Axiom Precision AUTO ROUTE PRO V5 User manual

AUTO ROUTE PRO V5 MANUAL
©Axiom Tool Group, Inc. All rights reserved. Rev. 2/28/2020


2 | Axiom Tool Group
Section Page
1. Safety Information 4
2. Emergency Switch Padlock 7
3. Router specifications 8
4. Glossary of terms 9
5. Setup and Assembly
5.1. Packaging Contents 12
5.2. Stand assembly 13
5.3. Installing Router 15
5.4. Finishing Machine Assembly 16
6. Electrical Connections
6.1. Grounding instructions 17
6.2. Extension cords 17
7. Operations
7.1. Operating procedure 19
7.2. HOME Position 19
7.3. Moving Router (Spindle Head) 20
7.4. Setting Work Origin 21
7.5. Setting Spindle RPM 23
7.6. Processing a File (Running a Toolpath) 23
7.6.1. Speed Scale Adjustment 24
7.6.2. Pausing During a Toolpath 24
7.6.3. Setting a Breakpoint 24
7.7. Power Failure 25
8. Spoil Board Surfacing
8.1. Setup and Operation 26
8.2. Job Setup Sheet 28
9. RichAuto B18 Functions
9.1. Basic Keypad Operations 29
9.2. Common Combination Keypad Functions 30
10. Advanced Processing
10.1. Array 30
10.2. Resume (from Breakpoint) 30
10.3. Mirror 30
10.4. Tool Changing 31
10.5. Stop State 31
10.6. Part Work 32
10.7. Calculating Boundaries 32
10.8. Auto Center 32
10.9. Mill Plane 33
10.10. Calculate Work Time 33
10.11. Find Break Number 33
10.12. Scale Work 34
10.13. Step Work 34
Table of Contents

3 | Axiom Tool Group
11. Optional Rotary 4th Axis Kit
11.1. Post Processor 35
11.2. Unboxing and Assembly 36
11.3. Job Setup 39
11.4. Required Controller Changes 40
12. Data Restoration and Updates
12.1. Restore/Backup Data 43
12.2. System Updates 44
13. Controller Menu Layout
13.1. Machine Setup 45
13.2. Auto Pro Setup 46
13.3. System Setup 46
13.4. Operate File 47
13.5. Version View 47
14. Maintenance
14.1. Routine Checks 48
14.2. Cooling System 49
14.3. Bearing Service 51
15. Troubleshooting
15.1. Mechanical and Electrical Problems 53
15.2. Controller function Problems 54
16. Wiring Schematics
16.1. 26 Pin Cable Connector Diagram 56
16.2. 7 Pin Cable Connector Diagram 57
16.3. RichAuto DSP Connection Diagram 58
17. Parts Diagram and Manual
17.1. V5 Machine Exploded View #1 59
17.2. V5 Machine Exploded View #2 60
17.3. Parts List 61
18. Warranty 64
19. Contact Us 65

4 | Axiom Tool Group
Axiom Tool Group, Inc. has provided this manual covering the safe operation and maintenance procedures
for the AutoRoute™ Pro V5 series machines. Contained in the manual are installation instructions, safety
precautions, operational procedures and maintenance guidelines.
The instructions set forth in this document, will ensure that the AutoRoute™ machine will provide
consistent, long-term operation.
This manual was not intended to cover every facet of machine operation. The use of jigs, fixtures, after
market CNC accessories, choice of materials and tooling may require additional research. Online forums, and
CNC blogs are a good source of knowledge from experienced users.
Regardless of the methods in place, personal safety is always a priority.
If you have any questions or comments, please email the Axiom Precision Customer Service team at
The AutoRoute™ is an electrical appliance and precision machine. Protect yourself and your investment. Read and
understand the entire owner's manual before attempting assembly or operation. Read and understand the warnings
posted on the machine and in this manual. Failure to comply with all the warnings may cause serious personal injury
or costly damage to your AutoRoute™.
This AutoRoute™ CNC machine is designed and intended for use by properly trained and experienced personnel only.
If you are not familiar with the proper and safe operation of a CNC machine, do not use the AutoRoute™ until proper
training and knowledge have been obtained.
Your AutoRoute™ machine is intended for cutting wood, acrylics, wood-fiber composites, certain plastics and non-
ferrous metals. Do not use this machine for other than its intended use. If used for other purposes, Axiom disclaims
any real or implied warranty and holds itself harmless from any injury that may result from that use.
Shop Environment
1. Ensure that the floor can bear the weight of the machine and work pieces mounted on it.
2. Keep the floor around the machine clean and free of scrap material, oil and grease.
3. Do not lean lumber or other heavy materials against the gantry, guide rails or table.
4. Support the weight of the dust hose attached to the dust shoe accessory to prevent the weight of the hose
from dislodging the dust shoe. Ensure that there is sufficient slack in the dust collection hose to allow the
spindle to cover the entire work area.
5. Locate the AutoRoute™ away from overhead pipes and plumbing fixtures to prevent condensation from
dripping on to the spoil boards and control system components.
6. Locate the AutoRoute™ away from sinks, faucets or other water supplies or storage to prevent splash-out
that can damage the spoil boards and control system components.
7. Do not operate in a dangerous environment. Do not use the machine in damp or wet locations or expose to
them to rain. Keep all work areas well lighted.
8. Provide adequate room between the AutoRoute™ and other machines in the shop to reduce the chance of
accidental jarring when transporting lumber or other heavy materials through the shop and while materials
are being worked on other machines.
9. Ensure adequate space between machines to allow for the possibility that the work piece will extend over
the end of the AutoRoute™ table.
10. Do not overreach. Be sure to keep proper footing and balance at all times.
Safety Information

