baxter OV310 Series User manual

OV310G MODEL SHOWN
OV310 Series Mini Rack Oven
Installation Instructions
OV310G ML-132515
OV310E ML-132516
- NOTICE -
This Manual is prepared for the use of trained Baxter Service
Technicians and should not be used by those not properly
qualified.
This manual is not intended to be all encompassing. If you have
not attended a Baxter Service School for this product, you should
read, in its entirety, the repair procedure you wish to perform to
determine if you have the necessary tools, instruments and skills
required to perform the procedure. Procedures for which you do
not have the necessary tools, instruments and skills should be
performed by a trained Baxter Service Technician.
The reproduction, transfer, sale or other use of this Manual,
without the express written consent of Baxter, is prohibited.
This manual has been provided to you by ITW Food Equipment
Group LLC ("ITW FEG") without charge and remains the property
of ITW FEG, and by accepting this manual you agree that you will
return it to ITW FEG promptly upon its request for such return at
any time in the future.
SERVICE MANUAL
A product of Baxter MFG. Co., Inc 19220 State Route 162 East Orting, WA 98360
F25422 Rev. B (0917)

TABLE OF CONTENTS
IMPORTANT FOR YOUR SAFETY ......................................................................... 3
IMPORTANT FOR YOUR SAFETY ..................................................................... 3
SERVICE UPDATES ....................................................................................... 4
SERVICE UPDATES ................................................................................... 4
GENERAL .................................................................................................. 5
INTRODUCTION ....................................................................................... 5
UNPACKING ........................................................................................... 5
LOCATION ............................................................................................. 5
CLEARANCE DIMENSIONS ............................................................................ 5
TESTING THE GAS SUPPLY PIPING SYSTEM (GAS OVENS ONLY) ................................... 5
INSTALLATION CODES AND STANDARDS ............................................................ 5
OVEN MOUNTED ON CASTERS (GAS OVENS ONLY) ............................................. 6
TOOLS ................................................................................................. 6
SPECIFICATIONS ...................................................................................... 6
INSTALLING OVEN ........................................................................................ 8
MOUNTING OVEN ..................................................................................... 8
LEVELING OVEN ...................................................................................... 8
VENTILATION .......................................................................................... 8
INITIAL START-UP ..................................................................................... 9
OV310/OV310 HIGH ALTITUDE CORRECTION CHART ............................................... 15
FINAL CHECKS ....................................................................................... 16
OV310 Series Mini Rack Oven Installation Instructions
© BAXTER 2017
F25422 Rev. B (0917) Page 2 of 16

IMPORTANT FOR YOUR SAFETY
IMPORTANT FOR YOUR SAFETY
THIS MANUAL HAS BEEN PREPARED FOR PERSONNEL QUALIFIED TO INSTALL GAS EQUIPMENT, WHO
SHOULD PERFORM THE INITIAL FIELD START-UP AND ADJUSTMENTS OF THE EQUIPMENT COVERED
BY THIS MANUAL
POST IN A PROMINENT LOCATION THE INSTRUCTIONS TO BE FOLLOWED IN THE EVENT THE SMELL OF
GAS IS DETECTED. THIS INFORMATION CAN BE OBTAINED FROM THE LOCAL GAS SUPPLIER
IMPORTANT
IN THE EVENT A GAS ODOR IS DETECTED, SHUT DOWN UNITS AT MAIN SHUTOFF VALVE AND CONTACT
THE LOCAL GAS COMPANY OR GAS SUPPLIER FOR SERVICE.
FOR YOUR SAFETY
DO NOT STORE OR USE GASOLINE OR OTHER FLAMMABLE VAPORS OR LIQUIDS IN THE VICINITY OF
THIS OR ANY OTHER APPLIANCE
WARNING
IMPROPER INSTALLATION, ADJUSTMENT, ALTERATION, SERVICE OR MAINTENANCE CAN CAUSE
PROPERTY DAMAGE, INJURY OR DEATH. READ THE INSTALLATION, OPERATING AND MAINTENANCE
INSTRUCTIONS THOROUGHLY BEFORE INSTALLING OR SERVICING THIS EQUIPMENT.
IN THE EVENT OF A POWER FAILURE, DO NOT ATTEMPT TO OPERATE THIS DEVICE.
KEEP AREA AROUND OVEN CLEAR OF COMBUSTIBLES.
DO NOT OBSTRUCT COMBUSTION AND VENTILATION OPENING ON THE OVEN.
OV310 Series Mini Rack Oven Installation Instructions - IMPORTANT FOR YOUR SAFETY
Page 3 of 16 F25422 Rev. B (0917)

