Ascon tecnologic CU-02 User manual

sigma
due
Control Unit CU-02
User Manual
M.U. CPU-CB/CU-02-5/14.04
Cod. J30 - 478 - 1A CU02 E

Copyright © 2007, 2014 Ascon Tecnologic Srl
All rights reserved
No part of this document may be stored in a retrieval system, or transmitted in
any form, electronic or mechanical, without prior written permission of Ascon
Tecnologic Srl.
Ascon Tecnologic has used the best care and effort in preparing this manual and
believes that the information contained in this publication is accurate.
As Ascon Tecnologic continues to improve and develop products, the information
contained in this manual may also be subject to change. Ascon Tecnologic
reserves the right to change such information without notice.
Ascon Tecnologic makes no warranty of any kind, expressed or implied, with
regard to the documentation contained in this manual. Ascon Tecnologic shall
not be liable in any event - technical and publishing error or omissions - for any
incidental and consequential damages, in connection with, or arising out of the
use of this manual.
sigmadue
®
, gammadue
®
and deltadue
®
, are trademarks of Ascon Tecnologic Srl.
All other trade names or product names are trademarks or registered trademarks.
Ascon Tecnologic srl
Headquarters:
viale Indipendenza 56,
27029 Vigevano (PV)
Phone: +39 0381 69871
Fax: +39 0381 698730
Internet Site: www.ascontecnologic.com

INDEX
iii
Chapter 1
Hardware description . . . . . . . . . . . . . . . . . . . . . . . . . . . . . . . . . 1
1-1 Architecture . . . . . . . . . . . . . . . . . . . . . . . . . . . . . . . . . . . . . . . . . . . . . 2
1-1-1 Communication ports . . . . . . . . . . . . . . . . . . . . . . . . . . . . . . 2
1-1-2 Auxiliary digital I/O . . . . . . . . . . . . . . . . . . . . . . . . . . . . . . . . 3
1-1-3 Diagnostics LEDs . . . . . . . . . . . . . . . . . . . . . . . . . . . . . . . . . 3
Chapter 2
Installation . . . . . . . . . . . . . . . . . . . . . . . . . . . . . . . . . . . . . . . . . . 5
2-1 Mechanical installation . . . . . . . . . . . . . . . . . . . . . . . . . . . . . . . . . . . . . 5
2-1-1 Installing modules and Removing modules . . . . . . . . . . . . . 5
2-2 Electrical installation . . . . . . . . . . . . . . . . . . . . . . . . . . . . . . . . . . . . . . 5
2-2-1 Connect the communication cables . . . . . . . . . . . . . . . . . . . 5
2-2-2 Connector “A” connections . . . . . . . . . . . . . . . . . . . . . . . . . . 6
Chapter 3
CPU setup . . . . . . . . . . . . . . . . . . . . . . . . . . . . . . . . . . . . . . . . . . 7
3-1 Connection of the CPU Setup Terminal . . . . . . . . . . . . . . . . . . . . . . . . 7
3-1-1 RS232 Serial Communications Connection . . . . . . . . . . . . . 7
3-1-2 USB Serial Communications Connection . . . . . . . . . . . . . . . 8
3-1-3 Setting the Communications Parameters of
the CPU RS232 Service Port . . . . . . . . . . . . . . . . . . . . . . . . 8
3-1-4 Entering the Setup Menu . . . . . . . . . . . . . . . . . . . . . . . . . . . 9
3-2 Main Menu . . . . . . . . . . . . . . . . . . . . . . . . . . . . . . . . . . . . . . . . . . . . . . 10
3-2-1 Network Setup Menu . . . . . . . . . . . . . . . . . . . . . . . . . . . . . . 10
3-2-2 CPU Setup Menu . . . . . . . . . . . . . . . . . . . . . . . . . . . . . . . . . 10
3-2-3 CAN Setup Menu . . . . . . . . . . . . . . . . . . . . . . . . . . . . . . . . . 11
3-2-4 CPU Info Menu . . . . . . . . . . . . . . . . . . . . . . . . . . . . . . . . . . . 12
3-2-5 ETHERNET Setup Menu . . . . . . . . . . . . . . . . . . . . . . . . . . . 12
3-2-6 Serial Setup Menu . . . . . . . . . . . . . . . . . . . . . . . . . . . . . . . . 13
3-2-7 CPU Setup Menu . . . . . . . . . . . . . . . . . . . . . . . . . . . . . . . . . 14
3-2-8 Startup Setup Menu . . . . . . . . . . . . . . . . . . . . . . . . . . . . . . . 14
3-2-9 Persistency Setup Menu . . . . . . . . . . . . . . . . . . . . . . . . . . . . 15
3-2-10 CLOCK Setup Menu . . . . . . . . . . . . . . . . . . . . . . . . . . . . . . . 16
3-2-11 Retain Config . . . . . . . . . . . . . . . . . . . . . . . . . . . . . . . . . . . . 16
3-2-12 Modbus TCP/IP Setup . . . . . . . . . . . . . . . . . . . . . . . . . . . . . 18
3-2-13 Modbus TC/IP Secure ADDRS Table Menu . . . . . . . . . . . . . 19
3-2-14 Modbus TC/IP Priority ADDRS Table Menu . . . . . . . . . . . . . 19

