Altec DRM 12 User manual

Copyright 2013 by Altec Industries, Inc.
All rights reserved. No part of this publication may be used or reproduced by any means, or stored in a
database or retrieval system, without prior written permission of the publisher. Making copies of any part
of this publication for any purpose other than personal use is a violation of United States copyright laws.
Altec Industries, Inc. reserves the right to improve models and change specications without notice.
2013
www.altec.com
DRM 12
Operator’s, Maintenance,
and Parts Manual
Operator’s and Maintenance Manual: 970413435 Parts Manual: 970413436

Preface
This unit is the result of Altec Environmental Products, LLC’s advanced technology and
quality awareness in design, engineering, and manufacturing. At the time of delivery from
the factory, this unit met or exceeded all applicable requirements of the American National
Standards Institute. All information, illustrations, and specications contained within this
manual are based on the latest product information available at the time of publication. It is
essential that all personnel involved in the use and/or care of this unit read and understand
the Operator’s Manual. Keep this manual with the unit.
Given reasonable care and operation, according to the guidelines set forth in the manuals
provided, this unit will provide many years of excellent service before requiring major main-
tenance.
Impacts to and excessive forces on the equipment, through vehicular accidents, rollovers,
excessive loading, and the like, may result in structural damage not obvious during a visual
inspection. If the equipment is subjected to such impacts or forces, a qualied person may
need to perform additional testing such as magnaux or ultrasonic testing as applicable. If
structural damage is suspected or found, contact Altec Environmental Products, LLC for
additional instructions.
Warning
Death or serious injury can result from component failure. Continued use of equipment
with hidden damage could lead to component failure.
Never alter or modify this unit in any way that might affect the structural integrity or opera-
tional characteristics without the specic written approval of Altec Environmental Products,
LLC. Unauthorized alterations or modications will void the warranty. Of greater concern,
is the possibility that unauthorized modication could adversely affect the safe operation of
this unit, resulting in personal injury and/or property damage.
Danger
Death or serious injury will result from operation of a chipper while coupled to an
energized aerial device. Non-insulated aerial devices have no dielectric rating. When
coupled, chipper to aerial lift and in the proximity of energized conductors, there shall
be no operation or contact with the chipper.
No unit can provide absolute safety when in proximity to energized conductors. No unit is
designed or intended to replace or supersede any protective device or safe work practice
relating to work in proximity to energized conductors. When in proximity to energized con-
ductors, this unit shall only be used by trained personnel using their company’s accepted
work methods, safety procedures, and protective equipment. Training manuals are available
from a variety of sources.
Set-up requirements, work procedures, and safety precautions for each particular situation
are the responsibility of the personnel involved in the use and/or care of this unit.


Section 1 — Introduction
About This Manual…..................................................................................................... 1
Section 2 — Unit Specications
Purpose of the Unit ....................................................................................................... 3
General Specications .................................................................................................. 3
Component Identication .............................................................................................. 4
Section 3 — Safety
Safety Instructions ........................................................................................................ 5
Lock-Out Tag Out Procedure (LOTO)..................................................................... 5
Capacity ........................................................................................................................ 5
Chipper Personnel Safety Devices ............................................................................... 6
Panic Bar Assembly................................................................................................ 6
Chip Curtain............................................................................................................ 6
Rotational Indicator................................................................................................. 7
Drum Blade Change Pin......................................................................................... 7
Guards.................................................................................................................... 7
Feed Roll Lock Pin ................................................................................................. 8
Safety Tow Chains.................................................................................................. 8
Breakaway Switch .................................................................................................. 8
Disclaimer of Liability .................................................................................................... 9
Accident Prevention Signs ............................................................................................ 9
Accident Prevention Signs Diagram ..................................................................... 10
Section 4 — Before You Operate…
Daily Preoperational Inspection .................................................................................. 19
Hitching to Tow Vehicle ............................................................................................... 20
Fueling Chipper........................................................................................................... 21
Controls....................................................................................................................... 21
Feed Roller Operation .......................................................................................... 21
PTO/Clutch Engagement...................................................................................... 22
FeedSense® (Electronic Feed Control)................................................................ 23
Work Site Preparation................................................................................................. 23
Brush Preparation................................................................................................. 24
Starting the Engine ............................................................................................... 25
Engaging/Disengaging the Cutter Head............................................................... 25
Feeding Brush to the Chipper............................................................................... 26
Winch Safety and Operation (Optional Equipment).............................................. 29
Section 5 — Clearing Feed System and Discharge Chute
Feed System............................................................................................................... 31
Discharge Chute ......................................................................................................... 32
Section 6 — Care of the Unit
Engine Oil ................................................................................................................... 33
Engine Coolant ........................................................................................................... 33
Engine Air Filter........................................................................................................... 33
Clutch and Power Take-Off (PTO) .............................................................................. 34
Battery......................................................................................................................... 34
Fasteners .................................................................................................................... 34
Tires and Wheels ........................................................................................................ 34
Tongue and Hitch ........................................................................................................ 34
Chipper Electric Braking System ................................................................................ 35
Table of Contents

