AXXIOM SCHMIDT BAABS User manual

BAABS
(Blasting Accessory & Assist Bracket System)
January 2023
SAVE THIS MANUAL AND MAKE AVAILABLE
TO ALL USERS OF THIS EQUIPMENT!
Manual Part Number 7200-370
Axxiom
Manufacturing
Website
Copyright © 2023 Axxiom Manufacturing, Inc.
11927 S. Highway 6, Fresno, Texas 77545
800.231.2085 * 281.431.0581 * fax 281.431.1717
Visit us at www.AxxiomMfg.com
See back cover for additional BAABS links
BAABS
Manual

2 Copyright © 2023 Axxiom Manufacturing, Inc.
WARNING
1. Any person intending to operate this equipment or any person intending to be in the
vicinity during its operation must receive proper training from his/her supervisor,
employer and/or supplier. If this equipment is to be leased or rented, the supplier must
assure that the lessee or renter has received proper training before the lessee or renter
takes possession of the equipment. Consult Axxiom Manufacturing, Inc.
2. Any person authorized to operate this equipment or any person intending to be in the
vicinity during its operation and who is not capable of reading and understanding this
manual must be fully trained regarding the Rules for Safer Operation and all operating
procedures, and must be made aware of all the Dangers, Warnings, and Cautions
identified herein. Consult Axxiom Manufacturing, Inc.
3. Do Not operate any abrasive blaster or blast equipment before reading and completely
understanding all the warnings, operating procedures and instructions, and the Rules
for Safer Operation contained in this manual.
4. Do Not operate any abrasive blaster or blast equipment without following the Rules for
Safer Operation and all the operating procedures and instructions. Failure to properly
use blast equipment could result in severe injury or death.
5. Do Not perform any maintenance on any abrasive blaster or blast equipment while it
is pressurized. Always depressurize the abrasive blaster vessel before loading abrasive
or performing any maintenance.
6. Do Not use abrasives containing free silica. Silica can cause silicosis or other related
respiratory damage. All operators must wear personal protective equipment for all
abrasive blasting operations. Observe all applicable local, state, and federal safety
regulations in conjunction with airline filters and respiratory protection. Reference
OSHA 29 CFR 1910.134.
7. Do Not enter areas during abrasive blasting operations without breathing protection.
All personnel in the vicinity of abrasive blasting operations should wear NIOSH
approved air fed respirators, hoods or helmets.
8. Do Not modify or alter any abrasive blaster, blast equipment or controls thereof
without written consent from Axxiom Manufacturing, Inc.
9. Do Not use bleeder type deadman valves on any Schmidt® abrasive blaster. The use of
A-BEC, Clemco or a similar bleeder type deadman valve can cause unintentional start-
up without warning, which can result in serious personal injury.
10. Do Not sell, rent, or operate abrasive blasters without remote controls. OSHA
regulations require remote controls on all blast machines. Failure to use remote
controls can cause serious injury or death to the operator(s) or other personnel in the
blasting area. Reference OSHA 29 CFR 1910.244(b).
11. Do Not repair or replace any portion of Schmidt® equipment using components that
are not Schmidt® original factory replacement parts. Use of replacement components
that are not Schmidt® original factory replacement parts may result in equipment
failure which can result in serious personal injury and in addition will void all
warranties.

Copyright © 2023 Axxiom Manufacturing, Inc. 3
1.1. GENERAL RULE FOR SAFER OPERATION.
SCHMIDT® ABRASIVE BLASTERS AND ACCESSORIES HAVE BEEN DESIGNED TO BE SAFER WHEN USED IN
THE PROPER MANNER.ALL ABRASIVE BLASTERS AND ACCESSORIES ARE POTENTIALLY DANGEROUS IF ALL
SAFETY PRECAUTIONS ARE NOT RIGOROUSLY FOLLOWED. PROPER TRAINING IS REQUIRED BEFORE
OPERATION. PROPER PROCEDURES MUST BE FOLLOWED. THE ABRASIVE BLASTER, ACCESSORIES, AND ALL
COMPONENTS MUST BE PROPERLY MAINTAINED. FAILURE TO OPERATE, SERVICE AND MAINTAIN THE
BLAST ACCESSORY AS SET FORTH IN THIS MANUAL MAY CAUSE INJURY OR EVEN DEATH TO ANY PERSON
USING, SERVICING OR IN THE VICINITY OF THE ABRASIVE BLAST OPERATION.
THIS MANUAL IDENTIFIES POTENTIAL HAZARDS BY DANGER, WARNING, AND CAUTION SYMBOLS.
HOWEVER, ALL THE RULES, PROCEDURES AND RECOMMENDATIONS MUST BE FOLLOWED. FAILURE TO
OPERATE PROPERLY IS VERY LIKELY TO PLACE PERSONS AND PROPERTY AT HIGH RISK OF DAMAGE,
INJURY OR EVEN DEATH.
ABRASIVE BLASTERS, SAFETY ACCESSORY AND THE ABRASIVE BLAST OPERATION ARE POTENTIALLY
DANGEROUS IF ALL SAFETY PRECAUTIONS ARE NOT FOLLOWED. FAILURE TO OPERATE THE ABRASIVE
BLASTER WITHOUT FOLLOWING ALL THE RULES FOR SAFER OPERATION MAY RESULT IN SERIOUS INJURY
OR DEATH TO OPERATING PERSONNEL OR PERSONS IN THE OPERATING VICINITY.
1.2KNOW YOUR EQUIPMENT. Do Not operate this equipment in a manner other than its intended application. Do Not operate
this equipment or any other Schmidt® equipment without following the Rules for Safer Operation and all the operating procedures
and instructions. Learn the applications and limitations as well as the specific potential hazards related to this machine. Failure
to do so could result in serious injury or death.
NOTE: The BAABS System is designed as an attachment to a blast hose assembly used an abrasive blast system. Operators must
follow the recommended operating procedures detailed in the operating and maintenance manual provided with abrasive blaster.
Failure to follow the procedures detailed Abrasive Blaster Operation and Maintenance Manual could result in severe injury or
death. In addition to these procedures provided in this manual, operators must consult the manual provided with abrasive blaster
that will be used with the BAABS System.
1.3 RECEIVE PROPER TRAINING. Do Not operate this equipment unless you have received operational and maintenance
training. Begin by thoroughly reading and understanding this operation and maintenance manual and all included information.
Consult an authorized Schmidt distributor or Axxiom Manufacturing, Inc.
1.4 USE PROPER PERSONAL PROTECTIVE EQUIPMENT. Do Not operate or perform maintenance on this equipment
without wearing OSHA approved eye, ear, foot, and lung protection. Reference OSHA 29 CFR 1910 and refer to the operating
and maintenance manual of the blast equipment to be used.
Failure to use personal protective equipment could result in severe injury or death. Refer to the operating and maintenance manual
of the blast equipment to be used.
1.5ADHERE TO ALL REGULATIONS. Do Not operate this equipment without observing all local, state, and federal safety
regulations including, but not limited to, OSHA (Occupational Health and Safety Administration).
1.6. ELECTRICALLY GROUND EQUIPMENT.
Static electricity is generated by the abrasive flow through the blast hose. To minimize chance of static electrical shock to
operating personnel only use anti-static blast hose and/or vacuum hose, properly electrically bond the blast nozzle, blast hose
couplings, and the equipment, and properly install an earth ground to the abrasive blaster. Refer to the operating and maintenance
manual of the blast equipment to be used.
1.0 RULES FOR SAFER OPERATION

