Barrier Systems X-TENSION XTGTSS1 Manual

INSTALLATION AND MAINTENANCE MANUAL
X-TENSION®
NCHRP 350 TL-3 Tangent / Flared End Terminal and Median Attenuator

Lindsay Transportation Solutions Sales and Services, Inc (888) 800-3691 [U.S. toll free] or +1 (707) 374-6800 Lindsay Transportation Solutions Sales and Services, Inc (888) 800-3691 [U.S. toll free] or +1 (707) 374-6800
2
INSTALLATION AND MAINTENANCE MANUAL
Table of Contents
Introduction ………………………………… 3
System Overview …………………………. 3
Before Installation ………………………… 3
Limitations and Warnings ………………… 4
Safety Statements ………………………… 4
Parts Identication ………………………… 5
Preparation ………………………………… 7
Soil Conditions …………………………….. 7
Tools Required …………………………….. 7
Before Starting …………………………….. 7
X-Tension Tangent Installation ………….. 8
X-Tension Flared Installation …………….. 16
X-Tension Median Installation ……………. 18
Optional Nose Cover ………………………. 23
Installation Checklist ……………………….. 24
MAINTENANCE
Trafc Face Impacts ……………………….. 25
Head on Impacts …………………………… 26
APPENDIX - Drawings
XTGTSS1 Roadside / Imperial Wood Blockout - Wood Post …………….. 27
XTGTSS2 Roadside / Imperial Wood Blockout - Steel Post …….............. 28
XTGTSS3 Roadside / Imperial Composite Blockout - Steel Post ............. 29
XTMTSS2 Median / Imperial Wood Blockout - Steel Post ……………… 30
XTMTSS3 Median / Imperial Composite Blockout - Steel Post ............. 31
XTGTSM1 Roadside / Metric Wood Blockout - Wood Post ……............. 32
XTGTSM2 Roadside / Metric Wood Blockout - Steel Post ……………… 33
XTGTSM3 Roadside / Metric Composite Blockout - Steel Post .............. 34
XTMTSM2 Median / Metric Wood Blockout - Steel Post ……………… 35
XTMTSM3 Median / Metric Composite Blockout - Steel Post .............. 36

Lindsay Transportation Solutions Sales and Services, Inc (888) 800-3691 [U.S. toll free] or +1 (707) 374-6800 3
X-TENSION®SYSTEM
X-Tension Introduction
Introduction
The X-Tension Guardrail End Terminal has been designed and tested to meet the evaluation
criteria of NCHRP 350 Test Level 3.
The system has been tested to the guidelines in NCHRP 350 for a non-gating, re-directive guard-
rail end treatment. When correctly installed and maintained, the system is capable of stopping,
containing, or re-directing an errant vehicle in a safe manner under NCHRP 350 impact condi-
tions.
The X-Tension Guardrail End Terminal is the world’s rst fully re-directive, non-gating guardrail
terminal end. The unique X-Tension technology is a tension based solution rather than compres-
sion based. It offers exceptional vehicle control and energy absorbing capabilities in head on
impacts, where the energy is absorbed with resistance at the impact head rather than being trans-
ferred down the rail as occurs with other systems. Even head on, high angle (15o during testing)
impacts on the nose resulted in the vehicle being redirected and controlled.
System Overview
The X-Tension Guardrail End Terminal is designed and constructed to provide acceptable struc-
tural adequacy, minimal occupant risk and safe trajectory as set forth in NCHRP 350 for guard-
rail terminal ends.
When impacted head on with an 820 – 2000kg (1800 – 4400lb) vehicle at speeds of up to 100kph
(62 mph), the impacting vehicle is brought to a controlled stop or allowed to penetrate to the back
side, depending on the impact conditions.
Before Installation
Placement and use of the X-Tension Guardrail End Terminal should be done in accordance with
the guidelines and recommendations set forth in the “AASHTO Roadside Design Guide”, FHWA
memoranda and other state and local standards.
Depending on the application and circumstances at the site, installation and assembly of a Test
Level 3 system should take a two person crew less than two hours.
The X-Tension Guardrail End Terminal is a highly engineered safety device made up of a rela-
tively small number of parts. Before starting installation ensure that one is familiar with the make
up of the system.

