Bardac drives OPTIDRIVE PLUS 3 GV User manual

24

2
Declaration of Conformity:
Invertek Drives Ltd hereby states that the Optidrive Plus product range is CE marked for the
low voltage directive and conforms to the following harmonised European directives :
- EN 61800-5-1 : Adjustable speed electrical power drive systems
-EN 61800-3 : Adjustable Speed Electrical Power Drive Systems – Part 3 (EMC)
- EN 55011 : Limits and Methods of measurement of radio interference
characteristics of Industrial Equipment (EMC)
CE - Konformitätserklärung:
gemäß den Produktnormen für Drehzahlveränderbare Antriebe, die Firma ‘Invertek Drives
Ltd., UK erklärt dass das Produkt: Optidrive VTC (statischer Frequenzumrichter zur
Drehzahlregelung von Asynchronmotoren) nach den folgenden harmonisierten
Produktnormen entwickelt und gebaut wird:
-EN 61800-5-1 : Elektrische Leistungsantriebssysteme mit einstellbarer Drehzahl
-EN 61800-3 : Drehzahlveränderbare elektrische Antriebe – Teil 3 (EMV)
-EN 55011 : Funkstörungen - Grenzwerte und Messverfahren (EMV)
Déclaration de Conformité:
Invertek Drives Ltd déclare par la présente que le produit Optidrive VTC porte le marquage
CE en relation avec la directive basse tension et est conforme aux norms Européennes
harmonisées suivantes :
-EN 61800-5-1 : Equipement electronique utilisé dans les installations de puissance
-EN 61800-3 : Entraînements electriques de puissance à vitesse variable - Partie 3
-EN 55011 : Normes génériques / Compatibilité électromagnétique (CEM)
23
2) For cUL compliance, use fuse type Bussmann KTN-R / KTS-R or equivalent
Model ODP-xxxxx-zz 1) 54450 54550 54750 54900
Motor output rating – industrial 150% o/l kW 45 55 75 90
Model ODP-xxxxx-USA 54600 54750 54100 54120
Motor output rating – industrial 150% o/l HP 60 75 100 120
Supply voltage / phases V±10% 380-480 / 1Ø (with 50% derating) or 3Ø
Supply fuse or MCB (type B) 2) A 160 200 250-300 250-300
Output voltage / phases V 0-480 / 3Ø
Output Amps – industrial 150% overload A 90 110 150 180
Motor cable size, Copper 75 oC mm2 25 35 55 70
Max motor cable length m 100
Min brake resistor Ω6
SIZE 6 (EXTERNAL LINE CHOKE, INTEGRAL RFI FILTER & BRAKING TRANSISTOR)
Model ODP-xxxxx-zz 1) 62055 62075 62090
Motor output rating – industrial 150% o/l kW 55 75 90
Model ODP-xxxxx-USA 62075 62100 62120
Motor output rating – industrial 150% o/l HP 75 100 120
Supply voltage / phases V±10% 220-240 / 1Ø (with 50% derating) or 3Ø
Supply fuse or MCB (type B) 2) A 315-350 400 450-500
Output voltage / phases V 0-240 / 3Ø
Output Amps – industrial 150% overload A 202 240 300
Motor cable size, Copper 75 oC mm2 90 120 170
Max motor cable length m 100
Min brake resistor Ω3
Model ODP-xxxxx-zz 1) 64110 64132 64160
Motor output rating – industrial 150% o/l kW 110 132 160
Model ODP-xxxxx-USA 64150 64175 64210
Motor output rating – industrial 150% o/l HP 150 175 210
Supply voltage / phases V±10% 380-480 / 1Ø (with 50% derating) or 3Ø
Supply fuse or MCB (type B) 2) A 315-350 400 450-500
Output voltage / phases V 0-480 / 3Ø
Output Amps – industrial 150% overload A 202 240 300
Motor cable size, Copper 75 oC mm2 90 120 170
Max motor cable length m 100
Min brake resistor Ω6
1) “-zz” in the part number refers to the country variation
2) For cUL compliance, use fuse type Bussmann KTN-R / KTS-R or equivalent
Maximum supply ratings for UL compliance :
Drive rating Maximum supply voltage Maximum supply current
230V ratings
0.37kW (0.5HP) to 18.5kW (22HP) 240V rms (AC) 5kA rms (AC)
230V ratings
22kW (30HP) to 90kW (120HP) 240V rms (AC) 10kA rms (AC)
400/460V ratings
0.75kW (1HP) to 37kW (50HP) 500V rms (AC) 5kA rms (AC)
400/460V ratings
45kW (60HP) to 160kW (250HP) 500V rms (AC) 10kA rms (AC)
Invertek Drives Ltd adopts a policy of continuous improvement and whilst every effort has been made to provide accurate and up
to date information, the information contained in this brochure should be used for guidance purposes only and does not form the
part of any contract.
Rev. 2.21

22
3) Part number for 1-phase supply different to part number for 3-phase supply
Model ODP-xxxxx-zz 1) 34055 34075 34110 34150 **
Motor output rating – industrial 150% o/l kW 5.5 7.5 11.0 15.0
Model ODP-xxxxx-USA 34075 34100 34150 34200 **
Motor output rating – industrial 150% o/l HP 7.5 10 15 20
Supply voltage / phases V±10% 380-480 / 1Ø (with 50% derating) or 3Ø
Supply fuse or MCB (type B) 2) A 32 32 50 50
Output voltage / phases V 0-480 / 3Ø
Output Amps – industrial 150% overload A 14 18 25 (* 24) 30
Motor cable size, Copper 75 oC mm2 2.5 2.5 4 6
Max motor cable length m 100
Min brake resistor Ω22
Model ODP-xxxxx-zz 1) 35075 35110 35150 **
Motor output rating – industrial 150% o/l kW 7.5 11.0 15.0
Model ODP-xxxxx-USA 35100 35150 35200 **
Motor output rating – industrial 150% o/l HP 10 15 20
Supply voltage / phases V±10% 440-575 / 1Ø (with 50% derating) or 3Ø
Supply fuse or MCB (type B) 2) A 32 32 50
Output voltage / phases V 0-575V / 3Ø
Output Amps – industrial 150% overload A 14 18 24
Motor cable size, Copper 75 oC mm2 2.5 4
Max motor cable length m 100
Min brake resistor Ω22
* Maximum rating for UL applications ** Models not UL listed
SIZE 4 (INTEGRAL RFI FILTER, LINE CHOKE & BRAKING TRANSISTOR)
Model ODP-xxxxx-zz 1) 42075 42110 42150 42185
Motor output rating – industrial 150% o/l KW 7.5 11 15 18.5
Model ODP-xxxxx-USA 42100 42150 42200 42250
Motor output rating – industrial 150% o/l HP 10 15 20 25
Supply voltage / phases V±10% 220-240 / 1Ø(with 50% derating) or 3Ø
Supply fuse or MCB (type B) 2) A 80 80-100 100 125
Output voltage / phases V 0-240 / 3Ø
Output Amps – industrial 150% overload A 39 46 61 72
Motor cable size, Copper 75 oC mm2 10 10 16 16
Max motor cable length m 100
Min brake resistor Ω12
Model ODP-xxxxx-zz 1) 44185 44220 44300 44370
Motor output rating – industrial 150% o/l KW 18.5 22 30 37
Model ODP-xxxxx-USA 44250 44300 44400 44500
Motor output rating – industrial 150% o/l HP 25 30 40 50
Supply voltage / phases V±10% 380-480 / 1Ø (with 50% derating) or 3Ø
Supply fuse or MCB (type B) 2) A 80 80-100 100 125
Output voltage / phases V 0-480 / 3Ø
Output Amps – industrial 150% overload A 39 46 61 72
Motor cable size, Copper 75 oC mm2 10 10 16 16
Max motor cable length m 100
Min brake resistor Ω12
SIZE 5 (INTEGRAL RFI FILTER, LINE CHOKE & BRAKING TRANSISTOR)
Model ODP-xxxxx-zz 1) 52220 52300 52370 52450
Motor output rating – industrial 150% o/l kW 22 30 37 45
Model ODP-xxxxx-USA 52300 52400 52500 52600
Motor output rating – industrial 150% o/l HP 30 40 50 60
Supply voltage / phases V±10% 220-240 / 1Ø (with 50% derating) or 3Ø
Supply fuse or MCB (type B) 2) A 160 200 250-300 250-300
Output voltage / phases V 0-240 / 3Ø
Output Amps – industrial 150% overload A 90 110 150 180
Motor cable size, Copper 75 oC mm2 25 35 55 70
Max motor cable length m 100
Min brake resistor Ω3
1) “-zz” in the part number refers to the country variation
3
CONTENTS
Page
1. General 4
1.1 Important safety information 4
1.2 Electromagnetic Compatibility (EMC) 4
2. Mechanical Installation 5
2.1 General 5
2.2 Mechanical dimensions and mounting 5
2.3 Enclosure mounting 6
3. Electrical Installation 7
3.1 Safety 7
3.2 Precautions 7
3.3 Drive and motor connection 8
3.4 Control terminal connections 9
4. Operation 10
4.1 Managing the keypad 10
4.2 Easy startup 10
5. Configuration 11
5.1 Basic parameters 11
5.2 Extended parameters 12
5.3 User Feedback control 15
5.4 High performance Motor control 15
5.5 Digital input configuration – terminal mode 16
5.6 Digital input configuration – keypad mode 17
5.7 Digital input configuration – User PID mode 17
5.8 Digital input configuration – Modbus control mode (Optional) 18
5.9 Real-time monitoring parameters 18
6. Troubleshooting 19
6.1 Fault finding chart 19
6.2 Fault messages 19
6.3 Auto-tune trouble shooting 20
7. Technical data 20
7.1 User interface 20
7.2 Power stage protection 20
7.3 Environmental 20
7.4 Rating tables 21
All rights reserved. No part of this User Guide may be reproduced or transmitted in any form
or by any means, electrical or mechanical including photocopying, recording or by any
information storage or retrieval system without permission in writing from the publisher.
Copyright Invertek Drives Ltd © 2006
The manufacturer accepts no liability for any consequences resulting from inappropriate,
negligent or incorrect installation, or adjustment of the optional operating parameters of the
drive or from mismatching of the drive to the motor.
The contents of this User Guide are believed to be correct at the time of printing. In the
interest of a commitment to a policy of continuous improvement, the manufacturer reserves
the right to change the specification of the product or its performance or the contents of the
User Guide without notice.
All Invertek drives products carry a 2-year warranty, valid from the data of manufacture. This
data is clearly visible on the rating label.

4
1. General
1.1 Important safety information
This variable speed drive product (Optidrive) is intended for professional
incorporation into complete equipment or systems. If installed incorrectly it may
present a safety hazard. The Optidrive uses high voltages and currents, carries a
high level of stored electrical energy, and is used to control mechanical plant that may cause
injury. Close attention is required to system design and electrical installation to avoid hazards
in either normal operation or in the event of equipment malfunction.
System design, installation, commissioning and maintenance must be carried out only by
personnel who have the necessary training and experience. They must carefully read this
safety information and the instructions in this Guide and follow all information regarding
transport, storage, installation and use of the Optidrive, including the specified environmental
limitations.
Please read the IMPORTANT SAFETY INFORMATION below, and all Warning and
Caution information elsewhere.
Safety of machinery, and safety-critical applications
The level of integrity offered by the Optidrive control functions – for example
stop/start, forward/reverse and maximum speed, is not sufficient for use in safety-
critical applications without independent channels of protection. All applications
where malfunction could cause injury or loss of life must be subject to a risk assessment and
further protection provided where needed. Within the European Union, all machinery in which
this product is used must comply with Directive 89/392/EEC, Safety of Machinery. In
particular, the electrical equipment should comply with EN60204-1.
1.2 Electromagnetic compatibility (EMC)
Optidrive is designed to high standards of EMC. EMC data is provided in a separate EMC
Data Sheet, available on request. Under extreme conditions, the product might cause or
suffer disturbance due to electromagnetic interaction with other equipment. It is the
responsibility of the installer to ensure that the equipment or system into which the product is
incorporated complies with the EMC legislation of the country of use. Within the European
Union, equipment into which this product is incorporated must comply with 89/336/EEC,
Electromagnetic Compatibility.
When installed as recommended in this User Guide, the radiated emissions levels of all
Optidrives are less than those defined in the Generic radiated emissions standard EN61000-
6-4. Every Optidrive has a built-in filter to reduce conducted emissions. The conducted
emission levels are less than those defined in the Generic radiated emissions standard
EN61000-6-4 (class A) for the following cable lengths :
Optidrive sizes #1 to #3 : up to 5m of screened cable
Optidrive sizes #4 to #6 : up to 25m of screened cable
Optidrive sizes #1 to #3 can be fitted with an optional external Optifiter (HF filter). When
correctly fitted with this filter, the conducted emission levels are less than those defined in the
Generic radiated emissions standard EN61000-6-3 (class B) for screened cable lengths up to
5m and with EN61000-6-4 (class A) for screened cable lengths up to 25m.
21
7.4 Drive rating tables
SIZE 1 (INTEGRAL RFI FILTER)
Model ODP-xxxxx-zz 1) 12037 12075 12150
Motor output rating – industrial 150% o/l kW 0.37 0.75 1.5
Model ODP-xxxxx-USA 12005 12010 12020
Motor output rating – industrial 150% o/l HP 0.5 1.0 2.0
Supply voltage / phases V±10% 220-240 / 1Ø
Supply fuse or MCB (type B) 2) A 6 10 20
Output voltage / phases V 0-240V / 3Ø
Output Amps – industrial 150% overload A 2.3 4.3 7
Motor cable size, Copper 75 oC mm2 1.0 1.5
Max motor cable length m 25
SIZE 2 (INTEGRAL RFI FILTER, INTEGRAL BRAKING TRANSISTOR)
Model ODP-xxxxx-zz 1) 22150 22220
Motor output rating – industrial 150% o/l kW 1.5 2.2
Model ODP-xxxxx-USA 22020 22030
Motor output rating – industrial 150% o/l HP 2 3
Supply voltage / phases V±10% 220-240 / 1Ø or 3Ø 3)
Supply fuse or MCB (type B) 2) A 20 32
Output voltage / phases V 0-240V / 3Ø
Output Amps – industrial 150% overload A 7 10.5 (* 9)
Motor cable size, Copper 75 oC mm2 1.5
Max motor cable length m 100
Min brake resistor Ω33 22
Model ODP-xxxxx-zz 1) 24075 24150 24220 24400
Motor output rating – industrial 150% o/l kW 0.75 1.5 2.2 4.0
Model ODP-xxxxx-USA 24010 24020 24030 24050
Motor output rating – industrial 150% o/l HP 1 2 3 5
Supply voltage / phases V±10% 380-480 / 1Ø(with 50% derating) or 3Ø
Supply fuse or MCB (type B) 2) A 6 10 10 20
Output voltage / phases V 0-480 / 3Ø
Output Amps – industrial 150% overload A 2.2 4.1 5.8 9.5
Motor cable size, Copper 75 oC mm2 1.0 1.5
Max motor cable length m 50 100 100 100
Min brake resistor Ω47 47 47 33
Model ODP-xxxxx-zz 1) 25075 25150 25220 25400 25550
Motor output rating – industrial 150% o/l kW 0.75 1.5 2.2 4.0 5.5
Model ODP-xxxxx-USA 25010 25020 25030 25050 25750
Motor output rating – industrial 150% o/l HP 1 2 3 5 7.5
Supply voltage / phases V±10% 440-575 / 1Ø(with 50% derating) or 3Ø
Supply fuse or MCB (type B) 2) A 6 10 10 10 20
Output voltage / phases V 0-575V / 3Ø
Output Amps – industrial 150% overload A 1.7 3.1 4.1 5.8 9.0
Motor cable size, Copper 75 oC mm2 1.0 1.5
Max motor cable length m 50 100 100 100 100
Min brake resistor Ω47
SIZE 3 (INTEGRAL RFI FILTER, INTEGRAL DC LINK CHOKE & BRAKING TRANSISTOR)
Model ODP-xxxxx-zz 1) 32030 32040 32055
Motor output rating – industrial 150% o/l kW 3.0 4.0 5.5
Model ODP-xxxxx-USA 32040 32050 32075
Motor output rating – industrial 150% o/l HP 4 5 7.5
Supply voltage / phases V±10% 220-240 / 1Ø (with 50% derating) or 3Ø
Supply fuse or MCB (type B) 2) A 32 32 50
Output voltage / phases V 0-240 / 3Ø
Output Amps – industrial 150% overload A 14 18 25 (* 24)
Motor cable size, Copper 75 oC mm2 2.5 2.5 4
Max motor cable length m 100
Min brake resistor Ω15
* Maximum rating for UL applications ** Models not UL listed
1) “-zz” in the part number refers to the country variation
2) For cUL compliance, use fuse type Bussmann KTN-R / KTS-R or equivalent