5 | Axiom Tool Group
Health and Safety
11. Always wear approved personal health and safety equipment as indicated for the materials and type of
operations that will be performed. These should include a dust mask, hearing protection, safety clothing,
and safety glasses/face shield. Do not rely on prescription or over-the-counter eyeglasses; they are not
safety glasses. Wear ear protectors (plugs or muffs) even during short periods of operation.
12. Before operating this machine; remove any hand, wrist, and neck jewelry and roll sleeves up past the
elbows. Be sure to not wear loose clothing which may become caught in the machine and confine long hair.
a. Non-slip footwear or anti-skid floor strips are recommended.
13. Use a dust mask or other safeguards to avoid inhaling dust generated from wood products. Install dust
collection equipment consistent with shop ventilation practices and budget. Remove dust and debris from
the floor frequently to prevent slipping. Drilling, sawing, sanding or machining wood products generates
wood dust and other substances known to the State of California to cause cancer. Wood products also emit
chemicals known to the State of California to cause birth defects or other reproductive harm. (California
Health and Safety Code Section 56).
14. In addition to other health hazards, dust from wood and other materials is flammable. Do not operate
welding, wood burning, smelting, soldering or other high-heat tools on the AutoRoute™ table or vicinity.
15. Do not operate this machine while tired or under the influence of drugs, alcohol or any medication.
16. Make workshop kid proof through the use of padlocks, master switches and/or by removing starter keys.
Electrical
17. Make certain the switch is in the OFF position before connecting the machine to the power supply.
18. Make certain the machine is properly grounded and the circuit is protected with a fuse or circuit breaker in
accordance with local codes. Install a separate circuit if necessary to limit power loss when multiple
machines in your shop are operating simultaneously. If necessary, place a cover on the outlet to prevent
accidental disconnection.
19. Perform all machine adjustments or maintenance with the machine unplugged from the power source.
20. Follow effective lockout procedures to reduce the risk from high voltage wires and components and to
prevent intentional bypassing of safety controls and accidental operation.
21. Don’t use in a damp or wet location, or expose to rain, fog or snow.
22. Keep the electrical cord away from sharp edges, heat or moving parts, and do not store materials on top of
it. Position the cord so it will not become a tripping hazard.
23. While the use of an extension cord is discouraged, it is recognized that the wiring layout of the shop may not
allow the placement of the AutoRoute™ directly next to an outlet. If it is necessary to use an extension cord,
make sure the extension cord is in good condition, heavy enough to carry the current requirements, and
installed to prevent a tripping hazard. An undersized cord will cause a reduction in voltage resulting in loss of
power and overheating which may result in fire or electrical shock.

6 | Axiom Tool Group
Other Safeguards
24. Remove and store adjusting keys and wrenches before turning on the power. If necessary for visibility, apply
safety markings to adjusting wrenches and keys.
25. Install safety guards consistent with general shop safety practices. Keep safety guards in place at all times
when the machine is in use. If removed for maintenance purposes, use extreme caution and replace the
guards immediately after completion of maintenance.
26. Check damaged parts immediately. Before further use of the machine, a guard or other part that is damaged
should be carefully checked to determine that it will operate properly and perform its intended function.
27. Keep visitors a safe distance from the work area. Keep children away.
28. Control liquids in your shop to limit the possibility of spillage that can damage the AutoRoute™ which can
cause damage or personal injury from electric shock or fire. Be careful with storage and use of cleaning
fluids, finishes and solvents. Never use the table to apply or dry finishes.
Operational Practice
29. Never leave the machine running unattended. Always be in close reach of the emergency stop button.
30. Turn the power off and do not leave the machine until it comes to a complete stop.
31. Avoid pinch points and entanglement hazards. Keep hands and clothing away from the ball screws, thrust
bearings, gantry, guide rails and rotating cutting tool while in operation.
32. Use the right tool at the correct speed and feed rate. Do not force a tool or attachment to do a job for which
it was not designed. The right tool will do the job better and more safely.
33. Do not touch a cutting tool immediately after use. It will be hot and may cause skin burns. Exercise caution
when handling the collet and spindle nut if the cutting tool is hot. Keep a heavy glove or oven mitt on hand
for the purpose.
34. Do not lay a hot cutting tool on its side. Create a rack for cooling off hot cutting tools.
35. Use recommended accessories; improper accessories may be hazardous.
36. Do not use dull, gummy, or damaged cutting tools. Keep bits and other cutting tools clean and sharp for best
and safest performance.
37. Turn off the machine before cleaning. Use a vacuum, brush or compressed air to remove chips or debris. Do
not use hands.
38. Do not climb or stand on the machine. Serious personal injury and costly damage could occur if the machine
tips over or the gantry is dislodged.
39. Remove loose items and unnecessary work pieces from the table before starting the machine.
40. Plan tool paths to make multiple passes rather than to take off a large amount of material at one time. This
will reduce mechanical stress and heat on cutting tools.
41. Always secure a work piece to the spoil board using clamps, vacuum, or double-sided tape. If the work piece
is mounted in a fixture or optional 4th Axis Rotary, ensure that all locks or clamps are securely fastened
before operating. Never hold a work piece down by hand while operating.
42. Inspect the material of the workpiece to detect any defects, do not mount a split workpiece or one
containing a knot that may result in the ejection of large pieces of scrap material.
43. When operating the optional 4th Axis Rotary kit, manually rotate all material to ensure that it rotates freely
with no mechanical interference before operating the toolpath.
44. Make sure the work piece is free from nails, hardware, or other foreign objects.
45. After installing a cutting tool, make sure the collet is securely tightened. An unsecured cutting tool may fly
loose from the collet and cause injury. Be sure that the adjusting wrenches have been removed and are
secured before turning on the power.

