Amberg Technologies Fidelity User manual

Amberg Fidelity
Fidelity
User guide
18/05/2021 (Application version 1.9.0.2)
© Amberg Technologies AG, 2021
Art.No. 10760
Amberg Technologies AG
Trockenloostrasse 21
8105 Regensdorf
Switzerland
Phone: +41 44 870 92 22
Mail: [email protected]
http://www.amberg.ch/at


User guide
© Amberg Technologies AG, 2021 Page 3 of 82
Table of Contents
Introduction ................................................................................................................................. 5
1 Use of manual ................................................................................................................. 5
2 Product description ......................................................................................................... 5
3 Software licence agreement ........................................................................................... 5
4 Installation ........................................................................................................................ 5
5 Licence ............................................................................................................................ 5
1 Program principles .................................................................................................................. 7
1.1 Screen description ....................................................................................................... 7
1.2 Navigation ..................................................................................................................... 7
1.3 Data handling ............................................................................................................... 8
1.4 License concept ........................................................................................................... 8
2 Sensorboard content ............................................................................................................... 9
2.1 Page: Trolley setup ...................................................................................................... 9
2.2 Page: Configuration ..................................................................................................... 11
3 Overview - Available functions ............................................................................................... 17
3.1 Button bar ..................................................................................................................... 17
3.2 Additional menu functions ............................................................................................ 19
3.2.1 Trolley ................................................................................................................ 19
3.2.2 Sites ................................................................................................................... 19
3.2.3 Inspections ......................................................................................................... 19
3.2.4 Devices .............................................................................................................. 20
3.2.5 Dump files ......................................................................................................... 20
3.2.6 Options .............................................................................................................. 20
4 Program settings ..................................................................................................................... 23
5 Sensor Check page ................................................................................................................ 25
6 Company and Operator management .................................................................................... 27
6.1 Companies .................................................................................................................... 27
6.2 Operators ...................................................................................................................... 28
7 Inspection devices ................................................................................................................... 29
8 Inspection site setup ............................................................................................................... 31
8.1 General ......................................................................................................................... 31
8.2 Hardware Setup ........................................................................................................... 32
8.2.1 Total station setup ............................................................................................ 32
8.3 Create a new Sitemap ................................................................................................. 32
9 Inspection procedures Trolley ................................................................................................. 37
9.1 Geometrical Inspection ................................................................................................ 37
9.1.1 End User ........................................................................................................... 37
9.1.2 Power user and higher license ......................................................................... 41
9.2 Wheel Wear Inspection ................................................................................................ 41
9.3 Gauge Adjustment ....................................................................................................... 43
9.3.1 Gauge Adjustment on Track ............................................................................. 44
9.3.2 Gauge Adjustment on Gauging Frame ............................................................ 45
9.4 Cant Sensor Inspection ............................................................................................... 46
9.5 Odometer Inspection .................................................................................................... 49
10 Inspection/verification procedures profiling devices ............................................................. 51
10.1 Vertical Angle Adjustment (GRPwin) ......................................................................... 51
11 Device Angle Inspection ....................................................................................................... 53
11.1 GRP 3000 ................................................................................................................... 55
11.2 IMS 3000 .................................................................................................................... 55
11.3 IMS 1000 .................................................................................................................... 55

