Beckhoff EP1957-0022 User manual

Operating Instructions | EN
EP1957-0022 and EP1957-2222
TwinSAFE EtherCAT Box with 8 fail-safe inputs and 4 fail-safe outputs
2023-03-07 | Version: 2.0.0


Table of contents
EP1957-0022 and EP1957-2222 3Version: 2.0.0
Table of contents
1 Notes on the documentation....................................................................................................................5
1.1 Disclaimer..........................................................................................................................................5
1.1.1 Trademarks........................................................................................................................5
1.1.2 Patents...............................................................................................................................5
1.1.3 Limitation of liability............................................................................................................6
1.1.4 Copyright............................................................................................................................6
1.2 Documentation issue status ..............................................................................................................7
1.3 Version history of the TwinSAFE product .........................................................................................8
1.4 Staff qualification...............................................................................................................................8
1.5 Safety and instruction........................................................................................................................9
1.5.1 Explanation of symbols ......................................................................................................9
1.6 Beckhoff Support and Service.........................................................................................................10
2 For your safety ........................................................................................................................................11
2.1 Duty of care.....................................................................................................................................11
2.2 Safety image signs..........................................................................................................................12
2.3 General safety instructions..............................................................................................................13
2.3.1 Before operation...............................................................................................................13
2.3.2 In operation ......................................................................................................................13
2.3.3 After operation..................................................................................................................13
3 System description .................................................................................................................................14
3.1 EtherCAT Box Modules...................................................................................................................14
4 Product description ................................................................................................................................15
4.1 EP1957-0022 and EP1957-2222 ....................................................................................................15
4.2 Intended use ...................................................................................................................................16
4.3 Technical data.................................................................................................................................18
4.4 Safety parameters...........................................................................................................................19
4.5 Safe inputs and outputs ..................................................................................................................19
4.6 Dimensions .....................................................................................................................................20
5 Operation .................................................................................................................................................21
5.1 Environmental conditions ................................................................................................................21
5.2 Installation .......................................................................................................................................21
5.2.1 Fixing................................................................................................................................21
5.2.2 Connection.......................................................................................................................22
5.2.3 Temperature measurement..............................................................................................29
5.2.4 Signal cables....................................................................................................................30
5.3 Configuration of the EtherCAT Box in TwinCAT .............................................................................32
5.3.1 Adding an EtherCAT device.............................................................................................32
5.3.2 Adding an EP1957 ...........................................................................................................32
5.3.3 EP1957-0022: using the integrated TwinSAFE Logic functions.......................................32
5.3.4 Address settings on the TwinSAFE EtherCAT Box..........................................................34
5.3.5 Alias devices ....................................................................................................................35
5.3.6 EP1957 parameters .........................................................................................................37
5.3.7 Process image of the EP1957..........................................................................................41

Table of contents
EP1957-0022 and EP1957-22224 Version: 2.0.0
5.4 TwinSAFE reaction times................................................................................................................43
5.5 Diagnosis ........................................................................................................................................45
5.5.1 EtherCAT- Fieldbus LEDs................................................................................................45
5.5.2 Status LEDs .....................................................................................................................46
5.5.3 Diagnostic LEDs...............................................................................................................48
5.5.4 Flash code display ...........................................................................................................49
6 Service life ...............................................................................................................................................50
7 Maintenance and cleaning .....................................................................................................................51
8 Decommissioning ...................................................................................................................................52
8.1 Disposal ..........................................................................................................................................52
8.1.1 Returning to the vendor....................................................................................................52
9 Appendix..................................................................................................................................................53
9.1 Protection classes according to IP code .........................................................................................53
9.2 Volatility...........................................................................................................................................54
9.3 Focus of certificates ........................................................................................................................55
9.4 Certificate ........................................................................................................................................56

