Beijer Electronics X2 base 15 v2 HP User manual

X2base15v2HP
English
MAEN333,2021-05

Foreword
InstallationmanualforX2base15v2HP
Foreword
All operator panels are developed to satisfy the demands of human-machine
communication. Built-in functions such as displaying and controlling text,
dynamic indication, time channels, alarm and recipe handling are included.
The operator panel works primarily in an object-oriented way, making it easy to
understand and use. Configuration is carried out on a PC using iX Developer
software. The project can then be transferred and stored in the operator panel
itself.
Various types of automation equipment such as PLCs, servos or drives can be
connected to the operator panels. In this manual, the term “the controller” refers
to the connected equipment.
This manual explains how to install the operator panel. Please refer to the
iX Developer reference manual for further information.
Order no: MAEN333
Copyright © 2021-05 Beijer Electronics AB. All rights reserved.
The information in this document is subject to changewithoutnoticeandisprovidedasavailableatthe
time of printing. Beijer Electronics AB, including all its group companies, reserves the right to change any
information without updating this publication. Beijer Electronics AB, including all its group companies,
assumesnoresponsibilityforanyerrorsthatmayappearinthisdocument. Readtheentireinstallation
manual prior to installing and using this equipment. Only qualified personnel may install, operate or repair
this equipment. Beijer Electronics AB, including all its group companies, are not responsible for modified,
altered or renovated equipment. Because the equipment has a wide range of applications, users must acquire
the appropriate knowledge to use the equipment properly in their specific applications. Persons responsible
for the application and the equipment must themselves ensure that each application is in compliance with
all relevant requirements, standards and legislationinrespecttoconfigurationandsafety. Onlypartsand
accessories manufactured according to specifications set by Beijer Electronics AB, including all its group
companies, may be used.
BEIJER ELECTRONICS AB, INCLUDING ALL ITS GROUP
COMPANIES, SHALL NOT BE LIABLE TO ANYONE FOR ANY
DIRECT, INDIRECT, SPECIAL, INCIDENTAL OR CONSEQUENTIAL
DAMAGES RESULTING FROM THE INSTALLATION, USE OR
REPAIR OF THIS EQUIPMENT, WHETHER ARISING IN TORT,
CONTRACT, OR OTHERWISE. BUYER'S SOLE REMEDY SHALL
BE THE REPAIR, REPLACEMENT, OR REFUND OF PURCHASE
PRICE, AND THE CHOICE OF THE APPLICABLE REMEDY SHALL
BE AT THE SOLE DISCRETION OF BEIJER ELECTRONICS AB,
INCLUDING ALL ITS GROUP COMPANIES.
BeijerElectronics, MAEN333

Contents
Contents
1 SafetyPrecautions ....................................................... 4
1.1 General ........................................................... 4
1.2 Hazardous Materials ............................................. 4
1.3 DisposalRequirementsUnderWEEERegulations ........... 5
1.4 DuringInstallation .............................................. 5
1.5 DuringUse ....................................................... 5
1.6 Service and Maintenance ........................................ 5
1.6.1 CleaningtheDisplay ............................................ 5
1.7 Dismantling and Scrapping ..................................... 6
1.8 Appearance of Air in Touch Screen ............................. 6
2 NamingConvention .................................................... 7
3 Installation ............................................................... 8
3.1 SpaceRequirements ............................................. 8
3.2 InstallationProcess .............................................. 8
3.2.1 ConnectionstotheController ..................................10
3.2.2 OtherConnectionsandPeripherals .............................10
3.2.3 OpenPorts .......................................................10
4 TechnicalData ........................................................... 11
5 ChemicalResistance .................................................... 13
5.1 Touch Screen and Overlay Material ............................ 13
5.1.1 ProtectiveFilm ...................................................13
5.1.2 TouchScreenSurface ............................................14
5.1.3 TouchScreenProtector ..........................................14
6 OperatorPanelDrawings .............................................. 15
6.1 Connectors ....................................................... 15
6.2 X2base15v2HPOutline ....................................... 18
7 Additional Installation Tips ............................................ 19
7.1 Grounding the operator panel .................................. 19
7.2 EthernetConnectionintheOperatorPanel ................... 20
7.3 To Achieve Better EMC Protection ............................. 21
7.4 AmbientTemperature ........................................... 22
7.5 Safety ............................................................. 24
7.6 GalvanicIsolation ................................................ 25
7.7 Cable and Bus Termination RS-485 ............................ 27
7.8 USBMemorystick ............................................... 27
BeijerElectronics, MAEN333