20
6.3 Auto-tune trouble shooting
Trip message Explanation and check point
At-F01 Measured motor stator resistance varies between phases. Ensure that all motor
phases are connected to the drive. Check motor for winding imbalance.
At-F02 Measured motor stator resistance is too large. Ensure that motor is connected.
Check that the motor power matches the drive power rating.
At-F03 Measured motor inductance is too low. Ensure that there is no short circuit on the
motor or a winding fault. Check that the motor power matches drive power rating.
At-F04 Measured motor inductance is too high. Check for motor connection fault. Check
that the motor power matches drive power rating.
At-F05…At-F07 Motor parameter measurements not convergent. Check motor windings for fault.
Check that the motor power matches drive power rating.
Notes: Ensure that the correct motor nameplate parameters are entered in P1-07…P1-09 before
the Auto-tune is carried out. Ensure that the motor winding (star or delta) connection is
correct and that the motor is connected to the drive.
7. Technical data
7.1 User interface
Bipolar Analog Input : Resolution = +/-12-bits (0.025%), 8ms sampling time
(terminal 6) Range settings: 0..10V, 0..24V, -10..10V. Max input voltage 30V DC
Input impedance: 22 kOhm
2nd Analog input : Resolution = +11-bits (0.05%), 8ms sampling time
(terminal 4) Range settings: 0..10V, 4..20mA, 0..20mA. Max input voltage 30V DC
Input impedance: 70 kOhm
Digital inputs : Positive logic only. Sampling interval : 8ms sampling time
(terminals 2, 3, 4) “Logic 1” input voltage range: 8V … 30V DC.
“Logic 0” input voltage range: 0 … 4V DC.
User +24V output : Output load regulation +/-0.4% over full load range.
(terminals 1, 5) Max output current = 100mA total. Short circuit proof.
Analog output : Resolution = 8-bits, 16ms update cycle time
(terminal 8) Output formats: 0…10V, 4…20mA. Max current = 20mA.
Short circuit proof.
2nd digital output : PNP output, max output current = 10mA.
(terminal 3) Short circuit proof.
User relay : Contact rating : 250Vac, 6A / 30Vdc, 5A.
(terminals 10, 11)
7.2 Power stage protection
- Output short-circuit, phase-to-phase, phase-to-earth.
- Output over-current. Trip set at 200% of RMS rated drive current.
- Overload protection. Drive delivers 150% of rated motor current for 60s.
- Braking transistor protected against short-circuit.
- Braking resistor overload. (when enabled)
- Over-voltage trip. Set at 123% of drive maximum rated supply voltage.
- Under-voltage trip.
- Over temperature trip.
- Under temperature trip. (Drive will trip if enabled below 0 OC)
- Supply Phase imbalance. A supply imbalance of > 3% persisting for more than 30s
will trip a running drive.
- Supply Phase loss. If one phase of a 3-phase supply is lost for more than 15s, a
running drive will trip.
7.3 Environmental
Operational temperature range : 0 … 50 OC
Storage temperature range : -40 … 60 OC
Maximum altitude : 2 000m. Derate above 1000m : 1% / 100m
Maximum humidity : 95%, non-condensing
5
2. Mechanical Installation
2.1 General
•Carefully inspect the Optidrive before installation to ensure it is undamaged
•Store the Optidrive in its box until required. Storage should be clean and dry and
within the temperature range –40oC to +60oC
•Install the Optidrive on a flat, vertical, flame-resistant, vibration-free mounting within a
suitable enclosure, according to EN60529 if specific Ingress Protection ratings are
required
•The Optidrive must be installed in a pollution degree 1 or 2 environment
•Flammable material should not be placed close to the drive
•The entry of conductive or flammable foreign bodies should be prevented
•Max. operational ambient temperature 50oC, min. 0oC. Refer to rating tables in
section 7.4
•Relative humidity must be less than 95% (non-condensing)
•Optidrives can be installed side-by-side with their heatsink flanges touching. This
gives adequate ventilation space between them. If the Optidrive is to be installed
above another drive or any other heat-producing device, the minimum vertical
spacing is 150mm. The enclosure should either be force-ventilated or large enough
to allow natural cooling (refer to tables in section 2.3 for further information).
2.2 Mechanical dimensions and mounting
Size 1 Size 2 Size 3 Size 4 Size 5
(#1) *
Size 5
(#2) * Size 6
Length / mm 155 260 260 520 1045 1100 1100
Width / mm 80 100 171 340 340 340 340
Depth / mm 130 175 175 220 220 330 330
Weight/ kg 1.1 2.6 5.3 28 67 68 55 **
A / mm 105 210 210 420 945 945 945
B / mm 72 92 163 320 320 320 320
J / mm 4 9.5
K / mm 25 50
Fixings 2 * M4 4 * M4 4 * M8
Power Terminal
torque settings 1 Nm 4 Nm 8 Nm
L
WD
A
J
B
K
* Size 5 (#1) – 90A and 110A ratings
* Size 5 (#2) – 150A and 180A ratings
** S6 has external line choke, weight 27kg

6
2.3 Enclosure mounting and dimensions
For applications that require a higher IP rating than the IP20 offered by the standard drive,
the drive must be mounted in a metallic enclosure. The following guidelines should be
observed for these applications:
•Enclosures should be made from a thermally conductive material, unless forced
ventilation is used.
•When vented enclosures are used, there should be venting above the drive and
below the drive to ensure good air circulation. Air should be drawn in below the
drive and expelled above the drive.
•If the external environment contains contamination particles (eg dust), a suitable
particle filter should be fitted to the vents and forced ventilation implemented. The
filter must be serviced / cleaned appropriately.
•High moisture, salt or chemical content environments should use a suitably sealed
(non-vented) enclosure.
Non-Vented Metallic Enclosure Dimensions (mm)
Drive Power rating L W D G
Size 1 0.75kW 230V 300 250 200 50
Size 1 1.5kW 230V 400 300 250 75
Size 2 1.5kW 230V / 2.2kW 400V 400 300 300 60
Size 2 2.2kW 230V / 4kW 400V 600 450 300 100
Vented Metallic Enclosure Dimensions (mm)
Free-Vented unit Force-vented unit
Drive Power
rating L W D G L W D G Air Flow
Size 1 1.5 kW 400 300 150 75 300 200 150 75 > 15m3/h
Size 2 4 kW 600 400 250 100 400 300 250 100 > 45m3/h
Size 3 15 kW 800 600 300 150 600 400 250 150 > 80m3/h
Size 4 22 kW 1000 600 300 200 800 600 300 200 > 300m3/h
Size 4 37 kW - - - - 800 600 300 200 > 300m3/h
Size 5 90 kW - - - - 1600 800 400 200 > 900m3/h
Size 6 160 kW - - - - 2000 800 400 200 >1000m3/h
Enclosure Front View Enclosure Side View
W
L
D
G
G
19
6. Troubleshooting
6.1 Fault-finding chart
Symptom Cause and Solution
Overload or over-current trip
on unloaded motor during
acceleration
Check Star / Delta terminal connection in motor. Rated operating voltage of
drive and motor should match. The Delta connection always gives the lower
voltage rating of a dual voltage motor
Overload or over-current –
motor does not spin
Check for locked rotor. Check that the mechanical brake is released (if fitted)
Drive will not enable –
display remains on ‘StoP’
Check that the hardware enable signal is applied to digital input 1. Ensure that
the User +24V output voltage (between terminals 5 and 7) is correct. If not,
check wiring to user terminal strip. Check P1-12 for terminal / keypad mode. If
keypad mode selected, press the START button. Check that supply voltage is
within specification.
Drive runs incorrectly when
in vector mode
Ensure that the motor name plate data has been entered into P1-07, P1-08,
P1-09 before the parameter auto-tune function has been carried out. Set P4-02
= 1 to carry out auto-tune.
In very cold ambient
conditions, drive will not
power up
If the ambient temperature is less than -10 OC, the drive may not power up.
Ensure that a local heating source keeps the ambient above 0 OC in these
conditions.
Speed limit or rated
frequency parameters
cannot be set above 250Hz,
500Hz or 1000Hz
The maximum output motor frequency is limited by the switching frequency.
Ensure that P2-24 is at least 16x greater than the required motor output
frequency before setting the required maximum or rated output frequency
parameters.
Extended menus cannot be
accessed
Ensure that P1-14 is set to the extended access code. This is “101” unless the
code in P2-37 has been changed by the user.
6.2 Fault messages
Trip message Explanation
P-dEF Default parameters loaded, usually after pressing STOP, UP & DOWN keys for 1s. Press
STOP to reset the trip. Display then reads “StoP”
“O-I”
“h O-I”
Over-current on drive output to motor.
Trip on drive enable : check for wiring error or short circuit
Trip on motor starting : check for stalled or jammed motor
Trip during operation : check for sudden overload or malfunction
If “h O-I” occurs, check for short circuit on output. If wiring correct, contact your supplier.
“I.t-trP” Drive overload trip, occurring when the drive has been delivering >100% rated current (set in
P1-08) for a period of time. The display flashes to indicate an overload condition.
“O-Uolt” Over-voltage on DC bus. Check supply voltage is within limits. If trip occurs on deceleration,
increase deceleration time or fit braking resistor.
“U-Uolt” Under-voltage trip. Happens routinely when drive powered down. If it occurs whilst running,
check supply voltage
“OI-b” Over current in the brake resistor circuit. Check cabling to brake resistor
“OL-br” Brake resistor overload. Increase deceleration time, reduce load inertia or add further brake
resistors in parallel. Min resistance values from ratings tables in section 7.4 must be observed.
“O-t” Over-temperature trip. Check drive cooling and possible enclosure dimensions
“U-t” Under-temperature trip. Trip occurs if ambient is less than 0oC. Drive ambient temperature
must be raised above zero in order to start the drive.
“th-Flt” Thermistor hardware fault. Contact your local distributor for further information.
“PS-trP” Trip on drive enable : check for wiring error or short circuit
Trip during operation : check for sudden overload or over-temperature
“dAtA-F” Occurs routinely after Flash upgrade. Reset using the STOP button or after a power down
cycle. All parameters set to default after an upgrade.
“P-LOSS” Drive intended for use with a 3-phase supply has lost one phase. Condition must persist for
>15s before a trip occurs. Phase loss detection disabled if parameters defaulted (P-dEF)
when L3 has been removed.
“Ph-Ib” Phase imbalance. Trips if the phase imbalance exceeds 3%. Condition must persist for >30s
before a trip occurs.
“SC-trP” Check integrity of OptiLink (communication link) between drives interconnected optically.
Check that each drive in a network has a unique drive address (P2-27)
If Modbus function enabled, check Modbus communication link.
“E-triP” External trip (connected to digital input 3). Check motor thermistor (if connected)
“At-Fxx” Auto-tune failed to complete successfully. (xx = 01…07) See 6.3 for more details.
“SPIN-F” Spin start function failed to detect the motor speed. Check cable connection between drive
and motor. Make sure that the motor actual speed is less than the maximum speed limit
(P1-01). Make sure that the motor base frequency (P1-09) is less than 100Hz.

18
5.8 Digital input configuration – Modbus control mode (Optional – P1-12 = 4)
The following table defines the digital input functionality when the drive is in Modbus control mode.
P2-01 Digi input 1 function Digi input 2 function Digi input 3 function Analog input function
0..2,4
6..9,
13..16,18
O : Stop (Disable)
C : Run (Enable) No effect No effect
3 O : Stop (Disable)
C : Run (Enable)
O : Forward
C : Reverse
O : Master speed ref
C : Preset speed 1
Digital input 1 must be closed
to enable the drive
Digi input 3 Analog input Preset value
Open Open Preset speed 1
Closed Open Preset speed 2
Open Closed Preset speed 3
5 O : Stop (Disable)
C : Run (Enable)
O : Master speed ref
C : Preset speed
Closed Closed Preset speed 4
10 O : Stop (Disable)
C : Run (Enable)
O : Master speed ref
C : Digital speed ref
External trip input :
O : trip C : OK
11 O : Stop (Disable)
C : Run (Enable)
O : Master speed ref
C : Preset speed 1
External trip input :
O : trip C : OK
12 O : Stop (Disable)
C : Run (Enable)
O : Preset speed 1
C : Master speed ref
External trip input :
O : trip C : OK
17 O : Stop (Disable)
C : Run (Enable)
O : Master speed ref
C : Bipolar analog input
O : Master / analog speed
C : Preset speed 1
19 O : Stop (Disable)
C : Run (Enable)
O : Master speed ref
C : 2nd analog input No effect
20,21 O : Stop (Disable)
C : Run (Enable)
2nd digital output :
Drive healthy = +24V
O : Master speed ref
C : Preset speed 1
22 O : Stop (Disable)
C : Run (Enable)
2nd digital output :
Drive healthy = +24V
External trip input :
O : trip C : OK
Digital input 1 must be closed
to enable the drive
Notes: If P2-19 = 2 or 3, drive can only be started / stopped by closing / opening digital input 1. If P2-19 = 0 or 2,
the master speed reference will be automatically reset to zero each time when drive is stopped.
5.9 Real-time monitoring parameters
Parameter group zero provides access to internal drive read-only parameters for monitoring purposes.
Par Description Display range Explanation
P0-01 Bipolar analog input value -100%...100% 100% = max input voltage
P0-02 2nd analog input value 0..100% 100% = max input voltage
P0-03 Speed controller reference -500%...500% 100% = Base frequency (P1-09)
P0-04 Digital speed ref (digi pot) - P1-01 … P1-01 Speed displayed in Hz / rpm
P0-05 Torque controller reference 0 ...200% 100% = motor rated torque
P0-06 User PID ref input 0..100% PID controller reference value
P0-07 User PID feedback 0..100% PID controller feedback value
P0-08 User PID error input 0..100% Reference – Feedback
P0-09 User PID P-term 0..100% Proportional component
P0-10 User PID I-term 0..100% Integral component
P0-11 User PID D-term 0..100% Differential component
P0-12 User PID output 0..100% Combined output
P0-13 Output Torque 0…200% 100% = motor rated torque
P0-14 Magnetising current A rms Magnetising current in A rms
P0-15 Rotor current A rms Rotor current in A rms
P0-16 Field strength 0..100% Magnetic field strength
P0-17 Stator resistance Ohm Phase – Phase stator resistance
P0-18 Stator inductance H Stator inductance in Henry
P0-19 Rotor resistance Ohm Calculated rotor resistance
P0-20 DC bus voltage V dc Internal DC bus voltage
P0-21 Drive temperature oC Internal drive temperature
P0-22 Supply voltage L1 – L2 V rms, ph-ph Phase – phase supply voltage
P0-23 Supply voltage L2 – L3 V rms, ph-ph Phase – phase supply voltage
P0-24 Supply voltage L3 – L1 V rms, ph-ph Phase – phase supply voltage
P0-25 Estimated Rotor speed Hz or rpm Applies to vector modes only
P0-26 kWh meter 0.0 … 999.9 kWh Cumulative energy consumption
P0-27 MWh meter 0.0 … 60 000 MWh Cumulative energy consumption
P0-28 Software ID, IO processor eg “1.00”, “493F” Version number and checksum
P0-29 Software ID, Motor control eg “1.00”, “7A5C” Version number and checksum
P0-30 Drive serial number 000000 … 999999
00-000 … 99-999
Unique drive serial number
eg 540102 / 24 / 003
7
3. Electrical Installation
3.1 Safety
Electric shock hazard! Disconnect and ISOLATE the Optidrive before attempting
any work on it. High voltages are present at the terminals and within the drive for up
to 10 minutes after disconnection of the electrical supply.
•Optidrives should be installed only by qualified electrical persons and in accordance with
local and national regulations and codes of practice.
•The Optidrive has an Ingress Protection rating of IP20. For higher IP ratings, use a
suitable enclosure.
•Where the electrical supply to the drive is through a plug and socket connector, do not
disconnect until 10 minutes have elapsed after turning off the supply
•Ensure correct earthing connections, see diagram below
•The earth cable must be sufficient to carry the maximum supply fault current which
normally will be limited by the fuses or MCB
3.2 Precautions
•Ensure that the supply voltage, frequency and number of phases (single or three phase)
correspond to the rating of the Optidrive as delivered
•An isolator or similar should be installed between the power supply and the drive
•Never connect the mains power supply to the Optidrive output terminals UVW
•Protect the drive by using slow-blow HRC fuses or an MCB located in the mains supply
to the drive
•Do not install any type of automatic switchgear between the drive and the motor
•Wherever control cabling is close to power cabling, maintain a minimum separation of
100 mm and arrange crossings at 90o
•Ensure that screening or armouring of power cables is effected in accordance with the
connections diagram below
•Ensure that all terminals are tightened to the appropriate torque (see table, left)
Connect drive according to the following diagram, ensuring that motor terminal box
connections are correct. There are two connections in general : Star and Delta. It is essential
to ensure that the motor is connected in accordance with the voltage at which it will be
operated. For more information, refer to the following diagram
For recommended cabling and wiring sizing, refer to section 7.4.
It is recommended that the power cabling should be 3-core or 4-core PVC-insulated
screened cable, laid in accordance with local industrial regulations and codes of practice.
The ground terminal of each Optidrive should be individually connected DIRECTLY to the
site earth (ground) bus-bar (through the filter if installed) as shown. Optidrive ground
connections should not loop from one drive to another, or to, or from any other equipment.
Ground loop impedance must conform to local industrial safety regulations. To meet UL
regulations, UL approved ring crimp terminals should be used for all earth wiring
connections.