4 Copyright © 2023 Axxiom Manufacturing, Inc.
1.7ALWAYS USE CORRECT REPLACEMENT PARTS AND ACCESSORIES. Do Not use replacement parts that are not
Schmidt® original factory replacement parts. Non-original parts may not fit properly and can cause equipment damage and/or
failure which can result in severe injury to operating personnel. Consult Axxiom Manufacturing, Inc.
Use of replacement components that are not Schmidt® original factory replacement parts may result in equipment failure which
can result in severe injury to operating personnel.
1.8 SAVE THIS OPERATION AND MAINTENANCE MANUAL. Refer to this operation and maintenance manual as needed as
well as any additional information included from other manufacturers. Never permit anyone to operate this equipment without
having him/her first read this manual and receive proper training. Make this manual readily available to all operating and
maintenance personnel. If the manual becomes lost or illegible replace it immediately. Periodically re-read this operation and
maintenance manual to maintain the highest skill level; it may prevent a serious accident.
2.1 The BAABS System with integrated Trigger Deadman is designed to be used in an abrasive blast control system as a device that
allows remote control of the on-off function of the blast operation. Consult an authorized Axxiom Distributor for system
compatibility verification.
2.2 The BAABS System with integrated Trigger Deadman comes in two different power configurations—pneumatic or electric. The
pneumatic BAABS Trigger Deadman requires a clean air supply at a minimum of 78 psig for proper operation of blast system
components. The electric BAABS Trigger Deadman operates on either 12V or 24VDC depending on the supply voltage for the
electric blast controls.
2.3 BAABS Assembly part numbers: Refer to Section 10.0.
2.0 GENERAL INFORMATION

Copyright © 2023 Axxiom Manufacturing, Inc. 5
Figure 2.1 –BAABS Main Assembly

6 Copyright © 2023 Axxiom Manufacturing, Inc.
BAABS Assembly
3.0 Installing BAABS Components
Thrust Management Brace Installation

Copyright © 2023 Axxiom Manufacturing, Inc. 7
Thrust Management Brace Installation
Do Not alter or make modifications to the BAABS System. Making alterations or modifications can cause
equipment malfunction which can lead to severe injury or death.
(See Figure 2.1 for part number identification)
3.1 Install Thrust Management Brace Assembly (#19)
3.1.1 Unscrew locking knob #23 until threads clear the rail slot and the brace assembly can slide back and forth.
3.1.2 Determine which hand will operate the G3 Trigger Deadman Assembly #24. The Thrust Management Brace
Assembly will be mounted on the opposite side of the hand to be used to operate the Trigger Deadman. Figure 3.1
shows the Thrust Management Brace set up for right-handed Trigger Deadman use. If left-handed Trigger Deadman
use is desired, unscrew locking knob #23, flip the Thrust management Brace over and screw in the locking knob #23
until the threads are slightly lower than the rail slot. Refer to video link below.
3.1.3 Line up Thrust Management Brace Assembly #19 rail slot with upper rail #5
3.1.4 Slide Thrust Management Brace Assembly onto upper rail #5 until it reaches the Thrust Management Brace
Assembly stop. Refer to Figure 3.5 below.
3.1.5 Hand tighten locking knob #23 to secure brace assembly into place.
Figure 3.5

8 Copyright © 2023 Axxiom Manufacturing, Inc.
3.2 Install G3 Trigger Deadman Assembly #24 (see Figure 15.1 –15.4 for G3 Trigger Deadman options)
3.2.1 Unscrew locking knob #29 until threads clear the rail slot and the Trigger Deadman assembly can slide back and
forth.
3.2.2 Line up G3 Trigger Deadman Assembly rail slot with lower rail #6.
3.2.3 Slide the trigger deadman onto the rail until deadman is completely on the rail. Refer to Figure 3.6.
Figure 3.6
3.2.4 Grab G3 Trigger Deadman Assembly. Position Thrust Management Brace Pad Cushion #22 at or near the center of
the right (or left) chest muscle (pectoral). Adjust pad as needed for comfort. (See Figure 3.4)
3.2.5 Slide the G3 Trigger Deadman to a position that is comfortable. (See Figure 3.3)
3.2.6 Line up the hash mark located on the side of the G3 Trigger Deadman above the locking knob #29 with the closest
hash mark on the lower rail assembly #4. See Figure 3.7.
3.2.7 Hand tighten locking knob #29.
Figure 3.7

