ANTEK ECD3AM-00-00 User manual

Operating Manual ECD3AM-00-00 Page 1 of 13
(07/16) R0117AGB
Operating Manual
Retrofit Speed-Controller Type
ECD3AM-00-00
Replacement for
ECdrive Type D400B001, Ziehl-Abegg

Operating Manual ECD3AM-00-00 Page 2 of 13
(07/16) R0117AGB
Content:
Page
1. SAFETY INFORMATION 3
2. TECHNICAL DATA 4
2.1 CONTROLLER ECD3AM 4
2.2 DIMENSIONS 5
3. INSTALLATION 6
3.1 MECHANICAL INSTALLATION 6
3.2 ELECTRICAL INSTALLATION 6
3.3 INFORMATION ON EMC 7
3.4 ELECTRICAL CONNECTION CONTROLLER 8
3.5 OPERATING -AND DISPLAY ELEMENTS 9
3.6 ADJUSTMENT 9
3.7 ADJUSTMENTS INTERNAL 10
3.8 CODING -JUMPERS INTERNALLY 11
3.9 BLOCK DIAGRAM 12
4. MANUFACTURER’S DECLARATION 13
-Errors and revisions are reserved-
ANTEK GmbH
Im Köchersgrund 1
71717 Beilstein
+49 7062 94060
+49 7062 940620
www.antek-online.de

Operating Manual ECD3AM-00-00 Page 3 of 13
(07/16) R0117AGB
1. Safety information
Electrical units are a source of danger.
Comply with the relevant laws and regulations when electrical units
are used in installations and control systems which require
observation of safety rules, and when carrying out installation work.
When working on live units, always comply with the current accident
prevention regulations.
For reasons of safety and in order to maintain the documented
system data and functions the unit or its components may only be
repaired by the manufacturer.
No liability can be accepted if the drive parameters have an
unsuitable, incorrect manual or automatic setting.
Incorrect handling may cause injuries and/or damage property!
Prior to installation technicians who are familiar with electrical drive
equipment must read the unit handbook thoroughly.
Ensure that the voltage is less than 60V before touching electrical
contacts.
The user must use independent monitoring units in order to ensure
that a malfunctioning drive is stopped safely.
The user is responsible for installing and connecting the motor, the
converter and auxiliary units pursuant to the acknowledged technical
rules in the country of installation and other current regional
regulations. In particular, cable dimensioning, shielding, earthing,
disconnection, isolation and overcurrent protection must be taken into
account.
Regulations pursuant to DIN 57100 are applicable.
The modules are fitted with electrostatically sensitive CMOS and
MOS components. Always comply with the following information
when handling and testing the units, otherwise these integrated
circuits may be damaged.
When servicing the unit, first ensure that there is equipotential
bonding (static charging) between the unit, tools, measuring
instruments and personnel.
Take hold of the modules only by the edges; do not touch the
components or their connections.

Operating Manual ECD3AM-00-00 Page 4 of 13
(07/16) R0117AGB
2.Technical Data
2.1 Controller ECD3AM
Mains input voltage: UN400 VAC, 45 ... 64 Hz
Nominal input current: IN3 AAC
Internal fuse: 6,3 AT
Output voltage UM0 ... 90% UZK
Max. output current: IMmax 6,5 A / Phase
Continuous output current: IM3 A / Phase
Rated output power 1: SN0,9 kVA
Efficiency: ηca. 95%
Power loss idling2PV0 ca. 18 W
Power loss full load: PVca. 50 W
Max. heatsink temperature: ϑca. 80 °C
Control range: 1 : 40
Device version IP20
Standards and regulations: see Page 13
1In relation to the mains voltage 400 VAC
2Losses in 3A and phase current 12 kHz clock frequency