GENERAL
INTRODUCTION
These instructions are for the OV310 Series Mini Rack
Oven. The Mini Rack Oven is shipped assembled
requiring minimal field assembly.
All Mini Rack Ovens will require leveling and
connection to utilities. All information, illustrations and
specifications contained in this manual are based on
the latest product information available at the time
indicated on the cover of the manual.
UNPACKING
Remove the crating from oven and check for possible
shipping damage. If the oven is found to be damaged
after unpacking, save packaging material and contact
the carrier within 15 days of delivery.
You will need to remove door(s), front trim and control
panel prior to maneuvering oven thru a standard 36"
doorway.
Prior to starting oven remove rack retainer screw used
to secure removable oven rack during shipment.
LOCATION
Level floor or noncombustible surface within 1/8" per
foot up to 3/4" in all directions.
Oven is intended to be installed with its back against
a wall and not directed toward food cooking or
preparation areas.
Oven can be mounted on a stand, MB300 Proofer
Cabinet or noncombustible surface.
Do not obstruct the flow of combustion and ventilation
air. Keep the appliance area free and clear from
combustibles.
Make sure there is an adequate supply of make-up air
in the room to allow for combustion.
The electrical diagram is located on the inside of the
right side panel.
CLEARANCE DIMENSIONS
Oven UL/CSA Listed for 0" clearance to combustible
surfaces for back and side walls.
Minimum 24" clearance is recommended on the right
side of oven for service access. If right side of oven is
within 30" of radiant heat or grease vapor source, a
vent guard is required.
A 1" to 4" back clearance is recommended for
plumbing rear drain connection.
Oven must be installed so that top of oven is located
above 6 feet from the floor.
Top of oven requires adequate clearance for servicing
accessibility.
TESTING THE GAS SUPPLY PIPING
SYSTEM (GAS OVENS ONLY)
When test pressures exceed 1/2 psig (14" w.c.)
(3.45kPa), the oven and its individual shutoff valve
must be disconnected from the gas supply piping.
When test pressure is 1/2 psig (14" w.c.) (3.45kPa) or
less, the oven must be isolated from the gas supply
piping system by closing its individual shutoff valve.
INSTALLATION CODES AND
STANDARDS
OV310 mini rack ovens must be installed in
accordance with:
United States
1. State and local codes.
2. National Fuel Gas Codes, ANSI-Z223.1 (latest
edition), available from:
American Gas Association
1515 Wilson Boulevard
Arlington, VA 22209
3. ANSI/NFPA 96, Vapor Removal from Cooking
Equipment (latest edition), available from:
National Fire Protection Association
1 Batterymarch Park
Quincy, MA 02169
4. National Electrical Code, ANSI/NFPA-70 (latest
edition).
Canada
1. Local codes.
2. CAN/CGA-B149-1, Installation for Natural Gas
Burning Appliances and Equipment (latest
edition).
OV310 Series Mini Rack Oven Installation Instructions - GENERAL
Page 5 of 16 F25422 Rev. B (0917)

