Bender ISOMETER isoRW425 User manual

Manual EN
isoRW425_D00052_05_M_XXEN / 04.2021
ISOMETER® isoRW425
Insulation monitoring device for unearthed
IT AC-, AC/DC and DC systems (IT systems)
for railway applications up to 3(N)AC, AC/DC 440 V
Software version: D0418 V2.xx

2 isoRW425_D00052_05_M_XXEN / 04.2021
Service and support for Bender products
First-level support
Technical support
Carl-Benz-Strasse 8 • 35305 Grünberg • Germany
Telephone: +49 6401 807-760
0700BenderHelp *
Fax: +49 6401 807-629
E-mail: support@bender.de
Available on 365 days from 7.00 a.m. to 8.00 p.m. (MEZ/UTC +1)
* Landline German Telekom: Mon-Fri from 9.00 a.m. to 6 p.m.: 6.3 cents/30 sec.; remaining time: 6.3
cents/min.
Mobile phone: higher, depending on mobile phone tariff
Repair service
Repair, calibration and replacement service
Londorfer Strasse 65 • 35305 Grünberg • Germany
Telephone: +49 6401 807-780 (technical issues) or
+49 6401 807-784, -785 (commercial issues)
Fax: +49 6401 807-789
E-mail: repair@bender.de
Field service
On-site service
Telephone: +49 6401 807-752, -762 (technical issues) or
+49 6401 807-753 (commercial issues)
Fax: +49 6401 807-759
E-mail: fieldservice@bender.de
Mon-Thu 7.00 a.m. to 4.00 p.m., Fri 7.00 a.m. to 1 p.m. (MEZ/UTC +1)

isoRW425_D00052_05_M_XXEN / 04.2021 3
ISOMETER® isoRW425
Table of Contents
1 General instructions ..........................................................................5
1.1 How to use this manual..............................................................................................5
1.2 Indication of important instructions and information....................................5
1.2.1 Signs and symbols ........................................................................................................5
1.3 Training courses and seminars.................................................................................5
1.4 Delivery conditions.......................................................................................................6
1.5 Inspection, transport and storage ..........................................................................6
1.6 Warranty and liability...................................................................................................6
1.7 Disposal of Bender devices........................................................................................6
1.8 Safety .................................................................................................................................7
1.9 Intended use...................................................................................................................7
2 Function...............................................................................................8
2.1 Device features ..............................................................................................................8
2.2 Functional description ................................................................................................9
2.2.1 Monitoring of the insulation resistance (R mode) .........................................10
2.2.2 Monitoring of the insulation impedance (Z mode)....................................... 10
2.2.3 Undervoltage/overvoltage monitoring .............................................................10
2.2.4 Self test/error codes .................................................................................................11
2.2.5 Malfunction ..................................................................................................................12
2.2.6 Assignment of the alarm relays K1/K2 ............................................................... 13
2.2.7 Measuring and response times.............................................................................13
2.2.8 Password protection (on, OFF).............................................................................. 14
2.2.9 Factory setting FAC ................................................................................................... 14
2.2.10 External, combined test or reset button T/R.................................................... 14
2.2.11 Fault memory ..............................................................................................................15
2.2.12 History memory HiS ..................................................................................................15
2.2.13 Interface/protocols.................................................................................................... 15
3 Installation, connection and commissioning ............................ 16
3.1 Installation ....................................................................................................................16
3.2 Wiring diagram ...........................................................................................................17
3.3 Commissioning ...........................................................................................................18
4 Device operation............................................................................. 19
4.1 Display elements........................................................................................................ 20
4.2 Menu structure............................................................................................................ 21
4.3 Menu „AL“ .....................................................................................................................22
4.3.1 Response value setting............................................................................................ 22
4.4 Menu „out“ ...................................................................................................................22
4.4.1 Configuration of the relay operating mode..................................................... 22
4.4.2 Relay alarm assignment „r1“ and „r2“ and LED assignment ......................23

4 isoRW425_D00052_05_M_XXEN / 04.2021
4.4.3 Fault memory configuration..................................................................................24
4.4.4 Interface configuration ............................................................................................24
4.5 Menu „t“......................................................................................................................... 24
4.5.1 Time configuration.................................................................................................... 24
4.6 Menu „SEt“.................................................................................................................... 25
4.6.1 Function configuration ............................................................................................25
4.7 Measuring value display and history memory................................................26
5 Data access using the BMS protocol ........................................... 27
6 Data access using the Modbus RTU protocol............................ 28
6.1 Reading out the Modbus register from the ISOMETER®..............................28
6.1.1 Command of the master to the ISOMETER® .................................................... 28
6.1.2 Answer of the ISOMETER® to the Master...........................................................28
6.2 Write Modbus register (parameter setting)......................................................29
6.2.1 Command of the Master to the ISOMETER®..................................................... 29
6.2.2 ISOMETER® answer to the Master ........................................................................ 29
6.3 Exception code ...........................................................................................................30
6.3.1 Structure of the exception code........................................................................... 30
7 Modbus register assignment of the ISOMETER® ...................... 31
7.1 Device-specific data types of the ISOMETER® ................................................. 34
7.1.1 Device name ................................................................................................................34
7.1.2 Measuring values .......................................................................................................34
7.1.2.1 Float = Floating point value of the channels..............................................................34
7.1.2.2 AT&T = Alarm type and test type (internal/external)...............................................35
7.1.2.3 R&U = Range and unit .........................................................................................................36
7.1.3 Alarm assignment of the relays ............................................................................ 37
7.2 Channel descriptions................................................................................................ 38
8 IsoData data string ......................................................................... 40
9 Technical data.................................................................................. 41
9.1 Tabular presentation.................................................................................................41
9.2 Standards, approvals and certifications.............................................................44
9.3 Ordering information ...............................................................................................44
9.4 Revision history........................................................................................................... 45