Operating Manual ECD3AM-00-00 Page 5 of 13
(07/16) R0117AGB
2.2 Dimensions

Operating Manual ECD3AM-00-00 Page 6 of 13
(07/16) R0117AGB
3.Installation
3.1 Mechanical Installation
♦Das Controller may only be installed in an upright position.
♦A clearance of 50 mm must be maintained both above and below the controller
♦An unobstructed inflow of cooling air and outflow of exhaust air must be ensured.
♦Appropriate counter-measures must be taken if the cooling air contains impurities (dust,
fluff, corrosive gases and grease) impairing operation of the controller, e.g. separate air
guidance, installation of filters, regular cleaning, etc.
♦The ambient temperature range must not be exceeded during operation.
♦Shock absorbing elements may be necessary if the controller is continuously exposed to
vibrations or impacts during operation.
3.2 Electrical Installation
♦The controller contains components sensitive to electrostatics. Before installation and
service work in the terminal clamp area, the staff must free itself of electrostatic electricity.
The discharging can be achieved by touching a grounded metal surface beforehand.
♦Due to the leakage currents of the controller (> 3.5 mA) via the protective conductor (PE)
must be in accordance with DIN EN 50178 the cable cross section of the protective
conductor to the cabinet at least 10 mm² Cu, or it must be laid electrically parallel, a
second protective conductor. For larger power ratings of minimum cross-section of the
protective conductor must be in appropriate relation to the cross section of the outer
conductor.
(see DIN 0100 Part 540)
♦The provisions on minimum cross sections of PE conductors must be maintained. The
cross-section of the PE conductor must be at least as large as the cross section of the
power connections.
♦Perform safety disconnection between the controller from the mains via an input-side
mains contactor.
♦It is recommended that the motor temperature monitoring conduct by thermal circuit
breaker.
♦Set point input, analog control inputs and measurement outputs are to be laid with
shielded cables.
♦Conductor diameters for power supply and motor wiring must be at least 1,5 mm²!
♦Observe the current local safety regulations

Operating Manual ECD3AM-00-00 Page 7 of 13
(07/16) R0117AGB
3.3 Information on EMC
In order to warranty electromagnetic compatibility (EMC) in your switch cabinets in an
electrically raw environment, the following EMC rules are to be observed during construction
and set-up:
♦All metallic parts of the switch cabinet are to be connected flatly and in a well-conducting
manner (not lacquer on lacquer!). If necessary, use contact or scraper wafers. The
cabinet door is to be connected with as short a circuit as possible via the metal powder
tapes (upper, middle, lower).
♦Signal lines and power cables are to be laid separated from each other in order to avoid
coupling intervals. Minimum distance: 20 cm:
♦Signal lines should be led to the cabinet from only one level, if possible.
Unshielded lines from the same electrical circuit (outgoing and return circuit) are to be
transposed, if possible.
♦Contactors, relays and magnetic valves in the switch cabinet, if necessary in the adjacent
cabinets, are to be wired with suppressor combinations, e.g. with RC elements, varistors
or diodes.
♦The braiding from signal lines are to be laid two-way (source and target), large-area and
well-conducting to a ground1. In case of poor potential equalization between shielded
connections, an additional balancing network of at least 10 mm² must be laid parallel to
the braiding to reduce the current.
♦Wiring is not to be laid freely in the cabinet, but should rather lead as tightly as possible to
the cabinet frame or to installation plates. This also applies to reserve cables. At least one
end of them must be grounded, but preferably both (additional shield effect).
♦Unnecessary wire lengths are to be avoided. Coupling capacities and coupling
inductance’s are thereby kept small.
♦The braiding from leads, such as resolver or incremental tachometer cables, must be laid
to the frame grounding. Approximately 2 cm of the insulation is to be removed in the area
where the cable is to be led into the frame in order to expose the braided cable. The
braided cable may not be damaged while removing the insulation. The cable is to be led
at the position where the insulation has been removed by grounded terminals or taut
supports.
cable
clamping yoke
1Generally all metallic conducting parts which can be connected to a protective conductor,
such as cabinet frames, motor frames, foundation grounding, etc. are designated as a
ground.

Operating Manual ECD3AM-00-00 Page 8 of 13
(07/16) R0117AGB
X5 Connector for power supply
(400 V / 3~ / 50/60 Hz)
1 = L1
2 = L2
3 = L3
4 = PE
X6 Connector for motor connection
1 = U
2 = V
3 = W
4 = PE
5 = Shield
X7 Connector for control lines (Motor)
1 = RLG (U)
2 = RLG (V)
3 = RLG (W)
4 = Encoder active High (n.c.)
5 = Encoder active Low
6 = Supply voltage +
7 = Supply voltage –
8 = Shield
X8 Connectors for signal lines
1 = +15 V
2 = 0 V
3 = Com. + Opt.out
4 = Ready
5 = Stand still
6 = Current limit
7 = Controller enable
8 = Direction of rotation
9 = Com. – Opt. in
10 = Set point (0...10 V)
11 = Set point (GND)
12 = Shield
3.4 Electrical Connection Controller
n_max
Fault
Current limit
Stand still
Enable
Ready