8
3.3 Drive and motor connection
Earth
L3
L2
L1
U V W + BR
Each drive sta
r
connected to system
earth point
To
othe
r
drives
* If fitted, a filter should be mounted
physically close to the Drive. For maximum
effectiveness, the metal case of the filter
and the heat sink of the drive should be
electrically connected, ie screw both to a
metal back plate and ensure metal-to-metal
contact.
Motor terminal box connections
Most general purpose motors are
wound for operation on dual voltage
supplies. This is indicated on the
nameplate of the motor
This operational voltage is normally
selected when installing the motor
by selecting either STAR or DELTA
connection.
STAR always gives the higher of
the two voltage ratings.
Typical ratings are :
400 / 230 ( )
690 / 400 ( )
DELTA ( ) Connection
STAR ( ) Connection
U V W
U V W
Earth
L3
L2
Isolato
r
Contactor, MCB or Fuses
Optional Filter*
Screened
cable connects to
motor frame earth
L1
Optional
Braking
Resisto
r
U V W
Optidrive size 2
Help card
IR lens
Cable
management
tie-wrap
L1 L2 L3
U V W + BR
Each drive sta
r
connected to system
earth point
To
othe
r
drives
RS485 Interface
Use UL listed crimp
terminals for all power
terminal connections
RS485 Interface
RS485 + / Modbus
0V
+24V
RS485 - / Optibus
RS485 + / Optibus
RS485 - / Modbus
For Optibus and Modbus,
data format is fixed as:
1 start bit, 8 data bits,
1 stop bit, no parity.
1 6
17
5.6 Digital input configuration – keypad mode (P1-12 = 1 or 2)
The following table defines the function of the digital inputs when the drive is in keypad mode
P2-01 Digi input 1 function Digi input 2 function Digi input 3 function Analog input function
0 1) O : Stop (Disable)
C : Run (Enable)
Closed : Remote
pushbutton UP
Closed : Remote
pushbutton DOWN
When drive is stopped, closing
digital inputs 2 & 3 together
starts drive. Bipolar analog
input has no effect
1 O : Stop (Disable)
C : Run (Enable)
Closed : Remote
pushbutton UP
External trip input :
O : Trip C : OK
Closed : Remote pushbutton
DOWN
2 O : Stop (Disable)
C : Run (Enable)
Closed : Remote
pushbutton UP
O : Digital speed ref
C : Preset speed 1
Bipolar analog input > 5V
reverses rotation
1)
3…9,
13,14,
16
O : Stop (Disable)
C : Run (Enable)
Closed : Remote
pushbutton UP
Closed : Remote
pushbutton DOWN
When drive is stopped, closing
digital inputs 2 & 3 together
starts the drive.
Bipolar analog input > 5V
reverses rotation
10 O : Stop (Disable)
C : Run (Enable)
O : Digital speed ref
C : Bipolar analog input
External trip input :
O : Trip C : OK Analog speed reference
11 O : Stop (Disable)
C : Run (Enable)
O : Digital speed ref
C : Preset speed 1
External trip input :
O : Trip C : OK
12 O : Stop (Disable)
C : Run (Enable)
O : Preset speed 1
C : Digital speed ref
External trip input :
O : Trip C : OK
Allows connection of motor
thermistor on terminal 4.
Bipolar analog input > 5V
reverses rotation
15 O : Stop (Disable)
C : Run (Enable)
O : Digital speed ref
C : Preset speed 1
O : Decel ramp 1
C : Decel ramp 2
Bipolar analog input > 5V
reverses rotation
17 O : Stop (Disable)
C : Run (Enable)
O : Digital speed ref
C : Bipolar analog input
O : Digital / analog speed
C : Preset speed 1 Analog speed reference
Digi input 3 Analog input Preset value
Open Open Preset speed 1
Closed Open Preset speed 2
Open Closed Preset speed 3
18 O : Stop (Disable)
C : Run (Enable)
O : Digital speed ref
C : Preset speed
Closed Closed Preset speed 4
19 O : Stop (Disable)
C : Run (Enable)
O : Digital speed ref
C : 2nd analog input No effect
20, 21 O : Stop (Disable)
C : Run (Enable)
2nd digital output :
Drive healthy = +24V
O : Digital speed ref
C : Preset speed 1
22 O : Stop (Disable)
C : Run (Enable)
2nd digital output :
Drive healthy = +24V
External trip input :
O : Trip C : OK
Bipolar analog input > 5V
reverses rotation
Notes:
1) In addition to the speed being set using the pushbuttons on the front of the drive, these
settings for P2-01 allow the speed to be controlled remotely using remote pushbuttons
connected to digital inputs 2 and 3.
2) When P2-19 = 2 or 3 in keypad mode, the drive START and STOP is controlled from the
hardware enable input (terminal 2). In this case, the START / STOP buttons will have no
effect.
3) Reverse rotation control using the analog input only works in keypad mode. If P1-12=1, the
rotation control only works when P2-19 = 2 or 3. If P2-35 = 2 or 3, the function is disabled.
4) When connecting a motor thermistor, connect between terminals 1 & 4, set P2-01 = 6, 10, 11,
12 or 22 (Uses external trip input)
5.7 Digital input configuration – User PID mode (P1-12 = 3)
The following table defines the function of the digital inputs when the drive is in User PID control mode.
P2-01 Digi input 1 function Digi input 2 function Digi input 3 function Analog input function
0..10,
13..16,18
O : Stop (Disable)
C : Run (Enable) No effect No effect
11 O : Stop (Disable)
C : Run (Enable)
O : PID control
C : Preset speed 1
External trip input :
O : Trip C : OK
12 O : Stop (Disable)
C : Run (Enable)
O : Preset speed 1
C : PID control
External trip input :
O : Trip C : OK
17 O : Stop (Disable)
C : Run (Enable)
O : PID control
C : Bipolar analog input No effect
19 O : Stop (Disable)
C : Run (Enable)
O : PID control
C : 2nd analog input No effect
20, 21 O : Stop (Disable)
C : Run (Enable)
2nd digital output :
Drive healthy = +24V No effect
22 O : Stop (Disable)
C : Run (Enable)
2nd digital output :
Drive healthy = +24V
External trip input :
O : Trip C : OK
Digital input 1 must be
closed to run the drive
External trip function only
works when bipolar analog
input is selected as
feedback signal (P3-10=1).

16
5.5 Digital input configuration – terminal mode (P1-12 = 0)
P2-01 Digi input 1 function Digi input 2 function Digi input 3 function Analog input function
0 O : Stop (Disable)
C : Run (Enable)
O : Bipolar analog input
C : Preset speed 1, 2
O : Preset speed 1
C : Preset speed 2 Bipolar analog input
1 O : Stop (Disable)
C : Run (Enable)
O : Preset speed 1
C : Preset speed 2
O : Preset speed 1, 2
C : Preset speed 3
O : Preset speed 1,2,3
C : Preset speed 4
Digi input 2 Digi input 3 Analog input Preset value
Open Open Open Preset speed 1
Closed Open Open Preset speed 2
Open Closed Open Preset speed 3
Closed Closed Open Preset speed 4
Open Open Closed Preset speed 5
Closed Open Closed Preset speed 6
Open Closed Closed Preset speed 7
2 O : Stop (Disable)
C : Run (Enable)
Closed Closed Closed Preset speed 8
3 O : Stop (Disable)
C : Run (Enable)
O : Forward
C : Reverse
O : Bipolar analog input
C : Preset speed 1 Bipolar analog input
4 O : Stop (Disable)
C : Run (Enable)
O : Forward
C : Reverse
2nd Analog Input
(eg varies torque limit) Bipolar analog input
Digi input 3 Analog input Preset value
Open Open Preset speed 1
Closed Open Preset speed 2
Open Closed Preset speed 3
5 O : Stop (Disable)
C : Run (Enable)
O : Forward
C : Reverse
Closed Closed Preset speed 4
6 2) O : Stop (Disable)
C : Run (Enable)
O : Forward
C : Reverse
External trip input :
O : Trip C : OK Bipolar analog input
7 O : Stop (Disable)
C : Run Forward
O : Stop (Disable)
C : Run Reverse
O : Bipolar analog input
C : Preset speed 1 Bipolar analog input
8 2) O : Stop (Disable)
C : Run Forward
O : Stop (Disable)
C : Run Reverse
O : Preset speed 1
C : Bipolar analog input Bipolar analog input
Digi input 3 Analog input Preset value
Open Open Preset speed 1
Closed Open Preset speed 2
Open Closed Preset speed 3
9 O : Stop (Disable)
C : Run Forward
O : Stop (Disable)
C : Run Reverse
Closed Closed Preset speed 4
10 2) O : Stop (Disable)
C : Run Forward
O : Stop (Disable)
C : Run Reverse
External trip input :
O : Trip C : OK Bipolar analog input
11 O : Stop (Disable)
C : Run (Enable)
O : Bipolar analog input
C : Preset speed 1
External trip input :
O : Trip C : OK Bipolar analog input
12 2) O : Stop (Disable)
C : Run (Enable)
O : Preset speed 1
C : Bipolar analog input
External trip input :
O : Trip C : OK Bipolar analog input
13 Normally open (NO)
Momentarily close to run
Normally closed (NC)
Momentarily open to stop
O : Bipolar analog input
C : Preset speed 1 Bipolar analog input
14
Normally open (NO)
Momentarily close to run
forward
Normally closed (NC)
Momentarily open to stop
Normally open (NO)
Momentarily close to run
reverse
Bipolar analog input
15 O : Stop (Disable)
C : Run (Enable)
O : Forward
C : Reverse
O : Decel ramp 1
C : Decel ramp 2 Bipolar analog input
16 O : Stop (Disable)
C : Run (Enable)
O : Forward
C : Reverse
O : Decel ramp 1
C : Decel ramp 2
O : Preset speed 1
C : Preset speed 2
17
Normally open (NO)
Momentarily close to run
forward
Normally closed (NC)
Momentarily open to stop
Normally open (NO)
Momentarily close to run
reverse
O : Preset speed 1
C : Keypad mode
Digi input 2 Digi input 3 Preset value
Open Open Preset speed 1
Closed Open Preset speed 2
Open Closed Preset speed 3
18 O : Stop (Disable)
C : Run (Enable)
Closed Closed Preset speed 4
O : Terminal mode
C : Keypad mode
19 O : Stop (Disable)
C : Run (Enable)
O : Bipolar analog input
C : 2nd analog input 2nd analog input Bipolar analog input
20 1) O : Stop (Disable)
C : Run (Enable)
2nd digital output :
Drive healthy = +24V
O : Bipolar analog input
C : Preset speed1 Bipolar analog input
21 1) O : Stop (Disable)
C : Run (Enable)
2nd digital output :
Drive healthy = +24V
O : Forward
C : Reverse Bipolar analog input
22 1) O : Stop (Disable)
C : Run (Enable)
2nd digital output :
Drive healthy = +24V
External trip input :
O : Trip C : OK Bipolar analog input
Notes :
1) When P2-01 = 20, 21 or 22, the 2nd digital input is configured as an output, which outputs +24V
when the drive is healthy, otherwise 0V
2) When connecting a motor thermistor, connect between terminals 1 & 4, set P2-01 = 6, 10, 11,
12 or 22 (Uses external trip input)
9
3.4 Control Terminal Connections
The User Control terminals are available via an 11-way pluggable connector. All
terminals are galvanically isolated, allowing direct connection to other equipment.
Do not connect mains supply voltages to any terminals other than the User
relay output. Permanent damage will otherwise result.
All other inputs will withstand up to 30V dc without damage.
The functionality of the inputs and outputs is user configurable. All operating modes are
set up via the parameter set.
Up to 100mA can be sourced from the User +24V output and up to 20mA from the
analog output.
The control terminals are defined as follows :
Terminal 1: +24V, 100mA user output.
Terminal 2: Digital input 1, positive logic. “Logic 1” when Vin > 8V DC
Terminal 3: Digital input 2, positive logic. “Logic 1” when Vin > 8V DC
2nd digital output : 0 / 24V, 10mA max
Terminal 4: 2nd analog input, 11-bit (0.05%). 0..10V, 0..20mA, 4..20mA.
Digital input 3, positive logic. “Logic 1” when Vin > 8V DC.
Terminal 5: +24V, 100mA reference output (for use with potentiometer).
Terminal 6: Bipolar analog input, +/-12-bit (0.025%).
Configurable for : 0..24V, 0..10V, -10V...10V, -24V…24V
Terminal 7: 0V (User GND). Connected to terminal 9
Terminal 8: Analog output, 8-bit (0.25%). 0..10V, 4..20mA.
Digital output : 0 / 24V, 20mA max
Terminal 9: 0V (User GND). Connected to terminal 7
Terminal 10: User relay output. Potential free contacts. 30Vdc 5A, 250Vac 6A
Terminal 11: User relay output. Potential free contacts. 30Vdc 5A, 250Vac 6A
Key control terminal information :
•Maximum input voltage on any terminal 30V dc
•All outputs short circuit proof
•Recommended potentiometer resistance : 10k Ohm
•Digital input response time < 8ms
•Bipolar analog input response time < 16ms. Resolution +/-12 bit (0.025%)
•Second analog input response time < 16ms. Resolution +11 bit (0.05%)
•Analog / Digital output response time < 16ms. Resolution 8 bit (0.25%)
2 3 4 5 6 7 8 9 10 111

10
4. Operation
4.1 Managing the keypad
The drive is configured and its operation monitored via the keypad and display
NAVIGATE: Used to display real-time information,
to access and exit parameter edit mode and to store
parameter changes
UP: Used to increase speed in real-time mode or to
increase parameter values in parameter edit mode
DOWN: Used to decrease speed in real-time mode
or to decrease parameter values in parameter edit
mode
RESET / STOP: Used to reset a tripped drive. When in Keypad mode (see
below and P1-12 in the parameter section) is used to Stop a running drive.
START: When in keypad mode, used to Start a stopped drive or to reverse the
direction of rotation if bi-directional keypad mode is enabled (see P1-12 in the
parameter section)
To change a parameter value press and hold the NAVIGATE key for >1s whilst the
drive displays STOP. The display changes to P1-01, indicating parameter 01 in
parameter group 1. Press and release the NAVIGATE key to display the value of this
parameter. Change to the required value using the UP and DOWN keys. Press and
release the NAVIGATE key once more to store the change. Press and hold the
NAVIGATE key for >1s to return to real-time mode. The display shows STOP if the drive
is stopped or the real-time information (eg speed) if the drive is running.
To change parameter group, ensure that extended menu access is enabled then
press NAVIGATE, simultaneously pressing and releasing the UP key until the required
parameter group is displayed.
To reset factory default parameters, press UP, DOWN and STOP for >2s. The
display shows “P-dEF”. Press the STOP button to acknowledge and reset the drive.
4.2 Easy startup
1. Connect motor to drive, checking star/delta connection for the voltage rating
2. Enter motor data from motor nameplate :
P1-07 = motor rated voltage
P1-08 = motor rated current
P1-09 = motor rated frequency
3. Enable the drive. The drive automatically carries out a static Auto-tune
4. Optidrive 3GV Only - For high performance vector, set P1-14 = 101, P4-01 = 0,
then set P4-05 = motor nameplate power factor (cos Φ). Setting P4-02 = 1 then
starts the static Auto-tune.
To operate in terminal mode (default setting), connect a switch between terminals 1
and 2 on the user terminal block. Connect a potentiometer (2k2 to 10k) between
terminals 5, 6 and 7 with the wiper connected to pin 6.
Close the switch to enable the drive. Adjust speed with the potentiometer.
To operate in keypad mode, set P1-12 = 1 (uni-directional) or 2 (bi-directional). Place
a wire link or switch between terminals 1 and 2 on the user terminal block to enable the
drive. Now press START. The drive enables at 0Hz. Press the UP button to increase
speed. Press the STOP button to ramp to stop.
The desired target speed can be preset by pressing STOP whilst the drive is stopped.
When the START key is subsequently pressed, drive will then ramp to this speed.
H
8
8
5
0
.
0
15
5.3 Group 3 : User feedback control (PID control) - Not available for 3GV Modbus version
P3-01 User PID Proprtional
Gain 0.1 ... 30.0 2 Higher value used for high inertia. Too
high a value gives instability.
P3-02 User PID Integral
time constant 0.0s ... 30.0s 1s Higher value gives slower, more
damped response.
P3-03 User PID Differential
time constant 0.00s ... 1.00s 0.00 Set to zero (disabled) for most
applications.
P3-04 User PID operating
mode
0: Direct
1: Inverse 0
If an increasing feedback signal should
increase the speed of the motor, set to
‘Inverse’ mode.
P3-05 User PID reference
select
0: Digital
1: Analog 0
Sets the source for the PID control
reference signal. When set to 1, the
bipolar analog input is used.
P3-06 User PID digital
reference 0 … 100% 0.0 % Sets the preset reference used when
P3-05 = 0.
P3-07 User PID controller
output high limit
P3-08 to 100% of control
range 100% Preset PID controller output upper
(speed) limit. 100% = P1-01.
P3-08 User PID controller
output low limit 0 to P3-07 0 Preset PID controller output lower
(speed) limit. 100% = P1-01.
P3-09 User PID output limit
control
0: Digital output limits
1: Analog upper limit
2: Analog lower limit
3: PID output + Bipolar
Analog input
0
When set to 1 or 2, the bipolar analog
input is used to vary the PID output
limit between P1-02 and P1-01.
When set to 3, the bipolar analog input
value will be added to the PID output.
P3-10 User PID feedback
select
0: 2nd Analog input
1: Bipolar analog input 0 This parameter selects feedback signal
source.
5.4 Group 4 : High performance Motor control
P4-01 Control mode
0: Speed control (vector)
1: Torque control (vector)
2: Speed control (V/F)
2
Whenever changing control mode,
ensure that an Auto-tune (P4-02) is
always carried out for best motor
performance.
P4-02 Motor parameter
auto-tune
0: Disable
1: Enable 0
When set to 1, drive immediately
carries out a static (non-rotating)
motor parameter measurement
operation to configure the motor
parameters.
Parameter P1-07, P1-08 P1-09 and
P4-05 must be set correctly according
to the motor nameplate before
enabling this function.
Auto-tune runs automatically on first
enable after parameter default
operation and P1-08 was changed.
No hardware enable is required.
P4-03 Speed controller
Proportional Gain
0 … 4096
(internal value)
Drive
rating
Higher value used for high inertia. Too
high a value gives instability.
P4-04 Speed controller
Integral time constant 0.000 … 1.000s 0.05s Higher value gives slower, more
damped response.
P4-05 Motor power factor 0.50 … 0.99 Drive
rating
Motor nameplate power factor (cos Φ)
Required for all vector control modes
P4-06 Torque reference
select
0: Preset value
1: Bipolar analog input
2: 2nd analog input
3: Modbus ref (Optional)
0
Used when in vector control mode to
set a maximum torque limit.
Note that option 3 is not available in
the standard OD Plus.
P4-07 Maximum torque limit
/ Torque reference 0 … 200% 200% Preset torque ref when P4-01 = 1.
Max torque limit when P4-01 = 0.
P4-08 Minimum torque limit 0…150% 0 Defines the minimum limit for the
motor shaft torque
P4-09 V/F characteristic
adjustment frequency 0 … P1-09 0.0Hz Sets the frequency at which the
adjustment voltage (P4-10) is applied.
P4-10 V/F characteristic
adjustment voltage 0 … P1-07 0 Adjusts the motor voltage by this
value at frequency set in P4-09.

