Arkel ARL-700 User manual

ARL-700 Quick Installation Guide V1.22
ARL-700
ELEVATOR CONTROLLER FOR TRACTION & HYDRAULIC LIFTS
(COMPATIBLE FOR EN81-20)
QUICK INSTALLATION GUIDE

ARL-700 Quick Installation Guide V1.22
Publisher ARKEL Elektrik Elektronik SAN. ve TİC. A.Ş.
Eyüp Sultan Mah. Şah Cihan Cad. No:69 Sancaktepe/Istanbul 34885 TURKIYE
TEL : +90(216) 540 67 24-25
Fax : +90(216) 540 67 26
E-mail: info@arkel.com.tr
www.arkel.com.tr
Date of issue 02.2023
Document version V1.22
This document has been created to be a guide for Arkel customers. Reproduction, transfer, distribution or storage of part or all
of the contents in this document in any form without the prior written permission of Arkel is prohibited. Arkel reserves the right
to make changes and improvements to any of the products described in this document without prior notice.
Arkel is not responsible for those mistakes that may be found in this manual and for the damages that they may cause.

ARL-700 Quick Installation Guide V1.22
CONTENTS
1. Mechanical Installation Of Control Cabinet .....................................................................................................................4
2. Motor Connections ..............................................................................................................................................................5
3. Preparations for Auto-tune.................................................................................................................................................6
4. ADrive settings and Auto-tuning process ..........................................................................................................................9
4.1. The Parameters For Asynchronous (Geared) Machines......................................................................................................9
4.2. Auto-Tune Process For Asynchronous (Geared) Machines................................................................................................9
4.3. The Parameters For Synchronous (Gearless) Machines....................................................................................................10
4.4. The Autotune Process For Synchronous (Gearless) Machines .........................................................................................11
5. Preparations for Normal Operation.................................................................................................................................11
6. Shaft Learning (With Motor Encoder Systems) & Test Driving ...................................................................................13
7. Landing And Car Calls Settings .......................................................................................................................................14
Car Calls:......................................................................................................................................................................................14
Landing Calls:..............................................................................................................................................................................14
8. LOP Learning with ARL-700 Keypad.............................................................................................................................14
9. LOP Learning with AREM hand terminal......................................................................................................................15
LOP Learning:..............................................................................................................................................................................15
10. Other Settings.....................................................................................................................................................................16
10.1. Picture Memory Settings of LCD .....................................................................................................................................16
11. Software Update.................................................................................................................................................................16
11.1. Software Update by AREM ..............................................................................................................................................16
11.2. Software Update by ARL-700 Keypad.............................................................................................................................17
12. Peripherals..........................................................................................................................................................................17
12.1. Dip Switch Settings Of CPC Board ..................................................................................................................................18
12.2. Dip Switch Settings of CPC-T Board ...............................................................................................................................18
12.3. IO-0210 Board ..................................................................................................................................................................18
12.4. MSP-16 Settings ...............................................................................................................................................................19
12.5. MSP-32 Settings ...............................................................................................................................................................19
12.6. FX-CAN Settings..............................................................................................................................................................20
13. Clearing Permanent Errors ..............................................................................................................................................20
13.1. Clearıig Permanent Errors with ARL-700 Keypad...........................................................................................................20
13.2. Clearing Permanent Errors with AREM ...........................................................................................................................20
14. New Functions Which Are Coming With EN81-20 ........................................................................................................20
By-Pass key..................................................................................................................................................................................20
Inspection Hand Terminals ..........................................................................................................................................................21
Back To Normal Operation From Pit Inspection..........................................................................................................................21
15. Error Codes - Possible Reasons And Solutions ...............................................................................................................21

ARL-700 Quick Installation Guide V1.22
1. Mechanical Installation Of Control Cabinet
Mount ARL-700 control cabinet, brake resistor, battery pack and UPS (if required) to their places.
12cm
16cm
38cm
Figure-1: Dimensions of battery pack (it is required only
when the inverter is supplied with battery during emergency
evacuation)
(It is not used for brake relase emergency evacuation)
ADrive Boy-B (5.5kW / 7.5 kW / 11 kW)
H
W
Şekil-2b: ADrive dimensions
Figure-2a: ARL-700 control panel (Control panel dimension and type can change depending on installation type)
D
Boyutlar
(mm)
ADrive
Boy-B
ADrive
Boy-C
W
260
289
H
387
442
D
184
205
Type - A
Mounting Holes
18 cm
32,5 cm
11,5 cm
Mounting Holes
30,5 cm
22,5 cm
15,5 cm
Type - B
Figure-3: Type-A and Type-B dimensions of brake resistors
Warning: Mount the brake
resistor horizontally! Don’t
mount it on control panel.

ARL-700 Quick Installation Guide V1.22
2. Motor Connections
Make the connections of motor phases & motor PTC, brakes & brake release contacts, motor fan, encoder, brake resistor and
battery pack with UPS (if required).
Synchronous motor
Batteries &UPS
Figure-4: Motor, brake, fan, encoder, brake resistor and batteries connections
1
2
3
ARL-700 Control
Panel
Brake Resistor
4
5
6