Hinge and Friction Points............................................................................................ 35
Drum and Feed Roll Bearings..................................................................................... 35
Section 7 — Maintenance
Equipment Storage ..................................................................................................... 38
Protective Measures............................................................................................. 38
Extended Storage ....................................................................................................... 38
Engine Storage..................................................................................................... 38
Chipper Storage ................................................................................................... 38
Hydraulic System ........................................................................................................ 39
Cleanliness Precautions ....................................................................................... 39
Filtration................................................................................................................ 39
Oil Specications .................................................................................................. 40
Oil Condition ......................................................................................................... 40
Changing Oil and Flushing the System ................................................................ 41
Lubrication .................................................................................................................. 42
Lubrication Chart .................................................................................................. 43
Structures.................................................................................................................... 44
Care of Exterior Surfaces ..................................................................................... 44
Welds ................................................................................................................... 45
Fasteners .................................................................................................................... 45
System Operation ....................................................................................................... 46
Oil Reservoir ............................................................................................................... 46
Oil Pump ..................................................................................................................... 46
Hydraulic Motors ......................................................................................................... 46
Valves.......................................................................................................................... 46
Leakage ...................................................................................................................... 46
Heat Generation.......................................................................................................... 47
Hydraulic Lines ........................................................................................................... 47
Drive Belt/Pulleys........................................................................................................ 47
Troubleshooting, Testing, and Adjustments ................................................................ 49
Synchronizing Tow Vehicle Brake Controller ........................................................ 49
Breakaway Braking System.................................................................................. 49
Mechanical ........................................................................................................... 50
Electrical ............................................................................................................... 53
Troubleshooting.................................................................................................... 54
Appendix
Glossary
Torque Values
Daily Preoperational Checklist
Preventive Maintenance and Inspection Checklist
Troubleshooting Chart
Parts

Section 1 — Introduction • 1
Section 1 — Introduction
convenience. This glossary provides an understanding
of the industry terms and phrases used in Altec manuals.
Throughout the manual, the term unit is used to describe
the Altec device.
Additional copies of this manual may be ordered through
your Altec representative. Supply the model and serial
number found on the serial number placard and the
manual part number from the front cover to assure that
the correct manual will be supplied.
This symbol is used throughout this manual to
indicate danger, warning, and caution instruc-
tions. These instructions must be followed to
reduce the likelihood of personal injury and/or property
damage.
The terms danger, warning, caution, and notice repre-
sent varying degrees of personal injury and/or property
damage that could result if the preventive instructions
are not followed. The following paragraphs from ANSI
publications explain each term.
Danger
Indicates a hazardous situation which, if not
avoided, will result in death or serious injury. This
signal word is to be limited to the most extreme
situations.
Warning
Indicates a hazardous situation which, if not
avoided, could result in death or serious injury.
Caution
Indicates a hazardous situation which, if not
avoided, may result in minor or moderate in-
jury. It may also be used to alert against unsafe
practices.
Notice
The preferred signal word to address practices
not related to personal injury.
About This Manual…
This manual provides instruction for the operation and
maintenance of the unit. The operator must be familiar
with the unit and its capabilities before using the unit
on the job. This manual is written to provide an under-
standing of the unit, safety, proper set-up, operation,
and maintenance.
Charts and gures are provided to support the text.
Because options vary from one model to another, some
gures may only be a representation of what is actually
on the unit.
Contact the following organizations for additional infor-
mation.
• American National Standards Institute (ANSI)
Z133.1 Pruning, Repairing, Maintaining, and Remov-
ing Trees, and Cutting Brush-Safety Requirements
• American Public Power Association
(Safety Manual for an Electric Utility)
• American Society for Testing and Materials
(ASTM)
• American Welding Society (AWS)
• European Committee for Standardization (CEN)
• Fluid Power Society (FPS)
• Hydraulic Tool Manufacturer’s Association (HTMA)
• International Electrotechnical Commission (IEC)
• International Organization for Standardization
(ISO)
• Occupational Safety and Health Administration
(OSHA)
• Federal Motor Carrier Safety Administration
(FMCSA)
• U.S. Department of Transportation (DOT)
• Federal Highway Administration (FHWA)
Dealers, installers, owners, users, operators, renters,
lessors, and lessees must comply with the appropriate
sections of the applicable ANSI standard.
The Appendix contains reference items to assist in unit
operation.Aglossary of industry terms is provided for your

2 • Section 1 — Introduction

Section 2 — Unit Specications • 3
Section 2 — Unit Specications
Purpose of the Unit
This unit has been designed and built to reduce brush
and above ground tree components into uniformed wood
chips.
General Specications
This unit is a 12″(30.5 cm) capacity, controlled feed drum
chipper. The chipper mechanism is permanently mounted
on the towable frame assembly. The chipper mechanism
is belt driven by a self contained engine. Material is fed
utilizing one horizontally mounted, hydraulically controlled
feed roll. Chip discharge is designed for 360 degree rota-
tion for chip body and road side discharge applications.
Item Specication
Chipping capacity 12″(30.5 cm)
Engine horsepower 85 horsepower (63 kW)
Weight 5,310 pounds (2,408 kg)
Tongue weight (may vary) 530 pounds (240 kg)
Travel height 8’ 2″(2.5 m)
Width 6’ 8″(2 m)
Travel length 15’ (4.5 m)
Operational length 16’ 11″(5.2 m)
Feed roller opening 17″(43.18 cm) wide x 12″(30.5 cm) high
Feed table dimensions 50″(127 cm) wide x 30″(76.2 cm) deep
Infeed chute opening 50″(127 cm) wide x 30″(76.2 cm) high
Length to feed roll nip point194″(2.4 m)
Drum dimensions 20″(50.8 cm) wide x 21″(53.3 cm) diameter
Drum weight 520 pounds (236 kg)
Drum rpm 2,230 rpm
Feed rolls 161/2″(41.9 cm) wide x 20″(50.8 cm) diameter
Feed rate 111 feet per minute (34 mpm)
Feed wheel motor rating 32.2 cu in displacement (528 cu cm)
Hydraulic pressure 2,500 psi (172.4 bar)
Hydraulic tank capacity 12 gallon (45.4 l)
Fuel tank capacity 18 gallon (68.1 l)
Discharge chute rotation 360°
1 Measured from ground level at infeed chute, through the center of the feed table.
Figure 2.1 — Unit Specications