Copyright © 2023 Axxiom Manufacturing, Inc. 9
3.3 Optional Side Grip Installation
3.3.1 Unscrew locking knob #18 until threads clear the rail slot and the Side Grip assembly can slide back and forth.
3.3.2 Position Side Grip on the same side as the Thrust Management Brace Assembly #19.
3.3.3 Line up rail slot with upper rail #5.
3.3.4 Slide the Side Grip onto the BAABS rail until the grip is completely on BAABS rail.
3.3.5 Grab G3 Trigger Deadman Assembly #24. Position Thrust Management Brace Pad Cushion #22 at or near the center
of the right (or left) chest muscle (pectoral). Adjust pad as needed for comfort. See Figure 3.4.
3.3.6 Slide the Side Grip to a position that is comfortable.
3.3.7 Line up the hash mark located on the side of the Side Grip by the locking knob #18 with the closest hash mark on
the upper rail assembly #5.
3.3.8 Hand tighten locking knob #18.
3.3.9 Adjust Side Grip position by turning the Side Grip handle counterclockwise, move to the desired position and
tighten by turning the Side Grip handle clockwise. See Figure 3.2.

10 Copyright © 2023 Axxiom Manufacturing, Inc.
Figure 4.1
4.0 Installing Blast Hose Gripper Module
Blast Hose Gripper Installation

Copyright © 2023 Axxiom Manufacturing, Inc. 11
4.1 If the BAABS is installed on a blast hose or in a latched position (See Figure 5.5), follow steps in Section 5.2 to open and
uninstall the BAABS.
4.2 Select Blast hose Gripper Module based on hose size and wall thickness. (See figure 4.1) The grippers are marked M1 –M4
on the inside on the gripper. See M4 marked on the left drawing in Figure 4.2 by the end of the upper arrow.
4.3 Snap Gripper Modules in Gripper Module slots in upper and lower rails. (See figure 4.1) Refer to the video link in Figure 4.1.
4.4 Gripper Modules are removed by pushing the two lock “springs” towards each other and pulling the Gripper Modules from
the Gripper Module slots. (See Figure 4.2)
Figure 4.2

12 Copyright © 2023 Axxiom Manufacturing, Inc.
5.0 Installation of BAABS on the Blast Hose and Connect Trigger Deadman
BAABS Assembly

Copyright © 2023 Axxiom Manufacturing, Inc. 13
Do Not use a BAABS System with damaged or incorrect components. Using a BAABS System with
damaged or incorrect components can result in equipment failure or malfunction which can cause severe
injury or death. Always check the blast hose and the BAABS System for damage before each use. Repair
or replace any component that shows any sign of wear or other damage.
(For Section 5, see Figure 2.1 for part numbers unless otherwise specified)
5.1 Install BAABS on the blast hose. Refer to video link in Figure 5.1.
5.2.1 Place the blast hose into the Lower Rail (See lower drawing Figure 2.1)
5.2.2 Close the Upper Rail until the Rail Snap-Lock Safety(s) #7 click into the Upper Rail (see Figure 5.2). Note: Long
Rail has 2 Safeties, Short Rail has 1 Safety.
5.2.3 Insert Grooved Latch Pin (Figure 5.1) into the slot in Lower Rail. (Figure 5.3)
5.2.4 Pull up on Rail Latch Lever Assembly #8 until it snaps into place (Figure 5.4).
5.2.5 Secure with Safety Pin #9. (Figure 5.5)
5.2 Remove (Uninstall) BAABS from blast hose
5.1.1 Remove Safety Pin(s) #9 to release Rail Latch Lever Assembly #8. (Figure 5.6)
5.1.2 Pull down on latch (Figure 5.7)
5.1.3 Remove Grooved Latch Pin from slot (Figure 5.8)
5.1.4 Open Upper Rail from Lower Rail until Rail Snap-Lock Safety #7 comes in contact with the upper rail. Push in the
safety latch and pull up on Upper Rail to allow the Upper Rail to fully open. (Figure 5.9) Note: The Long Rail has 2
safeties while the Short Rail has 1 Safety.
5.3 Installation Pneumatic Trigger Deadman. Refer to Figure 15.1 and 15.3.
5.3.1 The pneumatic G3 Trigger Deadman works in junction with a twinline 2 Position (Fig 15.1), or twinline with abrasive
cutoff control line hose assembly, 3 Position(Fig 15.3). The 2 Position Module uses a twinline hose assembly consisting
of two color coded 3/16” air lines. The air supply line is orange, and the signal/vent line is black. Each hose contains a
male flared rigid fitting onone end and a female flared swivel fitting at the other. The supply (orange) line of the twinline
has 1/4” fittings, and the signal/vent (black) line has 1/8” fittings. The G3 Trigger Deadman has matching 1/8” and 1/4”
male fittings. The 3 Position Module (Fig 15.3) uses twinline with abrasive cutoff control line hose assembly consisting
of three color coded 3/16” air lines. The air supply line is orange, and the signal/vent lines are black and green. Each
hose contains a male flared rigid fitting on one end and a female flared swivel fitting at the other. The supply (orange)
line of the twinline has 1/4” fittings, and the signal/vent (black / green) lines have 1/8” fittings. The G3 Trigger Deadman
has matching 1/8” and 1/4” male fittings with the 1/8” fittings labeled above the fittings on the G3 housing (BLK and
GRN). Match the hose color to the correct label on the fitting. It is important that the hoses have the correct sized fittings
to help mitigate the deadman valve from being installed incorrectly. Connecting the air supply to the incorrect port of
the G3 Trigger Deadman will stop the signal from venting and will not allow the blast operation to stop when the
deadman trigger is released.
Incorrect connection of the twinline hose to the G3 Trigger Deadman can result in the inability to stop the blast operation
which can result in severe injury or death.
5.3.2 Disconnect the twinline or twinline with abrasive cutoff control line hose from the blast system and remove the existing
deadman from the twinline or twinline with abrasive cutoff control line.
5.3.3 Secure the G3 Trigger Deadman to the BAABS lower rail if not previously attached. See Section 3.2.
5.3.4 Connect the 1/4" swivel fitting of the twinline to the 1/4” fitting on the G3 Trigger Deadman. No thread sealer is required
since fittings are flared. The opposite end of the twinline connects to the blast system air supply.
5.3.5 2 Position Module: Connect the 1/8” swivel fitting of the twinline to the 1/8” fitting on the G3 Trigger Deadman. No
thread sealer is required since fittings are flared. The opposite end of the twinline is the signal air which starts the blast.