Lindsay Transportation Solutions Sales and Services, Inc (888) 800-3691 [U.S. toll free] or +1 (707) 374-6800 Lindsay Transportation Solutions Sales and Services, Inc (888) 800-3691 [U.S. toll free] or +1 (707) 374-6800
4
INSTALLATION AND MAINTENANCE MANUAL
X-Tension Introduction (continued)
Limitations and Warnings
The X-Tension Guardrail End Terminal has been rigorously tested and evaluated per the recom-
mendations in the NCHRP 350 guidelines for terminals and crash cushions. The impact condi-
tions recommended in NCHRP 350 are intended to address typical in–service collisions.
When properly installed and maintained, the system is capable of containing and re-directing im-
pacting vehicles in a predictable and safe manner under the NCHRP 350 impact conditions.
Vehicle impacts that vary from the NCHRP 350 impact conditions described for guardrail end ter-
minals may result in signicantly different results than those experienced in testing. Vehicle impact
characteristics different than or in excess of those encountered in NCHRP 350 testing may result
in system performance that may not meet the NCHRP 350 evaluation criteria.
Safety Statements
General Safety
All required trafc safety precautions should be complied with. All workers should wear required
safety clothing (high visibility vests, steel capped footwear, gloves, hard hats, safety glasses etc.)
All underground services must be located before installation of any posts.
Only Authorized trained personnel should operate any machinery. Where overhead machinery is
used, care must be taken to avoid any overhead hazards.
Gloves should be worn at all times. Particular care should be taken to avoid galvanizing spikes.
X-Tension Safety Statements
All installers must be well clear of post driving machinery when in use.
Avoid placing hands or ngers in and around moving parts when components are being lifted and
manoeuvred into place. (i.e. around splice holes, etc.) permeable
The cables should be tted by one person only. Other workers should stand clear to avoid being
caught in moving cables.
Securely fasten the impact head and rail before turning the friction plate.
The friction plate should be turned manually with a crow bar and extension handle. Do not attempt
to turn it with the assistance of machinery. Ensure crow bar is securely held while the 4 locking
bolts are tightened.

Lindsay Transportation Solutions Sales and Services, Inc (888) 800-3691 [U.S. toll free] or +1 (707) 374-6800 5
X-TENSION®SYSTEM
X-Tension Parts Identication
Impact Head Friction Plate Soil Anchor
(1 Required) 1 Required) (1 Required)
B061072 B061058 B061104
Slider Bracket + Angle Bar Cable Bracket Cable Assembly
(1 Required Roadside – 2 Median) (1 Required) (2 Required)
B061079 B061083 B061109
Slider Panel Post 1 - Top Ground Strut
(1 Required Roadside – 2 Median) (1 Required) (1 Required)
B061088 B061099 B061094

Lindsay Transportation Solutions Sales and Services, Inc (888) 800-3691 [U.S. toll free] or +1 (707) 374-6800 Lindsay Transportation Solutions Sales and Services, Inc (888) 800-3691 [U.S. toll free] or +1 (707) 374-6800
6
INSTALLATION AND MAINTENANCE MANUAL
X-Tension Parts Identication (Continued)
Post # 2 (1 Req.) Standard Steel Line Post (3-6) Post #1 Bottom
Roadside can be CRT Timber (CRT Timber Posts allowed roadside) (1 Required)
B061100 4002338 B061098
Standard Highway Rail 12’-6” Median Radius Rail 1 (12’-6”) Median Secondary Head
(3 Required Roadside – 5 Median) (1 Required – Shop Curved) (1 Required)
4002018 B070233 B070219
Shear Bolts Blockout (Plastic or Timber) Hardware Set
(8 Required Roadside - 16 Median) (5 Required Roadside – 10 Median) (Roadside)
K080123 4001339 K070202 & K070204

Lindsay Transportation Solutions Sales and Services, Inc (888) 800-3691 [U.S. toll free] or +1 (707) 374-6800 7
X-TENSION®SYSTEM
X-Tension – Preparation for all Applications
Preparation
Before installing an X -Tension, ensure that all materials required for an 11.4 m (38 ft) system
are on site and have been identied. See bill of materials for the particular application and parts
identication sheet.
Ensure that the area where the X-Tension is to be installed is at enough so that the soil anchor
will not protrude more than 100mm (4 in) from ground level, when measured with a straight line
over a 1.5m (5 ft) cord. Minor site grading may be required.
Soil Conditions
The X-Tension has been designed to be installed in median or edge of road locations and in soil
that meets or exceeds the AASHTO “standard soil” specication. If rock or saturated soil is en-
countered during post installation, refer to appropriate State specications. Guidelines will vary
from State to State.
Tools Required
The same tools required to install standard highway guardrail will also install an X-Tension. Spe-
cically: Sockets (commonly used in Guardrail), Drill, Wrenches, Large Crow Bar, String line,
Level, Augers, Tampers and Post Pounders commonly used in driving posts.
Before Starting
For all applications, begin the installation from the downstream end of the terminal at the point
where it joins the standard guardrail (post 7).
For the tangent and ared applications, the X-Tension connects directly to standard steel post or
timber post strong post W – beam highway guardrail, SGR04a-b.
The median application X-Tension connects directly to standard steel post or timber post
strong post W-beam median barrier SGM04a-b
Follow step by step instructions for the appropriate application.
Important Note about posts and blockouts:
Tangent & Flared Systems:
Post 1 steel – Post 2 either CRT timber or crimped steel
Post 3-6 either CRT timber or standard steel I beam posts
Median system:
Posts 1 & 2 are always crimped steel.
Posts 3 – 6 are standard steel I beam posts
Blockouts may be either composite or timber.

