not broken after more than one minute’s hammering at the same point, change
the place to be hammered. Extended hammering at the same place causes the chisel to wear out
excessively.
∎ Do not move rocks.
Avoid moving rocks with the side of the bracket, because it is the major factor that causes
broken bolts installed on the bracket, chisel and will damage the boom and the arm.
∎ Do not use chisel as a lever.
When breaking rocks by using chisel as a lever, bolts and chisel may be broken, too.

∎ On a hard and large rock, start breaking from the edge.
Even a hard and big rock can be easily broken when hammering begins at a crack or an edge.
∎ Operate breaker at proper engine speed.
Break rocks at the specified engine speed. Raising engine speed more than necessary, does not
strengthen hammering force but increases oil temperature to the detriment of pistons and valves.
∎ Do not operate the breaker in water and mud.
Do not operate the breaker when all components except chisel is immersed in water and mud.
Piston and similar components may gather rust and become a damaged breaker at an early stage.

∎ Do not allow the breaker to fall to break a rock.
Falling down the breaker will apply excessive force in order to the breaker or the base machine,
causing damage to many parts and the base machine.
∎ Warm up base machine engine prior to operation.
Especially in winter, the base machine engine should be warmed up for five to ten minutes
30°C~40°C(86°F~105°F) before breaker operation. Follow the instruction book for the base machine
