Beckhoff EK1914 User manual

AS2000
Blindtext Blindtext Blindtext
Operating Manual | EN
EK1914
TwinSAFE Bus Coupler with 2 fail-safe inputs and 2 fail-safe outputs
2023-03-01 | Version: 2.0.0


Table of contents
EK1914 3Version: 2.0.0
Table of contents
1 Notes on the documentation....................................................................................................................5
1.1 Disclaimer..........................................................................................................................................5
1.1.1 Trademarks ........................................................................................................................5
1.1.2 Patents ...............................................................................................................................5
1.1.3 Limitation of liability ............................................................................................................6
1.1.4 Copyright............................................................................................................................ 6
1.2 Version numbers ...............................................................................................................................7
1.3 Staff qualification...............................................................................................................................8
1.4 Safety and instruction........................................................................................................................9
1.4.1 Explanation of symbols ...................................................................................................... 9
1.5 Beckhoff Support and Service.........................................................................................................10
2 For your safety ........................................................................................................................................11
2.1 Safety instructions...........................................................................................................................11
2.1.1 Before operation............................................................................................................... 11
2.1.2 In operation ...................................................................................................................... 11
2.1.3 After operation.................................................................................................................. 11
3 The Beckhoff EtherCAT Terminal system ............................................................................................12
3.1 EtherCAT Bus Coupler....................................................................................................................13
3.2 EtherCAT Terminals........................................................................................................................14
3.3 E-bus...............................................................................................................................................15
3.4 Power contacts................................................................................................................................15
4 System description TwinSAFE ..............................................................................................................16
4.1 Extension of the Beckhoff I/O system with safety functions............................................................16
4.2 Safety concept ................................................................................................................................16
5 Product description ................................................................................................................................17
5.1 General description .........................................................................................................................17
5.2 Intended use ...................................................................................................................................18
5.3 Technical data.................................................................................................................................19
5.4 Safety parameters...........................................................................................................................21
5.5 Environmental conditions ................................................................................................................22
5.6 Dimensions .....................................................................................................................................23
6 Transport and storage ............................................................................................................................24
7 Installation ..............................................................................................................................................25
7.1 Safety instructions...........................................................................................................................25
7.2 Transport / storage..........................................................................................................................25
7.3 Mechanical installation ....................................................................................................................25
7.3.1 Control cabinet / terminal box .......................................................................................... 26
7.3.2 Installation position and minimum distances.................................................................... 26
7.3.3 Installation on mounting rails............................................................................................ 27
7.4 Electrical installation........................................................................................................................29
7.4.1 Connections within a Bus Terminal block ........................................................................ 29
7.4.2 Overvoltage protection ..................................................................................................... 30
7.4.3 HD housing wiring ............................................................................................................31

Table of contents
EK19144 Version: 2.0.0
7.4.4 High Density terminals ..................................................................................................... 32
7.4.5 Wire cross sections (HD) ................................................................................................. 32
7.4.6 Pin assignment................................................................................................................. 33
7.5 TwinSAFE reaction times................................................................................................................39
7.5.1 Typical reaction time ........................................................................................................ 39
7.5.2 Worst-case reaction time ................................................................................................. 40
7.6 Tested devices ................................................................................................................................41
8 Configuration of the EK1914 in TwinCAT .............................................................................................42
8.1 Inserting a Beckhoff TwinSAFE Bus Coupler..................................................................................42
8.2 Address settings on the EK1914 TwinSAFE Bus Coupler ..............................................................43
8.3 Entering a TwinSAFE address and parameters in the System Manager........................................44
8.3.1 Configuration of the EK1914 for light barriers, light grids, light curtains, etc.................... 47
8.3.2 Configuration of the EK1914 for safety switching mats.................................................... 48
9 Diagnosis .................................................................................................................................................49
9.1 Diagnosis LEDs...............................................................................................................................49
9.1.1 Diag1 (green) ................................................................................................................... 49
9.1.2 Diag2 (red) ....................................................................................................................... 50
9.2 Diagnosis objects ............................................................................................................................51
9.3 Possible causes of diagnostic messages........................................................................................53
10 Service life ...............................................................................................................................................54
11 Maintenance and cleaning .....................................................................................................................55
12 Decommissioning ...................................................................................................................................56
12.1 Disposal ..........................................................................................................................................56
12.1.1 Returning to the vendor....................................................................................................56
13 Appendix..................................................................................................................................................57
13.1 Volatility...........................................................................................................................................57
13.2 Focus of certificates ........................................................................................................................58
13.3 Certificate ........................................................................................................................................59