4 • Section 2 — Unit Specications
Component Identication
Panic Bar
Fuel Tank
Hydraulic
Motor
Infeed Chute
Engine
Tow Bar
Fender
Breakaway
Switch
Clearance
Lights
Fender
Hydraulic
Filter
Hydraulic
Reservoir
Pintle
Hook
Belt Guard
Chute
Deector
Feed
Box
Discharge Chute
Feed Table
Chute
Rotation
Control
Bar
Jack
Stand Safety
Chains
Clutch
Chute Height
Adjustment

Section 3 — Safety • 5
Section 3 — Safety
Safety Instructions
This unit is designed and manufactured with many fea-
tures intended to reduce the likelihood of an accident.
Safety alerts throughout this manual highlight situations
in which accidents can occur. Pay special attention to
all safety alerts.
Danger
Death or serious injury will result from careless or
improper use of the unit. Do not operate the unit
without proper training.
Warning
Death or serious injury can result from careless
or improper use of the unit. The operator bears
ultimate responsibility for following all regulations
and safety rules of their employer and/or any state
or federal law.
It is very important that all personnel are properly trained
to act quickly and responsibly in an emergency, knowing
the location of the controls and how they operate. Keep
any tools or equipment needed to perform manual opera-
tions in a well-marked, designated area. Keep the work
area well organized and eliminate trip hazards.
Danger
Death or serious injury can result from entanglement
with material being fed into the chipper. Always wear
the proper protective equipment for the task being
performed. Make sure all safety operational and
maintenance parameters are strictly enforced.
Death or serious injury can result from accessing
moving components such as cutter drum/disc or drive
components. Never attempt access to or attempt to
cover moving components.
Death or serious injury will result from unprotected
contact with energized conductors. Do not operate
or come in contact with a chipper while coupled to
an operational aerial device.
Knowledge of the information in this manual and proper
training provide a basis for safely operating the unit. Follow
your employer’s safe work practices and the procedures
in this manual when operating the unit.
Lock-Out Tag Out Procedure (LOTO)
Warning
Death or serious injury can result from unexpected
movement. Follow the lock-out tag out procedure
before accessing internal components of the unit.
LOTO procedures must be completed prior to performing
maintenance or clearing debris from internal components
of the chipper or engine.
Never leave the chipper unattended with the keys in the
ignition.
1. Turn Ignition key off and remove key. Secure the key
in a safe location with controlled access.
2. Make sure chipper drum or disc comes to a complete
stop.
3. Remove negative battery cable.
4. Lock and tag battery box.
5. Follow all appropriate LOTO procedures according to
OSHA Standards 29 CFR Standard 1910.147 (The
Control of Hazardous Energy).
6. Follow any additional federal, state, local, or con-
trolling agency standards or procedures that may
apply.
General Operating Information
• Do not operate the unit without proper training.
• Be sure that the unit is operating properly, and has
been inspected, maintained, and tested in accordance
with the manufacturer’s and government’s require-
ments.
• Use required personal protective equipment.
• Be aware of the surroundings.
• Perform the Daily Preoperational Inspection before
operating the unit each day.
• Apply the tow vehicle parking brake and chock chip-
per and tow vehicle wheels.
• Properly set up chipper operational area, including
vehicle and pedestrian control.
• Never exceed the rated capacity values.
• Follow all of your employer’s work rules and applicable
government regulations.
• Verify there are no loose tools or materials on the
chipper or in the infeed chute.
Capacity
This unit capacity is the maximum size material which
will pass through the feed wheel opening. Always take