7 | Axiom Tool Group
To avoid accidental or unintended use by young children or others not qualified to use the tool, the use of a
padlock is required.
WARNING: FOR YOUR OWN SAFETY READ INSTRUCTION MANUAL
BEFORE OPERATING TOOL:
To lock out an Emergency switch:
1. Open the padlock.
2. Insert through hole in the
emergency switch (need
depress this button).
3. Close the padlock.
4. Place the KEY in a safe place
out of the reach of children.
Emergency Switch Padlock

8 | Axiom Tool Group
1
• Supports the standard G code, PLT format instructions; supports domestic and international mainstream CAM software, such
as: Type3, Art cam, UG, Pro / E, Master CAM, Cimatron, Wentai etc.
• Comes with USB communications port, file transfer efficiency can be directly read U disk, card reader file, Plug and Play.
AutoRoute:
4 Pro
V5
6 Pro
V5
8 Pro
V5
X Axis Travel
24" (610mm)
•
•
•
Y Axis Travel
24" (610mm)
•
36" (910mm)
•
48" (1210mm)
•
Z Axis Travel
6" (150mm)
•
•
•
Table Work Area
39.17" x 28.39" (995mm x 721mm)
•
51.18"x 28.39" (1300mm x 721mm)
•
62.99" x 28.39" (1600mm x 721mm)
•
Collet
ER-20
•
•
•
Collet Chuck
1/4" and 1/2" Included
•
•
•
High Speed Spindle
3 HP 2.2kW/7.5A Electro Spindle
•
•
•
Spindle Speed
0~24000 RPM
•
•
•
Max. Rec. Feed-Rate
200 IPM
•
•
•
Precision Linear Guide Rails
X/Y/Z Axis
•
•
•
Precision Ball Screw
X/Y/Z Axis
•
•
•
Power Requirements
115 V, 60Hz, 15A Single Phase
220V, 560 Hz, 10A Single Phase
•
•
•
Working Table
High Rigidity Interlocking Aluminum
•
•
•
Integrated MDF Spoil Board
•
•
•
Gantry Bridge
High Rigidity Aluminum Extrusion
•
•
•
Gantry Support
Gravity Cast Aluminum Alloy
•
•
•
Gantry Clearance
6.5" (165mm)
•
•
•
Machine Base
Welded Structural Steel Frame
•
•
•
Machine Footprint
35" x 30" (890mm x 770mm)
•
47" x 30" (1197mm x 770mm)
•
58.85" x 30" (1495mm x 770mm)
•
Required Floor Space
39.17" x 37.36" (995mm x 949mm)
•
51.18" x 37.36" (1300mm x 949mm)
•
62.99" x 37.36" (1600mm x 949mm)
•
Max. Machine Height
30.27" (769mm)
•
•
•
Machine Weight
130lbs (60kg)
320lbs (145kg)
•
360lbs (164kg)
•
405lbs (184kg)
•
Tool Touch Off Puck
Standard Accessory
•
•
•
Integrated Liquid Cooling System
Standard Accessory
•
•
•
Controller1
RichAuto B18 DSP
•
•
•
Specifications

9 | Axiom Tool Group
4th Axis – An accessory that enables the CNC to operate as a lathe.
Axis – Direction of movement. On a three-axis machine: X (left-right), Y (front-back) & Z (up-down).
Array Work – Division of the machine work surface into square or rectangular work spaces so that the toolpath can
be ran in each space to produce several identical profiles.
Ball End (Ball Nose) – A cutting tool that has a rounded cutting arc, where the arc diameter is equal to the cutting
diameter.
Ball-screw – Drive system component. The ball-screw is rotated by the stepper motor and provided the means for
moving the gantry and spindle along the axes.
Bed – The Bed of the CNC consists of a welded steel frame and an extruded aluminum table top, tongue and groove
table top with integrated T-slots.
Breakpoint – The point in a toolpath file where a break is created. In a job file, a breakpoint will allow you to stop
work and save a location to resume from later.
CAD – Computer aided design using software to assist in designs
CAM – Computer aided manufacturing using software to define toolpaths and assist in manufacturing processes.
Chip Load – Chip load is the measure of the thickness of a chip a cutter will cut.
CNC – Computer numerical control
Climb Cut – Refers to the relationship of the cutting tool rotation to the direction of feed. A climb cut deflects the
cutting away from the cut, with the direction of the feed.
Collet – A metal collar that holds the cutting tool within a spindle nut.
Conventional Cut – Refers to the relationship of the cutting tool rotation to the direction of feed. A conventional cut
deflects the toward the cut, against the direction of the feed.
Compression Bit – A cutting tool with a combination of up and down shear cutting edges. Typically used for cutting
laminate material to prevent tear-out on both sides of the sheet.
Deflection – Tool deflection occurs when the spindle speed and feed rate exert sufficient force to deflect the cutting
tool. Deflection leads to excessive wear and chatter which can shorten tool life and will leave unwanted tooling
marks on the material.
Down-Shear Bit – A cutting tool whose edges carve downward on the face of the toolpath. Reduces the potential for
tear-out but requires a slower feed-rate.
Drag Knife – A cutting tool that holds a razor or knife blade used to cut and inscribe material. Used with spindle or
router motors turned off, and freely spins as it follows the direction of the tool-path.
Dust Shoe – An accessory which aids in dust collection by limiting the spread of dust and debris by channeling the air
flow through an attached dust collection system.
End-Mill – A cutting tool with a straight end, typically with a spiral flute(s). It creates a channel with a flat bottom
perpendicular to the sides.
Feed and Speed – A combination of factors that must be set to control the work performed by the cutting tool.
Definitions