Lindsay Transportation Solutions Sales and Services, Inc (888) 800-3691 [U.S. toll free] or +1 (707) 374-6800 Lindsay Transportation Solutions Sales and Services, Inc (888) 800-3691 [U.S. toll free] or +1 (707) 374-6800
8
INSTALLATION AND MAINTENANCE MANUAL
X-Tension - Tangent Installation Instructions
At
Post 7
At
Post 5
At
Post 3
At
Post 1
Step 1 - Set Out
The tangent terminal is essentially an 11.4m (38 ft) continuation of the standard guardrail run.
Pull a string line out with the desired offset (0 -450mm : 0-1.5 ft) over the length of the system, in
a straight are (Figure 1). The system should not be installed on parabolic curve. The string
line should be set to follow the roadside edge of the posts.
All the posts except post #1 have a blockout so take care to place the roadside face of
post #1 200mm (8 in) towards the roadway to compensate for the lack of blockout.

Lindsay Transportation Solutions Sales and Services, Inc (888) 800-3691 [U.S. toll free] or +1 (707) 374-6800 9
X-Tension - Tangent Installation Instructions
Step 2 – Installing Posts 6- 2
Install posts 6 to 2 at standard highway rail
spacing (1905mm: 6 ft 3 in), to the correct
height. All posts should be the same height
from ground level throughout the entire sys-
tem.
Posts #6 to #3 are either standard “I” beam
posts OR timber CRT posts. Post 2 is either
the Special “I” beam post or a timber CRT (see
parts identication photo).
Posts may be directly driven, or in stiff soils
a 150mm (6 in) diameter hole drilled, and the
post then driven into the hole. The post may
also be placed in an oversized augured hole
but care must be taken to ensure the backll is
properly compacted.
Hint: Offset Post 3 back from the string line
40-50mm (up to 2 in) to make it easier to push
rail 1 and Slider Panel over rail 2.
When driving steel posts, ensure that a driving
cap with timber or plastic insert is used to pre-
vent damage to the galvanizing on the top of
the posts.
Ensure that Post 2 has the post bolt holes on
the side nearest the rail (notches go to the back-
side as shown and are only used on the median
application (Figure 2).
Bolt the blockout to the post at post 3,
prior to attaching to the rail (Figure 3).
Figure 1. Pull a string line with the desired offset.
Figure 2. Notches go to the backside.
Figure 3. Bolt the blockout prior to attaching the rail.
X-TENSION®SYSTEM

Lindsay Transportation Solutions Sales and Services, Inc (888) 800-3691 [U.S. toll free] or +1 (707) 374-6800 Lindsay Transportation Solutions Sales and Services, Inc (888) 800-3691 [U.S. toll free] or +1 (707) 374-6800
10
X-Tension - Tangent Installation Instructions
Step 3 – Post 1, Ground Strut and Soil Anchor
Place the roadside face of post 1 bottom anchor, 200mm (8 in) towards the roadway to
compensate for the lack of blockout (Figure 4). Post 1 bottom, the Ground Strut and the Soil
Anchor are then placed parallel to the string line at this roadside offset position.
Drive or place the bottom of post 1 in the augured hole so that no more than 75mm (3 in) [100mm
(4 in max)] protrudes above ground level (Figure 5). Use the Ground Strut as a template to place
the Soil Anchor in the correct place. The SoilAnchor can then be driven into place or placed in an
augured hole and backlled. The Ground Strut should be level or lower at the anchor end than at
the post 1 bottom end.
Place post 1 top in the post 1 bottom anchor ensuring that the post bolt notches are at the top
and facing the Soil Anchor (Figure 6). Use M16 x 200mm (5/8 in x 8 in) hex head bolt with nut and
washers. Do not over tighten bolt.
Figure 4. Measure 8 in. towards roadway. Figure 5. Drive post 1 into augured hole. Figure 6. Post 1 top in post bottom.
Step 4 – Hang Rail 3 and Cable Anchor Bracket
Rail 3 is installed like standard
guardrail with post 6 at the center
of the rail and blockouts between
the rail and post. Place the Cable
Anchor Bracket on the back of the
rail at the joint between rail 3 and
rail 4 (post
7).
The two “boxes” on the cable
bracket should be on the impact
head side of the splice joint. At-
tach rails to post with post bolt and
splice rail 3 to rail 4 with 8 standard
splice bolts (Figure 7).
Figure 7. Splice rail 3 to rail 4 with 8 standard splice bolts.
INSTALLATION AND MAINTENANCE MANUAL