14
P2-26 Modbus RTU
baudrate option 9.6kbps to 115.2kbps 115.2
Modbus RTU communication
network baudrate. Only available if
optional Modbus plug-in installed
P2-27 Drive communication
address 0: Disable 1..63 1 Distinct drive address used for all
drive serial communications.
P2-28 Master / Slave mode
select
0: Slave mode
1: Master mode 0
When in Master mode, the drive
transmits its operational status via
the serial data link. Used to control
slave drives via the serial link.
P2-27 must be 1 for Master mode.
P2-29
Digital speed
reference preset
scaling factor
0…500%, steps of 0.1% 100.0%
The digital speed reference input
to the drive is scaled by this factor
when P2-35 = 1. Operates on
references originating from the
serial data link.
Can be used as an electronic
gearbox for Master / Slave
applications.
P2-30 Bipolar analog input
format
0..24V, 0..10V, -10..10V,
-24..24V 0..24V
Configures the analog input format
to match that of the reference
signal connected to terminal 6
P2-31 Bipolar analog input
scaling 0...500.0% 100.0%
Scales the analog input by this
factor. Set to 200% to give full
speed range control with 0..5V
input (when P2-30 = 0..10V)
P2-32 Bipolar analog input
offset -500.0%...500.0% 0.0%
Sets the offset from zero at which
speed starts to ramp up.
Value is “%” of the full scale input
voltage.
P2-33 2nd analog input
format
0 / 24V (digital input)
0..10V,
4..20mA, 0..20mA
0 / 24V
Determines the format of the 2nd
analog input.
Selecting 0 / 24V sets up the input
as a digital input.
P2-34 2nd analog input
scaling 0...500.0% 100.0%
Scales the 2nd analog input by the
factor set in this parameter.
P2-35
Digital speed
reference scaling
control
0: Disabled (no scaling)
1: Scaling set by preset
value in P2-29
2: Slave speed scaled
by preset value in
P2-29, then bipolar
analog input added
as offset
3: Slave speed scaled
by preset value in
P2-29 and by bipolar
analog input
0
Only active in keypad control mode
and usually used in a Master/Slave
network application.
When P2-35 = 1, actual speed =
Digital speed * P2-29.
When P2-35 = 2, actual speed =
(Digital speed x P2-29) +
bipolar analog input
Max analog input is equal to P1-01
When P2-35 = 3, actual speed =
(Digital speed x P2-29) x
bipolar analog input
Analog input scales 0% … 200%
P2-36 Analog output format
0..10V
4..20mA
10..0V
20..4mA
0..10V
Determines the analog output
format.
Min load impedance in voltage
mode 1k Ohm.
Max load impedance in current
mode 1k Ohm.
P2-37 Extended menu
access code define 0…9999 101
Defines the extended menu
access code used in P1-14.
P2-38 Parameter Lock 0: Unlocked
1: Locked 0 When locked, all parameter
changes are prevented.
P2-39 Hours run clock 0 to 99999 hours Read
only
Indicates the number of hours the
drive has been running since new.
P2-40 Drive type / rating
“ 0.37“, “0 230” :
3GV 230V 0.37kW
“HP 20”, “1 460“ :
VTC, 460V 20HP
Read
only
Indicates drive power rating, type
code and voltage rating.
Drive type code indicates 3GV (0),
VTC (1) or other drive type
11
5. Drive Configuration
5.1 Group 1 : Basic Parameters
Par. Description Range Default Explanation
P1-01 Max speed limit P1-02 to P1-09 x 5
(up to 2 000Hz max) 50 Hz
Sets the maximum speed limit.
Display of Hz or rpm dependent on
P1-10. Maximum speed limit
dependent on switching frequency:
Max Limit = P2-24 / 16.
P1-02 Min speed limit 0 to P1-01 0 Hz Minimum speed limit. Hz or rpm
display depending on P1-10.
P1-03 Accel ramp time 0 to 3 000s 5.0s Time to ramp from 0 to rated
frequency (P1-09)
P1-04 Decel ramp time 0 to 3 000s 5.0s
Time to ramp from rated frequency
(P1-09) to 0. When P1-04 = 0, the
ramp is varied dynamically to give
the fastest possible ramp to STOP.
P1-05 Stop mode select
0: Ramp to stop
1: Coast to stop
2: Ramp to stop
0
If the supply is lost and P1-05 = 0
then the drive will try to continue
running by reducing load speed,
using the load as a generator
If P1-05 = 2, the drive ramps on
2nd decel ramp P2-25 to stop.
P1-06 Energy Optimisation 0: Disable
1: Enable 0
When enabled, automatically
reduces applied motor voltage on
light load. Used in V/F mode only.
P1-07 Motor rated voltage
0V, 20V to 250V
0V, 20V to 500V
0V, 20V to 600V
230V
400V
(460V)
575V
Set to motor rated voltage from
nameplate. When in V/F mode,
P1-07 = 0 gives faster deceleration
ramp without over-voltage trip
P1-08 Motor rated current 20% to 100% of drive
rated current
Drive
rating
Set to motor rated current from
nameplate (Amps)
P1-09 Motor rated
frequency 25 to 2 000Hz 50Hz
(60Hz)
Set to motor rated frequency from
nameplate (Hz). Maximum limit
dependent on switching frequency:
Max Limit = P2-24 / 16.
P1-10 Motor rated speed 0 to 60 000rpm 0
When 0, drive operates in Hz.
Upper limit set to 60 x P1-09.
This value usually can be found in
the motor nameplate.
P1-11 Preset speed 1 -P1-01 to P1-01 50Hz
(60Hz)
Sets jog / preset speed at which
drive runs when preset speed 1
selected via digital inputs.
(see also P2-01)
P1-12 Terminal / Keypad
control of drive
0: Terminal control
1: Keypad control
(Fwd only)
2: Keypad control
(Fwd and Rev)
3: Enable User PID
4: Modbus network
control (Optional)
0
0 : Terminal control
1 : Uni-direction keypad control.
2 : Bi-directional keypad control.
Keypad START button toggles
between forward and reverse.
3 : User PID (feedback control)
active, setup in parameter group 3.
4 : Drive controlled via integrated
Modbus RTU interface. Note that
this is an upgrade option and is not
available in the standard OD Plus.
P1-13 Trip Log Last 4 trips stored - Latest 4 trips stored. Most recent
trip displayed first.
P1-14 Extended Menu
Access code 0 to 30 000 0
Permits access to extended menu
when P1-14 = P2-37. Default
access value = 101.
Notes:
•Default parameter values for Horse Power rated drives are shown in brackets

12
5.2 Group 2 : Extended Parameters
Par. Description Range Default Explanation
P2-01 Digital input function
select 0 to 22 0
Defines the function of the digital
inputs. See sections 5.5 … 5.7 on
pages 16…18 for more details.
P2-02 Preset speed 2 -P1-01 to P1-01 0 Hz Sets jog / preset speed 2
P2-03 Preset speed 3 -P1-01 to P1-01 0 Hz Sets jog / preset speed 3
P2-04 Preset speed 4 -P1-01 to P1-01 0 Hz Sets jog / preset speed 4
P2-05 Preset speed 5 -P1-01 to P1-01 0 Hz Sets jog / preset speed 5
P2-06 Preset speed 6 -P1-01 to P1-01 0 Hz Sets jog / preset speed 6
P2-07 Preset speed 7 -P1-01 to P1-01 0 Hz Sets jog / preset speed 7
P2-08 Preset speed 8 -P1-01 to P1-01 0 Hz Sets jog / preset speed 8
P2-09 Skip frequency P1-02 to P1-01 0
Centre point of skip frequency
band set up in conjunction with
P2-10.
P2-10 Skip frequency band 0 to P1-01 0
(disable)
Width of skip frequency band
centred on frequency set in P2-09.
P2-11 Analog output
function select
(Digital output mode)
0: Drive enabled
1: Drive healthy
2: Motor at target speed
3: Motor speed > 0
4: Motor speed > limit
5: Motor torque > limit
6: 2nd Analog in > limit
(Analog output mode)
7: Motor speed
8: Motor torque
9: Motor power (kW)
10: Motor current
7
For values 0 to 6, analog output
functions as a digital output.
(0V or 24V output)
The control limit used for settings
4, 5 and 6 is defined in P2-12(h)
and P2-12(L).
For values between 7 and 9, the
output is analog signal, operating
between 0..10V or 4..20mA.
(as set in P2-36)
Full scale analog output results at
max speed, 2x rated motor torque
(motor rated output torque), 1.5x
rated power of the drive or 2x rated
motor current.
P2-12
(h)
Digital output control
high limit
Speed : 0..100%
(100% = max speed)
Torque : 0..200%
(100% = rated torque)
PID feedback : 0..100%
(100% = max 2nd analog
input)
100%
Digital output state set to logic 1
when selected value in P2-11
larger than this limit.
Limit in P2-12 relates to speed if
P2-11 = 4, to motor torque if P2-11
= 5 or to the PID feedback value
(2nd analog input) if P2-11 = 6.
P2-12
(L)
Digital output control
low limit 0 … P2-12(h) 100%
Digital output state back to logic 0
when selected value in P2-11 less
than or equal to this limit.
(P2-11 = 4,5 or 6)
P2-13 User relay output
function select
0: Drive Enabled
1: Drive healthy
2: Motor at target speed
3: Motor speed > 0
4: Motor speed > limit
5: Motor torque > limit
6: 2nd Analog in > limit
1
If P2-15 = 0 (Normally Open), the
relay contacts are closed when the
selected condition is fulfilled.
If P2-15 = 1 (Normally Closed), the
relay contacts are open when the
selected condition is fulfilled.
P2-14
(h)
User relay output
control high limit
Speed : 0..100%
(100% = max speed)
Torque : 0..200%
(100% = rated torque)
PID feedback : 0..100%
(100% = max 2nd analog
input)
100%
User relay output closes (P2-15=0)
when selected value in P2-13
larger than this limit.
Limit in P2-14 relates to speed if
P2-13 = 4, to motor torque if P2-13
= 5 or to the PID feedback value
(2nd analog input) if P2-13 = 6.
P2-14
(L)
User relay output
control low limit 0 … P2-14(h) 100%
Digital output state back to logic 0
when selected value in P2-13 less
than or equal to this limit.
(P2-13 = 4,5 or 6)
P2-15 Relay output mode 0: Normally Open (NO)
1: Normally Closed (NC) 0 (N.O.) The drive must be powered up for
the relay contacts to be closed.
13
P2-16 Zero Speed holding
time 0 … 60s 0.2s
Determines the time for which the
zero speed is held on the output
before disabling the drive.
P2-17 Start mode select
Edgr-r :
Close digital input 1after
power up to start drive
Auto-0 :
drive runs whenever
digital input 1 is closed
Auto-1…5 :
as Auto-0, except 1..5
attempts to restart after
a trip
Auto-0
When set to Edge-r, if drive is
powered up with digital Input 1
closed (enabled), drive will not run.
The switch (digital input 1) must be
opened and closed after power up
or after a clearing a trip for the
drive to run.
When set to Auto-0, drive will run
whenever digital input 1 is closed
(if not tripped).
Auto-1…5 makes 1…5 attempts to
automatically restart after a trip
(20s between attempts in default).
Drive must be powered down to
reset the counter.
P2-18
Spin Start Enable
(Not available for 3GV
Modbus version)
0: Disable
1: Enable 0
When enabled, drive detects motor
speed and starts driving the motor
from this speed. A short delay of
approx 1s will result after enabling
the drive before speed is detected.
(Not valid in torque control mode)
P2-19 Keypad restart mode
0: Minimum speed
1: previous speed
2: Min-speed (Auto-r)
3: prev. speed (Auto-r)
1
If set to 0 or 2, drive will always
start from minimum speed. If set to
1 or 3, drive ramps up to the
operating speed prior to the last
STOP command.
If set to 2 and 3, the status of
digital input 1 controls drive to start
or stop. The start and stop button
will not work in this case.
P2-20 Standby mode 0: Disable
1 … 60s 0
If P2-20 >0, drive enters standby
mode (disables output) if minimum
speed (P1-02) is maintained for
the time specified in P2-20. If
P2-16 >0, this function is disabled.
P2-21 Display scaling factor 0.000 to 30.000 0.000
Disabled if set to zero.
The variable selected in P2-22 is
multiplied by this factor and
displayed as a real-time value on
the drive, in addition to speed,
current and power.
P2-22 Display scaling
source
0: 2nd analog input
1: Speed
2: Motor output torque
0 Selects the variable to be scaled
by the factor set in P2-21.
P2-23 Brake circuit enable
0: Disable
1: Enable + lo power
2: Enable + hi power
3: Enable, no protection
0
Enables the internal brake chopper
Overload protection in software
when set to 1 or 2. See rating
tables for resistor sizing guidelines.
P2-24 Effective switching
frequency
S1, S2 230V : 4..32kHz
S2 400V : 4..32kHz
S3 400V : 4..24kHz
S4 400V : 4..24kHz
S5*400V : 4..16kHz
S6*400V : 4..16kHz
* Max limit dependent on
power rating
16 kHz
8 kHz
4 kHz
4 kHz
4 kHz
4 kHz
Effective power stage switching
frequency. Improved acoustic
noise and output current waveform
occurs with increasing switching
frequency at the expense of
increased losses within the drive.
“Auto” selects minimum possible
switching frequency for the speed
range selected (P2-24 must be
16x P1-01 or greater)
P2-25 Second deceleration
ramp time 0s … 3 000s 30s
Selected automatically on mains
loss if P1-05 = 0 or 2. Can also be
selected via digital inputs during
operation (see section 5.5 and 5.6)