User guide User guide
Page 4 of 82 © Amberg Technologies AG, 2021
12 Sensor Angle Verification ..................................................................................................... 57
12.1 GRP 3000 ................................................................................................................... 58
12.2 GRP TSC ................................................................................................................... 59
12.3 IMS 3000 .................................................................................................................... 59
12.4 IMS 1000 .................................................................................................................... 59
13 Horizontal Angle Verification ................................................................................................. 61
14 Certificates / Reports ............................................................................................................. 65
14.1 Parameter Test Report .............................................................................................. 65
14.2 Test and Adjustment Report ...................................................................................... 66
15 References ............................................................................................................................ 67
15.1 Licensing ..................................................................................................................... 67
15.2 Coordinate system of trolley ...................................................................................... 68
15.2.1 Coordinate system of GRP 1000 ................................................................... 68
15.2.2 Coordinate system of GRP 1000 using GNSS .............................................. 69
15.2.3 Coordinate system of GRP 3000 ................................................................... 70
15.2.4 Coordinate system of GRP 3000 using GNSS .............................................. 71
15.2.5 Coordinate system of GRP 5000 and ELISE ................................................. 72
15.2.6 Coordinate system of GRP 5000 using GNSS .............................................. 73
15.2.7 Coordinate system of GRP TSC .................................................................... 74
15.2.8 Coordinate system of IMS 1000 ..................................................................... 75
15.2.9 Coordinate system of IMS 3000 ..................................................................... 76
15.2.10 Coordinate system of IMS 5000 ................................................................... 77
15.2.11 Origin (Y) through Profiler ............................................................................ 78
15.3 Calculation of gauge width ........................................................................................ 80
15.4 Calculation of odometer value ................................................................................... 80

User guide
© Amberg Technologies AG, 2021 Page 5 of 82
Introduction
Congratulations on your purchase of the Amberg Fidelity. Amberg Fidelity is an additional tool
for GRP System FX and will considerably increase productivity.
1 Use of manual
Use this manual as a reference book. You will find information about the functions in Amberg
Fidelity.
2 Product description
Amberg Fidelity is a tool to measure the geometry of the GRP Sytem FX and to adjust the
trolley sensors. The goal is to assure the quality during the whole time of track surveying. There
are eleven system configurations which can be checked:
■GRP 1000
■GRP 3000
■GRP 5000
■GRP 1000 GNSS
■GRP 3000 GNSS
■GRP 5000 GNSS
■GRP TSC
■IMS 1000 (incl. GNSS)
■IMS 3000 (incl. GNSS)
■IMS 5000 (incl. GNSS)
■ELISE
3 Software licence agreement
The full text of the End User Licence Agreement can be read in the "About"-dialogue of Amberg
Fidelity and it is delivered as a hard copy with the system.
4 Installation
To run Amberg Fidelity the following minimal system requirements are necessary:
■Windows 7/10, 1GHz Processor, 1GB MB Ram, 60MB free HD space
5 Licence
The license for Amberg Fidelity software is stored on the dongle shipped with the software.
When using Amberg Fidelity without dongle some program options are not available.
If you purchase an additional licence or you have some problems with your dongle
Amberg Technologies AG will send you a new key for your dongle. Please send your
request to <[email protected]>.

Page 6 of 82

User guide
© Amberg Technologies AG, 2021 Page 7 of 82
Chapter 1 Program principles
1.1 Screen description
The user interface of Amberg Fidelity is divided in four main parts:
■Menu bar
The menu bar contains all available functions for using Amberg Fidelity.
■Tool bar
The most important functions can be directly accessed through the tool bar.
■Program tree
The program tree area contains access to all information about the inspections and the trol-
leys.
■Working area
The working area allows user input and displays results. Depending on the active inspection
wizard or database this area shows appropriate information.
1.2 Navigation
Use the program tree to navigate the different sections of the program:
■Trolley sensorbox
A trolley sensorbox contains the geometric parameters for all configurations stored on the
trolley, up to 14 and the licence for GRP 1000/3000/5000, IMS 1000/3000/5000. When con-
necting a trolley all available trolley configurations are stored in the database of Amberg Fi-
delity. If a trolley was already connected at an earlier date to this database the configurations
in the database will be updated.
■Inspection database
The inspection database contains all data of all inspections. An overview about the trolleys
and their last inspection is shown, and the type and results of all inspections executed.
■Sites
A site is necessary to determine the geometrical parameters of a trolley. Sites are patterns
for different trolley configurations and gauge widths. Once defined for a certain trolley con-
figuration (GRP type and gauge width) a site will be later used to automatically detect the
prisms to measure the geometrical parameters of a trolley.
■Company / Operator
Companies, customer and operators can be managed in a separate database of Amberg
Fidelity. This data is used for the report generation.
■Inspection devices
All total stations and gauging frame used for geometrical inspections are listed in this section.
You can enter the last inspection certificate information.
■Dumps
Dump file can be loaded and listed.