6 • Section 3 — Safety
into consideration general material shape, protrusions,
and attached limbs.
Chipper Personnel Safety Devices
Danger
Death or serious injury will result from careless or
improper use of the unit. Do not operate the unit
without proper training.
All personnel using this chipper must be trained and
qualied in all aspects of the operations, maintenance,
repair, and safety procedures dened in this manual
prior to conducting any operations or procedures. All
maintenance personnel and operators shall ensure the
proper operation of each safety device prior to starting
the engine or operating the chipper. Contact Altec Envi-
ronmental Products for replacement parts.
Warning
Death or serious injury can result when operating
this unit. Safety devices are not a substitution for
proper operation. Read the entire manual and all
safety decals and placards.
Panic Bar Assembly
In the event of an unforeseen situation the panic bar
(refer to Figures 3.1 and 3.2) can be activated by pulling
down on bar A or by pulling or pushing bar B towards the
rear of the chipper. This action will stop all movement of
the feed roller.
Figure 3.1 — Panic Bar Assembly
Warning
Death or serious injury can result from unexpected
roller movement. Feed rollers begin movement as
soon as the valve handle is activated. Make sure all
operators are advised prior to your actions and that
the infeed chute is clear of all personnel and tools
before reactivation of the feed system.
Figure 3.2 — Valve and Bar Linkage
The panic bar assembly consists of two bars (A and B),
the hydraulic valve and the bar linkage. When you pull
down on bar A or push towards the rear of the chipper
on bar B, the bar connecting linkage activates the handle
on the valve. This action stops all movement of the feed
rollers. To continue operation you must manually reset
the handle on the valve to the Run position.
1. Test the panic bar assembly daily and whenever new
personnel are assigned to the chipper.
2. After completing all appropriate safety and operational
checks and with no material in the infeed chute, pull
or push the feed bar to activate the feed roller in the
forward or reverse direction. Visually verify the rota-
tion of the feed roller.
3. Push down on bar A or move bar B.
4. Feed roller movement must stop.
5. If feed rollers do not stop, repair as necessary prior
to operating the chipper.
Chip Curtain
The kickback curtain (refer to Figure 3.3) stops or deects
chips and small debris from leaving the infeed chute
area. This also helps in decreasing the amount of clean
up around the chipper.
Run Stop
Valve
Bar Linkage
A
B

Section 3 — Safety • 7
Figure 3.3 — Chip Curtain
Warning
Death or serious injury can result from ying objects.
The chip curtain must be properly installed and in
good condition. Wear appropriate safety equipment.
Inspect chip curtain for damage or missing segments.
Replace the chip curtain if damaged.
Rotational Indicator
The rotational indicator (refer to Figure 3.4) is located on
the belt guard. Movement of the bolt head seen through
this guard indicates movement of the drum and drive
components.
Figure 3.4 — Rotational Indicator
Warning
Death, serious injury, or property damage can result
when attempting to access moving components.
Make sure components have come to a complete
stop before performing inspection or maintenance.
Inspect visibility of the rotational indicator. Make sure no
debris is blocking view.
Drum Blade Change Pin
Complete LOTO procedures prior to performing mainte-
nance on the blades.
A pin (refer to Figure 3.5) is used to lock drum while
performing blade maintenance. After the drum hood has
been opened, rotate the pin, and slide it into the slot.
Engage the pin directly in front of the drum blade. Rotate
drum 180 degrees, lock to perform maintenance on the
second blade. Prior to closing the drum access hood, lift
and rotate the pin back to the start position.
Figure 3.5 — Drum Blade Change Pin
Warning
Death or serious injury can result while performing
blade maintenance. Wear appropriate safety equip-
ment.
Wear cut resistant gloves when performing blade main-
tenance or inspection.
Guards
The chipper is equipped with safety guards (refer to Figure
3.6) to protect you from injury. Do not start or operate the
chipper with these guards removed. Inspect all guards
to make sure they are in place, in good condition, and
properly secured. Never attempt to install a guard or close
the drum hood while the chipper is running. Make any
necessary repairs prior to starting the chipper.

8 • Section 3 — Safety
Figure 3.6 — Guards
Warning
Death, serious injury, or property damage can result
from starting or operating the chipper without the
guards in place. Make sure all guards are in place
before operating the chipper.
Feed Roll Lock Pin
The feed roll lock pin (refer to Figure 3.7) holds the feed
roll in the raised position to assist operators in clearing
infeed material clogs. Make sure pin is in good condition
and tethered to the chipper. Make sure the lift cylinder
operating system is operating properly.
Figure 3.7 — Feed Roll Lock Pin
1. Disengage clutch and wait for all drum movement to
stop.
2. With the lift cylinder controls, fully raise the feed roll.
Hold while inserting pin.
3. Feed the pin though the feed roll box and feed roll
assembly. Make sure the pin goes completely through
both feed roll assembly and box uprights.
4. Using the lift cylinder control, slowly lower the feed
roll. Do not apply down pressure.
5. Perform LOTO procedures.
6. Slowly lower the feed roller.
Warning
Death or serious injury can result if the upper feed
roller is not returned to the proper position. Do not
feed material into the chipper with the upper feed
roller in the locked open position.
Caution
Injury can result from being pinched or trapped be-
tween moving components. Keep hands clear.
Safety Tow Chains
Tow chains (refer to Figure 3.8) are to be utilized every
time a chipper is transported. Chains must be routed
under the trailer tongue in an X pattern between the tow
vehicle and trailer.
Figure 3.8 — Chain Routing
Slack in the chain should be adjusted by installing the
hook in the proper chain link to permit turning but not
dragging on the ground. Inspect chain, clevis, and hook
for damage or excessive wear.
Breakaway Switch
In the event of an unwanted separation of the chipper from
the tow vehicle, the tongue should drop into the cradle
formed by the X pattern of the chains. The breakaway
cable must pull the plunger from the switch before the
entire tongue weight of the chipper comes to rest in the
chain cradle.
When the breakaway switch is activated full voltage
from the chipper battery is applied to the brakes. The
chipper will come to a complete stop, but will not lock
up the wheels.
Pin