10 | Axiom Tool Group
Feed-rate – The speed at which the cutting tool moves along a work piece.
Flute Length – The length of the cutting portion on a router bit or cutting tool.
Flutes – The cutting edges or inserts of a router bit or cutting tool.
Finish Cut – A 3D tool-path the reduces or eliminates the irregular contours left by the rough cut.
Form Bit – A bit that carves a standard profile such as a round over, ogee or similar contours.
Gantry – The frame structure that straddles the bed and carries the spindle. It moves on guide rails along the length
of the bed and is driven by the ball-screw system.
Gantry Bridge – The part of the gantry that lies between the upright towers. The upper bridge carries the spindle
and cooling system. The lower bridge supports the weight of the gantry and affixes directly to the Y axis ball-screw.
Gantry Upright (Towers) – Parts of the gantry that extend upward, supporting the upper gantry bridge.
G-Code – A machine language that uses axis points and commands which the machine uses to move and perform
functions.
Grid – The minimal movement units of the router. The router head automatically moves to the next grid position
when the directional button is toggled in either continuous or step mode.
HHC – The handheld controller component of the control system.
Hold-down – A clamp or other such device used to firmly hold a workpiece or fixture to the table. Includes clamps,
double-sided tape, vacuum pods and others.
Home Position – Mechanical point set using magnetic limits switches.
Origin – User designated zero point for the work piece. From which the router will reference the positioning of all
cutting.
Plunge – The distance on the Z axis that the spindle and cutting tool moves toward, into, or along the material.
Plunge Rate – The speed of descent of the spindle on the Z axis.
Pocket Tool-path – A tool-path that creates a cavity in the horizontal surface of a work piece.
Post Processor – A software function that enables the CAD/CAM application to format G-Code enabling the control
system of a CNC to follow the designated tool-paths.
Profile Tool-path – A tool paths that cuts along the profile of a set of vectors. Typically used to cut out the shape of a
design.
Proximity Switch – A magnetic limit switch that is used to find the HOME position.
Restore Point – The point along a tool-path where the spindle will start to resume a tool-path following a break.
Rough Cut – A 3D toolpath where the initial cut is designed to remove unwanted material, leaving a rough contour.
Soft Limits – Limits on movement availability. Imposed by the work space boundaries and based on controller
settings and the location of HOME. An “out of soft limits error” implies that based on the positioning of the
workpiece, there is not enough room to move in a designated direction.
Speed Scale – Allows for the reduction of the feed-rate at the beginning of a tool-path to reduce the stress on a
cutting tool as it first contacts the material.
Spindle Speed – Rotational speed of cutting tool (RPM).

11 | Axiom Tool Group
Step Down – Distance in Z-axis that the cutting tool plunges into the material.
Step-over – The amount the cutting tool moves away from the previous cutting path as it routes the new path.
Stepper Motor – DC motor that moves in very precise steps upon the receipt of “pulses”, which result in very
accurate positioning and speed control.
Surfacing – The process of leveling the surface of the spoil boards so that they are perpendicular to the spindle.
Tool-path – User defined route which the cutter follows to machine a workpiece.
Touch-Off Puck – A device used to set the zero point (Origin) for the Z axis.
U-Disk – External data storage device that is inserted into a USB interface.
Up-Shear Bit – A cutting tool whose edges carve upward along the face of the toolpath. Increases the potential for
tear-out but allows for a slightly higher feed-rate.
VFD – Variable Frequency Drive which controls the speed (RPM) of the spindle. Enables the fine tuning of the spindle
during the operation of a tool-path.
Working Envelope – The three-dimensional area that the spindle can travel within while cutting or milling.

12 | Axiom Tool Group
Failure to read and understand all the assembly and setup instructions before attempting assembly may result in
serious injury.
Packaging contents for the Axiom Precision Stand.
2-Stand upright (front & back)
2-Cross braces
1-Lower shelf plate
1-Stand hardware package
Hardware package contains:
4-Swivel casters
4-Leveling Feet
4-hex nuts
16-Hex bolts (M8x25)
16-Lock washers (M8)
16-Flat washer (M8)
16-Hex bolts (M6x12)
16-Lock washer (M6)
16-Flat washer (M6)
1-Controller hook
2-Machine screws
(M4x6)
4-Small rubber pads
Remove all contents from shipping boxes. Do not discard carton or packing material until assembly is complete.
Accessories commonly ship inside machine or stand packaging and can be easily over looked.
Tools required for assembly:
#2 Philips-Screwdriver
10mm, 13mm and 17mm sockets and socket wrench
24mm open-end wrench
2mm and 3mm Allen key
Level
Setup and Assembly