Index (continue)
iv
Chapter 4
Programming the CPU . . . . . . . . . . . . . . . . . . . . . . . . . . . . . . . . 21
4-1 Installing OpenPCS . . . . . . . . . . . . . . . . . . . . . . . . . . . . . . . . . . . . . . . 21
4-1-1 Hardware and Software Requirements . . . . . . . . . . . . . . . . . 21
4-1-2 Installation . . . . . . . . . . . . . . . . . . . . . . . . . . . . . . . . . . . . . . . 21
4-1-3 Starting OpenPCS . . . . . . . . . . . . . . . . . . . . . . . . . . . . . . . . 21
4-1-4 Configuring OpenPCS . . . . . . . . . . . . . . . . . . . . . . . . . . . . . 22
4-2 OpenPCS Setup . . . . . . . . . . . . . . . . . . . . . . . . . . . . . . . . . . . . . . . . . 22
4-3 Communication Ports Protocols . . . . . . . . . . . . . . . . . . . . . . . . . . . . . . 24
4-4 Auxiliary digital port . . . . . . . . . . . . . . . . . . . . . . . . . . . . . . . . . . . . . . . 24
4-5 Watchdog Timer . . . . . . . . . . . . . . . . . . . . . . . . . . . . . . . . . . . . . . . . . . 24
4-6 CANopen Extension for Ascon sigmadue CPU . . . . . . . . . . . . . . . . . . 25
4-6-1 Introduction . . . . . . . . . . . . . . . . . . . . . . . . . . . . . . . . . . . . . . 25
Chapter 5
CPU TFTP File Access . . . . . . . . . . . . . . . . . . . . . . . . . . . . . . . . 27
5-1 TFTP Protocol Access . . . . . . . . . . . . . . . . . . . . . . . . . . . . . . . . . . . . . 27
5-2 IEC61131-3 OpenPCS Runtime Errors log file . . . . . . . . . . . . . . . . . . 28
Chapter 6
Ascon Tecnologic Function Blocks Libraries . . . . . . . . . . . . . 29
6-1 AT_CU02_Cpu_Lib . . . . . . . . . . . . . . . . . . . . . . . . . . . . . . . . . . . . . . . 29
6-2 AT_IO_Modules_Basic_Lib . . . . . . . . . . . . . . . . . . . . . . . . . . . . . . . . . 29
6-3 AT_Generic_Advanced_Lib . . . . . . . . . . . . . . . . . . . . . . . . . . . . . . . . . 30
6-4 AT_Process_Control_Lib . . . . . . . . . . . . . . . . . . . . . . . . . . . . . . . . . . . 31
6-5 AT_Communications_Lib . . . . . . . . . . . . . . . . . . . . . . . . . . . . . . . . . . . 32
6-6 AT_IO_Modules_Adv_Lib . . . . . . . . . . . . . . . . . . . . . . . . . . . . . . . . . . 33
6-7 Firmware Function Blocks List . . . . . . . . . . . . . . . . . . . . . . . . . . . . . . . 34
Appendix A
Reference documents . . . . . . . . . . . . . . . . . . . . . . . . . . . . . . . . . 39

v
Prerequisites
The products described in this manual should be installed, operated and
maintained only by qualified application programmers and software engineers who
are almost familiar with EN 61131-3 concepts of PLC programming, automation
safety topics and applicable national standards.
Using this manual
Specifications within the text of this manual are given in the International System
of Units (SI), with non SI equivalents in parentheses.
Fully Capitalized words within the text indicate markings found on the equipment.
Words
in bold
style within the text indicate markings found in the Configuration Tools.
Warnings, Cautions and Notes are used to emphasize critical instructions:
DANGER!
Indicates an imminently hazardous situation which, if not avoided, will result in
death or serious injury.
WARNING
Indicates a potentially hazardous situation which, if not avoided, could result in
death or serious injury.
Caution
Indicates a potentially hazardous situation which, if not avoided, may result in
minor or moderate injury, or property damage.
Note: Highlights important information about an operating procedure or the equipment.

Sigmadue - sigmaPAC CU-02 - User manual
vi
Current Documentation on the Internet
Make sure you are always working with the latest version of this document.
Ascon Tecnologic Srl reserves the right to make changes to its products in the
name of technological advancement. New manual revisions, when published, and
can be found online at:
http://www.ascontecnologic.com

1
Chapter 1
Hardware description
The system described in this User Manual is mainly composed of three
components:
•Asconsigmadue series CPU (CU-02), ready to work with
OpenPCS EN 61131-3 compliant programming system;
•Asconsigmadue I/O-CB remote I/O series of modules;
• Infoteam OpenPCS programming system.
sigmadue CPU is a powerful processing unit, based on an ARM RISC
processor, different types of memory and several communication ports.
sigmadue
I/O-CB is a complete family of I/O analogue and digital remote
modules with special functions, based on the CANopen protocol over a CAN bus.
Infoteam OpenPCS is a powerful and useful standard programming system for
PLC applications.
It is a clearly structured, easily operated tool for editing, compiling, debugging,
managing and printing PLC applications in all the development phases.
OpenPCS supports EN61131-3 programming under Windows server 2003,
Windows XP SP2 or Windows Vista 32 bit.
Ascon sigmadue line is based on the sigmadue remote I/O system, combining
its functionality with the capabilities of a PLC. The modular concept and the
possibility of fieldbus networking means that you can adapt the system to your
requirements quickly and easily. This gives the sigmadue automation system
an especially economical price/performance ratio.
This User Manual handbook introduces you to work with sigmadue CPU line
and the Infoteam OpenPCS programming system.
It explains how to install the hardware and software, and how to start up the system.
Information on maintenance, troubleshooting and service are also included.