3. CAN/CGA-B149-2, Installation for Propane
Burning Appliances and Equipment (latest
edition).
4. Canadian Electrical Code, Part 2, CSA Standard
C22.1 (latest edition).
Oven Mounted on Casters (Gas Ovens Only)
Appliances equipped with casters, instructions
that:
1. The installation shall be made with a connector
that complies with the Standard for Connectors
for Moveable Gas Appliances ANSI Z21.69 or
Connectors for Moveable Gas Appliances CAN/
CGA-6.16, and a quick-disconnect device that
complies with the Standard for Quick-
Disconnect Devices for Use with Gas Fuel ANSI
Z21.41 or Quick Disconnect Devices for Use with
Gas Fuel CAN1-6.9.
2. Adequate means must be provided to limit the
movement of the appliance.
TOOLS
Standard Tools
1. Standard set of hand tools.
2. Field service grounding kit Part No. TL-84919.
3. Screwdriver set (Jeweler's).
Test Equipment
1. Bacharach combustion analyzer No. 125 Fyrite
Pro (Order from Bakery Support).
2. Multi-Meter that measures 200 micro amps
Grainger No. 6MR09.
3. Digital thermometer with 6' probe Grainger No.
4YV88.
4. Dwyer incline manometer Grainger No. 3T294.
5. Force gauge measure in lbs. (Min. 0-10lbs).
Special Tools
1. Mini laser level, self-leveling with tripod Harbor
Freight No. 92703-OVGA.
SPECIFICATIONS
Plumbing Connections
Water and waste piping and connections shall comply
with the International Plumbing Code 2003,
International Code Council (ICC), or to the Uniform
Plumbing Code 2003, International Association of
Plumbing and Mechanical Officials (IAPMO).
NOTE: Plumbing connections must comply with
applicable sanitary, safety and plumbing codes and
provide adequate backflow protection to comply with
applicable federal, state and local codes.
1. Water connection:
1/2" NPTF water line connection.
Cold water 30-75 psi flow (1.2 G.P.M.).
Recommended water hardness range: 2-4 grains
per gallon.
Recommended pH range: 7.0 to 8.0.
Acceptable range for chloride concentration:
0-30 ppm.
2. Drain connection:
1/2" NPTF rear drain connection, route to
minimum 1" air gap drain.
Separate drain line recommended if oven
installed on a proofer cabinet.
3. Gas connection (Gas Oven):
3/4" NPT pipe size 95,000 BTU/Hr.
Standard - Natural gas.
Optional - Propane gas.
SUPPLY GAS PRESSURE INPUT
Natural Propane BTU/HR
5" to 14" w.c. 11" to 14" w.c. 95,000
4. Electrical connection:
Control circuit
Both gas and electric ovens require a
dedicated control circuit 120V 60Hz 1 Phase
15 Amp Maximum.
RATINGS:
CONTROL CIRCUIT (ALL OVENS) *
Volts Amps Phase HZ
120 10 1 60
* Includes auxiliary circuit
AUXILIARY EXTERNAL OUTPUT CIRCUIT (ALL
OVENS)
Volts Amps Phase HZ
120 5 1 60
5. Combustion vent:
OV310 Series Mini Rack Oven Installation Instructions - GENERAL
F25422 Rev. B (0917) Page 6 of 16

8" DIA connection collar. Combustion vent can
be directly vented or indirectly (canopy hood)
outside. Direct venting requires draft diverter. All
services must comply with all federal, state and
local codes.
6. Indirect vent standard:
Oven located under an exhaust hood with
adequate overhangs and exhaust rates to
completely capture byproducts of combustion
from flue. A minimum clearance of 18" must be
maintained from the termination of the oven flue
to the filters of the hood venting system. The
hood exhaust fan must be electrically interlocked
with the oven. All services must comply with all
federal, state and local codes.
7. Direct vent option:
Duct and fan (if required) to be supplied by
customer. All services must comply with all
federal, state and local codes. Draft of -0.03"w.c.
to -0.11"w.c. required at a point 6" above draft
hood upper collar.
NOTES:
• Oven start-up must be performed by an
Authorized Servicer.
• Customer responsible to finish and install all
utilities to and from oven.
• All services must comply with all Federal,
State and Local codes.
• Oven must be installed on a level floor.
Oven is UL/C-UL classified and CSA (AGA/
CGA) approved for 0" clearance to
combustible surfaces on the side and rear
walls. If right side of oven is within 30" of
radiant heat or grease vapor source, a vent
guard is required. Unit requires 1" to 4"
clearance for rear drain connection.
• Top of oven requires adequate clearance for
service accessibility.
• Oven will fit through a standard 36" doorway
with doors, control panel, and trim package
removed.
• Manufacturer reserves the right to make
changes in sizes and specifications.
Fig. 1
OV310 Series Mini Rack Oven Installation Instructions - GENERAL
Page 7 of 16 F25422 Rev. B (0917)