Program principles User guide
Page 8 of 82 © Amberg Technologies AG, 2021
1.3 Data handling
Data flow
After you executed all necessary inspections, Amberg Fidelity calculates the corrections and
the new parameters. The sensor parameters are stored onto the sensorbox of the trolley and
the reports can be generated.
1.4 License concept
Amberg Fidelity supports in general four different licenses:
■End user license. There is no dongle needed. Most of the functionality in Amberg Fidelity
is accessible to an End user. Geometrical inspection results can be compared with the ge-
ometrical values on the sensorboard, but the new results can't be stored.
■Power user license. A dongle with the Power user license is needed. Most obvious differ-
ence to an End user license is that the Power user can store geometrical inspection results
on the sensorboard.
■ASC (Authorized Service Center) license. A dongle with the ASC license is needed. An ASC
license allows for example to create an Inspection Certificate ASC.For further information
please refer to Amberg Fidelity Manual Extended functionalities for ASC.
■Expert license. For Amberg Technologies only.
A detailed list of the first 2 licenses can be found here: Section 15.1, “Licensing” on page 67.

User guide
© Amberg Technologies AG, 2021 Page 9 of 82
Chapter 2 Sensorboard content
When Amberg Fidelity is started a connection to the trolley can be achieved by selecting Trolley
Sensorbox, first button in button bar.
When the trolley is connected, the program tree shows in the node Trolley Sensorbox the
content of the connected sensorboard. In case a connection failed, check the settings of the
COM ports in Program Settings Chapter 4, Program settings on page 23.
2.1 Page: Trolley setup
Trolley sensorboard contains one Trolley Setup page. The content of this page applies to all
available configurations.
General settings
License Amberg Rail Here the operator can enter the license code that the trolley
can be used with Amberg Rail. This field is editable when
pressing the Edit button at the bottom.
License GRPWin Here the operator can enter the license code that the trol-
ley can be used with GRPwin. This field is editable when
pressing the Edit button at the bottom.
Axis distance between wheels
of two-wheel-part
Distance between the two wheels on the two-wheel-part. It
can differ between 0.75 and 1.1 m due to the chosen two-
wheel-part. This field is not editable without Power user li-
cense.

Sensorboard content User guide
Page 10 of 82 © Amberg Technologies AG, 2021
Sensors
Gauge resolution Shows the number of increments per meter. Default value is 630000
incs/m (older sensorboard firmware version 5 & 6 show a lower reso-
lution of 315000 inc/m). This field is not editable without Power user
license. Find out more about the gauge inspection here: Section 9.3,
“Gauge Adjustment” on page 43.
Odometer Shows the number of increments per meter. Default value for new
wheels is 190.986 incs/m. This field is not editable without Power us-
er license. The value can be adjusted via a new odometer inspec-
tion. Find out more about the odometer inspection here: Section 9.5,
“Odometer Inspection” on page 49.
Cant Const S1/S2 Results from the cant sensor adjustment in both faces and constant
value. The cant adjustment is carried out every time before measuring
with a GRP System FX. This field is not editable. The adjustment can
be done in Amberg Rail or GRPwin as well. Find out more about cant
adjustment here: Section 9.4, “Cant Sensor Inspection” on page 46.
Wheel Wear Off
Wheel Wear Off This part shows the stored values for the wheel wear. It can be opened
and closed by the small +/- button. The value can be adjusted via a new
wheel wear inspection. Find out more about the wheel wear inspection
here: Section 9.2, “Wheel Wear Inspection” on page 41