isoRW425_D00052_05_M_XXEN / 04.2021 5
ISOMETER® isoRW425
1 General instructions
1.1 How to use this manual
This manual is intended for qualified personnel working in electrical engineering and elec
tronics! Part of the device documentation, in addition to this manual, is the enclosed
“Safety instructions for Bender products”.
Read the manual before installing, connecting and commissioning the device.
Always keep the manual within easy reach for future reference.
1.2 Indication of important instructions and information
I Danger! Indicates a high risk of danger that will result in death or serious injury if
not avoided.
I Warning! Indicates a medium risk of danger that can lead to death or serious injury, if
not avoided.
I Caution! Indicates a low-level risk that can result in minor or moderate
injury or damage to property if not avoided.
i
Information can help to optimise the use of the product.
1.2.1 Signs and symbols
Disposal Temperature range protect from dust
protect from wetness Recycling RoHS
guidelines
1.3 Training courses and seminars
www.bender.de > Know-how-> Seminars.
1.4 Delivery conditions
The conditions of sale and delivery set out by Bender apply. These can be obtained from Bender
in printed or electronic format.
The following applies to software products:
“Software clause in respect of the licensing of standard software as part of de-
liveries, modifications and changes to general delivery conditions for products
and services in the electrical industry.”
Die Elektroindustrie

6 isoRW425_D00052_05_M_XXEN / 04.2021
General instructions
1.5 Inspection, transport and storage
Check the shipping and device packaging for transport damage and scope of delivery. The follow-
ing must be observed when storing the devices:
1.6 Warranty and liability
Warranty and liability claims in the event of injury to persons or damage to property are excluded
in case of:
• Improper use of the device.
• Incorrect mounting, commissioning, operation and maintenance of the device.
• Failure to observe the instructions in this operating manual regarding transport, com-
missioning, operation and maintenance of the device.
• Unauthorised changes to the device made by parties other than the manufacturer.
• Non-observance of technical data.
• Repairs carried out incorrectly.
• Use of accessories and spare parts not recommended by Bender.
• Catastrophes caused by external influences and force majeure.
• Mounting and installation with device combinations not recommended by the manufac-
turer.
This operating manual and the enclosed safety instructions must be observed by all persons
working with the device. Furthermore, the rules and regulations that apply for accident preven-
tion at the place of use must be observed.
1.7 Disposal of Bender devices
Abide by the national regulations and laws governing the disposal of this device.
For more information on the disposal of Bender devices, refer to
www.bender.de -> Service & support.

isoRW425_D00052_05_M_XXEN / 04.2021 7
ISOMETER® isoRW425
1.8 Safety
If the device is used outside the Federal Republic of Germany, the applicable local standards and
regulations must be complied with. In Europe, the European standard EN 50110 applies.
I Danger! Risk of electrocution due to electric shock!
Touching live parts of the system carries the risk of:
• A fatal electric shock
• Damage to the electrical installation
• Destruction of the device
Before installing and connecting the device, make sure that the installation has been de-ener-
gised. The rules for working on electrical systems must be observed.

8 isoRW425_D00052_05_M_XXEN / 04.2021
Function
2 Function
2.1 Intended use
The ISOMETER® monitors the insulation resistance RF(R mode) or the insulation impedance ZF
(Z mode) of unearthed AC/DC main circuits (IT systems) with nominal system voltages of 3(N)AC,
AC, AC/DC or DC 0 … 440 V. DC components existing in 3(N)AC, AC/DC systems do not influence
the operating characteristics, when a minimum load current of DC 10 mA flows.
A separate supply voltage Usallows deenergised systems to be monitored as well. The maximum
permissible system leakage capacitance Ceis 300 µF in R mode and 1µF in Z mode.
Any use other than that described in this manual is regarded as improper.
i
To ensure that the ISOMETER® functions correctly, an internal resistance of ≤ 1 kΩ must exist
between L1/+ and L2/- via the source (e.g. the transformer) or the load.
2.2 Device features
• Monitoring of the insulation resistance RF(R mode) or the insulation impedance ZF
(Z mode) of unearthed 3(N)AC, AC and DC systems (IT systems) with galvanically
connected rectifiers or inverters
• Insulation impedance ZF(Z mode) for 50 Hz or 60 Hz
• Measurement of the nominal system voltage Un(True RMS) with undervoltage and
overvoltage detection
• Measurement of residual voltages system to earth (L+/PE and L-/PE)
• Automatic adaptation to the system leakage capacitance Ceup to 300 μF in R mode and
1 μF in Z mode
• Automatic device self test with connection monitoring
• Selectable start-up delay, response delay and delay on release
• Two separately adjustable response ranges of 1…990 kΩ (alarm 1, alarm 2)
• Alarm signalling via LEDs („AL1“, „AL2“), a display and alarm relays („K1“, „K2“)
• N/C operation or N/O operation can be selected for the relays
• Measured value indication via multi-functional LCD
• Fault memory can be activated
• RS-485 (galvanically isolated) including the following protocols:
– BMS interface (Bender measuring device interface) for data exchange with other Bender components
– Modbus RTU
– IsoData (for continuous data output)
• Password protection to prevent unauthorised parameter changes