Safety Precautions
1SafetyPrecautions
Both the installer and the owner and/or operator of the operator panel must read
and understand this installation manual.
1.1 General
•Read the safety precautions carefully.
•Check the delivery for transportation damage. If damage is found, notify the
supplier as soon as possible.
•Do not use the operator panel in an environment with high explosive hazards.
•The supplier is not responsible for modified, altered or reconstructed
equipment.
•Use only parts and accessories manufactured according to specifications of
the supplier.
•Read the installation and operating instructions carefully before installing,
using or repairing the operator panel.
•Neverallowfluids,metalfilingsorwiringdebristoenteranyopeningsinthe
operator panel. This may cause fire or electrical shock.
•Only qualified personnel may operate the operator panel.
•Storing the operator panel where the temperature is lower/higher than
recommended in this manual can cause the LCD display liquid to
congeal/become isotropic.
•The LCD display liquid contains a powerful irritant. In case of skin contact,
wash immediately with plenty of water. In case of eye contact, hold the eye
open,flushwithplentyofwaterandgetmedicalattention.
•Thefiguresinthismanualserveanillustrativepurpose. Becauseofthemany
variables associated with any particular installation, the supplier cannot
assume responsibility for actual use based on the figures.
•The supplier neither guarantees that the operator panel is suitable for your
particular application, nor assumes responsibility for your product design,
installation or operation.
•It is recommended to turn on and shut down the operator panel at least once
before installing any components/cards or before connecting the operator
panel to external devices; for example serial devices.
•For Marine panels only:
–The operator panel must be installed and operated as described in this
document to meet this certification.
–Observe precautions for handling electrostatic discharge sensitive devices
1.2 HazardousMaterials
Toxicandhazardousmaterialsorelements
有毒和有害的材料或元素
Partdescription
零件描述
Pb Hg Cd Cr6+ PBB PBDE
PCBandelectronic
components
PCB和电子元件
XOO O O O
BeijerElectronics, MAEN333 4

Safety Precautions
1.3 DisposalRequirementsUnder
WEEERegulations
For professional users in the European Union: If you wish to discard electrical
and electronic equipment (EEE), please contact your dealer or supplier for further
information.
For disposal in countries outside of the European Union: If you wish to discard
this product please contact your local authorities or dealer and ask for the correct
method of disposal.
1.4 DuringInstallation
•Install the operator panel according to the accompanying installation
instructions.
•Ground the operator panel according to the accompanying installation
instructions.
•Only qualified personnel may install the operator panel.
•Separate the high voltage, signal, and supply cables.
•Make sure that the voltage and polarity of the power source is correct before
connecting the operator panel to the power outlet.
•Peripheral equipment must be appropriate for the application and location.
1.5 DuringUse
•Keep the operator panel clean.
•Emergency stop and other safety functions may not be controlled from the
operator panel.
•Do not use excessive force or sharp objects when operating the touch screen.
1.6 ServiceandMaintenance
•Only qualified personnel should carry out repairs.
•The agreed warranty applies.
•Before carrying out any cleaning or maintenance operations, disconnect the
equipment from the electrical supply.
•Clean the display and surrounding front cover with a soft cloth and mild
detergent.
1.6.1 CleaningtheDisplay
We recommend using a dry, clean cloth to wipe off dust regularly. Use alcohol or
ammonia-based cleaning agent for cleaning only when necessary. When other
solvents or cleaning agents are used, be sure to follow manufacturers’ instructions.
The agent should be applied to a clean cloth and should not be sprayed directly
onto the panel surface. After cleaning the agent should be removed.
Ammonia based glass cleaners (typically 5-10% ammonia) or 75% alcohol can be
used to clean the surface of PCAP and resistive touch panels.
When you clean the surface of your touch panel, please follow these steps:
BeijerElectronics, MAEN333 5