Lindsay Transportation Solutions Sales and Services, Inc (888) 800-3691 [U.S. toll free] or +1 (707) 374-6800 11
X-Tension - Tangent Installation Instructions
Figure 10. Bolt Slider Bracket to end of rail 2 at post 3. Figure 11. Remove angle bar bolts.
Step 5 – Hang Rail 2 and Shear Bolts
Before installing rail 2, double check that the blockout is already bolted to post 3.
Bolt rail 2 to the post and blockouts at posts 4 and 5 with the appropriate post bolt (Figure 8).
DO NOT BOLT THE RAIL TO POST 3.
Splice rail 2 to rail 3 with the 8 special shear bolts (yellow) supplied (Figure 9). Put the
washer and nut on inside of rail.
IMPORTANT NOTE: DO NOT USE STANDARD SPLICE BOLTS AT POST 5 SPLICE. DO
NOT USE AN AIR-IMPACT WRENCH TO TIGHTEN SHEAR BOLTS. SHEAR BOLTS WILL
BREAK IF OVER-TIGHTEND.
Figure 8. Bolt rail 2 to post and blockouts. Figure 9. Splice rail 2 to rail 3 with 8 special shear bolts.
Step 6 – Attach Slider Bracket to Rail 2
Bolt the Slider Bracket to the end of rail 2 at post 3 (Figure 10). Use 4 standard splice bolts. The
angle bar end should be closest to the Impact Head end. Remove the angle bar and 2 x M20 x
25mm (3/4 in x 1 in) bolts (Figure 11).
X-TENSION®SYSTEM

Lindsay Transportation Solutions Sales and Services, Inc (888) 800-3691 [U.S. toll free] or +1 (707) 374-6800 Lindsay Transportation Solutions Sales and Services, Inc (888) 800-3691 [U.S. toll free] or +1 (707) 374-6800
12
X-Tension - Tangent Installation Instructions
Step 7 – Assemble Slider Panel onto Rail 1
Start by sitting rail 1 on a blockout or post so that it is raised off the ground as shown (Figure 12).
Slide the Slider Panel onto the downstream end of rail at post 3 location (Figure 13) and bolt into
place using 4 standard splice bolts, pushing the bolt through from the inside of the slider to the
outside so that the nut is on the trafc face.
The curved and reinforced (post breaker) end of Slider Panel sits at the rail end.
Use guardrail pin bar or crow bar to assist with lining up splice holes.
Figure 12. Sit rail 1 so it is raised off the ground.
Step 8 – Hang Rail 1 Figure 13. Slide the Slider Panel onto downstream end.
Lift rail 1 with Slider Panel attached and push the slider end over rail 2 (Figure 14). Overlap the
rails as per a standard splice joint overlap.
Bolt rail 1 and blockout to post 2 using a standard post bolt that is supplied (Figure 15).
Re-attach the angle bar to the slider bracket on the backside of the rail (Figure 16).
Figure 14. Push Slider Panel over rail 2. Figure 15. Bolt rail 1 and blockout to post 2. Figure 16. Reattach the angle bar.
INSTALLATION AND MAINTENANCE MANUAL

Lindsay Transportation Solutions Sales and Services, Inc (888) 800-3691 [U.S. toll free] or +1 (707) 374-6800 13
Figure 17. Attach Impact Head to rail 1. Figure 18. Bolt head and rail 1 to post 1 with washer.
Step 9 – Attach Impact Head
Place Impact Head on upstream end of rail 1 and attach using 8 standard splice bolts with nuts on
trafc face (Figure 17). Hint: Place bottom two bolts rst then use guardrail pin bar to lever head
up snug onto rail.
Bolt head and rail 1 to post 1 using the supplied M16 x 50mm (5/8 in x 2 in) guardrail post bolt.
Use a 50mm x 50mm (2 in x 2 in) washer under the nut on the inside of post 1 (Figure 18).
Step 10 – Place the Cables
Push the cables under the steel strap on the Ground Strut (Figure 19) and forward through the
holes at the top of the anchor. Lay the cables out parallel to the guardrail, downstream from the
anchor.
Ensure that bottom cable (closest to road) has half the thread protruding through the anchor, as
shown. Ensure the top cable has the nut wound on a least two turns past the end of the thread
(Figure 20).
Figure 19. Push cables under steel strap on Ground Strut. Figure 20. Thread the nuts as shown.
X-TENSION®SYSTEM

Lindsay Transportation Solutions Sales and Services, Inc (888) 800-3691 [U.S. toll free] or +1 (707) 374-6800 Lindsay Transportation Solutions Sales and Services, Inc (888) 800-3691 [U.S. toll free] or +1 (707) 374-6800
14
INSTALLATION AND MAINTENANCE MANUAL
Figure 23. Use crow bar to turn Friction Plate. Figure 24. Use socket to lock bar in the turned position.
Page 14
Step 11 – Installing the Cables
Install the
Friction Plate in the top of the Impact Head, adjustment hole up. Take the cable closest to the
road, pick up the downstream cable tting and walk to the head, passing the cable through the
bottom hole, through the Friction Plate (Figure 21) and out the backside of the Impact Head.
Now thread
the cable down the backside of the rail following the bottom trough of the W-beam and attach to
the bottom “box” on the Cable Bracket at post 7. Repeat this process with the other cable but
push it through the top hole and thread it along the top trough of the W-beam.
Place the nuts and washer on the cables at the Cable Bracket end but only run them a few turns (Figure
22).
Do not tighten cables at this stage (or the Friction Plate will not turn)
Figure 21. Pass the cable through the bottom hole. Figure 22. Do not tighten nuts at this time.
Step 12 – Turning the Friction Plate
Put a crow bar through the hole at the top of the friction plate (Figure 23) and turn it to the nal
position. Using a socket, tighten the 4 - M20 x 75mm (3/4 in x 3 in) bolts on the side of the impact
head to lock the bar in the turned position (Figure 24).