ARL-700 Quick Installation Guide V1.22
Figure-5: UPS connections
***If there is SERVOSAN brand UPS inside the control panel these connections are not used.
***If you do not have UPS you must bridge connectors U-LI with U-LO and U-NI with U-NO using with suitable cables.
Otherwise you can not run control panel.
3. Preparations for Auto-tune
Auto-tune process must be performed by ADrive before initial set-up of an elevator. In this way ADrive learns characteristic of
motor. During the Auto-tune the elevator must be operated manually, therefore the recall command has to be provided. For recall
operation make the following connections.
•Connect the mains power of the control panel (L1, L2, L3, N, PE)
•Bridge the safety circuit by the terminals in control panel shown below.
Control Panel Terminals
Figure-6: Bridging of safety chain
•Bridge the signals of top and bottom limit switches (817 and 818) to terminal 100 on KBK-12&13 connection board
shown below.
KBK-12&13
Figure- 7a: bridging of top and bottom limit switches
•Bridge the car top (869) and pit (868) inspection signals to terminal 100 on KBK-12&13 connection board shown below.
KBK-12&13
Figure-7b: bridging of car top and pit inspection signals

ARL-700 Quick Installation Guide V1.22
Figure- 8a: KBK12&13 board
•KBK12&13 connection board is used for all required connections for shaft. That board includes supply and inputs of
all safety chain, car CANBus input/output, and car connections. If you prefer pre-wired connections, all connector
connections are sign with labels on flex cables.
Figure- 8b: AREM hand terminal
•ARL-700 can be programmed with two ways. It can be
programmed either internal keypad onto ARL-700 or
AREM hand terminal.
•AREM hand terminal can be connected to CANBus line
which is located in shaft LOP, COP or control panel.
The programming can be done with keypad in case
AREM is not exist.
•AREM will run automatically when it is connected
CANBus line. It can be connected to KXCBA board or
any CANBus access point. For first installation ARL-
700 software must be updated by AREM. (See
“Software Update”).
Figure- 8c: KXCBA CANBus terminal

ARL-700 Quick Installation Guide V1.22
•Activate the manual operation mode by turning the recall switch on the recall hand terminal to “Insp” position. In this
case the motor can be moved by recall buttons from the control panel.
Figure-8d: Recall hand terminal
•Turn on the SMP switch after all fuses is turned on.
•When the system is first energized, the screen of ARL-
700 that shown on Figure. 9a is displayed.
Figure- 9a first energised screen of ARL-700
•For the parameter changes that will be explained, you
must enter the advanced menu. To do this, press the Up-
Down-Red (ESC) button together. Select “Advanced”
from the appearing screen by pressing ENT button. The
advanced menu is activated.
•Press “ENT” button onto the ARL-700 keypad to enter
the ARL-700 menu.
•Password screen will be displayed. If no password is
entered, the factory setting is "000000".
•Press the "ENT" button again.
Figure-9b: Entering Menu
•“BASIC SETTINGS” menu is displayed after “ENT”
button is pressed.
Figure-9c: “BASIC SETTINGS”
•In order of, arrange the “NUMBER OF FLOORS”, arrange the “OPERATION MODE” to “INSTALLATION
MODE”. “DRIVER TYPE” parameter should be arranged to “VVVF(ADrive)”. If you use another brand inverter,
this parameter should be arranged to “VVVF(Other)”.
Note: HSR Board should be used in case of using hydraulic lift or another brand inverter.
•If there is a motor encoder in the system, shaft learning feature can be used. And the parameter “SHAFT READ SYTM”
should be arranged to “motor encoder”. If there is no motor encoder, it should be arranged to “ML1- ML2 magnet”.
•Before starting autotuning procedure, the motor brake monitoring parameter should be disabled to avoid encountering
brake monitoring error if the motor has brake microswitches and they were connected. The brake monitoring parameter
should be enabled after autotuning is complated. If there are no brake micro switches, the following steps are skipped.
•Please come to “PROTECT&MONITORING” screen
under the parameter menu.
•It can be arranged to “off” with coming The “BRAKE
MONITORING” screen.
Figure-9d: Disabling of “Brake Monitoring” control

ARL-700 Quick Installation Guide V1.22
4. ADrive settings and Auto-tuning process
•The machine plate information should be entered to ADrive parameters before starting auto-tuing process. The machine
plate informations are entered by following below steps.
4.1. The Parameters For Asynchronous (Geared) Machines
4.2. Auto-Tune Process For Asynchronous (Geared) Machines
•The pulse of the incremental encoder per revolution
is entered to this parameter. If the system is usedin
open loop, there is no need to enter a value.
•Main line voltage is 380V at factory settings.
•Go to 2-MOTOR SETUP parameter.
•Arrange the MOTOR TYPE to induction.
•Nom. Motor speed is arranged acc to suspension
ratio.E.g. if motor speed is 2.00 m/s with 2:1
suspension ratio; It should be arranged to VN: 1.00
m/s
•Motor rpm value is entered acc to motor plate.
•Voltage that must be applied to motor for full
speed. This value is specified on the motor plate
by the motor manufacturer.
•Nominal current of the motor. This value is
specified
•Nominal frequency of the motor. This value is
specified on
the motor plate by the motor
manufacturer.
•Usually there is no rotor slip frequency
information on the motor plate. It should be
calculated with formula. You can find the info you
needed in the ADrive manual. If the system is used
in open loop, there is no need to enter a value.