Safety Precautions
1. Apply cleaning agent (alcohol, bleach, or glass cleaner) to a clean cloth. Make
sure the cloth is well saturated.
2. Wipe touch panel in a “Z” motion on the touch panel surface.
3. Dry the panel thoroughly with a dry cloth, removing as much of the cleaning
solution as possible.
4. Do not mix bleach and ammonia because this will produce a dangerous
chemical reaction.
5. Please do not spray cleaning solution directly onto the touch panel surface.
Note:
•Cleaningsolutionscontainingbleach,alcohol,andammoniaarecorrosiveto
touchpanelsurfacecoatingsandITOfilm. So,youshouldnotleavethesolutionon
thetouchpanelsurfaceformorethan2minutes. Makesuretoremoveallresidue
whenfinishedcleaning.
•Donotusesharptoolstocleanthesurfaceofthetouchscreen.
•Donotuseairguns,waterjets,orsteam,tocleanthesurfaceoftouchscreensas
theymaydamagetouchscreenfunctionality.
•Ifcondiments,food,ordrinksarespilledonthesurfaceofthetouchscreen,please
removethemimmediately.
•Ensuremoisturedoesnotseepthroughthecableconnectionareafromtheedges
duringcleaning.
1.7 DismantlingandScrapping
•The operator panel or parts thereof shall be recycled according to local
regulations.
•The following components contain substances that might be hazardous to
health and the environment: lithium battery, electrolytic capacitor, and
display.
1.8 AppearanceofAirinTouchScreen
The layer structure of the touch screen contains air. In rare cases, the appearance
of bubbles can arise. This is purely cosmetic and does not affect the functionality
of the operator panel. The appearance can occur under certain environmental
conditions such as temperature, humidity, and atmospheric pressure.
BeijerElectronics, MAEN333 6

Naming Convention
2 NamingConvention
The name of each panel is based on its properties according to the table below.
X2family Size(inches) Genera-
tion/Version Variant
base
pro
marine(=with
BL)
control(=with
SC)
motion(=with
SM)
extreme
4
5
7
10
12
15
21
v2 SC
SM
HB
HP
BL
12V
SL
RO
CO
web
SoftControl
SoftMotion
HighBrightness
Highperformance
Black
12Volt
Sealed
RuggedOnly
CertificationOnly
Examples:
•X2 base 5 v2
•X2 pro 7
•X2 control 10
•X2 marine 12 SC
•X2 marine 15 HB SC
•X2 extreme 7 12V*
•X2 extreme 12 HP SC*
•X2 extreme 7 SL HP*
•X2 extreme 12 SL HP SC*
•X2 extreme 7 CO*
•X2 extreme 12 SL HP RO
Note:
Notallcombinationsareavailable.
Note:
*indicatesvariantsincludingIECEx\ATEXandC1D2accreditation.
BeijerElectronics, MAEN333 7

Installation
3Installation
3.1 SpaceRequirements
•Maximum installation plate thickness: 5 mm.
The following drawings show the space requirements in millimeters when
installing the operator panel. The drawings are only illustrative and may be out of
proportion.
100,00
100,00
50,00 50,00
100,00
3.2 InstallationProcess
The following is needed:
•A Phillips/slot screwdriver
Do the following:
1. Unpack and check the delivery. If damage is found, notify the supplier.
Note:
Placetheoperatorpanelonastablesurfaceduringinstallation.
Droppingtheoperatorpanelorlettingitfallmaycausedamage.
2. To cut a correct opening for the operator panel, use the cut out dimensions
in the outline drawing.A separate cut out drawing is available for download
from the Beijer Electronics web site. For more information, see sections
Operator Panel Drawings and Technical Data.
BeijerElectronics, MAEN333 8