Notes on the documentation
EK1914 5Version: 2.0.0
1 Notes on the documentation
1.1 Disclaimer
Beckhoff products are subject to continuous further development. We reserve the right to revise the
operating instructions at any time and without prior announcement. No claims for the modification of products
that have already been supplied may be made on the basis of the data, diagrams and descriptions in these
operating instructions.
In these operating instructions we define all permissible use cases whose properties and operating
conditions we can guarantee. The use cases we define are fully tested and certified. Use cases beyond this,
which are not described in these operating instructions, require the approval of Beckhoff Automation GmbH
& Co KG.
1.1.1 Trademarks
Beckhoff®, TwinCAT®, EtherCAT®, EtherCAT G®, EtherCAT G10®, EtherCAT P®, Safety over EtherCAT®,
TwinSAFE®, XFC®, XTS® and XPlanar® are registered and licensed trademarks of Beckhoff Automation
GmbH.
The use of other brand names or designations by third parties may lead to an infringement of the rights of
the owners of the corresponding designations.
1.1.2 Patents
The EtherCAT technology is protected by patent rights through the following registrations and patents with
corresponding applications and registrations in various other countries:
• EP1590927
• EP1789857
• EP1456722
• EP2137893
• DE102015105702
EtherCAT® is a registered trademark and patented technology,
licensed by Beckhoff Automation GmbH.
Safety over EtherCAT® is a registered trademark and patented
technology, licensed by Beckhoff Automation GmbH.

Notes on the documentation
EK19146 Version: 2.0.0
1.1.3 Limitation of liability
All components in this product as described in the operating instructions are delivered in a specific
configuration of hardware and software, depending on the application regulations. Modifications and
changes to the hardware and/or software configuration that go beyond the documented options are
prohibited and nullify the liability of Beckhoff Automation GmbH & Co. KG.
The following is excluded from the liability:
• Failure to observe these operating instructions
• Improper use
• Use of untrained personnel
• Use of unauthorized spare parts
1.1.4 Copyright
© Beckhoff Automation GmbH & Co. KG, Germany.
The distribution and reproduction of this document as well as the use and communication of its contents
without express authorization are prohibited.
Offenders will be held liable for the payment of damages. All rights reserved in the event of the grant of a
patent, utility model or design.

Notes on the documentation
EK1914 7Version: 2.0.0
1.2 Version numbers
Version Comment
2.0.0 • Migration
• Editorially revised
• In chapter Technical data link to download page of certificates added
• Appendix adapted and expanded
1.3.1 • Technical data permissible air pressure extended
1.3.0 • Note on the extended temperature range added to the technical data
1.2.0 • Reliability document updated
• Safety parameters updated
• Foreword revised
1.1.2 • Reliabililty document added
• Chapter reaction times added
1.1.1 • Certificate updated
1.1.0 • Version numbers added
• Company address changed
• Description DateCode added
• HFT and classification element added
1.0.1 • Certificate added
1.0.0 • First released version
Currentness
Please check whether you are using the current and valid version of this document. The current version can
be downloaded from the Beckhoff homepage at http://www.beckhoff.de/twinsafe. In case of doubt, please
contact Technical Support (see Beckhoff Support and Service [}10]).
Origin of the document
The original documentation is written in German. All other languages are derived from the German original.
Product features
Only the product properties specified in the current operating instructions are valid. Further information given
on the product pages of the Beckhoff homepage, in emails or in other publications is not authoritative.