ARL-700 Quick Installation Guide V1.22
•6- CONTROL TYPE should be arranged to open loop with the parameter 6.1- CONTROL TYPE CT: OPEN LOOP. If
there is an encoder in the system, it should be arranged to CT: CLOSED LOOP after autotune process is complated
with motor first running.
•9.1-AUTO TUNE parameter should be arranged to “ENABLED” and go to main screen with “ESC” button.
•Vout message specifies the lift is in open loop. Then the lift is taken to recall mode with hand terminal. Press and hold
the up or down button until the autotune procedure is completed. The lift is moved in recall mode after the autotune is
complated. It is checked that when the up button is pressed, the car goes up or when the down button is pressed, the car
goes down. If the car moves to the opposite direction, it should be corrected with reversing motor direction with the
parameter 2.17 MOTOR DIRECTION.
•The system is arranged to the closed loop after checking the car goes to the correct direction in open loop. (6.1
CONTROL TYPE: CLOSED LOOP). The motor turning is observed in recall mode again. 2.18 ENCODER
DIRECTION parameter is arranged with inverse if the motor turns too slow or draws too much current from nominal
current in both direction (up&down). If the direction of the encoder is reverse, ADrive may give overcurrent or low
speed errors other than drawing over current. The necessary connection should be made with disconnection below
bridges after mechanical installation.
•Remove the brdiging made between 110-140 terminals at the safety. (See Figure-6)
•Remove the bridging made for the up and down forced deceleration switches 817 and 818. (See Figure-7a)
4.3. The Parameters For Synchronous (Gearless) Machines
•Nom. Motor speed is arranged acc to suspension
ratio. E.g. if motor speed is 2.00 m/s with 2:1
suspension ratio; It is arranged to VN: 1.00 m/s.
•Motor rpm value is entered acc to motor plate.
•Go to 2-MOTOR SETUP parameter.
•MOTOR TYPE is arranged to synchronous.
•Main line voltage is 380V at factory settings.
•Voltage that must be applied to motor for full speed.
This value is specified on the motor plate by the
motor manufacturer.

ARL-700 Quick Installation Guide V1.22
4.4. The Autotune Process For Synchronous (Gearless) Machines
•9.1-AUTO TUNE parameter should be arranged to “ENABLED” if the motor is with ropes. And come to main screen
with “ESC” button.
•9.1-AUTO TUNE parameter should be arranged to “ENABLE_STATIC” if the motor is without ropes. And come to
main screen with “ESC” button.
•Then the lift is taken to recall mode with hand terminal. Press and hold the up or down button until the autotune
procedure is completed. If the autotune is arranged to “ENABLED” and if “wrong encoder direction” error occurs, 2.18
ENCODER DIRECTION is reversed and the autotune procedure is repeated. If the autotune is arranged to
“ENABLE_STATIC” and if the motor cannot be turned at first moving, 2.18 ENCODER DIRECTION parameter is
reversed and the autotune procedure is repeated.
•The lift is moved in recall mode after the autotune is complated. It is checked that when the up button is pressed, the
car goes up or when the down button is pressed, the car goes down. If the car moves to the opposite direction, it is
corrected with reversing motor direction with the parameter 2.17 MOTOR DIRECTION.
•The necessary connection is made with disconnection below bridges after mechanical installation.
•Remove the brdiging made for 10-140 terminals at the safety. (See Figure-6)
•Remove the bridging made for the up and down forced deceleration switches 817 and 818. (See Figure-7a)
5. Preparations for Normal Operation
•Make all the other mechanical installations of elevator system.
•Make the inspection box wiring, pit box wiring and safety circuit wirings.
•Make the installation of round magnets for SKSR1 bottom limit switch (bottom correction sensor). The cables of
SKSR1 magnetic switch must be connected 100 and 817 terminals in IBC-S board. Round magnets of bottom limit
switch must be put to the needed distance as shown below. The needed distance for magnets is shown on AREM screen
when parameter “Shaft Learning” is selected.
•
Nominal current of the motor is arranged. This
value is specified on the motor plate by the motor
manufacturer.
•The number of poles of the motor. Enter the data on
the motor name plate.
•The type of absolute encoder is arranged acc to the
encoder you used. ADrive gives error if the encoder
type is arranged incorrect or the connection of it
made wrong.

ARL-700 Quick Installation Guide V1.22
Black Side of the magnets
Red side
•Move the car to the bottom floor. Car must be exactly at
the floor level.
•Install the round magnet with red color side above the
SKSR1 magnetic switch as deceleration distance.
•Install the round magnet with black color side a little
above the red color magnet.
•The distance between magnetic switch and magnets
must be 1- 2 cm.
BOTTOM FLOOR LEVEL
Figure-10a: Installation of magnets for SKSR1 bottom
•Make the installation of round magnets for SKSR2 top limit switch (top correction sensor) so that the one side of the
rail can be seen. The cables of SKSR2 magnetic switch must be connected 100 and 818 terminals in IBC-S board.
Round magnets of top limit switch must beput to the needed distance as shown below.
•Move the car to the top floor. Car must be exactly at the
floor level.
•Install the round magnet with red color side below the
SKSR2 magnetic switch as deceleration distance (See
Table 1).
•Install the round magnet with black color side a little
•above the red color magnet.
•The distance between magnetic switch and magnets
must be 1- 2 cm.
Figure-10b: Installation of magnets for SKSR2
•Make the installation of bar magnets for SML1&SML2 door zone switches. The cables of magnetic switches must be
connected ML1-ML0-1000 and ML2-ML0-1000 terminals on IBC-S board respectively. Place the strip magnets
required for the door zone magnetic switches as described below.
•Move the car to the end of floors.
•Car threshold must be exactlyat the floor level.
•Install the bar magnet opposite to the zone magnetic
switches. The middle of the ribbon magnet must be on a
level with the middle of the magnetic switches. The
distance beween magnetic swtiches and magnets must
be 1-2cm.
•Bar magnets must be fixed with screw or glue.
•
•Repeat this installing operation at all floors.
Figure-10c: Installation of magnets for SML1-
SML2 door zone sensors
•If motor has brake mikroswitch(es) connect it to BRM and BRM2 inputs. (see figure 4-2). Go to
“PROTECTION&MONITORING” settings under the “PARAMETERS”. Go to submenu wiht pressing Enter. And
select “on” with coming “Mechanical brake monitoring” screen.
•In the same way, arrange the "OPERATION MODE" under "BASIC SETTINGS" to "Normal operation".
Up forced
deceleration distance
TOP FLOOR LEVEL
15cm
15cm
FLOOR LEVEL