Installation
3. Make sure that the mounting surface of the cutout is smooth and cleaned from
any burrs or debris.
4. Install the operator panel into the cutout.
5. In cases where the front panel seal is critical, use a torque wrench to ensure all
screws are torqued within the specification above.
6. Connect the cables in the specified order, according to the drawing and steps
below.
Caution:
•Theoperatorpanelmustbebroughttoambienttemperaturebeforeitisstarted
up. Ifcondensationforms,ensurethattheoperatorpanelisdrybeforeconnecting
ittothepoweroutlet.
•Ensurethattheoperatorpanelandthecontrollersystemhavethesameelectrical
grounding(referencevoltagelevel),otherwiseerrorsincommunicationmay
occur.
•Ensurethatthevoltageandpolarityofthepowersourceiscorrect.
•Separatehighvoltagecablesfromsignalandsupplycables.
•Shieldedcommunicationcablesarerecommended.
24V DC
RS232/
RS422/
RS485
24V DC
A
D
Controller
Power
B
Ethernet
C
The image is illustrative only and may differ slightly from the actual panel.
–Connect cable A.
–Connect cable B, using 14-20 AWG (2.08–0.52 mm2), 180–220 N-cm
torque.
–Connect cable C.
–Connect cable D. The recommended cross-section of the cable is 1.5
mm2.
7. Carefully remove the protective film over the operator panel display, take care
to avoid static electricity that could damage the panel.
BeijerElectronics, MAEN333 9

Installation
3.2.1 ConnectionstotheController
For information about the cables to be used when connecting the operator panel to
the controller, please refer to the help file for the driver in question.
3.2.2 OtherConnectionsandPeripherals
Cables, peripheral equipment and accessories must be suitable for the application
and its environment. For further details or recommendations, please refer to the
supplier.
3.2.3 OpenPorts
In the firmware there are some ports that are open by default due to the operating
system or that the internal application requires it.
Type Description Openbydefault
UDP Projecttransfer(9999) Yes
UDP Netbios(137) Yes
UDP Netbios(138) No(1)
(1)Filtered.
BeijerElectronics, MAEN333 10

Technical Data
4TechnicalData
Parameter X2base15v2HP
Frontpanel,W×H×D 409x270x43mm
Cutoutdimensions,
W×H 393x254(+/-1)mm
Mountingdepth 38mm(138mmincludingclearance)
Mounting Switchboardinstallation
Frontpanelseal IP65
Rearpanelseal IP20
Touchscreen
material Polyesteronglass,ITOfilm,resistive
Frameoverlay AutoflexEBA250L
Touchscreen
operations 1millionfingertouchoperations
Reverseside
material Plastic
Framematerial Plastic
Weight 2.46kg
CPU TISitaraAM335xSingleCore1GHz,(TIAM3352BZCZ100)
SerialportCOMA StandardDSUB(9-pin,female).
1xRS232RX/TXwithRTS/CTS
1xRS422or2xRS485
SerialportCOMB StandardDSUB(9-pin,female).
1xRS232RX/TXwithRTS/CTS
1xRS422or1xRS485
SerialportCOMC 3pinscrewconnector
1xRS485
EthernetLANA 10/100Mbit/s. ShieldedRJ45
EthernetLANB 10/100Mbit/s. ShieldedRJ45
USB-A 1×USBHost2.0,maxoutput500mA
USB-B 1×USBHost2.0,maxoutput500mA
Externalstorage
media 1×µSDcard
Flashmemory
(application
memory)
2GB
MemoryRAM 512MB(DDR3)
NVRAM 16kB
LED N/A
Realtimeclock Yes
Battery LithiumbatterytypeCR2032,exchangeable
Powerconsumption
atratedvoltage 17.8W
Fuse InternalDCfuse,3AT,SMD
BeijerElectronics, MAEN333 11

Technical Data
Parameter X2base15v2HP
Powersupply +24VDC(18-32VDC)
CE:Thepowersupplymustconformwiththerequirements
accordingtoEN/IEC60950andEN/IEC61558-2-4.
ULandcUL:Thepowersupplymustconformwiththe
requirementsforclass2powersupplies.
Display 15.6”TFT-LCDwithLEDbacklight. 1360x768pixels,16.7M
colors
Activeareaof
display,W×H 344.23x193.53mm
Pixelerrors ClassI(ISO9241-307)
Backlightbrightness 300cd/m2
Backlightlifetime 50000hours
Operating
temperature 0°C–+50°C
Storagetemperature -20°C–+60°C
Relativehumidityin
operation 5-90%non-condensed/25°C
Vibration 1g,accordingtoIEC60068-2-6,TestFc
Mechanicalshock 10g,half-sine,6msaccordingtoIEC60068-2-27
ULapproval Informationisavailableonhttp://www.beijerelectron-
ics.comand/orhttps://UL.com
BeijerElectronics, MAEN333 12