Section 3 — Safety • 9
Testing of the breakaway can be accomplished by jack-
ing up the chipper, spinning the wheel and pulling the
plunger. The brakes should apply. This test only ensures
the basic braking circuit is properly functioning. For com-
plete testing and tow vehicle controller set-up, refer to
the chipper brake section in this manual.
Notice
The breakaway switch is to be used for emergencies
only. The breakaway system rapidly discharges the
battery when the plunger pin is removed. Reinstall
plunger immediately after completion of test.
Disclaimer of Liability
Altec Environmental Products, LLC will not be liable for
unauthorized alterations or modications of the unit.
Altec Environmental Products, LLC will not be liable for
improper or abusive operation of the unit.
Do not alter or modify this unit in any way that might affect
its structural integrity, dielectric integrity, or operational
characteristics without specic written approval from Altec
Environmental Products, LLC.
Unauthorized alterations or modications will void the
warranty. However, of a greater concern is the possibility
that unauthorized changes could adversely affect the unit’s
operation that could endanger personnel and/or damage
property. Altec will not be responsible for unauthorized
alterations or modications that cause death, serious
injury, and/or property damage.
Altec Environmental Products, LLC assumes no liability
for any personal injury and/or property damage related
to the use of this manual when performing testing, op-
erating, maintenance and/or repair procedures on this
Altec unit.
Accident Prevention Signs
This unit was equipped with accident prevention signs
at the time of manufacture. If any of these are lost or
become illegible, obtain replacements from your Altec
representative.
The location, part numbers, and descriptions of all
placards are listed in the Parts Manual. Refer to the Ac-
cident Prevention Signs and Diagram for examples of
the placards and their locations.

10 • Section 3 — Safety
Accident Prevention Signs Diagram
26
Both
Sides
A
A
B
B
C
C
21
8
7
30
20
28
4
1
12
2
18
30
1
21
31
4
Both
Sides
7

Section 3 — Safety • 11
Section A - A Section B - B
Section C - C Front View
96
29
14 15
24
16
13
8 27 11
25
Per Engine
or

12 • Section 3 — Safety
Rear View
Top View
Bottom View
12
5
22
19
102310
17
30
20
3 2
30