12
5.2 Group 2 : Extended Parameters
Par. Description Range Default Explanation
P2-01 Digital input function
select 0 to 22 0
Defines the function of the digital
inputs. See sections 5.5 … 5.7 on
pages 16…18 for more details.
P2-02 Preset speed 2 -P1-01 to P1-01 0 Hz Sets jog / preset speed 2
P2-03 Preset speed 3 -P1-01 to P1-01 0 Hz Sets jog / preset speed 3
P2-04 Preset speed 4 -P1-01 to P1-01 0 Hz Sets jog / preset speed 4
P2-05 Preset speed 5 -P1-01 to P1-01 0 Hz Sets jog / preset speed 5
P2-06 Preset speed 6 -P1-01 to P1-01 0 Hz Sets jog / preset speed 6
P2-07 Preset speed 7 -P1-01 to P1-01 0 Hz Sets jog / preset speed 7
P2-08 Preset speed 8 -P1-01 to P1-01 0 Hz Sets jog / preset speed 8
P2-09 Skip frequency P1-02 to P1-01 0
Centre point of skip frequency
band set up in conjunction with
P2-10.
P2-10 Skip frequency band 0 to P1-01 0
(disable)
Width of skip frequency band
centred on frequency set in P2-09.
P2-11 Analog output
function select
(Digital output mode)
0: Drive enabled
1: Drive healthy
2: Motor at target speed
3: Motor speed > 0
4: Motor speed > limit
5: Motor torque > limit
6: 2nd Analog in > limit
(Analog output mode)
7: Motor speed
8: Motor torque
9: Motor power (kW)
10: Motor current
7
For values 0 to 6, analog output
functions as a digital output.
(0V or 24V output)
The control limit used for settings
4, 5 and 6 is defined in P2-12(h)
and P2-12(L).
For values between 7 and 9, the
output is analog signal, operating
between 0..10V or 4..20mA.
(as set in P2-36)
Full scale analog output results at
max speed, 2x rated motor torque
(motor rated output torque), 1.5x
rated power of the drive or 2x rated
motor current.
P2-12
(h)
Digital output control
high limit
Speed : 0..100%
(100% = max speed)
Torque : 0..200%
(100% = rated torque)
PID feedback : 0..100%
(100% = max 2nd analog
input)
100%
Digital output state set to logic 1
when selected value in P2-11
larger than this limit.
Limit in P2-12 relates to speed if
P2-11 = 4, to motor torque if P2-11
= 5 or to the PID feedback value
(2nd analog input) if P2-11 = 6.
P2-12
(L)
Digital output control
low limit 0 … P2-12(h) 100%
Digital output state back to logic 0
when selected value in P2-11 less
than or equal to this limit.
(P2-11 = 4,5 or 6)
P2-13 User relay output
function select
0: Drive Enabled
1: Drive healthy
2: Motor at target speed
3: Motor speed > 0
4: Motor speed > limit
5: Motor torque > limit
6: 2nd Analog in > limit
1
If P2-15 = 0 (Normally Open), the
relay contacts are closed when the
selected condition is fulfilled.
If P2-15 = 1 (Normally Closed), the
relay contacts are open when the
selected condition is fulfilled.
P2-14
(h)
User relay output
control high limit
Speed : 0..100%
(100% = max speed)
Torque : 0..200%
(100% = rated torque)
PID feedback : 0..100%
(100% = max 2nd analog
input)
100%
User relay output closes (P2-15=0)
when selected value in P2-13
larger than this limit.
Limit in P2-14 relates to speed if
P2-13 = 4, to motor torque if P2-13
= 5 or to the PID feedback value
(2nd analog input) if P2-13 = 6.
P2-14
(L)
User relay output
control low limit 0 … P2-14(h) 100%
Digital output state back to logic 0
when selected value in P2-13 less
than or equal to this limit.
(P2-13 = 4,5 or 6)
P2-15 Relay output mode 0: Normally Open (NO)
1: Normally Closed (NC) 0 (N.O.) The drive must be powered up for
the relay contacts to be closed.
13
P2-16 Zero Speed holding
time 0 … 60s 0.2s
Determines the time for which the
zero speed is held on the output
before disabling the drive.
P2-17 Start mode select
Edgr-r :
Close digital input 1after
power up to start drive
Auto-0 :
drive runs whenever
digital input 1 is closed
Auto-1…5 :
as Auto-0, except 1..5
attempts to restart after
a trip
Auto-0
When set to Edge-r, if drive is
powered up with digital Input 1
closed (enabled), drive will not run.
The switch (digital input 1) must be
opened and closed after power up
or after a clearing a trip for the
drive to run.
When set to Auto-0, drive will run
whenever digital input 1 is closed
(if not tripped).
Auto-1…5 makes 1…5 attempts to
automatically restart after a trip
(20s between attempts in default).
Drive must be powered down to
reset the counter.
P2-18
Spin Start Enable
(Not available for 3GV
Modbus version)
0: Disable
1: Enable 0
When enabled, drive detects motor
speed and starts driving the motor
from this speed. A short delay of
approx 1s will result after enabling
the drive before speed is detected.
(Not valid in torque control mode)
P2-19 Keypad restart mode
0: Minimum speed
1: previous speed
2: Min-speed (Auto-r)
3: prev. speed (Auto-r)
1
If set to 0 or 2, drive will always
start from minimum speed. If set to
1 or 3, drive ramps up to the
operating speed prior to the last
STOP command.
If set to 2 and 3, the status of
digital input 1 controls drive to start
or stop. The start and stop button
will not work in this case.
P2-20 Standby mode 0: Disable
1 … 60s 0
If P2-20 >0, drive enters standby
mode (disables output) if minimum
speed (P1-02) is maintained for
the time specified in P2-20. If
P2-16 >0, this function is disabled.
P2-21 Display scaling factor 0.000 to 30.000 0.000
Disabled if set to zero.
The variable selected in P2-22 is
multiplied by this factor and
displayed as a real-time value on
the drive, in addition to speed,
current and power.
P2-22 Display scaling
source
0: 2nd analog input
1: Speed
2: Motor output torque
0 Selects the variable to be scaled
by the factor set in P2-21.
P2-23 Brake circuit enable
0: Disable
1: Enable + lo power
2: Enable + hi power
3: Enable, no protection
0
Enables the internal brake chopper
Overload protection in software
when set to 1 or 2. See rating
tables for resistor sizing guidelines.
P2-24 Effective switching
frequency
S1, S2 230V : 4..32kHz
S2 400V : 4..32kHz
S3 400V : 4..24kHz
S4 400V : 4..24kHz
S5*400V : 4..16kHz
S6*400V : 4..16kHz
* Max limit dependent on
power rating
16 kHz
8 kHz
4 kHz
4 kHz
4 kHz
4 kHz
Effective power stage switching
frequency. Improved acoustic
noise and output current waveform
occurs with increasing switching
frequency at the expense of
increased losses within the drive.
“Auto” selects minimum possible
switching frequency for the speed
range selected (P2-24 must be
16x P1-01 or greater)
P2-25 Second deceleration
ramp time 0s … 3 000s 30s
Selected automatically on mains
loss if P1-05 = 0 or 2. Can also be
selected via digital inputs during
operation (see section 5.5 and 5.6)

14
P2-26 Modbus RTU
baudrate option 9.6kbps to 115.2kbps 115.2
Modbus RTU communication
network baudrate. Only available if
optional Modbus plug-in installed
P2-27 Drive communication
address 0: Disable 1..63 1 Distinct drive address used for all
drive serial communications.
P2-28 Master / Slave mode
select
0: Slave mode
1: Master mode 0
When in Master mode, the drive
transmits its operational status via
the serial data link. Used to control
slave drives via the serial link.
P2-27 must be 1 for Master mode.
P2-29
Digital speed
reference preset
scaling factor
0…500%, steps of 0.1% 100.0%
The digital speed reference input
to the drive is scaled by this factor
when P2-35 = 1. Operates on
references originating from the
serial data link.
Can be used as an electronic
gearbox for Master / Slave
applications.
P2-30 Bipolar analog input
format
0..24V, 0..10V, -10..10V,
-24..24V 0..24V
Configures the analog input format
to match that of the reference
signal connected to terminal 6
P2-31 Bipolar analog input
scaling 0...500.0% 100.0%
Scales the analog input by this
factor. Set to 200% to give full
speed range control with 0..5V
input (when P2-30 = 0..10V)
P2-32 Bipolar analog input
offset -500.0%...500.0% 0.0%
Sets the offset from zero at which
speed starts to ramp up.
Value is “%” of the full scale input
voltage.
P2-33 2nd analog input
format
0 / 24V (digital input)
0..10V,
4..20mA, 0..20mA
0 / 24V
Determines the format of the 2nd
analog input.
Selecting 0 / 24V sets up the input
as a digital input.
P2-34 2nd analog input
scaling 0...500.0% 100.0%
Scales the 2nd analog input by the
factor set in this parameter.
P2-35
Digital speed
reference scaling
control
0: Disabled (no scaling)
1: Scaling set by preset
value in P2-29
2: Slave speed scaled
by preset value in
P2-29, then bipolar
analog input added
as offset
3: Slave speed scaled
by preset value in
P2-29 and by bipolar
analog input
0
Only active in keypad control mode
and usually used in a Master/Slave
network application.
When P2-35 = 1, actual speed =
Digital speed * P2-29.
When P2-35 = 2, actual speed =
(Digital speed x P2-29) +
bipolar analog input
Max analog input is equal to P1-01
When P2-35 = 3, actual speed =
(Digital speed x P2-29) x
bipolar analog input
Analog input scales 0% … 200%
P2-36 Analog output format
0..10V
4..20mA
10..0V
20..4mA
0..10V
Determines the analog output
format.
Min load impedance in voltage
mode 1k Ohm.
Max load impedance in current
mode 1k Ohm.
P2-37 Extended menu
access code define 0…9999 101
Defines the extended menu
access code used in P1-14.
P2-38 Parameter Lock 0: Unlocked
1: Locked 0 When locked, all parameter
changes are prevented.
P2-39 Hours run clock 0 to 99999 hours Read
only
Indicates the number of hours the
drive has been running since new.
P2-40 Drive type / rating
“ 0.37“, “0 230” :
3GV 230V 0.37kW
“HP 20”, “1 460“ :
VTC, 460V 20HP
Read
only
Indicates drive power rating, type
code and voltage rating.
Drive type code indicates 3GV (0),
VTC (1) or other drive type
11
5. Drive Configuration
5.1 Group 1 : Basic Parameters
Par. Description Range Default Explanation
P1-01 Max speed limit P1-02 to P1-09 x 5
(up to 2 000Hz max) 50 Hz
Sets the maximum speed limit.
Display of Hz or rpm dependent on
P1-10. Maximum speed limit
dependent on switching frequency:
Max Limit = P2-24 / 16.
P1-02 Min speed limit 0 to P1-01 0 Hz Minimum speed limit. Hz or rpm
display depending on P1-10.
P1-03 Accel ramp time 0 to 3 000s 5.0s Time to ramp from 0 to rated
frequency (P1-09)
P1-04 Decel ramp time 0 to 3 000s 5.0s
Time to ramp from rated frequency
(P1-09) to 0. When P1-04 = 0, the
ramp is varied dynamically to give
the fastest possible ramp to STOP.
P1-05 Stop mode select
0: Ramp to stop
1: Coast to stop
2: Ramp to stop
0
If the supply is lost and P1-05 = 0
then the drive will try to continue
running by reducing load speed,
using the load as a generator
If P1-05 = 2, the drive ramps on
2nd decel ramp P2-25 to stop.
P1-06 Energy Optimisation 0: Disable
1: Enable 0
When enabled, automatically
reduces applied motor voltage on
light load. Used in V/F mode only.
P1-07 Motor rated voltage
0V, 20V to 250V
0V, 20V to 500V
0V, 20V to 600V
230V
400V
(460V)
575V
Set to motor rated voltage from
nameplate. When in V/F mode,
P1-07 = 0 gives faster deceleration
ramp without over-voltage trip
P1-08 Motor rated current 20% to 100% of drive
rated current
Drive
rating
Set to motor rated current from
nameplate (Amps)
P1-09 Motor rated
frequency 25 to 2 000Hz 50Hz
(60Hz)
Set to motor rated frequency from
nameplate (Hz). Maximum limit
dependent on switching frequency:
Max Limit = P2-24 / 16.
P1-10 Motor rated speed 0 to 60 000rpm 0
When 0, drive operates in Hz.
Upper limit set to 60 x P1-09.
This value usually can be found in
the motor nameplate.
P1-11 Preset speed 1 -P1-01 to P1-01 50Hz
(60Hz)
Sets jog / preset speed at which
drive runs when preset speed 1
selected via digital inputs.
(see also P2-01)
P1-12 Terminal / Keypad
control of drive
0: Terminal control
1: Keypad control
(Fwd only)
2: Keypad control
(Fwd and Rev)
3: Enable User PID
4: Modbus network
control (Optional)
0
0 : Terminal control
1 : Uni-direction keypad control.
2 : Bi-directional keypad control.
Keypad START button toggles
between forward and reverse.
3 : User PID (feedback control)
active, setup in parameter group 3.
4 : Drive controlled via integrated
Modbus RTU interface. Note that
this is an upgrade option and is not
available in the standard OD Plus.
P1-13 Trip Log Last 4 trips stored - Latest 4 trips stored. Most recent
trip displayed first.
P1-14 Extended Menu
Access code 0 to 30 000 0
Permits access to extended menu
when P1-14 = P2-37. Default
access value = 101.
Notes:
•Default parameter values for Horse Power rated drives are shown in brackets

10
4. Operation
4.1 Managing the keypad
The drive is configured and its operation monitored via the keypad and display
NAVIGATE: Used to display real-time information,
to access and exit parameter edit mode and to store
parameter changes
UP: Used to increase speed in real-time mode or to
increase parameter values in parameter edit mode
DOWN: Used to decrease speed in real-time mode
or to decrease parameter values in parameter edit
mode
RESET / STOP: Used to reset a tripped drive. When in Keypad mode (see
below and P1-12 in the parameter section) is used to Stop a running drive.
START: When in keypad mode, used to Start a stopped drive or to reverse the
direction of rotation if bi-directional keypad mode is enabled (see P1-12 in the
parameter section)
To change a parameter value press and hold the NAVIGATE key for >1s whilst the
drive displays STOP. The display changes to P1-01, indicating parameter 01 in
parameter group 1. Press and release the NAVIGATE key to display the value of this
parameter. Change to the required value using the UP and DOWN keys. Press and
release the NAVIGATE key once more to store the change. Press and hold the
NAVIGATE key for >1s to return to real-time mode. The display shows STOP if the drive
is stopped or the real-time information (eg speed) if the drive is running.
To change parameter group, ensure that extended menu access is enabled then
press NAVIGATE, simultaneously pressing and releasing the UP key until the required
parameter group is displayed.
To reset factory default parameters, press UP, DOWN and STOP for >2s. The
display shows “P-dEF”. Press the STOP button to acknowledge and reset the drive.
4.2 Easy startup
1. Connect motor to drive, checking star/delta connection for the voltage rating
2. Enter motor data from motor nameplate :
P1-07 = motor rated voltage
P1-08 = motor rated current
P1-09 = motor rated frequency
3. Enable the drive. The drive automatically carries out a static Auto-tune
4. Optidrive 3GV Only - For high performance vector, set P1-14 = 101, P4-01 = 0,
then set P4-05 = motor nameplate power factor (cos Φ). Setting P4-02 = 1 then
starts the static Auto-tune.
To operate in terminal mode (default setting), connect a switch between terminals 1
and 2 on the user terminal block. Connect a potentiometer (2k2 to 10k) between
terminals 5, 6 and 7 with the wiper connected to pin 6.
Close the switch to enable the drive. Adjust speed with the potentiometer.
To operate in keypad mode, set P1-12 = 1 (uni-directional) or 2 (bi-directional). Place
a wire link or switch between terminals 1 and 2 on the user terminal block to enable the
drive. Now press START. The drive enables at 0Hz. Press the UP button to increase
speed. Press the STOP button to ramp to stop.
The desired target speed can be preset by pressing STOP whilst the drive is stopped.
When the START key is subsequently pressed, drive will then ramp to this speed.
H
8
8
5
0
.
0
15
5.3 Group 3 : User feedback control (PID control) - Not available for 3GV Modbus version
P3-01 User PID Proprtional
Gain 0.1 ... 30.0 2 Higher value used for high inertia. Too
high a value gives instability.
P3-02 User PID Integral
time constant 0.0s ... 30.0s 1s Higher value gives slower, more
damped response.
P3-03 User PID Differential
time constant 0.00s ... 1.00s 0.00 Set to zero (disabled) for most
applications.
P3-04 User PID operating
mode
0: Direct
1: Inverse 0
If an increasing feedback signal should
increase the speed of the motor, set to
‘Inverse’ mode.
P3-05 User PID reference
select
0: Digital
1: Analog 0
Sets the source for the PID control
reference signal. When set to 1, the
bipolar analog input is used.
P3-06 User PID digital
reference 0 … 100% 0.0 % Sets the preset reference used when
P3-05 = 0.
P3-07 User PID controller
output high limit
P3-08 to 100% of control
range 100% Preset PID controller output upper
(speed) limit. 100% = P1-01.
P3-08 User PID controller
output low limit 0 to P3-07 0 Preset PID controller output lower
(speed) limit. 100% = P1-01.
P3-09 User PID output limit
control
0: Digital output limits
1: Analog upper limit
2: Analog lower limit
3: PID output + Bipolar
Analog input
0
When set to 1 or 2, the bipolar analog
input is used to vary the PID output
limit between P1-02 and P1-01.
When set to 3, the bipolar analog input
value will be added to the PID output.
P3-10 User PID feedback
select
0: 2nd Analog input
1: Bipolar analog input 0 This parameter selects feedback signal
source.
5.4 Group 4 : High performance Motor control
P4-01 Control mode
0: Speed control (vector)
1: Torque control (vector)
2: Speed control (V/F)
2
Whenever changing control mode,
ensure that an Auto-tune (P4-02) is
always carried out for best motor
performance.
P4-02 Motor parameter
auto-tune
0: Disable
1: Enable 0
When set to 1, drive immediately
carries out a static (non-rotating)
motor parameter measurement
operation to configure the motor
parameters.
Parameter P1-07, P1-08 P1-09 and
P4-05 must be set correctly according
to the motor nameplate before
enabling this function.
Auto-tune runs automatically on first
enable after parameter default
operation and P1-08 was changed.
No hardware enable is required.
P4-03 Speed controller
Proportional Gain
0 … 4096
(internal value)
Drive
rating
Higher value used for high inertia. Too
high a value gives instability.
P4-04 Speed controller
Integral time constant 0.000 … 1.000s 0.05s Higher value gives slower, more
damped response.
P4-05 Motor power factor 0.50 … 0.99 Drive
rating
Motor nameplate power factor (cos Φ)
Required for all vector control modes
P4-06 Torque reference
select
0: Preset value
1: Bipolar analog input
2: 2nd analog input
3: Modbus ref (Optional)
0
Used when in vector control mode to
set a maximum torque limit.
Note that option 3 is not available in
the standard OD Plus.
P4-07 Maximum torque limit
/ Torque reference 0 … 200% 200% Preset torque ref when P4-01 = 1.
Max torque limit when P4-01 = 0.
P4-08 Minimum torque limit 0…150% 0 Defines the minimum limit for the
motor shaft torque
P4-09 V/F characteristic
adjustment frequency 0 … P1-09 0.0Hz Sets the frequency at which the
adjustment voltage (P4-10) is applied.
P4-10 V/F characteristic
adjustment voltage 0 … P1-07 0 Adjusts the motor voltage by this
value at frequency set in P4-09.