isoRW425_D00052_05_M_XXEN / 04.2021 9
ISOMETER® isoRW425
2.3 Functional description
The ISOMETER® measures the insulation resistance RFand the system leakage capacitance Ce
between the system to be monitored (L1/+, L2/-) and earth (PE). Z mode (selectable in the „SEt“
menu) calculates the insulation impedance ZFfrom RFand Cewith a system frequency parameter
fn= 50 Hz or fn= 60 Hz. The RMS value of the nominal system voltage Unbetween L1/+ and L2/-,
as well as the residual voltages UL1e (between L1/+ and earth) and UL2e (between L2/- and earth)
are also measured.
From a minimum value of the nominal system voltage, the ISOMETER® determines the faulty
conductor in % (represented by „R %“), which shows the distribution of the insulation resistance
between conductors L1/+ and L2/-. The distribution is indicated by a positive or negative sign
preceding the insulation resistance measurement. The value range of the faulty conductor is
±100 %:
Display Meaning
–100 % one-sided fault at conductor L2/-
0 % symmetrical fault
+100 % one-sided fault at conductor L1/+
The partial resistances can be calculated from the total insulation resistance RFand the faulty
conductor (R %) using the following formula:
Fault at conductor L1/+ RL1F = (200 % * RF)/(100 % + R %)
Fault at conductor L2/- RL2F = (200 % * RF)/(100 % – R %)
Also from a minimum value of the nominal system voltage, the ISOMETER® determines the
insulation resistance RUGF from the residual voltages UL1e and UL2e. It is an approximate value for
one-sided insulation faults and can be used as a trend indicator in cases where the ISOMETER® has
to adapt to an RFand Cerelation that varies considerably.
It is possible to assign the detected fault or the faulty conductor to an alarm relay via the menu. If
the values RF, ZFor Unexceed the response values activated in the „AL“ menu, this will be
indicated by the LEDs and relays „K1“ and „K2“ according to the alarm assignment set in the „out“
menu. In addition, the operation of the relay (n.o./n.c.) can be set and the fault memory „M“
activated.
If the values RF, ZFor Undo not exceed their release value (response value plus hysteresis) for the
period toff without interruption, the alarm relays will switch back to their initial position and the
alarm LEDs „AL1“/“AL2“ stop lighting. If the fault memory is activated, the alarm relays remain in
alarm condition and the LEDs light until the reset button „R“ is pressed or the supply voltage Usis
interrupted.
The device function can be tested using the test button „T“. Parameters are assigned to the
device via the LCD and the control buttons on the front panel; this function can be
password-protected. Parameterisation is also possible via the BMS bus, for example by using the
BMS Ethernet gateway (COM465IP) or the Modbus RTU.

10 isoRW425_D00052_05_M_XXEN / 04.2021
Function
2.3.1 Monitoring of the insulation resistance (R mode)
The two parameters that monitor the insulation resistance, „R1“ and „R2“, can be found in the
menu „AL“ (see table on page 22). The value R1 can only be set higher than the value R2. Each
time the mode is switched from R mode to Z mode, parameters „R1“ and „R2“, and hence the
monitoring of the insulation resistance will be deactivated.
In Z mode the insulation impedance ZFis the main measured value and the measured insulation
resistance RFcan have tolerances depending on the system condition. If required, the parameters
R1 and R2 can also be activated in Z mode.
If the insulation resistance RFreaches or falls below the activated values R1 or R2, an alarm
message will be signalled. If RFexceeds the values R1 or R2 plus the hysteresis value (see table on
page 22), the alarm will be cleared.
2.3.2 Monitoring of the insulation impedance (Z mode)
The parameters „Z1“ and „Z2“ for monitoring the insulation impedance ZFare available in the
„AL“ menu only when Z mode is activated. The value Z1 must be set higher than value Z2. The
insulation impedance ZFfor the selected system frequency fn (50 Hz or 60 Hz in the „SEt“ menu)
can be calculated from the measured values RFand Ceusing the formula below:
The lower resistance component of RFor Xce determines the amount of ZF. The higher resistance
component of RFor Xce can have a higher tolerance due to the measuring signal resolution.
If the insulation impedance ZFreaches or falls below the activated values Z1 or Z2, an alarm
message will be signalled. If ZFexceeds the values Z1 or Z2 plus the hysteresis value (see table on
page 22), the alarm will be cleared.
2.3.3 Undervoltage/overvoltage monitoring
In the menu „AL“ (see page 22), the parameters („U <“ and „U >“) for monitoring the nominal
system voltage Uncan be activated or deactivated. The maximum undervoltage value is limited
by the overvoltage value.
The RMS value of the nominal system voltage Unis monitored. If the nominal system voltage Un
reaches, falls below or exceeds the limit values („U <“ or „U >“), an alarm will be signalled. If the
maximum permissible system leakage capacitance Ceset for the ISOMETER® is exceeded, an alarm
message will be initiated even when the overvoltage limit value has been deactivated. The alarm
will be deleted when the limit values plus the hysteresis (see page 22) are no longer violated.