Sigmadue - sigmaPAC CU-02 - User manual
2
1-1 Architecture
From the programmer’s point of view, a complete system is made up as in “Figure
1.1 - Programming the sigmadue Control Unit” below:
Figure 1.1 - Programming the sigmadue Control Unit
In “Figure 1.1 - Programming the sigmadue Control Unit”
the configuration station
(VT100 terminal) and the PC with OpenPCS are displayed as two different
devices, but it is possible to use just one PC to run both OpenPCS and a VT100
emulator (e.g. HyperTerminal).
1-1-1 Communication ports
The CPU has 3 fixed communication ports (see figure 2):
• The CAN port will be used for the connection, through a CANopen network,
to the distributed I/O;
• The Ethernet port (TCP/IP) will be used for the connection, through a LAN
network, to the PC with the Infoteam OpenPCS environment, for:
- Programming, Debuging and commissioning;
- Modbus TCP data exchange;
• The Service RS232 port will be used as:
- Configuration port of the device with VT100 terminal;
- Standard ASCII serial port;
- Modbus RTU data exchange.
In addition to the three mentioned fixed ports, a plug in board can be added (see
Ordering Codes), by which the communication capabilities are increased, e.g.:
• Two channels RS232/485 with Modbus RTU protocol (master or slave);
• Profibus DP (slave).
Pinout of all communication Ports are described hereafter and in the
“CU02 Installation Manual” [6].
Programming
station
Configuration
station
Ethernet 10 Mbit base T
RS232/USB Service port
Input
sensor Output
Power
Controller

Chapter 1 - Hardware Description
3
1-1-2 Auxiliary digital I/O
DI General Purpose Digital Input or RUN/STOP program functionality
ALARM General Fault Relay Output (IEC 61131 Watch Dog function);
WAKE UP Isolated General Purpose Digital Output (can be used, in conjunction
with the Real Time Clock, for unattended applications).
Figure 1.2 - Control Unit I/O and Communication Ports
1-1-3 Diagnostics LEDs
Referring to “Figure 1.2 - Control Unit I/O and Communication Ports” a description
of the LEDs functions is given in the table below.
Table 1.1 - Diagnostics LEDs description
Serial Connector (X1): RS232 or USB
Optional
Communications
expansion port
CAN Connector (X0): CANopen
AConnector
Ethernet
10 Base T
port (X2)
Wake UP
output
terminals (1, 2)
Alarm output
terminals
(3, 4)
Digital
Input
terminal (5)
Power Supply
Terminals
= Ground (6, 7)
= 0V (8, 9)
= +24 Vac/dc (10, 11)
Diagnostics LEDs
•= DI
•= ERR
•= RUN
•= CAN
•= PWR
LED Color Action (note 1) Description
DI Yellow ON Digital Input active
ERR Red ON Error on CANopen network
RUN Green ON Program running (with no errors)
RUN Green OFF Program stop (with no errors)
RUN Green Flickering Back-Up battery low
RUN Green Single flash Error in configuration file, reset to default
RUN Green Blinking Checksum error in VAR RETAIN data
RUN Green Triple flash Checksum error VAR % RETAIN (note 2)
CAN Green ON/OFF RUN LED for CANopen Network
PWR Green ON Power Supply ON

Sigmadue - sigmaPAC CU-02 - User manual
4
Notes: 1. As the ON/OFF sequence of the LEDs has a specific meaning, it is important
that the user recognizes each LED status:
2. The first time some %M variable has been defined as RETAIN (see “Retain
Config Menu” on page 16), the system needs to reboot in order to create the
dedicated files. The error indication will disappear automatically.
Sequence Meaning
OFF the LED is not lit
Steady ON the LED is lit in a stable way
Blinking the LED blinks at a frequence of 2.5 Hz (slow)
Flickering the LED blinks at a frequence of 10 Hz (fast)
Single flash the LED lits once for at least 200 ms
Double flash the LED lits twice with pulses of 200 ms each
Triple flash the LED lits three with pulses of 200 ms each

5
Chapter 2
Installation
2-1 Mechanical installation
The sigmadue Control Unit and the I/O modules are designed to be installed on
standard DIN rails.
As the CPU has, on board, a CAN termination, it must be installed at one end
of the CAN chain.
Up to 127 I/O modules can be connected in chain to each CPU. This value is the
theoretical limit, Ascon spa reccomends to never exceed the number of 32 units.
2-1-1 Installing modules and Removing modules
A complete description on how the modules can be mounted on or removed from
a DIN Rail can be found in the “Control Unit CU-02 Installation Manual”
[6]
.
2-2 Electrical installation
Refer to: “Figure 1.2 -Control Unit I/O and Communication Ports” “Control Unit
CU-02 Installation Manual”[6] for details.
2-2-1 Connect the communication cables
CANopen
remote I/O Port
For CANopen I/O modules connection (
X0
). I/O modules are connected with the
included cables in a daisy chain fashion. The RJ45 type connectors have the pinout:
Serial Port RS232 service port (X1)
The connector X1 on the CPU module is an RJ45 type, with the following pinout:
USB service port (X1)
When installed , the connector X1 on the Contro Unit is a B type USB standard
connector. The pinout of this cable is meaningless as the connection is standard.
Ethernet
10baseT
For OpenPCS development station (X2). The connector on the CPU module is
an RJ45 type, with the following pinout:
Pin 1 2 3 4 5 6 7 8
Signal CANH CANL
CAN-GND
NC NC CAN-SHLD
CAN-GND
CAN-V+
Pin 123 4 5678
Signal NC NC NC GND RX TX NC NC
Pin 1 2 3 4 5 6 7 8
Signal TX+ TX- RX+ NC NC RX- NC NC