14 Copyright © 2023 Axxiom Manufacturing, Inc.
5.3.6 3 Position Module: Connect the 1/8” swivel fittings of the twinline with abrasive cutoff control line to the 1/8” fittings
on the G3 Trigger Deadman. The black hose attaches to the G3 1/8” fitting labeled black. The black hose is the signal
air which starts the air (ACO). The green hose attaches to the 1/8” G3 fitting labeled green. The green hose provides a
signal to the abrasive metering valve for abrasive. No thread sealer is required since fittings are flared.
5.3.7 Reconnect opposite ends of the twinline hose to the mating connections on the abrasive blast system.
5.3.8 To test the G3 Trigger Deadman 2 Position Module, press down the Safety Flap (Fig 6.1 #2) and pull the Trigger (Fig
6.1 #3) to activate the deadman valve and start the blast operation. See Figures 6.1 and 6.2. Release the trigger to stop
blasting.
5.3.9 To test the G3 Trigger Deadman 3 Position Module, press down the Safety Flap (Fig 6.3 #2) and pull the Trigger (Fig
6.1 #3) to the ACO position activate the deadman valve to start the AIR ONLY operation (See Fig 6.4). The Safety Flap
should enter a recessed spot in the trigger to hold the Safety Flap in place. Press down the Safety Flap and pull the
trigger to move the trigger to the blast position (See Fig 6.5). Release the trigger to stop blasting.
5.3.10 Follow the setup andpre-operating instructions provided with the blast system, then retest the operationof the G3 Trigger
Deadman. Check for air leaks at all applicable connections and repair as required.
5.4 Installation Electric Trigger Deadman. Refer to Figure 15.2 and 15.4.
5.4.1 The electric G3 Trigger Deadman functions as an electric switch. When the deadman trigger (Fig 6.1 #3) is pulled it
completes the electric circuit and supplies electric current to the blast controls which allows the signal air to activate the
blast. When the deadman trigger is released, the electric current to the blast controls is interrupted, the signal air vents
to atmosphere, and ends the blast operation.
Electric shock hazard. Abrasive blasters equipped with G3 Trigger Deadman and electric blast control systems must
operate on low voltage supply (12Vor 24VDC). To minimize shock hazard, only use low voltage sources and use caution
when connecting and disconnecting the power source to and from the abrasive blaster.
5.4.2 Turn off or disconnect the power source from the blast system and unplug the existing deadman from the blast controls.
5.4.3 Secure the G3 Trigger Deadman to the BAABS lower rail if not previously attached. See Section 3.2
5.4.4 Connect the electric plug on the G3 Trigger Deadman into the mating connection on the abrasive blaster.
5.4.5 Turn on or reconnect the power source to the abrasive blast system.
5.4.6 To test the G3 Trigger Deadman 2 Position Module (Fig 15.2), press down the Safety Flap (Fig 6.1 #2) and pull the
Trigger (Fig 6.1 #3) to activate the deadman valve and start the blast operation. See Figures 6.1 and 6.2. Release the
trigger to stop blasting.
5.4.7 To test the G3 Trigger Deadman 3 Position Module (Fig 15.4), press down the Safety Flap (Fig 6.3 #2) and pull the
Trigger (Fig 6.3 #3) to the ACO position activate the deadman valve to start the AIR ONLY operation (See Fig 6.4).
The Safety Flap should enter a recessed spot in the trigger to hold the Safety Flap in place. Press down the Safety Flap
and pull the trigger to move the trigger to the blast position (AIR AND ABRASIVE) (See Fig 6.5). Release the trigger
to stop blasting.
5.4.8 Follow the setup and pre-operating instructions provided with the blast system, then retest the operation of the G3 Trigger
Deadman.