Notes on the documentation
EP1957-0022 and EP1957-2222 5Version: 2.0.0
1 Notes on the documentation
1.1 Disclaimer
Beckhoff products are subject to continuous further development. We reserve the right to revise the
operating instructions at any time and without prior announcement. No claims for the modification of products
that have already been supplied may be made on the basis of the data, diagrams and descriptions in these
operating instructions.
In these operating instructions we define all permissible use cases whose properties and operating
conditions we can guarantee. The use cases we define are fully tested and certified. Use cases beyond this,
which are not described in these operating instructions, require the approval of Beckhoff Automation GmbH
& Co KG.
1.1.1 Trademarks
Beckhoff®, TwinCAT®, EtherCAT®, EtherCAT G®, EtherCAT G10®, EtherCAT P®, Safety over EtherCAT®,
TwinSAFE®, XFC®, XTS® and XPlanar® are registered and licensed trademarks of Beckhoff Automation
GmbH.
The use of other brand names or designations by third parties may lead to an infringement of the rights of
the owners of the corresponding designations.
1.1.2 Patents
The EtherCAT technology is protected by patent rights through the following registrations and patents with
corresponding applications and registrations in various other countries:
• EP1590927
• EP1789857
• EP1456722
• EP2137893
• DE102015105702
EtherCAT® is a registered trademark and patented technology,
licensed by Beckhoff Automation GmbH.
Safety over EtherCAT® is a registered trademark and patented
technology, licensed by Beckhoff Automation GmbH.

Notes on the documentation
EP1957-0022 and EP1957-22226 Version: 2.0.0
1.1.3 Limitation of liability
All components in this product as described in the operating instructions are delivered in a specific
configuration of hardware and software, depending on the application regulations. Modifications and
changes to the hardware and/or software configuration that go beyond the documented options are
prohibited and nullify the liability of Beckhoff Automation GmbH & Co. KG.
The following is excluded from the liability:
• Failure to observe these operating instructions
• Improper use
• Use of untrained personnel
• Use of unauthorized spare parts
1.1.4 Copyright
© Beckhoff Automation GmbH & Co. KG, Germany.
The distribution and reproduction of this document as well as the use and communication of its contents
without express authorization are prohibited.
Offenders will be held liable for the payment of damages. All rights reserved in the event of the grant of a
patent, utility model or design.

Notes on the documentation
EP1957-0022 and EP1957-2222 7Version: 2.0.0
1.2 Documentation issue status
Version Comment
2.0.0 • Foreword changed to Notes on the documentation [}5] and For your safety [}11]
•Service life [}50] moved
•Maintenance and cleaning [}51] and Decommissioning [}52] adapted
• Appendix adapted and expanded
1.2.1 • Typo in Technical data [}18] corrected
1.2.0 • In chapter Technical data [}18] link to download page of certificates added
• Chapter "Firmware update of TwinSAFE products" removed
• I/O component EP1957-2222 added as variant of EP1957-0022
• Chapter Project design limits of EP1957 [}33] moved
• Figure labels changed
1.1.0 • Project design limits added
1.0.0 • First release
• Dimensioning updated
• Certificate added
0.5.0 • Dimensions of the EP1957 updated in the text
0.4.0 • Revision following review
0.3.0 • Diagrams updated
• Description of Module Fault Link active parameter added
0.2.0 • Parameter descriptions expanded
• Technical data updated
• EN81-20, EN81-22 and EN81-50 notes added
0.0.1 • First draft
Currentness
Please check whether you are using the current and valid version of this document. The current version can
be downloaded from the Beckhoff homepage at http://www.beckhoff.de/twinsafe. In case of doubt, please
contact Technical Support (see Beckhoff Support and Service [}10]).
Origin of the document
The original documentation is written in German. All other languages are derived from the German original.
Product features
Only the product properties specified in the current operating instructions are valid. Further information given
on the product pages of the Beckhoff homepage, in emails or in other publications is not authoritative.

Notes on the documentation
EP1957-0022 and EP1957-22228 Version: 2.0.0
1.3 Version history of the TwinSAFE product
This version history lists the software and hardware version numbers. A description of the changes
compared to the previous version is also given.
Updated hardware and software
TwinSAFE products are subject to a cyclical revision. We reserve the right to revise and change the
TwinSAFE products at any time and without prior notice.
No claims for changes to products already delivered can be asserted from these hardware and/or
software changes.
Date Software ver-
sion
Hardware
version
Modifications
First release of the EP1957-2222
31/07/2018 01 00 First release of the EP1957-0022
1.4 Staff qualification
These operating instructions are intended exclusively for trained specialists in control technology and
automation with the relevant knowledge.
The trained specialist personnel must ensure that the applications and use of the described product meet all
safety requirements. This includes all applicable and valid laws, regulations, provisions and standards.
Trained specialists
Trained specialists have extensive technical knowledge from studies, apprenticeships or technical training.
Understanding of control technology and automation is available. Trained specialists can:
• Independently identify, avoid and eliminate sources of hazard.
• Apply relevant standards and directives.
• Implement specifications from accident prevention regulations.
• Evaluate, prepare and set up the workplaces.
• Evaluate, optimize and execute work independently.