Notes on the documentation
EK19148 Version: 2.0.0
1.3 Staff qualification
These operating instructions are intended exclusively for trained specialists in control technology and
automation with the relevant knowledge.
The trained specialist personnel must ensure that the applications and use of the described product meet all
safety requirements. This includes all applicable and valid laws, regulations, provisions and standards.
Trained specialists
Trained specialists have extensive technical knowledge from studies, apprenticeships or technical training.
Understanding of control technology and automation is available. Trained specialists can:
• Independently identify, avoid and eliminate sources of hazard.
• Apply relevant standards and directives.
• Implement specifications from accident prevention regulations.
• Evaluate, prepare and set up the workplaces.
• Evaluate, optimize and execute work independently.

Notes on the documentation
EK1914 9Version: 2.0.0
1.4 Safety and instruction
Read the contents that refer to the activities you have to perform with the product. Always read the chapter
For your safety in the operating instructions.
Observe the warnings in the chapters so that you can handle and work with the product as intended and
safely.
1.4.1 Explanation of symbols
Various symbols are used for a clear arrangement:
1. The numbering indicates an action that should be taken.
• The bullet point indicates an enumeration.
[…] The square brackets indicate cross-references to other text passages in the document.
[1] The number in square brackets indicates the numbering of a referenced document.
1.4.1.1 Pictograms
In order to make it easier for you to find text passages, pictograms and signal words are used in warning
notices:
DANGER
Failure to observe will result in serious or fatal injuries.
WARNING
Failure to observe may result in serious or fatal injuries.
CAUTION
Failure to observe may result in minor or moderate injuries.
NOTE
Notes
Notes are used for important information on the product. The possible consequences of failure to observe
these include:
• Malfunctions of the product
• Damage to the product
• Damage to the environment
Information
This sign indicates information, tips and notes for dealing with the product or the software.

Notes on the documentation
EK191410 Version: 2.0.0
1.5 Beckhoff Support and Service
Support
Beckhoff Support offers technical advice on the use of individual Beckhoff products and system planning.
The employees support you in the programming and commissioning of sophisticated automation systems.
Hotline: +49 5246/963-157
E-mail: [email protected]
Web: www.beckhoff.com/support
Training
Training in Germany takes place in our training center at the Beckhoff headquarters in Verl, at subsidiaries
or, by arrangement, at the customer's premises.
Hotline: +49 5246/963-5000
E-mail: [email protected]
Web: www.beckhoff.com/training
Service
The Beckhoff Service Center supports you with after-sales services such as on-site service, repair service or
spare parts service.
Hotline: +49 5246/963-460
E-mail: [email protected]
Web: www.beckhoff.com/service
Download area
In the download area you can obtain product information, software updates, the TwinCAT automation
software, documentation and much more.
Web: www.beckhoff.com/download
Headquarters
Beckhoff Automation GmbH & Co. KG
Hülshorstweg 20
33415 Verl
Germany
Phone: +49 5246/963-0
E-mail: [email protected]
Web: www.beckhoff.com
For the addresses of our worldwide locations, please visit our website at Global Presence.

For your safety
EK1914 11Version: 2.0.0
2 For your safety
2.1 Safety instructions
2.1.1 Before operation
Ensure traceability
Ensure the traceability of the TwinSAFE component via the serial number.
Use in machines according to the Machinery Directive
Only use the TwinSAFE component in machines that comply with the Machinery Directive. This is how you
ensure safe operation.
Carry out commissioning test
Before commissioning, wiring faults to the sensors must be excluded. Before commissioning, carry out a
commissioning test. After a successful commissioning test, you can use the TwinSAFE component for the
intended safety-related task.
In case of wiring errors, the safety function of the product is at risk. Depending on the machine, death and
danger to life, serious bodily injury and damage to the machine may result.
Use SELV/PELV power supply
Use a SELV/PELV power supply unit with an output-side voltage limit of Umax = 36VDC to supply the
TwinSAFE component with 24VDC.
Failure to observe this will endanger the safety function of the product. Depending on the machine, death
and danger to life, serious physical injury and damage to the machine may result.
2.1.2 In operation
Interference due to emitted interference
Do not operate the following devices in the vicinity of the TwinSAFE component: for example, radio
telephones, radios, transmitters or high-frequency systems.
TwinSAFE components comply with the requirements of the applicable electromagnetic compatibility
standards with regard to interference emission and immunity. If you exceed the limits for emitted interference
specified in the standards, the function of the TwinSAFE component may be impaired.
2.1.3 After operation
De-energize and switch off components before working on them
Check all safety-relevant equipment for functionality before working on the TwinSAFE component. Secure
the working environment. Secure the machine or plant against being inadvertently started up. Observe the
chapter Decommissioning [}56].