Lindsay Transportation Solutions Sales and Services, Inc (888) 800-3691 [U.S. toll free] or +1 (707) 374-6800 15
X-TENSION®SYSTEM
Step 13 – Tightening the Cables
Only tighten the cables using the nuts at the Cable Bracket end (post 7) (Figure 25). Do not
tighten the cable nuts at front of the Ground Anchor.
Tighten the cables until they are taut, i.e. they rest in the backside of the W-beam and do not
visibly sag between posts (Figure 26). There is no torque requirement for the cables.
Figure 25. Tighten cables at Cable Bracket end (post 7). Figure 26. Tighten cables until they are taut.
Step 14 – Attach Nosing
Push nosing into place on the front of the impact head. Attach using the supplied nylon push riv-
ets (Figure 27).
Delineation to be attached to nosing, as per the Local Authorities requirements.
Figure 27. Attach nose using nylon push rivets.

Lindsay Transportation Solutions Sales and Services, Inc (888) 800-3691 [U.S. toll free] or +1 (707) 374-6800 Lindsay Transportation Solutions Sales and Services, Inc (888) 800-3691 [U.S. toll free] or +1 (707) 374-6800
16
X-Tension - Flared Installation Instructions
0 - 1.2 m (0 - 4 ft)
This section deals with installation of a Flared X-Tension system in a roadside guardrail terminal
end application.
Apart from the initial set out, the ared X-Tension and installation procedure is identical to the
Tangent system, the only difference being the amount of offset used.
Site preparation
The Flared terminal may be installed either parallel to the edge of the roadway (tangent) or with
the impact head end of the rail offset by up to 1.2m (4 ft) away from the road (Figure 28) in a
straight are, over the length of the system. The system should not be installed on parabolic
curve.
Ensure that the area where the X-Tension is to be installed is at enough so that the anchor will
not protrude more than 75 mm (3 in) [100 mm (4 in) max] above ground level, when measured
with a straight line over a 1.5m (5 ft) cord. Minor site grading may be required.
Figure 28. Maximum offset is 1.2 m (4 ft).
INSTALLATION AND MAINTENANCE MANUAL

Lindsay Transportation Solutions Sales and Services, Inc (888) 800-3691 [U.S. toll free] or +1 (707) 374-6800 17
X-Tension - Flared Installation Instructions
Figure 30. Place roadside face of post 1 towards roadway.
0 - 1.2 m (0 - 4 ft)
Figure 29. Pull string line to follow roadside edge of posts.
Figure 31. Place Ground Strut parallel to string line.
Now follow steps 2 – 14 in the Tangent installation instructions.
Note: The “kink” in the line of rail between rail 3 and rail 4 (at post #7) is
formed by simply pushing the rails around to follow the ared line of posts.
This is not factory bent.
Step 1 - Set Out
Pull a string line out with the desired offset (0 -1.2m; 0-4 ft)
Note that the are is a straight are, over the length of the system (11.4m; 38 ft)
The string line should be set to follow the roadside edge of the posts (Figure 29).
All the posts except post 1 have a blockout so take care to place the roadside face of post 1
200mm (8 in) towards the roadway (Figure 30).
Post 1 bottom, the Ground Strut and the Soil Anchor are then placed parallel to the string line on
the roadside of it (Figure 31).
X-TENSION®SYSTEM

Lindsay Transportation Solutions Sales and Services, Inc (888) 800-3691 [U.S. toll free] or +1 (707) 374-6800 Lindsay Transportation Solutions Sales and Services, Inc (888) 800-3691 [U.S. toll free] or +1 (707) 374-6800
18
X-Tension - Median Installation Instructions
Slider Brackets
Figure 32. X-Tension median installation.
Post 5 Shear Bolts
Median Radius Rail
Impact Head
Median Impact Head
This section deals with installation of a Median X-Tension system as a Median guardrail terminal
end application.
Site
preparation
The Median X-Tension system is installed parallel to the standard median barrier, therefore no
offset is used (Figure 32).
Ensure that the area where the X-Tension is to be installed is at enough so that the soil anchor
will not protrude more than 100mm (4 in) [preferred 75 mm 3 in)] from ground level when mea-
sured with a straight line over a 1.5m (5 ft) cord. Minor site grading may be required.
INSTALLATION AND MAINTENANCE MANUAL