Copyright © 2023 Axxiom Manufacturing, Inc. 15
G3 Trigger Deadman Hand Placement
Two position Trigger Deadman (2PP shown)
G3 Trigger Deadman (2PP or 2PE) Operation
6.1 Securely grip G3 Trigger Deadman Assembly (Figure 2.1, #24)
6.2 Place thrust pad (Figure 2.1, #22) securely and comfortably against appropriate part of the body such as the center of the right
(or left) chest muscle (pectoral). Adjust pad for comfort. Refer to Section 3.0 and Figure 3.4.
6.3 Blast hose should be on the same side as the hand that is gripping the trigger deadman, such as between arm and torso. Pull
blast hose as close to the body as comfortably possible. This allows for thrust management pad to be mostly centered on the
right (or left) area of the chest.
6.4 Use the free hand that is not operating the deadman for added control and safety.
6.4.1 Place on side grip if installed.
6.4.2 If side grip is not installed, place on top of long BAABS.
6.4.3 If side grip is not installed, place on the top of blast hose or nozzle holder for short BAABS.
6.5 Place the thumb on top of safety flap (Figure 6.1 #2) and just under the curved safety flap guard (Figure 6.1, #1) on the
trigger deadman handle. Thumb must be placed in the proper location to easily move the safety flap down to allow the trigger
to move to the blast position. (See Figure 6.1) Only place thumb in ready position when ready to blast. Refer to video link
below.
6.6 Prepare for thrust before turning on blast air by activating G3 Trigger Deadman. If standing with pad placed on the chest:
6.6.1 Take a wide stance with one foot forward and one back. The back foot based on operator comfort.
6.6.2 Prior to activating blast, shift body weight towards front foot, leaning forward slightly. Upon activation, the nozzle
thrust should push the operator back to more centered weight distribution.
6.6.3 To maintain balance, always keep torso or body center of mass between feet while blasting.
6.6.4 Keep hands close to the body in a comfortable position with elbows bent at about 90 degrees.
6.7 Trigger the deadman by pushing the safety flap (Figure 6.1, #2) down and out of the trigger safety lock position with the
thumb and pulling back on the deadman trigger with the fingers. (Figure 6.1 #3).
6.7.1 The trigger deadman is 2-position (Blast OFF/ON: see Figures 15.1 –15.2). The hand position will move from
Figure 6.1 to Figure 6.2.
6.8 The nozzle thrust will transfer to the body through the Thrust Management Brace Assembly to the Thrust Management Brace
Pad (See Figure 3.1) This allows the muscles in the hands and arms, not needed to control the BAABS blasting motion, to be
relaxed.
6.9 Release deadman trigger to stop blasting. Safety flap will spring back into the safety position to guard against accidental blast
activation.
6.0 Standard Operation

16 Copyright © 2023 Axxiom Manufacturing, Inc.
G3 Trigger Deadman Hand Placement
Three position Trigger Deadman (3PP shown)
G3 Trigger Deadman (3PP or 3PE) Operation
6.10 Securely grip G3 Trigger Deadman Assembly (Figure 2.1, #24).
6.11 Place thrust pad (Figure 2.1, #22) securely and comfortably against appropriate part of the body such as the center of the right
(or left) chest muscle (pectoral). Adjust pad for comfort. Refer to Section 3.0 and Figure 3.4.
6.12 Blast hose should be on the same side as the hand that is gripping the trigger deadman, such as between arm and torso. Pull
blast hose as close to the body as comfortably possible. This allows for thrust management pad to be mostly centered on the
right (or left) area of the chest.
6.13 Use the free hand that is not operating the deadman for added control and safety.
6.13.1 Place on side grip if installed.
6.13.2 If side grip is not installed, place on top of long BAABS.
6.13.3 If side grip is not installed, place on the top of blast hose or nozzle holder for short BAABS.
6.14 Place the thumb on top of safety flap (Figure 6.3 #2) and just under the curved safety flap guard (Figure 6.3, #1) on the trigger
deadman handle. Thumb must be placed in the proper location to easily move the safety flap down to allow the trigger to move
to the blast position. (See Figure 6.3) Only place thumb in ready position when ready to blast. Refer to video link below.
6.15 Prepare for thrust before turning on blast air by activating G3 Trigger Deadman. If standing with pad placed on the chest:
6.15.1 Take a wide stance with one foot forward and one back. The back foot based on operator comfort.
6.15.2 Prior to activating blast, shift body weight towards front foot, leaning forward slightly. Upon activation, the nozzle
thrust should push the operator back to more centered weight distribution.
6.15.3 To maintain balance always keep torso or body center of mass between feet during blasting.
6.15.4 Keep hands close to the body in a comfortable position with elbows bent at about 90 degrees.
6.16 Activate the deadman by pushing the safety flap (Figure 6.3, #2) down and out of the trigger safety lock position with the
thumb and pulling back on the deadman trigger with the fingers. (Figure 6.3 #3).
6.16.1 The trigger deadman is 3-position (OFF, AIR ONLY, AIR & ABRASIVE: See Figures 15.3 –15.4). The hand
position will move from Figure 6.3 to Figure 6.4 to Figure 6.5. In the air-only position, Figure 6.4, the trigger has a
locking slot the safety flap slides into to hold lever in proper position. The 3 Position trigger deadman allows the
operator to move between the each of the three positions in any manner.
6.17 The nozzle thrust will transfer to the body through the Thrust Management Brace Assembly to the Thrust Management Brace
Pad (See Figure 3.1) This allows the muscles in the hands and arms, not needed to control the BAABS blasting motion, to be
relaxed.
6.18 Release deadman trigger to stop blasting. Safety flap will spring back into the safety position to guard against accidental blast
activation.