Sigmadue - sigmaPAC CU-02 - User manual
6
2-2-2 Connector “A” connections
Power supply Use the 6 poles on the right of the “A” connector and respect the polarity. Each of
these terminals is doubled in order to allow the user to power, using an additional
terminal block, other devices or sensors.
Auxiliary ports The 5 poles on the left of the “A” connector are auxiliary ports.
Wake up Software activated Digital Output. 24Vdc, 0.2A high side power switch,
terminals 1 and 2;
Alarm Relay type digital output. SPST NO 24V, 1A, terminals 3 and 4;
DI 24Vdc digital Input, terminal 6. The return path can be linked to terminal
M- (terminal 8 or 9) or to Wake-Up terminal (teminal 1).
Pin 1234567 8 9 10 11
Name -+ICNOSFE FE M- M- L+ L+
Function WAKE UP ALARM DI F. EARTH POWER SUPPLY
Signal FE FE 0V 0V +24V +24V
Power Supply
Pin 1234 5 67 8 9 10 11
Name -+ICNOSFEFE M- M- L+ L+
Function WAKE UP ALARM DI F. EARTH POWER SUPPLY
Signal COM OUT COM OUT INPUT FE FE 0V 0V +24V +24V
Auxiliary ports

7
Chapter 3
CPU setup
At start-up, the system starts a configuration session to perform the setup of
the CPU devices. The user can insert the CPU setup data using a dumb
VT100 terminal or a Personal Computer with Hyper Terminal program.. In
Appendix B is inserted the tree structure of the setup menus.
3-1 Connection of the CPU Setup Terminal
There are 2 ports available on the CPU to enter the configuration session: the
X0 port for the serial RS232 connection or the LAN port for the ethernet
connection. Depending on the setup method used, the user must:
• Set the X0 or the LAN port (consult the “CU-02 Installation Manual” [9]
for details);
• Provide the proper connection cable;
• Set the correct communications parameters;
• Run the communications program.
3-1-1 RS232 Serial Communications Connection
In order to connect a VT100 terminal or a PC with Hyper Terminal program,
install an RS232 cable having the following characteristics:
Setting the
communications
parameters
At this point the user must configure the HyperTerminal in order to
communicate with the correct COM Serial port. The number of the COM port
linked to the USB connector can be found in:
Start\ControlPanel\System\Hardware\Peripherals\Ports (COM and LPT)
Using the COM port number open a new session of HyperTerminal and set the
default communication parameters for the service port:
Front viewUpper view
Ground (4)
RX (5)
TX (6)
Ground (5)
TX (3)
RX (2)
Pin 1
Pin 5
Pin 6
Pin 9
Front view
CPU side
RJ45 (male) connector
VT100 Terminal side
9 pin sub-D male connector
8
7
6
5
4
3
2
1
8
7
6 TX
5 RX
4 GND
3
2
1
Baud rate 9600
Data 8bit
Stop bit 1
Parity None
Flow Control None

Sigmadue - sigmaPAC CU-02 - User manual
8
3-1-2 USB Serial Communications Connection
Installing
the cable
In order to connect a Personal Computer using the USB (optional) connection, install
an USB standard cable having an USB type “B” connector (CPU side) and an USB
type “A” connector (PC side). This type of cable is standard for the USB connections
and the installation is easy as each connector has only one insertion versus.
Installing the
USB driver
1. In Internet at the address:
http://www.ftdichip.com/Drivers/VCP.htm
locate the FT232B device and download the latest driver for the
Operating System installed on the PC.
2. Connect the USB cable between the CPU and the PC.
3. Install the 2 drivers as explained in the installation manual, first the
one of the USB device, then the driver that links the USB port to a
COM port in the Personal Computer.
Setting the
communications
parameters
Once connected the CPU to the PC with the USB cable, the user must configure
the HyperTerminal in order to communicate with the USB port. The number of the
COM port linked to the USB connector can be found in:
Start\ControlPanel\System\Hardware\Peripherals\Ports (COM and LPT)
(locate the “USB to COM # ” entry). Using the COM port number open a new
session of HyperTerminal and set the default communication parameters for the
service port:
3-1-3 Setting the Communications Parameters of the CPU RS232 Service Port
The default configuration for the Service RS232 port is:
During the configuration session it will be possible to change the baudrate, stop bit
and parity. When the communications parameters of the CPU are changed, the
communications parameters of the terminal (or PC) must be changed accordingly.
The setup is performed by browsing the menus sent to the VT100 terminal or to
the terminal emulation program (HyperTerminal) by the CPU.
PC side
USB Type A Connector
CPU side
USB Type B Connector
Baud rate 9600
Data 8bit
Stop bit 1
Parity None
Flow Control None
Baud rate 9600
Data 8bit
Stop bit 1
Parity None
Flow Control None

