ANDILOG DRIVETWIST User manual

Instruction manual - 1.1
DRIVETWIST
Page 2
Contents
1. Introduction..................................................................................................................................... 4
1.1. Presentation ............................................................................................................................ 4
1.2. Documentation ........................................................................................................................ 5
1.3. Definitions................................................................................................................................ 5
2. Installation and start-up................................................................................................................... 6
2.1. Product opening ...................................................................................................................... 6
2.2. Recommendations before use................................................................................................. 6
2.3. Booting your system ................................................................................................................ 8
2.4. Operating principle DriveTwist .............................................................................................. 13
3. Travel controls ............................................................................................................................... 14
3.1. Controls ................................................................................................................................. 14
3.2. Travel configuration............................................................................................................... 16
3.3. Start-up configuration rotation.............................................................................................. 18
3.4. High-speed travel................................................................................................................... 19
3.5. Reset position to 0 ................................................................................................................. 19
3.6. Units....................................................................................................................................... 20
3.7. Change language.................................................................................................................... 20
3.8. Drivepack digital inputs.......................................................................................................... 20
3.9. Drivepack's TOR output ......................................................................................................... 20
4. Measuring with DriveTwist ............................................................................................................ 22
4.1. Main measurement screen.................................................................................................... 22
4.2. Measurement screen touch zones ........................................................................................ 24
4.3. Main menu............................................................................................................................. 25
4.4. Zero or Tare ........................................................................................................................... 25
4.5. Backlighting............................................................................................................................ 26
5. Start measuring ............................................................................................................................. 27
5.1. Start a measurement ............................................................................................................. 27
5.2. Status indicator...................................................................................................................... 28
5.3. Curve display area.................................................................................................................. 28
6. Modify my screen display .............................................................................................................. 30
7. Setting a limit or thresholds........................................................................................................... 32
7.1. Activate / Deactivate.............................................................................................................. 32
7.2. Sensor tab.............................................................................................................................. 32
7.3. Choice of limit value .............................................................................................................. 32
7.4. Setting limit values................................................................................................................. 33
7.5. Stop the frame on a torque value .......................................................................................... 33
8. Setting up graphics and tests......................................................................................................... 34
8.1. Test tab .................................................................................................................................. 34
8.2. Configuration of test conditions ............................................................................................ 34
9. Setting up calculations................................................................................................................... 37
9.1. Choice of calculations ............................................................................................................ 37
9.2. Action following a calculation ................................................................................................ 38
10. Storing results and statistics .......................................................................................................... 39
10.1. Statistics configuration .......................................................................................................... 39
10.2. Save values............................................................................................................................. 40
11. Communication with a computer .................................................................................................. 41
11.1. RS232 or Serial link ................................................................................................................ 41
11.2. USB connection...................................................................................................................... 43
11.3. Bluetooth link......................................................................................................................... 44

Instruction manual - 1.1
DRIVETWIST
Page 3
11.1. Analog link ............................................................................................................................. 44
11.2. Data Stick (Option)................................................................................................................. 44
12. Digital and pedal inputs and outputs............................................................................................. 47
12.1. Centor Touch releases ........................................................................................................... 47
12.2. Inputs and pedals................................................................................................................... 48
13. General parameters....................................................................................................................... 49
13.1. Sounds ................................................................................................................................... 49
13.2. Eco mode ............................................................................................................................... 49
13.3. Feed management................................................................................................................. 49
13.4. Screen orientation ................................................................................................................. 49
13.5. Language................................................................................................................................ 49
14. Maintenance.................................................................................................................................. 50
14.1. General .................................................................................................................................. 50
14.2. Clock setting: ......................................................................................................................... 50
14.3. Tracks..................................................................................................................................... 51
14.4. Factory settings...................................................................................................................... 51
15. DriveTwist configuration examples................................................................................................ 52
15.1. Overload protection............................................................................................................... 52
15.2. Open plug + return to start position ...................................................................................... 53
16. Appendices .................................................................................................................................... 58
16.1. Acquisition software .............................................................................................................. 58
16.2. Interface cables...................................................................................................................... 58
16.3. Error messages ...................................................................................................................... 58
16.4. Factory settings...................................................................................................................... 62
16.5. Connections ........................................................................................................................... 64
16.6. Dimensions ............................................................................................................................ 66
Review
Date
Description
Rev 1.1
Nov 2023
Complete revision
Rev 1.0
Sept 2016
Redesigning the document