Notes on the documentation
EP1957-0022 and EP1957-2222 9Version: 2.0.0
1.5 Safety and instruction
Read the contents that refer to the activities you have to perform with the product. Always read the chapter
For your safety [}11] in the operating instructions.
Observe the warnings in the chapters so that you can handle and work with the product as intended and
safely.
1.5.1 Explanation of symbols
Various symbols are used for a clear arrangement:
1. The numbering indicates an action that should be taken.
• The bullet point indicates an enumeration.
[…] The square brackets indicate cross-references to other text passages in the document.
[1] The number in square brackets indicates the numbering of a referenced document.
1.5.1.1 Pictograms
In order to make it easier for you to find text passages, pictograms and signal words are used in warning
notices:
DANGER
Failure to observe will result in serious or fatal injuries.
WARNING
Failure to observe may result in serious or fatal injuries.
CAUTION
Failure to observe may result in minor or moderate injuries.
NOTE
Notes
Notes are used for important information on the product. The possible consequences of failure to observe
these include:
• Malfunctions of the product
• Damage to the product
• Damage to the environment
Information
This sign indicates information, tips and notes for dealing with the product or the software.

Notes on the documentation
EP1957-0022 and EP1957-222210 Version: 2.0.0
1.6 Beckhoff Support and Service
Support
Beckhoff Support offers technical advice on the use of individual Beckhoff products and system planning.
The employees support you in the programming and commissioning of sophisticated automation systems.
Hotline: +49 5246/963-157
E-mail: [email protected]
Web: www.beckhoff.com/support
Training
Training in Germany takes place in our training center at the Beckhoff headquarters in Verl, at subsidiaries
or, by arrangement, at the customer's premises.
Hotline: +49 5246/963-5000
E-mail: [email protected]
Web: www.beckhoff.com/training
Service
The Beckhoff Service Center supports you with after-sales services such as on-site service, repair service or
spare parts service.
Hotline: +49 5246/963-460
E-mail: [email protected]
Web: www.beckhoff.com/service
Download area
In the download area you can obtain product information, software updates, the TwinCAT automation
software, documentation and much more.
Web: www.beckhoff.com/download
Headquarters
Beckhoff Automation GmbH & Co. KG
Hülshorstweg 20
33415 Verl
Germany
Phone: +49 5246/963-0
E-mail: [email protected]
Web: www.beckhoff.com
For the addresses of our worldwide locations, please visit our website at Global Presence.

For your safety
EP1957-0022 and EP1957-2222 11Version: 2.0.0
2 For your safety
Read this chapter containing general safety information. In addition, always observe the safety instructions
and warnings in these operating instructions for your own safety, the safety of other persons and the safety
of the product.
When working with control and automation products, many dangers can result from careless or incorrect use.
Work particularly thoroughly, not under time pressure and responsibly towards other people.
2.1 Duty of care
Read entire documentation for TwinSAFE component
• TwinSAFE application manual
• EL6910 TwinSAFE logic terminal operating manual
• TwinSAFE Logic FB documentation manual
The operator must comply with all the requirements and notes specified in these operating instructions in
order to fulfill his duty of care. This includes in particular that you
• comply with the provisions defined in the chapter Limitation of liability [}6].
• only operate the TwinSAFE component when it is in perfect working order.
• provide the operating instructions in a legible condition and complete at the place of use of the
TwinSAFE component.
• do not remove the safety markings attached to the TwinSAFE component and maintain their legibility.
No disposal in domestic waste
Products marked with a crossed-out waste bin must not be disposed of with domestic
waste. The device is considered waste electrical and electronic equipment when it is
disposed of. Observe the national regulations for the disposal of waste electrical and
electronic equipment.