ARL-700 Quick Installation Guide V1.22
6. Shaft Learning (With Motor Encoder Systems) & Test Driving
If shaft copy system is not used, the lift can be tried to run in normal operation after the magnet installation has been made in
accordance with the scheme.
If ARL-700 "SHAFT POSITION. SYSTEM " parameter arranged to "ML1-ML2 magnets", the deceleration distance is
determined with 141&142 magnets.
The distance of the deceleration magnets is determined by the speed of the car.
The distances shown in Table-1 are the ideal deceleration distances. "SHAFT POS.
SYSTEM "parameter is arranged to "ML1-ML2” magnets ", the distances in Table-1
can be used when the 141-142 magnets are placed in accordance with the diagram.
These distances are also used for "817-818" forced decelerations. If the parameter
“SHAFT POS. SYSTEM” is arranged to “Motor encoder”, these values can also be
used for the parameter “deceleration distance”
In shaft copy systems, ARL-700 should do shaft learning procedure once to sense the car and floor positions before normal
operation. Therefore, check the magnetic switch, magnets layout and encoder connections according to the encoder counting
system as described earlier. After checking, perform shaft learning procedure as described below.
•Go to the "DRIVER SETTINGS" parameter under the "PARAMETERS" menu. Press "ENT" button and the
"SLOWING DISTANCE" value is arranged according to Table-1.
•Also the slowing distance should be arrange for ADrive. In order to arrange it;
•"1.1-HIGH SPEED" value is arranged in the "1- TRAVEL CURVE" menu. This value is used to determine the
maximum speed the lift can reach.
•“1.4-LOW SPEED” parameters ideal value is 0.13m/s. It can be used without any change. The Parameter “1.8-
SLOWING DST” should be arranged to 15 cm less than ARL-700 parameter “SLOWING DISTANCE” value. Also
if ARL-700 "SHAFT POSITION. SYSTEM" parameter arranged to "ML1-ML2 magnets", the ADrive parameter
“1.8-SLOWING DST” should be arranged to 15 cm less than the deceleration distance of 141&142 magnets.
•The lift should not to be in recall or inspection mode in order to be able to perform shaft learning procedure. In such a
case a warning message will be displayed on the screen.
•The “SHAFT POS. SYS” parameter under “BASIC SETTINGS” should be arranged to “Motor encoder”.
•The car position is not important while shaft learning. The system automatically starts to move, after reaching bottom
floor the car goes to the top floor with learning shaft and complete the driving.
Car Speed
Deceleration Distance
1.00m/s
180cm
1.60m/s
240cm
2.00m/s
360cm
2.5m/s
520cm
Table-1 Ideal Deceleration
•“1.10-STOPING TYP” parameter is arranged to
“STP WITH DSTNCE”.

ARL-700 Quick Installation Guide V1.22
•Go to the “SHAFT LEARNING” menu by clicking the right or left button on the main menu. Press "ENT" button to
go to the "Shaft learning" parameter.
•By pressing the ENT button, the shaft learning process is started.
•This may take some time depending on the number of stops of the elevator. For this reason, do not hurry.
•After shaft learning is completed, answer "Yes" to the question "SAVE?" Otherwise, the shaft learning process is not
saved and shaft learning will be required again.
•After "Yes" is selected and the ENT button is pressed, the system will be automatically restarted and the car will go to
the bottom floor to reset floor information. In this case, "RESETTNG POSITION" will appear on the ARL-700
display. All the time the system is started, the system will go to find lift positions in shaft copying systems.
7. Landing And Car Calls Settings
Car Calls:
•CPC or CPC-T (Car Panel Controller) boards are used to give car calls. These are connected to IBC-S (Inspection Box
Controller) board by serial communication. If dipswitch settings were done which is shown ni “Software Update”, it
is not necessary to do any additional settings. (Note that CPC and CPC-T dipswitch settings are different from each
other.)
•The FX-CAN board is a combination of IBC-S and CPC cards, and for used car calls. The settings and features are
described in “Software Update”.
•Check that the lift goes to all floors with car calls before arranging the settings for the landing calls.
Landing Calls:
•ARL-700 can accept landing calls both serial connection(CANBus) and parallel connection. If landing calls are wanted
to use as paralel, the MSP-16 or MSP-32 board has to be used. (see “Software Update” and “Settings” for more
information)
•If CANBus is wanted to use for landing calls, position of landing calls’ buttons would be defined to ARL-700. This
can be done in two ways. With ARL-700 keypad or AREM hand terminal.
8. LOP Learning with ARL-700 Keypad
•Make sure the car is on the top floor before LOP Learning.
•Go to “LOP LEARNING” menu by clicking the right or left button on the main menu. Then press “ENT” and the state
“Off” will change to “LOP-A learn:Actv” or “LOP-B learn:Actv” for the A or B door. Afterwards it isn’t necessart to
press again the “ENT” button.