Chemical Resistance
5 ChemicalResistance
5.1 TouchScreenandOverlayMaterial
5.1.1 ProtectiveFilm
SolventResistance
The protective film withstands exposure of more than 24 hours duration under
DIN42115Part2tothefollowingchemicalswithoutvisiblechange:
Acetonitrile Diesel Petroleumspirit(1)
Ajax/Viminsolution Downy/Lenor(1) Phosphoricacid(<30%)
Alkalicarbonate
solution(1) Ethanol Potassiumferricyanide
Ammonia(<40%)(1) Glycerine Potassiumhydroxide(<30%)
Aceticacid(<50%) Glycol PureTurpentine
Arielpowderin
solution(1) Gumption(1) SBP60/95(1)
Bleach(1) Hydrochloricacid(<36%) Sulfuricacid(<10%)
Castoroil Linseedoil Tomatoketchup
Causticsoda(<40%)(1) Methanol Trichloroaceticacid(<50%)
Cuttingoil Nitricacid(<10%) WhiteSpirit
Cyclohexanol Paraffinoil Windex(1)
Diacetonealcohol Persilpowderinsolution(1) Wisk
(1)Extremelyfaintglossingofthetexturewasnoted.
The Autoflex protective film withstands DIN 42 115 Part 2 exposure of up to 1
hour duration to glacial acetic acid without visible change.
The Autoflex protective film is not resistant to high pressure steam at over 100
°C or the following chemicals:
Concentratedmineralacids Benzylalcohol
Concentratedcausticsolution Methylenechloride
BeijerElectronics, MAEN333 13

Chemical Resistance
5.1.2 TouchScreenSurface
The touch screen surface on the operator panel withstands exposure to the
following solvents without visible change:
Solvents Time
Acetone 10minutes
Isopropanol 10minutes
Toluene 5 hours
Thetouchscreensurfaceontheoperatorpanelismadeofpolyesterwithahard
coat to resist scratches and withstand exposure to many solvents without visible
change.
5.1.3 TouchScreenProtector
For harsh environments and exposure to outdoor conditions, it is recommended
to use a protective film to guard the touch screen from damage. This optional part
can be ordered from Beijer Electronics.
BeijerElectronics, MAEN333 14

Operator Panel Drawings
6 OperatorPanelDrawings
6.1 Connectors
Pos Connector Description
1 Groundscrew Screwtoconnectfunctionalgrund
2 Powersupply 3-pinscrewconnector,+24VDC(18-32VDC)
3 COM-A DSUB(9-pin,female),serialcommunicationport
4 LAN-A RJ45(shielded),10/100Mbit
5 USB-A/B USB2.0Host,maxoutputcurrent500mA
6 LAN-B RJ45(shielded),10/100Mbit
7 COM-B DSUB(9-pin,female),serialcommunicationport
8 COM-C 3-pinscrewconnector
BeijerElectronics, MAEN333 15

Operator Panel Drawings
COM-A
Serialportpinassignment
Pin COM1 COM2 COM3
1RS422TX+or
RS485Tx+/Rx+
2 RS232RxD
3 RS232TxD
4 RS422RX+ RS485Tx+/Rx+
5 GND GND GND
6RS422TX-or
RS485Tx-/Rx-
7RS232RTS
8RS232CTS
9 RS422RX- RS485Tx+/Rx-
Theconnectorsupportsuptothreeindependentserialcommunicationchannelsand
canbeconfiguredforRS-232andRS-422or2×RS-485.
COM-B
Serialportpinassignment
Pin COM4 COM5
1RS422TX+or
RS485Tx+/Rx+
2 RS232RxD
3 RS232TxD
4RS422RX+
5GND GND
6RS422TX-or
RS485Tx-/Rx-
7RS232RTS
8RS232CTS
9RS422RX-
Theconnectorsupportsuptotwoindependentserialcommunicationchannelsandcan
beconfiguredforRS-232andRS-422orRS-485.
BeijerElectronics, MAEN333 16