Instruction manual - 1.1
DRIVETWIST
Page 4
1. Introduction
1.1. Presentation
Thank you for choosing the DriveTwist torsiometer manufactured by ANDILOG Technologies for your
torque measurements.
This system is the result of over 30 years' experience in force and torque measurement. It
incorporates the latest technologies available to offer you unrivalled performance and measurement
quality.
Thanks to a completely redesigned graphical user interface, DriveTwist is intuitive and easy to use. This
user's manual will guide you through the set-up and enable you to obtain your first measurements. It
then goes on to cover the frame's advanced functions, enabling you to perform more complex tests
and automate your results.
Rotating shaft
Torque sensor

Instruction manual - 1.1
DRIVETWIST
Page 5
1.2. Documentation
This manual provides information on:
•System configuration and settings before starting tests
•Instructions for tests and their execution
Please refer to the CALIFORT software user manual for information on how to install and set up
automated tests, and how to use the software. You should have received the operating manual by
email or in Califort press the ? at the top right to open the manual.
1.3. Definitions
To make this manual easier to understand, here are some definitions of terms frequently used in this
manual.
1.3.1. SPIP
SPIP is a technology developed by Andilog that enables our systems to automatically recognize
external sensors. This technology stores capacity, serial number and calibration parameters inside the
sensor.
1.3.2. Calibration
Systems are delivered calibrated by Andilog Technologies with a COFRAC calibration certificate. It is
generally recommended to calibrate force measurement instruments once a year unless a different
internal procedure is used. At each calibration, Andilog Technologies guarantees a complete
verification of the instrument, as well as an adjustment of the calibration to guarantee perfect
accuracy.

Instruction manual - 1.1
DRIVETWIST
Page 6
2. Installation and start-up
Refer to the safety and installation instructions - When opening the
product. Check that the system has not been damaged in transit. If in
doubt, contact Andilog Technologies to obtain further information and
check that your measurement system is working properly.
2.1. Product opening
The DriveTwist system is supplied with:
•Torque transducer with calibration certificate
•A controller
•A torsion test stand
•Power cables and connection cables between components
2.2. Recommendations before use
2.2.1. Sensor
Despite this instrument's overload protection, applying torque over the transducer's
capacity can damage the system. The instrument will lock up if its capacity has been
exceeded 10 times. You will then need to return your transducer to ANDILOG
Technologies to check that it is working properly.
It is important that the measured values are generally less than 90% of the sensor's
capacity. Constant use of the load cell above 90% of its capacity can lead to premature
wear. When the transducer is used on a motorized frame, it is necessary to program a frame stop
when the force approaches the transducer's maximum capacity. This limit must take into account the
fact that, at high speeds, a frame will not stop immediately, and the risk of damage to the transducer
is high due to the motor's inertia.
2.2.2. Precautions during testing
Most of the tests carried out with instruments from the Andilog Technologies range are destructive
tests. The hazards associated with this type of testing require our instruments to be used by
experienced and trained operators. Due to the nature and use of equipment sold by Andilog, the
purchaser's acceptance of Andilog Technologies' products constitutes acceptance of the risks and
damages that may result from the use of Andilog's instruments.

Instruction manual - 1.1
DRIVETWIST
Page 7
2.2.3. Ambient conditions
•Operating temperature: 0 to 35° C
•Storage temperature: -20 to 45° C
•Relative humidity: 5% to 95%, non-condensing
•Maximum operating altitude: 3,000 m
2.2.4. Warranty
Subject to the conditions below, Andilog Technologies warrants to the purchaser that it will repair or
replace at no charge new instruments sold subject to normal use and maintenance. This warranty
applies if the purchaser detects a defect in workmanship or materials within a period of two (2) years
from the date of shipment.
The conditions of application are:
•ANDILOG Technologies has been notified in writing of the defect before the end of the
warranty period.
•Products are shipped to Andilog Technologies with prior agreement from Andilog
Technologies.
•All transport costs are paid by the buyer.
•The products have been used and maintained under normal conditions of use.
Any repair or replacement carried out by the seller without the agreement of Andilog Technologies
voids the warranty.
In no event shall Andilog Technologies be liable for any damages, business interruption, or production
stoppage resulting from the purchase, use, or non-operation of our products. Even if Andilog
Technologies has been informed of the possibility of such damage.
The accuracy of our devices is guaranteed at the time of shipment at the value indicated in our
documentation or offers.
If products are damaged during shipment, notify the carrier and Andilog Technologies immediately.
The warranty is void in the event of accident, misuse or abuse.
The warranty does not cover calibration, overloaded sensors or consumable parts such as batteries,
unless the damage is due to a material or manufacturing defect.