The Beckhoff EtherCAT Terminal system
EK191412 Version: 2.0.0
3 The Beckhoff EtherCAT Terminal system
The Beckhoff EtherCAT Terminal system is used for decentralized connection of sensors and actuators to a
controller. The components of the Beckhoff EtherCAT Terminal system are mainly used in industrial
automation and building management systems. As a minimum, a bus station consists of an EtherCAT
Coupler and connected EtherCAT Terminals. The EtherCAT Coupler forms the communication interface to
the higher-level controller, while the EtherCAT Terminals form the interface to the sensors and actuators.
The whole bus station is clipped onto a 35mm DIN mounting rail (EN 60715). The mechanical link of the bus
station is established with a slot and key system on EtherCAT Couplers and EtherCAT Terminals.
The sensors and actuators are connected with the terminals via the screwless (spring-loaded) connection
system.
Fig.1: Slot and key system and screwless (spring-loaded) connection system

The Beckhoff EtherCAT Terminal system
EK1914 13Version: 2.0.0
3.1 EtherCAT Bus Coupler
Mechanical data Bus Coupler
Material polycarbonate, polyamide (PA6.6).
Dimensions (W x H x D) 44mm x 100mm x 68mm
Mounting on 35 mm mounting rail (EN60715) with locking
Attachable by double slot and key connection
Fig.2: Bus Coupler (EtherCAT)
Connection technology Bus Coupler
Wiring Spring-loaded system
Connection cross-section 0.08mm² ... 2.5mm², stranded wire, solid wire
Fieldbus connection EtherCAT
Power contacts 3 spring contacts
Current load 10A
Nominal voltage 24VDC

The Beckhoff EtherCAT Terminal system
EK191414 Version: 2.0.0
3.2 EtherCAT Terminals
Mechanical data Bus Terminal
Material polycarbonate, polyamide (PA6.6).
Dimensions (W x H x D) 12mm x 100mm x 68mm or 24mm x 100mm x 68mm
Mounting on 35 mm mounting rail (EN60715) with locking
Attachable by double slot and key connection
Fig.3: Overview of EtherCAT Terminals
Connection technology Bus Terminal
Wiring Spring-loaded system
Connection cross-section typically 0.08mm² – 2.5mm², stranded wire, solid wire
Communication E-bus
Power contacts Up to 3 blade/spring contacts
Current load 10A
Nominal voltage Depending on terminal type (typically 24 VDC)

The Beckhoff EtherCAT Terminal system
EK1914 15Version: 2.0.0
3.3 E-bus
The E-bus is the data path within a terminal strip. The E-bus is led through from the Bus Coupler through all
the terminals via six contacts on the terminals' side walls.
3.4 Power contacts
The operating voltage is passed on to following terminals via three power contacts. Terminal strip can be
split into galvanically isolated groups by means of potential supply terminals as required. The supply
terminals play no part in the control of the terminals, and can be inserted at any locations within the terminal
strip.