Operator Panel Drawings
COM-C
Serialportpinassignment
Pin COM6
1GND
2 RS485Tx+/Rx+
3 RS485Tx-/Rx-
BeijerElectronics, MAEN333 17

Additional Installation Tips
7 AdditionalInstallationTips
When experiencing communication problems in noisy environments or when
operating close to temperature limits, the following recommendations are to be
noticed.
7.1 Groundingtheoperatorpanel
1
2
3
4
5
6
5350
Door
Operator panel
Ferrite core
Mounting plate in the cabinet
Power supply
24 V DC
The mounting clamps of the operator panel do not provide a secure grounding
connection between the panel and the device cabinet, see 1 in drawing above.
1. Connect a wire, that is sized correctly according to local electrical codes,
between the quick-connect terminal connector on the operator panel and the
chassis of the panel, see 2 in drawing above.
2. Connect a wire or grounding braid, that is sized correctly according to local
electrical codes, between the chassis of the operator panel and the closest
grounding point on the door, see 3 in drawing above.
3. Connect a strong but short grounding braid between the door and the device
cabinet, see 4 in drawing above.
4. Twist the cables onto the 24 V DC feed, see 5 in drawing above.
2 turns around the ferrite core provide 4 times the suppression of 1 turn.
3 turns around the ferrite core provide 9 times the suppression of 1 turn.
Connect a wire or grounding braid, that is sized correctly according to local
electrical codes, between the chassis of the operator panel and the closest
grounding point.
BeijerElectronics, MAEN333 19

Additional Installation Tips
Note:
Thegroundingwiresshouldbeshortandtheconductorshouldhavealargearea.
Along,thingroundingwirehasaveryhighimpedance(resistance)athighfrequencies
anddoesnotguidedisturbancestotheground.
Multi-wireconductorsarebetterthansinglewireconductorswiththesamearea.
Abraidedconductorwirewiththesameareaisevenbetter. Thebestisashort,thick
groundingbraid.
7.2 EthernetConnectioninthe
OperatorPanel
1
2
3
4
5
RJ45
RJ45
RJ45
RJ45
RJ45
RJ45
RJ45
RJ45
Industrial Ethernet
Operator panel
Operator panel
Operator panel
Operator panel
Shielded
Short and
unshielded
0.1 μF
250 V
1-1
3-3
8-8
2-2
In some industrial units for Ethernet, the RJ45 contact’s shield is connected to the
chassis via a capacitor, see 1 in drawing above.
The operator panel’s Ethernet shield is directly connected to the chassis, see 2 in
drawing above.
1. Check whether the other Ethernet unit has its shield directly grounded or
grounded via a capacitor.
Note:
Inmanycases,connectingtheshieldedEthernetcablingtothechassisatbothendsis
inappropriate. Humorgroundingloopscanoccur. Unshieldedcablingmayevenresult
infewercommunicationerrors.
BeijerElectronics, MAEN333 20
Other manuals for X2 base 15 v2 HP
1
Table of contents
Other Beijer Electronics Thermostat manuals
Popular Thermostat manuals by other brands
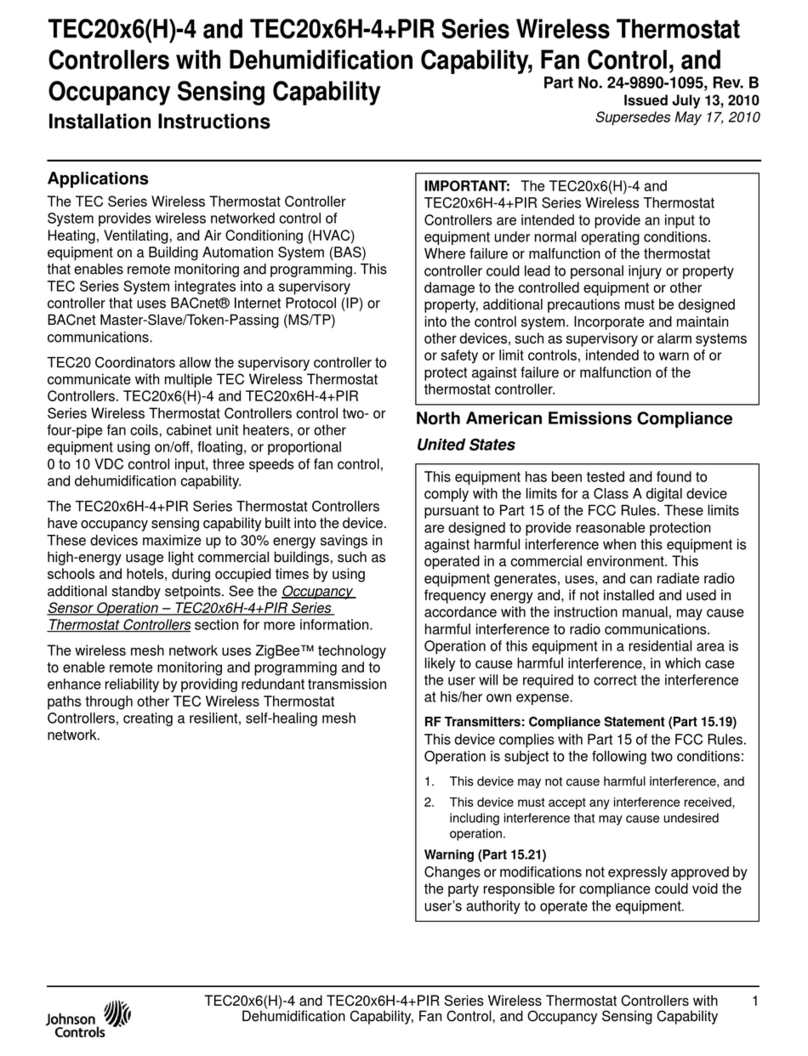
Johnson Controls
Johnson Controls TEC20x6-4 Series installation instructions