Chapter 3 - CPU Setup
9
3-1-4 Entering the Setup Menu
The two types of CPU (RS232 and USB) have activation modes of CPU setup pro-
gram that differ for few actions.
• For a RS232 service port CPU, it is enought to run the HyperTerminal pro-
gram using the correct configuration file and pressing the connect button.
• In case an USB service port CPU, after having installed and configured
the USB driver and HyperTerminal, the user must:
1. Run the HyperTerminal program using the correct configuration file;
2. Power on the sigmadue CPU;
3. Wait for the audio notification that means that the Personal
Computer has recognized and installed the “USB to COM” Driver;
4. Press the connect button (☎).
Accessing the
Main Menu
This procedure is valid for both the types of CPU (RS232 and USB). To start the
setup session, press the ENTER (the PC sends a CR character to the CPU) key on
the setup terminal
while CAN and ERR LEDs are blinking on the CPU
. If the
character CR is not sent before a predefined time (start-up timeout) the system ends
the configuration session and starts the PLC application. In this chapter some
templates of a configuration session made with Windows Hyper Terminal are shown.
After the reception of the first CR character, the welcome screen appears.
Press ENTER again to reach the configuration session Main Menu.
Main Menu
Figure 3.1 - CPU configuration Main Menu
Please note that the system has a further timeout that controls the life of the
configuration session; this is the inactivity timeout. If the user does not work with
the console for a time greater than this timeout, the configuration session will be
automatically stopped and the PLC application will be started.
Both the described timeouts can be set during the configuration. The user should
not set too short timeouts, thus preventing the possibility to work with the
configuration console. To select an item of a menu or to insert a value for a
parameter, the user has to type the corresponding number and than press ENTER.
AAA SSS CCCCCC OOOOOO NNNNNNNNNNNNN
AAA SSS CCCCCCCCCCCC OOOOOOOOOO NNNNNNNNNNNNNN
AAA SSS CCCC CCC OOO OOO NNN NNN
AAA SSSS CCCC OOO OOONNN NNN
A AAA SSSS CCC OOO OOONNN NNN
AAA AAA SSSS CCC OOO OOONNN NNN
AAA AAA SSSS CCC OOO OOONNN NNN
AAA AAA SSSSCCC CCOOO OOONNN NNN
AAA AAA SSCCC CCCOOO OOONNN NNN
AAA AAA SSSCCC CCCC OOO OOO NNN NNN
AAAAAAAAAAAASSSSSSSSSSSS CCCCCCCCCCC OOOOOOOOOO NNN NNN
AAAAAAAAASSSSSSSSSSSS CCCCCCC OOOOOO NNN NNN
Press Enter to Continue_
Ascon S.p.a.
SigmaPAC Control Unit CU-02
Device configuration
MAIN MENU
1. Network Setup
2. Cpu Setup
3. Modbus TCP/IP Setup
4. Cpu info
5. Exit
Enter Selection:

Sigmadue - sigmaPAC CU-02 - User manual
10
3-2 Main Menu
As in Figure 3.1 - CPU configuration Main Menu, the Main menu has four sub
menu selections:
Network Setup:
To set the parameters of all the communication ports in the
CPU;
CPU Setup:
To set some parameter of the CPU;
Modbus TCP/IP Setup:
Where the user can set the “priority connection pool” and
the “security address pool”. Moreover the user can set the
number of messages per cycle and the “broken connection
timeout”.
CPU info:
To see the release values of the FW, HW of the actual CPU;
Exit:
To exit this menu and end the configuration session.
3-2-1 Network Setup Menu
Figure 3.2 - Network Setup Menu
CAN Setup:
To set the parameters for the CAN port;
Ethernet Setup:
To set the parameters for the Ethernet port;
Serial Setup:
To set the parameters for the RS232 port;
Exit:
To exit this menu and return to the previous menu.
3-2-2 CPU Setup Menu
Figure 3.3 - Figure 5 - CPU Setup Menu
Startup Timeout Setup:
To set the startup timeouts;
Persistency Setup:
To set the parameters that control the saving of PLC pro-
gram in the retentive memory;
CLOCK Setup:
T
o set the parameters of the CPU real time clock;
Retain Config Retentive Registers Configuration;
Exit:
To exit this menu and return to the previous menu.
Network setup menu
1. CAN Setup
2. Ethernet Setup
3. Serial Setup
4. Exit
Enter Selection:
Ascon S.p.a.
SigmaPAC Control Unit CU-02
Device configuration
CPU SETUP MENU
1. Startup Setup
2. Persistency Setup
3. Clock Setup
4. Retain Config
5. Exit
Enter Selection:
Ascon S.p.a.
SigmaPAC Control Unit CU-02
Device configuration