For your safety
EP1957-0022 and EP1957-222212 Version: 2.0.0
2.2 Safety image signs
On Beckhoff products you will find attached or lasered safety pictograms, which vary depending on the
product. They serve to serve to ensure safety for people and to prevent damage to the products. Safety
pictograms must not be removed and must be legible for the user.
Read and observe the operating instructions
Commissioning is only permitted if the operating instructions have been read and understood
beforehand. This applies in particular to the safety instructions and warnings.
Electrostatic sensitive components
Work with and on the TwinSAFE component is only permitted in protected workplaces.

For your safety
EP1957-0022 and EP1957-2222 13Version: 2.0.0
2.3 General safety instructions
2.3.1 Before operation
Use in machines according to the Machinery Directive
Only use the TwinSAFE component in machines that comply with the Machinery Directive. This is how you
ensure safe operation.
Ensure traceability
Ensure the traceability of the TwinSAFE component via the serial number.
Use SELV/PELV power supply
Use a SELV/PELV power supply unit with an output-side voltage limit of Umax = 36VDC to supply the
TwinSAFE component with 24VDC.
Failure to observe this will endanger the safety function of the product. Depending on the machine, death
and danger to life, serious physical injury and damage to the machine may result.
Carry out commissioning test
Before commissioning, wiring faults to the sensors must be excluded. Before commissioning, carry out a
commissioning test. After a successful commissioning test, you can use the TwinSAFE component for the
intended safety-related task.
In case of wiring errors, the safety function of the product is at risk. Depending on the machine, death and
danger to life, serious bodily injury and damage to the machine may result.
Use permitted engineering tools and procedures
The TÜV SÜD certificate applies to the TwinSAFE component, the function blocks available in it, the
documentation and the engineering tool. TwinCAT 3.1 and the TwinSAFE Loader are permitted as
engineering tools.
Procedures or engineering tools deviating from this are not covered by the certificate. This applies in
particular to externally generated xml files for the TwinSAFE import.
2.3.2 In operation
Interference due to emitted interference
Do not operate the following devices in the vicinity of the TwinSAFE component: for example, radio
telephones, radios, transmitters or high-frequency systems.
TwinSAFE components comply with the requirements of the applicable electromagnetic compatibility
standards with regard to interference emission and immunity. If you exceed the limits for emitted interference
specified in the standards, the function of the TwinSAFE component may be impaired.
2.3.3 After operation
De-energize and switch off components before working on them
Check all safety-relevant equipment for functionality before working on the TwinSAFE component. Secure
the working environment. Secure the machine or plant against being inadvertently started up. Observe the
chapter Decommissioning [}52].

System description
EP1957-0022 and EP1957-222214 Version: 2.0.0
3 System description
3.1 EtherCAT Box Modules
The EtherCAT system has been extended with EtherCAT Box modules with protection class IP67. Through
the integrated EtherCAT interface the modules can be connected directly to an EtherCAT network without an
additional Coupler Box. The high-performance of EtherCAT is thus maintained into each module.
The extremely low dimensions of only e.g.126x30x26.5mm are identical to those of the Fieldbus Box
extension modules. They are thus particularly suitable for use where space is at a premium. The small mass
of the EtherCAT modules facilitates applications with mobile I/O interface (e.g. on a robot arm). The
EtherCAT connection is established via screened M8 connectors.
Fig.1: EtherCAT Box modules extend the EtherCAT system with IP67 protection
The robust design of the EtherCAT Box modules enables them to be used directly at the machine. Control
cabinets and terminal boxes are now no longer required. The modules are fully sealed and therefore ideally
prepared for wet, dirty or dusty conditions.
Pre-assembled cables significantly simplify EtherCAT and signal wiring. Very few wiring errors are made, so
that commissioning is optimized. In addition to pre-assembled EtherCAT, power and sensor cables, field-
configurable connectors and cables are available for maximum flexibility. Depending on the application, the
sensors and actuators are connected through M8 or M12 connectors.
Basic EtherCAT documentation
You will find a detailed description of the EtherCAT system in the Basic System Documentation for
EtherCAT, which is available for download from our website (www.beckhoff.com) under Downloads.