13 | Axiom Tool Group
Packaging contents for Axiom Precision CNC machines:
1-Router table assembly
1-Electrical control box
1-RichAuto B18 handheld controller
1-Controller cable
1-Tool touch-off puck
1-Stepper Motor
1-Top stepper motor cover
2-Collet wrenches (V5 Model Only)
1-1/4” ER-20 Collet (V5 Model Only)
1-1/2” ER-20 Collet (V5 Model Only)
4-Rubber bushings
4-Hex Bolts (M17x45)
4-Washers (M17)
1-2mm Allen Key
Assembling Stand (all models):
Assembly for stands fitting all V5 series machines is the same. The only
difference is the length of the cross braces.
1- Thread a (1) loose hex-nut onto each of the (4) leveling feet.
2- Turn the square stand uprights upside down. Do this on top of the
cardboard packaging to prevent scratching.
a. Install the (4) leveling feet and (4) swivel casters using (1) M6 hex
bolt, (1) M6 lock washer, and (1) M6 flat washer for each caster.
Tighten all the caster hardware securely. The leveling feet can be
adjusted later.
b. Rotate uprights so the cross-brace mounting plates are facing each
other. Separate the uprights far enough that the braces can fit
between them.
c. Align the cross-braces between the uprights and bolt the mounting
flanges to the plates using (4) M8 hex bolt, (4) lock washers and (4)
flat washers for each side.
*As seen in the diagram above, the braces should be rotated correctly
for the toolbox and shelf to sit at the correct height. Braces should be
mounted so that the top and bottom are the larger flat surfaces*
6- With assistance, the stand can now be flipped over onto the casters and
leveling feet.
7- Flip the Shelf upside down and stick (1) of the rubber pads on each corner
of the shelf flange.
a. Install shelf between the braces on the stand, all the way forward.
b. The small rubber pads should now be between the flange and the
top surface of the brace. This will help prevent unwanted movement
and scratching.

14 | Axiom Tool Group
8- If the optional tool-box has been purchased, the shelf can be slide to the
far back of the stand (AR6 and AR8 models only, AR4 models, will no longer
have room for the shelf).
a. Turn the tool-box upside down. Install (1) of each hanger on either
side of the toolbox using the installed threaded inserts and (2) 3mm
cap-screw each.
b. Insert the tool-box into the stand, from the top. The hangers will
with snugly between the braces on either side of the tool-box.
c. The front can be slid forward to rest within the opening on the stand
upright.
9- Install the hook on the front right-hand side of the stand using the included
hardware.
Installing the Toolbox:
The tool-box will sit to the front of the stand, so be sure to orient the shelf towards the rear to serve as storage.
a. Turn the tool-box upside down. Install (1) of each hanger on either side of the toolbox using the installed
rivnuts and (2) 3mm cap-screw each.
b. Insert the tool-box into the stand, from the top. The hangers will
with snugly between the braces on either side of the tool-box.
c. The front can be slid forward to rest within the opening on the stand
upright.

15 | Axiom Tool Group
Installing the router table on the Stand:
The CNC router table assembly is heavy. Please use a secure means and use caution when lifting onto the stand.
To avoid damage, be careful to never lift the router by the gantry.
1- If using a forklift, keep forks under the steel frame to avoid damaging the wiring and mechanics of the
machine.
a. Place a scrap piece of lumber beneath the router assembly and carefully slide forks beneath the
steel base.
Make sure the forks extend through to the other side of the machine for safe lifting.
2- Position router over the stand and align holes on router mounting flanges and stand uprights. Being careful
to make sure the stand is properly oriented with the
machine front.
3- Place (1) rubber bushing over the holes in the stand. Lower
the machine to sit on the bushings.
a. Attach the machine to the stand using (1) M10 Hex
bolt, (1) washer at each corner.
b. Insert the bolt/washer through the machine
mounting flange and the rubber bushing.
c. Thread the bolt loosely into the stand mounting
holes. Do not tighten until all bolts have been
threaded.
d. Remove fork lift and tighten bolts evenly.
4- Place level on the router table, then level the assembled
machine by adjusting the leveling feet. Be sure to level
the machine in all directions.

16 | Axiom Tool Group
Finishing machine assembly:
With the machine mounted on the stand, or safely on a secure
work surface if a stand was not acquired, now it’s time to begin
finishing the setup.
1- Insert the control box into the front right cavity of the
toolbox, or for stands without toolboxes just sit the
control box on the shelf.
a. Power and communication cables will run
through the lower hole in the back of the tool-
box.
2- Insert the cable connectors into their corresponding
female receptacles and twist the collar to tighten. The
receptacles are keyed so the plugs will only insert one
way.
3- Be sure to position the electrical cord through the back
of the stand safely, so it will not be ran over by the
castors and to prevent tripping hazards.
4- Attach the metal end of the controller cable to the front
of the control box.
a. connect the hand-held controlled securely to the
opposite cable end. Be careful to not overtighten
the screws.
b. When complete the controller can be hung on
the hook found on the right-hand side of the
stand.
5- Locate and install the stepper motor to the top of the Z-
axis motor seat, on the gantry tower.
a. Use the existing 4 cap-screws found on the motor
seat to secure the stepper motor
b. Tighten the two set screws in coupling that attaches stepper motor shaft to the ball-screw.
c. Install plastic cover over stepper motor mount and tighten the two screws.