Operating Manual ECD3AM-00-00 Page 9 of 13
(07/16) R0117AGB
3.5 Operating - and display elements
Fault (RD) Indicates a fault
Current limit (YE) Indicates that the permissible peak current has been exceeded.
Stand still (GN) Indicates the reaching of an engine speed <5 U/min.
Enable (GN) Indicates the active ENABLE input
Operation (GN) ON = Controller ready
OFF= Controller collective fault
- Intermediate circuit > 450 V
- Intermediate circuit < 150 V
- Heat sink temperature > 80°C
If there is a fault, the output stage is disabled immediately. The fault
is stored until acknowledgment. The acknowledgment of the fault
message is given to the removal of the controller enable.
3.6 Adjustment
n-max Setting the maximum speed
1. Maximum set point voltage (10V) preset.
2. On trimmer "n-max" adjust the required max. speed
Setting range: about 1600-3100 U / min1
Factory setting: 3000 min-1

Operating Manual ECD3AM-00-00 Page 10 of 13
(07/16) R0117AGB
3.7 Adjustments internal
OFFSET Speed offset adjustment can only be set in the device
set point input to "0".
Enable controller,
ENABLE active. Adjust with trimmer "OFFSET" the engine at
standstill.
n
n-max
Sollwert 10V
0V
I-max Internal factory setting may not be changed!
tH Ramp-up time of the set point integrator
tR Return time of the set point integrator
Setting the set point ramp
Set point jump (0 10V) preset at set point input and adjust with
trimmer "tH" or "tR" the required speed ramp.
Setting range: 100 ms ... 2 s
Factory setting: 100 ms
Set point
Signal after set point jump
Internally
set point

Operating Manual ECD3AM-00-00 Page 11 of 13
(07/16) R0117AGB
PI Setting the speed controller behavior. Customize if necessary, on the
particular application. Clockwise rotation increases the proportional
gain.
Incorrectly adjusted control behavior leads to oscillation of the drive,
which can damage the motor or the after switched components (etc.
gearbox).The manufacturer takes no liability for damages by an
incorrect parameter.
.
3.8 Coding - jumpers internally
C37
OFFSET
n-max
PI
tH
tR
STB1 Jumper position a
Brake A cut-off of the control voltage on connecting terminal 2-5 and/or
X2-6 causes the motor to come to a standstill. This is the normal
operation mode of the control device.
Jumper position b with brake function for positioning
After the cut-off of the control voltage the motor winding is short-
circuited. The current is dependent upon the braking energy and
must not exceed 8 A, otherwise the motor or the control device could
be destroyed. Is the bridge put in position a, for damage caused to
the engine or controller, no liability is assumed.
STB2, STB3 not in use!
Set value source (STB3)
Relay function (STB2)
Brake ( STB1)

Operating Manual ECD3AM-00-00 Page 12 of 13
(07/16) R0117AGB
3.9 Block diagram
tRtH
f
un-max
& 1
Offset
PI
_
U
V
W
M
3~
UZK
U
W
V
L1
L3
PE
>1
>1RLG
3
+15V
GND
+10V
I-max
STB1
S1
L2
-UZK
Rotation direction logic
Set-point intergator Drehzahlregelung
monitoring
-heatsink temperature
-UZK
switching power internal voltage
supply
counter clockwise
clockwise
Output stage
engergization
control
and PWM
potential free
Output
stand still
pulse
generator
optional
current
brake
Rotation speed set-point 0 - 10V
Controler enable
Direction
limit