Copyright © 2023 Axxiom Manufacturing, Inc. 17
BAABS: Hose Inspection
BAABS: G3 Deadman Maintenance
Do Not use a BAABS System with damaged or incorrect components. Using a BAABS System with
damaged or incorrect components can result in equipment failure or malfunction which can cause severe
injury or death. Always check the blast hose and the BAABS System for damage before each use. Repair
or replace any component that shows any sign of wear or other damage.
7.1 BAABS Short Rail Assembly Figure 9.1, Long Rail Assembly Figure 10.1. Refer to Hose Inspection video link below.
7.1.1 Remove BAABS from blast hose and disconnect electric or pneumatic connections daily. See Section 5.2 for
removal procedure.
7.1.2 Inspect blast hose. If the blast hose is frayed, replace the blast hose, or cut back to good hose. See Figure 7.1.
Figure 7.1
7.1.3 Check the grippers (See Fig 4.1) for signs of wear. Replace if worn. See Section 4.1 for Gripper replacement.
7.1.4 Inspect Rail Latch Spring #6 for wear. (See Figure 11.1 for short BAABS, and Figure 12.1 for Long BAABS)
Replace if worn. See Section 8.2 for Latch Spring replacement.
7.1.5 Blow off or clean BAABS thoroughly before installing on hose (See Section 5.1 for installation).
7.2 G3 Electric Trigger Deadman Assembly
7.2.1 While electric supply to the Trigger Deadman is disconnected, push the Safety Flap (#2) down and squeeze the
Trigger (#3) until it is fully engaged (see Figures 6.1 - 6.2 for 2 Position and Figures 6.3 –6.5 for 3 Position).
Release the Trigger. The Trigger and Safety Flap should return to off position. Squeeze the Trigger again, without
moving the Safety Flap, to confirm the Safety Flap does not allow the trigger to move. If the Trigger and Safety
Flap do not return to the off position, clean the Trigger and Safety Flap pivot points. Repeat until the Trigger and
Safety Flap function properly. (See Figure 14.1)
7.2.2 Periodically check wiring for bare spots, fraying, cuts, or cracks. Repair or replace any components that show signs
of wear or damage. Damaged wires can cause abrasive system malfunctions resulting in accidental and unintentional
blast startup which may result in severe injury or death to operating personnel.
7.2.3 Refer to Section 16.0 for typical troubleshooting procedures regarding the G3 Trigger Deadman.
7.3 G3 Pneumatic Trigger Deadman Assembly
7.3.1 While air supply to the Trigger Deadman is disconnected, push the Safety Flap (#2) down and squeeze the Trigger
(#3) until it is fully engaged (see Figures 6.1 - 6.2 for 2 Position and Figures 6.3 –6.5 for 3 Position). Release the
Trigger. The Trigger and Safety Flap should return to off position. Squeeze the Trigger again, without moving the
Safety Flap, to confirm the Safety Flap does not allow the Trigger to move. If the Trigger and Safety Flap do not
return to the off position, clean the Trigger and Safety Flap pivot points. Repeat until the Trigger and Safety Flap
function properly. (See Figure 14.1)
7.3.2 Dirty air supply and/or back flow situations can result in an accumulation of debris in the twinline and trigger
module body which can result in malfunctions. Clean out or replace twinline. Replace Trigger Deadman Control
Module Assembly if necessary. See Section 16.0 for troubleshooting procedures.
7.0 Maintenance and Inspection

18 Copyright © 2023 Axxiom Manufacturing, Inc.
8.1 Grippers Module (See Section 4.1)
8.2 Rail Latch Spring replacement. See Short Rail Base Assembly Figure 11.1 or Long Rail Base Assembly Figure 12.1
8.2.1 Slide the Latch Slotted Spring Pin #7, with a small, slotted screwdriver, far enough to remove the Rail Latch Spring
#6. Leaving the Latch Slotted Spring Pin in the Rail Latch Lever #5 will make reassembly easier.
8.2.2 Remove Grooved Latch Pin #8 from the Rail Latch Spring #6.
8.2.3 Install the Grooved Latch Pin #8 into the new Rail Latch Spring #6.
8.2.4 Line up the Rail Latch Spring with the Latch Slotted Spring Pin #7 hole in the Rail Latch Lever #5.
8.2.5 Push the Latch Slotted Spring Pin #7 through the Rail Latch Spring and into the hole in the opposite side of the Rail
Latch Lever #5 until the Latch Slotted Spring Pin #7 is completely inside the Rail Latch Lever
8.3 Thrust Management Brace Pad Cushion replacement. (See Figure 13.1)
8.3.1 Remove clamp screws on pad side Thrust Management Brace Flexible Coupling Clamps #5.
8.3.2 Pry Thrust Management Brace Pad Cushion #3 while holding Thrust Management Brace Flexible Coupling #2 until
the connector on the Brace Pad Cushion pops out of the Flexible Coupling.
8.3.3 Install the new Thrust Management Brace Pad Cushion #3 by placing a portion of the Brace Pad Cushion connector
in the hole of the Flexible Coupling and rolling the connector into the hole.
8.3.4 Tighten clamp screws on pad side Thrust Management Brace Flexible Coupling Clamps #5.
8.0 Part Replacement

Copyright © 2023 Axxiom Manufacturing, Inc. 19
Figure 9.1
9.0 Dimensions
360° view of
Short BAABS
360° view of
Long BAABS