Instruction manual - 1.1
DRIVETWIST
Page 8
2.3. Booting your system
2.3.1. Connect controller to frame
The controller Drivetouch should be placed on a stable, vibration-free table. It must be connected to
the frame and to the computer using the cables supplied and the following connectors:
•Connect the frame to the controller using the round connector.
•Connect the torque sensor's 9-pin connector to the back of the Drivetouch.
•Connect the power chord to the Drivetouch.
•Turn on the Drivetouch
USB connector for data acquisition
Connector to frame
Drivepack connector for Califort
software control
Torque sensor connector
Datastick
I/O connector

Instruction manual - 1.1
DRIVETWIST
Page 9
2.3.2. Mounting the sensor on the frame
Switch on the controller using the switch next to the power cable. If necessary, release the emergency
stop if the controller does not switch on.
Handle the sensor with care and ensure that it cannot be overloaded.
Torques to be measured must act precisely in the axis of the torque transducer. Torsional moments
and eccentric loads may cause measurement errors and destroy the transducer. Tightening torques on
mounting screws need not be very high.
Use the 4 screws supplied to position the sensor on the frame.

Instruction manual - 1.1
DRIVETWIST
Page 10
1/ Position the sensor at the top of
the frame
2/ Loosely tighten the 4 sensor
retaining screws
3/ Press the center of the touch-
sensitive display to tare. Then,
using a hexagonal wrench, gently
tighten the 2 screws, watching the
torque value. Once all 4 screws
have been tightened, the torque
value should remain close to 0Nm.

Instruction manual - 1.1
DRIVETWIST
Page 11
Start
The DriveTwist controller consists of two separate controls:
•DRIVEPACK frame motor control: controls the movement of the motorized column:
displacement, speed, stop...
•CENTOR TOUCH DUAL: measurement of force as a function of displacement.
CENTOR TOUCH DUAL
measurement display
DRIVEPACK frame control
Test start button
Emergency stop

Instruction manual - 1.1
DRIVETWIST
Page 12
Start-up information screen :
Current date: Displayed in Europe: "DD / MM / YYYY" or US: "MM / DD / YYYY" format, can be set in
the Maintenance menu (See chapter " Maintenance ")
Software version: This line indicates the embedded software version installed on the controller.
Internal and external sensor: Indicates the type of sensor connected (force, torque, displacement or
angle) to your test machine and its operating status.
•A red "X" symbol indicates that the sensor is not recognized or has a serious problem. See
chapter Maintenance for more information.
•Red exclamation mark!Indicates a minor warning on the sensor: an overload or an out-of-date
calibration, for example.
Sensor information: At start-up, the CENTOR TOUCH display detects whether internal or external
sensors are connected. External sensors are connected to the CENTOR TOUCH via a special connector,
called SPIP.
Sensor information is displayed in the green rectangle at the center of the screen:
•Channel V1 for internal or V2 for external
•Date of next calibration
•Number of overloads
If the measurement window does not appear: While displaying the low battery indication, CENTOR
TOUCH runs internal tests. If, during these tests, problems are detected, the Autotest icon is displayed
at the bottom left of the screen. See chapter Appendices for the meaning of error messages.
Rotation sensor
Torque sensor
Sensor information
Software version
Today's
date

Instruction manual - 1.1
DRIVETWIST
Page 13
If the error detected makes measurement impossible (major error such as a faulty sensor, for
example), the device will remain stuck on this display and it will be impossible to carry out any other
measurement. In this case, please contact the ANDILOG Technologies team to find out how to return
the device.
If the error detected does not make measurement impossible (minor error such as low battery level or
overload), you can go to the main screen by pressing the Measure button on the bottom right.
2.4. Operating principle DriveTwist
DriveTwist is designed around two independent interfaces: CENTOR TOUCH DUAL (for measurement
acquisition) and DRIVEPACK (for motor commands).
•DRIVEPACK frame control: controls frame rotation: movement, speed, stop...
•CENTOR TOUCH DUAL measurement: force measurement as a function of displacement.
These two systems are configured separately, each with its own control command. However, they
communicate with each other via digital inputs and outputs.
The general operating principle is as follows:
•Drivepack configuration of frame movement: rotation speed, maximum movement, stops,
cycles, actions when frame meets a stop
•Use Centor Touch Dual to configure torque acquisition as a function of rotation, calculations
(breakage, average...) and force limits.
•Configuring Centor Touch Dual outputs so that Drivepack performs specific actions (stop,
return, etc.) at particular times during measurements. The most common configurations are
described in configuration examplesDriveTwist DriveTwist, for example: frame stop on sensor
overflow, stop on limit, return on ring break, etc.
This manual is therefore structured in the same way. First we look at the rotation configuration, then
at the measurement acquisition configuration, and finally at communication between the two
systems. In the final section, detailed examples of common configurations are presented.
NOTE: In addition, the optional CALIFORT control and command software lets you combine these 2
commands to configure and parameter your tests from a PC.