Chapter 3 - CPU Setup
11
3-2-3 CAN Setup Menu
Figure 3.4 - Figure 6 - CAN Setup Menu
CAN Baudrate
:
To set the baud rate for the CAN network. The correspondence
between the baud rate and the number of this item is indicated in Table
3.1 - CAN Network speed (note).
Table 3.1 - CAN Network speed
CAN node ID:
To set the Node-ID of the CPU in the CAN network;
Diagnostic:
It is possible to work with Heartbeat protocol (default) that allows the
CPU to receive a message from every node that is in the network or it
is possile to select the Node Guarding protocol (1) in order to set the
CPU to send and receive an “Alive message” from every node of the
network and let the CPU and the nodes to understand if they are
working well or there is a problem.
Enable Sync:
It is possible to set the Sync communications (process data objects
on the CAN network are exchanged when a sync message occours).
Sync time:
Generation time in millisecond of the sync message.
Exit:
To exit this menu and return to the previous menu.
To change the value of an item the user must select the item number pressing the
correnspondig item digit on the keyboard and press ENTER. The screen will then
change, asking the user to “Insert new value:”.
Note: Value 0 (10kbps) is not currently supported by sigmadue I/O modules.
VALUE 0124567 8
Speed kbps 10 20 50 125 250 500 800 1000
CAN SETUP MENU
1. CAN Baudrate (0..2; 4..8): 1 (20kBps)
2. CAN Node-ID: 32
3. Diagnostics (0..1): (1) Node Guarding
4. Enable Sync (0..1): DISABLED
5. Sync Time (0..1000000ms): 0
6. Exit
Enter Selection:
Ascon S.p.a.
SigmaPAC Control Unit CU-02
Device configuration

Sigmadue - sigmaPAC CU-02 - User manual
12
3-2-4 CPU Info Menu
Figure 3.5 - CPU Info
HW version:
Revision of the CPU Hadrware;
FW version:
Revision of the CPU Firmware;
OEM ID:
ASCON code for the runtme Software;
V.MACHINE:
Version of the runtime Software (5-3-2)
PLC-Status:
In this field is pointed out the CPU status:
Table 3.2 - Error codes that can be displayed in “CPU Info” screen.
Entering 1 and pressing the return key, the user acqnowledges the
alarms active displayed by “CPU Info” screen.
Exit:
To Exit this menu and return to the previous menu.
3-2-5 ETHERNET Setup Menu
Figure 3.6 - Ethernet Setup Menu
MAC Address:
To display the MAC address;
IP Address:
To set the IP Address of the device;
Subnet Mask:
To set the subnet mask of the device;
VALUE Meaning
0 Normal status
1 Data Configuration Error (DCE)
2 Retain Error (RE)
3 Data Configuration Errorr + Retain Error (DCE + RE)
4 Battery Low (BL)
5 Battery Low + Data Configuration Error (BL + DCE)
6 Battery Low + Retain Error (BL + RE)
7 Battery Low + Retain Error + Data Configuration Error
(BL + RE +DCE)
CPU INFO
HW Version: 3.0
FW Version: 3.0
OEM-ID: 536
Virtual Machine: 5.3-2
1) PLC-Status: 0
2) Exit
Enter Selection:
Ascon S.p.a.
SigmaPAC Control Unit CU-02
Device configuration
ETHERNET SETUP MENU
1. MAC Address: 00:50:c2:47:60:6e
2. IP Address: 192.168.5.11
3. Subnet Mask: 255.255.255.0
4. Gateway Address: 192.168.5.110
5. Server Address: 192.168.5.110
6. DHCP: DISABLED
7. Port: 1200
8. Exit
Enter Selection:
Ascon S.p.a.
SigmaPAC Control Unit CU-02
Device configuration

Chapter 3 - CPU Setup
13
Gateway Address:
To set the Gateway Address of the device;
Server Address:
To set the Server Address of the device;
DHCP:
To enable or disable DHCP Client on the device;
Port:
To set the Port for the connection with OpenPCS;
Exit:
To exit this menu and return to the previous one.
To set items 2, 3, 4 and 5, the user must digit on the keyboard the menu item
number and press ENTER. The screen will then change, asking the user to “insert
new value:”. When the system displays the “insert new value:” message the user
can enter the new values in number and dot notation.
To set DHCP value select item 6 and set 0 to DISABLE or 1 to ENABLE. To set the
Port, select item 7 and enter the desired value.
WARNING Please note that items 2, 4 and 5 MUST have the same subnet in order to avoid communications
problems.
3-2-6 Serial Setup Menu
Figure 3.7 - Serial Setup Menu
Baudrate:
This choice allows the user to set the baud rate for the RS232 commu-
nications port. The correspondence between the baud rate and the
item number is specified in Table 3.3 - Serial Port Speed:
Table 3.3 - Serial Port Speed
Parity:
To set the parity for the RS232 communication port, according to Table
3.4 - Parity;
Table 3.4 - Parity
Stop Bit:
To set the number of stop bits for the RS232 communications. Valid val-
ues are1 or 2;
Exit:
To exit this menu and return to the previous one.
To change the value of an item, the user has to select the item number and press
ENTER. The screen will then change, asking the user to “Insert new value:”.
VALUE 012345
Speed bps 2400 4800 9600 19200 38400 57600
VALUE 0 1 2
Parity NONE EVEN ODD
SERIAL SETUP MENU
1. Baudrate: 2, (9600bps)
2. Parity: 0 (NO PARITY)
3. Stop Bit: 1
4. Exit
Enter Selection:
Ascon S.p.a.
SigmaPAC Control Unit CU-02
Device configuration