Operating Manual ECD3AM-00-00 Page 13 of 13
(07/16) R0117AGB
4.Manufacturer’s declaration
The manufacturer, ANTEK GmbH, herewith declares that the drive regulator ECE3AP must
be used as a component of the control equipment for variable speed motors to be installed in
a machine or to be used for the construction of a machine together with other components.
The drive regulators are not machines as defined in the machine guideline 89/392/EWG.
Notes and recommendations for the installation and proper operation are included in this
technical documentation.
The start-up of the machine is prohibited until it has been determined that the protection and
safety requirements of the machine guideline 89/392/EWG including revisions 68/EWG are
fulfilled.
In this technical documentation, the measures are described with which the drive regulator
complies with the EMC-limiting values. The electromagnetic compatibility of the machine is
based on the method and thoroughness of the conducted installation. The User is
responsible for the compliance of the EMC guideline 89/336/EWG including the revisions
92/31/EWG during operation of the machine.
Norms and regulations observed
♦Installation of high-voltage current plants with electrical operating equipment: DIN VDE
0160
♦Regulations for the set-up of high-voltage current plants: DIN VDE 0100
♦IP-protection systems: EN 60529
♦Basis material for printed circuits: DIN IEC 249 Part 1
♦Printed circuits, circuits boards: DIN IEC 326 Part 1
♦Regulation of air and flow routes: DIN VDE 0110 Part 1-2
♦De-charging of statically electricity (ESD): EN 50082-2
♦Rapid transient interference factors (Burst): EN 50082-2
♦Radio shielding of electrical operating equipment and plants: EN 50081-2, EN 55011
Table of contents
Other ANTEK Controllers manuals
Popular Controllers manuals by other brands
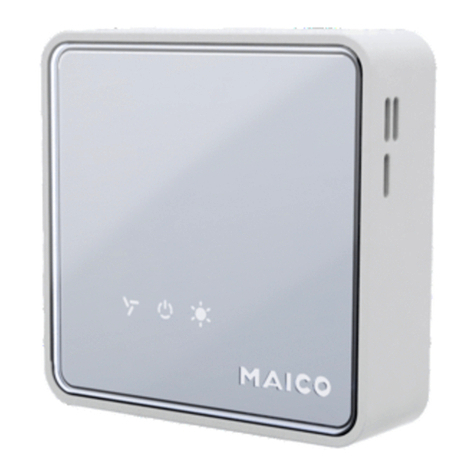
Maico
Maico EAQ 10/3 Mounting and operating instructions
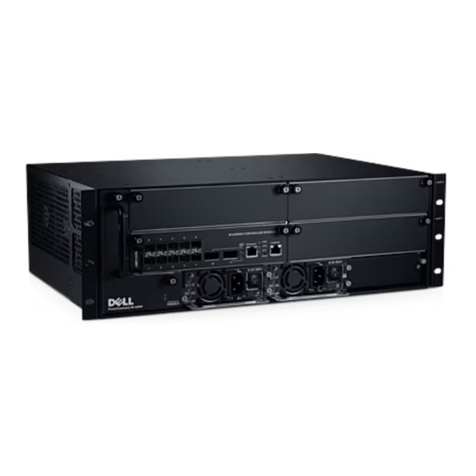
Dell
Dell PowerConnect W-6000 installation guide
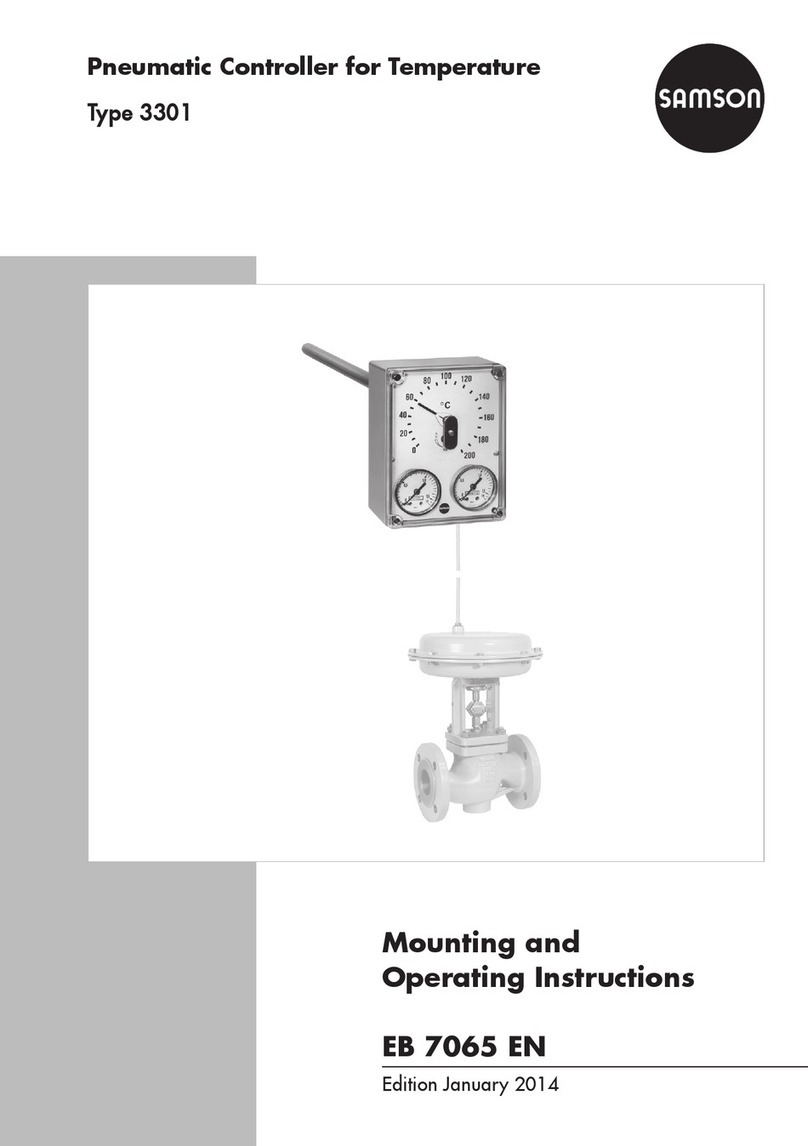
Samson
Samson 3301 Mounting and operating instructions