INSTALLING OVEN
This manual is written for OV310 Mini Rack Ovens. Before installing oven, compare parts to packing list to ensure
all parts were received. Wait as long as possible before removing plastic protective covering from panels and doors.
Prior to installing oven, check facility floor or noncombustible surface being level within 1/8" per foot up to 3/4" in all
directions.
MOUNTING OVEN
Oven can be installed on a stand, MB300 proofer
cabinet, or noncombustible surface.
1. Mount oven:
A. Run a bead of sealant on mounting surface
around inside perimeter of the oven
footprint. Use NSF approved sealant, Dow
Corning 732 or GE RTV108.
B. Position oven onto mounting surface.
C. Secure the rear of the oven to the mounting
surface using tie-down brackets.
2. Position oven into final location.
LEVELING OVEN
1. Check oven to be level front to back side to side
by placing level on oven rack, shim if necessary.
A. If oven is installed on a stand with adjustable
legs, rotate the foot clockwise or counter
clockwise to level oven front to back and
side to side.
B. If oven is installed on casters, determine
which caster needs to be adjusted.
1) Ensure locks on casters are locked.
2) Use a block of wood to support
equipment near caster that needs
adjustment.
3) Loosen the bolt on the caster needing
adjustment and insert shim(s) between
the caster plate and bottom of stand
leg/proofer cabinet.
4) Re-tighten caster bolt and check oven
for being level.
VENTILATION
Ventilation requirements will vary with each
installation and must comply with applicable portions
of the National Fire Protection Association Standards
#96, #94 and with local codes.
Exhaust Fan Interlock
A connection point (maximum 5-amps) is provided for
Indirect Vent (Exhaust Hood) or optional Direct Vent
(Draft Hood). It is located behind the right side service
panel adjacent to the 120 V power connection.
Consult local codes for vent interlock requirements.
Indirect Vent (Under Exhaust Hood)
Locate the oven under an exhaust hood with adequate
overhangs and exhaust rates to completely capture
the byproducts of combustion discharged from the
flue. From the termination of the flue to the filters of
the hood venting system, a minimum clearance of 18"
must be maintained. The hood exhaust fan must be
electrically interlocked with the oven.
Direct Vent (Draft Hood)
1. Remove four screws from the tabs securing fan
grille to top of draft inducer and lift grille off.
Fig. 2
2. Bend the four exposed oven flue collar tabs
vertically and secure the draft diverter to the oven
flue collar with four screws.
OV310 Series Mini Rack Oven Installation Instructions - INSTALLING OVEN
F25422 Rev. B (0917) Page 8 of 16

Fig. 3
3. With oven in position connect customer supplied
exhaust ducting to the draft diverter.
NOTE: Draft diverter must be installed with 6"
clearance between bottom of draft diverter skirt and
top of draft inducer, and 8" dia. flue stack. All services
must comply with all federal, state and local codes.
Fig. 4
INITIAL START-UP
Disconnect the electrical power to
the machine and follow lockout /
tagout procedures. There may be
multiple circuits. Be sure all circuits
are disconnected.
NOTE: Remove all protective plastic sheeting from
oven surfaces and wipe down to remove all
fingerprints, prior to heating oven.
NOTE: Remove single retainer screw located in top
of rack just below rotator shaft as well as the two flat
washers located between shoulder bolts and rack
bottom support.
NOTE: All utility connections by others.
Verify the following:
• Gas supply line shut-off valve is in the OFF
position.
• Gas supplied matches data plate and gas valve
on oven.
• Gas valve is in the OFF position.
• Electrical connections have been made by
electrician. 120V control circuit, high voltage
heating circuit, and powered exhaust fan
interlock (external device maximum 5 amp).
Fig. 5
• Drain connected by plumber at right rear corner
of oven.
• Water line is connected by plumber to pressure
regulator assembly located at right rear corner of
oven.
• Water shut off is installed in supply line.
NOTE: If a water filtration unit is installed in water
supply line, verify that a filter cartridge (supplied by
customer) is installed in unit (performed by a plumber).
OV310 Series Mini Rack Oven Installation Instructions - INSTALLING OVEN
Page 9 of 16 F25422 Rev. B (0917)