Instruction manual - 1.1
DRIVETWIST
Page 14
3. Travel controls
The motorized two-column test machine is moved using the DRIVEPACK control below. It is used to
adjust the system's behavior during rotation.
3.1. Controls
The control buttons behave differently depending on the mode you're in. There are two modes:
•Normal mode
•Configuration mode
3
4
6
5
8
7
0
1
2

Instruction manual - 1.1
DRIVETWIST
Page 15
3.1.1. Functions in Normal mode
KEY #
NAME
DESCRIPTION
0
Display
Displays real-time information: displacement, speed, error,
etc.
1
MENU button
Access to configuration mode
2
+ button
No function
3
Button -
No function
4
Up button
Clockwise start-up of frame at set speed
5
Down button
Counterclockwise start-up at set speed
6
Rapid ascent button
Clockwise frame start-up at maximum speed
7
Rapid descent button
Counterclockwise start-up at maximum speed
8
Reset button
Reset displacement value
PRESSING ANY CONTROL BUTTON WHILE THE FRAME IS MOVING CAUSES THE MOTOR TO STOP
A LONG PRESS (3 seconds) ON THE ZERO KEY RESETS THE CONSOLE
3.1.2. Functions in configuration mode
KEY #
NAME
DESCRIPTION
1
MENU button
Back to Normal mode
2
+ button
Go to next parameter
3
Button -
Go to previous parameter
4 Up button Increment parameter
5
Down button
Decrements the parameter
6
Rapid ascent button
Increment parameter quickly
7
Rapid descent button
Decrements the parameter quickly
8
Reset button
No function
Note: The rotation value can be set to zero at any time when the motor is stopped. The origin of
displacements is therefore 'relative'.
3.1.3. Emergency stop
The machine is equipped with a mechanically-locked emergency stop button on the front panel. The
emergency stop button stops the machine when the power supply is completely cut off. To restart the
machine, the emergency stop button must be unlocked.

Instruction manual - 1.1
DRIVETWIST
Page 16
Caution: if the machine is stopped by the emergency stop, the displacement value may be incorrect,
so check the displacement value when restarting.
This does not apply when the machine is switched off at the end of operation, via the switch, with the
motor stopped. In this case, the displacement value is stored and displayed when the machine is
switched back on.
3.2. Travel configuration
Drivepack lets you configure clockwise and counterclockwise rotation of the motorized frame.
Rotation settings are separate and have independent parameters. For each direction of movement,
you can configure the following:
•Speed
•Rotation stop
•Stop action
•Travel time
•Action on end of travel time
•Cycles
Navigating menus, changing parameters or modifying a value is always done in the same way,
whatever the parameter:
•To access the configuration menu, press the key.
•Use the + and - keys to move from one menu to another.
•To exit the menu and confirm the configuration, press the key.
•Change parameters or values using the buttons, ,
3.2.1. Menu architecture
•Hourly speed
•Counterclockwise speed
•Hourly travel stop
•Type of stop (fast or precise)
•Counter-clockwise travel stop
•Type of stop (fast or precise)
•Hourly time stop
•Anti-clockwise time stop
•Climbing break
•Downhill break
•Cycles
•Pedal
•Input 1
•Input 2

Instruction manual - 1.1
DRIVETWIST
Page 17
•Output
•Units
•Language
The menu is dynamic, i.e. if one of the stops is inactive, then its setting menu is not proposed by
Drivepack.
3.2.2. Speed settings
The first two menus allow separate clockwise and counterclockwise speed settings. Use the and
keys to increase or decrease speed in steps of 0.01 rpm, and the and keys to increase speed
in steps of 1 rpm. A long press on these keys increases the values more rapidly.
Caution: Frame speed is adjustable. During testing, too high a speed may prevent the sensor
protection system from triggering in time if you exceed the maximum capacity.
3.2.3. Travel stops
A travel stop is a fixed point where the motorized frame's moving center crosspiece will stop during its
travel. The upper travel stop corresponds to a travel limit when the frame is moving upwards, and the
lower travel stop corresponds to a travel limit when the frame is moving downwards.
If several limits are configured in Drivepack, the first limit encountered by the frame will be executed
and the other limits ignored.
Drivepack offers 3 different configurable limits: mechanical, displacement and temporal. For each
limit, 4 actions can be configured for the frame:
•Inactive : the frame does not take into account the limit
•Stop the frame stops when it meets this stop
•Inverter the frame moves in the opposite direction at the set speed
•Inv temp : the frame starts moving again in the opposite direction at the
defined speed after a pause of X seconds defined in the Pause me nu.
Multiple stops can be configured for a single test. It is strongly recommended to use mechanical stops
as safety limit switches to avoid destroying the sample, fixtures or sensor. Consequently, time or
displacement stops are generally used to terminate tests.
Rotational stops: These are defined by displacement in revolutions or degrees. If they are active, an
angle configuration menu appears in Drivepack and can be accessed by pressing the + key once. These
limits can be configured in the "Stop pos " menu for clockwise travel and the "Stop pos "
menu for counter-clockwise travel.
Note: The displacement value set for this limit is relative to frame position 0, which can be reset to 0
at any time using the key. Clockwise displacement is positive, counter-clockwise negative.
Example configuration, if you enter the following parameters in Drivepack:

Instruction manual - 1.1
DRIVETWIST
Page 18
•Speed 2 rpm
•Speed 3 rpm
•Butee pos Arret
•Butee pos 1 tr
•Butee neg Inverseuse
•Butee neg -2 tr
•All other stops are inactive
If you return to Normal mode, there are several possibilities:
•If you press the key to reset the frame movement to 0 and then press the key, the
DriveTwist will move counterclockwise at a speed of 3 rpm. When it reaches -2 revolutions, it
will start moving in the opposite direction at a speed of 2 rpm until it reaches 1 revolution and
then stop.
•If you press the key to reset the frame movement to 0 and then press the key, the
DriveTwist will move clockwise at 2 rpm until it reaches the 1-turn position.
Note: These limits, if activated, ARE NOT taken into account when moving manually at high speed.
Time stops: Time stops are defined by a travel time in seconds. If they are active, a time configuration
menu appears in Drivepack and can be accessed by pressing the + key once. These limits can be
configured in the "Time stop " menu for upward movement and the "Time stop " menu for
downward movement of the frame. Operation is identical to that of the position stops.
Note: These limits, if activated, ARE NOT taken into account when moving manually at high speed.
Pause: If at least one of the above stops is set to "Inv temp", then the "Pause " and "Pause "
menus are available in Drivepack. These menus define the waiting times, in seconds, when the frame
encounters a stop before it starts again in the opposite direction.
Note: The system may appear to be inactive when using the "Pause" function but will start to move
without warning once the function is complete. Do not attempt to adjust accessories or remove
samples until the test is complete.
Cycle: If at least two stops are set to "Inverse" or "Inv temp", then the "Cycle" menu is available in
Drivepack. This menu is used to define the number of times the frame will cycle up/down between
the reversing stops. The number of cycles can be set from 1 to 255.
3.3. Start-up configuration rotation
The DriveTwist can be started in two different ways:
•Press the and keys to start turning the frame.

Instruction manual - 1.1
DRIVETWIST
Page 19
•A long press on the green button on the front of the controller can start the DriveTwist
moving. This button can be configured in a number of different ways, as follows.
Configuring the green Start button on the front of the controller: To configure this button, go to the
Drivepack menu, then to the "Action Pedal" menu. You then have several choices:
•Inactive No action
•Dem neg starts the frame clockwise
•Dem pos starts the frame counter-clockwise
•Stop Stopping the frame in its tracks
•RESET Reset position value to zero (equivalent to )
Once the test has started, the Drivepack display shows :
•Travel speed
•Direction of travel
•Real-time frame position
Example:
In this example, the frame moves clockwise at a speed of 1 rpm and has covered 2.1 revolutions.
To stop the DriveTwist, press any key on the Drivepack control.
Note: If the DriveTwist reaches one of the stops while moving, it will execute the configured action
(Stop, Return...).
3.4. High-speed travel
You can manually move the frame at high speed using the Drivepack command, for example, to
position the frame at the test start point. To do this, use the and keys to move up or down. If the
key is released, the rack stops.
Note: In fast travel mode, the stops are not taken into account by the frame. This mode should only be
used to move to the original position. It must not be used for testing purposes.
3.5. Reset position to 0
To reset the Drivepack position to 0, press the button when the engine is stopped.
1.0 rpm
+ 2.10 tr