20 Copyright © 2023 Axxiom Manufacturing, Inc.
Figure 10.1
10.0 Ordering
360° view of
Long BAABS
360° view of
Short BAABS
Table of contents
Popular Power Tools manuals by other brands
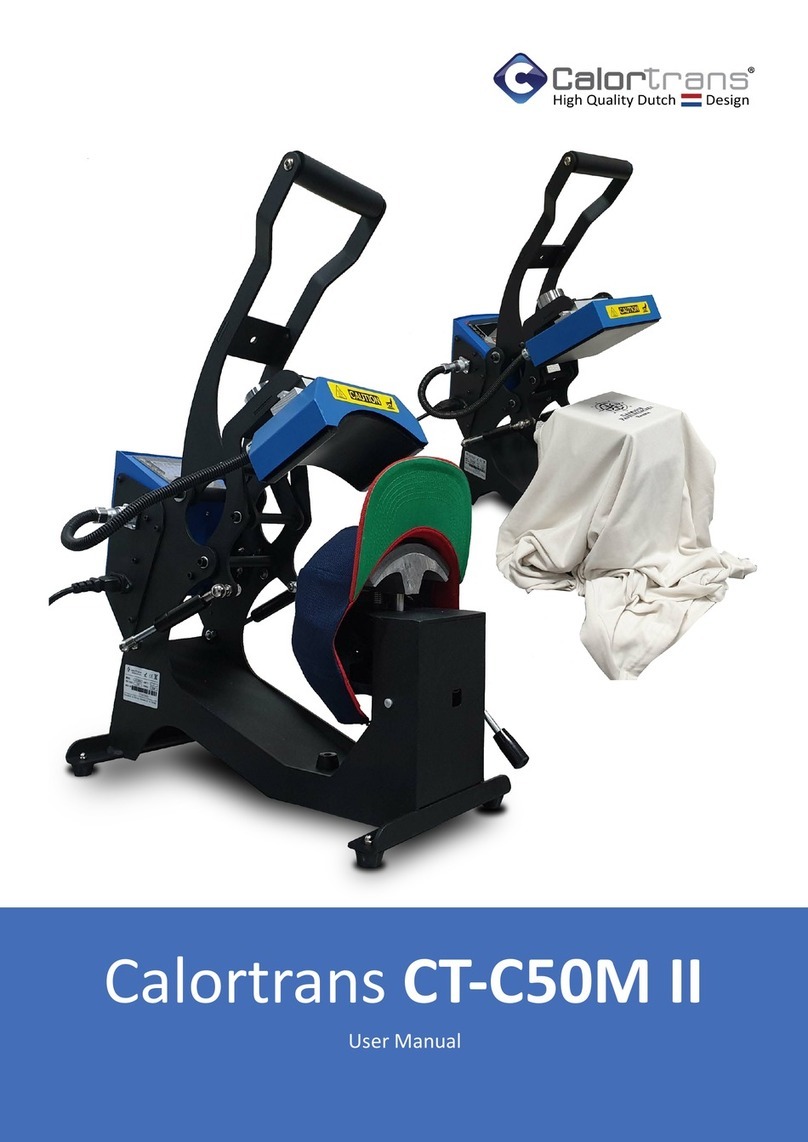
Calortrans
Calortrans CT-C50M II user manual
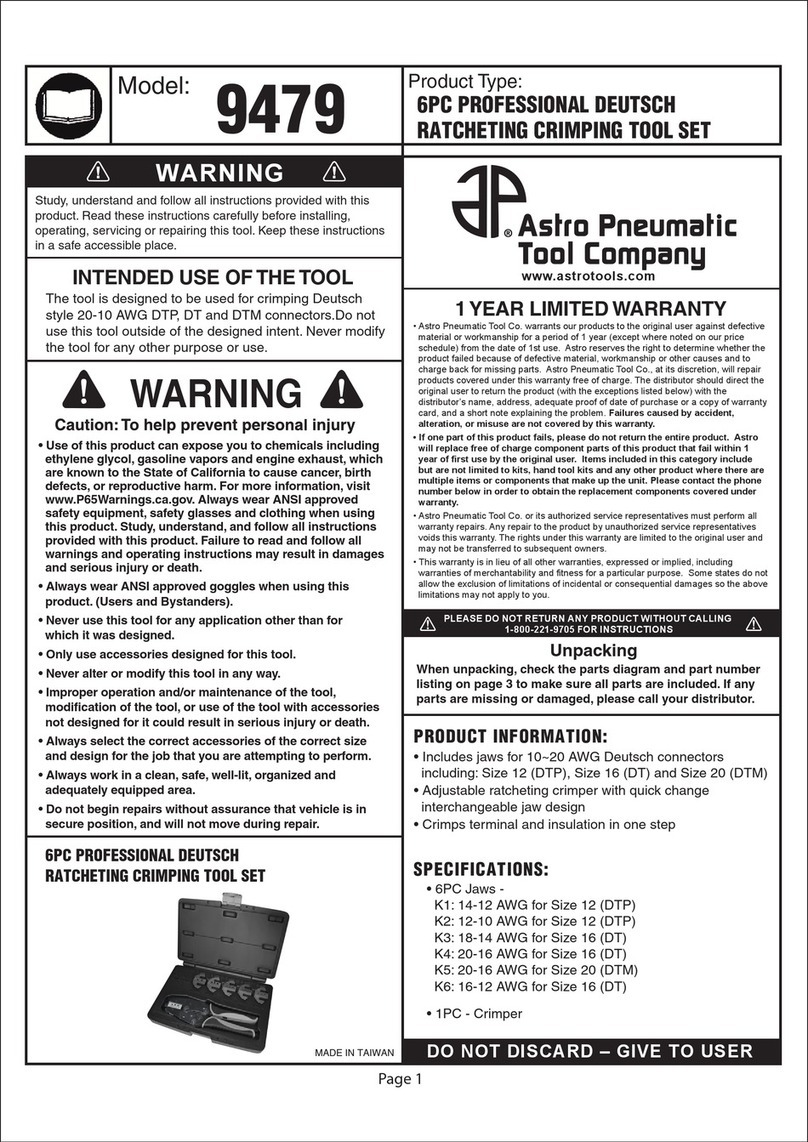
Astro Pneumatic
Astro Pneumatic 9479 instructions