17 | Axiom Tool Group
All Electrical connections must be performed by a qualified electrical and follow any local codes
and ordinances. Failure to comply may result in serious injury.
Electrical connections that are improperly installed or are outside operational specifications may cause machine
damage and void any warranties that are in place.
The V5 series CNC machines are rated for 220V +/-10% having an operational range
of 200-240V. The machines come pre-wired with a NEMA 6-20 plug for use on a
circuit with a grounded outlet as pictured. It is recommended that these machines
be connected to a dedicated 10-amp circuit.
Make sure the machine is connected to a matching outlet. No adapter is available,
nor should one be used.
If the machine must be reconnected for use with a different type of electric circuit,
the connection must be done by qualified person(s) and must comply with all local
codes and ordinances.
Grounding Instructions:
Axiom CNC machines must be grounded. This grounding provides a path of least resistance for electrical current,
which during a malfunction will reduce the risk of electrical shock.
All Axiom machines are equipped with an electrical cord with grounding conductor and plug. The plug must be used
with a matching outlet that is properly installed and grounded in accordance with local codes and ordinances.
These plugs must not be modified, if a matching outlet is need, one must be installed by a qualified electrician.
Improper installation may result in electrical shock.
If grounding instructions are not completely understood or if in doubt as to whether the
machine is properly grounded, a qualified electrician should be consulted.
Extension Cords:
The use of extension cords should be discouraged. It is recommended to place the machines as near to the power
source as possible.
If an extension cord is necessary, make sure any cord used is in good conditions. Worn or damaged cords should be
replaced immediately.
When using an extension cord, be sure to use one that is heavy enough to carry the required current and use only 3-
wire extension cords that feature the correct 3-prong grounding plugs and 3-pole receptacles.
An undersized cord will cause a drop-in line voltage resulting in loss of power, overheating and runs the risk of
fire.
It is recommended that if an extension cord must be used, it be a 10-12 gauge grounded-three wire cord of no more
than 8-10 feet.
Electrical Connections

18 | Axiom Tool Group
Before getting started with the machine, it is recommended to become familiar with the handheld controller for
operation of the machine, setting up a job and processing a file.
Controller:
Toolpaths, that are created in the design software are communicated to the CNC router through the handheld
controller. On the V5 series machines, this is done through the RichAuto B18 controller.
Processing tool-paths or jobs, is performed either by using a USB Flash drive (USB2.0 of 8GB or smaller FAT 32) or
from 0internal memory. (512MB)
Internal memory is recommended for jobs of 1 hour
run time or longer, and any files that will be used
frequently.
USB flash drives should be USB2.0 8GB or smaller,
formatted to FAT32
The RichAuto B18 Key pad which is seen here, uses
either;
Single touch functions where buttons may
perform one of many single tasks or if held
down, will perform a task continuously (such as
machine movement).
Combination functions, where two keys are
pressed at the same time.
Operations
A+
A-

19 | Axiom Tool Group
Operating Procedure:
Machine operations may be done several ways; either through the controller keypad or through the design files
(tool-paths) which can be downloaded to the controller through the USB (Udisk) or ran from internal memory.
Before performing an operation:
1- Make sure machine stand leveling feet (if available) have been lowered to prevent the machine from
moving.
2- Ensure that the workpiece is secured to the table which can be done using any of the following:
a. Clamps
b. Fixtures
c. Vacuum hold-downs (Optional Accessory)
d. Double sided tape
3- Turn on the machine by rotating the green switch located on the white control box to the right. The
controller display should light, displaying the loading screen.
a. The emergency stop button may need released if it has been used.
Once done loading, a HOME operation must be performed before any other function.
HOME Position:
When turning on the machine, once the controller has finished loading, the
following message will be displayed:
At this point, the controller can be used to scroll up and down the list using the
X+/X- buttons. The top option of “All axis home” should be
selected using the ORIGIN/OK button.
Home position is determined by a set of magnetic proximity
sensors, one of which can be found on each axis. These sensors
can be calibrated, however, their position should not change.
During a HOME operation the following will occur:
1- First the Z axis will raise to the top of the axis travel.
2- Then the X & Y axes will travel, simultaneously, to the front left corner of the machine.
3- When complete the controller will display the coordinate screen.
Coordinate screen will display the coordinate state the controller is currently using and the position of the router in
relation to the programmed Origin (0,0 point).
It is important that a HOME operation is performed at every start-up to ensure that the limit switches and internal
software settings are properly working. All machine movements are software driven and based upon the HOME
position.
At any time during a machine operation, the HOME operation can be selected to run from the controller using the
HOME button. (Must be done from the main coordinate screen)
Selecting the HOME button will display the HOME Type menu where several options are available, such as:
1- Home all
2- Home X (X axis only)
3- Home Y (Y axis only)
4- Home Z (Z axis only)
Table of contents
Popular Control System manuals by other brands