to warm up the engine.
∎ Do not lift things with the breaker.
Lifting materials with a hanging wire in the bracket or chisel will not only cause damage to the
breaker but also is very dangerous while operating.

Blank Firing
To understand "Blank Firing", the operator needs to be aware that if the chisel is not pressed
against the work surface, the chisel will drop down in the lower body cavity far enough so that
the piston cannot strike it. Blank firing occurs whenever the breaker is operating and the piston is
not able to strike the chisel solidly or not strike the chisel at all. Blank firing accelerates wear and
tear on breaker and excavator components and may result in failure of one or more components.
Excessive blank firing may be considered equipment abuse and may result in voiding warranties.
Break-through or difficult surface contact results in blank firing when the material being broken
fractures and the chisel is no longer in "hard contact" with the material but is still pushed high
enough in the lower body cavity so that the piston can strike it. In this condition, the piston
strikes the chisel and the chisel is driven against the tool pins because it is not in sufficient contact
with the material to be broken. The energy is absorbed by the chisel pins, stop pins, front head
chisel pin area, other breaker components, and the excavator boom components. Blank firing of this
type can be experienced in trench work where obtaining striking contact with the work surface is
difficult or the wrong chisel is used, or in flat rock work where the operator fails to stop operation
of the breaker when slippage, fracturing or material break-through occurs.
Blank firing as a result of operator error occurs when the chisel is not in contact with the work
surface to be broken and is allowed to drop down in the lower body cavity so that the piston is
not able to strike it. Instead, the downward movement of the piston will be stopped by an
internal oil cushion located at the bottom of the pistons's stroke and the energy of the piston will
be absorbed by breaker components and excavator boom components. Blank firing of this type
can be experienced when the operator fails to stop operation of the breaker when the material
fractures or material break-through occurs, or during re-positioning of the breaker.
While blank firing cannot always be avoided, it can be kept to a minimum by avoiding the above
conditions as much as possible.
This manual suits for next models
7
Table of contents
Popular Power Tools manuals by other brands

Desoutter
Desoutter PT070-T6000-I13S user manual
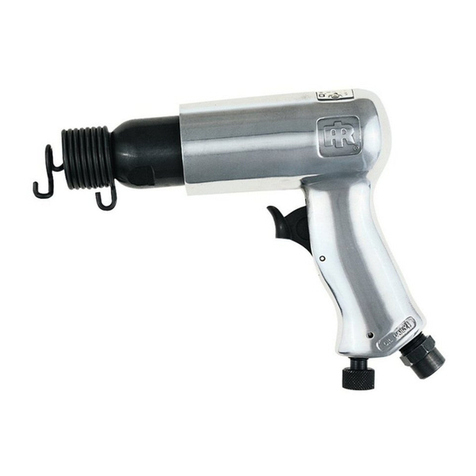
Ingersol Rand
Ingersol Rand 115 Series Product information
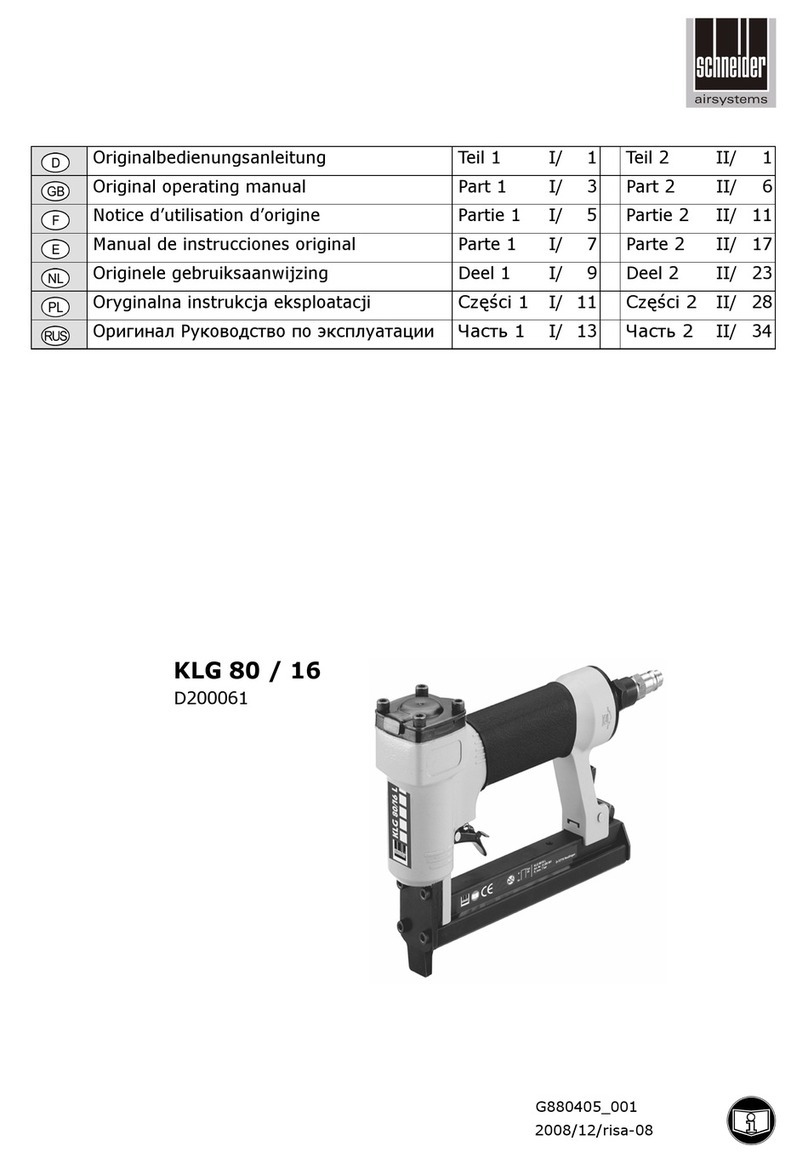
Schneider Airsystems
Schneider Airsystems D200061 Original operating manual
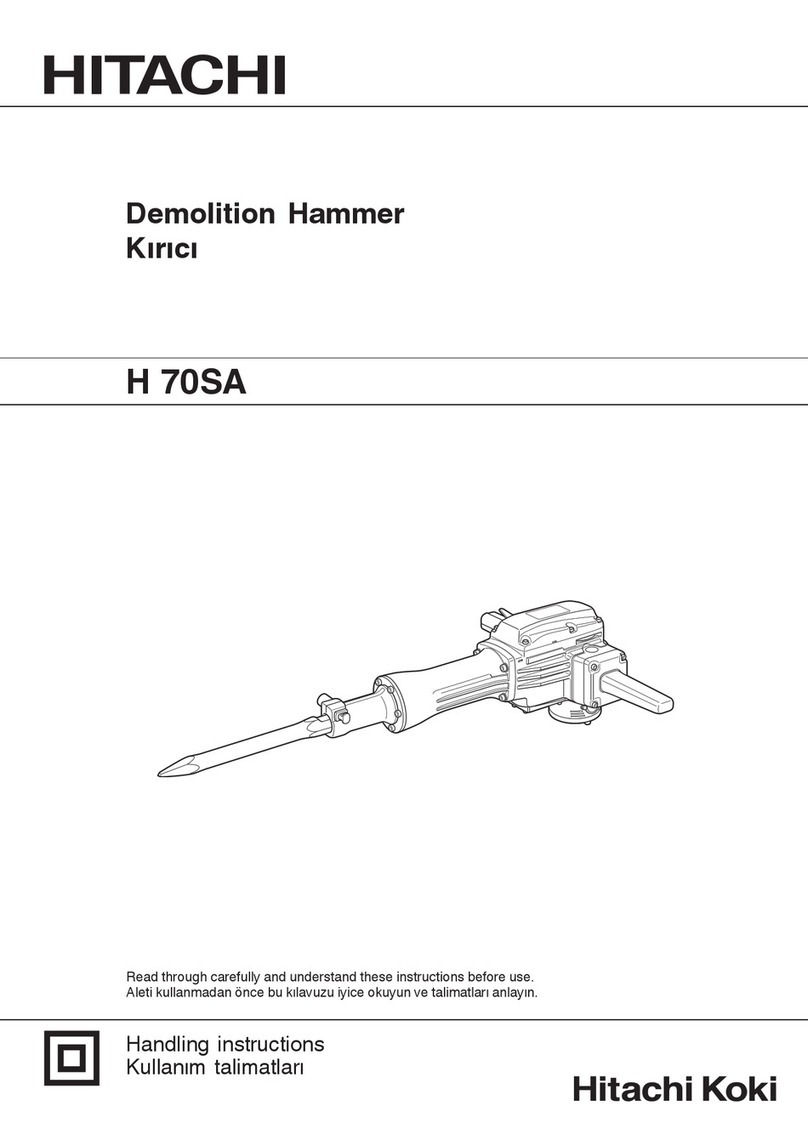
Hitachi Koki
Hitachi Koki EM4028 R2 Handling instructions
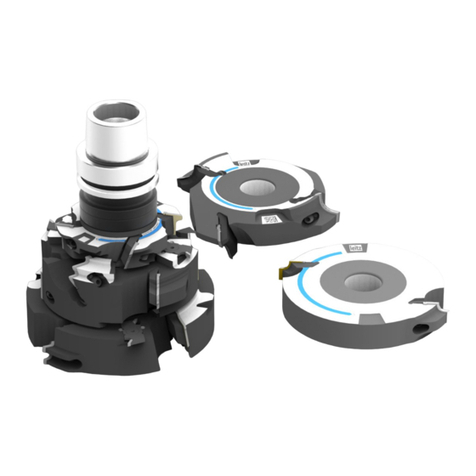
LEITZ
LEITZ ProfilCut instruction manual
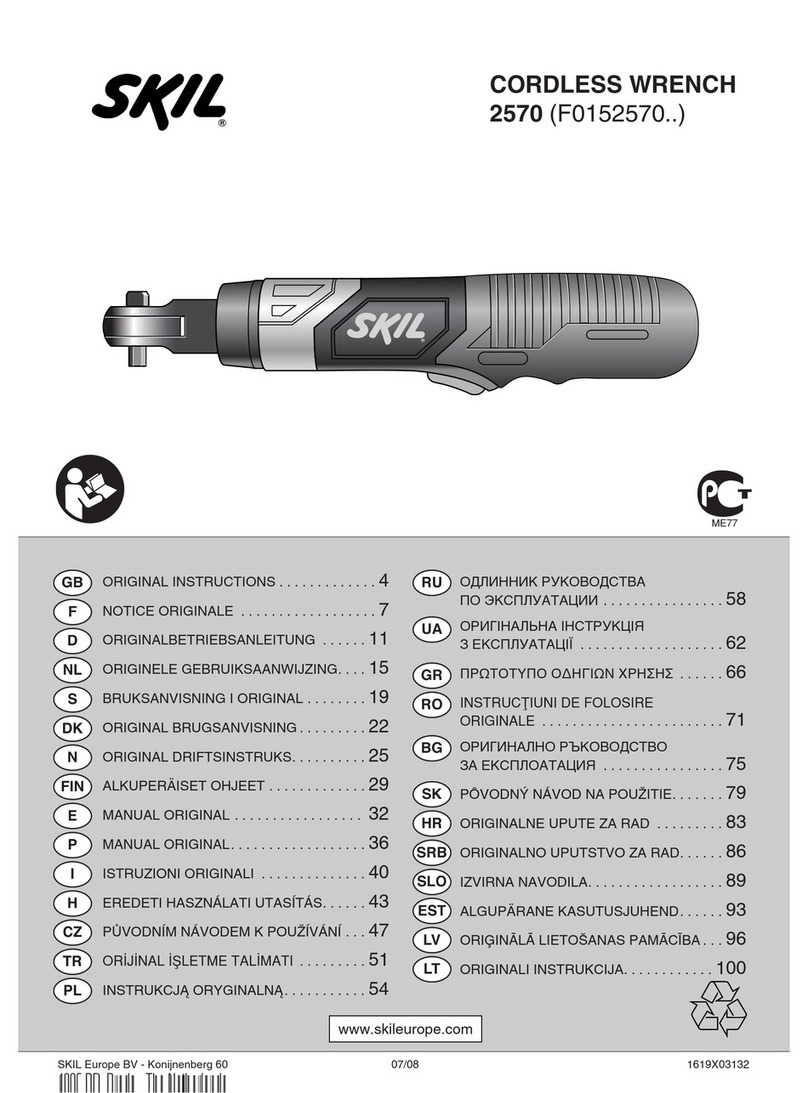
Skil
Skil 2570 Original instructions