Instruction manual - 1.1
DRIVETWIST
Page 20
3.6. Units
This menu allows you to select the unit for displaying speed and displacement. Use the and keys
to toggle between rpm and °/s.
3.7. Change language
The last menu allows you to change the Drivepack language. The languages available are :
•French
•English
•German
•Spanish
3.8. Drivepack digital inputs
The Drivepack motion controller has 2 configurable digital inputs. These two inputs are accessible via
the 15-pin connector on the rear of the controller (see "Appendix" for details of connector input
numbers). They enable the Drivepack to perform actions on command from another device.
For example, they can be used to stop the frame when the controller detects a break or reaches a
limit. For example, it is possible to perform a force threshold stop or a breakage stop.
The different actions possible on the activation of its inputs :
•Inactive no action
•Dem neg starts the frame clockwise
•Dem pos starts the frame counterclockwise
•Stop stops the frame in its tracks
•RESET resets the position value to zero (equivalent to the key)
•Inverter the frame moves in the opposite direction at the set speed
•Inv temp : the frame starts moving again in the opposite direction at the set
speed after a pause of X seconds defined in the Pause menu.
•RS232 The Drivepack sends the information 'TOR input' on its RS232 output to
the Califort software. If you are not using Califort, this action has no effect.
When used with CALIFORT software, the software takes control of the digital inputs.
3.9. Drivepack's TOR output
The Drivepack motion controller features a configurable digital output. This output is accessible via the
15-pin connector on the rear of the controller (see appendix for details of the connector output
number). It is used to inform another device of an event.
The various events that can trigger this output are :
•Inactive Output is disabled
Table of contents
Other ANDILOG Test Equipment manuals
Popular Test Equipment manuals by other brands
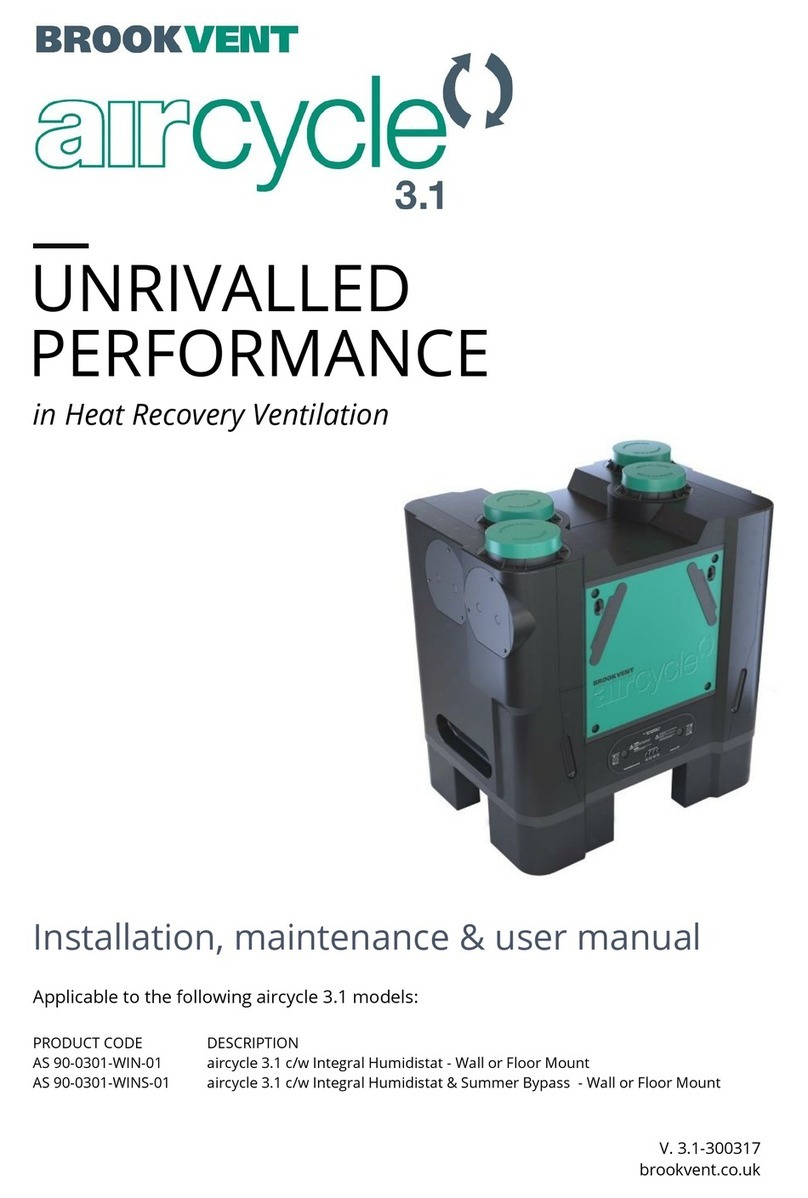
BrookVent
BrookVent Aircycle 3.1 Installation, maintenance & user manual
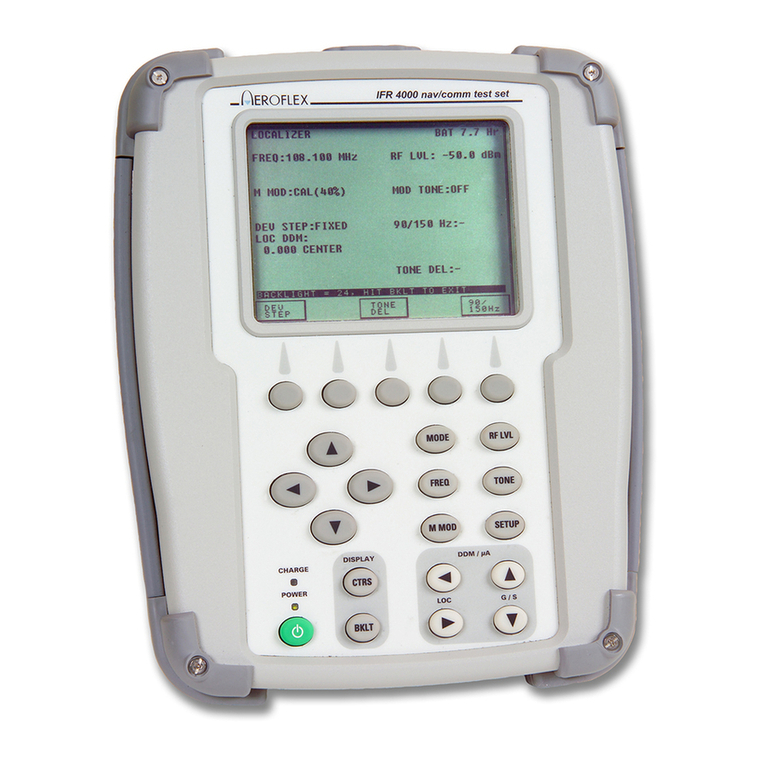
Aeroflex
Aeroflex IFR 4000 Getting started manual