NOTE: Refer to oven installation checklist and
complete during initial start-up.
1. Verify flue draft (direct vent with gas oven only).
A. Insert a draft tube into the flue stack 6"
above the top of the draft diverter. If
required, drill a hole in flue stack to insert
draft tube.
B. Connect a incline manometer or equivalent
to the draft tube.
Fig. 6
C. With the oven turned off and doors closed,
check the manometer reading. Reading
should be a vacuum of 0.03" to 0.11" W.C.
1) If vacuum requirements are met,
proceed to step D.
2) If vacuum requirements are not met,
the customer supplied flue stack must
be modified to meet the above stated
requirements.
3) After flue stack change has been done,
repeat the procedure.
D. Operate the oven for a minimum of 5
minutes.
1) While burner is lit, check for a back
draft at the draft diverter relief opening
(i.e. smoke emitted from a smoldering
source).
2) If no back draft indicated (smoke going
up draft diverter relief opening) test is
complete.
3) If back draft indicated (smoke not going
up draft diverter relief opening) the
oven must not be operated, until proper
adjustments have been made (correct
flue stack to have adequate up draft
through the draft diverter relief
opening).
E. Verify oven rack rotates and baking
compartment circulation fan is turning. If not,
door switches will need to be adjusted, as
outlined under DOOR SWITCH
ADJUSTMENT Step 4.
NOTE: Baking compartment circulation fan will run
continuously with time entered in the bake timer and
cycle on/off with heating circuit if no time is entered in
the bake timer.
2. Ignition Sequence Check (Gas Ovens Only).
NOTE: Ignition module makes one attempt to light
burner before locking out.
NOTE: Remove power from ignition control module
by turning main circuit breaker to oven off or by
opening the loading doors for a minimum of 5
seconds.
A. Turn gas valve off to test ignition sequence
check.
B. Set oven to call for heat by pressing bake
temperature display UP ARROW key, until
HEAT ON LED illuminates.
C. Draft inducer energized for 15 seconds pre-
purge cycle.
D. Hot surface igniter glows indicating that it is
energized.
E. 2 seconds after igniter was energized, gas
valve solenoid is energized.
F. After igniter has been energized for 4
seconds, flame sensor will not have
recognized a flame.
1) Power is removed from igniter and gas
valve.
G. After initial try for ignition and the burner has
not lit, there will be an additional 15 second
purge time.
H. LED on ignition control will flash in a 3 flash
sequence indicating a flame recognition
failure and that the control is in lock-out
mode.
I. This indicates the safety lock-out circuit is
functioning properly.
NOTE: See IGNITION SEQUENCE TIMING
DIAGRAM Fig. 19
3. Gas Pressure Adjustment (Gas Ovens Only).
A. Remove the gas valve cover to access the
gas valve pressure taps.
OV310 Series Mini Rack Oven Installation Instructions - INSTALLING OVEN
F25422 Rev. B (0917) Page 10 of 16