Sigmadue - sigmaPAC CU-02 - User manual
14
3-2-7 CPU Setup Menu
Figure 3.8 - CPU Setup Menu
Startup Timeout Setup:
To set the startup timeouts;
Persistency Setup:
To set the parameters that control the saving of PLC pro-
gram in the retentive memory;
CLOCK Setup:
To set the parameters of the CPU real time clock;
Exit:
To exit this menu and return to the previous menu.
3-2-8 Startup Setup Menu
Figure 3.9 - Startup Setup Menu
Startup Timeout:
To set the Startup Timeout;
Inactivity Timeout:
To set the Inactivity Timeout;
DO1 used by watchdog
If enabled, the digital output DO1 could be connected to
a software function block to signal a watchdog event
Exit:
To exit this menu and return to the previous one;
To change the value of an item, the user has to select the item number and press
ENTER. The screen will then change, asking the user to “insert new value:”.
CPU SETUP MENU
1. Startup Timeout Setup
2. Persistency Setup
3. Clock Setup
4. Exit
Enter Selection:
Ascon S.p.a.
SigmaPAC Control Unit CU-02
Device configuration
STARTUP TIMEOUT MENU
Ascon S.p.a.
SigmaPAC Control Unit CU-02
Device configuration
1. Startup Timeout (2..120s): 10
2. Inactivity Timeout (2..120s): 30
3. DO1 used for watchdog (0..1): Disabled
4. Exit
Enter Selection:
Table of contents
Other Ascon tecnologic Control Unit manuals
Popular Control Unit manuals by other brands
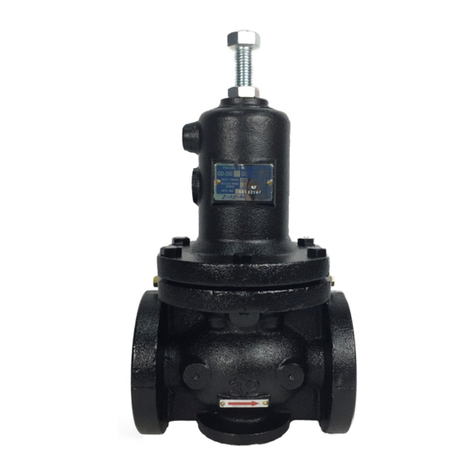
Yoshitake
Yoshitake GD-200 Series manual
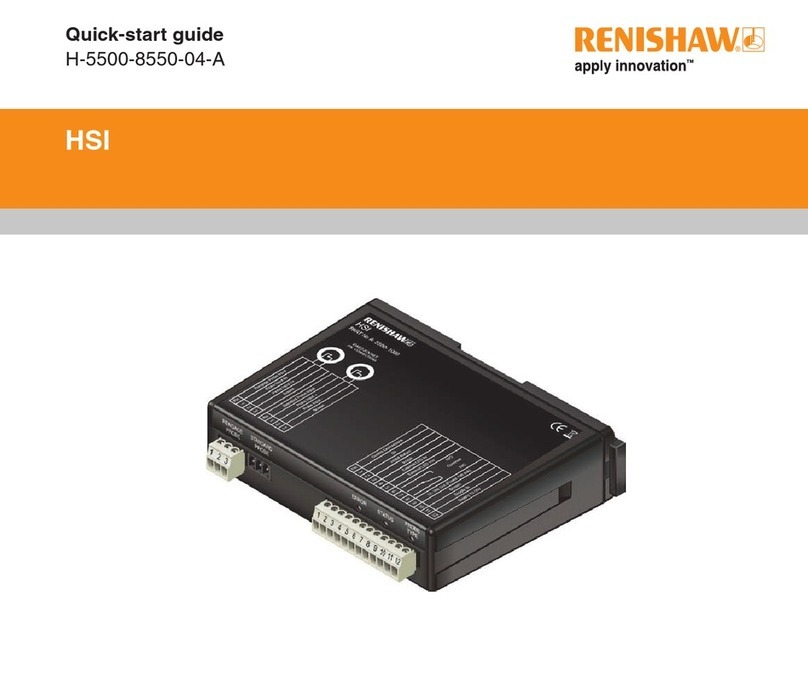
Renishaw
Renishaw HSI quick start guide
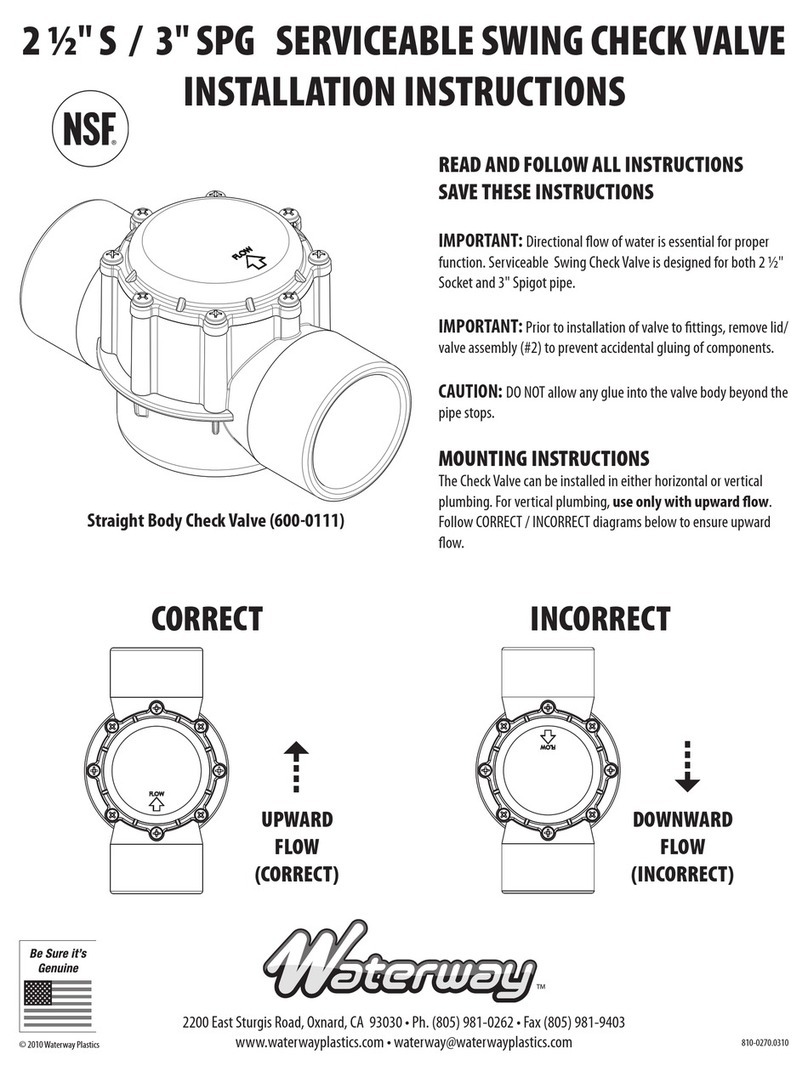
Waterway
Waterway 600-0111 installation instructions
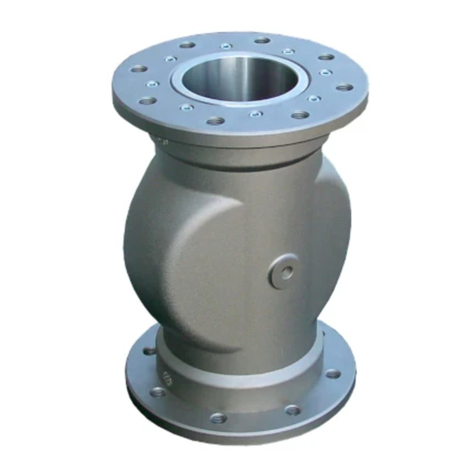
WAMGROUP
WAMGROUP TOREX VM Series Assembly and main instructions for use and maintenance
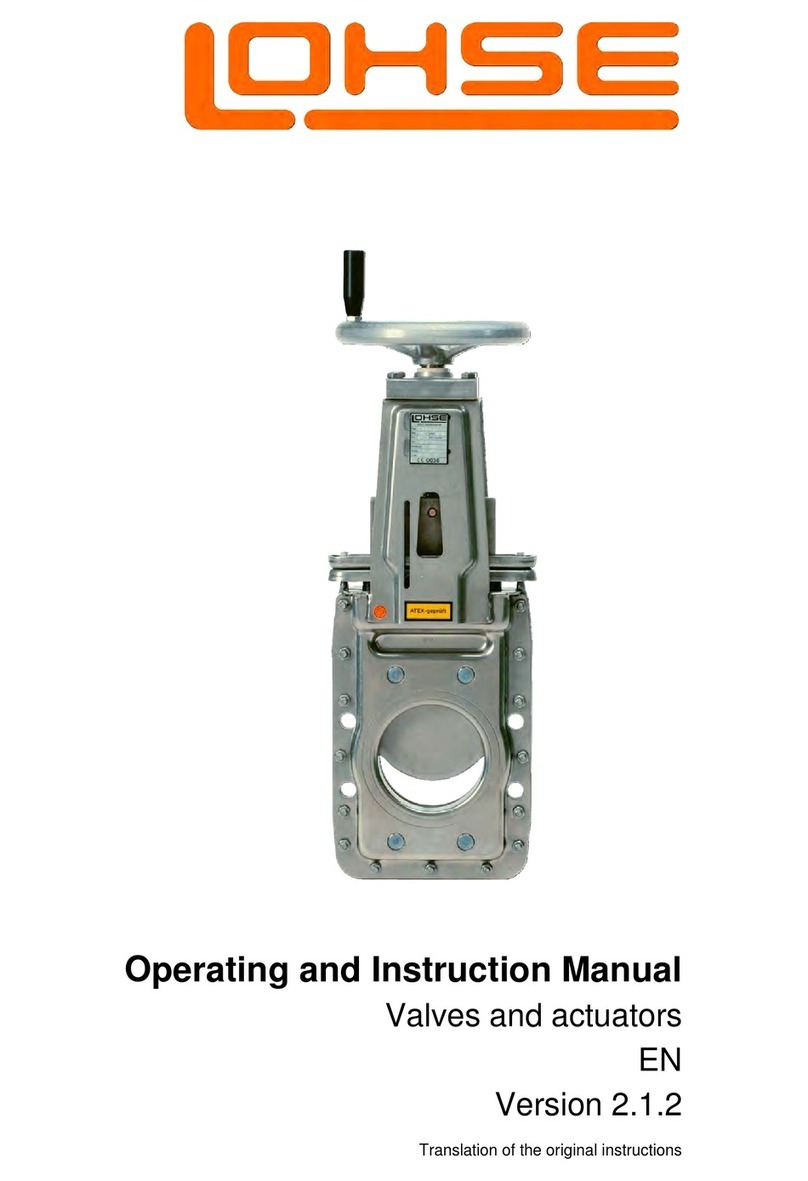
LOHSE
LOHSE CNA Series Operating and instruction manual

IFM Electronic
IFM Electronic Ecomat 300 AC2618 operating instructions