ARL-700 Quick Installation Guide V1.22
•“LOP-A learn:Actv” is displayed on the screen. When the display is in this state, the process of teaching LOPs of A-
door is started. Please go to the top floor without pressing any key. You will see the car door is open. And you will see
“??” picture on the LOP if there is a screen. In this case, press and hold the call button. After a whileyou will see that
the call button LED starts flashing. "A", "+" and the corresponding floor number will flash on the display respectively.
Leave the button and get in the car. Make a call to one down floor. The door will open when the car comes to the floor.
Do the same process for this floor too. After all LOPs have been taught, go to the machine room and press the ESC
button. The LOP learning process will complete by this way.
9. LOP Learning with AREM hand terminal
•Firstly AREM hand terminal should be connected to
CANBus connector on the CPC or FX-CAN board to
define place of landing buttons
•Give a call to bottom floor from COP.
•Press “Tools” button and select icon of “LOP
Learning” and press Enter button.
•“LOP learning” must be selected to start to learn
landing button position.
•“LOP position reset” is used to reset which was learnt
LOP positions
Figure- 13a: Selection of LOP Learning
•When selected “LOP learning” the figure-18c appears
on the screen of AREM. If there aren’t any learned
position you will see figure right side of floor
numbers. In that situation if your LOP has a display you
will see “??” on LOP screen. If position learning was
done previously you will see figure right side of
floor numbers. In that situation you will see “A” “+” and
defined floor number on LOP screen respectively.
•For B door this sign will be “B”. “+” means the display
is used for landing call button. If “-” sign appears on
screen of LOP, this means the display is used only
display.
LOP Learning:
•If the car is at bottom floor and LOP display shows “??” or wrong landing floor, you must hold down call button of
LOP until appears correct floor number on LOP screen. For first floor door A you must see “A” “+” and ”1” respectively.
If your system has B door you should slide scroll box to right side and hold down call button of LOP until appears “B”
“+” and “1” respectively. The while figure will change as figure . Give a call from COP to second floor after
completed definition of first floor. All LOPs must be defined for all floor according to explanation above.
•If LOP doesn’t have a screen, you should hold down call button of LOP until figure will change as figure on
AREM screen. The while led of LOP will flash for a second when landing position is learned.
•If the LOPs are used only for display you don’t have to do these settings. The display will show floor number when
elevator starts to normal working.
Figure-13b: LOP Position Learning

ARL-700 Quick Installation Guide V1.22
10. Other Settings
10.1. Picture Memory Settings of LCD
The software must be updated like explained “Software Update” when first time a LCD is connected CANBus line. The software
update should be done after all LCDs are connected CANBus line. The Picture memory is empty when first time an LCD is
connected CANBus line.
•The AREM must be connected which is located same
LCD CANBus line. If you want to update LCD of COP
the AREM must be connected to COP. If LCDs of
landings are wanted to update this time the AREM must
be connected shaft CANBus line. Other wise ARL-700
can not find correct LCDs
•To update Picture memory of LCD, select “LCD update
screen” and press Enter button.
Figure-14a: LCD Update Screen
•Updated LCD type is selected and pressed Enter button.
•To select message right/left arrows are used. To select
Picture for message up/down arrows are used.
•All changes are saved in memory of LCD.
Note: The dip switch on the back of the LCD must be set for the
intended use (Horizontal / Vertical).
Figure-14b: LCD type selection
11. Software Update
11.1. Software Update by AREM
•When AREM is first connected to the CANBus line, if
AREM’s SD card doesn’t have the software found in
ARL-700, AREM will inform that an update is needed.
Start the update pressing the button F1. The system will
be restarted when the update is complete. All ARL-700
peripherals are updatable. For this reason, with each
peripheral added to the elevator, the software needs to
be updated.
Figure-15a: Firmware Update

ARL-700 Quick Installation Guide V1.22
•Choose “firmware update” icon and press “Enter”.
•The latest update is the one having the nearest date. Start
software update by pressing “Enter”.
•While carrying out setup, if there are peripherals not
connected to the CANBus line, you will have to update
the software again. Otherwise, peripherals you
connected later won’t work.
Figure-15b: Selecting the software to be updated
11.2. Software Update by ARL-700 Keypad
•In order to update the software with the ARL-700 keypad, a microSD card must be exist in the SD card slot on the ARL-
700. ARCODE and ARL-700 use the same software folders. For this reason, the relevant software folders should already
be copied into the SD card. Go to the “SDCARD OPERATION” menu by clicking the right or left button on the main
menu. Go to the “Update firmware” parameter and press “ENT”.
•When the "SELECT FIRMWARE" screen is displayed, the version to be updated is selected with the up and down
buttons. The latest update is the one having the nearest date. Start software update by pressing “Enter”.
•While carrying out updating, if there are peripherals not connected to the CANBus line, you will have to update the
software again. Otherwise, peripherals you connected later won’t work.
12. Peripherals
They are all units that run on CANBus line. Each unit has a unique address. During update, other peripherals are searched and
updated after ARL-700 is updated
CPC (CAR PANEL CONTROLLER): It is the board for car call. It is used to make a call for the car. (socket type) CPC-T
(CAR PANEL CONTROLLER): The car call buttons are connected to this board wire by wire. (terminal type). More than 16
stops, this is not possible to use CPC-T board.
FX-CAN: This card, which can be placed on the car top, includes some features of the IBC-S card as well as connecting the car
calls.
IBC-S (INSPECTION BOX CONTROLLER): It is revision box’s card. The communication between control panel and car is
made by this board.
IO-0210 (I/O BOARD): This board gives extra 2 prog. inputs and 10 prog.transistor outputs to the user.
MSP-16 In the parallel installation Systems, LOP calls are connected to this board. Up to 16 stops can be used. Up to 16
floors can be used when one button is used, and up to 9 floors can be used when a double button is used for car calls.
MSP-32: With MSP-16, double button can be operated up to 9 floors. If you want to use double button for between 10 and 16
floors, MSP-32 board should be used.
BC-BUT: It is the landing call button without indicator.
BC-D2X: landing call button with two parts and a dotmatrix indicator. (can be used for car indicator or landing indicator).
BC-D3X: landing call button with three parts and a dotmatrix indicator. (can be used for car indicator or landing indicator).