User guide Sensorboard content
© Amberg Technologies AG, 2021 Page 11 of 82
2.2 Page: Configuration
When double clicking a configuration the geometrical values and corrections for one specific
hardware configuration is displayed.
Config Name Displays the name of the actual configuration. This field can
be edited with a Power user license or higher after pressing
the Edit button at the bottom of the page.
Default naming convention is system type with the 11 pos-
sible configurations and used gauge at the beginning of the
name.
Assembled: Displays the assembled configuration type
with all important parameters by clicking on it.
Position Reference Pos. Info: Description where the prism was during the ge-
ometrical inspection. This field can be empty. This field can
be edited by a Power user license or higher after pressing
the Edit button at the bottom of the page.
The six fields describe the geometrical parameters of a trol-
ley by prism or IMU (coordinates of prism from internal ori-
gin or IMU origin). The three fields below Whell Wear Off
are the results of the Geometrical Inspection Results with
the wheel wear values applied. These fields can't be edited.
Only the original values of Original can be changed. The
geometrical values from this part are used in Amberg Rail
or GRPwin. This field can be edited by a Power user license
or higher after pressing the Edit button at the bottom of the
page.

Sensorboard content User guide
Page 12 of 82 © Amberg Technologies AG, 2021
Changing a value here will have a direct impact on
the accuracy of a measurement. Only experienced
users should change values. After changing a value
the button Save at the button has to be pressed.
You can find more information about the coordinate system
of a GRP System FX here: Section 15.2, “Coordinate sys-
tem of trolley” on page 68
Geometry Measurement De-
vice
The six fields describe the geometrical parameters of a de-
vice (coordinates from rotation center of profiling device
from internal origin). The three fields below Wheel Wear
Off are the results of the Geometrical Inspection Results
with the wheel wear values applied. These fields can't be
edited. Only the original values of Original can be changed.
The geometrical values from this part are used in Amberg
Rail or GRPwin.
Changing a value here will have a direct impact on
the accuracy of a measurement. Only experienced
users should change values. After changing a value
the button Save at the button has to be pressed.
You can find more information about the coordinate system
of a GRP System FX here: Section 15.2, “Coordinate sys-
tem of trolley” on page 68
Geometry GNSS The six fields describe the geometrical parameters of a
GNSS device (coordinates from device center from inter-
nal origin). The three fields below Wheel Wear Off are the
results of the Geometrical Inspection Results with the
wheel wear values applied. These fields can't be edited.
Only the original values of Original can be changed. The
geometrical values from this part are used in Amberg Rail
or GRPwin.

User guide Sensorboard content
© Amberg Technologies AG, 2021 Page 13 of 82
Changing a value here will have a direct impact on
the accuracy of a measurement. Only experienced
users should change values. After changing a value
the button Save at the button has to be pressed.
You can find more information about the coordinate system
of a GRP System FX here: Section 15.2, “Coordinate sys-
tem of trolley” on page 68
Gauge The gauge part handles everything that concerns the
gauge. The gauge parameters can be opened and closed
by clicking on the small +/- button and edited by a Power
user license or higher after pressing the Edit button at the
bottom of the page.
■Gauge Type Text. Just a text describing the Gauge
Type.
■Gauge Type. Adjustments which will be applied to sev-
eral configurations (e.g. Gauge Adjustment) will use the
Gauge Type to determine whether a configuration is af-
fected by a change.
■Nominal gauge.
■Reference Gauge. Gauge width that has been used
during the gauge adjustment (e.g. when using a gauge
frame). Each gauge frame does have a slightly different
gauge which is stated in a document when purchasing a
gauge frame.
■Sensor Raw Value. Gauge sensor increments that have
been read out during the adjustment.
■Sensor Origin Position. Result of [Reference Gauge] -
[Sensor raw value / Gauge sensor increments from Trol-
ley setup]. During the measurement the measured incre-