B. Attach a manometer to the 1/8" NPT outlet
pressure tap and one to the 1/8" NPT inlet
pressure tap on the gas valve and turn the
gas supply and gas valve on.
C. Remove the pressure regulator adjustment
cap screw from the main gas valve to
access the adjustment screws.
D. Turn the main gas valve on, turn the oven
on and set the temperature to call for heat.
E. With the burner flame established, insure
the proper line pressure (adjust supply
regulator if necessary) and adjust the outlet
manifold pressure regulator to:
3.5" W.C. (Natural Gas)
10.0"W.C. (Propane Gas)
4. Door Switch Adjustment.
If the rack does not rotate and the circulation fan
does not come on, then the door switches may
be out of adjustment. The door switches are
located on top of oven.
A. Turn the power On.
B. Access door switches on top of oven.
C. With the oven doors closed loosen door
switch screws and position door switch
bracket until door switch closes.
D. Secure door switch screws and put oven
into operation.
NOTE: If unable to determine which switch is not
closing, adjust switches inward / outward until
switches are activated when doors are completely
closed and deactivated when doors are opened more
than ½".
Fig. 9
5. Door Adjustment Procedure.
A. Check to ensure that the door gap is a
consistent 3/8" between the doors. Check
from top of doors to bottom of doors.
Fig. 10
NOTE: If door gap needs to be adjusted - adjust hinge
plates to obtain consistent 3/8" gap.
OV310 Series Mini Rack Oven Installation Instructions - INSTALLING OVEN
Page 11 of 16 F25422 Rev. B (0917)

Fig. 11
B. Ensure the top of the doors and the bottom
of the doors are even. Place a straight edge
on the top of the doors to verify.
NOTE: If adjustments are required - adjust hinge
plates.
Fig. 12
C. If a door is difficult to open loosen the (top
and bottom) corresponding strikers and
slide the strikers toward the door hinge
point.
Fig. 13
D. If a door will not remain closed loosen the
(top and bottom) corresponding strikers and
slide the strikers away from the door hinge
point.
Fig. 14
E. If the top of the door unlatches before the
bottom of the door - or the bottom of the door
unlatches before the top of the door - loosen
the corresponding striker that is unlatching
first and move away from the door hinge
point.
OV310 Series Mini Rack Oven Installation Instructions - INSTALLING OVEN
F25422 Rev. B (0917) Page 12 of 16

Fig. 15
6. Rack stopping position adjustment.
If rack is adjusted without customer's typical bake
product load weight on it, position rack
approximately 5° prior to being square with the
loading doors. Some under or over travel of rack
positioning should be expected depending on
product load. The rack rotation components are
located on top of the oven.
A. Put oven into operation and perform rack
operation test with customer's typical bake
product load weight on rack. If rack does not
stop in the proper rack load/unload position,
perform rack stopping position adjustment.
B. To adjust rack stopping position:
1) Open oven loading doors and verify
rack is square with the loading doors, if
not position rack so it is square.
2) Align the pointer switch actuator
sideways to align with pointer switch on
top of the rotation shaft.
NOTE: If rack stops to soon, move pointer switch
actuator away from pointer switch on top of the
rotation shaft.
3) Put oven into operation and check for
proper rack load/unload positioning.
4) Repeat the procedure until load/unload
rack position is achieved.
Fig. 16
7. Initial heating of oven (All Ovens).
A. Place a thermocouple 1/2" away from air
louver and near the vertical center of right
hand front air louver inside the baking
compartment.
Fig. 17
B. Route thermocouple lead to the outside of
the oven. Make sure that the lead is kept
clear of the rack carrier.
C. Close the loading doors.
D. Set the control baking temperature to 300F.
(150C.) and bake timer for 30 minutes.
NOTE: Baking compartment circulation fan will run
continuously with time entered in the bake timer and
cycle on/off with heating circuit if no time is entered in
the bake timer.
E. After time elapses, press Stop key to silence
beeper.
F. Fully open loading doors to verify that
baking compartment circulation fan de-
energizes.
OV310 Series Mini Rack Oven Installation Instructions - INSTALLING OVEN
Page 13 of 16 F25422 Rev. B (0917)