Rain Bird
Rain Bird IQ Installation & user guide
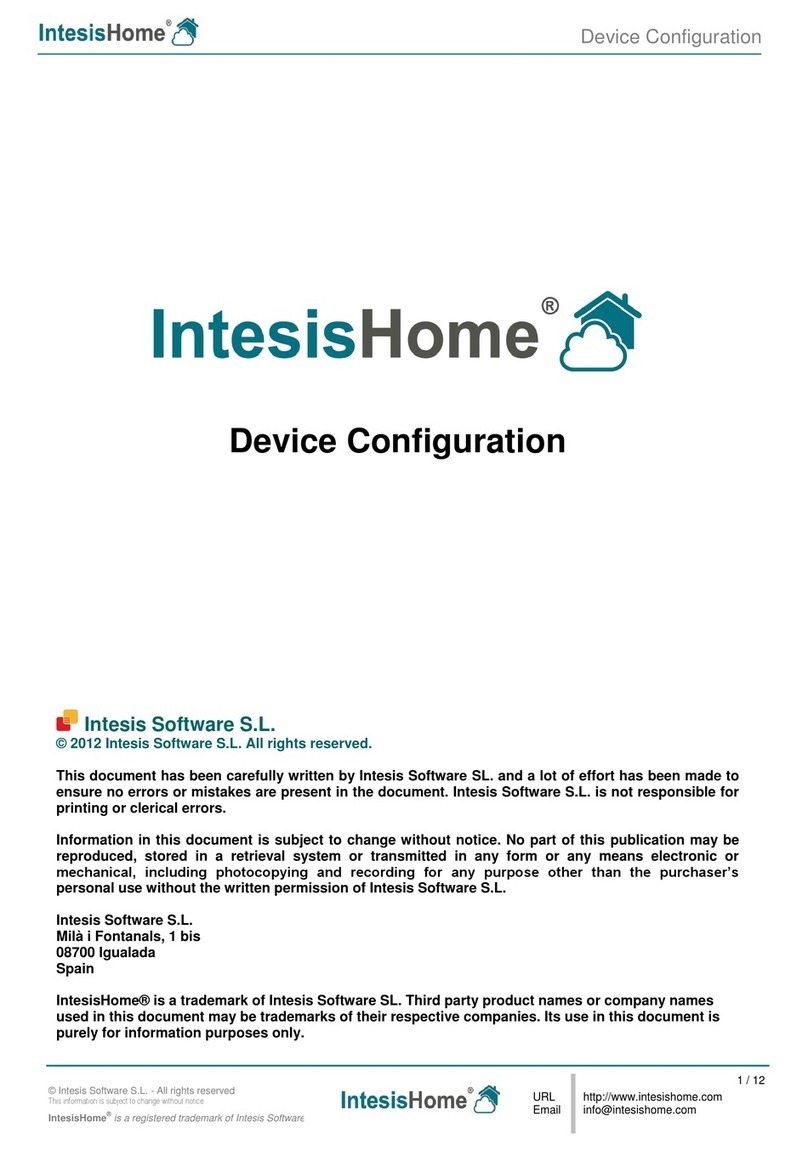
Intesis Software
Intesis Software IntesisHome Configuration guide
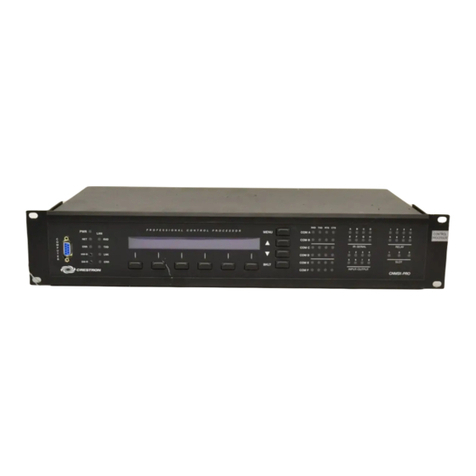
Crestron
Crestron CNMSX-PRO Operation guide
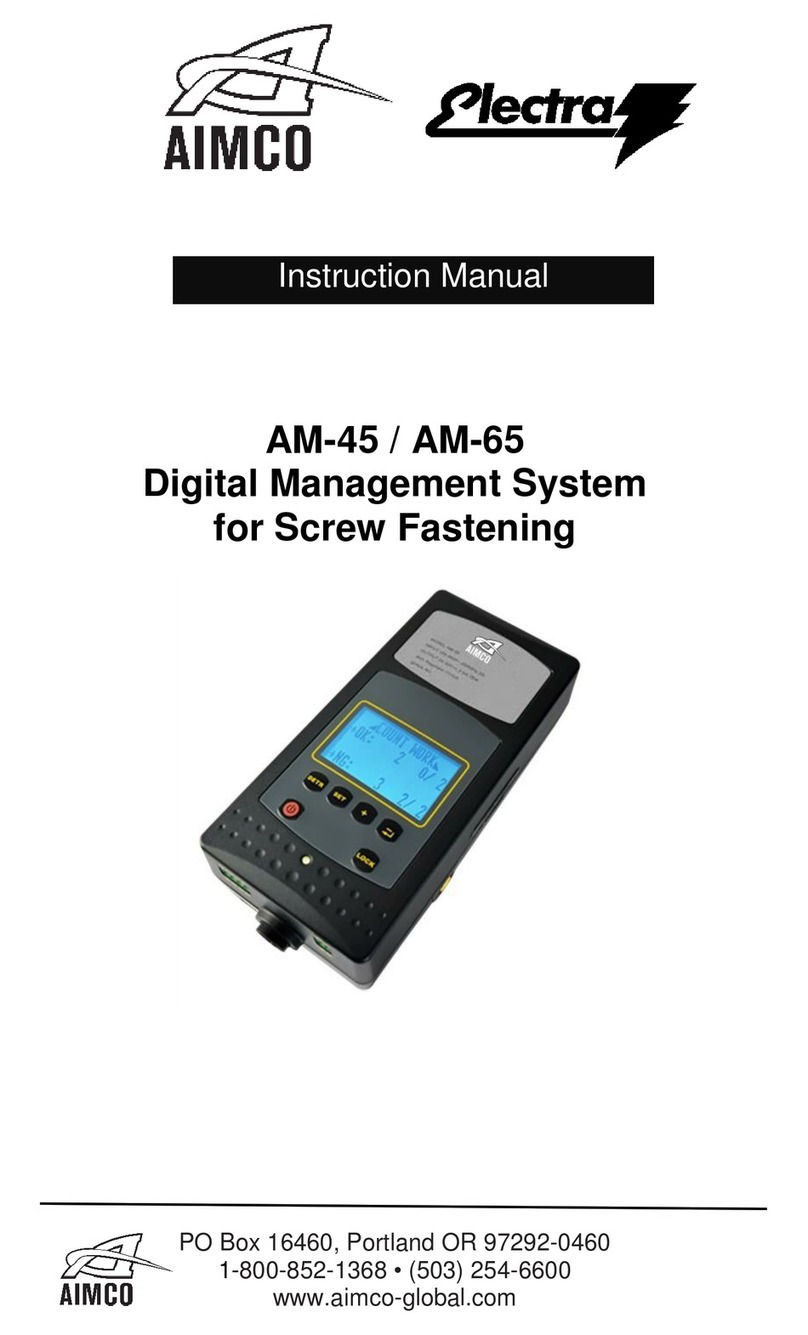