isoRW425_D00052_05_M_XXEN / 04.2021 11
ISOMETER® isoRW425
2.3.4 Self test/error codes
The integrated self-test function checks the function of the insulation monitoring device and the
connection monitoring checks the connections to the system to be monitored. The alarm relays
are not switched during the self test. This can be changed using the parameter „test“ in the alarm
assignment (see Chapter 5.4 Menu „out“). During the test, the display indicates „tES“.
When malfunctions are detected or connections are missing, the LEDs „ON“/“AL1“/“AL2“ flash.
The respective error codes („E.xx“) will be indicated on the display and the relay „K2“ switches.
The relays can be assigned to a device error with the parameter“Err“ in the „out“ menu in the
alarm assignment.
Error codes
If, contrary to expectations, a device error should occur, error codes will appearon the display.
Some of these are described below:
Error code Meaning
E.01
PE connection error
The connections„E“ or„KE“ to earth are interrupted.
Action:
Check connection, eliminate error. The error code will be erased automatically once the error has been
eliminated.
E.02
Connection error system (L1/+ , L2/-)
The mains internal resistance is too high, the connection between terminals„L1/+“ or„L2/-“ and the
mains supply is poor or has been interrupted, or L1/+ and L2/- are connected in reverse polarity to the
DC system to be monitored (Un< -50 V).
Action:
Check connection, eliminate error. The error code will be erased automatically once the error has been
eliminated.
E.05 Measurement technique error/calibration invalid
For the current software version
E.07
The maximum permissible system leakage capacitance Ceis exceeded
Action:
Device not suitable for the existing leakage capacitance:
Uninstall device.
E.08
Calibration error during the device test
Action:
If the error continues to exist after checking the device connections, there is an error inside the device.

12 isoRW425_D00052_05_M_XXEN / 04.2021
Function
Internal device errors „E.xx“ can be caused by external disturbances or internal hardware errors. If
the error message occurs again after restarting the device or after a reset to factory settings
(menu item „FAC“) , the device must be repaired.
After eliminating the fault, the alarm relays switch back automatically or they return to the initial
position by pressing the reset button.
The self test can take a few minutes. It can be suppressed for the duration of the device start by
setting the parameter in the menu „SEt“ to „S.Ct = off“. This allows the ISOMETER® to enter
measurement mode quickly after connecting the supply voltage Us.
Automatic self test
After switching on the supply voltage Us, the device runs a self test and repeats it every 24 h
(selectable: off, 1h, 24 h).
Manual self test
A self test is initiated by pressing the test button for a period greater than 1.5 s. While pressing
the internal test button „T“, all display elements available for this device are shown.
Connection monitoring
The connection monitoring, activated by the self test, checks the connections of the terminals „E“
and „KE“ to the protective earth conductor (PE). When an error is detected, the message device
error (Err) will be signalled and the error code „E.01“ appears on the display.
The system connection monitoring is used to check the terminal connections „L1/+“ and „L2/-“ to
the system to be monitored. When an interruption or a high-resistance connection between L1/+
and L2/- is detected via the internal resistance of the system, the device error („Err“) will be
signalled and the error code „E.02“ appears on the display. Since a test of the system connection
may take considerable time due to system disturbances or may even provide incorrect results,
the system connection monitoring can be disconnected using the parameter „nEt“ in the „SEt“
menu.
2.3.5 Malfunction
In addition to the self test described above, several functions in the insulation monitoring device
are continuously checked during operation. If a fault is detected, the device error („Err“) will be
signalled, the error code „E.xx“ appears on the display as an identifier for the error type xx and the
LEDs „ON“/“AL1“/„AL2“ will flash.
If the error occurs again after restarting the device or after a reset to factory settings, then contact
Bender Service.

isoRW425_D00052_05_M_XXEN / 04.2021 13
ISOMETER® isoRW425
2.3.6 Assignment of the alarm relays K1/K2
The messages „device error“, „insulation fault“, „insulation impedance fault“,„undervoltage/over-
voltage fault“, „device test“ or „device start with alarm“ can be assigned to the alarm relays via the
„out“ menu. An insulation fault is indicated by the messages „+R1“, „-R1“, „+R2“ and „-R2“.
Messages „+R1“ and „+R2“ can be assigned to indicate an insulation fault on conductor L1/+ and
the messages „-R1“ and „-R2“ could indicate an insulation fault on conductorL2/-. If an assignment
is not possible, for example in the event of a symmetrical insulation fault, the message
corresponding to „+“ and „-“ are shown together.
The message „test“ indicates a self test.
The message „S.AL“ indicates a so-called „device start with alarm“. After connecting to the supply
voltage Usand setting the parameter value to „S.AL = on“, the ISOMETER® starts with the
insulation measurement value RF= 0 Ω and ZF= 0 Ω in Z mode and displays all activated alarms.
The alarms will be cleared only when the measured values are up-to-date and no thresholds are
exceeded.
In the factory setting „S.AL = off“, the ISOMETER® starts without an alarm. It is recommended that
the value set for the „S.AL“ parameter is identical for both relays.
2.3.7 Measuring and response times
The measuring time is the period essential for the detection of the measuring value.
The measuring time is reflected in the operating time tae.
In R mode, the measuring time for the insulation resistance value is mainly determined by the
required measuring pulse duration, which depends on the insulation resistance RFand system
leakage capacitance Ceof the system to be monitored. The measuring pulse is produced by the
measuring pulse generator integrated in the ISOMETER® . The measuring times for Ce, UL1e, UL2e
and R % are synchronous. System disturbances may lead to extended measuring times.
In contrast, the time for the nominal system voltage measurement Unis independent and
considerably shorter. In Z mode a fixed and short measuring pulse time is applied, leading to a
short measuring time for all measured values.
Total response time tan
The total response time tan is the sum of the operating time tae and the on-delay time ton.
Operating time tae
The operating time tae is the time required by the ISOMETER® to determine the measuring value.
The insulation resistance measuring value depends on the the insulation resistance RFand the
system leakage capacitance Ce. For example, a maximum permissible system leakage capacitance
of Ce= 300 μF and an insulation fault of RF= 2.5 kΩ (Ran = 5 kΩ) in a 400 V DC system results in an
operating time of tae < 40 s. High system leakage capacitances and system interferences lead to
longer operating times.