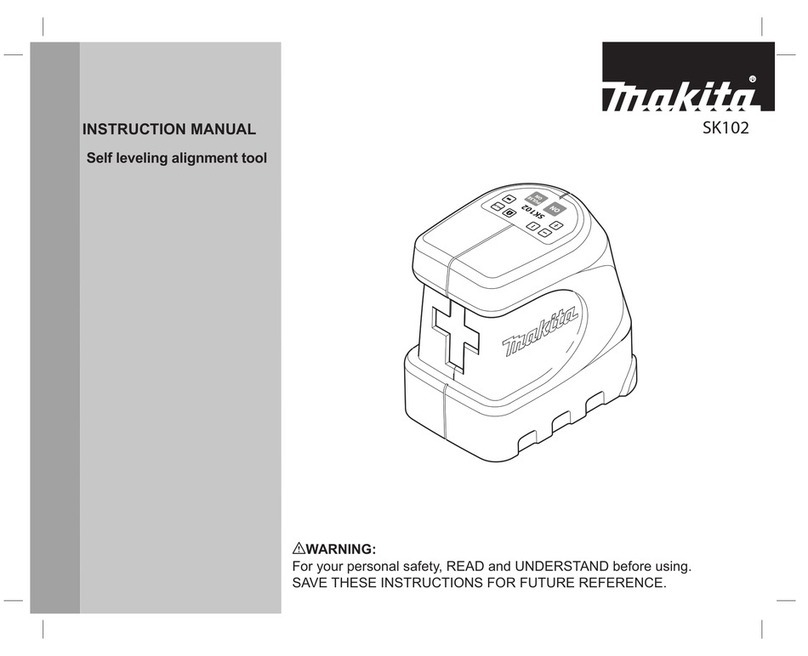
Makita
Makita SK102 instruction manual
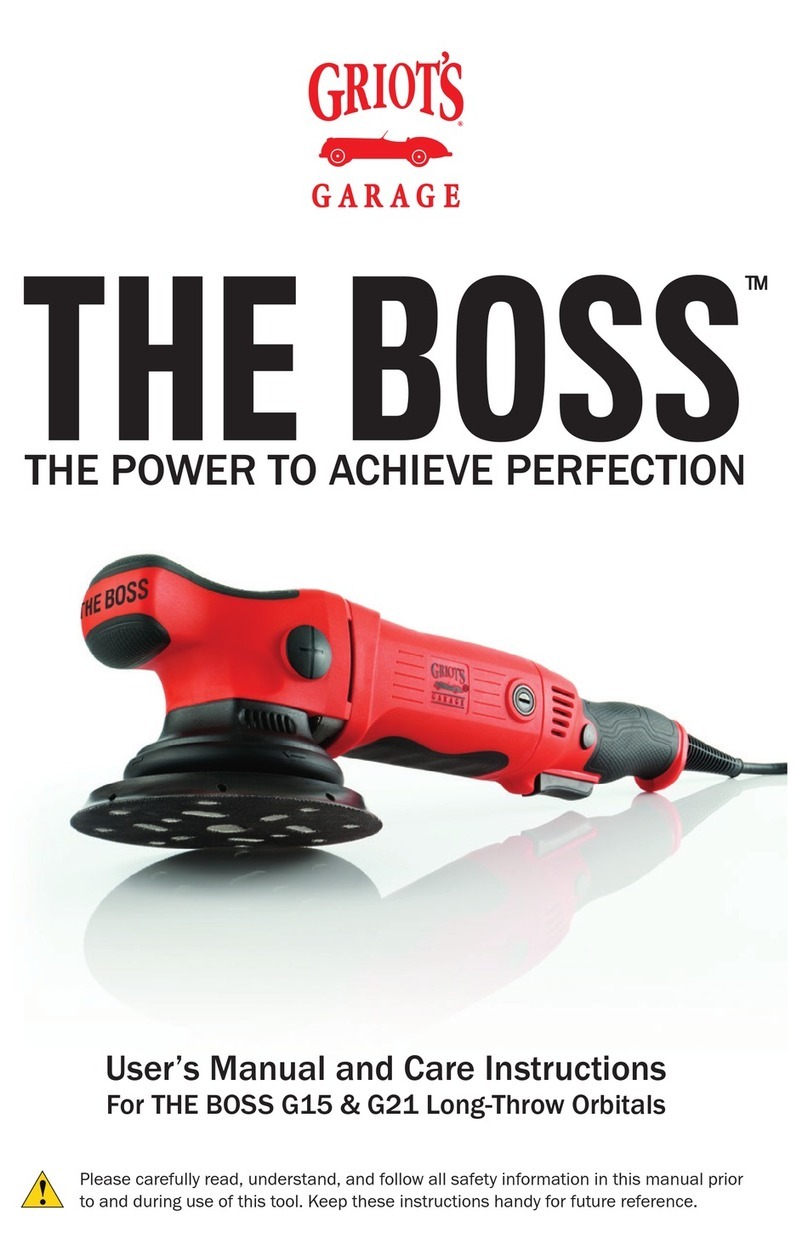
Griots Garage
Griots Garage THE BOSS G21 User's manual and care instructions
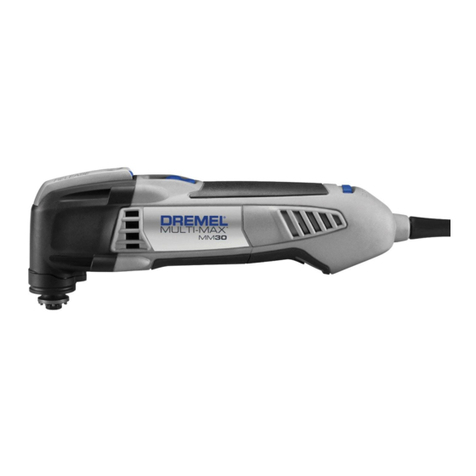
Dremel
Dremel Multi-Max MM30 Operating/safety instructions
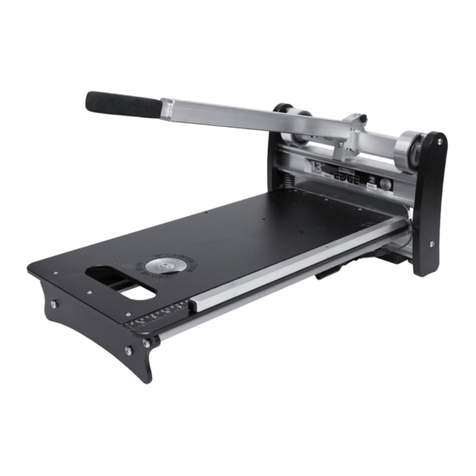
Marshalltown
Marshalltown BULLET MS90-1913 manual