ARL-700 Quick Installation Guide V1.22
BC-LCDA: 128x64 resolution LCD. The idicator can be used both inside the car and landing or door indicator. It can be used
vertical or horizontal.
BC-LCD240128: 240x128 resolution LCD. The idicator can be used both inside the car and landing or door indicator. It can be
used vertical or horizontal.
BC-LCD10555: 105x55 resolution indicator. It can be used both inside the car and landing or door indicator. The LCD display
color can be adjusted from menu.
HSR: It is the peripherals used to connect valves in hydraulic systems or to connect command signals when an inverter other
than ADrive is used.
12.1. Dip Switch Settings Of CPC Board
ARL-700, that can work with two-door support up to a total of 64 stops, collects car calls with the help of a CPC card. Each CPC
card can serve up to 24 stops. If there are more than 24 floors or on condition that it has two doors, two CPC cards must be used.
For an elevator with 64 stops and two doors, a sum of 6 CPC cards must be used. The dipswitch which is located on CPC board
is used to determine working type and door settings.
Dipswitch-1
Dipswitch-2
Dipswitch-3
Dipswitch-4
0
0
1
0
CPC-1A
Up to 24 floors
0
1
1
0
CPC-2A
Up to 48 floors
1
0
1
0
CPC-3A
Up to 64 floors
0
0
0
1
CPC-1B
Upto24floors for 2nddoor
0
1
0
1
CPC-2B
Upto48floors for 2nddoor
1
0
0
1
CPC-3B
Upto64floors for 2nddoor
0
0
1
1
CPC-1AB
Up to 24 floors
0
1
1
1
CPC-2AB
Up to 48 floors
1
0
1
1
CPC-3AB
Up to 64 floors
Figure-16a: dipswitch settings of CPC board
For example: If you have a one-door system up to 24 floors, dip switch settings must be done “0010”. “ON” on the dip switch
means 1.
12.2. Dip Switch Settings of CPC-T Board
CPC-T board can work up to 16 stops.
Dipswitch-1
Dipswitch-2
Dipswitch-3
Dipswitch-4
ON
Door-A enable
Door-B enable
Gray outputs
Outputs are inverted
OFF
Door-A disable
Door-B disable
Binary outputs
Outputs are normal
Figure-16b: Dip switch settings of CPC-T
CPC-T board can be optionally used instead of CPC board. As seen in the table above, the dip-switch settings are different from
each other. So, please pay attention this case while doing dip-switch settings.
For CPC-T board, car call button connections are done wire by wire with terminal. If the system has more than 16 stops, it is not
possible to use CPC-T board.
12.3. IO-0210 Board
In some cases, programmable inputs and outputs may not be enough. Then, this IO-0210 board would be useful. This board gives
2 inputs and 10 transistor outputs to the user.
From “Programmable outputs” parameter, the outputs should be assigned from related group number. (Tools device
parameters programmable outputs IO-0210 board outputs)
1 pc. IO-0210 board gives 10 programmable transistor outputs to the user. There are 8 dip-switches. The logic of these
dip-switches is as follows:
For outputs, 1 and 2 dipswitches are used to select the group number of output:
1
2
Outputs
OFF
OFF
Group-1 outputs
OFF
ON
Group-2 outputs
ON
OFF
Group-3 outputs
ON
ON
Group-4 outputs
Figure-16c: Dip switch settings of IO-0210
For inputs, other 6 dipswitches (from 3(MSB) to 8(LSB)) works with a binary logic. For example; MSB: Most Significant Bit
(3rd dip-switch)
LSB: Least Significant Bit (8th dip-switch)
You can program 64 different IO-0210 boards for inputs.

ARL-700 Quick Installation Guide V1.22
000000“IO-0210-1 board PI1 and IO-0210-1 board PI2”
000001“IO-0210-2 board PI1 and IO-0210-2 board PI2”
000010“IO-0210-3 board PI1 and IO-0210-3 board PI2”
000011“IO-0210-4 board PI1 and IO-0210-4 board PI2”
000100“IO-0210-5 board PI1 and IO-0210-5 board PI2” and so on... This can be chosen from 0 up to 63. (64 pcs.)
Programmable inputs should be assigned from the related parameter depending on the dip-switch settings. (Tools device
parameters programmable inputs IO-0210 board inputs)
3
4
5
6
7
8
IO-0210-x
OFF
OFF
OFF
OFF
OFF
OFF
1
OFF
OFF
OFF
OFF
OFF
ON
2
OFF
OFF
OFF
OFF
ON
OFF
3
OFF
OFF
OFF
OFF
ON
ON
4
OFF
OFF
OFF
ON
OFF
OFF
5
Figure-16c: Dip Switch Settings of IO-0210
12.4. MSP-16 Settings
MSP-16 card is used when buttons are not serial communication (CANBus). It can serve up to 16 floors at most. In oneway
collective external calls can be collected up to 16 floors with a MSP-16. In case of twoway collective, calls can be collected up
to 9 floors with a MSP-16. Dip switch settings must be done according to the following table.
Figure-16d: Dip Switch Settings of MSP-16
12.5. MSP-32 Settings
For double buttons between 10-16 floors two MSP-32 must be used. Dip switch settings must be done according to the following
table.
Figure- 16e: Dip Switch Settings of MSP-32
Dip switches 5 and 6 for both MSP-16 and MSP-32 boards are
used to set the display outputs. Gray, binary, 7-segment outputs
as well as 31, 32 and 02 outputs can be received via MSP boards.
Figure-16f: Display Output Settings