Prolon
Prolon C1050 Series Hardware guide
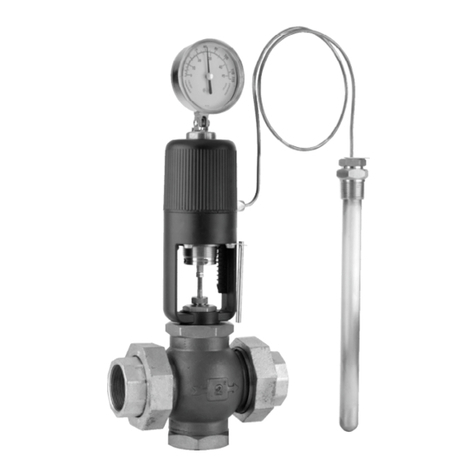
Trerice
Trerice 91000 Series Operation installation maintenance manual
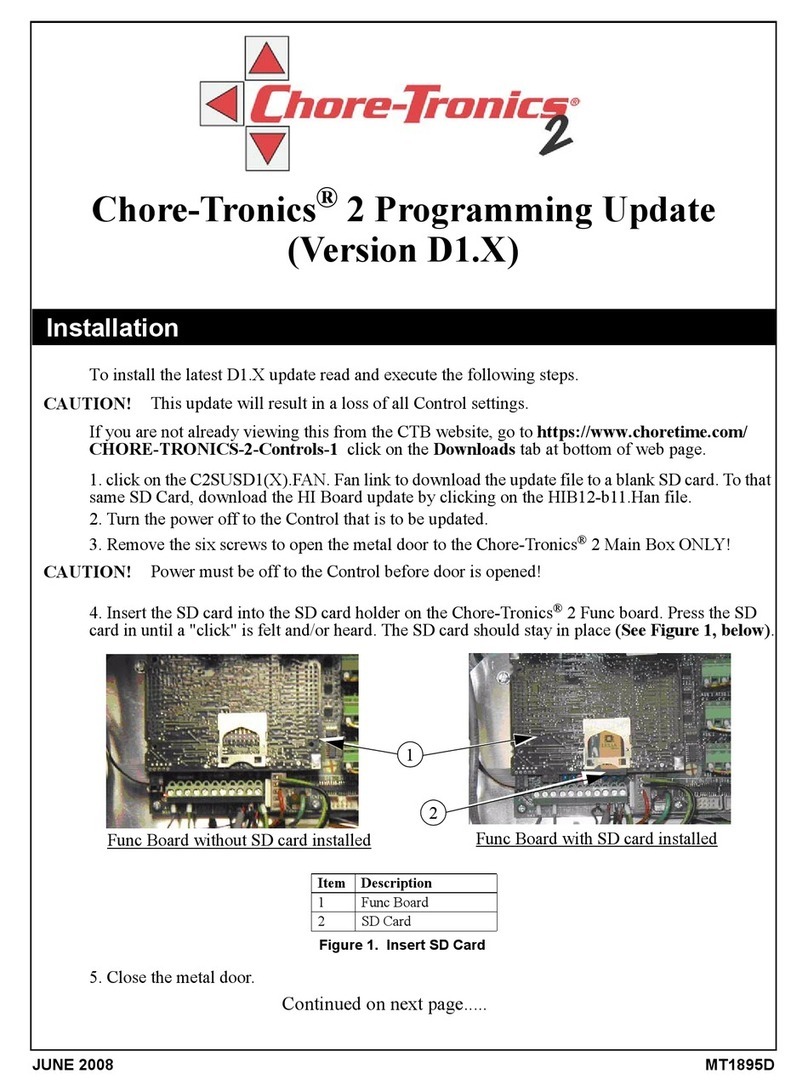
Chore-Tronics
Chore-Tronics 2 instruction manual