16
5.5 Digital input configuration – terminal mode (P1-12 = 0)
P2-01 Digi input 1 function Digi input 2 function Digi input 3 function Analog input function
0 O : Stop (Disable)
C : Run (Enable)
O : Bipolar analog input
C : Preset speed 1, 2
O : Preset speed 1
C : Preset speed 2 Bipolar analog input
1 O : Stop (Disable)
C : Run (Enable)
O : Preset speed 1
C : Preset speed 2
O : Preset speed 1, 2
C : Preset speed 3
O : Preset speed 1,2,3
C : Preset speed 4
Digi input 2 Digi input 3 Analog input Preset value
Open Open Open Preset speed 1
Closed Open Open Preset speed 2
Open Closed Open Preset speed 3
Closed Closed Open Preset speed 4
Open Open Closed Preset speed 5
Closed Open Closed Preset speed 6
Open Closed Closed Preset speed 7
2 O : Stop (Disable)
C : Run (Enable)
Closed Closed Closed Preset speed 8
3 O : Stop (Disable)
C : Run (Enable)
O : Forward
C : Reverse
O : Bipolar analog input
C : Preset speed 1 Bipolar analog input
4 O : Stop (Disable)
C : Run (Enable)
O : Forward
C : Reverse
2nd Analog Input
(eg varies torque limit) Bipolar analog input
Digi input 3 Analog input Preset value
Open Open Preset speed 1
Closed Open Preset speed 2
Open Closed Preset speed 3
5 O : Stop (Disable)
C : Run (Enable)
O : Forward
C : Reverse
Closed Closed Preset speed 4
6 2) O : Stop (Disable)
C : Run (Enable)
O : Forward
C : Reverse
External trip input :
O : Trip C : OK Bipolar analog input
7 O : Stop (Disable)
C : Run Forward
O : Stop (Disable)
C : Run Reverse
O : Bipolar analog input
C : Preset speed 1 Bipolar analog input
8 2) O : Stop (Disable)
C : Run Forward
O : Stop (Disable)
C : Run Reverse
O : Preset speed 1
C : Bipolar analog input Bipolar analog input
Digi input 3 Analog input Preset value
Open Open Preset speed 1
Closed Open Preset speed 2
Open Closed Preset speed 3
9 O : Stop (Disable)
C : Run Forward
O : Stop (Disable)
C : Run Reverse
Closed Closed Preset speed 4
10 2) O : Stop (Disable)
C : Run Forward
O : Stop (Disable)
C : Run Reverse
External trip input :
O : Trip C : OK Bipolar analog input
11 O : Stop (Disable)
C : Run (Enable)
O : Bipolar analog input
C : Preset speed 1
External trip input :
O : Trip C : OK Bipolar analog input
12 2) O : Stop (Disable)
C : Run (Enable)
O : Preset speed 1
C : Bipolar analog input
External trip input :
O : Trip C : OK Bipolar analog input
13 Normally open (NO)
Momentarily close to run
Normally closed (NC)
Momentarily open to stop
O : Bipolar analog input
C : Preset speed 1 Bipolar analog input
14
Normally open (NO)
Momentarily close to run
forward
Normally closed (NC)
Momentarily open to stop
Normally open (NO)
Momentarily close to run
reverse
Bipolar analog input
15 O : Stop (Disable)
C : Run (Enable)
O : Forward
C : Reverse
O : Decel ramp 1
C : Decel ramp 2 Bipolar analog input
16 O : Stop (Disable)
C : Run (Enable)
O : Forward
C : Reverse
O : Decel ramp 1
C : Decel ramp 2
O : Preset speed 1
C : Preset speed 2
17
Normally open (NO)
Momentarily close to run
forward
Normally closed (NC)
Momentarily open to stop
Normally open (NO)
Momentarily close to run
reverse
O : Preset speed 1
C : Keypad mode
Digi input 2 Digi input 3 Preset value
Open Open Preset speed 1
Closed Open Preset speed 2
Open Closed Preset speed 3
18 O : Stop (Disable)
C : Run (Enable)
Closed Closed Preset speed 4
O : Terminal mode
C : Keypad mode
19 O : Stop (Disable)
C : Run (Enable)
O : Bipolar analog input
C : 2nd analog input 2nd analog input Bipolar analog input
20 1) O : Stop (Disable)
C : Run (Enable)
2nd digital output :
Drive healthy = +24V
O : Bipolar analog input
C : Preset speed1 Bipolar analog input
21 1) O : Stop (Disable)
C : Run (Enable)
2nd digital output :
Drive healthy = +24V
O : Forward
C : Reverse Bipolar analog input
22 1) O : Stop (Disable)
C : Run (Enable)
2nd digital output :
Drive healthy = +24V
External trip input :
O : Trip C : OK Bipolar analog input
Notes :
1) When P2-01 = 20, 21 or 22, the 2nd digital input is configured as an output, which outputs +24V
when the drive is healthy, otherwise 0V
2) When connecting a motor thermistor, connect between terminals 1 & 4, set P2-01 = 6, 10, 11,
12 or 22 (Uses external trip input)
9
3.4 Control Terminal Connections
The User Control terminals are available via an 11-way pluggable connector. All
terminals are galvanically isolated, allowing direct connection to other equipment.
Do not connect mains supply voltages to any terminals other than the User
relay output. Permanent damage will otherwise result.
All other inputs will withstand up to 30V dc without damage.
The functionality of the inputs and outputs is user configurable. All operating modes are
set up via the parameter set.
Up to 100mA can be sourced from the User +24V output and up to 20mA from the
analog output.
The control terminals are defined as follows :
Terminal 1: +24V, 100mA user output.
Terminal 2: Digital input 1, positive logic. “Logic 1” when Vin > 8V DC
Terminal 3: Digital input 2, positive logic. “Logic 1” when Vin > 8V DC
2nd digital output : 0 / 24V, 10mA max
Terminal 4: 2nd analog input, 11-bit (0.05%). 0..10V, 0..20mA, 4..20mA.
Digital input 3, positive logic. “Logic 1” when Vin > 8V DC.
Terminal 5: +24V, 100mA reference output (for use with potentiometer).
Terminal 6: Bipolar analog input, +/-12-bit (0.025%).
Configurable for : 0..24V, 0..10V, -10V...10V, -24V…24V
Terminal 7: 0V (User GND). Connected to terminal 9
Terminal 8: Analog output, 8-bit (0.25%). 0..10V, 4..20mA.
Digital output : 0 / 24V, 20mA max
Terminal 9: 0V (User GND). Connected to terminal 7
Terminal 10: User relay output. Potential free contacts. 30Vdc 5A, 250Vac 6A
Terminal 11: User relay output. Potential free contacts. 30Vdc 5A, 250Vac 6A
Key control terminal information :
•Maximum input voltage on any terminal 30V dc
•All outputs short circuit proof
•Recommended potentiometer resistance : 10k Ohm
•Digital input response time < 8ms
•Bipolar analog input response time < 16ms. Resolution +/-12 bit (0.025%)
•Second analog input response time < 16ms. Resolution +11 bit (0.05%)
•Analog / Digital output response time < 16ms. Resolution 8 bit (0.25%)
2 3 4 5 6 7 8 9 10 111

8
3.3 Drive and motor connection
Earth
L3
L2
L1
U V W + BR
Each drive sta
r
connected to system
earth point
To
othe
r
drives
* If fitted, a filter should be mounted
physically close to the Drive. For maximum
effectiveness, the metal case of the filter
and the heat sink of the drive should be
electrically connected, ie screw both to a
metal back plate and ensure metal-to-metal
contact.
Motor terminal box connections
Most general purpose motors are
wound for operation on dual voltage
supplies. This is indicated on the
nameplate of the motor
This operational voltage is normally
selected when installing the motor
by selecting either STAR or DELTA
connection.
STAR always gives the higher of
the two voltage ratings.
Typical ratings are :
400 / 230 ( )
690 / 400 ( )
DELTA ( ) Connection
STAR ( ) Connection
U V W
U V W
Earth
L3
L2
Isolato
r
Contactor, MCB or Fuses
Optional Filter*
Screened
cable connects to
motor frame earth
L1
Optional
Braking
Resisto
r
U V W
Optidrive size 2
Help card
IR lens
Cable
management
tie-wrap
L1 L2 L3
U V W + BR
Each drive sta
r
connected to system
earth point
To
othe
r
drives
RS485 Interface
Use UL listed crimp
terminals for all power
terminal connections
RS485 Interface
RS485 + / Modbus
0V
+24V
RS485 - / Optibus
RS485 + / Optibus
RS485 - / Modbus
For Optibus and Modbus,
data format is fixed as:
1 start bit, 8 data bits,
1 stop bit, no parity.
1 6
17
5.6 Digital input configuration – keypad mode (P1-12 = 1 or 2)
The following table defines the function of the digital inputs when the drive is in keypad mode
P2-01 Digi input 1 function Digi input 2 function Digi input 3 function Analog input function
0 1) O : Stop (Disable)
C : Run (Enable)
Closed : Remote
pushbutton UP
Closed : Remote
pushbutton DOWN
When drive is stopped, closing
digital inputs 2 & 3 together
starts drive. Bipolar analog
input has no effect
1 O : Stop (Disable)
C : Run (Enable)
Closed : Remote
pushbutton UP
External trip input :
O : Trip C : OK
Closed : Remote pushbutton
DOWN
2 O : Stop (Disable)
C : Run (Enable)
Closed : Remote
pushbutton UP
O : Digital speed ref
C : Preset speed 1
Bipolar analog input > 5V
reverses rotation
1)
3…9,
13,14,
16
O : Stop (Disable)
C : Run (Enable)
Closed : Remote
pushbutton UP
Closed : Remote
pushbutton DOWN
When drive is stopped, closing
digital inputs 2 & 3 together
starts the drive.
Bipolar analog input > 5V
reverses rotation
10 O : Stop (Disable)
C : Run (Enable)
O : Digital speed ref
C : Bipolar analog input
External trip input :
O : Trip C : OK Analog speed reference
11 O : Stop (Disable)
C : Run (Enable)
O : Digital speed ref
C : Preset speed 1
External trip input :
O : Trip C : OK
12 O : Stop (Disable)
C : Run (Enable)
O : Preset speed 1
C : Digital speed ref
External trip input :
O : Trip C : OK
Allows connection of motor
thermistor on terminal 4.
Bipolar analog input > 5V
reverses rotation
15 O : Stop (Disable)
C : Run (Enable)
O : Digital speed ref
C : Preset speed 1
O : Decel ramp 1
C : Decel ramp 2
Bipolar analog input > 5V
reverses rotation
17 O : Stop (Disable)
C : Run (Enable)
O : Digital speed ref
C : Bipolar analog input
O : Digital / analog speed
C : Preset speed 1 Analog speed reference
Digi input 3 Analog input Preset value
Open Open Preset speed 1
Closed Open Preset speed 2
Open Closed Preset speed 3
18 O : Stop (Disable)
C : Run (Enable)
O : Digital speed ref
C : Preset speed
Closed Closed Preset speed 4
19 O : Stop (Disable)
C : Run (Enable)
O : Digital speed ref
C : 2nd analog input No effect
20, 21 O : Stop (Disable)
C : Run (Enable)
2nd digital output :
Drive healthy = +24V
O : Digital speed ref
C : Preset speed 1
22 O : Stop (Disable)
C : Run (Enable)
2nd digital output :
Drive healthy = +24V
External trip input :
O : Trip C : OK
Bipolar analog input > 5V
reverses rotation
Notes:
1) In addition to the speed being set using the pushbuttons on the front of the drive, these
settings for P2-01 allow the speed to be controlled remotely using remote pushbuttons
connected to digital inputs 2 and 3.
2) When P2-19 = 2 or 3 in keypad mode, the drive START and STOP is controlled from the
hardware enable input (terminal 2). In this case, the START / STOP buttons will have no
effect.
3) Reverse rotation control using the analog input only works in keypad mode. If P1-12=1, the
rotation control only works when P2-19 = 2 or 3. If P2-35 = 2 or 3, the function is disabled.
4) When connecting a motor thermistor, connect between terminals 1 & 4, set P2-01 = 6, 10, 11,
12 or 22 (Uses external trip input)
5.7 Digital input configuration – User PID mode (P1-12 = 3)
The following table defines the function of the digital inputs when the drive is in User PID control mode.
P2-01 Digi input 1 function Digi input 2 function Digi input 3 function Analog input function
0..10,
13..16,18
O : Stop (Disable)
C : Run (Enable) No effect No effect
11 O : Stop (Disable)
C : Run (Enable)
O : PID control
C : Preset speed 1
External trip input :
O : Trip C : OK
12 O : Stop (Disable)
C : Run (Enable)
O : Preset speed 1
C : PID control
External trip input :
O : Trip C : OK
17 O : Stop (Disable)
C : Run (Enable)
O : PID control
C : Bipolar analog input No effect
19 O : Stop (Disable)
C : Run (Enable)
O : PID control
C : 2nd analog input No effect
20, 21 O : Stop (Disable)
C : Run (Enable)
2nd digital output :
Drive healthy = +24V No effect
22 O : Stop (Disable)
C : Run (Enable)
2nd digital output :
Drive healthy = +24V
External trip input :
O : Trip C : OK
Digital input 1 must be
closed to run the drive
External trip function only
works when bipolar analog
input is selected as
feedback signal (P3-10=1).