ARL-700 Quick Installation Guide V1.22
12.6. FX-CAN Settings
The FX-CAN board is an ARL-700 peripheral that is used to collect up to 16 car calls and fulfill some of the features of the IBC-
S board. FX-CAN board can not be used with IBC-S, CPC or CPC-T. If the double doors on the same floor are opened
independently, this card can not be used (It sends the calls that received as AB door to the ARL-700.). Gray, binary, 7-segment
31, 32 and 02 signals can be received via this board. Inspection signals (500-501) can be connected to this card. It has speaker
output for gong and button sound. Output can be taken for emergency lighting with battery connection. Connection terminals for
magnetic switches (ML1-ML2 or liftsense) are available. It has relay outputs for car light, fan, door open and close (single door).
There are 10 programmable inputs on it that can be used for connection of photocell, overload, full load.
Two dip switch on the board is used to operate car indicators which have
different working type.
Figure-16g: Display output settings
13. Clearing Permanent Errors
13.1. Clearıig Permanent Errors with ARL-700 Keypad
It is obligation that certain error are permanent acc to EN-81-1 / 2 + A3 or EN 81-20 standards. After finding the root cause of
the error, the permanent error should be cleared so that the system returns to normal operation. This process is done in the
following way;
13.2. Clearing Permanent Errors with AREM
In order to clear the permanent error, the following 2 steps should be performed. On AREM,
1) Tools →System Tools →Clear Permanent Error
2) Tools →System Tools →Reset System
14. New Functions Which Are Coming With EN81-20
By-Pass key
The pacco switch is used to bridge safety circuit for maintenance purpose.
•The key which has 4 positions can bridges only one part of the safety circuit in same
time.
•Position 0: No bridge in that position.
•Position 1: 120-130 are bridged. Landing door contacts are bridged for semi automatic
doors.
•Position 2: 130-135 are bridged. Landing door contacts for full automatic door or
Landing door locks for semi automatic doors are bridged.
•Position 3: 135-140 are bridged. Car door locks are bridged.
•By pressing the right or left button on the main menu, go to
the “CLEAR PERM. ERR.” screen. Afterwards press the
ENT button to clear the permanent error. After the error is
cleared, either the system is restarted or the lift is taken first
to inspection mode and then to normal mode.
Figure 17a: By-pass key
Table of contents
Other Arkel Controllers manuals
Popular Controllers manuals by other brands