Product description
EP1957-0022 and EP1957-2222 15Version: 2.0.0
4 Product description
4.1 EP1957-0022 and EP1957-2222
The EP1957 is an EtherCAT Box with digital inputs for 24VDC encoders or for potential-free contacts, with
digital outputs for 24VDC actuators. The EtherCAT Box has 8 fail-safe inputs and 4 fail-safe outputs.
With a two-channel connection, the EP1957 meets the requirements of EN61508-1:2010SIL3 and
ENISO13849-1:2015(Cat4, PLe), see chapter Safe inputs and outputs [}19].
Fig.2: Connection diagram
The control voltage US supplies the module electronics.
The clock outputs / sensor supply voltage (parameterizable) and the safe outputs are supplied from the field
voltage UP.
The TwinSAFE EtherCAT Box has the typical design of an EtherCAT Box with 60mm width.

Product description
EP1957-0022 and EP1957-222216 Version: 2.0.0
EP1957 variants
The EP1957 has an integrated safety control that can be used for user-specific applications directly
on the component. The variant EP1957-2222 does not have this functionality and represents a pure
I/O component.
4.2 Intended use
WARNING
Caution - Risk of injury!
TwinSAFE components shall only be used for the purposes described below!
The TwinSAFE EtherCAT Box expands the application range of the Beckhoff system with functions that
enable it to be used for machine safety applications. The TwinSAFE Boxes are designed for machine safety
functions and directly associated industrial automation tasks. They are therefore only approved for
applications with a defined fail-safe state. This safe state is the wattless state. Fail-safety according to the
relevant standards is required.
The TwinSAFE EtherCAT Box allows the connection of:
24VDC sensors such as
• emergency stop push buttons, pull cord switches, position switches, two-hand switches, safety mats,
light curtains, light barriers, laser scanners etc.
• Safe sensors, which use a 24VDC supply and send safe OSSD signals.
24VDC actuators such as
• Contactors, protective door switches with tumblers, valves etc.
WARNING
The fail-safe principle!
The basic rule for a safety system such as TwinSAFE is that failure of a part, a system component or the
overall system must never lead to a dangerous condition. The safe state is always the switched off and
wattless state.
WARNING
System limits
The TÜV SÜD certificate applies to this TwinSAFE component, the function blocks available in it, the
documentation and the engineering tool. TwinCAT 3.1 and the TwinSAFE Loader are permitted as
engineering tools. Any deviations from these procedures or tools, particularly externally generated xml files
for TwinSAFE import or externally generated automatic project creation procedures, are not covered by the
certificate.
WARNING
Power supply from SELV/PELV power supply unit!
The TwinSAFE components must be supplied with 24VDC by an SELV/PELV power supply unit with an
output voltage limit Umax of 36VDC. Failure to observe this can result in a loss of safety.
WARNING
Commissioning test
Before the EP1957 can be used for the safety task, the user must carry out a commissioning test so that
sensor and actuator wiring errors can be ruled out.
CAUTION
Follow the machinery directive!
The TwinSAFE components shall only be used in machines as defined in the machinery directive.

Product description
EP1957-0022 and EP1957-2222 17Version: 2.0.0
CAUTION
Ensure traceability!
The buyer has to ensure the traceability of the device via the serial number.
CAUTION
Note on approval according to EN 81-20, EN 81-22 and EN 81-50
• The release does not apply to the EL1918-2200, EL2911-2200 and EP1957-2222 variants.
• The TwinSAFE components may only be used in machines that have been designed and installed in
accordance with the requirements of the EN60204-1 standard.
• Provide a surge filter for the supply voltage of the TwinSAFE components against overvoltages
(reduction to overvoltage category II).
• EN81 requires that in the case of devices with internal temperature monitoring, a stop must be reached
in the event of an overtemperature. In this case, passengers must be able to disembark (see EN81-20
chapter 5.10.4.3, for example). To ensure this, application measures are necessary. The internal
terminal temperature of the TwinSAFE components can be read out by the user. A direct switch-off
occurs at the maximum permissible temperature of the respective TwinSAFE component (see chapter
Temperature measurement).
The user must select a temperature threshold below the maximum temperature such that a stop can be
reached in all cases before the maximum temperature is reached. Information on the optimum terminal
configuration can be found under Notes on the arrangement of TwinSAFE components and under
Example configuration for temperature measurement.
• For the use of the TwinSAFE components according to EN81-22 and EN81-50, the conditions
described in the manuals for achieving category4 according to ENISO13849-1:2015 must be
observed.
• The use of TwinSAFE components is limited to indoor applications.
• Basic protection against direct contact must be provided, either by fulfilling protection class IP2X or by
installing the TwinSAFE components in a control cabinet which corresponds at least to protection class
IP54 according to EN60529.
• The ambient conditions regarding temperature, humidity, heat dissipation, EMC and vibrations, as
specified in the operating instructions under technical data, must be observed.
• The operating conditions in potentially explosive atmospheres (ATEX) are specified in the operating
instructions.
• The safe state (triggering) of the application must be the de-energized state. The safe state of the
TwinSAFE components is always the de-energized, switched-off state, and this cannot be changed.
• The service life specified in the operating instructions must be observed.
• If the TwinSAFE component is operated outside the permissible temperature range, it changes to
"Global Shutdown" state.
• The TwinSAFE components must be installed in a control cabinet with protection class IP54 according to
EN60529, so that the requirement for degree of pollution3 according to EN60664-1 can be reduced to
level2.
• The TwinSAFE components must be supplied by a SELV/PELV power supply unit with a maximum
voltage of Umax≤36VDC.