Sensorboard content User guide
Page 14 of 82 © Amberg Technologies AG, 2021
ments will be divided by the Gauge sensor increments
and then added to the value from Gauge Origin Position
in order to get the measured gauge.
Measurement Device The measurement device part handles everything that con-
cerns the profiling device that belongs to this configuration.
The parameters can be opened and closed by clicking on
the small +/- button and edited with a power user license
or higher after pressing the Edit button at the bottom of the
page.
■Type. Could be:
■None (GRP 1000)
■Profiler 110/120 FX (P110/120 FX)
■TPS12000/15/16/30, *S50/60
■Amberg Profiler (5002, 5003, 5033, 6012), Leica Profil-
er (Leica HDS6000, Leica HDS7000) and Z+F Imager
5016
■Serial No. Serial number of the profiling device.
■V-Angle I. Vertical angle correction [RAD].
■Longitudinal tilt. Correction for longitudinal tilt (e.g.
when using a base plate for a scanner which inclines the
scanner by 3°).
■Horizontal tilt. Correction for horizontal tilt.
IMU The IMU part handles everything that concerns the IMU
unit. The parameters can be opened and closed by clicking
on the small +/- button and edited with a power user license
or higher after pressing the Edit button at the bottom of the
page in case an IMS configuration is given.
■Type. Could be:
■None (GRP)
■AMU 1030
■AMU 1010_2010
■AMU 2020_2030
■Serial No. Serial number of the IMU.
■pitch. angle correction [RAD] for pitch angle
■roll. angle correction [RAD] for roll angle
■yaw. angle correction [RAD] for yaw angle
Odometer The Odometer part handles everything that concerns the
Odometer position. The parameters can be opened and
closed by clicking on the small +/- button and edited with a
power user license or higher after pressing the Edit button
at the bottom of the page in case an IMS configuration is
given.
■Xodo. X value for odometer [m] (related to gauge width)
■Yodo. Y value for odometer [m] (constant offset)
■Zodo. Z value for odometer [m] (zero)

User guide Sensorboard content
© Amberg Technologies AG, 2021 Page 15 of 82

Page 16 of 82

User guide
© Amberg Technologies AG, 2021 Page 17 of 82
Chapter 3 Overview - Available
functions
This chapter gives an overview of the possible functions and provide a quick access to more
information about a certain topic.
3.1 Button bar
Open Trolley Sensorbox
In order to carry out inspections, checks or verifications a connection to the trolley
has to be opened. The function can be started as well via Trolley\Trolley Sen-
sorbox.
Close Trolley Sensorbox
The connection to the sensorbox is closed with this button. The function can only
be started, when Open Trolley Sensorbox was started before. When closing Am-
berg Fidelity the connection is aborted automatically.
Geometrical Inspection
Starts the geometrical inspection wizard. To be able to do a geometrical inspection
some information needs to be available already.
■A site is defined. For more information see Chapter 8, Inspection site set-
up on page 31.
■A company and operator is defined. For more information see Chapter 6, Com-
pany and Operator management on page 27.
■A measuring device is defined. For more information see Chapter 7, Inspection
devices on page 29.
The function can be started as well via Inspection\Geometrical Inspection.
Learn more about Geometrical Inspection here: Section 9.1, “Geometrical Inspec-
tion” on page 37.
Wheel Wear Off
The wheel wear can be modelled to improve the measurement accuracy. The
function can be started as well via Inspection\Wheel Wear Off. Learn more about
wheel wear inspection here: Section 9.2, “Wheel Wear Inspection” on page 41.
Gauge Adjustment
The gauge measurement can be adjusted. The function can be started as well
via Inspection\Gauge Adjustment. Learn more about gauge adjustment here:
Section 9.3, “Gauge Adjustment” on page 43.
Cant sensor Adjustment
The cant sensor can be adjusted. This is basically the two-face check of the cant
sensor at the beginning of the measurement. The function can be started as well
via Inspection\Cant Sensor Adjustment. Learn more about cant sensor adjust-
ment here: Section 9.4, “Cant Sensor Inspection” on page 46.