Lindsay Transportation Solutions Sales and Services, Inc (888) 800-3691 [U.S. toll free] or +1 (707) 374-6800 19
X-Tension - Median Installation Instructions
Step 1 - Set Out
The Median X -Tension is essentially one Tangent X-Tension installed parallel to one side of the
median barrier (Figure 33), with a small number of additional components and rail attached
parallel with the other side of the barrier (Figure 34).
Determine which side of the barrier will have the Tangent X-Tension portion of the Median X-
Tension installed parallel to it. (Usually the heaviest trafc volume side)
Pull a string line out the length of the system, parallel with the median barrier posts.
The string line should be set to follow the side of the posts, on the side that it is desired to install
the tangent X-Tension.
Figure 33. Essentially a tangent system installed parallel to
median barrier. Figure 34. Small number of additional components.
Step 2 – Installing Tangent X-Tension Portion
Follow steps 2 – 13 in the Tangent installation instructions, with the following exceptions.
(1) DO NOT set post 3 back 30-50mm (1 -2 in) as per the instructions in Step
2 of the Tangent installation instructions. For the Median application, Post 3
remains parallel with the other line posts.
(2) As noted on page #7, Post 2 must be steel crimped and Post 3-6 are
always standard steel I-beam posts.
Now follow the remaining steps 3 to 8 to complete the backside of the median terminal.
X-TENSION®SYSTEM