Aimco
Aimco AM-45 instruction manual
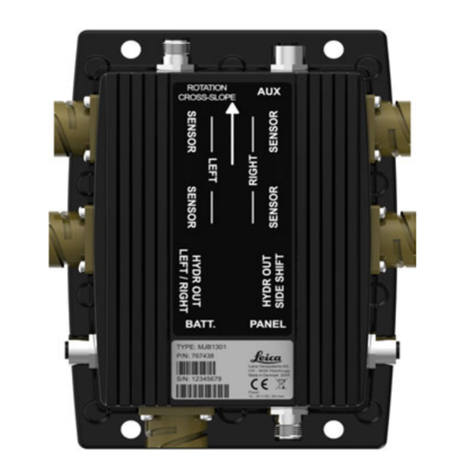
Leica Geosystems
Leica Geosystems iCON grade iGG Series installation manual
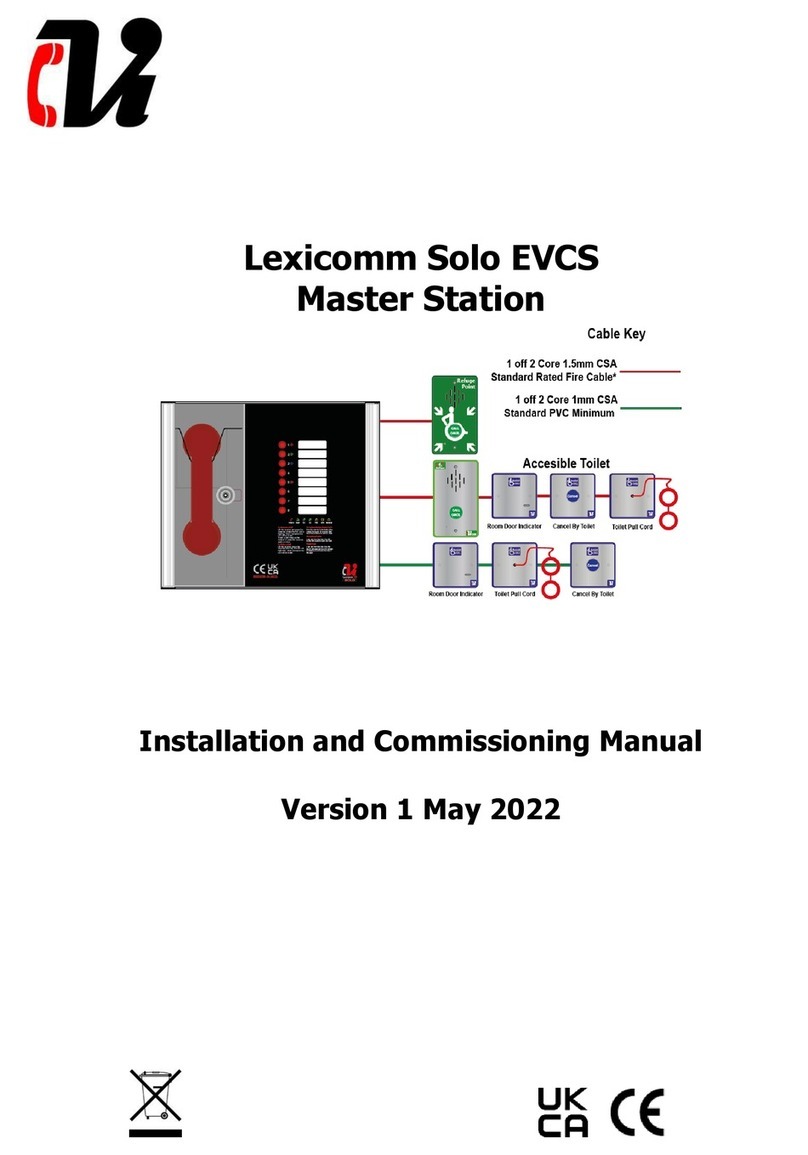
Lexicomm
Lexicomm Solo EVCS Installation and commissioning manual