Radio Thermostat
Radio Thermostat CT110 install guide

Secure
Secure SRT323 User and installation instructions
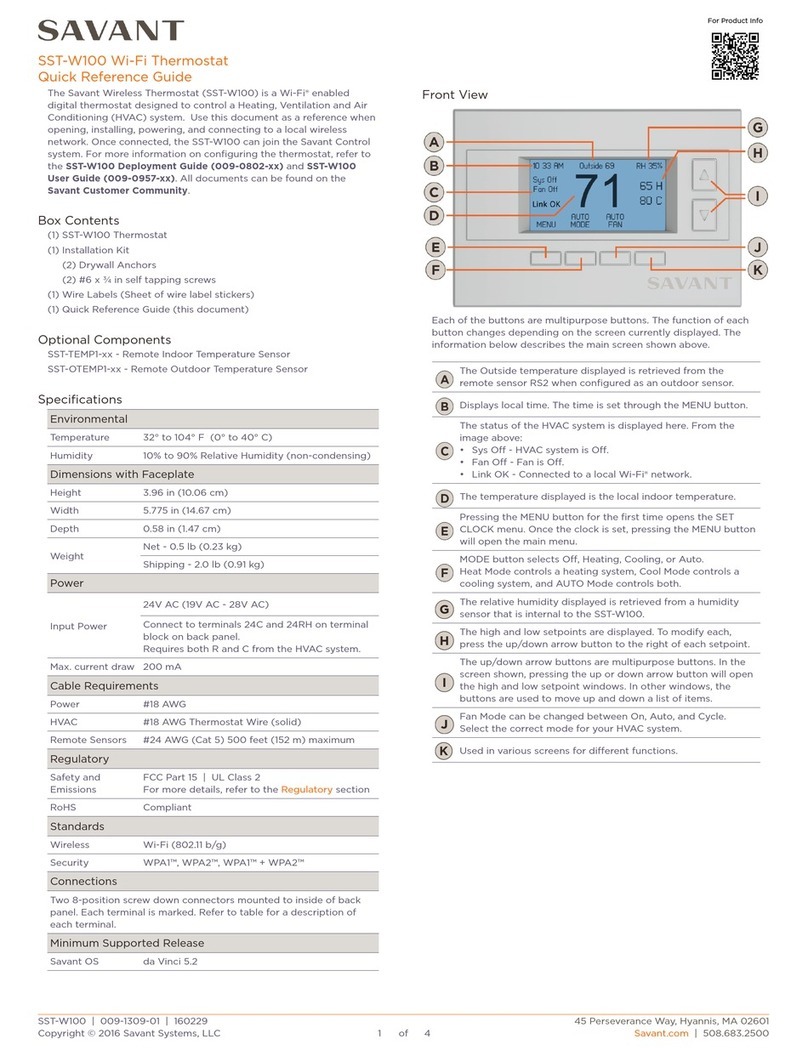
Savant
Savant SST-W100 Quick reference guide