Cooper
Cooper S225-10-30 Installation, operation and maintanance instructions
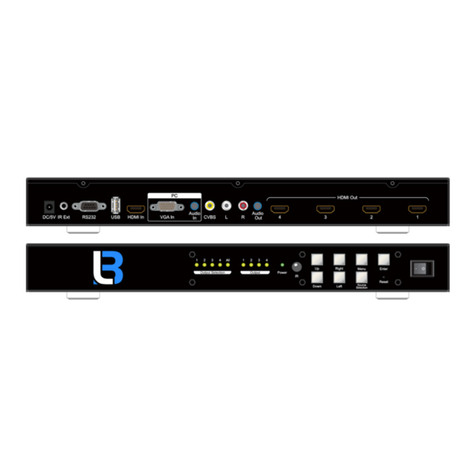
Brightlink
Brightlink BL-VW22 operating instructions
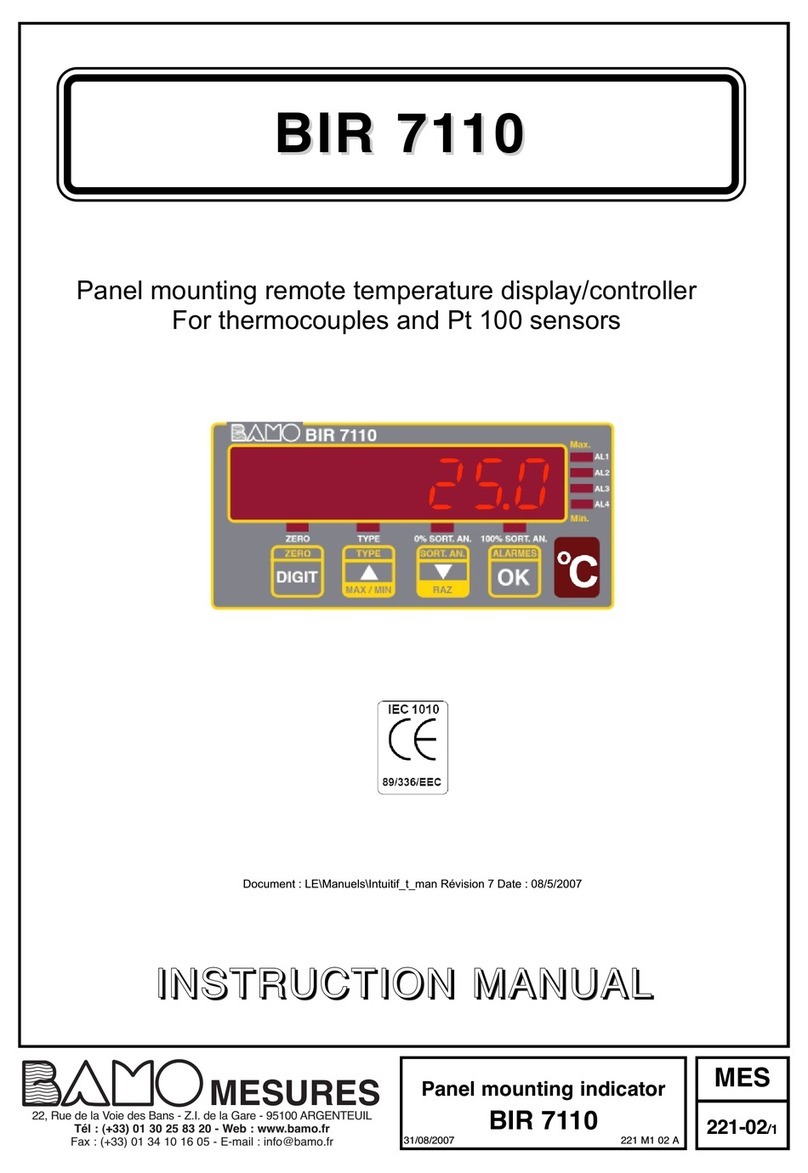
Bamo
Bamo BIR 7110 instruction manual
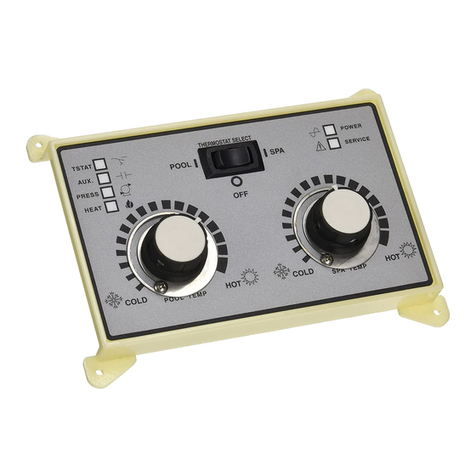
Pentair Pool Products
Pentair Pool Products MiniMax NT 6800 installation instructions
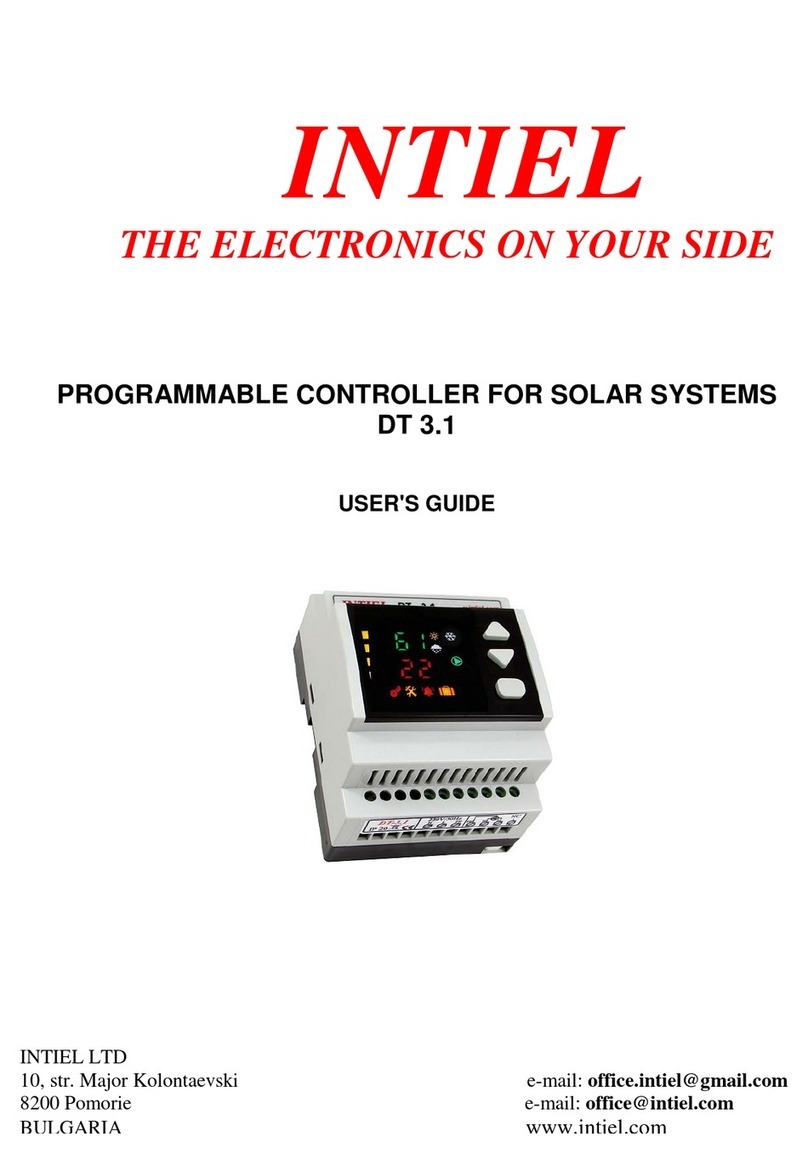
Intiel
Intiel DT-3.1 user guide
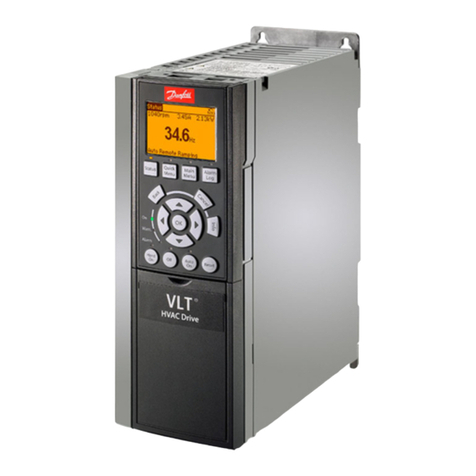
Danfoss
Danfoss VLT PROFIBUS DP MCA 101 Programming guide