Lindsay Transportation Solutions Sales and Services, Inc (888) 800-3691 [U.S. toll free] or +1 (707) 374-6800 Lindsay Transportation Solutions Sales and Services, Inc (888) 800-3691 [U.S. toll free] or +1 (707) 374-6800
20
INSTALLATION AND MAINTENANCE MANUAL
X-Tension - Median Installation Instructions
Figure 35. Fit secondary head to main head. Figure 36. Fix secondary head into place.
Figure 37. Rails installed with blockouts. Figure 38. Splice rail 2 to rail 3 with 8 special shear bolts.
Step 3 – Attach Secondary Impact Head
Fit secondary head to main head by pushing sideways onto the main head as shown below
(Figure 35), until the holes in the gussets line up. Fix into place with either the 25mm (1 in) pin
and pin lynch, or 2 M24 x 50mm (1 in X 2 in) bolts as shown (Figure 36).
Step 4 – Attach Backside Rail #3 and Rail #2
Rails 3 and 2 are installed like standard guardrail with blockouts between the rail and post (Figure
37). Attach rails to post 2, 4, 5 and 6 with blockouts and post bolts supplied (do not bolt the rail to
post 3) and splice rail 3 to rail 4 with 8 standard splice bolts. At post 7 lap rail in the direction of
trafc as per standard median barrier.
Ensure that rail 2 is spliced to rail 3 using the special shear bolts (yellow head) supplied.
DO NOT use standard splice bolts at this joint (Figure 38). Be sure rail 2 is lapped outside
rail 3 in both directions. DO NOT USE AN AIR-IMPACT WRENCH TO TIGHTEN SHEAR
BOLTS. SHEAR BOLTS WILL BREAK IF OVER-TIGHTEND.
This manual suits for next models
9
Table of contents
Popular Other manuals by other brands
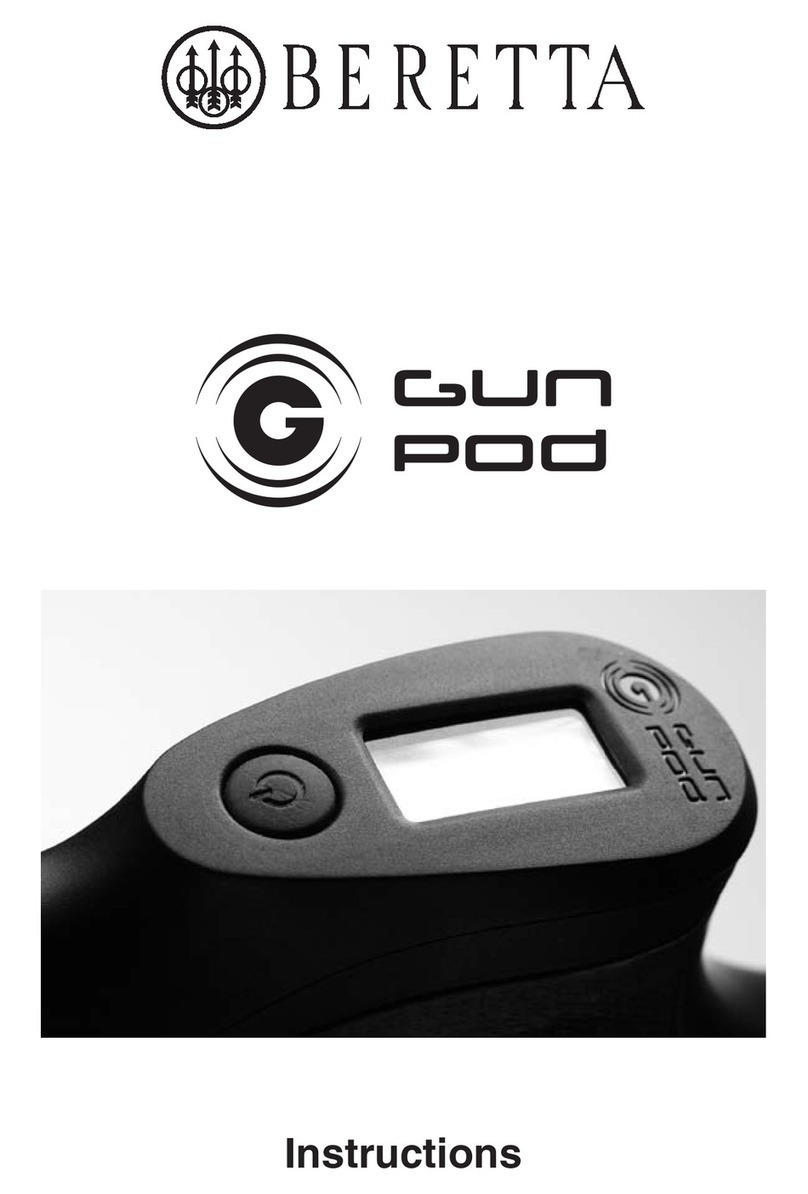
Beretta
Beretta A400 Xcel Sporting instructions
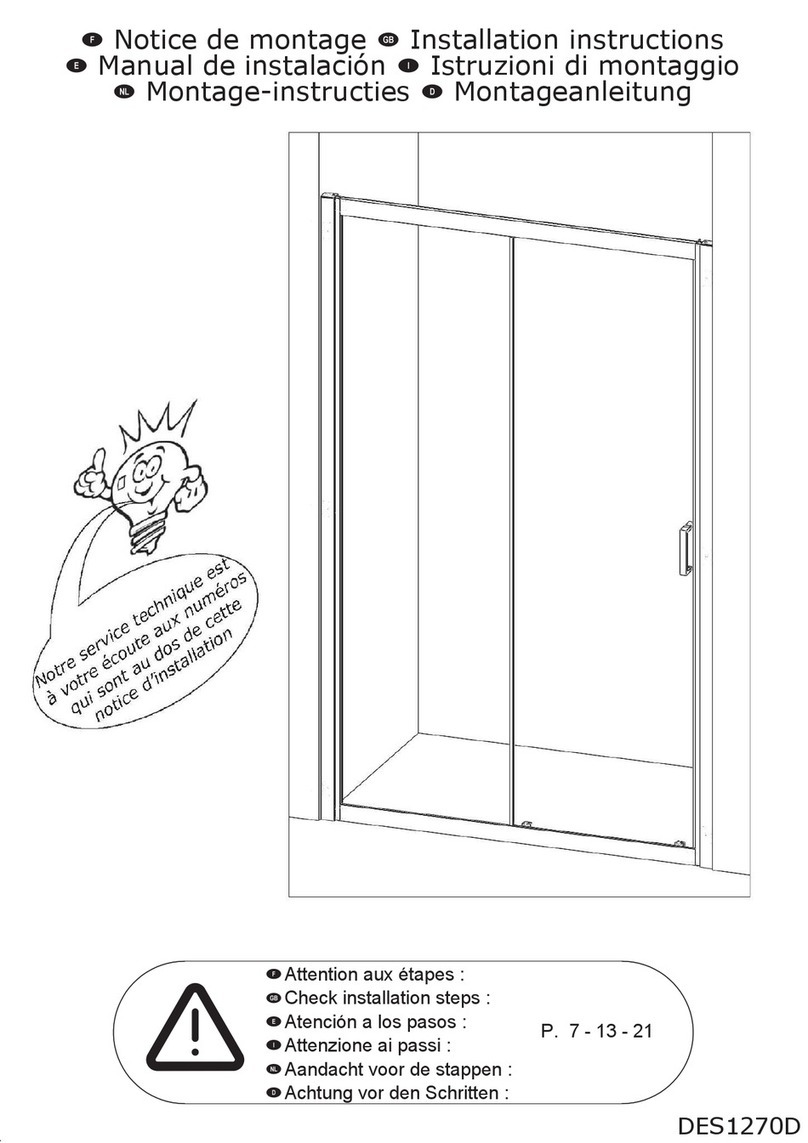
Kinedo
Kinedo DES1270D Installation instruction
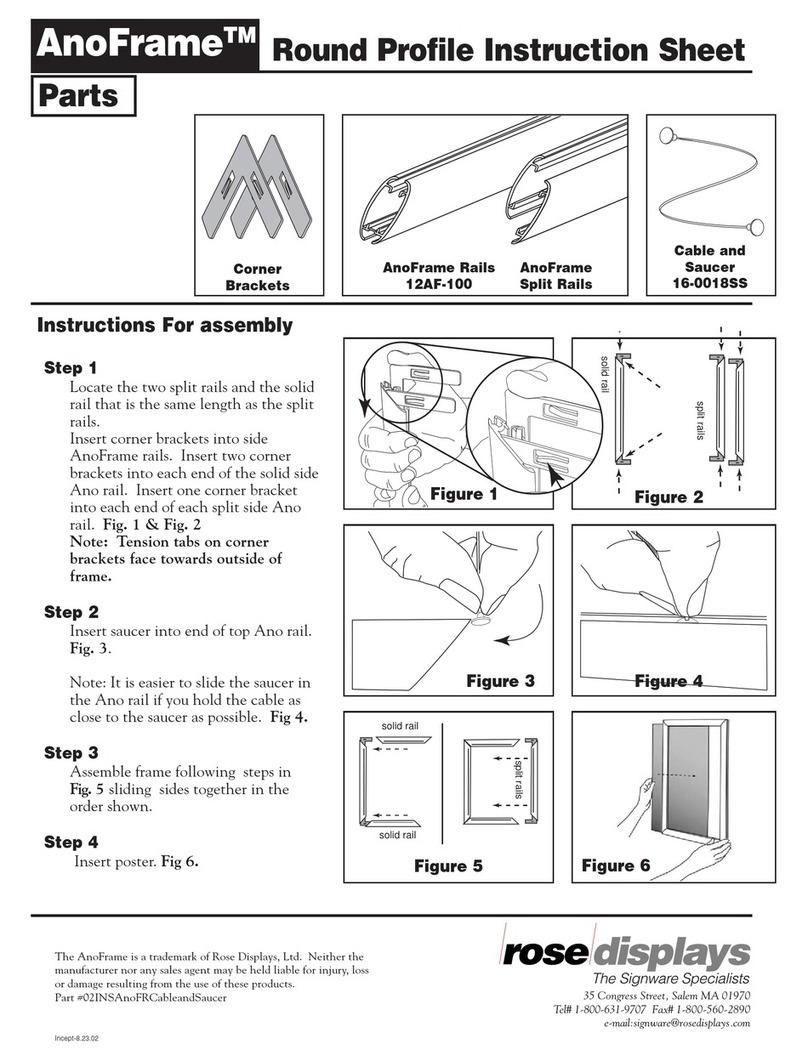
ROSE DISPLAYS
ROSE DISPLAYS ANOFRAME ROUND WITH CABLE AND SAUCER manual
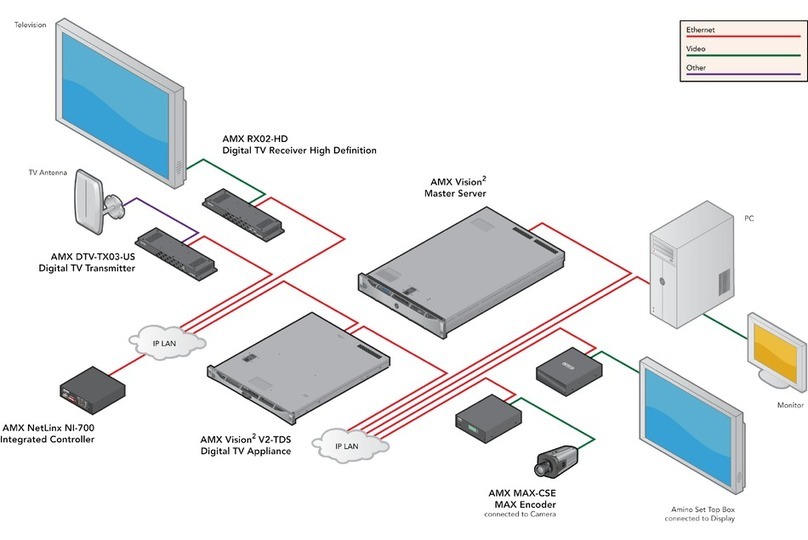
AMX
AMX DTV VISION2 INTEGRATION - DIAGRAM manual

Stierius
Stierius VARIO 5 operating instructions
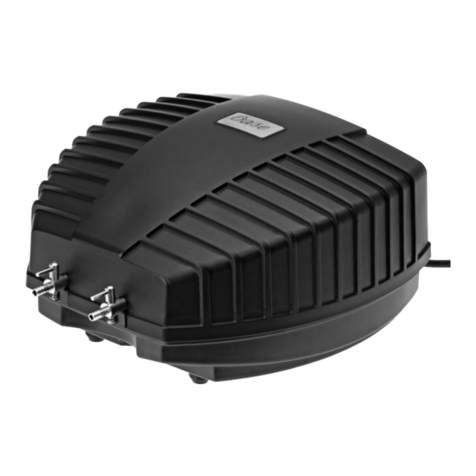
Oase
Oase AquaOxy 1000 operating instructions