14 isoRW425_D00052_05_M_XXEN / 04.2021
Function
Response delay ton
The response delay ton is set uniformly for all messages in the menu „t“ using the parameter „ton“.
This delay time can be used for interference suppression in the case of short measuring times.
An alarm will only be signalled when a threshold value of the respective measuring value is
violated for the period of ton without interruption. Every time the threshold value is violated
within the time ton, the response time „ton“ restarts once again.
Every alarm message listed in the alarm assignment has its own timer for ton.
Delay-on release toff
The delay-on release toff can be set uniformly for all messages in the menu „t“ using the parameter
„toff“.
An alarm will continuously be signalled until the threshold value of the respective measuring
value is not violated (including hysteresis) for the period of toff without interruption. Each time the
threshold value is not violated for the period of toff, the delay-on release toff restarts once again.
Every alarm message listed in the alarm assignment has its own timer for toff.
Start-up delay t
After connection to the supply voltage USthe alarm indication for the preset time (0…10 s) in the
parameter „t“ is suppressed.
2.3.8 Password protection (on, OFF)
If password protection has been activated (on), settings can only be made subject to the correct
password being entered (0...999).
2.3.9 Factory setting FAC
Activating the factory setting will reset all modified settings, with the exception of the interface
parameters, to the default upon delivery.
2.3.10 External, combined test or reset button T/R
Reset = Press the external button < 1.5 s
Reset with subsequent test = Press the external button > 1.5 s
Stop measuring function = Press and hold the external button
i
When the measuring function is stopped, the display shows „STP“.
The stop function can also be triggered by an interface command and in this case it can only be
reset via the interface.
Only one ISOMETER® may be controlled via a test/reset button. A galvanic parallel connection of
several test or reset inputs for testing multiple insulation monitoring devices is not allowed.

isoRW425_D00052_05_M_XXEN / 04.2021 15
ISOMETER® isoRW425
2.3.11 Fault memory
The fault memory can be activated or deactivated with the parameter „M“ in the menu „out“.
When the fault memory is activated, all pending alarm messages of the LEDs and relays remain
available until they are deleted by using the reset button (internal/external) or the supply voltage
Usis turned off.
2.3.12 History memory HiS
When the first error occurs after clearing the history memory, all measured values (that are
marked in the table on page 26) are stored in the history memory. This data can be read out
using the „HiS“ menu item. In order to be able to record a new data record, the history memory
must first be cleared via the imenu using „Clr“.
2.3.13 Interface/protocols
The ISOMETER® uses the serial hardware interface RS-485 with the following protocols:
• BMS
The BMS protocol is an essential component of the Bender measuring device interface
(BMS bus protocol). ASCII characters are used for the data transfer.
• Modbus RTU
Modbus RTU is an application layer messaging protocol and it provides Master/Slave
communication between devices that are connected altogether via bus systems and net-
works. Modbus RTU messages have a 16-ibit-CRC (Cyclic-Redundant Checksum), which
guarantees the reliability.
• IsoData
The ISOMETER® continously sends an ASCII data string with a cycle time of approximate-
ly 1 second. A communication with the ISOMETER® within this mode is not possible and
no additional transmitter may be connected via the RS-485 bus cable. The ASCII data
string for the ISOMETER® is described on page 41.
The parameter address, baud rate and parity for the interface protocols are configured in the
menu „out“.
i
With „Adr = 0“, the menu entries baud rate and parity are not shown in the menu and the
IsoData protocol is activated. With a valid bus address (i.e. not equal to 0), the menu item
„baud rate“ is displayed in the menu. The parameter value „---“ for the baud rate indicates the
activated BMS protocol. In this event, the baud rate for the BMS protocol is set to 9,600 baud.
If the baud rate is set unequal to „---“, the Modbus protocol with configurable baud rate is
activated.