Section 3 — Safety • 13
4
8
7
2
3
970116658
1
6
5

14 • Section 3 — Safety
970116649
970116652 12
14
13
10
11
9

Section 3 — Safety • 15
•
•
•
•
•
•
•
970116654
WARNING
ALL DECALS AND PLACARDS
SHALL BE PROPERLY POSITIONED
ON THE EQUIPMENT, COMPLETELY
LEGIBLE AND UNDERSTOOD BY
ALL OPERATIONAL AND
MECHANICAL PERSONNEL PRIOR
TO OPERATION OR MAINTENANCE
OF THIS EQUIPMENT. FAILURE TO
ENSURE THIS COULD RESULT IN
EQUIPMENT DAMAGE, SERIOUS
INJURY OR DEATH.
TO OBTAIN DECAL & PLACARD
PLACEMENT GUIDES OR
REPLACEMENT DECALS &
PLACARDS, CONTACT ALTEC AT:
1-877-I FLY ALTEC
1-877-435-9258
OR ONLINE AT:
http://www.Altec.com
DO NOT REMOVE THIS TAG
970122659
21
20
16
15
18
19
17
Table of contents
Popular Chipper manuals by other brands
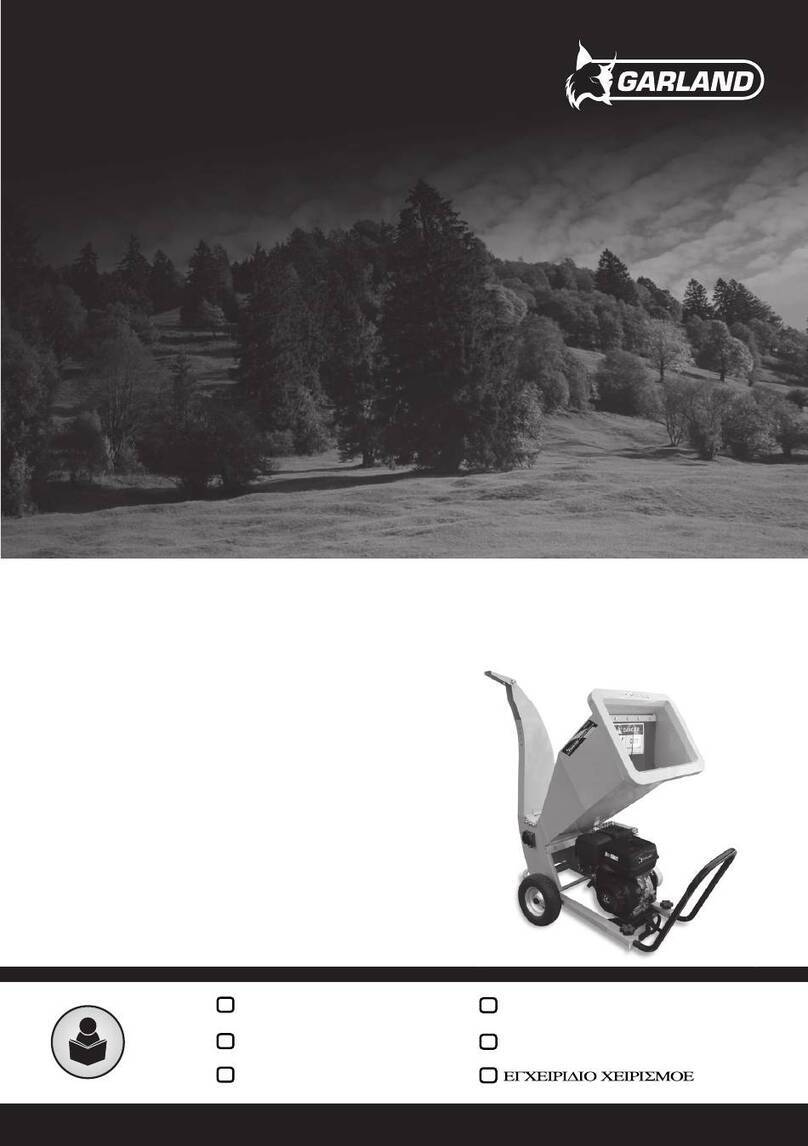
Garland
Garland 1280 QG instruction manual
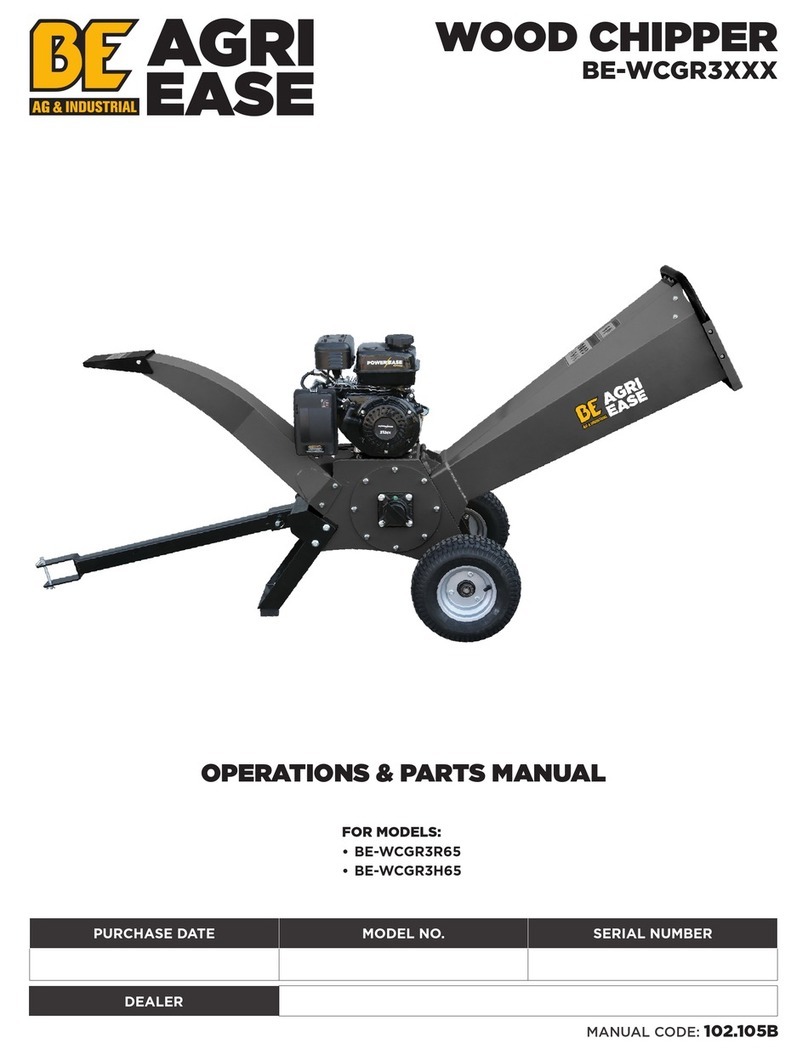
AGRI EASE
AGRI EASE BE-WCGR3 Series Operations & parts manual
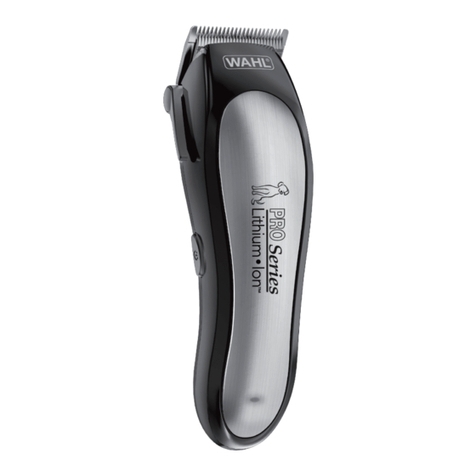
Wahl
Wahl 9766 Product guide
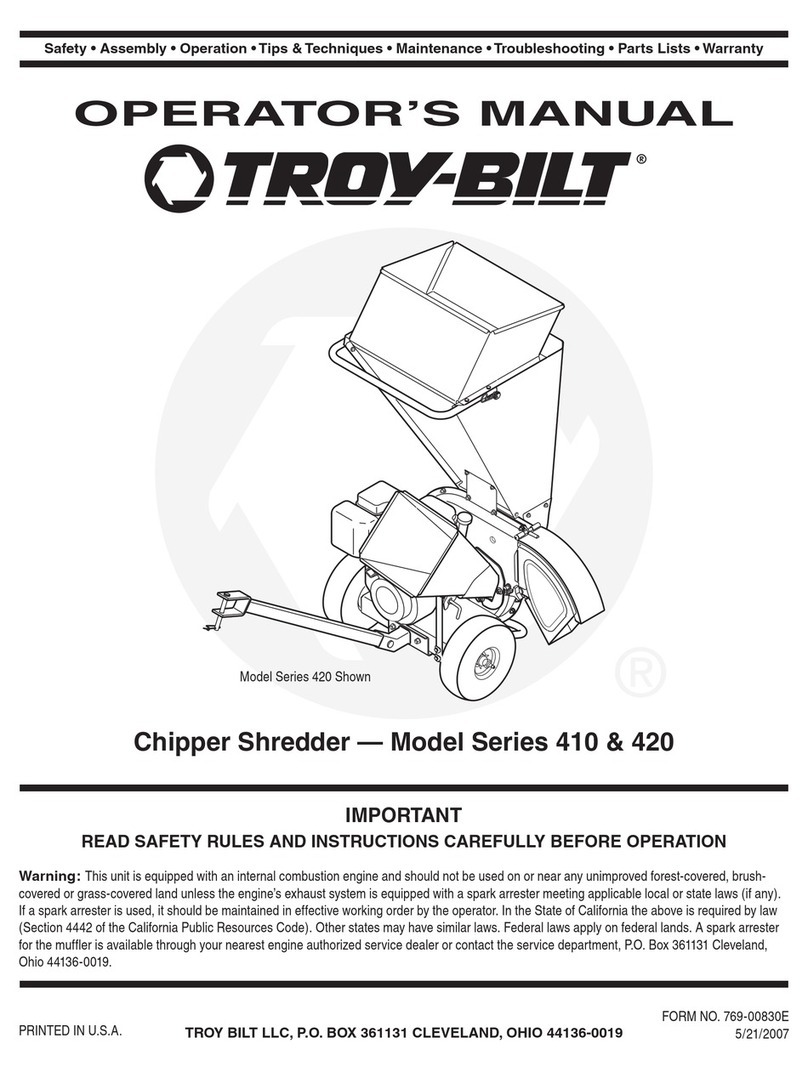
Troy-Bilt
Troy-Bilt 410 Series Operator's manual