Vector
Vector TLC3-BCR Series manual
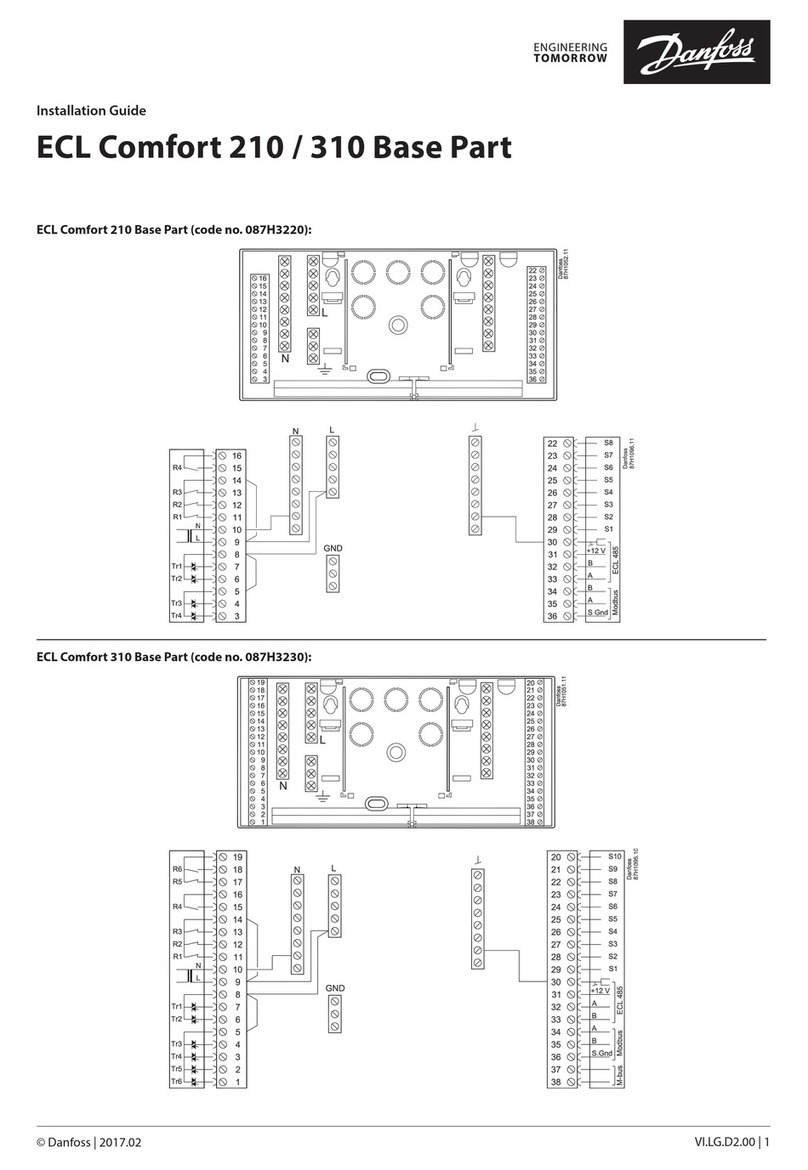
Danfoss
Danfoss ECL Comfort 210 installation guide