Product description
EP1957-0022 and EP1957-222218 Version: 2.0.0
4.3 Technical data
The current certificates of all TwinSAFE products with the underlying standards and directives can be found
at https://www.beckhoff.com/en-en/support/download-finder/certificates-approvals/.
Product designation EP1957-0022 and EP1957-2222
Fieldbus EtherCAT
Number of inputs 8
Number of outputs 4
Input and output connections M12
Status display 12 (one green LED per input/output) + 5 diagnostic LEDs + 2 LEDs
for Us/Up + 2 LEDs for EtherCAT link/act
Response time
(read input/write to E-bus)
typical: 4ms (in default setting without local TwinSAFE logic),
maximum: see fault reaction time
Watchdog time adjustable from 2ms to 60s
Fault reaction time ≤ watchdog time
Cable length between sensor and EtherCAT Box Unshielded: max. 100m (0.75 or 1mm²)
Shielded: max. 100m (0.75 or 1mm²)
Output current of the clock outputs
(Input Power Mode parameter: diag test pulse)
typically 10mA
Output current of sensor supply
(Input Power Mode parameter: PowerMode A/B)
max. 250mA
Max. output current clock outputs/sensor supply in the event of
an error
max. 3A (the duration depends on the overtemperature-related
shutdown of the output driver)
Safe outputs max. 0.5A per channel
Diagnostic thresholds:
>4.7V -> high signal is detected
<1.0V -> low signal is detected
Input process image 7bytes
Output process image 7bytes
Supply voltage for the EP1957 24VDC (–15%/+20%)
Current consumption US
(wired with 8 potential-free contacts and 4 outputs)
12 channels occupied: typically 120mA
0 channels occupied: typically 100mA
(provide 4 A fuse)
Current consumption from UP
(connected with 8 potential-free contacts and 4 actuators, without
load currents)
12 channels occupied: approx. 60mA
0 channels occupied: approx. 20mA
(provide 4 A fuse)
Power loss of the EtherCAT Box typically 4.7watts
Electrical isolation (between the channels) no
Electrical isolation (between the channels and EtherCAT) yes
Insulation voltage (between the channels and EtherCAT, under
common operating conditions)
Insulation tested with 500VDC
Dimensions (WxHxD) 60(+0.5)mmx126(+0.5)mmx26.5mm
Housing material PBT+PET (Valox 855)
Sealing compound Polyurethane
Weight approx.315g
Permissible ambient temperature (operation) -25°C to +60°C
Permissible ambient temperature (transport/storage) -40°C to +85°C
Permissible air pressure (operation/storage/transport) 750hPa to 1100hPa
(this is equivalent to an altitude of approx. -690m to 2450m above
sea level assuming an international standard atmosphere)
Inadmissible operating conditions TwinSAFE EtherCAT Boxes must not be used under the following
conditions:
• under the influence of ionizing radiation (exceeding the natural
background radiation)
• in corrosive environments
EMC immunity/emission conforms to EN61000-6-2/ EN61000-6-4
Vibration/shock resistance conforms to EN60068-2-6/ EN60068-2-27
Shocks 15g with pulse duration 11ms in all three axes
Protection rating (when screwed together) IP67 (according to EN 60529)
Correct installation position variable