System description TwinSAFE
EK191416 Version: 2.0.0
4 System description TwinSAFE
4.1 Extension of the Beckhoff I/O system with safety
functions
The TwinSAFE products from Beckhoff enable convenient expansion of the Beckhoff I/O system with safety
components, and integration of all the cabling for the safety circuit within the existing fieldbus cable. Safe
signals can be mixed with standard signals as required. The transfer of safety-related TwinSAFE telegrams
is handled by the standard controller. Maintenance is simplified significantly thanks to faster diagnosis and
simple replacement of components.
The following basic functionalities are included in the TwinSAFE components:
digital inputs (e.g. EL19xx, EP1908), digital outputs (e.g. EL29xx), drive components (e.g. AX5805) and logic
units (e.g. EL6900, EL6910). For a large number of applications, the complete safety sensor and actuator
technology can be wired on these components. The required logical link of the inputs and the outputs is
handled by the EL69xx. In addition to Boolean operations, the EL6910 now also enables analog operations.
4.2 Safety concept
TwinSAFE: Safety and I/O technology in one system
• Extension of the familiar Beckhoff I/O system with TwinSAFE components
• Safe and non-safe components can be combined as required
• Logical link of the I/Os in the EL69xx TwinSAFE logic terminal
• Suitable for applications up to SIL3 according to EN61508:2010 and Cat4, PLe according to
DINENISO13849-1:2008
• Safety-relevant networking of machines via bus systems
• In the event of an error, all TwinSAFE components always switch to the wattless and therefore safe
state
• No safety requirements for the higher-level standard TwinCAT system
Safety over EtherCAT protocol (FSoE)
• Transfer of safety-relevant data via any media (“genuine black channel”)
• TwinSAFE communication via fieldbus systems such as EtherCAT, Lightbus, PROFIBUS, PROFINET
or Ethernet
• IEC 61508:2010 SIL 3 compliant
• FSoE is IEC standard (IEC 61784-3-12) and ETG standard (ETG.5100)
Fail-safe principle (fail stop)
The basic rule for a safety system such as TwinSAFE is that failure of a part, a system component or the
overall system must never lead to a dangerous condition. The safe state is always the switched off and
wattless state.
CAUTION
Safe state
For all TwinSAFE components the safe state is always the switched-off, wattless state.

Product description
EK1914 17Version: 2.0.0
5 Product description
5.1 General description
EK1914 - TwinSAFE Bus Coupler with two fail-safe inputs and two fail-safe outputs
The EK1914 is an EtherCAT Bus Coupler with 4 standard inputs, 4 standard outputs, and 2 fail-safe inputs
and 2 fail-safe outputs.
The EK1914 fulfils the requirements of DIN EN ISO 13849-1:2008 (Cat 4, PL e).
The TwinSAFE Bus Coupler has the usual design of an EtherCAT coupler.
Fig.4: EK1914 overview

Product description
EK191418 Version: 2.0.0
5.2 Intended use
WARNING
Caution - Risk of injury!
The TwinSAFE compact controller may only be used for the purposes described below!
The EK1914 TwinSAFE Bus Coupler expands the application area of the Beckhoff Bus Terminal system by
functions that enable it to be used in the field of machine safety as well. The TwinSAFE Bus Coupler is
designed for machine safety functions and directly associated industrial automation tasks. They are therefore
only approved for applications with a defined fail-safe state. This safe state is the wattless state. Fail-safety
according to the relevant standards is required.
The TwinSAFE Bus Coupler permits the connection of
• 24 VDC sensors such as
emergency off push-button switches, rope pull switches, position switches, two-hand switches, safety
switching mats, light curtains, light barriers, laser scanner, etc.
• 24 VDC actuators such as
contactors, protective door switches with tumbler, signal lamps, servo drives, etc.
NOTE
Test pulses
When selecting actuators, please ensure that the EK1914 test pulses do not lead to actuator switching or a
diagnostic message from the EK1914.
This module is suitable for operation in an EtherCAT network and can be extended by EtherCAT Terminals
of the type ELxxxx.
CAUTION
Follow the machinery directive
The TwinSAFE Bus Coupler may only be used in machines in accordance with the machinery directive.
CAUTION
Ensure traceability
The buyer has to ensure the traceability of the device via the serial number.