Farmi Forest Corporation
Farmi Forest Corporation VALBY CH 140 OPERATION, MAINTENANCE AND SPARE PARTS MANUAL
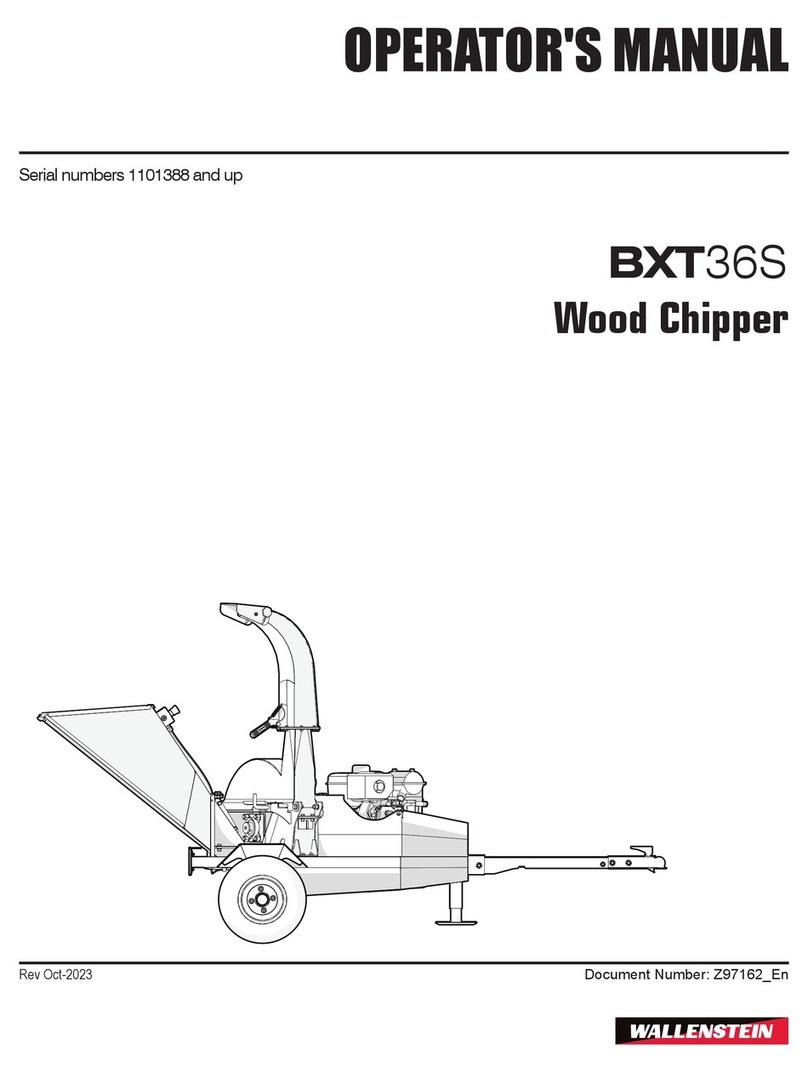
Wallenstein
Wallenstein BXT36S Operator's manual
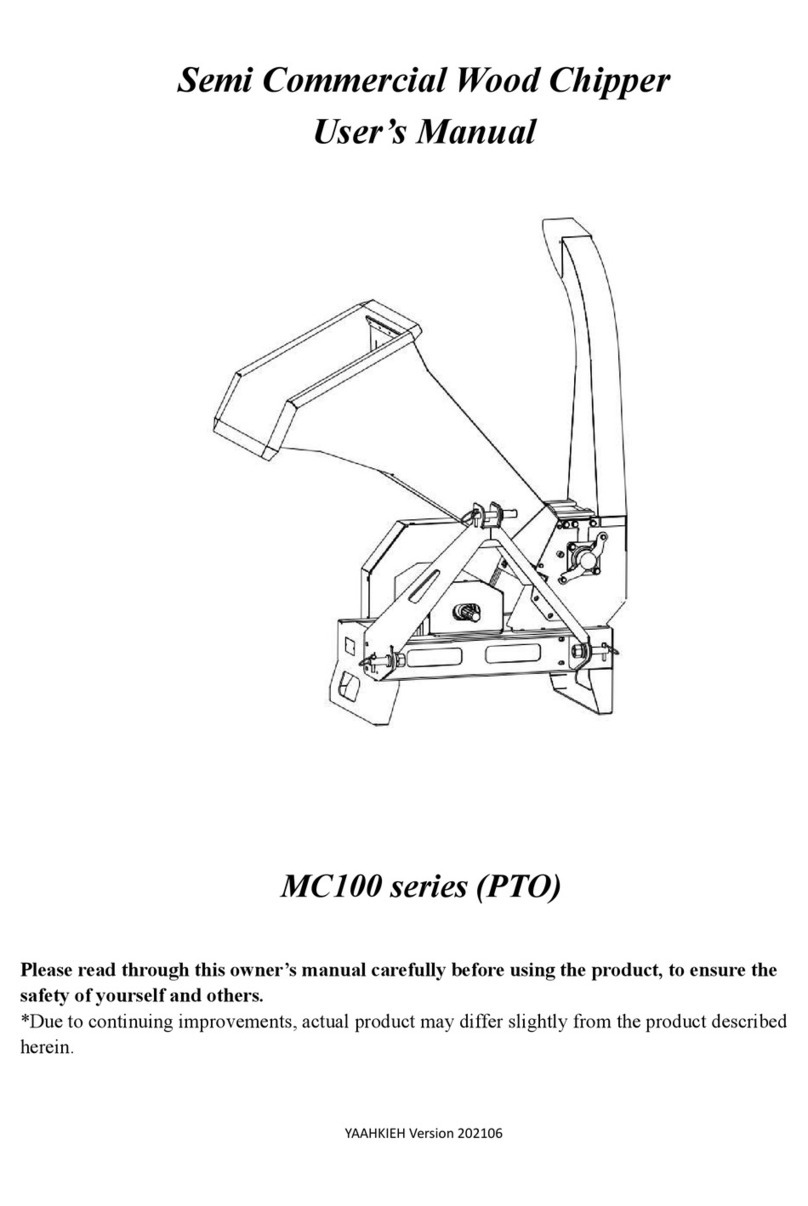
YAAHKIEH
YAAHKIEH PTO MC100 Series user manual