16 isoRW425_D00052_05_M_XXEN / 04.2021
Installation, connection and commissioning
3 Installation, connection and commissioning
i
Application in railway vehicles/DIN EN 45545-2:2016
If the horizontal or vertical distance to adjacent components which do not meet the
requirements in table 2 of DIN EN 45545-2 is less than 20 mm or less than 200 mm respectively,
they are to be regarded as grouped. Refer to DIN EN 45545-2 chapter 4.3 Grouping rules.
3.1 Dimensions
Fig. 3–1 All dimensions in mm
3.2 Mounting
Variant A: DIN rail mounting Variant B: Screw mounting
The front plate cover can be opened at the lower part marked with an arrow.
93
45
67,5
36
31,1
47,5
74,5
2
2
1.
2.
3. Click!
&2 x
1 x
100
107
Click
M4
M4
!

isoRW425_D00052_05_M_XXEN / 04.2021 17
ISOMETER® isoRW425
3.3 Wiring diagram
For details about the conductor cross sections required for wiring, refer to the technical data on page 42.
Legend
Terminal Connections
A1, A2 Connection to the supply voltage Usvia fuse (line protection):
If supplied from an IT system, both lines have to be protected by a fuse.*
E, KE Connect each terminal separately to PE:
The same wire cross section as for„A1“,„A2“ is to be used.
L1/+, L2/– Connection to the 3(N)AC, AC or DC system to be monitored
T/R Connection for the external combined test and reset button
11, 14 Connection to alarm relay„K1“
11, 24 Connection to alarm relay„K2“
A, B RS-485 communication interface with connectable terminating resistance
Example: Connection of a BMS-Ethernet-Gateway COM465IP
i
* For UL applications:
Only use 60/75°C copper lines!
For UL and CSA applications, it is mandatory to use 5 A fuses for the protection of the
supply voltage Us.
US
L1/+
KE A1 A2
Test / Reset
14 24 11
K1 K2
T/R
L2/
E
L1/+
L2/-
PE
L3
COM465IP
RS-485
AB
R
ON AL1AL2 k
TR
MENU
R
on
o
14
24
11
A
T/R
B
L1/+
L2/-
E
KE
A2
A1

18 isoRW425_D00052_05_M_XXEN / 04.2021
Installation, connection and commissioning
3.4 Commissioning
1. Check that the ISOMETER® is properly connected to the system to be monitored.
2. Connect the supply voltage Usto the ISOMETER®.
The device carries out a calibration, a self test and adjusts itself to the IT system to be
monitored. When high system leakage capacitances are involved, this procedure may
take up to 4 min. The standard display then appears showing the present insulation
resistance, e.g.:
The pulse symbol signals an error-free update of the resistance and capacitance
measuring values. If the measuring value cannot be updated due to disturbances, the
pulse symbol will be blanked.
3. Starting a manual self test by pressing the test button „T“. Whilst the test button is
pressed and held down, all display elements available for this device are shown. During
the test, the „tES“ symbol flashes. Any internal malfunctions detected are shown on the
display as error codes (see page 11). The alarm relays are not checked during the test
(factory setting). The setting can be changed in the „out“ menu, so that the relays switch
into the alarm state during the manual self test.
4. Check factory setting for suitability.
Are the settings suitable for the monitored installation?
For the list of factory settings, refer to the tables on page 22 to page 25.
5. Check the function using a genuine insulation fault.
Check the ISOMETER® in the system being monitored against earth, e.g. via a suitable
resistance.

isoRW425_D00052_05_M_XXEN / 04.2021 19
ISOMETER® isoRW425
4 Device operation
The menu structure is illustrated schematically on the following pages.
After pressing the „MENU“ button for > 1.5 s, the first menu item „AL“ appears. Use and
(Enter) buttons for navigation and settings.
Up and down button:
• to navigate up or down the menu settings
• increasing or decreasing values
MENU
Pressing the MENU/Enter button for more than 1.5 s:
• Starts menu mode
or
• when the device already is in menu mode:
Exit menu item (Esc).
Any recent changes will not be stored.
Pressing the MENU/Enter button for less than 1.5 s:
• Confirms menu selection
or
• confirms modified value.
i
The areas of the display that can be configured flash!