G. Close loading doors and set the control
baking temperature to 400F. (200C.) and
bake timer for 60 minutes.
H. Check the temperature reading on the
thermocouple meter when the at the exact
time the heat light on the controller goes out.
I. Compare the readings of the thermocouple
meter and the controller temperature
display.
J. If the temperature difference between the
two readings is greater than ±2F. or ±1C.
adjust the temperature offset (P4).
1) If temperature test shows a
temperature higher than controller,
increase temperature offset (P4).
2) If temperature test shows a
temperature lower than controller,
decrease temperature offset (P4).
NOTE: Do not calibrate controller if the difference in
temperature readings is greater than the range of the
controller, replace controller (range ±50°F.).
NOTE: Before calibrating the controller the oven must
maintain a constant temperature for at least one hour.
K. To Adjust:
1) Access set-up mode by pressing and
holding Start and On/Off for 3
seconds.
2) Press Set Temp UP Arrow to select
set-up item P4 shown in timer display.
3) Use the Bake Timer Arrow to adjust
offset temperature in the temperature
display.
4) Press On/Off to exit set-up mode.
8. Combustion Analysis (Gas Oven Only).
NOTE: The burner must be operating during this test.
A. Allow oven to cool to 300F. (150C.).
B. Insert a combustion analyzer meter into hole
in top of the draft inducer.
Fig. 18
C. With burner flame established, take
combustion measurements O2, CO2 and
CO readings.
O2: (Range 6% to 10%)
CO2: (Range 6% to 8%)
CO: Not to exceed 0.04% (400PPM)
D. Record set-up information on the label
provided inside the controller compartment.
9. Steam Test (All Ovens).
A. Set 20 seconds on steam timer, one minute
on bake timer, and press Start key to initiate
steam test.
NOTE: Only a minimal amount of water should exit out
the drain after 20 seconds.
B. Check for steam leakage around loading
doors. If leakage is present, adjust door as
required.
C. After time has expired press Stop key to
silence beeper.
D. Press the Vent key to open baking chamber
vent. Allow oven to vent for two minutes,
then close vent.
E. Set the control baking temperature below
room temperature and open loading doors
to release vapors.
OV310 Series Mini Rack Oven Installation Instructions - INSTALLING OVEN
F25422 Rev. B (0917) Page 14 of 16

Fig. 19
OV310/OV310 HIGH ALTITUDE CORRECTION CHART
ALTITUDE CORRECTION CHART
ELEVATION IN FEET
OV310G OV310G
Natural Gas Propane Gas
Orifice #52
Orifice Diameter 0.0635
Orifice #60
Orifice Diameter 0.0400
Oven Rating BTU/Hr Manifold Pressure
"W.C. Oven Rating BTU/Hr Manifold Pressure
"W.C.
0 (sea level) 95,000 3.5 95,000 10
3,000 83,600 2.9 83,600 7.9
3,500 81,700 2.8 81,700 7.6
4,000 79,800 2.7 79,800 7.2
4,500 77,900 2.5 77,900 6.9
5,000 76,000 2.4 76,000 6.6
5,500 74,100 2.3 74,100 6.2
6,000 72,200 2.2 72,200 5.9
OV310 Series Mini Rack Oven Installation Instructions - INSTALLING OVEN
Page 15 of 16 F25422 Rev. B (0917)

ALTITUDE CORRECTION CHART
ELEVATION IN FEET
OV310G OV310G
Natural Gas Propane Gas
Orifice #54
Orifice Diameter 0.0550
Orifice #65
Orifice Diameter 0.0350
Oven Rating BTU/Hr Manifold Pressure
"W.C. Oven Rating BTU/Hr Manifold Pressure
"W.C.
6,500 70,300 3.7 70,300 9.6
7,000 68,400 3.5 68,400 9.1
7,500 66,500 3.3 66,500 8.6
8,000 64,600 3.1 64,600 8.1
8,500 62,700 2.9 62,700 7.6
9,000 60,800 2.7 60,800 7.2
9,500 58,900 2.6 58,900 6.7
10,000 57,000 2.4 57,000 6.3
FINAL CHECKS
1. Test for proper operation.
NOTE: Baking compartment circulation fan will cycle
on/off with heating circuit.
2. Cool-Down:
A. Press Off key to turn off oven.
B. With loading doors open, press Vent key to
initiate oven cool-down.
C. After oven has reached a safe cool-down
temperature, stop automatic cool-down by
closing loading doors and/or turning the
oven power off.
3. Complete Installation Checklist and distribute
copies per instructions on checklist.
OV310 Series Mini Rack Oven Installation Instructions - INSTALLING OVEN
F25422 Rev. B (0917) Page 16 of 16
This manual suits for next models
2
Table of contents
Other baxter Oven manuals
Popular Oven manuals by other brands