Overview - Available functions User guide
Page 18 of 82 © Amberg Technologies AG, 2021
Odometer Adjustment
The odometer can be adjusted. The function can be started as well via Inspec-
tion\Odometer Inspection. Learn more about odometer adjustment here: Sec-
tion 9.5, “Odometer Inspection” on page 49.
Sensor Check and Initialisation
Allows to access the sensorboard of the trolley.
■The measured values of all sensors can be seen and also be recorded in case
of any problems with a sensor.
■Displays of mode of the trolley (GRP, TSC, GRP_IMU, GRP_DC_IMU)
■Version of firmware installed is displayed. Newer trolleys (Firmware 35.44 and
newer) allow a firmware update via the USB cable. For trolleys with an older
firmware direct access to the sensorboard is required.
■The port connection test requires the GRP Com-Port Test Box to check the
connection between the ports.
Learn more about the Sensor Check and Initialisation page here: Chapter 5, Sen-
sor Check page on page 25.
Vertical Angle Adjustment (GRPWin)
For GRPWin the vertical angle of the Profiler 110 FX can be adjusted. The func-
tion can be started as well via Devices\Profiler 110 FX\Vertical Angle Adjust-
ment (GRPWin). Learn more about Vertical Angle Adjustment (GRPWin) here:
Section 10.1, “Vertical Angle Adjustment (GRPwin)” on page 51.
Device Angle Inspection
Beside Vertical Angle Adjustment (GRPWin) for GRP 3000, vertical angles of IMS
1000/3000 devices (total station and profiler) can be inspected by using a known
reference point with or without known vertical offset. The function can be started
as well via Inspection\Device Angle Inspection. Learn more about Device Angle
Inspection here: Chapter 11, Device Angle Inspection on page 53.
Sensor Angle Verification
Sensor angle adjustment of Device Angle Inspection and Vertical Angle Adjust-
ment (GRPWin) can be verified with this tool, for example for a TSC trolley without
having to set up the whole VMS system. The function can be started as well viaIn-
spection\Verification Tool. Learn more about creating reports here: Chapter 12,
Sensor Angle Verification on page 57.
Create Reports
Creates a report of all inspections done with a trolley. The function can be started
as well via Certificates\Create Report. Learn more about creating reports here:
Chapter 14, Certificates / Reports on page 65.
Program Settings
Only accessible as long as no trolley is connected. Allows to set communication
parameters for trolley, profiler and total station. The function can be started as
well via Options\Program Settings. Learn more about the program settings here:
Chapter 4, Program settings on page 23.

User guide Overview - Available functions
© Amberg Technologies AG, 2021 Page 19 of 82
3.2 Additional menu functions
3.2.1 Trolley
Function Description
Trolley Sensorbox Opens the connection to the trolley sensor-
box by using the communication parameters
set in the program options (Chapter 4, Pro-
gram settings on page 23) and closes
the connection to the trolley sensorbox after-
wards.
Show Config Shows the configuration(s) from the list.
Set Hot One configuration needs to be set as hot. It
means that this configuration will be shown
as first suggested configuration when using
the measurement wizard in Amberg Rail.
Clone Config An existing configuration can be cloned and
if necessary its values can be adjusted (only
for power user and higher licenses). Please
note that when cloning a GRP 1000/3000
configuration it can't be used as a GRP 5000
configuration and vice versa.
Remove Config Removes a configuration from the list and
deletes it from the trolley sensorbox.
Sensor Check and Initialisation Opens the Sensor Check and Initialisation
page. Please refer to Chapter 5, Sensor
Check page on page 25.
3.2.2 Sites
Function Description
New Sitemap Allows to create a new Sitemap.Please re-
fer to the respective chapter for more in-
formation: Chapter 8, Inspection site set-
up on page 31.
Delete Sitemap Allows to delete a Sitemap.
3.2.3 Inspections
Function Description
Inspection The functions here are explained in detail in
their respective chapter:
■Geometrical Inspection: Section 9.1, “Ge-
ometrical Inspection” on page 37
■Wheel Wear: Section 9.2, “Wheel Wear In-
spection” on page 41