Dräger
Dräger Alcotest 6820 quick start guide
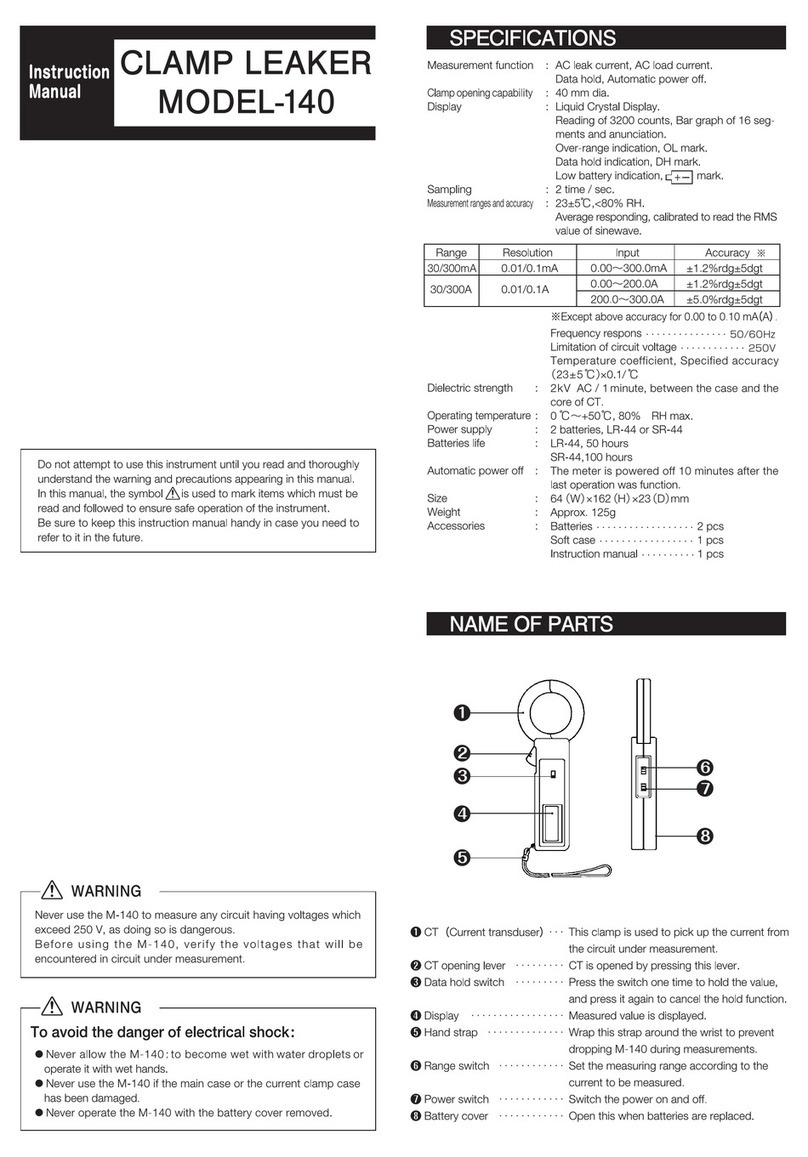
MULTI MEASURING INSTRUMENTS CO.,LTD.
MULTI MEASURING INSTRUMENTS CO.,LTD. M-140 instruction manual