18
5.8 Digital input configuration – Modbus control mode (Optional – P1-12 = 4)
The following table defines the digital input functionality when the drive is in Modbus control mode.
P2-01 Digi input 1 function Digi input 2 function Digi input 3 function Analog input function
0..2,4
6..9,
13..16,18
O : Stop (Disable)
C : Run (Enable) No effect No effect
3 O : Stop (Disable)
C : Run (Enable)
O : Forward
C : Reverse
O : Master speed ref
C : Preset speed 1
Digital input 1 must be closed
to enable the drive
Digi input 3 Analog input Preset value
Open Open Preset speed 1
Closed Open Preset speed 2
Open Closed Preset speed 3
5 O : Stop (Disable)
C : Run (Enable)
O : Master speed ref
C : Preset speed
Closed Closed Preset speed 4
10 O : Stop (Disable)
C : Run (Enable)
O : Master speed ref
C : Digital speed ref
External trip input :
O : trip C : OK
11 O : Stop (Disable)
C : Run (Enable)
O : Master speed ref
C : Preset speed 1
External trip input :
O : trip C : OK
12 O : Stop (Disable)
C : Run (Enable)
O : Preset speed 1
C : Master speed ref
External trip input :
O : trip C : OK
17 O : Stop (Disable)
C : Run (Enable)
O : Master speed ref
C : Bipolar analog input
O : Master / analog speed
C : Preset speed 1
19 O : Stop (Disable)
C : Run (Enable)
O : Master speed ref
C : 2nd analog input No effect
20,21 O : Stop (Disable)
C : Run (Enable)
2nd digital output :
Drive healthy = +24V
O : Master speed ref
C : Preset speed 1
22 O : Stop (Disable)
C : Run (Enable)
2nd digital output :
Drive healthy = +24V
External trip input :
O : trip C : OK
Digital input 1 must be closed
to enable the drive
Notes: If P2-19 = 2 or 3, drive can only be started / stopped by closing / opening digital input 1. If P2-19 = 0 or 2,
the master speed reference will be automatically reset to zero each time when drive is stopped.
5.9 Real-time monitoring parameters
Parameter group zero provides access to internal drive read-only parameters for monitoring purposes.
Par Description Display range Explanation
P0-01 Bipolar analog input value -100%...100% 100% = max input voltage
P0-02 2nd analog input value 0..100% 100% = max input voltage
P0-03 Speed controller reference -500%...500% 100% = Base frequency (P1-09)
P0-04 Digital speed ref (digi pot) - P1-01 … P1-01 Speed displayed in Hz / rpm
P0-05 Torque controller reference 0 ...200% 100% = motor rated torque
P0-06 User PID ref input 0..100% PID controller reference value
P0-07 User PID feedback 0..100% PID controller feedback value
P0-08 User PID error input 0..100% Reference – Feedback
P0-09 User PID P-term 0..100% Proportional component
P0-10 User PID I-term 0..100% Integral component
P0-11 User PID D-term 0..100% Differential component
P0-12 User PID output 0..100% Combined output
P0-13 Output Torque 0…200% 100% = motor rated torque
P0-14 Magnetising current A rms Magnetising current in A rms
P0-15 Rotor current A rms Rotor current in A rms
P0-16 Field strength 0..100% Magnetic field strength
P0-17 Stator resistance Ohm Phase – Phase stator resistance
P0-18 Stator inductance H Stator inductance in Henry
P0-19 Rotor resistance Ohm Calculated rotor resistance
P0-20 DC bus voltage V dc Internal DC bus voltage
P0-21 Drive temperature oC Internal drive temperature
P0-22 Supply voltage L1 – L2 V rms, ph-ph Phase – phase supply voltage
P0-23 Supply voltage L2 – L3 V rms, ph-ph Phase – phase supply voltage
P0-24 Supply voltage L3 – L1 V rms, ph-ph Phase – phase supply voltage
P0-25 Estimated Rotor speed Hz or rpm Applies to vector modes only
P0-26 kWh meter 0.0 … 999.9 kWh Cumulative energy consumption
P0-27 MWh meter 0.0 … 60 000 MWh Cumulative energy consumption
P0-28 Software ID, IO processor eg “1.00”, “493F” Version number and checksum
P0-29 Software ID, Motor control eg “1.00”, “7A5C” Version number and checksum
P0-30 Drive serial number 000000 … 999999
00-000 … 99-999
Unique drive serial number
eg 540102 / 24 / 003
7
3. Electrical Installation
3.1 Safety
Electric shock hazard! Disconnect and ISOLATE the Optidrive before attempting
any work on it. High voltages are present at the terminals and within the drive for up
to 10 minutes after disconnection of the electrical supply.
•Optidrives should be installed only by qualified electrical persons and in accordance with
local and national regulations and codes of practice.
•The Optidrive has an Ingress Protection rating of IP20. For higher IP ratings, use a
suitable enclosure.
•Where the electrical supply to the drive is through a plug and socket connector, do not
disconnect until 10 minutes have elapsed after turning off the supply
•Ensure correct earthing connections, see diagram below
•The earth cable must be sufficient to carry the maximum supply fault current which
normally will be limited by the fuses or MCB
3.2 Precautions
•Ensure that the supply voltage, frequency and number of phases (single or three phase)
correspond to the rating of the Optidrive as delivered
•An isolator or similar should be installed between the power supply and the drive
•Never connect the mains power supply to the Optidrive output terminals UVW
•Protect the drive by using slow-blow HRC fuses or an MCB located in the mains supply
to the drive
•Do not install any type of automatic switchgear between the drive and the motor
•Wherever control cabling is close to power cabling, maintain a minimum separation of
100 mm and arrange crossings at 90o
•Ensure that screening or armouring of power cables is effected in accordance with the
connections diagram below
•Ensure that all terminals are tightened to the appropriate torque (see table, left)
Connect drive according to the following diagram, ensuring that motor terminal box
connections are correct. There are two connections in general : Star and Delta. It is essential
to ensure that the motor is connected in accordance with the voltage at which it will be
operated. For more information, refer to the following diagram
For recommended cabling and wiring sizing, refer to section 7.4.
It is recommended that the power cabling should be 3-core or 4-core PVC-insulated
screened cable, laid in accordance with local industrial regulations and codes of practice.
The ground terminal of each Optidrive should be individually connected DIRECTLY to the
site earth (ground) bus-bar (through the filter if installed) as shown. Optidrive ground
connections should not loop from one drive to another, or to, or from any other equipment.
Ground loop impedance must conform to local industrial safety regulations. To meet UL
regulations, UL approved ring crimp terminals should be used for all earth wiring
connections.

6
2.3 Enclosure mounting and dimensions
For applications that require a higher IP rating than the IP20 offered by the standard drive,
the drive must be mounted in a metallic enclosure. The following guidelines should be
observed for these applications:
•Enclosures should be made from a thermally conductive material, unless forced
ventilation is used.
•When vented enclosures are used, there should be venting above the drive and
below the drive to ensure good air circulation. Air should be drawn in below the
drive and expelled above the drive.
•If the external environment contains contamination particles (eg dust), a suitable
particle filter should be fitted to the vents and forced ventilation implemented. The
filter must be serviced / cleaned appropriately.
•High moisture, salt or chemical content environments should use a suitably sealed
(non-vented) enclosure.
Non-Vented Metallic Enclosure Dimensions (mm)
Drive Power rating L W D G
Size 1 0.75kW 230V 300 250 200 50
Size 1 1.5kW 230V 400 300 250 75
Size 2 1.5kW 230V / 2.2kW 400V 400 300 300 60
Size 2 2.2kW 230V / 4kW 400V 600 450 300 100
Vented Metallic Enclosure Dimensions (mm)
Free-Vented unit Force-vented unit
Drive Power
rating L W D G L W D G Air Flow
Size 1 1.5 kW 400 300 150 75 300 200 150 75 > 15m3/h
Size 2 4 kW 600 400 250 100 400 300 250 100 > 45m3/h
Size 3 15 kW 800 600 300 150 600 400 250 150 > 80m3/h
Size 4 22 kW 1000 600 300 200 800 600 300 200 > 300m3/h
Size 4 37 kW - - - - 800 600 300 200 > 300m3/h
Size 5 90 kW - - - - 1600 800 400 200 > 900m3/h
Size 6 160 kW - - - - 2000 800 400 200 >1000m3/h
Enclosure Front View Enclosure Side View
W
L
D
G
G
19
6. Troubleshooting
6.1 Fault-finding chart
Symptom Cause and Solution
Overload or over-current trip
on unloaded motor during
acceleration
Check Star / Delta terminal connection in motor. Rated operating voltage of
drive and motor should match. The Delta connection always gives the lower
voltage rating of a dual voltage motor
Overload or over-current –
motor does not spin
Check for locked rotor. Check that the mechanical brake is released (if fitted)
Drive will not enable –
display remains on ‘StoP’
Check that the hardware enable signal is applied to digital input 1. Ensure that
the User +24V output voltage (between terminals 5 and 7) is correct. If not,
check wiring to user terminal strip. Check P1-12 for terminal / keypad mode. If
keypad mode selected, press the START button. Check that supply voltage is
within specification.
Drive runs incorrectly when
in vector mode
Ensure that the motor name plate data has been entered into P1-07, P1-08,
P1-09 before the parameter auto-tune function has been carried out. Set P4-02
= 1 to carry out auto-tune.
In very cold ambient
conditions, drive will not
power up
If the ambient temperature is less than -10 OC, the drive may not power up.
Ensure that a local heating source keeps the ambient above 0 OC in these
conditions.
Speed limit or rated
frequency parameters
cannot be set above 250Hz,
500Hz or 1000Hz
The maximum output motor frequency is limited by the switching frequency.
Ensure that P2-24 is at least 16x greater than the required motor output
frequency before setting the required maximum or rated output frequency
parameters.
Extended menus cannot be
accessed
Ensure that P1-14 is set to the extended access code. This is “101” unless the
code in P2-37 has been changed by the user.
6.2 Fault messages
Trip message Explanation
P-dEF Default parameters loaded, usually after pressing STOP, UP & DOWN keys for 1s. Press
STOP to reset the trip. Display then reads “StoP”
“O-I”
“h O-I”
Over-current on drive output to motor.
Trip on drive enable : check for wiring error or short circuit
Trip on motor starting : check for stalled or jammed motor
Trip during operation : check for sudden overload or malfunction
If “h O-I” occurs, check for short circuit on output. If wiring correct, contact your supplier.
“I.t-trP” Drive overload trip, occurring when the drive has been delivering >100% rated current (set in
P1-08) for a period of time. The display flashes to indicate an overload condition.
“O-Uolt” Over-voltage on DC bus. Check supply voltage is within limits. If trip occurs on deceleration,
increase deceleration time or fit braking resistor.
“U-Uolt” Under-voltage trip. Happens routinely when drive powered down. If it occurs whilst running,
check supply voltage
“OI-b” Over current in the brake resistor circuit. Check cabling to brake resistor
“OL-br” Brake resistor overload. Increase deceleration time, reduce load inertia or add further brake
resistors in parallel. Min resistance values from ratings tables in section 7.4 must be observed.
“O-t” Over-temperature trip. Check drive cooling and possible enclosure dimensions
“U-t” Under-temperature trip. Trip occurs if ambient is less than 0oC. Drive ambient temperature
must be raised above zero in order to start the drive.
“th-Flt” Thermistor hardware fault. Contact your local distributor for further information.
“PS-trP” Trip on drive enable : check for wiring error or short circuit
Trip during operation : check for sudden overload or over-temperature
“dAtA-F” Occurs routinely after Flash upgrade. Reset using the STOP button or after a power down
cycle. All parameters set to default after an upgrade.
“P-LOSS” Drive intended for use with a 3-phase supply has lost one phase. Condition must persist for
>15s before a trip occurs. Phase loss detection disabled if parameters defaulted (P-dEF)
when L3 has been removed.
“Ph-Ib” Phase imbalance. Trips if the phase imbalance exceeds 3%. Condition must persist for >30s
before a trip occurs.
“SC-trP” Check integrity of OptiLink (communication link) between drives interconnected optically.
Check that each drive in a network has a unique drive address (P2-27)
If Modbus function enabled, check Modbus communication link.
“E-triP” External trip (connected to digital input 3). Check motor thermistor (if connected)
“At-Fxx” Auto-tune failed to complete successfully. (xx = 01…07) See 6.3 for more details.
“SPIN-F” Spin start function failed to detect the motor speed. Check cable connection between drive
and motor. Make sure that the motor actual speed is less than the maximum speed limit
(P1-01). Make sure that the motor base frequency (P1-09) is less than 100Hz.

20
6.3 Auto-tune trouble shooting
Trip message Explanation and check point
At-F01 Measured motor stator resistance varies between phases. Ensure that all motor
phases are connected to the drive. Check motor for winding imbalance.
At-F02 Measured motor stator resistance is too large. Ensure that motor is connected.
Check that the motor power matches the drive power rating.
At-F03 Measured motor inductance is too low. Ensure that there is no short circuit on the
motor or a winding fault. Check that the motor power matches drive power rating.
At-F04 Measured motor inductance is too high. Check for motor connection fault. Check
that the motor power matches drive power rating.
At-F05…At-F07 Motor parameter measurements not convergent. Check motor windings for fault.
Check that the motor power matches drive power rating.
Notes: Ensure that the correct motor nameplate parameters are entered in P1-07…P1-09 before
the Auto-tune is carried out. Ensure that the motor winding (star or delta) connection is
correct and that the motor is connected to the drive.
7. Technical data
7.1 User interface
Bipolar Analog Input : Resolution = +/-12-bits (0.025%), 8ms sampling time
(terminal 6) Range settings: 0..10V, 0..24V, -10..10V. Max input voltage 30V DC
Input impedance: 22 kOhm
2nd Analog input : Resolution = +11-bits (0.05%), 8ms sampling time
(terminal 4) Range settings: 0..10V, 4..20mA, 0..20mA. Max input voltage 30V DC
Input impedance: 70 kOhm
Digital inputs : Positive logic only. Sampling interval : 8ms sampling time
(terminals 2, 3, 4) “Logic 1” input voltage range: 8V … 30V DC.
“Logic 0” input voltage range: 0 … 4V DC.
User +24V output : Output load regulation +/-0.4% over full load range.
(terminals 1, 5) Max output current = 100mA total. Short circuit proof.
Analog output : Resolution = 8-bits, 16ms update cycle time
(terminal 8) Output formats: 0…10V, 4…20mA. Max current = 20mA.
Short circuit proof.
2nd digital output : PNP output, max output current = 10mA.
(terminal 3) Short circuit proof.
User relay : Contact rating : 250Vac, 6A / 30Vdc, 5A.
(terminals 10, 11)
7.2 Power stage protection
- Output short-circuit, phase-to-phase, phase-to-earth.
- Output over-current. Trip set at 200% of RMS rated drive current.
- Overload protection. Drive delivers 150% of rated motor current for 60s.
- Braking transistor protected against short-circuit.
- Braking resistor overload. (when enabled)
- Over-voltage trip. Set at 123% of drive maximum rated supply voltage.
- Under-voltage trip.
- Over temperature trip.
- Under temperature trip. (Drive will trip if enabled below 0 OC)
- Supply Phase imbalance. A supply imbalance of > 3% persisting for more than 30s
will trip a running drive.
- Supply Phase loss. If one phase of a 3-phase supply is lost for more than 15s, a
running drive will trip.
7.3 Environmental
Operational temperature range : 0 … 50 OC
Storage temperature range : -40 … 60 OC
Maximum altitude : 2 000m. Derate above 1000m : 1% / 100m
Maximum humidity : 95%, non-condensing
5
2. Mechanical Installation
2.1 General
•Carefully inspect the Optidrive before installation to ensure it is undamaged
•Store the Optidrive in its box until required. Storage should be clean and dry and
within the temperature range –40oC to +60oC
•Install the Optidrive on a flat, vertical, flame-resistant, vibration-free mounting within a
suitable enclosure, according to EN60529 if specific Ingress Protection ratings are
required
•The Optidrive must be installed in a pollution degree 1 or 2 environment
•Flammable material should not be placed close to the drive
•The entry of conductive or flammable foreign bodies should be prevented
•Max. operational ambient temperature 50oC, min. 0oC. Refer to rating tables in
section 7.4
•Relative humidity must be less than 95% (non-condensing)
•Optidrives can be installed side-by-side with their heatsink flanges touching. This
gives adequate ventilation space between them. If the Optidrive is to be installed
above another drive or any other heat-producing device, the minimum vertical
spacing is 150mm. The enclosure should either be force-ventilated or large enough
to allow natural cooling (refer to tables in section 2.3 for further information).
2.2 Mechanical dimensions and mounting
Size 1 Size 2 Size 3 Size 4 Size 5
(#1) *
Size 5
(#2) * Size 6
Length / mm 155 260 260 520 1045 1100 1100
Width / mm 80 100 171 340 340 340 340
Depth / mm 130 175 175 220 220 330 330
Weight/ kg 1.1 2.6 5.3 28 67 68 55 **
A / mm 105 210 210 420 945 945 945
B / mm 72 92 163 320 320 320 320
J / mm 4 9.5
K / mm 25 50
Fixings 2 * M4 4 * M4 4 * M8
Power Terminal
torque settings 1 Nm 4 Nm 8 Nm
L
WD
A
J
B
K
* Size 5 (#1) – 90A and 110A ratings
* Size 5 (#2) – 150A and 180A ratings
** S6 has external line choke, weight 27kg
Table of contents
Popular Controllers manuals by other brands
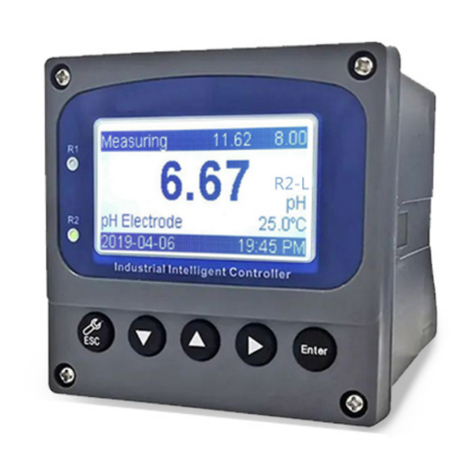
EYC
EYC DPME01 Operation manual
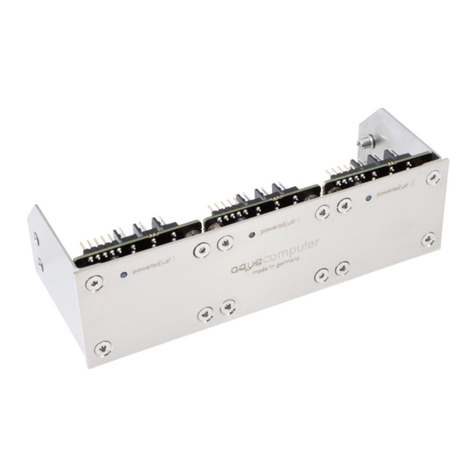
Aqua Computer
Aqua Computer poweradjust 3 User and installation manual
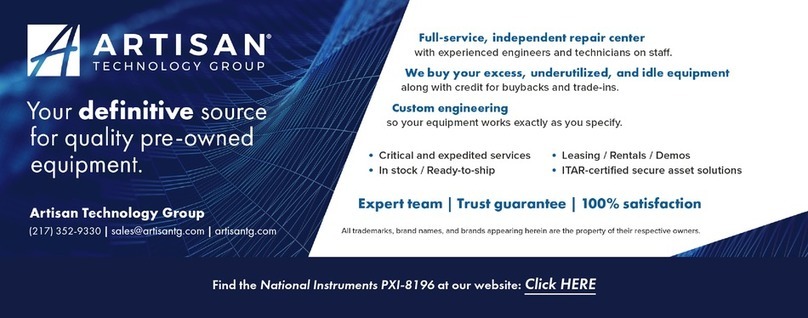
National Instruments
National Instruments PXI-8195 installation guide
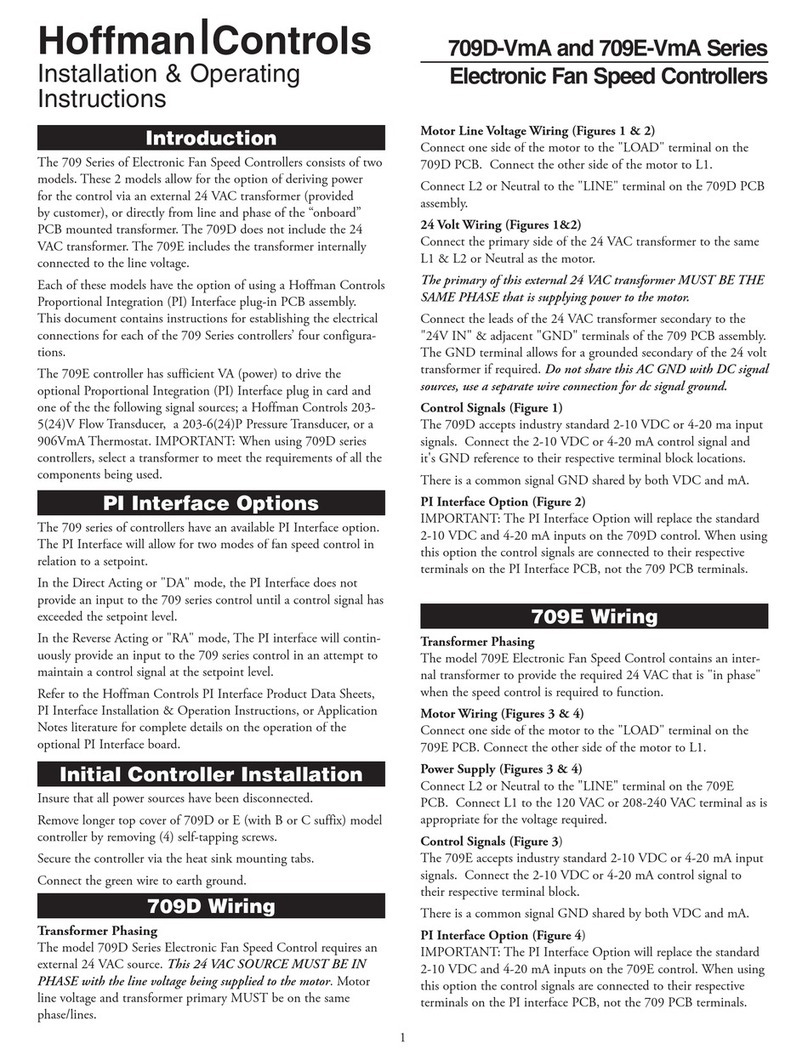
Hoffman
Hoffman 709D-VmA Series Installation and operating instructions