Product description
EP1957-0022 and EP1957-2222 19Version: 2.0.0
Product designation EP1957-0022 and EP1957-2222
Approvals CE, TÜV SÜD
4.4 Safety parameters
Key data EP1957-0022 and EP1957-2222
Lifetime [a] 20
Proof test interval [a] not required1
PFHD6.50E-09
PFD 8.30E-05
MTTFDhigh
DC high
Performance level PL e
Category 4
HFT 1
Classification element2Type B
1. Special proof tests throughout the service life of the EtherCAT Box are not required.
2. Classification according to EN61508-2:2010 (see chapters 7.4.4.1.2 and 7.4.4.1.3)
The EtherCAT Box can be used for safety-related applications according to IEC61508:2010 up to SIL3 and
ENISO13849-1:2015 up to PLe (Cat4).
Further information on calculating or estimating the MTTFD value from the PFHD value can be found in the
TwinSAFE Application Guide or in ENISO13849-1:2015, TableK.1.
In terms of safety-related parameters, the Safety-over-EtherCAT communication is already considered with
1% of SIL3 according to the protocol specification.
4.5 Safe inputs and outputs
The safe input modules and corresponding clock outputs have a two-channel design. This has the
advantage that a two-channel safe sensor with an M12 connection can be used, and a fault such as cross-
circuit or external feed results in shutdown of the whole module.
The safe output modules have a single-channel design.
DANGER
Clocked signals inside a sheathed cable
If clocked signals (clock outputs for the safe inputs and safe outputs) of different modules are used within a
sheathed cable, a fault in one module, such as cross-circuit or external feed, must lead to the disconnection
of all these modules. This is achieved by setting the Module Fault Link active parameter for all modules
involved. This parameter is set to TRUE by default. The parameter acts separately for the input and output
modules.
DANGER
Safe inputs in Cat.4 / PL e
If two safe input channels are to be used in a category 4 structure that are not on one M12 connector,
please make sure to combine always an even and an odd channel number.

Product description
EP1957-0022 and EP1957-222220 Version: 2.0.0
4.6 Dimensions
Fig.3: Dimensions
The EtherCAT Box has the following dimensions:
Width: 60(+0.5) mm
Height: 126(+0.5) mm
Depth: 26.5 mm
When fully wired, the connected cables increase the total depth of the module.
This manual suits for next models
1
Table of contents
Other Beckhoff Portable Generator manuals
Popular Portable Generator manuals by other brands
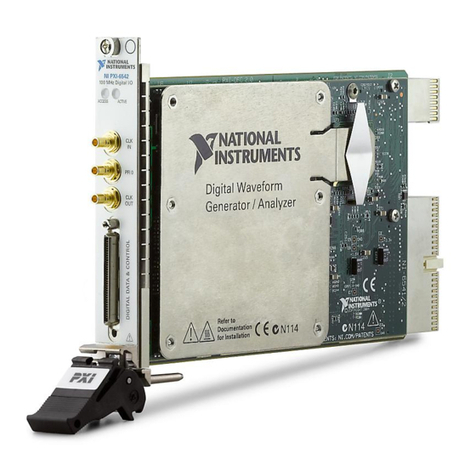
National Instruments
National Instruments NI PCI-6542 Getting started guide