Overview - Available functions User guide
Page 20 of 82 © Amberg Technologies AG, 2021
Function Description
■Gauge Adjustment: Section 9.3, “Gauge
Adjustment” on page 43
■Cant Sensor Adjustment: Section 9.4,
“Cant Sensor Inspection” on page 46
■Odometer Inspection: Section 9.5,
“Odometer Inspection” on page 49
■Device Angle Inspection: Chapter 11, De-
vice Angle Inspection on page 53
■Sensor Angle Verification: Chapter 12,
Sensor Angle Verification on page 57
3.2.4 Devices
Function Description
Profiler 110 FX \ Vertical Angle Adjustment
(GRPwin)
Adjusts the vertical angle of a P110 FX for
GRPwin. Learn more about it here: Sec-
tion 10.1, “Vertical Angle Adjustment (GRP-
win)” on page 51.
3.2.5 Dump files
Function Description
Dump Sensorbox Allows to create a dump file of the sensorbox.
The dump file might be sent to Amberg Tech-
nologies for analysis or created for backup
reasons on customer side after a new inspec-
tion.
Load Sensorbox Dump Dump files can be loaded and saved on the
trolley. Only dump files from same trolley
(same serial number) can be loaded.
View/Edit Dump Allows to view and edit a dump file of the sen-
sorbox in Amberg Fidelity.
Remove Dump Dump file can be removed in Amberg Fideli-
ty.
3.2.6 Options
Function Description
Program Settings Please refer to the respective chapter for
more information: Chapter 4, Program set-
tings on page 23.
Language Allows to change the language of the graph-
ical user interface. Available languages:
■English
■German
■French
Table of contents
Other Amberg Technologies Measuring Instrument manuals
Popular Measuring Instrument manuals by other brands
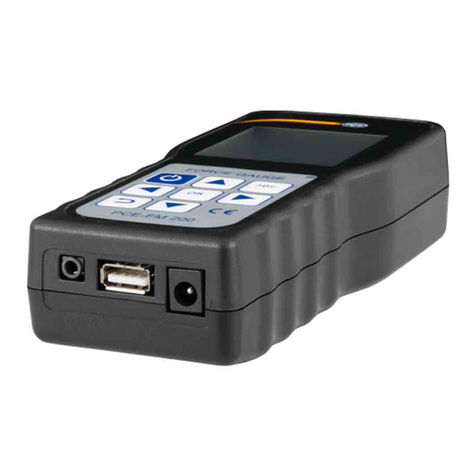
PCE Instruments
PCE Instruments PCE-FM 20 user manual
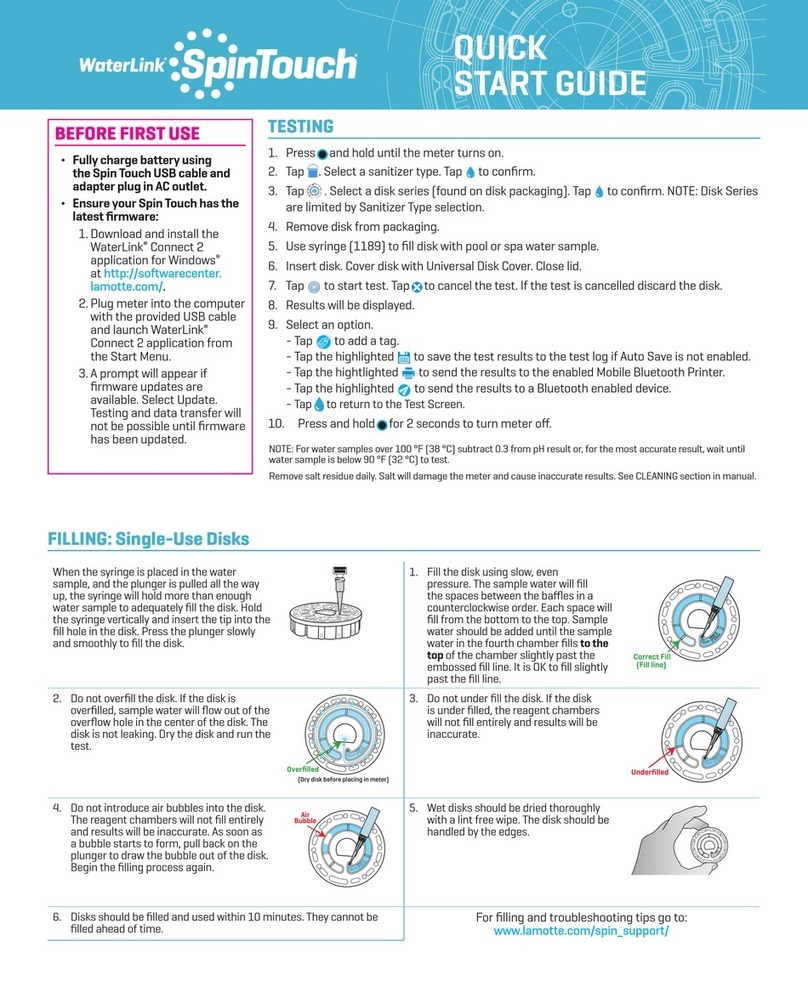
LaMotte
LaMotte WaterLink Spin Touch quick start guide
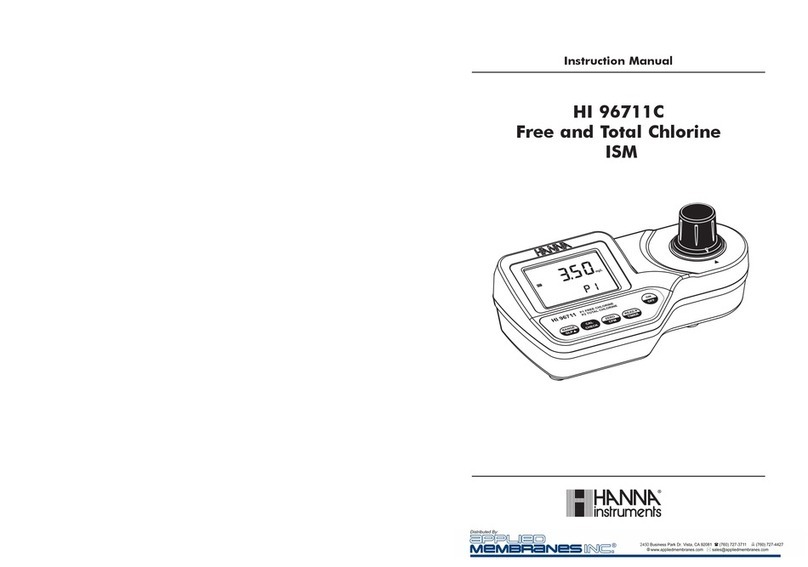
Hanna Instruments
Hanna Instruments 96711C instruction manual

Sartorius
Sartorius MA45 operating instructions

IFM Electronic
IFM Electronic SI5007 operating instructions
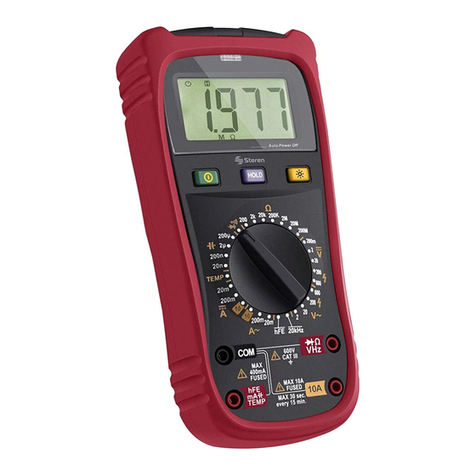
Steren
Steren MUL-288 instruction manual