Product description
EK1914 19Version: 2.0.0
5.3 Technical data
The current certificates of all TwinSAFE products with the underlying standards and directives can be found
at https://www.beckhoff.com/en-en/support/download-finder/certificates-approvals/.
Data Comment
• Task within the EtherCAT
system
Coupling of EtherCAT Terminals
(ELxxxx) to 100BASE-TX
EtherCAT networks
• Protocol / Baud rate EtherCAT Device Protocol / 100
MBaud
• Cable length between two Bus
Couplers
max. 100 m 100BASE-TX
• Transmission medium at least Ethernet CAT-5 cable
• Bus connection 2 x RJ45
• Supply voltage for the EK1914
(PELV)
24 VDC (–15% / +20%)
• Number of standard inputs 4
• Number of standard outputs 4
• Number of safe inputs 2
• Number of safe outputs 2
• Status display 16 LEDs
• Reaction time typical: 4 ms,
max.: see error reaction time
Read input/write to E-bus
• Error reaction time ≤ watchdog time
• Signal voltage “0”, standard
inputs
-3 V - 5 V EN 61131-2, type 1/3
• Signal voltage “1”, standard
inputs
11 V - 30 V EN 61131-2, type 3
• Input filter of standard inputs 500 µs
• Input current of standard inputs typical 3 mA EN 61131-2, type 3
• Output current per standard
output
max. 0,5A
• Output current of the clock
outputs
typical 10 mA,
max. 15 mA
• Output current per safe output max. 500 mA,
min. 20 mA
• Actuators When selecting actuators please
ensure that the test pulses from
the safe outputs do not lead to
actuator switching
• Cable length
between
sensor/
actuator and
Bus Coupler
unshielded max. 100 m
(at 0,75 or 1 mm²)
shielded max. 100 m
(at 0,75 or 1 mm²)
• Input process image 8 byte
• Output process image 8 byte
• E-bus power supply (5 V) max. 500 mA In case of higher current consumption,
use additional EL9410 power feed
terminals.
• Power contacts (PELV) max. 24VDC, max. 4A