Patriot
Patriot 1800 quick start guide
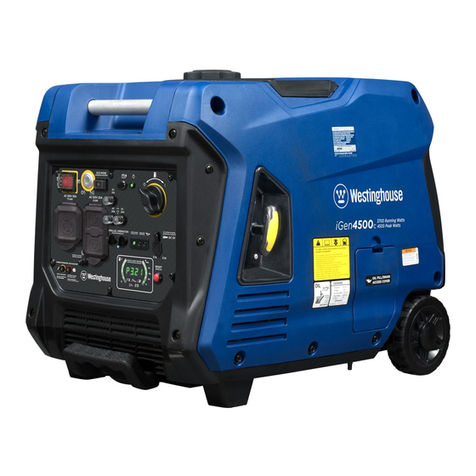
Westinghouse
Westinghouse iGen4500c user manual
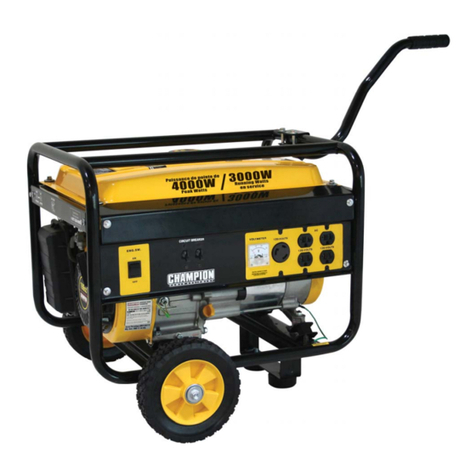
Champion Power Equipment
Champion Power Equipment CSA40037 Owner's Manual and Operating Instructions
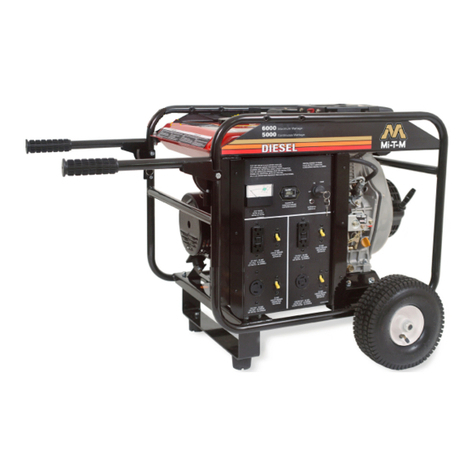
Mi-T-M
Mi-T-M GEN-6000-0MYE Operator's manual
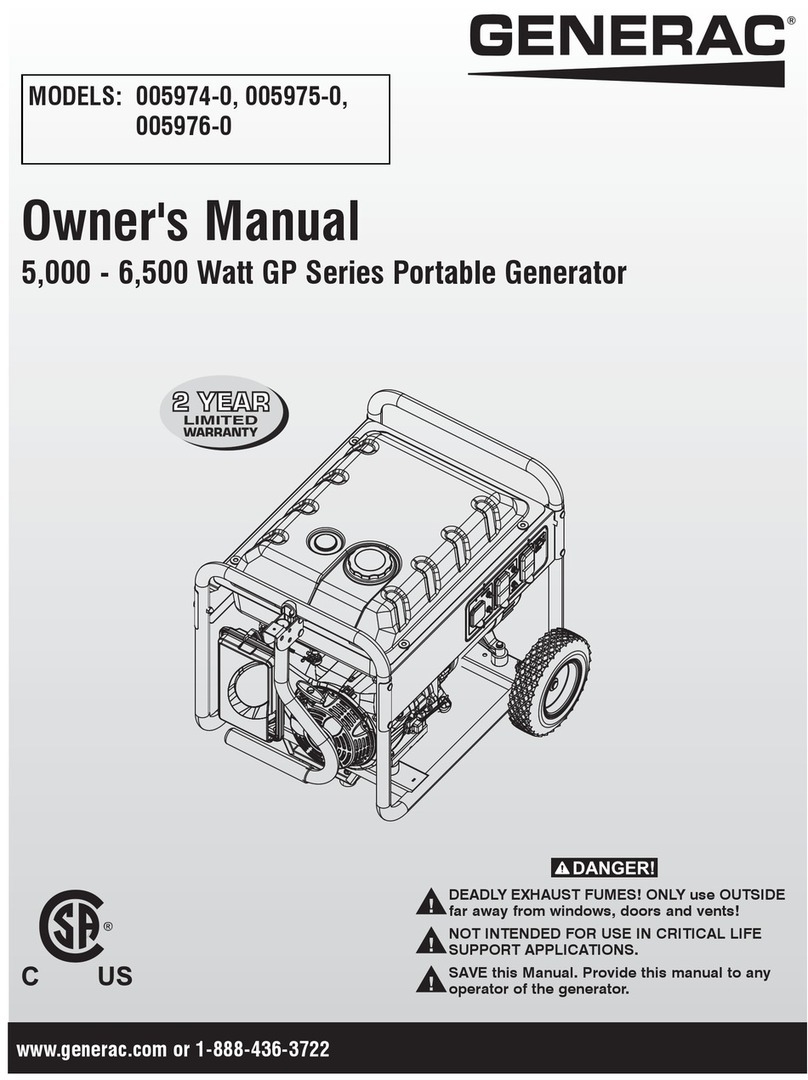
Generac Power Systems
Generac Power Systems 005975-0 owner's manual