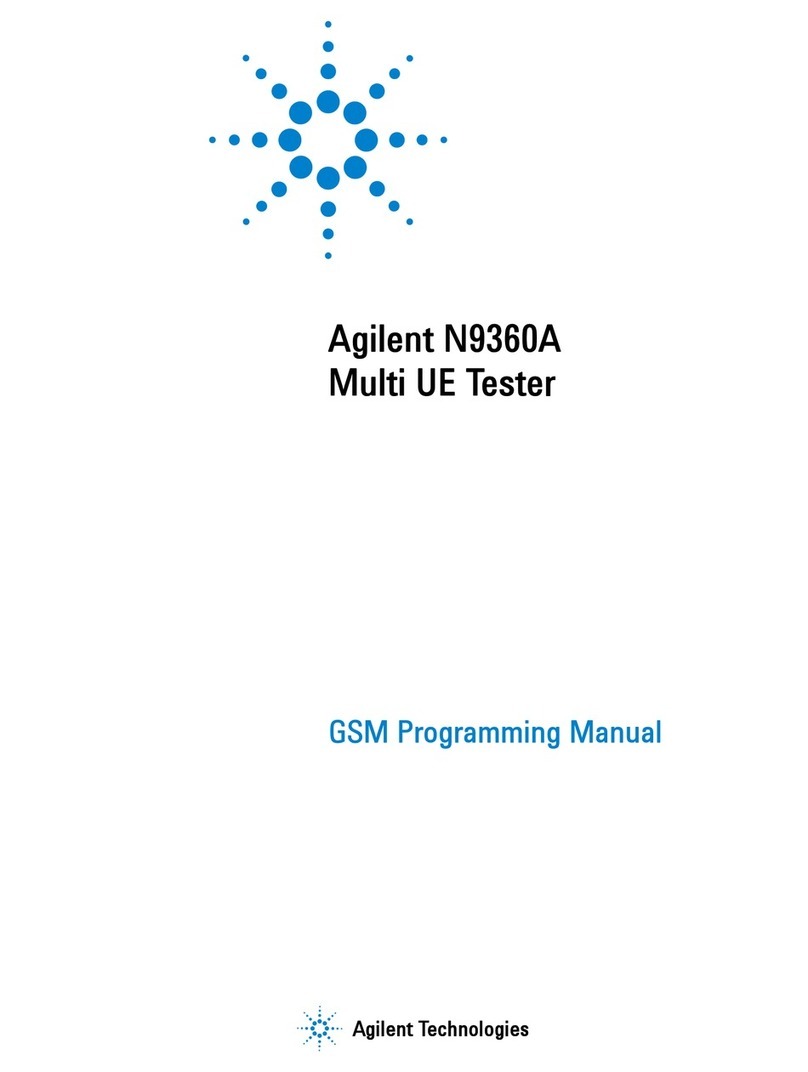
Agilent Technologies
Agilent Technologies N9360A Programming manual
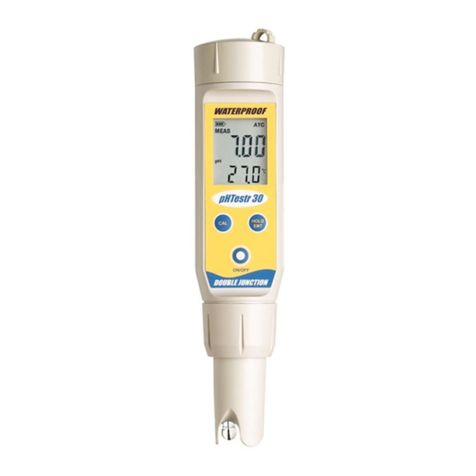
Oakton
Oakton pHTestr 30 operating instructions