Salsco
Salsco 818 Operator's & parts manual

Country Home Products
Country Home Products C163-CHP Operating and assembly instruction
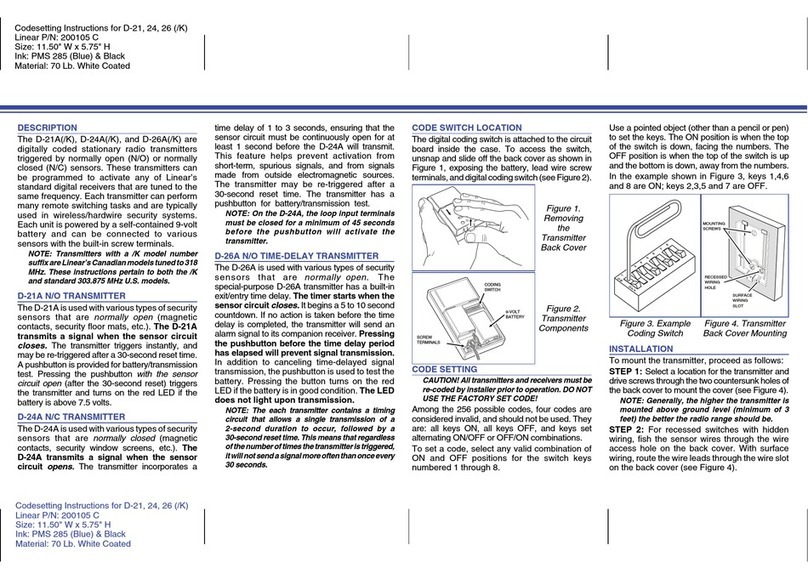
Linear
Linear D-21A(/K) user manual

Champion
Champion 91050 Owner's Manual and Operating Instructions

Garland
Garland CHIPPER 1190 TQG instruction manual