Electrolux
Electrolux Air-O-Steam 267553 Specification sheet

Miele
Miele H 6200 BM Quick install

Kenwood
Kenwood CKB200 Instructions for use - installation advice
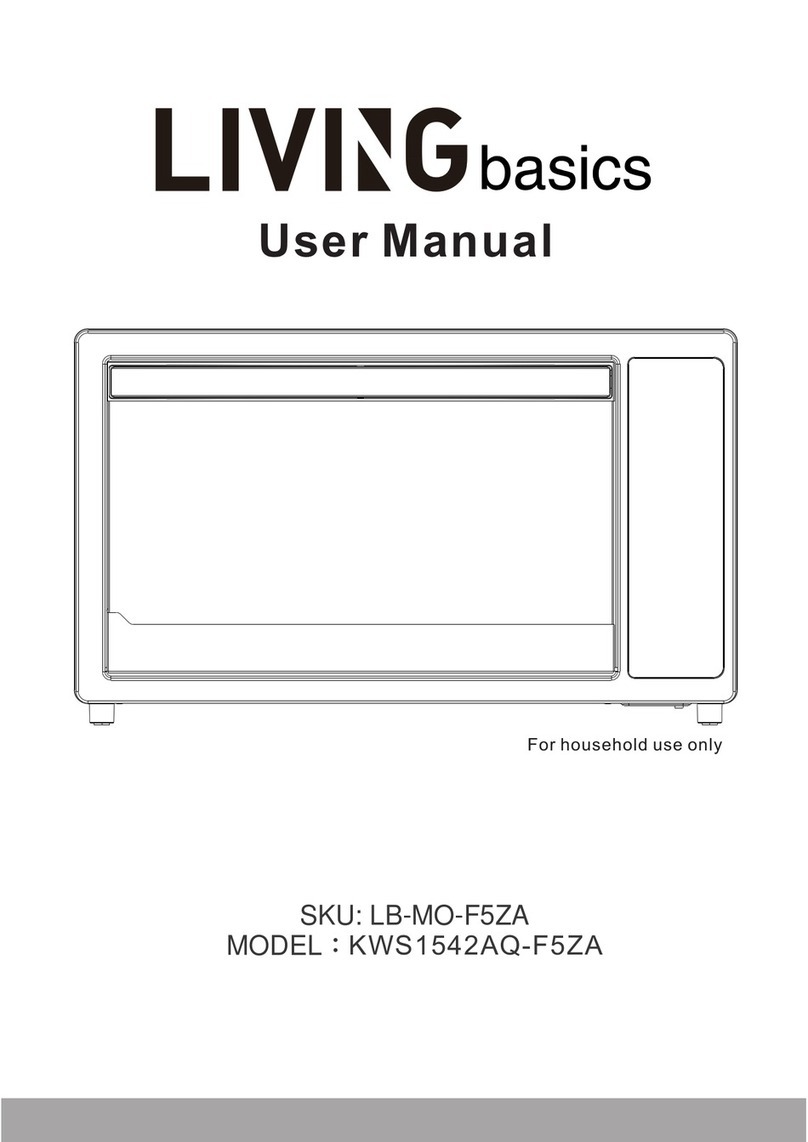
LIVING BASICS
LIVING BASICS KWS1542AQ-F5ZA user manual

Brandt
Brandt BOP7539 BB User instructions

Gastroback
Gastroback Design Bistro Ofen Advanced Pro operating instructions