Fisher
Fisher EMERSON VSX4 Series instruction manual
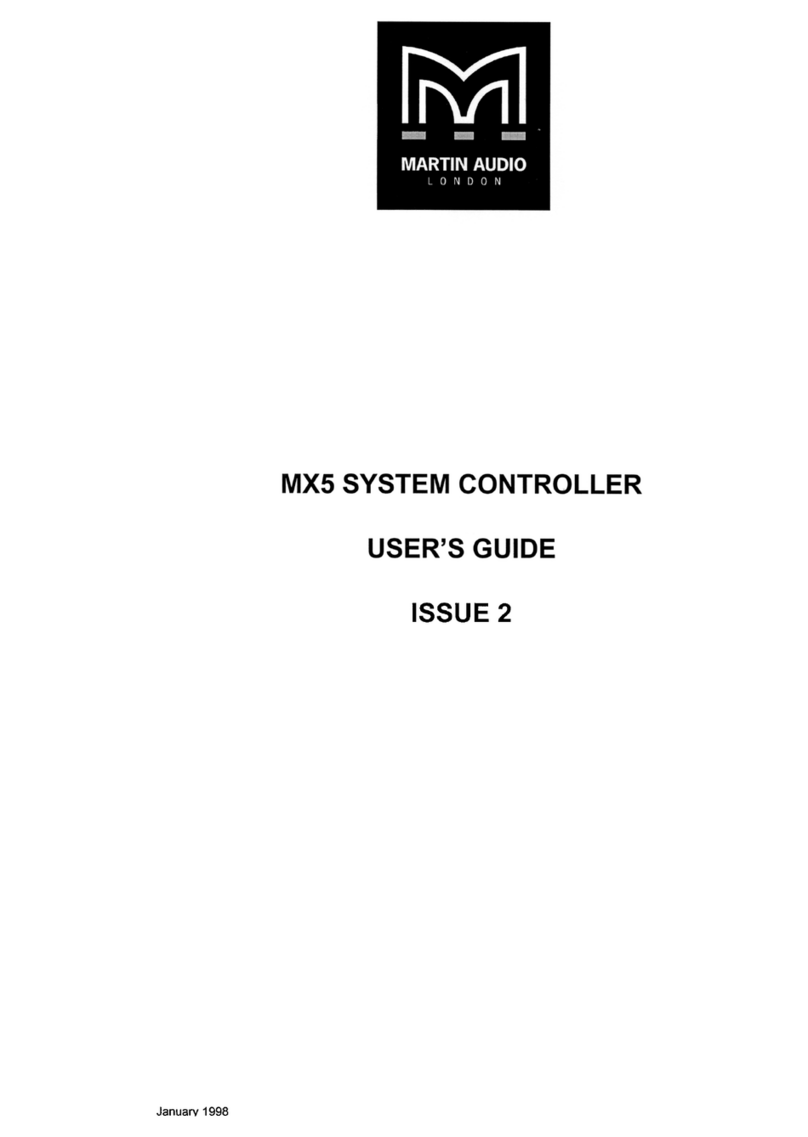
Martin Audio
Martin Audio MX5 - V2 manual
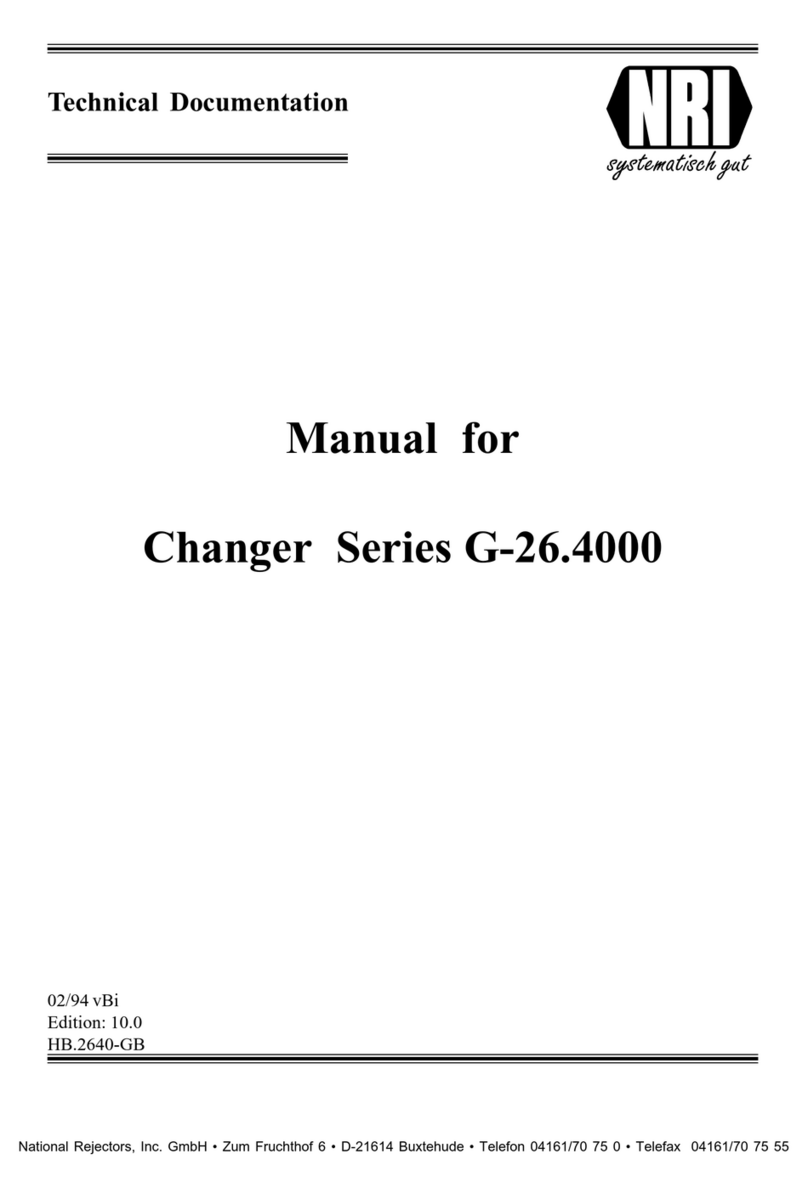
NRI
NRI G-26.4000 Series manual
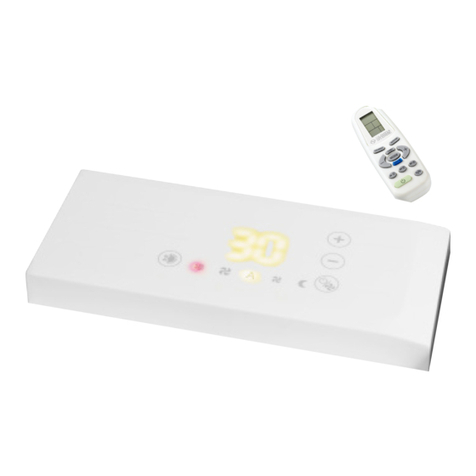
Olimpia splendid
Olimpia splendid Bi2 B0828 Instructions for mounting and use

United Electric Controls
United Electric Controls 120 Series Installation and maintenance instructions
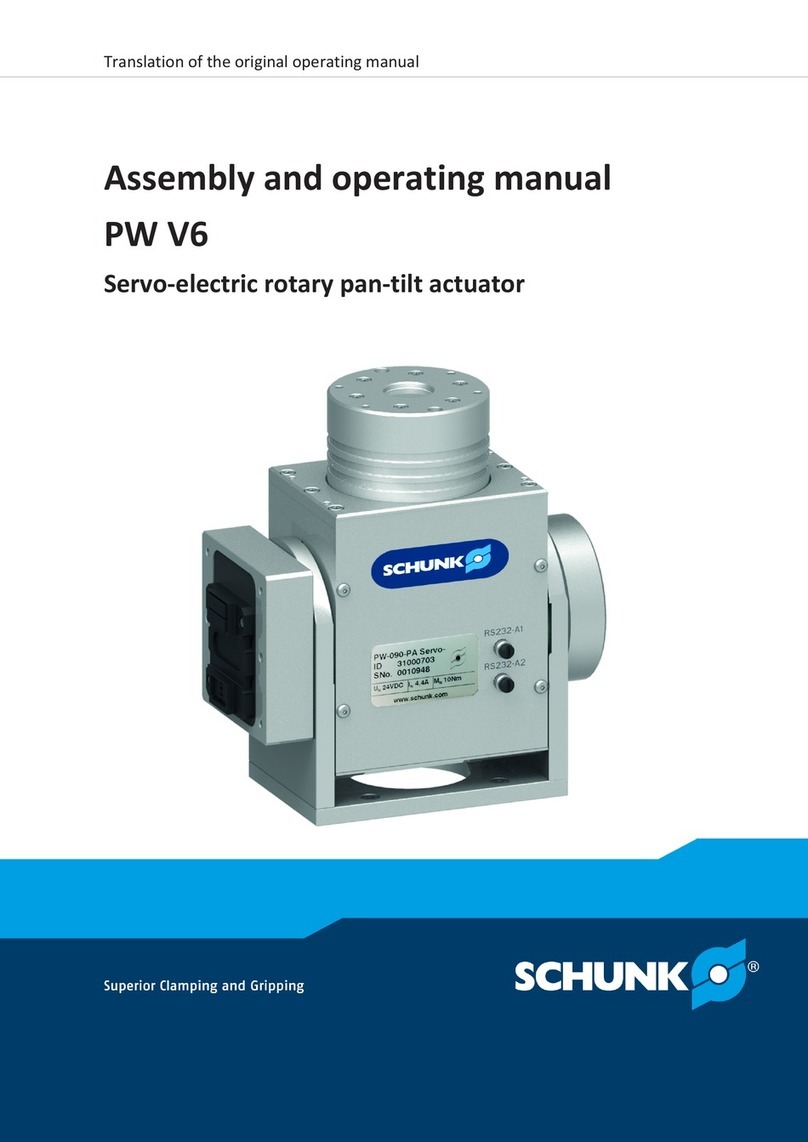
SCHUNK
SCHUNK PW V6 Assembly and operating manual
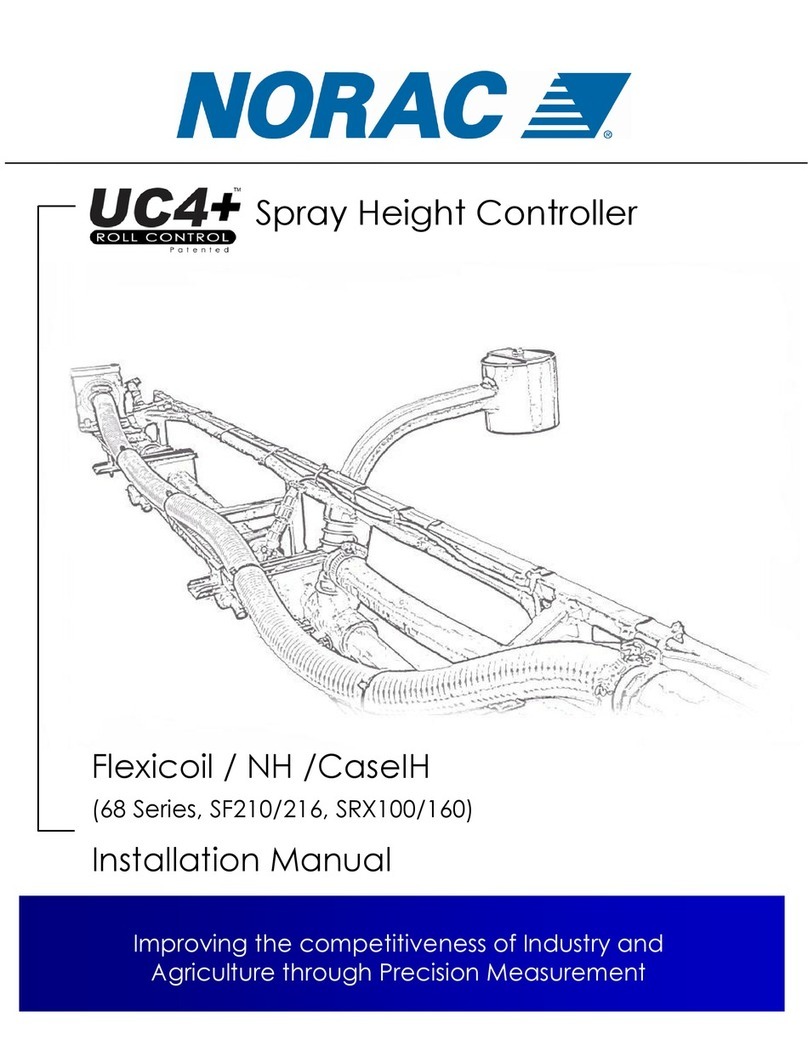
Norac
Norac UC4+ installation manual
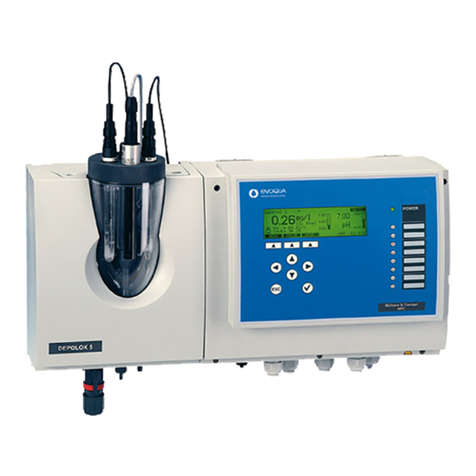
Evoqua
Evoqua WALLACE & TIERNAN MFC instruction manual