20 isoRW425_D00052_05_M_XXEN / 04.2021
Device operation
4.1 Display elements
Device front/display Function
AL1 AL2
ON
AL1
AL2
green - On
yellow - Alarm
yellow - Alarm
Assignment according to table on page 23
T
Up button
Test button (press > 1.5 s)
R
Down button
Reset button (press > 1.5 s)
MENU
ENTER
MENU button (press > 1.5 s)
+
test onoff MAdr
L1L2
C
<
>
s
kM %
Fµ
{
{
{
{
12
3
4
567
8
{
9
{
10
Z
1 U: Nominal system voltage Un
R: InsuIation resistance RF
Z: Insulation impedance ZF
C: System leakage capacitance Ce
2Monitored conductor
3= :Voltage type DC
: Error-free measuring value update
~ :Voltage type AC
4Measured values and units
5Password protection is activated.
6In the menu mode, the operating mode of the respective alarm relay
is displayed.
7Communication interface
With measured value: isoData operation
8The fault memory is activated.
9Status indicators
10 Identification for response values and response value violation
Other manuals for ISOMETER isoRW425
6
Table of contents
Other Bender Power Distribution Unit manuals
Popular Power Distribution Unit manuals by other brands
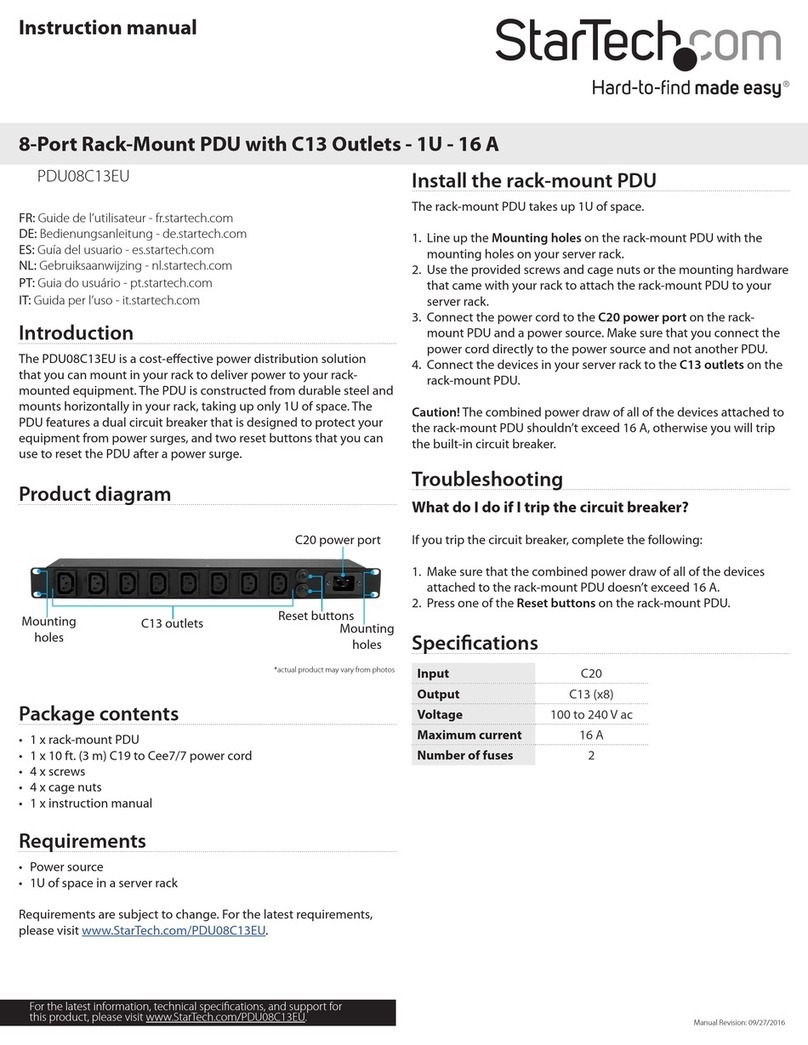
StarTech.com
StarTech.com PDU08C13EU instruction manual
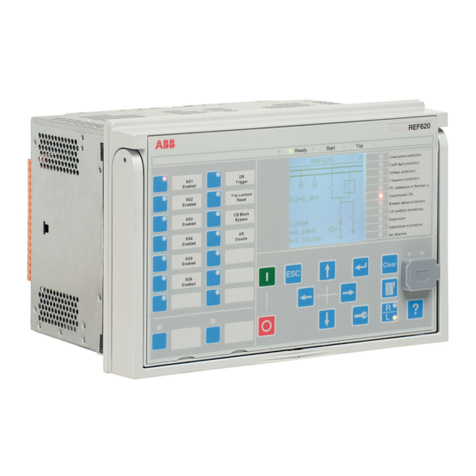
ABB
ABB Relion 620 Series Technical manual
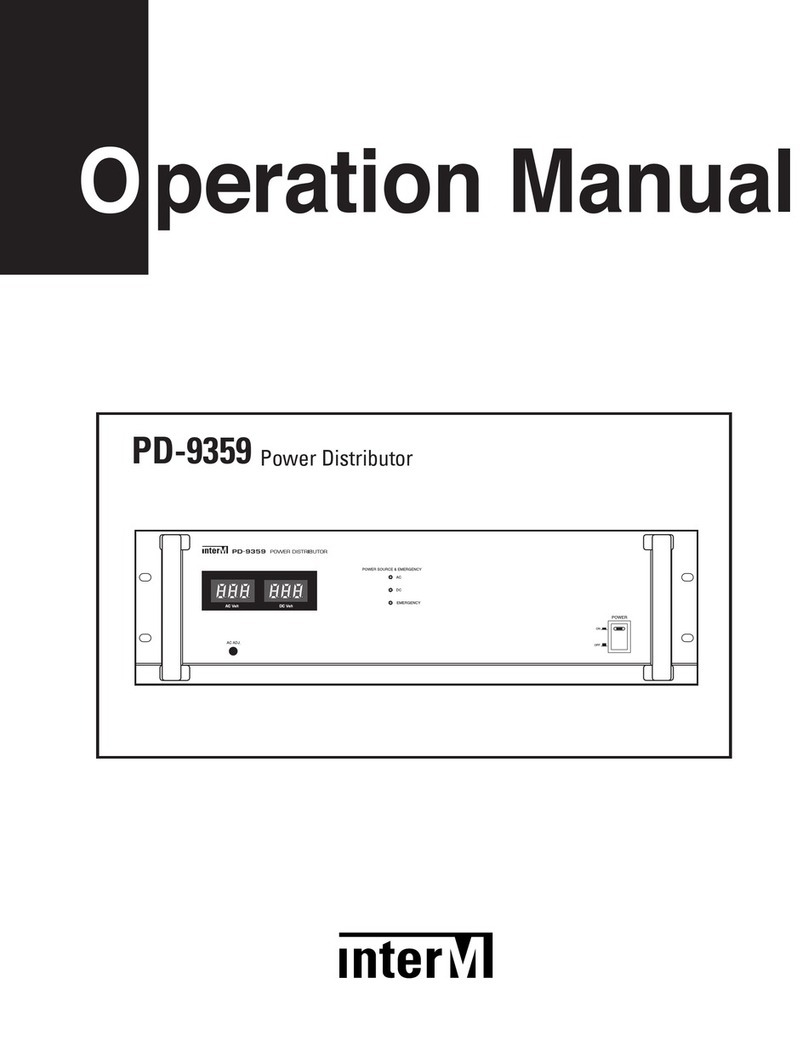
Inter-m
Inter-m PD-9359 Operation manual
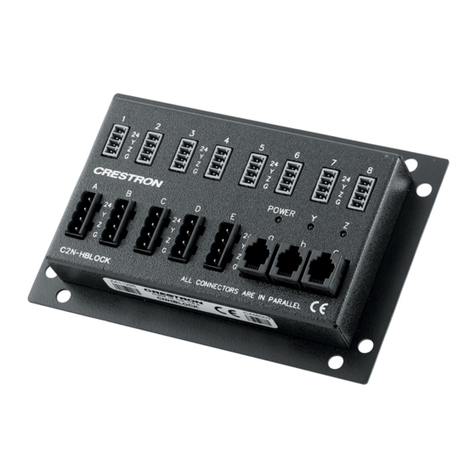
Crestron
Crestron Cresnet Network Design guide
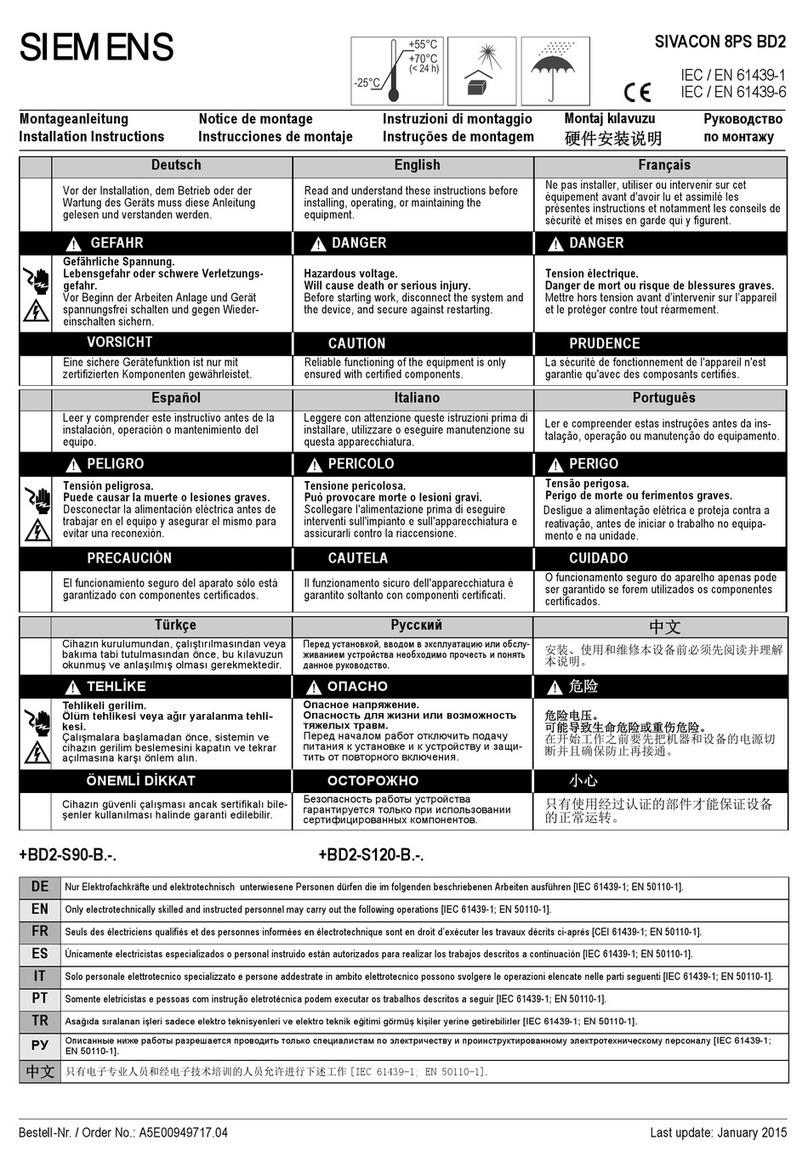
Siemens
Siemens SIVACON 8PS BD2-S90-B Series installation instructions
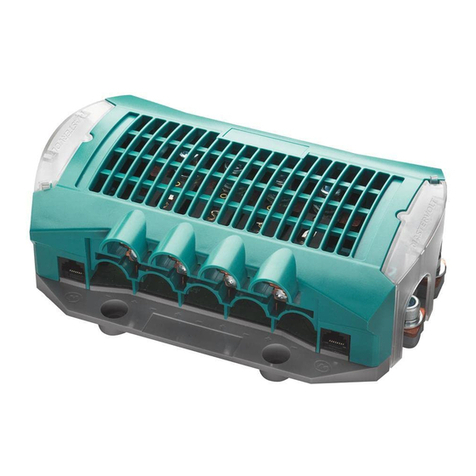
Mastervolt
Mastervolt DC Distribution 500 user manual