Product description
EK191420 Version: 2.0.0
Data Comment
• Current consumption typical 72 mA Excluding current consumption of the
sensors/actuators and further
terminals on the E-bus.
• Power loss of the Bus Coupler typical 1,8 W Without connected sensors/actuators
• Electrical isolation channels No Between the channels
• Electrical isolation E-bus No Between the channels and the E-bus
• Electrical isolation EtherCAT Yes Between the EtherCAT connections
and the channels/E-bus
• Insulation voltage Insulation tested with 500 VDC Between the EtherCAT connections
and the channels/E-bus, under
common operating conditions
• Dimensions (W x H x D) approx. 44 mm x 100 mm x 68
mm
For further information see
Dimensions [}23].
• Weight approx. 123 g
Table of contents
Other Beckhoff Portable Generator manuals
Popular Portable Generator manuals by other brands
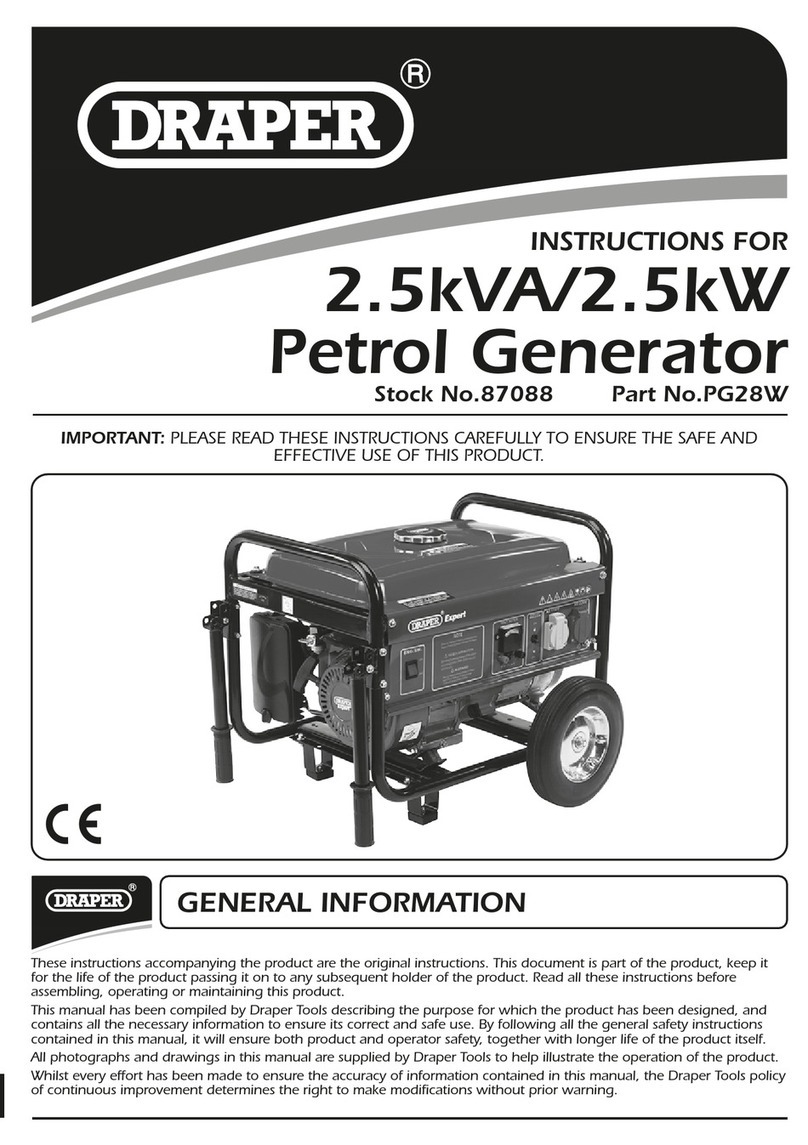
Draper
Draper PG28W instructions
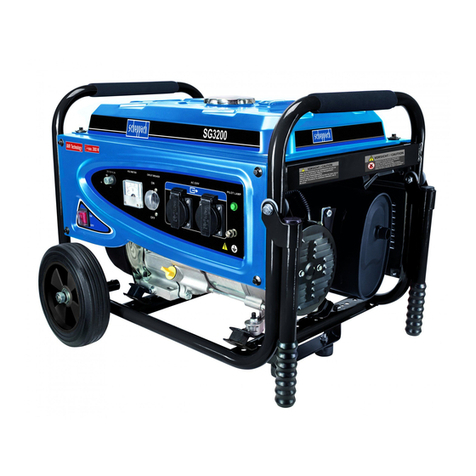
Scheppach
Scheppach SG3200 Translation of original instruction manual
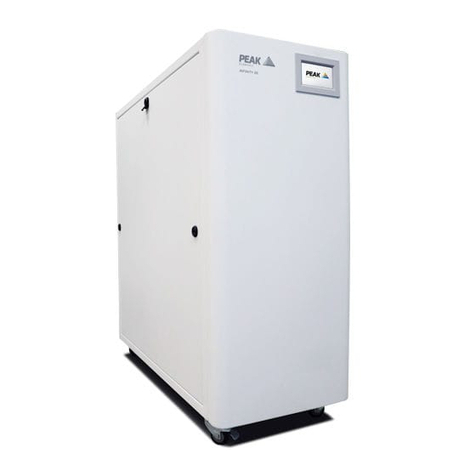
Peak Scientific
Peak Scientific Infinity XE 60 Series installation guide
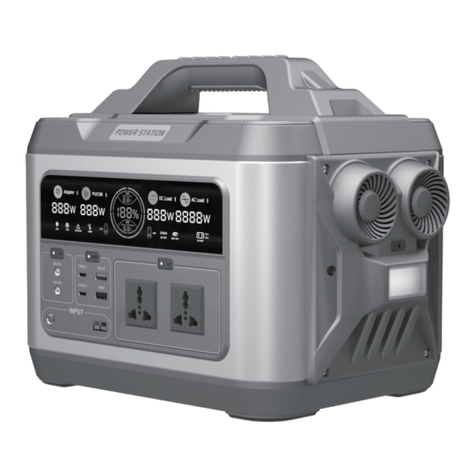
LIPOWER
LIPOWER M1200 user manual
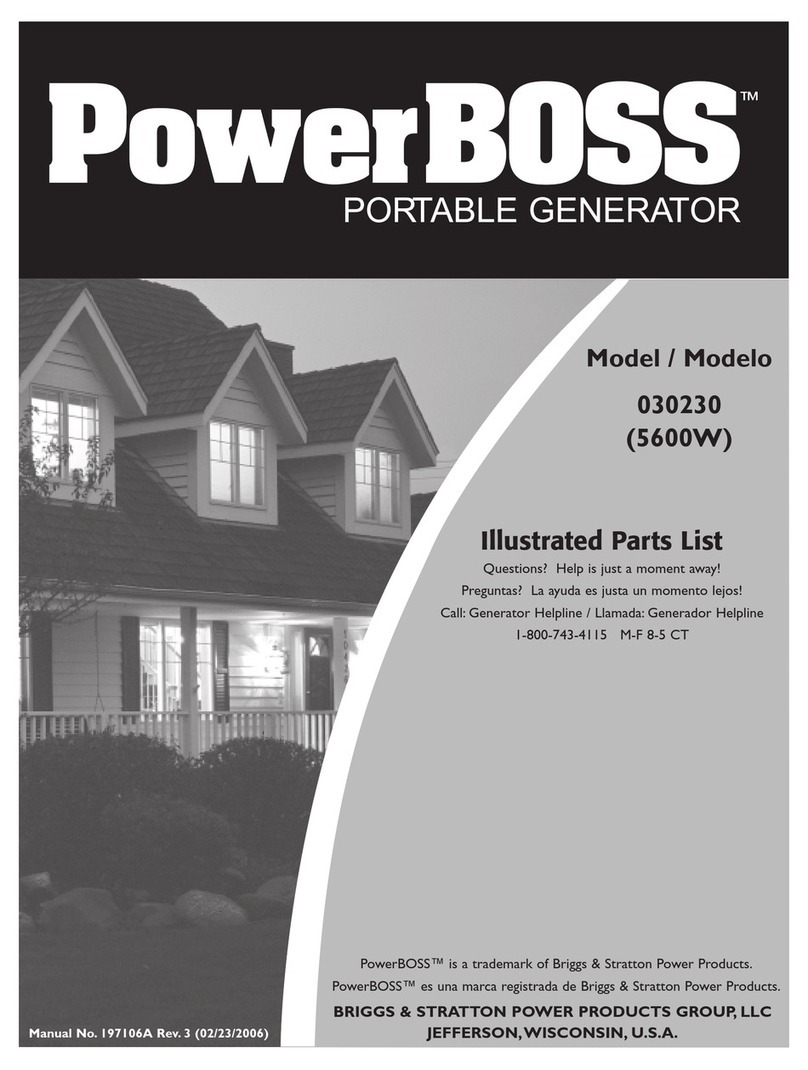
Briggs & Stratton
Briggs & Stratton 30230 Illustrated parts list
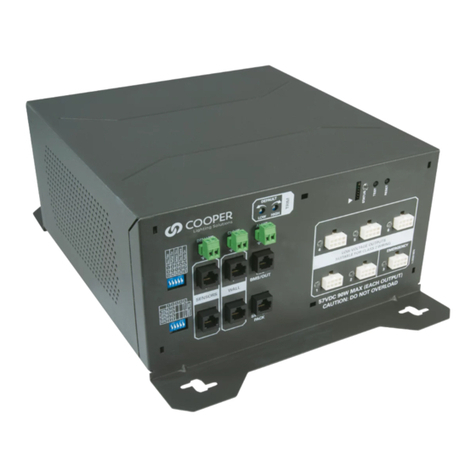
Cooper Lighting Solutions
Cooper Lighting Solutions DLVP quick start guide